Утверждена
Миннефтегазстроем
СССР
3 мая 1983 года
ВЕДОМСТВЕННЫЕ СТРОИТЕЛЬНЫЕ НОРМЫ
ИНСТРУКЦИЯ
ПО ПРОИЗВОДСТВУ ОЧИСТКИ ПОЛОСТИ
И ИСПЫТАНИЮ СТРОЯЩИХСЯ МАГИСТРАЛЬНЫХ ТРУБОПРОВОДОВ
ВСН 157-83
Срок введения в
действие
1 мая 1984 года
В настоящей
Инструкции рассмотрены вопросы организации и технологии производства работ при
очистке полости, испытании и удалении воды после испытания трубопроводов,
приведены технические характеристики приборов, механизмов и машин, используемых
при этих технологических процессах.
При составлении
Инструкции были учтены предложения и замечания строительных и проектных
организаций Миннефтегазстроя и Мингазпрома.
Инструкция
предназначена для инженерно-технических работников, занятых проектированием
организации строительства и производством работ по очистке полости и испытанию
трубопроводов.
С введением в
действие настоящей Инструкции утрачивают силу "Указания по производству
работ при сооружении магистральных стальных трубопроводов. Вып. 7. Очистка
полости и испытание магистральных трубопроводов" (ВСН
1-50-74/Миннефтегазстрой).
Инструкция
разработана сотрудниками ВНИИСТа:
кандидатами техн. наук. Е.М. Климовским,
В.В. Рождественским, А.И. Тоутом, инженерами Л.П. Богачевой, В.П. Бровкиной,
Ю.В. Колотиловым, А.М. Резник, Я.Г. Ротмистровым и главным технологом Главного
технического управления инж. В.Г. Селиверстовым.
Внесена ВНИИСТом,
ОПН.
Утверждена Министерством строительства предприятий нефтяной и газовой
промышленности от 3 мая 1983 г.
1. ОБЩИЕ
ПОЛОЖЕНИЯ
1.1. Настоящая
Инструкция разработана на основании и в развитие норм и правил,
регламентированных СНиП III-42-80.
1.2. Требования
настоящей Инструкции необходимо соблюдать при производстве работ по очистке
полости, испытанию и удалению воды на строительстве новых магистральных
стальных трубопроводов диаметром до 1400 мм (включительно) с избыточным
давлением среды не выше 10 МПа (100 кгс/см2).
1.3. Очистку
полости и испытание трубопроводов, а также удаление из них воды следует вести
поточным методом специализированными участками (бригадами, звеньями),
обеспечивающими непрерывность всех работ в строгой технологической последовательности.
1.4. При разработке
технологии выполнения работ по очистке полости, испытанию трубопроводов и
удалению из них воды должны быть предусмотрены мероприятия, обеспечивающие:
высокое качество
работ;
сокращение сроков,
стоимости и трудоемкости работ;
максимальную
экономию природного газа, сжатого воздуха и воды, исключающую их
непроизводительные потери.
Указанные
мероприятия должны включать:
использование
сжатого воздуха или природного газа, накопленного в испытываемом участке, для
продувки или испытания прилегающего участка, а также для удаления из него воды;
использование воды,
накопленной в испытываемом участке для промывки прилегающего участка и
заполнения его водой и последующего испытания;
применение
инвентарных узлов обвязки машин для закачки воды или воздуха, а также узлов
подключения этих машин к трубопроводу;
применение
инвентарных узлов пуска и приема очистных (разделительных) устройств и, в
первую очередь, стационарных (проектных) узлов.
1.5. Результаты
производства работ по очистке полости и испытанию трубопроводов, а также по
удалению из трубопроводов воды должны быть оформлены актами, формы которых
приведены в Приложении 1 обязательном.
1.6. Требования по
технологии производства работ, регламентированные настоящей Инструкцией,
являются основанием для разработки специальных (рабочих) инструкций,
предусмотренных СНиП III-42-80, раздел II, применительно к конкретным условиям
строительства.
2. ОЧИСТКА
ПОЛОСТИ МАГИСТРАЛЬНЫХ ТРУБОПРОВОДОВ
2.1. Полость
магистральных трубопроводов до испытания должна быть очищена.
При очистке полости
для каждого объекта (на всем его протяжении или в пределах отдельных участков)
необходимо:
удалить
поверхностный рыхлый слой ржавчины и окалины, а также случайно попавшие внутрь
трубопровода при строительстве грунт, воду и различные предметы;
проверить проходное
сечение трубопроводов и тем самым обеспечить возможность многократного
беспрепятственного пропуска очистных, разделительных или других специальных
устройств;
создать условия для
заполнения трубопровода транспортируемой средой без изменения ее
физико-химических свойств.
2.2. Очистку
полости трубопроводов необходимо осуществлять одним из следующих способов:
продувкой с
пропуском очистных поршней, а при очистке надземных трубопроводов -
поршней-разделителей;
продувкой без
пропуска очистных поршней;
промывкой с
пропуском очистных поршней или поршней-разделителей.
На трубопроводах,
монтируемых без внутренних центраторов, следует выполнять предварительную
очистку полости протягиванием очистных устройств в процессе
сборки секций или труб в нитку.
2.3. Очистка
полости должна быть осуществлена:
на подземных
трубопроводах - после укладки и засыпки;
на наземных
трубопроводах - после укладки и обвалования;
на надземных трубопроводах
- после укладки и крепления их на опорах.
Особо сложные
участки трубопроводов, прокладываемые подземно в сильно заболоченной или
обводненной местности, продувают до укладки их в траншею (на бровке), при этом
укладку выполняют таким образом, чтобы в трубопровод не могла попасть вода, ил
и т.п.
Очистку полости
переходов через видные преграды следует выполнять путем пропуска эластичных
поршней-разделителей следующим образом:
на газопроводах -
промывкой, осуществляемой в процессе заполнения водой для предварительного
гидравлического испытания, или продувкой, проводимой до испытания переходов;
на нефтепроводах -
промывкой, осуществляемой в процессе заполнения трубопровода водой для
гидравлического испытания переходов.
2.4. Если очистное
устройство застряло в трубопроводе в процессе продувки или промывки, то это
устройство должно быть извлечено из трубопровода, а участок трубопровода
подвергнут повторной продувке или промывке.
2.5. После очистки
полости на открытых концах трубопроводов должны быть установлены временные
инвентарные заглушки, предотвращающие повторное загрязнение участка.
2.6. Для достижения
высокого качества и снижения затрат на очистку необходимо:
проводить
пооперационный контроль чистоты полости на всех этапах строительства
трубопроводов;
устанавливать
временные инвентарные заглушки:
а) на отдельные
трубы или секции при их длительном хранении на стеллажах, а также при
транспортировке к местам монтажа или перевалочным пунктам;
б) на концах плетей
в местах технологических разрывов.
ПРОДУВКА
ТРУБОПРОВОДОВ
2.7.
Последовательность продувки не зависит от назначения трубопроводов (газо-, нефте- или продуктопровод) и ее определяют по
конструктивной характеристике участка.
2.8. При продувке
подземных и наземных трубопроводов диаметром 219 мм и более необходимо
пропускать металлические очистные поршни.
2.9. Продувку
трубопроводов следует проводить сжатым воздухом. В отдельных случаях как
исключение по специальному согласованию продувку можно выполнять природным
газом.
2.10. При продувке
трубопроводов газом из них предварительно должен быть вытеснен воздух.
Газ для вытеснения
воздуха следует подавать под давлением не более 0,2 МПа (2 кгс/см2). Вытеснение воздуха считается законченным, когда
содержание кислорода в газе, выходящем из трубопроводов, составляет не более
2%. Содержание кислорода определяют газоанализатором.
2.11. При продувке
трубопровода запрещается пропускать загрязнения и очистное устройство через
линейную арматуру.
2.12. Источниками
воздуха для продувки трубопроводов служат передвижные компрессорные станции или
воздуходувки промышленных предприятий, расположенные вблизи сооружаемого
трубопровода.
2.13. Ресивер для
продувки создается на прилегающем участке трубопровода, ограниченном с обеих
сторон заглушками или запорной арматурой.
2.14. При
заполнении ресивера воздухом передвижные компрессорные станции можно
использовать по одной или объединить их в группы (ГК). В последнем случае
нагнетательные трубопроводы каждого компрессора подключают к коллектору, по
которому воздух подают к ресиверу.
2.15. Природный газ
для продувки газопроводов можно подавать:
из месторождений
газа, которые будут источником газа для строящегося объекта;
из действующего
магистрального газопровода, к которому присоединяют строящийся
трубопровод-отвод;
из действующих
газопроводов, пересекающих строящуюся магистраль или проходящих непосредственно
около нее (параллельная нитка).
При продувке
нефтепродуктопроводов природный газ подводят:
из действующих
газопроводов, пересекающих нефтепродуктопровод или проходящих непосредственно
около него;
из месторождений
газа, расположенных непосредственно около нефтепродуктопровода.
Для продувки могут
быть использованы также инертные газы, подводимые к трубопроводам от газовых
установок промышленных предприятий.
2.16. Продувку
трубопроводов от одного источника газа (или воздуха) следует проводить в
соответствии с принципиальными схемами (рис. 1).
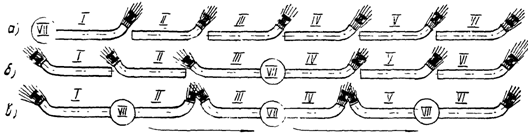
Рис. 1.
Принципиальные схемы организации продувки
трубопроводов от
одного источника газа (или воздуха):
а - линейная односторонняя при подключении головного
участка к
источнику, являющемуся ресивером; б - линейная
двусторонняя при расположении источника в одном пункте;
в - линейная двусторонняя при перемещении источников
воздуха; I - VI -
номера участков;
VII - источник газа
(или воздуха)
Участки
трубопроводов, непосредственно прилегающие к источнику газа, который является
ресивером, продувают по схеме, приведенной на рис. 1, а.
Продувку по
линейной односторонней схеме выполняют по отдельным участкам по мере их
готовности и в направлении от источника газа.
Продувку по
двусторонней линейной схеме (см. рис. 1, б) выполняют в двух направлениях от
узла подключения, который располагают в центре нескольких участков. В этом
случае группы компрессоров можно поместить между любыми двумя подготовленными к
продувке участками, которые поочередно используют в качестве ресивера.
Если по состоянию
строительных работ нельзя провести продувку более двух участков, то группу
компрессоров рационально перебазировать в соответствии со схемой (см. рис. 1,
в) для продувки других подготовленных участков.
Такое решение
принимают после определения технической и экономической целесообразности
перебазировки. Это положение приобретает особо важное
значение при работах в труднопроходимой местности.
2.17. Продувку
трубопроводов большой протяженности рекомендуется проводить от нескольких
источников газа (или воздуха) в соответствии с принципиальными схемами,
приведенными на рис. 2.
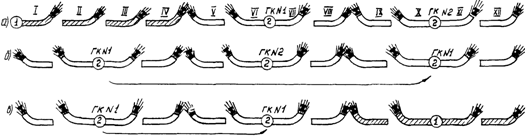
Рис. 2.
Принципиальные схемы организации продувки
трубопроводов от
нескольких источников газа или воздуха:
а - схема продувки
от одного источника газа, расположенного
в начале объекта, и
двух источников воздуха; б - схема
продувки воздухом; в - схема продувки от одного
источника
газа,
расположенного в конце объекта, и двух источников
воздуха; I - XII -
номера участков; 1 - источник газа;
2 - источник
воздуха; ГК - группа компрессоров
Схема продувки от
одного источника газа и двух источников воздуха показана на рис. 2, а, причем
источник газа расположен в начале трубопровода.
По приведенной
схеме продувают газопроводы, а также нефте- и продуктопроводы, в головной части
которых имеется источник газа. Газом продувают лишь участки I - IV, а участки V
- XII продувают воздухом от двух ГК.
Схема продувки
всего трубопровода воздухом (вариант с использованием двух ГК) показана на рис.
2, б, причем ГК N 1 располагают последовательно в двух пунктах, а ГК N 2 - в
одном пункте. Продувку по такой схеме выполняют на трубопроводах любого
назначения.
На рис. 2, в приведена схема продувки от источника
газа, расположенного в концевой части объекта, и двух источников воздуха, - в
головной и средней частях. Продувка по такой схеме может быть организована на
трубопроводе, концевой участок которого может быть подан газ из пересекающего
или проходящего вблизи газопровода.
2.18. Продувку
трубопроводов, строящихся между двумя источниками газа, следует проводить по
принципиальным схемам, приведенным на рис. 3.
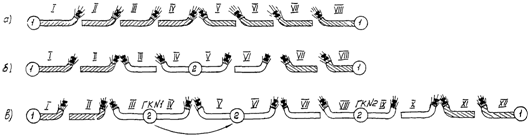
Рис. 3.
Принципиальная схема организации продувки
газопроводов,
строящихся между двумя источниками газа:
а - схема продувки газом; б - схема продувки от двух
источников газа и
одной или двух ГК; в - схема
продувки
от двух источников
газа и двух ГК;
I - XII - номера
участков;
1 - источник газа;
2 - источник воздуха;
ГК - группа
компрессоров
Продувку
газопроводов, начальный и конечный участки которых примыкают к источникам газа
(схема 3, а), осуществляют одновременно от обоих источников по линейной
односторонней схеме.
Схема продувки
газопроводов газом и воздухом приведена на рис. 3, б. Газом продувают головные
участки (I и II) и конечные (VII и VIII), а воздухом - средние участки (III,
IV, V и VI).
В зависимости от
протяженности участков, продуваемых воздухом, и темпа изоляционно-укладочных
работ создают одну или несколько ГК, причем ГК можно располагать в одном пункте
либо перемещать на подготовленные к продувке участки.
Схема продувки
газом от двух источников, расположенных на концах объекта, и воздухом от двух
ГК приведена на рис. 3, в ГК N 1 располагают в двух пунктах, из которых
закачивают воздух для продувки соответственно участков III - IV и V - VI. ГК N
2 устанавливают в одном пункте, из которого закачивают воздух для продувки
участков VII, VIII, IX и X. Участки I, II, XI и ХII
продувают газом от прилегающих источников.
2.19. Отбор
природного газа из действующего газопровода для продувки пересекающих или
строящихся трубопроводов проводят в соответствии с принципиальными схемами
(рис. 4).
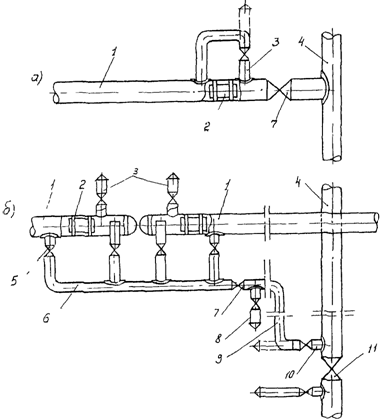
Рис. 4.
Схема отбора природного газа из действующих
газопроводов для
продувки пересекающих и строящихся
трубопроводов:
а - непосредственно
на месте проектной врезки
газопровода-отвода
в действующий газопровод;
б - через свечу действующего газопровода и временный шлейф,
подведенный к продуваемому участку;
1 - продуваемый
участок; 2 - поршень;
3 - свеча на узле
запасовки поршней;
4 - действующий
газопровод; 5 - кран коллектора;
6 - коллектор; 7 -
кран отключающий; 8 - свеча на шлейфе;
9 - шлейф; 10 -
свеча на действующем газопроводе;
11 - линейный кран
на действующем газопроводе
При отборе газа
непосредственно в месте проектной врезки газопровода-отвода в действующий
газопровод используют схему рис. 4, а.
При отборе газа от
газопровода, пересекающего строящуюся магистраль или проходящего
непосредственно около нее, целесообразно применять схему (рис. 4, б), по
которой подключение газа выполняют от продувочной свечи действующего
газопровода с прокладкой при необходимости временных шлейфов.
2.20. Отбор
природного газа при продувке второй и последующих ниток газопровода проводят от
места проектной врезки в действующую нитку по мере лупингования отдельных
участков.
2.21. При отборе
газа из действующих газопроводов следует проводить специальные мероприятия,
обеспечивающие бесперебойную эксплуатацию газопровода в период продувки
строящихся участков: разрабатывать схемы подключения шлейфа, определять
давление и объем газа для продувки, устанавливать время отбора газа и схему
связи.
Эти мероприятия
должны быть согласованы с управлением эксплуатации газопровода.
Все
сварочно-монтажные работы по прокладке шлейфа необходимо выполнять в
соответствии с нормами и правилами сооружения магистральных трубопроводов.
Продувка подземных
и наземных трубопроводов
с пропуском
очистных поршней
2.22. Продувку
трубопроводов следует проводить с применением поршней, оборудованных очистными
и герметизирующими элементами.
2.23. Продувка
должна быть выполнена с подачей сжатого воздуха от ресивера.
Оптимальные режимы
и параметры продувки, обеспечивающие высокое качество очистки полости
трубопроводов, рассчитывают в соответствии с методикой, приведенной в
Приложении 2 рекомендуемом.
2.24. При продувке
по очищаемому участку пропускают один поршень. Продувка считается законченной,
когда после вылета очистного поршня из продувочного патрубка начинает выходить
струя незагрязненного воздуха или газа.
Если после вылета
очистного поршня из трубопровода продолжает выходить струя загрязненного
воздуха или газа, то необходимо провести повторную продувку данного участка.
Если после вылета
очистного поршня из продувочного патрубка выходит вода, то по трубопроводу
следует дополнительно пропустить поршень-разделитель.
2.25. В ряде
случаев на газопроводах по согласованию с заказчиком проводят очистку полости в
три этапа. Дополнительные этапы очистки выполняют в период пусконаладочных
работ. С этой целью по участкам газопровода между стационарными камерами пуска
и приема очистных устройств пропускают
поршни-разделители в потоке газа, транспортируемого потребителю (рис. 5).
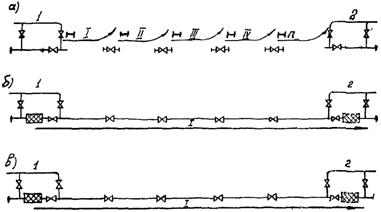
Рис. 5.
Принципиальная схема работ по очистке полости
магистральных
газопроводов в период строительства
и пусконаладочных
работ в три этапа:
а - продувка с
пропуском металлических очистных поршней
в период
строительства по отдельным участкам
(между линейной
арматурой) (I этап); б, в - очистка
полости
с пропуском
поршней-разделителей в потоке заполняющего
объект газа по участкам
между камерами приема и пуска
очистных устройств (б - 2 этап и в - 3 этап);
I, II, III, ..., n
- участки пропуска очистных устройств;
1 - камера пуска
очистных устройств;
2 - камера приема
очистных устройств
2.26.
Принципиальная схема продувки сжатым воздухом приведена на рис. 6.
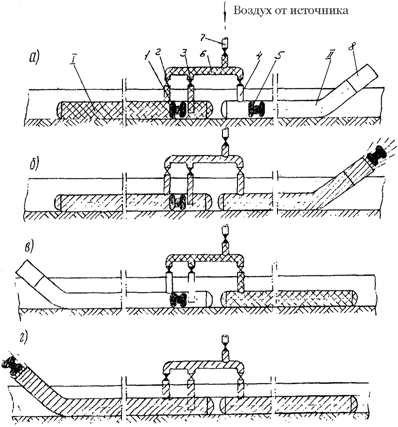
Рис. 6.
Принципиальная схема продувки
трубопроводов
воздухом:
а - участок
подготовлен к продувке плеча II;
б - выпуск поршня из плеча II; в - участок подготовлен
к продувке плеча I;
г - выпуск поршня из плеча I;
1 и 5 - очистные
поршни; 2, 3, 4 - перепускные патрубки
с кранами; 6 -
коллектор; 7 - подводящий патрубок;
8 - продувочный
патрубок
Узел подключения в
соответствии со схемами располагают в середине продуваемого участка, который
разделяет участок на два плеча, попеременно являющиеся ресивером и продувочным
плечом.
Продувку с
пропуском очистных поршней проводят в приведенной последовательности:
закачивают воздух
по патрубку 7 и коллектору 6 в плечо I (рис. 6, а), при этом краны на патрубках
3 и 4 должны быть закрыты и предварительно проверена герметичность плеча I;
открывают кран на
патрубке 4 и продувают плечо II (рис. 6, б);
отрезают
продувочный патрубок 8 на конце плеча II и вместо него устанавливают заглушку
(рис. 6, в);
срезают на конце
плеча I заглушку и устанавливают продувочный патрубок;
закачивают воздух
по подводящему патрубку и перепускному патрубку 4 в плечо II, при этом краны на
патрубках 2 и 3 необходимо закрыть и предварительно проверить герметичность
плеча II;
закрывают кран на
подводящем патрубке 7;
открывают краны на
перепускных патрубках 3 и 4 и продувают плечо I (рис. 6, в).
2.27. Продувку под
давлением природного газа проводят в последовательности, приведенной на рис. 7.
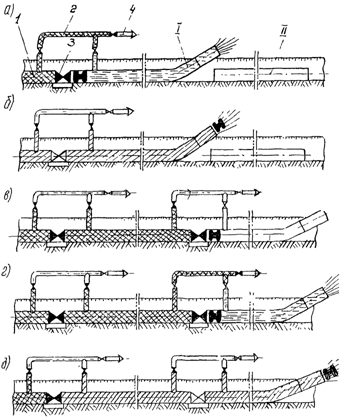
Рис. 7.
Принципиальная схема продувки трубопроводов газом
при подключении
участка непосредственно к источнику газа:
а - вытеснение
воздуха газом из участка I;
б - пропуск очистного поршня по участку I;
в - участок
заполнен газом для продувки участка II;
г - вытеснение воздуха газом из участка II;
д - пропуск
очистного поршня по участку II;
I, II - продуваемые
участки; 1 - источник газа,
являющийся ресивером для продувки участка I;
2 - байпас; 3 -
кран; 4 - свеча
Продувка
трубопроводов без пропуска очистных поршней
2.28. Продувку без
пропуска очистных поршней осуществляют скоростным потоком воздуха или газа.
2.29. Протяженность
участка трубопровода, продуваемого без пропуска поршней, не должна превышать 5
км.
2.30. Границы
продуваемых участков выбирают около мест возможного скопления загрязнений
(пониженные участки трассы, переходы через болота, глубокие овраги и т.п.).
Продувка надземных
трубопроводов
2.31. Продувку
надземных трубопроводов следует выполнять одним из способов, приведенных в
табл. 1.
Таблица 1
───────────────────────────────────────┬───────────────────────────────────
Конструктивная характеристика объекта
│ Способ очистки полости
───────────────────────────────────────┴───────────────────────────────────
В
виде змейки или прямолинейно
Продувка сжатым воздухом или
со
слабоизогнутыми участками из труб
природным газом в два этапа:
диаметром
от 114 до 1420 мм
предварительный - с пропуском
очистных устройств со скоростью
С
П-образными или трапецеидальными не
более 10 км/ч
компенсаторами
из труб диаметром окончательный - без пропуска
от
114 до 325 мм
очистных устройств скоростным
потоком воздуха
или газа
С
П-образными и трапецеидальными Продувка сжатым воздухом или
компенсаторами
из труб диаметром природным газом
без пропуска
от
325 до 1420 мм
очистных устройств
2.32. Надземные
трубопроводы необходимо продувать с пропуском очистных устройств облегченной
конструкции, масса и скорость передвижения которых не вызовут разрушения
трубопровода или опор.
2.33. Для продувки
надземных трубопроводов используют эластичные поршни-разделители ДЗК или
ДЗК-РЭМ.
2.34. Пропуск
разделителей следует осуществлять по отдельным участкам протяженностью не более
10 км со скоростью, не превышающей 10 км/ч.
2.35. Для снижения
износа эластичных разделителей их наружная поверхность перед запасовкой должна
быть увлажнена водой, а в условиях низких температур - дизельным топливом.
2.36. Сжатый воздух
для продувки подают:
а) непосредственно
от групп передвижных компрессорных станций при пропуске поршней-разделителей;
б) из ресивера при
создании скоростного потока в очищаемом участке или пропуске поршней.
Принципиальная
схема очистки надземных трубопроводов с пропуском очистных поршней
непосредственно от компрессорных станций с последующей продувкой скоростным
потоком воздуха приведена на рис. 8.

Рис. 8.
Принципиальная схема очистки надземных
трубопроводов с
пропуском очистных устройств
непосредственно от
компрессорных станций и последующей
продувкой
скоростным потоком воздуха:
а - заполнение
ресивера I сжатым воздухом;
б - пропуск очистного устройства под давлением воздуха,
поступающего непосредственно от компрессорных станций;
в - продувка плеча
II от ресивера без пропуска очистных
устройств; 1 и 5 -
очистные устройства;
2, 3, 4 -
перепускные патрубки с кранами; 6 - коллектор;
7 - подводящий
патрубок; 8 - продувочный патрубок;
9 - передвижные
компрессорные станции
2.37. Природный газ
для продувки с пропуском очистных устройств подают:
а) из ресивера;
б) непосредственно
от выходных узлов сборного пункта газового месторождения.
2.38. При появлении
в трубопроводах воды при продувке необходимо дополнительно пропустить
эластичный разделитель.
2.39. Чтобы
избежать разрушения газопроводов и опор в местах выхода воды и очистных
поршней, необходимо устанавливать временные опоры и закреплять на них
продувочные патрубки.
ПРОМЫВКА
ТРУБОПРОВОДОВ
2.40. Очистку
полости промывкой следует выполнять на трубопроводах (участках трубопроводов)
любых назначений и диаметров, которые испытывают гидравлическим способом.
2.41. При промывке
по трубопроводам пропускают поршни-разделители, перемещающиеся в потоке воды,
закачиваемой для гидравлического испытания.
Впереди
поршней-разделителей в трубопровод для размыва загрязнений заливают воду в
объеме, равном 10 - 15% от объема участка.
Принципиальная
схема производства работ при промывке трубопроводов приведена на рис. 9.
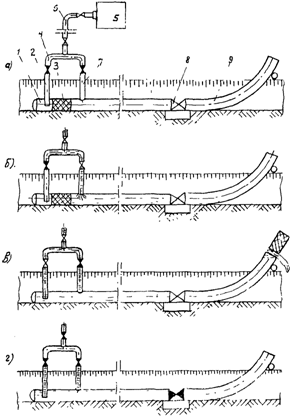
Рис. 9.
Принципиальная схема производства работ
при промывке
трубопроводов:
а - подготовка
участка к проведению промывки;
б - подача воды перед поршнем-разделителем;
в - пропуск
поршня-разделителя в потоке воды;
г - подготовка участка к испытанию; 1 - очищаемый участок;
2 и 7 - перепускные
патрубки с кранами;
3 -
поршень-разделитель; 4 - коллектор;
5 - наполнительные
агрегаты; 6 - подводящий патрубок;
8 - линейная
арматура; 9 - сливной патрубок
2.42. Пропуск
очистных устройств в потоке вода обеспечивает удаление из трубопроводов не
только загрязнений, но и воздуха, что исключает необходимость устанавливать воздухоспускные
краны (кроме кранов, предусмотренных проектом для эксплуатации).
2.43. Скорость
перемещения очистных устройств при промывке должна
быть не менее 1 - 1,5 км/ч.
2.44. Промывка
считается законченной, когда очистное устройство после прохода по трубопроводу
выйдет из него неразрушенным.
ПРЕДВАРИТЕЛЬНАЯ
ОЧИСТКА ТРУБОПРОВОДОВ
ПРОТЯГИВАНИЕМ
МЕХАНИЧЕСКИХ ОЧИСТНЫХ УСТРОЙСТВ
2.45. Очистку
полости трубопроводов методом протягивания очистных устройств выполняют
непосредственно в технологическом потоке сварочно-монтажных работ.
2.46. Очистные
устройства протягивают по трубопроводам, укладываемым подземным или наземным
способом, в процессе сборки и сварки отдельных секций или труб в нитку
трубопровода.
Очистку полости
надземных трубопроводов протягиванием очистных устройств выполняют до их
монтажа на опорах в процессе сборки и сварки секций или плетей.
2.47. В процессе
сборки трубопроводов очистное устройство перемещают внутри труб с помощью
штанги трубоукладчиком (трактором), приданным бригаде потолочной сварки.
Загрязнения удаляют в конце каждой секции (рис. 10).
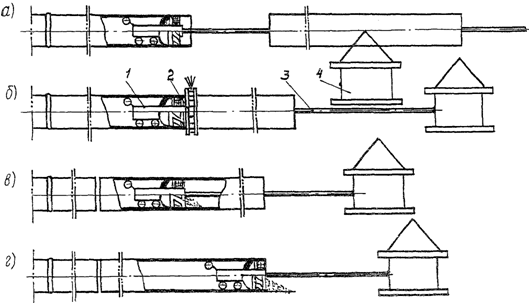
Рис. 10.
Принципиальная схема очистки полости трубопроводов
в процессе их
сборки в нитку с наружным центратором:
а - пропуск штанги
очистного устройства через секцию;
б - центровка
секций и сварка стыка; в - очистка
полости
собранной секции; г - выброс загрязнений из секций;
1 - очистное
устройство; 2 - наружный центратор;
3 - штанга; 4 -
трубоукладчик
2.48. В качестве
очистных устройств при протягивании могут быть
использованы специальные приспособления, оборудованные очистными щетками или
скребками, а также поршни, применяемые для продувки трубопроводов. При
использовании для протягивания поршней типа ОП последние должны быть
дополнительно оборудованы штангой (по типу используемых на
внутренних центраторах).
2.49. Очистка
полости в процессе сборки секций в нитку при положительной температуре воздуха
(если нет наледи на внутренней стенке трубы) должна обеспечивать удаление из
трубопроводов основного объема загрязнений.
Очистку полости при
отрицательной температуре воздуха проводят с целью удалить из трубопроводов не
примерзшие к стенке трубы загрязнения, посторонние предметы и снег.
3.
ИСПЫТАНИЕ МАГИСТРАЛЬНЫХ ТРУБОПРОВОДОВ
НА ПРОЧНОСТЬ И
ПРОВЕРКА ИХ НА ГЕРМЕТИЧНОСТЬ
3.1. Испытание
магистральных трубопроводов на прочность и проверку их на герметичность следует
выполнять одним из следующих способов:
гидравлическим (водой, незамерзающими жидкостями) - газопроводы, нефтепроводы и
нефтепродуктопроводы;
пневматическим
(воздухом, природным газом) - газопроводы;
комбинированным
(воздухом и водой или газом и водой) - газопроводы в горной и пересеченной
местности.
3.2. Испытание
магистральных трубопроводов на прочность и проверку на герметичность следует
проводить только при полной готовности всего трубопровода (или его участка),
для этого испытываемый объект должен быть:
уложен и засыпан;
обвалован или укреплен на опорах;
очищена полость;
установлены
арматура и приборы, катодные выводы;
удален персонал и
вывезена техника из опасной зоны;
обеспечена
постоянная или временная связь.
До выполнения
указанных работ по испытанию должна быть представлена в комиссию исполнительная
документация на испытываемый объект.
3.3. Способы
испытания, границы участков, величины испытательных давлений и схемы проведения
испытания, в которых указаны места забора и слива воды, согласованные с
заинтересованными организациями, а также пункты подачи газа и обустройство
временных коммуникаций определяются проектом.
Протяженность
испытываемых участков не ограничивается, за исключением случаев гидравлического
испытания и комбинированного способа, когда протяженность участков назначается
с учетом гидростатического давления.
В зависимости от
категорий участков трубопроводов и их назначения этапы, величины давлений и
продолжительность испытаний трубопроводов на прочность
и проверку на герметичность следует принимать в соответствии с табл. 17 СНиП
III-42-80 (Приложение 3 обязательное).
3.4. Установленные
проектом способы испытания на прочность и проверки на герметичность могут быть
изменены при представлении строительно-монтажной организацией своих технических
решений, согласованных с проектной организацией и заказчиком в зависимости от
конкретных условий производства работ.
Изменения способов
испытания на прочность и проверки на герметичность газопроводов должны быть
согласованы с органами Госгазнадзора СССР.
3.5. В целях повышения качества строящихся трубопроводов границы испытываемых
участков следует по возможности совмещать с местами, где на трубопроводе
установлена линейная арматура, а также сокращать количество неиспытанных
"гарантийных" стыков.
3.6. Если в
процессе испытания трубопровода произошли отказы (разрывы, утечки и т.п.), то
трубопровод подлежит ремонту и повторному испытанию на прочность и проверке на герметичность.
ГИДРАВЛИЧЕСКОЕ
ИСПЫТАНИЕ
3.7. Для проведения
гидравлического испытания давление внутри трубопроводов следует создавать
водой.
В отдельных случаях
(испытание коротких участков трубопроводов при минусовых температурах наружного
воздуха) по согласованию с проектной организацией и заказчиком допускается
применять для гидравлического испытания незамерзающие среды (раствор поваренной
соли, антифризы, дизельное топливо).
3.8. В качестве
источников воды для гидравлического испытания следует использовать естественные
или искусственные водоемы (реки, озера, водохранилища, каналы и т.п.),
пересекаемые строящимся трубопроводом или расположенные вблизи от него.
Объем воды в источниках
должен быть достаточным для проведения испытания, а уровень обеспечивать подачу
ее в трубопровод чистой (без механических примесей). Время заполнения
трубопроводов водой и воздухом определяют по номограмме (Приложение 4
рекомендуемое).
3.9. В состав работ
по гидравлическому испытанию входят следующие работы:
подготовка к
испытанию и удалению воды;
наполнение
трубопровода водой;
подъем давления в
трубопроводе до испытательного;
испытание на
прочность;
сброс давления до
максимального рабочего;
проверка на
герметичность;
сброс давления до
0,1 - 0,2 МПа (1 - 2 кгс/см2);
удаление воды.
При необходимости
включаются дополнительные работы, связанные с ликвидацией отказов.
3.10. Для
гидравлического испытания трубопровод следует разделить на участки, протяженность
которых ограничивают с учетом разности высотных отметок по продольному профилю
и испытательных давлений, установленных проектом.
Методика
определения протяженности и числа участков испытания в пределах одного объекта
приведена в Приложении 2 рекомендуемом.
3.11. Изменение
давления при гидравлическом испытании каждого участка должно соответствовать
графику, приведенному на рис. 11.
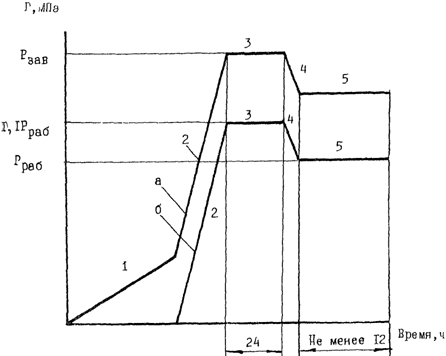
Рис. 11. График
изменения давления в трубопроводе
при гидравлическом
испытании:
1 - заполнение
трубопровода водой; 2 - подъем давления
до
(а - в нижней точке
трубопровода
;
б - в верхней точке трубопровода
не менее 1,1
;
3 - испытание на
прочность; 4 - снижение давления до
;
5 - проверка на
герметичность
3.12. При
подготовке к испытанию каждого участка необходимо в соответствии с принятой
схемой испытания выполнить следующие операции:
отключить
испытываемый участок от смежных участков сферическими заглушками или линейной
арматурой;
смонтировать и
испытать обвязочные трубопроводы наполнительных и опрессовочных агрегатов;
смонтировать узел
подключения агрегатов к трубопроводу, совмещенный с узлом пуска
поршней-разделителей для промывки;
запасовать
разделитель в узел пуска;
смонтировать узел
приема поршней-разделителей;
смонтировать
контрольно-измерительные приборы;
смонтировать (при
необходимости) воздухоспускные краны.
3.13.
Гидравлическое испытание выполняют по двум основным схемам - в одну или в обе
стороны от источника воды.
3.14. При
выполнении работ по односторонней схеме наполнительные и опрессовочные агрегаты
устанавливают в начале или в конце испытываемого участка. Наполнение и подъем
давления осуществляют в одну сторону от узла подключения до конца участка.
При выполнении
работ по двусторонней схеме испытания агрегаты устанавливают в средней части
участка, разделяя его на два плеча, испытываемых самостоятельно. В этом случае
узел подключения выполняют так, чтобы наполнение и подъем давления в каждом
плече можно было выполнять независимо от работ на другом плече.
В схеме испытания
необходимо предусматривать возможность перепуска воды в участки, которые
подлежат последующему испытанию.
3.15. При
необходимости создать на отдельных участках различные давления или использовать
источники воды, расположенные на соседних участках (если их нет на испытываемом
участке), то выполняют гидроиспытание с перемещением агрегатов по одной из
схем, приведенных на рис. 12.

Рис. 12.
Принципиальные схемы гидравлического испытания
объектов большой
протяженности:
а - первый вариант
односторонней схемы;
б - второй вариант односторонней схемы;
в - третий вариант
односторонней схемы;
г - первый вариант двусторонней схемы;
д - второй вариант
двусторонней схемы; I - IV участки;
V - VII - источники
воды; 1 - наполнительный агрегат;
2 - опрессовочный
агрегат; 3 - заполнение; 4 - опрессовка
3.16. При
заполнении участков трубопроводов водой для гидравлического испытания из них необходимо
полностью удалить воздух.
Удаление воздуха из
трубопроводов должно быть осуществлено с помощью поршней-разделителей или через
воздухоспускные краны, установленные в местах возможного скопления воздуха и
перед обводненными участками, на которых не предусмотрена балластировка.
3.17. Диаметр
воздухоспускных кранов следует выбирать в зависимости от суммарной
производительности наполнительных агрегатов и диаметра трубопровода.
Для трубопроводов
диаметром до 500 мм и суммарной производительности агрегатов менее 300 м3/ч
устанавливают воздухоспускные краны диаметром 25 - 32 мм, при диаметрах
трубопроводов более 500 мм и большей суммарной производительности агрегатов -
воздухоспускные краны диаметром 50 - 100 мм.
На концах
испытываемых участков в узлах обвязки следует устанавливать воздухоспускные
краны диаметром не менее 50 мм.
3.18. Наполнение
трубопроводов без пропуска разделителя необходимо осуществлять при открытых
воздухоспускных кранах, которые закрывают, как только через них перестанет
выходить воздух и потечет плотная струя воды.
3.19. Вытеснение из
трубопроводов воздуха с пропуском поршней-разделителей следует выполнять по
отдельным участкам, подготовленным к гидравлическому испытанию.
3.20. Для
вытеснения воздуха поршни-разделители необходимо перемещать впереди потока
воды, поступающей в трубопровод для гидравлического испытания.
3.21. Перед
пропуском поршня-разделителя должны быть закрыты все воздухоспускные краны, а
также полностью открыты линейные задвижки.
3.22. Выход
разделителя из узла пуска, а также его проход в узел приема следует
контролировать по приборам типа СКГ (сигнализатор для контроля
за перемещением разделителей).
Прибор СКР
монтируют на патрубке, приваренном к трубопроводу. Подвижный рычажок прибора
входит через патрубок внутрь трубопровода. При проходе разделителя рычажок
утапливается в патрубок и одновременно поворачивает лимб-указатель.
3.23. На
трубопроводах, испытываемых гидравлическим способом (поршни-разделители
перемещаются под давлением воды), операцию вытеснения воздуха объединяют с
процессом очистки полости трубопровода промывкой.
3.24. При
проведении гидравлических испытаний в осенне-зимний период следует учитывать
начало и глубину промерзания грунтов в районах сооружения трубопровода.
3.25. Проведение
гидравлического испытания при температуре окружающего воздуха ниже 0 °C
допускается лишь при условии предохранения трубопровода, линейной арматуры и
приборов от замерзания.
3.26. При
подготовке к гидравлическому испытанию в осенне-зимний период, чтобы
предупредить замерзание воды при внезапном похолодании, необходимо тщательно
проконтролировать засыпку или обваловывание трубопровода на всем его
протяжении. Особое внимание следует обратить на то, чтобы линейная арматура и
узлы подключения были тщательно укрыты.
3.27. После того
как выпадет снег, необходимо дополнительно утеплить трубопровод путем его
обвалования снегом, так как теплозащитные свойства слоя снега толщиной 20 см
эквивалентны примерно 100 см грунта.
3.28. При испытании
трубопроводов на прочность и их проверку на герметичность места утечек следует
определять следующими методами:
визуальным методом,
предполагающим определение места выхода из трубопроводов непосредственно
испытательной среды (вода, воздух, газ) и учитывающим основные признаки
появления утечек, приведенные в табл. 2;
визуальным методом,
предполагающим определение места выхода из трубопроводов воды, окрашенной
трассирующими веществами - красителями;
акустическим
методом, предполагающим определение места утечек по звуку вытекающей из
трубопроводов жидкости или газа без помощи или с помощью приборов;
методом поиска
утечек по запаху специальных веществ (одорантов), добавляемых в испытательную
среду (воду, воздух, газ);
методом
поиска утечек природного газа, основанном на анализе приборами проб воздуха над
поверхностью грунта;
методом определения
утечки по падению давления на испытываемом участке.
Таблица 2
─────────────────────────────────┬─────────────────────────────────────────
Основные признаки утечек │ Способы испытаний
├──────────────┬──────────────────────────
│гидравлический│
пневматический
│
├────────┬─────────────────
│ │воздухом│ природным
│ │ │ газом
─────────────────────────────────┴──────────────┴────────┴─────────────────
Видимый
выход воды, воздуха, газа +
<*> + +
Выброс
грунта из траншеи +
<**> + +
Изменение
цвета
- - +
(пожелтение
растительности)
Изменение
цвета - + +
(потемнение
снежного покрова)
Появление
пены или пузырей + (пена) + +
на
поверхности воды
(пузыри) (пузыри)
Намокание
валика, промоины
+ - -
и
провалы валика и траншеи
--------------------------------
<*>
Видимый выход воды может быть не обнаружен при утечках в нижней части трубы.
<**>
Выброс грунта из траншеи наблюдается редко и только при больших разрывах.
Методика
определения размера дефекта по падению давления в трубопроводе приведена в
Приложении 4 рекомендуемом.
Места утечек с
помощью трассирующих веществ (красителей), а также с помощью приборов следует
определять при условии выполнения требований специальных инструкций по
технологии производства работ конкретным методом.
Для ускорения и
упрощения поиска утечек трубопроводы, на которых ведут эти работы, разделяют на
отдельные захватки, ограниченные арматурой или заглушками.
ПНЕВМАТИЧЕСКОЕ
ИСПЫТАНИЕ
3.29. Для
проведения пневматического испытания давление внутри трубопроводов следует
создавать сжатым воздухом или природным газом.
3.30. В качестве
источников сжатого воздуха используют передвижные компрессорные станции,
которые в зависимости от объема полости испытываемого участка и величины
испытательного давления применяют по одной или объединяют в группы (ГК).
3.31. В качестве
источников природного газа необходимо использовать:
месторождения
(промыслы), которые являются источниками газа для данного строящегося объекта
или расположены вблизи от этого объекта;
действующие
газопроводы, к которым присоединяют строящиеся объекты-отводы или
объекты-перемычки;
действующие
газопроводы, пересекающие строящийся объект или проходящие непосредственно
около него.
3.32. Работы по
пневматическому испытанию трубопроводов следует в основном вести в соответствии
с принципиальными схемами, приведенными на рис. 13.
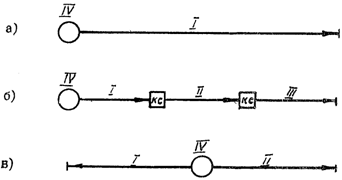
Рис. 13.
Принципиальные схемы пневматического испытания
а - в одну сторону
от источника газа (или воздуха);
б - в одну сторону от источника газа (или воздуха)
с подъемом давления
по отдельным участкам с помощью
компрессоров; в - в обе стороны от источника газа
(или воздуха); I -
III - испытываемые участки;
IV - источник газа
(или воздуха);
КС - компрессорная
станция
3.33. Изменение
давления в трубопроводах при пневматическом испытании на прочность и проверке
на герметичность должно соответствовать графику (рис. 14), причем закачивать
испытательную среду в трубопровод следует плавно со скоростью не более 0,3 МПа
(3 кгс/см2) с осмотром трассы при давлении, равном 0,3
от испытательного на прочность, но не выше 2 МПа (20 кгс/см2).

Рис. 14. График
изменения давления в трубопроводе
при пневматическом
испытании:
1 - подъем давления
от 0 до 0,3
, но не
выше 2 МПа
(20 кгс/см2); 2 - осмотр трассы; 3 - подъем давления до
;
4 - испытание на
прочность; 5 - снижение давления до
;
6 - проверка на
герметичность
3.34. Положение
арматуры на испытываемом участке трубопровода должно соответствовать схеме,
показанной на рис. 15.

Рис. 15.
Принципиальная схема положения арматуры
и расстановки
манометров при пневматическом испытании
газопроводов
(вариант для участка испытания газопровода
1400 мм с установкой одного крана с односторонней
продувкой (I) и
двух кранов с двусторонней продувкой (II):
а - заполнение и
испытание на прочность; б - проверка
на герметичность; 1
- одоризатор; 2 - заглушка;
3 - игольчатый
вентиль; 4 - манометр; 5 - свеча;
6 - кран байпасной
линии; 7 - линейный кран
3.35. Заполнение
трубопровода средой до создания в нем испытательного давления на прочность, а
также испытание на прочность в течение 12 ч следует выполнять при открытых
кранах байпасных линий и закрытых линейных кранах (рис. 15, а).
После того как
испытания трубопровода на прочность закончены для проверки его на герметичность,
должны быть закрыты краны байпасных линий (рис. 15, б).
3.36. Чтобы быстрее
выявить утечку воздуха или природного газа, в трубопроводы в процессе их
закачки необходимо добавлять одорант. Для этого на узлах подключения к
источникам воздуха или газа необходимо монтировать установки для дозирования
одоранта. Рекомендуемая норма одоризации этилмеркаптаном 50 - 80 г на 1000 м3
газа или воздуха.
3.37. Если при
осмотре трассы или в процессе подъема давления будет обнаружена утечка, то
подачу воздуха или газа в трубопроводы следует немедленно прекратить, после
чего должна быть установлена возможность и целесообразность дальнейшего
проведения испытаний или необходимость перепуска воздуха или газа в соседний
участок. Выпуск газа в атмосферу допускается лишь в исключительных случаях.
3.38. Осмотр трассы
при увеличении давления от 0,3
до
и в течение 12 ч (время испытания трубопровода
на прочность) запрещается.
3.39. После
окончания испытаний трубопровода на прочность давление необходимо снизить до
максимального рабочего и только после этого выполнять контрольный осмотр трассы
для проверки герметичности.
Давление необходимо
снижать плавно при этом воздух или газ следует по возможности перепускать в
соседний участок, а не выбрасывать в атмосферу.
3.40. Учитывая, что
при пневматическом испытании трубопроводов большого диаметра основное время
занимают процессы его наполнения воздухом или природным газом до испытательного
давления, необходимо особое внимание обращать на рациональное использование
накопленной в трубопроводе энергии путем многократного использования перепуска
и перекачивания воздуха или газа из испытанных участков в участки, подлежащие
испытанию.
3.41. Время
перепуска газа из одного участка трубопровода в другой и время опорожнения
трубопровода в атмосферу может быть определено по номограмме (рис. 3 Приложения
4 рекомендуемого).
3.42. Конечное
давление перепуска газа или воздуха из одного участка трубопровода в другой
может быть определено по номограмме (рис. 4 Приложения 4 рекомендуемого).
КОМБИНИРОВАННЫЙ
СПОСОБ ИСПЫТАНИЯ
3.43. При
комбинированном способе испытания давление внутри трубопроводов создают двумя
средами - природным газом и водой или воздухом и водой.
3.44. Комплекс
работ по комбинированному способу испытания включает следующие этапы:
подготовку участка
к испытанию и удалению воды;
заполнение
испытываемого участка природным газом или воздухом;
заполнение
испытываемого участка водой до создания в нем давления, необходимого для
испытания на прочность;
испытание на
прочность;
снижение
испытательного давления до максимального рабочего в верхней точке участка;
проверку участка на
герметичность;
удаление из
испытываемого участка воды.
3.45. При
подготовке трубопроводов к испытанию необходимо в соответствии с принятой
схемой провести следующие работы:
отключить
испытываемый участок от смежных участков сферическими заглушками или линейной
арматурой;
смонтировать узлы
подключения к источникам газа, а также узлы пуска и приема разделителя;
установить
контрольно-измерительные приборы;
смонтировать и
предварительно испытать узлы подключения к трубопроводу и обвязку опрессовочных
агрегатов;
опробовать работу
агрегатов и подсоединить их к испытываемому трубопроводу.
3.46. Испытываемый
участок заполняют природным газом путем его отбора из действующего газопровода
до создания в этом участке давления, равного максимальному давлению в
действующем трубопроводе.
3.47. Заполнение
испытываемого участка природным газом или воздухом и подъем давления в нем
должны быть выполнены в последовательности, принятой для пневматического
испытания.
3.48. После
заполнения участка природным газом или воздухом давление в нем до испытательного следует поднимать, закачивая воду
опрессовочными агрегатами.
При испытании
комбинированным способом количество мест и последовательность закачки воды
определяют расчетом (см. Приложение 2 рекомендуемое).
3.49. Испытательное
давление при комбинированном способе должно быть:
в верхней точке
участка - максимальным испытательным давлением, принятым (
) при
пневматическом способе;
в нижней точке
участка - максимальным испытательным давлением принятым (
)при
гидравлическом способе.
3.50.
Продолжительность испытания трубопровода на прочность при комбинированном
способе определяют продолжительностью испытания на прочность при пневматическом
способе.
3.51. Изменение
давления при комбинированном способе испытания трубопровода на прочность и
проверки его на герметичность с учетом снижения испытательного давления только
сливом воды или сбросом газа следует выполнять в соответствии с графиком рис.
16.
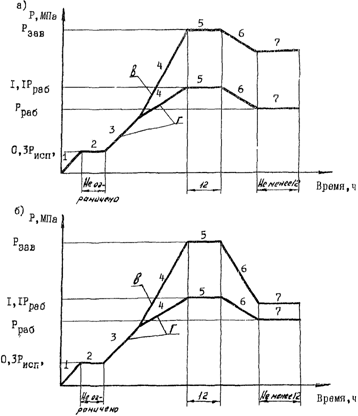
Рис. 16.
График изменения давления в трубопроводе
при комбинированном
способе испытания:
1 - подъем давления
от 0 до 0,3
, но не
выше 2 МПа;
2 - осмотр трассы;
3, 4 - подъем давления до
(г - газ;
в - вода;
в верхней точке трубопровода;
в нижней точке трубопровода);
5 - испытание на
прочность; 6 - снижение давления
до
(а - снижение
осуществляют выпуском только газа;
б - снижение осуществляют выпуском только воды);
7 - проверка на
герметичность
3.52. После
испытания участка трубопровода комбинированным способом из него необходимо
полностью удалить воду в соответствии с разделом 4 настоящей Инструкции,
предварительно слив воду под давлением природного газа или воздуха через
патрубки, заранее установленные в местах закачки воды.
3.53. Пример
расчета схемы испытания участка трубопровода комбинированным способом с
определением количества мест закачки и распределением давления на участке
приведен в Приложении 2 рекомендуемом.
ИСПЫТАНИЕ УЧАСТКОВ
КАТЕГОРИЙ B, I и II
3.54. Участки
категорий B, I и II следует испытывать в один, два или три этапа.
3.55. В один этап
должны быть испытаны:
а) участки
категории B - участки газопроводов внутри зданий и в пределах территорий
компрессорных и газораспределительных станций, станций подземного хранения
газа, а также трубопровода топливного и пускового газа;
б) участки
категории I - участки нефте- и нефтепродуктопроводов внутри зданий и в пределах
территорий перекачивающих насосных станций;
в) участки
категорий I и II - перехода газо-, нефте- и
нефтепродуктопроводов через болота III типа (если требование об испытании в два
этапа специально не оговорено проектом).
3.56. Испытание
участков, указанных в пп. 3.55, а и б необходимо
выполнять при технической возможности с подключенными агрегатами и аппаратами,
которые следует поставлять в монтаж испытанными на заводе-изготовителе, что
должно быть подтверждено соответствующей записью в паспорте агрегата или
аппарата.
3.57. В два этапа
необходимо испытывать:
а) участки
категории I - узлы подключения перекачивающих насосных и компрессорных станций,
всасывающие и нагнетательные трубопроводы, а также узлы пуска и приема очистных
устройств между охранными кранами газопроводов или между задвижками нефте- и
нефтепродуктопроводов;
б) участки
категории I - перехода через железные и автомобильные дороги; пересечения с
воздушными линиями электропередачи напряжением 500 кВ и более;
в) участки
категорий I и II - участки нефте- и нефтепродуктопроводов протяженностью не
менее расстояния между соседними линейными задвижками.
3.58. В три этапа
следует испытывать:
а) участки категорий
B, I, II - переходы нефте- и нефтепродуктопроводов через водные преграды и
прилегающие прибрежные участки;
б) участки
категории I - переходы газопроводов через водные преграды и прилегающие
прибрежные участки.
Требование по
испытанию в три этапа участков категорий B, I, II, указанное в настоящем
пункте, следует соблюдать только в случаях, когда эти участки укладывают с
помощью подводно-технических средств. Во всех остальных случаях указанные
участки испытывают в два этапа.
3.59. Участки
категорий B, I, II, испытываемые в три этапа, разрешается испытывать на первом
и втором этапах не целиком, а отдельными захватками (длинномерными секциями или
плетями). Количество таких захваток (секций, плетей) должно быть по возможности
минимальным, а все сварные соединения между ними следует проверить
неразрушающими методами контроля (кроме
магнитографического).
3.60. Испытание
участков категорий B, I, II в три этапа необходимо выполнять на первом и втором
этапах только гидравлическим способом (водой). Пневматическим способом (сжатым
воздухом, газом) разрешается проводить второй этап испытания только на
газопроводах.
3.61. Третий этап
испытания участков категорий B, I, II должен быть выполнен способом и при
соблюдении параметров, предусмотренных СНиП III-42-80 для прилегающих участков.
4. УДАЛЕНИЕ ВОДЫ ИЗ ТРУБОПРОВОДОВ
4.1. После
гидравлического испытания трубопроводов из них должна быть полностью удалена
вода.
4.2. Удаление воды
проводят одним из следующих способов:
с помощью
поршней-разделителей, перемещаемых по трубопроводам под давлением воздуха или
транспортируемого продукта (газ, нефть и нефтепродукты);
непосредственно
транспортируемым продуктом (нефть и нефтепродукты);
свободным сливом
воды через патрубки, предварительно установленные в нижних точках
трубопроводов.
Слив воды самотеком
разрешается только из коротких участков трубопроводов категории B и I после их
гидравлического испытания, а также после проведения испытания трубопроводов
комбинированным способом. В остальных случаях слив воды самотеком запрещен.
4.3. Для удаления
воды из газопроводов пропускают поршни-разделители под давлением сжатого
воздуха или природного газа в два этапа:
предварительный - удаление основного объема воды;
окончательный (контрольный) - полное удаление воды из газопроводов.
4.4. Для полного
удаления воды из газопроводов поршни-разделители необходимо пропускать с
оптимальной скоростью, величина которой должна оставаться в допустимых пределах
во время перемещения его по всей длине участка (см. пп. 5.3 и 5.4).
Методика
определения оптимальных параметров полного удаления воды из газопроводов после
их гидравлического испытания приведена в Приложении 2 рекомендуемом.
4.5. Результаты
удаления воды из газопроводов следует считать удовлетворительными, если впереди
контрольного поршня-разделителя нет воды, и он вышел неразрушенным. В противном
случае необходимо дополнительно пропускать контрольные поршни-разделители до
тех пор, пока из газопроводов не будет полностью удалена вода.
4.6. Сжатый воздух
для пропуска поршней-разделителей можно подавать от ресивера, образованного на
прилегающем участке магистрали, или непосредственно от передвижных
компрессорных станций; природный газ для этой цели подают из ресивера.
4.7. На
окончательном этапе удаления воды очистные устройства необходимо пропускать на
открытый конец газопровода.
4.8. Полное
удаление воды поршнями-разделителями, перемещаемыми под давлением сжатого
воздуха из участков нефте- и нефтепродуктопроводов, проложенных на водных
переходах, а также по обводненной или заболоченной местности, допускается
только при наличии балластировки участков.
4.9. Воду из нефте-
и нефтепродуктопроводов удаляют с помощью одного поршня-разделителя,
перемещаемого под давлением транспортируемого продукта или непосредственно
самим транспортируемым продуктом.
В исключительных
случаях, если нет транспортируемого продукта к моменту окончания испытания,
удаление воды проводят двумя поршнями-разделителями, перемещаемыми под
давлением сжатого воздуха. В этом случае последующее заполнение нефтью или
нефтепродуктом должно быть проведено таким образом, чтобы исключить попадание
воздуха в полость трубопровода, особенно на участках переходов через водные
преграды.
4.10. Скорость
перемещения поршня-разделителя при пропуске под давлением нефти или
нефтепродуктов устанавливают по фактической производительности средств закачки.
4.11. Для
исключения слива воды самотеком после гидравлического испытания газопроводов, а
также при вытеснении воды из нефте- и нефтепродуктопроводов запорная арматура
на конце испытанного участка должна быть открыта только после полной готовности
этого участка к удалению из него воды и получения извещения о начале движения
поршня-разделителя из камеры пуска.
4.12. После испытания
участка трубопроводов комбинированным способом из него необходимо удалить воду
в следующем порядке:
первый этап -
предварительный слив воды под давлением природного газа или воздуха через
патрубки, заранее установленные в местах закачки воды;
второй этап - с
пропуском разделителей, перемещаемых по трубопроводу под давлением газа или
воздуха.
4.13. С применением
поршней-разделителей удаляют воду как по отдельным участкам, не превышающим
расстояния между соседними линейными кранами, так и по участкам большей
протяженности, в том числе и с установленными на них линейными кранами.
4.14. Удалять воду
из трубопроводов после испытаний следует в основном в направлении от наиболее
высоких точек (по рельефу местности) к пониженным.
4.15. Выпускать
воду из трубопроводов необходимо в сторону от траншеи, в направлении пониженных
участков рельефа местности при максимальном сохранении окружающей среды.
4.16. Узлы пуска и
приема разделителей следует располагать в местах технологических разрывов
трубопровода (места установки линейной арматуры, переходы через естественные
препятствия и т.п.).
Принципиальные
схемы узлов пуска и приема поршней-разделителей, монтируемых на газопроводах,
приведены на рис. 17 и 18.
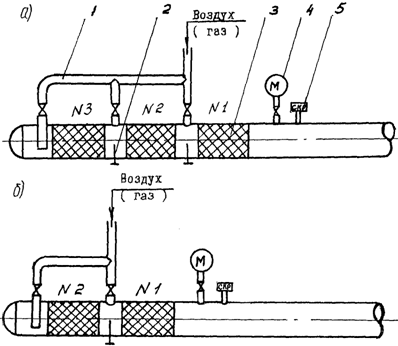
Рис. 17.
Принципиальные схемы узлов пуска
поршней-разделителей,
монтируемых на газопроводах;
а - для трех
поршней-разделителей;
б - для двух поршней-разделителей; 1 - коллектор;
2 - стопор; 3 -
поршни-разделители; 4 - манометр;
5 - сигнализатор
для контроля за движением
поршней-разделителей;
N 1, N 2 и N 3 - последовательность
пропуска
поршней-разделителей
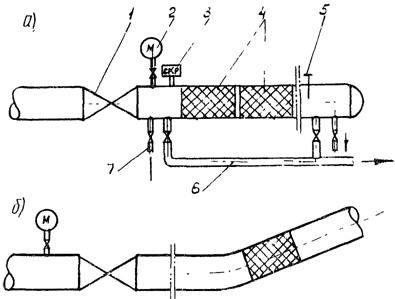
Рис. 18.
Принципиальные схемы узлов приема
поршней-разделителей,
монтируемых на газопроводах:
а - закрытого типа;
б - открытого типа с задвижкой;
1 - линейный кран;
2 - манометр;
3 - сигнализатор
для контроля за движением разделителя;
4 - очистные или
разделительные устройства; 5 - стопор;
6 - сливной
патрубок; 7 - контрольный сливной патрубок
Принципиальные
схемы узлов пуска и приема поршней-разделителей, монтируемых на нефтепроводах и
продуктопроводах, приведены на рис. 19.
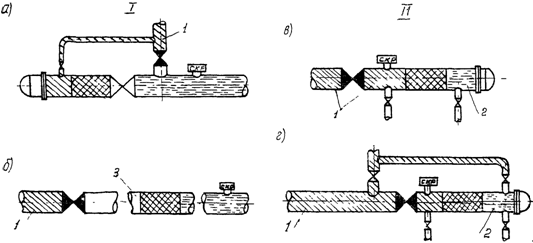
Рис. 19.
Принципиальные схемы узлов пуска
и приема
поршней-разделителей при удалении воды
из нефтепроводов и
продуктопроводов с одновременным
заполнением нефтью
или продуктом:
а - из камеры пуска
поршня-разделителя;
б - между камерами;
в - камера приема; г - на камеру приема
поршня-разделителя;
I - узлы пуска; II - узлы приема;
1 - нефть,
нефтепродукт; 2 - вода; 3 - катушка;
СКР - сигнализатор
для контроля за движением
поршня-разделителя
4.17. Узел (рис.
18, а) рекомендуется применять при промывке и удалении воды на газопроводах
большого диаметра при необходимости отвода воды на значительное расстояние по
временному шлейфу меньшего диаметра. На окончательном этапе удаления воды
следует демонтировать концевую заглушку для выпуска поршней-разделителей на
открытый конец газопроводов.
4.18. Узел (рис.
18, б) целесообразно использовать на газопроводах малого диаметра при промывке
и удалении воды.
4.19. Контроль за перемещением поршней-разделителей следует
осуществлять:
по сообщениям
обходчиков с трассы;
по показаниям
сигнализаторов для контроля за движением
поршня-разделителя или образцовых манометров, измеряющих давление в узлах пуска
и приема поршней-разделителей и в ресивере;
по данным закачки
нефти или нефтепродукта в трубопровод.
4.20. Камеры
приема, а также сливные и продувочные патрубки во избежание их смещения и
вибрации должны быть надежно закреплены.
4.21. Для приема и
пуска очистных устройств, кроме типовых инвентарных узлов, используют:
стационарные камеры
приема и пуска очистных устройств;
линейные или
инвентарные краны в качестве отключающих элементов на временных узлах пуска
очистных устройств.
4.22. Если для
удаления воды используют поршни-разделители ДЗК или ДЗК-РЭМ, то запрещается их
запасовыватъ в камеру пуска до проведения гидравлического испытания, так как
эти поршни-разделители могут насыщаться водой.
4.23. Для слива
воды самотеком из коротких участков трубопроводов категорий B и I в пониженных
точках этих участков необходимо предусмотреть установку временных сливных
патрубков, которые демонтируют после проведения испытаний.
5.
ТЕХНОЛОГИЧЕСКИЕ ВАРИАНТЫ КОМПЛЕКСНОГО ПРОВЕДЕНИЯ
РАБОТ ПО ОЧИСТКЕ
ПОЛОСТИ, ГИДРАВЛИЧЕСКОМУ ИСПЫТАНИЮ
И УДАЛЕНИЮ ВОДЫ ИЗ
ГАЗОПРОВОДОВ
5.1. Наиболее
высокие качественные показатели готовности газопроводов к надежной эксплуатации
достигают путем комплексного проведения работ по очистке полости, испытанию и
полному удалению воды. Указанные процессы очистки полости, испытания и удаления
воды технологически взаимосвязаны между собой и окончательный результат всего
комплекса работ зависит от качества выполнения каждого процесса.
5.2. Комплекс работ
по очистке полости, испытанию и удалению воды из газопроводов проводят по двум
технологическим вариантам, обеспечивающим нормативные требования по качеству
строительства при минимальном количестве пропусков очистных устройств.
5.3. Работы по первому варианту выполняют на участках, собираемых с
внутренним центратором или предварительно очищенных протягиванием в процессе
сборки и сварки труб и секций в нитку. Порядок и параметры проведения
работ по этому варианту приведены в табл. 3.
Таблица 3
────┬──────────────────────────────────────┬──────────┬────────────────────
Этап│ Работы │ Очистные │
Оптимальные границы
│ │устройства│
изменения скорости
│
│
│перемещения очистных
│
│ │ устройств, м/с
│
│
├──────────┬─────────
│
│ │ V
│ V
│
│ │ min
│ max
────┴──────────────────────────────────────┴──────────┴──────────┴─────────
I Промывка с пропуском поршней ДЗК-РЭМ 1 2
ДЗК-РЭМ или ОПР-М, совмещенная ОПР-М
с удалением воздуха и наполнением
газопровода водой
II Гидравлическое испытание - - -
III Предварительное удаление воды ОПР-М 0,5 4
с пропуском поршней ОПР-М или ДЗК-РЭМ ДЗК-РЭМ
0,5 3
IV Окончательное удаление воды ОПР-М 0,5 4
с пропуском поршней ОПР-М ДЗК-РЭМ 0,5 3
или ДЗК-РЭМ (контрольный пропуск)
5.4. Работы
по второму варианту выполняют на участках, проложенных в особо сложных
условиях, где возможно скопление значительных объемов загрязнений,
препятствующих бесперебойному проведению процесса промывки и вызывающих
застревание поршней-разделителей. Порядок и параметры работ по этим вариантам
устанавливают в соответствии с табл. 4.
Таблица 4
────┬─────────────────────────────────────┬──────────┬─────────────────────
Этап│ Работы │ Очистные │
Оптимальные границы
│
│устройства│ изменения скорости
│
│
│перемещения очистных
│
│ │ устройств, м/с
│
│
├──────────┬──────────
│
│ │ V
│ V
│
│ │ min
│ max
────┴─────────────────────────────────────┴──────────┴──────────┴──────────
I Продувка с пропуском поршней ОП ОП 10 20
II Заполнение газопровода водой ОПР-М 0,5 2
с пропуском поршня ОПР-М или ДЗК-РЭМ ДЗК-РЭМ
0,2 2
и гидравлическое испытание
III Предварительное удаление воды ОПР-М 0,5 4
с пропуском поршня ОПР-М или ДЗК-РЭМ ДЗК-РЭМ 0,5 3
IV Окончательное удаление воды ОПР-М 0,5
4
с пропуском поршня ОПР-М или ДЗК-РЭМ ДЗК-РЭМ 0,5 3
(контрольный пропуск)
6. МАШИНЫ,
УСТРОЙСТВА И ПРИБОРЫ ДЛЯ ОЧИСТКИ ПОЛОСТИ
И ИСПЫТАНИЯ
ТРУБОПРОВОДОВ, А ТАКЖЕ ДЛЯ УДАЛЕНИЯ ИЗ НИХ ВОДЫ
МАШИНЫ
6.1. При
очистке полости и испытании трубопроводов необходимо использовать машины,
указанные в табл. 5 и 6 и предназначенные для:
закачки в
трубопроводы воды - наполнительные, опрессовочные и наполнительно-опрессовочные
агрегаты;
закачки в
трубопроводы сжатого воздуха - передвижные компрессорные станции.
Таблица 5
──────────┬──────────┬────────────────────┬──────────┬──────────┬─────┬─────
Марка
│ Марка │ Производительность │Напор при
│Давление │Мощ- │Мас-
агрегата │ насоса
│ агрегата, м3/ч │наполне- │при опрес-│ность│са,
│
├─────────┬──────────┤нии, │совании, │дви-
│кг
│ │при на- │при опрес-│м вод.
ст.│МПа │гате-│
│ │полнении │совании │ │(кгс/см2)
│ля, │
│ │ │ │ │ │л.с. │
──────────┴──────────┴─────────┴──────────┴──────────┴──────────┴─────┴─────
Наполнительные
агрегаты
АН-2 8МС-7 x 3 200 - 400
- 200 - 150 - 300
8200
АН-261 8МС-7 x 3 260
- 155 -
300 9400
АН-501 ЭВ-200 x 4 540
- 240 -
500 9400
АН-1001 12НДС 1000 - 60 -
300 8200
Опрессовочные агрегаты
АО-2 9Т - 25 - 56 -
8 - 3,5 108 9250
(80 - 36)
АО-161 ОМТр-61 -
20 - 40 - 16 (160) 130
9500
Азинмаш-32
1НП-160 - 12 - 51 -
16 - 4 100 15100
(160 - 40)
ЦА-320М 9Т - 18,4 - -
18,2 - 4 180 17200
82,2
(182 - 40)
Наполнительно-опрессовочные
агрегаты
АНО-202 К-45/55 45 - 55 - -
-
ГБ-351А -
1,8 - 20 (200) 30
2360
Таблица 6
────────┬────────┬───────┬──────────┬───────┬──────┬────────────────────┬──────
Марка │Произво-│Давле-
│ База │Привод │Мощ- │ Габаритные размеры,│Масса,
компрес-│дитель- │ние │ │от │ность │ мм │ кг
сорной
│ность │нагне-
│ │двига-
│двига-│
│
│КС, │тания, │ │теля │теля,
│ │
│м3/мин │кгс/см2│ │ │л.с. │ │
────────┴────────┴───────┴──────────┴───────┴──────┴────────────────────┴──────
Компрессорные станции низкого
давления
АМС-4 57,5 -
10 - 20 Тележка на
700 13820 x 3250 x 3450 52000
70,3 пневмо-
колесном
ходу
ЗИФ-55 5,0
7 То
же ЗИЛ-121 98
3450 x 1820 x 1770 2750
КС-9 8,5
6 " КДМ-100
100 5080 x 1890 x 2100 5750
ДК-9 10,0
6 " КДМ-100
100 5035 x 1850 x 2550 5650
ПК-10 10,5
7 " Д-108
108 4700 x 1890 x 2610 5100
Компрессорные станции высокого
давления
АМС-2 57,5 -
10 - Тележка на 770
11320 x 3250 x 3450 38700
70,3 100 пневмо-
колесном
ходу
КС-100 16,0
100 То
же 1Д12Б 410
11000 x 3140 x 3400 23000
АКС-8 2,0
230 " ЯАЗ-204
110 3530 x 1910 x 2220 3950
УКП-80 8,0
80 Тележка В2-300
300 6570 x 2590 x 2870 16100
"Восток"
на гусе-
ничном
ходу
Примечание.
Компрессоры ЗИФ-55, КС-9, ДК-9, КП-10, АКС-8, УКП-80 применяют для вытеснения
воды на газопроводах диаметром до 500 мм (в связи с их небольшой
производительностью).
6.2. Для закачки в
трубопроводы воды и воздуха разрешается использовать машины, применяющиеся в
других отраслях народного хозяйства и обеспечивающие параметры
и режимы проведения процессов очистки полости и испытания в пределах,
регламентированных СНиП III-42-80.
УСТРОЙСТВА ДЛЯ
ОЧИСТКИ ПОЛОСТИ ТРУБОПРОВОДОВ
И УДАЛЕНИЯ ИЗ НИХ
ВОДЫ
6.3. Для очистки
полости трубопроводов, удаления из них воздуха и воды следует применять
специальные очистные устройства.
6.4. Для
эффективного проведения конкретного процесса (промывки, продувки, удаления
воды) очистное устройство должно быть выбрано в соответствии с его назначением.
Использование очистных
и разделительных устройств не по назначению и с нарушением нормативных
параметров может привести к аварийным ситуациям при сооружении и эксплуатации
трубопроводов.
6.5. Очистные
поршни ОП (рис. 20) применяют:
для продувки
магистральных трубопроводов под давлением воздуха или природного газа на
участках протяженностью не более 40 км и не более расстояния между линейными
кранами;
для очистки полости
протягиванием в процессе сборки и сварки секций в нитку с применением наружного
центратора.
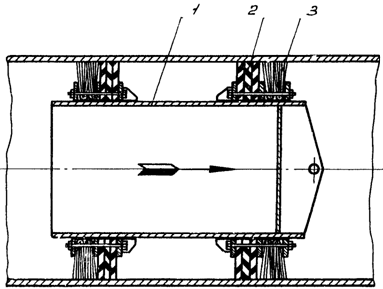
Рис. 20. Очистной
поршень типа ОП:
1 - корпус
металлический; 2 - манжета эластичная; 3 - щетка
Запрещается
продувка трубопроводов, проложенных надземным способом на опорах, а также
продувка через линейную арматуру.
6.6. Размеры и
масса очистных поршней ОП приведены в табл. 7.
Таблица 7
─────────────────────────┬───────────────────────┬───────────┬─────────────
Условный диаметр D , мм │Наружный
диаметр D, мм │ Длина, мм │
Масса, кг
у │ │ │
─────────────────────────┴───────────────────────┴───────────┴─────────────
250 254 575 47
300 306 660 63
350 358 720 90
400 407 740 120
500 518 825 165
600 615 1090 210
700 705 1090 257
800 808 1190 450
1000 1010 1150 600
1200 1200 1300 810
1400 1400 1500 1020
6.7.
Поршни-разделители ДЗК (рис. 21) применяют:
для освобождения
трубопроводов диаметром 100 - 700 мм от воды после гидравлического испытания
или балластировки, скорость перемещения разделителей в этом процессе должна
быть в пределах 3 - 10 км/ч;
для промывки
трубопроводов диаметром 100 - 700 мм и одновременного освобождения их от
воздуха в процессе наполнения водой для гидравлического испытания, скорость
перемещения разделителей в этом процессе должна быть 1 - 1,5 км/ч;
для продувки
трубопроводов диаметром 100 - 700 мм, прокладываемых надземным способом на
опорах, по участкам протяженностью не более 10 км и при скорости перемещения
разделителей не более 10 км/ч.
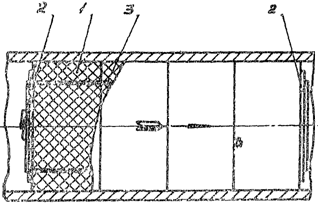
Рис. 21.
Поршень-разделитель эластичный типа ДЗК:
1 - блок
поролоновый; 2 - диск защитный; 3 - трос
Размеры и масса
поршней-разделителей ДЗК приведены в табл. 8.
Таблица 8
────────────────────┬─────────┬────────────────────────────────────────────
Поршень-разделитель
│ Диаметр │ Масса сухого разделителя при длине 2D , кг
│ D, мм
│ у
────────────────────┴─────────┴────────────────────────────────────────────
ДЗК-100 120 0,09
ДЗК-150 180 0,3
ДЗК-200 240 0,6
ДЗК-250 300 1,4
ДЗК-300 330 2,0
ДЗК-350 385 3,2
ДЗК-400 430 4,6
ДЗК-500 530 8,7
ДЗК-600 630 14,8
ДЗК-700 730 23,2
6.8.
Поршни-разделители ДЗК запрещается:
пропускать по
участкам протяженностью более 30 км;
использовать для
продувки трубопроводов, проложенных подземно и наземно;
пропускать со
скоростью более 10 км/ч.
6.9.
Поршни-разделители ДЗК-РЭМ (рис. 22) применяют:
для освобождения
трубопроводов диаметром 520 - 1420 мм от воды после гидравлического испытания
или балластировки; скорость пропуска поршней в этом процессе должна быть в пределах
3 - 10 км/ч;
для промывки
трубопроводов диаметром 520 - 1420 мм и одновременного освобождения их от
воздуха в процессе наполнения водой для гидравлического испытания; скорость
перемещения поршней-разделителей в этом процессе должна быть не менее 1 км/ч;
для продувки
трубопроводов, прокладываемых надземным способом на опорах по участкам
протяженностью не более 10 км и при скорости поршней-разделителей не более 10
км/ч.

Рис. 22.
Поршень-разделитель эластичный манжетный
типа ДЗК-РЭМ:
1 - диск защитный;
2 - манжета эластичная;
3 - блок
поролоновый; 4 - трос; 5 - зажим
6.10. Размеры и
масса поршней-разделителей ДЗК-РЭМ приведены в табл. 9.
Таблица 9
─────────────────────┬───────────────┬──────────────┬─────────────
Поршень-разделитель │ Диаметр D, мм
│ Длина, мм │
Масса, кг
─────────────────────┴───────────────┴──────────────┴─────────────
ДЗК-РЭМ-500 570 800 15
ДЗК-РЭМ-600 650 900 25
ДЗК-РЭМ-700 770 1100 50
ДЗК-РЭМ-800 840 1200 70
ДЗК-РЭМ-1000 1050 1500 90
ДЗК-РЭМ-1200 1260 1800 150
ДЗК-РЭМ-1400 1450 2100 300
6.11.
Поршни-разделители ДЗК-РЭМ запрещается:
применять для
продувки трубопроводов, прокладываемых подземным или наземным способом;
пропускать по
участкам трубопроводов протяженностью более 100 км;
пропускать при
скоростях более 10 км/ч.
6.12.
Поршни-разделители ОПР-М (рис. 23) следует применять на трубопроводах диаметром
325 - 1420 мм:
для промывки и
одновременного освобождения от воздуха и заполнения водой при гидравлических
испытаниях; скорость перемещения поршней в этом процессе должна быть 1 - 1,5
км/ч;
для освобождения
трубопроводов от воды после гидравлического испытания или балластировки;
скорость перемещения поршней в этом процессе должна находиться в пределах 3 -
10 км/ч.

Рис. 23.
Очистной поршень-разделитель типа ОПР-М:
1 - корпус
металлический; 2 - герметизирующий элемент;
3 - втулка
распорная; 4 - кольцо упорное неподвижное;
5 - фланец; 6 -
болтовое соединение; 7 - амортизатор
Размеры и масса
поршней-разделителей ОПР-М приведены в табл. 10.
Таблица 10
────────────────────┬──────────────┬──────────────┬───────────────
Поршень-разделитель
│Диаметр D, мм │ Длина,
мм │ Масса, кг
────────────────────┴──────────────┴──────────────┴───────────────
ОПР-М-300 325 500 25
ОПР-М-500 570 785 60
ОПР-М-700 770 1130 106
ОПР-М-800 840 1254 179
ОПР-М-1000 1050 1470 281
ОПР-М-1200 1260 1610 410
ОПР-М-1400 1450 1990 639
6.13.
Поршни-разделители ОПР-М-Э (рис. 24) применяют:
для промывки
трубопроводов, скорость перемещения поршней-разделителей 1 - 1,5 км/ч;
для освобождения
трубопроводов от воды после гидравлического испытания или балластировки,
скорость перемещения поршней в этом процессе должна быть в пределах 3 - 10
км/ч.
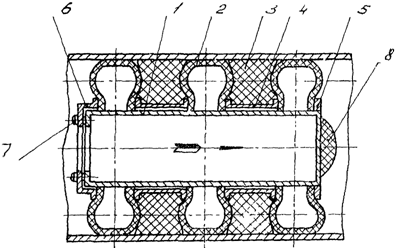
Рис. 24.
Очистной поршень-разделитель типа ОПР-МЭ:
1 - корпус
металлический; 2 - герметизирующий элемент;
3 - блок
поролоновый; 4 - втулка распорная;
5 - кольцо упорное
неподвижное; 6 - фланец;
7 - болтовое
соединение; 8 - амортизатор
6.14. Размеры и
масса поршней-разделителей ОПР-М-Э приведены в табл. 11.
Таблица 11
────────────────────┬──────────────┬──────────────┬───────────────
Поршень-разделитель
│Диаметр D, мм │ Длина,
мм │ Масса, кг
────────────────────┴──────────────┴──────────────┴───────────────
ОПР-М-Э-1000 1050 1470 299
ОПР-М-Э-1200 1260 1610 430
ОПР-М-Э-1400 1450 1990 671
6.15.
Поршни-разделители ОПР-М и ОПР-М-Э запрещается применять:
для продувки
трубопроводов;
пропускать на
участках протяженностью свыше 150 км.
6.16.
Поршни-разделители манжетные переменного сечения РМ-ПС (рис. 25) следует
применять на трубопроводах, имеющих местные сужения сечения (в частности,
неравнопроходная арматура, подводные переходы):
для промывки
трубопроводов при скорости перемещения не менее 1 км/ч;
для удаления воды,
скорость перемещения поршней в процессе должна быть в пределах 3 - 10 км/ч.
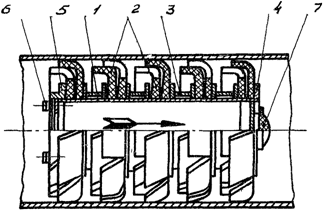
Рис. 25.
Разделитель манжетный переменного сечения
типа РМ-ПС:
1 - корпус
металлический; 2 - манжета с вырезами;
3 - втулка
распорная; 4 - кольцо упорное неподвижное;
5 - фланец; 6 -
болтовое соединение; 7 - амортизатор
6.17. Размеры и
масса поршней-разделителей РМ-ПС приведены в табл. 12.
Таблица 12
────────────────────┬────────────────────────────────────┬────────┬────────
Поршень-разделитель
│ Диаметр поршня-разделителя, D, мм
│ Длина, │ Масса,
├────────────┬───────────────────────┤ мм │
кг
│до
запасовки│ после запасовки │ │
│ в
│ в
трубопровод │ │
│трубопровод
├───────────┬───────────┤ │
│ │в основном │в суженном │
│
│ │ сечении
│ сечении │
│
────────────────────┴────────────┴───────────┴───────────┴────────┴────────
РМ-ПС-700/500 770 700
500 1119
165
РМ-ПС-800/700 865 800 700 1157
220
РМ-ПС-1000/800 1065 1000 800 1240
355
РМ-ПС-1200/1000 1260 1200 1000 1560
522
РМ-ПС-1400/1200 1450 1400 1200 1722
763
6.18.
Поршни-разделители РМ-ПС запрещается применять для продувки и на участках
трубопровода протяженностью более 150 км.
6.19. Перед
запасовкой очистных устройств в трубопроводы следует
проверить и затянуть все имеющиеся в них крепления.
6.20. Очистные
поршни, оборудованные кардной лентой ОПКЛ, применяют для очистки трубопроводов
диаметром 150 - 720 мм. Скорость перемещения очистных поршней ОПКЛ должна быть:
при промывке
трубопроводов 1 - 1,5 км/ч;
при продувке
трубопроводов, уложенных подземно или наземно, - в пределах 35 - 70 км/ч.
6.21. Для удаления
воды из нефтепроводов диаметром 1020 - 1220 мм можно применять разработанные
Урало-Сибирским нефтепроводным управлением манжетные поршни-разделители,
пропускаемые по магистрали под давлением нефтепродукта. Параметры пропуска этих
поршней устанавливает эксплуатирующая органиаация, проводящая заполнение
магистрали нефтью в предпусковой период.
ПРИБОРЫ
6.23. На всех
этапах выполнения комплекса работ по испытанию газопроводов гидравлическим
способом следует применять проверенные, опробованные и имеющие паспорт
манометры класса точности не ниже 1,5 с предельной шкалой на давление около 4/3
от испытательного. Для этих целей применяют
дистанционные регистрирующие приборы.
6.24. Для
обнаружения в трубопроводах застрявших очистных или разделительных устройств
используют прибор типа "Волна", а для обнаружения утечек газа -
установки "Искатель" (разработки ВНПО "Союзгазавтоматика"
Мингазпрома).
7. ТЕХНИКА
БЕЗОПАСНОСТИ
При очистке
полости, испытании трубопроводов, удалении из них воды, а также при
эксплуатации машин и оборудования следует руководствоваться следующими
документами по технике безопасности:
СНиП III-4-80.
"Техника безопасности в строительстве" (М., Госстрой СССР, 1980);
Правилами техники
безопасности при строительстве магистральных стальных трубопроводов (М., Недра,
1982).
Приложение
1
Обязательное
АКТЫ О
ПРОИЗВОДСТВЕ И РЕЗУЛЬТАТАХ ОЧИСТКИ ПОЛОСТИ,
А ТАКЖЕ ИСПЫТАНИЙ
ТРУБОПРОВОДОВ НА ПРОЧНОСТЬ
И ПРОВЕРКИ ИХ НА
ГЕРМЕТИЧНОСТЬ
Форма N 1
АКТ N
ОЧИСТКИ ПОЛОСТИ МАГИСТРАЛЬНОГО ТРУБОПРОВОДА
"
" __________________ 19__ г.
Населенный пункт _____________________________
Наименование трубопровода
_________________________________________________
Мы, нижеподписавшиеся, председатель и члены комиссии
по очистке полости,
назначенной приказом
______________________________________________________
(наименование организации)
от ________________ N ____ в составе
______________________________________
___________________________________________________________________________
(должность, фамилия, имя,
отчество)
составили настоящий акт о том, что
строительно-монтажной организацией _____
___________________________________________________________________________
при участии
_______________________________________________________________
выполнено
_________________________________________________________________
(способ очистки полости - продувка с пропуском
___________________________________________________________
очистка полости
или без пропуска очистного поршня, промывка)
участка от ПК ______ км до ПК ______ км.
Очистка
полости выполнена в соответствии с действующим СНиПом.
Во время
очистки полости отказов не было.
Участок трубопровода, указанный
в настоящем акте, следует
считать
прошедшим очистку полости.
Председатель комиссии ______________
(подпись)
Члены комиссии ______________
______________
______________
Форма N 2
АКТ N
ИСПЫТАНИЯ МАГИСТРАЛЬНОГО ТРУБОПРОВОДА НА ПРОЧНОСТЬ
И ПРОВЕРКИ НА ГЕРМЕТИЧНОСТЬ
"
" __________________ 19__ г.
Населенный пункт _____________________________
Наименование трубопровода
_________________________________________________
Мы,
нижеподписавшиеся,
председатель и члены
комиссии по испытанию,
назначенной приказом
______________________________________________________
(наименование
организации)
от _________________ N ____ в составе
_____________________________________
(должность,
фамилия, имя, отчество)
___________________________________________________________________________
___________________________________________________________________________
составили настоящий акт о том, что в период с _____________________________
по ___________________________ 19____ г.
строительно-монтажной организацией
___________________________________________________________________________
при участии
_______________________________________________________________
выполнено _________________________________________________________________
(способ испытания - гидравлический, пневматический,
___________________________________________________________________________
газом или воздухом, комбинированный)
испытание на прочность и проверка на герметичность
участка от ПК _______ км
до ПК _______ км.
Рабочее
давление на участке трубопровода составляет по проекту ____ МПа
(кгс/см2), а давление в
нижней точке испытываемого участка на ПК _______ км
___________ составляет по проекту ____________ МПа
(кгс/см2).
Испытание на прочность
и проверка на герметичность проведены в
соответствии с действующим
СНиПом:
на
прочность давлением в нижней точке _____________ МПа (кгс/см2),
а в
верхней точке (ПК ____________ км ____________)
____________ МПа (кгс/см2);
на
герметичность давлением _________ МПа (кгс/см2) в
точке (ПК ________
км ___________).
Для замера
давлений при испытании на прочность
и его проверке на
герметичность использованы технические манометры
класса точности __________
с диаметром шкалы ____ мм,
установленные на ПК ____ км ____________________
N 1, 2 и т.д.
Во время испытания трубопровода на прочность отказов (разрывы, утечки,
и т.д.)
___________________________________________________________________
(не произошло,
произошло)
Участок
трубопровода, указанный в настоящем акте, _____________________
(после
___________________________________________________________________________
устранения отказов)
считать выдержавшим испытание на прочность и
проверку на герметичность.
Председатель комиссии ______________ / /
(подпись)
Члены комиссии ______________ / /
______________ / /
______________
/ /
Форма N 3
АКТ N
УДАЛЕНИЯ ВОДЫ ПОСЛЕ ГИДРАВЛИЧЕСКОГО ИСПЫТАНИЯ
МАГИСТРАЛЬНОГО
ТРУБОПРОВОДА
"
" __________________ 19__ г.
Населенный пункт _____________________________
Наименование трубопровода
_________________________________________________
Мы, нижеподписавшиеся, председатель и члены комиссии
по удалению воды после
гидравлического испытания, назначенной
приказом ___________________________
(наименование организации)
от ________________ N ____ в составе
______________________________________
(должность, фамилия, имя, отчество)
___________________________________________________________________________
___________________________________________________________________________
составили настоящий акт о том, что в период с
________ по _________ 19__ г.
строительно-монтажной организацией
________________________________________
___________________________________________________________________________
при участии
_______________________________________________________________
выполнено удаление воды после гидравлического
испытания ___________________
___________________________________________________________________________
(число этапов процесса; количество и тип поршней-разделителей,
___________________________________________________________________________
при помощи которых шел процесс удаления воды)
на участке от ______ ПК ______ км до ______ ПК
______ км.
Удаление воды из трубопроводы после
гидравлического испытания
произведено в соответствии с действующим
СНиПом.
Результаты проведения процесса
удаления воды считаются
удовлетворительными.
Участок трубопровода, указанный
в настоящем акте, следует
считать
полностью освобожденным от
воды.
Председатель комиссии ______________
(подпись)
Члены комиссии ______________
______________
______________
Форма N 4
АКТ N
ПРЕДВАРИТЕЛЬНОЙ ОЧИСТКИ ПОЛОСТИ ТРУБОПРОВОДА
МЕТОДОМ ПРОТЯГИВАНИЯ
"
" __________________ 19__ г.
Населенный пункт _____________________________
Наименование трубопровода _________________________________________________
Мы, нижеподписавшиеся, представитель
строительно-монтажной организации ____
__________________ и представитель заказчика
составили настоящий акт в том,
что строительно-монтажной организацией
____________________________________
выполнена предварительная очистка полости методом
протягивания ____________
______________________________ в процессе сборки и
сварки _________________
(тип
очистного устройства) (секций или труб)
в нитку трубопровода от ______ ПК ______ км до
______ ПК ______ км.
Предварительная очистка полости проведена в соответствии с действующим
СНиПом.
Результаты
проведения очистки полости считаются удовлетворительными.
Участок, указанный в
настоящем акте, следует считать
прошедшим
предварительную очистку полости.
Представитель строительно-
монтажной организации ______________
(подпись)
Представитель заказчика ______________
Приложение
2
Рекомендуемое
МЕТОДИКИ
ОПРЕДЕЛЕНИЯ ТЕХНОЛОГИЧЕСКИХ ПАРАМЕТРОВ
МЕТОДИКА ОПРЕДЕЛЕНИЯ ПАРАМЕТРОВ ПРОДУВКИ
СТРОЯЩИХСЯ
МАГИСТРАЛЬНЫХ ТРУБОПРОВОДОВ
1. Для достижения
нормативных требований по качеству очистки полости при минимальных
энергетических затратах необходимо устанавливать оптимальные параметры
продувки.
2. Для продувки
подземных и наземных трубопроводов с пропуском очистных поршней при соотношении
длин ресивера и продуваемого участка 1:1 и диаметра байпасной линии, равном 0,3
- 0,35 диаметра участка, давление воздуха или газа в ресивере определяют по
осредненным данным, приведенным в табл. 1.
Таблица 1
──────────────────┬────────────────────────────────────────────────────────
Условный диаметр │ Давление в ресивере, МПа (кгс/см2)
трубопровода, мм
├──────────────────────────┬─────────────────────────────
│ для трубопроводов, │
для трубопроводов,
│ очищенных
протягиванием │ не очищенных
протягиванием
│ очистных устройств │
очистных устройств
──────────────────┴──────────────────────────┴─────────────────────────────
До
400 0,6 (6) 1,2 (12)
От
500 до 800 0,5 (5) 1,0 (10)
От
1000 до 1400 0,4 (4) 0,8 (8)
Примечания. 1. Для
участков, проходящих по резко пересеченной, по
обводненной или болотистой местностям, указанные давления следует увеличить в
1,2 - 1,4 раза.
2. В таблице
приведены величины избыточного давления.
3. При других
исходных данных, а также для уточнения параметров продувки с учетом конкретных
условий производства строительных работ предварительно рассчитывают оптимальные
параметры по приведенной ниже методике.
Физическая сущность
и исходные параметры
процесса продувки
4. Очистной поршень
при передвижении по трубопроводу под давлением воздуха или газа разрушает
загрязнения, отделяя их от стенки трубы. В зависимости от скорости передвижения
потока газа перед поршнем по трубопроводу продувку можно проводить в следующих
режимах:
с механическим перемещением
загрязнений непосредственно перед поршнем (режим I);
с перемещением
загрязнений в скоростном потоке газа перед поршнем (режим II);
со скоростным
перетоком газа через перепускное устройство движущегося поршня (режим III).
5. Режим I -
продувка с механическим перемещением загрязнений перед очистным поршнем
эффективна при очистке полости трубопроводов диаметром 700 - 1400 мм,
прокладываемых в нормальных условиях, а также при необходимости повторной
очистки трубопроводов при повышенных требованиях к чистоте полости объекта.
Использовать этот
режим для продувки участков трубопроводов большой протяженности диаметром 200 -
500 мм нецелесообразно, так как образование грунтовой пробки может привести к
застреванию очистного поршня.
6. Режим II
- при передвижении очистного поршня со скоростью, при которой частицы
загрязнений, отделенные от стенки трубы, переходят во взвешенное состояние,
загрязнения перемещаются и выносятся из трубопроводов в потоке газа.
Пропуск очистных
поршней в таком режиме значительно снижает сопротивление перемещению
загрязнений, однако в этом режиме требуется погашенный расход газа для
поддержания оптимальных скоростей потока в продуваемом трубопроводе.
Режим II эффективно
применять при продувке трубопроводов диаметром 700 - 1400 мм, в том числе
прокладываемых в сложных условиях.
Продувку с
перемещением загрязнений в скоростном потоке газа перед очистным поршнем
необходимо проводить при следующих скоростях передвижения очистного поршня по
трубопроводу:
при очистке от
сухих загрязнений - не менее 12 м/с;
при очистке от
мокрых и смешанных загрязнений - не менее 15 м/с.
7. Режим III - при
продувке с перетоком газа через перепускное устройство движущегося очистного
поршня загрязнения, отделенные от стенки трубы, отбрасываются скоростным
потоком газа, что препятствует их скоплению перед поршнем.
В режиме III
продувку проводят при скоростях перемещения очистного поршня, которые
значительно меньше скоростей выноса для данного типа загрязнений.
Использование этого
режима эффективно при продувке сильнозагрязненных участков трубопроводов
большой протяженности, особенно диаметром 200 - 700 мм.
8. При
продувке подземных, полуподземных и наземных трубопроводов скорость перемещения
очистных поршней не должна превышать 20 м/с.
Превышение
максимальной скорости перемещения очистных поршней снижает качество очистки
полости, а также может привести к застреванию поршней или аварии трубопроводов
при последующей эксплуатации.
Расчетные
зависимости для определения параметров продувки
9. Расчетная схема
продувки приведена на рис. 1.
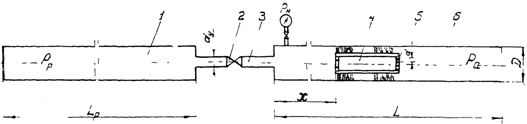
Рис. 1. Расчетная
схема процесса продувки:
1 - ресивер; 2 -
запорный кран; 3 - перепускная линия;
4 - очистной
поршень; 5 - перепускной патрубок
очистного поршня; 6
- продуваемый участок;
L - длина
продуваемого участка;
- длина ресивера;
x - текущая
координата по длине продуваемого участка;
- начальное давление газа в ресивере;
- атмосферное давление; D - диаметр
трубопровода;
- диаметр байпасной линии и условный диаметр
запорной арматуры;
d - диаметр перепускных патрубков
В формулах (1) -
(11) приняты следующие обозначения и единицы измерения входящих параметров:
L - длина
продуваемого участка, м;
- длина ресивера, м;
D - диаметр
трубопровода, м;
S - площадь
поперечного сечения трубопровода, м2;
- площадь поперечного сечения крана, м2;
F - суммарная
площадь перепускных патрубков поршня, м2;
d - диаметр
перепускных патрубков, м;
k - количество
патрубков;
- диаметр байпасной линии и условный диаметр
запорной арматуры, м;
- давление в начале продуваемого участка, МПа;
- начальное давление газа в ресивере, МПа;
- атмосферное давление, равное 0,1 МПа;
v - скорость
поршня, м/с;
- сопротивление механического перемещения
загрязнений непосредственно перед поршнем, МПа;
- сопротивление перемещению очистного поршня
по трубопроводу, МПа;
= 0,05 - 0,1 МПа;
- сопротивление перемещению загрязнений в
скоростном потоке газа перед поршнем, МПа;
R - газовая
постоянная:
для воздуха R = 287
м2/с2 x град;
для газа R = 519 м2/с2 x град;
T - абсолютная
температура газа, К;
- коэффициент гидравлического сопротивления
трубопровода,
= 0,02 - 0,03;
- плотность грунта, кг/м3;
- коэффициент бокового давления грунта;
f - коэффициент
трения при перемещении загрязнений по внутренней поверхности трубопровода;
- объем загрязнений в расчете на 1 м
продуваемого трубопровода, м3/м;
- масса загрязнений в расчете на 1 м
продуваемого трубопровода, кг/м;
C - удельное сцепление
грунта, МПа;
- коэффициент расхода крана байпасной линии;
- коэффициент, характеризующий сужение потока
в запорной арматуре;
- коэффициент расхода перепускного устройства
очистного поршня;
n - коэффициент
запаса, равный 1,5 - 2,0.
При расчете
параметров продувки используют абсолютное давление воздуха или газа.
10. При
продувке в режиме механического перемещения загрязнений непосредственно перед
поршнем (режим I) используют следующие расчетные зависимости.
Предельную длину
продуваемого участка
определяют из соотношения
, (1)
где
,
= 2,5 - 3 - при очистке от глинистых грунтов;
= 4,0 - 5,0 - при очистке от других загрязнений.
Значения
определяют по табл. 2.
Таблица 2
────────────────────┬──────────────────────────────────────────────────────
Диаметр
трубопровода│ Масса загрязнений в
расчете на 1 м продуваемого
(D), мм │ -
│ участка (P), кг/м
├─────────────────────────┬────────────────────────────
│ для трубопроводов, │
для трубопроводов,
│ очищенных
протягиванием │ не очищенных протягиванием
│ очистных устройств │
очистных устройств
────────────────────┴─────────────────────────┴────────────────────────────
0,2 - 0,7 0,02 - 0,03 0,2 - 0,3
0,8 - 1,0 0,04 - 0,05 0,3 - 0,4
1,2 - 1,4 0,06 - 0,1 0,4 - 0,6
Примечание. При
расчете параметров продувки трубопроводов, прокладываемых в сложных условиях,
приведенные в табл. 2 значения
увеличивают в 1,5 - 2 раза.
Распределение
сопротивлений по длине участка трубопровода при его очистке определяют по
формуле
. (2)
При расчетах
используют следующие осредненные параметры грунтовых загрязнений, которые даны
в табл. 3.
Таблица 3
─────────────────┬──────────────┬───────────────┬─────────────┬────────────
Грунтовые
│ Плотность │
Коэффициент │ Коэффициент │ Удельное,
загрязнения
│грунта гамма, │ трения грунта │ бокового
│ сцепление
│ кг/м3
│ по внутренней │давления эта
│ грунта C ,
│ │
поверхности │ │ 1
│ │трубопровода f
│ │ МПа
─────────────────┴──────────────┴───────────────┴─────────────┴────────────
Песчаные
и 1800 0,50 0,43 0,002
супесчаные
Сухие
глинистые 1600 0,40 0,50 0,003
Влажные
глинистые 1800 0,40 0,85 0,008
Начальное давление
в ресивере определяют для конца продуваемого участка по формуле
. (3)
Максимальную
площадь проходного сечения крана байпасной линии вычисляют по формуле
, (4)
где
;
;
v = 5 - 7 м/с;
;
- для воздуха;
- для газа.
Значения
и
в формулах (3) и (4) вычисляют при
x = L.
Диаметр перепускной
(байпасной) линии и условный диаметр арматуры находят по формуле
. (5)
11. При
продувке в режиме перемещения загрязнений и скоростном потоке газа перед
очистным поршнем (режим II) используют приводимые ниже расчетные зависимости.
Предельную длину
продуваемого участка
определяют по формуле
, (6)
где
- максимальная величина рабочего давления
имеющегося компрессорного оборудования или давление газа в магистрали.
Начальное давление
в ресивере находят для двух точек трубопровода - начала и конца продуваемого
участка:
а) для начала
участка:
; (7)
б) для конца
участка:
. (8)
Из двух полученных
значений
и
выбирают максимальное и принимают его за
исходную величину начального давления
при продувке в данном режиме.
Максимальную
площадь проходного сечения крана байпасной линии
вычисляют для точки, где
.
При
в начале продуваемого участка
определяют по формуле
, (9)
где
.
При
в конце участка продувки
определяют как
. (10)
Диаметр перепускной
(байпасной) линии и условный диаметр арматуры находят по формуле (5).
В приведенных
формулах
.
При расчетах
параметров продувки трубопроводов, очищенных протягиванием очистных устройств,
принимают
. Для
трубопроводов, не очищенных протягиванием очистных устройств, осредненные
значения
определяют в соответствии с табл. 4.
Таблица 4
────────────────────────────┬─────────────────────────────────────
Диаметр трубопровода D, м │
Сопротивление загрязнений
│ в потоке газа сигма, МПа
────────────────────────────┴─────────────────────────────────────
0,2 - 0,4 0,18 - 0,10
0,5 - 0,8 0,08 - 0,05
1,0 - 1,4 0,04 - 0,03
Оптимальную
величину скорости перемещения поршня v принимают в зависимости от вида
удаляемых загрязнений с учетом конструктивной характеристики трубопровода в
соответствии с пп. 6 и 8 данного приложения.
12. При
продувке со скоростным перетоком газа через пропускное устройство движущегося
очистного поршня (режим III) используют следующие расчетные зависимости.
Предельную длину
продуваемого участка
определяют по формуле (6).
Начальное давление
в ресивере
находят для двух точек трубопровода - начала и
конца продуваемого участка:
а) для начала
участка давление - вычисляют по формуле (7);
б) для конца
участка - по формуле
, (11)
где
;
;
.
Из двух полученных
значений
и
выбирают максимальное и принимают его за
исходную величину начального давления
при продувке в данном режиме.
Максимальную
площадь проходного сечения крана байпасной линии
определяют для точки, где
по формулам (9) и (10).
Диаметр байпасной
линии и условный диаметр арматуры определяют по формуле (5).
При расчетах
оптимальную величину скорости перемещения поршня принимают в пределах v = 10 -
15 м/с.
Величину сопротивления
перемещению загрязнений в потоке газа перед поршнем
принимают по табл. 4.
Последовательность
расчета параметров продувки
13. Расчет
параметров продувки с пропуском очистных поршней необходимо проводить в
приведенной последовательности:
наметить возможные
участки продувки с учетом расположения по трассе технологических разрывов
трубопровода (в частности, места установки линейной арматуры, переходы через
естественные препятствия);
найти предельную длину
очищаемого участка при различных режимах продувки с учетом характеристики
используемого компрессорного оборудования или давления газа в магистрали;
определить
оптимальный режим продувки и соответствующее этому режиму начальное давление в
ресивере;
определить диаметр
перепускной (байпасной) линии и условный диаметр запорной арматуры.
14. При
наличии данных о виде и объеме загрязнений, находящихся в подготовленном к
очистке участке трубопровода, продувку этого участка проводят в одном из трех
режимах (I, II или III).
Для этих режимов в
соответствии с пп. 10, 11 и 12 данного приложения определяют предельную длину
продуваемого участка
,
,
.
Оптимальный вариант
продувки и начальное давление в ресивере выбирают в зависимости от соотношения
полученных величин.
При
,
и
в соответствии с пп. 10, 11 и 12 настоящего
приложения последовательно вычисляют начальное давление в ресивере для I, II и
III режимов продувки.
При
и
,
в соответствии с пп.
11 и 12 последовательно вычисляют начальное давление в ресивере
для продувки во II и III режимах. Для обоих
случаев, сравнивая полученные эначения
,
принимают минимальную величину за начальное давление в ресивере
, а
соответствующий
режим продувки выбирают в качестве оптимального.
При
и
продувку проводят в режиме III. Оптимальную
величину начального давления выбирают в соответствии с п. 12 настоящего
приложения.
15. Если
нет данных о загрязненности очищаемого участка, то продувку проводят в одном из
двух режимов (II или III). Для этих режимов в соответствии с пп. 11 и 12
настоящего приложения определяют предельную длину продуваемого участка
и
.
Оптимальный вариант
продувки и начальное давление в ресивере выбирают в зависимости от соотношения
полученных величин.
При
и
в соответствии с пп. 11 и 12 последовательно для
обоих режимов продувки вычисляют начальное давление в ресивере
.
Сравнивая полученные значения
,
принимают минимальную величину за начальное давление в ресивере
, и
соответствующий
режим продувки выбирают в качестве
оптимального.
При
и
продувку проводят в
III режиме. Оптимальную величину начального давления выбирают в соответствии с
п. 12.
16. Если при
расчетах по пп. 14 и 15
, то
необходимо уменьшить длину продуваемого участка.
17. После
определения оптимального варианта продувки и величины начального давления в
ресивере для выбранного режима в соответствии с одним из пп. 10, 11 или 12
определяют диаметр перепускной (байпасной) линии и условный диаметр запорной
арматуры, округляя полученные величины до ближайшего стандартного значения.
Если нет
характеристик крана, то принимают следующие осредненные значения коэффициентов
и
:
= 0,60,
= 0,60 - 0,70.
Пример расчета
Дано:
D = 1,4 м;
L =
;
;
;
P = 0,4 кг/м.
Загрязнения -
супесчаный грунт.
Определить
параметры продувки трубопровода, смонтированного в нитку при помощи внутреннего
центратора (без предварительной очистки полости протягиванием очистных
устройств).
Расчет
Расчет параметров
продувки проводят в следующем порядке:
вычисляют
предельную длину очищаемого участка при различных режимах продувки:
;
;
.
Сопоставляя эти
величины, получают:
;
вычисляют начальное
давление в ресивере для различных режимов продувки:
для I режима - 0,65
МПа;
для II режима - 0,7
МПа;
для III режима -
0,5 МПа;
выбирают в качестве
оптимального режим III продувки при начальном давлении в ресивере
= 0,5 МПа.
Для оптимального
режима
= 0,35 м.
Следовательно,
продувку проводят через полностью открытый кран байпасной линии
= 0,35 м.
Если нет
специальных поршней, оборудованных перепускным устройством для направленного
перетока газа, то продувку участка проводят с использованием поршней серии ОП.
В этом случае в
качестве оптимального режима продувки выбирают режим I при начальном давлении в
ресивере
= 0,65 МПа.
Для этого режима
= 0,25 м.
Таким образом,
продувку в этом режиме можно проводить, используя временные инвентарные узлы
пуска с коллектором, оборудованным кранами
= 0,25 м или до указанной величины перекрывать
поперечное сечение крана на байпасной линии.
МЕТОДИКА ОПРЕДЕЛЕНИЯ ПРОТЯЖЕННОСТИ УЧАСТКОВ
ПРИ ГИДРАВЛИЧЕСКОМ
ИСПЫТАНИИ ТРУБОПРОВОДОВ
18. Настоящая
методика предусматривает использование графоаналитического метода расчета.
19. Исходными
данными для расчета являются продольный профиль и технологическая схема
испытываемых трубопроводов, а также величины давлений, которые должны быть
созданы в пределах одного участка испытания:
- максимальное давление испытания в нижней
точке трубопровода равно
, МПа;
- минимальное давление испытания в верхней
точке трубопровода равно, но не меньше
, МПа;
- гарантированное заводом испытательное
давление без учета осевого подпора, МПа;
- рабочее (нормативное) давление, МПа.
20. Применительно к условному трубопроводу, продольный профиль и
технологическая схема которого приведены на рис. 2, методика предполагает
проведение расчета в приведенной последовательности:
определяют
максимальную разность высот продольного профиля (
в м) в
пределах одного участка испытания:.
;
сопоставляют
разницу высотных отметок всего трубопровода
с величиной
.
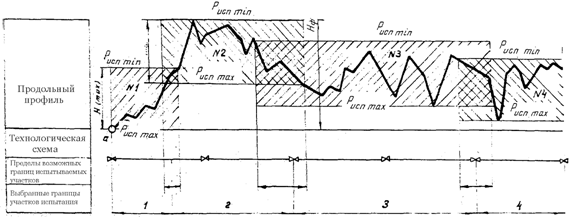
Рис. 2.
Схема определения числа и протяженности участков
испытания
магистрального газопровода
1 - 4 участки
испытания;
N 1 - N 4 -
максимально возможные зоны испытания
В случае, когда
, можно
проводить гидравлические испытания всего трубопровода или разделить его на
участки без учета продольного профиля.
Если
, то
выполняют графические построения на продольном профиле, как показано на рис. 2,
для этого:
1) проводят
горизонтальную линию через точку a (источник воды);
2) проводят
параллельно этой линии (на расстоянии, равном
от нее) другую линию до пересечения с линией
продольного профиля;
3) получают линии,
которые образуют максимально возможную зону испытания на первом участке
трубопровода (заштрихованный участок N 1);
4) определяют зоны
испытания других участков трубопровода, для этого проводя линии
и
через характерные верхние и нижние по профилю
точки таким образом, чтобы получить максимально возможную длину участков
испытания (заштрихованные прямоугольники N 2, 3, 4).
На этом заканчивают
предварительное определение протяженности и числа участков испытываемого
трубопровода с учетом допустимой разности отметок продольного профиля.
Окончательное
определение протяженности и числа участков ведут с учетом расположения на
трассе линейной арматуры.
Если разность
вертикальных отметок между соседними кранами меньше величины
, то
целесообразно проводить испытания целиком всего участка между кранами (участок
N 4 на рис. 2).
Если указанное
условие выполнено для нескольких соседних участков между линейными кранами
(участок N 3), тогда целесообразно испытывать весь участок целиком.
В случаях, когда
граница между участками испытания не может быть совмещена с местом установки
линейной арматуры, то ее устанавливают в зависимости от местных условий производства
работ.
МЕТОДИКА
РАСЧЕТА ИСПЫТАНИЯ УЧАСТКА МАГИСТРАЛЬНЫХ
ТРУБОПРОВОДОВ
КОМБИНИРОВАННЫМ СПОСОБОМ
Принципиальная
схема испытания участка трубопровода комбинированным способом показана на рис.
3.
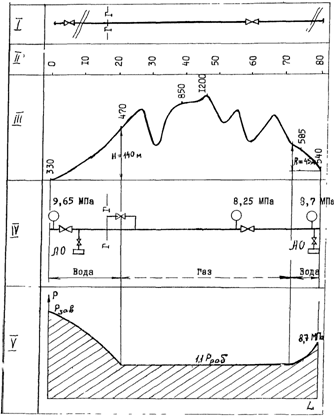
Рис. 3.
Принципиальная схема испытания участка
магистрального
трубопровода комбинированным способом:
I - схема
газопровода; II - километраж;
III - сжатый
продольный профиль;
IV - схема
заполнения трубопровода испытательными средами;
V - график
распределения давления
по длине
испытываемого трубопровода;
АО - опрессовочные
агрегаты; Г-Г - действующий газопровод
Дано: D - диаметр
испытываемого участка газопровода, D = 1420 мм; L - протяженность участка L = 80
км;
- рабочее давление,
= 7,5 МПа (75 кгс/см2);
- испытательное давление равно
= 1,1
= 8,25
МПа;
заводское
испытательное давление труб
= 9,65 МПа.
Газопровод
расположен в сильно пересеченной местности с большими разностями вертикальных
отметок отдельных участков (см. рис. 3, III) и пересекает действующий
газопровод (-Г-Г-) с рабочим давлением
= 5,5 МПа.
Испытываемый
газопровод заполняют газом через временную перемычку от действующего
газопровода до P = 5,5 МПа. Для создания испытательного давления часть объема
испытываемого газопровода заполняют водой с помощью опрессовочных агрегатов.
Расчет
Рассчитаем объем
воды (V), необходимый для создания испытательного давления на всей
протяженности трубопровода:
.
Испытательное
давление в нижних точках газопровода с учетом гидростатического давления не
должно превышать заводского испытательного давления. Учитывая это требование,
находим допустимый перепад высот для первого участка, заполняемого водой:
= 1,4 МПа или H = 140 м.
Этому перепаду
высот соответствует участок протяженностью
,
которую определяют графически по профилю трассы (см. рис. 3).
Объем закачиваемой
воды на первом участке составит:
,
что меньше
требуемого для создания испытательного давления на величину:
.
Этот объем воды
необходимо закачать в следующий участок. Протяженность этого участка равна:
.
Графически
по профилю газопровода находим положение второго участка от км 80 до км 73,5 и
максимальную разность высотных отметок на этом участке h = 45 м, которая меньше
предельной величины H = 140 м.
МЕТОДИКА ОПРЕДЕЛЕНИЯ ОПТИМАЛЬНЫХ ПАРАМЕТРОВ
ПОЛНОГО УДАЛЕНИЯ
ВОДЫ ИЗ ГАЗОПРОВОДОВ
ПОСЛЕ ИХ
ГИДРАВЛИЧЕСКОГО ИСПЫТАНИЯ
21. Эффективность
удаления воды в значительной степени определяется скоростью перемещения
поршней-разделителей по газопроводу.
Для достижения
высоких технико-экономических показателей необходимо проводить расчет
технологических параметров удаления воды, а при отклонении скорости
поршней-разделителей от оптимальных значений - регулирование параметров в
процессе передвижения этих устройств по осушаемому участку.
22. Оптимальная
скорость перемещения поршней-разделителей ограничена в пределах между
максимально и минимально допустимыми величинами этой скорости.
Максимальная
скорость поршней-разделителей
зависит от их конструктивной характеристики и
приведена в табл. 3 и 4 пп. 5.3 и 5.4 настоящей Инструкции.
Превышение
допустимой скорости очистных устройств приводит к
возрастанию динамических нагрузок, нарушению осесимметричного движения
поршней-разделителей, к их интенсивному износу и разрушению, что в свою очередь
значительно снижает качество проведения процесса удаления воды и требует
многократного повторения этого процесса.
Бесконтрольное
увеличение скорости перемещения поршней-разделителей затрудняет также
запланированный отвод воды из трубопроводов.
23. Минимальная
скорость перемещения поршней-разделителей
по предварительно очищенным газопроводам
(протягиванием в процессе сборки и сварки в нитку, продувкой с пропуском
металлических поршней ОП, а такие при повторном удалении воды) определена
необходимостью поддержания равномерного движения очистных устройств в потоке
воды и составляет
.
24. Минимальная
скорость поршней-разделителей при удалении воды, проводимом одновременно с
очисткой полости от загрязнений, определяется величиной, необходимой для
образования грунтовой пульпы в потоке воды перед разделителем, и составляет
.
25. Дальнейшее
снижение скорости передвижения поршней-разделителей вызывает скопление грунта
непосредственно перед разделителем. Перемещение поршней-разделителей в таком
режиме приводит к их деформации и к тому, что в газопроводах остаются вода и
загрязнения.
26. При удалении
воды из газопроводов поршни-разделители можно пропускать под давлением воздуха,
подаваемого в освобожденный от воды участок от ресивера, образованного на
прилегающем участке магистрали, или поступающего непосредственно от передвижных
компрессорных станций.
Подача воздуха от
передвижных компрессорных станций сокращает время и средства на удаление воды,
однако в этом случае для обеспечения оптимальной скорости перемещения
поршней-разделителей необходимо применять компрессоры высокой
производительности (см. п. 6.1 настоящей Инструкции).
Применение ресивера
позволяет использовать компрессоры меньшей производительности, чем при
непосредственной закачке воздуха в участок за разделителем, что особенно важно
в случаях удаления воды из трубопроводов большого диаметра и значительной
протяженности.
27. Наиболее эффективное удаление воды при минимальном числе пропусков
поршней-разделителей достигают равномерным перемещением этих устройств или
плавным изменением их скорости в пределах допустимых значений для поддержания
такого режима перемещения поршней-разделителей регулируют параметры процесса,
изменяя степень открытия запорной арматуры в узлах пуска или приема поршней и
контролируя эти параметры по показаниям образцовых манометров.
28. Если невозможно
провести регулирование, указанное в п. 27, то скорость передвижения поршней
стабилизируют, устанавливая в узлах приема сливные патрубки необходимых
размеров или перекрывая до определенного сечения запорную арматуру на узлах
пуска и приема поршней.
При правильном
выборе исходных параметров и проведении такой стабилизации
процесса колебания скорости поршня будут значительно снижены и не превысят
допустимых пределов.
29. Расчетные схемы
удаления воды приведены на рис. 4. В формулах (12) - (27), приведенных ниже,
приняты следующие обозначения и единицы измерения параметров:
L - длина
продуваемого участка, м;
- длина ресивера, м;
l - длина сливного
патрубка в узле приема поршней, м;
D - диаметр
трубопровода, м;
- диаметр ресивера, м;
F - площадь
поперечного сечения трубопровода, м2;
- площадь поперечного сечения ресивера, м2;
- площадь поперечного сечения сливного
патрубка, м2;
f - площадь
поперечного сечения запорной арматуры, м2;
- диаметр сливного патрубка, м;
- диаметр байпасной линии от ресивера и
условный диаметр запорной арматуры, м;
- давление при нормальных условиях (при
), МПа;
- давление в конце продуваемого участка, МПа;
- давление в начале продуваемого участка, МПа;
- начальное давление в ресивере, МПа;,
- атмосферное давление, равное 0,1 МПа;
x - текущая
координата по длине продуваемого участка, м;
z - координата
поршня-разделителя, м;
t - текущее время, с;
- продолжительность продувки данного участка
трубопровода, с;
v - скорость
перемещения поршня-разделителя, м/с;
- сопротивление перемещению поршня-разделителя
по трубопроводу (для ДЗК и ДЗК-РЭМ
, для
ОП, ОПР-М и РМ-ПС
), МПа;
R - газовая
постоянная:
для воздуха R = 287
м2/с2 x град;
для газа R = 519 м2/с2 x град;
- плотность воды (
= 1000
кг/м3), кг/м3;
- коэффициент гидравлического сопротивления
трубопровода;
- коэффициент расхода запорной арматуры. При
отсутствии данных о характеристике арматуры принимают усредненное значение
коэффициента
= 0,60;
T и
- абсолютная температура воздуха (или газа)
соответственно в трубопроводе или ресивере, К;
- абсолютная температура воздуха или газа в
нормальных условиях,
= 293 К;
K - количество
компрессоров, шт.;
Q -
производительность одного компрессора, м3/с;
h - разность
высотных отметок между концом очищаемого участка и поршнем при его перемещении
по газопроводу, проложенному по пересеченной местности, м. (При прохождении
поршня через точки газопровода, расположенные по продольному профилю выше конца
очищаемого участка, величину h принимают отрицательной);
g - ускорение
свободного падения, равное 9,81 м/с2;
n - коэффициент
запаса.
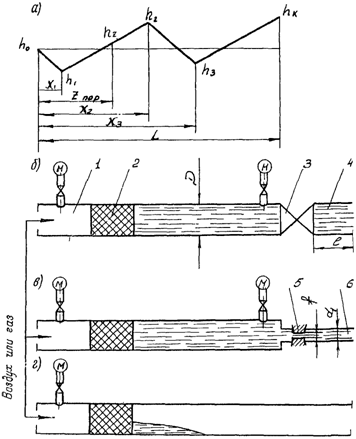
Рис. 4.
Расчетные схемы удаления воды:
а - продольный
профиль очищаемого участка;
б - удаление воды через линейный кран;
в - удаление воды
через сливной патрубок с запорной
арматурой; г - удаление воды на открытый конец газопровода;
1 - газопровод; 2 -
поршень-разделитель; 3 - линейный кран;
4 - сливной
патрубок; 5 - запорная арматура;
6 - водоспускная
линия;
L - длина участка,
освобождаемого от воды;
l - длина сливного
патрубка;
- диаметр сливного патрубка;
f - площадь
поперечного сечения запорной арматуры;
D - диаметр
трубопровода; Z - координата поршня-разделителя;
- индексами обозначены
соответствующие
точки продольного профиля
Предварительное
удаление воды
после
гидравлического испытания
30. При
удалении воды с помощью поршней-разделителей, перемещающихся по газопроводу под
давлением воздуха, подаваемого в очищаемый участок непосредственно от
передвижных компрессорных станций, используют следующие расчетные зависимости.
Минимальное давление
нагнетания компрессоров (
) определяют
по формуле
. (12)
Необходимое
количество компрессорных станций (K) вычисляют из соотношения
, (13)
где
при удалении воды из предварительно очищенных
(протягиванием или продувкой) участков газопровода;
- при удалении воды из газопровода после его
предварительной промывки;
n = 1,10 - для
газопроводов, проложенных по равнинной местности;
n = 1,25 - для
газопроводов, проложенных по пересеченной местности.
В формулах (12) и
(13) величина
может принимать следующие значения:
а) при удалении
воды на свободный конец газопровода без линейного крана или при полностью
открытом кране (рис. 4, б, г)
;
б) при удалении
воды на свободный конец газопровода при частично перекрытом линейном кране
(рис. 4, б), а также при удалении воды через сливной патрубок, оборудованный
запорной арматурой меньшего диаметра (рис. 4, в) или арматурой, перекрытой до
определенных размеров для стабилизации скорости передвижения
поршней-разделителей (см. ниже п. 13)
, (14)
где f - площадь
поперечного сечения неравнопроходной или частично перекрытой запорной арматуры;
в) при удалении
воды через сливной патрубок, оборудованный полностью открытой равнопроходной
запорной арматурой
. (15)
Расчет значений
и K по формулам (12) и (13) проводят для ряда
характерных точек очищаемого участка: начала (Z = 0), конца (Z = L), а также
нижних точек перегиба продольного профиля трассы газопровода (
и
, см.
рис. 4). Для этих же точек по продольному профилю трассы газопровода определяют
величины h.
Величину
минимальной скорости перемещения поршней-разделителей
принимают в соответствии с табл. 3, 4 (см. пп.
5.3 и 5.4).
Из ряда полученных
величин
и K выбирают максимальные и принимают их за
исходные значения давления нагнетания
и необходимого количества компрессорных
станций
.
Величину K при этом округляют до ближайшего большего целого числа.
Если нет
необходимого количества компрессорных станций заданной производительности Q, то
подачу воздуха в осушаемый участок следует проводить из ресивера.
31. При
удалении воды поршнями-разделителями, перемещающимися по газопроводам под
давлением воздуха (или газа), подаваемого в очищаемый участок от ресивера,
используют следующие соотношения.
Начальное давление
воздуха (или газа) в ресивере определяют по формуле
, (16)
где
и
- выбирают в соответствии с п. 30;
n = 1,10 - для
газопроводов, проложенных по равнинной местности;
n = 1,25 - для
газопроводов, проложенных по пересеченной местности.
Расчет значений
по формуле (16) ведут для ряда характерных
точек очищаемого участка, начала (Z = 0), конца (Z = L), а также нижних точек
перегиба продольного профиля трассы газопровода (
и
, см.
рис. 5).
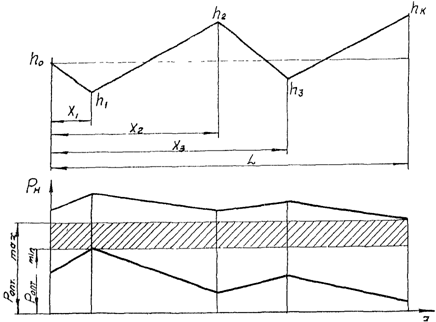
Рис. 5.
Схема определения параметров стабилизации скорости
движения
поршней-разделителей:
L - длина участка,
освобождаемого от воды; Z - координата
поршня-разделителя;
и
- верхняя и нижняя границы
изменения
начального давления ресивера для оптимального
режима удаления
воды;
- индексами обозначены
соответствующие
точки продольного профиля
Для этих же точек
по продольному профилю трассы газопровода определяют величины h. Величину
минимальной скорости перемещения поршней-разделителей
принимают в соответствии с табл. 3, 4 (см. пп.
5.3 и 5.4).
Из ряда полученных
величин
выбирают максимальную и принимают ее за
оптимальную величину начального давления ресивере (
).
Условный диаметр
запорной арматуры или диаметр байпасной линии от ресивера к очищаемому участку
равен:
.
32. Если воду
удаляют из трубопровода, не регулируя параметры этого процесса, то для
уменьшения колебаний скорости передвижения поршней-разделителей устанавливают
на узлах приема сливные патрубки заданного размера (диаметра
и длины l).
Оптимальные размеры
сливного натрубка определяют в зависимости от диаметра очищаемого участка D и
отношения длины к диаметру этого патрубка
по табл. 5.
Таблица 5
───────────────────┬───────────┬──────────────┬───────────────┬────────────
Отношение длины │ l │ l
│ l │ l
к
диаметру сливного│ -- < 100 │100 < -- < 500│500 < --
< 1000│ -- > 1000
l │ d │ d
│ d │ d
патрубка -- │
1 │ 1
│ 1 │
1
d │ │ │ │
1 │ │ │ │
───────────────────┴───────────┴──────────────┴───────────────┴────────────
Отношение
диаметра 0,20 - 0,30 0,30 - 0,40 0,40 - 0,50 0,50 - 0,60
сливного
патрубка
к
диаметру
трубопровода

--------------------------------
Примечание. Если по
условиям материально-технического снабжения узлы приема невозможно оборудовать
сливными патрубками оптимальных размеров, допускается устанавливать патрубки
меньшего диаметра. Однако необходимо учитывать, что при значительном уменьшении
диаметров патрубков скорость передвижения поршней-разделителей существенно
уменьшена, что ухудшит качество проведенного процесса удаления воды, увеличит
энергетические затраты и увеличит время этой операции.
33. Если одна или
несколько точек продольного профиля расположены выше конца очищаемого участка,
то необходимо перекрыть запорную арматуру на сливном патрубке в узле приема
поршней-разделителей, чтобы предотвратить слив воды самотеком из участка за
перевальной точкой в процессе передвижения поршня-разделителя.
Оптимальную степень
перекрытия запорной арматуры определяют из соотношения
,
где
- разность высотных отметок между наиболее
высокой (перевальной) точкой и концом очищаемого участка трубопровода, м.
После того как
поршень-разделитель прошел перевальную точку газопровода, запорную арматуру на
сливном патрубке открывают на полное сечение (в соответствии с табл. 5). Время
от начала пропуска поршня до момента открытия арматуры определяют из выражения
, (17)
где
- расстояние от начала очищаемого участка до
перевальной точки, м.
Окончательное
удаление воды
(контрольный
пропуск поршней-разделителей)
34. При
контрольном пропуске поршней-разделителей, перемещающихся по газопроводу под
давлением воздуха, подаваемого в осушаемый участок непосредственно от
передвижных компрессорных станций, используют те же компрессорные станции, что
и при предварительном удалении воды после гидравлического испытания.
Необходимое
количество передвижных компрессорных станций для контрольного пропуска
поршней-разделителей вычисляют по формуле
, (18)
где n = 1,1 - 1,2 -
для газопроводов, проложенных по равнинной местности;
n = 1,2 - 1,5 - для
газопроводов, проложенных по пересеченной местности;
- оптимальная скорость передвижения
поршня-разделителя.
При необходимости
повторения контрольного пропуска коэффициент n принимают n = 1.
В формуле (18)
величина B может принимать следующие значения:
при
будет
;
при
принимают B = 1.
Величину
оптимальной скорости перемещения поршней-разделителей при контрольных пропусках
рекомендуется принимать из соотношения
, (19)
где значения
и
выбирают в соответствии с табл. 3, 4 (см. пп.
5.3 и 5.4).
Величину
коэффициента гидравлического сопротивления
принимают
.
Полученную по формуле (18) величину округляют до ближайшего большего целого
числа.
35. При
контрольном пропуске поршней-разделителей, перемещающихся по газопроводу под
давлением воздуха (или газа), подаваемого в осушаемый участок от ресивера,
используют следующие соотношения.
Начальное давление
воздуха или газа в ресивере определяют по формуле
, (20)
где n = 1,5 - 2,0 -
для газопроводов, проложенных по равнинной местности;
n = 2,0 - 2,5 - для
газопроводов, проложенных по пересеченной местности.
При необходимости
повторения контрольного пропуска значения коэффициента n принимают n = 1,2 -
1,5.
В формуле (20)
величины
и
принимают следующие значения:
при
будет
; (21)
; (22)
при
.
Величину
оптимальной скорости перемещения поршней-разделителей принимают из соотношения
(19), а коэффициент гидравлического сопротивления
.
Расчет значений
по формуле (20) проводят для двух точек
осушаемого участка начала Z = 0 и конца Z = L. Из полученных величин выбирают
максимальную и принимают ее за оптимальную величину начального давления в
ресивере (
).
Условный диаметр
запорной арматуры или диаметр байпасной линии от ресивера к осушаемому участку
принимают
. (23)
Регулирование
скорости поршней-разделителей
при предварительном
удалении воды
после гидравлического
испытания
36. При удалении воды с помощью поршней-разделителей, перемещающихся по
газопроводу под давлением воздуха, подаваемого в очищаемый участок
непосредственно от передвижных компрессорных станций, для поддержания
равномерного передвижения поршней по всей длине очищаемого участка необходимо
плавно регулировать параметры процесса, изменяя степень открытия запорной
арматуры в узле приема поршней и контролируя эти параметры по показаниям
образцового манометра.
Изменение давления
в узле приема
при регулировании скорости передвижения
поршней определяют по формуле
, (24)
где
.
Параметры
регулирования вычисляют с учетом реальной производительности используемых
компрессорных станций KQ для следующих значений:
;
;
;
;
,
а также для
значений, соответствующих всем точкам перегиба продольного профиля трассы
газопровода (см. рис. 4):
;
;
.
Для этих же точек
по продольному профилю трассы газопровода определяют величины h.
Величину
оптимальной скорости перемещения поршней-разделителей v принимают равной
минимально допустимой скорости их движения, установленной при выборе исходных
параметров процесса в соответствии с табл. 3, 4 (см. пп. 5.3 и 5.4). Величину
выбирают в соответствии с п. 30 настоящего
приложения.
37. При удалении воды с применением поршней-разделителей, которые
перемещаются по газопроводу под давлением воздуха или газа, подаваемого в
очищаемый участок от ресивера, чтобы предотвратить отклонение скорости
поршней-разделителей от допустимых значений, необходимо ограничить величину
давления в начале очищаемого участка; для этого перекрывают запорную арматуру
на перемычке от ресивера и контролируют величину давления по показаниям
образцового манометра.
Такое ограничение
давления рекомендуется осуществлять в случаях, когда по условиям проведения
предшествующих или последующих этапов очистки полости и удаления воды подачу
воздуха (или газа) от ресивера целесообразно проводить через байпасную линию
большего диаметра, чем указано в п. 31, или, если давление воздуха (или газа)
превышает расчетную величину давления в ресивере (
).
Для определения
оптимального давления в начале очищаемого участка
используют графоаналитический метод расчета
параметров процесса.
Величину давления в
начале очищаемого участка вычисляют по формуле
, (25)
где
выбирают в соответствии с п. 30.
В формуле (25)
величина
может принимать следующие значения:
а) при удалении
воды на свободный конец газопровода без линейного крана или при полностью
открытом линейном кране (см. рис. 4, б, г)
;
б) при удалении
воды на свободный конец газопровода при частично перекрытом линейном кране (см.
рис. 4, б), а также при удалении воды через сливной патрубок, оборудованный
неравнопроходной запорной арматурой меньшего диаметра (рис. 4, в) или
арматурой, перекрытой до определенных размеров для стабилизации скорости
передвижения поршней-разделителей,
,
где f - площадь
поперечного сечения неравнопроходной или частично перекрытой запорной арматуры;
в) при удалении
воды через сливной патрубок, оборудованный полностью открытой равнопроходной
запорной арматурой (рис. 4, в)
. (26)
Расчет
по формуле (25) проводят для двух значений
скорости перемещения поршней-разделителей: максимально допустимой
и минимально допустимой
- табл. 3, 4 (см. пп. 5.3 и 5.4).
Значения
определяют для всех характерных точек
очищаемого участка: начала Z = 0, конца Z = L, а также при значениях в верхних
и нижних точках перегиба продольного профиля трассы газопровода
;
и
(см. рис. 4, а). Для этих же точек по
продольному профилю трассы газопровода определяют величины h.
По
полученным значениям
строят график изменения давления в начале
очищаемого участка при равномерном перемещении поршней-разделителей по всей его
длине с максимальной и минимальной скоростями (см. рис. 5). В этом случае для стабилизации скорости поршней-разделителей
достаточно поддерживать давление
в пределах
.
Изменение давления
в начале очищаемого участка в указанных пределах не приведет к отклонению
скорости поршней-разделителей от допустимых величин при их перемещении по всей
дайне магистрали.
Регулирование
параметров при окончательном удалении
воды (контрольный
пропуск поршней-разделителей)
38. При контрольном
пропуске очистных устройств, перемещающихся по газопроводам под давлением
воздуха или газа, подаваемого в осушаемый участок от ресивера, для
предотвращения значительного отклонения скорости поршней-разделителей от
оптимальных значений, необходимо ограничить величину давления в начале
продуваемого участка, перекрывая запорную арматуру на перемычке от ресивера.
Такое регулирование
проводят, если по условиям выполнения предшествующих этапов очистки полости и
удаления воды целесообразно использовать запорную арматуру большего диаметра,
чем указано в п. 35, или в случаях превышения давления газа
расчетной величины давления в ресивере (
).
Величину давления в
начале очищаемого участка определяют по формуле
, (27)
где n = 1,5 - 2,0 -
для газопроводов, проложенных по равнинной местности;
n = 2,0 - 2,5 - для
газопроводов, проложенных по пересеченной местности.
При необходимости
повторения контрольного пропуска коэффициент n принимают n = 1,2 - 1,5.
В формуле (27)
величины
и
принимают следующие значения.
При контрольном
пропуске поршней-разделителей ДЗК, ДЗК-РЭМ, ОПР-М для
значения
и
вычисляют по формулам (20) и (21), принимая
, а для
,
.
Расчет значений
по формуле (27) проводят для двух точек
очищаемого участка: начала Z = 0 и конца Z = L. Оптимальную скорость
перемещения поршней-разделителей по осушаемому участку принимают в соответствии
с соотношением (19).
Из двух полученных
значений
выбирают максимальное и принимают его за
оптимальную величину начального давления в осушаемом участке
(
). Перекрывая
запорную арматуру на перемычке от ресивера, поддерживают величину оптимального
давления в начале осушаемого участка в процессе всего времени передвижения
поршней-разделителей.
Пример расчета
параметров удаления воды
На участке
газопровода длиной L = 50 x
м, диаметром D = 1,2 м (укрупненный профиль
приведен на рис. 4, а настоящего приложения).
Воду удаляли в два
этапа:
I этап -
предварительное удаление с пропуском поршня-разделителя ОПР-М;
II этап -
окончательное удаление с пропуском поршня-разделителя ДЗК-РЭМ.
Для данного участка
газопровода характерные точки профиля имеют следующие координаты:
,
,
,
,
.
Высота столба воды
перед поршнем в момент прохождения им этих точек, т.е. разность отметок между
концом газопровода и рассматриваемой точкой по продольному профилю трассы
составит:
.
Воду удаляли через
сливной патрубок, оборудованный равнопроходной запорной арматурой. По условиям
проведения работ воду отводили в сторону от узла приема на расстояние l = 30 м.
Рассмотрим два
варианта подачи воздуха:
I вариант - от
компрессора;
II вариант - из
ресивера.
Дополнительные
данные, необходимые для расчета: Т = 20 °C;
;
;
.
Расчет
Для I и II
вариантов по табл. 5 данного приложения определяем оптимальный диаметр сливного
патрубка
.
Минимальную
скорость перемещения поршней-разделителей принимают равной
(в соответствии с табл. 4, п. 5.4).
Давление в конце
продуваемого участка в соответствии с п. 30 данного приложения (формула 15)
составит
.
Подача воздуха от
компрессоров (I вариант)
Предварительное
удаление воды. По формуле (12) рассчитываем минимальное давление нагнетания для
нескольких характерных точек участка:

.
По наибольшей
величине
выбираем (по табл. 6, п. 6.1) компрессоры
АМС-4 производительностью Q = 57,5 м3/мин.
По формуле (13)
определяем количество компрессоров K = 4,98.
Принимаем K = 5 шт.
Окончательное
удаление воды. Оптимальная скорость перемещения поршней (из п. 34 данного
приложения) принимаем равной v = 1,3 м/с.
Количество
компрессоров вычисляется по формуле (18) данного приложения
K = 2,76.
Принимаем K = 3 шт.
(так как
, то B
= 1).
В связи с
необходимостью применения большого количества компрессоров удалять воду
целесообразно с подачей воздуха от ресивера.
Подача воздуха от
ресивера (II вариант)
Предварительное
удаление воды. По формуле (16) определяют давление в ресивере для нескольких
характерных точек:

.
Принимаем давление
в ресивере
.
Диаметр байпасной
линии (по п. 31) принимаем равным
.
Окончательное
удаление воды. Так как
, то
,
.
Начальное давление
в ресивере при первом пропуске по формуле (20) данного приложения составит:
;
.
За расчетную
величину принимаем
.
Диаметр байпасной
линии (по п. 35) принимаем равным
.
Параметры
регулирования скорости поршней-разделителей
При удалении воды
поршнями-разделителями, которые перемещаются по газопроводу под давлением
воздуха, подаваемого в очищаемый участок непосредственно от передвижных
компрессорных станций, изменение давления в узле приема определяют по формуле
(24) данного приложения.
Полученные
результаты сводят в табл. 6.
Таблица 6
────┬──────┬───────┬──────────┬───────┬─────────┬──────────┬───────┬───────
│
│ x │ │ x
│ │ │ x
│
│
│ 1 │ │ 2 │ │ │ 3 │
t,
с│t = 0 │t = -- │t = 0,25t │t = -- │t = 0,5t
│t = 0,75t │t = -- │t = t
│
│ v │ k│ v
│ k│ k│ v
│ k
────┴──────┴───────┴──────────┴───────┴─────────┴──────────┴───────┴───────
P, 0,84
0,57 0,76 0,95
0,72 0,75 0,72
0,10
МПа
При удалении воды
поршнями-разделителями, перемещающимися по газопроводу под давлением воздуха
или газа от ресивера, для определения оптимального давления в начале очищаемого
участка используют графоаналитический метод расчета параметров процесса.
В соответствии с п.
37 настоящего приложения вычисляем давление в узле приема при движении поршня
ОПР-М со скоростью
и
.
По формуле (25)
просчитываем давления во всех характерных точках при скоростях
и
и полученные
результаты сводим в табл. 7 (по рис. 5).
Таблица 7
───────────┬───────────┬───────────┬────────────┬───────────┬──────────────
x
│ x │
x │
x │ x
│ L
│ 0
│ 1 │
2 │ 3
│
───────────┴───────────┴───────────┴────────────┴───────────┴──────────────
P
(v ) 0,30 0,68 0,36 0,58 0,16
min
P
(v ) 9,38 9,08 7,28 6,04 4,13
max
По полученным
данным строим график в соответствии с рис. 5 данного приложения. Анализ этого
графика показывает, что для стабилизации скорости поршней-разделителей давление
в начале очищаемого участка необходимо поддерживать в пределах
.
Большая величина
верхнего предела этого давления объясняется тем, что удаление воды ведется
через сливной патрубок оптимального сечения, препятствующий резкому увеличению
скорости воды и поршней-разделителей.
В связи с этим для
достижения оптимальной скорости движения поршней-разделителей практически
достаточно поддерживать в начале очищаемого участка давление не ниже P = 0,7
МПа.
При контрольном
пропуске поршней-разделителей, перемещающихся по газопроводу под давлением
воздуха от ресивера, оптимальную величину давления в начале очищаемого участка
определяют по формуле (27) данного приложения при
.