Утвержден и введен в
действие
Приказом
Федерального агентства
по техническому
регулированию
и метрологии
от 11 октября 2004
г. N 32-ст
МЕЖГОСУДАРСТВЕННЫЙ СОВЕТ ПО СТАНДАРТИЗАЦИИ,
МЕТРОЛОГИИ И СЕРТИФИКАЦИИ
INTERSTATE COUNCIL FOR
STANDARDIZATION,
METROLOGY AND CERTIFICATION
МЕЖГОСУДАРСТВЕННЫЙ СТАНДАРТ
КОЛЕСА ЦЕЛЬНОКАТАНЫЕ
ТЕХНИЧЕСКИЕ УСЛОВИЯ
All-rolled
wheels. Specifications
ГОСТ 10791-2004
Группа В41
ОКП 09 4300
Предисловие
Цели, основные
принципы и основной порядок проведения работ по межгосударственной
стандартизации установлены ГОСТ 1.0-92 "Межгосударственная система
стандартизации. Основные положения" и ГОСТ 1.2-97 "Межгосударственная
система стандартизации. Стандарты межгосударственные, правила и рекомендации по
межгосударственной стандартизации. Порядок разработки, принятия, применения,
обновления и отмены".
1. Разработан
Федеральным государственным унитарным предприятием "Всероссийский
научно-исследовательский институт железнодорожного транспорта" (ФГУП
ВНИИЖТ) МПС России, Федеральным государственным научно-исследовательским
институтом вагоностроения (ФГУП ГосНИИВ), Институтом
черной металлургии Украины (ИЧМО) и ОАО "Уральский институт металлов"
(ГНЦ РФ ОАО УИМ).
2. Внесен Федеральным агентством по техническому регулированию
и метрологии.
3. Принят
Межгосударственным советом по стандартизации, метрологии и сертификации
(протокол N 25 от 26 мая 2004 г.).
За принятие
проголосовали:
┌─────────────────────┬─────────────────┬────────────────────────┐
│Краткое
наименование │Код страны по МК │Сокращенное наименование│
│ страны по │(ИСО 3166)004-97 │ национального органа │
│МК
(ИСО 3166)004-97 │ │ по стандартизации │
├─────────────────────┼─────────────────┼────────────────────────┤
│Азербайджан │AZ │Азстандарт │
│Армения │AM │Армстандарт │
│Беларусь │BY │Госстандарт
Республики │
│ │ │Беларусь │
│Грузия │GE │Грузстандарт │
│Казахстан │KZ │Госстандарт
Республики │
│ │ │Казахстан │
│Кыргызстан │KG │Кыргызстандарт │
│Молдова │MD │Молдовастандарт │
│Российская
Федерация │RU
│Госстандарт России
│
│Таджикистан │TJ │Таджикстандарт │
│Туркменистан │TM │Главгосслужба │
│ │ │"Туркменстандартлары"
│
│Узбекистан │UZ │Узгосстандарт │
│Украина │UA │Госстандарт Украины │
└─────────────────────┴─────────────────┴────────────────────────┘
4. Настоящий
стандарт разработан с учетом основных нормативных положений международного
стандарта ИСО 1005-6-94 "Подвижной состав железных дорог. Часть 6.
Безбандажные колеса для подвижного состава. Технические условия поставки".
5. Приказом
Федерального агентства по техническому регулированию и метрологии от 11 октября
2004 г. N 32-ст межгосударственный стандарт ГОСТ 10791-2004 введен в действие
непосредственно в качестве национального стандарта Российской Федерации с 1
июля 2005 г.
6. Взамен ГОСТ
10791-89.
1. Область
применения
Настоящий стандарт
распространяется на цельнокатаные колеса (далее - колеса) исполнения УХЛ по
ГОСТ 15150 для колесных пар грузовых и пассажирских тележек вагонов
локомотивной тяги, пассажирских, маневровых и грузовых локомотивов, путевых
машин, немоторных вагонов электро-
и дизель-поездов магистральных железных дорог колеи 1520 мм.
Допускается по
согласованию между изготовителем и потребителем изготовлять колеса в
соответствии с требованиями Приложения А.
2.
Нормативные ссылки
В настоящем
стандарте использованы ссылки на следующие стандарты:
ГОСТ 8.010-99
<*>. Государственная система обеспечения единства измерений. Методика
выполнения измерений
------------------------------------
<*> На
территории Российской Федерации действует ГОСТ Р
8.563-96.
ГОСТ 12.1.004-91.
Система стандартов безопасности труда. Пожарная безопасность. Общие требования
ГОСТ 12.1.005-88.
Система стандартов безопасности труда. Общие санитарно-гигиенические требования
к воздуху рабочей зоны
ГОСТ 12.1.007-76.
Система стандартов безопасности труда. Вредные вещества. Классификация и общие
требования безопасности
ГОСТ 12.2.003-91.
Система стандартов безопасности труда. Оборудование производственное. Общие
требования безопасности
ГОСТ 12.3.002-75.
Система стандартов безопасности труда. Процессы производственные. Общие
требования безопасности
ГОСТ 380-94. Сталь
углеродистая обыкновенного качества. Марки
ГОСТ 1497-84 (ИСО
7801-84). Металлы. Методы испытания на растяжение
ГОСТ 1778-70 (ИСО
4967-79). Сталь. Металлографические методы определения неметаллических
включений
ГОСТ 7564-97.
Прокат. Общие правила отбора проб, заготовок и образцов для механических и
технологических испытаний
ГОСТ 7565-81 (ИСО
377-2-89). Чугун, сталь и сплавы. Метод отбора проб для определения химического
состава
ГОСТ 9012-59 (ИСО
410-82, ИСО 6506-81). Металлы. Метод измерения твердости по Бринеллю
ГОСТ 9036-88.
Колеса цельнокатаные. Конструкция и размеры
ГОСТ 9454-78.
Металлы. Метод испытания на ударный изгиб при пониженных, комнатной
и повышенных температурах
ГОСТ 10243-75.
Сталь. Метод испытаний и оценки макроструктуры
ГОСТ 15150-69.
Машины, приборы и другие технические изделия. Исполнения для различных
климатических районов. Категории, условия эксплуатации, хранения и
транспортирования в части воздействия климатических факторов внешней среды
ГОСТ 17745-90.
Стали и сплавы. Методы определения газов
ГОСТ 18895-97.
Сталь. Метод фотоэлектрического спектрального анализа
ГОСТ 22536.0-87.
Сталь углеродистая и чугун нелегированный. Общие требования к методам анализа
ГОСТ 22536.1-88.
Сталь углеродистая и чугун нелегированный. Методы определения общего углерода и
графита
ГОСТ 22536.2-87.
Сталь углеродистая и чугун нелегированный. Методы определения серы
ГОСТ 22536.3-88.
Сталь углеродистая и чугун нелегированный. Методы определения фосфора
ГОСТ 22536.4-88.
Сталь углеродистая и чугун нелегированный. Методы определения кремния
ГОСТ 22536.5-87
(ИСО 629-82). Сталь углеродистая и чугун нелегированный. Методы определения
марганца
ГОСТ 22536.7-88.
Сталь углеродистая и чугун нелегированный. Методы определения хрома
ГОСТ 22536.8-87.
Сталь углеродистая и чугун нелегированный. Методы определения меди
ГОСТ 22536.9-88.
Сталь углеродистая и чугун нелегированный. Методы определения никеля
ГОСТ 22536.12-88.
Сталь углеродистая и чугун нелегированный. Методы определения ванадия
ГОСТ 28033-89.
Сталь. Метод рентгенофлюоресцентного анализа.
Примечание. При
пользовании настоящим стандартом целесообразно проверить действие ссылочных
стандартов (и классификаторов) по указателю "Национальные стандарты",
составленному по состоянию на 1 января текущего года, и по соответствующим
информационным указателям, опубликованным в текущем году. Если ссылочный
документ заменен (изменен), то при пользовании настоящим стандартом следует
руководствоваться замененным (измененным) стандартом. Если ссылочный документ
отменен без замены, то положение, в котором дана ссылка на него, применяется в
части, не затрагивающей эту ссылку.
3.
Конструкция и размеры
3.1.
Конструкция и размеры колес - по ГОСТ 9036. Допускается изготовлять колеса
других конструкций и размеров по чертежам, согласованным с потребителем.
Схема условного
обозначения колес:
Диаметр колеса по кругу катания
────────────────────────────────
/ Диаметр расточки ступицы
/
─────────────────────────
/ / Обозначение стандарта на размеры
/ /
─────────────────────────────────
/ /
/
Х -
Х Х
Колесо -----------
Х Х
\ \ Обозначение настоящего стандарта
\
─────────────────────────────────
\
Марка стали
────────────
3.2. Пример
условного обозначения колеса диаметром по кругу катания 957 мм, внутренним
диаметром отверстия ступицы 190 мм по ГОСТ 9036, из стали марки 1 по ГОСТ
10791:
957
- 190 ГОСТ 9036-88
Колесо
----------------------
1
ГОСТ 10791-2004
4. Технические требования
4.1. Колеса
изготовляют в соответствии с требованиями настоящего стандарта.
4.2. Колеса
изготовляют из стали марок:
1 - для
пассажирских вагонов локомотивной тяги, пассажирских локомотивов, путевых
машин, немоторных вагонов электро-
и дизель-поездов;
2 и 3 - для
грузовых вагонов, маневровых и грузовых локомотивов.
Колеса из стали
марки 2 с содержанием углерода не более 0,63% изготовляют по требованию
потребителя для пассажирских вагонов и немоторных
вагонов электро- и дизель-поездов.
4.3. Колеса должны
быть изготовлены из спокойной стали, полученной мартеновским,
кислородно-конвертерным или электросталеплавильным способом. Сталь должна быть
подвергнута внепечной обработке инертным газом.
Сталь может
подвергаться вакуумированию.
4.4. При
изготовлении колес из слитков для гарантии отсутствия усадочных раковин и
чрезмерных ликваций от каждого конца слитка отрезают часть, достаточную для
удаления этих дефектов.
4.5. Химический
состав стали колес по ковшевой
пробе должен соответствовать нормам, указанным в таблице 1.
Таблица 1
Химический состав
стали колес
┌──────┬─────────────────────────────────────────────────────────┐
│Марка
│ Массовая доля
элементов, % │
│стали
├──────────┬─────────┬─────────┬─────────┬────────┬───────┤
│ │ Углерод │Марганец │ Кремний │
Ванадий │ Сера │Фосфор │
│ │ │ │ │
├────────┴───────┤
│ │ │ │ │ │ не более
│
├──────┼──────────┼─────────┼─────────┼─────────┼────────┬───────┤
│1 │0,44 - │0,80 - │0,40 - │0,08 - │0,030 │0,035
│
│ │ 0,52│ 1,20│ 0,65│ 0,15│ │ │
├──────┼──────────┼─────────┼─────────┼─────────┼────────┼───────┤
│2 │0,55 - │0,50 - │0,22 - │Не более │0,030 │0,035
│
│ │ 0,65│ 0,90│ 0,45│0,10 │ │ │
├──────┼──────────┼─────────┼─────────┼─────────┼────────┼───────┤
│3 │0,58 - │0,50 - │0,22 - │0,08 - │0,020 │0,030
│
│ │ 0,67│ 0,90│ 0,45│ 0,15│ │ │
├──────┴──────────┴─────────┴─────────┴─────────┴────────┴───────┤
│ Примечания. 1. В стали допускается
отклонение от массовой │
│доли
углерода +/- 0,02%. │
│ 2. Массовая доля никеля, хрома и меди не
должна быть более │
│0,30%
каждого элемента, молибдена - более 0,08%. │
│ 3. При использовании непрерывно-литой
заготовки массовая
│
│доля
серы не должна превышать 0,020%. │
│ 4. В готовых колесах: предельные отклонения
по массовой доле│
│углерода,
марганца, кремния, серы и фосфора от указанных в │
│таблице
- в соответствии с ГОСТ 380, по массовой доле ванадия - │
│не
более +/- 0,02%.
│
└────────────────────────────────────────────────────────────────┘
4.6. Для вакуумированной стали массовая доля водорода не должна
превышать 0,0002%.
4.7.
Готовые колеса должны быть без флокенов, расслоений,
трещин, завернувшихся и утонувших корочек, остатков усадочных раковин.
Внутренние дефекты, выявляемые при ультразвуковом контроле, число и размеры
которых превышают нормы, согласованные с потребителем, не допускаются. Место
расположения, размер и характер допустимых дефектов макроструктуры должны
соответствовать требованиям нормативно-технической документации, согласованным
с потребителем.
4.8. Средний балл
по неметаллическим включениям в вакуумированной и невакуумированной стали ободьев колес допускается в
пределах, указанных в таблице 2.
Таблица 2
Средний балл по
неметаллическим включениям
(вакуумированная/невакуумированная
сталь)
┌─────────────────────────────┬────────────────────┬─────────────┐
│ Тип включений │Условное обозначение│Средний
балл,│
│ │ неметаллических │
не более │
│ │ включений │ │
├─────────────────────────────┼────────────────────┼─────────────┤
│Сульфиды │С │2/3 │
│Оксиды
строчечные │ОС │1/1 │
│Силикаты
пластичные │СП │1,5/3 │
│Силикаты
хрупкие │СХ │2/3 │
│Оксиды
глобулярные, силикаты │СН
│2,5/3 │
│недеформирующиеся │ │ │
└─────────────────────────────┴────────────────────┴─────────────┘
4.9. Поверхность
колес должна быть без дефектов: плен, закатов, трещин, раскатанных загрязнений.
Для устранения дефектов допускается механическая обработка поверхностей по ГОСТ
9036.
До термообработки
допускается абразивная зачистка дефектов и неровностей поверхности колес (кроме
мест перехода от обода к диску), не выводящая сечение за минимальные размеры.
Шероховатость обрабатываемых поверхностей Rz
40 мкм (Ra
12,5 мкм). После термообработки допускается
зачистка местных неровностей боковых поверхностей обода глубиной до 0,3 мм.
4.10.
Поверхность колес должна быть без окалины и защищена от коррозии. Методы
предотвращения или удаления окалины, качество поверхности должны соответствовать
требованиям технической документации, согласованной с потребителем.
4.11. Ободья колес
подвергают упрочняющей термической обработке прерывистой закалкой и отпуском.
Температура отпуска колес - не менее 450 °С.
По согласованию с
потребителем допускаются другие способы упрочняющей термической обработки.
4.12.
Сходимость обода колеса при радиальной разрезке после термической обработки
должна быть не менее 1 и не более 5 мм. Расходимость не допускается.
4.13. Диски колес,
изготовленных по ГОСТ 9036, подвергают упрочнению обработкой дробью и защищают
от коррозии. Условия поставки колес без упрочнения обработкой дисков дробью
должны быть согласованы с потребителем.
4.14.
Механические свойства, твердость и ударная вязкость колес, подвергнутых
упрочняющей термической обработке, должны соответствовать указанным
в таблице 3.
Таблица 3
Механические
свойства, твердость и ударная вязкость колес
┌─────┬───────────┬────────┬───────┬───────────┬─────────────────┐
│Марка│Временное
│Относи- │Относи-│ Твердость
│Ударная вязкость │
│стали│сопротив-
│тельное │тельное│на
глубине │ KCU на образцах │
│ │ление │удлине- │сужение│ 30
мм от │ при температуре │
│ │сигма , │ние │пси, %
│поверхности│ 20 °С, Дж/см2 │
│ │
в │дельта, │ │катания, НВ│ (кгс х м/см2), │
│ │Н/мм2 │% │ │ │ не менее
│
│ │(кгс/мм2)
├────────┴───────┴───────────┼────────┬────────┤
│ │ │ не менее │из обода│из
диска│
├─────┼───────────┼────────┬───────┬───────────┼────────┼────────┤
│1 │880 - 1080 │12 │21 │248 │30 (3,0)│30 (3,0)│
│ │(90 - 110) │ │ │ │ │ │
├─────┼───────────┼────────┼───────┼───────────┼────────┼────────┤
│2 │910 - 1110 │8 │14 │255 │20 (2,0)│20 (2,0)│
│ │(93 - 113) │ │ │ │ │ │
├─────┼───────────┼────────┼───────┼───────────┼────────┼────────┤
│3 │980 - 1130 │8 │14 │285 │16 (1,6)│16 (1,6)│
│ │(100 - 115)│ │ │ │ │ │
├─────┴───────────┴────────┴───────┴───────────┴────────┴────────┤
│ Примечания.
1. На переходе
обода в диск
(точка А на│
│рисунке
3) значения твердости
должны быть не менее
чем на│
│15 единиц
ниже усредненной твердости
на глубине 30 мм│
│от
поверхности катания.
│
│ 2. Значения временного сопротивления
образцов, вырезанных из│
│диска,
не должны превышать 80% значений, полученных на образцах,│
│вырезанных из обода. Результаты испытаний
факультативные. │
│ 3.
Ударная вязкость на образцах из диска
при температуре│
│минус
60 °С должна быть не менее 15 (1,5) Дж/см2 (кгс х
м/см2). │
│ 4.
Результаты испытаний на ударную
вязкость образцов из│
│обода
- факультативные.
│
└────────────────────────────────────────────────────────────────┘
4.15.
Разница значений твердости ободьев на глубине (30 +/- 1) мм по периметру колес
не должна превышать 20 НВ.
4.16. На боковой
поверхности обода в горячем состоянии с наружной стороны колеса на расстоянии 3
- 10 мм от кромки внутренней поверхности до основания знаков (цифр) маркировки
наносят знаки (цифры) высотой 10 - 12 мм и глубиной до 4 мм в следующем
порядке:
- год изготовления
(две последние цифры);
- марку стали;
- номер плавки;
- условный номер
предприятия-изготовителя;
- при содержании
углерода в стали более 0,63% после марки стали колеса наносят букву
"Г";
- порядковый номер
колеса по системе нумерации предприятия-изготовителя;
- дополнительный
код, обозначающий собственность колес стран СНГ и Балтии, наносят в двух
местах. Первое клеймо - на расстоянии 150 - 200 мм от основной маркировки,
второе - на противоположной стороне. Допускается нанесение знаков кода
собственности в холодном состоянии после термообработки и до 10% месячного
объема поставок без кода собственности.
Между условным
номером предприятия-изготовителя и номером колеса на боковой поверхности обода
должна быть оставлена площадка для приемочных клейм потребителя. Изменение
порядка маркировки не допускается.
Две цифры
маркировки колеса допускается зачищать и наносить в холодном состоянии после
упрочняющей термической обработки.
После механической
обработки наружной боковой поверхности обода колеса допускается наносить всю
маркировку в холодном состоянии. В этом случае колеса маркируют до упрочняющей
термической обработки.
Удаление знаков,
неправильно нанесенных горячей маркировкой, допускается обточкой или зачисткой
наждаком с последующим нанесением маркировки в холодном состоянии до
упрочняющей термической обработки или отпуска.
По согласованию
изготовителя с потребителем допускается наносить дополнительные знаки
маркировки.
5.
Требования безопасности
5.1. Требования
безопасности при изготовлении колес - по стандартам предприятий по безопасности
и инструкциям по охране труда в соответствии с системой стандартов безопасности
труда.
5.2. Безопасность
при изготовлении колес обеспечивают: соответствием производственных процессов -
ГОСТ 12.3.002, режимов работы производственного оборудования - ГОСТ 12.2.003,
способов безопасного производства погрузочно-разгрузочных работ - ГОСТ
12.1.004, требований санитарной безопасности - ГОСТ 12.1.007.
5.3. Безопасность
эксплуатации колес - по разделам 4, 7 и 8 настоящего стандарта.
6.
Требования охраны окружающей среды
6.1. При
производстве колес применяют технологические процессы, не загрязняющие
окружающую среду, и предусматривают комплекс мероприятий с целью ее охраны.
6.2.
Санитарно-гигиенические требования к воздуху рабочей зоны - по ГОСТ 12.1.005.
7. Правила приемки
7.1. Для проверки
соответствия колес требованиям настоящего стандарта проводят приемосдаточные
испытания на соответствие 3.1, 4.4 - 4.9, 4.12, 4.14, 4.15 настоящего стандарта
в объеме, указанном в таблице 4.
Таблица 4
Виды и объем
испытаний и измерений колес
при приемосдаточных
испытаниях
┌───────────────────────────────┬─────────────────┬──────────────┐
│ Испытания и измерения │
Объем выборки
│Периодичность │
│ │ │ испытаний
│
├───────────────────────────────┼─────────────────┼──────────────┤
│Размеры
колес (3.1) │Каждое
колесо │Каждая
партия │
├───────────────────────────────┼─────────────────┼──────────────┤
│Химический
состав стали (4.4) │Ковшевая проба │Каждая плавка │
├───────────────────────────────┼─────────────────┼──────────────┤
│Загрязненность
неметаллическими│Одно
колесо │10% плавок │
│включениями
(4.7) │ │ │
├───────────────────────────────┼─────────────────┼──────────────┤
│Массовая
доля водорода (4.5) │Специальная проба│Каждая плавка │
│(для
вакуумированной стали) │перед разливкой │ │
│
│стали
│ │
├───────────────────────────────┼─────────────────┼──────────────┤
│Макроструктура
(4.6) │Одно колесо │Каждая
плавка │
├───────────────────────────────┼─────────────────┼──────────────┤
│Внутренние
дефекты - ультра- │Каждое колесо │Каждая
партия │
│звуковой
контроль (4.6) │ │ │
├───────────────────────────────┼─────────────────┼──────────────┤
│Качество
поверхности - │Каждое
колесо │Каждая
партия │
│визуальный
контроль (4.9) │ │ │
├───────────────────────────────┼─────────────────┼──────────────┤
│Механические
свойства обода
│Одно колесо
│Каждая партия │
│(4.14)
на четырехкратных │ │ │
│образцах │ │ │
├───────────────────────────────┼─────────────────┼──────────────┤
│Механические
свойства обода
│Одно колесо
│На 4% партий │
│(4.14)
на пятикратных образцах │
│ │
├───────────────────────────────┼─────────────────┼──────────────┤
│Механические
свойства диска
│Одно колесо
│На 4% партий │
│(4.14) │ │ │
├───────────────────────────────┼─────────────────┼──────────────┤
│Ударная
вязкость при +20 °С
│Одно колесо
│Каждая партия │
│диска
(4.14) │ │ │
├───────────────────────────────┼─────────────────┼──────────────┤
│Ударная
вязкость обода при
│Одно колесо
│На 4% партий │
│+20 °С (4.14)
│ │ │
├───────────────────────────────┼─────────────────┼──────────────┤
│Ударная
вязкость диска при
│Одно колесо
│На 4% партий │
│-60 °С (4.14)
│
│ │
├───────────────────────────────┼─────────────────┼──────────────┤
│Твердость
(4.14) │Одно колесо │Каждая
партия │
├───────────────────────────────┼─────────────────┼──────────────┤
│Равномерность
твердости (4.15) │Одно колесо │На 4% партий │
├───────────────────────────────┼─────────────────┼──────────────┤
│Остаточные
напряжения (4.12) │Одно колесо │Каждая
партия │
├───────────────────────────────┴─────────────────┴──────────────┤
│ Примечания. 1. По требованию потребителя или при экспертизе│
│допускается
проводить химический анализ состава стали
(см. 4.4)│
│на
пробах, взятых от готовых колес. │
│ 2.
Объем выборки для контроля макроструктуры, остаточных│
│напряжений, механических
свойств, ударной вязкости
диска и│
│твердости
при объеме партии колес свыше 250 шт. - по 7.4. │
└────────────────────────────────────────────────────────────────┘
Колеса, принятые
отделом технического контроля предприятия-изготовителя, предъявляют
представителю потребителя.
7.2. Колеса
предъявляют к приемке партиями. Партию составляют из колес одного назначения,
изготовленных из стали одной плавки - ковша, подвергнутых термообработке по
одному режиму.
Разъединять партии
колес при приемке не допускается.
Колеса, отставшие
от основной партии до упрочняющей термической обработки или в процессе ее
проведения, допускается комплектовать в сборную партию числом до 50 шт.
Сборную партию
комплектуют по эквиваленту "углерод плюс 1/4 марганца" с разницей в
продолжительности охлаждения при упрочняющей термической обработке не более 30
с.
7.3. Каждое колесо
подвергают внешнему осмотру и ультразвуковому контролю по 4.7, 4.9, 4.10, а
также проверяют размеры по 3.1.
7.4. От
каждой партии колес отбирают одно колесо от 250 шт. (2 от 251 шт. и более, 3 от
351 шт. и более и т.д.), принятое по внешнему виду и прошедшее визуальный и
ультразвуковой контроль, для проверки макроструктуры, остаточных напряжений,
механических свойств ободьев колес на растяжение, ударной вязкости диска при
температуре 20 °С и твердости. Отбор колес проводят
совместно с представителем потребителя.
7.5. Испытания на
ударную вязкость ободьев колес при температуре 20 °С,
дисков колес - при минус 60 °С, механических свойств ободьев колес - на
образцах с пятикратной расчетной длиной и контроль равномерности твердости
проводят на 4% партии колес; контроль неметаллических включений - на 10%
партий.
7.6. Химический
состав стали по ковшевой
пробе определяют на пробах, отбираемых по ГОСТ 7565 от каждой плавки-ковша.
При контроле
химического состава готовых колес отбор стружки или пробы проводят из средней
части обода колес или из головки образца, испытанного на растяжение.
Результаты проверки
распространяют на все колеса данной плавки.
7.7. Испытания
ободьев колес на растяжение проводят на одном образце. Отбор проб для испытания
стали ободьев колес на растяжение - по ГОСТ 7564.
7.8. Твердость
ободьев испытывают на одном макротемплете,
представляющем собой радиальное поперечное сечение обода колес и его перехода в
диск.
7.9. По
согласованию с потребителем допускается контролировать поверхностные дефекты
цельнокатаных колес магнитопорошковым, вихретоковым
или другими неразрушающими методами.
7.10. При
обнаружении внутренних дефектов, дефектов поверхности и отклонений от размеров,
превышающих допустимые, колеса бракуют.
При
неудовлетворительных результатах исследований макроструктуры и загрязненности
стали неметаллическими включениями проводят повторный контроль на удвоенном
числе колес от конкретной партии. Результаты повторного контроля распространяют
на всю партию.
При несоответствии
по результатам ультразвукового контроля 10% и более колес в партии проводят
контроль макроструктуры на одном из забракованных колес для выявления природы
дефектов, вызвавших забракование.
7.11. При
отсутствии в металле колес флокенов и
неудовлетворительных результатах испытаний механических свойств, ударной
вязкости, твердости, сходимости обода после разрезки проводят повторные
испытания на двух колесах, отобранных от той же партии.
7.12. При
неудовлетворительных результатах повторных испытаний механических свойств,
ударной вязкости, твердости (включая ее равномерность по периметру колеса),
сходимости обода после разрезки и при удовлетворительных результатах контроля
макроструктуры и загрязненности стали неметаллическими включениями для каждой
партии колес проводят не более двух дополнительных термических обработок.
Допускается проведение не более трех дополнительных отпусков.
После повторной
упрочняющей термической обработки или отпуска колеса подвергают испытаниям,
предусмотренным настоящим стандартом, за исключением контроля макроструктуры и
неметаллических включений. При неудовлетворительных результатах повторных
испытаний по одному из показателей всю партию бракуют.
7.13. Принятые
колеса маркируют клеймом потребителя.
8. Методы контроля
8.1. Внешний вид
колес контролируют визуально. Размеры и форму колес на соответствие требованиям
ГОСТ 9036 или согласованным чертежам проверяют универсальным мерительным
инструментом и контролируют калиброванными шаблонами по ГОСТ 8.010.
8.2. Отбор проб для
определения химического состава стали - по ГОСТ 7565. Определение массовой доли
химических элементов в стали - по ГОСТ 22536.0 - ГОСТ 22536.5, ГОСТ 22536.7 -
ГОСТ 22536.9, ГОСТ 22536.12, ГОСТ 17745, ГОСТ 18895, ГОСТ 28033.
Химический состав
стали допускается определять другими методами, не уступающими по точности
вышеуказанным.
8.3. Испытания на
растяжение стали ободьев колес проводят по ГОСТ 1497 на образцах диаметром 15
мм с расчетной длиной 60 мм и диаметром 10 мм с расчетной длиной 50 мм. Место
вырезки образцов показано на рисунке 1.
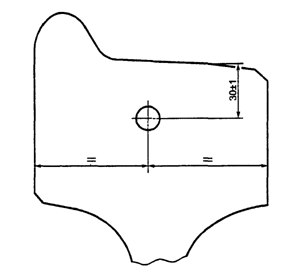
Рисунок 1. Место
вырезки образца на растяжение
из обода колеса
Испытания на
растяжение стали дисков колес проводят по ГОСТ 1497 на образцах диаметром 10 мм
расчетной длиной 50 мм. Место вырезки образцов показано на рисунке 2.
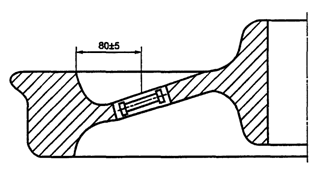
Рисунок 2. Место
вырезки образца на растяжение
из диска колеса
8.4. Твердость
ободьев колес измеряют по ГОСТ 9012 шариком диаметром 10 мм при усилии 29430 Н
(3000 кгс); на поперечном темплете обода проводят
четыре измерения в точках 1, 2, 3 и А, как показано на
рисунке 3.
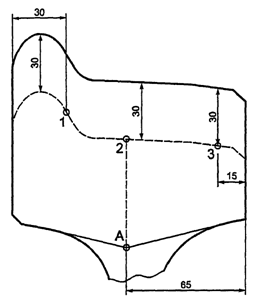
Рисунок 3.
Точки измерения твердости обода колеса
8.5. Равномерность
твердости по периметру обода колеса определяют по ГОСТ 9012 на четырех
поперечных темплетах, вырезанных равномерно по
окружности обода.
За твердость колеса
принимают среднее значение твердости в точках 1 - 3, показанных на рисунке 3.
8.6. Ударную
вязкость колес определяют:
- при температуре
плюс (20 +/- 10) °С - по ГОСТ
9454 на образцах типа 1 для диска и типа 8 - для обода по среднему значению,
полученному в результате испытания трех образцов;
- при температуре
минус (60 +/- 10) °С - на
образцах размером 10 х 10 х 55 мм с надрезом радиусом 5 мм и глубиной 2 мм по
минимальному значению результатов испытаний трех образцов.
Отбор проб для
определения ударной вязкости - по ГОСТ 7564. Положение образцов на
перпендикулярном сечении обода показано на рисунке 4.
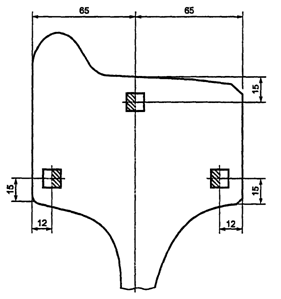
Рисунок 4. Место
вырезки образцов для определения
ударной вязкости
обода
Образцы вырезают из диска в месте перехода диска в ступицу в радиальном направлении
в соответствии с рисунком 5.
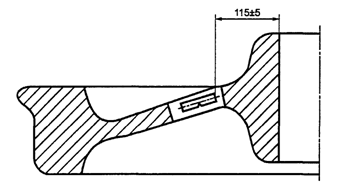
Рисунок 5. Место
вырезки образца для определения ударной
вязкости из диска в
месте перехода в ступицу
Допускается
вырезать образцы из диска в месте перехода его в обод.
8.7. Отбор проб и
изготовление образцов для контроля макроструктуры - по ГОСТ 10243. Оценку
макроструктуры колес проводят после травления темплетов.
Допускается проводить оценку макроструктуры по Бауману.
Проверку
макроструктуры стали колес проводят по нормативно-технической документации,
согласованной с потребителем.
8.8. Ультразвуковой
контроль ободьев колес проводят в двух направлениях (радиальном и осевом). Зоны
цельнокатаных колес, которые должны подвергаться ультразвуковому контролю, а
также типы и размеры эталонных отражателей и стандартных образцов
регламентируют в нормативно-технической документации, согласованной с
потребителем.
8.9. Неразрушающий контроль поверхности колес магнитопорошковым, вихретоковым либо другими методами проводят по
нормативно-технической документации, согласованной с потребителем.
8.10. Контроль
загрязненности стали колес неметаллическими включениями проводят по ГОСТ 1778
(метод Ш1) по среднему баллу отдельно по каждому виду
включений. Контроль проводят на шести шлифах, отобранных из двух радиальных
поперечных сечений обода в соответствии с рисунком 6. Площадь каждого шлифа -
не менее 200 мм2, расстояние центров шлифов от
поверхности катания и друг от друга должно соответствовать показанным на
рисунке 6 с предельным отклонением +/- 5 мм.

Рисунок 6.
Расположение шлифов по отношению
к поверхности
катания
8.11. Контроль
напряженного состояния колеса проводят методом разрезки. Для этого наносят две
метки на сторону обода, противоположную гребню, на середине толщины обода на
расстоянии 100 мм друг от друга. Радиальный разрез должен быть произведен
посредине между двумя метками в направлении от гребня к
отверстию в ступице. Ширина реза должна быть не менее 5 мм. Допускается
огневая резка колеса.
8.12. Упрочнение
дисков колес обработкой дробью с последующим нанесением антикоррозионной защиты
проводят по нормативно-технической документации, согласованной с потребителем.
9.
Транспортирование и хранение
9.1. Каждую партию
колес сопровождают документом, удостоверяющим ее соответствие требованиям
настоящего стандарта, подписанным отделом технического контроля
предприятия-изготовителя, представителем потребителя и содержащим:
- наименование
предприятия-изготовителя;
- марку стали
колеса;
- номинальный
диаметр отверстия ступицы;
- число колес;
- номера колес;
- номера плавок;
- дату отгрузки;
- обозначение
настоящего стандарта.
Погрузка колес из
стали разных марок в одно транспортное средство не допускается. Отгрузка колес
без документа о качестве не допускается.
9.2. Колеса
транспортируют в соответствии с правилами перевозки грузов, действующими на
конкретном виде транспорта.
9.3. Погрузку и
крепление колес на транспортных средствах производят в соответствии с ТУ на
погрузку и крепление конкретных грузов.
9.4. Условия
транспортирования и хранения колес в части воздействия климатических факторов -
по группе 8 (ОЖЗ) ГОСТ 15150.
10.
Указания по эксплуатации
10.1. Эксплуатация
колес - в соответствии с нормами, утвержденными для магистральных железных
дорог.
11.
Гарантии изготовителя
11.1. Изготовитель
гарантирует соответствие колес требованиям настоящего стандарта при соблюдении
условий эксплуатации, хранения, транспортирования и монтажа. Изготовитель
гарантирует качество стали (см. 4.5 - 4.7) и поверхности колес (см. 4.9, 4.10)
на весь срок службы со дня получения колес потребителем.
11.2. Гарантии
изготовителя не распространяются на колеса, подвергнутые: сварке; наплавке;
лазерной обработке; нагреву газовой горелкой, плазмой, токами высокой частоты
или иным способом; металлизации; нанесению электролитических или химических
покрытий при ремонте и техническом обслуживании колесных пар у потребителя.
Приложение А
(рекомендуемое)
ИСО
1005-6-94 ПОДВИЖНОЙ СОСТАВ ЖЕЛЕЗНЫХ ДОРОГ
ЧАСТЬ 6
БЕЗБАНДАЖНЫЕ КОЛЕСА
ДЛЯ ПОДВИЖНОГО СОСТАВА.
ТЕХНИЧЕСКИЕ УСЛОВИЯ
ПОСТАВКИ
1.
Назначение и область применения
1.1. Настоящий
стандарт устанавливает требования к изготовлению и поставке катаных, кованых
или литых безбандажных колес из нелегированной стали для локомотивов и вагонов
подвижного состава (таблица А.1 и раздел 4).
Примечание.
Создание международного стандарта на материал, испытания и требования к
размерам компонентов колесной пары и собранной колесной пары затруднено из-за
коммерческих и эксплуатационных различий путей в развитии железных дорог в
разных странах мира. Эти различия касаются, например, железнодорожных систем, в
которых грузовое движение объединено с интенсивным и, возможно,
высокоскоростным пассажирским движением или системами, целиком предназначенными
для перевозки грузов. Инфраструктура систем обычно различна, и это, как и
промышленная политика, может определять практику, принятую в разработке
колесных пар в разделах материалов и геометрических характеристик.
Таблица А.1
Марки,
химический состав, виды термической обработки
в состоянии
поставки и механические свойства стали
┌──────────────────────────────────┬─────────────────────────────────────────┬─────┬─────┬──────────────────────────────────────────┬───────────────────────┐
│ Обозначение марки стали │
Химический состав по данным анализа
│Вид │Ка- │ Механические свойства, определяемые │
Другие механические │
│ │ ковшевой пробы разливаемого металла │тер- │тего-│
испытанием образцов на растяжение
│ свойства │
│ │ (готового изделия) <1>, %, max │ми- │рия │ <4> │ │
├────────────────┬─────────────────┼──────┬──────┬──────┬───────┬───────┬────┤чес- │по
├────────────────────────┬─────────────────┼─────┬─────┬─────┬─────┤
│для
катаных или │ для литых колес │ C
│ Si
│ Mn
│ P │
S │дру-│кой │испы-│ 1 (рисунок А.4) │ 2 (рисунок А.4) │ра- │твер-│пос-
│оста-│
│
кованых колес │ │ max │ max│ max│ max │ max │гие │обра-│тани-│ │ │бота │дость│ледо-│точ-
│
├─────────┬──────┼──────────┬──────┤ │ │ │
<5> │ <5>
│ │бот- │ям
├──────┬──────┬──────────┼─────┬───────────┤уда-
│обода│ва- │ные │
│ новое
│ста-
│ новое │ста-
│ │ │ │ │ │ │ки │<3> │R
│R , │А <7> min │R ,
│А <7> min │ра, │<9>, │тель-│нап- │
│ <10>
│рое
│ <10> │рое
│ │ │ │ │ │ │<2> │
│ eH
│ m │ │ m │ │KU │НВ
│ные
│ряже-│
│ │<11> │ │<11> │
│ │ │ │ │ │
│ │или │Н/мм2
├─────┬────┤max,
├──────┬────┤<8>,
│ │зна- │ния │
│ │ │ │ │ │ │ │ │ │
│ │ │R
,│ │кова-│ли-
│Н/мм2│ко- │ли-
│min, │ │чения│ │
│ │ │ │ │ │ │ │ │ │
│ │ │ p0,2 │ │ные,
│тые,│
│ва- │тые,│Дж
│ │твер-│
│
│ │ │ │ │ │ │ │ │ │ │
│ │Н/мм2 │
│% │% │
│ные, %│% │
│ │дости│
│
├─────────┼──────┼──────────┼──────┼──────┼──────┼──────┼───────┼───────┼────┼─────┼─────┼──────┼──────┼─────┼────┼─────┼──────┼────┼─────┼─────┼─────┼─────┤
│C44GW-N-A│R1-N │GC44GW-N-A│RC1-N
│0,46 │0,40 │0,90
│0,040 │0,040 │<13>│N │A
│<12> │600 -
│18 │9 │-
│- │- │15
│- │- │-
│
│ │ │ │ │(0,48)│(0,43)│(0,95)│(0,045)│(0,045)│ │
│ │
│ 720│ │
│ │ │
│ │ │
│ │
├─────────┼──────┼──────────┼──────┤ │ │ │ │ │ │
├─────┼──────┼──────┼─────┼────┼─────┼──────┼────┼─────┼─────┼─────┼─────┤
│C44GW-N-B│- │GC44GW-N-B│- │ │ │ │ │ │ │
│B │- │- │-
│- │- │-
│- │- │166 -│- │-
│
│ │ │ │ │ │ │ │ │ │
│ │ │ │ │ │
│ │ │
│ │ 217│
│ │
├─────────┼──────┼──────────┼──────┤ │ │ │ │ │
├─────┼─────┼──────┼──────┼─────┼────┼─────┼──────┼────┼─────┼─────┼─────┼─────┤
│C44GW-T-A│R6-T │GC44GW-T-A│RC6-T │ │ │ │ │ │
│T │A │<12> │770 - │15 │8
│<15> │16
│9 │15 │-
│<16> │<17> │
│ │ │ │ │ │ │ │ │ │
│<14> │
│ │ 890│ │
│ │ │
│ │ │
│ │
├─────────┼──────┼──────────┼──────┤ │ │ │ │ │ │
├─────┼──────┼──────┼─────┼────┼─────┼──────┼────┼─────┼─────┼─────┼─────┤
│C44GW-T-B│- │GC44GW-T-B│- │ │ │ │ │ │ │
│B │- │- │-
│- │- │-
│- │- │197 -│- │-
│
│ │ │ │ │ │ │ │ │ │
│ │ │ │ │ │
│ │ │
│ │ 277│
│ │
├─────────┼──────┼──────────┼──────┼──────┼──────┼──────┼───────┼───────┼────┼─────┼─────┼──────┼──────┼─────┼────┼─────┼──────┼────┼─────┼─────┼─────┼─────┤
│C48GW-N-A│- │GC48GW-N-A│- │0,50 │0,40
│0,90 │0,040 │0,040
│<13>│N
│A │<12> │630 - │17 │8
│- │- │-
│14 │- │-
│- │
│ │ │ │ │(0,52)│(0,43)│(0,95)│(0,045)│(0,045)│ │
│ │ │
750│ │ │
│ │ │
│ │ │
│
├─────────┼──────┼──────────┼──────┤ │ │ │ │ │ │
├─────┼──────┼──────┼─────┼────┼─────┼──────┼────┼─────┼─────┼─────┼─────┤
│C48GW-N-B│- │GC48GW-N-B│- │ │ │ │ │ │ │
│B │- │- │-
│- │- │-
│- │- │174 -│- │-
│
│ │ │
│ │ │ │ │ │ │ │
│ │ │ │ │
│ │ │
│ │ 223│
│ │
├─────────┼──────┼──────────┼──────┤ │ │ │ │ │
├─────┼─────┼──────┼──────┼─────┼────┼─────┼──────┼────┼─────┼─────┼─────┼─────┤
│C48GW-T-A│R7-T │GC48GW-T-A│RC7-T │ │ │ │ │ │ │T
│A │<12> │820 - │14 │7
│<15> │16
│8 │15 │-
│<16> │<17> │
│ │ │ │ │ │ │ │
│ │ │<14> │ │ │
940│ │ │
│ │ │
│ │ │
│
├─────────┼──────┼──────────┼──────┤ │ │ │ │ │ │
├─────┼──────┼──────┼─────┼────┼─────┼──────┼────┼─────┼─────┼─────┼─────┤
│C48GW-T-B│- │GC48GW-T-B│- │ │ │ │ │ │ │
│B │- │- │-
│- │- │-
│- │- │235 -│- │-
│
│ │ │ │ │ │ │ │ │ │
│ │ │ │ │
│ │ │ │
│ │ 285│
│ │
├─────────┼──────┼──────────┼──────┼──────┼──────┼──────┼───────┼───────┼────┼─────┼─────┼──────┼──────┼─────┼────┼─────┼──────┼────┼─────┼─────┼─────┼─────┤
│C51GW-N-A│- │GC51GW-N-A│- │0,54 │0,40
│0,30 │0,040 │0,040
│<13>│N
│A │<12> │660 - │15 │7
│- │- │-
│12 │- │-
│- │
│ │ │ │ │(0,57)│(0,43)│(0,95)│(0,045)│(0,045)│ │
│ │ │
800│ │ │
│ │ │
│ │
│ │
├─────────┼──────┼──────────┼──────┤ │ │ │ │ │ │
├─────┼──────┼──────┼─────┼────┼─────┼──────┼────┼─────┼─────┼─────┼─────┤
│C51GW-N-B│- │GC51GW-N-B│- │ │ │ │ │ │
│ │B
│- │- │-
│- │- │-
│- │- │187 -│- │-
│
│ │ │ │ │ │ │ │ │ │
│ │ │ │ │ │
│ │ │
│ │ 241│
│ │
├─────────┼──────┼──────────┼──────┤ │ │ │ │ │
├─────┼─────┼──────┼──────┼─────┼────┼─────┼──────┼────┼─────┼─────┼─────┼─────┤
│C51GW-T-A│R8-T │GC51GW-T-A│RC8-T │ │ │ │ │ │ │T
│A │<12> │860 - │13 │6
│<15> │16
│7 │15 │-
│<16> │<17> │
│ │ │ │ │ │ │ │ │ │
│<14> │
│ │ 980│ │
│ │ │
│ │ │
│ │
├─────────┼──────┼──────────┼──────┤ │ │
│ │ │ │
├─────┼──────┼──────┼─────┼────┼─────┼──────┼────┼─────┼─────┼─────┼─────┤
│C51GW-T-B│- │GC51GW-T-B│- │ │ │ │ │ │ │
│B │- │- │-
│- │- │-
│- │- │248 -│- │-
│
│ │ │ │ │ │ │ │ │ │
│ │ │ │ │ │
│ │ │
│ │ 302│
│ │
├─────────┼──────┼──────────┼──────┼──────┼──────┼──────┼───────┼───────┼────┼─────┼─────┼──────┼──────┼─────┼────┼─────┼──────┼────┼─────┼─────┼─────┼─────┤
│C55GW-N-A│R2-N │GC55GW-N-A│RC2-N
│0,58 │0,40 │0,90
│0,040 │0,040 │<13>│N │A
│<12> │700 -
│14 │6 │-
│- │- │10
│- │- │-
│
│ │ │ │ │(0,61)│(0,43)│(0,95)│(0,045)│(0,045)│ │
│ │ │
840│ │ │
│ │ │
│ │ │
│
├─────────┼──────┼──────────┼──────┤ │ │ │ │ │ │
├─────┼──────┼──────┼─────┼────┼─────┼──────┼────┼─────┼─────┼─────┼─────┤
│C55GW-N-B│- │GC55GW-N-B│- │ │ │ │ │ │ │
│B │- │- │-
│- │- │-
│- │- │197 -│- │-
│
│ │ │ │ │ │ │ │ │ │
│ │ │ │ │ │
│ │ │
│ │ 255│
│ │
├─────────┼──────┼──────────┼──────┤ │ │ │ │ │
├─────┼─────┼──────┼──────┼─────┼────┼─────┼──────┼────┼─────┼─────┼─────┼─────┤
│C55GW-T-A│R9-T │GC55GW-T-A│RC9-T │ │ │ │ │ │ │T
│A │<12> │900 - │12 │5
│<15> │14
│6 │12 │-
│<16> │<17> │
│ │ │ │ │ │ │ │ │ │
│<14> │
│ │ 1050│
│ │
│ │ │
│ │ │
│
├─────────┼──────┼──────────┼──────┤ │ │ │ │ │ │
├─────┼──────┼──────┼─────┼────┼─────┼──────┼────┼─────┼─────┼─────┼─────┤
│C55GW-T-B│- │GC55GW-T-B│- │ │ │
│ │ │ │
│B │- │- │-
│- │- │-
│- │- │255 -│- │-
│
│ │ │ │ │ │ │ │ │ │
│ │ │ │ │ │
│ │ │
│ │ 311│ │
│
├─────────┼──────┼──────────┼──────┼──────┼──────┼──────┼───────┼───────┼────┼─────┼─────┼──────┼──────┼─────┼────┼─────┼──────┼────┼─────┼─────┼─────┼─────┤
│C64GW-N-A│R3-N │GC64GW-N-A│RC3-N
│0,67 │0,40 │0,90
│0,040 │0,040 │<13>│N │A │<12> │800 - │11 │5
│- │- │-
│10 │- │-
│- │
│ │ │ │ │(0,70)│(0,43)│(0,95)│(0,045)│(0,045)│ │
│ │ │
940│ │ │
│ │ │
│ │ │
│
├─────────┼──────┼──────────┼──────┤ │ │ │ │ │ │
├─────┼──────┼──────┼─────┼────┼─────┼──────┼────┼─────┼─────┼─────┼─────┤
│C64GW-N-B│- │GC64GW-N-B│- │ │ │ │ │ │ │
│B │- │- │-
│- │- │-
│- │-
│223 -│-
│- │
│ │ │ │ │ │ │ │ │ │
│ │ │ │ │ │
│ │ │
│ │ 285│
│ │
├─────────┼──────┼──────────┼──────┤ │ │ │ │ │
├─────┼─────┼──────┼──────┼─────┼────┼─────┼──────┼────┼─────┼─────┼─────┼─────┤
│C64GW-T-A│- │GC64GW-T-A│- │ │ │ │ │ │ │T
│A │<12> │940 - │11 │4
│<15> │12
│5 │10 │-
│<16> │<17> │
│ │ │ │ │ │ │ │ │ │ │<14> │ │ │
1140│ │ │
│ │ │
│ │ │
│
├─────────┼──────┼──────────┼──────┤ │ │ │ │ │ │
├─────┼──────┼──────┼─────┼────┼─────┼──────┼────┼─────┼─────┼─────┼─────┤
│C64GW-T-B│- │GC64GW-T-B│- │ │ │ │ │ │ │
│B │- │- │-
│- │- │-
│- │- │277 -│- │-
│
│ │ │ │ │ │ │ │ │ │ │
│ │ │ │ │
│ │ │
│ │ 341│
│ │
├─────────┼──────┼──────────┼──────┼──────┼──────┼──────┼───────┼───────┼────┼─────┼─────┼──────┼──────┼─────┼────┼─────┼──────┼────┼─────┼─────┼─────┼─────┤
│C74GW-N-A│- │GC74GW-N-A│- │0,77 │0,40
│0,90 │0,040 │0,040
│<13>│N
│A │<12> │830 - │9 │4
│- │- │-
│8 │- │-
│- │
│ │ │ │ │(0,80)│(0,43)│(0,95)│(0,045)│(0,045)│ │
│ │ │
1000│ │ │
│ │ │
│ │ │
│
├─────────┼──────┼──────────┼──────┤ │ │ │ │ │ │
├─────┼──────┼──────┼─────┼────┼─────┼──────┼────┼─────┼─────┼─────┼─────┤
│C74GW-N-B│- │GC74GW-N-B│- │ │ │ │ │ │ │
│B │- │- │-
│- │- │-
│- │- │235 -│- │-
│
│ │ │ │ │ │ │ │ │ │
│ │ │ │ │ │
│ │
│ │ │
311│ │ │
├─────────┼──────┼──────────┼──────┤ │ │ │ │ │
├─────┼─────┼──────┼──────┼─────┼────┼─────┼──────┼────┼─────┼─────┼─────┼─────┤
│C74GW-T-A│- │GC74GW-T-A│- │ │ │ │ │ │ │T
│A │<12> │1040 -│9 │3
│<15> │10
│4 │8 │-
│<16> │<17> │
│ │ │ │ │ │ │ │ │ │
│<14> │
│ │ 1240│ │
│ │ │
│ │ │
│ │
├─────────┼──────┼──────────┼──────┤ │ │ │ │ │ │
├─────┼──────┼──────┼─────┼────┼─────┼──────┼────┼─────┼─────┼─────┼─────┤
│C74GW-T-B│- │GC74GW-T-B│- │ │ │ │ │ │ │
│B │- │- │-
│- │- │-
│- │- │293 -│- │-
│
│ │ │ │ │ │ │ │ │ │
│ │ │ │ │ │
│ │ │
│ │ 363│
│ │
├─────────┴──────┴──────────┴──────┴──────┴──────┴──────┴───────┴───────┴────┴─────┴─────┴──────┴──────┴─────┴────┴─────┴──────┴────┴─────┴─────┴─────┴─────┤
│
<1> Если не оговорено иное, требования по
химическому составу
│
│следует
сопоставлять с анализом ковшевой пробы разливаемого
│
│металла.
Однако в спорных случаях решающим критерием должен │
│служить
химический состав материала готового изделия.
│
│
<2> Виды термической обработки:
│
│ N - нормализация или нормализация и
отпуск;
│
│ Т - закалка и отпуск обода (символ Т позднее может быть
│
│изменен). │
│
<3> См. примечание к 1.1 и таблицу
А.2.
│
│
<4> R - верхний предел
текучести;
│
│ eH │
│
│
│
R - условный предел текучести
0,2% (непропорциональное
│
│ p0,2
│
│удлинение);
│
│ R
- временное сопротивление;
│
│ m
│
│
│
│ А - относительное удлинение после разрыва
образца в
│
│ __
│
│процентах
(L = 5,65 \/S ).
│
│ 0 0
│
│
│
│
<5> В случае нормализации (N) или закалки
и отпуска обода (Т)
│
│колес
при запросе и заказе может быть оговорено максимальное
│
│содержание
серы и фосфора 0,035% по анализу материала готового
│
│изделия (и максимальное содержание 0,030% по
анализу ковшевой
│
│пробы
разливаемого металла).
│
│
В случае стали, изготовляемой кислым
процессом, по
│
│соглашению
при запросе и заказе, допускается максимальное │
│содержание
фосфора и серы 0,055% по анализу материала готового
│
│изделия (и максимальное содержание 0,050% по
анализу ковшевой
│
│пробы
разливаемого металла).
│
│ <6> Если
измеренное значение временного сопротивления при
│
│полном
удлинении 0,5% R не превышает 600
Н/мм2, допускается │
│ p0,5
│
│приводить
значение R вместо R или R
.
│
│ p0,5 eH p0,2
│
│
<7> Низкие значения удлинения литых колес категории А требуют
│
│"низконапряженной" конструкции (с искривленным диском),
если
│
│такие
колеса будут подвергаться значительному или
жесткому
│
│торможению
на гребень.
│
│
<8> KU - среднее значение из трех испытаний образцов с │
│U-образным
надрезом по ИСО-83 при комнатной температуре
│
│(23
+/- 5) °С. К отдельным результатам применяются требования
│
│ИСО
404.
│
│
<9> Различия между наибольшим и наименьшим значениями
│
│твердости
обода колес одной партии не должны превышать
│
│приведенных
значений. Однородность твердости по ободу должна быть
│
│30
НВ.
│
│
<10> Первая часть нового обозначения находится в соответствии
│
│с
системой обозначения марок стали, описанной в ИСО/TR 4949.
│
│Символы
в обозначении марки стали имеют следующие значения:
│
│
│
│ G C 44 GW
│
│ │ │ │ │
│
│ Литая сталь ──┘ │ │ │
│
│ Углеродистая сталь
──┘
│ │
│
│ Среднее содержание углерода при разливке
──┘ │ │
│ Марка для колес
─────────────────────────────────┘
│
│ │
│ Символ после первого дефиса обозначает вид термической
│
│обработки.
Символ Т (treat hardened - обработанные закалкой) в
│
│будущем
будет резервирован за отпущенными (tempered).
Если это
│
│будет
вести к недоразумениям, Т следует заменять на ТМ или TR
│
│(R для "rim quenched and tempered"
- "с закалкой и отпуском
│
│обода").
│
│ Символы после второго дефиса обозначают
категорию по
│
│испытаниям. │
│
<11> "Старые" означает наименования в соответствии с
│
│ИСО
1005-6-82.
│
│
<12> Приводить для целей
документирования. │
│
<13> Cr 0,30% (0,28%);
│
│ Cu 0,30%
(0,28%);
│
│ Мо 0,08% (0,08%); │
│ Ni 0,30%
(0,28%);
│
│ V
0,05% (0,05%).
│
│
<14> В особых случаях, если оговорена
поставка колес с │
│объемной
закалкой (Е), следует использовать значения временного
│
│сопротивления,
ударной вязкости и твердости, указанные в
│
│настоящей
таблице для вида термической обработки Т. Однако
для
│
│колес
особой конструкции допустимо согласование более низких
│
│значений
временного сопротивления и твердости обода при запросе и │
│заказе.
│
│
<15> Значение временного сопротивления при растяжении
│
│образцов
из диска должно быть ниже, чем значение временного │
│сопротивления
при растяжении образцов из обода, по меньшей мере,
│
│на:
100 Н/мм2 для C44GW и C51GW; 70 Н/мм2 для C55GW; 50
Н/мм2 для
│
│C64GW
и C74GW.
│
│
<16> Глубина эффекта закалки обода, оцененная по результатам
│
│испытаний
твердости (см. 7.7.3.4), должна быть не менее полной │
│глубины
износа. Заказ или прилагаемые к нему документы могут
│
│также
указывать минимальную твердость на границе глубины износа.
│
│
<17> Целью закалки и отпуска обода, в частности, является │
│создание
благоприятных остаточных сжимающих напряжений по
│
│окружности
обода колеса. Изготовитель должен показать, что
│
│технология
закалки обода и отпуска проявляется в соответствующем
│
│значении остаточного сжатия по окружности: один из
методов
│
│описан
в 7.8.2.4.
│
└───────────────────────────────────────────────────────────────────────────────────────────────────────────────────────────────────────────────────────────┘
Настоящий стандарт
серии ИСО 1005-6 составлен с учетом этих различий и предусматривает как две
категории А и В материала в части требований к
качеству, так и две категории в части допусков по размерам Y и Z.
Наиболее очевидные
различия между категориями материала А и В состоят в
том, что механические характеристики указывают:
- для категории А - по результатам испытаний на растяжение и ударный изгиб;
- для категории В - по результатам испытаний твердости.
Различия между
значениями категорий допусков на размеры Y и Z указывают:
- для цельнолитых
колес - по ИСО 1005-8;
- для колесных пар
- по ИСО 1005-7.
Следует отметить,
что:
- комбинацию
категории по испытаниям А с категорией допусков Y
обычно применяют на железнодорожных системах с преимущественно интенсивным или
высокоскоростным пассажирским движением;
- комбинацию
категории по испытаниям В с категорией допусков Z
обычно применяют на железнодорожных системах с преимущественно грузовым
движением;
- окончательная
комбинация категорий - по усмотрению заказчика.
1.2. В дополнение к
настоящему стандарту применимы требования ИСО 404.
2.
Нормативные ссылки
Требования
приведенных ниже стандартов, на которые имеются ссылки в тексте, включены в
требования стандарта ИСО 1005-6. При пересмотре указанных ниже стандартов
стороны, участвующие в соглашениях, оказывают поддержку в исследовании
возможности применения их самых последних изданий. Члены МЭК и ИСО имеют
реестры действующих в настоящее время международных стандартов.
В настоящем
стандарте применяют ссылки на следующие стандарты:
ИСО 83-76. Сталь.
Испытание на ударную прочность по Шарпи (образцы с U-образным надрезом)
ИСО 377-1-89. Отбор
и подготовка образцов и проб для испытаний деформированной стали. Часть 1.
Образцы и пробы для механических испытаний
ИСО 377-2-89. Отбор
и изготовление образцов и проб для испытаний деформируемой стали. Часть 2.
Образцы для определения химического состава
ИСО 404-92. Сталь и
заготовки стальные. Общие технические требования поставки
ИСО 1005-7-82.
Подвижной состав железных дорог. Часть 7. Колесные пары для тяговых и прицепных
вагонов. Технические условия поставки
ИСО 1005-8-86.
Подвижной состав железных дорог. Часть 8. Цельнолитые колеса для локомотивов и
вагонов. Требования к размерам и балансировке
ИСО 1580-94. Винты с шлицем в цилиндрической головке с закругленным торцем. Класс изделия А
ИСО 4032-86. Гайки
шестигранные типа 1. Классы изделия А и В
ИСО/TR 4949-89.
Обозначение сталей на основе буквенных символов
ИСО 4960-86. Полоса
холоднокатаная из углеродистой стали с содержанием углерода свыше 0,25%
ИСО 5948-94.
Подвижной состав железных дорог. Ультразвуковой приемочный контроль
ИСО 6506-81.
Материалы металлические. Испытание на твердость. Определение твердости по
Бринеллю
ИСО 6892-84.
Материалы металлические. Испытание на растяжение
ИСО 6933-86.
Подвижной состав железных дорог. Магнитопорошковый приемочный контроль
ИСО/TR 9769-91.
Сталь и чугун. Обзор существующих методов анализа
ИСО 10474-91. Сталь
и изделия стальные. Инспекционная документация.
3.
Информация, предоставляемая потребителем
Потребитель в
запросе и заказе приводит следующую информацию:
а) номер настоящего
стандарта;
b) марку стали (см.
4.1 и таблицу А.1);
c) вид термической
обработки (см. 4.2 и 6.5);
d) категорию по
испытаниям (см. 4.3 и 7.3.1);
e) размеры колеса
(см. 5.4);
f) степень чистоты
обработки и категорию допусков (см. 4.4 и 4.5).
Допускаются
варианты изготовления колес, поэтому заказчик в своем запросе и заказе может
указать необходимость:
g) поставки
колес в нормализованном или закаленном и отпущенном состоянии, пониженного
содержания фосфора и серы (см. таблицу А.1, Примечание 4);
h) измерения длины
окружности и нанесения соответствующей маркировки (см. 5.6 и 7.8.4);
i) специальной
маркировки (см. 5.6);
j) особой обработки
для литых колес (см. 6.2.2);
k) дробеструйной
обработки (см. 6.8);
l) проведения
дополнительных испытаний и проверок, указанных в таблице А.2, с предоставлением
следующей дополнительной информации:
- в случае
испытания на последовательные значения твердости - отличается ли глубина
предела износа от значения 35 мм (см. 7.7.3.4);
- в случае
испытаний на статический дисбаланс - следует ли внести в маркировку значение и
положение остаточного дисбаланса (см. 5.6) и, для колес вагонов, какой метод
устранения дисбаланса может быть применен, если он отличается от указанного в 6.6;
m) дополнительные
проверки размеров и, если требуется, число проверяемых колес (см. таблицу А.2,
Примечание 8);
n) иные, чем
указанные в 7.1.1, обязанности инспекции по контролю производства и инспекции
по контролю требований качества;
о) защита
от коррозии и, если требуется, какие методы следует применять (см. 8.1).
Примечание.
Конкретные разделы или пункты таблиц А.1 и А.2, оставляющие выбор между двумя и
более вариантами, должны быть открыты для соглашения по просьбе заказчика при
запросе или заказе (выделены курсивом).
Таблица А.2
Виды и
число испытаний и проверок
┌───┬───────────────────────────┬─────┬───────────────────────┬───────┬──────┬──────┬─────────┐
│Но-│ Испытания и контроль │Сим- │Обязательные (m) и до-
│Приме- │Испы- │Число │ Число │
│мер│ │волы,│полнительные (о) испы- │чания │туемая│колес
│испытаний│
│ис-│ │обоз-│тания и контроль для
│ │еди- │в каж-│ каждого │
│пы-│ │наче-│колес
с видами терми-
│ │ница │дой │
колеса │
│та-│ │ния │ческой
обработки <1> │ │<2> │испы-
│ │
│ния│ │
├───────────┬───────────┤ │ │туемой│ │
│ │ │ │Категория А│Категория
В│ │ │партии│ │
│ │ │
├─────┬─────┼─────┬─────┼───┬───┤ │ │ │
│ │ │ │
N │ Т
│ N │
Т
│<3>│<4>│ │ │ │
├───┼─────────┬─────────────────┼─────┼─────┼─────┼─────┼─────┼───┼───┼──────┼──────┼─────────┤
│1 │Химичес- │По данным
анализа│- │m │m
│m │m │-
│- │с │- │- │
│ │кий │ковшевой пробы │
│<5>
│<5> │<5> │<5> │
│ │ │ │ │
│ │анализ │разливаемого │
│ │ │
│ │ │
│ │ │ │
│ │(см. 5.1)│металла │ │
│ │ │
│ │ │
│ │ │
│ │
├─────────────────┼─────┼─────┼─────┼─────┼─────┼───┼───┼──────┼──────┼─────────┤
│ │ │По данным анализа│РА │о
│о
│о │о │а
│- │с │1 │1 │
│ │ │материала гото- │
│ │ │
│ │ │
│ │ │ │
│ │ │вого
изделия │ │
│ │ │
│ │ │
│ │ │
├───┼─────────┼─────────────────┼─────┼─────┼─────┼─────┼─────┼───┼───┼──────┼──────┼─────────┤
│2 │Механи- │Испытание на │-
│m │m │-
│- │b │h
│с, h │1 │1 │
│ │ческие │растяжение, обод │ │
│ │ │
│ │ │
│ │ │
├───┤испы-
├─────────────────┼─────┼─────┼─────┼─────┼─────┼───┼───┼──────┼──────┼─────────┤
│3 │тания │Испытание на │-
│- │m │-
│- │b │h
│с, h │1 │1 │
│ │ │растяжение, диск │ │
│<6> │ │
│ │ │
│ │ │
├───┤
├─────────────────┼─────┼─────┼─────┼─────┼─────┼───┼───┼──────┼──────┼─────────┤
│4 │ │Ударное испытание│- │m
│m │- │-
│b │h │с, h
│1 │3 │
│ │ │(KU) │ │
│ │ │
│ │ │
│ │ │
├───┤
├─────────────────┼─────┼─────┼─────┼─────┼─────┼───┼───┼──────┼──────┼─────────┤
│5 │ │Испытание твер- │RH
│- │- │m
│m
│а │h │с, h
│10% │1 │
│ │ │дости
обода │ │
│ │ │
│ │ │
│<7> │ │
├───┤
├─────────────────┼─────┼─────┼─────┼─────┼─────┼───┼───┼──────┼──────┼─────────┤
│6 │ │Испытание после- │HS │-
│о │- │-
│b │h │с, h
│1
│(7.7.3.4)│
│ │ │довательных
зна- │
│ │<6> │
│ │ │
│ │ │ │
│ │ │чений
твердости │ │
│ │ │
│ │ │
│ │ │
├───┤
├─────────────────┼─────┼─────┼─────┼─────┼─────┼───┼───┼──────┼──────┼─────────┤
│7 │ │Испытание на │RS
│- │m │-
│- │b │h
│с, h │1 │1 │
│ │ │остаточные │ │
│<6> │ │
│ │ │
│ │ │
│ │ │напряжения │ │
│ │ │
│ │ │
│ │ │
├───┤
├─────────────────┼─────┼─────┼─────┼─────┼─────┼───┼───┼──────┼──────┼─────────┤
│8 │ │Равномерность │-
│о │о │о │о
│а │h │c, h
│100% │- │
│ │ │твердости обода │
│ │ │
│ │ │
│ │ │ │
├───┼─────────┼─────────────────┼─────┼─────┼─────┼─────┼─────┼───┼───┼──────┼──────┼─────────┤
│9 │Внешний │Визуальный осмотр│- │m
│m │m │m
│а │- │W
│100% │1 │
├───┤вид
и
├─────────┬───────┼─────┼─────┼─────┼─────┼─────┼───┼───┼──────┼──────┼─────────┤
│10
│отсут-
│Магнито- │для ка-│MP&US│о
│о
│m │m │а
│- │W │100% │1 │
│ │ствие │порошко- │таных │ │
│ │ │
│ │ │
│ │ │
│ │дефектов │вый │или ко-│ │
│ │ │
│ │ │
│ │ │
│ │ │контроль │ваных │ │
│ │ │
│ │ │
│ │ │
│ │ │и ульт- │колес
│ │ │
│ │ │
│ │ │ │ │
│ │ │развуко-
├───────┤ │
│ │ │
├───┼───┼──────┼──────┼─────────┤
│ │ │вой кон-
│для │ │
│ │ │
│а │- │W
│100% │1 │
│ │ │троль │литых │
│ │ │
│ │ │
│ │ │ │
│ │ │ │колес │
│ │ │
│ │ │
│ │ │ │
├───┼─────────┴─────────┴───────┼─────┼─────┼─────┼─────┼─────┼───┼───┼──────┼──────┼─────────┤
│11
│Контроль размеров
│- │m │m
│m │m │а │f
│W │100% │1 │
│ │ │ │<8> │<8> │<8> │<8> │
│ │ │<8> │ │
├───┼───────────────────────────┼─────┼─────┼─────┼─────┼─────┼───┼───┼──────┼──────┼─────────┤
│12
│Испытание статической
│SB │о │о │о
│о │а │f
│W │100% │1 │
│ │балансировки │ │
│ │ │
│ │ │
│ │ │
├───┴───────────────────────────┴─────┴─────┴─────┴─────┴─────┴───┴───┴──────┴──────┴─────────┤
│
<1> N - нормализация или нормализация и отпуск;
│
│ Т - с закалкой и отпуском обода. │
│
<2> с - колеса той же плавки;
│
│ с, h - колеса той же плавки и того же
цикла термической
│
│обработки
(7.3.2); │
│ w - колесо является испытуемой
единицей.
│
│
<3> Если не оговорено иное (7.1),
проверки или испытания
│
│проводятся:
│
│ а) назначаемым контролем компетентного
отдела изготовителя
│
│(ИСО
404) или
│
│ b) в присутствии заказчика.
│
│
<4> h - испытания не должны проводиться до заказанной │
│термической
обработки;
│
│ f - приемные испытания проводят в
окончательном состоянии │
│поставки.
│
│
<5> Если не заказан анализ материала
готового изделия, │
│изготовитель
должен предоставить сертификат во время первого │
│предъявления
для контроля по результатам своего анализа │
│разливаемого
металла.
│
│
<6> В особых случаях, когда в
соответствии с таблицей А.1,
│
│сноска
13, оговорена поставка в состоянии объемной закалки и │
│отпуска
(Е), не требуются испытания на растяжение образцов, │
│взятых
из диска, испытание последовательных значений твердости и │
│испытания
по определению остаточных напряжений.
│
│
<7> Однако если число колес менее 20,
испытывают не менее двух │
│колес.
│
│
<8> Для некоторых размерных характеристик
измерения проводят в
│
│соответствии с ИСО 1005-8, таблицы 3 - 5 (дополнительно).
Если
│
│оговорены
проверки по этим характеристикам, также следует │
│оговорить
число испытуемых колес.
│
└─────────────────────────────────────────────────────────────────────────────────────────────┘
4. Классификация
Безбандажные колеса
классифицируют в соответствии с маркой стали, условиями термической обработки в
состоянии поставки, видами испытаний, степенью отделки, категорией допусков и
дополнительными требованиями (перечисления g) - о) раздела 3).
4.1. Марки
стали
Настоящий стандарт
регламентирует следующие марки стали в соответствии с требованиями,
приведенными в таблице А.1:
a) С - катаные или
кованые колеса;
b) GC - литые
колеса.
4.2. Виды
термической обработки в состоянии поставки
В зависимости от
заказа колеса поставляют:
a) с нормализацией
или с нормализацией и отпуском (символ N);
b) с закаленным и
отпущенным <*> ободом в соответствии с 6.5.2 (символ Т) <**>.
-------------------------------
<*> В
редакции ИСО 1005-6-82 для данного вида термообработки использовался термин
"поверхностная обработка". Термин "направленная закалка"
также часто используется для этого вида обработки.
<**> Символ Т может быть в дальнейшем изменен.
Кованые или катаные
колеса также могут поставляться необработанными
(обозначения нет). В этом случае механические свойства должны быть согласованы
при запросе и заказе.
Колеса могут также
поставляться с объемной закалкой и отпуском (символ Е).
4.3.
Категории по испытаниям
Колеса допускается
поставлять как соответствующие категориям А или В (см.
Примечание к 1.1 и таблицу А.2).
4.4.
Чистота обработки
Определения
терминов "необработанные", "с черновой механической
обработкой", "в полуготовом виде",
"в готовом виде", "готовые к сборке" - по ИСО 1005-8.
4.5.
Категории допусков
Категории допусков
- по ИСО 1005-8 и Примечанию к 1.1.
5. Технические требования
5.1.
Химический состав
5.1.1. Химический
состав колес должен соответствовать требованиям, установленным в таблице А.1.
5.1.2. При
отсутствии других соглашений между изготовителем и потребителем результаты
анализа материала изделий могут предусматривать их замену результатами анализа
ковшевой пробы разливаемого металла, соответствующими приведенным в таблице
А.1.
5.2. Механические
свойства
Механические
свойства колес должны соответствовать требованиям, установленным в таблице А.1.
5.3.
Внешний вид и отсутствие дефектов
5.3.1. Общие
требования
Структура колес
должна быть плотной; колеса не должны иметь дефектов, ухудшающих их
эксплуатационные свойства.
5.3.1.1.
Механически необработанные участки поверхности колеса должны плавно переходить в обработанные.
Чистота обработанных
поверхностей должна, если иное не указано в заказе, соответствовать ИСО 1005-8.
5.3.2.
Магнитопорошковый контроль
Проведение
магнитопорошкового приемочного контроля по ИСО 6933 (таблица А.2) и оценка
наличия нарушений однородности порошка магнитных частиц - по ИСО 6933, который
согласуют с потребителем при заказе. Следует учитывать расположение, форму,
размер, ориентацию и распределение неоднородностей, а также условия движения,
для которых предназначено колесо.
5.3.3.
Ультразвуковой контроль
Проведение
ультразвукового приемочного контроля (таблица А.2) - по ИСО 5948 (если иное не
согласовано при запросе и заказе).
5.4.
Припуски на механическую обработку и допуски на размеры
Припуски на
механическую обработку и допуски на размеры - по ИСО 1005-8.
5.5. Остаточный
дисбаланс
Результат проверки
остаточного дисбаланса (таблица А.2) должен удовлетворять требованиям ИСО
1005-8, значение дисбаланса маркируют в соответствии с 5.6.
5.6.
Маркировка
Каждое колесо
маркируют, как указано в заказе или в прилагаемых к нему документах.
При отсутствии
других указаний на каждом колесе маркируют:
a) фабричное клеймо
изготовителя;
b) номер плавки
либо номер партии, который может быть идентифицирован с конкретной плавкой;
c) марку стали и
вид термической обработки (см. 4.2), включая категорию по испытаниям и (или)
категорию допусков, если требуется;
d) дату
изготовления (месяц и две последние цифры года изготовления);
e) клеймо
контролера, если колесо принимают в соответствии с 7.9;
f) положение
дисбаланса, если следует провести проверку статического дисбаланса (таблица
А.2) и (если требуется) значение статического дисбаланса;
g) длину окружности
колеса, если ее требуется измерить (см. 7.8.4).
При отсутствии
других указаний маркировку наносят в соответствии с рисунками А.1 и А.2:
- знаки,
относящиеся к перечислениям а) - е), наносят штамповкой на наружную поверхность
ступицы, если иное не оговорено в заказе. Использовать клейма остроугольной
формы не допускается (см. 6.4);
- знаки,
соответствующие перечислениям а) - d) для литых колес, могут быть отлиты,
клеймо контролера наносят штамповкой на задней (т.е. внутренней) поверхности
диска.
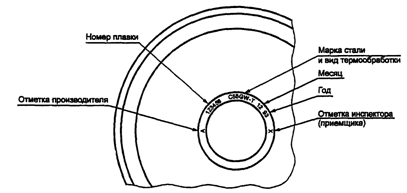
Рисунок
А.1. Пример маркировки катаных, кованых или литых
колес штамповкой
(см. 5.6)
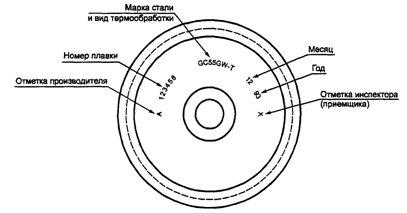
Рисунок
А.2. Пример альтернативной маркировки литых колес
отлитыми знаками
(см. 5.6)
Если при запросе и
заказе оговорены испытания на балансировку колес, положение дисбаланса отмечают
краской радиальной полосой шириной около 15 мм. В случае необходимости
допускается указывать значение дисбаланса в грамм-метрах
с нанесением цифр краской ниже этой полосы.
Если при заказе
оговорено измерение окружности колеса, размер окружности наносят краской на
диск знаками высотой не менее 25 мм.
Поверхность колеса
не маркируют в местах, не указанных в заказе или прилагающихся
к нему документах.
6. Производство
6.1. Процесс
выплавки стали
Колеса должны быть
изготовлены из стали, выплавленной кислородно-конвертерным, мартеновским или
электродуговым методами; другие процессы выплавки стали могут использоваться по
соглашению между изготовителем и потребителем.
Сталь должна быть раскислена в печи или ковше и разлита сифонным способом или
на машине непрерывной разливки.
6.2. Процесс
производства
6.2.1. Катаные или
кованые колеса
Катаные или кованые
колеса должны быть изготовлены из слитков или заготовок, из которых после
обрубки прибыльной части или концов могут быть изготовлены два и более колеса.
Специальные слитки для изготовления одного колеса могут быть использованы
только при условии предварительного согласия заказчика. Обрезка концов
заготовок и обрубка прибыльной части слитков должны обеспечить удаление
дефектных частей слитка (см. 6.3).
Заготовки колес
подвергают ковке, прошивке и черновому формоизменению на молоте или прессе. Они
должны быть подвергнуты окончательному формоизменению прокаткой или объемной
штамповкой, сопровождаемой дополнительной калибровкой (если необходимо).
При горячей
обработке металла должны быть приняты меры для предотвращения избыточного роста
зерна или других дефектов, вызванных перегревом.
Примечание. Для
указанной выше цели температура горячей обработки не должна быть слишком
высокой, а время выдержки при этой температуре слишком длительным. В целом
горячая обработка не должна проводиться при температуре свыше 1260 °С и должна заканчиваться при температуре 850 °С - 1000 °С.
После ковки или
прокатки и калибровки (если применяется) и нанесения идентификационной
маркировки колеса оставляют охлаждаться на воздухе. Если
сталь не подвергалась вакуумированию, следует принять
меры для предотвращения образования флокенов
(водородного растрескивания}, например, замедленное охлаждение.
6.2.2.
Литые колеса
Литые колеса
изготавливают отливкой металла в формы, позволяющие получить контур колеса в
соответствии с технологией, согласованной с заказчиком, с учетом требований ИСО
1005-8. Верхняя часть формы должна иметь прибыли для обратной подачи металла в
колесо при кристаллизации и получения бездефектной отливки.
Литые колеса должны
оставаться в форме до полного завершения процесса кристаллизации. При
последующей разборке формы применяют меры, гарантирующие, что колеса не будут
повреждены из-за слишком быстрого охлаждения. Если сталь не была подвергнута вакуумированию, принимают меры для предотвращения
образования флокенов (водородного растрескивания),
например, применяют замедленное охлаждение.
6.3.
Удаление дефектных участков
Дефектные участки,
не отвечающие требованиям 5.3, должны быть удалены перед изготовлением колес
или в процессе их изготовления.
6.4.
Идентификация колес в ходе производства
Каждая заготовка и
колесо должны иметь маркировку для их идентификации перед поставкой
потребителю, как указано в 5.6. Если предварительно нанесенная маркировка
отличается от окончательной маркировки по 5.6, ее глубина должна быть такой,
чтобы маркировка не была видна на готовом колесе.
6.5. Термическая
обработка
6.5.1. Колеса
должны пройти термическую обработку, предусмотренную в заказе или прилагаемых к
нему документах (см. 4.2).
6.5.2.
Колеса, обод которых должен быть подвергнут закалке и отпуску (Т) или объемной
закалке и отпуску (Е), должны быть равномерно нагреты до температуры,
уменьшающей величину зерна, после чего их ободья подвергают ускоренному
охлаждению. После закалки колеса помещают в печь для отпуска с последующим
охлаждением в контролируемых условиях.
6.6.
Механическая обработка и корректировка дисбаланса
Режим механической
обработки выбирают так, чтобы чистота поверхности колеса и допуски отвечали
требованиям 5.3 и ИСО 1005-8.
Если иное не
оговорено в заказе, корректировку дисбаланса допускается проводить стачиванием
центра галтели между диском и ободом со стороны реборды (рисунок А.3). Толщина
удаляемого металла не должна превышать 4 мм, а сточенная поверхность должна
плавно переходить в смежные поверхности и соответствовать требованиям к чистоте
поверхности по ИСО 1005-8.
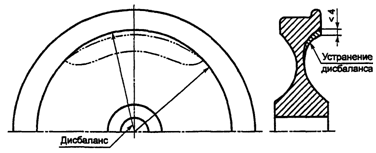
Рисунок А.3. Пример
корректировки дисбаланса
Крепление
дополнительных грузов при балансировке не допускается.
Сверление отверстий
для балансировки в колесах тяговых средств подвижного состава не допускается. В
случае сверления для балансировки колес прицепных средств подвижного состава
должно быть получено предварительное согласие заказчика.
6.7. Удаление
поверхностных дефектов
6.7.1. Допустимые
исправления
За исключением
участков, на которых удаление дефектов не допускается, поверхностные дефекты
колес могут быть удалены перед статической балансировкой и дробеструйной
обработкой вырубкой, обработкой резанием или мягкой шлифовкой при условии, что
при этом не образуются тепловые трещины и сохраняются допуски на размеры, а
обточенные поверхности плавно переходят в смежные поверхности. Если необходимо,
при помощи соответствующих средств (например, испытаний магнитопорошковым
методом) гарантируют, что дефект полностью устранен.
6.7.2. Недопустимые
исправления
Любая сварка,
обработка газовой горелкой, нагрев, электрический разряд, заполнение металлом
металлизации, электролитическое или химическое нанесение покрытий и т.п., а
также заделка с целью сокрытия дефектов поверхности являются недопустимыми и
колеса должны быть забракованы.
6.8.
Дробеструйная обработка
Поверхность диска
колеса подвергают дробеструйной обработке в соответствии с порядком, указанным
в Приложении Б. Дробеструйную обработку проводят после любого исправления
поверхности диска.
Наличие заметных
следов дробеструйной обработки на других поверхностях колеса, кроме диска, не
является причиной для забракования колеса.
7. Контроль
7.1.
Организация и тип контроля
7.1.1.
Соответствие колеса методам производства (раздел 6) и требованиям качества
(раздел 5) контролируют:
a) по поручению
заказчика - компетентный отдел изготовителя (см. примечание);
b) в
присутствии заказчика - представитель изготовителя или назначенный им орган.
Методы производства
контролирует компетентный отдел изготовителя, а требования качества должны
соответствовать графе 5 таблицы А.2.
Примечание. Термин
"компетентный отдел" означает здесь и далее отдел технического
контроля изготовителя, независимый от его производственных подразделений,
уполномоченных в соответствии с ИСО 10474 выпускать сертификаты контроля типа
3.1.В.
7.1.2. Передача
заказчиком права контроля компетентному отделу изготовителя не лишает заказчика
права отслеживать эффективность управления производством, а также методов
испытаний и контроля.
В этом случае
заказчику должна быть предоставлена возможность присутствовать при испытаниях,
проведение которых возложено на изготовителя, и контролировать полученные
результаты.
7.2. Контроль
производства
В случае, если контроль производства возложен на компетентный отдел
изготовителя или заказчика, контроль проводят в следующем порядке.
7.2.1. Изготовитель информирует заказчика об основном технологическом
процессе, который будет использован при выполнении заказа, о любых дальнейших
существенных изменениях, которые он намерен осуществить и которые могут
повлиять на качество колес, и получает предварительное согласие заказчика на
эти изменения.
Если контроль
остается возложенным на заказчика, его представителю должна быть предоставлена
возможность контролировать процессы производства с целью гарантировать
выполнение требований настоящего стандарта и заказа.
7.2.2. При
предъявлении колес к приемке изготовитель обязан удостоверить соответствие
требований к производству настоящего стандарта (см. 7.5).
7.3. Контроль
характеристик колес
7.3.1.
Категории и виды испытаний
Настоящий стандарт
устанавливает категории испытаний А и В.
Виды испытаний,
входящие в эти категории, а также являются ли эти испытания обязательными или
дополнительными - по таблице А.2.
7.3.2.
Испытуемые единицы
Для каждого вида
испытаний в графе "Испытуемая единица" таблицы А.2 указывают состав
испытуемой единицы для конкретного вида испытаний на основании производственных
характеристик колес.
Для конкретных
испытаний механических свойств каждую испытуемую партию формируют из колес,
изготовленных из одной плавки и прошедших одинаковую термическую обработку.
Допускается включать в партию колеса разного профиля. Для колес, подвергнутых
испытаниям по категории А, все колеса испытуемой
партии для испытания механических свойств должны быть одного номинального
диаметра и сечения обода. Для колес, подвергнутых испытаниям по категории В, испытуемая партия может содержать колеса разных
номинальных диаметров и сечений обода, при условии, что будет проведено не
менее одного испытания на твердость не менее одного колеса от каждого
номинального диаметра и сечения обода.
7.3.3. Состояние
колес, предъявляемых для контроля
Состояние колес при
предъявлении для контроля должно соответствовать требованиям графы
"Примечание" таблицы А.2.
7.4. Предъявление
колес для контроля заказчику
7.4.1 Заказчик, его
представитель или назначенный им орган (см. 7.1.1, перечисление b) должны быть
своевременно письменно уведомлены (см. 7.5.2) о дате предъявления колес для
контроля с указанием номера заказа и числа колес в каждой испытуемой партии,
сформированной для испытания механических свойств.
7.4.2. Если
контроль, который должен быть проведен после механической обработки в
соответствии с таблицей А.2 (см. графу 6 (Примечания 2 и 3)), возложен на
заказчика (см. 7.1.1; перечисление b), то изготовитель может предъявить колеса
для контроля на двух стадиях обработки:
a) после
окончательной термической обработки, но до механической обработки и
b) в окончательном
состоянии поставки.
7.5. Удостоверение
качества
7.5.1. Если
контроль производства возложен на компетентный отдел изготовителя или
заказчика, изготовитель должен удостоверить, что требования настоящего
стандарта к производству соблюдены. Документ о качестве после окончательных
испытаний должен также включать результаты:
- химического
анализа;
- испытаний на
растяжение (только по испытаниям категории А);
- испытаний на
ударный изгиб (только по испытаниям категории А);
- испытаний на
последовательное определение твердости, если требуются (только по испытаниям
категории А);
- испытаний
твердости обода для всех испытанных колес (только по испытаниям категории В);
- испытаний
твердости обода для всех испытанных колес, если требуются испытания на
равномерность твердости.
Кроме того,
документ о качестве должен включать указание на то, что результаты обязательных
испытаний и проверок и заказанных дополнительных испытаний (таблица А.2)
соответствуют требованиям настоящего стандарта.
7.5.2.
Изготовитель обязан предоставить протоколы возложенных на него испытаний и
проверок в следующие сроки:
а) к моменту
поставки, если на него возложена ответственность за проведение всех испытаний;
b) к моменту
предъявления для контроля, если колеса предъявляют для контроля заказчику, его
представителю или назначенному им органу в одну стадию;
c) к моменту
первого предъявления для контроля, если в соответствии с 7.4.2 колеса
предъявляют для контроля заказчику, его представителю или назначенному им
органу на двух стадиях обработки:
- для проведения
испытаний и проверок;
- после
окончательной термической обработки, но до механической обработки;
- к моменту
окончательного предъявления для контроля в иных случаях.
7.6. Число проверок
и испытаний
Число колес в
испытуемой партии, подвергаемой проверкам, и испытаний каждого колеса приведены
в графе "Число колес в каждой испытуемой партии" таблицы А.2 и 9.7.7.
7.7. Отбор и подготовка
образцов
7.7.1. Общие
требования
7.7.1.1. Если
испытывают не каждое колесо (графа "Число колес в каждой испытуемой
партии" таблицы А.2), контролер должен выбрать колесо (колеса),
предназначенное (предназначенные) для испытаний методом случайного отбора.
7.7.1.2.
При испытании остаточных напряжений испытание проводят до вырезания сегментов
колеса для других испытаний.
7.7.1.3. При отборе
образцов контролер обводит на каждом выбранном для испытаний колесе контур
сегмента, из которого будет вырезан (вырезаны) образец (образцы) (рисунок А.4).
7.7.1.4. Если в
заказе не оговорено иное, подготовка и идентификация проб и образцов для
испытаний должны проводиться в соответствии с требованиями ИСО 377-1 и ИСО
377-2.
7.7.1.5. На пробах
и образцах для испытаний должны быть сохранены идентификационная маркировка и
клейма контролера и (если иное не оговорено в заказе) могут быть изменены
только в присутствии заказчика.
7.7.2. Анализ
материала
При проведении
анализа материала изделия по выбору изготовителя и в соответствии с ИСО 377-2
пробы отбирают:
a) для колес по
испытаниям категории А - из одного колеса, выбранного
для механических испытаний;
1) из стружки,
отобранной из радиального сечения колеса, либо
2) из образца для
испытания на растяжение, взятого в положении 1, рисунок А.4;
b) из избытка
материала в области отверстия - для колес по испытаниям категории В.
В спорных случаях
следует руководствоваться пунктом 1 перечисления а).

-----------------------------------
<1> Положения
образцов для испытаний указывают относительно номинальной поверхности катания.
Рисунок
А.4. Положения образцов для испытаний на разрыв
и ударных испытаний
7.7.3. Механические
испытания
7.7.3.1. Испытание
на растяжение
От каждого
испытуемого колеса отбирают один образец, как показано на рисунке А.4,
положение 1.
Для колес,
подвергнутых закалке и отпуску обода (Т), отбирают еще один образец, как
показано на рисунке А.4, положение 2.
Образцы должны быть
подготовлены в соответствии с ИСО 6892, диаметр образца - не менее 10 мм;
расчетная длина - не менее пяти диаметров.
7.7.3.2. Ударное
испытание (U-образный надрез)
Из пробы вырезают
три образца в соответствии с рисунком А.4. Образцы для ударного испытания
должны иметь маркировку, позволяющую идентифицировать их поверхности,
параллельные оси АА (рисунок А.4). Подготовка образцов - в соответствии с
требованиями ИСО 83. Продольная ось цилиндрического основания надреза должна
быть параллельна оси АА (рисунок А.4).
7.7.3.3. Испытание
твердости и равномерности твердости обода
Колеса подвергают
испытанию на твердость по Бринеллю (таблица А.2) в соответствии с ИСО 6506 на
плоской поверхности обода со стороны, противоположной гребню. Место, выбранное
для испытания вдавливанием шариком, должно находиться на окружности, радиус
которой примерно на 25 мм меньше номинального диаметра поверхности катания
(рисунок А.5). Место для испытания должно быть подготовлено шлифовкой или вальцовкой
для удаления обезуглероженного слоя металла.
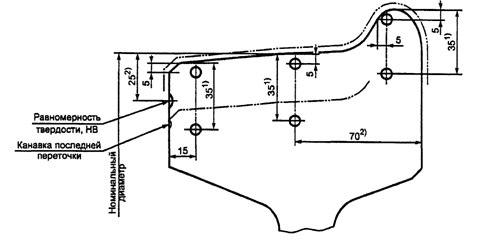
-----------------------------------
<1> В случаях полной глубины износа менее 35 мм вместо
расстояния 35 мм вдавливание следует осуществлять на границе износа.
<2> Если не определено иное.
Рисунок А.5.
Расположение отпечатков при измерении
твердости по
Бринеллю
7.7.3.4.
Испытание на последовательные значения твердости
Образец для
испытания на последовательные значения твердости должен представлять собой темплет полного радиального сечения обода и его перехода в
диск, отобранный из сегмента пробы (рисунок А.5). Одна из сторон темплета должна быть подготовлена в соответствии с ИСО
6506. Шесть отпечатков индектора должны находиться на
трех радиальных линиях, показанных на рисунке А.5.
7.7.3.5. Остаточные
напряжения
Остаточные
напряжения - по 7.7.1.2 и 7.8.2.4.
7.7.4. Проверка
внешнего вида и отсутствия дефектов
7.7.4.1.
Магнитопорошковый контроль
Контроль проводят
на целом колесе. Подготовка к испытанию - по ИСО 6933.
7.7.4.2.
Ультразвуковой контроль
Ультразвуковой
контроль проводят на колесе, подвергнутом определенному виду термической
обработки, указанной в заказе, с качеством обработки поверхности по ИСО 5948.
7.7.4.3.
Статический дисбаланс
Статический дисбаланс
контролируют на готовом колесе.
7.8. Методы
испытаний
7.8.1. Химический
анализ
Химический анализ
проводят в соответствии с методами, определенными в конкретных международных
стандартах (ИСО/TR 9769) или любыми иными методами, в том числе спектральными.
В спорных случаях следует использовать только методы, рекомендованные настоящим
стандартом.
7.8.2. Механические
испытания
7.8.2.1. Испытания
на растяжение
Испытания на
растяжение проводят в соответствии с требованиями ИСО 6892.
7.8.2.2. Ударные
испытания (с U-образным надрезом)
Ударные испытания
проводят в соответствии с требованиями ИСО 83.
7.8.2.3. Твердость
по Бринеллю
Определение
твердости по Бринеллю проводят в соответствии с требованиями ИСО 6506.
Определение
последовательных значений твердости проводят с использованием шарика
номинальным диаметром не более 5 мм.
7.8.2.4.
Проверка остаточных напряжений
Для проверки
остаточных напряжений наносят две отметки на расстоянии 100 мм друг от друга в
центре толщины обода на его плоской поверхности со стороны, противоположной
гребню; радиальный разрез делают от вершины гребня до отверстия ступицы на
середине расстояния между отметками.
Измеряют расстояние
между отметками; схождение отметок должно быть более 1 мм.
7.8.3. Проверка
внешнего вида и отсутствия дефектов
7.8.3.1. Визуальный
осмотр
Колеса перед
отгрузкой проверяют визуально.
7.8.3.2.
Магнитопорошковый контроль
Магнитопорошковый
контроль проводят в соответствии с ИСО 6933.
7.8.3.3.
Ультразвуковой контроль на отсутствие несплошностей
Ультразвуковой
контроль на отсутствие несплошностей проводят по ИСО
5948.
7.8.4.
Проверка размеров
Размеры колеса
должны соответствовать требованиям ИСО 1005-8. Размеры допускается проверять
калибрами (шаблонами). Измерение длины окружности вместо измерения диаметра
колеса должно быть согласовано при заказе.
7.8.5. Статический
баланс
Статический
дисбаланс колеса проверяют устройством, согласованным с заказчиком.
7.9.
Повторные испытания
Повторные испытания
проводят по ИСО 404, если в заказе не оговорено иное.
7.10. Заключение по
результатам контроля
Любые дефекты
внешнего вида, несоответствие размеров или балансировки ведут к отбраковке
колеса. То же относится к превышающим допустимые
дефектам, выявленным ультразвуковым или магнитопорошковым контролем.
Перед отгрузкой все
принятые колеса маркирует контролер после окончательной проверки. Клеймо
контролера должно находиться вблизи клейма изготовителя.
8. Поставка
8.1. Защита
от коррозии при транспортировании
Если указано в
заказе, после контроля и до отправки на хранение или потребителю, по крайней
мере, все окончательно механически обработанные части, кроме поверхности
катания принятых колес, должны быть защищены от коррозии методом, согласованным
с заказчиком.
Примечание.
Эффективность любого защитного покрытия сохраняется ограниченное время,
особенно в условиях транспортирования по морю и в географических районах с
высокой влажностью. Поэтому после транспортирования к месту назначения колеса
должны быть немедленно проверены для принятия решения о возобновлении защитного
покрытия (если требуется).
8.2. Защита от
механических повреждений при транспортировании
Перед отправкой
окончательно механически обработанные поверхности, особенно отверстия колес,
должны быть надежно защищены от механических повреждений.
Приложение Б
(рекомендуемое)
ПРОВЕДЕНИЕ
ДРОБЕСТРУЙНОЙ ОБРАБОТКИ
Б.1. Общая часть
Б.1.1.
Дробеструйную обработку поверхности диска проводят в соответствии с
требованиями Б.1.2 и Б.1.3.
Б.1.2. Используют
закаленную стальную дробь диаметром 1,40 мм или твердость более 90% дроби
должна быть от 40 до 50 HRC.
Б.1.3.
Дробеструйная машина должна быть оборудована сепаратором для непрерывного
удаления сломанной дроби. Новую дробь добавляют в количестве, достаточном для
обеспечения в машине не менее 85% дроби указанного выше или большего размера.
Б.2.
Интенсивность дробеструйной обработки
Интенсивность
дробеструйной обработки при измерении на испытательной пластине по Б.3 в
условиях, указанных в Б.4 - Б.7, должна быть достаточной для образования дуги
высотой не менее 0,20 мм.
Примечание.
Расположение испытательной пластины меняют в зависимости от конструкции диска.
Б.2.1. Стандартная
конструкция диска (рисунок Б.1)
Испытательную
пластину располагают на передней поверхности диска вблизи галтели ступицы и на
задней поверхности диска вблизи галтели обода.
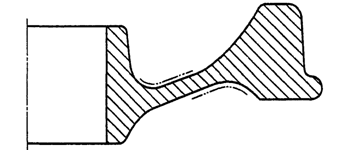
Рисунок Б.1.
Расположение испытательных пластин на передней
стороне диска
вблизи галтели ступицы и на задней стороне
диска вблизи
галтели обода при дробеструйной обработке
колес стандартной
конструкции
Б.2.2. Реверсная
конструкция диска (рисунок Б.2)
Испытательную
пластину располагают на передней поверхности диска вблизи галтели обода и на
задней поверхности диска вблизи галтели ступицы.
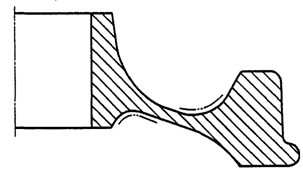
Рисунок Б.2.
Расположение испытательных пластин на задней
стороне диска вблизи
галтели ступицы и на передней стороне
диска вблизи
галтели обода при дробеструйной обработке
колес реверсной
конструкции
Б.3.
Испытательная пластина
Испытательная
пластина должна быть изготовлена из стали марки CS 70 по ИСО 4690, иметь
следующие размеры: толщину (2,4 +/- 0,02) мм, длину (75 +/- 0,4) мм, ширину
мм. Пластины должны быть равномерно закалены и
изотермически выдержаны между плоскими плитами в течение не менее 2 ч при
температуре (425 +/- 15) °С. Поверхность должна быть серо-голубой и
неполированной или ярко отожженной. Твердость пластин должна быть в диапазоне
от 450 до 520 HV, отклонение от плоскостности пластин - в пределах 0,025 мм.
Б.4.
Фиксация в держателях
Испытательную
пластину закрепляют в держателях в соответствии с рисунком Б.3.
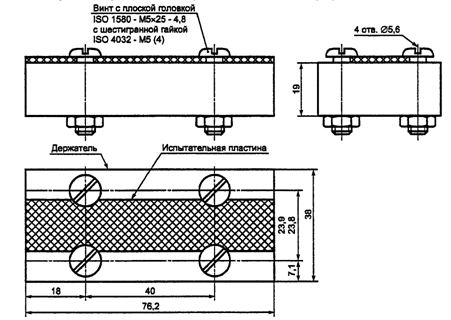
Рисунок Б.3.
Испытательная пластина и держатель в сборе
Б.5.
Расположение испытательных пластин на колесе
Держатели с
закрепленными в них испытательными пластинами располагают на колесах следующим
образом:
а) для стандартной
конструкции диска - на передней стороне диска вблизи галтели ступицы и на
задней стороне диска вблизи галтели обода;
б) для реверсной
конструкции диска - на передней стороне диска вблизи галтели обода и на задней
поверхности диска вблизи поверхности ступицы;
в) для других
конструкций диска - в местах, согласованных при запросе и заказе.
Б.6.
Продолжительность обработки
Минимальное время
дробеструйной обработки изделия и испытательной пластины должно быть
достаточным для обеспечения полного покрытия испытательной полосы.
Б.7.
Измерение высоты дуги
Измеритель для
определения кривизны испытательной пластины показан на рисунке Б.4.
Испытательную пластину помещают в приборе так, чтобы стержень индикатора
располагался напротив необработанной поверхности. Кривизну пластины в
миллиметрах определяют измерением высоты объединенных продольной и поперечной
хорд, т.е. измерением смещения центральной точки необработанной поверхности от
плоскости четырех поддерживающих шариков измерителя.
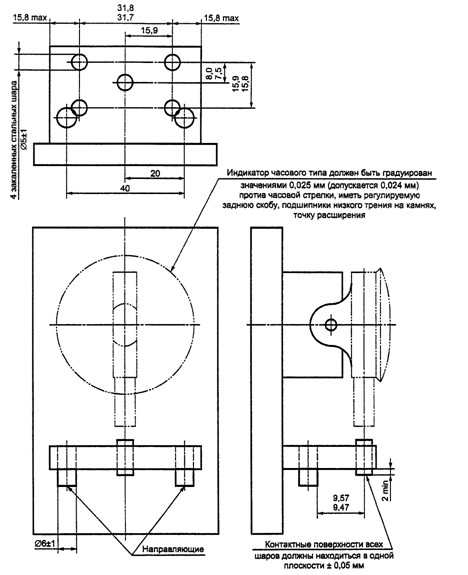
Рисунок Б.4.
Измеритель для определения кривизны
испытательной
пластины
Б.8. Периодичность
испытаний
Испытание должно
проводиться в начале и в конце каждого производственного цикла, но не реже чем
через каждые 8 ч работы.
Б.9. Повторные
испытания
Если в результате
испытания значение высоты дуги меньше 0,20 мм, проводят два повторных
испытания. По результатам двух повторных испытаний и первого испытания среднее
значение должно быть не менее 0,20 мм, установленных в Б.2.
Б.10. Повторная
дробеструйная обработка
Если результаты
испытаний не соответствуют требованиям Б.5, предпринимают меры для получения
удовлетворительных результатов испытаний до продолжения дальнейшей
дробеструйной обработки изделий. Если среднее значение высоты
дуги при неудовлетворительном испытании находится в пределах 0,16 - 0,19 мм,
вторая половина партии колес, обработанных сначала с неудовлетворительным
результатом испытаний, а затем с удовлетворительным, должна быть повторно
подвергнута дробеструйной обработке со временем выдержки не менее половины
времени первоначальной обработки. Если среднее значение высоты дуги
меньше 0,16 мм, все колеса, обработанные с момента последнего
удовлетворительного испытания, должны быть подвергнуты повторной дробеструйной
обработке с полной выдержкой.
|