Утвержден и
введен в действие
Распоряжением ОАО
"Газпром"
от 28 июня 2007 г.
N 171
ОТКРЫТОЕ АКЦИОНЕРНОЕ ОБЩЕСТВО "ГАЗПРОМ"
СТАНДАРТ ОРГАНИЗАЦИИ
ДОКУМЕНТЫ НОРМАТИВНЫЕ ДЛЯ ПРОЕКТИРОВАНИЯ,
СТРОИТЕЛЬСТВА И ЭКСПЛУАТАЦИИ ОБЪЕКТОВ ОАО
"ГАЗПРОМ"
ИНСТРУКЦИЯ
ПО ТЕХНОЛОГИЯМ СВАРКИ ПРИ СТРОИТЕЛЬСТВЕ И РЕМОНТЕ
ПРОМЫСЛОВЫХ И МАГИСТРАЛЬНЫХ ГАЗОПРОВОДОВ
ЧАСТЬ I
СТО Газпром 2-2.2-136-2007
Дата введения
22 сентября 2007
года
Предисловие
1. Разработан
Обществом с ограниченной ответственностью "Научно-исследовательский
институт природных газов и газовых технологий - ВНИИГАЗ" с участием
Управления по транспортировке, подземному хранению и использованию газа ОАО
"Газпром".
2. Внесен
Управлением по транспортировке газа и газового конденсата Департамента по
транспортировке, подземному хранению и использованию газа ОАО
"Газпром".
3. Утвержден и
введен в действие Распоряжением ОАО "Газпром" от 28 июня 2007 г. N
171 с 22 сентября 2007 г.
4. Взамен ВСН
006-89 "Строительство магистральных и промысловых трубопроводов.
Сварка" в части требований раздела 2 "Электродуговая сварка
магистральных и промысловых трубопроводов" (пп. 2.1 - 2.10) и приложений
1, 2, 4;
СП 105-34-96
"Свод правил сооружения магистральных газопроводов. Производство сварочных
работ и контроль качества сварных соединений".
Введение
Настоящий стандарт
разработан с целью установления требований к сварным соединениям, порядку
выполнения сборочно-сварочных работ, применению сварочных материалов и
сварочного оборудования при строительстве, реконструкции и капитальном ремонте
промысловых и магистральных газопроводов.
В разработке
настоящего стандарта участвовал авторский коллектив: В.В. Харионовский, В.И.
Беспалов, Д.Г. Будревич, С.А. Курланов, Т.В. Артеменко, Т.Л. Лучина (ООО
"ВНИИГАЗ"), В.В. Салюков, Е.М. Вышемирский, А.В. Шипилов (ОАО
"Газпром"), С.В. Головин, Н.Г. Блехерова, В.А. Данильсон, В.В.
Прохоров (ООО "Институт-ВНИИСТ").
1. Область
применения
1.1.
Настоящий стандарт распространяется на сварку кольцевых соединений труб,
соединительных деталей трубопроводов, запорной и регулирующей арматуры при
строительстве, реконструкции и капитальном ремонте <*> промысловых и
магистральных газопроводов и конденсатопроводов <**>, изготовленных из
сталей с нормативным значением временного сопротивления на разрыв до 590 МПа
(60 кгс/мм2) включительно условным диаметром DN
от 20 до 1400 с толщиной стенки от 2,0 до 32,0
мм включительно, в т.ч.:
а) промысловых
газопроводов с рабочим давлением среды свыше 1,2 МПа до 9,8 МПа включительно, к
которым относятся:
1)
газопроводы-шлейфы от скважин до установок предварительной, комплексной
подготовки газа, газовые коллекторы, межпромысловые коллекторы от установок
предварительной, комплексной подготовки газа до головных сооружений, дожимных
компрессорных станций, компрессорных станций, газоперерабатывающих заводов;
2)
газопроводы технологической обвязки установок предварительной, комплексной
подготовки газа, компрессорных станций, узлов редуцирования газа,
газоизмерительных станций;
б) магистральных
газопроводов с рабочим давлением среды свыше 1,2 МПа до 8,3 МПа, к которым
относятся:
1) линейная
часть с отводами, лупингами и перемычками, запорной и регулирующей арматурой,
переходами через естественные и искусственные препятствия, узлами пуска и
приема очистных устройств и дефектоскопов, узлами сбора и хранения конденсата,
устройствами для ввода метанола в газопровод;
2)
газопроводы технологической обвязки компрессорных станций с узлами подключения,
газораспределительных станций, подземных хранилищ газа, станций охлаждения
газа, узлов редуцирования газа, газоизмерительных станций.
--------------------------------
<*>
Разделка кромок труб должна соответствовать параметрам в соответствии с
требованиями технологии сварки.
<**>
В тексте стандарта, за исключением особых случаев, вместо терминов:
"промысловый(е) и магистральный(е) газопровод(ы) и
конденсатопровод(ы)" употребляется термин "газопровод(ы)".
1.2. Стандарт не
распространяется на сварку промысловых газопроводов с рабочим давлением среды
св. 9,8 МПа, магистральных газопроводов с рабочим давлением среды св. 8,3 МПа,
трубопроводов для транспортирования сероводородактивного газа, нефти и
нефтепродуктов.
1.3. Стандарт
устанавливает порядок выполнения сборочно-сварочных работ, применения сварочных
материалов и оборудования, а также требования к параметрам и свойствам сварных
соединений, технологиям сварки при строительстве промысловых и магистральных
газопроводов следующими дуговыми способами <***>:
- ручной дуговой
сваркой покрытыми электродами;
- ручной
аргонодуговой сваркой неплавящимся электродом;
- механизированной
сваркой плавящимся электродом в среде активных газов и смесях;
- механизированной
сваркой самозащитной порошковой проволокой;
- автоматической
сваркой плавящимся электродом в среде инертных газов и смесях;
- автоматической
сваркой плавящимся электродом в среде активных газов и смесях;
- автоматической
сваркой порошковой проволокой в среде инертных газов и смесях;
- автоматической
сваркой под флюсом.
--------------------------------
<***>
Автоматическая контактная сварка оплавлением и другие способы сварки могут
применяться по отдельным технологическим инструкциям, согласованным с ОАО
"Газпром" и разработчиком настоящего стандарта.
1.4. Положения
стандарта обязательны для применения структурными подразделениями, дочерними
обществами и организациями ОАО "Газпром", а также сторонними
организациями, выполняющими сварочные работы и технический надзор за качеством
работ при строительстве, реконструкции и капитальном ремонте промысловых и
магистральных газопроводов ОАО "Газпром".
1.5. При применении
настоящего стандарта в полном или частичном объеме в проектных, нормативных,
технологических и иных документах ссылки на стандарт обязательны.
2.
Нормативные ссылки
В настоящем
стандарте использованы нормативные ссылки на следующие стандарты:
ГОСТ 12.0.004-90.
ССБТ. Организация обучения безопасности труда. Общие положения
ГОСТ 12.1.019-79.
ССБТ. Электробезопасность. Общие требования и номенклатура видов защиты
ГОСТ 12.2.003-91.
ССБТ. Оборудование производственное. Общие требования безопасности
ГОСТ 2246-70.
Проволока стальная сварочная. Технические условия
ГОСТ 2601-84.
Сварка металлов. Термины и определения основных понятий
ГОСТ 6996-66.
Сварные соединения. Методы определения механических свойств
ГОСТ 8050-85.
Двуокись углерода газообразная и жидкая. Технические условия
ГОСТ 8732-78. Трубы
стальные бесшовные горячедеформированные. Сортамент
ГОСТ 8734-75. Трубы
стальные бесшовные холоднодеформированные. Сортамент
ГОСТ 9466-75.
Электроды покрытые металлические для ручной дуговой сварки сталей и наплавки.
Классификация и общие технические условия
ГОСТ 9467-75.
Электроды покрытые металлические для ручной дуговой сварки конструкционных и
теплоустойчивых сталей. Типы
ГОСТ 10157-79.
Аргон газообразный и жидкий. Технические условия
ГОСТ 14254-96.
Степени защиты, обеспечиваемые оболочками (Код IP)
ГОСТ 15150-69.
Машины, приборы и другие технические изделия. Исполнения для различных
климатических районов. Категории, условия эксплуатации, хранения и
транспортирования в части воздействия климатических факторов внешней среды.
ГОСТ 16037-80.
Соединения сварные стальных трубопроводов. Основные типы, конструктивные
элементы и размеры
ГОСТ 16504-81.
Система государственных испытаний продукции. Испытания и контроль качества
продукции. Основные термины и определения
ГОСТ 17516.1-90.
Изделия электротехнические. Общие требования в части стойкости к механическим
внешним воздействующим факторам
ГОСТ 19903-74.
Прокат листовой горячекатаный. Сортамент
ГОСТ 26271-84.
Проволока порошковая для дуговой сварки углеродистых и низколегированных
сталей. Общие технические условия
ГОСТ 28555-90.
Флюсы керамические для дуговой сварки углеродистых и низколегированных сталей.
Общие технические условия
ГОСТ Р 52222-04.
Флюсы сварочные плавленые для автоматической сварки
ГОСТ Р 52079-2003.
Трубы стальные для магистральных газопроводов, нефтепроводов и
нефтепродуктопроводов. Технические условия
СТО Газпром
14-2005. Типовая инструкция по проведению огневых работ на газовых объектах ОАО
"Газпром"
СТО Газпром
2-2.4-083-2006. Инструкция по неразрушающим методам контроля сварных соединений
при строительстве и ремонте промысловых и магистральных газопроводов
СТО Газпром
2-2.2-115-2007. Инструкция по сварке магистральных газопроводов с рабочим
давлением до 9,8 МПа включ.
Примечание. При
пользовании настоящим стандартом целесообразно проверить действие ссылочных
стандартов по соответствующему указателю, составленному на 1 января текущего
года, и информационным указателям, опубликованным в текущем году. Если
ссылочный документ заменен (изменен), то при пользовании настоящим стандартом
следует руководствоваться замененным (измененным) стандартом. Если ссылочный
документ отменен без замены, то положение, в котором дана ссылка на него,
применяется в части, не затрагивающей эту ссылку.
3. Термины,
определения и сокращения
3.1. В настоящем
стандарте применены термины в соответствии с ГОСТ 2601, ГОСТ 16504, ГОСТ Р
52079, а также следующие термины с соответствующими определениями:
3.1.1.
Автоматическая сварка: дуговая сварка, при которой возбуждение дуги, подача
сварочной проволоки и относительное перемещение дуги и свариваемых соединений
осуществляется автоматически, а установка, корректировка параметров режимов
сварки осуществляется оператором.
3.1.2.
Аттестованный сварочный материал: сварочный материал, прошедший аттестацию и
имеющий свидетельство об аттестации в соответствии с требованиями РД 03-613-03
[1].
3.1.3.
Аттестованное сварочное оборудование: сварочное оборудование, прошедшее
аттестацию и имеющее свидетельство об аттестации в соответствии с требованиями
РД 03-614-03 [2].
3.1.4.
Аттестованная технология сварки: технология сварки, прошедшая приемку в
конкретной производственной организации в соответствии с требованиями
настоящего стандарта и имеющая свидетельство о производственной аттестации в
соответствии с требованиями РД 03-615-03 [3].
3.1.5.
Аттестованный сварщик: квалифицированный сварщик, прошедший аттестацию в
соответствии с требованиями ПБ 03-273-99 [4], РД 03-495-02 [5] и имеющий
аттестационное удостоверение.
3.1.6.
Аттестационный центр: организация, являющаяся частью организационной структуры
системы аттестации сварочного производства и осуществляющая аттестацию
сварщиков и специалистов сварочного производства, сварочных материалов,
оборудования и технологий в соответствии с требованиями нормативных и
методических документов системы аттестации сварочного производства.
3.1.7. Газ
активный: защитный газ, вступающий в химическое взаимодействие с жидким
металлом в зоне сварки (например, углекислый газ).
3.1.8. Газ инертный:
защитный газ, не вступающий в химическое взаимодействие с жидким металлом в
зоне сварки (например, аргон, гелий).
3.1.9. Давление
рабочее (нормативное): наибольшее избыточное давление, при котором
обеспечивается заданный режим эксплуатации газопровода.
3.1.10. Горячий
проход: слой шва, выполняемый незамедлительно после сварки и зачистки корневого
слоя шва, при сварке которого температура металла корневого слоя шва не должна
опускаться ниже регламентированного значения.
3.1.11. Захлест:
стыковое кольцевое сварное соединение двух участков газопровода в месте
технологического разрыва, выполняемое без подварки изнутри корневого слоя шва.
┌─────────────────────────────────────────────────────────────────────────┐
│
3.1.12. Зазор: кратчайшее расстояние
между кромками собранных
для│
│сварки деталей.
│
│
[ГОСТ 2601-84, п. 104а]
│
└─────────────────────────────────────────────────────────────────────────┘
┌─────────────────────────────────────────────────────────────────────────┐
│
3.1.13. Зона термического влияния, ЗТВ: участок основного металла,
не│
│подвергшийся расплавлению, структура и свойства
которого изменились в│
│результате нагрева при сварке или
наплавке.
│
│
[ГОСТ 2601, п. 124]
│
└─────────────────────────────────────────────────────────────────────────┘
┌─────────────────────────────────────────────────────────────────────────┐
│
3.1.14. Импульсно-дуговая сварка:
дуговая сварка, при
которой│
│сварочная
дуга дополнительно питается
импульсами тока по
заданной│
│программе.
│
│ [ГОСТ
2601, п. 15]
│
└─────────────────────────────────────────────────────────────────────────┘
3.1.15. Катушка:
отрезок трубы, предназначенный для соединения двух участков газопровода либо
для сварки контрольных сварных соединений при производственной аттестации
технологий сварки, допускных испытаниях и аттестации сварщиков, операторов.
┌─────────────────────────────────────────────────────────────────────────┐
│
3.1.16. Класс прочности труб:
прочность металла труб,
оцениваемая│
│временным сопротивлением сигма и обозначаемая символами от К34 до
К60,│
│ в
│
│что соответствует нормативным значениям
сигма (кгс/мм2). │
│
в
│
│
[ГОСТ Р 52079-2003, п. 3.15]
│
└─────────────────────────────────────────────────────────────────────────┘
┌─────────────────────────────────────────────────────────────────────────┐
│
3.1.17. Корневой слой шва: часть сварного шва, наиболее удаленная от│
│его лицевой поверхности.
│
│
[ГОСТ 2601, п. 81] │
└─────────────────────────────────────────────────────────────────────────┘
3.1.18. Контрольное
сварное соединение, КСС: сварное соединение, выполняемое при аттестации
сварщиков, сварочных материалов, сварочного оборудования, технологий сварки,
допускных испытаниях сварщиков и являющееся однотипным по отношению к
производственным сварным соединениям газопроводов.
┌─────────────────────────────────────────────────────────────────────────┐
│
3.1.19. Металл шва: сплав, образованный расплавленным
основным и│
│наплавленным металлами или только
переплавленным основным металлом.
│
│
[ГОСТ 2601, п. 121]
│
└─────────────────────────────────────────────────────────────────────────┘
3.1.20.
Механизированная (полуавтоматическая) сварка: дуговая сварка, при которой
подача сварочной проволоки осуществляется автоматически, а установка,
корректировка параметров режимов сварки и перемещение сварочной горелки
осуществляются оператором.
3.1.21.
Национальная Ассоциация Контроля и Сварки, НАКС: организация, являющаяся частью
организационной структуры системы аттестации сварочного производства и
осуществляющая разработку нормативных и методических документов, методическое
руководство, контроль и координацию деятельности аттестационных центров по
аттестации сварщиков и специалистов сварочного производства, сварочных
материалов, оборудования и технологий, ведение реестра аттестационных центров и
результатов аттестаций.
┌─────────────────────────────────────────────────────────────────────────┐
│
3.1.22. Направление сварки: направление движения сварочной дуги
вдоль│
│продольной оси сварного соединения. │
│
[ГОСТ 2601, п. 94] │
└─────────────────────────────────────────────────────────────────────────┘
┌─────────────────────────────────────────────────────────────────────────┐
│
3.1.23. Непровар: дефект в виде
несплавления в сварном
соединении│
│вследствие
неполного расплавления кромок
или поверхностей ранее│
│выполненных валиков сварного шва. │
│
[ГОСТ 2601, п. 196]
│
└─────────────────────────────────────────────────────────────────────────┘
3.1.24. Нутрение:
подготовка внутренней поверхности торца трубы газовой резкой с последующей
механической обработкой либо механической обработкой под определенным углом.
3.1.25. Однотипные
сварные соединения: группа сварных соединений, выполняемых по одной и той же
технологии сварки, имеющих общие основные параметры с определенным диапазоном
их значений (материал (металл), диаметр, толщина стенки, конструктивные
элементы и др.).
3.1.26.
Операционно-технологическая карта сборки и сварки: карта операционного описания
технологического процесса в технологической последовательности по всем
операциям подготовки, сборки и сварки, с указанием технологических режимов
сварки и данных о средствах технологического оснащения, разработанная по форме
типовой операционно-технологической карты.
3.1.27. Отпуск: вид
термообработки, заключающийся в нагреве сварных соединений ниже температур
превращения, выдержке при заданной температуре и последующем охлаждении с
определенной скоростью, с целью снижения уровня сварочных напряжений, улучшения
структуры и свойств сварных соединений.
3.1.28. Отпуск
высокотемпературный (высокий): вид отпуска, заключающийся в нагреве сварных
соединений до температуры от 500 °C до 680 °C, выдержке от 1 до 5 ч при заданной
температуре и охлаждении под слоем теплоизоляционных материалов.
3.1.29. Переходное
кольцо: патрубок, отрезок трубы промежуточной толщины, длиной не менее 250 мм,
предназначенный для соединения труб, соединительных деталей трубопроводов,
запорной и регулирующей арматуры при разнотолщинности свариваемых элементов.
3.1.30. Подварочный
слой корневого слоя шва: часть сварного шва, выполняемая изнутри трубы после
выполнения снаружи корневого слоя шва.
┌─────────────────────────────────────────────────────────────────────────┐
│
3.1.31. Полярность обратная:
полярность, при которой
электрод│
│присоединяется к
положительному полюсу источника
питания дуги,│
│свариваемые элементы - к отрицательному. │
│ [ГОСТ 2601, п. 128]
│
└─────────────────────────────────────────────────────────────────────────┘
┌─────────────────────────────────────────────────────────────────────────┐
│
3.1.32. Полярность прямая:
полярность, при которой
электрод│
│присоединяется к
отрицательному полюсу источника
питания дуги, а│
│свариваемые элементы - к положительному. │
│
[ГОСТ 2601, п. 129] │
└─────────────────────────────────────────────────────────────────────────┘
┌─────────────────────────────────────────────────────────────────────────┐
│
3.1.33. Притупление кромки:
нескошенная часть торца
кромки,│
│подлежащей сварке.
│
│
[ГОСТ 2601, п. 112]
│
└─────────────────────────────────────────────────────────────────────────┘
┌─────────────────────────────────────────────────────────────────────────┐
│
3.1.34. Разделка кромок:
придание кромкам, подлежащим
сварке,│
│необходимой формы.
│
│
[ГОСТ 2601, п. 110] │
└─────────────────────────────────────────────────────────────────────────┘
3.1.35.
Разнотолщинное сварное соединение: кольцевое стыковое сварное соединение труб,
труб с соединительными деталями трубопроводов, запорной и регулирующей
арматурой с разностью номинальных толщин стенок более 2,0 мм.
┌─────────────────────────────────────────────────────────────────────────┐
│
3.1.36. Ручная дуговая
сварка: дуговая сварка,
при которой│
│возбуждение дуги, подача электрода и его
перемещение выполняются вручную.│
│
[ГОСТ 2601, п. 16]
│
└─────────────────────────────────────────────────────────────────────────┘
3.1.37. Ремонт
сварного шва: исправление в сварном шве дефектов, выявленных по результатам
неразрушающих методов контроля.
Примечание.
Исправление дефектов при выполнении сварного шва в определение термина
"ремонт сварного шва" не входит.
3.1.38. Сварка
методом STT: автоматическая или механизированная импульсно-дуговая сварка
проволокой сплошного сечения в углекислом газе с мелкокапельным управляемым
переносом наплавляемого металла за счет специального электронного
микропроцессорного модуля инверторного источника сварочного тока.
3.1.39. Сварка
неповоротных соединений: сварка по замкнутому контуру во всех пространственных
положениях, при которой свариваемые элементы неподвижны.
3.1.40. Сварка
поворотных соединений: сварка по замкнутому контуру в одном пространственном
положении, при которой свариваемые элементы подвижны (поворачиваются,
вращаются).
3.1.41. Сварка
односторонняя: сварка, выполняемая с одной стороны свариваемых элементов.
┌─────────────────────────────────────────────────────────────────────────┐
│
3.1.42. Сварка двухдуговая:
дуговая сварка, при
которой нагрев│
│осуществляется одновременно двумя дугами с
раздельным питанием их током. │
│
[ГОСТ 2601, п. 19]
│
└─────────────────────────────────────────────────────────────────────────┘
3.1.43. Сварка
двухсторонняя: сварка, выполняемая с двух сторон (снаружи и изнутри)
свариваемых элементов.
Примечание. Сварка
с подваркой изнутри дефектных участков корневого слоя шва в понятие
"двухсторонняя сварка" не входит.
┌─────────────────────────────────────────────────────────────────────────┐
│
3.1.44. Сварка на подъем: дуговая сварка, при которой сварочная
ванна│
│перемещается снизу вверх.
│
│
[ГОСТ 2601, п. 104] │
└─────────────────────────────────────────────────────────────────────────┘
┌─────────────────────────────────────────────────────────────────────────┐
│
3.1.45. Сварка на спуск: дуговая сварка, при которой сварочная ванна│
│перемещается сверху вниз.
│
│
[ГОСТ 2601, п. 103]
│
└─────────────────────────────────────────────────────────────────────────┘
┌─────────────────────────────────────────────────────────────────────────┐
│
3.1.46. Сварка углом вперед: сварка, при
которой электрод наклонен│
│под острым углом к направлению сварки. │
│
[ГОСТ 2601, п. 105] │
└─────────────────────────────────────────────────────────────────────────┘
┌─────────────────────────────────────────────────────────────────────────┐
│
3.1.47. Сварка углом назад: сварка, при которой электрод наклонен
под│
│тупым углом к направлению сварки. │
│
[ГОСТ 2601-84, п. 106]
│
└─────────────────────────────────────────────────────────────────────────┘
┌─────────────────────────────────────────────────────────────────────────┐
│
3.1.48. Сварное соединение:
неразъемное соединение, выполненное│
│сваркой.
│
│
[ГОСТ 2601, п. 57]
│
└─────────────────────────────────────────────────────────────────────────┘
3.1.49. Сварной
шов: участок сварного соединения, образовавшийся в результате кристаллизации
расплавленного металла.
3.1.50. Сертификат:
документ о качестве конкретных партий труб, сварочных материалов и др.,
удостоверяющий соответствие их качества требованиям технических условий, а
также специальным требованиям к контракту на поставку.
3.1.51. Слой
сварного шва: часть металла сварного шва, состоящая из одного или нескольких
валиков, располагающихся на одном уровне поперечного сечения шва.
3.1.52. Система
аттестации сварочного производства, САСв: комплекс требований, определяющих
правила и процедуру аттестации сварщиков, специалистов сварочного производства,
сварочных материалов, сварочного оборудования, технологий сварки для
производства сварочных работ при изготовлении, реконструкции, монтаже и ремонте
оборудования и объектов, надзор за которыми осуществляет Ростехнадзор.
3.1.53.
Соединительная деталь трубопровода, СДТ: изделие (отвод, переход, днище,
тройник), ввариваемое в трубопровод и предназначенное:
отвод - для
изменения направления трубопровода;
переход - для
изменения сечения трубопровода;
днище - для
герметизации конца трубопровода;
тройник - для
ответвления основного трубопровода.
3.1.54. Специальное
сварное соединение: сварное соединение, выполняемое со специальными
требованиями к подготовке, сборке, сварке и контролю качества (захлесты, прямые
вставки (катушки), разнотолщинные сварные соединения, угловые и нахлестанные
сварные соединения).
┌─────────────────────────────────────────────────────────────────────────┐
│
3.1.55. Термитная сварка:
сварка, при которой
для нагрева│
│используется энергия горения термитной
смеси. │
│
[ГОСТ 2601, п. 33]
│
└─────────────────────────────────────────────────────────────────────────┘
3.1.56. Термическая
обработка (термообработка): нагрев, выдержка и охлаждение сварных соединений по
определенным режимам с целью получения заданных свойств.
3.1.57. Температура
предварительного подогрева: температура подогрева кромок сварного соединения
непосредственно перед операциями сварки, как правило, указывается минимальная
величина этой температуры.
3.1.58. Температура
сопутствующего (межслойного) подогрева: минимальная температура
предварительного подогрева в зоне сварного шва, которая должна поддерживаться в
случае прерывания сварочного процесса, а также перед сваркой последующих слоев
шва после сварки предыдущих слоев.
3.1.59. Технические
условия, ТУ: документ, разработанный по решению разработчика (изготовителя) или
по требованию заказчика (потребителя), регламентирующий полный комплекс
требований к продукции (трубы, соединительные детали, запорная и регулирующая
арматура, сварочные материалы, сварочное оборудование), ее изготовлению,
контролю и приемке.
┌─────────────────────────────────────────────────────────────────────────┐
│
3.1.60. Угол скоса кромки: острый угол между плоскостью скоса кромки│
│и плоскостью торца.
│
│
[ГОСТ 2601, п. 113]
│
└─────────────────────────────────────────────────────────────────────────┘
3.1.61. Усиление
сварного шва: выпуклость шва, определяемая расстоянием между плоскостью,
проходящей через видимые линии границы сварного шва с основным металлом и
поверхностью сварного шва, измеренным в месте наибольшей выпуклости.
3.1.62. Условный
проход (номинальный размер): безразмерный параметр, применяемый для
трубопроводных систем в качестве характеристики присоединяемых частей, например
соединений труб, труб с соединительными деталями, запорной и регулирующей
арматурой, указываемый как DN
.
3.1.63. Флюс плавленый:
флюс для дуговой сварки, полученный сплавлением его составляющих и последующей
грануляцией расплава.
3.1.64. Флюс
керамический (агломерированный): флюс для дуговой сварки, полученный
перемешиванием порошкообразных материалов со связующим веществом, грануляцией и
последующей термической обработкой.
3.1.65. Центратор:
устройство для обеспечения сборки по заданным параметрам стыковых кольцевых
соединений труб, соединительных деталей трубопроводов, запорной и регулирующей
арматуры.
3.2. В настоящем
стандарте применены следующие сокращения:
ЗРА - запорная и
регулирующая арматура;
ЗТВ - зона
термического влияния;
КСС - контрольное
сварное соединение;
КЭН -
комбинированный электронагреватель;
НАКС - Национальная
Ассоциация Контроля и Сварки;
РТФ - разовая тигель-форма;
САСв - система
аттестации сварочного производства;
СДТ -
соединительная деталь трубопровода;
ЭХЗ -
электрохимическая защита.
3.3. В
настоящем стандарте применены следующие обозначения способов сварки:
РД - ручная дуговая
сварка покрытыми электродами;
РАД - ручная
аргонодуговая сварка неплавящимся электродом;
МП -
механизированная сварка плавящимся электродом в среде активных газов и смесях;
МПС -
механизированная сварка самозащитной порошковой проволокой;
ААДП -
автоматическая сварка плавящимся электродом в среде инертных газов и смесях;
АПГ -
автоматическая сварка плавящимся электродом в среде активных газов и смесях;
АПИ -
автоматическая сварка порошковой проволокой в среде инертных газов и смесях;
АФ - автоматическая
сварка под флюсом.
4. Аттестация технологий сварки
4.1.
Аттестация технологий сварки подразделяется на исследовательскую и
производственную и проводится согласно требованиям РД 03-615-03 [3] и других
руководящих и методических документов САСв.
4.2.
Исследовательская аттестация новых технологий (технологических вариантов)
сварки, не регламентированных настоящим стандартом, проводится с целью
подтверждения того, что они обеспечивают необходимые количественные и качественные
характеристики сварных соединений для безопасной эксплуатации газопроводов.
Исследовательскую аттестацию проводит разработчик настоящего стандарта (ООО
"ВНИИГАЗ") или другая организация совместно с ООО "ВНИИГАЗ"
по согласованию с ОАО "Газпром".
4.3.
Производственная аттестация технологий сварки, регламентированных настоящим
стандартом, проводится с целью подтверждения того, что организация, применяющая
технологии сварки, обладает необходимыми техническими, организационными
возможностями и квалифицированными кадрами для производства сварочных работ.
Производственную аттестацию проводит организация, выполняющая сварку
газопроводов, совместно со специализированным аттестационным центром САСв по
сварке газонефтепроводов.
4.4.
Производственная аттестация подразделяется на первичную, периодическую и
внеочередную.
4.5. Первичная
производственная аттестация проводится организациями, впервые применяющими
технологии сварки, регламентированные настоящим стандартом, а также в случае,
если в технологию сварки, прошедшую производственную аттестацию, внесены
изменения, выходящие за пределы области распространения свидетельства о
производственной аттестации. Срок действия производственной аттестации - три
года.
4.6. Периодическая
производственная аттестация технологий сварки проводится по истечению срока
действия свидетельства о первичной производственной аттестации, а также в
случае, если перерыв в применении технологий сварки превышает один год.
4.7.
Внеочередная производственная аттестация технологий сварки проводится в случаях
выполнения сварочных работ с систематически неудовлетворительным качеством
выполнения сварных соединений и/или нарушением требований
операционно-технологических карт сборки и сварки.
4.8.
Производственная аттестация технологий сварки должна проводиться путем сварки
КСС, однотипных производственным, в условиях, тождественных производственным.
Группы однотипных
сварных соединений приведены в Приложении А.
4.9. Сварку КСС
должны выполнять сварщики организации, выполняющей сварочные работы,
аттестованные в соответствии с ПБ 03-273-99 [4], РД 03-495-02 [5].
4.10. КСС,
выполненные при производственной аттестации технологий сварки, должны
оцениваться визуальным, измерительным и неразрушающими физическими методами
контроля и соответствовать требованиям раздела 6 СТО Газпром 2-2.4-083.
4.11. КСС,
выполненные при производственной аттестации технологий сварки, после получения
положительных результатов неразрушающего контроля качества, должны пройти
механические испытания с целью проверки соответствия их механических свойств
требованиям настоящего стандарта. Требования к механическим испытаниям
приведены в Приложении Б.
4.12. По
результатам производственной аттестации технологий сварки аттестационным
центром оформляется заключение о готовности организации, выполняющей сварочные
работы, к применению аттестованной технологии. В заключении указывается
установленная область распространения производственной аттестации технологий
сварки с учетом конструктивных и технологических параметров КСС, которые приведены
в Приложении В, на основании которого оформляется свидетельство НАКС о
производственной аттестации технологий сварки в соответствии с требованиями РД
03-615-03 [3] и выдается организации, выполняющей сварочные работы.
4.13. Организации,
выполняющие сварку газопроводов с применением технологий сварки, прошедших
производственную аттестацию до ввода в действие настоящего стандарта, могут
применять ранее аттестованные технологии до завершения срока действия
свидетельств о производственной аттестации технологий сварки согласно
требованиям РД 03-615-03 [3] при условиях:
- производственная
аттестация выполнена с применением КСС, конструктивные элементы которых
соответствуют требованиям настоящего стандарта;
- сварка КСС
выполнена с применением сварочных материалов и сварочного оборудования,
соответствующих требованиям разделов 7, 8;
- механические
свойства КСС соответствуют требованиям, предъявляемым к свойствам сварных
соединений, регламентированных разделом 9.
5. Допускные испытания сварщиков
5.1. Сварщики
ручной сварки (далее - сварщики), сварщики-операторы механизированной и
автоматической сварки (далее - операторы), выполняющие сварочные работы на
газопроводах, должны быть аттестованы в соответствии с ПБ 03-273-99 [4], РД
03-495-02 [5], при этом в протоколах аттестации сварщиков, специалистов
сварочного производства должна быть ссылка на настоящий стандарт.
5.2. Допускные
испытания сварщиков, операторов, бригады сварщиков (операторов) проводятся с
целью подтверждения необходимых квалификационных способностей для выполнения
сварных соединений по аттестованным технологиям сварки, регламентированным
настоящим стандартом.
5.3. Допускные
испытания сварщиков, операторов проводятся в организации, выполняющей сварочные
работы, перед началом производства работ путем сварки КСС в присутствии
представителя технического надзора (по согласованию).
5.4. КСС для
допускных испытаний должны быть однотипны производственным сварным соединениям
и выполняться по аттестованным технологиям сварки, при этом должны соблюдаться
все требования операционно-технологических карт сборки и сварки, применяться
сварочные материалы и оборудование, соблюдаться техника ведения сварки и
скорость выполнения операций технологий сварки, по которым проведена
производственная аттестация.
5.5. КСС при
допускных испытаниях подлежат:
- операционному
контролю в процессе сварки;
- визуальному и
измерительному контролю;
- физическим
методам контроля (радиографический - для кольцевых стыковых сварных соединений,
ультразвуковой - для угловых и нахлесточных сварных соединений);
- контролю по
макрошлифам (при двухсторонней автоматической сварке под флюсом);
- механическим
испытаниям на статический изгиб (при механизированной и автоматической сварке в
защитных газах).
5.6. Сварщики,
операторы, бригады сварщиков (операторов) признаются прошедшими допускные
испытания, если по результатам контроля качества КСС получены положительные
заключения, что должно быть отражено в протоколе допускных испытаний по
рекомендуемой форме, приведенной в Приложении Г.
5.7. На основании
протокола допускных испытаний на каждого сварщика, оператора, в том числе при
работе в составе бригады, оформляется Допускной лист по форме, приведенной в
Приложении Г. Протокол допускных испытаний и Допускной лист оформляются
организацией, в которой сварщики, операторы состоят в трудовых отношениях, и
которая выполняет сварочные работы по аттестованным технологиям сварки.
5.8. Не требуется
проведение допускных испытаний сварщиков, операторов если:
- они выполняли
сварку КСС при производственной аттестации технологий сварки, при этом по
результатам контроля качества КСС получены положительные заключения, а время,
прошедшее с даты производственной аттестации технологии сварки, не превышает
трех месяцев;
- они были ранее
аттестованы в соответствии с ПБ 03-273-99 [4], РД 03-495-02 [5] в этой
организации, при этом, сварка и контроль качества КСС при практическом экзамене
выполнены в полном соответствии с аттестованными технологиями сварки
газопроводов и перерыв в работе по сварке однотипных сварных соединений не
превышает трех месяцев.
5.9. Срок
действия Допускного листа сварщика устанавливается на время выполнения
сварочных работ, по которым сварщик (оператор) прошел допускные испытания, если
перерыв в работе не превышает трех месяцев, но не более срока действия
аттестационного удостоверения.
5.10. Организациям,
выполняющим сварочные работы на нескольких объектах, разрешается оформлять
Допускной лист сварщика на каждый объект или несколько объектов, если сварные
соединения объектов однотипны сварным соединениям, приведенным в протоколе
допускных испытаний, при этом допускается оформлять Допускной лист сварщика на
новый объект по данным протокола допускных испытаний, оформленного на
предыдущем объекте, с указанием срок действия нового Допускного листа в
соответствии с 5.9.
6.
Требования к трубам и соединительным деталям
6.1. Общие
требования
6.1.1. При
сварке промысловых и магистральных газопроводов по 1.1 применяются трубы, СДТ,
ЗРА отечественных или зарубежных заводов-производителей, изготовленные по
специальным ТУ, согласованным с ОАО "Газпром", ГОСТ и рекомендованные
к применению нормативными документами ОАО "Газпром".
6.1.2. Трубы
(каждая партия) должны быть обеспечены сертификатами качества, СДТ, ЗРА -
техническими паспортами заводов-производителей с указанием приемо-сдаточных
характеристик.
6.1.3. До начала
сварочных работ трубы, СДТ, ЗРА должны пройти входной контроль в порядке,
установленном в организации, выполняющей сварочные работы.
6.1.4. Трубы, СДТ,
изготавливаемые из углеродистой или низколегированной спокойной или
полуспокойной стали, должны иметь эквивалент углерода
не более 0,46%. Классы прочности и
механические свойства сталей труб, СДТ приведены в таблице 6.1.
Таблица 6.1
Классы прочности и
механические свойства сталей труб, СДТ
Класс
прочности
|
Нормативные механические свойства (не
менее)
|
Временное сопротивление
разрыву, МПа (кгс/мм2)
|
Предел текучести,
МПа (кгс/мм2)
|
Относительное
удлинение, %
|
К34
|
333 (34)
|
206 (21)
|
24
|
К38
|
372 (38)
|
235 (24)
|
22
|
К42
|
412 (42)
|
245 (25)
|
21
|
К45 <1>
|
441 (45)
|
341 (35)
|
20
|
К48 <1>
|
471 (48)
|
324 (33)
|
20
|
К50 <1>
|
490 (50)
|
340 (35)
|
20
|
К52
|
510 (52)
|
360 (37)
|
20
|
К54 <1>
|
530 (54)
|
380 (39)
|
20
|
К55
|
540 (55)
|
380 (39)
|
20
|
К56 <1>
|
550 (56)
|
390 (40) <2>
|
20
|
К58 <1>
|
570 (58)
|
470 (48)
|
20
|
К60
|
590 (60)
|
460 (47) <1>, <3>
|
20
|
480 (49) <4>
|
20
|
<1> Трубы по специальным ТУ, согласованным с ОАО
"Газпром".
<2> По минимальному значению
предела текучести соответствует классу
X60 по API 5L [20].
<3> По минимальному значению
предела текучести соответствует классу
X65 по API 5L [20].
<4> По минимальному значению
предела текучести соответствует классу
X70 по API 5L [20].
Примечания. 1. Класс прочности соответствует нормативному значению
временного сопротивления разрыву, определяемому на поперечных образцах.
2. Трубы, СДТ из сталей других
классов прочности должны применяться в
соответствии с требованиями 6.1.1.
|
6.1.5. Эквивалент
углерода
сталей труб, СДТ, обечаек ЗРА определяется по
формуле
,
(6.1)
где C, Mn, Cr, Mo,
V, Ti, Ni, Cu, B - содержание, % от массы, в составе металла трубной стали
соответственно углерода, марганца, хрома, молибдена, ванадия, ниобия, титана,
меди, никеля, бора.
6.1.6. Остаточная
величина магнитного поля (намагниченность) торцов труб, СДТ должна быть не
более 20 Гс. При намагниченности торцов труб, СДТ более 20 Гс должно
производиться размагничивание в соответствии с нормативными документами ОАО
"Газпром".
6.1.7. Концы труб,
СДТ, ЗРА должны быть обработаны механическим способом и защищены от
механических повреждений обечайками, а также для предотвращения попадания
внутрь труб, СДТ влаги, снега и др. при транспортировке их концы должны быть
закрыты инвентарными заглушками.
6.1.8. Усиление
внутреннего заводского шва труб и СДТ, изготовленных с применением
электродуговой двухсторонней сварки, на длине не менее 150 мм от торцов должно
быть снято до величины от 0 до 0,5 мм, допускается снятие усиления наружного
шва на длине не менее 150 мм от торцов труб до величины от 0 до 0,5 мм.
6.1.9. Не
допускаются вмятины любых размеров торцов труб, СДТ, ЗРА с механическими
повреждениями поверхности металла.
6.1.10. Не
допускаются на наружной и внутренней поверхности концов труб, СДТ на расстоянии
менее 40 мм от торцов трещины, закаты, расслоения. Концы труб, СДТ могут иметь
поверхностные дефекты механического происхождения (риски, продиры, царапины),
регламентированные специальными ТУ, ГОСТ.
6.1.11. Устранение
поверхностных дефектов концов труб, СДТ, ЗРА производится механическим способом
(шлифмашинками с набором абразивных кругов и дисковых проволочных щеток)
<*>, при этом толщина стенки концов труб, СДТ после механической
обработки не должна выйти за пределы минусовых допусков.
--------------------------------
<*> В тексте
стандарта вместо термина "обработка или зачистка механическим способом
шлифмашинками с набором абразивных кругов и дисковых проволочных щеток",
далее, за исключением особых случаев, употребляется термин "механическая
обработка шлифмашинками".
6.1.12. Не
допускается выполнять ремонт сваркой основного металла тела труб, СДТ, ЗРА.
6.2. Требования к
трубам
6.2.1. При сварке
газопроводов применяются:
а) трубы большого
диаметра (наружным диаметром от 530 до 1420 мм):
- прямошовные,
изготовленные с применением электродуговой сварки, с одним или двумя
продольными сварными швами;
- спирально-шовные,
изготовленные с применением электродуговой сварки;
- прямошовные,
изготовленные с применением электроконтактной сварки токами высокой частоты;
б) трубы малого
диаметра (наружным диаметром от 20 до 426 мм):
- прямошовные,
изготовленные с применением электроконтактной сварки токами высокой частоты;
- спирально-шовные,
изготовленные с применением электродуговой сварки;
- бесшовные.
6.2.2.
Геометрические параметры заводской разделки кромок торцов труб для сборки под
сварку с номинальной толщиной стенки до 15,0 мм включ. приведены на рисунке 6.1
а, геометрические параметры разделки кромок торцов труб с номинальной толщиной
стенки более 15,0 мм при отсутствии специальных требований в ТУ или
спецификации к контракту на поставку труб приведены на рисунке 6.1 б.
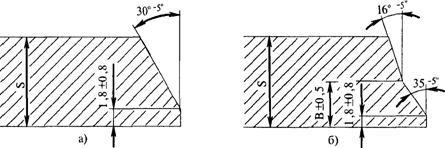
а) трубы с толщиной
стенки (S) до 15,0 мм включ.;
б) трубы с толщиной
стенки св. 15,0 мм
Значение параметра
B:
- 9,0 мм для толщин стенок труб св. 15,0 до
19,0 мм включ.;
- 10,0
мм " " 19,0 " 21,5 ";
- 12,0 мм " " 21,5 " 32,0 "
Рисунок
6.1. Геометрические параметры заводской
разделки кромок
торцов труб для сборки под сварку
6.2.3. Концы труб
на расстоянии до 40 мм от торцов могут иметь допустимые предельные отклонения
от номинальных размеров, которые оговариваются специальными ТУ или ГОСТ.
6.3. Требования к
соединительным деталям
6.3.1. При сварке
газопроводов применяются СДТ:
а) тройники
штампованные бесшовные и штампосварные с решетками и без решеток;
б) тройники сварные
с усиливающими накладками и без усиливающих накладок, с решетками и без
решеток;
в) отводы
крутоизогнутые из бесшовных или электросварных труб;
г) отводы
крутоизогнутые штампосварные;
д) отводы гнутые из
бесшовных или электросварных труб;
е) переходы
концентрические штампованные бесшовные и штампосварные;
ж) днища, заглушки
штампованные эллиптические;
з) кольца
переходные из труб (бесшовных или электросварных) и вальцованных обечаек.
Примечания. 1.
Электросварные СДТ должны изготавливаться с применением дуговых способов
сварки.
2. Не допускается
изготавливать отводы, переходные кольца из прямошовных электросварных труб,
сваренных токами высокой частоты.
6.3.2. Кромки СДТ,
ЗРА под сварку должны быть обработаны механическим способом, при этом
геометрические параметры наружной и внутренней разделки и скоса кромок должны
назначаться в зависимости от номинальных размеров (рисунок 6.2): наружного и
присоединительного диаметра и толщины стенки СДТ, ЗРА, наружного диаметра и
толщины стенки свариваемых труб и оговариваться специальными ТУ. Геометрические
параметры кромок СДТ, ЗРА для сварки стыковых соединений одной толщины стенки
приведены на рисунке 6.1.
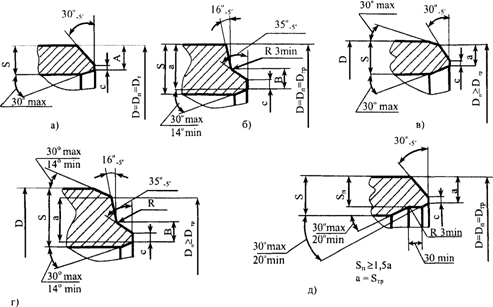
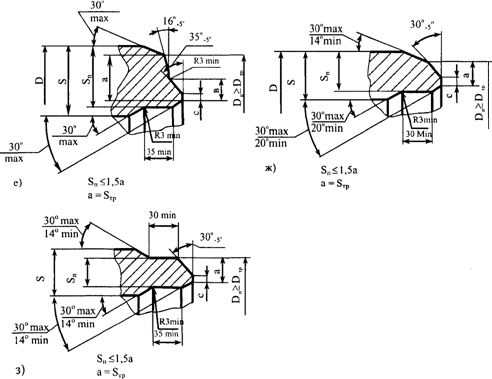
a - размер для присоединения
трубы или переходного кольца;
c - ширина
кольцевого притупления;
в - высота фаски;
D - наружный
диаметр детали;
- присоединительный диаметр детали, равный
;
- наружный диаметр трубы;
S - толщина стенки
детали;
- толщина стенки присоединяемой трубы;
- толщина стенки детали при расточке
внутреннего диаметра.
Рисунок
6.2. Геометрические параметры
заводской разделки
кромок СДТ, ЗРА для сборки
под сварку
разнотолщинных сварных соединений
6.3.3. При разности
толщин стенки СДТ, ЗРА и присоединяемой трубы по внутреннему диаметру более 2,5
мм (для толщин стенок, максимальная из которых 12 мм и менее) и 3,0 мм (для
толщин стенок, максимальная из которых более 12 мм), но не более 0,5 толщины
стенки присоединяемой трубы должен быть выполнен внутренний скос кромки по
схемам а) - г) рисунка 6.2.
6.3.4. При разности
толщин стенки СДТ, ЗРА и присоединяемой трубы более 0,5 толщины стенки присоединяемой
трубы должна быть выполнена разделка кромок (расточка) по схемам д) - з)
рисунка 6.2.
6.3.5. Концы СДТ,
ЗРА могут иметь допустимые предельные отклонения от номинальных размеров,
которые оговариваются специальными ТУ или ГОСТ.
7. Требования к сварочным материалам
7.1. Общие
требования
7.1.1. Для сварки
соединений труб, труб с СДТ, ЗРА газопроводов могут применяться:
- электроды с
основным и целлюлозным видом покрытия для ручной дуговой сварки;
- проволоки
сплошного сечения для механизированной, автоматической сварки в защитных газах
и автоматической сварки под флюсом;
- порошковые
проволоки для автоматической сварки в защитных газах;
- самозащитные
порошковые проволоки для механизированной сварки;
- флюсы плавленые и
керамические (агломерированные) для автоматической сварки проволокой сплошного
сечения;
- защитные газы
(углекислый газ, аргон) и их смеси для ручной дуговой сварки неплавящимся
электродом, механизированной и автоматической сварки проволокой сплошного
сечения и порошковой проволокой.
7.1.2.
Сварочные материалы (покрытые электроды, проволоки сплошного сечения,
порошковые проволоки, самозащитные порошковые проволоки, керамические и
плавленые флюсы, защитные газы и их смеси), предназначенные для ручной,
механизированной и автоматической сварки газопроводов, должны изготавливаться
по специальным ТУ и могут применяться при наличии:
а) сертификатов
качества, удостоверяющих их соответствие требованиям ТУ, для сварочных
материалов импортного производства - дубликатами сертификатов качества на
русском языке;
б)
санитарно-гигиенических сертификатов (рекомендательно);
в) свидетельств
НАКС об аттестации сварочных материалов согласно РД 03-613-03 [1] с областью
применения для производства сварочных работ на газопроводах.
7.1.3. Сварочные
материалы должны соответствовать требованиям ТУ, сертификатов качества и
обеспечивать:
а)
сварочно-технологические свойства:
- качественное
формирование металла шва при сварке во всех пространственных положениях и
направлениях;
- стабильность
горения дуги;
- легкое удаление
шлака, образующегося в процессе сварки, в т.ч. при сварке в разделку кромок;
б) металлургические
свойства наплавленного металла:
- гарантированное
содержание основных легирующих элементов;
- допустимое
содержание вредных примесей (S, P и др.) и диффузионного водорода;
- отсутствие
дефектов металлургического характера (поры, горячие трещины и др.);
в) механические
свойства наплавленного металла с гарантированными значениями:
- временного
сопротивления разрыву;
- предела
текучести;
- относительного
удлинения;
- относительного
сужения;
- ударной вязкости.
7.1.4. Сварочные
материалы должны обеспечивать механические свойства сварных соединений в
соответствии с требованиями раздела 9.
7.1.5. Выбор и
назначение сварочных материалов выполняется исходя из:
- способа и
технологии сварки;
- классов прочности
и номинальных размеров (диаметр, толщина стенки) свариваемых элементов;
-
сварочно-технологических свойств и производительности наплавки;
- схемы организации
сварочно-монтажных работ.
7.1.6. При сварке
соединений труб, труб с СДТ, ЗРА из сталей различных классов прочности
сварочные материалы назначаются:
- для соединений
одной толщины стенки - по меньшему классу прочности;
- для соединений
разной толщины стенки - по большему классу прочности.
7.1.7. Номенклатура
сварочных материалов (покрытые электроды, проволоки сплошного сечения,
порошковые проволоки, самозащитные порошковые проволоки, керамические и
плавленые флюсы), рекомендованных к применению для производства сварочных работ
на газопроводах, приведена в Приложении Д и может дополняться или
пересматриваться по результатам первичной, дополнительной, периодической или
внеочередной аттестации согласно РД 03-613-03 [1].
7.1.8. Сварочные
материалы, не регламентированные настоящим стандартом, до производства
сварочных работ на газопроводах должны пройти квалификационные испытания в
объеме аттестации тех технологий (способов) сварки, для которых эти сварочные
материалы предназначены.
7.1.9. Структурное
подразделение ОАО "Газпром", отвечающее за сварочное производство, не
реже одного раза в год утверждает реестр сварочных материалов, допущенных к
применению по результатам аттестации.
7.2. Требования к
покрытым электродам
7.2.1. Электроды с
основным и целлюлозным видом покрытия для ручной дуговой сварки газопроводов по
типам и техническим характеристикам должны соответствовать требованиям ГОСТ
9467, ГОСТ 9466 (электроды отечественных производителей), AWS A5.1 [21], AWS
A5.5 [22], EN 499 [23], EN 757 [24] (электроды зарубежных производителей),
специальных ТУ и сертификатов качества.
7.2.2. Технические
требования к покрытым электродам, классификация и назначение приведены в
таблицах Д.1 - Д.3 (Приложение Д).
7.2.3. Электроды с
основным видом покрытия, рекомендованные к применению для ручной дуговой сварки
неповоротных кольцевых стыковых, угловых и нахлесточных соединений труб, труб с
СДТ, ЗРА, приведены в таблице Д.4 (Приложение Д).
7.2.4. Электроды с
целлюлозным видом покрытия, рекомендованные к применению для сварки
неповоротных стыковых соединений труб, приведены в таблице Д.5 (Приложение Д).
7.3. Требования к
сварочным проволокам
7.3.1. Проволоки
сплошного сечения для механизированной и автоматической сварки плавящимся
электродом в защитных газах, автоматической сварки под флюсом должны
соответствовать требованиям ГОСТ 2246 (проволоки отечественных производителей),
AWS A5.17 [25], A5.18 [26], A5.23 [27], A5.28 [28], EN 440 [29], EN 756 [30],
EN 12534 [31] (проволоки зарубежных производителей), специальных ТУ и
сертификатов качества.
7.3.2. Порошковые
проволоки, в т.ч. самозащитные, для механизированной и автоматической сварки в
защитных газах или открытой дугой должны соответствовать требованиям ГОСТ 26271
(проволоки отечественных производителей), AWS 5.20 [32], A5.29 [33], EN 758
[34] (проволоки зарубежных производителей), специальных ТУ и сертификатов
качества.
7.3.3. Технические
требования к сварочным проволокам, классификация и назначение приведены в
таблицах Д.6 - Д.10 (Приложение Д).
7.3.4. Проволоки
сплошного сечения, рекомендованные к применению для механизированной сварки в
углекислом газе неповоротных кольцевых стыковых соединений труб, приведены в
таблице Д.11 (Приложение Д), для автоматической сварки в защитных газах - в
таблице Д.12 (Приложение Д).
7.3.5. Проволоки
сплошного сечения в комбинации с флюсами, рекомендованные к применению для
автоматической сварки поворотных кольцевых стыковых соединений труб, приведены
в таблице Д.13 (Приложение Д).
7.3.6. Порошковые
проволоки, рекомендованные к применению для автоматической сварки в защитных
газах неповоротных кольцевых стыковых соединений труб, приведены в таблице Д.14
(Приложение Д).
7.3.7. Самозащитные
порошковые проволоки, рекомендованные к применению для механизированной сварки
неповоротных кольцевых стыковых соединений труб, приведены в таблице Д.15
(Приложение Д).
7.4. Требования к
сварочным флюсам
7.4.1. Плавленые и
керамические (агломерированные) флюсы для автоматической сварки должны
соответствовать требованиям ГОСТ 52222, ГОСТ 28555 (для отечественных флюсов),
AWS A5.17 [25], A5.23 [27] (для импортных флюсов), специальных ТУ и
сертификатов качества.
7.4.2. Технические
требования к сварочным флюсам приведены в таблице Д.16 (Приложение Д).
Классификация и назначение сварочных флюсов приведены в таблице Д.8 (Приложение
Д).
7.4.3. Сварочные
флюсы, рекомендованные к применению для автоматической сварки проволокой
сплошного сечения поворотных кольцевых стыковых соединений труб, приведены в
таблице Д.13 (Приложение Д).
7.5. Требования к
защитным газам
7.5.1. Защитные
газы (активные, инертные газы и их смеси) для механизированной и автоматической
сварки должны соответствовать требованиям ГОСТ 10157 (аргон газообразный высший
сорт), ГОСТ 8050 (двуокись углерода газообразная и жидкая высший сорт), ТУ и
сертификатов качества.
7.5.2. Технические
требования к защитным газам приведены в таблице Д.17 (Приложение Д).
7.5.3. Защитные
газы (активные, инертные газы и их смеси), рекомендованные к применению для
механизированной и автоматической сварки неповоротных кольцевых стыковых
соединений труб, приведены в таблице Д.18 (Приложение Д).
7.6. Специальные
требования к сварочным материалам
7.6.1. Покрытые
электроды для ручной дуговой сварки должны:
а) иметь
ионизирующее покрытие на контактном торце электрода;
б) формировать
равномерный обратный валик корневого слоя шва <*>;
в) быть герметично
упакованы в вакуумные металлические банки, герметичные пластмассовые коробки
или картонные коробки, обтянутые термоусадочной пленкой. Отдельные упаковки с
электродами (герметичные пластмассовые коробки, картонные коробки, обтянутые
термоусадочной пленкой) должны быть упакованы в коробки в количестве от 3 до 4
шт. в каждой упаковке.
--------------------------------
<*> Только
для электродов, предназначенных для сварки корневого слоя шва.
7.6.2. Сварочные
проволоки для механизированной и автоматической сварки должны:
а) формировать
равномерный обратный валик корневого слоя шва при односторонней сварке
<**>;
б) быть упакованы с
рядной и цельной намоткой на унифицированные катушки (кассеты, бухты) с
возможностью установки в механизмы подачи проволоки и сварочные головки, с
надежной фиксацией свободного конца проволоки для исключения самопроизвольного
"распушивания";
в) быть герметично
упакованы в катушки (кассеты, бухты), обтянутые термоусадочной пленкой, и
уложены в пластмассовые или картонные коробки с влагопоглощающим компонентом.
--------------------------------
<**>
Только для порошковых проволок, предназначенных для сварки корневого слоя шва.
7.6.3. Сварочные
флюсы для автоматической сварки должны быть упакованы в герметичные мешки
массой не более 25 кг, обеспечивающие сохранность и возможность использования
флюса без дополнительной сушки.
7.7. Хранение и
подготовка сварочных материалов
7.7.1.
Сварочные материалы должны проходить входной контроль в порядке, установленном
в ОАО "Газпром" и в организации, выполняющей сварочные работы при
строительстве и ремонте газопроводов. При входном контроле следует проверять:
- наличие
сертификатов качества (для сварочных материалов импортного производства -
дубликатов сертификатов качества на русском языке);
- сохранность
упаковки;
- внешний вид;
-
сварочно-технологические свойства.
7.7.2. Сварочные
материалы следует хранить в соответствии с рекомендациями
заводов-изготовителей, при этом сварочные электроды следует хранить в помещениях
при температуре воздуха не ниже +15 °C, относительной влажности не более 60% в
количестве не более пяти упаковок (рядов) в высоту.
7.7.3. Сварочные
материалы, хранящиеся более одного года, непосредственно перед использованием
должны пройти повторный входной контроль в соответствии с требованиями 7.7.1.
7.7.4. Электроды,
проволоки, флюсы с нарушением герметичности упаковки должны пройти повторный
входной контроль в соответствии с требованиями 7.7.1 и должны быть использованы
в первую очередь.
7.7.5. Электроды с
основным видом покрытия, поставляемые в герметичных пластмассовых коробках или
картонных коробках, обтянутых термоусадочной пленкой, перед сваркой должны быть
прокалены в соответствии с рекомендациями изготовителя. При отсутствии
рекомендаций изготовителя электроды должны быть прокалены при температуре от
+350 °C до +380 °C в течение от 1 до 2 ч.
7.7.6. Электроды с
основным видом покрытия, поставляемые в герметичных металлических банках, не
требуют прокалки перед сваркой. При нарушении герметичности банки, а также в
случае, если электроды из открытой банки не были использованы в течение рабочей
смены, необходимо произвести их прокалку перед сваркой в соответствии с
рекомендациями изготовителя. При отсутствии рекомендаций изготовителя электроды
должны быть прокалены при температуре от +350 °C до +380 °C в течение от 1 до 2
ч.
7.7.7. Электроды с
основным видом покрытия после прокалки должны храниться:
- в термостатах
(термопеналах), сушильных шкафах, прокалочных печах при температуре от +100 °C
до +150 °C;
- в герметичных
емкостях в сухих отапливаемых помещениях при температуре воздуха не ниже +15 °C
и относительной влажности не более 60% в течение не более 2-х суток; после
истечения 2-х суток перед использованием электродов требуется повторная прокалка.
7.7.8. Повторная
прокалка электродов с основным видом покрытия должна проводиться не более 5
раз, при общем времени прокалки не более 10 ч.
7.7.9. Прокалка
электродов с целлюлозным видом покрытия не допускается. В случае нарушения
целостности упаковки, прямого попадания влаги допускается их просушка при
температуре от +80 °C до +90 °C в течение от 10 до 20 мин.
7.7.10. Проволоки
сплошного сечения, порошковые проволоки, в т.ч. самозащитные порошковые
проволоки марки "Иннершилд", не требуют предварительной сушки,
прокалки перед сваркой. После вскрытия упаковки проволока должна быть
использована в течение 24 ч в случае хранения на открытом воздухе, исключающем
попадание влаги. При попадании влаги или хранении проволоки в открытой упаковке
более 24 ч перед использованием проволоки требуется просушка.
7.7.11. Флюсы перед
сваркой должны подвергаться сушке или прокалке в соответствии с требованиями
ТУ.
7.7.12. Флюс должен
выдаваться в количестве, необходимом для односменной работы трубосварочной
базы.
7.7.13. Не
допускается смешивать флюсы разных марок.
8. Требования к сварочному оборудованию
8.1. Общие
требования
8.1.1. Сварочное
оборудование (сварочные выпрямители тиристорного и инверторного типа, сварочные
головки, механизмы подачи сварочной проволоки, сварочные горелки, в том числе в
составе передвижных и самоходных сварочных установок и сварочных агрегатов),
предназначенное для ручной, механизированной и автоматической сварки <*>
газопроводов, должно изготавливаться по специальным ТУ и может применяться при
наличии:
а) паспортов и
руководств по эксплуатации (для сварочного оборудования импортного производства
- дубликатов паспортов, руководств по эксплуатации на русском языке);
б) сертификата
соответствия ГОСТ Р (по безопасности);
в) одобрения типа
транспортного средства ГОСТ Р (для передвижных сварочных агрегатов, передвижных
и самоходных сварочных установок);
г) свидетельств
НАКС об аттестации сварочного оборудования согласно РД 03-614-03 [2] с областью
применения для производства сварочных работ на газопроводах;
д) разрешения
Ростехнадзора на применение сварочного оборудования с областью применения для
производства сварочных работ на газопроводах.
--------------------------------
<*>
Для автоматической сварки вместо термина "сварочные установки"
применяется термин "сварочные комплексы".
8.1.2. Сварочное
оборудование должно соответствовать требованиям ТУ, паспортов, руководств по
эксплуатации и обеспечивать:
а)
сварочно-технологические свойства:
- надежность
зажигания, повышенную устойчивость горения и высокую эластичность дуги при
питании от сети переменного тока (3380 В, 50 Гц);
- получение сварных
соединений высокого качества;
б) безопасность
эксплуатации:
- удобство доступа
к узлам и механизмам;
- наглядность и
доступность органов управления, надписей и условных знаков, указывающих их
функциональное назначение;
- надежность
фиксации всех органов управления, исключающее самопроизвольное или случайное их
включение, отключение;
- ограничение
напряжения холостого хода до значения, не превышающего 12 В, не позже чем через
0,6 с после обрыва сварочной дуги для проведения сварочных работ в особо
опасных условиях (внутри труб, обводненных котлованах и траншеях и т.п.);
- заземление
штепсельных соединений пультов дистанционного управления;
- защиту
отключающими предохранителями или автоматами со стороны питающей сети;
- надежность
ограждения вращающихся частей сварочного оборудования, частей, находящихся под
высоким напряжением или высокой температурой (более +40 °C);
- надежность
крепления газоподводящих шлангов на присоединительных ниппелях аппаратуры,
горелок, редукторов.
8.1.3. Номенклатура
источников сварочного тока (сварочных выпрямителей тиристорного и инверторного
типа, сварочных агрегатов), рекомендованных к применению для производства
сварочных работ на газопроводах, приведена в Приложении Е и может дополняться
или пересматриваться по результатам первичной, дополнительной, периодической
или внеочередной аттестации согласно РД 03-614-03 [2].
8.1.4. Сварочное
оборудование для механизированной и автоматической сварки, не
регламентированное настоящим стандартом, до производства сварочных работ на
газопроводах должно пройти квалификационные испытания в объеме аттестации тех
технологий (способов) сварки, для которых оборудование предназначено.
8.2. Требования к
источникам сварочного тока
8.2.1. Технические
требования к источникам сварочного тока (сварочным выпрямителям тиристорного и
инверторного типа), сварочным головкам, механизмам подачи сварочной проволоки,
сварочным горелкам для ручной, механизированной и автоматической сварки
приведены в таблицах Е.1 - Е.7 (Приложение Е).
8.2.2. Сварочные
выпрямители тиристорного и инверторного типа, рекомендованные к применению для
ручной, механизированной и автоматической сварки приведены в таблице Е.8
(сварочные выпрямители тиристорного типа) и таблице Е.9 (сварочные выпрямители
инверторного типа) (Приложение Е).
8.2.3. Источники
сварочного тока (сварочные выпрямители, сварочные головки, механизмы подачи
сварочной проволоки, сварочные горелки) по стойкости к воздействию внешних
климатических и механических факторов должны соответствовать требованиям
таблицы Е.10 (Приложение Е).
8.2.4. Сварочные
выпрямители тиристорного и инверторного типа, предназначенные для работы в
составе многопостовых передвижных (блок-контейнеров или на базе колесной
техники) и самоходных (на базе колесной или гусеничной техники) сварочных
установок, должны обеспечивать возможность применения в автономной электросети
переменного тока ограниченной мощности.
8.3. Требования к
сварочным агрегатам и сварочным установкам
8.3.1. Технические
требования к сварочным агрегатам для ручной и механизированной сварки типа АДДУ
(одно-, двух- и четырехпостовые с источником сварочного тока - генератором типа
ГД), а также к автономным многопостовым передвижным (блок-контейнеры или на
базе колесной техники) и самоходным (на базе колесной или гусеничной техники)
сварочным установкам для ручной, механизированной и автоматической сварки
приведены в таблицах Е.11 - Е.13 (Приложение Е).
8.3.2. Сварочные
агрегаты, рекомендованные к применению для ручной и механизированной сварки,
приведены в таблице Е.14 (Приложение Е).
8.3.3. Сварочные
агрегаты с двигателями внутреннего сгорания, автономные многопостовые
передвижные (блок-контейнеры или на базе колесной техники) и самоходные
сварочные установки на базе колесной или гусеничной техники (а/м "Урал",
КамАЗ, тракторов "Кировец", ТТ, ТЛТ, ДТ, РТМ) с приводом от вала
отбора мощности двигателя базовой техники либо с автономными электростанциями
должны комплектоваться:
а) основным
сварочным оборудованием:
- источниками
сварочного тока: сварочными выпрямителями тиристорного или инверторного типа,
работающими от источника переменного тока (генератора или электростанции, ~ 380
В, 50 Гц), или сварочными генераторами типа ГД;
- пультами
дистанционного управления для ручной сварки, сварочными горелками и подающими
механизмами для механизированной сварки, сварочными головками и блоками
управления для автоматической сварки;
- шкафом
управления;
- выводом
однофазного напряжения (~ 220 В, 50 Гц) для питания электрооборудования;
- печью просушки и
прокалки сварочных материалов;
б) вспомогательным
оборудованием (рекомендательно):
-
воздушно-плазменной, кислородной или механической резки труб;
- предварительного
и сопутствующего (межслойного) подогрева (горелки и подогреватели);
- сборки сварных
соединений (наружные центраторы);
- укрытиями места
сварочных работ от воздействия окружающей среды;
-
электрооборудованием для освещения места работ;
-
электроинструментом для механической обработки кромок свариваемых элементов и
сварных соединений.
8.4. Требования к
оборудованию для предварительного и сопутствующего (межслойного) подогрева и
термической обработки
8.4.1. Для
выполнения предварительного и сопутствующего (межслойного) подогрева кромок
свариваемых соединений и послесварочной термической обработки сварных
соединений могут применяться следующие способы нагрева:
- индукционный
(токами средней частоты от 400 до 10000 Гц, преимущественно 2500 Гц);
- радиационный
(электрический сопротивлением, газопламенный);
-
электронагревателями комбинированного действия (электрический сопротивлением в
сочетании с индукционным током промышленной частоты 50 Гц).
8.4.2. Для
выполнения подогрева индукционными, радиационными способами,
электронагревателями комбинированного действия может применяться специальное
оборудование:
- установки
индукционного нагрева;
- установки с
применением электронагревателей сопротивления;
- установки с
применением электронагревателей комбинированного действия;
- газопламенные
нагревательные устройства.
8.4.3. Технические требования
к установкам, электронагревателям, теплоизоляционным материалам приведены в пп.
Е.1 - Е.3 (Приложение Е).
8.4.4. Установки
для нагрева, рекомендованные к применению, приведены в таблицах Е.15 - Е.18
(Приложение Е).
9. Требования к сварным соединениям
9.1. Сварные
соединения газопроводов (стыковые, угловые, нахлесточные) должны быть выполнены
дуговой сваркой по технологиям, регламентированным настоящим стандартом.
Сварные швы должны быть многослойными, без конструктивного непровара.
9.2. Не допускается
применять присадки, непосредственно подаваемые в сварочную дугу или
предварительно закладываемые в разделку кромок свариваемых элементов.
9.3. Внешний вид и
геометрические параметры сварных швов, выполненных односторонней и двухсторонней
дуговой сваркой в поворотном и неповоротном положениях, должны соответствовать
требованиям настоящего стандарта, операционно-технологических карт сборки и
сварки, разработанных по аттестованным технологиям сварки, при этом:
а) корневой
(первый) слой шва не должен иметь недопустимые наружные дефекты (утяжины,
провисы, непровары, несплавления), усиление обратного валика, выполненного
ручной, механизированной, автоматической односторонней сваркой методом STT,
должно быть от 0,5 до 3,0 мм, автоматической односторонней сваркой на медном
подкладном кольце - от 0 до 3,0 мм;
б) подварочный слой
корневого слоя шва должен быть выполнен с плавным переходом к основному металлу
без образования подрезов по кромкам, иметь ширину от 8,0 до 10,0 мм, усиление
от 1,0 до 3,0 мм;
в) внутренний слой
шва, выполненного автоматической двухсторонней сваркой в защитных газах, должен
быть выполнен с плавным переходом к основному металлу без образования подрезов
по кромкам, иметь усиление от 1,0 до 3,0 мм и ширину от 2,0 до 10,0 мм;
г) внутренний слой
шва, выполненного автоматической двухсторонней сваркой под флюсом, должен быть
выполнен с плавным переходом к основному металлу без образования подрезов по
кромкам, иметь усиление от 1,0 до 3,0 мм и ширину в соответствии с требованиями
таблицы 10.29;
д) заполняющие и
облицовочные слои шва могут выполняться за один или несколько проходов;
е) при выполнении
заполняющих и облицовочного слоев шва несколькими валиками каждый последующий
проход (валик) должен перекрывать предыдущий не менее чем на 1/3 часть его
ширины, при этом:
- усиление каждого
валика облицовочного слоя шва не должно превышать 3,0 мм;
- усиление в каждой
межваликовой канавке должно быть не менее 1,0 мм;
- глубина каждой
межваликовой канавки должна быть не более 1,0 мм;
ж)
облицовочный слой шва должен быть выполнен с плавным переходом к основному
металлу без образования подрезов по кромкам и перекрывать основной металл в
каждую сторону на расстояние:
- от 2,5 до 3,0 мм
при ручной сварке покрытыми электродами;
- от 1,5 до 2,5 мм
при механизированной сварке самозащитной порошковой проволокой и автоматической
сварке проволокой сплошного сечения и порошковой проволокой в защитных газах;
з) ширина
облицовочного слоя шва сварных соединений, выполненных автоматической сваркой
под флюсом, должна соответствовать требованиям таблицы 10.28 (двухсторонняя
сварка), таблицы 10.33 (односторонняя сварка);
и) облицовочный
слой шва должен иметь усиление:
- от 1,0 до 3,0 мм
для кольцевых стыковых соединений;
- 3,0 + 2,0 мм для
угловых соединений прямых врезок (тройниковых соединений) с толщиной стенки
патрубка до 10,0 мм включ. и 5,0 + 2,0 мм для угловых соединений прямых врезок
с толщиной стенки патрубка более 10,0 мм;
к) участки
облицовочного слоя с чешуйчатостью, при которой превышение гребня над впадиной
составляет более 1,0 мм, а также участки с превышением усиления шва более 3,0
мм, а также при отсутствии плавного перехода от усиления к основному металлу
должны быть обработаны механическим способом шлифмашинками до достижения требуемых
параметров;
л) величина катета
угловых швов усиливающих накладок прямых врезок (нахлесточных соединений)
должна быть не менее толщины стенки основной трубы;
м) наружная
поверхность сварных швов и прилегающие участки околошовной зоны должны быть
зачищены шлифмашинками до полного удаления шлака и брызг наплавленного металла.
9.4. Методы, объемы
и нормы оценки качества сварных соединений должны соответствовать требованиям
раздела 6 СТО Газпром 2-2.4-083.
9.5. Механические
свойства сварных соединений должны определяться при производственной аттестации
технологий сварки согласно требованиям Приложения А. Виды механических
испытаний сварных соединений при производственной аттестации технологий сварки
приведены в Приложении Б.
9.6. Механические
свойства кольцевых стыковых сварных соединений газопроводов подземной
прокладки, при отсутствии в проектной документации специальных требований,
должны отвечать требованиям:
а) временное
сопротивление разрыву при испытаниях на статическое растяжение должно быть не
ниже нормативного значения временного сопротивления разрыву основного металла
труб, установленного по ТУ или по техническим спецификациям к контракту на
поставку труб;
б) угол изгиба при
испытаниях на статический изгиб, определяемый как среднее арифметическое значение
по результатам испытаний, должен быть не менее 120°, при этом минимальное
значение угла изгиба должно быть не менее 100°;
в) ударная вязкость
металла шва и ЗТВ при испытаниях на ударный изгиб по Шарпи при температуре 20
°C <*>, определяемая как среднее арифметическое по результатам испытаний
трех образцов:
- электросварных
труб, изготовленных по специальным ТУ с применением дуговых способов сварки, из
сталей с классом прочности К60 наружным диаметром от 1020 до 1420 мм включ.
газопроводов с рабочим давлением среды от 8,3 МПа до 9,8 МПа включ. должна быть
не менее 50 Дж/см2 (по Шарпи), при этом минимальное значение ударной вязкости
для одного образца должно быть не менее 37,0 Дж/см2;
- электросварных
труб, изготовленных по специальным ТУ с применением дуговых способов сварки, из
сталей с классом прочности до К60 включ. наружным диаметром до 1420 мм включ.
газопроводов с рабочим давлением среды св. 1,2 МПа до 8,3 МПа должна быть не
менее 34,4 Дж/см2 (по Шарпи), при этом минимальное значение ударной вязкости
для одного образца должно быть не менее 29,4 Дж/см2;
- бесшовных и
электросварных труб, сваренных токами высокой частоты, должна быть не менее
значений, установленных требованиями ГОСТ, ТУ или техническими спецификациями к
контракту на поставку к основному металлу труб, но не менее 24,5 Дж/см2, при
этом минимальное значение ударной вязкости для одного образца должно быть не
менее 19,6 Дж/см2;
г)
твердость металла шва должна быть не более
, зоны
термического влияния - не более
для труб из сталей с классом прочности до К55
включ. и не более
для труб из сталей с классом прочности св. К55
до К60 включ.
--------------------------------
<*>
Испытания сварных соединений проводятся при температуре на 20 °C ниже
минимальной температуры стенки трубы газопровода при эксплуатации, определяемой
проектной документацией.
9.7. Механические
свойства угловых и нахлесточных сварных соединений газопроводов подземной
прокладки, при отсутствии в проектной документации специальных требований,
должны отвечать требованиям:
а) испытания на
излом должны продемонстрировать полный провар, сплавление между слоями шва,
отсутствие внутренних дефектов недопустимых размеров, регламентированных СТО
Газпром 2-2.4-083, при этом дефекты типа флокенов ("рыбьи глаза") не
являются браковочным признаком;
б) твердость
металла шва должна соответствовать требованиям, приведенным в перечислении г)
9.6.
9.8. Специальные
требования к механическим свойствам кольцевых стыковых, угловых и нахлесточных
сварных газопроводов наземной, надземной прокладки, а также прокладки в зонах
сейсмической активности устанавливаются проектной документацией.
9.9. При наличии в
проектной документации специальных требований к механическим свойствам сварных
соединений они должны быть подтверждены результатами производственной
аттестации технологий сварки, регламентированных настоящим стандартом.
10.
Технологии сварочно-монтажных работ
при строительстве,
реконструкции и капитальном
ремонте промысловых
и магистральных газопроводов
10.1. Общие положения
10.1.1. Настоящий
раздел регламентирует требования к порядку выполнения подготовительных,
монтажных и сварочных работ при строительстве, реконструкции и капитальном
ремонте газопроводов.
10.1.2.
Сварка газопроводов должна выполняться одним или несколькими способами по
технологиям, приведенным в 10.4 - 10.6:
а) технологии
ручной дуговой сварки покрытыми электродами (РД);
б) технологии
механизированной сварки проволокой сплошного сечения в углекислом газе (МП);
в) технологии
механизированной сварки самозащитной порошковой проволокой (МПС);
г) технологии
автоматической двухсторонней сварки проволокой сплошного сечения в защитных
газах (ААДП, АПГ);
д) технологии
автоматической односторонней сварки проволокой сплошного сечения в защитных
газах (АПГ);
е) технологии
автоматической односторонней сварки порошковой проволокой в защитных газах
(АПИ);
ж) технологии
двухсторонней автоматической сварки под флюсом (АФ);
з) комбинированной
технологии сварки (РД + МПС, РД + АПИ, РД + АФ, МП + РД, МП + МПС, МП + МПС +
АФ, РАД + РД и др.).
Применение других
способов и технологий сварки допускается при условии положительных результатов
исследовательской аттестации технологии сварки и производственной аттестации
технологии сварки в соответствии с требованиями 4.1, 4.2, опыта применения
технологий при сварке газонефтепроводов в отечественных или международных проектах
и при наличии сервисных центров по обслуживанию, наладке и ремонту сварочного
оборудования.
10.1.3. Сварку труб
протяженных участков газопроводов, указанных в перечислениях 1), а) и 1), б)
1.1, рекомендуется выполнять преимущественно механизированными (МП, МПС),
автоматическими (ААДП, АПГ, АПИ, АФ) способами сварки и их комбинациями
согласно 10.1.2.
10.1.4. Ручную
дуговую сварку покрытыми электродами (РД) рекомендуется применять при сварке
участков газопроводов в случаях невозможности или нецелесообразности применения
механизированных и автоматических способов сварки, выполнении специальных
сварных соединений - захлестов, прямых вставок (катушек), разнотолщинных
стыковых соединений, тройниковых соединений, а также при ремонте сварных
соединений.
10.2. Подготовительные работы, сборка, сварка. Общие требования
10.2.1. Подготовка,
сборка, сварка соединений труб, труб с СДТ, ЗРА должны выполняться в
соответствии с требованиями операционно-технологических карт сборки и сварки,
разработанных по аттестованным технологиям сварки, согласованных главным
сварщиком или лицом, ответственным за сварочное производство, - специалистом
сварочного производства IV-го уровня профессиональной подготовки в соответствии
с ПБ 03-273-99 [4] - и утвержденных организацией, выполняющей сварочные работы.
Типовые формы операционно-технологических карт сборки и сварки приведены в
Приложении Ж.
10.2.2. Дефекты
наружной поверхности механического происхождения (риски, продиры, царапины)
концов труб, СДТ, размеры которых превышают предельно допустимые по специальным
ТУ, ГОСТ, должны быть устранены механическим способом шлифмашинками, при этом
шероховатость поверхности после шлифовки должна быть не более
,
толщина стенки концов труб, СДТ после механической обработки не должна выйти за
пределы минусовых допусков.
10.2.3. Свариваемые
кромки труб с забоинами глубиной до 5,0 мм включ. допускается ремонтировать
сваркой с последующей механической зачисткой мест исправления дефектов до
восстановления необходимого угла скоса и притупления кромки. Ремонт следует
выполнять с обязательным предварительным подогревом дефектного участка до
температуры
для труб с толщиной стенки до 27,0 мм включ.
или до температуры
для труб с толщиной стенки более 27,0 мм
электродами с основным видом покрытия диаметром от 2,5 до 3,25 мм, при этом тип
электродов должен соответствовать классу прочности основного металла труб.
10.2.4. Концы труб
с плавными вмятинами глубиной до 3,5% включ. от номинального диаметра труб, а
также овальностью в пределах значений, регламентированных специальными ТУ,
ГОСТ, следует устранить с помощью безударных разжимных устройств (калибраторов)
гидравлического типа с обязательным местным подогревом независимо от
температуры окружающего воздуха до температуры от +100 °C до +150 °C для труб
из стали с классом прочности до К54 включ. либо до температуры от +150 °C до
+200 °C для труб из стали с классом прочности св. К54. Не допускается правка
концов труб ударным инструментом.
После правки
плавных вмятин, с целью выявления возможных расслоений, необходимо выполнить
ультразвуковой контроль поверхности трубы в границах, превышающих размеры
вмятин на величину не менее 40 мм.
10.2.5. Концы труб
с рисками, задирами, царапинами глубиной более минусового допуска на толщину
стенки, забоинами глубиной более 5,0 мм, наружными дефектами (риски, задиры,
царапины) глубиной более 5,0% от номинальной толщины стенки, плавными вмятинами
глубиной более 3,5% от номинального диаметра труб, а также любыми вмятинами,
исправлению не подлежат и должны быть отрезаны.
10.2.6. После
вырезки дефектного участка трубы с повреждениями, а также во всех случаях резки
труб, с целью выявления возможных расслоений, необходимо выполнить
ультразвуковой контроль всего периметра участка трубы на ширине не менее 40 мм
от резаного торца. При наличии расслоений торец трубы должен быть отрезан на
расстояние не менее 300 мм и произведен повторный ультразвуковой контроль в
аналогичном порядке.
10.2.7. Допускается
производить резку труб, в т.ч. для выполнения специальных сварных соединений
(захлестов и др.), с применением оборудования механизированной орбитальной
газовой или воздушно-плазменной резки с последующей механической обработкой резаных
торцов труб станком подготовки кромок или шлифмашинками до требуемой разделки,
при этом, в случае обработки торцов труб станком подготовки кромок, металл
резаных торцов должен быть предварительно сошлифован механической обработкой
шлифмашинками на глубину от 0,5 до 1,0 мм, а внутреннее усиление заводского шва
должно быть сошлифовано заподлицо с внутренней поверхностью трубы.
10.2.8. В
случае несоответствия заводской разделки кромок труб требованиям технологии
механизированной и автоматической сварки, обработку (переточку) кромок под
сварку необходимо производить механическим способом с применением станков
подготовки кромок типа СПК. Для обеспечения возможности механической обработки
трубы должны быть выложены на инвентарных опорах (лежках), деревянных брусьях,
мешках с песком или др. наполнителем под углом от 15° до 20° к оси траншеи
таким образом, чтобы расстояние между нижней образующей трубы и грунтом было не
менее 450 мм.
После механической
обработки концы труб должны быть защищены от механических повреждений
обечайками, а также для предотвращения попадания внутрь труб влаги, снега и
др., их концы должны быть закрыты инвентарными заглушками.
10.2.9.
Допускается выполнять расточку изнутри трубы (нутрение) шлифмашинками. После
нутрения следует проверить соответствие минимальной фактической толщины стенки
в зоне свариваемых торцов допускам, установленным в ТУ.
10.2.10.
Геометрические параметры торцов труб, СДТ, ЗРА с заводской разделкой кромок
либо обработанных механическим способом, должны соответствовать требованиям
настоящего стандарта (10.4 - 10.8) и операционно-технологических карт сборки и
сварки.
10.2.11. Контроль
размеров подготовки кромок труб под сварку должен выполняться универсальными
шаблонами типа УШС.
10.2.12. Внутренняя
полость труб, СДТ и ЗРА перед сборкой должна быть очищена от попавшего грунта,
снега и других загрязнений. При очистке внутренней полости труб с внутренним
гладкостным покрытием его целостность не должна быть нарушена.
10.2.13.
Свариваемые кромки и прилегающие к ним внутренние и наружные поверхности
свариваемых элементов должны быть зачищены механическим способом шлифмашинкой
на ширину не менее 15 мм.
10.2.14. Усиление
заводских швов снаружи трубы должно быть удалено механическим способом
(шлифованием) до остаточной величины от 0,5 до 1,0 мм на расстоянии от 10 до 15
мм от торца трубы.
10.2.15.
Сборку соединений труб DN
400 и более одной номинальной толщины стенки
следует выполнять с применением внутренних гидравлических или пневматических
центраторов.
10.2.16. Сборку
захлестных соединений труб, прямых вставок (катушек), соединений труб с
патрубками, труб с СДТ, ЗРА, а также в случаях, когда применение внутренних
центраторов нецелесообразно или технически невозможно (например, выполнение
работ на уклонах), сборку соединений следует выполнять с применением
специальных наружных центраторов (многозвенные с ручным или гидромеханическим
приводом, специальные центраторы-корректоры).
10.2.17.
Внутренние и наружные центраторы не должны оставлять недопустимых дефектов,
загрязнений (масляных пятен и др.) на внутренней или наружной поверхности
свариваемых элементов (рисок, царапин и др.).
Внутренние
центраторы, внутренние головки автоматической сварки не должны нарушать
целостность внутреннего покрытия труб с внутренним гладкостным покрытием.
10.2.18. Требования
к геометрическим параметрам разделки кромок и сборки стыковых и угловых сварных
соединений труб, труб с СДТ, ЗРА приведены в соответствующих разделах по
технологиям сварки настоящего стандарта.
10.2.19.
Допускаются смещения кромок при сборке стыковых соединений:
а)
электросварных труб, при этом:
- наружное смещение
стыкуемых кромок с номинальной толщиной стенки 10,0 мм и более не должно
превышать 20% толщины стенки, но не более 3,0 мм;
- наружное смещение
стыкуемых кромок с номинальной толщиной стенки менее 10,0 мм не должно
превышать 40% толщины стенки, но не более 2,0 мм;
б) бесшовных труб,
при этом:
- внутреннее
смещение стыкуемых кромок с номинальной толщиной стенки от 2,0 до 3,2 мм не
должно превышать 0,5 мм;
" св.
3,2 " 4,5 " " 1,0 мм;
" " 4,5 "
8,0 " " 1,5 мм;
" " 8,0 "
10,0 " " 2,0 мм;
- для труб с
номинальной толщиной стенки 10,0 мм и более допускаются локальные внутренние
смещения кромок до 3,0 мм на длине не более 100 мм;
- наружное смещение
не нормируется, однако при выполнении облицовочного слоя шва должен быть
обеспечен плавный переход поверхности шва к основному металлу.
10.2.20. Измерение
величины смещения кромок при сборке следует выполнять универсальными шаблонами
типа УШС по наружным поверхностям или специальными шаблонами по внутренним
поверхностям свариваемых элементов.
10.2.21. При сборке
заводские швы свариваемых труб, СДТ, ЗРА рекомендуется располагать в верхней
половине периметра, при этом их следует смещать друг относительно друга на
расстояние не менее:
- 100 мм
для сварных соединений DN
500 и более;
- 75 мм
" " DN
менее 500.
10.2.22. В случаях
технической невозможности смещения заводских швов при сборке соединений
захлестов и др., расстояние между смежными заводскими швами рекомендуется
согласовать с органами технического надзора Заказчика.
10.2.23. Не
допускается в процессе сборки соединений труб, труб с СДТ, ЗРА с применением
центраторов для установления необходимых параметров сборки (зазора, смещения
кромок) применять ударный инструмент.
10.2.24.
Величина зазора при сборке стыковых соединений труб, труб с СДТ, ЗРА
назначается в зависимости от применяемых способов сварки первого (корневого)
слоя шва, диаметров сварочных материалов и приведена в таблице 10.1.
Таблица 10.1
Величина
зазора при сборке стыковых
соединений труб,
труб с СДТ, ЗРА
В миллиметрах
┌───────────────────────────────┬─────────────────┬───────────────────────┐
│ Способы сварки первого │Диаметр электрода│ Величина зазора │
│ (корневого) слоя шва │
или проволоки │ │
├───────────────────────────────┼─────────────────┼───────────────────────┤
│Ручная
дуговая сварка │
2,5; 2,6; │ 2,0 - 3,0 │
│электродами
с основным видом │ 3,0; 3,20;
3,25 │ 2,5 - 3,5 │
│покрытия
на подъем неповоротных│
│
│
│кольцевых
стыковых соединений │ │ │
│труб,
труб с СДТ, ЗРА │ │ │
├───────────────────────────────┼─────────────────┼───────────────────────┤
│Ручная
дуговая сварка │ 3,2;
│ 1,0 - 2,5 │
│электродами
с целлюлозным видом│ 4,0 │ 1,5 - 2,5 │
│покрытия
на спуск неповоротных │
│
│
│кольцевых
стыковых соединений │ │ │
│труб │ │ │
├───────────────────────────────┼─────────────────┼───────────────────────┤
│Ручная
дуговая сварка │ 3,2
│ 1,5 - 3,5 │
│электродами
с целлюлозным видом│
│ │
│покрытия
на подъем неповоротных│
│
│
│кольцевых
стыковых соединений │ │ │
│труб │ │ │
├───────────────────────────────┼─────────────────┼───────────────────────┤
│Механизированная
сварка │ 1,14
│ 2,5 - 3,5 │
│проволокой
сплошного сечения в │
│
│
│углекислом
газе неповоротных │ │ │
│кольцевых
стыковых соединений │ │ │
│труб │ │ │
├───────────────────────────────┼─────────────────┼───────────────────────┤
│Автоматическая
сварка │ 0,9; 1,0
│Без зазора. Допускается│
│проволокой
сплошного сечения в │
│наличие зазора не более│
│защитных
газах неповоротных │ │0,5 на участках │
│кольцевых
стыковых соединений │ │стыкового
соединения │
│труб
комплексом оборудования │ │длиной до 100 │
│(ф. CRC-Evans AW,
Autoweld │ │ │
│Systems) │ │ │
├───────────────────────────────┼─────────────────┼───────────────────────┤
│Автоматическая сварка │ 1,0
│Без зазора. Допускается│
│плавящимся
электродом в │ │наличие зазора не
более│
│защитных
газах неповоротных │ │0,5 на участках │
│кольцевых
стыковых соединений │ │стыкового
соединения │
│труб
комплексом оборудования │ │длиной до 100 │
│CWS.02
(ф. PWT) │ │ │
├───────────────────────────────┼─────────────────┼───────────────────────┤
│Автоматическая
сварка │ 1,0
│Без зазора. Допускается│
│плавящимся
электродом в │ │наличие зазора не
более│
│защитных
газах неповоротных │ │0,5 на участках │
│кольцевых
стыковых соединений │ │стыкового
соединения │
│труб
комплексом оборудования │ │длиной до 100 │
│Saturnax
(ф. Serimax) │ │ │
├───────────────────────────────┼─────────────────┼───────────────────────┤
│Автоматическая
сварка │ 1,14
│ 2,0 - 3,0 │
│проволокой
сплошного сечения в │ │ │
│углекислом
газе неповоротных │ │ │
│кольцевых
стыковых соединений │ │ │
│труб
сварочными головками │ │ │
│М300-С (М300)
(ф. CRC-Evans AW)│
│
│
├───────────────────────────────┼─────────────────┼───────────────────────┤
│Автоматическая двусторонняя │ 3,0/3,2/4,0
│Без зазора. Допускается│
│сварка
проволокой сплошного │ │наличие зазора не
более│
│сечения
под флюсом поворотных │ │0,5 на участках │
│стыковых
соединений труб на │ │стыкового
соединения │
│трубосварочных
базах типа БТС │ │длиной до 100 │
├───────────────────────────────┴─────────────────┴───────────────────────┤
│ Примечание.
Величина зазора при
ручной аргонодуговой сварке│
│устанавливается
требованиями 10.4.3.3. │
└─────────────────────────────────────────────────────────────────────────┘
10.2.25. Сборку
неповоротных кольцевых стыковых соединений труб на внутреннем центраторе
рекомендуется выполнять без прихваток.
10.2.26. При сборке
неповоротных кольцевых стыковых соединений труб на внутреннем центраторе на
прихватках они должны быть полностью удалены механическим способом шлифмашинкой
в процессе сварки корневого слоя шва.
Количество, размеры
прихваток в зависимости от номинального диаметра свариваемых элементов должны
соответствовать требованиям таблицы 10.2. Прихватки следует выполнять
сварочными материалами, рекомендованными для сварки корневого слоя шва.
Таблица 10.2
Величина зазора при
сборке стыковых
соединений труб,
труб с СДТ, ЗРА
┌──────────────────────────────┬─────────────────────┬────────────────────┐
│ DN (Д ) труб, СДТ, ЗРА │Количество прихваток │ Длина прихватки │
│ у │ не менее, шт. │
не менее, мм │
├──────────────────────────────┼─────────────────────┼────────────────────┤
│До
400 включ. │ 2 │ 20 - 30 │
├──────────────────────────────┼─────────────────────┼────────────────────┤
│Св. 400 до 1000 включ. │ 3 │ 60 - 100 │
├──────────────────────────────┼─────────────────────┼────────────────────┤
│
" 1000 " 1400
" │ 4 │ 100 - 200 │
└──────────────────────────────┴─────────────────────┴────────────────────┘
10.2.27. Сборку
поворотных кольцевых сварных соединений труб на внутреннем центраторе под
автоматическую двустороннюю сварку под флюсом на трубосварочных базах типа БТС
следует выполнять с одной прихваткой длиной не менее 200 мм на режимах сварки
первого наружного слоя шва.
10.2.28. Прихватки
должны располагаться на расстоянии не ближе 100 мм от заводских швов
свариваемых элементов. Начальный и конечный участок каждой прихватки следует
обработать механическим способом шлифмашинкой для обеспечения плавного перехода
при сварке первого (корневого) слоя шва.
10.2.29. До начала
сварки (в т.ч. прихваток) должен производиться предварительный подогрев
свариваемых кромок и прилегающих к ним участков труб, СДТ, ЗРА в соответствии с
требованиями 10.3.
10.2.30.
Освобождать жимки внутреннего центратора следует после завершения сварки:
- всего периметра
первого (корневого) слоя шва ручной дуговой сваркой электродами с основным
видом покрытия, механизированной сваркой проволокой сплошного сечения в углекислом
газе, автоматической двухсторонней сваркой под флюсом;
- корневого слоя
шва и горячего прохода ручной дуговой сваркой электродами с целлюлозным видом
покрытия;
- корневого слоя
шва и горячего прохода (1-го заполняющего слоя) при автоматической сварке
проволокой сплошного сечения в защитных газах <*>.
10.2.31.
При сварке корневого слоя шва соединений, сборка которых выполнена на наружном
звенном центраторе, не допускается освобождать стягивающие механизмы центратора
до выполнения не менее 60% корневого слоя шва, при этом участки корневого слоя
шва следует равномерно располагать по периметру сварного соединения, начало и
конец каждого участка должны быть обработаны механическим способом шлифмашинкой
и иметь плавный переход для сварки оставшейся части корневого слоя шва. При
применении специальных наружных центраторов, позволяющих выполнять сварку
полного периметра корневого слоя шва, корневой слой шва должен быть выполнен по
полному периметру.
10.2.32. Укладку
(опускание) трубы или трубной секции на инвентарные опоры (лежки), деревянные
брусья, мешки с песком или др. наполнителем следует выполнять после сварки:
- корневого слоя
шва ручной дуговой сваркой электродами с основным видом покрытия или
механизированной сваркой проволокой сплошного сечения в углекислом газе;
- корневого слоя
шва и горячего прохода ручной дуговой сваркой электродами с целлюлозным видом
покрытия;
- корневого слоя
шва и горячего прохода (1-го заполняющего слоя) автоматической сваркой
проволокой сплошного сечения в защитных газах <*>.
--------------------------------
<*>
Либо корневого слоя шва при автоматической однодуговой сварке проволокой
сплошного сечения в защитных газах кольцевых стыковых соединений труб с
толщиной стенки менее 19,0 мм.
10.2.33. Расстояние
между нижней образующей трубы и грунтом после укладки (опускания) трубы или
трубной секции на инвентарные опоры (лежки), деревянные брусья, мешки с песком
или др. наполнителем должно быть не менее 450 мм.
10.2.34. Не
допускается производить подъем и опускание труб, трубных секций, а также любые
виды работ, связанные с возможным перемещением газопровода, до полного
окончания сварки захлестных сварных соединений, соединений труб с СДТ, ЗРА,
ремонтных сварных соединений.
10.2.35.
Возбуждение дуги при сварке следует выполнять только с поверхности разделки
кромок свариваемых элементов. Не допускается зажигать дугу на поверхности
металла труб, СДТ и ЗРА.
10.2.36. Сварные
соединения труб DN
1000 и более должны быть зачищены шлифмашинкой
с дисковой проволочной щеткой изнутри трубы для проведения визуального и
измерительного контроля.
10.2.37.
Разнотолщинные сварные соединения труб, труб с СДТ, ЗРА DN
1000 и более должны быть подварены изнутри по
всему периметру сварного соединения.
10.2.38. Сварные
соединения труб одной толщины стенки DN
1000 и более из сталей с классом прочности К55
и выше, в случае выполнения корневого слоя шва электродами с основным видом
покрытия, должны быть подварены изнутри на нижней четверти периметра сварного
шва <*>.
--------------------------------
<*>
Допускается по согласованию с Заказчиком выполнять подварку по полному периметру
сварного шва.
10.2.39. Сварные
соединения труб одной толщины стенки DN
1000 и более в местах видимых изнутри дефектов
корневого слоя шва: смещений кромок более 2,0 мм, непроваров, несплавлений,
подрезов и др. должны быть подварены изнутри.
10.2.40.
Допускается при необходимости выполнять подварку корневого слоя шва сварных
соединений диаметром DN
менее 1000 при наличии технической возможности
выполнения подварочного слоя шва изнутри и инструкции по безопасности
проведения работ, разработанной и утвержденной в установленном порядке
организацией, выполняющей сварочные работы.
10.2.41. Подварка
изнутри корневого слоя шва должна выполняться до начала сварки заполняющих
слоев шва (горячего прохода, 1-го заполняющего слоя). Температура корневого
слоя шва перед выполнением подварочного слоя должна соответствовать требованиям
10.3.6.
10.2.42.
Подварка изнутри корневого слоя шва должна выполняться на подъем электродами с
основным видом покрытия постоянным током обратной полярности. Назначение
сварочных электродов следует производить в соответствии с таблицей Д.4
(Приложение Д).
10.2.43. Количество
слоев сварного шва, проходов (валиков) в каждом слое сварного шва при
многопроходной (многоваликовой) сварке следует назначать в зависимости от
толщины свариваемых кромок труб, СДТ, ЗРА, способа сварки, параметров сборки и
режимов сварки и указывать в операционно-технологической карте сборки и сварки.
10.2.44.
Количество сварщиков ручной дуговой сварки, одновременно выполняющих сварку
соединений труб, СДТ, ЗРА DN
500 и более должно быть не менее 2-х, при этом
рекомендуется для сварных соединений DN
от 1000 до 1200 - не менее 3-х сварщиков, для
сварных соединений DN
1400 - не менее 4-х сварщиков.
10.2.45. Места
начала и окончания сварки каждого слоя сварного шва должны быть удалены от
заводских сварных швов труб, СДТ, ЗРА на расстояние не менее:
- 100 мм
для сварных соединений DN
800 и более;
- 50 мм
" " DN
менее 800.
10.2.46. Места
начала и окончания сварки каждого последующего слоя сварного шва должны быть
смещены относительно мест начала и окончания сварки предыдущего слоя шва, при
этом место начала сварки должно быть смещено на расстояние не менее 30 мм,
место окончания сварки должно быть смещено на расстояние не менее 70 мм. При
многопроходной (многоваликовой) сварке места начала и окончания сварки соседних
проходов (валиков) должны быть смещены друг от друга на расстояние не менее 30
мм.
10.2.47. В процессе
сварки должен осуществляться пооперационный внешний осмотр качества выполнения
слоев шва на отсутствие дефектов. Видимые дефекты швов должны своевременно
устраняться. Пооперационный внешний осмотр должен осуществляться
непосредственным руководителем сварочных работ (мастером, прорабом), являющимся
специалистом сварочного производства не ниже II-го уровня профессиональной
подготовки в соответствии с ПБ 03-273-99 [4].
10.2.48. В процессе
сварки каждый слой шва и свариваемые кромки, а также после завершения сварки
облицовочный слой и прилегающие к нему поверхности труб на расстоянии не менее
10 мм должны быть зачищены от шлака и брызг наплавленного металла механическим
способом шлифмашинками.
10.2.49.
Специальные сварные соединения захлестов, прямых вставок (катушек),
разнотолщинных труб, СДТ, ЗРА, ремонтные сварные соединения должны выполняться
за один цикл без перерывов до полного завершения работ. Для стыковых соединений
труб в случае технических причин временного перерыва в работе должны быть
выполнены следующие требования:
- сварное соединение
должно быть выполнено не менее чем на 2/3 толщины стенки;
- незавершенное
сварное соединение должно быть накрыто влагонепроницаемым теплоизолирующим
поясом, обеспечивающим замедленное и равномерное остывание;
- перед
возобновлением сварки температура сварного шва должна соответствовать
требованиям 10.3.11;
- сварное
соединение должно быть полностью завершено в течение 24 ч после начала
временного перерыва.
10.2.50. После
завершения сварки всех слоев шва неповоротных кольцевых стыковых соединений
труб, СДТ сваренный газопровод, до укладки в траншею, может быть переложен с
инвентарных опор (лежек) на деревянные брусья, мешки с песком или др.
наполнителем или земляные призмы, накрытые специальным покрытием,
обеспечивающим сохранность изоляции (по согласованию с Заказчиком).
10.2.51. По
окончании сварки при температуре воздуха ниже +5 °C и/или при наличии осадков
сварные соединения должны быть накрыты влагонепроницаемым теплоизолирующим
поясом до полного остывания. В непосредственной близости от выполненного сварного
шва несмываемой краской должны быть нанесены клейма сварщиков, операторов или
бригады сварщиков, операторов.
10.2.52.
Специальные сварные соединения (захлестные соединения, прямые вставки
(катушки), разнотолщинные соединения, соединения труб с СДТ, ЗРА, ремонт
кольцевых стыковых и угловых сварных соединений труб, труб с СДТ, ЗРА) должны
выполняться в соответствии с требованиями 10.7.
10.2.53.
Присоединение обратного кабеля к свариваемым трубам, СДТ, ЗРА должно
выполняться с помощью специальных устройств, обеспечивающих надежный контакт с
телом трубы, СДТ, ЗРА и исключающих образование искрений на теле трубы при сварке.
Конструкция устройств должна обеспечивать токоподвод преимущественно в разделку
кромок труб. Не допускается приваривать к телу трубы какие-либо крепежные
элементы обратного кабеля.
10.2.54. Не
допускается выполнять сварку двух- или трехтрубных секций с различной
нормативной толщиной стенки односторонней или двухсторонней автоматической
сваркой под флюсом.
10.3. Предварительный, сопутствующий (межслойный) подогрев
10.3.1.
Порядок проведения работ по предварительному, сопутствующему (межслойному)
подогреву, требования к персоналу определяются нормативными документами ОАО
"Газпром" и настоящим разделом.
10.3.2. Для
предварительного, сопутствующего (межслойного) подогрева кромок свариваемых
соединений следует применять:
- при толщинах
стенки до 17,0 мм - газопламенные нагревательные устройства (кольцевые и
плоские газовые подогреватели, однопламенные горелки и др.), а также установки
индукционного нагрева, радиационного нагрева способом электросопротивления или
нагрева с применением электронагревателей комбинированного действия;
- при толщинах
стенки св. 17,0 до 22,0 мм при температуре воздуха выше 0 °C - установки
индукционного нагрева, радиационного нагрева способом электросопротивления,
нагрева с применением электронагревателей комбинированного действия или
газопламенные нагревательные устройства (кольцевые газовые подогреватели,
однопламенные горелки и др.);
- при толщинах
стенки св. 17,0 до 22,0 мм при отрицательных температурах воздуха - установки
индукционного нагрева, радиационного нагрева способом электросопротивления или
нагрева с применением электронагревателей комбинированного действия;
- при толщинах
стенки св. 22,0 мм при любых температурах воздуха - установки индукционного
нагрева.
10.3.3. Выбор
оборудования для предварительного и сопутствующего (межслойного) подогрева
выполняется производителями сварочных работ. Оборудование должно обеспечивать
равномерный предварительный подогрев свариваемых соединений по толщине стенки и
периметру в зоне шириной не менее 150 мм (т.е. не менее 75 мм в каждую сторону
от свариваемых кромок) и, если необходимо, подогрев в процессе выполнения
прихваток и межслойный подогрев в процессе сварки.
10.3.4. При
проведении подогрева установками индукционного нагрева, радиационного нагрева
способом электросопротивления, нагрева с применением электронагревателей
комбинированного действия в случаях прекращения энергообеспечения или при
выходе из строя установок нагрева допускается выполнять нагрев газопламенными
нагревательными устройствами (кольцевыми газовыми подогревателями,
однопламенными горелками и др.) до возобновления энергообеспечения или замены
вышедшего из строя оборудования, но не более чем до конца рабочей смены или
полного завершения сварного шва.
10.3.5. Подогрев не
должен нарушать целостность изоляции. При применении газопламенных
нагревательных устройств (горелок) следует применять термоизоляционные
материалы (термоизолирующие пояса) и/или боковые ограничители пламени.
Максимальная температура нагрева трубы в месте начала заводского изоляционного
покрытия труб не должна превышать +100 °C.
10.3.6.
Температура предварительного подогрева свариваемых кромок труб, СДТ, ЗРА перед
выполнением прихваток, первого (корневого) слоя шва должна соответствовать:
а) требованиям
таблицы 10.3 - для ручной дуговой сварки электродами с основным видом покрытия
и механизированной сваркой проволокой сплошного сечения в углекислом газе;
б) требованиям
таблицы 10.4 - для ручной дуговой сварки электродами с целлюлозным видом
покрытия;
в)
независимо от температуры окружающего воздуха
- для автоматической двухсторонней сварки проволокой сплошного сечения в
защитных газах неповоротных кольцевых стыковых соединений труб комплексом
оборудования фирм CRC-Evans AW, Autoweld Systems, а также для автоматической
односторонней сварки проволокой сплошного сечения в защитных газах сварочными
головками M300-C, M300 фирмы CRC-Evans AW, комплексами оборудования CWS.02
фирмы PWT, Saturnax фирмы Serimax;
г)
при температуре окружающего воздуха ниже 0 °C
и/или при наличии влаги на свариваемых кромках - для автоматической
двухсторонней сварки под флюсом поворотных кольцевых стыковых соединений труб
на трубосварочных базах типа БТС;
д)
независимо от температуры окружающего воздуха
- при ремонте сварных соединений с толщинами стенок до 27,0 мм включ.;
е)
независимо от температуры окружающего воздуха
- при ремонте сварных соединений с толщинами стенок св. 27,0 мм;
ж) требованиям
таблицы 10.5 - при сварке труб с ЗРА.
Таблица 10.3
Температура
предварительного подогрева при ручной
дуговой сварке
электродами с основным видом покрытия
и механизированной
сварке проволокой сплошного
сечения в
углекислом газе первого (корневого) слоя
шва, прихваток
соединений труб, труб с СДТ
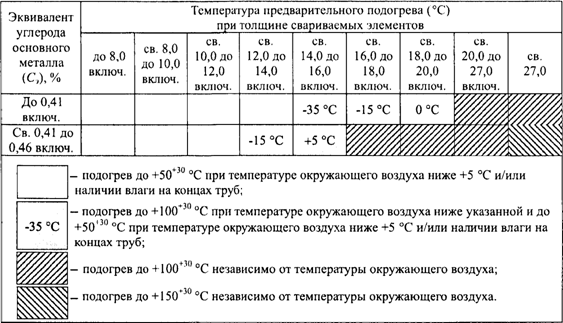
Таблица 10.4
Температура
предварительного подогрева
при сварке
корневого слоя шва соединений труб
электродами с
целлюлозным видом покрытия
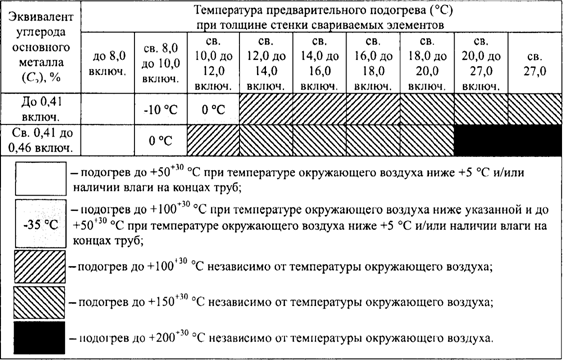
Таблица 10.5
Температура
предварительного подогрева при сварке
прихваток, первого
(корневого) слоя шва соединений с ЗРА
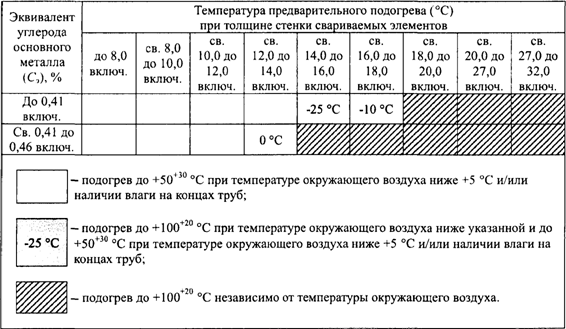
10.3.7. При
сварке труб, труб с СДТ, ЗРА с различными толщинами стенок или имеющих
различное значение эквивалента углерода
температура предварительного подогрева должна
соответствовать максимальному значению, требуемому для одного из свариваемых
элементов.
10.3.8. Контроль
температуры предварительного подогрева свариваемых соединений газопламенными
нагревательными устройствами должен выполняться непосредственно перед выполнением
прихваток, первого (корневого) слоя шва контактными приборами на наружной
поверхности в местах, равномерно расположенных по периметру, на расстоянии от
10 до 15 мм в обе стороны от свариваемых кромок.
10.3.9. Процесс
подогрева кромок свариваемых соединений установками индукционного нагрева,
радиационного нагрева способом электросопротивления и нагрева с применением
электронагревателей комбинированного действия должен контролироваться в
автоматическом режиме, при этом контроль температуры подогрева должен
выполняться в местах, равномерно расположенных по периметру, с применением
термопар и записью температуры подогрева на диаграмме автоматического
регистрирующего потенциометра. Одна из этих термопар должна быть регулирующей и
устанавливаться в зените газопровода. Места крепления термопар должны
находиться на расстоянии не более 25 мм от края предполагаемого сварного шва
вне зоны сварочной дуги.
10.3.10. Количество
мест контроля температуры подогрева рекомендуется назначать по количеству
прихваток.
10.3.11. В
случае снижения температуры кромок свариваемых элементов в процессе сборки и
сварки ниже значений, регламентированных 10.3.6, необходимо выполнить подогрев
до регламентированной температуры предварительного подогрева.
10.3.12.
Допускается при снижении температуры предварительного подогрева свариваемых
кромок не более чем на 10 °C ниже регламентированного значения +50 °C, не более
чем на 20 °C ниже регламентированного значения +100 °C и не более чем на 30 °C
ниже регламентированных значений +150 °C и +200 °C выполнять подогрев
газопламенными устройствами (ручными, кольцевыми, одно- и многосопловыми
горелками).
10.3.13. В процессе
сварки температура предыдущего слоя сварного шва перед наложением последующего
слоя должна быть в интервале от +50 °C до +250 °C. При механизированной сварке
самозащитной порошковой проволокой температура предыдущего слоя сварного шва
перед наложением последующего слоя должна быть в интервале от +50 °C до +200
°C. Если температура опустилась ниже +50 °C, следует произвести сопутствующий
(межслойный) подогрев до температуры
.
10.3.14.
Допускается для достижения необходимой межслойной температуры перед наложением
последующего слоя (заполняющего, облицовочного) дополнительно подогревать
сварные соединения кольцевыми и однопламенными (одно- и многосопловыми)
газопламенными горелками.
10.4. Ручная дуговая сварка
10.4.1.
Ручная дуговая сварка электродами с основным видом покрытия
10.4.1.1. Ручная
дуговая сварка электродами с основным видом покрытия рекомендуется для сварки
всех слоев шва неповоротных кольцевых стыковых соединений труб диаметром от 25
до 1420 мм, а также специальных сварных соединений газопроводов (захлесты,
прямые вставки (катушки), разнотолщинные соединения труб, СДТ, ЗРА, угловые
соединения - прямые врезки, ремонт кольцевых стыковых и угловых сварных
соединений труб, СДТ, ЗРА).
10.4.1.2. Ручная
дуговая сварка электродами с основным видом покрытия может быть использована в
составе следующих комбинированных технологий сварки:
- корневой слой шва
- электродами с основным видом покрытия, заполняющие и облицовочный слои шва -
механизированной сваркой самозащитной порошковой проволокой;
- корневой слой шва
- электродами с основным видом покрытия, заполняющие и облицовочный слои шва -
автоматической сваркой под флюсом на трубосварочной базе ССТ-ПАУ;
- корневой слой шва
- электродами с основным видом покрытия, заполняющие и облицовочный слои шва -
автоматическая сварка порошковой проволокой в защитных газах сварочными
головками M300-C, M300 фирмы CRC-Evans AW;
- корневой слой шва
- электродами с основным видом покрытия, первый заполняющий слой -
механизированной сваркой самозащитной порошковой проволокой, последующие
заполняющие и облицовочный слои - автоматической сваркой под флюсом на
трубосварочной базе ССТ-ПАУ.
10.4.1.3. Для
ручной дуговой сварки электродами с основным видом покрытия должны применяться
сварочные агрегаты, сварочные установки, укомплектованные источниками
сварочного тока и вспомогательным оборудованием, отвечающие специальным
требованиям и условиям эксплуатации, приведенным в разделе 8.
10.4.1.4. Электроды
с основным видом покрытия, рекомендованные к применению для ручной дуговой
сварки, приведены в таблице Д.4 (Приложение Д).
10.4.1.5.
Подготовка, сборка и предварительный подогрев соединений труб, СДТ, ЗРА должны
выполняться в соответствии с требованиями 10.2, 10.3.
10.4.1.6.
Температуру предварительного подогрева кромок труб при сварке корневого слоя
шва электродами с основным видом покрытия следует назначать по таблице 10.3.
10.4.1.7. Ручная
дуговая сварка электродами с основным видом покрытия выполняется:
- корневого и
подварочного слоев шва - на подъем постоянным током обратной полярности
<*>;
- заполняющих и
облицовочного слоев шва - на подъем или на спуск постоянным током обратной
полярности.
--------------------------------
<*>
Допускается выполнять сварку корневого слоя шва постоянным током прямой
полярности стыковых соединений труб с заниженным зазором для обеспечения проплава
свариваемых кромок.
10.4.1.8.
Рекомендуемые режимы ручной дуговой сварки электродами с основным видом
покрытия на подъем приведены в таблице 10.6, на спуск - в таблице 10.7.
Таблица 10.6
Рекомендуемые
режимы ручной дуговой сварки
электродами с
основным видом покрытия на подъем
┌───────────────┬──────────────┬──────────────────────────────────────────┐
│ Слои шва
│ Диаметр │ Сварочный ток (А) в положении при
сварке │
│ │электрода, мм
├─────────────┬──────────────┬─────────────┤
│ │ │ нижнее
│ вертикальное │ потолочное
│
├───────────────┼──────────────┼─────────────┼──────────────┼─────────────┤
│Корневой │
2,0 - 2,6 │ 80 - 90
│ 70 - 90 │
70 - 80 │
│ │
3,0 - 3,25 │ 90 - 120
│ 90 - 110 │
80 - 110 │
├───────────────┼──────────────┼─────────────┼──────────────┼─────────────┤
│Подварочный │
3,0 - 3,25 │ 90 - 120
│ 90 - 110 │
80 - 110 │
│ │ (4,0)
│ 130 - 180 │
110 - 170 │ 110 - 150
│
├───────────────┼──────────────┼─────────────┼──────────────┼─────────────┤
│Заполняющие: │ │ │ │ │
│
- первый │ 3,0 - 3,25
│ 90 - 120 │
90 - 110 │ 80 - 110
│
│
- последующие │ 3,0 - 3,25 │
100 - 120 │ 90 - 110
│ 80 - 110 │
│ │ 4,0
│ 130 - 180 │
110 - 170 │ 110 - 150
│
├───────────────┼──────────────┼─────────────┼──────────────┼─────────────┤
│Облицовочные │
3,0 - 3,25 │ 100 - 120
│ 90 - 110 │
80 - 110 │
│ │ 4,0
│ 130 - 180 │
110 - 170 │ 110 - 150
│
└───────────────┴──────────────┴─────────────┴──────────────┴─────────────┘
Таблица 10.7
Рекомендуемые
режимы ручной дуговой сварки
электродами с
основным видом покрытия на спуск
┌────────────────┬──────────────┬─────────────────────────────────────────┐
│ Слои шва
│ Диаметр │Сварочный ток (А) в положении при
сварке │
│ │электрода, мм ├─────────────┬─────────────┬─────────────┤
│ │ │ нижнее
│вертикальное │ потолочное
│
├────────────────┼──────────────┼─────────────┼─────────────┼─────────────┤
│Заполняющие: │
3,2 │ 110 - 160
│ 120 - 150 │
110 - 150 │
│
- первый │ 3,2
│ 120 - 160 │
120 - 150 │ 110 - 150
│
│
- последующие │ 4,0
│ 190 - 210 │
190 - 200 │ 180 - 200
│
│ │ 4,5
│ 210 - 240 │
210 - 230 │ 200 - 230
│
├────────────────┼──────────────┼─────────────┼─────────────┼─────────────┤
│Облицовочные │
3,2 │ 190 - 210
│ 190 - 200 │
180 - 200 │
│ │ 4,0
│ 210 - 240 │
210 - 230 │ 200 - 230
│
└────────────────┴──────────────┴─────────────┴─────────────┴─────────────┘
10.4.1.9.
Облицовочный слой шва следует выполнять при толщинах стенки трубы, СДТ, ЗРА:
- до 16
мм - за один проход;
- от 16 до
20 мм - за один-два прохода;
- более 20
мм - за два-три прохода.
10.4.1.10.
Минимальное число слоев шва при сварке электродами с основным видом покрытия
приведено в таблице 10.8. Число слоев указано без учета подварочного слоя.
Таблица 10.8
Минимальное
число слоев шва при сварке
электродами с
основным видом покрытия
┌───────────────────────────┬─────────────────────────────────────────────┐
│
Толщина стенки трубы, мм │ Минимальное число слоев │
├───────────────────────────┼─────────────────────────────────────────────┤
│До
7,0 включ. │ 2 │
├───────────────────────────┼─────────────────────────────────────────────┤
│Св. 7,0 до 12,0 включ. │ 3 │
├───────────────────────────┼─────────────────────────────────────────────┤
│
" 12,0 " 15,0
" │ 4 │
├───────────────────────────┼─────────────────────────────────────────────┤
│
" 15,0 " 18,0
" │ 5 │
├───────────────────────────┼─────────────────────────────────────────────┤
│
" 18,0 " 20,0
" │ 6 │
├───────────────────────────┼─────────────────────────────────────────────┤
│Св.
20,0 │В соответствии
с операционно-технологической │
│ │картой сборки
и сварки, но не менее 6 │
└───────────────────────────┴─────────────────────────────────────────────┘
10.4.1.11. Ручную
дуговую сварку электродами с основным видом покрытия на спуск следует выполнять
с учетом следующих особенностей:
- сварка ведется
короткой дугой;
- не допускается
повторное зажигание одного и того же электрода;
- сварка второго и
последующих заполняющих слоев шва выполняется за два-три прохода (валика), при
этом в процессе сварки каждый валик должен быть зачищен механическим способом;
- последний
заполняющий слой следует выводить заподлицо с разделкой кромок с оплавлением ее
краев;
- облицовочный слой
следует выполнять с поперечными колебаниями, при этом минимальная амплитуда
колебаний должна составлять два диаметра электрода.
10.4.2.
Ручная дуговая сварка электродами с целлюлозным видом покрытия
10.4.2.1. Ручная
дуговая сварка электродами с целлюлозным видом покрытия рекомендуется для
сварки на спуск корневого слоя и горячего прохода шва неповоротных кольцевых
стыковых соединений труб диаметром от 530 до 1420 мм.
Допускается
выполнять ручную дуговую сварку электродами с целлюлозным видом на подъем
корневого слоя шва захлестных сварных соединений, прямых вставок (катушек) при
условии прохождения производственной аттестации указанной технологии и при
наличии в аттестационных удостоверениях и протоколах допускных испытаний
сварщиков разрешения (допуска) для выполнения ручной дуговой сварки на подъем
электродами с целлюлозным видом покрытия.
10.4.2.2. Ручная
дуговая сварка электродами с целлюлозным видом покрытия может быть использована
в составе следующих комбинированных технологий сварки:
- корневой слой шва
и горячий проход - электродами с целлюлозным видом покрытия; заполняющие и
облицовочный слои шва - механизированной сваркой самозащитной порошковой
проволокой;
- корневой слой шва
- электродами с целлюлозным видом покрытия; горячий проход, заполняющие и
облицовочный слои шва - механизированной сваркой самозащитной порошковой
проволокой;
- корневой слой шва
и горячий проход - электродами с целлюлозным видом покрытия, последующие слои -
электродами с основным видом покрытия на подъем;
- сварка на
трубосварочной базе ССТ-ПАУ электродами с целлюлозным видом покрытия корневого
слоя шва и горячего прохода, электродами с основным видом покрытия 1-го
заполняющего или подварочного слоев шва и автоматической сваркой под слоем
флюса заполняющих и облицовочного слоев шва.
10.4.2.3. Для
ручной дуговой сварки электродами с целлюлозным видом покрытия должны
применяться сварочные агрегаты, сварочные установки, укомплектованные
источниками сварочного тока и вспомогательным оборудованием, отвечающие
специальным требованиям и условиям эксплуатации, приведенным в разделе 8.
10.4.2.4. Электроды
с целлюлозным видом покрытия, рекомендованные к применению для ручной дуговой
сварки, приведены в таблице Д.5 (Приложение Д).
10.4.2.5.
Подготовка, сборка и предварительный подогрев соединений труб должны
выполняться в соответствии с требованиями 10.2, 10.3.
10.4.2.6.
Температуру предварительного подогрева кромок труб при сварке корневого слоя
шва электродами с целлюлозным видом покрытия следует назначать по таблице 10.4.
10.4.2.7. Ручная
дуговая сварка электродами с целлюлозным видом покрытия корневого слоя шва
выполняется на спуск постоянным током прямой или обратной полярности, горячего
прохода - на спуск постоянным током обратной полярности.
10.4.2.8.
Рекомендуемые режимы ручной дуговой сварки электродами с целлюлозным видом
покрытия приведены в таблице 10.9.
Таблица 10.9
Рекомендуемые
режимы ручной дуговой сварки
электродами с
целлюлозным видом покрытия
┌───────────────┬──────────────┬──────────────────────────────────────────┐
│ Слои шва
│ Диаметр │ Сварочный ток (А) в положении при
сварке │
│ │электрода, мм
├────────────┬─────────────┬───────────────┤
│ │ │ нижнее
│вертикальное │
потолочное │
├───────────────┼──────────────┼────────────┼─────────────┼───────────────┤
│Корневой │
3,2 <*> │ 100 -
120 │ 100 - 120
│ 90 - 110 │
│ │ 4,0
│ 120 - 160 │ 120 - 160
│ 100 - 140 │
├───────────────┼──────────────┼────────────┼─────────────┼───────────────┤
│Горячий
проход │ 4,0 │ 140 - 180 │
150 - 170 │ 140 - 170
│
├───────────────┴──────────────┴────────────┴─────────────┴───────────────┤
│ <*> Электроды диаметром 3,2 мм
рекомендуются только для
сварки на│
│подъем
корневого слоя шва захлестных сварных соединений, прямых
вставок│
│(катушек).
│
└─────────────────────────────────────────────────────────────────────────┘
10.4.2.9. Места
обрыва или прерывания дуги, "замки" при сварке корневого слоя шва
электродами с целлюлозным видом покрытия должны быть обработаны механическим
способом шлифмашинкой.
10.4.2.10. При
вынужденных перерывах во время сварки корневого слоя шва необходимо
поддерживать температуру торцов труб на уровне требуемой температуры
предварительного подогрева.
10.4.2.11. После
сварки корневого слоя шва его следует обработать механическим способом
шлифмашинками для вскрытия шлаковых "карманов" и удаления чрезмерного
усиления шва.
10.4.2.12. После
зачистки корневого слоя шва следует выполнить сварку электродами с целлюлозным
видом покрытия горячего прохода. Допускается выполнять горячий проход
механизированной сваркой самозащитной порошковой проволокой на спуск в
соответствии с требованиями 10.5.
10.4.2.13. Интервал
времени между окончанием сварки корневого слоя шва и началом выполнения
горячего прохода должен быть не более 5 мин.
10.4.2.14. В
процессе сварки горячего прохода температура корневого слоя шва должна быть в
интервале от +70 °C до +250 °C. Если температура опустилась ниже +70 °C,
следует произвести сопутствующий (межслойный) подогрев до температуры
.
10.4.2.15. После
окончания сварки горячего прохода его следует обработать механическим способом
шлифмашинкой с набором дисковых проволочных щеток.
10.4.2.16.
Минимальное число слоев сварного шва, выполненного комбинированной технологией
сварки: ручная дуговая сварка электродами с целлюлозным видом покрытия
корневого слоя шва и горячего прохода и ручная дуговая сварка электродами с
основным видом покрытия заполняющих и облицовочного слоев шва, на один слой
больше, указанного в таблице 10.8.
10.4.2.17. Ручная
дуговая сварка электродами с целлюлозным видом покрытия может применяться при
температуре окружающего воздуха не ниже -20 °C при условии полного соблюдения
требований к температуре предварительного и сопутствующего (межслойного)
подогрева.
10.4.3. Ручная
аргонодуговая сварка неплавящимся электродом
10.4.3.1. Ручная
аргонодуговая сварка неплавящимся электродом (РАД) рекомендуется для сварки
всех слоев шва неповоротных кольцевых стыковых и угловых соединений труб, труб
с СДТ и ЗРА DN
от 20 до 80 с толщиной стенки от 2,0 до 4,0
мм, а также для сварки корневого слоя шва неповоротных кольцевых стыковых и
угловых соединений труб DN
от 50 до 80 с толщиной стенки от 4,0 до 10,0
мм.
10.4.3.2.
Подготовительные работы, сборка, предварительный подогрев должны выполняться в
соответствии с требованиями 10.1.
10.4.3.3.
Величина зазора при сборке неповоротных кольцевых стыковых и угловых соединений
труб, СДТ, ЗРА должна составлять:
-
для соединений с толщиной стенки от 2,0 до 3,0
мм;
- (1,5 +/- 0,5) мм
для соединений с толщиной стенки св. 3,0 до 4,0 мм.
Внутреннее смещение
кромок в обоих случаях должно быть не более 0,5 мм.
10.4.3.4. В
качестве неплавящегося электрода рекомендуется применять прутки
лантанированного вольфрама диаметром 2,0 мм. Для легкого возбуждения дуги и
улучшения стабильности ее горения электрод должен быть заточен на конус. Форма
заточки представлена на рисунке 10.1.
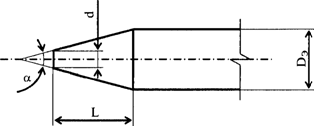
- угол конуса от 28° до 30°;
- диаметр электрода;
L - длина
конической части (5 - 6)
;
d - диаметр
притупления от 0,2 до 0,5 мм
Рисунок 10.1. Форма
заточки вольфрамового электрода
10.4.3.5. В
качестве защитного газа следует применять аргон высшего сорта по ГОСТ 10157.
Перед использованием баллона с аргоном необходимо проверить качество газа путем
выполнения наплавки длиной от 100 до 150 мм на поверхность пластины. Внешним
осмотром наплавки определяют надежность газовой защиты. В случае обнаружения
пор газ бракуют.
10.4.3.6. В
качестве присадочного металла следует применять сварочную проволоку диаметром
от 1,6 до 2,0 мм марки Св-08Г2С по ГОСТ 2246.
10.4.3.7. Для
ручной аргонодуговой сварки неплавящимся электродом следует использовать
источники питания постоянного тока с падающей вольт-амперной характеристикой в
комплекте с малогабаритными горелками, обеспечивающими доступ к месту сварки в
стесненных условиях. Сварочные выпрямители, прошедшие аттестацию и рекомендованные
к применению, приведены в таблицах Е.8, Е.9 (Приложение Е).
10.4.3.8. Прихватка
соединений труб должна производиться тем же сварщиком, который будет выполнять
сварку корневого слоя шва. Рекомендуется выполнять две прихватки длиной от 10
до 15 мм, располагающиеся симметрично по периметру кромок свариваемых
элементов. В качестве присадочного металла должна использоваться та же
проволока, что и для сварки корневого слоя шва.
10.4.3.9. Ручную
аргонодуговую сварку неплавящимся электродом необходимо выполнять постоянным
током прямой полярности короткой дугой. Зажигание и гашение дуги следует
производить на свариваемой кромке или на выполненном ранее шве на расстоянии от
20 до 25 мм позади кратера.
10.4.3.10. Подачу
аргона из горелки следует начинать на 15 - 20 секунд раньше момента зажигания
дуги и прекращать через 10 - 15 секунд после обрыва дуги. В течение этих
интервалов времени струю аргона следует направлять на кратер.
10.4.3.11. В
начальный момент сварки после возбуждения дуги необходимо подогреть и оплавить
кромки труб и конец присадочного прутка. После образования сварочной ванны
можно начинать поступательное движение горелки. В процессе сварки корневого
слоя необходимо следить за полным проплавлением кромок и отсутствием непровара.
Степень проплавления можно оценить по форме ванны расплавленного металла:
хорошему проплавлению соответствует ванна, вытянутая в сторону направления
сварки (рисунок 10.2 а), недостаточному - круглая или овальная (рисунок 10.2
б).
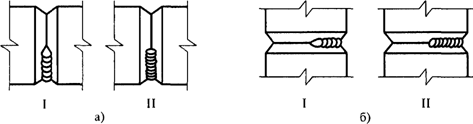
Рисунок 10.2. Форма
сварочной ванны при полном (I)
и недостаточном
(II) проплавлении корня шва ручной
аргонодуговой
сваркой неплавящимся электродом
вертикального (а) и
горизонтального (б)
кольцевых стыковых
соединений труб
10.4.3.12.
Минимальное количество слоев шва для стыковых соединений труб с толщиной стенки
от 2,0 до 4,0 мм - два. Рекомендуемая высота слоя (валика) составляет от 2,0 до
2,5 мм. Направление и порядок сварки вертикального и горизонтального
неповоротных стыковых сварных соединений должны соответствовать рисунку 10.3.
Длина сваренных участков не должна превышать 200 мм. При большей длине участка
шва его необходимо выполнять обратноступенчатым способом.
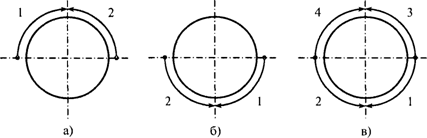
а) корневой слой
шва вертикального стыкового соединения;
б) второй и
последующие слои шва вертикального стыкового соединения;
в) корневой и
последующие слои шва горизонтального стыкового соединения;
1; 2; 3; 4 -
последовательность выполнения участков и слоев шва
Рисунок 10.3.
Порядок сварки неповоротного кольцевого
стыкового
соединения труб одним сварщиком
10.4.3.13. При
изготовлении укрупненных заготовок допускается поворот стыковых соединений труб
в удобную для сварщика позицию, чтобы избежать сварки в потолочном положении.
Если периодический поворот свариваемых труб, СДТ, ЗРА затруднителен, то сварка
корневого слоя может быть выполнена в два поворота согласно схеме,
представленной на рисунке 10.4.
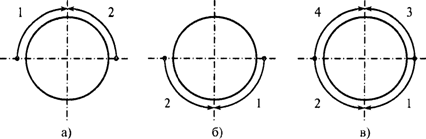
1; 2; 3; 4 -
последовательность сварки участков корневого слоя шва.
а) сварка I и II
четвертей;
б) поворот
свариваемых труб на 180°;
в) сварка III и IV
четвертей
Рисунок 10.4. Схема
сварки корневого слоя шва вертикального
кольцевого
стыкового соединения труб в два поворота
10.4.3.14. Взаимное
расположение горелки и проволоки при сварке вертикального и горизонтального
стыковых сварных соединений представлено на рисунке 10.5. Угол (между
электродом и радиусом трубы в месте сварки) зависит от качества защиты и
конструктивных особенностей горелки: для горелок, приспособленных для сварки в
стесненных условиях и в глубокую разделку, угол
может изменяться в пределах от 0° до 70°, для
остальных горелок с канальной схемой истечения газа - в пределах от 0° до 25°.
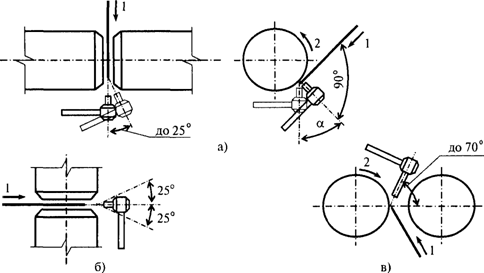
а) сварка
вертикального стыкового соединения в обычных условиях;
б) сварка
горизонтального стыкового соединения в обычных условиях;
в) сварка
горизонтального стыкового соединения в стесненных условиях горелкой с
удлиненным мундштуком;
1 - направление
подачи проволоки;
2 - направление
сварки
Рисунок
10.5. Схема расположения горелки
и присадочной
проволоки при ручной аргонодуговой
сварке неплавящимся
электродом вертикальных
и горизонтальных
кольцевых стыковых соединений труб
10.5. Механизированная сварка
10.5.1.
Механизированная сварка шва проволокой сплошного сечения в углекислом газе
10.5.1.1. Общие
требования
Механизированная
сварка неповоротных кольцевых стыковых соединений труб одной толщины стенки
выполняется по комбинированной технологии сварки, при которой сварка корневого
слоя шва выполняется проволокой сплошного сечения в среде углекислого газа,
сварка заполняющих и облицовочного слоев шва - самозащитной порошковой
проволокой.
Механизированная
сварка проволокой сплошного сечения в углекислом газе (МП) рекомендуется для
сварки корневого слоя шва неповоротных кольцевых стыковых соединений труб одной
толщины стенки линейной части магистральных газопроводов диаметром от 325 до
1420 мм с толщинами стенок от 6,0 до 32,0 мм.
Для
механизированной сварки корневого слоя шва в углекислом газе должны применяться
сварочные агрегаты, сварочные установки, укомплектованные источниками
сварочного тока, механизмами подачи сварочной проволоки, сварочными горелками,
газовыми рампами с баллонами углекислого газа и вспомогательным оборудованием,
отвечающие специальным требованиям и условиям эксплуатации, приведенным в
разделе 8.
Проволоки сплошного
сечения, рекомендованные к применению для механизированной сварки в углекислом
газе, приведены в таблице Д.11 (Приложение Д).
Специальные
источники сварочного тока должны обеспечивать импульсно-дуговой режим
механизированной сварки и отвечать требованиям к установке следующих
параметров:
- скорость подачи
сварочной проволоки;
- режим работы
сварочной горелки;
- длительность
предварительной и послесварочной подачи газа.
Кромки труб для
механизированной сварки корневого слоя шва проволокой сплошного сечения в
углекислом газе должны иметь нормативную заводскую разделку либо должны быть
подготовлены механическим способом станками подготовки кромок типа СПК с
нормативным притуплением. Допускается для механизированной импульсно-дуговой
сварки методом STT выполнять подготовку кромок труб орбитальной газовой резкой
с последующей обработкой механическим способом шлифмашинками.
Для труб с толщиной
стенки до 13,0 мм следует применять стандартные сопла горелки диаметром 12,7 мм
или зауженные - диаметром 9,6 мм. Для труб с толщиной стенок более 13,0 мм
следует применять зауженные сопла диаметром 9,6 мм.
Для улучшения
обзора зоны сварки следует выдвигать наконечник горелки из сопла на расстояние
до 6,0 мм.
Для предотвращения
замерзания газовые редукторы баллонов с углекислым газом следует оснастить
подогревателями.
Количество
операторов механизированной сварки, одновременно выполняющих сварку корневого
слоя шва, должно быть не менее 2-х для сварных соединений
500 мм и более.
Корневой слой шва
при сборке на внутреннем центраторе рекомендуется выполнять без прихваток. В
случае технической обоснованности применения прихваток они должны быть удалены
механическим способом шлифмашинками при выполнении корневого слоя шва.
Механизированная
сварка корневого слоя шва проволокой сплошного сечения в углекислом газе должна
выполняться на постоянном токе обратной полярности. Направление сварки - на
спуск.
Возбуждение дуги
должно проводиться только на кромках свариваемых элементов. Для предотвращения
образования пор обрыв дуги следует проводить на одной из свариваемых кромок.
Сварку рекомендуется
начинать в положении
и заканчивать в положении
на расстоянии не менее 100 мм от заводских
швов труб.
Начальный и
конечный участок корневого слоя шва, выполненного первым оператором, следует
обработать механическим способом (абразивным кругом) для обеспечения плавного
перехода при сварке корневого слоя шва вторым оператором.
После выполнения
корневого слоя шва его необходимо зачистить механическим способом
шлифмашинками.
При наличии видимых
дефектов корневого слоя шва типа непроваров, подрезов и др. необходимо
выполнить подварку дефектных участков ручной дуговой сваркой электродами с
основным видом покрытия согласно требованиям 10.2.40 - 10.2.42.
Операции по
подварке изнутри корневого слоя шва следует рассматривать как составную часть
технологического процесса и предусматривать при составлении
операционно-технологических карт сборки и сварки.
10.5.1.2.
Особенности механизированной сварки корневого слоя шва проволокой сплошного
сечения в углекислом газе с применением источников сварочного тока инверторного
типа
Механизированная
импульсно-дуговая сварка методом STT корневого слоя шва проволокой сплошного
сечения в углекислом газе с применением специальных источников сварочного тока
инверторного типа и подающих механизмов подачи сварочной проволоки производства
The Lincoln Electric Company и их аналогов выполняется с учетом приведенных
специальных требований, которые должны быть отражены в
операционно-технологических картах сборки и сварки.
Перед началом работ
должны быть выставлены следующие значения параметров режимов сварки:
а) пиковый ток - от
400 до 430 А;
б) базовый ток - от
45 до 50 А для толщин стенок труб менее 12 мм либо от 50 до 55 А для толщин
стенок труб от 12 мм и более;
в) скорость подачи
проволоки от 230 до 305 см/мин (от 90 до 120 дюйм/мин) в положении сварки от
до
либо от 330 до 405 см/мин (от 130 до 160
дюйм/мин) в положении сварки от
до
;
г) переключатель
длительности заднего фронта импульса (Tailout) должен быть установлен в
положение "0";
д) переключатель
"горячий старт" должен быть установлен в положение "2" или
"3";
е) расход газа - от
10 до 16 л/мин;
ж) длительность
предварительной подачи газа - 0,5 с;
з) длительность
послесварочной подачи газа - от 0,5 до 1,0 с.
Величина зазора
определяется требованиями 10.2.24.
При зазоре 2,5 мм
рекомендуется установить значение базового тока от 50 до 55 А, а в положении от
до
рекомендуется повысить скорость подачи
проволоки до от 330 до 355 см/мин (от 130 до 140 дюйм/мин).
При повышенных
зазорах рекомендуется установить значение базового тока от 35 до 40 А, а
скорость подачи проволоки в положении от
до
понизить до величины от 230 до 250 см/мин (от
90 до 100 дюйм/мин) и в положении от
до
- до величины от 380 до 405 см/мин (от 150 до
160 дюйм/мин).
До начала сварки
корневого слоя шва независимо от температуры окружающего воздуха должен быть
выполнен предварительный подогрев свариваемых кромок труб до температуры,
регламентированной требованиями 10.3.6.
Оптимальный вылет
сварочной проволоки от 10 до 16 мм. Допускается вылет сварочной проволоки до 20
мм.
Основные элементы
техники ведения сварки корневого слоя шва механизированной сваркой проволокой
сплошного сечения в углекислом газе с применением оборудования фирмы The
Lincoln Electric Company методом STT (рисунок 10.6):
- для начала сварки
в положении
и возбуждения дуги угол наклона сварочной
горелки должен составлять от 10° до 20° (углом назад) (поз. 1, рисунок 10.6);
- после возбуждения
дуги и образования сварочной ванны дугу следует плавно перевести с кромки на
середину разделки. При этом пятно дуги должно располагаться в передней части
сварочной ванны (первой трети сварочной ванны) (поз. 2, рисунок 10.6);
- в положении от
до
сварку следует выполнять небольшими быстрыми
дугообразными поперечными колебаниями (без задержки на кромках). Угол наклона
сварочной горелки должен составлять от 30° до 45° (углом назад) (поз. 3,
рисунок 10.6);
- в положении
сварки от
до
колебания следует прекратить и в дальнейшем
сварку следует выполнять прямолинейным движением сварочной горелки по центру
разделки. Угол наклона сварочной горелки в положении от
до
должен составлять от 20° до 45° (углом назад)
(поз. 4 - 6, рисунок 10.6);
- в положении
сварки от
до
угол наклона сварочной горелки следует
постепенно уменьшать и довести до нулевого значения (перпендикулярно
поверхности трубы);
- в положении
сварки от
до
сварочную горелку следует держать в положении,
перпендикулярном поверхности трубы (поз. 7, рисунок 10.6), либо с небольшим
углом от 5° до 10° (углом назад). При зазоре более 3,5 мм в потолочном
положении возможно возобновление поперечных колебаний;
- обрыв дуги для
прекращения сварки в положении
следует выполнить на одной из свариваемых
кромок (поз. 8, рисунок 10.6).
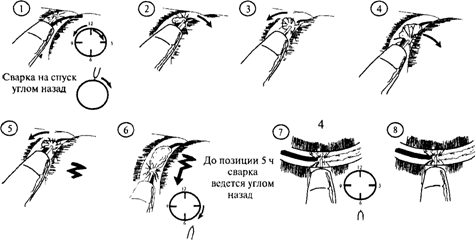
Рисунок
10.6. Техника механизированной сварки
корневого слоя шва
проволокой сплошного
сечения в
углекислом газе методом STT
Схема положения
сварочной горелки при механизированной сварке корневого слоя шва проволокой
сплошного сечения в углекислом газе методом STT в различных пространственных
положениях приведена на рисунке 10.7.
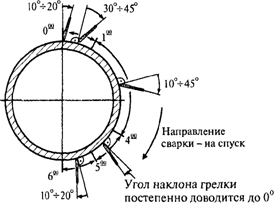
Рисунок 10.7.
Положение сварочной горелки
при
механизированной сварке корневого слоя шва
проволокой
сплошного сечения в углекислом газе
методом STT в
различных пространственных положениях
10.5.1.3.
Особенности механизированной сварки корневого слоя шва проволокой сплошного
сечения в углекислом газе с применением источников сварочного тока тиристорного
типа
А) Механизированная
сварка корневого слоя шва проволокой сплошного сечения в углекислом газе с
применением специальных источников сварочного тока тиристорного типа и
механизмов подачи сварочной проволоки производства ЗАО "НПФ
"ИТС" и их аналогов выполняется с учетом приведенных специальных
требований, которые должны быть отражены в операционно-технологических картах
сборки и сварки.
Перед началом работ
должны быть выставлены следующие значения параметров режимов сварки:
а) переключатель
тока короткого замыкания должен быть установлен в режим от "0" до
"2" в положении сварки от
до
либо в режим от "5" до
"10" в положении сварки от
до
;
б) среднее
напряжение на дуге - от 16,0 до 18,5 В;
в) скорость подачи
сварочной проволоки - от 2,5 до 4,7 м/мин;
г) длительность
предварительной подачи газа - 0,5 с;
д) длительность
послесварочной подачи газа - от 0,5 до 1,0 с.
Переключатель
параметра индуктивности цепи переноса капли электродного металла в сварочную
ванну должен быть уставлен в минимальное значение.
Величина зазора
между свариваемыми кромками труб должна быть в интервале от 2,5 до 3,5 мм.
До начала сварки
корневого слоя шва независимо от температуры окружающего воздуха должен быть
выполнен предварительный подогрев свариваемых кромок труб до температуры
.
После окончания сварки полного периметра корневого слоя шва незамедлительно
должен быть выполнен "горячий проход" механизированной сваркой
самозащитной порошковой проволокой, при этом межслойная температура не должна
опускаться ниже +100 °C.
Оптимальный вылет
сварочной проволоки - от 5,0 до 16 мм.
Основные элементы
техники ведения сварки корневого слоя шва механизированной сваркой проволокой
сплошного сечения в углекислом газе с применением оборудования ЗАО "НПФ
"ИТС" аналогичны технике ведения сварки методом STT по 10.5.1.2 с
учетом следующих особенностей:
- после возбуждения
дуги на одной из свариваемых кромок и образования сварочной ванны дугу следует
плавно перевести с кромки в середину разделки, далее сварка может выполняться
либо с опережением, либо с совмещением сварочной дуги с передней границей
сварочной ванны;
- при сварке с опережением
сварочная дуга должна опережать передний фронт сварочной ванны, а при сварке с
совмещением сварочная дуга должна располагаться по передней границе сварочной
ванны;
- сварка с
опережением сварочной дуги передней границы сварочной ванны обеспечивает максимальную
линейную скорость сварки при условии обязательного соблюдения нормативного
притупления и зазора;
- в положении от
до
сварку следует выполнять дугообразными
поперечными колебаниями с кратковременными задержками по краям сварочной ванны.
Угол наклона сварочной горелки должен составлять от 45° до 50° (сварка углом
назад);
- в положении от
до
сварку следует выполнять без колебаний или с
минимальными поперечными колебаниями. Угол наклона сварочной горелки должен
составлять 60° (сварка углом назад);
- в потолочном
положении от
до
угол наклона сварочной горелки следует
постепенно уменьшить и довести до нулевого значения (перпендикулярно
поверхности трубы). При зазоре 3,5 мм в потолочном положении возможно
возобновление поперечных колебаний.
Схема положения
сварочной горелки при механизированной сварке корневого слоя шва проволокой
сплошного сечения в углекислом газе с применением оборудования ЗАО "НПФ
"ИТС" в различных пространственных положениях приведена на рисунке
10.8 а.
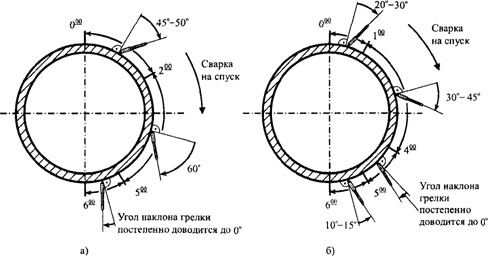
а) сварка с применением
оборудования ЗАО "НПФ "ИТС",
б) сварка с
применением оборудования ЗАО "Уралтермосвар"
Рисунок
10.8. Положение сварочной горелки
при
механизированной сварке корневого слоя
шва проволокой
сплошного сечения в углекислом
газе в различных
пространственных положениях
Б) Механизированная
сварка корневого слоя шва проволокой сплошного сечения в углекислом газе с
применением специальных источников сварочного тока тиристорного типа, сварочных
агрегатов, механизмов подачи сварочной проволоки ЗАО "Уралтермосвар"
и их аналогов выполняется с учетом приведенных специальных требований, которые
должны быть отражены в операционно-технологических картах сборки и сварки.
Перед началом работ
должны быть выставлены следующие значения параметров режимов сварки:
а) настройки меню
источника сварочного тока:
- способ сварки -
"полуавтоматическая" (механизированная);
- тип сварочной
проволоки - "сплошная";
- тип шва -
"корень";
- способ передачи
обратной связи по напряжению на дуге - "внешняя";
- напряжение на
дуге - от 16,0 до 19,0 В;
- предел
дистанционной коррекции напряжения на дуге
- "+/- 0 В";
б) настройки меню
механизма подачи сварочной проволоки:
- единицы скорости
подачи, выводимые на индикатор, - м/мин;
- скорость подачи
проволоки - от 2,4 до 4,8 м/мин;
- тип сварочной
проволоки - "сплошная";
- режим кнопки
горелки - "2Т"/"4Т" <*>;
- длительность
послесварочной подачи газа - от 1,0 до 2,5 с.
--------------------------------
<*> В режиме
"2Т" сварка начинается после нажатия и отпускания кнопки на горелке,
завершение сварки осуществляется повторным нажатием и отпусканием кнопки. В
режиме "4Т" сварка выполняется при нажатии и удержании кнопки на
горелке, завершение сварки осуществляется после отпускания кнопки.
Величина зазора
между свариваемыми кромками труб должна быть в интервале от 2,5 до 3,5 мм.
До начала сварки
корневого слоя шва независимо от температуры окружающего воздуха должен быть
выполнен предварительный подогрев свариваемых кромок труб до температуры,
соответствующей требованиям 10.3.6.
Оптимальный вылет
сварочной проволоки от 5,0 до 15 мм.
Основные элементы
техники ведения сварки корневого слоя шва механизированной сваркой проволокой
сплошного сечения в углекислом газе с применением оборудования ЗАО
"Уралтермосвар" аналогичны технике ведения сварки методом STT,
приведенным в 10.5.1.2, с учетом следующих особенностей:
- горелка при
зажигании дуги устанавливается под углом от 20° до 30° относительно
перпендикуляра к стыку, углом назад;
- после
расплавления одной из кромок и стабилизации процесса горения дуга переводится
на противоположную кромку. Когда жидкий металл с обеих кромок сформируется в
одну округлую сварочную ванну, дугу необходимо расположить по центру зазора,
после чего необходимо начать движение горелки вдоль свариваемых кромок;
- управление
процессом формирования корневого шва производится регулированием линейной
скорости сварки, угла наклона горелки, а также, при необходимости, введением
соответствующих колебаний;
- линейная скорость
сварки, т.е. скорость перемещения горелки по стыку, определяется установленным
режимом сварки и величиной зазора между свариваемыми кромками;
- линейная скорость
сварки поддерживается и визуально контролируется сварщиком исходя из условия
формирования полноценного валика корня шва и гарантированного сплавления
наплавляемого валика с основным металлом;
- углом наклона
горелки контролируется положение пятна дуги в оптимальной точке передней части
сварочной ванны;
- для обеспечения
надежного проплавления свариваемых кромок пятно дуги должно удерживаться на
переднем фронте сварочной ванны, не выходя из ванны, или, при достаточном
зазоре между свариваемыми кромками, в передней (головной) части сварочной ванны
(передней трети сварочной ванны);
- поперечные
дугообразные колебательные движения рекомендуется выполнять в верхней части
стыкового соединения (нижнее пространственное положение) для предотвращения
прожогов и стекания сварочной ванны;
- на вертикальном и
потолочном участках стыкового соединения при увеличенном зазоре поперечные
дугообразные колебания выполняются для предотвращения образования утяжины.
Рекомендуются
следующие углы наклона горелки (относительно перпендикуляра к поверхности
трубы):
- в положении от
до
- от 20° до 30° (сварка углом назад);
- в положении от
до
- угол может увеличиваться до 45° (сварка
углом назад);
- в положении от
до
- угол наклона горелки постепенно уменьшается
и доводится до положения, близкого к перпендикулярному;
- в положении от
до
- угол наклона горелки может варьироваться от
0° (перпендикулярно к поверхности трубы) до величины от 10° до 15° (сварка
углом назад либо углом вперед).
Схема положения
сварочной горелки при механизированной сварке корневого слоя шва проволокой
сплошного сечения в углекислом газе с применением оборудования ЗАО
"Уралтермосвар" в различных пространственных положениях приведена на
рисунке 10.8, б.
10.5.2.
Механизированная сварка самозащитной порошковой проволокой
10.5.2.1.
Механизированная сварка самозащитной порошковой проволокой (МПС) рекомендуется
для сварки заполняющих и облицовочного слоев шва неповоротных кольцевых
стыковых соединений труб, а также специальных сварных соединений газопроводов
(захлестные соединения, прямые вставки (катушки), разнотолщинные соединения
труб, соединения труб с СДТ, ЗРА) диаметром от 325 до 1420 мм с толщинами
стенок от 6,0 до 22,0 мм.
10.5.2.2. Для
механизированной сварки самозащитной порошковой проволокой заполняющих и
облицовочного слоев шва должны применяться сварочные агрегаты, сварочные
установки, укомплектованные источниками сварочного тока, механизмами подачи
сварочной проволоки, сварочными горелками и вспомогательным оборудованием,
отвечающие специальным требованиям и условиям эксплуатации, приведенным в
разделе 8.
10.5.2.3.
Самозащитные порошковые проволоки, прошедшие аттестацию и рекомендованные к
применению для механизированной сварки, приведены в таблице Д.15 (Приложение
Д).
При сварке труб
одной толщины, разнотолщинных труб (элементов) с различными нормативными
значениями временного сопротивления разрыву сварочные проволоки должны
назначаться по наибольшему значению временного сопротивления разрыву металла
труб и деталей газопроводов.
10.5.2.4. Сварку
труб с толщиной стенки от 14,0 до 22,0 мм рекомендуется выполнять с
предварительной обработкой кромок труб под специальную разделку (рисунок 10.9).
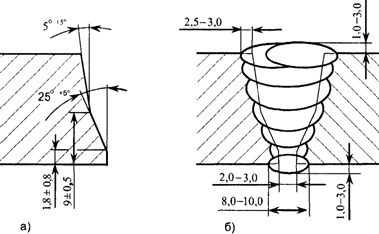
Рисунок 10.9.
Геометрические параметры специальной разделки
кромок труб (а) и
сварного шва (б) неповоротных кольцевых
стыковых соединений
труб, выполненных механизированной
сваркой
самозащитной порошковой проволокой
10.5.2.5. Перед
выполнением самозащитной порошковой проволокой первого заполняющего слоя либо
горячего прохода (в случае сварки корневого слоя шва электродами с целлюлозным
видом покрытия) необходимо тщательно (до чистого металла) зачистить абразивным
кругом корневой слой шва, предварительно сваренный электродами с основным или
целлюлозным видом покрытия. В случае сварки корневого слоя шва механизированной
сваркой проволокой сплошного сечения в углекислом газе зачистка проводится
дисковой проволочной щеткой. При необходимости, чрезмерное усиление корневого
слоя шва в потолочной части сварного соединения снимается шлифкругом.
10.5.2.6. Сварка
самозащитной порошковой проволокой выполняется на спуск постоянным током прямой
полярности.
10.5.2.7. Перед
началом работ необходимо на механизме подачи сварочной проволоки установить два
параметра сварочного процесса - напряжение и скорость подачи проволоки.
Следует строго
соблюдать соотношение между устанавливаемыми параметрами сварочного процесса,
т.к. отклонение значения напряжения для конкретной скорости подачи проволоки
более чем на 1,0 В может приводить к возникновению дефектов.
Рекомендуемые
режимы механизированной сварки самозащитной порошковой проволокой марки
"Иннершилд" диаметром 1,7 мм приведены в таблице 10.10, диаметром 2,0
мм - в таблице 10.11.
Таблица 10.10
Рекомендуемые
режимы механизированной сварки самозащитной
порошковой
проволокой марки "Иннершилд" диаметром 1,7 мм
Слои
|
Скорость подачи проволоки,
см/мин (дюйм/мин)
|
Напряжение, В
|
Корневой
|
200 (80)
|
15,0 - 16,0
|
230 (90)
|
16,0 - 17,0
|
Заполняющие
|
250 (100)
|
18,5 - 19,5
|
280 (19)
|
19,5 - 20,5
|
Корректирующий
|
200 (80)
|
17,0 - 17,5
|
230 (90)
|
17,5 - 18,5
|
Облицовочный
|
200 (80)
|
17,0 - 17,5
|
230 (90)
|
17,5 - 18,5
|
Таблица 10.11
Рекомендуемые
режимы механизированной сварки самозащитной
порошковой
проволокой марки "Иннершилд" диаметром 2,0 мм
Слои
|
Скорость подачи проволоки,
см/мин (дюйм/мин)
|
Напряжение, В
|
Заполняющие
|
200 (90)
|
18,5 - 19,5
|
250 (100)
|
19,5 - 20,5
|
280 (110)
|
20,5 - 21,5
|
Корректирующий
|
200 (80)
|
17,5 - 18,5
|
230 (90)
|
18,5 - 19,5
|
Облицовочный
|
200 (80)
|
17,5 - 18,5
|
230 (90)
|
18,5 - 19,5
|
10.5.2.8. При
работе в потолочном положении рекомендуется понизить скорость подачи проволоки.
Это делается без остановки процесса сварки переключением в положение
"2" переключателя, расположенного на рукоятке горелки. При этом
скорость подачи проволок понижается на величину от 15% до 20%. Одновременно
необходимо увеличить вылет до величины от 25 до 30 мм.
10.5.2.9. Сварка
выполняется способом на спуск.
10.5.2.10.
Заполняющие и облицовочный слои шва соединений труб с толщинами стенок до 14 мм
следует выполнять по методу "слой за один проход".
При сварке стыковых
сварных соединений труб с толщинами стенок более 14 мм заполняющие слои,
начиная с третьего, рекомендуется выполнять по методу "слой за два
прохода".
Облицовочный слой
шва стыковых сварных соединений труб с толщинами стенок более 14 мм следует
выполнять по методу "слой за три прохода". Допускается выполнять
облицовочный слой шва стыковых сварных соединений труб с толщинами стенок от 14
до 16 мм по методу "слой за два прохода".
10.5.2.11. Начинать
сварку следует при вылете проволоки от 12 до 15 мм (рисунок 10.10). При этом
срез проволоки слегка соприкасается с трубой или немного приподнят над ее
поверхностью. После зажигания дуги вылет электрода (проволоки) должен быть
увеличен до 20 мм. В потолочном положении рекомендуется увеличить вылет
электрода до 25 - 30 мм.
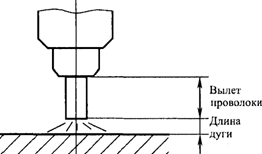
Рисунок 10.10.
Определение вылета проволоки и длины дуги
10.5.2.12. Угол
наклона проволоки должен постоянно меняться в процессе сварки (рисунок 10.11):
- в точке начала
сварки
угол должен составлять от 20° до 30° (углом
назад);
- в положении от
до
угол постепенно увеличивается до величины в
интервале от 45° до 60° (углом назад);
- в положении от
до
угол постепенно доводится до 0°
(перпендикулярно телу трубы в точке касания);
- в положении от
до
угол доводится до величины в интервале от 10°
до 15° (углом вперед).
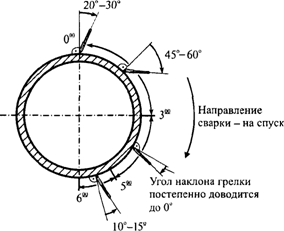
Рисунок
10.11. Изменение угла наклона сварочной горелки
при
механизированной сварке самозащитной порошковой
проволокой
неповоротных кольцевых стыковых соединений труб
10.5.2.13. При
изменении угла наклона сварочной горелки изменяется степень проплавления. При
уменьшении угла степень проплавления увеличивается, при увеличении угла -
уменьшается.
Скорость сварки
следует отрегулировать так, чтобы поддерживать соответствующую форму слоя
(валика) и контролировать сварочную ванну. Низкая скорость приводит к
повышенному разбрызгиванию сварочной ванны, возникновению пористости и шлаковых
включений.
10.5.2.14. При
сварке заполняющих и облицовочного слоев шва необходимо следить за тем, чтобы
температура перед наложением каждого последующего слоя была не ниже +50 °C и не
более +200 °C. Если температура участка шва, подлежащего сварке, упала ниже +50
°C, необходимо подогреть свариваемые кромки до температуры предварительного
подогрева.
10.5.2.15.
Межслойная зачистка после первого заполняющего слоя (горячего прохода)
выполняется дисковой проволочной щеткой или шлифкругом, после последующих слоев
- дисковой проволочной щеткой.
10.5.2.16. В связи
с неравномерностью заполнения разделки по периметру стыкового соединения и
ослаблением сечения шва в вертикальном положении перед выполнением
облицовочного слоя в положении от
до
и от
до
(ориентировочно) выполняется дополнительный
(корректирующий) слой.
10.5.2.17.
Ориентировочное количество слоев в зависимости от толщины стенки трубы
приведено в таблицах 10.12, 10.13.
Таблица 10.12
Ориентировочное количество
заполняющих и облицовочных
слоев шва при
механизированной сварке самозащитной
порошковой
проволокой диаметром 1,7 мм
Толщина
стенки, мм
|
Наименование слоя
|
заполняющие <*>
|
корректирующий
|
облицовочный
|
6
|
-
|
1
|
1
|
8
|
1
|
1
|
1
|
10
|
1 - 2
|
1
|
1
|
12
|
2 - 3
|
1
|
1
|
14
|
3 - 4
|
1
|
1
|
<*> Количество заполняющих
слоев зависит от
величины зазора при
сборке, угла раскрытия кромок и ряда других параметров.
|
Таблица 10.13
Ориентировочное
количество заполняющих и облицовочных
слоев шва при
механизированной сварке самозащитной
порошковой
проволокой диаметром 2,0 мм
Толщина
стенки, мм
|
Наименование слоя
|
заполняющие <*>
|
корректирующий
|
облицовочный
|
14
|
3 - 4
|
1
|
1 - 2
|
16
|
3 - 5
|
1
|
2 - 3
|
18
|
4 - 7
|
1
|
3
|
20
|
5 - 9
|
1
|
3
|
<*> Количество заполняющих
слоев зависит от величины зазора
при
сборке, угла раскрытия кромок и ряда других параметров.
|
10.5.2.18. Для
обеспечения лучшей формы облицовочного слоя шва рекомендуется некоторое
"недозаполнение" разделки перед его выполнением в нижнем и потолочном
положениях (на величину от 1,0 до 1,5 мм в нижнем положении и на величину от
1,0 до 2,0 мм в потолочном положении). При этом в вертикальном положении
разделка должна быть заполнена практически заподлицо с поверхностью стыкуемых
труб.
10.5.2.19. При
выполнении облицовочного слоя рекомендуется выполнять обработку шлифовальным
кругом участков начала и конца сварки.
Облицовочный слой
шва и прилегающая поверхность труб должны быть подвергнуты чистовой обработке
дисковой проволочной щеткой для очистки поверхности от шлака и брызг.
Допускается использование шлифкругов для выравнивания возможных неровностей
поверхности облицовочного слоя.
10.5.2.20. Для труб
с толщиной стенки от 14 до 18 мм облицовочный слой рекомендуется выполнять за
один проход, для труб с толщиной стенки более 18 мм - за два прохода.
10.5.2.21. В случае
рестарта (возобновления процесса сварки) сварка начинается с верхней части
предварительно очищенного от шлака кратера, кратер заполняется с малыми
колебаниями электрода, и после этого сварка продолжается с нужной скоростью.
10.5.2.22. В случае
вынужденного перерыва в работе сварное соединение следует накрыть
влагонепроницаемым теплоизолирующим поясом. При этом перед началом сварки
следует проконтролировать температуру сварного шва, и при его охлаждении ниже
+50 °C возобновлять работу допускается только после подогрева стыкового
соединения до температуры +50 °C.
Оставлять не
полностью сваренные соединения не допускается. В случае, когда производственные
условия не дают возможности без перерыва завершить сварку соединения, следует
соблюдать требования 10.2.49.
10.5.2.23. Процесс
дуговой сварки рекомендуется начинать и заканчивать на расстоянии не менее 100
мм от заводского шва трубы или детали газопровода.
10.5.2.24. Место
начала и окончания процесса сварки каждого слоя ("замок" шва) должно
располагаться на расстоянии не менее 20 мм от замков предыдущего слоя шва.
10.5.2.25. Не
допускается возбуждать дугу на поверхности трубы. Дуга должна возбуждаться
только на поверхности разделки кромок или на поверхности металла уже
выполненного шва.
10.6. Автоматическая сварка
10.6.1.
Автоматическая двухсторонняя сварка проволокой сплошного сечения в защитных
газах
10.6.1.1. Общие
требования
Автоматическая
двухсторонняя одно- или двухдуговая сварка проволокой сплошного сечения в
защитных газах (ААДП, АПГ) (далее - автоматическая двухсторонняя сварка) сварочными
комплексами (установками) в составе сборочно-сварочных колонн рекомендуется для
сварки неповоротных кольцевых стыковых соединений труб протяженных участков
газопроводов.
В состав
сборочно-сварочной колонны должны входить:
- многоголовочный
<*> автомат однодуговой сварки изнутри трубы, совмещенный с внутренним
самоходным центратором (один на сборочно-сварочную колонну);
- сварочные
комплексы (установки) автоматической одно- или двухдуговой сварки снаружи
трубы;
- станок подготовки
кромок труб с гидро- или электроприводом в составе грузоподъемной гусеничной
техники (один или два на сборочно-сварочную колонну);
- программатор
параметров режимов автоматической двухсторонней одно- и двухдуговой сварки
(один или два на сборочно-сварочную колонну);
- передвижная
мастерская (блок-контейнер или на базе колесной техники) или самоходная
мастерская на базе колесной или гусеничной техники (одна на сборочно-сварочную
колонну) для наладки, ремонта оборудования и хранения запасных частей
сборочно-сварочной колонны.
--------------------------------
<*>
Количество сварочных головок (от 4 до 8 шт.) определяется диаметром свариваемых
труб.
Количество
сварочных комплексов (установок) в сборочно-сварочной колонне при
поточно-расчлененном методе сварки определяется толщиной стенки труб
газопровода и требуемой производительностью сварочно-монтажных работ.
Для выполнения
работ по ремонту сваркой изнутри трубы дефектных участков корневого слоя шва в
состав сборочно-сварочной колонны должно входить сварочное оборудование для
механизированной сварки проволокой сплошного сечения в защитных газах
(источники сварочного тока, механизмы подачи проволоки, сварочные горелки) или
ручной дуговой сварки (источники сварочного тока).
Проволоки сплошного
сечения, рекомендованные к применению для автоматической сварки в защитных
газах внутреннего (корневого) и наружных (горячего прохода, заполняющих и
облицовочного) слоев шва, приведены в таблице Д.12 (Приложение Д).
Защитные газы
(активные, инертные и их смеси), рекомендованные для автоматической сварки
проволокой сплошного сечения внутреннего (корневого) и наружных (горячего
прохода, заполняющих и облицовочного), приведены в таблице Д.18 (Приложение Д).
Геометрические
параметры разделки кромок и сборки соединений труб для автоматической
двухсторонней сварки приведены на рисунке 10.12. Разделка кромок концов труб
должна быть выполнена механическим способом станками подготовки кромок типа СПК
заблаговременно до начала сборочно-сварочных работ.
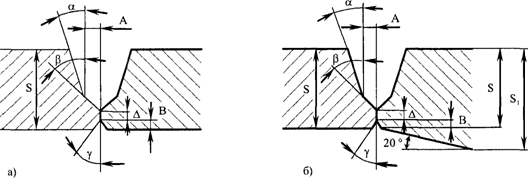
Обозначение параметра
|
Значение параметра
|
альфа
|
от (5° +/- 1°) до (10° +/- 1°)
|
бета
|
от (45° +/- 1°) до (52° +/- 1°)
|
гамма
|
37,5° +/- 1°
|
A, мм
|
от
(2,3° +/- 0,2°) до (3,6° +/- 0,2°)
|
B, мм
|
от
(1,0° +/- 0,2°) до (1,8° +/- 0,2°)
|
Дельта, мм
|
от
(1,0° +/- 0,2°) до (1,8° +/- 0,2°)
|
а) соединение труб
одной толщины стенки,
б) соединение труб
разной толщины стенки <*>
--------------------------------
<*> Отношение
номинальных толщин стенки труб
не более 1,5.
Рисунок
10.12. Геометрические параметры разделки кромок
и сборки соединений
труб для автоматической двухсторонней
сварки проволокой
сплошного сечения в защитных газах
Заблаговременно до
начала сборочно-сварочных работ на концы труб, обращенные в сторону движения
сборочно-сварочной колонны, должны устанавливаться направляющие пояса для
сварочных головок автоматической сварки. Направляющие пояса должны
устанавливаться с применением инвентарных шаблонов, обеспечивающих требуемую
точность установки и входящих в комплект специальных приспособлений
(аксессуаров) сварочного комплекса (установки).
Предварительный
подогрев кромок труб каждого стыкового соединения может выполняться до сборки
на внутреннем центраторе, при этом методы, оборудование и режимы
предварительного подогрева должны соответствовать требованиям 10.3.
Сборка труб должна
выполняться на инвентарных опорах (лежках), деревянных брусьях, мешках с
песком, при этом расстояние между нижней образующей трубы и грунтом должно быть
не менее 450 мм.
Величина зазора
должна соответствовать требованиям таблицы 10.1.
Схема
автоматической двухсторонней сварки неповоротных кольцевых стыковых соединений
труб приведена на рисунке 10.13.
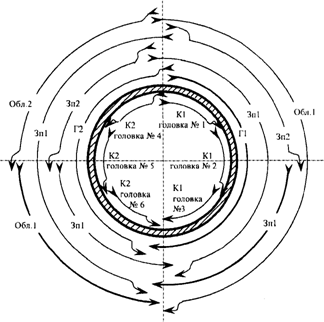
К - внутренний
(корневой) слой; Г - горячий проход;
Зп - заполняющий
слой; Обл. - облицовочный
слой (цифра после
обозначения слоя указывает
на очередность
сварки данного участка в пределах
слоя);
- указывает направление сварки
Рисунок 10.13.
Схема автоматической двухсторонней
сварки неповоротных
кольцевых стыковых соединений труб
Сварка внутреннего
(корневого) слоя шва выполняется на спуск изнутри трубы многоголовочным
сварочным автоматом, вначале в положении от
до
одновременно всеми сварочными головками,
расположенными по одну сторону многоголовочного сварочного автомата, затем в
положении от
до
одновременно всеми сварочными головками,
расположенными по другую сторону многоголовочного сварочного автомата.
Сварка первого
наружного слоя шва (горячего прохода) выполняется на спуск снаружи трубы двумя
однодуговыми сварочными головками, перемещающимися по направляющему поясу, при
этом одна сварочная головка выполняет сварку в положении от
до
,
другая в положении от
до
.
Сварку следует начинать после выполнения не менее 250 мм внутреннего
(корневого) слоя шва на соответствующем полупериметре трубы.
Интервал времени
между окончанием сварки внутреннего (корневого) слоя шва и началом сварки
первого наружного слоя (горячего прохода) при автоматической двухсторонней
сварке должен составлять не более 10 мин. В случае превышения указанного
интервала времени следует выполнить сопутствующий (межслойный) подогрев
сварного соединения до температуры предварительного подогрева.
Сварка последующих
наружных слоев шва (заполняющих и облицовочного) выполняется на спуск снаружи
трубы двумя одно- или двухдуговыми сварочными головками, перемещающимися по
направляющему поясу, при этом одна из сварочных головок выполняет сварку в
положении от
до
, а
другая сварочная головка сначала выполняет сварку в положении от
до
,
затем в положении от
до
.
Сварка следующего слоя выполняется по противоположной схеме.
Наружные дефекты
внутреннего (корневого) слоя шва следует устранить непосредственно после сварки
первого наружного слоя (горячего прохода). Выборка дефектов внутреннего
(корневого) слоя шва должна выполняться механическим способом шлифмашинкой.
Исправление дефектных участков следует выполнять механизированной сваркой
проволокой сплошного сечения в защитных газах по режимам, приведенным в таблице
10.14, допускается выполнять исправление дефектных участков внутреннего
(корневого) слоя шва ручной дуговой сваркой в соответствии с требованиями
раздела 10.7.3.
Таблица 10.14
Режимы
механизированной сварки проволокой
сплошного сечения в
защитных газах при исправлении
дефектов
внутреннего (корневого) слоя шва
┌────────┬──────┬──────────┬───────┬───────┬────────┬─────────┬───────────┐
│Направ-
│Вылет │ Скорость │Ско-
│Расход │Род
│Сварочный│Напряжение │
│ление │элек- │ подачи
│рость │ газа,
│тока, │ ток, А │на дуге, В │
│сварки
│трода,│проволоки,│сварки,│ л/мин
│поляр- │ │ │
│ │мм │
см/мин │см/мин │ │ность │ │ │
├────────┼──────┼──────────┼───────┼───────┼────────┼─────────┼───────────┤
│На
спуск│ 9,0 │ 889
│36 - 51│33 - 59│Посто- │150 - 190│19,0 - 20,5│
│ │ │ │ │ │янный,
│ │ │
│ │ │ │ │ │обратная│ │ │
├────────┴──────┴──────────┴───────┴───────┴────────┴─────────┴───────────┤
│ Примечания.
1. Параметры режимов
сварки корректируются при│
│производственной аттестации
технологии сварки и
фиксируются в│
│операционно-технологических
картах сборки и сварки.
│
│ 2. Сварка выполняется проволокой
сплошного сечения, рекомендованной│
│для сварки
внутреннего (корневого) слоя
шва согласно таблице
Д.12│
│(Приложение
Д).
│
│ 3. Состав защитного газа 75% Ar + 25% CO
. │
│
2 │
└─────────────────────────────────────────────────────────────────────────┘
Участки внутреннего
слоя шва с усилением более 3,0 мм следует обработать механическим способом
шлифмашинкой.
В случае
возникновения отказа одной или нескольких сварочных головок многоголовочного
автомата в процессе выполнения внутреннего (корневого) слоя шва следует:
- выполнить сварку
первого наружного слоя (горячего прохода) наружными сварочными головками на
участках периметра сварного соединения, где был выполнен внутренний (корневой)
слой;
- сдвинуть
внутренний центратор внутрь газопровода и выполнить механизированную сварку
проволокой сплошного сечения в защитных газах на режимах, приведенных в таблице
10.14, на участках периметра сварного соединения, на которых произошел отказ
сварочных головок многоголовочного автомата;
- выполнить сварку
первого наружного слоя (горячего прохода) наружными сварочными головками на
участках периметра сварного соединения, в которых внутренний (корневой) слой
шва был выполнен механизированной сваркой.
Общая протяженность
участков периметра сварного соединения, на которых произошел отказ сварочных
головок многоголовочного автомата, не должна превышать 50% периметра сварного
соединения.
После завершения
сварки заполняющих слоев шва выполняется облицовочный слой шва. Амплитуда
колебаний сварочной горелки при сварке облицовочного слоя шва должна
обеспечивать необходимую величину перекрытия свариваемых кромок труб на
величину, регламентированную перечислением ж) 9.3.
Места обрыва или
прерывания дуги, "замки" при сварке горячего прохода, заполняющих и
облицовочного слоев шва должны быть обработаны механическим способом
шлифмашинкой.
После завершения
сварки следует осмотреть поверхность облицовочного слоя шва. Выявленные
наружные дефекты сварного шва (кратеры, поры, подрезы и др.) следует удалить
механическим способом шлифмашинкой и до проведения неразрушающего контроля
сварного соединения откорректировать автоматической сваркой на участках
вышлифовки. Участки облицовочного слоя шва с усилением, превышающим
регламентируемые значения ("замки"), следует обработать механическим
способом шлифмашинкой.
Операции по
устранению наружных дефектов внутреннего (корневого) и наружного облицовочного
слоя шва считаются составной частью технологического процесса автоматической
двухсторонней сварки и должны быть предусмотрены в операционно-технологических
картах сборки и сварки, а также при производственной аттестации технологии
сварки.
10.6.1.2.
Автоматическая двухсторонняя сварка проволокой сплошного сечения в защитных
газах сварочным комплексом CRC-Evans
Сварочный комплекс
ф. CRC-Evans AW предназначен для автоматической двухсторонней одно- или
двухдуговой сварки проволокой сплошного сечения в защитных газах (ААДП, АПГ)
(далее - сварка комплексом CRC-Evans) неповоротных кольцевых стыковых
соединений труб газопроводов диаметром от 630 до 1420 мм.
Сварочным
комплексом CRC-Evans выполняется:
- однодуговая
сварка многоголовочным автоматом ИВМ (IWM), смонтированном на внутреннем
самоходном центраторе, на спуск изнутри трубы внутреннего (корневого) слоя шва;
- однодуговая
сварка двумя сварочными головками П-200 (P-200), П-260 (P-260) на спуск снаружи
трубы горячего прохода, заполняющих и облицовочного слоев шва;
- двухдуговая
сварка двумя сварочными головками П-600 (P-600) на спуск снаружи трубы
двухваликовых заполняющих и облицовочного слоя шва.
Геометрические
параметры разделки кромок и сборки соединений труб для сварки комплексом
CRC-Evans должны соответствовать требованиям рисунка 10.12.
Рекомендуемые режимы
сварки комплексом CRC-Evans:
- многоголовочным
автоматом ИВМ (IWM) внутреннего (корневого) слоя шва приведены в таблице 10.15;
- однодуговыми
сварочными головками П-200 (P-200), П-260 (P-260) горячего прохода шва
приведены в таблице 10.15, заполняющих и облицовочного слоев шва приведены в
таблице 10.16;
- двухдуговыми
сварочными головками П-600 (P-600) заполняющих и облицовочного слоев шва
приведены в таблице 10.17.
Таблица 10.15
Рекомендуемые
режимы сварки комплексом CRC-Evans
внутреннего
(корневого) слоя шва многоголовочным
автоматом ИВМ (IWM)
и горячего прохода шва однодуговыми
сварочными
головками П-200 (P-200), П-260 (P-260)
┌────────────────────────────────┬────────────────────────────────────────┐
│ Наименование параметра │ Слои шва │
│
├──────────────────┬─────────────────────┤
│ │ внутренний │первый наружный слой │
│ │
(корневой) слой │ (горячий проход) │
├────────────────────────────────┼──────────────────┴─────────────────────┤
│Диаметр
проволоки, мм │ 0,9 │
├────────────────────────────────┼────────────────────────────────────────┤
│Род
тока, полярность │ Постоянный, обратная │
├────────────────────────────────┼──────────────────┬─────────────────────┤
│Скорость
подачи электродной │ 965 +/- 25% │
1270 +/- 25% │
│проволоки,
см/мин │ │ │
├────────────────────────────────┼──────────────────┼─────────────────────┤
│Сила
тока, А │ 170 - 210 │ 220 - 270 │
├────────────────────────────────┼──────────────────┼─────────────────────┤
│Напряжение
на дуге, В │ 19,0 - 22,0 │ 23 - 26 │
├────────────────────────────────┼──────────────────┼─────────────────────┤
│Вылет
электродной проволоки, мм │
9,0 │ 9,5 │
├────────────────────────────────┼──────────────────┼─────────────────────┤
│Скорость
сварки, см/мин │ 76 +/- 5% │
127 +/- 10% │
├────────────────────────────────┼──────────────────┼─────────────────────┤
│Защитный
газ │ 75% Ar/25% CO │
100% CO │
│ │ 2 │ 2 │
├────────────────────────────────┼──────────────────┴─────────────────────┤
│Расход
газа, л/мин │ 33 - 52 │
├────────────────────────────────┼────────────────────────────────────────┤
│Угол
наклона электродной │ 0° - 7° │
│проволоки
(вперед) │ │
├────────────────────────────────┼────────────────────────────────────────┤
│Частота
колебаний электродной │ Без поперечных колебаний │
│ -1 │ │
│проволоки,
мин │ │
├────────────────────────────────┴────────────────────────────────────────┤
│ Примечание. Параметры
режимов сварки корректируются при│
│производственной аттестации
технологии сварки и
фиксируются в│
│операционно-технологических
картах сборки и сварки.
│
└─────────────────────────────────────────────────────────────────────────┘
Таблица 10.16
Рекомендуемые
режимы сварки комплексом CRC-Evans
заполняющих и
облицовочного слоев шва однодуговыми
головками П-200
(P-200), П-260 (P-260)
┌───────────────────────┬─────────────────────────────────────────────────┐
│ Наименование │ Порядок наложения слоев │
│ параметра
├───────────────┬───────────────┬─────────────────┤
│ │ заполняющие
│ последний │
облицовочный │
│ │ │ заполняющий
│ │
├───────────────────────┼───────────────┴───────────────┴─────────────────┤
│Диаметр
проволоки, мм │ 0,9 │
├───────────────────────┼─────────────────────────────────────────────────┤
│Род
тока, полярность │ Постоянный, обратная │
├───────────────────────┼───────────────┬───────────────┬─────────────────┤
│Скорость
подачи │ 1295 +/- 25% │ 1295 +/- 25% │1067 +/- 25% <*> │
│электродной
проволоки, │
│ │1397
+/- 25% <**>│
│см/мин │ │ │ │
├───────────────────────┼───────────────┼───────────────┼─────────────────┤
│Сила
тока, А │ 200 - 250
│ 210 - 250 │
180 - 260 │
├───────────────────────┼───────────────┼───────────────┼─────────────────┤
│Напряжение
на дуге, В │ 22 - 25
│ 23 - 26 │
18,0 - 22,5 │
├───────────────────────┼───────────────┼───────────────┼─────────────────┤
│Вылет
электродной │ 13,0
│ 13,0 │ 9,5
│
│проволоки,
мм │ │ │ │
├───────────────────────┼───────────────┼───────────────┼─────────────────┤
│Скорость
сварки, см/мин│38 +/- 25% <*> │38 +/- 25% <*> │
33 +/- 25% <*> │
│ │51 +/- 25%
<**>│46 +/- 25% <**>│ 46 +/- 25% <**> │
├───────────────────────┼───────────────┼───────────────┼─────────────────┤
│Защитный
газ │ 100% CO
│ 100% CO │ 75% Ar/25% CO │
│ │ 2
│ 2 │ 2
│
├───────────────────────┼───────────────┴───────────────┴─────────────────┤
│Расход
газа, л/мин │ 33 - 52 │
├───────────────────────┼─────────────────────────────────────────────────┤
│Угол
наклона │ 0° - 7° │
│электродной
проволоки │
│
│(вперед) │ │
├───────────────────────┼───────────────┬───────────────┬─────────────────┤
│Частота
колебаний │ 140 - 190
│ 140 - 190 │
110 - 120 <*> │
│электродной
проволоки, │
│ │ 130
- 160 <**> │
│ -1 │ │ │ │
│мин │ │ │ │
├───────────────────────┼───────────────┴───────────────┴─────────────────┤
│Амплитуда
колебаний, мм│ Регулируется
по ширине разделки │
├───────────────────────┴─────────────────────────────────────────────────┤
│
00 00 30
30 │
│
<*> В пространственном положении от 10 до 2
ч и от 4 до 7 ч. │
│
00 30 30
00 │
│
<**> В пространственном положении от 2 до 4
ч и от 7 до 10 ч.│
│ │
│ Примечание. Параметры
режимов сварки корректируются при│
│производственной аттестации
технологии сварки и
фиксируются в│
│операционно-технологических
картах сборки и сварки.
│
└─────────────────────────────────────────────────────────────────────────┘
Таблица 10.17
Рекомендуемые
режимы сварки комплексом CRC-Evans
заполняющих и
облицовочного слоев шва
однодуговыми
головками П-600 (P-600)
┌────────────────────────┬────────────────────────────────────────────────┐
│ Наименование │ Порядок наложения слоев │
│ параметра
├───────────────┬───────────────┬────────────────┤
│ │ заполняющие
│ последний │
облицовочный │
│ │ │ заполняющий
│ │
├────────────────────────┼───────────────┴───────────────┴────────────────┤
│Диаметр
проволоки, мм │ 1,0 │
├────────────────────────┼────────────────────────────────────────────────┤
│Род
тока, полярность │ Постоянный, обратная │
├────────────────────────┼───────────────┬───────────────┬────────────────┤
│Скорость
подачи │ 1095 +/- 25% │
995 +/- 25% │765 +/- 25%
<*> │
│электродной
проволоки, │ │ │995 +/- 25%
<**>│
│см/мин │ │ │ │
├────────────────────────┼───────────────┼───────────────┼────────────────┤
│Сила
тока, А │ 190 - 230
│ 180 - 220 │
150 - 220 │
├────────────────────────┼───────────────┼───────────────┼────────────────┤
│Напряжение
на дуге, В │ 21 - 25
│ 22 - 25 │
18 - 23 │
├────────────────────────┼───────────────┼───────────────┼────────────────┤
│Вылет
электродной │ 13,0
│ 13,0 │ 9,5
│
│проволоки,
мм │ │ │ │
├────────────────────────┼───────────────┼───────────────┼────────────────┤
│Скорость
сварки, см/мин │44 +/- 25% <*> │38 +/- 25% <*> │
34 +/- 25% <*> │
│ │52 +/- 25%
<**>│46 +/- 25% <**>│43 +/- 25% <**> │
├────────────────────────┼───────────────┴───────────────┴────────────────┤
│Защитный
газ │ 85% Ar/15% CO │
│ │ 2 │
├────────────────────────┼────────────────────────────────────────────────┤
│Расход
газа, л/мин │ 33 - 52 │
├────────────────────────┼────────────────────────────────────────────────┤
│Угол
наклона электродной│
0° - 7°
│
│проволоки
(вперед) │ │
├────────────────────────┼───────────────┬───────────────┬────────────────┤
│Частота
колебаний │ 140 - 190
│ 140 - 190 │ 110 - 120 <*> │
│электродной
проволоки, │ │ │ 130 - 160 <**>
│
│ -1 │ │ │ │
│мин │ │ │ │
├────────────────────────┼───────────────┴───────────────┴────────────────┤
│Амплитуда
колебаний │ Регулируется по ширине разделки │
│электродной
проволоки, │
│
│мм │
│
├────────────────────────┴────────────────────────────────────────────────┤
│
00 00 30
30 │
│
<*> В пространственном положении от 10 до 2
ч и от 4 до 7 ч. │
│
00 30 30
00 │
│
<**> В пространственном положении от 2 до 4
ч и от 7 до 10 ч.│
│
│
│ Примечание. Параметры
режимов сварки корректируются при│
│производственной аттестации
технологии сварки и
фиксируются в│
│операционно-технологических
картах сборки и сварки.
│
└─────────────────────────────────────────────────────────────────────────┘
Допускается
регулировать параметры скорости сварки и скорости подачи сварочной проволоки в
пределах +/- 25% от номинальных значений для предотвращения стекания металла
сварочной ванны на вертикальных участках, регулирования высоты заполняющих
слоев шва, а также формы и размеров облицовочного слоя шва в различных
пространственных положениях.
10.6.1.3.
Автоматическая двухсторонняя сварка проволокой сплошного сечения в защитных
газах комплексом Autoweld
Сварочный комплекс
ф. Autoweld Systems предназначен для автоматической двухсторонней однодуговой
сварки проволокой сплошного сечения в защитных газах (ААДП, АПГ) (далее -
сварка комплексом Autoweld) неповоротных кольцевых стыковых соединений труб
газопроводов диаметром от 630 до 1420 мм.
Сварочным
комплексом Autoweld выполняется:
- однодуговая
сварка многоголовочным автоматом ВМС, смонтированном на внутреннем самоходном
центраторе, на спуск изнутри трубы корневого слоя шва;
- однодуговая
сварка двумя сварочными головками ВГС на спуск снаружи трубы горячего прохода,
заполняющих и облицовочного слоев шва.
Сварка выполняется
несколькими сварочными комплексами (установками) в составе сборочно-сварочной
колонны по поточно-расчлененной схеме (корневой слой шва - многоголовочным
автоматом, совмещенным с внутренним самоходным центратором, горячий проход шва
- одним сварочным комплексом, заполняющие слои - одним или несколькими
сварочными комплексами, облицовочный слой - одним сварочным комплексом) либо
многоголовочным автоматом - корневого слоя шва и одним сварочным комплексом с
двумя сварочными головками - горячего прохода, заполняющих и облицовочного
слоев шва.
В сварочный
комплекс (установку) Autoweld для автоматической однодуговой сварки снаружи
трубы входят:
- две сварочные
головки ВГС с механизмами подачи сварочной проволоки пультами дистанционного управления
(одна резервная - рекомендательно) для однодуговой сварки всех слоев шва
(корневой слой, горячий проход, заполняющие и облицовочный слои);
- направляющий пояс
на две сварочные головки (один резервный - рекомендательно);
- агрегат
энергообеспечения с дизель-генератором на базе колесной или гусеничной техники
с двумя отдельными источниками сварочного тока инверторного или тиристорного
типа на сварочный комплекс (один резервный - рекомендательно), со стрелой
установки и перемещения защитных инвентарных укрытий (палаток), с рампой
баллонов защитных газов, газовыми смесителями с оборудованием контроля состава
смеси газов.
Геометрические
параметры разделки кромок и сборки соединений труб для сварки комплексом
Autoweld должны соответствовать требованиям рисунка 10.12.
Рекомендуемые
режимы сварки комплексом Autoweld:
- внутреннего
(корневого) слоя шва многоголовочным автоматом ВМС приведены в таблице 10.18;
- горячего прохода
шва однодуговыми сварочными головками ВГС приведены в таблице 10.18;
- заполняющих и
облицовочного слоев шва однодуговыми сварочными головками ВГС приведены в
таблице 10.19.
Таблица 10.18
Рекомендуемые
режимы сварки комплексом Autoweld
внутреннего
(корневого) слоя шва многоголовочным
автоматом ВМС и
горячего прохода шва однодуговыми
сварочными
головками ВГС
┌───────────────────────────────┬─────────────────────────────────────────┐
│ Наименование параметра │ Слои шва │
│
├───────────────────┬─────────────────────┤
│
│ внутренний │
горячий проход │
│ │ (корневой) слой │ │
├───────────────────────────────┼───────────────────┴─────────────────────┤
│Диаметр
проволоки, мм │ 0,9 │
├───────────────────────────────┼─────────────────────────────────────────┤
│Род
тока, полярность │ Постоянный, обратная │
├───────────────────────────────┼───────────────────┬─────────────────────┤
│Скорость
подачи электродной │ 965 +/- 10% │
1270 +/- 10% │
│проволоки,
см/мин │ │ │
├───────────────────────────────┼───────────────────┼─────────────────────┤
│Сила
тока, А │ 170 - 210 │ 230 - 280
│
├───────────────────────────────┼───────────────────┼─────────────────────┤
│Напряжение
на дуге, В │ 19,0 - 22,0 │ 23 - 26 │
├───────────────────────────────┼───────────────────┼─────────────────────┤
│Вылет
электродной проволоки, мм│
9,0 │ 8,0 │
├───────────────────────────────┼───────────────────┼─────────────────────┤
│Скорость
сварки, см/мин │ 76 +/- 5% │
127 +/- 10% │
├───────────────────────────────┼───────────────────┼─────────────────────┤
│ │ +5 │ │
│Защитный
газ │ 80 % Ar/20
% CO │ 100% CO │
│ │ -5 2│ 2 │
├───────────────────────────────┼───────────────────┼─────────────────────┤
│Расход
газа, л/мин │ 33 - 52 │ 38 - 46 │
├───────────────────────────────┼───────────────────┴─────────────────────┤
│Угол
наклона электродной │ 0° - 10° │
│проволоки
(вперед) │
│
├───────────────────────────────┼─────────────────────────────────────────┤
│Частота
колебаний электродной │ Без поперечных колебаний │
│ -1 │
│
│проволоки,
мин │
│
├───────────────────────────────┴─────────────────────────────────────────┤
│ Примечание. Параметры
режимов сварки корректируются при│
│производственной аттестации
технологии сварки и
фиксируются в│
│операционно-технологических
картах сборки и сварки. │
└─────────────────────────────────────────────────────────────────────────┘
Таблица 10.19
Рекомендуемые
режимы сварки комплексом Autoweld
заполняющих и
облицовочного слоев шва
однодуговыми
сварочными головками ВГС
┌──────────────────────────────┬──────────────────────────────────────────┐
│ Наименование параметра │ Порядок наложения слоев │
│
├─────────────┬─────────────┬──────────────┤
│ │
заполняющие │ последний │ облицовочный │
│ │ │ заполняющий │ │
├──────────────────────────────┼─────────────┴─────────────┴──────────────┤
│Диаметр
проволоки, мм │ 0,9 │
├──────────────────────────────┼──────────────────────────────────────────┤
│Род
тока, полярность │ Постоянный, обратная │
├──────────────────────────────┼─────────────┬─────────────┬──────────────┤
│Скорость
подачи электродной │1295 +/- 10%
│1295 +/- 10% │ 955 +/- 10%
│
│проволоки,
см/мин │ │ │ │
├──────────────────────────────┼─────────────┼─────────────┼──────────────┤
│Сила
тока, А │ 200 - 250
│ 210 - 250 │
170 - 220 │
├──────────────────────────────┼─────────────┼─────────────┼──────────────┤
│Напряжение
на дуге, В │ 23 - 26
│ 23 - 26 │ 18,0 - 22,5 │
├──────────────────────────────┼─────────────┼─────────────┼──────────────┤
│Вылет
электрода, мм │13,0 +/-
10% │13,0 +/- 10% │ 8,0 +/- 10%
│
├──────────────────────────────┼─────────────┼─────────────┼──────────────┤
│Скорость
сварки, см/мин │ 40 +/-
25% │ 40 +/- 25% │
30 +/- 25% │
├──────────────────────────────┼─────────────┼─────────────┼──────────────┤
│Защитный
газ │ 100% CO
│ 100% CO │80% Ar/20% CO │
│ │ 2
│ 2 │ 2│
├──────────────────────────────┼─────────────┴─────────────┴──────────────┤
│Расход
газа, л/мин │ 33 - 45 │
├──────────────────────────────┼──────────────────────────────────────────┤
│Угол
наклона электродной │ 0° - 10° │
│проволоки
(вперед) │
│
├──────────────────────────────┼─────────────┬─────────────┬──────────────┤
│Частота
колебаний электродной │ 150 -
190 │ 150 - 190
│ 100 - 130 │
│ -1 │ │ │ │
│проволоки,
мин │ │ │ │
├──────────────────────────────┼─────────────┴─────────────┴──────────────┤
│Амплитуда
колебаний │ Регулируется по ширине разделки │
│электродной
проволоки, мм │
│
├──────────────────────────────┴──────────────────────────────────────────┤
│ Примечание. Параметры
режимов сварки корректируются при│
│производственной аттестации
технологии сварки и
фиксируются в│
│операционно-технологических
картах сборки и сварки.
│
└─────────────────────────────────────────────────────────────────────────┘
Допускается
регулировать параметры скорости сварки и скорости подачи сварочной проволоки в
пределах +/- 10% от номинальных значений для предотвращения стекания металла
сварочной ванны на вертикальных участках, регулирования высоты заполняющих
слоев шва, а также формы и размеров облицовочного слоя шва в различных
пространственных положениях.
10.6.2.
Автоматическая односторонняя сварка проволокой сплошного сечения в защитных
газах
10.6.2.1. Общие
требования
Автоматическая
односторонняя одно- или двухдуговая сварка проволокой сплошного сечения в
защитных газах (АПГ) (далее - автоматическая односторонняя сварка) сварочными
комплексами (установками) в составе сборочно-сварочных колонн рекомендуется для
сварки неповоротных кольцевых стыковых соединений труб протяженных участков
газопроводов.
В состав
сборочно-сварочной колонны должны входить:
- сварочные
комплексы (установки) автоматической односторонней сварки;
- внутренний
самоходный центратор с медным подкладным кольцом с пневмо- или гидроприводом
(один на сварочную колонну);
- станок подготовки
кромок труб с гидро- или электроприводом в составе грузоподъемной гусеничной
техники (один или два на сборочно-сварочную колонну);
- программатор
параметров режимов автоматической односторонней одно- и двухдуговой сварки (один
или два на сборочно-сварочную колонну);
- передвижная
мастерская (блок-контейнер или на базе колесной техники) или самоходная
мастерская на базе колесной или гусеничной техники (одна на сварочную колонну)
для наладки, ремонта оборудования и хранения запасных частей сборочно-сварочной
колонны.
Количество
сварочных комплексов (установок) в сборочно-сварочной колонне при
поточно-расчлененном методе сварки определяется толщиной стенки труб
газопровода и требуемой производительностью сварочно-монтажных работ.
Проволоки сплошного
сечения, рекомендованные для автоматической односторонней сварки, приведены в
таблице Д.12 (Приложение Д).
Защитные газы
(активные, инертные и их смеси), рекомендованные для автоматической
односторонней сварки, приведены в таблице Д.18 (Приложение Д).
Геометрические
параметры разделки кромок и сборки соединений труб для автоматической
односторонней сварки регламентируются особенностями технологии автоматической
сварки сварочными комплексами. Разделка кромок концов труб должна быть выполнена
механическим способом станками подготовки кромок типа СПК заблаговременно, до
начала сборочно-сварочных работ.
Заблаговременно до
начала сборочно-сварочных работ на концы труб, обращенные в сторону движения
сборочно-сварочной колонны, должны устанавливаться направляющие пояса для
сварочных головок автоматической сварки. Направляющие пояса должны
устанавливаться с применением инвентарных шаблонов, обеспечивающих требуемую
точность установки и входящих в комплект специальных приспособлений
(аксессуаров) сварочного комплекса (установки).
С целью исключения
наружных дефектов внутренней поверхности корневого слоя шва медное подкладное
кольцо внутреннего центратора до начала работ должно регулярно зачищаться
шлифмашинкой с лепестковым абразивным кругом.
Просушку и подогрев
медного подкладного кольца внутреннего центратора необходимо выполнять после
каждого перерыва работ.
Предварительный
подогрев кромок труб каждого стыкового соединения может выполняться до сборки
или после сборки на внутреннем центраторе, при этом методы, оборудование и
режимы предварительного подогрева должны соответствовать требованиям 10.3.
При сборке труб
медное подкладное кольцо внутреннего центратора должно находиться в плоскости
стыкового соединения. Величина зазора при сборке должна соответствовать
требованиям таблицы 10.1.
Допускаются
распределенные смещения кромок при сборке стыковых соединений не более 3,0 мм.
Если распределенное смещение кромок выше 3,0 мм и качество сборки не может быть
улучшено поворотом стыкуемой трубы вокруг горизонтальной оси, то следует
заменить трубу, подаваемую на сборку.
До начала работ
параметры режимов автоматической односторонней сварки всех слоев шва с учетом
пространственного положения сварки неповоротных кольцевых стыковых соединений
труб конкретного типоразмера должны быть внесены в блоки автоматического
управления каждой сварочной головкой (скорость перемещения сварочной головки по
направляющему поясу, скорость подачи сварочной проволоки, напряжение сварочной
дуги, сила тока сварочной дуги, частота поперечных колебаний сварочных горелок,
вылет электродной проволоки).
Регулирование
параметров режимов автоматической односторонней сварки в установленных системой
автоматического управления пределах может выполняться через выносной пульт
дистанционного управления (амплитуда колебаний сварочной горелки, скорость
продольного перемещения сварочной головки и др.).
Автоматическая
односторонняя сварка корневого слоя шва (корневого слоя и горячего прохода),
заполняющих и облицовочного слоев шва каждого стыкового соединения выполняется
на спуск двумя одно- или двухдуговыми сварочными головками, при этом каждой
сварочной головкой выполняется сварка одного из полупериметров трубы
(относительно вертикальной оси).
После окончания
сварки корневого слоя (корневого слоя и горячего прохода) стыкуемая труба
укладывается на инвентарную опору, внутренний центратор перемещается на
очередную позицию сборки.
Участки корневого
слоя шва с видимыми недопустимыми дефектами следует подварить ручной дуговой
сваркой изнутри трубы.
Участки корневого
слоя шва с усилением, превышающим регламентируемые значения, следует обработать
механическим способом шлифмашинкой, видимые дефекты корневого слоя шва (поры,
непровары и др.), имеющие недопустимые размеры, должны быть подварены ручной
дуговой сваркой. Эти операции следует предусматривать при составлении
операционно-технологических карт сборки и сварки и рассматривать как составную
часть технологического процесса автоматической односторонней сварки.
Интервал времени
между окончанием сварки корневого слоя и началом сварки горячего прохода
(первого заполняющего слоя) при однодуговой автоматической односторонней сварке
должен составлять не более 10 мин.
Автоматическая
односторонняя сварка заполняющих и облицовочного слоев шва выполняется
одновременно двумя сварочными головками с поперечными колебаниями сварочной
горелки (сварочных горелок), при этом каждой сварочной головкой выполняется
сварка одного из полупериметров трубы (относительно вертикальной оси).
Места начала и
окончания автоматической односторонней сварки каждого последующего слоя
("замки") должны быть обработаны механическим способом для
предотвращения образования дефектов типа несплавлений и удаления кратерных
трещин.
После завершения
автоматической односторонней сварки заполняющих слоев шва выполняется
облицовочный слой шва. Амплитуда колебаний сварочной горелки при сварке
облицовочного шва должна обеспечивать необходимую величину перекрытия
свариваемых кромок труб на величину, регламентированную перечислением ж) 9.3.
После завершения
сварки следует осмотреть поверхность облицовочного слоя шва. Выявленные
наружные дефекты сварного шва (кратеры, поры, подрезы и др.) следует удалить
механическим способом шлифмашинкой и до проведения неразрушающего контроля
сварного соединения откорректировать автоматической сваркой на участках
вышлифовки. Участки облицовочного слоя шва с усилением, превышающим
регламентируемые значения ("замки"), следует обработать механическим
способом шлифмашинкой. Указанные операции считаются составной частью технологического
процесса автоматической сварки и должны быть предусмотрены в
операционно-технологических картах сборки и сварки, а также при
производственной аттестации технологии сварки.
10.6.2.2.
Автоматическая односторонняя сварка проволокой сплошного сечения в защитных
газах сварочным комплексом Saturnax
Сварочный комплекс
(установка) Saturnax (ф. Serimax) предназначен для автоматической односторонней
сварки проволокой сплошного сечения в защитных газах (АПГ) (далее - сварка
комплексом Saturnax) неповоротных кольцевых стыковых соединений труб
газопроводов диаметром от 159 до 1420 мм.
Сварочным
комплексом Saturnax выполняется:
- односторонняя
двухдуговая сварка двумя сварочными головками на спуск снаружи трубы корневого
слоя и горячего прохода на медном подкладном кольце, установленном между рядами
жимков внутреннего центратора;
- односторонняя
двухдуговая сварка двумя сварочными головками на спуск снаружи трубы
двухваликовых заполняющих слоев шва;
- односторонняя
двухдуговая сварка двумя сварочными головками на спуск снаружи трубы
двухваликового облицовочного слоя шва;
- односторонняя
однодуговая сварка всех слоев шва, а также корректирующих слоев или отдельных
слоев шва в случаях отказа одной из двух сварочных горелок при двухдуговой
сварке.
Сварка выполняется
несколькими сварочными комплексами в составе сборочно-сварочной колонны по
поточно-расчлененной схеме (корневой слой шва и горячий проход шва - одним
сварочным комплексом, двухваликовые заполняющие слои - одним или несколькими
сварочными комплексами, двухваликовый облицовочный слой - одним сварочным
комплексом) либо одним сварочным комплексом с двумя сварочными головками всех
слоев шва.
В сварочный
комплекс Saturnax входят:
- две сварочные
головки с пультами дистанционного управления (одна резервная - рекомендательно)
для двухдуговой сварки всех слоев шва (корневой слой и горячий проход,
двухваликовые заполняющие слои, двухваликовый облицовочный слой);
- один блок
автоматического управления параметров режимов сварки на каждую сварочную
головку, совмещенные с блоками контроля и записи параметров режимов сварки;
- один совмещенный
блок механизмов подачи сварочной проволоки на каждую сварочную головку,
включающий систему распределения и контроля расхода защитного газа;
- блок
автоматического управления на две сварочные головки;
- направляющий пояс
на две сварочные головки (один резервный - рекомендательно);
- агрегат
энергообеспечения с дизель-генератором на базе колесной или гусеничной техники
с четырьмя отдельными источниками сварочного тока инверторного или тиристорного
типа на сварочный комплекс (один резервный - рекомендательно), со стрелой
установки и перемещения защитных инвентарных укрытий (палаток), с рампой
баллонов защитных газов, газовыми смесителями с оборудованием контроля состава
смеси газов.
Геометрические
параметры разделки кромок и сборки соединений труб для сварки комплексом
Saturnax должны соответствовать требованиям рисунка 10.14.
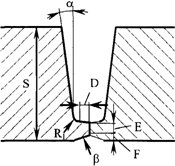
а)
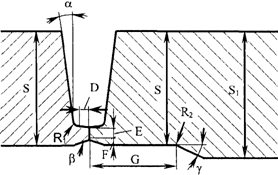
б)
┌─────────┬───────────┬───────────┬───────────┬───────────┬───────────┬───────────┬──────────┬─────────┬───────┐
│Обозна- │ альфа, ° │
R , мм │ D, мм
│ E, мм │
F, мм │ бета, °
│ гамма, ° │ G,
мм │R , мм │
│чение │ │ 1
│ │ │ │ │ │ │ 2 │
│параметра│ │ │ │ │ │ │ │ │ │
├─────────┼───────────┼───────────┼───────────┼───────────┼───────────┼───────────┼──────────┼─────────┼───────┤
│Величина
│5,0 +/- 2,0│2,4 +/- 0,8│0,1 +/- 0,1│2,1 +/-
0,2│2,3 +/- 0,2│4,0 +/- 1,0│25 +/- 5,0│80 +/-
10│3,0 min│
│параметра│ │ │ │ │ │ │ │ │ │
└─────────┴───────────┴───────────┴───────────┴───────────┴───────────┴───────────┴──────────┴─────────┴───────┘
а) соединение труб
одной толщины стенки;
б) соединение труб
разной толщины стенки <*>
--------------------------------
<*> Отношение
номинальных толщин стенки труб
не более 1,5. Сварное соединение выполняется
без обязательной подварки изнутри ручной дуговой сваркой корневого слоя шва.
Рисунок
10.14. Геометрические параметры разделки кромок
и сборки соединений
труб для сварки комплексом Saturnax
Сварка всех слоев
шва (корневого слоя, горячего прохода, заполняющих и облицовочного слоя)
выполняется в смеси защитных газов с постоянным процентным содержанием
(пределами) каждого газа (50%
+ 50% Ar).
Рекомендуемая схема
сварки комплексом Saturnax неповоротных кольцевых стыковых соединений труб
приведена на рисунке 10.15.

К1, К2, Г1, Г2 -
участки первого прохода (корневого слоя
и горячего прохода)
на левом и правом полупериметрах трубы.
Зп 1.1 -
заполняющие слои. Первая цифра обозначает номер
прохода, вторая -
последовательность сварки в пределах
прохода. За один
проход производится сварка двух
заполняющих слоев.
Обл. 1 - облицовочный слой.
Цифра обозначает
последовательность сварки
в пределах прохода
Рисунок 10.15.
Рекомендуемая схема автоматической
односторонней
сварки комплексом Saturnax неповоротных
кольцевых стыковых
соединений труб
Для обеспечения
равномерного заполнения разделки кромок перед сваркой облицовочного слоя в
случае необходимости выполняется корректирующий слой шва. Сварка корректирующего
слоя должна выполняться с отключением на сварочной головке одной сварочной
горелки.
Сварка
облицовочного слоя шва должна выполняться за один проход двумя параллельными
валиками. Допускается выполнять сварку облицовочного слоя шва за два прохода в
однодуговом режиме работы сварочной головки. Валики облицовочного слоя должны
перекрывать друг друга, обеспечивая плавное сопряжение между собой и с основным
металлом трубы.
Геометрические
параметры сварного шва, выполненного сварочным комплексом Saturnax, приведены
на рисунке 10.16.
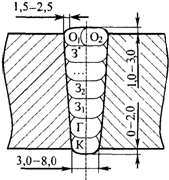
К - корневой слой,
Г - горячий проход шва
(выполняются за
один проход сварочных головок);
,
и т.д. - заполняющие слои шва (за один проход
выполняются два
слоя); З* - корректирующий слой
(выполняется в
случае необходимости);
и
- валики
облицовочного слоя
шва
Рисунок 10.16.
Геометрические параметры сварного шва,
выполненного
сварочным комплексом Saturnax
Параметры режимов
сварки комплексом Saturnax неповоротных кольцевых стыковых соединений труб
диаметром от 1020 до 1420 мм с толщинами стенок от 11,0 мм и более приведены в
таблице 10.20.
Таблица 10.20
Рекомендуемые
режимы сварки комплексом Saturnax
соединений труб
диаметром от 1020 до 1420 мм
┌───────────┬─────────────────────────────────────────────────────────────────────┐
│
Параметры │
Режимы сварки
│
│
├─────────────────────────────────────────────────────────────────────┤
│ │ Наименование
слоя │
│
├───────────────────┬─────────────────────────────────────────────────┤
│ │ 1-й проход │ Последующие проходы │
│
├─────────┬─────────┼─────────┬─────────┬─────────┬─────────┬─────────┤
│ │корневой │ горячий
│заполня- │заполня- │корректи-│облицо- │облицо- │
│ │ слой
│ проход │ющие
слои│ющие слои│рующий
│вочный │вочный │
│ │(горелка │(горелка
│(горелка │(горелка │(горелка │слой │слой │
│ │ N 1)
│ N 2) │N 1) │N 2) │N 1) │(горелка │(горелка │
│ │ │ │ │ │ │N 1) │N 2) │
├───────────┼─────────┼─────────┼─────────┼─────────┼─────────┼─────────┼─────────┤
│Направление│На
спуск │На спуск │На спуск │На спуск │На спуск │На
спуск │На спуск │
│сварки │ │ │ │ │ │ │ │
├───────────┼─────────┼─────────┼─────────┼─────────┼─────────┼─────────┼─────────┤
│Диаметр │
1,0 │ 1,0
│ 1,0 │
1,0 │ 1,0
│ 1,0 │
1,0 │
│электродной│ │ │ │ │ │ │ │
│проволоки,
│ │ │ │ │ │ │ │
│мм │ │ │ │ │ │ │ │
├───────────┼─────────┼─────────┼─────────┼─────────┼─────────┼─────────┼─────────┤
│Род
тока, │ =; (+) │ =; (+) │ =; (+) │ =; (+) │ =; (+) │ =; (+) │ =; (+) │
│полярность
│ │ │ │ │ │ │ │
├───────────┼─────────┴─────────┼─────────┴─────────┼─────────┼─────────┴─────────┤
│Скорость │
95 - 170 │ 40 - 95 │ 55 - 80 │ 45 - 90 │
│сварки, │ │ │ │ │
│см/мин │ │ │ │ │
│(+/-
10%) │ │ │ │ │
├───────────┼─────────┬─────────┼─────────┬─────────┼─────────┼─────────┬─────────┤
│Скорость │11 - 15 │ 9 - 13 │ 9 - 14 │ 8 - 13 │ 9 - 11 │ 8 - 10 │ 7 - 10 │
│подачи │ │ │ │ │ │ │ │
│электродной│ │ │ │ │ │ │ │
│проволоки,
│ │ │ │ │ │ │ │
│м/мин │ │ │ │ │ │ │ │
│(+/-
10%) │ │ │ │ │ │ │ │
├───────────┼─────────┴─────────┴─────────┴─────────┴─────────┴─────────┴─────────┤
│Вылет
│ Устанавливается
автоматически │
│электродной│
│
│проволоки,
│
│
│мм │
│
├───────────┼─────────┬─────────┬─────────┬─────────┬─────────┬─────────┬─────────┤
│Защитный │
50/50 │ 50/50
│ 50/50 │
50/50 │ 50/50
│ 50/50 │
50/50 │
│газ
Ar/CO │ │ │ │ │ │ │ │
│ 2 │ │ │ │ │ │ │ │
├───────────┼─────────┼─────────┼─────────┼─────────┼─────────┼─────────┼─────────┤
│Расход │ 50 - 60 │ 50 - 60 │ 50
- 60 │ 50 - 60 │ 50 - 60 │ 50 - 60 │ 50 - 60 │
│газа,
л/мин│ │ │ │ │ │ │ │
│(+/-
10%) │ │ │ │ │ │ │ │
├───────────┼─────────┼─────────┼─────────┼─────────┼─────────┼─────────┼─────────┤
│Сила
тока, │250 - 295│220 - 270│210 - 270│200 -
260│210 - 245│190 - 240│180 - 235│
│А
(+/- 10%)│ │ │ │ │ │ │ │
├───────────┼─────────┼─────────┼─────────┼─────────┼─────────┼─────────┼─────────┤
│Напряжение
│24 - 25,5│24,5 -
│23,0 - │23,5 - │23,5 - │22,5 - │22,5 - │
│на
дуге, В │ │ 26,0│ 26,0│ 25,5│ 25,5│ 24,5│ 24,5│
│(+/-
10%) │ │ │
│ │ │ │ │
├───────────┼─────────┴─────────┼─────────┴─────────┼─────────┼─────────┴─────────┤
│Частота │ 200 │ 180 │ 180
│ 200 │
│колебаний │ │ │ │ │
│электродной│ │ │ │ │
│проволоки,
│ │ │ │ │
│Гц │ │ │ │ │
│(+/-
10%) │ │ │ │ │
├───────────┼───────────────────┴───────────────────┴─────────┴───────────────────┤
│Амплитуда │ Устанавливается по ширине
разделки │
│колебаний │
│
│электродной│
│
│проволоки,
│ │
│мм │
│
├───────────┼─────────────────────────────────────────────────────────────────────┤
│Угол │ 7°30' │
│наклона │
│
│электродной│
│
│проволоки,
│
│
│° │
│
├───────────┴─────────────────────────────────────────────────────────────────────┤
│ Примечание. Параметры режимов
сварки соединений труб
диаметром │
│менее 1020 мм
могут корректироваться при
производственной аттестации │
│технологии
сварки.
│
└─────────────────────────────────────────────────────────────────────────────────┘
10.6.2.3.
Автоматическая односторонняя сварка проволокой сплошного сечения в защитных
газах сварочным комплексом CWS.02
Сварочный комплекс
(установка) CWS.02 (ф. PWT) предназначен для автоматической односторонней
сварки проволокой сплошного сечения в защитных газах (АПГ) (далее - сварка
комплексом CWS.02) неповоротных кольцевых стыковых соединений труб газопроводов
диаметром от 426 до 1420 мм.
Сварочным
комплексом CWS.02 выполняется:
- односторонняя
однодуговая сварка двумя сварочными головками на спуск снаружи трубы корневого
слоя на медном подкладном кольце, установленном между рядами жимков внутреннего
центратора;
- односторонняя
однодуговая сварка двумя сварочными головками на спуск снаружи трубы
заполняющих слоев шва;
- односторонняя
однодуговая сварка двумя сварочными головками на спуск снаружи трубы
облицовочного слоя шва;
Сварка выполняется
несколькими сварочными комплексами в составе сварочной колонны по
поточно-расчлененной схеме (корневой слой шва - одним сварочным комплексом,
заполняющие слои - одним или несколькими сварочными комплексами, облицовочный
слой - одним сварочным комплексом) либо одним сварочным комплексом с двумя
сварочными головками всех слоев шва.
В сварочный
комплекс CWS.02 входят:
- две сварочные
головки с механизмами подачи сварочной проволоки (одна резервная -
рекомендательно), пультами дистанционного управления для однодуговой сварки
всех слоев шва (корневой слой, заполняющие слои, облицовочный слой);
- направляющий пояс
на две сварочные головки (один резервный - рекомендательно);
- агрегат
энергообеспечения с дизель-генератором на базе колесной или гусеничной техники
с двумя отдельными специальными источниками сварочного тока на сварочный
комплекс (один резервный - рекомендательно), с двумя блоками автоматического
управления параметров режимов сварки на сварочный комплекс, совмещенных с
блоками контроля параметров режимов сварки, со стрелой установки и перемещения
защитных инвентарных укрытий (палаток), с рампой баллонов защитных газов,
газовыми смесителями с оборудованием контроля расхода и состава смеси газов.
После сборки
стыкового соединения следует простучать его по всему периметру кувалдой с
ударной частью из цветного металла для более плотного прилегания секторов
медного подкладного кольца к внутренней поверхности трубы.
Геометрические
параметры разделки кромок и сборки соединений труб для сварки комплексом CWS.02
должны соответствовать требованиям рисунка 10.17.
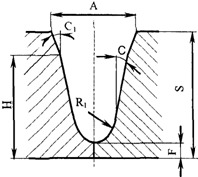
а)
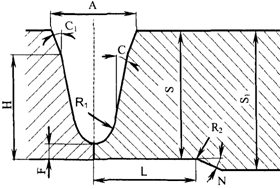
б)
┌───────────┬────┬─────┬───────────┬──────┬─────┬─────────┬────────┬───────┐
│Обозначение│C,
°│C , °│ F , мм │R , мм│H, мм│ L, мм │ N, °
│R , мм │
│параметра │
│ 1 │ │ 1 │
│ │ │ 2 │
├───────────┼────┼─────┼───────────┼──────┼─────┼─────────┼────────┼───────┤
│Величина │10
│ 12 │2,0 +/-
0,2│ 3,2 │14,5 │50 +/-
10│25 +/- 5│3,0 min│
│параметра │
-2│ -2│ │ │ │ │ │ │
└───────────┴────┴─────┴───────────┴──────┴─────┴─────────┴────────┴───────┘
Примечания. 1.
Неуказанные предельные отклонения размеров +/- 0,3 мм.
2. Величина
параметра A должна составлять:
- для труб
с толщиной стенки 15,7 мм от 8,0 до 10,0 мм;
- " " "
18,7 мм от 9,0 до 11,5 мм;
-
" " "
21,6 мм от 10,0 до 13,0 мм;
- " " "
23,2 мм от 10,5 до 13,5 мм;
- " " "
25,8 мм от 11,0 до 14,5 мм.
а) соединение труб
одной толщины стенки;
б) соединение труб
разной толщины стенки <*>
--------------------------------
<*> Отношение
номинальных толщин стенки труб
- не более 1,5. Сварное соединение выполняется
без обязательной подварки изнутри ручной дуговой сваркой корневого слоя шва.
Рисунок
10.17. Геометрические параметры разделки кромок
и сборки соединений
труб для сварки комплексом CWS.02
Рекомендуемая схема
сварки комплексом CWS.02 неповоротных кольцевых стыковых соединений труб
приведена на рисунке 10.18.
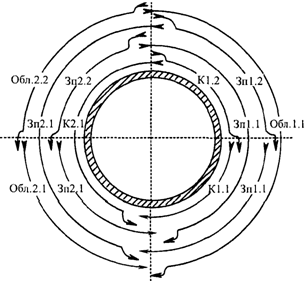
В обозначении слоев
шва приняты сокращения:
К - корневой слой;
Зп - заполняющий слой,
Обл. - облицовочный
слой; первая цифра обозначает
половину сварного
соединения относительно вертикальной оси
(1 - правая
половина, 2 - левая половина); вторая цифра
обозначает
последовательность сварки в пределах слоя;
- указывает направление сварки
Рисунок 10.18.
Рекомендуемая схема сварки комплексом CWS.02
неповоротных
кольцевых стыковых соединений труб
Допускается сварку
облицовочного слоя выполнять за два прохода.
Геометрические
параметры сварного шва, выполненного сварочным комплексом CWS.02, приведены на
рисунке 10.19.

Рисунок 10.19.
Геометрические параметры сварного шва,
выполненного
сварочным комплексом CWS.02
Рекомендуемые
параметры режимов сварки комплексом CWS.02 неповоротных кольцевых стыковых
соединений труб диаметром от 1020 до 1420 мм приведены в таблице 10.21. Режимы
сварки изменяются через каждые 15° при отсчете положения сварочной головки от
зенита трубы в угловых координатах.
Таблица 10.21
Рекомендуемые
режимы сварки комплексом CWS.02
соединений труб
диаметром от 1020 до 1420 мм
┌───────────┬────────────────────────────────────────────────────────────────────────┐
│
Параметры │ Режимы сварки (по слоям) │
│
├───────────┬───────────┬───────────┬───────────┬───────────┬────────────┤
│ │ корневой │
1-й │ 2-й
│ 3-й │
4-й │облицовочный│
│ │ │заполняющий│заполняющий│заполняющий│заполняющий│ │
├───────────┼───────────┼───────────┼───────────┼───────────┼───────────┼────────────┤
│Направление│
На спуск │ На спуск │ На спуск │ На спуск │ На спуск │ На спуск │
│сварки │ │ │ │ │ │ │
├───────────┼───────────┼───────────┼───────────┼───────────┼───────────┼────────────┤
│Скорость │34,8 - 51,6│27,0 -
30,0│21,0 - 23,4│20,4 - 22,8│19,2 - 22,8│ 6,6 - 13,8
│
│сварки,
м/ч│ │ │ │ │ │ │
├───────────┼───────────┼───────────┼───────────┼───────────┼───────────┼────────────┤
│Диаметр │
1,0 │ 1,0
│ 1,0 │
1,0 │ 1,0
│ 1,0 │
│электродной│ │ │ │ │ │ │
│проволоки,
│ │ │ │ │ │ │
│мм │ │ │ │ │ │ │
├───────────┼───────────┼───────────┼───────────┼───────────┼───────────┼────────────┤
│Скорость │11,0 - 12,5│ 9,4 - 11,0│
9,5 - 10,3│ 9,5 - 10,3│ 7,1 - 8,0 │ 3,0 - 6,2 │
│подачи │ │ │ │ │ │ │
│электродной│ │ │ │ │ │ │
│проволоки,
│ │ │ │ │ │ │
│м/мин │ │ │ │ │ │ │
├───────────┼───────────┼───────────┼───────────┼───────────┼───────────┼────────────┤
│Вылет │
8 - 12 │ 10 - 14
│ 10 - 14 │
10 - 14 │ 10 - 14
│ 8 - 12 │
│электродной│ │ │ │ │ │ │
│проволоки,
│ │ │ │ │ │ │
│мм │ │ │ │ │ │ │
├───────────┼───────────┼───────────┼───────────┼───────────┼───────────┼────────────┤
│Защитный │
0/100 │ 0/100
│ 40/60 │
40/60 │ 40/60
│ 60/40 │
│газ
Ar/CO ,│ │ │ │ │ │ │
│ 2 │ │ │ │ │ │ │
│% │ │ │ │ │ │ │
├───────────┼───────────┼───────────┼───────────┼───────────┼───────────┼────────────┤
│Расход │
25 - 28 │ 25 - 28
│ 25 - 28 │
25 - 28 │ 25 - 28
│ 25 - 28 │
│газа, │ │ │ │ │ │ │
│л/мин │ │ │ │ │ │ │
├───────────┼───────────┼───────────┼───────────┼───────────┼───────────┼────────────┤
│Сила
тока, │ 240 - 290 │ 220 - 270 │ 200 - 245 │ 200 - 245
│ 200 - 245 │ 119 - 170
│
│А │ │ │ │ │ │ │
├───────────┼───────────┼───────────┼───────────┼───────────┼───────────┼────────────┤
│Напряжение
│20,4 - 22,2│21,8 - 22,4│20,6 - 21,0│20,6 -
21,2│19,0 - 20,0│15,8 - 18,8 │
│на
дуге, В │ │ │ │ │ │ │
├───────────┼───────────┼───────────┼───────────┼───────────┼───────────┼────────────┤
│Скорость │ 176 - 200 │ 260 - 270 │
250 - 270 │ 250 - 270 │ 220 - 254 │ 90 - 180
│
│колебаний │ │ │ │ │ │ │
│электродной│ │ │ │ │ │ │
│проволоки,
│ │ │ │ │ │ │
│см/мин │ │ │ │ │ │ │
├───────────┼───────────┼───────────┼───────────┼───────────┼───────────┼────────────┤
│Амплитуда │ 0,5 - 1,5 │ 4,0 - 4,5 │
5,0 - 5,5 │ 6,0 - 6,5 │ 7,0 - 7,5 │ 9,0 - 9,5 │
│колебаний │ │ │ │ │ │ │
│электрода,
│ │ │ │ │ │ │
│мм │ │ │ │ │ │ │
├───────────┼───────────┼───────────┼───────────┼───────────┼───────────┼────────────┤
│Задержка │0,00 - 0,32│0,20 - 0,24│0,20
- 0,24│0,20 - 0,26│0,20 - 0,32│0,30 - 2,3 │
│электродной│ │ │ │ │ │ │
│проволоки │ │ │ │ │ │ │
│в
крайних │ │ │ │ │ │ │
│положениях,│ │ │ │ │ │ │
│с │ │ │ │ │ │ │
├───────────┼───────────┼───────────┼───────────┼───────────┼───────────┼────────────┤
│Угол │
+/- 5 │ +/- 5
│ +/- 5 │
+/- 5 │ +/- 5
│ +/- 5 │
│наклона │ │ │ │ │ │ │
│электродной│ │ │ │ │ │ │
│проволоки,
│ │ │ │ │ │ │
│° │ │ │ │ │ │ │
├───────────┴───────────┴───────────┴───────────┴───────────┴───────────┴────────────┤
│ Примечания. 1. Параметры
режимов сварки соединений
труб могут │
│корректироваться
при производственной аттестации технологии сварки. │
│ 2. Допускаются отклонения процентного
содержания компонентов в газовой
│
│смеси
в пределах +/- 10% от указанного в таблице. │
│ 3. Количество заполняющих слоев.
│
└────────────────────────────────────────────────────────────────────────────────────┘
10.6.3.
Автоматическая односторонняя сварка проволокой сплошного сечения и порошковой
проволокой в защитных газах сварочными головками М300-С (М300)
10.6.3.1. Сварочные
головки М300-С (М300) (ф. CRC - Evans AW) предназначены для автоматической
односторонней сварки проволокой сплошного сечения в защитных газах (ААДП)
корневого слоя методом STT и порошковой проволокой в защитных газах (АПИ)
горячего прохода, заполняющих и облицовочного слоев шва (далее - сварка
головками М300-С (М300)) неповоротных кольцевых стыковых соединений труб
газопроводов одной толщины стенки диаметром от 426 до 1420 мм.
10.6.3.2. Сварочным
головками М300-С (М300) выполняется:
- односторонняя
однодуговая сварка двумя сварочными головками на спуск снаружи трубы корневого
слоя шва проволокой сплошного сечения в защитных газах методом STT;
- односторонняя
однодуговая сварка двумя сварочными головками на спуск или на подъем снаружи
трубы горячего прохода шва порошковой проволокой в защитных газах;
- односторонняя
однодуговая сварка двумя сварочными головками на подъем снаружи трубы
заполняющих и облицовочного слоев шва порошковой проволокой в защитных газах.
10.6.3.3. Кромки
труб для сварки корневого слоя шва проволокой сплошного сечения в защитных
газах методом STT должны иметь нормативную заводскую разделку либо должны быть
подготовлены механическим способом станками подготовки кромок типа СПК в
соответствии с требованиями рисунка 6.1.
10.6.3.4. Проволоки
сплошного сечения, порошковые проволоки, рекомендованные для сварки головками
М300-С (М300), приведены в таблице Д.12 (Приложение Д).
10.6.3.5. Сварка
всех слоев шва (корневого слоя, горячего прохода, заполняющих и облицовочного
слоев шва) выполняется в смеси защитных газов с постоянным процентным
содержанием (пределами) каждого газа (75% Ar + 25%
).
10.6.3.6. Сварка
выполняется несколькими сварочными комплексами (установками) в составе сборочно-сварочной
колонны по поточно-расчлененной схеме (корневой слой шва - одним сварочным
комплексом, горячий проход шва - одним сварочным комплексом, заполняющие слои -
одним или несколькими сварочными комплексами, облицовочный слой - одним или
несколькими сварочным комплексами) либо одним сварочным комплексом с двумя
сварочными головками всех слоев шва.
10.6.3.7.
Регулирование параметров режимов сварки головками М300-С (М300) в установленных
системой автоматического управления пределах выполняется через выносной пульт
дистанционного управления (установка сварочной горелки по оси стыкового
соединения, вылет электродной проволоки, амплитуда колебаний электродной
проволоки, время задержки электродной проволоки на кромке, скорость сварки).
10.6.3.8. В
сварочный комплекс (установку) входят:
- две сварочные
головки М300-С (М300) с механизмами подачи сварочной проволоки (одна резервная
- рекомендательно), с пультами дистанционного управления для однодуговой сварки
всех слоев шва (корневой слой, горячий проход, заполняющие слои, облицовочный
слой);
- два электронных
блока управления параметрами режимов сварки на каждую сварочную головку;
- направляющий пояс
на две сварочные головки (один резервный - рекомендательно);
- агрегат
энергообеспечения с дизель-генератором на базе колесной или гусеничной техники
с двумя специальными источниками сварочного тока инверторного типа (Invertec
STT II) для сварки корневого слоя шва методом STT на каждую сварочную горелку
(один резервный - рекомендательно), двумя источниками сварочного тока
инверторного или тиристорного типа на каждую сварочную головку (один резервный
- рекомендательно) для сварки горячего прохода, заполняющих и облицовочного
слоев шва и не менее одного резервного, со стрелой установки и перемещения
защитных инвентарных укрытий (палаток), с рампой баллонов защитных газов,
газовыми смесителями с оборудованием контроля расхода и состава смеси газов.
10.6.3.9. Сварочные
головки М300-С (М300) должны отвечать требованиям к установке следующих
параметров режимов сварки:
- скорость и
направление сварки;
- скорость подачи
электродной проволоки;
- амплитуда и
частота колебаний электродной проволоки;
- время задержки
электрода в крайних положениях;
- время
предварительной и послесварочной подачи газа.
10.6.3.10.
Рекомендуемая схема сварки головками М300-С (М300) неповоротных кольцевых
стыковых соединений труб приведена на рисунке 10.20.
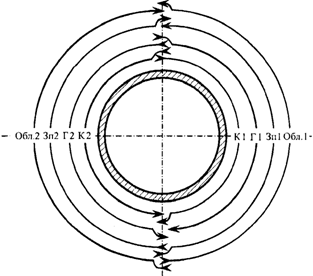
К1, К2 - участки
корневого слоя на левом
и правом
полупериметрах трубы; Г1, Г2 - участки
горячего прохода на
левом и правом полупериметрах трубы;
Зп1, Зп2 - участки
заполняющих слоев на левом и правом
полупериметрах
трубы; Обл. 1, Обл. 2 - участки облицовочных
слоев на левом и
правом полупериметрах трубы
Примечание.
допускается выполнять горячий проход на подъем.
Рисунок
10.20. Рекомендуемая схема сварки
головками М300-С
(М300) неповоротных кольцевых
стыковых соединений
труб
10.6.3.11. С целью
исключения попадания в полость труб влаги, снега и др. загрязнений концы труб
должны быть закрыты инвентарными заглушками или др. материалами.
10.6.3.12.
Заблаговременно, до начала сборочно-сварочных работ на концы труб, обращенные в
сторону движения сборочно-сварочной колонны, должны устанавливаться
направляющие пояса для сварочных головок М300-С (М300). Направляющие пояса
должны устанавливаться с применением инвентарных шаблонов, обеспечивающих
требуемую точность установки и входящих в комплект специальных приспособлений
(аксессуаров) сварочных головок.
10.6.3.13.
Предварительный подогрев кромок труб каждого стыкового соединения может
выполняться до сборки или после сборки на внутреннем центраторе, при этом
методы, оборудование и режимы предварительного подогрева должны соответствовать
требованиям 10.3.
10.6.3.14. Корневой
слой шва при сборке на внутреннем центраторе рекомендуется выполнять без
прихваток. В случае технической обоснованности применения прихваток они должны
быть удалены механическим способом при выполнении корневого слоя шва.
10.6.3.15. Перед
выполнением сварки корневого слоя шва методом STT необходимо установить:
а) на электронных
блоках управления сварочными головками М300-С (М300):
- скорость и
направление сварки;
- скорость подачи
электродной проволоки;
- амплитуду и
частоту колебаний электродной проволоки;
- время задержки
электрода в крайних положениях;
- время
предварительной и послесварочной подачи газа;
б) на специальных
инверторных источниках сварочного тока (Invertec STT II):
- значение пикового
тока;
- значение базового
тока;
- длительность
заднего фронта импульса;
в) на газовых
баллонах - специальные газовые редукторы, предназначенные для сварки методом
STT и предварительно настроенные на необходимый расход газа на
заводе-изготовителе.
10.6.3.16.
Рекомендуемые параметры режимов сварки корневого слоя шва методом STT сварочными
головками М300-С (М300) приведены в таблице 10.22.
Таблица 10.22
Рекомендуемые
параметры режимов сварки корневого слоя шва
методом STT
сварочными головками М300-С (М300)
┌───────────────────────────────────────────────────────────────┬─────────┐
│ Параметры режимов
сварки │Величина
│
│
│параметра│
├───────────────────────────────────────────────────────────────┼─────────┤
│Скорость
подачи электродной проволоки, м/мин │4,6 - 5,1│
├───────────────────────────────────────────────────────────────┼─────────┤
│Пиковый
ток, А
│400 - 460│
├───────────────────────────────────────────────────────────────┼─────────┤
│Базовый
ток, А
│ 50 - 90 │
├───────────────────────────────────────────────────────────────┼─────────┤
│Скорость
изменения заднего фронта импульса (Tailout), │ 3 - 5
│
│условн.
ед.
│ │
├───────────────────────────────────────────────────────────────┼─────────┤
│Установка
параметра горячего старта (Hot start), │1,5 - 3,0│
│условн.
ед. │ │
├───────────────────────────────────────────────────────────────┼─────────┤
│Вылет
электродной проволоки, мм │ 3 - 11 │
├───────────────────────────────────────────────────────────────┼─────────┤
│Скорость
сварки, см/мин │
20 - 35 │
├───────────────────────────────────────────────────────────────┼─────────┤
│Частота
колебаний электродной проволоки, см/с │ <*>
│
├───────────────────────────────────────────────────────────────┼─────────┤
│Амплитуда
колебаний электродной проволоки, мм │ <*>
│
├───────────────────────────────────────────────────────────────┼─────────┤
│Время
задержки электродной проволоки на кромке, с │ <*>
│
├───────────────────────────────────────────────────────────────┼─────────┤
│Угол
наклона электродной проволоки (вперед), ° │ 3 - 5
│
├───────────────────────────────────────────────────────────────┼─────────┤
│Расход
газа, л/мин
│ 24 - 28 │
├───────────────────────────────────────────────────────────────┴─────────┤
│
<*> При зазоре от 2,4 до 3,0 мм
на участке стыкового
соединения в│
│ 00
30
│
│положении
от 0 до 1 ч сварку корневого слоя на данном участке
следует│
│выполнять с
колебаниями электродной проволоки:
частота колебаний -│
│7,1 см/с;
время задержки - от 0
до 0,7 с;
амплитуда колебаний -│
│регулируется
по месту. На других
участках шва сварка выполняется без│
│поперечных
колебаний электродной проволоки. │
│
│
│ Примечание.
Уточненные параметры режимов
сварки труб конкретных│
│типоразмеров должны
быть подтверждены
результатами производственной│
│аттестации технологии
сварки и зафиксированы в
операционно- │
│технологической
карте сборки и сварки. │
└─────────────────────────────────────────────────────────────────────────┘
10.6.3.17. Сварка
корневого слоя шва должна выполняться постоянным током обратной полярности.
Направление сварки - на спуск. Каждой сварочной головкой выполняется сварка
одного из полупериметров трубы (относительно вертикальной оси), при этом сварку
второй сварочной головкой рекомендуется начинать после сварки первой головкой
участка периметра сварного соединения, длина которого достаточна для
одновременной работы сварочных головок.
10.6.3.18.
Начальный и конечный участок корневого слоя шва, выполненного первой сварочной
головкой, следует обработать механическим способом шлифмашинкой для обеспечения
плавного перехода при сварке корневого слоя шва второй сварочной головкой.
10.6.3.19. После
выполнения корневого слоя шва его необходимо зачистить механическим способом
шлифмашинками с набором абразивных кругов и дисковых проволочных щеток.
10.6.3.20. При
наличии видимых дефектов корневого слоя шва типа пор, непроваров и др.
необходимо выполнить подварку дефектных участков ручной дуговой сваркой
электродами с основным видом покрытия согласно требованиям 10.2.40 - 10.2.42.
10.6.3.21. Операции
по подварке изнутри корневого слоя шва следует рассматривать как составную
часть технологического процесса и предусматривать при составлении
операционно-технологических карт сборки и сварки.
10.6.3.22. Участки
корневого слоя шва с усилением, превышающим регламентируемые значения, следует
обработать механическим способом шлифмашинкой. Эти операции следует
предусматривать при составлении операционно-технологических карт сборки и
сварки и рассматривать как составную часть технологического процесса сварки
головками М300-С (М300).
10.6.3.23. Перед выполнением
сварки горячего прохода, заполняющих и облицовочных слоев шва необходимо
установить:
а) на электронных
блоках управления сварочными головками М300-С (М300):
- скорость и
направление сварки;
- скорость подачи
электродной проволоки;
- амплитуду и
частоту колебаний электродной проволоки;
- время задержки
электродной проволоки в крайних положениях;
- время
предварительной и послесварочной подачи газа;
б) на источниках
сварочного тока - заданные режимы сварки;
в) на газовых
баллонах - газовый редуктор, отрегулированный на заданный расход смеси газов.
10.6.3.24. Интервал
времени между окончанием сварки корневого слоя методом STT и началом сварки
горячего прохода (первого заполняющего слоя) должен составлять не более 10 мин.
10.6.3.25. Сварка
горячего прохода, заполняющих и облицовочного слоев шва сварочными головками
М300-С (М300) должна выполняться постоянным током обратной полярности.
10.6.3.26.
Направление сварки:
- горячего прохода
- на спуск или на подъем;
- заполняющих и
облицовочного слоев - на подъем.
10.6.3.27. Каждой
сварочной головкой выполняется сварка одного из полупериметров трубы
(относительно вертикальной оси), при этом сварку второй сварочной головкой
рекомендуется начинать после сварки первой головкой участка периметра сварного
соединения, длина которого достаточна для одновременной работы сварочных
головок.
10.6.3.28. Для
стыковых соединений труб диаметром от 1020 до 1420 мм следует соблюдать
следующую последовательность выполнения слоев шва:
- при выполнении
горячего прохода на спуск второй оператор начинает сварку после того, как
первый оператор выполнил сварку участка горячего прохода длиной не менее 1,0 м;
- при выполнении
горячего прохода, заполняющих, облицовочного слоев на подъем, второй оператор
начинает сварку после того, как первый оператор выполнил сварку участка
горячего прохода, заполняющих, облицовочного слоев длиной не менее 0,5 м, при
этом одному сварщику оператору следует выполнить вначале сварку на участке от
до
, а
затем на участке от
до
.
10.6.3.29. Места
начала и окончания сварки каждого последующего слоя сварного шва
("замки") должны быть смещены относительно мест начала и окончания
сварки предыдущего слоя шва на расстояние не менее 100 мм и после выполнения
сварки должны быть обработаны механическим способом для предотвращения
образования дефектов типа непроваров и удаления кратерных трещин.
10.6.3.30. После
завершения сварки заполняющих слоев шва выполняется облицовочный слой шва.
Амплитуда колебаний мундштука сварочной горелки при сварке облицовочного шва
должна обеспечивать необходимую величину перекрытия свариваемых кромок труб на
величину, регламентированную перечислением ж) 9.3.
10.6.3.31. После
завершения сварки следует осмотреть поверхность облицовочного слоя шва.
Выявленные наружные дефекты сварного шва (кратеры, поры, подрезы и др.) следует
удалить механическим способом шлифмашинкой и до проведения неразрушающего
контроля сварного соединения откорректировать автоматической сваркой на
участках вышлифовки. Участки облицовочного слоя шва с усилением, превышающим
регламентируемые значения ("замки"), следует обработать механическим
способом шлифмашинкой. Указанные операции считаются составной частью
технологического процесса сварки головками М300-С (М300) и должны быть
предусмотрены в операционно-технологических картах сборки и сварки, а также при
производственной аттестации технологии сварки.
10.6.3.32.
Рекомендуемые параметры режимов сварки головками М300-С (М300) горячего
прохода, заполняющих, облицовочного слоев порошковой проволокой диаметром:
- 1,20 мм приведены
в таблице 10.23;
- 1,32 мм (1,4 мм)
приведены в таблице 10.24.
Таблица 10.23
Рекомендуемые
параметры режимов сварки
головками М300-С
(М300) горячего прохода, заполняющих,
облицовочного слоев
порошковой проволокой диаметром 1,20 мм
Параметры
|
Наименование слоя шва
|
первый заполняющий
(горячий проход)
|
последующие
заполняющие
|
облицовочный
|
Направление
сварки
|
На спуск
|
На подъем
|
На подъем
|
На подъем
|
Скорость
сварки,
м/ч (дюйм/мин)
|
27 +/- 3
(18 +/- 2)
|
12,2
- 19,8
(8 - 13)
|
7,6 - 16,8
(5 - 11)
|
6,9 - 13,7
(4,5 - 9,0)
|
Скорость
подачи
электродной
проволоки, м/мин
(дюйм/мин)
|
6,9 - 7,4
(270 - 290)
|
5,6 - 7,1
(220 - 280)
|
7,6 - 8,6
(300 - 340)
|
6,6 - 7,1
(260 - 280)
|
Вылет
электродной
проволоки, мм
|
8 - 12
|
8 - 12
|
8 - 12
|
8 - 15
|
Сила
тока, А
|
190 - 220
|
160 - 200
|
220 - 250
|
190 - 215
|
Напряжение
на дуге,
В
|
20,5 - 22,5
|
20,5
- 22,5
|
21 - 23
|
20 - 22
|
Расход
защитного
газа, л/мин
|
32 - 42
|
Частота
колебаний
электродной
проволоки, бит/мин
|
130 - 160
|
90 - 120
|
80 - 100
|
90 - 120
|
Амплитуда
колебаний
электродной
проволоки, мм
|
Устанавливается по ширине
разделки
|
Время
задержки
электродной
проволоки на
кромках, с
|
0
|
0 - 0,1
|
0 - 0,6
|
0 - 0,6
|
Угол
наклона
электродной
проволоки (вперед),
°
|
0 - 7
|
Примечание. Уточненные параметры
режимов сварки труб
конкретных
типоразмеров должны быть
подтверждены результатами производственной
аттестации технологии сварки и
зафиксированы в
операционно-технологической карте сборки и сварки.
|
Таблица 10.24
Рекомендуемые
режимы сварки
сварочными
головками М300-С (М300) горячего прохода,
заполняющих,
облицовочного слоев порошковой проволокой
диаметром 1,32 мм
(1,4 мм)
Параметры
режимов сварки
|
Наименование слоя шва
|
первый заполняющий
(горячий проход)
|
последующие
заполняющие
|
облицовочный
|
Направление
сварки
|
На спуск
|
На подъем
|
На подъем
|
На подъем
|
Скорость
сварки, м/ч
(дюйм/мин)
|
27 +/- 3
(18 +/- 2)
|
12,2
- 19,8
(8 - 13)
|
7,6
- 16,8
(5 - 11)
|
6,9 - 13,7
(4,5 - 9)
|
Скорость
подачи
электродной проволоки,
м/мин (дюйм/мин)
|
5,1 - 5,6
(200 - 220)
|
4,3 - 5,3
(170 - 210)
|
5,8 - 6,6
(230 - 260)
|
4,8 - 5,3
(190 - 210)
|
Вылет
электродной
проволоки, мм
|
8 - 12
|
8 - 12
|
8 - 12
|
8 - 15
|
Сила
тока, А
|
190 - 220
|
160 - 200
|
220 - 250
|
190 - 215
|
Напряжение
на дуге, В
|
20,5
- 22,5
|
20,5
- 22,5
|
21 - 23
|
20 - 22
|
Расход
защитного газа,
л/мин
|
32 - 42
|
Частота
колебаний
электродной проволоки,
бит/мин
|
130 - 160
|
90 - 120
|
80 - 100
|
90 - 120
|
Амплитуда
колебаний
электродной проволоки,
мм
|
Устанавливается по ширине
разделки
|
Время
задержки
электродной проволоки
на кромках, с
|
0
|
0 - 0,1
|
0 - 0,6
|
0 - 0,6
|
Угол
наклона электродной
проволоки (вперед), °
|
0 - 7
|
Примечание. Уточненные параметры
режимов сварки труб
конкретных
типоразмеров должны быть
подтверждены результатами производственной
аттестации технологии сварки
и зафиксированы в
операционно-
технологической карте сборки и сварки.
|
10.6.4.
Автоматическая двухсторонняя сварка под флюсом
10.6.4.1.
Автоматическая двухсторонняя сварка проволокой сплошного сечения под флюсом
(АФ) трубосварочными базами типа БТС рекомендуется для сварки поворотных
кольцевых стыковых соединений трубных секций диаметром от 1020 до 1420 мм с
толщинами стенок от 12,0 до 27,0 мм.
Технология
двухсторонней автоматической сварки проволокой сплошного сечения под флюсом
трубосварочными базами типа БТС поворотных кольцевых стыковых соединений труб
обеспечивает полную механизацию сборочно-сварочных и транспортных операций в
процессе изготовления трубных секций и гарантирует сохранность наружной
изоляции труб.
Подготовку, сборку
и предварительный подогрев свариваемых труб следует выполнять в соответствии с
требованиями 10.2, 10.3.
При подготовке
производится механическая обработка торцов труб станками типа СПК, входящими в
состав оборудования трубосварочной базы. Геометрические параметры разделки
кромок труб для двухсторонней автоматической сварки под флюсом приведены на
рисунке 10.21.
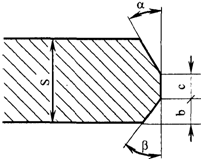
┌───────────┬─────────────────────────────────────────────────────────────┐
│Обозначение│ Величина параметра при толщине стенки
трубы (S, мм) │
│
параметра
├────────────────────┬────────────────────┬───────────────────┤
│ │
св. 10,0 до 18,0 │ св. 18,0 до 21,0 │ св. 21,0 до 27,0 │
├───────────┼────────────────────┼────────────────────┼───────────────────┤
│ │ +0° │ +0° │ +0° │
│
альфа, ° │ 30° │ 25° │ 25° │
│ │ -5° │ -3° │ -3° │
├───────────┼────────────────────┼────────────────────┼───────────────────┤
│ │ +0° │ +0° │ +0°
│
│ бета, °
│ 35° │ 35° │ 35° │
│ │ -5° │ -3° │ -3° │
├───────────┼────────────────────┼────────────────────┼───────────────────┤
│ b, мм
│ 1,0 +/- 0,5 │
3,0 +/- 0,5 │ 4,0 +/- 0,5 │
├───────────┼────────────────────┼────────────────────┼───────────────────┤
│ c, мм
│ 7,0 +/- 1,0 │
8,0 +/- 1,0 │ 8,0 +/- 1,0 │
└───────────┴────────────────────┴────────────────────┴───────────────────┘
Рисунок
10.21. Геометрические параметры разделки
кромок труб для
двухсторонней автоматической сварки
под флюсом
Усиление заводского
шва изнутри и снаружи трубы следует сошлифовать до величины от 0,5 до 1,0 мм на
ширине от 15 до 20 мм от торца.
10.6.4.2. Сварка
осуществляется с использованием аттестованных комбинаций "агломерированный
флюс + проволока" либо "плавленый флюс + проволока".
Перечень
аттестованных комбинаций "агломерированный флюс + проволока" для сталей
различных прочностных групп приведен в таблице Д.13 (Приложение Д).
10.6.4.3.
Последовательность выполнения слоев шва:
- первый наружный
слой шва;
- последующие
наружные слои шва;
- внутренний слой
шва.
Рекомендуется
выполнять одновременную сварку второго наружного и внутреннего слоев шва.
Сварное соединение
следует повернуть на 180° таким образом, чтобы прихватка находилась в нижней
части стыкового соединения (в положении
),
после чего в верхней части стыкового соединения (в положении
)
начинают сварку первого наружного слоя шва.
Во избежание
образования шлаковых включений и непроваров рекомендуется выполнять
шлифмашинкой пропилы начального и конечного участков прихватки, а также
начального участка первого наружного слоя. Глубина пропила - от 3,0 до 4,0 мм,
ширина - от 3,0 до 4,0 мм, длина - от 25 до 40 мм. Допускается шлифовка
усиления на прихватке до 0,5 - 1,0 мм.
Режимы
двухсторонней автоматической сварки поворотных кольцевых стыковых соединений
труб с использованием комбинаций "плавленый флюс + проволока"
приведены в таблице 10.25, комбинаций "агломерированный флюс +
проволока" представлены в таблице 10.26.
Таблица 10.25
Режимы
двухсторонней автоматической сварки поворотных
кольцевых стыковых
соединений труб с использованием
комбинаций
"плавленый флюс + проволока"
Толщина
стенки
трубы, мм
|
Диаметр
электродной
проволоки,
мм
|
Порядковый
номер слоя
|
Сварочный
ток, А
|
Напря-
жение
на
дуге, В
|
Ско-
рость
сварки,
м/ч
|
Смещение
электрода
с зенита
(надира)
трубы
<*>, мм
|
Наружная
сварка
|
12,0
- 17,5
|
3,0; 3,2
|
Первый
|
650
- 800
|
42
- 44
|
40
- 50
|
50 - 70
|
Последующие
|
700
- 800
|
44
- 46
|
35
- 45
|
40 - 60
|
17,6
- 27,0
|
3,0; 3,2
|
Первый
|
800
- 900
|
42
- 44
|
40
- 50
|
60 - 80
|
Последующие
|
850
- 950
|
44
- 46
|
45
- 55
|
50 - 70
|
Облицовочный
|
750
- 800
|
46
- 48
|
40
- 45
|
40 - 60
|
15,7
- 27,0
|
4,0
|
Первый
|
850
- 950
|
42
- 44
|
40
- 50
|
60 - 80
|
Последующие
|
900
- 1000
|
44
- 46
|
50
- 60
|
50 - 70
|
Облицовочный
|
800
- 900
|
46
- 48
|
40
- 45
|
40 - 60
|
Внутренняя сварка
|
12,0
- 17,5
|
3,0; 3,2
|
Первый
|
600
- 800
|
42
- 46
|
35
- 45
|
10 - 20
|
17,6
- 27,0
|
3,0; 3,2
|
Первый
|
700
- 850
|
42
- 46
|
40
- 50
|
10 - 20
|
15,7
- 27,0
|
4,0
|
Первый
|
750
- 850
|
44
- 46
|
40
- 50
|
15 - 25
|
<*> Смещение с зенита
трубы устанавливается
против направления ее
вращения, смещение с надира трубы - по или против направления вращения.
Примечания. 1. Сварочный ток -
постоянный, полярность обратная.
2. Вылет электродной
проволоки диаметром 3,0 и 3,2
мм составляет
от 35 до 40 мм, диаметром 4,0 мм - от 40 до 45 мм.
3. Угол наклона электродной
проволоки вперед - до 30° включ.
|
Таблица 10.26
Режимы
двухсторонней автоматической сварки поворотных
кольцевых стыковых
соединений труб с применением комбинаций
"агломерированный
флюс + проволока"
Толщина
стенки
трубы, мм
|
Диаметр
электродной
проволоки,
мм
|
Порядковый
номер слоя
|
Сварочный
ток, А
|
Напря-
жение
на
дуге, В
|
Скорость
сварки,
м/ч
|
Смещение
электрода
с зенита
(надира)
трубы
<*>, мм
|
Наружная
сварка
|
12,0
- 17,5
|
3,0; 3,2
|
Первый
|
650
- 750
|
29
- 32
|
40
- 50
|
50 - 70
|
Последующие
|
600
- 700
|
33
- 36
|
30
- 40
|
40 - 60
|
17,6
- 27,0
|
3,0; 3,2
|
Первый
|
700
- 780
|
30
- 34
|
38
- 45
|
55 - 70
|
Последующие
|
730
- 790
|
32
- 35
|
35
- 42
|
50 - 65
|
Облицовочный
|
580
- 650
|
34
- 37
|
30
- 35
|
45 - 60
|
15,7
- 27,0
|
4,0
|
Первый
|
750
- 830
|
29
- 33
|
35
- 45
|
55 - 75
|
Последующие
|
730
- 800
|
31
- 34
|
33
- 43
|
50 - 70
|
Облицовочный
|
700
- 750
|
33
- 36
|
30
- 33
|
45 - 60
|
Внутренняя
сварка
|
12,0
- 17,5
|
3,0; 3,2
|
Первый
|
630
- 750
|
31
- 33
|
31
- 36
|
(5
- 20)
|
17,6
- 27,0
|
3,0; 3,2
|
Первый
|
750
- 820
|
32
- 34
|
30
- 35
|
(5
- 20)
|
15,7
- 27,0
|
4,0
|
Первый
|
720
- 800
|
32
- 34
|
30
- 33
|
(10
- 50)
|
<*> Смещение с зенита
и надира трубы
устанавливается против
направления ее вращения.
Примечания. 1. Сварочный ток - постоянный,
полярность - обратная.
Источник питания должен
быть настроен для
сварки на жесткой вольт-
амперной характеристике. Отклонение напряжения на дуге
от номинального
значения должно быть не более +/- 1,0 В.
2. Вылет электродной проволоки - от 32 до
40 мм.
3. Угол наклона электродной
проволоки вперед - от
10° до 20° для
наружной сварки и от 2° до 8° для внутренней сварки.
4. Высота слоя флюса при сварке должна
быть не менее 25 мм. При его
повторном применении следует добавлять к ранее использованному флюсу
от
25 до 50% нового (неиспользованного) флюса.
|
10.6.4.4. Жимки
внутреннего центратора могут быть освобождены только после полного завершения
сварки первого наружного слоя шва.
10.6.4.5. Сварку
всех слоев шва следует производить без перерывов в работе. Интервал времени
между завершением первого наружного и началом сварки внутреннего слоя шва не
должен превышать 30 мин при температуре окружающего воздуха выше 0 °C и 10 мин
при температуре окружающего воздуха 0 °C и ниже.
10.6.4.6. При
заклинивании шлака в разделке во время сварки первого наружного слоя шва и для
улучшения сопряжения шва со стенками разделки смещение электрода с зенита трубы
рекомендуется увеличить на величину от 5 до 10 мм по сравнению со значениями,
приведенными в таблицах 10.25, 10.26.
10.6.4.7.
Минимальное число наружных слоев шва в зависимости от типоразмера труб
приведено в таблице 10.27.
Таблица 10.27
Минимальное число
наружных слоев шва при двухсторонней
автоматической
сварке под флюсом поворотных кольцевых
стыковых соединений
труб
┌──────────────────────┬─────────────────────────┬────────────────────────┐
│ Диаметр трубы, мм │Толщина стенки трубы, мм │ Минимальное число │
│ │ │ наружных слоев шва │
├──────────────────────┼─────────────────────────┼────────────────────────┤
│От
1020 до 1420 включ.│ от 12,0 до
21,5 включ. │ 2 │
│
├─────────────────────────┼────────────────────────┤
│ │ св. 21,5 до 24,0
включ. │ 3 │
│
├─────────────────────────┼────────────────────────┤
│ │ "
24,0 " 27,0 "
│ 4 │
└──────────────────────┴─────────────────────────┴────────────────────────┘
10.6.4.8.
Внутренний слой шва должен свариваться в один проход. Величина усиления
внутреннего и облицовочного слоев шва должна находиться в пределах от 1,0 до
3,0 мм. Ширина облицовочного слоя шва должна соответствовать требованиям
таблицы 10.28, а внутреннего слоя - таблицы 10.29.
Таблица 10.28
Ширина
облицовочного слоя шва соединений труб,
выполненных
двухсторонней автоматической сваркой под флюсом
┌───────────────────────────┬─────────────────────────────────────────────┐
│
Толщина стенки трубы, мм │ Ширина облицовочного слоя шва при сварке │
│ │ под флюсом │
│
├──────────────────────┬──────────────────────┤
│ │ плавленым │
агломерированным │
├───────────────────────────┼──────────────────────┼──────────────────────┤
│От 12,0 до 17,5 включ. │
18 +/- 3 │ 16 +/- 3 │
├───────────────────────────┼──────────────────────┼──────────────────────┤
│Св.
17,5 до 21,5 " │ 20 +/- 4 │ 18 +/- 3 │
├───────────────────────────┼──────────────────────┼──────────────────────┤
│" 21,5 "
24,0 " │ 21 +/- 4 │ 19 +/- 3 │
├───────────────────────────┼──────────────────────┼──────────────────────┤
│"
24,0 " 27,0
" │ 23 +/- 4 │ 21 +/- 3 │
└───────────────────────────┴──────────────────────┴──────────────────────┘
Таблица 10.29
Геометрические
параметры внутреннего слоя
шва соединений
труб, выполненных двухсторонней
автоматической
сваркой под флюсом
┌───────────────────────┬────────────────┬────────────────────────────────┐
│
Толщина стенки трубы, │
Глубина │Ширина
внутреннего слоя B , мм, │
│ мм │проплавления h ,│ B
│
│ │ B │ при сварке под флюсом │
│ │ мм (не
более)
├───────────────┬────────────────┤
│ │ │ плавленым
│агломерированным│
├───────────────────────┼────────────────┼───────────────┼────────────────┤
│От 12,0 до 12,3 включ.│ 7,0
│ 18 +/- 3 │
16 +/- 2 │
├───────────────────────┼────────────────┼───────────────┼────────────────┤
│Св.
12,3 до 15,2 включ.│ 8,0 │
18 +/- 3 │ 16 +/- 2
│
├───────────────────────┼────────────────┼───────────────┼────────────────┤
│" 15,2 "
18,0 " │
9,0 │ 20 +/- 3
│ 18 +/- 2 │
├───────────────────────┼────────────────┼───────────────┼────────────────┤
│" 18,0 "
21,0 " │
10,0 │ 20 +/- 4
│ 18 +/- 2 │
├───────────────────────┼────────────────┼───────────────┼────────────────┤
│" 21,0 "
27,0 " │
12,0 │ 20 +/- 4
│ 20 +/- 3 │
├───────────────────────┴────────────────┴───────────────┴────────────────┤
│ Примечание. Значение коэффициента формы
внутреннего слоя шва (B /h )│
│
B B │
│должно
быть не менее 2,0. │
└─────────────────────────────────────────────────────────────────────────┘
10.6.4.9.
Геометрические параметры сварных соединений труб, выполненных двухсторонней
автоматической сваркой под флюсом, определяемые по макрошлифам, должны
соответствовать требованиям рисунка 10.22 и таблицам 10.28, 10.29.
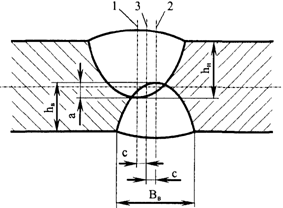
1 - ось первого
(наружного) слоя шва;
2 - ось внутреннего
слоя шва; 3 - условная ось сварного
соединения; a -
перекрытие наружного и внутреннего слоев
шва (a >= 3 мм);
c - смещение осей первого наружного
и внутреннего слоев
шва от условной оси сварного
соединения (c = +/-
1 мм);
и
- глубина
проплавления
соответственно первого наружного
и внутреннего слоев
шва;
- ширина
внутреннего слоя
шва
Рисунок 10.22.
Геометрические параметры
сварных соединений
труб, выполненных двухсторонней
автоматической
сваркой под флюсом
10.6.4.10.
Геометрические размеры сварных швов определяют на трех макрошлифах,
изготовленных из каждого 200-го сварного соединения. Темплеты для макрошлифов
вырезают на любом участке сварного соединения равномерно по периметру сварного
соединения, но не ближе 200 мм от места начала или окончания процесса сварки.
В случае отклонения
геометрических параметров от заданных значений сварку следует прекратить,
отладить оборудование и параметры режимов сварки, после чего выполнить сварку
двух новых соединений трубных секций, из которых вырезать макрошлифы. В случае,
если размеры сварных швов по макрошлифам соответствуют установленным
требованиям, сварку можно продолжить.
Остальные 199
сварных соединений, предшествующие первому вырезанному, следует считать
годными, если в результате неразрушающего контроля в них не выявлено
недопустимых дефектов.
Сварное соединение
считается годным, если облицовочный слой шва смещен относительно первого
наружного слоя, но при этом перекрывает всю его ширину, при условии отсутствия
недопустимых дефектов сварного шва и соблюдении заданных режимов. В данном
случае оси первого наружного слоя и внутреннего слоя шва должны совпадать или
быть смещены относительно друг друга на расстояние не более 2,0 мм.
10.6.4.11. Флюс,
остающийся на поверхности трубы в процессе сварки, следует ссыпать в чистый
сухой поддон, просеять через сито, освобождая его от кусков шлаковой корки и
инородных включений. Очищенный флюс допускается использовать повторно. При его
повторном применении следует добавлять к ранее использованному флюсу от 25% до
50% нового (неиспользованного) флюса. Флюс, оставшийся по окончании смены в
бункере сварочной головки, должен быть удален из бункера и помещен до следующей
смены в герметичную тару.
10.6.4.12. Не
допускается оставлять незаконченными сварные соединения, выполненные за одну
рабочую смену. В порядке исключения, в случае выхода из строя оборудования,
отключения сети и др. разрешается оставлять до следующей смены сварное
соединение трубной секции с невыполненным облицовочным слоем шва. Перед
возобновлением сварки следует выполнить предварительный подогрев до температуры
. При
невыполнении указанных требований сварное соединение должно быть вырезано.
10.6.4.13. Не
допускается сброс сваренных секций, их соударение, скатывание на мокрый грунт
или снег до полного остывания сварного соединения до температуры окружающей
среды.
10.6.5.
Автоматическая односторонняя сварка под флюсом
10.6.5.1.
Автоматическая односторонняя сварка проволокой сплошного сечения под флюсом
(АФ) рекомендуется для сварки заполняющих и облицовочного слоев шва поворотных
кольцевых стыковых соединений трубных секций:
-
диаметром от 530 до 1420 мм трубосварочными базами типа ССТ-ПАУ;
- "
от 325 до 820 мм
" " БНС.
Сварка поворотных
кольцевых стыковых соединений труб диаметром менее 325 мм может быть выполнена
на трубосварочных базах специальной конструкции, обеспечивающих качественное
выполнение всех сборочно-сварочных операций и сохранность наружной изоляции
труб.
10.6.5.2. Описание
технологии
Сварка корневого
слоя шва может быть выполнена следующими способами:
- ручной дуговой
сваркой электродами с покрытием основного вида, согласно требованиям 10.4.1;
- механизированной
сваркой проволокой сплошного сечения в углекислом газе методом STT с
применением оборудования фирмы The Lincoln Electric Company, согласно
требованиям 10.5.1;
- ручной дуговой
сваркой электродами с покрытием целлюлозного вида, согласно требованиям 10.4.2.
В данном случае должен быть выполнен также горячий проход шва. Сварку корневого
слоя и горячего прохода шва следует производить на одном стенде без
перекатывания и продольного перемещения трубной секции.
10.6.5.3. Сварка
осуществляется с использованием аттестованных комбинаций "агломерированный
флюс + проволока" либо "плавленый флюс + проволока".
Перечень комбинаций
"агломерированный флюс + проволока", прошедших аттестацию и
рекомендованных к применению приведен в таблице Д.13.
10.6.5.4. При ручной
сварке корневого слоя электродами с покрытием основного вида и механизированной
сварке методом STT допускается периодический поворот свариваемой секции без
освобождения жимков центратора в удобное для сварщиков положение. Перекатывание
секции на промежуточный стеллаж разрешается только после завершения сварки
корневого слоя по всему периметру стыкового соединения.
10.6.5.5. В случае
сварки корневого слоя шва электродами с покрытием основного вида для избежания
прожогов при автоматической сварке по всему периметру стыкового соединения
выполняется подварка корня шва изнутри трубы электродами с основным видом
покрытия либо выполняется первый заполняющий слой механизированной сваркой
самозащитной порошковой проволокой или электродами с основным видом покрытия.
10.6.5.6. В случае
выполнения корневого слоя шва и горячего прохода электродами с целлюлозным
покрытием или корневого слоя шва методом STT первый заполняющий слой перед
автоматической сваркой под флюсом следует выполнить механизированной сваркой
самозащитной порошковой проволокой или электродами с основным видом покрытия.
Подварка изнутри осуществляется только в местах непроваров и несплавлений или
других визуально определяемых дефектов.
10.6.5.7. Перед
выполнением подварочного слоя следует проконтролировать температуру изнутри
трубы, которая должна быть в интервале от +50 °C до +250 °C. В случае снижения
температуры ниже 50 °C следует произвести подогрев стыкового соединения до
температуры
.
10.6.5.8. Для
предотвращения остывания сварных соединений ниже минимальной температуры
предварительного подогрева и увлажнения после ручной дуговой или
механизированной сварки их следует укрывать до начала автоматической сварки под
флюсом влагонепроницаемыми теплоизоляционными поясами шириной не менее 300 мм.
В том случае, если температура свариваемых кромок опустилась ниже +50 °C,
следует произвести сопутствующий (межслойный) подогрев до температуры
.
10.6.5.9.
Рекомендуемые режимы автоматической сварки под флюсом заполняющих и
облицовочного слоев шва поворотных стыковых сварных соединений труб диаметром
от 325 до 1420 мм с использованием комбинации "плавленый флюс +
проволока" приведены в таблице 10.30.
Таблица 10.30
Рекомендуемые
режимы односторонней
автоматической
сварки поворотных кольцевых стыковых
соединений труб с
использованием комбинации
"плавленый
флюс + проволока"
Диаметр
труб,
мм
|
Толщина
стенки
трубы, мм
|
Диаметр
элек-
тродной
про-
волоки,
мм
|
Порядковый
номер слоя
|
Сварочный
ток, А
|
Напря-
жение
на
дуге, В
|
Ско-
рость
сварки,
м/ч
|
Смеще-
ние
элек-
трода с
зенита
трубы,
мм
|
325
-
426
|
6,0
|
2,0
|
1-й
|
350
- 450
|
34
- 36
|
15
- 20
|
35
- 40
|
Последующие
|
350
- 450
|
36
- 38
|
15
- 20
|
30
- 35
|
Св. 6,0
до 12,5
включ.
|
2,0/2,5
|
1-й
|
400
- 500
|
34
- 36
|
30
- 35
|
35
- 40
|
Последующие
|
450
- 500
|
36
- 38
|
25
- 30
|
30
- 35
|
Более
12,5
|
3,0/3,2
|
1-й
|
500
- 600
|
34
- 36
|
25
- 35
|
35
- 40
|
Последующие
|
600
- 700
|
36
- 38
|
30
- 40
|
30
- 40
|
530
-
820
|
6,0
-
12,5
|
2,0/2,5
|
1-й
|
400
- 500
|
36
- 38
|
35
- 40
|
40
- 60
|
Последующие
|
450
- 550
|
40
- 44
|
30
- 40
|
30
- 40
|
3,0/3,2
|
1-й
|
500
- 600
|
42
- 44
|
35
- 45
|
40
- 65
|
Последующие
|
600
- 700
|
44
- 46
|
30
- 40
|
30
- 45
|
Более
12,5
|
3,0/3,2
|
1-й
|
500
- 600
|
42
- 44
|
35
- 50
|
40
- 65
|
Последующие
|
600
- 750
|
44
- 48
|
30
- 45
|
30
- 45
|
1020
-
1420
|
7,0
-
12,5
|
3,0/3,2
|
1-й
|
500
- 600
|
44
- 46
|
40
- 50
|
60
- 80
|
Последующие
|
600
- 750
|
46
- 48
|
35
- 45
|
40
- 60
|
4,0
|
1-й
|
600
- 750
|
44
- 46
|
45
- 55
|
60
- 80
|
Последующие
|
700
- 850
|
46
- 48
|
35
- 45
|
40
- 60
|
Более
12,5
|
3,0/3,2
|
1-й
|
650
- 750
|
44
- 46
|
45
- 55
|
60
- 80
|
Последующие
|
500
- 600
|
46
- 48
|
40
- 50
|
40
- 60
|
4,0
|
1-й
|
700
- 850
|
44
- 46
|
50
- 60
|
60
- 80
|
Заполняющие
|
850
- 1000
|
46
- 48
|
45
- 55
|
50
- 70
|
Облицовочный
|
800
- 900
|
46
- 48
|
40
- 50
|
40
- 60
|
Примечания. 1. Сварочный ток -
постоянный, полярность - обратная.
2. Вылет электродной проволоки
диаметром 2,0 и 2,5 мм составляет от
30 до 35 мм, диаметром 3,0 и 3,2 мм - от 35 до 40 мм, диаметром 4,0 мм -
от 40 до 45 мм.
3. Смещение с зенита трубы
устанавливается против направления
ее
вращения.
4. Угол наклона электродной
проволоки вперед - до 30°.
|
10.6.5.10.
Рекомендуемые режимы сварки поворотных стыковых сварных соединений труб с
использованием комбинации "агломерированный флюс + проволока"
приведены в таблице 10.31.
Таблица 10.31
Рекомендуемые
режимы односторонней
автоматической
сварки поворотных кольцевых стыковых
соединений труб с
использованием комбинации
"агломерированный
флюс + проволока"
Диаметр
труб,
мм
|
Толщина
стенки
трубы,
мм
|
Диаметр
элек-
тродной
проволо-
ки, мм
|
Порядковый
номер слоя
|
Сварочный
ток, А
|
Напря-
жение
на
дуге, В
|
Ско-
рость
сварки,
м/ч
|
Смещение
электрода
с зенита
трубы, мм
|
1020
-
1420
|
8,0
-
12,5
|
3,0/3,2
|
1-й
|
500
- 550
|
27
- 30
|
45
- 50
|
60 - 80
|
Последующие
|
550
- 600
|
30
- 33
|
35
- 45
|
50 - 60
|
Облицовочный
|
600
- 650
|
34
- 36
|
30
- 35
|
40 - 60
|
4,0
|
1-й
|
500
- 550
|
26
- 29
|
40
- 50
|
60 - 80
|
Последующие
|
600
- 700
|
30
- 33
|
35
- 45
|
50 - 70
|
Облицовочный
|
650
- 750
|
34
- 37
|
30
- 35
|
40 - 65
|
Более
12,5
|
3,0/3,2
|
1-й
|
500
- 550
|
27
- 29
|
45
- 50
|
60 - 80
|
Последующие
|
550
- 650
|
30
- 33
|
35
- 45
|
50 - 60
|
Облицовочный
|
600
- 650
|
34
- 36
|
30
- 35
|
40 - 60
|
4,0
|
1-й
|
500
- 550
|
26
- 29
|
40
- 50
|
60 - 80
|
Последующие
|
650
- 750
|
30
- 33
|
35
- 45
|
50 - 70
|
Облицовочный
|
700
- 750
|
34
- 37
|
30
- 35
|
40 - 65
|
Примечания. 1. Сварочный
ток - постоянный,
полярность обратная.
Источник питания должен быть настроен
для сварки на
жесткой вольт-
амперной характеристике. Отклонение
напряжения на дуге от номинального
значения - не более +/- 1 В.
2. Вылет электродной проволоки составляет
от 30 до
40 мм. Угол
наклона электрода вперед составляет от 10° до 25°.
3. Смещение с зенита трубы
устанавливается против направления
ее
вращения.
4. Высота слоя флюса при сварке
должна быть не менее 25 мм. При его
повторном применении следует добавлять к ранее использованному флюсу
от
25% до 50% нового (неиспользованного) флюса.
|
10.6.5.11.
Минимальное число слоев шва (без учета подварочного слоя) соединений труб,
выполненных односторонней автоматической сваркой под флюсом, должно
соответствовать таблице 10.32.
Таблица 10.32
Минимальное число
наружных слоев шва
при односторонней
автоматической сварке под флюсом
поворотных
кольцевых стыковых соединений труб
┌────────────────────────────────────┬────────────────────────────────────┐
│ Толщина стенки трубы, мм │Минимальное число наружных слоев
шва│
├────────────────────────────────────┼────────────────────────────────────┤
│До 11,5 включ. │ 2 │
├────────────────────────────────────┼────────────────────────────────────┤
│Св.
11,5 до 16,5 включ.
│ 3 │
├────────────────────────────────────┼────────────────────────────────────┤
│Св.
16,5 до 20,5 включ.
│ 4 │
├────────────────────────────────────┼────────────────────────────────────┤
│
" 20,5 " 24,0
" │ 5 │
├────────────────────────────────────┼────────────────────────────────────┤
│
" 24,0 " 27,0
" │ 6 │
├────────────────────────────────────┴────────────────────────────────────┤
│ Примечание. В случае выполнения первого
заполняющего слоя электродами│
│с основным
покрытием или самозащитной
порошковой проволокой марки│
│"Иннершилд"
число автоматных слоев уменьшается на один слой. │
└─────────────────────────────────────────────────────────────────────────┘
10.6.5.12. При
сварке труб с толщиной стенки св. 23,0 мм рекомендуется выполнять заполняющие
(второй, третий и т.д.) и облицовочный слои шва параллельными (с перекрытием)
проходами (валиками). В этом случае напряжение на дуге снижают на величину от
2,0 до 4,0 В (для плавленых флюсов) и на величину от 1,0 до 2,0 В (для
агломерированных флюсов), а скорость сварки увеличивают не менее чем на 20%
(для плавленых флюсов) и на величину от 15% до 20% (для агломерированных
флюсов).
10.6.5.13. Ширина
облицовочного слоя шва, выполненного двумя параллельными проходами (валиками),
не должна превышать допустимой ширины однопроходного облицовочного шва в
соответствии с таблицей 10.33.
Таблица 10.33
Ширина
облицовочного слоя шва соединений труб,
выполненных
односторонней автоматической сваркой под флюсом
┌────────────────────────────┬────────────────────────────────────────────┐
│
Толщина стенки трубы, мм │ Ширина
облицовочного слоя шва при сварке
│
│ │ под флюсом, мм │
│
├──────────────────────┬─────────────────────┤
│ │ плавленым │
агломерированным │
├────────────────────────────┼──────────────────────┼─────────────────────┤
│От 6,0 до
8,0 включ. │ 14 +/- 3 │ 12 +/- 3 │
├────────────────────────────┼──────────────────────┼─────────────────────┤
│Св. 8,0 до 12,0 включ. │ 20 +/- 4 │ 19 +/- 3 │
├────────────────────────────┼──────────────────────┼─────────────────────┤
│От 12,0 до 16,0 включ. │ 23 +/- 4 │ 21 +/- 3 │
├────────────────────────────┼──────────────────────┼─────────────────────┤
│Св.
16,0 до 20,5 включ. │ 24 +/- 4 │ 22 +/- 3 │
├────────────────────────────┼──────────────────────┼─────────────────────┤
│
" 20,5 " 27,0
" │ 26 +/- 4 │ 24 +/- 4 │
└────────────────────────────┴──────────────────────┴─────────────────────┘
10.6.5.14. Не
допускается оставлять незаконченными сварные соединения, выполненные за одну
рабочую смену. В порядке исключения, в случае выхода из строя оборудования,
отключения сети и др. разрешается оставлять до следующей смены сварное
соединение трубной секции с невыполненным облицовочным слоем шва. Перед
возобновлением сварки должен быть выполнен предварительный подогрев до
температуры
.
10.6.5.15. Не
допускается сброс сваренных секций, их соударение при скатывании на грунт или
снег.
10.7. Сварка специальных сварных соединений
10.7.1. Сварка
разнотолщинных соединений труб, соединительных деталей трубопроводов, запорной
и регулирующей арматуры
10.7.1.1. Общие
требования
К разнотолщинным
сварным соединениям относятся:
- сварные
соединения труб, отличающихся по номинальной толщине стенки более чем на 2,0
мм;
- соединения СДТ с
трубами, переходными кольцами;
- соединения ЗРА с
трубами, переходными кольцами.
Допускается
выполнять сборку и сварку разнотолщинных соединений труб, труб с СДТ, труб с
ЗРА без дополнительной обработки (нутрения) кромок, если разность номинальных
толщин стенок свариваемых труб, СДТ, ЗРА не превышает:
- 2,5 мм
при максимальной толщине стенки до 12,0 мм включ.;
- 3,0
мм " " более 12,0 мм.
Подготовка, сборка
и сварка разнотолщинных сварных соединений производится в соответствии с
типовыми схемами, представленными на рисунке 10.23:
а) схема А -
применяется для соединений труб, труб с СДТ при разнотолщинности
не более 1,5;
б) схема Б -
применяется для соединений труб, труб с СДТ, труб с ЗРА газопроводов без
специальной обработки торца толстостенного элемента при разнотолщинности
не более 1,5;
в) схема В -
применяется для соединений труб, труб с СДТ, труб с ЗРА газопроводов в случае
специальной обработки торца толстостенного элемента с наружной стороны до
разнотолщинности элементов в зоне сварки
не более 1,5;
г) схема Г -
применяется для соединений труб, труб с СДТ, труб с ЗРА газопроводов в случае
специальной обработки торца толстостенного элемента как с наружной, так и с
внутренней стороны до разнотолщинности элементов в зоне сварки
не более 1,5. Допускается соединение труб с
СДТ заводского изготовления, имеющими кольцевую цилиндрическую расточку (на
схеме указана пунктиром) внутренней поверхности до соответствующего диаметра
присоединяемой трубы.
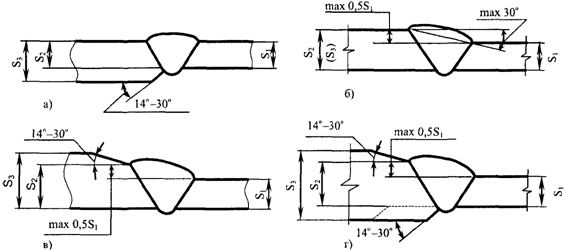
а) обработка стенки
с толщиной
с внутренней стороной
до размера
; б)
соединение
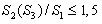
без дополнительной
обработки свариваемых торцов
;
в) обработка стенки
с толщиной
с наружной стороны
до размера
; г)
обработка стенки с толщиной

с наружной и
внутренней стороны до размера
;
- толщина стенки тонкостенного элемента;
- толщина
свариваемого торца
толстостенного элемента;
- толщина
стенки
толстостенного элемента
Рисунок
10.23. Геометрические параметры разнотолщинных
сварных соединений
труб, труб с СДТ, труб с ЗРА
При
разнотолщинности
более 1,5 (для схем А и Б - при
более 1,5) соединение элементов выполняется
путем вварки между ними переходного кольца или патрубка того же номинального
диаметра
с промежуточной толщиной стенки с
разнотолщинностью не более 1,5 по отношению к свариваемым элементам,
изготовленных в заводских условиях или трассовых условиях, длиной не менее 250
мм.
Выбор
конструктивных параметров разнотолщинных соединений, указанных на схемах б),
в), г) рисунка 10.23 должен определяться с учетом выполнения неравенства:
,
где
,
- нормативные значения толщины стенки (мм) и
временного сопротивления разрыву (МПа) элемента с меньшей толщиной стенки;
,
- нормативные значения толщины стенки (мм) и
временного сопротивления разрыву (МПа) элемента с большей толщиной стенки.
Допускается
разнотолщинность сварных соединений, указанных на схеме а) рисунка 10.23,
не более 1,5 при разности нормативных значений
временного сопротивления разрыву основного металла свариваемых элементов до 98
МПа (10 кгс/мм2) включительно, и разнотолщинность
не более 2,0 в случае равнопрочности основного
металла свариваемых элементов по нормативным значениям временного сопротивления
разрыву.
10.7.1.2. Сварка
разнотолщинных соединений труб
Сварка
разнотолщинных соединений труб может быть выполнена следующими технологиями
сварки:
- технология ручной
дуговой сварки электродами с основным видом покрытия всех слоев шва (РД);
- комбинированная
технология ручной дуговой сварки электродами с основным видом покрытия
корневого слоя шва и механизированной сварки самозащитной порошковой проволокой
заполняющих и облицовочного слоев шва (РД + МПС);
- комбинированная
технология ручной дуговой сварки электродами с основным видом покрытия
корневого слоя шва и автоматической сварки порошковой проволокой в защитных
газах сварочными головками М300-С (М300) фирмы CRC-Evans AW заполняющих и
облицовочного слоев шва (РД + АПИ);
- комбинированная
технология механизированной сварки проволокой сплошного сечения в среде
углекислого газа методом STT корневого слоя шва и ручной дуговой сварки
электродами с основным видом покрытия заполняющих и облицовочного слоев шва (МП
+ РД);
- комбинированная
технология механизированной сварки проволокой сплошного сечения в среде
углекислого газа методом STT корневого слоя шва и механизированной сварки
самозащитной порошковой проволокой заполняющих и облицовочного слоев шва (МП +
МПС);
- комбинированная
технология механизированной сварки проволокой сплошного сечения в среде
углекислого газа методом STT корневого слоя шва и автоматической сварки
порошковой проволокой в защитных газах сварочными головками М300-С (М300) фирмы
CRC-Evans AW заполняющих и облицовочного слоев шва (МП + АПИ);
- технология
автоматической двухсторонней сварки проволокой сплошного сечения в защитных
газах комплексами CRC-Evans, Autoweld.
При выполнении
разнотолщинных соединений труб с заводской разделкой кромок допускается
нутрение (растачивание изнутри) трубы с большей толщиной стенки (рисунок 10.23,
а) до величины меньшей толщины стенки
.
Допускается после выполнения нутрения двухскосую заводскую разделку кромки
путем механической обработки довести до односкосой с углом скоса кромки от 25°
до 30°.
Сборку
разнотолщинных соединений труб диаметром от 1020 до 1420 мм в зависимости от
применяемого способа сварки следует производить на внутреннем или наружном
центраторе.
Для разнотолщинных
соединений, указанных на схеме а) рисунка 10.23, наружное смещение кромок
должно соответствовать требованиям 10.2.19.
Для разнотолщинных
соединений, указанных на схемах б) и в) рисунка 10.23, смещение внутренних
кромок должно соответствовать требованиям, приведенным в перечислении а)
10.2.19.
Разнотолщинные
соединения труб должны выполняться с внутренней подваркой согласно требованиям
10.2.37, 10.2.40.
Сварка всех слоев
шва должна выполняться без перерыва до полного завершения сварки стыкового соединения.
10.7.1.3. Сварка
разнотолщинных соединений "труба + СДТ" и "труба + ЗРА"
Разнотолщинные
соединения "труба + СДТ" выполняются, как правило, согласно схеме а)
(рисунок 10.23), а соединение "труба + ЗРА" - согласно схемам б), в)
и г) (рисунок 10.23).
Сварка
разнотолщинных соединений "труба + СДТ", "труба + ЗРА"
может быть выполнена следующими технологиями сварки:
- технология ручной
дуговой сварки электродами с основным видом покрытия всех слоев шва (РД);
- комбинированная
технология механизированной сварки проволокой сплошного сечения в среде
углекислого газа методом STT корневого слоя шва и ручной дуговой сварки
электродами с основным видом покрытия заполняющих и облицовочного слоев шва (МП
+ РД);
- комбинированная
технология ручной дуговой сварки электродами с основным видом покрытия
корневого слоя шва и автоматической сварки порошковой проволокой в защитных
газах сварочными головками М300-С (М300) фирмы CRC-Evans AW заполняющих и
облицовочного слоев шва (РД + АПИ) <*>;
- комбинированная
технология механизированной сварки проволокой сплошного сечения в среде
углекислого газа методом STT корневого слоя шва и автоматической сварки
порошковой проволокой в защитных газах сварочными головками М300-С (М300) фирмы
CRC-Evans AW заполняющих и облицовочного слоев шва (МП + АПИ) <*>.
--------------------------------
<*> Только
для схемы "а" (рисунок 10.23).
Сборку и сварку
разнотолщинных соединений "переходное кольцо + ЗРА" рекомендуется
производить в стационарных (базовых) условиях, обеспечивающих возможность их
позиционирования и фиксации в удобном для сварки пространственном положении. До
сборки следует убедиться в совпадении их внутренних диаметров, выполнив замер
внутреннего диаметра ЗРА в зоне сварки и выполнив проверочный расчет по
формуле:
,
где
- фактический (измеренный) внутренний диаметр
ЗРА в зоне сварки, мм;
- номинальный внутренний диаметр трубы,
рассчитанный как разность номинального наружного диаметра и двух номинальных
толщин стенок, мм.
В случае
несоответствия заводской разделки кромки переходного кольца геометрическим
параметрам кромки ЗРА обработку (переточку) кромки переходного кольца под
сварку необходимо выполнять с учетом требований 10.2.8, 10.2.9.
Перед сборкой
следует осмотреть торцы труб, СДТ, ЗРА. Внутренняя поверхность ЗРА должна быть
защищена согласно рекомендациям завода-изготовителя. С кромок ЗРА или
переходного кольца дисковой проволочной щеткой следует удалить защитный
(консервационный) слой. Зачистить до металлического блеска кромки труб, СДТ,
ЗРА и прилегающие к ним внутреннюю и наружную поверхность на ширину не менее 15
мм.
Предварительный
подогрев стыковых сварных соединений "труба + СДТ" и "труба +
переходное кольцо ЗРА" следует выполнять в соответствии с требованиями
10.3.6.
В случае выполнения
предварительного подогрева температура на кромках стыкового соединения перед
сваркой корневого слоя шва (выполнением прихваток) должна быть не ниже +100 °C.
При наличии в
паспорте на ЗРА требований завода-изготовителя по максимально допустимой
температуре нагрева корпуса ЗРА в рабочей зоне следует предпринять меры по
ограничению нагрева (сопутствующее охлаждение) корпуса ЗРА в процессе
сборочно-сварочных операций.
Контроль
температуры предварительного подогрева следует проводить согласно 10.3.7.
Сборка
разнотолщинных соединений "труба + СДТ" и "труба + ЗРА"
должна выполняться с применением наружных центраторов. Допускается применение
специальных монтажных приспособлений (например, неприварных струбцин), обеспечивающих
сборку разнотолщинных соединений с различными наружными диаметрами соединяемых
элементов.
Приварка монтажных
приспособлений к трубам, СДТ и ЗРА не допускается.
Допускается, по
согласованию с органами технического надзора Заказчика, выполнять сборку
разнотолщинных соединений "труба + СДТ", "труба + ЗРА"
диаметром от 426 до 1420 мм на внутреннем центраторе, при этом должна быть
обеспечена защита внутренней поверхности ЗРА от попадания грязи, брызг металла,
окалины, шлака и других предметов. Для этой цели допускается применять
резиновые коврики и прокладки из несгораемых тканевых материалов. При
выполнении сборочно-сварочных работ ЗРА должна находиться в положении
"открыто".
Удаление наружного
центратора должно выполняться с учетом требований 10.2.31.
Разнотолщинные
соединения труб с СДТ и ЗРА должны выполняться с внутренней подваркой согласно
требованиям 10.2.37, 10.2.40.
В случае отсутствия
паспорта и/или сертификата СДТ, ЗРА ее приемка для сварки не разрешается без
освидетельствования в установленном порядке.
Механическую
обработку торцов СДТ, ЗРА станками подготовки кромок допускается выполнять в
монтажных (трассовых) условиях, если это оговорено в ТУ, при этом после
механической обработки должен быть выполнен визуально-измерительный и
ультразвуковой контроль обработанных кромок и торцов.
10.7.2. Сварка
стыковых соединений захлестов, прямых вставок (катушек)
10.7.2.1. Сварка
стыковых соединений захлестов, прямых вставок (катушек) при ликвидации
технологических разрывов производится по одной из нижеприведенных схем,
выбираемой исходя из конкретных условий выполнения работ:
а) схема 1
- оба конца трубопровода свободны (не засыпаны землей), находятся в траншее
(или на ее бровке) и имеют свободу перемещения, как в вертикальной, так и в
горизонтальной плоскостях;
б) схема 2
- конец одного из стыкуемых участков трубопровода свободно перемещается в
вертикальной и горизонтальной плоскостях, а другой защемлен (подходит к
крановому узлу, засыпан и т.п.);
в) схема 3
- оба конца соединяемых участков трубопровода засыпаны (защемлены), но оси
соединяемых участков находятся в пределах, соответствующих условиям сборки
(10.1).
10.7.2.2. В
соответствии с первыми двумя схемами соединение участков газопровода может
осуществляться сваркой одного захлестного соединения или путем вварки прямой
вставки (катушки) с выполнением двух кольцевых сварных соединений. В
соответствии с третьей схемой ликвидацию технологического разрыва производят
исключительно путем вварки прямой вставки (катушки) с выполнением двух
кольцевых сварных соединений.
10.7.2.3. Для
сварки стыковых сварных соединений захлестов, прямых вставок (катушек) могут
быть использованы следующие технологии и технологические варианты,
регламентированные настоящим стандартом:
- технология ручной
дуговой сварки электродами с основным видом покрытия всех слоев шва (РД);
- комбинированная
технология ручной дуговой сварки электродами с основным видом покрытия
корневого слоя шва и механизированная сварка самозащитной порошковой проволокой
заполняющих и облицовочного слоев шва (РД + МПС);
- комбинированная
технология ручной дуговой сварки электродами с целлюлозным видом покрытия
корневого слоя шва на подъем, горячего прохода на спуск и электродами с
основным видом покрытия заполняющих и облицовочного слоев шва (РД(Ц) + РД(Б));
- комбинированная
технология ручной дуговой сварки электродами с целлюлозным видом покрытия
корневого слоя шва на подъем, горячего прохода на спуск и механизированной
сварки самозащитной порошковой проволокой заполняющих и облицовочного слоев
шва, при этом горячий проход может выполняться механизированной сваркой
самозащитной порошковой проволокой (РД + МПС);
- комбинированная
технология механизированной сварки проволокой сплошного сечения в среде
углекислого газа методом STT корневого слоя шва и ручной дуговой сварки
электродами с основным видом покрытия заполняющих и облицовочного слоев шва (МП
+ РД);
- комбинированная
технология механизированной сварки проволокой сплошного сечения в среде
углекислого газа методом STT корневого слоя шва и механизированной сварки
самозащитной порошковой проволокой заполняющих и облицовочного слоев шва (МП +
МПС);
- комбинированная
технология механизированной сварки проволокой сплошного сечения в среде
углекислого газа методом STT корневого слоя шва и автоматической сварки
порошковой проволокой в защитных газах сварочными головками М300-С, М300 фирмы
CRC-Evans AW заполняющих и облицовочного слоев шва (МП + АПИ);
- комбинированная
технология ручной дуговой сварки электродами с основным видом покрытия
корневого слоя шва и автоматической сварки порошковой проволокой в защитных
газах сварочными головками М300-С, М300 фирмы CRC-Evans AW заполняющих и
облицовочного слоев шва (РД + АПИ).
10.7.2.4. До начала
сварочно-монтажных работ необходимо:
- произвести
откачку воды (при необходимости) в летнее время, а в зимнее время очистить
котлован (приямок) от снега;
- очистить наружную
поверхность газопровода на расстоянии не менее 2,0 м от торца, а также
внутреннюю полость трубы от возможных загрязнений (снег, лед, грунт и др.).
10.7.2.5. При
монтаже захлестного соединения по схеме 1 подготовительно-сборочные и сварочные
операции осуществляются в следующей последовательности:
- подготовить под
сварку один из концов трубопровода, уложить его на опоры высотой не менее 500
мм (по оси трубопровода) либо выкопать приямок необходимой величины;
- вывесить
трубоукладчиком вторую плеть рядом с первой и выполнить разметку места реза.
Разметка места реза должна быть произведена с помощью шаблона, чтобы обеспечить
перпендикулярность плоскости реза оси трубопровода;
- обрезать конец
трубы механизированной газовой резкой с последующей подготовкой кромок станком
типа СПК;
- состыковать трубы
путем подъема обрезанной плети трубоукладчиками с помощью мягких полотенец на
высоту не более 1,5 м на расстоянии от 40 до 50 м от конца трубы так, чтобы
обрезанный конец трубы провисал за счет упругих деформаций, что позволит
совместить один конец трубопровода с другим;
- осуществить
регулировку зазора в стыке изменением высоты подъема трубопровода
трубоукладчиками, установить страховочную опору и наружный центратор, выполнить
прихватку для фиксации сборочного зазора;
- произвести
предварительный подогрев захлестного соединения, выполнить сварку корневого
слоя шва с учетом требований 10.2.31, последующих заполняющих и облицовочного
слоев шва.
10.7.2.6. При
ликвидации технологического разрыва путем вварки прямой вставки (катушки)
катушка должна быть изготовлена из труб того же диаметра, той же толщины стенки
и класса прочности трубной стали, что и соединяемые участки газопровода, при
этом рекомендуемая длина прямой вставки (катушки) - не менее диаметра трубы.
10.7.2.7. Подготовка
труб к сборке и сварке прямых вставок - катушек (схема 2) осуществляется в
следующей последовательности:
- на торцах труб
соединяемых плетей произвести замер (с точностью 1,0 мм) их периметров по
внутренней и наружной поверхностям. На основании полученных результатов
произвести выбор трубы аналогичного размера и класса прочности для изготовления
катушки;
- подготовить
катушку длиной не менее одного диаметра трубы с разделкой кромок,
соответствующей разделке соединяемых труб. На одном из торцов катушки
целесообразно иметь заводскую разделку;
- при необходимости
освободить от грунта не защемленный участок трубопровода на длине от 80 до 100
м, необходимой для манипулирования плетью при сборке захлестного соединения;
- подготовить под
сварку защемленную плеть трубопровода, выкопав приямок, размеры которого
достаточны для безопасного проведения работ по сварке и контролю;
- приподнять
трубоукладчиками не защемленную плеть, установить опору и пристыковать катушку
к трубопроводу;
- произвести
предварительный подогрев;
- выполнить сборку
с применением наружного центратора, выполнить прихватку, зафиксировав
необходимый зазор;
- произвести
предварительный подогрев свариваемых кромок и выполнить сварку корневого слоя
шва, при этом отдельные участки корневого слоя шва должны быть равномерно
распределены по периметру сварного соединения. Снятие наружного центратора
должно выполняться с учетом требований 10.2.31. Перед продолжением сварки
корневого слоя шва все сваренные участки должны быть зачищены, а концы участков
- обработаны шлифмашинкой с абразивным кругом для обеспечения плавного перехода
при сварке оставшихся участков корневого слоя шва. После завершения сварки
корневого слоя шва выполняется сварка заполняющих и облицовочного слоев;
- вывесить
трубоукладчиком не защемленную плеть с приваренной катушкой и разметить на
катушке место реза;
- установить
страховочную опору и выполнить газовую резку с последующей подготовкой кромок
труб станком типа СПК;
- поднять
трубоукладчиком незащемленную плеть на высоту, необходимую для совмещения с
торцом защемленной плети трубопровода. В некоторых случаях вблизи зоны сварки
на поднятом конце трубопровода используется второй трубоукладчик;
- выполнить
предварительный подогрев, сборку и сварку второго стыкового соединения в соответствии
с выше приведенными регламентациями.
10.7.2.8. При
монтаже и сварке захлестного соединения по схеме 3, когда оба конца соединяемых
плетей защемлены (отсутствует возможность их свободного перемещения), работы
следует проводить в следующей последовательности:
- произвести
проверку соосности соединяемых участков трубопровода;
- выкопать приямок,
размеры которого достаточны для безопасного проведения работ по сварке и
контролю стыковых сварных соединений;
- на торцах труб
соединяемых плетей произвести замер (с точностью 1,0 мм) их периметров по
внутренней и наружной поверхностям. На основании полученных результатов произвести
выбор трубы аналогичного размера и класса прочности для изготовления прямой
вставки (катушки);
- изготовить прямую
вставку (катушку) длиной не менее одного диаметра трубы. Прямая вставка
(катушка) должна быть иметь тот же диаметр, толщину стенки и класса прочности,
что трубы соединяемых участков газопровода, при этом торцы прямой вставки
(катушки) должны иметь разделку кромок в соответствии с применяемой технологией
сварки;
- установить
трубоукладчиком прямую вставку (катушку) в место технологического разрыва
газопровода и выставить необходимые зазоры между свариваемыми кромками прямой
вставки (катушки) и трубами соединяемых участков газопровода, при этом сборка
должна выполняться с применением страховочной инвентарной опоры;
- выполнить
предварительный подогрев, сборку и сварку обоих захлестных сварных соединений,
при этом эти операции рекомендуется выполнять на обоих захлестных сварных
соединениях одновременно.
10.7.2.9. Сборку
стыковых сварных соединений захлестов, прямых вставок (катушек) следует выполнять
на наружных центраторах.
10.7.2.10. Для
повышения качества сборки стыковое соединение следует собирать с зазором
меньшим рекомендуемого на величину от 0,5 до 1,0 мм с последующим сквозным
калиброванным пропилом зазора абразивным кругом толщиной от 2,5 до 3,0 мм.
10.7.2.11. В
процессе монтажа захлестного соединения не допускается для установки требуемого
зазора или обеспечения соосности труб натягивать или изгибать трубы силовыми
механизмами, а также нагревать за пределами зоны сварного стыкового соединения.
10.7.2.12. В
процессе сварки захлестного соединения не допускается производить изменение
параметров монтажной схемы, зафиксированной к моменту завершения сборки.
Укладку (опускание) приподнятого при монтаже участка (участков) трубопровода
разрешается только после окончания сварки стыкового соединения.
10.7.2.13. Не
допускается сварка разнотолщинных труб при монтаже захлестов.
10.7.2.14. Не
допускается выполнение захлестов на соединениях труб с СДТ, ЗРА.
10.7.2.15. Сварку
захлестов, прямых вставок (катушек) следует выполнять в присутствии
ответственного руководителя при минимальной суточной температуре.
10.7.2.16. Сварку
захлестов, прямых вставок (катушек) следует выполнять без перерывов. Не
допускается оставлять незаконченными сварные соединения захлестов, прямых
вставок (катушек).
10.7.2.17. После
окончания сварки захлестное сварное соединение следует накрыть
влагонепроницаемым теплоизолирующим поясом до полного остывания.
10.7.3.
Ремонт сварных соединений
10.7.3.1. Ремонт
дефектов сварных соединений газопроводов, выполненных способами сварки,
регламентированными настоящим стандартом, должен выполняться ручной дуговой
сваркой (РД) электродами с основным видом покрытия.
10.7.3.2.
Допускается ремонт сваркой следующих дефектов сварных соединений:
- шлаковых
включений;
- пор;
- непроваров;
- несплавлений;
- подрезов.
Ремонт трещин не
допускается.
10.7.3.3. Суммарная
длина участков шва с недопустимыми дефектами не должна превышать 1/6 периметра
сварного шва. Максимальная длина единовременно ремонтируемого участка:
- 300 мм -
для сварных соединений диаметром от 720 до 1420 мм;
- 270
мм " " " 530 мм;
- 200
мм " " " 426 мм;
- 10%
периметра для сварных соединений диаметром
от 50 до 400.
Сварные соединения
диаметром
менее 50 с недопустимыми дефектами ремонту
сваркой не подлежат и должны быть вырезаны.
10.7.3.4.
Минимальная длина участка вышлифовки должна составлять не менее:
- 150 мм -
для сварных соединений
более 400;
- 100
мм " " " св. 175 до 400 включ.;
- 80
мм " " " св. 65 до 175 включ.;
- 60
мм " "
" св. 50 до 65 включ.
10.7.3.5. Ремонт
сварных соединений труб, СДТ, ЗРА диаметром до 1020 мм осуществляют только
снаружи <*>, а сварных соединений труб, СДТ, ЗРА диаметром 1020 мм и
более - снаружи или изнутри, в зависимости от глубины залегания дефекта.
--------------------------------
<*>
Допускается выполнять ремонт сварных соединений труб, СДТ, ЗРА диаметром менее
1020 мм изнутри с учетом требований 10.2.40.
10.7.3.6. Ремонт
изнутри трубы выполняется в том случае, если дефекты расположены в корневом
слое шва, подварочном слое и в горячем проходе (ремонт дефектов в горячем
проходе может осуществляться также снаружи трубы).
10.7.3.7. При
ремонте заполняющих слоев шва производится частичная U-образная выборка по
глубине шва с углом раскрытия кромок от 50° до 60° (рисунок 10.24, а).
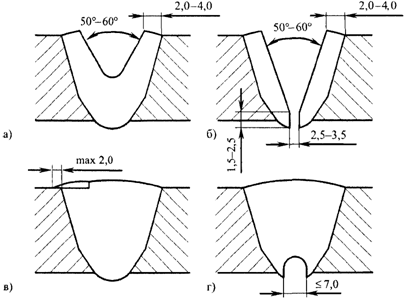
а) выборка дефектов
заполняющих слоев сварного шва;
б) выборка дефектов
корневого слоя шва при ремонте
снаружи трубы; в)
ремонт дефектов (подрезов, недостаточного
перекрытия) облицовочного
слоя шва; г) выборка дефектов
корневого слоя шва
при ремонте изнутри трубы
Рисунок
10.24. Геометрические параметры выборки
дефектов сварных
соединений
10.7.3.8. Ремонт
дефектов корневого слоя шва кольцевых стыковых сварных соединений диаметром
менее 1020 мм выполняется снаружи (со сквозным пропилом) при условии, что
дефекты расположены по центру (по оси) соответствующего слоя. В данном случае
должна быть обеспечена U-образная выборка части шва с углом раскрытия кромок от
50° до 60° глубиной, обеспечивающей остаточную толщину стенки трубы в интервале
от 1,5 до 2,5 мм, с последующим сквозным пропилом шлифовальным кругом толщиной
от 2,5 до 3,0 мм (рисунок 10.24, б). Границы выборки (разделки кромок) на
ремонтируемом участке должны быть прямолинейными и параллельными.
Аналогичная схема
ремонта в исключительных случаях, связанных с невозможностью доступа к
ремонтируемому участку изнутри трубы, может быть использована для стыковых
сварных соединений диаметром 1020 мм и более.
10.7.3.9. При
ремонте подрезов или недостаточного перекрытия в облицовочном слое шва и
подрезов в подварочном или внутреннем (при двухсторонней сварке) слоях шва
выполняется вышлифовка части сечения соответствующего ремонтируемого слоя
заподлицо с трубой. Ширина вышлифовки устанавливается таким образом, чтобы
ширина ремонтируемого шва не вышла за пределы допустимой величины (габариты
шва). Ремонт дефектов данного вида выполняется наложением одного или двух
валиков. Допускается увеличение ширины шва на участке ремонта не более чем на
2,0 мм (рисунок 10.24, в).
10.7.3.10. При
выборке дефектов снаружи трубы ширина раскрытия кромок должна быть меньше
ширины облицовочного слоя на величину от 2,0 до 4,0 мм, а при выборке дефектов
изнутри трубы ширина раскрытия кромок должна составлять не более 7,0 мм
(рисунок 10.24, г).
10.7.3.11. Во всех
случаях выборка дефектных участков должна осуществляться механическим способом
шлифмашинкой.
Для удаления
дефектных участков длиной более 200 мм допускается выполнять выборку
воздушно-дуговой строжкой, с последующей механической обработкой мест выборки
шлифмашинками на глубину от 0,5 до 1,0 мм.
Не допускается
выплавлять дефекты сваркой.
10.7.3.12.
Подготовку к ремонту осуществляют следующим образом:
- по результатам
неразрушающего контроля отмечают на стыке место расположения и тип дефекта.
Номер ремонтируемого стыкового соединения и место ремонта должны быть указаны
дефектоскопистом с использованием несмываемого маркера;
- руководитель
ремонтных работ и дефектоскопист производят разметку дефектного участка под
вышлифовку. Длина участка вышлифовки должна превышать фактическую длину
наружного или внутреннего дефекта не менее чем на 30 мм в каждую сторону.
Глубина вышлифованного участка должна быть больше глубины залегания дефекта на
величину от 1,0 до 2,0 мм;
- руководитель
ремонтных работ должен убедиться в том, что в процессе вышлифовки дефекты
вскрыты и удалены.
10.7.3.13. До
начала сварки должен быть выполнен предварительный подогрев выборки дефектного
участка до температуры
независимо от температуры окружающего воздуха
и толщины стенки трубы в соответствии с требованиями 10.3.1:
- на расстоянии не
менее 100 мм от границ выборки - при длине выборки до 150 мм включ.;
- всего периметра
сварного соединения - при длине выборки более 150 мм.
10.7.3.14. Ручная
дуговая сварка в процессе ремонта кольцевых стыковых сварных соединений труб
должна выполняться на подъем электродами с основным видом покрытия диаметром от
2,5 до 3,25 мм, приведенными в таблице Д.4 (Приложение Д). Рекомендуемые режимы
сварки приведены в таблице 10.6.
10.7.3.15. В
процессе сварки следует контролировать межслойную температуру, которая должна
быть не менее +50 °C. В случае остывания зоны сварки следует выполнить
сопутствующий подогрев до
.
10.7.3.16. Высота
каждого слоя при заварке дефектного участка не должна превышать 3,5 мм.
Рекомендуемая высота каждого слоя - от 2,5 до 3,5 мм.
10.7.3.17. В
процессе ремонта следует производить обязательную межслойную и окончательную
очистку слоев шва от шлака и брызг. Облицовочный (или внутренний подварочный)
слой шва должны быть подвергнуты чистовой обработке щеткой, шлифовальным кругом
и/или напильником для сглаживания грубой чешуйчатости и улучшения формы шва.
Следует также удалить щеткой брызги с прилегающей поверхности трубы.
10.7.3.18. Ремонт
сварных соединений трубных секций на трубосварочных базах следует производить в
удобном для выборки дефекта и сварки пространственном положении.
10.7.3.19.
Ремонтные работы должны осуществляться от начала до конца без длительных
перерывов.
10.7.3.20.
Повторный ремонт одного и того же дефектного участка не разрешается. Сварное
соединение должно быть вырезано. Минимальная длина прямой вставки (катушки),
ввариваемой на место вырезанного сварного соединения - не менее диаметра трубы,
но не менее 100 мм.
10.7.3.21. К
ремонтным работам допускаются сварщики ручной дуговой сварки, успешно прошедшие
допускные испытания по выполнению ремонтных работ в соответствии с
аттестованной технологией ремонта сваркой. Ремонт сварного соединения от начала
до конца должен выполнять один сварщик.
10.8. Сварка обвязочных газопроводов, узлов и оборудования
10.8.1. Общие
требования
10.8.1.1. Настоящий
подраздел регламентирует требования к порядку выполнения подготовительных,
монтажных и сварочных работ при строительстве, реконструкции и капитальном
ремонте газопроводов технологической обвязки <*> узлов и оборудования
промысловых и магистральных газопроводов, указанных в перечислениях 2, а) и 2,
б) 1.1.
--------------------------------
<*> Далее по
тексту обвязочные газопроводы.
10.8.1.2. Сварку
обвязочных газопроводов рекомендуется выполнять одним или несколькими способами
по технологиям, приведенным в 10.4 - 10.6:
- технологии ручной
дуговой сварки электродами с основным видом покрытия (РД) всех слоев шва
соединений
от 25 до 1400 с толщиной стенки 3,0 мм и
более;
- технологии ручной
аргонодуговой сварки неплавящимся электродом (РАД) всех слоев шва соединений
от 20 до 80 и толщиной стенки от 2,0 до 4,0 мм
или корневого слоя шва соединений
от 50 до 80 и толщиной стенки от 4,0 до 10,0
мм;
- технологии
механизированной сварки проволокой сплошного сечения в углекислом газе (МП)
корневого слоя шва соединений
300 и более;
- технологии
механизированной сварки самозащитной порошковой проволокой (МПС) заполняющих и
облицовочного слоев шва соединений
300 и более;
- технологии
автоматической сварки порошковой проволокой в защитных газах (АПИ) сварочными
головками М300-С, М300 фирмы CRC-Evans AW заполняющих и облицовочного слоев шва
соединений
400 и более с толщиной стенки 12,0 мм и более;
- комбинированной
технологии сварки (РД + МПС, РД + АПИ, РД + АФ, МП + РД, МП + МПС, МП + МПС +
АФ, РАД + РД и др.)
10.8.1.3.
Допускается применять механизированную сварку проволокой сплошного сечения в
углекислом газе (МПС) для сварки корневого слоя шва соединений труб
менее 300 при условии, что при сварке
корневого слоя шва прихватки полностью удаляются механическим способом
шлифмашинкой.
10.8.1.4.
Допускается применять одностороннюю автоматическую сварку под флюсом (АФ) для
сварки заполняющих и облицовочного слоев шва поворотных кольцевых стыковых
соединений укрупненных заготовок труб
200 и более в стационарных (базовых) условиях
на специальных стендах.
10.8.1.5. Сварку
трубопроводов импульсной обвязки узлов ЗРА
от 10 до 25 следует выполнять способами сварки
согласно ГОСТ 16037 (РД, РАД, газовая сварка) по операционно-технологическим
картам сборки и сварки, при условии проведения производственной аттестации
технологий сварки согласно требованиям РД 03-615-03 [3].
10.8.1.6.
Номенклатура труб, СДТ, ЗРА обвязочных газопроводов определяется проектной
документацией и должна соответствовать специальным техническим требованиям, ТУ,
ГОСТ.
10.8.1.7.
Подготовка, сборка, сварка труб, СДТ, ЗРА обвязочных газопроводов должна
выполняться с учетом требований 10.2 - 10.7 в соответствии с
операционно-технологическими картами сборки и сварки, разработанными по
аттестованным технологиям сварки. Допускается разрабатывать типовые
операционно-технологические карты сборки и сварки однотипных сварных соединений
по способам сварки, конструктивным элементам, классам прочности, диаметрам и
толщинам стенок свариваемых элементов.
10.8.1.8. Сборку и
сварку узлов и оборудования в укрупненные заготовки рекомендуется производить в
стационарных (базовых, заводских) условиях по рабочим чертежам проектной
документации. Разбивка узлов и оборудования на укрупненные заготовки
выполняется проектной организацией.
10.8.1.9. При
сборке стыковых соединений под сварку в горизонтальном положении с вертикальным
расположением осей труб, СДТ, ЗРА рекомендуется выполнить механическую
обработку кромок свариваемых под несимметричную разделку, при этом угол скоса
верхней кромки должен составлять от 30° до 35°, нижней кромки - от 10° до 15°.
10.8.1.10. Сборка
соединений обвязочных газопроводов под сварку должна выполняться с применением
сборочного оборудования и приспособлений (наружные и внутренние центраторы, струбцины
и др.) с учетом требований 10.2.15 - 10.2.17.
10.8.1.11. Для
сборки соединений обвязочных газопроводов с различными наружными диаметрами
свариваемых труб, СДТ, ЗРА сборочные приспособления (наружные центраторы,
струбцины и др.) должны быть специально подготовлены для обеспечения требуемых
параметров сборки (зазор, смещение кромок).
10.8.1.12.
Допускаются смещения кромок при сборке стыковых соединений обвязочных
газопроводов с учетом требований 10.2.19.
10.8.1.13. Величина
зазора при сборке стыковых соединений обвязочных газопроводов должна
назначаться в зависимости от способа сварки корневого слоя шва по таблице 10.1.
10.8.1.14.
Предварительный и сопутствующий подогрев свариваемых кромок труб, СДТ, ЗРА должен
выполняться в соответствии с требованиями и рекомендациями, указанными в 10.3.1
- 10.3.11. Допускается выполнять предварительный и сопутствующий подогрев
свариваемых кромок труб, СДТ, ЗРА
до 400 включ. однопламенными газовыми
горелками.
10.8.1.15. При
сварке температура предыдущего слоя перед наложением последующего слоя должна
быть в интервале, указанном в 10.3.11, при этом для сварных соединений труб,
переходных колец с ЗРА температура предыдущего слоя перед наложением
последующего слоя не должна превышать:
- +200 °C
при сварке соединения "переходное кольцо + ЗРА";
- +180
°C " " "труба + переходное кольцо".
10.8.1.16. Ручную
дуговую сварку (РД) соединений труб, СДТ, ЗРА обвязочных газопроводов
от 25 до 500 следует выполнять электродами с
основным видом покрытия диаметром:
- 2,5; 2,6
мм для соединений с толщиной стенки до 8,0 мм включ.;
- от 2,5
до 3,25 мм " " " св. 8,0 мм.
10.8.1.17. Сварные
соединения обвязочных газопроводов
до 250 включ. должны выполняться одним
сварщиком. Количество сварщиков ручной дуговой сварки выполняющих одновременно
сварку каждого слоя шва сварных соединений обвязочных газопроводов
св. 250 должно соответствовать требованиям
10.2.44. Требования к количеству операторов механизированной и автоматической
сварки приведены в соответствующих разделах по технологиям сварки 10.5, 10.6.
10.8.1.18. При
сварке заполняющих и облицовочных слоев соединений труб, СДТ, ЗРА в укрупненные
заготовки допускается периодически проворачивать сварное соединение в удобную
для сварщика позицию.
10.8.1.19.
Допускается снимать наружный центратор при сборке соединений обвязочных
газопроводов
до 400 включ. после выполнения прихваток.
10.8.1.20.
Количество слоев сварных швов соединений обвязочных газопроводов, выполненных
ручной дуговой сваркой, должно соответствовать требованиям таблицы 10.8.
Требования по количеству слоев сварных швов, выполненных механизированной и
автоматической сваркой, приведены в соответствующих разделах по технологиям
сварки 10.5, 10.6.
10.8.1.21.
Допускается многопроходная (многоваликовая) сварка заполняющих и облицовочного
слоев сварного шва, при этом рекомендуемое значение ширины прохода (валика) -
от 9,0 до 12,0 мм.
10.8.1.22. При
сборке и сварке соединений труб, переходных колец с ЗРА следует предпринять
меры по защите внутренней поверхности ЗРА от попадания грязи, брызг
расплавленного металла, окалины, шлака и др. При наличии в паспорте ЗРА
требований по максимальной температуре нагрева корпуса ЗРА в рабочей зоне
следует предпринять дополнительные меры по снижению нагрева корпуса ЗРА
(теплоизоляционные материалы, боковые ограничители пламени, принудительное
охлаждение и др.).
10.8.2. Сварка
тройниковых соединений (прямых врезок)
10.8.2.1. Под
термином "тройниковое соединение (прямая врезка)" следует понимать
ответвление от магистрали (основной трубы) газопровода патрубком меньшего
диаметра, конструктивно выполняемое как переходной тройник в базовых
(стационарных) или монтажных (трассовых) условиях.
10.8.2.2.
Конструкции тройниковых сварных соединений (прямых врезок) регламентируются
требованиями проектной документации при условии, что диаметр ответвления не
превышает 0,3 диаметра основной трубы. Если диаметр ответвления превышает 0,3
диаметра основной трубы, следует применять тройники заводского изготовления.
10.8.2.3.
Конструкции тройниковых соединений должны быть без конструктивного непровара
угловых соединений с усиливающей накладкой и без усиливающей накладки.
Изготовление усиливающих накладок, как правило, выполняется заблаговременно в
базовых (стационарных) условиях, при этом накладка должна изготавливаться из
трубы того же класса прочности и той же толщины стенки, что и основная труба.
10.8.2.4.
Тройниковые соединения, изготавливаемые из спокойных или полуспокойных
углеродистых сталей, с толщиной стенки патрубка до 16 мм включ. не подлежат
послесварочной термообработке.
10.8.2.5. При
выполнении тройниковых соединений из углеродистых низколегированных сталей в
монтажных (трассовых) условиях рекомендуется, как правило, применять
конструкции, не требующие послесварочной термообработки. В случае необходимости
проведения термической обработки тройниковых сварных соединений, ее следует
проводить в соответствии с 10.10 и нормативными документами ОАО
"Газпром".
10.8.2.6.
Расположение трубы ответвления (патрубка) на основной трубе должно быть на
расстоянии не ближе 250 мм от заводского шва, отклонение от перпендикулярности
трубы ответвления (патрубка) к основной трубе должна быть не более 1,0°,
смещение осей трубы ответвления (патрубка) и основной трубы должно быть не
более 5,0 мм.
10.8.2.7. Для
обеспечения параметров сборки (перпендикулярности, соосности) ответвления
(патрубка) с основной трубой следует применять специальные инструменты и
оснастку (уровень, отвес, угольник, теодолит и др.).
10.8.2.8. Вырезку
отверстия в основной трубе следует выполнять механизированной газовой или
механической резкой, с последующей зачисткой резаных торцов отверстия
шлифмашинкой с абразивным инструментом и дисковыми проволочными щетками.
10.8.2.9.
Геометрические параметры разделки кромок торцов трубы ответвления и усиливающих
накладок должны соответствовать требованиям рисунка 10.25.
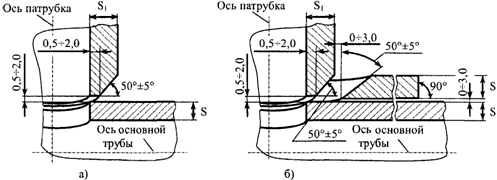
а) сборка
тройникового соединения без усиливающей накладки;
б) сборка
тройникового соединения с усиливающей накладкой;
S - толщина стенки
основной трубы и усиливающей накладки;
- толщина стенки трубы ответвления (патрубка)
Рисунок 10.25.
Геометрические параметры сборки
тройниковых сварных
соединений
10.8.2.10. До
начала сварки (в т.ч. прихваток) следует произвести предварительный подогрев
свариваемых кромок патрубка и вырезанного отверстия основной трубы до
температуры, регламентированной требованиями 10.3.6, и контролироваться
контактными приборами на расстоянии от 10 до 15 мм от свариваемых кромок.
10.8.2.11. Ручная
дуговая сварка тройниковых сварных соединений должна выполняться электродами с
основным видом покрытия в соответствии с требованиями 10.4.1. Назначение
сварочных материалов следует производить исходя из класса прочности металла
основной трубы по таблице Д.4 (Приложение Д). Режимы ручной дуговой сварки
должны соответствовать требованиям таблицы 10.6.
10.8.2.12.
Сварка должна быть многопроходной, количество слоев должно соответствовать
требованиям таблицы 10.8. Допускается выполнять многоваликовую сварку
заполняющих и облицовочного слоев шва.
10.8.2.13. Сварку
каждого валика шва необходимо выполнять участками. Количество участков должно
быть не менее 2-х для патрубков
менее 100, не менее 4-х - для патрубков
от 100 до 150, не менее 6-ти - для патрубков
более 150. Каждый последующий участок должен
быть диаметрально противоположен предыдущему участку. Направление сварки
каждого последующего участка должно совпадать с направлением сварки предыдущего
участка при вертикальной врезке либо должно быть противоположным направлению
сварки предыдущего участка при горизонтальной врезке. Во всех случаях сварка
должна выполняться на подъем.
10.8.2.14.
"Замки" смежных слоев должны быть смещены друг от друга на расстояние
от 25 до 30 мм.
10.8.2.15.
Параметры угловых швов тройниковых сварных соединений приведены на рисунке
10.26.
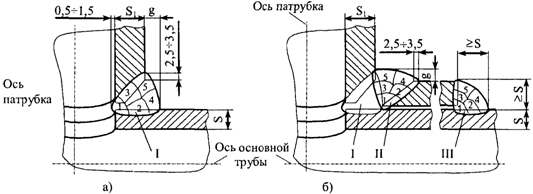
а) сварка трубы
ответвления (патрубка) с основной трубой;
б) сварка
усиливающей накладки с патрубком и основной
трубой; I - угловой
шов "патрубок - основная труба";
II - угловой шов
(внутренний) "усиливающая накладка -
патрубок"; III
- угловой шов (наружный) "усиливающая
накладка - основная
труба"; g - усиление угловых швов;
величина g должна
составлять:
-
для толщин стенки патрубка до 10,0 мм включ.;
-
"
более 10,0 мм.
Рисунок
10.26. Параметры угловых швов тройниковых
сварных соединений
10.8.2.16. Угловые
швы "патрубок - основная труба" (шов I на рисунке 10.26, б)
тройниковых сварных соединений, выполняемых с усиливающими накладками, должны
контролироваться неразрушающими физическими методами до выполнения сборки и
сварки усиливающих накладок.
10.8.2.17. Допускается
изготавливать усиливающие накладки для основной трубы из двух частей, при этом
сварка стыковых швов усиливающих накладок должна выполняться до начала сварки
угловых швов усиливающей накладки с патрубком и основной трубой.
10.8.2.18.
Параметры разделки кромок, сборки и сварки стыковых швов полуворотников должны
соответствовать требованиям, предъявляемым к ручной дуговой сварке стыковых
соединений труб, приведенным в 10.4.1.
10.8.2.19. Угловые
швы усиливающей накладки с основной трубой (шов III на рисунке 10.26, б) могут
выполняться одновременно или последовательно со сваркой угловых швов
усиливающей накладки с патрубком (шов II на рисунке 10.26, б), при этом должны
соблюдаться требования 10.8.2.12.
10.8.2.20.
Тройниковые соединения с диаметром трубы ответвления св. 325 до 426 мм должны
быть выполнены с подваркой изнутри корневого слоя шва. Подварка должна
выполняться в соответствии с требованиями 10.2.42.
10.8.2.21. Сварка
тройниковых соединений в монтажных (трассовых) условиях должна выполняться за
один цикл без перерывов. Тройниковые сварные соединения с диаметром трубы
ответвления до 325 мм включ. выполняются одним сварщиком, с диаметром трубы
ответвления св. 325 до 426 мм - двумя сварщиками. В случае вынужденных
перерывов в работе необходимо выполнить сопутствующий подогрев до температуры
не ниже температуры предварительного подогрева.
10.8.2.22. В
процессе сварки должен осуществляться приемочный пооперационный визуальный
контроль каждого слоя шва. Видимые дефекты швов должны своевременно
устраняться.
10.8.2.23. В
процессе сварки каждый слой шва должен быть зачищен механическим способом.
После завершения сварки облицовочный слой шва должен быть зачищен от шлака и
брызг наплавленного металла механическим способом шлифмашинками.
10.8.2.24. По
окончании сварки тройниковые сварные соединения должны быть накрыты
влагонепроницаемым теплоизолирующим поясом до полного остывания. В
непосредственной близости от тройникового сварного соединения несмываемой
краской должны быть нанесены клейма сварщиков.
10.8.3. Сварка
технологических трубопроводов
10.8.3.1.
Технологические газопроводы уплотнительного, пускового и топливного газа могут
изготавливаться из высоколегированных сталей аустенитного класса (далее -
высоколегированные стали) или низколегированных теплоустойчивых
хромомолибденовых и хромомолибденованадиевых сталей (далее - теплоустойчивые
стали), технологические маслопроводы и воздуховоды - из теплоустойчивых сталей.
10.8.3.2.
Подготовка, сборка, сварка труб, СДТ, ЗРА технологических трубопроводов,
обвязки оборудования промысловых и магистральных газопроводов (газопроводы
топливного, уплотнительного газа, маслопроводы системы смазки, воздуховоды
горячего тракта турбин и др.) должны выполняться по операционно-технологическим
картам сборки и сварки с учетом требований СНиП 3.05.05-84 [10], ПБ 03-585-03
[11], РД 51-31323949-38-98 [12], нормативных документов ОАО
"Газпром", регламентирующих подготовку, сборку и сварку труб, СДТ,
ЗРА технологических трубопроводов и оборудования.
10.8.3.3.
Производственная аттестация технологий сварки технологических трубопроводов
должна выполняться согласно требованиям раздела 4 настоящего стандарта путем
сварки КСС, однотипность которых должна определяться согласно требованиям
нормативных документов, указанных в 10.8.3.2.
10.9.
Сварка выводов электрохимической защиты
10.9.1. Общие
требования
10.9.1.1. Сварку
(далее - приварка) выводов ЭХЗ к газопроводам следует выполнять:
- ручной дуговой
сваркой покрытыми электродами;
- термитной
сваркой;
- конденсаторной
сваркой <*>.
--------------------------------
<*>
Конденсаторная приварка выводов ЭХЗ может применяться по отдельным
технологическим инструкциям, согласованным с ОАО "Газпром" и
разработчиком настоящего стандарта.
10.9.1.2.
Требования к выводам ЭХЗ (материал изготовления - медные, латунные, стальные;
электросопротивление материала, сечение, длина и др.) регламентируются
нормативными документами ЭХЗ.
10.9.1.3. Материалы
(сварочные электроды, термитные смеси либо паяльно-сварочные стержни и
термокарандаши из термитных смесей), предназначенные для приварки выводов ЭХЗ,
должны соответствовать требованиям раздела 7.
10.9.1.4.
Производственная аттестация технологий приварки выводов ЭХЗ, допускные
испытания сварщиков должны проводиться с учетом требований разделов 4, 5.
10.9.1.5. КСС,
выполненные при производственной аттестации технологий и допускных испытаниях
сварщиков, должны оцениваться визуальным, измерительным методами контроля и
пройти механические испытания с целью проверки соответствия их механических
свойств требованиям настоящего стандарта. Методика механических испытаний
приведена в Приложении Б.
10.9.1.6.
КСС признаются прошедшими испытания:
- если по
результатам визуального и измерительного контроля в сварных швах переходной
пластины и вывода ЭХЗ, выполненных ручной дуговой сваркой, наплавке,
выполненной термитной сваркой, отсутствуют недопустимые поверхностные дефекты и
размеры сварных швов и наплавок соответствуют требованиям настоящего раздела;
- если по
результатам механических испытаний значение прочности при сдвиге наплавки,
выполненной термитной сваркой, составляет не менее 50 МПа, при этом отношение
площади сплавления к площади наплавки должно быть не менее 50%.
10.9.1.7.
Подготовка газопровода к приварке, приварка выводов ЭХЗ должны выполняться в
соответствии с требованиями операционных технологических карт сборки, ручной
дуговой сварки, термитной сварки выводов ЭХЗ, разработанных по аттестованным
технологиям сварки и утвержденных организацией, выполняющей приварку выводов
ЭХЗ.
10.9.1.8. Место приварки
выводов ЭХЗ следует располагать в верхней четверти периметра газопровода с
максимальным отклонением от зенита +/- 10°, при этом при ручной дуговой сварке
- на кольцевом сварном шве на расстоянии не менее 100 мм от пересечения
продольного и кольцевого швов, при термитной сварке - на поверхности
газопровода на расстоянии не менее 100 мм от продольного, кольцевого сварных
швов и их пересечения.
10.9.1.9.
Поверхность газопровода в месте приварки выводов ЭХЗ и на расстоянии не менее
50 мм в каждую сторону должна быть очищена механическим способом до
металлического блеска. Допускается очистка поверхности шлифмашинкой с
применением дисковых проволочных щеток, ручной проволочной щеткой, напильником,
наждачной бумагой.
10.9.1.10. Вывод
ЭХЗ должен быть зачищен механическим способом до металлического блеска на длину
не менее 50 мм.
10.9.1.11. На
поверхности газопровода в месте приварки выводов ЭХЗ не допускается наличие
следов влаги или конденсата.
10.9.2. Ручная
дуговая сварка выводов ЭХЗ
10.9.2.1. Для
ручной дуговой приварки выводов ЭХЗ следует применять сварочные электроды с
основным видом покрытия, приведенные в таблице Д.4 (Приложение Д),
рекомендованные для сварки заполняющих и облицовочных слоев сварных швов
газопроводов.
10.9.2.2. Ручная
дуговая приварка выводов ЭХЗ выполняется в следующей последовательности,
приведенной на рисунке 10.27:
- подготовить до
начала производства работ переходную пластину из малоуглеродистой стали (марок
ВСт. 3сп, 10, 20) с толщиной стенки от 2,0 до 3,0 мм в поперечном сечении по
форме усиления кольцевого сварного шва, в продольном - по диаметру газопровода,
с параметрами, приведенными на рисунке 10.28;
- произвести
очистку внутренней и наружной поверхности пластины механическим способом до
металлического блеска;
- снять усиление
сварного шва механическим способом шлифмашинкой, напильником до образования на
облицовочном шве ровной поверхности шириной не менее ширины пазов пластины и
длиной, равной длине пластины;
- установить
пластину на подготовленную поверхность по оси кольцевого сварного шва;
- выполнить в
центре пазов пластины прихватки к кольцевому сварному шву по одной с каждой
стороны;
- выполнить сварку
пластины с кольцевым сварным швом наплавочными швами электродами с основным
видом покрытия диаметром от 2,5 до 3,25 мм с полным заполнением пазов и
перекрытием металла пластины не менее 1,0 мм в каждую сторону;
- установить вывод
ЭХЗ по оси центральной части пластины;
- выполнить сварку
вывода ЭХЗ к центральной части пластины угловыми швами электродами с основным
видом покрытия диаметром от 2,5 до 3,25 мм с образованием катета не менее
диаметра вывода ЭХЗ;
- зачистить
металлической щеткой наплавочные швы пластины и угловые сварные швы приварки
вывода ЭХЗ от шлака;
- провести
визуальный и измерительный контроль сварных швов по внешнему виду. Внешний вид
сварных швов приварки пластины и вывода ЭХЗ должен соответствовать требованиям,
предъявляемым к сварным швам газопроводов;
- проверить
прочность наплавки многократным изгибом приваренного вывода ЭХЗ.
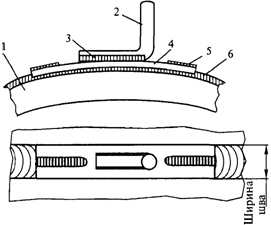
1 - стенка
газопровода; 2 - стальной вывод ЭХЗ;
3 - угловые швы; 4
- переходная пластина; 5 - наплавочные
швы; 6 -
облицовочный слой кольцевого сварного шва
Рисунок
10.27. Схема приварки вывода ЭХЗ
к кольцевому шву газопровода
через переходную пластину
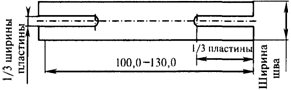
Рисунок
10.28. Размеры переходной пластины
для приварки
выводов ЭХЗ к кольцевым швам газопроводов
10.9.3. Термитная
сварка выводов ЭХЗ
10.9.3.1. Для
термитной приварки выводов ЭХЗ следует применять:
а) медные термитные
смеси, герметично упакованные в разовые тигель-формы (рисунок 10.29);
б) медные термитные
смеси (порошок) с многоразовыми графитовыми тигель-формами из двух полутиглей
(рисунок 10.30);
в) медные термитные
смеси, спрессованные на клеевой основе в карандаши (термокарандаши) с
многоразовыми графитовыми тигель-формами;
г) медные термитные
смеси, герметично упакованные в бумажную цилиндрическую оболочку
(паяльно-сварочные стержни), с многоразовыми графитовыми оправками <*>
(рисунок 10.31).
--------------------------------
<*> В тексте
документа, за исключением особых случаев, вместо приведенных наименований
термитных смесей употребляются термины "термитные сварочные
материалы".
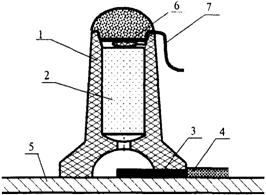
1 - разовая
тигель-форма; 2 - термитная смесь;
3 - вывод ЭХЗ; 4 -
провод вывода ЭХЗ; 5 - стенка
газопровода; 6 -
термоподжиг; 7 - огнепроводный шнур
Рисунок
10.29. Схема установки РТФ

1 - многоразовая
тигель-форма; 2 - термитная смесь;
3 - вывод ЭХЗ; 4 -
провод вывода ЭХЗ; 5 - стенка
газопровода; 6 -
термоподжиг; 7 - огнепроводный шнур;
8 - магнитные
башмаки
Рисунок
10.30. Схема установки многоразовой тигель-формы
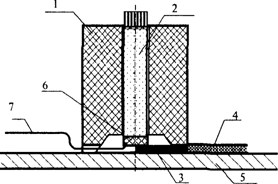
1 - многоразовая
графитовая оправка; 2 - паяльно-сварочный
стержень; 3 -
теплоотводящая трубка с выводом ЭХЗ;
4 - провод вывода
ЭХЗ; 5 - стенка газопровода;
6 - зажигательная
головка стержня ЭХЗ;
7 - огнепроводный
шнур
Рисунок
10.31. Схема установки графитовой оправки
и
паяльно-сварочного стержня
10.9.3.2. Медные
термитные смеси (порошки), термокарандаши, паяльно-сварочные стержни с
дополнительной оснасткой, рекомендуемые к применению для приварки выводов ЭХЗ,
приведены в таблице Д.19 (Приложение Д).
10.9.3.3. Перед
проведением работ по приварке выводов ЭХЗ необходимо провести осмотр
многоразовых, разовых тигель-форм или оправок. Не допускается применять
тигель-формы и оправки с недопустимыми трещинами, сколами опорного торца,
неплотностями поверхностей замыкания полутиглей многоразовых тигель-форм.
10.9.3.4.
Подготовка опорного торца тигель-формы или оправки для плотного прилегания
рабочей поверхности к трубе должна производиться заблаговременно притиранием на
наждачной бумаге, уложенной на трубу (элемент трубы) того же диаметра.
10.9.3.5. Установка
тигель-формы или оправки на место приварки выводов ЭХЗ должна производиться на
предварительно зачищенную механическим способом и обезжиренную спиртом или
ацетоном поверхность газопровода. Канал для установки вывода ЭХЗ должен
располагаться по оси газопровода.
10.9.3.6. Конец
провода вывода ЭХЗ или теплоотводящая металлическая трубка, надетая на конец
провода вывода ЭХЗ, должны быть введены в литниковую камеру тигель-формы или
графитовой оправки.
10.9.3.7. Вскрытие
индивидуальной упаковки и контроль внешнего вида сварочных материалов для
приварки выводов ЭХЗ должны производиться непосредственно перед установкой и
применением.
10.9.3.8. При
применении для приварки выводов ЭХЗ медной термитной смеси с многоразовой
графитовой тигель-формой из двух полутиглей предварительно на дно камеры
сгорания устанавливается стальная или медная мембрана толщиной 0,3 +/- 0,02 мм.
С целью исключения попадания термосмеси в полость тигель-формы мембрана должна
устанавливаться ровно, без перекосов.
10.9.3.9. До
вскрытия герметичной упаковки термитной смеси массой 1 кг (20 порций)
необходимо произвести перемешивание упаковки путем встряхивания. После вскрытия
упаковки термитная смесь высыпается в центральный канал многоразовой
тигель-формы мерной емкостью (стаканом), входящей в комплект, соответствующей
одной весовой порции (от 54 до 56 г), в два этапа с послойным уплотнением.
10.9.3.10.
Паяльно-сварочные стержни или термокарандаши устанавливаются в центральный
канал графитовой оправки или тигель-формы.
10.9.3.11.
Огнепроводный шнур для поджига термосмеси выводится наружу через запальное
отверстие крышки тигель-формы или через шлакоотводящий канал графитовой
оправки.
10.9.3.12. Поджиг
огнепроводного шнура замедленного горения производится источником открытого
огня (спичкой, термоспичкой и др.) либо посредством передатчика и приемника
устройства дистанционного поджига.
10.9.3.13. С целью
исключения попадания брызг расплавленной меди рекомендуется защищать
поверхность газопровода инвентарными защитными экранами из несгораемого
материала (металлические кольца, полукольца) или уложенным влажным песком в
радиусе от 20 до 30 см от места приварки.
10.9.3.14. По
окончании приварки выводов ЭХЗ необходимо:
- дать остыть месту
приварки, снять тигель-форму или оправку легким пошатыванием;
- зачистить
наплавку и место приварки вывода ЭХЗ от шлака металлической щеткой, наждачной
бумагой до металлического блеска;
- провести
визуальный и измерительный контроль размеров наплавки: высота наплавки должна
быть 5,0 +/- 2,0 мм, диаметр - 30 +/- 5,0 мм, допускаются отдельные поры на
поверхности наплавки диаметром до 1,0 мм;
- проверить
прочность наплавки многократным изгибом приваренного вывода ЭХЗ;
- очистить от шлака
и брызг расплавленной меди многоразовую тигель-форму, графитовую оправку, не
повреждая поверхностей, зачистить шлифшкуркой ("нулевкой") на
тканевой основе литниковую камеру для последующего применения, шлако- и
газоотводящие каналы графитовой оправки зачищаются разверткой или сварочным
электродом диаметром от 4,0 до 5,0 мм.
10.10. Термическая обработка сварных соединений
10.10.1. Порядок
проведения работ, выбор оборудования и режимов термообработки, требования к
персоналу определяются нормативными документами ОАО "Газпром" по
термической обработке (далее - термообработка) и настоящим разделом.
10.10.2. Не
требуется термическая обработка кольцевых стыковых сварных соединений
газопроводов из трубных сталей с нормативным значением временного сопротивления
на разрыв до 590 МПа (60 кгс/мм2) включ., с разнородностью по классу прочности
до 8,0 кгс/мм2 (80 МПа) включ., условным
диаметром
до 1400 включ. с толщиной стенки до 32,0 мм
включ.
10.10.3.
Послесварочной термообработке подлежат сварные соединения газопроводов:
а) разнородные
сварные соединения с разнородностью по классу прочности
более 8,0 кгс/мм2 (80 МПа);
б) тройниковые
сварные соединения прямых врезок с толщиной стенки ответвления св. 16,0 мм;
в) сварные
соединения приварки ложементов надземных газопроводов в местах установки
"мертвых" опор.
10.10.4. Вид
термообработки, номенклатура сварных соединений газопроводов, подлежащих
послесварочной термообработке, уточняются при проектировании и разработке
проекта производства работ.
10.10.5.
Оборудование для термообработки, рекомендованное к применению, приведено в
таблицах Е.16 - Е.18 (Приложение Е).
10.10.6. Описание
технологического процесса послесварочной термообработки сварных соединений по
всем операциям с указанием технологических режимов и средств оснащения должно
быть изложено в операционно-технологической карте термообработки или в
операционно-технологических картах сборки, сварки и термообработки сварных
соединений при строительстве газопроводов.
10.10.7.
Операционные технологические карты должны содержать:
- характеристики
основного металла трубы (класс прочности, диаметр, толщина стенки);
- описание
технологии сварки с указанием сварочных материалов и оборудования, режимов
сварки, параметров предварительного и сопутствующего подогрева, параметров
сварных швов и др.;
- описание вида
послесварочной термообработки с указанием оборудования нагрева, режима
термообработки, контроля параметров нагрева.
10.10.8. Местная
термообработка кольцевых стыковых сварных соединений газопроводов проводится
путем нагрева всего периметра сварного соединения, при этом ширина зоны полного
нагрева должна быть не менее
, где
D и S - соответственно наружный диаметр и толщина стенки трубы газопровода, для
случаев разнотолщинных сварных соединений принимается большее значение толщины
стенки.
10.10.9. Местная
термообработка тройниковых соединений газопроводов (прямых врезок) проводится
путем нагрева полного периметра тройникового сварного соединения по основной
трубе и по трубе-ответвлению, включая сварные швы и зоны шириной не менее
в каждую сторону от сварных швов, где D и S -
соответственно наружный диаметр и толщина стенки трубы газопровода.
10.10.10. Зона
теплоизоляции при термообработке сварных соединений должна быть не менее
, где
D и S - соответственно наружный диаметр и толщина стенки трубы газопровода.
10.10.11. Вид
термообработки сварных соединений, выполненных дуговыми способами сварки при
строительстве газопроводов из низкоуглеродистых, низколегированных сталей
перлитного класса - высокий отпуск. Режимы термообработки приведены в таблице
10.34.
Таблица 10.34
Режимы
термообработки сварных соединений газопроводов
┌──────────────────┬─────────┬───────────────────────────────┬────────────┐
│ Стали │
Класс │ Режимы термообработки │
Условия │
│
│прочности├───────────┬─────────┬─────────┤
охлаждения │
│ │ │температура│скорость
│выдержка │
│
│ │ │ нагрева, │ нагрева │ t , мин │ │
│ │ │ T , °C
│V , °C/ч │ в │ │
│ │ │ н
│ н │ │ │
├──────────────────┼─────────┼───────────┼─────────┼─────────┼────────────┤
│Низкоуглеродистые,│
До К54 │ 580 - 600 │Не более
│1,5 мин │Под слоем │
│низколегированные,│
включ. │ │ 400
│на 1,0 мм│тепло-
│
│перлитного
класса
├─────────┼───────────┤ │толщины │изоляции до │
│ │ Св. К54 │ 600 -
620 │ │стенки │температуры │
│ │ до К60 │ │ │трубы, но│окружающего
│
│ │ включ. │ │ │не менее │воздуха │
│ │ │ │ │60 мин │ │
└──────────────────┴─────────┴───────────┴─────────┴─────────┴────────────┘
10.10.12.
Термообработка проводится после получения положительных результатов контроля
качества сварного соединения.
10.10.13. После
термообработки сварного соединения должен быть выполнен контроль твердости
металла шва и ЗТВ, при этом твердость металла шва и ЗТВ должны отвечать
требованиям перечисления г) п. 9.6.
10.10.14. При
проведении термической обработки необходимо руководствоваться инструкциями по
эксплуатации оборудования для термической обработки и нормативными документами
ОАО "Газпром".
11.
Требования к контролю качества сварных соединений
11.1. Контроль
качества сварных соединений газопроводов должен производиться лабораториями
неразрушающего контроля, аттестованными в соответствии с ПБ 03-372-00 [7],
специалистами неразрушающего контроля, аттестованными в соответствии с ПБ
03-440-02 [8].
11.2. Контроль качества
сварных соединений газопроводов должен осуществляться визуальным, измерительным
и физическими методами контроля (основным, дублирующим, дополнительным).
Методы, объемы неразрушающего контроля и нормы оценки качества сварных
соединений газопроводов должны соответствовать требованиям раздела 6 СТО
Газпром 2-2.4-083.
11.3. Формы
исполнительной документации на выполненные сварные соединения - Журнал сварки
сварных соединений - и проконтролированные сварные соединения - Журнал контроля
сварных соединений неразрушающими методами приведены в Приложении Г.
12. Техника
безопасности и охрана труда
При проведении
сварочных работ при строительстве газопроводов необходимо соблюдать требования
безопасности и охраны труда в соответствии с нормативной документацией:
- Единая система
управления охраной труда и промышленной безопасностью в Открытом Акционерном
обществе "Газпром" ВРД 39-1.14-021-2001 [13];
- Правила
технической эксплуатации магистральных газопроводов ВРД 39-1.10-006-2000* [14];
- Типовая
инструкция по проведению огневых работ на газовых объектах ОАО
"Газпром" СТО Газпром 14-2005;
- Инструкция по
производству строительных работ в охранных зонах магистральных трубопроводов
Министерства газовой промышленности ВСН 51-1-80 [15];
- Безопасность
труда в строительстве СНиП 12-03-2001, ч. 1 [16];
- Правила
безопасности в нефтяной и газовой промышленности ПБ 08-624-03 [17];
- Межотраслевые
правила по охране труда при электро- и газосварочных работах ПОТ РМ 020-2001
[18];
- Правила
устройства электроустановок ПУЭ [19];
- Система
стандартов безопасности труда. Электробезопасность. Общие требования и
номенклатура видов защиты ГОСТ 12.1.019-79;
- Система
стандартов безопасности труда. Оборудование производственное. Общие требования
безопасности ГОСТ 12.2.003-91;
- ССБТ. Организация
обучения безопасности труда. Общие положения ГОСТ 12.0.004-90.
Приложение
А
(обязательное)
ГРУППЫ
ОДНОТИПНОСТИ СВАРНЫХ СОЕДИНЕНИЙ ТРУБОПРОВОДОВ
А.1. Определение
групп однотипности сварных соединений газопроводов
А.1.1. Однотипными
сварными соединениями следует считать группы сварных соединений, имеющие
основные параметры однотипности, установленные в настоящем разделе.
Однотипность производственных сварных соединений - это характеристика схожести
условий выполнения сварных соединений, определяющаяся набором признаков
однотипности и диапазоном значений этих признаков.
А.1.2. В состав
основных параметров, определяющих однотипность производственных сварных
соединений газопроводов, входят:
- способ(ы) сварки;
- конструктивный
элемент (соединение) газопровода;
- класс прочности
материалов свариваемых элементов;
- диаметр
свариваемых элементов;
- толщина
свариваемых элементов;
- сварочные
материалы (вид покрытия электродов, вид сварочных проволок, классификация
сварочного флюса по способу изготовления, состав защитного газа);
- сварочное
оборудование (тип - для РД, марка - для МП, МПС, ААДП, АПГ, АПИ, АФ; число и
вид плавящихся электродов - для АФ, ААДП, АПГ; импульсно-дуговой процесс - для
МП, ААДП);
- тип соединения,
тип шва, вид соединения;
- геометрические
параметры разделки кромок свариваемых элементов;
- положение при
сварке;
- предварительный и
сопутствующий подогрев;
- тип центрирующего
приспособления (центратора).
- термообработка.
При изменении
основных параметров за пределы установленной области распространения,
приведенной в Приложении В, требуется проведение производственной аттестации
технологии сварки.
А.1.3. В одну
группу однотипных сварных соединений объединяются сварные соединения,
выполняемые одним из способов сварки, приведенных в таблице А.1. Сварные
соединения, выполняемые по комбинированным технологиям, т.е. с последовательным
применением двух или нескольких способов сварки, выделяются в отдельную группу
однотипных сварных соединений.
Таблица А.1
Группы
однотипных сварных соединений газопроводов
по способам сварки
┌────────────────────────────────────────────────────┬────────────────────┐
│ Наименование способа сварки │Условное обозначение│
├────────────────────────────────────────────────────┼────────────────────┤
│Ручная
дуговая сварка покрытыми электродами
│ РД │
├────────────────────────────────────────────────────┼────────────────────┤
│Ручная
аргонодуговая сварка неплавящимся электродом │ РАД │
├────────────────────────────────────────────────────┼────────────────────┤
│Механизированная
сварка плавящимся электродом в
│ МП │
│среде
активных газов и смесях │ │
├────────────────────────────────────────────────────┼────────────────────┤
│Механизированная
сварка самозащитной порошковой
│ МПС │
│проволокой
│ │
├────────────────────────────────────────────────────┼────────────────────┤
│Автоматическая
сварка плавящимся электродом в среде │ ААДП │
│инертных
газов и смесях
│ │
├────────────────────────────────────────────────────┼────────────────────┤
│Автоматическая
сварка плавящимся электродом в среде │ АПГ │
│активных
газов и смесях
│ │
├────────────────────────────────────────────────────┼────────────────────┤
│Автоматическая
сварка порошковой проволокой в среде │ АПИ │
│инертных
газов и смесях
│ │
├────────────────────────────────────────────────────┼────────────────────┤
│Автоматическая
сварка под флюсом
│ АФ │
├────────────────────────────────────────────────────┴────────────────────┤
│ Примечания. 1. Для технологий сварки,
регламентированных
настоящим│
│стандартом,
приняты следующие условные обозначения: │
│ - РД - технология ручной дуговой сварки
покрытыми электродами; │
│ - РАД
- технология ручной
аргонодуговой сварки неплавящимся│
│электродом;
│
│ - ААДП
+ АПГ -
технология автоматической двухсторонней сварки│
│проволокой
сплошного сечения в защитных газах
комплексом оборудования│
│фирм
CRC-Evans AW, Autoweld Systems; │
│ - МП - технология механизированной
сварки в
среде углекислого газа│
│проволокой
сплошного сечения;
│
│ - МПС - технология механизированной сварки самозащитной порошковой│
│проволокой; │
│ - АПГ - технология автоматической сварки
проволокой сплошного сечения│
│в
защитных газах комплексом оборудования CWS.02 фирмы PWT; │
│ - АПГ - технология автоматической сварки
проволокой сплошного сечения│
│в
защитных газах комплексом оборудования Saturnax фирмы Serimax; │
│ - АПИ -
технология автоматической сварки порошковой проволокой
в│
│защитных
газах специализированными
сварочными головками М300-С
(М300)│
│фирмы
CRC-Evans AW; │
│ - АФ - технологии односторонней и
двухсторонней автоматической сварки│
│под
флюсом.
│
│ 2. Для обозначения комбинированных технологий
сварки используются│
│комбинации условных
обозначений способов сварки: РД + МПС, РД + АПИ,│
│РД
+ АФ, МП + РД, МП + МПС, МП + МПС + АФ, РАД + РД и др. │
└─────────────────────────────────────────────────────────────────────────┘
А.1.4. В одну
группу однотипных сварных соединений объединяются сварные соединения по
конструктивным элементам газопровода отнесенные к одной из приведенных в
таблице А.2 групп сварных соединений газопроводов. Однотипные сварные
соединения газопровода по конструктивным элементам - это типовые сварные
соединения одной конструкции, характеризующиеся типовыми операциями сборки и
сварки в определенной последовательности.
Таблица А.2
Группы
сварных соединений газопроводов
по конструктивным
элементам газопровода
N
группы
|
Сварные соединения газопровода по
конструктивным
элементам при односторонней и
двухсторонней сварке
|
Условное
обозначение
|
1
|
Одностороннее
сварное соединение труб одной толщины
стенки без подварки изнутри ("труба + труба") <1>
|
ТТ-БП
|
2
|
Одностороннее
сварное соединение труб одной толщины
стенки с подваркой изнутри или двухстороннее сварное
соединение труб одной толщины стенки
("труба + труба")
|
ТТ-П, ТТ-ДС
|
3
|
Одностороннее
сварное соединение труб разной толщины
стенки с подваркой изнутри или двухстороннее сварное
соединение труб разной толщины стенки
("труба + труба")
|
РТ-П, РТ-ДС
|
4
|
Одностороннее
сварное соединение труб разной толщины
стенки без подварки изнутри ("труба + труба")
|
РТ-БП
|
5
|
Одностороннее
сварное соединение "труба + СДТ (ЗРА)"
|
ТД, ТА-БП
|
6
|
Одностороннее
сварное соединение труб одной толщины
стенки без подварки изнутри (захлест, прямая вставка
(катушка))
|
ЗС,
ЗК
|
7
|
Одностороннее
тройниковое сварное соединение (прямая
врезка) с усиливающей накладкой (воротником)
|
ТС-Н
|
8
|
Одностороннее
тройниковое сварное соединение (прямая
врезка) без усиливающей накладки (воротника)
|
ТС-БН
|
<1> В
операционно-технологической
карте сборки и
сварки данного
соединения может регламентироваться подварка
изнутри на отдельных
участках периметра сварного
шва со смещениями
кромок, непроварами,
несплавлениями.
|
Группы однотипных
сварных соединений по классам прочности материалов труб, соединительных деталей
трубопроводов, запорной и регулирующей арматуры приведены в таблице А.3.
Таблица А.3
Группы
однотипных сварных соединений
по классам
прочности материалов свариваемых элементов
Номер группы
(индекс
однотипности) по
классу прочности
материалов
|
Характеристики групп
материалов
|
Диапазон классов
прочности
|
Нормативное значение
временного сопротивления
разрыву, МПа (кгс/мм2)
|
1
|
М01
|
До К54 включ.
|
До 530 (54) включ.
|
2
|
М03
|
Св. К54 до К60 включ.
|
Св. 530 (54)
до 590 (60) включ.
|
3
|
М03
|
Св. К60
|
Св. 590 (60)
|
1(М01) + 2(М03)
|
Сочетание
сталей группы 2
со сталями группы 1
|
-
|
1(М01) + 3(М03)
|
Сочетание
сталей группы 3
со сталями группы 1
|
-
|
2(М03) + 3(М03)
|
Сочетание
сталей группы 3
со сталями группы 2
|
-
|
В одну группу
однотипных сварных соединений объединяются сварные соединения из сталей одной
группы или одного сочетания групп по классам прочности материалов свариваемых
элементов.
А.1.5. Группы
однотипных сварных соединений по номинальным диаметрам свариваемых элементов
приведены в таблице А.4.
Таблица А.4
Группы
однотипных сварных соединений
по номинальным
диаметрам свариваемых элементов
Номер группы (индекс однотипности)
по наружному диаметру
|
Диапазон номинальных диаметров, мм
|
1
|
До 25 включ.
|
2
|
Св. 25 до 159 включ.
|
3
|
Св. 159 до 530 включ.
|
4
|
Св. 530
|
При отнесении
сварных соединений к диапазонам, указанным в таблице А.4, номинальный диаметр
свариваемых элементов измеряется для стыковых сварных соединений одной толщины
стенки - по наружной поверхности свариваемых элементов; для сварных соединений
разной толщины стенки - по наружной поверхности элемента меньшей толщины
стенки; для угловых тройниковых соединений (прямых врезок) - по наружной
поверхности привариваемой трубы-ответвления (патрубка).
Для нахлесточных
тройниковых соединений (прямых врезок) с усиливающей накладкой не является
параметром однотипности наружный диаметр накладки в зоне расположения шва.
А.1.6. Группы
однотипных сварных соединений по номинальным толщинам стенки труб стыковых
соединений для элементов одной толщины стенки приведены в таблице А.5. В одну
группу однотипных сварных соединений объединяются сварные соединения одной
группы по номинальной толщине стенки свариваемых элементов.
Таблица А.5
Группы
однотипных сварных соединений
по номинальным
толщинам труб стыковых соединений
для элементов одной
толщины стенки
┌───────────────────────────────────┬─────────────────────────────────────┐
│Номер
группы (индекс однотипности) │ Диапазон номинальных толщин стенки │
│ по толщине │ │
├───────────────────────────────────┼─────────────────────────────────────┤
│ 1 │ До 5,0 мм включ. │
├───────────────────────────────────┼─────────────────────────────────────┤
│ 2 │ Св. 5,0 до 12,0 мм включ. │
├───────────────────────────────────┼─────────────────────────────────────┤
│ 3 │ " 12,0 " 19,0
" " │
├───────────────────────────────────┼─────────────────────────────────────┤
│ 4 │ " 19,0 " 32,0
" " │
├───────────────────────────────────┼─────────────────────────────────────┤
│ 5 │ " 32,0 " 50,0
" " │
└───────────────────────────────────┴─────────────────────────────────────┘
А.1.7. Группы
однотипных сварных соединений по номинальным толщинам стенки труб стыковых
соединений для элементов разной толщины стенки приведены в таблице А.6.
Таблица А.6
Группы однотипных
сварных соединений
по номинальным
толщинам труб стыковых соединений
для элементов одной
толщины стенки
┌─────────────────┬─────────────────────────────┬─────────────────────────┐
│ Номер группы
│ Диапазон номинальных толщин │ Диапазон номинальных │
│ (индекс
│тонкостенных труб (элементов)│толщин толстостенных
труб│
│ однотипности)
│
│ (элементов) <*> │
│ по толщине
│
│
│
├─────────────────┼─────────────────────────────┼─────────────────────────┤
│ 1
│ До 5,0 мм включ. │ До 7,5 мм включ. <**> │
├─────────────────┼─────────────────────────────┼─────────────────────────┤
│ 2
│ Св. 5,0 до 12,0 мм включ. │Св. 7,5 мм 18,0 мм
включ.│
├─────────────────┼─────────────────────────────┼─────────────────────────┤
│ 3
│ " 12,0
" 19,0 "
" │ " 15,0 " 28,5
" " │
├─────────────────┼─────────────────────────────┼─────────────────────────┤
│ 4
│ " 19,0
" 32,0 "
" │ " 22,0 " 48,0
" " │
├─────────────────┼─────────────────────────────┼─────────────────────────┤
│ 5
│ " 32,0
" 50,0 "
" │ " 35,0 " 75,0
" " │
├─────────────────┴─────────────────────────────┴─────────────────────────┤
│
<*> Разнотолщинные соединения указанных диапазонов толщин
установлены│
│исходя
из разнотолщинности элементов не более 1,5. │
│
<**> Разнотолщинные
соединения указанного диапазона
толщин│
│установлены для
толстостенного элемента без
специальной обработки│
│кромок
- нутрения.
│
└─────────────────────────────────────────────────────────────────────────┘
В одну группу
однотипных сварных соединений объединяются сварные соединения одной группы по
номинальным толщинам стенок для тонкостенных и толстостенных свариваемых труб
(элементов).
А.1.8. Группы
однотипных сварных соединений прямых врезок по классам прочности, номинальным
диаметрам и номинальным толщинам стенки свариваемых элементов приведены в
таблице А.7.
Таблица А.7
Группы
однотипных тройниковых соединений прямых врезок
по классам
прочности, номинальным диаметрам и номинальным
толщинам стенки
свариваемых элементов с учетом параметров
конструктивных
элементов
┌─────────┬───────────────────────────────────────────────┬────────────────────┬────────────────────┬──────────┐
│
Группа │ Группы номинальных диаметров патрубков │ Группы номинальных │ Группы
номинальных │Условное │
│материала│ в сочетании с номинальными диаметрами │
толщин стенок │ толщин стенок │обозна- │
│ <*>
│ основной
трубы │ патрубков │
основной трубы
│чение │
│
├─────────────┬────────────────────────┬────────┼───────────┬────────┼───────────┬────────┤соединения│
│ │ Диапазон
│ Сочетания диаметров │Индекс │ Диапазон, │Индекс │ Диапазон, │Индекс │"отвод- │
│ │ диаметров
│ патрубка и основной │одно- │
мм │одно- │
мм │одно- │труба" │
│ │патрубка, мм │ трубы для
контрольных │типности│ │типности│ │типности│ │
│ │ │ сварных соединений, мм
│ │ │ │ │ │ │
│ │
├────────┬───────────────┤ │ │ │ │ │ │
│ │ │патрубок│основная
труба │ │ │ │ │ │ │
├─────────┼─────────────┼────────┼───────────────┼────────┼───────────┼────────┼───────────┼────────┼──────────┤
│Группа 1 │До 25 включ. │ 25
│ от 114 │
1 │До 5
включ.│ 1 │ От 6,5 до │ 2
│ОТ-1-1.1.2│
│ (М01)
│ │ │до 1420 включ. │ │ │ │12,0 включ.│ │ │
│ │ │ │ │ │ │
├───────────┼────────┼──────────┤
│
│ │ │ │ │ │ │ Св. 12,0 │
3 │ОТ-1-1.1.3│
│
├─────────────┼────────┼───────────────┼────────┼───────────┼────────┼───────────┼────────┼──────────┤
│
│ Св. 25 │
57 │" 219 " 1420
" │ 2 │
" 5 " │ 1
│ От 6,5 до │ 2 │ОТ-1-2.1.2│
│ │до 159 включ.│ │ │ │ │ │12,0 включ.│ │ │
│ │ │ │ │ │ │
├───────────┼────────┼──────────┤
│
│ │ 76
│" 273 " 1420 " │ │ │ │ Св. 12,0 │
3 │ОТ-1-2.1.3│
│ │ │ │ │
├───────────┼────────┼───────────┼────────┼──────────┤
│
│ │ 108
│" 377 " 1420 " │ │Св. 5 до 12│ 2
│ От 6,5 до │ 2 │ОТ-1-2.2.2│
│ │ │ │ │ │
включ. │ │12,0 включ.│ │ │
│ │ │ │ │ │ │
├───────────┼────────┼──────────┤
│
│ │
159 │" 530 "
1420 " │ │ │ │ Св. 12,0 │
3 │ОТ-1-2.2.3│
│
├─────────────┼────────┼───────────────┼────────┼───────────┼────────┼───────────┼────────┼──────────┤
│
│" 159 " 325 "│ 168
│" 630 " 1420 " │ 3
│До 5 включ.│ 1 │ От 6,5 до │ 2
│ОТ-1-3.1.2│
│ │ │ │ │ │ │ │12,0 включ.│ │ │
│ │ │ │ │ │ │
├───────────┼────────┼──────────┤
│
│ │ 219
│" 720 " 1420 " │ │ │ │ Св. 12,0 │
3 │ОТ-1-3.1.3│
│ │ │ │ │
├───────────┼────────┼───────────┼────────┼──────────┤
│
│ │ 245
│" 820 " 1420 " │ │Св. 5 до 12│ 2
│ От 6,5 до │ 2 │ОТ-1-3.2.2│
│ │ │ │ │ │
включ. │ │12,0 включ.│ │ │
│ │ │ │ │ │ │
├───────────┼────────┼──────────┤
│
│ │ 273
│" 920 " 1420 " │ │ │ │ Св. 12,0 │
3 │ОТ-1-3.2.3│
│
│ │ │ │
├───────────┼────────┼───────────┼────────┼──────────┤
│
│ │ 325
│" 1220 " 1420 "│ │" 12 " 16
"│ 3 │ От 6,5 до │ 2
│ОТ-1-3.3.2│
│ │ │ │ │ │ │ │12,0 включ.│ │ │
│ │ │ │ │ │ │
├───────────┼────────┼──────────┤
│
│ │ 426
│ 1420 │ │ │ │ Св. 12,0 │
3 │ОТ-1-3.3.3│
├─────────┼─────────────┼────────┼───────────────┼────────┼───────────┼────────┼───────────┼────────┼──────────┤
│Группа 2 │До 25 включ. │ 25
│" 114 " 1420 " │ 1
│До 5 включ.│ 1 │ От 6,5 до │ 2
│ОТ-2-1.1.2│
│ (М03)
│ │ │ │ │ │ │12,0 включ.│ │ │
│ │ │ │ │ │ │ ├───────────┼────────┼──────────┤
│
│ │ │ │ │ │ │ Св. 12,0 │
3 │ОТ-2-1.1.3│
│
├─────────────┼────────┼───────────────┼────────┼───────────┼────────┼───────────┼────────┼──────────┤
│
│ Св. 25 │
57 │" 219 " 1420
" │ 2 │
" 5 " │ 1
│ От 6,5 до │ 2 │ОТ-2-2.1.2│
│ │до 159 включ.│ │ │ │ │ │12,0 включ.│ │ │
│ │ │ │ │ │ │
├───────────┼────────┼──────────┤
│
│ │ 76
│" 273 " 1420 " │ │ │ │ Св. 12,0 │
3 │ОТ-2-2.1.3│
│ │ │ │ │ ├───────────┼────────┼───────────┼────────┼──────────┤
│
│ │ 108
│" 377 " 1420 " │ │Св. 5 до 12│ 2
│ От 6,5 до │ 2 │ОТ-2-2.2.2│
│ │ │ │ │ │
включ. │ │12,0 включ.│ │ │
│ │ │ │ │ │ │
├───────────┼────────┼──────────┤
│
│ │ 159
│" 530 " 1420 " │ │ │ │ Св. 12,0 │
3 │ОТ-2-2.2.3│
│
├─────────────┼────────┼───────────────┼────────┼───────────┼────────┼───────────┼────────┼──────────┤
│
│" 159 " 325 "│ 168
│" 630 " 1420 " │ 3
│До 5 включ.│ 1 │ От 6,5 до │ 2
│ОТ-2-3.1.2│
│ │ │ │ │ │ │ │12,0 включ.│ │ │
│ │
├────────┼───────────────┤ │ │
├───────────┼────────┼──────────┤
│
│ │ 219
│" 720 " 1420 " │ │ │ │ Св. 12,0 │
3 │ОТ-2-3.1.3│
│ │
├────────┼───────────────┤
├───────────┼────────┼───────────┼────────┼──────────┤
│
│ │ 245
│" 820 " 1420 " │ │Св. 5 до 12│ 2
│ От 6,5 до │ 2 │ОТ-2-3.2.2│
│ │ │ │ │ │
включ. │ │12,0 включ.│ │ │
│ │ ├────────┼───────────────┤ │ │
├───────────┼────────┼──────────┤
│
│ │ 273
│" 920 " 1420 " │ │ │ │ Св. 12,0 │
3 │ОТ-2-3.2.3│
│ │ ├────────┼───────────────┤
├───────────┼────────┼───────────┼────────┼──────────┤
│
│ │ 325
│" 1220 " 1420 "│ │" 12 " 16
"│ 3 │ От 6,5 до │ 2
│ОТ-2-3.3.2│
│ │ │ │ │ │ │ │12,0 включ.│ │ │
│ │
├────────┼───────────────┤ │ │
├───────────┼────────┼──────────┤
│
│ │ 426
│ 1420 │ │ │ │ Св. 12,0 │
3 │ОТ-2-3.3.3│
├─────────┴─────────────┴────────┴───────────────┴────────┴───────────┴────────┴───────────┴────────┴──────────┤
│
<*> Группа материала основной
трубы действующего газопровода: марки │
│сталей
патрубка относятся к группе материалов 1 (М01).
│
└──────────────────────────────────────────────────────────────────────────────────────────────────────────────┘
А.1.9. Группы
однотипных сварных соединений по типам и маркам сварочных материалов
устанавливаются отдельно для каждого вида и назначения сварочных материалов
(покрытые электроды, проволоки сплошного сечения, порошковые проволоки,
самозащитные порошковые проволоки, сварочные флюсы, защитные газы) по таблицам
Д.4, Д.5, Д.12 - Д.15, Д.18 (Приложение Д).
А.1.10. Группы
однотипных сварных соединений (для РД) по видам покрытия электродов
устанавливаются отдельно для каждого вида покрытия электродов (основное - Б,
целлюлозное - Ц). В одну группу однотипных сварных соединений, выполняемых
ручной дуговой сваркой, объединяются сварные соединения, выполняемые
электродами с одним видом покрытия.
А.1.11. Группы
однотипных сварных соединений (для АФ) по классификации сварочного флюса по
способу изготовления устанавливаются отдельно для каждого класса флюса
(плавленый, керамический). В одну группу однотипных сварных соединений,
выполняемых автоматической сваркой, объединяются сварные соединения,
выполняемые под флюсом одной классификации по способу изготовления.
А.1.12. Группы
однотипных сварных соединений по составу защитного газа устанавливаются
отдельно для каждого защитного газа или номинальных составов смесей защитных
газов:
- 100% углекислый
газ;
- от 40% до 60%
аргон, остальное - углекислый газ;
- 50% аргон + 50%
углекислый газ;
- 75% аргон + 25%
углекислый газ;
- 80% аргон + 20%
углекислый газ;
- 85% аргон + 15%
углекислый газ;
- 100% аргон.
В одну группу
однотипных сварных соединений объединяются сварные соединения, выполняемые с
применением защитного газа одного из вышеприведенных составов.
А.1.13. Группы
однотипных сварных соединений по маркам сварочного оборудования (для МП, МПС,
ААДП, АПГ, АПИ, АФ) устанавливаются отдельно для каждой марки сварочного
оборудования.
А.1.14. Группы
однотипных сварных соединений по применению импульсно-дугового процесса сварки
(для МП, ААДП) устанавливаются отдельно для сварных соединений, выполняемых с
применением импульсно-дугового процесса сварки и без применения
импульсно-дугового процесса сварки.
А.1.15.
Группы однотипных сварных соединений по типам сварных соединений
устанавливаются отдельно для каждого типа сварного соединения (стыковое сварное
соединение - С, угловое сварное соединение - У, нахлестанное сварное соединение
- Н). В одну группу однотипных сварных соединений объединяются сварные
соединения с одним типом сварного соединения.
Допускается
включать в одну группу однотипности угловые и нахлесточные сварные соединения.
А.1.16. Группы однотипных
сварных соединений по типам шва устанавливаются отдельно для каждого типа шва
(стыковой шов - СШ, угловой шов - УШ). В одну группу однотипных сварных
соединений объединяются сварные соединения с одним типом шва.
А.1.17. Группы
однотипных сварных соединений по виду сварных соединений устанавливаются
отдельно для каждого из следующих видов сварных соединений:
- соединения,
выполняемые с одной стороны (односторонняя сварка) - "ос";
- соединения,
выполняемые без подкладки (на весу) - "бп";
- соединения,
выполняемые на съемной или остающейся подкладке - "сп";
- соединения,
выполняемые с двух сторон (двухсторонняя сварка) - "дс".
В одну группу
однотипных сварных соединений объединяются сварные соединения одного вида.
А.1.18. Группы
однотипных сварных соединений по геометрическим параметрам разделки кромок
свариваемых элементов приведены в таблице А.8. В одну группу однотипных сварных
соединений объединяются сварные соединения одной группы по форме разделки
кромок свариваемых элементов.
Таблица А.8
Группы
однотипных сварных соединений по геометрическим
параметрам разделки
кромок свариваемых элементов
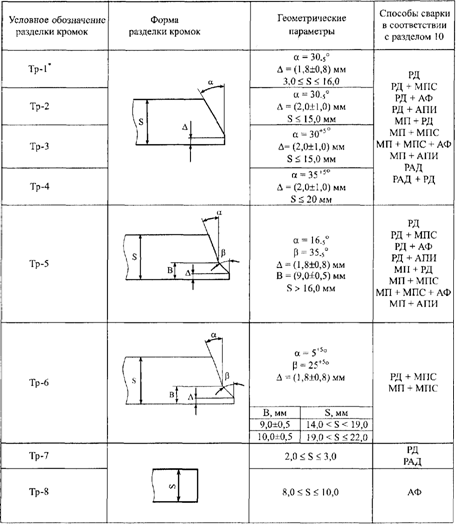
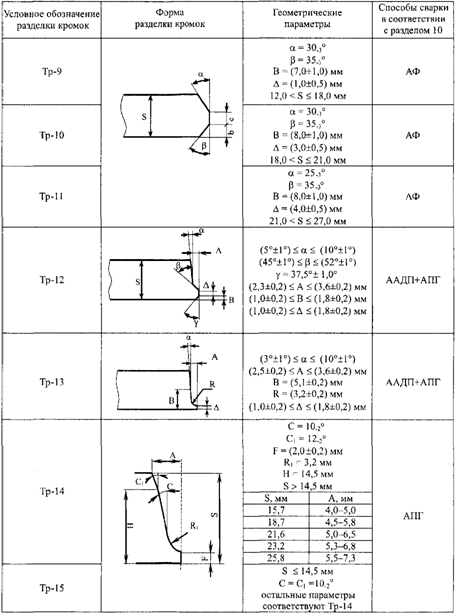
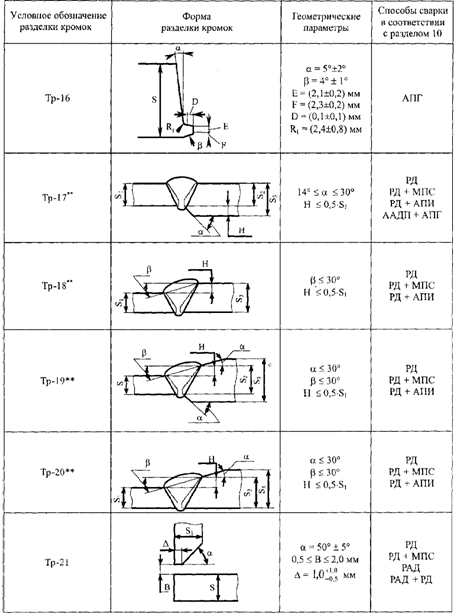
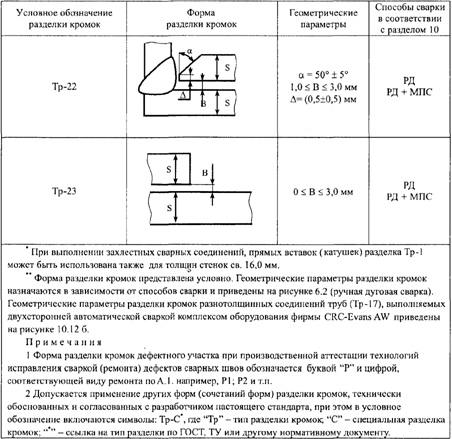
А.1.19. Группы
однотипных сварных соединений по пространственному положению при сварке
устанавливаются отдельно для стыковых и угловых соединений труб и приведены в
таблице А.9.
Таблица А.9
Группы однотипных
сварных соединений
по пространственным
положениям при сварке
Условное
обозначения
положения
сварки
|
Тип
сварного
соединения
по А.1.15
|
Наименование положения сварки
|
Н1
|
С
|
Нижнее
при горизонтальном расположении осей труб,
свариваемых с поворотом
|
У
|
Нижнее
при горизонтальном расположении оси
патрубка, свариваемого с поворотом
|
Н2
|
У
|
Нижнее
при вертикальном расположении оси патрубка,
свариваемых с поворотом или без поворота
|
В1
|
С
|
Переменное
при горизонтальном расположении осей
труб, свариваемых без поворота на подъем <*>
|
У
|
Переменное
при горизонтальном расположении оси
патрубка, свариваемых без поворота на подъем
|
В2
|
С
|
Переменное
при горизонтальном расположении осей
труб, свариваемых без поворота на спуск <*>
|
У
|
Переменное
при горизонтальном расположении оси
патрубка, сварка без поворота на спуск
|
Г
|
С
|
Горизонтальное
при вертикальном расположении осей
труб, свариваемых без поворота или с поворотом
|
Н45
|
С
|
Переменное
при наклонном (под углом 45°)
расположении осей труб, свариваемых без поворота
|
У
|
Переменное
при наклонном (под углом 45°)
расположении оси патрубка, свариваемых без
поворота
|
П2
|
У
|
Потолочное
при вертикальном расположении оси
патрубка, свариваемых с поворотом или без поворота
|
<*> Допускаемое
отклонение оси трубы от
горизонтали составляет
+/- 20°.
|
В одну группу
однотипных сварных соединений объединяются сварные соединения одной группы
однотипности по типу сварного соединения, выполняемые в одном пространственном
положении при сварке.
Примечания. 1.
Положение КСС при сварке должно соответствовать требованиям
операционно-технологической карты сборки и сварки по аттестуемой технологии
сварки. Если технология сварки предусматривает выполнение производственных
сварных соединений в различных пространственных положениях, то сварку КСС
следует производить в наиболее трудновыполнимом.
2. Сварка КСС при
производственной аттестации технологий сварки кольцевых стыковых соединений
линейной части магистральных газопроводов в условиях гористой местности с углом
наклона оси газопровода к линии горизонта более 20° должна проводиться в
пространственном положении Н45 или в положении, соответствующем величине
максимального наклона оси газопровода к линии горизонта.
А.1.20. Группы
однотипных сварных соединений по выполнению предварительного, сопутствующего
(межслойного) подогрева устанавливаются отдельно для сварных соединений,
выполняемых с предварительным, сопутствующим (межслойным) подогревом и без
подогрева.
А.1.21. Группы
однотипных сварных соединений по типам центраторов (центрирующих
приспособлений) устанавливаются отдельно для каждого типа центратора (наружный,
внутренний). В одну группу однотипных сварных соединений объединяются сварные
соединения, выполненные с применением одного типа центратора.
А.1.22. Группы
однотипных сварных соединений по выполнению термической обработки
устанавливаются отдельно для сварных соединений, выполняемых с послесварочной
термической обработкой и без обработки.
А.1.23.
Группы однотипных сварных соединений по виду ремонта устанавливаются отдельно
для каждого из следующих видов ремонта:
1) ремонт
дефектов корневого, подварочного или внутреннего слоев шва с частичной выборкой
сварного шва изнутри трубопровода;
2) ремонт
внутренних дефектов заполняющих слоев шва, внутренних и наружных дефектов
облицовочного слоя с частичной выборкой сварного шва снаружи трубопровода;
3) ремонт
дефектов корневого слоя шва со сквозной выборкой дефектного участка сварного
шва снаружи трубопровода;
4) ремонт
подрезов в облицовочном слое сварного шва;
5) ремонт
подрезов в подварочном, внутреннем слоях сварного шва изнутри газопровода;
6) ремонт
внутренних и наружных дефектов угловых и нахлесточных сварных соединений с
частичной выборкой сварного шва;
7) ремонт
подрезов в облицовочном слое шва угловых и нахлесточных сварных соединений.
Примечания. 1. Виды
ремонта 1), 2), 3) не включают ремонт подрезов.
2. Ремонт сваркой
дефектов сварных соединений изнутри труб (элементов) должен осуществляться для
КСС диаметром 1020 мм и более, а для КСС диаметром менее 1020 мм с учетом
требований 10.2.40.
В одну группу
однотипных сварных соединений объединяются сварные соединения, выполняемые
одним из вышеприведенных видов ремонта.
А.2. Общие
требования к производственной аттестации технологий сварки
А.2.1.
Производственная аттестация технологий сварки проводится путем сварки КСС,
однотипных производственным, в условиях, тождественных производственным, с
целью подтверждения того, что организация, применяющая технологии сварки,
обладает необходимыми техническими, организационными возможностями и
квалифицированными кадрами для производства сварочных работ. Производственную
аттестацию проводит организация, выполняющая сварку газопроводов, совместно со
специализированным аттестационным центром САСв по сварке газонефтепроводов.
Этапы работ при
проведении производственной аттестации технологий сварки приведены в таблице
А.10.
Таблица А.10
Этапы проведения
производственной аттестации
технологий сварки
N
этапа
|
Наименование этапа
|
Исполнитель
|
1
|
Оформление
заявок на производственную
аттестацию технологий сварки
|
Организация-заявитель
|
2
|
Разработка,
согласование и утверждение
программ производственной аттестации
технологий сварки, определение параметров
КСС
|
Аттестационный
центр
Организация-заявитель
|
3
|
Назначение
ответственных за организацию и
безопасность проведения производственной
аттестации технологий сварки
|
Организация-заявитель
|
4
|
Назначение
аттестационной комиссии
|
Аттестационный
центр
|
5
|
Проверка
готовности организации к
выполнению сварочных работ по заявляемым к
аттестации технологиям сварки
|
Аттестационная
комиссия
|
6
|
Сварка
КСС
|
Организация-заявитель
|
7
|
Проведение
неразрушающего контроля качества
и механических испытаний КСС
|
Организация-заявитель
Аттестационный центр
|
8
|
Оформление
заключений о готовности
организации, выполняющей сварочные работы,
к использованию аттестованных технологий
сварки
|
Аттестационный
центр
|
9
|
Оформление
свидетельств о производственной
аттестации технологий сварки
|
Аттестационный
центр,
НАКС
|
10
|
Оформление
заключений о готовности
организации, выполняющей сварочные работы,
к использованию аттестованных технологий
сварки
|
Аттестационный
центр
|
Примечание. Порядок
аттестации технологии сварки
соединений
"труба + СДТ", "труба
+ ЗРА" устанавливается с
учетом положений,
изложенных в А.2.11.
|
А.2.2. Заявителем
производственной аттестации технологий сварки является организация, выполняющая
сварочные работы. Заявка, оформленная согласно требованиям РД 03-615-03 [3], с
необходимыми приложениями направляется для рассмотрения в аттестационный центр.
Для проведения внеочередной аттестации, согласно 4.7, организацией-заявителем в
аттестационный центр должно быть направлено письмо с указанием установленных
фактов нарушений или отклонений в применении аттестованных технологий сварки
организацией, выполняющей сварочные работы. К письму может быть приложена копия
предписания технического надзора.
А.2.3.
Аттестационный центр создает комиссию по производственной аттестации технологий
сварки, в состав которой по согласованию могут быть дополнительно включены:
- представитель
организации-заявителя - главный сварщик или замещающее его лицо - специалист
сварочного производства III или IV уровня;
- представитель
технического надзора Заказчика.
А.2.4. На основании
заявки аттестационная комиссия с привлечением уполномоченных специалистов
организации-заявителя разрабатывает программу производственной аттестации
технологий сварки. Форма программы должна соответствовать требованиям РД
03-615-03 [3]. Программа должна быть согласована с руководителем
организации-заявителя и утверждена руководителем аттестационного центра.
А.2.5.
Организация-заявитель издает распорядительные документы о назначении
ответственных за организацию и безопасность проведения работ при
производственной аттестации технологий сварки, за регистрацию фактических
параметров режимов сварки КСС, определяет порядок маркировки КСС для
неразрушающего контроля качества и механических испытаний.
А.2.6. Для
регистрации параметров режимов сварки, в соответствии с программой
производственной аттестации, следует подготовить рабочие бланки в виде таблиц в
количестве не менее трех экземпляров для каждого КСС.
А.2.7. Перед
сваркой КСС аттестационная комиссия проверяет наличие у организации-заявителя
технических и организационных возможностей, квалифицированных кадров для
выполнения сварочных работ по аттестуемым технологиям сварки, включая наличие:
а) необходимого
количества сварщиков, специалистов сварочного производства, аттестованных в
соответствии с ПБ 03-273-99 [4], РД 03-495-02 [5];
б) необходимого
количества специалистов неразрушающего контроля, аттестованных в соответствии с
ПБ 03-440-02 [8];
в) необходимой
номенклатуры сварочных материалов, аттестованных в соответствии с требованиями
РД 03-613-03 [1];
г) необходимого
парка сварочного оборудования, передвижных сварочных агрегатов, передвижных и
самоходных сварочных установок, аттестованных в соответствии с требованиями РД
03-614-03 [2] и оснащенных необходимой номенклатурой и количеством
вспомогательного оборудования;
д) лаборатории
неразрушающего контроля (собственной либо привлеченной), аттестованной в
соответствии с ПБ 03-372-00 [7] и оснащенной необходимой номенклатурой
оборудования и материалов для контроля качества сварных соединений
газопроводов.
А.2.8. Если в
результате проверки установлено, что по каким-либо признакам
организация-заявитель не удовлетворяет необходимым требованиям и не имеет
возможности исправить выявленные недостатки за короткий период времени,
аттестационный центр оформляет соответствующее отрицательное заключение с
указанием причин. В дальнейшем организация-заявитель может быть допущена к
производственной аттестации технологии сварки только после устранения
выявленных несоответствий.
А.2.9. Виды КСС при
односторонней и двухсторонней сварке, выполняемые в процессе аттестации
технологий сварки, представлены в таблице А.11.
Таблица А.11
Виды КСС
N группы
конструктивных
элементов
по таблице А.2
|
Вид КСС
|
Индекс
однотипности
|
1
|
Стыковое
сварное соединение труб одной
толщины стенки без подварки изнутри
("труба + труба") <1>
|
1.1
|
2
|
Стыковое
сварное соединение труб одной
толщины стенки с подваркой изнутри <2>
(для РД, односторонней сварки под флюсом
и механизированных способов, включая
комбинированные способы сварки)
("труба + труба")
|
2.1
|
Стыковое
сварное соединение труб одной
толщины стенки (для двухсторонней
автоматической сварки) ("труба + труба")
|
2.2
|
3
|
Стыковое
сварное соединение труб разной
толщины стенки с подваркой изнутри <2>
(для ручной дуговой и механизированной
сварки, включая комбинированные технологии
сварки) ("труба + труба")
|
3.1
|
Стыковое
сварное соединение труб разной
толщины стенки (для двухсторонней
автоматической сварки) ("труба + труба")
|
3.2
|
4
|
Стыковое
сварное соединение труб разной
толщины стенки без подварки изнутри <3>
("труба + труба")
|
4.1
|
5
|
Стыковое
сварное соединение "труба + СДТ"
|
5.1
|
Стыковое
сварное соединение
"труба + катушка-имитатор СДТ"
|
5.2
|
Стыковое
сварное соединение "труба + ЗРА"
|
5.3
|
Стыковое
сварное соединение
"труба + катушка-имитатор ЗРА"
|
5.4
|
6
|
Стыковое
сварное соединение труб одной
толщины стенки без подварки изнутри
(захлест, прямая вставка (катушка))
|
6.1
|
7
|
Угловое
сварное соединение
"патрубок + основная труба"
|
7.1
|
Угловое
сварное соединение
"патрубок + накладка"
|
7.2
|
Нахлесточное
сварное соединение
"накладка + основная труба"
|
7.3
|
8
|
Угловое
сварное соединение
"патрубок + основная труба"
|
8.1
|
<1> В карте
технологического процесса сварки
КСС может
регламентироваться подварка изнутри
на отдельных участках
периметра
сварного шва со смещениями кромок,
непроварами, несплавлениями. Участки
подварки должны располагаться вне зоны вырезки образцов (темплетов)
для
механических испытаний.
<2> В
карте технологического процесса
сварки КСС должна
регламентироваться обязательная подварка изнутри сварного шва.
<3> При условии,
что сварное соединение
выполняется из труб
(элементов) номинальным диаметром менее 1020 мм.
|
А.2.10. Количество
КСС должно быть достаточным для выявления особенностей технологий сварки,
регистрации параметров режимов сварки, проведения пооперационного, визуального,
измерительного, неразрушающего контроля качества и механических испытаний КСС.
При производственной аттестации технологий автоматической сварки проволокой
сплошного сечения и порошковой проволокой в защитных газах количество КСС
должно быть не менее трех.
А.2.11.
Выбор КСС для производственной аттестации технологий сварки соединений
"труба + СДТ", "труба + ЗРА" при экономической
нецелесообразности или технической невозможности вырезки образцов для
проведения механических испытаний КСС производится с учетом следующих
положений.
А.2.11.1. Для
производственной аттестации технологий сварки допускается применение
катушек-имитаторов СДТ, ЗРА. Диаметр и толщина стенки, химический состав
трубной стали, класс прочности, разделка кромок, термообработка катушек-имитаторов
должны соответствовать требованиям ТУ на поставку СДТ и ЗРА для магистрального
газопровода. Длина катушек-имитаторов должна составлять не менее половины их
номинального диаметра.
А.2.11.2.
Допускается проводить производственную аттестацию технологий сварки "труба
+ СДТ", "труба + ЗРА" на первых товарных сварных соединениях,
соответствующих области распространения технологий сварки, прошедших
производственную аттестацию с использованием катушек-имитаторов. Аттестационный
центр должен письменно согласовать с Заказчиком проведение такой аттестации.
Выбор сварщиков для выполнения КСС производит аттестационная комиссия. Перед
сваркой КСС рекомендуется выполнить одно или два тренировочных сварных
соединения катушек труб соответствующих типоразмеров.
А.2.12. Типоразмеры
КСС прямых врезок следует устанавливать с учетом требований таблицы А.7. Длина
катушек должна обеспечивать возможность качественной подготовки отверстия,
сборки и сварки КСС, а также изготовления комплекта образцов для механических
испытаний. При этом длина катушек должна составлять не менее:
- 350 мм - для
ввариваемого патрубка
до 200 включ.;
- 500 мм - для
ввариваемого патрубка
более 200;
- одного диаметра
для основной трубы
до 500 включ.;
- 0,5 диаметра для
основной трубы
более 500 включ.
Разметка места
вырезки отверстия в основной трубе и заготовки для изготовления усиливающей
накладки (воротника) производится бригадиром по специальному шаблону, вырезка
отверстий - высококвалифицированным газорезчиком. Подготовка отверстий, а также
подготовка трубы-ответвления (патрубка) и сборка стыкового соединения
осуществляется бригадиром и электросварщиком, который должен выполнить сварку
контрольного сварного соединения. Для сборки стыковых сварных соединений
следует использовать приспособления, обеспечивающие регламентируемые
технологической картой сварки требования к перпендикулярности и смещениям осей
труб.
А.2.13. В
соединениях прямых врезок с установкой усиливающей накладки (воротника) каждый
из трех швов следует считать отдельным КСС (таблица А.11), которые выполняются
последовательно на одном соединении по одной операционно-технологической карте
сборки и сварки. Аттестацию технологии сварки угловых и нахлесточных соединений
прямых врезок следует производить в условиях, тождественных производственным.
Пространственное положение сварки при аттестации должно соответствовать
положению, регламентированному операционно-технологической картой сборки и
сварки, и последующему выполнению товарных сварных соединений. Если в
операционно-технологической карте сборки и сварки предусмотрено выполнение
сварных соединений прямых врезок в разных пространственных положениях, то для
сварки КСС должно быть выбрано наиболее трудновыполнимое из них.
А.2.14. Выборку
имитаторов дефектных участков при производственной аттестации технологий
ремонта сваркой корневого слоя шва неповоротных кольцевых стыковых сварных
соединений со сквозным пропилом, согласно А.1.23, следует выполнять в
потолочной части (в пространственном положении от
до
или от
до
).
Расположение имитаторов дефектных участков при производственной аттестации
технологий ремонта сваркой дефектов сварных швов других видов определяется
аттестационной комиссией с учетом результатов неразрушающего контроля качества
сварных соединений, на которых будет выполняться сварка КСС. Аттестацию
технологии ремонта поворотных стыков трубных секций, выполненных на
трубосварочных базах, следует производить в удобном для сварки пространственном
положении.
Допускается
выполнять сварку КСС при производственной аттестации технологий ремонта сваркой
дефектов сварных швов различными видами ремонта на одном сварном шве, при этом
общая длина участков каждого вида ремонта должна быть достаточной для
проведения неразрушающего контроля качества и вырезки образцов для механических
испытаний КСС, но не менее:
- 150 мм
для КСС
от 80
до 350;
- 200
мм " " " св. 350 до 500;
- 300
мм " " " св. 500 до 1400.
В заключениях,
протоколах результатов неразрушающего контроля качества и механических
испытаний каждый вид ремонта должен идентифицироваться различными клеймами КСС.
А.2.15. Сварку КСС
следует выполнять в условиях, тождественных производственным, в присутствии
представителей аттестационной комиссии, организации-заявителя.
А.2.16. В процессе
производственной аттестации при необходимости корректируются последовательность
выполнения операций подготовки, сборки и сварки, параметры режимов сварки.
А.2.17. Члены аттестационной
комиссии производят запись в рабочих бланках фактических параметров режимов
сварки и других технологических операций. Датированные и подписанные бланки
регистрации параметров режимов сварки должны быть переданы в аттестационный
центр. На основе анализа зарегистрированных параметров сварки КСС
аттестационным центром оформляются карты технологического процесса сварки КСС.
Карты
технологического процесса сварки КСС с применением специального оборудования
механизированной и автоматической сварки (МП, МПС, ААДП, АПГ, АПИ) должны
согласовываться с разработчиком настоящего стандарта и содержать требования по
технике сварки в различных пространственных положениях, последовательности
выполнения слоев шва, предварительному, сопутствующему (межслойному) подогреву.
А.2.18. Карты
технологического процесса сварки КСС должны включать:
- наименование
технологии сварки (способ или комбинация способов сварки);
- наименование
конструктивного элемента (соединения) газопровода;
- идентификатор
(шифр) однотипности сварных соединений;
- вид соединения;
- тип шва;
- группу основного
материала (класс прочности, марка стали), ГОСТ или ТУ, эквивалент углерода
;
- размеры и
конструкцию КСС (толщина, диаметр, форма и размеры разделки кромок, зазор);
- требования к
подготовке кромок свариваемых труб (способ обработки, требования к зачистке);
- положение КСС при
сварке;
- требования к
сборке сварных соединений (тип применяемых центраторов и сборочных
приспособлений, параметры сборки, количество, расположение и размеры
прихваток);
- применяемые
сварочные материалы (марки, типы и диаметры, состав смеси защитных газов и
т.д.), ГОСТ или ТУ на изготовление;
- применяемое сварочное
оборудование (тип, марка);
- перечень и
последовательность технологических операций, выполняемых в процессе сварки КСС;
-
зарегистрированные параметры режимов сварки КСС, последовательность наложения
слоев шва и их количество и др.;
- наличие предварительного,
сопутствующего (межслойного) подогрева и послесварочной термообработки, а также
их параметры, средства и условия контроля температуры;
- геометрические
параметры КСС;
- методы и объемы
неразрушающего контроля качества и механических испытаний КСС;
- дополнительные
параметры и характеристики, являющиеся существенными для выполнения КСС по
аттестуемым технологиям сварки;
- дата и место
сварки КСС;
- погодные условия
при сварке КСС;
- Ф.И.О. сварщиков
или операторов, номера и срок действия аттестационных удостоверений.
Примечание. Состав
идентификатора однотипности сварных соединений:
1 - обозначение
способа сварки (согласно табл. А.1);
2 - номер группы
материалов (согласно табл. А.3);
3 - индекс
однотипности по диаметру (А.4);
4 - индекс
однотипности по толщине стенки (А.5);
5 - индекс типа
сварного соединения ("С" или "У");
6 - индекс
необходимости подогрева ("-" или "П");
7 - индекс необходимости
термообработки ("-" или "Т");
8 - обозначение
формы разделки кромок по таблице А.8.
В заключительной
части карты технологического процесса сварки КСС члены комиссии должны
подтвердить соответствие или несоответствие содержания и последовательности
работ требованиям технологической карты сварки и настоящего стандарта. Карта
технологического процесса сварки КСС должна быть подписана представителем
аттестационной комиссии и представителем организации-заявителя,
присутствовавшими при сварке. К карте технологического процесса сварки КСС
должны быть приложены копии сертификатов качества на основные и сварочные
материалы.
А.2.19. При
положительных результатах неразрушающего контроля качества и механических
испытаний КСС оформляется акт производственной аттестации технологии сварки.
Рекомендуемая форма акта производственной аттестации технологии сварки
приведена в Приложении А.3. Акт производственной аттестации технологии сварки
является основанием для разработки, согласования и утверждения операционно-технологических
карт сборки и сварки. Один экземпляр акта производственной аттестации
передается Заказчику в составе исполнительной документации.
А.2.20. Сводные
таблицы, оформленные по результатам неразрушающего контроля качества и
механических испытаний КСС, должны быть переданы в аттестационный центр для
оформления заключения о готовности организации-заявителя к использованию
аттестованной технологии сварки.
В процессе
производственной аттестации при необходимости корректируются последовательность
выполнения операций подготовки, сборки и сварки, режимы сварки и вносятся
изменения и дополнения в операционно-технологические карты сборки и сварки.
А.2.21. Качество
КСС должно оцениваться визуальным, измерительным и неразрушающими физическими
методами контроля (основным, дублирующим, дополнительными) и соответствовать
требованиям СТО "Газпром" 2-2.4-083.
А.2.22.
Неразрушающий контроль качества КСС должен выполняться лабораториями
неразрушающего контроля, аттестованными в соответствии с ПБ 03-372-00 [7].
А.2.23. При
неудовлетворительных результатах неразрушающего контроля качества КСС
аттестационная комиссия с привлечением специалистов и сварщиков или операторов
организации-заявителя проводит анализ возможных причин образования дефектов
сварных швов и по результатам анализа принимает решение о сварке
дополнительного КСС.
А.2.24.
Механические испытания КСС должны выполняться лабораториями, аккредитованными в
установленном порядке на соответствующие виды испытаний, оснащенными
необходимой номенклатурой испытательного оборудования и материалов, имеющими в
своем составе квалифицированных специалистов, аттестованных в установленном
порядке на соответствующие виды испытаний.
А.2.25.
Механические испытания КСС должны выполняться после получения положительных
результатов неразрушающего контроля качества КСС.
А.2.26. Количество
образцов и виды механических испытаний КСС приведены в таблице А.12.
Таблица А.12
Количество образцов
и виды механических испытаний КСС
Диаметр
КСС, мм
|
Толщина
стенки
КСС, мм
|
Количество образцов для испытаний,
шт.
|
на
ста-
тиче-
ское
рас-
тяже-
ние
|
на статический изгиб
|
на
ударный
изгиб
|
на
твер-
дость
|
на
ма-
кро-
шлиф
|
на
сплю-
щива-
ние
|
с
расположением
корня шва
|
боковой
поверх-
ностью
(на
ребро)
|
по
оси
шва
|
по
около-
шовной
зоне
|
наружу
|
внутрь
|
До 89
включ.
|
от 2,0
до 5,0
включ.
|
3
<1>
|
3
<1>
|
-
|
-
|
-
|
-
|
-
|
-
|
-
|
Св.
89
до 377
включ.
|
от 2,0
до 12,0
включ.
|
2
|
-
|
2
|
2
|
-
|
-
|
-
|
-
|
-
|
более
12,0
|
2
|
-
|
-
|
-
|
4
|
-
|
-
|
-
|
-
|
Более
377
|
до
12,0
включ.
|
4
|
-
|
4
|
4
|
-
|
3
|
3
|
1
|
1
<3>
|
св.
12,0
до 19,0
включ.
|
4
|
-
|
-
|
-
|
8
|
3
|
3
|
1
|
1
<3>
|
более
19,0
|
4
|
-
|
-
|
-
|
8
|
6
<2>
|
6
<2>
|
1
|
1
<3>
|
<1> Испытания проводятся на трубчатых образцах.
<2> Три образца вырезаются из
нижних (внутренних) слоев шва
и три
образца - из верхних (наружных) слоев шва.
<3> Для технологии
автоматической двухсторонней сварки под флюсом.
|
А.2.27. Схема
вырезки образцов из неповоротных кольцевых стыковых КСС должна соответствовать
рисункам А.1, А.2.
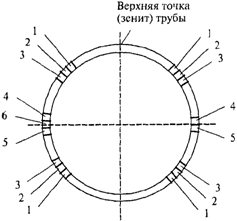
N 1 - образец для
испытания на статическое растяжение;
N 2 - образец для
испытания на статический изгиб корнем шва
наружу или на
ребро; N 3 - образец для испытаний
на статический
изгиб корнем шва внутрь или на ребро;
N 4 - образцы для
испытаний на ударный изгиб (по оси шва);
N 5 - образцы для
испытаний на ударный изгиб
(по линии
сплавления); N 6 - образец
для измерения
твердости
Примечание.
Образцы, отмеченные знаком "*", испытываются для сварных соединений с
толщиной стенки более 19,0.
Рисунок
А.1. Схема вырезки образцов
для проведения
механических испытаний кольцевых
стыковых сварных
соединений диаметром 377 мм и более
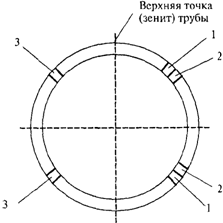
N 1 - образец для
испытания на статическое растяжение;
N 2 - образец для
испытания на статический изгиб
корнем шва внутрь;
N 3 - образец для испытания
на статический
изгиб корнем шва наружу
Рисунок
А.2. Схема вырезки образцов
для механических
испытаний кольцевых стыковых
сварных соединений
диаметром св. 89 до 377 мм
А.2.28. При
производственной аттестации технологий сварки неповоротных кольцевых стыковых
соединений элементов одинаковой толщины стенки с подваркой изнутри отдельных
участков корневого слоя шва, из этих участков должны быть вырезаны
дополнительные образцы для испытаний на статическое растяжение (2 шт.) и
статический изгиб (4 шт.).
А.2.29. Образцы для
механических испытаний могут быть вырезаны из участков шва, не имеющих
каких-либо допустимых дефектов, выявленных методами неразрушающего контроля.
Разметку и вырезку темплетов следует производить с учетом припусков на резку и
механическую обработку. Величина припуска должна обеспечивать минимальное
влияние резки на механические свойства металла сварного шва и околошовной зоны
образцов.
Величина припуска
должна составлять:
- при кислородной
(газовой) или воздушно-плазменной дуговой резке - не менее 5,0 мм;
- при механической
резке - не менее 3,0 мм.
А.2.30. Маркировка
темплетов должна включать номер операционно-технологической карты сборки и
сварки, номер сектора КСС, номер темплета и наноситься несмываемой краской или
маркером.
А.2.31. Темплеты из
поворотных стыковых сварных соединений должны вырезаться равномерно по
периметру сварного соединения по схеме, аналогичной рисунку А.1, но не ближе
200 мм от места окончания процесса сварки.
А.2.32. Методика
механических испытаний КСС, тип и размеры образцов приведены в Приложении Б.
А.2.33.
Механические испытания КСС при аттестации технологий сварки газопроводов из
труб с классом прочности К56 и выше надземной прокладки, а также прокладки в
зонах сейсмической активности должны выполняться в испытательном центре ООО
"ВНИИГАЗ".
А.2.34. Для
периодической производственной аттестации технологий сварки допускается не
проводить механические испытания на ударный изгиб при условии, что КСС выполнены
сварочными материалами, которые применялись при первичной производственной
аттестации.
А.2.35. Перед
проведением механических испытаний на статическое растяжение и статический
изгиб КСС, выполненных с электродами с целлюлозным видом покрытия или самозащитной
порошковой проволокой марки "Иннершилд", следует провести
дефлокирующую термическую обработку образцов при температуре +250 °C в течение
6 ч.
А.2.36. При сварке
КСС прямых врезок должен осуществляться приемочный пооперационный визуальный
контроль каждого слоя шва. По окончании сварки КСС подвергается визуальному и
измерительному контролю, основному контролю ультразвуковому (или
радиографическому) контролю и капиллярному (или магнитопорошковому) контролю, а
также испытаниям на ударный излом.
А.2.37. Для
проведения механических испытаний на излом соединений прямых врезок с
усиливающей накладкой (воротником) должны быть вырезаны 2 образца для испытания
углового соединения (рисунок А.3, а) и 2 образца для испытаний нахлесточного
соединения (рисунок А.3, б). Форма и размеры образцов углового и нахлесточного
соединений, а также методика механических испытаний приведены в Приложении Б.
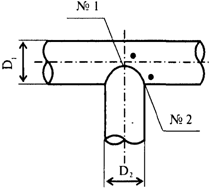
а)
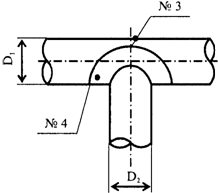
б)
а) без установки
воротника;
б) с усиливающей
накладкой (воротником);
N 1 и N 2 - образцы
из углового сварного соединения;
N 3 и N 4 - образцы
из нахлесточного сварного соединения
Рисунок А.3. Схема
отбора образцов
для механических
испытаний угловых сварных швов
(прямых врезок)
А.2.38. С учетом
требований А.2.37 в процессе производственной аттестации технологии сварки
соединений прямых врезок с усиливающей накладкой (воротником) следует выполнить
не менее двух КСС:
- без усиливающей
накладки (воротника) (рисунок А.3, а);
- с усиливающей
накладкой (воротником) (рисунок А.3, б).
При
производственной аттестации технологии сварки соединений прямых врезок с
диаметром трубы-ответвления (патрубка) менее 57 мм рекомендуется дополнительно
выполнить еще одну врезку без установки воротника (шов I). В данном случае из
каждого углового соединения следует вырезать по одному образцу шириной 40 мм
(ориентировочно) для испытаний на излом.
А.2.39. Количество
образцов и виды механических испытаний КСС при производственной аттестации
технологий ремонта сваркой дефектов сварных швов приведены в таблице А.13.
Таблица А.13
Количество образцов
и виды механических испытаний КСС
при
производственной аттестации технологий ремонта
сваркой дефектов
сварных швов
Толщина
стенки
трубы,
мм
|
Вид
ремонта
<1>
(см.
А.1.23)
|
Количество образцов для испытаний,
шт.
|
на
растяжение
|
на статический изгиб
|
на ударный изгиб
|
с
расположением
корня шва
|
боковой
поверхностью
(на ребро)
|
по
оси
шва
|
по
околошовной
зоне
|
наружу
|
внутрь
|
До
12,0
включ.
|
1
|
-
|
2
|
-
|
-
|
-
|
-
|
2
|
1
|
2
|
-
|
-
|
-
|
-
|
3
|
1
|
2
|
-
|
-
|
-
|
-
|
4
|
-
|
-
|
2
|
-
|
-
|
-
|
5
|
-
|
2
<2>
|
-
|
-
|
-
|
-
|
Св.
12,0
до 19,0
включ.
|
1
|
-
|
-
|
-
|
2
|
-
|
-
|
2
|
1
|
-
|
-
|
2
|
-
|
-
|
3
|
1
|
-
|
-
|
2
|
-
|
-
|
4
|
-
|
-
|
-
|
2
|
-
|
-
|
5
|
-
|
-
|
-
|
2
|
-
|
-
|
Более
19,0
|
1
|
-
|
-
|
-
|
2
|
-
|
-
|
2
|
1
|
-
|
-
|
2
|
3
|
3 <3>
|
3
|
1
|
-
|
-
|
2
|
6
<3>
|
6 <3>
|
4
|
-
|
-
|
-
|
2
|
-
|
-
|
5
|
-
|
-
|
-
|
2
|
-
|
-
|
<1> Кроме видов ремонта N 1, 2 А.1.23.
<2> Образцы изгибают с
расположением внутреннего слоя шва наружу.
<3> Три образца вырезаются из
нижних (внутренних) слоев
шва и три
образца - из верхних (наружных) слоев шва.
|
А.2.40. Для КСС,
выполненных при производственной аттестации технологий ремонта сваркой видов
6), 7) по п. А.1.23, должны быть проведены механические испытания на излом
образцов, вырезанных из углового соединения "основная труба +
патрубок", при этом для углового соединения "патрубок + усиливающая
накладка" и нахлесточного соединения "усиливающая накладка + основная
труба" проведение механических испытаний не требуется.
А.2.41. При
неудовлетворительных результатах механических испытаний КСС аттестационная
комиссия принимает решение о механических испытаниях дополнительных образцов,
вырезаемых из повторно-сваренного КСС, количество которых должно
соответствовать требованиям таблицы А.14.
Таблица А.14
Количество
дополнительных образцов
для проведения
механических испытаний КСС
┌────────────────────────┬─────────────────────────────────┬──────────────┐
│ Вид
испытания │ Причина неудовлетворительного │
Количество │
│ │ результата │дополнительных│
│ │ │
образцов для │
│ │ │испытания,
шт.│
├────────────────────────┼─────────────────────────────────┼──────────────┤
│Испытание
сварного │Разрыв одного
образца по сварному│ 2
<*> │
│соединения
на │шву или ЗТВ со
значением предела │
│
│статическое
растяжение │прочности ниже
установленного │ │
│(плоские
поперечные │нормативного
значения │ │
│образцы) │ │ │
├────────────────────────┼─────────────────────────────────┼──────────────┤
│Испытание
сварного │Угол загиба одного
образца не │ 2 <*> │
│соединения
на │превышает
установленного │ │
│статический
изгиб │минимально допустимого
значения │ │
├────────────────────────┼─────────────────────────────────┼──────────────┤
│Испытание
сварного │Ударная вязкость для
одного │ 3 <*> │
│соединения
на ударный │образца ниже
установленного │ │
│изгиб │минимально
допустимого значения │ │
├────────────────────────┼─────────────────────────────────┼──────────────┤
│Измерение
твердости │В одной точке
значение твердости │
<**> │
│по
Виккерсу (HV ) │превышает максимально допустимое
│ │
│ 10 │значение │ │
│металла
шва и ЗТВ │ │ │
├────────────────────────┼─────────────────────────────────┼──────────────┤
│Оценка
геометрических │На одном
макрошлифе перекрытие │ 3
макрошлифа │
│параметров
и качества │внутреннего и первого
наружного │ <***> │
│шва
по макрошлифам │слоев шва, а
также их смещение от│
│
│ │условной оси
симметрии шва не │ │
│ │соответствуют
установленным │ │
│ │требованиям │ │
├────────────────────────┴─────────────────────────────────┴──────────────┤
│
<*> Образцы должны
быть вырезаны из
участка сварного соединения│
│повторно-сваренного КСС,
максимально приближенного к
месту вырезки│
│образца,
который не выдержал механических испытаний. │
│
<**> Три дополнительных замера в непосредственной близости от точки,│
│в которой
превышено значение твердости,
на образце, вырезанном
из│
│повторно
сваренного КСС.
│
│
<***> Места вырезки макрошлифов должны располагаться
равномерно по│
│периметру
повторно сваренного КСС (ориентировочно под углом 120°), но не│
│ближе
200 мм от места вырезки макрошлифа, не прошедшего испытания. │
└─────────────────────────────────────────────────────────────────────────┘
А.2.42. При
неудовлетворительных результатах неразрушающего контроля качества
дополнительного КСС по п. А.2.23 или механических испытаний дополнительных
образцов КСС по п. А.2.41 аттестационный центр оформляет соответствующее
отрицательное заключение с указанием причин. В дальнейшем организация-заявитель
может быть допущена к производственной аттестации технологии сварки после
устранения причин неудовлетворительных результатов испытаний. Для выявления
причин, по согласованию, могут быть привлечены специалисты аттестационного
центра. Для проведения производственной аттестации технологии сварки после
устранения причин неудовлетворительных результатов в аттестационный центр должна
быть представлена новая заявка на проведение производственной аттестации
технологии сварки.
А.2.43. При
положительных результатах производственной аттестации в случае необходимости
корректируются последовательность выполнения операций подготовки, сборки и
сварки, параметры режимов сварки и вносятся изменения и дополнения в
операционно-технологические карты сборки и сварки.
А.2.44. По
результатам производственной аттестации технологий сварки аттестационная
комиссия составляет заключения о готовности организации-заявителя к
использованию аттестованных технологий. Заключения составляют в трех
экземплярах на основании первичных документов - карт технологических процессов
сварки КСС (операционно-технологических карт сборки и сварки), сертификатов на
основные и сварочные материалы, протоколов и заключений по неразрушающему
контролю качества и механическим испытаниям КСС.
А.2.45. Заключения
оформляются на один способ сварки с указанием области распространения
результатов аттестации с учетом заявленных условий. При сварке КСС
комбинированной технологией сварки (с применением нескольких способов сварки)
заключение оформляется на комбинацию способов сварки.
А.2.46.
Аттестационный центр направляет заключения в НАКС. На основании экспертизы
представленных документов НАКС оформляет свидетельство о готовности
организации-заявителя к использованию аттестованных технологий сварки.
А.2.47. Аттестационный
центр передает оформленное свидетельство организации-заявителю для получения у
Заказчика разрешения на начало производства сварочных работ с применением
технологий сварки, прошедших производственную аттестацию.
А.3. Форма акта производственной аттестации технологии сварки для
применения при строительстве магистрального газопровода (рекомендуемая)
___________________________________________________________________________
(указать
название магистрального газопровода или участка газопровода)
____________________________ 200_ г. _____________________________
(дата проведения аттестации) (место проведения аттестации)
1. Название,
адрес и тел. организации-
_____________________________
заявителя (подрядчика), аттестующей _____________________________
технологию сварки
_____________________________
2. Название,
адрес и тел. организации-
_____________________________
разработчика технологии сварки _____________________________
3. Название,
адрес и тел. аттестационного
_____________________________
центра
_____________________________
4. Состав
аттестационной комиссии
_____________________________
Председатель
_____________________________
Члены
комиссии _____________________________
_____________________________
_____________________________
_____________________________
5. Вид
аттестации
_____________________________
6. Перечень
нормативно-технической
_____________________________
документации, согласно которой проводится _____________________________
аттестация:
6.1.
Технологическая карта на аттестуемую
_____________________________
технологию
сварки (наименование и номер,
_____________________________
кем и когда
разработана и утверждена)
_____________________________
6.2. СНиП,
РД и др. документы по сварке
_____________________________
6.3. СНиП,
РД и др. документы
_____________________________
по контролю
качества
7. Название,
краткая характеристика
_____________________________
технологии сварки
_____________________________
8.
Наименование конструктивного элемента (соединения) газопровода
___________________________________________________________________________
9.
Характеристика свариваемых труб (СДТ, ЗРА)
Свариваемый
элемент
(труба, деталь,
арматура)
|
Диаметр,
мм
|
Толщина
стенки,
мм
|
Марка стали
и класс
прочности
|
Номер
ТУ, ГОСТ
|
Эквивалент
углерода, %
|
|
|
|
|
|
|
|
|
|
|
|
|
10. Форма и
параметры разделки кромок
┌───────────────────────────┐
(угол скоса кромок, притупление, │ │
зазор и т.д.) - в виде эскиза │ │
└───────────────────────────┘
11. Тип
(марка) центратора
_____________________________
(сборочного приспособления)
_____________________________
12. Тип
(марка) сварочных
_____________________________
материалов (в т.ч. защитного газа) _____________________________
13. Тип
(марка) сварочного _____________________________
и вспомогательного оборудования _____________________________
14.
Температура предварительного
_____________________________
подогрева
_____________________________
15.
Количество и размеры прихваток
_____________________________
16. Схема
сварки шва (число слоев,
┌───────────────────────────┐
последовательность их выполнения) - │ │
в виде эскиза │ │
│
│
│ │
└───────────────────────────┘
17. Состав
бригады сварщиков, участвующих в аттестации технологии сварки
N
п/п
|
Ф.И.О. сварщика
(оператора)
|
Клеймо
сварщика
|
Содержание работы,
выполняемой в бригаде
|
|
|
|
|
|
|
|
|
|
|
|
|
|
|
|
|
|
|
|
|
|
|
|
|
|
|
|
|
18. Положение
при сварке _________________________________________________
_________________________________________________
19. Схема
расстановки сварщиков
при выполнении неповоротного стыка -
в виде эскиза
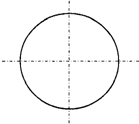
20.
Количество и номера
_____________________________
сваренных стыков (КСС)
_____________________________
21.
Фактические параметры режима сварки, зарегистрированные при сварке КСС
(в виде отдельной
таблицы, наименование параметров
- в соответствии с
технологической картой)
22. Интервал
времени между выполнением
_____________________________
отдельных слоев шва (если регламентируется _____________________________
в технологической карте)
23.
Межслойная
температура

24.
Геометрические параметры шва
Ширина шва = ___ мм;
(в т.ч. подварочного или внутреннего) Высота усиления = ____ мм
25. Режим
термообработки
_____________________________
(при наличии требований)
_____________________________
26. Другие
данные, в том числе погодные
_____________________________
условия при проведении аттестации технологии _____________________________
27.
Результаты аттестации:
Аттестация
технологии сварки проведена в
соответствии с вышеупомянутой
нормативной документацией, технология сварки
рекомендуется к применению при
строительстве магистрального газопровода (участка
газопровода)
___________________________________________________________________________
(наименование магистрального газопровода или участка газопровода)
___________________________________________________________________________
(название
организации)
Приложения:
1. Технологическая карта сварки.
2. Протоколы механических испытаний сварного
соединения.
3.
Заключение по неразрушающему контролю сварных соединений физическими
методами.
4. Протокол визуального и измерительного контроля
сварных швов.
5. Протокол
оценки геометрических параметров
шва по макрошлифам
(для двухсторонней автоматической сварки под
флюсом).
6.
Результаты других видов
контроля, если они предусмотрены нормативной
документацией.
Ф.И.О. и подписи членов комиссии
Председатель ____________________________________
Члены комиссии
____________________________________
Приложение
Б
(обязательное)
ВИДЫ
МЕХАНИЧЕСКИХ ИСПЫТАНИЙ СВАРНЫХ СОЕДИНЕНИЙ
ПРИ
ПРОИЗВОДСТВЕННОЙ АТТЕСТАЦИИ ТЕХНОЛОГИЙ СВАРКИ
Б.1. Испытания на
статическое растяжение
Б.1.1. Испытания
следует проводить на образцах типа XII или XIII (ГОСТ 6996). Размеры образца
указаны в таблице Б.1. Форма образца представлена на рисунке Б.1.
Таблица Б.1
Плоские образцы для
испытаний на статическое растяжение
┌──────────────────────┬──────────┬──────────┬────────────┬───────┬───────┐
│
Толщина стенки трубы │ Толщина
│ Ширина │
Ширина │ Длина │
Общая │
│ (элемента), мм │ образца │ рабочей │ захватной │рабочей│ длина │
│ │ (a), мм │
части │ части
│ части │образца│
│ │ │ образца │
образца
│образца│(L), мм│
│ │ │ (b), мм │
(b ), мм │(l),
мм│ │
│ │ │ │ 1
│ │ │
├──────────────────────┼──────────┼──────────┼────────────┼───────┼───────┤
│До
6,0 включ. │ Равна
│15 +/- 0,5│
25 │ 50
│l + 2h │
├──────────────────────┤
толщине
├──────────┼────────────┼───────┤ │
│Св.
6,0 до 10,0 включ.│ стенки │20 +/- 0,5│ 30
│ 60 │
│
├──────────────────────┤ трубы
├──────────┼────────────┼───────┤ │
│" 10,0
" 25,0 " │(элемента)│25 +/- 0,5│ 35
│ 100 │
│
├──────────────────────┴──────────┴──────────┴────────────┴───────┴───────┤
│ Примечания. 1. Длину захватной части
образца (h) устанавливают
в│
│зависимости
от конструкции испытательной машины. │
│ 2. Скорость нагружения
образцов в процессе
испытаний должна│
│составлять
не более 15 мм/мин.
│
└─────────────────────────────────────────────────────────────────────────┘
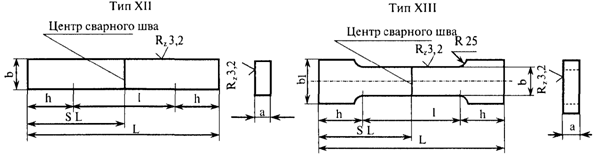
Рисунок
Б.1. Форма и размеры образцов (тип XII и XIII)
для испытаний
сварного соединения на статическое растяжение
Б.1.2. Усиление шва
на образцах должно быть снято механическим способом до уровня основного
металла, при этом допускается удалять основной металл по всей поверхности
образца на глубину до 15% от толщины стенки трубы, но не более 4,0 мм. Удаление
основного металла с поверхности образца производят только с той стороны, с
которой снимают усиление шва. Строгать усиление следует поперек шва. Острые
кромки плоских образцов в пределах рабочей части должны быть закруглены
радиусом не более 1,0 мм путем сглаживания напильником вдоль кромки.
Разрешается строгать усиление вдоль продольной оси шва с последующим удалением
рисок. Шероховатость поверхности
в местах удаления усиления должна быть не
более 6,3 мкм.
Б.1.3. Временное
сопротивление разрыву, определяемое на плоских образцах со снятым усилением,
должно быть не ниже нормативного значения временного сопротивления разрыву
основного металла труб (по ТУ на трубы).
Б.2. Испытание
сварных соединений труб диаметром до 89 мм включ. на статическое растяжение и
сплющивание
Б.2. Для оценки
механических свойств аттестационных соединений диаметром до 89 мм включ. должны
быть изготовлены три полноразмерных трубчатых образца для испытаний на
растяжение и три трубчатых образца для испытаний на сплющивание. Форма и размеры
образцов для испытаний на растяжение представлены на рисунке Б.2. Размеры
образца и схема испытаний на сплющивание представлены на рисунке Б.3. Скорость
нагружения при испытаниях на растяжение и сплющивание не должна превышать 15
мм/мин. Перед выбором типоразмера труб для аттестации следует произвести расчет
площади поперечного сечения трубы и возможного усилия разрыва.
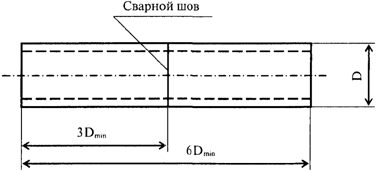
D - диаметр трубы
Рисунок Б.2. Эскиз
трубчатого образца
(тип XVIII по ГОСТ
6996) для испытаний на растяжение
сварных соединений
труб диаметром до 89 мм включ.
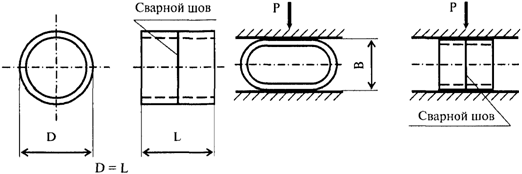
D - диаметр трубы;
L - длина образца;
P - направление
приложения сжимающей нагрузки;
B - величина
просвета между сжимающими плитами
Рисунок
Б.3. Эскиз трубчатого образца для испытаний
на сплющивание и
схема испытаний
Б.2.2. Перед
испытанием трубчатых образцов на растяжение следует удалить усиление сварного
шва. В формулу расчета временного сопротивления разрыву должна быть введена
площадь сечения трубы вне сварного шва. Концы трубчатого образца перед
испытанием могут быть сплющены, если этого требует конструкция разрывной
машины. Расстояние от оси шва до начала сплющиваемого участка должно быть в
данном случае не менее двух диаметров (2D) трубы. Временное сопротивление
разрыву при растяжении трубчатых образцов должно быть не ниже нормативного
значения временного сопротивления разрыву основного металла труб (по ТУ на
трубы).
Б.2.3. Перед
испытанием трубчатых образцов на сплющивание следует удалить усиление сварного
шва заподлицо с основным металлом. При испытании образцов сварной шов
располагают по оси сжимающей нагрузки. Результаты испытания образцов на
сплющивание характеризуются величиной просвета B между сжимающими плитами до
появления первой трещины на поверхности образца (рисунок Б.3). Допустимая
величина просвета B для труб диаметром до 48 мм включ. равна 3S, для труб
диаметром св. 48 до 89 мм - 4S (S - толщина стенки трубы, мм). Появление
надрывов длиной до 5,0 мм на кромках и на поверхности образца, не развивающихся
в трещину в процессе дальнейших испытаний до полного сплющивания образца,
браковочным признаком не является.
Б.2.4. Результаты
испытаний трубчатых образцов на растяжение и сплющивание оценивают, как среднее
арифметическое значение, рассчитанное для трех образцов. Допускается снижение
результатов испытаний для одного образца на 10% ниже нормативного значения,
если средний арифметический результат отвечает нормативным требованиям.
Б.3. Испытания на
статический изгиб
Б.3.1. Форма и
размеры образцов представлены в таблицах Б.2; Б.3 и на рисунке Б.4.
Таблица Б.2
Размеры образцов
для испытаний на статический изгиб
Вид изгиба
|
Толщина
основного
металла (S), мм
|
Ширина
образца (b),
мм
|
Общая
длина
образца
(l), мм
|
Расстояние
между
опорами, мм
|
Корнем
шва наружу
или внутрь
|
до 12,0 включ.
|
1,5S,
но не
менее 10
|
2,5D + 80
|
2,5D
|
Боковой
поверхностью
(на ребро)
|
более 12,0
|
12,5
+/- 0,2
|
180 - 200
|
80
|
Примечание. D -
диаметр нагружающей оправки,
определяемый по
таблице Б.3 настоящего приложения.
|
Таблица Б.3
Определение
диаметра нагружающей оправки (B)
для испытаний на
статический изгиб
Класс прочности трубной стали
|
Толщина
основного
металла, мм
|
Диаметр
нагружающей
оправки, мм
|
До К50 включ.
|
до 12,0 мм
включ.
|
2S +/- 2
|
более 12,0
|
30 +/- 2
|
Св. К50 до К54 включ.
|
до 12,0 мм
включ.
|
3S +/- 2
|
более 12,0
|
40 +/- 2
|
Св. К55 до К60 включ.
|
до 12,0 мм
включ.
|
4S +/- 2
|
более 12,0
|
50 +/- 2
|
Примечание. S - диаметр нагружающей
оправки, мм.
|
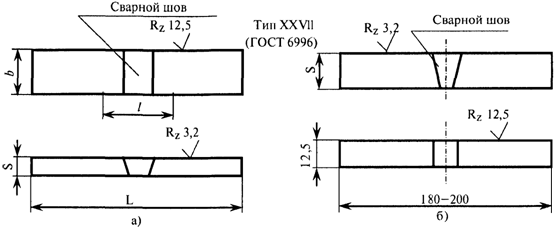
а) образец для
изгиба корнем шва наружу или внутрь;
б) образец для
изгиба на ребро
Рисунок
Б.4. Форма и размеры образцов
для испытаний на
статический изгиб
Б.3. Толщина
образцов должна равняться толщине основного металла. Усиление шва по обеим
сторонам образца снимается механическим способом до уровня основного металла.
Разрешается строгать усиление шва в любом направлении с последующим удалением
рисок. Кромки образцов в пределах их рабочей части должны быть закруглены
радиусом не менее 0,1 толщины образца (но не более 2,0 мм) путем сглаживания
напильником вдоль кромки.
Б.3.3. Обязательным
условием проведения испытаний является плавность возрастания нагрузки на
образец. Испытания проводят со скоростью не более 15 мм/мин, до достижения
нормируемого угла изгиба или угла изгиба, при котором образуется первая
трещина, являющаяся признаком брака. Угол изгиба при испытании до образования
первой трещины замеряют в ненапряженном состоянии с погрешностью +/- 2°.
Б.3.4. Среднее
арифметическое значение угла изгиба образцов должно быть не менее 120°, а
минимальное значение угла изгиба одного образца должно быть не ниже 100°. При
подсчете среднего арифметического значения угла изгиба все углы более 150°
следует принимать равными 150°.
Б.3.5. Если длина
трещин, возникающих в растянутой зоне образца в процессе испытания, не
превышает 20% от его ширины (но не более 5 мм), то такие трещины не являются
признаком брака. Определяется также место образования трещины или разрушения
(металл шва, металл околошовной зоны или основной металл).
Б.4. Механические
испытания на излом угловых сварных соединений прямых врезок
Б.4.1. Образцы для
испытаний углового соединения должны иметь ширину 50 мм (приблизительно) и
длину от 100 до 150 мм (рисунок Б.5). Надрез по оси сварного шва выполняют
ножовкой на глубину 1,5 мм.
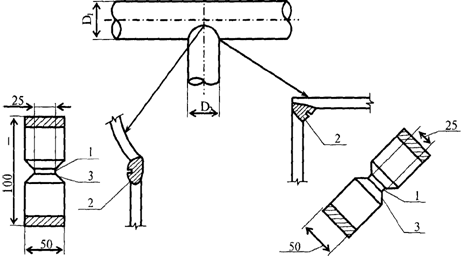
1 - надрез ножовкой
по оси шва глубиной 1,5 мм;
2 - сварной шов; 3
- обработка сварного шва газовой резкой
Рисунок Б.5. Форма
и размеры образцов
для испытания
металла шва угловых соединений
прямых врезок на
излом
Б.4.2. Образцы для
испытания нахлесточного соединения должны иметь ширину 25 мм (приблизительно) и
длину от 100 до 150 мм (рисунок Б.6). Надрез выполняется ножовкой со стороны,
противоположной усилению сварного шва. Глубина надреза равна толщине стенки
трубы плюс половина высоты поперечного сечения сварного шва. Допускается
применение шлифмашинки (с узким шлифкругом) для выполнения части наклонного
надреза (пропила) на глубину, равную толщине стенки трубы. Заключительную часть
надреза следует выполнять ножовкой.
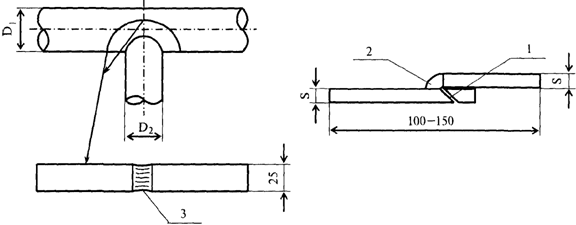
1 - надрез глубиной
S + половина высоты поперечного
сечения сварного
шва (S - толщина стенки трубы);
2 - сварной шов; 3
- обработка сварного шва
газовой резкой
Рисунок Б.6. Форма
и размеры образцов для испытания металла
шва нахлесточных
соединений прямых врезок на излом
Б.4.3. Образцы для
испытания на излом должны иметь параллельные гладкие кромки. Следы окалины
после газовой резки должны быть удалены путем механической обработки или
зачистки шлифмашинкой.
Б.4.4. При испытаниях
металла шва на излом образцы разрушают ударом по свободному участку образца при
закрепленном другом участке. Удар наносится со стороны корневого слоя шва.
Поверхность излома каждого образца должна продемонстрировать полный провар и
сплавление между слоями шва. Максимальный размер любой газовой поры не должен
превышать 2,0 мм, а суммарная площадь всех газовых пор не должна быть более 2%
площади излома образца. Глубина шлаковых включений - не более 1,0 мм, а их
длина - не более 3,5 мм. Расстояние между соседними шлаковыми включениями
должно быть не менее 13 мм. Любые трещины являются браковочным признаком. Не
являются браковочным признаком дефекты типа флокенов.
Б.5. Испытания на
ударный изгиб
Б.5.1. При
испытании на ударный изгиб определяют энергию удара и ударную вязкость металла
шва на образцах с острым надрезом (Шарпи) типа IX (для толщины основного
металла 11 мм и более) по ГОСТ 6996. Форма и размеры образцов представлены на
рисунке Б.7. Схема нанесения надреза на образцах приведена на рисунке Б.8.
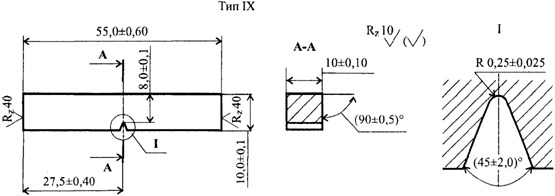
Рисунок Б.7. Форма
и размеры образцов для испытаний
на ударный изгиб по
ГОСТ 6996

а)
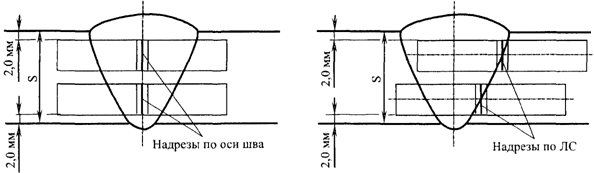
б)
а) для труб с
толщиной стенки (S) до 19,0 мм включ.;
б) для труб с
толщиной стенки (S) более 19,0 мм
Рисунок
Б.8. Схема вырезки и выполнения надреза
на образцах для
испытаний на ударный изгиб
Б.5.2. Вырезку и
изготовление образцов следует производить таким образом, чтобы одна из чистовых
поверхностей каждого образца (после окончательной обработки) располагалась на
расстоянии от 2,0 до 3,0 мм внутренней поверхности трубы. При вырезке образцов
из соединений с толщиной основного металла 11,0 мм и 6,0 мм допускается наличие
необработанного основного металла на двух поверхностях образца. Надрез наносят
перпендикулярно поверхности трубы (см. схему на рисунке Б.8). При испытании ЗТВ
линия надреза должна пересекать линию сплавления сварного шва в середине
образца.
Б.5.3. При
номинальной толщине стенки трубы более 19,0 мм для испытаний на ударный изгиб
следует изготовить дополнительно два комплекта образцов (по шву и по линии
сплавления), одна из чистовых поверхностей которых расположена на расстоянии от
2,0 до 3,0 мм от наружной поверхности трубы. Каждый комплект должен включать в
себя не менее 3-х образцов.
Б.5.4. Ударная
вязкость, определяемая как среднее арифметическое результатов испытаний трех
образцов, должна быть не менее значений, указанных в разделе 9.
Б.6. Измерение
твердости металла различных участков сварных соединений
Б.6.1. Измерение
твердости по Виккерсу
производится на образцах (макрошлифах),
вырезанных таким образом, чтобы были охвачены все участки сварного соединения
(шов, ЗТВ, основной металл). Должна быть обеспечена параллельность сечений
шлифа и обработка поверхности в местах замеров с шероховатостью не более Rz 80.
Схема замера твердости приведена на рисунке Б.9. В каждой зоне замера должно
быть не менее трех отпечатков (для ЗТВ и основного металла - с двух сторон от
оси шва).
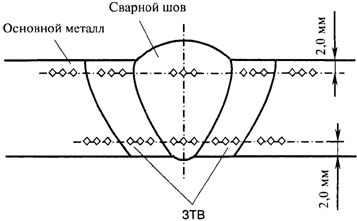
Рисунок Б.9. Схема
замера твердости по Виккерсу

в различных зонах
сварного соединения
Б.6.2. Значения
твердости по Виккерсу
не должны превышать максимальных значений,
регламентированных разделом 9.
Б.7. Испытания на
прочность при сдвиге
Б.7.1. Испытания на
прочность при сдвиге наплавки вывода ЭХЗ, выполненной термитной сваркой,
выполняются на разрывной машине любой стандартной марки, обеспечивающей
необходимое усилие сдвига. Схема испытаний приведена на рисунке Б.10.
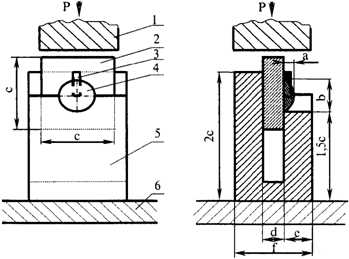
1 - подвижная часть
разрывной машины;
2 - плоский образец
с наплавкой; 3 - вывод ЭХЗ;
4 - наплавка; 5 -
приспособление (оправка) для испытания
на прочность при
сдвиге; 6 - неподвижная часть разрывной
машины; a - высота
наплавки; b - диаметр наплавки;
c - размеры
плоского образца (не менее 3-х диаметров
наплавки), d -
толщина плоского образца (ширина паза
оправки); e -
толщина стенки оправки (не менее 2-х толщин
плоского образца);
f - ширина оправки
Рисунок Б.10. Схема
испытаний на прочность при сдвиге
наплавки вывода
ЭХЗ, выполненной термитной сваркой
Б.7.2. Испытания
проводятся со скоростью нагружения 2,0 мм/мин.
Б.7.3. Значение
прочности при сдвиге, а также отношение площади сплавления к площади наплавки
должны отвечать требованиям 10.9.1.6.
Б.7.4. Рекомендуемая
форма протокола испытаний на прочность при сдвиге приведена ниже.
ПРОТОКОЛ
N __________ от "___" ___________ 200_ г.
испытаний на прочность при сдвиге
1. Характеристики контрольного сварного соединения:
- характеристики стальной пластины (класс прочности
трубной стали, толщина
стенки)
__________________________________________________________________.
- марка сварочного материала приварки выводов ЭХЗ
________________________.
2. Оборудование и условия испытаний:
___________________________________________________________________________
___________________________________________________________________________
3. Результаты испытаний:
┌───┬─────┬───────┬────────┬───────┬─────────┬───────────┬────────────────┐
│
N │N │ N
│Площадь │Темпе- │ Предел │
Площадь │S │
│п/п│пар-
│образца│наплавки│ратура
│прочности│сплавления,│ сплав │
│ │тии
│ КСС │ S
, │испыта-│на сдвиг │
S , │
x 100, % │
│ │
│ │ напл
│ний │ сигма, │
сплав │S │
│ │
│ │ мм2
│ │ МПа
│ мм2 │ напл │
├───┼─────┼───────┼────────┼───────┼─────────┼───────────┼────────────────┤
│
1 │ 2 │
3 │ 4
│ 5 │
6 │ 7
│ 8 │
├───┼─────┼───────┼────────┼───────┼─────────┼───────────┼────────────────┤
│ │
│ │ │ │ │ │ │
└───┴─────┴───────┴────────┴───────┴─────────┴───────────┴────────────────┘
4. Выводы:
Испытания провел:
________________
_________________________
Результаты
испытаний проверил: ________________ _________________________
Приложение
В
(обязательное)
ОБЛАСТЬ
РАСПРОСТРАНЕНИЯ РЕЗУЛЬТАТОВ
ПРОИЗВОДСТВЕННОЙ
АТТЕСТАЦИИ ТЕХНОЛОГИЙ СВАРКИ
В.1. Область
распространения результатов производственной аттестации технологий сварки
регламентирует диапазон допустимых изменений основных параметров однотипности
сварных соединений в рамках заявленных условий на производственную аттестацию
по характеристикам выполненных КСС.
В.2. Установленная
по результатам производственной аттестации область распространения не должна
выходить за пределы, регламентированные настоящим стандартом и за пределы
технологических возможностей специализированного сварочного оборудования (для
ААДП, АПГ, АФ), при этом область распространения результатов производственной
аттестации может быть сокращена по сравнению с диапазоном основных параметров однотипности
сварных соединений.
В.3. Область
распространения результатов аттестации технологий сварки по классам прочности
материалов труб (элементов) устанавливается в пределах одной группы по классу
прочности материалов труб (элементов) КСС в соответствии с требованиями таблицы
В.1.
Таблица В.1
Область
распространения результатов
производственной
аттестации технологий сварки
по классам
прочности материалов труб (элементов) КСС
Группы и сочетания групп
основного материала КСС
|
Область распространения
|
1
|
М01
|
1 (М01)
|
2
|
М03
|
2 (М03); 2 (М03) + 1 (М01)
|
3
|
М03
|
3
(М03); 3 (М03) + 2 (М03); 3 (М03) + 1 (М01)
|
1 (М01) + 2 (М03)
|
1 (М01) + 2 (М03)
|
1 (М01) + 3 (М03)
|
1 (М01) + 3 (М03)
|
2 (М03) + 3 (М03)
|
2 (М03) + 3 (М03)
|
В.4. Область
распространения результатов производственной аттестации технологий сварки по
номинальным толщинам труб (элементов) стыковых соединений для элементов одной
толщины устанавливается в пределах одной группы по номинальным толщинам труб
(элементов) КСС в соответствии с требованиями таблицы В.2.
Таблица В.2
Область
распространения результатов
производственной
аттестации технологий сварки
по номинальным
толщинам труб (элементов) КСС
для элементов одной
толщины
┌──────────────────────────────────────┬──────────────────────────────────┐
│ Диапазон номинальных толщин стенки │
Область распространения
│
│ труб (элементов) КСС, мм │ по группам толщин │
├──────────────────────────────────────┼──────────────────────────────────┤
│
До 5,0 включ.
│ 1 │
├──────────────────────────────────────┼──────────────────────────────────┤
│Св.
5,0 до 12,0 включ. │ 2 │
├──────────────────────────────────────┼──────────────────────────────────┤
│" 12,0
" 19,0 " │ 3 │
├──────────────────────────────────────┼──────────────────────────────────┤
│" 19,0
" 32,0 " │ 4 │
├──────────────────────────────────────┼──────────────────────────────────┤
│" 32,0
" 50,0 " │ 5 │
└──────────────────────────────────────┴──────────────────────────────────┘
В.5. Область
распространения результатов аттестации технологий сварки по номинальным
толщинам труб (элементов) для элементов разной толщины устанавливается в
пределах одной группы по номинальным толщинам труб (элементов) КСС в
соответствии с требованиями таблицы В.3.
Таблица В.3
Область
распространения результатов
производственной
аттестации технологий сварки
по номинальным
толщинам труб (элементов) КСС
для элементов
разной толщины
┌──────────────────────┬──────────────────────┬───────────────────────────┐
│
Диапазон номинальных │ Диапазон номинальных │ Область
распространения │
│
толщин тонкостенной │ толщин
толстостенной │ по группам разной толщины │
│
трубы (элемента) КСС │ трубы
(элемента) │ стенок труб (элементов) │
├──────────────────────┼──────────────────────┼───────────────────────────┤
│
До 5,0 включ. │До 7,5 включ. │ 1 │
├──────────────────────┼──────────────────────┼───────────────────────────┤
│Св.
5,0 до 12,0 включ.│Св. 7,5 до 18,0 включ.│ 2 │
├──────────────────────┼──────────────────────┼───────────────────────────┤
│" 12,0 "
19,0 " │" 15,0 "
28,5 " │ 3 │
├──────────────────────┼──────────────────────┼───────────────────────────┤
│" 19,0 "
32,0 " │" 22,0 "
48,0 " │ 4 │
├──────────────────────┼──────────────────────┼───────────────────────────┤
│" 32,0 "
50,0 " │" 35,0 "
75,0 " │ 5 │
├──────────────────────┴──────────────────────┴───────────────────────────┤
│ Примечание. Максимальные значения
диапазонов толщин установлены│
│исходя из
соотношения толщин стенок
(разнотолщинности)
свариваемых│
│элементов,
равного 1,5. Форма подготовки кромок разнотолщинных элементов│
│соответствует
Тр-16 - Тр-19.
│
└─────────────────────────────────────────────────────────────────────────┘
В.6. Область
распространения результатов производственной аттестации технологий сварки по
номинальным диаметрам труб (элементов) устанавливается в пределах одной группы
по номинальным диаметрам труб (элементов) КСС в соответствии с требованиями
таблицы В.4. Область распространения результатов производственной аттестации
технологии сварки прямых врезок устанавливается в зависимости от типоразмера
КСС с учетом группы основного материала, комбинации диаметров и толщин стенок
свариваемых элементов в соответствии с требованиями таблицы В.5.
Таблица В.4
Область
распространения результатов
производственной
аттестации технологий сварки
по номинальным
диаметрам труб (элементов) КСС
┌────────────────────────────────┬────────────────────────────────────────┐
│Диапазоны
номинальных диаметров │ Область
распространения по группам │
│ труб (элементов) КСС, мм │ диаметров │
├────────────────────────────────┼────────────────────────────────────────┤
│До 25 включ. │ 1 │
├────────────────────────────────┼────────────────────────────────────────┤
│Св.
25 до 159 включ. │ 2 │
├────────────────────────────────┼────────────────────────────────────────┤
│
" 159,0 " 530 " │ 3 │
├────────────────────────────────┼────────────────────────────────────────┤
│Св.
530 (включая плоские детали)│ 4 │
└────────────────────────────────┴────────────────────────────────────────┘
Таблица В.5
Область
распространения результатов аттестации технологий
сварки прямых
врезок в зависимости от типоразмеров КСС
(номинальных
диаметров, толщин стенок
и группы основного
материала)
Условное обозначение КСС
(согласно таблице А.7)
|
Область распространения
(согласно таблице А.7)
|
ОТ-1-1.1.3
|
ОТ-1-1.1.2
|
ОТ-1-1.1.3
|
ОТ-1-2.1.3
|
ОТ-1-2.1.2
|
ОТ-1-2.1.3
|
ОТ-1-2.2.3
|
ОТ-1-2.2.2
|
ОТ-1-2.2.3
|
ОТ-1-3.1.3
|
ОТ-1-3.1.2
|
ОТ-1-3.1.3
|
ОТ-1-3.2.3
|
ОТ-1-3.2.2
|
ОТ-1-3.2.3
|
ОТ-1-3.3.3
|
ОТ-1-3.3.2
|
ОТ-1-3.3.3
|
ОТ-2-1.1.3
|
ОТ-2-1.1.2
|
ОТ-2-1.1.3
|
ОТ-2-2.1.3
|
ОТ-2-2.1.2
|
ОТ-2-2.1.3
|
ОТ-2-2.2.3
|
ОТ-2-2.2.2
|
ОТ-2-2.2.3
|
ОТ-2-3.1.3
|
ОТ-2-3.1.2
|
ОТ-2-3.1.3
|
ОТ-2-3.2.3
|
ОТ-2-3.2.2
|
ОТ-2-3.2.3
|
ОТ-2-3.3.3
|
ОТ-2-3.3.2
|
ОТ-2-3.3.3
|
В.7. Область
распространения результатов производственной аттестации технологий сварки по
виду КСС и конструктивным элементам устанавливается в соответствии с
требованиями таблицы В.6.
Таблица В.6
Область
распространения результатов
производственной
аттестации технологий сварки
по виду КСС и
конструктивным элементам
┌─────────┬─────────────────────────────────────────────┬─────────────────┐
│N
группы │ Номер и вид
КСС │ Область
│
│конструк-│
│ распространения │
│тивных │
│по конструктивным│
│элементов│
│ элементам │
├─────────┼─────────────────────────────────────────────┼─────────────────┤
│ 1
│Стыковое сварное соединение труб одной │ 1 (1.1),
│
│ │толщины стенки без подварки
изнутри │5 (5.1; 5.3)
<1>,│
│ │("труба +
труба") │ 4 (4.1) <2> │
├─────────┼─────────────────────────────────────────────┼─────────────────┤
│ 2
│Стыковое сварное соединение труб одной │ 2 (2.1),
│
│ │толщины стенки с подваркой
изнутри │5 (5.1; 5.3)
<3> │
│ │(для РД, односторонней сварки
под флюсом │ │
│ │и механизированных способов,
включая │ │
│ │комбинированные способы
сварки) │ │
│ │("труба + труба") │ │
│
├─────────────────────────────────────────────┼─────────────────┤
│ │Стыковое сварное соединение
труб одной │ 2 (2.2)
│
│ │толщины стенки (для
двухсторонней │ │
│ │автоматической сварки)
("труба + труба")
│ │
├─────────┼─────────────────────────────────────────────┼─────────────────┤
│ 3
│Стыковое сварное соединение труб разной │3 (3.1), 2 (2.1),│
│ │толщины стенки с подваркой
изнутри │5 (5.1; 5.3)
<4> │
│ │(для ручной дуговой и
механизированной │ │
│ │сварки, включая комбинированные
технологии │ │
│ │сварки) ("труба + труба") │ │
│
├─────────────────────────────────────────────┼─────────────────┤
│ │Стыковое сварное соединение
труб разной │3 (3.2), 2 (2.2)
│
│ │толщины стенки (для
двухсторонней │ │
│ │автоматической сварки)
("труба + труба")
│ │
├─────────┼─────────────────────────────────────────────┼─────────────────┤
│ 4
│Стыковое сварное соединение труб разной │4 (4.1), 1 (1.1) │
│ │толщины стенки без подварки
изнутри │ <5> │
│ │("труба +
труба")
│ │
├─────────┼─────────────────────────────────────────────┼─────────────────┤
│ 5
│Стыковое сварное соединение "труба + СДТ" │
5 (5.1) │
│
├─────────────────────────────────────────────┼─────────────────┤
│ │Стыковое сварное
соединение │ 5 (5.1),
│
│ │"труба + катушка-имитатор
СДТ" │ 1 (1.1) <6>, │
│ │
│ 2 (2.1) <7>, │
│ │
│ 3 (3.1) <8>, │
│ │
│ 4 (4.1) <9> │
│
├─────────────────────────────────────────────┼─────────────────┤
│ │Стыковое сварное соединение
"труба + ЗРА" │ 5 (5.3)
│
│
├─────────────────────────────────────────────┼─────────────────┤
│ │Стыковое сварное
соединение │ 5 (5.1),
│
│ │"труба + катушка-имитатор
ЗРА" │ 1 (1.1)
<10>, │
│ │
│ 2 (2.1) <11>,
│
│ │
│ 3 (3.1) <12>,
│
│ │
│ 4 (4.1) <13> │
├─────────┼─────────────────────────────────────────────┼─────────────────┤
│ 6
│Стыковое сварное соединение труб одной │ 6 (6.1),
│
│ │толщины стенки без подварки
изнутри │ 1 (1.1) <14> │
│ │(захлест, прямая вставка
(катушка)) │ │
├─────────┼─────────────────────────────────────────────┼─────────────────┤
│ 7
│Угловое сварное соединение │
7 (7.1) │
│ │"патрубок + основная
труба" │ │
│
├─────────────────────────────────────────────┼─────────────────┤
│ │Угловое сварное соединение │ 7 (7.2)
│
│ │"патрубок + накладка" │ │
│
├─────────────────────────────────────────────┼─────────────────┤
│ │Нахлесточное сварное
соединение │ 7 (7.3)
│
│ │"накладка + основная труба" │ │
├─────────┼─────────────────────────────────────────────┼─────────────────┤
│ 8
│Угловое сварное соединение │ 8 (8.1)
│
│ │"патрубок + основная
труба" │ │
├─────────┴─────────────────────────────────────────────┴─────────────────┤
│
<1> Область распространения действительна при следующих
условиях: │
│ - соединение N 5.1 является соединением
трубы и
СДТ с одинаковыми│
│толщинами
стенок;
│
│ - соединение N 5.3 является соединением
трубы и
переходного кольца│
│ЗРА
с одинаковыми толщинами стенок; │
│ - соединения N 5.1 и N 5.3 выполняются без
подварки изнутри; │
│ - совпадают другие
основные параметры однотипности
соединений│
│N
1.1; N 5.1 и N 5.3.
│
│
<2> Область распространения действительна при условии, что
соединение│
│N
4.1 является соединением
труб из сталей
одной группы по
классу│
│прочности.
│
│
<3> Область распространения действительна при следующих
условиях: │
│ - диаметр свариваемых элементов более 1020
мм либо менее 1020 мм
с│
│учетом
требований 10.2.40;
│
│ - соединение N 5.1 является соединением
трубы и
СДТ с одинаковыми│
│толщинами
стенок;
│
│ - соединение N 5.3 является соединением
трубы и
переходного кольца│
│ЗРА
с одинаковыми толщинами стенок; │
│ - операционно-технологические карты сборки
и сварки соединений N 5.1│
│и
N 5.3 регламентируют выполнение подварки изнутри; │
│ - совпадают другие основные параметры
однотипности соединений N 2.1;│
│N
5.1 и N 5.3.
│
│
<4> Область распространения действительна при следующих
условиях: │
│ - соединение N 5.1 является соединением
переходного кольца (патрубка)│
│и
СДТ разной толщины стенки с одинаковыми наружными диаметрами (Тр-16 по│
│таблице
А.8);
│
│ - соединение N 5.3 является соединением
переходного кольца и корпуса│
│ЗРА
разной толщины стенки;
│
│ - операционно-технологические карты сборки
и сварки соединений N 5.1│
│и
N 5.3 регламентируют выполнение подварки изнутри; │
│ - совпадают другие основные параметры
однотипности соединений N 3.1;│
│N
5.1 и N 5.3. │
│
<5> Область
распространения
действительна для сварных
соединений│
│диаметром
менее 1020 мм.
│
│
<6> Область распространения действительна при следующих
условиях: │
│ - выполненные КСС имеют одинаковые диаметры
и толщины стенок; │
│ - сварка КСС выполнена без подварки
изнутри; │
│ - совпадают другие основные параметры
однотипности соединений N 5.2 и│
│N
1.1. │
│
<7> Область распространения действительна при следующих
условиях: │
│ - диаметр свариваемых элементов более 1020
мм либо менее 1020 мм
с│
│учетом
требований 10.2.40;
│
│ - выполненные КСС имеют одинаковые диаметры
и толщины стенок; │
│ - сварка
КСС выполнена с
подваркой изнутри по
всему периметру│
│корневого
слоя шва;
│
│ - совпадают другие основные параметры
однотипности соединений N 5.2 и│
│N
2.1.
│
│
<8> Область распространения действительна при следующих условиях: │
│ - диаметр свариваемых элементов более 1020
мм либо менее 1020 мм
с│
│учетом
требований 10.2.40;
│
│ - выполненные КСС имеют разные толщины
стенок и одинаковые наружные│
│диаметры
(Тр-16 по таблице А.8);
│
│ - сварка
КСС выполнена с
подваркой изнутри по
всему периметру│
│корневого
слоя шва;
│
│ - совпадают другие основные параметры однотипности
соединений N 5.2 и│
│N
3.1.
│
│
<9> Область распространения действительна при следующих
условиях: │
│ - диаметр кольцевых стыковых соединений
менее 1020 мм; │
│ - выполненные КСС имеют разные толщины
стенок и одинаковые наружные│
│диаметры
(Тр-16 по таблице А.8);
│
│ - сварка КСС выполнена без подварки
изнутри; │
│ - совпадают другие основные параметры
однотипности соединений N 5.2 и│
│N
4.1.
│
│
<10> Область распространения действительна при следующих
условиях: │
│ - выполненные КСС имеют одинаковые диаметры
и толщины стенок; │
│ - сварка КСС выполнена без подварки
изнутри; │
│ - совпадают другие основные параметры
однотипности соединений N 5.4 и│
│N
1.1.
│
│
<11> Область распространения действительна при следующих
условиях: │
│ - диаметр свариваемых элементов более 1020
мм либо менее 1020 мм
с│
│учетом
требований 10.2.40; │
│ - выполненные КСС имеют одинаковые диаметры
и толщины стенок; │
│ - сварка
КСС выполнена с
подваркой изнутри по
всему периметру│
│корневого
слоя;
│
│ - совпадают другие основные параметры
однотипности соединений N 5.4 и│
│N
2.1.
│
│
<12> Область распространения действительна при следующих
условиях: │
│ - диаметр свариваемых элементов более 1020
мм либо менее 1020 мм
с│
│учетом
требований 10.2.40;
│
│ - выполненные КСС имеют разные толщины
стенок и одинаковые наружные│
│диаметры
(Тр-16 по таблице А.8); │
│ - сварка
КСС выполнена с
подваркой изнутри по
всему периметру│
│корневого
слоя;
│
│ - совпадают другие основные параметры
однотипности соединений N 5.4 и│
│N
3.1. │
│
<13> Область распространения действительна при следующих
условиях: │
│ - диаметр кольцевых стыковых соединений
менее 1020 мм; │
│ - выполненные КСС имеют разные толщины
стенок и одинаковые наружные│
│диаметры
(Тр-16 по таблице А.8);
│
│ - КСС производилась без подварки
изнутри;
│
│ - совпадают другие основные параметры
однотипности соединений N 5.4 и│
│N
4.1.
│
│
<14> Область
распространения
действительна при условии,
что│
│операционно-технологическая карта
сборки и сварки
соединения N 1.1│
│не
предусматривает подварки изнутри
на отдельных участках
периметра│
│корневого
слоя шва.
│
└─────────────────────────────────────────────────────────────────────────┘
В.8. Результаты
производственной аттестации технологий сварки распространяются на сварочные
материалы, применяемые при сварке КСС, а также на другие сварочные материалы,
прошедшие аттестацию и рекомендованные к применению настоящим стандартом.
В.9. Область
распространения результатов производственной аттестации технологий сварки по
составу защитного газа устанавливается в соответствии с требованиями таблицы
В.7.
Таблица В.7
Область
распространения результатов
производственной
аттестации технологий сварки
составу защитного
газа
Состав
защитного газа при сварке КСС
|
Область распространения
по составу защитных газов
|
100% углекислый газ
|
100% углекислый газ
|
50% аргон + 50% углекислый газ
|
50% аргон + 50% углекислый газ
|
От 40% до 60% аргон,
остальное - углекислый газ
|
от 40% до 60% аргон,
остальное - углекислый газ
|
75% аргон + 25% углекислый газ
|
75% аргон + 25% углекислый газ;
80% аргон + 20% углекислый газ
|
80% аргон + 20% углекислый газ
|
80% аргон + 20% углекислый газ;
85% аргон + 15% углекислый газ
|
85% аргон + 15% углекислый газ
|
85% аргон + 15% углекислый газ
|
100% аргон
|
100% аргон
|
В.10. Область
распространения результатов производственной аттестации технологий сварки в
зависимости от пространственного положения при сварке устанавливается в
соответствии с требованиями таблицы В.8.
Таблица В.8
Область
распространения результатов
производственной
аттестации технологий сварки
в зависимости от
пространственного положения при сварке
Пространственное
положение сварки
КСС
|
Область распространения по
пространственному положению при сварке
|
Для стыковых соединений труб, труб с
СДТ и ЗРА
|
Н1
|
Н1
|
В1
|
В1
|
В2
|
В2
|
Г
|
Г
|
Н45
|
Н45; Г; В1 <*>
|
Н45; Г; В2 <**>
|
Для угловых соединений труб
(прямых врезок)
|
Н1
|
Н1
|
Н2
|
Н2
|
В1
|
В1; Н1; Н2; П2; Н45
|
П2
|
П2; Н1; Н2
|
Н45
|
Н45; Н1; Н2
|
<*> При сварке КСС на подъем.
<**> При сварке КСС на
спуск.
|
В.11. Область
распространения результатов производственной аттестации технологий сварки по
параметрам режимов сварки (сварочный ток, напряжение на дуге, скорость сварки,
скорость подачи проволоки и др.) устанавливается в рамках диапазонов
фактических значений параметров, зафиксированных в карте технологического
процесса сварки КСС. Эти параметры должны быть отражены в
операционно-технологических картах сборки и сварки, разрабатываемых по
результатам производственной аттестации технологий сварки. В случае
необходимости внесения изменений в параметры режимов сварки, выходящих за
пределы, установленные операционно-технологическими картами сборки и сварки,
требуется проведение новой производственной аттестации.
В.12. Область
распространения результатов производственной аттестации технологий сварки в
зависимости от формы разделки кромок свариваемых элементов устанавливается в
соответствии с требованиями таблицы В.9.
Таблица В.9
Область
распространения результатов
производственной
аттестации технологий сварки
в зависимости от
формы разделки кромок
свариваемых
элементов
Форма
разделки КСС (обозначение по табл. А.8)
|
Область распространения
|
Тр-1
|
Тр-1; Тр-2; Тр-3; Тр-4
|
Тр-2
|
Тр-1; Тр-2; Тр-3; Тр-4
|
Тр-3
|
Тр-1; Тр-2; Тр-3; Тр-4
|
Тр-4
|
Тр-1; Тр-2; Тр-3; Тр-4
|
Тр-5
|
Тр-5
|
Тр-6
|
Тр-6
|
Тр-7
|
Тр-7
|
Тр-8
|
Тр-8
|
Тр-9
|
Тр-9; Тр-10; Тр-11
|
Тр-10
|
Тр-9; Тр-10; Тр-11
|
Тр-11
|
Тр-9; Тр-10; Тр-11
|
Тр-12
|
Тр-12
|
Тр-13
|
Тр-13
|
Тр-14
|
Тр-14; Тр-15
|
Тр-15
|
Тр-14; Тр-15
|
Тр-16
|
Тр-16
|
Тр-17
|
Тр-17 <*>; Тр-19 <*>
|
Тр-18
|
Тр-18 <*>; Тр-20 <*>
|
Тр-19
|
Тр-19 <*>; Тр-17 <*>
|
Тр-20
|
Тр-20 <*>; Тр-18 <*>
|
Тр-21
|
Тр-21
|
Тр-22
|
Тр-22
|
Тр-23
|
Тр-23
|
<*> Геометрические параметры
разделки кромок (угол
скоса,
притупление) должны соответствовать
геометрическим параметрам разделки
кромок КСС.
|
В.13. В области
распространения результатов производственной аттестации технологий сварки,
использующих универсальное сварочное оборудование, следует указывать типы
сварочного оборудования согласно требованиям РД 03-614-03 [2].
В.14. В области
распространения результатов производственной аттестации технологий сварки,
использующих специализированное сварочное оборудование - специальные источники
сварочного тока (МП, МПС), сварочные комплексы (ААДП, АПГ, АПИ), трубосварочные
базы (АФ), следует указывать тип и марку оборудования. Допускается расширять
область распространения производственной аттестации на другие марки однотипного
оборудования при условии его аттестации согласно требованиям РД 03-614-03 [2] с
областью применения для сварки газопроводов.
В.15. В область
распространения результатов производственной аттестации технологий ремонта
сваркой дефектов сварных швов, следует включать вид ремонта, согласно А.1.23.
Результаты аттестации технологии ремонта сваркой вида 3) А.1.23 могут быть
распространены на технологию ремонта вида 2) А.1.23, а технологии ремонта
сваркой вида 4) А.1.23 - на технологию ремонта вида 5) А.1.23 при условии
использования одного способа сварки и сварочного материала.
В.16. По
результатам производственной аттестации технологий сварки в область
распространения следует включать следующие основные параметры:
- способ сварки;
- характер
выполняемых работ;
- конструктивный
элемент газопровода (номер группы по таблице А.2);
- группы основных
материалов по классу прочности;
- диаметр свариваемых
элементов;
- толщина
свариваемых элементов;
- сварочные
материалы (тип, марка), вид покрытия электродов (для РД), тип сварочного флюса
(для АФ), состав защитного газа (для МП, ААДП, АПГ, АПИ);
- тип сварочного
оборудования (марка - для МП, МПС, ААДП, АПГ, АПИ, АФ; число и вид плавящихся
электродов - для АФ, ААДП, АПГ; импульсно-дуговой процесс - для МП, ААДП);
- тип соединения,
тип шва, вид соединения;
- геометрические
параметры разделки кромок свариваемых элементов (обозначение по таблице А.8);
- положение при
сварке;
- предварительный и
сопутствующий подогрев;
- тип центратора
(центрирующего приспособления);
- термообработка;
- вид ремонта (по
п. А.1.23);
- перечень
нормативных документов, по которым проводилась производственная аттестация
технологий сварки, в т.ч. настоящий стандарт;
- шифры
операционно-технологических карт сборки и сварки, разработанных по
аттестованным технологиям сварки.
Приложение
Г
(рекомендательное)
ФОРМЫ
ИСПОЛНИТЕЛЬНОЙ ДОКУМЕНТАЦИИ
Г.1. Форма
допускного листа сварщика <*>
--------------------------------
<*> Взамен
формы N 3.2 ВСН 012-88 [35].
УТВЕРЖДАЮ:
___________________________
___________________________
___________________________
(подпись)
"___" _____________ 200_ г.
(М.П.)
ДОПУСКНОЙ ЛИСТ N ________
от _________
Объект:
_______________________________________________________________
Общие
сведения о сварщике (операторе) _________________________________
1.
Фамилия, имя, отчество
_________________________________
2. Год
рождения
_________________________________
3. Стаж
работы по сварке
_________________________________
4.
Квалификационный разряд по ОК
______________________________
5.
Клеймо
_________________________________
6. Номер
аттестационного
удостоверения, срок действия
_________________________________
7. Номер
и дата протокола
допускных
испытаний, срок действия
_________________________________
Параметры сварки
|
Область
распространения
|
1.
Способы сварки
|
|
2.
Шифр НД по сварке, технологической карты
аттестованной технологии сварки
|
|
3.
Шифр НД по контролю качества КСС допускных испытаний
|
|
4.
Характер выполняемых работ
|
|
5.
Группы (марки) основного материала
|
|
6.
Сварочные материалы
|
|
7.
Типы швов
|
|
8.
Типы сварных соединений
|
|
9.
Виды сварных соединений
|
|
10.
Форма разделки кромок
|
|
11.
Диапазон диаметров свариваемых деталей, мм
|
|
12.
Диапазон толщин свариваемых деталей
|
|
13.
Положения при сварке
|
|
14.
Наличие подогрева
|
|
15.
Наличие термической обработки
|
|
16.
Вид, тип (марка) сварочного оборудования
|
|
Представитель отдела главного сварщика
___________________________
________________
________________
(организация, должность)
(подпись, дата) (Ф.И.О.)
Представитель
службы контроля качества
___________________________
________________
________________
(организация, должность)
(подпись, дата) (Ф.И.О.)
Представитель технического надзора (по согласованию)
___________________________
________________
________________
(организация, должность)
(подпись, дата) (Ф.И.О.)
Г.2. Форма
протокола допускных испытаний
УТВЕРЖДАЮ:
___________________________
___________________________
___________________________
(подпись)
"___" _____________ 200_ г.
(М.П.)
ПРОТОКОЛ ДОПУСКНЫХ ИСПЫТАНИЙ N
________ от _________
Объект:
________________________________________________________________
1. Общие
сведения о сварщике (операторе) _______________________________
1.1.
Фамилия, имя, отчество
_______________________________
1.2. Год
рождения
_______________________________
1.3. Стаж
работы по сварке
_______________________________
1.4. Квалификационный разряд по ОК _______________________________
1.5. Клеймо
_______________________________
1.6. Номер
аттестационного
удостоверения, срок действия
_______________________________
2. Данные о сварке (наплавке) КСС _______________________________
2.1. Вид
(способ) сварки (наплавки)
┌─────────┬────────┬─────────┐
2.2. Шифр
НД по сварке, технологической
│ │ │ │
карты
аттестованной технологии сварки
│ │ │ │
2.3. Клеймо КСС
├─────────┼────────┼─────────┤
2.4. Группа
и марка свариваемого
├─────────┼────────┼─────────┤
материала
├─────────┼────────┼─────────┤
2.5. Вид
свариваемых деталей
├─────────┼────────┼─────────┤
2.6. Тип
шва
├─────────┼────────┼─────────┤
2.7. Слой шва
├─────────┼────────┼─────────┤
2.8.
Диаметр, мм ├─────────┼────────┼─────────┤
2.9.
Толщина, мм
├─────────┼────────┼─────────┤
2.10. Тип и
вид соединения
├─────────┼────────┼─────────┤
2.11.
Положение при сварке
├─────────┼────────┼─────────┤
2.12. Сварочное оборудование
├─────────┼────────┼─────────┤
2.13. Вид
покрытия и марка электродов
├─────────┼────────┼─────────┤
2.14. Марка
присадочной сварочной
├─────────┼────────┼─────────┤
проволоки │ │ │ │
2.15. Марка
защитного газа, флюса и др.
├─────────┼────────┼─────────┤
2.16. Дополнительная информация о КСС
└─────────┴────────┴─────────┘
3. Контроль качества КСС
3.1. Нормативный документ по контролю
3.2. Результаты контроля качества КСС:
Вид контроля
|
Результат и номер Заключения
|
Клеймо
КСС
|
|
|
|
Визуальный
и измерительный
|
|
|
|
Радиографический
|
|
|
|
Ультразвуковой
|
|
|
|
Испытания
на статический изгиб
|
|
|
|
Анализ
макрошлифов
|
|
|
|
4. Область распространения КСС
Параметры сварки
|
Обозначение условий
сварки
|
Область
распространения
|
4.1.
Способ сварки
|
|
|
4.2.
Вид деталей
|
|
|
4.3.
Типы швов
|
|
|
4.4.
Слой шва
|
|
|
4.5.
Группа свариваемого материала
|
|
|
4.6.
Сварочные материалы
|
|
|
4.7.
Толщина деталей, мм
|
|
|
4.8.
Наружный диаметр, мм
|
|
|
4.9.
Положения при сварке
|
|
|
4.10.
Вид соединения
|
|
|
4.11.
Сварочное оборудование
|
|
|
Допускной
лист N _______________ выдан ________________________
(подпись, дата)
Представитель отдела главного сварщика
___________________________
________________
________________
(организация, должность)
(подпись, дата) (Ф.И.О.)
Представитель службы контроля качества
___________________________
________________
________________
(организация, должность)
(подпись, дата) (Ф.И.О.)
Представитель технического надзора (по согласованию)
___________________________
________________
________________
(организация, должность)
(подпись, дата) (Ф.И.О.)
Примечания. 1. В п. 1.5 указывается личное клеймо сварщика, присвоенное
приказом по организации, в п. 2.3 указывается
клеймо, присвоенное КСС при
допускных испытаниях сварщика.
2. В п.
1.4 указывается общий стаж работы по сварке.
3. В
п. 2 и 3 вносятся
сведения о каждом
контрольном сварном
соединении, сварку
которого выполнял сварщик
при допускных испытаниях
по конкретной технологической карте аттестованной
технологии сварки.
4. В
п. 2.7 указывается
слой шва (корневой (К), подварочный (П),
горячий
проход (Гп), заполняющий
(Зп), облицовочный (О), наружный (Н),
внутренний (В)), который выполнялся сварщиком при
допускных испытаниях.
5. П.
2.12 заполняется только
для допускных испытаний
операторы
механизированной или автоматической сварки, при этом
указываются конкретные
марки сварочного оборудования, на которых
выполнялись допускные испытания.
6. В
п. 2.17 вносятся дополнительные сведения о контрольных
сварных
соединениях,
необходимых для правильного определения области
распространения (например, толщина слоя,
выполненного ручной сваркой
при
комбинированной сварке, и т.п.).
7. В
п. 3.1 вносятся наименования
методов контроля качества, которые
применялись
при допускных испытаниях
в соответствии с
требованиями
нормативных документов и результатов
производственной аттестации технологии
сварки.
8. Результаты контроля
(п. 3.2) указываются словами
"удовлетворительно" и
"неудовлетворительно" с указанием номера и даты акта,
заключения и т.п.
9. Область
распространения определяется требованиями
нормативного
документа
и
операционно-технологической
карты сборки и
сварки,
разработанной по аттестованной технологии сварки.
10. Если
при допускных испытаниях
выполнено несколько КСС, области
распространения
которых не перекрываются, то
в таблице "Область
распространения" раздельно
указывается диапазон параметров
области
распространения с учетом выполненных КСС.
11. Информацию
об области распространения допускается
указывать
условными обозначениями, принятыми в РД 03-615-03
[3].
12.
Протокол оформляется в двух экземплярах, один из которых хранится в
организации, выполняющей сварочные
работы, другой передается
в составе
исполнительной документации.
13.
Регистрацию допускного листа выполняет служба контроля качества.
14. Допускные
испытания сварщиков для выполнения ремонта сварных швов
должны проводиться по каждому виду ремонта, регламентированному настоящим
стандартом и соответствующими технологическими картами
сварки, при этом
длина КСС для каждого вида ремонта должна быть не
менее 200 мм.
15. Длина катушки КСС при допускных испытаниях
сварщиков ручной сварки
и операторов механизированной сварки должна быть не
менее 125 мм, при этом:
- для
КСС диаметром менее 1020 мм должна выполняться сварка
полного
периметра всех слоев или соответствующего слоя
(слоев) шва;
- для
КСС диаметром от 1020 до 1420 мм допускается выполнять
сварку
одной из половин периметра (относительно
вертикальной оси) всех слоев или
конкретного слоя (слоев) шва.
16. Длина
труб (катушки) КСС
при допускных испытаниях операторов
автоматической сварки устанавливается исходя
из возможности обеспечения
всех
требований
операционно-технологической
карты сборки и
сварки,
при этом:
- для
неповоротной односторонней и
двухсторонней сварки труб в
защитных
газах выполняется сварка
всех наружных слоев
шва полного
периметра, а для соединений диаметром от 1020 до
1420 мм - одной из половин
периметра (относительно вертикальной оси);
- для неповоротной автоматической двухсторонней
сварки труб в защитных
газах выполняется сварка корневого слоя шва изнутри
трубы полного периметра
независимо от диаметра;
- для
поворотной автоматической
двухсторонней сварки труб под флюсом
выполняется
сварка наружных и
внутренних слоев шва полного периметра
независимо от диаметра;
- для
поворотной автоматической односторонней
сварки под флюсом
выполняется сварка всех автоматных слоев шва
полного периметра независимо
от диаметра.
Г.3. Форма
журнала сварки сварных соединений <*>
--------------------------------
<*> Взамен
формы N 2.6 ВСН 012-88 [35].
Наименование организации, в подчинении которой
находится организация (подразделение), выполняющая сварку
Наименование организации (подразделения), выполняющей сварку
Наименование объекта
(строительство, реконструкция,
капитальный ремонт)
______________________________
______________________________
______________________________
ЖУРНАЛ N _______
сварки сварных
соединений
Год
начала ведения журнала
20__ г.
Сквоз-
ной
поряд-
ковый
номер
|
Дата
свар-
ки
|
Темпе-
ратура
воз-
духа,
°C
|
Диа-
метр
эле-
мента,
мм
|
Тол-
щина
стенки
эле-
мента,
мм
|
ГОСТ
или ТУ,
марка
стали,
завод -
поставщик
труб
|
Темпе-
ратура
пред-
вари-
тельного
подо-
грева
(просуш-
ки), °C
|
Номер сварного
соединения
|
кило-
метр
|
номер
свар-
ного
соеди-
нения
в
кило-
метре
|
допол-
нитель-
ная
марки-
ровка
|
1
|
2
|
3
|
4
|
5
|
6
|
7
|
8
|
9
|
10
|
Продолжение формы журнала сварки сварных соединений
Наимено-
вание
и номер
свари-
ваемых
элементов
|
Завод-
ской
номер
эле-
мента
|
Длина
эле-
мента,
м
|
Привязка
сварного
соединения
|
Способ
сварки
и поло-
жение
при
сварке
|
Марки
свароч-
ных
мате-
риалов
|
Фамилия,
инициалы
бригадира
(звеньевого)
и номер
схемы
расположения
сварщиков
|
Номер
шифра
бригады
или
сварщика
|
кило-
метр
|
пикет
|
11
|
12
|
13
|
14
|
15
|
16
|
17
|
18
|
19
|
Продолжение формы журнала сварки сварных соединений
Соблюдение
технологии
(подпись
бригадира)
|
Приемка сварного соединения
|
Сведения о проведении
ремонта или вырезки
сварного соединения
|
|
по
внешнему
осмотру,
подпись
прораба
(мастера)
|
по результатам контроля
физическими методами или
механическим испытаниям
|
|
отремон-
тировано,
вырезано
|
дата
|
подпись
прораба
(мастера)
|
|
вид
кон-
троля
|
N
заклю-
чения
|
дата
кон-
троля
|
резуль-
тат
|
|
20
|
21
|
22
|
23
|
24
|
25
|
26
|
27
|
28
|
|
Продолжение формы журнала сварки сварных соединений
Приемка сварного соединения после
ремонта
|
Дублирующий контроль
физическими методами
|
Примеча-
ние
|
по
внешнему
осмотру,
подпись
мастера
(прораба)
|
по результатам контроля
физическими методами или
механическим испытаниям
|
вид
кон-
троля
|
N
заклю-
чения
|
дата
кон-
троля
|
резуль-
тат
|
вид
кон-
троля
|
N
заклю-
чения
|
дата
кон-
троля
|
резуль-
тат
|
29
|
30
|
31
|
32
|
33
|
34
|
35
|
36
|
37
|
38
|
К журналу
сварки сварных соединений
газопроводов технологической
обвязки
узлов и оборудования
схема сварных соединений,
выполненная в
изометрии.
Г.4. Форма
журнала контроля сварных соединений неразрушающими методами
Наименование организации, в подчинении которой
находится организация (подразделение), выполняющая контроль
Наименование организации (подразделения), выполняющей контроль
Наименование объекта
(строительство, реконструкция,
капитальный ремонт)
______________________________
______________________________
______________________________
ЖУРНАЛ N ______
контроля сварных соединений неразрушающими методами
Год
начала ведения журнала
20___ г.
N
п/п
|
Наимено-
вание узла,
детали;
N сварного
соединения
по свароч-
ному
журналу
или
сварочной
схеме;
N свароч-
ного
журнала или
схемы
|
Шифр
сварщика
(опера-
тора)
или
бригады;
фамилия,
инициалы
|
Методы
нераз-
рушаю-
щего
контроля
(ВИК,
РК, УЗК,
МК, ПВК)
и дата
его
прове-
дения
|
Диа-
метр
и тол-
щина
стенки
трубы,
мм
|
Условия
прове-
дения
кон-
троля
|
Сред-
ства
кон-
троля
|
Описание
выявлен-
ных
дефектов
(коорди-
наты по
пери-
метру
шва)
|
Схема
прокон-
тролиро-
ванного
сварного
соеди-
нения
|
1
|
2
|
3
|
4
|
5
|
6
|
7
|
8
|
9
|
|
|
|
|
|
темпе-
ратура,
освещен-
ность
и др.
|
|
|
|
Продолжение формы журнала
контроля сварных соединений неразрушающими
методами
|
Сведения о качестве
проведения контроля
|
Примечания
|
N
заклю-
чения НК
и дата его
выдачи
|
Сведения
о качестве
проконтро-
лированного
сварного
соединения
|
Подписи
|
Замечания
технического
надзора
по качеству
проведения
НК с
указанием
должности,
фамилии и
даты
|
Дата
и подпись
ответ-
ственного
лица об
устранении
замечаний
|
специ-
алиста
НК
(ВИК,
РК,
УЗК,
МК,
ПВК)
|
началь-
ника,
инженера
службы
контроля
качества
|
10
|
11
|
12
|
13
|
14
|
15
|
16
|
|
|
|
|
|
|
|
Приложение
Д
(обязательное)
СВАРОЧНЫЕ
МАТЕРИАЛЫ ДЛЯ РУЧНОЙ, МЕХАНИЗИРОВАННОЙ
И АВТОМАТИЧЕСКОЙ
СВАРКИ ГАЗОПРОВОДОВ
Таблица Д.1
Требования
к техническим характеристикам электродов
с основным и
целлюлозным видом покрытия
для ручной дуговой
сварки
┌────────────────────────────────────────────────────────────┬────────────┐
│ Наименование показателя │ Требование │
├────────────────────────────────────────────────────────────┼────────────┤
│а)
Кривизна электрода при длине:
│ │
│
- 300 мм не более .........................................│ 0,6 мм
│
│
- 350 мм не более .........................................│ 0,7 мм
│
│
- 450 мм не более .........................................│ 0,9 мм
│
├────────────────────────────────────────────────────────────┼────────────┤
│б)
Характеристики покрытия электрода: │ │
│
- количество пор на 100 мм длины электрода не более .......│ 2 шт.
│
│
- наружный размер поры в процентном отношении к толщине │ │
│покрытия
не более 150%, но не более ........................│ 2,0 мм
│
│
- глубина поры в процентном отношении к толщине покрытия │ │
│не
более ...................................................│ 50%
│
│
- количество продольных волосяных трещин и местных сетчатых│ │
│растрескиваний
в суммарном количестве не более .............│ 2 шт.
│
│
- длина волосяной трещины или местного сетчатого │ │
│растрескивания
не более ....................................│ 10,0 мм
│
│
- суммарная протяженность отдельных продольных рисок │ │
│и
местных вмятин не более ..................................│ 25,0 мм
│
│
- глубина отдельных продольных рисок в процентном отношении│ │
│к
толщине покрытия не более ................................│ 25%
│
├────────────────────────────────────────────────────────────┼────────────┤
│
- глубина местных вмятин в процентном отношении к толщине │
│
│покрытия
не более ..........................................│ 50%
│
│
- количество местных задиров не более .....................│ 2 шт.
│
│
- глубина местных задиров в процентном отношении к толщине │ │
│покрытия
не более ..........................................│ 25%
│
│
- разнотолщинность покрытия (эксцентриситет) при диаметре │ │
│электрода:
│ │
│ - 2,5; 2,6 мм не более ...................................│ 0,08 мм
│
│ - 3,0; 3,2; 3,25 мм не более
.............................│
0,10 мм │
│ - 4,0 мм не более
........................................│
0,12 мм │
│
- суммарная протяженность откалывания покрытия │ │
│при
испытаниях на прочность не более .......................│ 5%
│
│
- визуальное определение маркировки после прокалки не менее│ 3-х раз
│
├────────────────────────────────────────────────────────────┼────────────┤
│в)
Сварочно-технологические свойства при сварке во всех │ │
│пространственных
положениях и направлениях:
│ │
│
- возбуждение дуги ........................................│ с 1-го
│
│
│ зажигания │
│
- стабильность горения дуги
...............................│равномерное,│
│
│без вибраций│
│
- формирование равномерного мелкочешуйчатого валика │ │
│с
плавным переходом к основному металлу с превышением гребня│ │
│над
впадиной не более ......................................│ 1,0 мм
│
│
- эластичность дуги не менее ..............................│ 3-х
│
│ │
диаметров │
│
│ электрода │
│
- размер козырька не более ................................│ 1-го
│
│
│ диаметра │
│
│ электрода │
│
- отделимость шлаковой корки ..............................│ при
│
│
│ небольшом │
│ │механическом│
│
│воздействии │
└────────────────────────────────────────────────────────────┴────────────┘
Таблица Д.2
Классификация и
назначение электродов
с основным видом
покрытия для ручной дуговой сварки
┌───────────────┬────────┬─────────┬──────────────────────────────────────┐
│ Назначение
│Диаметр,│ Класс │ Типы электродов │
│ │
мм
│прочности├─────┬──────────────┬─────────────────┤
│ │ │ металла │ГОСТ │AWS
A5.1 [21],│ EN 499 [23], │
│ │ │
труб │9467 │ A5.5 [22]
│ EN 757 [23] │
├───────────────┼────────┼─────────┼─────┼──────────────┼─────────────────┤
│Для
сварки │ От 2,5 │ До
К60 │Э50А │ E7016
│ E 42 2 B 4 2 H5 │
│корневого │до 3,25 │ включ. │
│ E7018 │ │
│(1-го)
и │ включ. │ │ │ │ │
│подварочного │ │ │ │ │ │
│слоев
шва │ │ │ │ │ │
│сварных │ │ │ │ │ │
│соединений │
│ │ │ │ │
│труб,
СДТ и ЗРА│ │ │ │ │ │
├───────────────┼────────┼─────────┼─────┼──────────────┼─────────────────┤
│Для
сварки │ От 3,0 │ До
К54 │Э50А,│ E7016
│ E 42 2 B 4 2 H5 │
│заполняющих │ до 4,0 │ включ. │ Э55 │ E8018
│ E 46 2 B 4 2 H5 │
│и
облицовочного│ включ.
├─────────┼─────┼──────────────┼─────────────────┤
│слоев
шва │ │ Св. К54 │ Э60
│ E8018 │E 50 2 X B 4 2 H5│
│сварных │ │ до К60 │
│ E9018 │E 55 4 X B 4 5 H5│
│соединений │ │ включ. │
│ │ │
│труб,
СДТ и ЗРА│ │ │ │ │ │
└───────────────┴────────┴─────────┴─────┴──────────────┴─────────────────┘
Таблица Д.3
Классификация
и назначение электродов
с целлюлозным видом
покрытия для ручной дуговой сварки
┌─────────────┬────────┬─────────┬────────────────────────────────────────┐
│
Назначение │Диаметр,│ Класс
│
Классификация │
│ │ мм
│прочности├─────────┬───────────────┬──────────────┤
│ │ │ металла │ГОСТ 9467│
AWS A5.1 [21],│ EN 499 [23], │
│ │ │
труб │ │
A5.5 [22] │ EN 757
[23] │
├─────────────┼────────┼─────────┼─────────┼───────────────┼──────────────┤
│Для
сварки │ От 3,2 │ До
К60 │ Э46А
│ E6010 │ E 38 3 C 2 1 │
│корневого │ до 4,0 │ включ. │
Э50А │ E7010
│ E 42 2 C 2 5 │
│(1-го)
слоя │ включ. │ │ │ │ │
│шва
стыковых │ │ │ │ │ │
│сварных │ │ │ │ │ │
│соединений │
│ │ │ │ │
│труб │ │ │ │ │ │
├─────────────┼────────┼─────────┼─────────┼───────────────┼──────────────┤
│Для
сварки │ От 4,0 │ До
К54 │ Э46А,
│ E6010
│ E 38 3 C 2 1 │
│горячего │ включ. │ включ. │
Э50А │ E7010
│ E 42 2 C 2 5 │
│прохода
шва │
├─────────┼─────────┼───────────────┼──────────────┤
│стыковых │ │ Св. К54 │ Э60
│ E8018 │ E 42 2 C 2 5 │
│сварных
труб │ │ до К60 │ │ E9018
│ │
│ │ │ включ. │ │ │ │
└─────────────┴────────┴─────────┴─────────┴───────────────┴──────────────┘
Таблица Д.4
Электроды с
основным видом покрытия для ручной
дуговой сварки
неповоротных кольцевых стыковых, угловых
и нахлесточных
соединений труб, труб с СДТ, ЗРА
─────────────┬────────────┬──────────────────────┬────────┬────────────────
Назначение
│ Марка │Тип по ГОСТ, AWS, EN │Диаметр,│ Производитель
│ │ │ мм
│
─────────────┼────────────┼──────────────────────┼────────┼────────────────
1
│ 2 │ 3 │ 4
│ 5
─────────────┼────────────┼──────────────────────┼────────┼────────────────
Для сварки
│ LB-52U │
E 7016 по AWS A5.1 │ 2,6;
│ Kobe-Steel
корневого, │
(ЛБ-52У) │ [21] │3,2; 4,0│ (Япония)
подварочного
├────────────┼──────────────────────┼────────┼────────────────
слоев
шва │ OK 53.70
│ Э50А по ГОСТ 9467, │
2,5; │ ESAB AB
соединений │ │ E 7016-1 по AWS А5.1
│ 3,25; │ (Швеция)
труб,
СДТ, │ │ [21], │ 4,0
│
ЗРА
из сталей│ │ EN 42 5 B 12 H5 │ │
с
классом │ │ по EN 499 [23] │
│
прочности │ │ │ │
до
К60 включ.│ │ │ │
├────────────┼──────────────────────┼────────┼────────────────
Для сварки
│Fox EV Pipe │ E
7016-1 H4 R │2,5; 3,2│

заполняющих │ ("Фокс ЕВ │
по AWS A5.1 [21], │ │

и
облицовоч- │ Пайп") │
EN 42 4 B 12 H5 │ │

ного
слоев │ │ по EN 499 [23] │
│ (Австрия)
шва │ │ │ │
соединений │ │ │ │
труб,
СДТ и │ │ │ │
ЗРА
из сталей│ │ │ │
с
классом │ │ │ │
прочности │ │ │ │
до
К54 включ.│ │ │ │
├────────────┼──────────────────────┼────────┼────────────────
Для сварки
│Phoenix K50R│ E 7016
по AWS A5.1 │ 2,5;
│

корневого, │Mod ("Феникс│ [21] │3,2; 4,0│

подварочного
│ К50Р Мод") │ │ │

слоев
шва │ │ │ │ (Германия)
соединений ├────────────┼──────────────────────┼────────┼────────────────
труб,
СДТ, │ P47 (П47) │E 7016-1 по AWS
A5.1│ 2,5; │
ELGA AB
ЗРА
из сталей│ │[21],
E 46 4 B 12 H5 │3,2;
4,0│ (Швеция)
с
классом │ │ по EN 499 [23] │ │
прочности │ │ │ │
до
К60 включ.│ │ │ │
├────────────┼──────────────────────┼────────┼────────────────
Для
сварки │ Pipeliner │
E 7016 H4 │2,5;
3,2│ The Lincoln
заполняющих │
16P │ по AWS A5.1 [21] │ │Electric Company
и
облицовоч- │("Пайплайнер│ │ │ (США)
ного
слоев │ 16П")
│
│ │
шва
├────────────┼──────────────────────┼────────┼────────────────
соединений │МТГ-01К <*> │ Э50А по ГОСТ 9467 │2,5; 3,0│ ООО "Сычевский
труб,
СДТ и │ │ │ │
электродный
ЗРА
из сталей│ │ │ │
завод"
с
классом │ │ │ │ (Россия)
прочности
├────────────┼──────────────────────┼────────┼────────────────
до
К54 включ.│МТГ-02 <**> │
Э50А по ГОСТ 9467 │ 4,0
│ ООО "Сычевский
│ │ │ │
электродный
│ │ │ │ завод"
│ │ │ │ (Россия)
├────────────┼──────────────────────┼────────┼────────────────
│ OK 53.70
│ Э50А по ГОСТ 9467 │
2,5; │ ЗАО
"ЕСАБ-СВЭЛ"
│ │ │3,0;
4,0│ (Россия)
│ │ │ │
├────────────┼──────────────────────┼────────┼────────────────
│ SE-08-00
│ Э50А по ГОСТ 9467 │
2,5; │ ЗАО "СИБЕС"
│ │ │3,0;
4,0│ (Россия)
├────────────┼──────────────────────┼────────┼────────────────
│УОНИ 13/55 R│ Э50А по ГОСТ 9467 │
2,0; │ ООО "Сычевский
│ │ │ 2,5;
│ электродный
│ │ │3,0;
4,0│ завод"
│ │ │ │ (Россия)
├────────────┼──────────────────────┼────────┼────────────────
│УОНИ-13/55Р │ Э50А по ГОСТ 9467 │
2,0; │ЗАО
"ЕСАБ-СВЭЛ"
│ │ │ 2,5;
│ (Россия)
│ │ │3,0; 4,0│
─────────────┼────────────┼──────────────────────┼────────┼────────────────
Для сварки
│ LB-62D │
Э50А по ГОСТ 9467, │3,2;
4,0│ Kobe-Steel
заполняющих
и│ │ E 9018-G по
AWS A5.5 │ │ (Япония)
облицовочного│ │ [22] │ │
слоев
шва
├────────────┼──────────────────────┼────────┼────────────────
соединений │
OK 74.70 │ Э60 по ГОСТ 9467, │ 3,25; │
ESAB AB
труб,
СДТ и │ │ E 8018-G по AWS A5.5
│ 4,0 │
(Швеция)
ЗРА
из сталей│ │ [22], │ │
с
классом │ │E 50 4 Mn Mo B 4 2 H5
│ │
прочности
св.│ │ по EN 499 [23] │ │
К54
до К60 ├────────────┼──────────────────────┼────────┼────────────────
включ. │ Phoenix SH │ E 8018-G по
AWS A5.5 │3,2; 4,0│

│ Schwarz 3K │ [22], │ │

│Mod ("Феникс│ E 50 4 Mo B 4 2 │ │

│СШ Шварц 3К │ по EN 499 [23] │ │ (Германия)
│ Мод")
│
│ │
├────────────┼──────────────────────┼────────┼────────────────
│ P62MR
│ E 8018-G по AWS A5.5 │
2,5; │ ELGA AB
│(П62МР) <*>
│ [22], │3,2; 4,0│ (Швеция)
│ │ E 46 5 1 Ni B 3 2 H5
│ │
│ │ по EN 499 [23] │ │
├────────────┼──────────────────────┼────────┼────────────────
│ Pipeliner │
E 8018-G H4 по AWS │3,2;
4,0│Lincoln Electric
│ 18P
│ A5.5 [22] │
│ Company (США)
│("Пайплайнер│ │ │
│ 18П") <*>│ │ │
├────────────┼──────────────────────┼────────┼────────────────
│Kessel 5520│ E 8018-G по AWS A5.5 │3,2;
4,0│

│Mo
("Кессель│ [22] │ │

│ 5520 Mo") │ │ │

│ │ │ │ (Германия)
├────────────┼──────────────────────┼────────┼────────────────
│ Phoenix
│ E 8018-G по AWS A5.5 │3,2; 4,0│

│ SH V 1
│ [22], │ │

│ ("Феникс
│E 50 6 Mn 1 Ni B 42 H5│ │

│СШ В1") <*>
│ по EN 499 [23] │ │ (Германия)
├────────────┼──────────────────────┼────────┼────────────────
│ МТГ-03 <*>
│ Э60 по ГОСТ 9467 │3,0; 4,0│ ООО "Сычевский
│ │ │ │
электродный
│ │ │ │ завод"
│ │ │ │ (Россия)
├────────────┼──────────────────────┼────────┼────────────────
│ SE-10-00
│ Э60 по ГОСТ 9467 │3,0; 4,0│ ЗАО "СИБЕС"
│ (СЕ-10-00) │ │ │ (Россия)
─────────────┼────────────┼──────────────────────┼────────┼────────────────
Для сварки
│ FOX BVD 90 │ E 9018-G по AWS A5.5 │ 3,2; │

заполняющих
и│ <*> │ [22], │4,0; 4,5│

облицовочного│
("Фокс БВД │ E 55 5 Z2Ni B 4 5 H5 │ │

слоев
шва │ 90")
│ по EN 757 [23] │ │ (Австрия)
соединений │ │ │ │
труб,
СДТ и │ │ │ │
ЗРА
из сталей│ │ │ │
с
классом │ │ │ │
прочности
св.│ │ │ │
К54
до К60 │ │ │ │
включ. │ │ │ │
─────────────┴────────────┴──────────────────────┴────────┴────────────────
<*>
Электроды обеспечивают повышенные
вязкопластические свойства и
ударную
вязкость металла шва.
<**> Электроды рекомендуются
к применению только
для сварки
заполняющих
и облицовочного слоев шва.
Примечание.
Электроды, приведенные в
таблице, рекомендованы к
применению
для сварки кольцевых стыковых и угловых соединений труб, СДТ и
ЗРА
на подъем, за исключением электродов марки
FOX BVD 90 (Фокс БВД 90),
сварка
которыми выполняется на спуск.
───────────────────────────────────────────────────────────────────────────
Таблица Д.5
Электроды с
целлюлозным видом покрытия для сварки
неповоротных
стыковых соединений труб
──────────────┬───────────────┬──────────────────┬────────┬────────────────
Назначение
│ Марка │
Классификация
│Диаметр,│ Производитель
│ │ │ мм
│
──────────────┼───────────────┼──────────────────┼────────┼────────────────
Для
сварки │Pipeliner 6P+ │E 6010 по AWS A5.1│3,2;
4,0│ The Lincoln
корневого
слоя│("Пайплайнер
│ [21] │ │Electric Company
и
горячего │ 6 П+") │ │ │ (США)
прохода
шва ├───────────────┼──────────────────┼────────┼────────────────
соединений │ Fleetweld 5P+ │E 6010 по AWS
A5.1│3,2; 4,0│Lincoln KD S.A.
труб
из сталей│ ("Флитвелд │
[21] │ │ (Испания)
с
классом │ 5П+") │ │ │
прочности
до
├───────────────┼──────────────────┼────────┼────────────────
К60
включ. │ Fox Cel <*> │E 6010 по AWS A5.1│3,2;
4,0│

│ ("Фокс Цель")
│ [21], │ │

│ │ EN 38 3 C 2 1 │
│

│ │ по EN 499 [23] │
│ (Австрия)
├───────────────┼──────────────────┼────────┼────────────────
│Fox Cel Mo
<**>│ E 7010-A1 по AWS │3,2; 4,0│

│ ("Фокс Цель │
A5.1 [21], │ │

│ Мо") │
EN 38 3 C 2 1 │ │

│ │ по EN 499 [23] │
│ (Австрия)
──────────────┴───────────────┴──────────────────┴────────┴────────────────
<*>
Сварку горячего прохода
указанными электродами рекомендуется
выполнять
для соединений труб из сталей с классом прочности до К54 включ.
<**>
Рекомендованы только для сварки горячего прохода соединений
труб
из
сталей с классом прочности от К55 до К60 включ.
Примечание.
Сварку горячего прохода
следует выполнять электродами
диаметром
4,0 мм.
───────────────────────────────────────────────────────────────────────────
Таблица Д.6
Требования
к техническим характеристикам
проволок сплошного
сечения, порошковых проволок,
в т.ч.
самозащитным, для механизированной
и автоматической
сварки
┌────────────────────────────────────────────────────────────┬────────────┐
│ Наименование показателя │ Требование │
├────────────────────────────────────────────────────────────┼────────────┤
│а)
Характеристики проволок сплошного сечения: │ │
│
- предельные отклонения по диаметру (диаметром до 4,0 мм │ │
│включ.)
....................................................│+/- 0,09 мм │
│
- овальность в процентном отношении к предельному │ │
│отклонению
по диаметру не более ............................│ 50%
│
│
- глубина мелких волочильных рисок, царапин, следов │ │
│шлифовки,
местной рябизны и отдельных вмятин в процентном │ │
│отношении
к предельному отклонению по диаметру не более ....│ 25%
│
│
- толщина медного покрытия омедненной проволоки не менее ..│ 0,20 мкм
│
│
- отсутствие отслаивания, растрескивания медного покрытия, │ │
│поверхностных
пленок, закатов, раковин, забоин, окалины,
│ │
│следов
ржавления, масла, технологических смазок и других │ │
│загрязнений │ │
├────────────────────────────────────────────────────────────┼────────────┤
│б)
Характеристики порошковых проволок, в т.ч. самозащитных: │ │
│
- предельные отклонения по диаметру для проволок диаметром:│ │
│ - от 1,2 до 1,6 мм включ.
................................│+/- 0,05 мм │
│ - св. 1,8 до 2,2 мм включ.
...............................│+/- 0,08 мм │
│
- предельные отклонения коэффициента заполнения в процентах│ │
│от
номинального значения ...................................│ +/- 1,5%
│
│
- относительную разность показаний при взвешивании отрезков│ │
│проволоки
из разных мест мотков (катушек, кассет, бухт) │ │
│не
более ...................................................│ 5%
│
│
- пригодность проволоки к сварке при переломе без высыпания│ │
│порошка-наполнителя
│ │
├────────────────────────────────────────────────────────────┼────────────┤
│в)
Сварочно-технологические свойства при сварке во всех │ │
│пространственных
положениях и направлениях:
│ │
│
- возбуждение дуги ........................................│ с 1-го
│
│ │
зажигания │
│
- стабильность горения дуги
...............................│равномерное,│
│
│без вибраций│
│
- формирование с плавным переходом к основному металлу │ │
│равномерного
мелкочешуйчатого валика с превышением гребня
│ │
│над
впадиной не более ......................................│ 1,0 мм
│
│
- эластичность дуги не менее ..............................│ 3-х
│
│
│ диаметров │
│
│ проволоки │
│
- отделимость шлаковой корки ..............................│ при
│
│ │
небольшом │
│
│механическом│
│
│воздействии │
└────────────────────────────────────────────────────────────┴────────────┘
Таблица Д.7
Классификация и
назначение проволок сплошного сечения
для
механизированной и автоматической сварки в защитных
газах неповоротных
кольцевых стыковых соединений труб
┌─────────────────┬─────────┬─────────────────────────────────────────────┐
│ Назначение
│ Класс │ Классификация │
│
│прочности├────────────┬────────────────┬───────────────┤
│ │ металла │ ГОСТ
2246 │AWS A5.18 [26], │ EN
440 [29], │
│ │ труб
│ │ A5.28 [28]
│ EN 12534 [31] │
├─────────────────┼─────────┼────────────┼────────────────┼───────────────┤
│Для
механизи- │ До К54 │Легированная│ E R 70 S-G
│ G 42 2 M (C) │
│рованной
и │ включ. │ │ │ G 46 2 M (C) │
│автоматической │ │ │ │ │
│сварки
├─────────┼────────────┼────────────────┼───────────────┤
│неповоротных │ Св. К54
│Легированная│ E R 70
S-G │ G 46 2 M (C) │
│кольцевых │ до К60 │ │ E R 80 S-G
│ G 50 2 M (C) │
│стыковых │ включ. │ │ │ │
│соединений
труб │ │ │ │ │
└─────────────────┴─────────┴────────────┴────────────────┴───────────────┘
Таблица Д.8
Классификация
и назначение проволок сплошного сечения
для автоматической
сварки под флюсом поворотных
кольцевых стыковых
соединений труб
Назначение
|
Класс
прочности
металла труб
|
Классификация
|
ГОСТ
2246
|
AWS
A5.17 [25],
A5.23 [27]
|
EN 756 [30]
|
Для сварки
всех слоев шва
поворотных
кольцевых
стыковых
сварных
соединений труб
|
До К52
включ.
|
Легированная
|
F 8 A 0 E 12
|
S
42 2 AS (AF)
|
Св. К52 до
К56 включ.
|
Легированная
|
F 8 A 0 E A1
|
S
46 2 AF (AS)
|
Св. К56 до
К60 включ.
|
Легированная
|
F 9 A 2 E A2
|
S
50 2 AF (AS)
|
Таблица Д.9
Классификация и
назначение порошковых проволок
для
механизированной и автоматической сварки в защитных
газах и смесях
неповоротных кольцевых стыковых
соединений труб
┌─────────────────────┬─────────┬─────────────────────────────────────────┐
│ Назначение │
Класс │ Классификация │
│
│прочности├──────────┬────────────────┬─────────────┤
│ │ металла
│ГОСТ 26271│AWS A5.20 [32], │ EN 758 [34] │
│ │ труб
│ │
A5.29 [33] │ │
├─────────────────────┼─────────┼──────────┼────────────────┼─────────────┤
│
Для сварки │ До К54 │ПГ 44-А2В │ E 71TX-XM
│ T 42 2 RM │
│заполняющих │ включ. │ │ │ T 46 2 RM
│
│и
облицовочного
слоев├─────────┼──────────┼────────────────┼─────────────┤
│шва
неповоротных │ Св. К54
│ПГ 49-А2В │ E 71TX-XM │
T 46 2 RM │
│кольцевых
стыковых │ до К60 │ПГ 54-А5В │ E 81TX-XM
│ T 50 2 RM │
│сварных
соединений │ включ.
│ │ │ │
│труб │ │ │ │ │
└─────────────────────┴─────────┴──────────┴────────────────┴─────────────┘
Таблица Д.10
Классификация
и назначение самозащитных
порошковых проволок
для механизированной и автоматической
сварки неповоротных
кольцевых стыковых соединений труб
┌──────────────────────┬─────────┬────────────────────────────────────────┐
│ Назначение │
Класс │ Классификация │
│
│прочности├──────────┬───────────────┬─────────────┤
│ │ металла
│ГОСТ 26271│AWS A5.20 [32],│ EN 758 [34] │
│ │ труб
│ │ A5.29 [33]
│ │
├──────────────────────┼─────────┼──────────┼───────────────┼─────────────┤
│
Для сварки │ До К54 │ ПС 44-2В │ E 71T
│ T 42 2 XY │
│заполняющих │ включ. │ │ │ T 46 2 XY
│
│и
облицовочного слоев │ │ │ │ │
│шва
неповоротных
├─────────┼──────────┼───────────────┼─────────────┤
│кольцевых
стыковых │ Св. К54 │ ПС
49-2В │ E 71T │
T 46 2 XY │
│сварных
соединений │ до К60 │ПС 54-А5В │ E 81T
│ T 50 2 XY │
│труб │ включ. │ │ │ │
└──────────────────────┴─────────┴──────────┴───────────────┴─────────────┘
Таблица Д.11
Проволоки
сплошного сечения для механизированной сварки
в углекислом газе
неповоротных кольцевых
стыковых соединений
труб
Назначение
|
Марка
|
Классификация
|
Диаметр,
мм
|
Производитель
|
Для сварки корневого
слоя шва соединений
труб, труб с СДТ, ЗРА
из сталей с классом
прочности до К60
включ.
|
Super
Arc L-56
|
E R 70 S-6
по AWS A5.18
[26]
|
1,14
|
The Lincoln
Electric
Company (США)
|
Примечание. Сварочные проволоки,
приведенные в таблице,
могут
дополняться в соответствии с требованиями 7.1.2.
|
Таблица Д.12
Проволоки
сплошного сечения для автоматической сварки
в защитных газах
неповоротных кольцевых
стыковых соединений
труб
────────────────────┬──────────┬──────────────┬────────┬───────────────────
Назначение │
Марка │Классификация
│Диаметр,│ Производитель
│ │ │ мм
│
────────────────────┼──────────┼──────────────┼────────┼───────────────────
1
│ 2 │ 3
│ 4 │ 5
────────────────────┼──────────┼──────────────┼────────┼───────────────────
Для сварки первого │ Thyssen │E R 70 S-G по │ 0,9
│

внутреннего │ K-Nova
│AWS A5.28 [28]│
│

(корневого)
слоя шва│ (TS-6) │ │ │

соединений
труб │ │ │ │ (Германия)
из
сталей с классом │ │ │ │
прочности
до К60 │ │ │ │
включ.
много- │ │ │ │
головочным
автоматом│ │ │ │
ИВМ
(IWM) фирмы │ │ │ │
CRC-Evans
AW │ │ │ │
Для сварки первого │ │ │ │
наружного
слоя │ │ │ │
("горячего │ │ │ │
прохода"), │ │ │ │
заполняющих
и │ │ │ │
облицовочного
слоев │ │ │ │
шва
соединений труб │
│ │ │
из
сталей с классом │
│ │ │
прочности
до К60 │ │ │ │
включ.
сварочными │ │ │ │
головками
П-200 │ │ │ │
(P-200),
П-260 │ │ │ │
(P-260)
фирмы │ │ │ │
CRC-Evans
AW и │ │ │ │
сварочными
головками│ │ │ │
ЕВМ
(EWM) фирмы │ │ │ │
Autoweld
Systems │ │ │ │
────────────────────┼──────────┼──────────────┼────────┼───────────────────
Для сварки │ K-600
│ E R 80 S по │ 1,0
│

заполняющих
и │ │AWS A5.28 [28]│ │

облицовочного
слоев │ │ │ │

шва
соединений труб │
│ │ │ (Германия)
из
сталей с классом │
│ │ │
прочности
до К60 │ │ │ │
включ.
сварочными │ │ │ │
головками
П-600 │ │ │ │
(P-600)
фирмы │ │ │ │
CRC-Evans
AW │ │ │ │
────────────────────┼──────────┼──────────────┼────────┼───────────────────
Для сварки первого │ SG3-P
│E R 70 S-6 по │
0,9 │

внутреннего │ │AWS A5.18 [26]│ │

(корневого)
слоя шва│ │ │ │

соединений
труб │ │ │ │ (Австрия)
из
сталей с классом │
│ │ │
прочности
до К60 │ │ │ │
включ.
много- │ │ │ │
головочным
автоматом│ │ │ │
ИВМ
(IWM) фирм │ │ │ │
CRC-Evans
AW, │ │ │ │
Autoweld
Systems │ │ │ │
Для сварки первого │ │ │ │
наружного
слоя │ │ │ │
("горячего │ │ │ │
прохода"), │ │ │ │
заполняющих
и │ │ │ │
облицовочного
слоев │ │ │ │
шва
соединений труб │
│ │ │
из
сталей с классом │
│ │ │
прочности
до К60 │ │ │ │
включ.
сварочными │ │ │ │
головками
ЕВМ (EWM) │ │ │ │
фирмы │ │ │ │
Autoweld
Systems │ │ │ │
────────────────────┼──────────┼──────────────┼────────┼───────────────────
Для сварки │Super Arc │E R 70 S-6 по
│ 1,14 │
The Lincoln
корневого
слоя шва │ L-56
│AWS A5.18 [26]│
│ Electric Company
соединений
труб │ │ │ │ (США)
из
сталей с классом │
│ │ │
прочности
до К60 │ │ │ │
включ.
сварочными │ │ │ │
головками
M300-C │ │ │ │
(M300)
фирмы │ │ │ │
CRC-Evans
AW │ │ │ │
────────────────────┼──────────┼──────────────┼────────┼───────────────────
Для сварки всех │OK Autrod │E R 70 S-6 по
│ 1,0 │
ESAB VAMBERG sro
слоев
шва соединений│ 12.66 │AWS A5.18 [26]│ │ (Чехия)
труб
из сталей │ │ │ │
с
классом прочности │
│ │ │
до
К60 включ. │ │ │ │
комплексом │ │ │ │
оборудования
CWS.02 │ │ │ │
фирмы
PWT │ │ │ │
────────────────────┼──────────┼──────────────┼────────┼───────────────────
Для сварки всех │ Lincoln │E R 70 S-6 по │ 1,0
│ Lincoln Electric
слоев
шва соединений│Supra Mig │AWS A5.18 [26]│ │ (U.K.) Ltd.
труб
из сталей │ │ │ │
(Великобритания)
с
классом прочности
├──────────┼──────────────┼────────┼───────────────────
до
К60 включ. │ Thyssen │E R 80 S-G по │ 1,0
│

комплексом │K-Nova Ni │AWS A5.28
[28]│ │

оборудования │ │ │ │

Saturnax
фирмы │ │ │ │ (Германия)
Serimax │ │ │ │
────────────────────┴──────────┴──────────────┴────────┴───────────────────
Примечание. Перечень видов сварочной
проволоки, приведенный в таблице,
может
дополняться в соответствии с требованиями 7.1.2.
───────────────────────────────────────────────────────────────────────────
Таблица Д.13
Комбинации
"проволока + флюс"
для автоматической
сварки поворотных кольцевых
стыковых соединений
труб
Назначение
|
Комбинация
"проволока +
флюс"
|
Классификация
|
Диаметр
проволоки,
мм
|
Производитель
|
Для сварки
всех слоев
шва
соединений
труб
из сталей
с классом
прочности
до К54
включ.
|
Pipeliner
L-61 +
Pipeliner 860
|
E
7 A 4 - EM 12K
по AWS A5.23 [27]
|
3,2
|
The Lincoln
Electric
Company (США)
|
OK
Autrod 12.22 +
OK Flux 10.71
|
E 7 A 4 - EM 12K
по AWS A5.23 [27],
S2Si по EN 756
[30]
|
3,0; 4,0
|
проволока -
ESAB VAMBERG
sro (Чехия),
флюс - ESAB
Sp z.o.o.
(Польша)
|
Для сварки
всех слоев
шва
соединений
труб
из сталей
с классом
прочности
св. К54 до
К60 включ.
|
Pipeliner
LA-85 +
Pipeliner 860
|
F8A4-ENi5-Ni5-H8
по AWS A5.23 [27]
|
3,2
|
The Lincoln
Electric
Company (США)
|
Pipeliner
LA-85 +
Pipeliner MIL800H
<*>
|
F9A4-ENi5-G-H2
по AWS A5.23 [27]
|
3,2
|
The Lincoln
Electric
Company (США)
|
OK
Autrod 12.24 +
OK Flux 10.71
|
F8A2-EA2-A4,
F7P0-EA2-A4
по AWS A5.23 [27],
S 46 2 AB S2Mo
по EN 756 [30]
|
3,0; 4,0
|
проволока -
ESAB VAMBERG
sro (Чехия),
флюс - ESAB
Sp z.o.o.
(Польша)
|
OK
Autrod 13.24 +
OK Flux 10.71
|
F8A5-EG-G,
F8P4-EG-G
по AWS A5.23 [27],
S 50 4 AB S0
по EN 756 [30]
|
3,0; 4,0
|
проволока -
ESAB VAMBERG
sro (Чехия),
флюс - ESAB
Sp z.o.o.
(Польша)
|
<*> Комбинация обеспечивает повышенные вязкопластические свойства
и
ударную вязкость металла шва.
Примечание. Допускается применение плавленых флюсов
АН-47
производства ОАО "Запорожский завод сварочных флюсов и стеклоизделий" в
сочетании с проволоками
сплошного сечения марок
Св-08ГА, Св-08ХМ,
Св-08МХ, Св-08ГНМ, изготовленными по
специальным ТУ, при
условии
их аттестации согласно требованиям РД 03-613-03[1]
в специализированных аттестационных центрах по сварке газонефтепроводов.
|
Таблица Д.14
Порошковые
проволоки для автоматической сварки
в защитных газах
неповоротных кольцевых
стыковых соединений
труб
Назначение
|
Марка
|
Классификация
|
Диаметр,
мм
|
Производитель
|
Для сварки
заполняющих
и облицовочного
слоев шва
соединений труб,
труб с СДТ и ЗРА
из сталей с классом
прочности св. К55
до К60 включ.
|
Pipeliner
Autoweld G70M
<*>
|
E 71T 1MJH8,
E 71T 9MJH8
AWS A5.20 [32]
|
1,32
|
The Lincoln
Electric
Company (США)
|
Filarc
PX 701
|
E71T 1
AWS A5.20 [32]
|
1,40
|
ESAB
(Швеция)
|
OK Tubrod
15.19
|
E81T1 Ni1M по
AWS A5.29 [33]
|
1,20
|
ESAB AB
VAMBERG sro
(Чехия)
|
<*> Проволока обеспечивает
повышенные вязкопластические
свойства и
ударную вязкость металла шва.
|
Таблица Д.15
Самозащитные
порошковые проволоки
для
механизированной сварки неповоротных кольцевых
стыковых соединений
труб
Назначение
|
Марка
|
Классификация
|
Диаметр,
мм
|
Производитель
|
Для сварки
корневого слоя,
горячего прохода,
подварочного слоя
шва соединений труб
из сталей с классом
прочности до К60
включ.
Для сварки
заполняющих и
облицовочного слоев
шва соединений труб,
труб с СДТ и ЗРА
с классом прочности
до К54 включ.
|
Innershield
NR-204H
|
E71T-GS
по AWS A5.29
[33]
|
1,7
|
The Lincoln
Electric
Company (США)
|
Innershield
NR-207
|
E71T8-K6
по AWS A5.29
[33]
|
1,7
|
The Lincoln
Electric
Company (США)
|
Для сварки
заполняющих и
облицовочного слоев
шва соединений труб,
труб с СДТ и ЗРА с
классом прочности
св. К54 до К60
включ.
|
Pipeliner
NR-208-Special
|
E81T8-G
по AWS A5.29
[33]
|
1,7;
2,0
|
The Lincoln
Electric
Company (США)
|
Pipeliner
NR-208-XP <*>
|
E81T8-G по
AWS A5.29
[33]
|
1,7;
2,0
|
The Lincoln
Electric
Company (США)
|
<*> Проволока обеспечивает
повышенные вязкопластические свойства
и
ударную вязкость металла шва.
|
Таблица Д.16
Требования
к техническим характеристикам флюсов
для автоматической
сварки
┌────────────────────────────────────────────────────────────┬────────────┐
│ Наименование показателя │ Требование │
├────────────────────────────────────────────────────────────┼────────────┤
│а)
Характеристики плавленых флюсов: │ │
│
- влажность в состоянии поставки не более .................│ 0,05%
│
│
- отсутствие инородных частиц │ │
│
- допускаемое количество зерен с цветом, отличающимся от │ │
│нормативного,
в процентном отношении по массе не более .....│ 3,0%
│
│
- допускаемое количество зерен с размером, отличающимся от │ │
│нормативных
минимального и максимального значений не более .│ 3,0%
│
├────────────────────────────────────────────────────────────┼────────────┤
│б)
Характеристики керамических флюсов: │ │
│
- влажность в состоянии поставки не более .................│ 0,1%
│
│
- размер гранул в пределах ................................│ от 0,25
│
│ │ до 2,0 мм │
│
- количество гранул размером менее 0,25 мм в процентном │ │
│отношении
по массе не более ................................│ 5%
│
│
- количество гранул размером более 2,0 мм в процентном │
│
│отношении
по массе не более ................................│ 8%
│
├────────────────────────────────────────────────────────────┼────────────┤
│в)
Сварочно-технологические свойства флюсов: │ │
│
- возбуждение дуги ........................................│ с 1-го
│
│
│ зажигания │
│
- стабильность горения дуги
...............................│равномерное,│
│ │без вибраций│
│
- формирование с плавным переходом к основному металлу │ │
│гладкого
валика с усилением не более .......................│ 4,0 мм
│
│
- отделимость шлаковой корки после охлаждения .............│ при
│
│
│ небольшом │
│
│механическом│
│
│воздействии │
└────────────────────────────────────────────────────────────┴────────────┘
Таблица Д.17
Требования
к техническим характеристикам защитных
(активных и
инертных) газов и смесей для механизированной
и автоматической
сварки
┌──────────────────────────────────────────────────────────────┬──────────┐
│ Наименование показателя │Требование│
├──────────────────────────────────────────────────────────────┼──────────┤
│а)
Аргон газообразный должен иметь: │ │
│
- объемную долю аргона не менее .............................│ 99,9930%
│
│
- объемную долю азота не более ..............................│
0,0050% │
│
- объемную долю кислорода не более ..........................│
0,0007% │
│
- массовую концентрацию водяных паров при 20 °C и давлении │ │
│760
мм рт. ст. не более ......................................│0,01
г/см3│
├──────────────────────────────────────────────────────────────┼──────────┤
│б)
Двуокись углерода газообразная и жидкая должна иметь: │ │
│
- объемную долю двуокиси углерода не менее ..................│ 99,6%
│
│
- точку росы не выше ........................................│ -48 °C
│
├──────────────────────────────────────────────────────────────┼──────────┤
│в)
Смесь газообразная аргона и двуокиси углерода должна иметь:│ │
│
- массовую долю влаги не более ..............................│ 0,008%
│
│
- объемную долю азота не более ..............................│ 0,010%
│
│
- предельные отклонения объемной доли двуокиси углерода │ │
│в
зависимости от состава смеси: │ │
│
- 15% CO - 85% Ar
..........................................│ +/- 1,5% │
│ 2
│ │
│
- 25% CO - 75% Ar
..........................................│ +/- 2,5% │
│ 2
│ │
│
- 50% CO - 50% Ar
..........................................│ +/- 5,0% │
│ 2
│ │
└──────────────────────────────────────────────────────────────┴──────────┘
Таблица Д.18
Защитные
газы и их смеси для механизированной
и автоматической
сварки неповоротных кольцевых
стыковых соединений
труб
┌─────────────────┬───────────────────────────┬───────────────────────────┐
│ Назначение
│ Защитный газ │ Способ сварки │
├─────────────────┼───────────────────────────┼───────────────────────────┤
│
Для сварки │ 100% CO │Механизированная сварка │
│первого │ 2 │проволокой сплошного │
│(корневого, │ │сечения │
│внутреннего)
слоя│ │Автоматическая
сварка │
│шва
соединений │ │проволокой
сплошного │
│труб
из сталей │ │сечения
комплексом │
│с
классом │ │оборудования
CWS.02 фирмы │
│прочности
до К60 │
│PWT
│
│включ.
├───────────────────────────┼───────────────────────────┤
│ │ 50% Ar, │Автоматическая сварка │
│ │ 50% CO │проволокой сплошного │
│ │ 2 │сечения комплексом │
│ │ │оборудования
Saturnax фирмы│
│ │ │Serimax │
│
├───────────────────────────┼───────────────────────────┤
│ │ 75% Ar, │Автоматическая сварка │
│ │ 25% CO │проволокой сплошного │
│ │ 2 │сечения многоголовочным │
│ │ │автоматом ИВМ
(IWM) фирмы │
│ │ │CRC-Evans
AW │
│ │
│Автоматическая сварка
│
│ │ │проволокой
сплошного │
│ │ │сечения
сварочными │
│ │ │головками M300-C (M300) │
│ │ │фирмы
CRC-Evans AW │
│
├───────────────────────────┼───────────────────────────┤
│ │ 80% Ar, │Автоматическая сварка │
│ │ 20% CO │проволокой сплошного │
│ │ 2 │сечения многоголовочным │
│ │ │автоматом ВМС
фирмы │
│ │ │Autoweld
Systems │
├─────────────────┼───────────────────────────┼───────────────────────────┤
│
Для сварки │ 100% CO │Автоматическая сварка │
│горячего
прохода │ 2 │проволокой сплошного │
│шва
соединений │ │сечения
сварочными │
│труб
из сталей с │
│головками П-200 (P-200),
│
│классом
прочности│
│П-260 (P-260) фирмы
│
│до
К60 включ. │ │CRC-Evans
AW │
│ │
│Автоматическая сварка
│
│ │ │проволокой
сплошного │
│ │ │сечения
сварочными │
│ │ │головками ВГС
фирмы │
│ │ │Autoweld
Systems │
│ │ │Автоматическая
сварка │
│ │ │проволокой
сплошного │
│ │ │сечения
комплексом │
│ │ │оборудования
CWS.02 фирмы │
│ │ │PWT │
├─────────────────┼───────────────────────────┼───────────────────────────┤
│
Для сварки │ 100% CO │Автоматическая сварка │
│заполняющих
и │ 2
│проволокой сплошного
│
│облицовочного │ │сечения
сварочными │
│слоев
шва │ │головками ВГС
фирмы │
│соединений
труб │ │Autoweld
Systems <*> │
│из
сталей с
├───────────────────────────┼───────────────────────────┤
│классом
прочности│ 45 +/- 5% Ar, │Автоматическая │
│до
К60 включ. │ 55 +/- 5% CO │односторонняя сварка │
│ │ 2 │проволокой сплошного │
│ │ │сечения
комплексом │
│ │ │оборудования
CWS.02 фирмы │
│ │ │PWT │
│
├───────────────────────────┼───────────────────────────┤
│ │ 50% Ar, │Автоматическая │
│ │ 50% CO │односторонняя сварка │
│ │ 2 │проволокой сплошного │
│ │ │сечения
комплексом │
│ │ │оборудования
Saturnax │
│ │ │фирмы
Serimax │
│
├───────────────────────────┼───────────────────────────┤
│ │ 75% Ar, │Автоматическая │
│ │ 25% CO │односторонняя сварка │
│ │ 2 │проволокой сплошного │
│ │ │сечения
сварочными │
│ │ │головками
П-200 (P-200), │
│ │ │П-260 (P-260)
фирмы │
│ │ │CRC-Evans AW
<**> │
│ │
│Автоматическая
│
│ │ │односторонняя сварка │
│ │ │порошковой
проволокой │
│ │ │сварочными
головками M300-C│
│ │ │(M300) фирмы
CRC-Evans AW │
│
├───────────────────────────┼───────────────────────────┤
│ │ 85% Ar, │Автоматическая │
│ │ 15% CO │односторонняя сварка │
│ │ 2 │проволокой сплошного │
│ │ │сечения
сварочными │
│ │ │головками
П-600 (P-600) │
│ │ │фирмы CRC-Evans AW │
├─────────────────┴───────────────────────────┴───────────────────────────┤
│
<*> Сварка облицовочного слоя шва выполняется в смеси защитных
газов│
│(80%
Ar/20% CO ).
│
│ 2
│
│
<**> Сварка облицовочного
слоя шва выполняется
в углекислом газе│
│(100%
CO ).
│
│ 2
│
└─────────────────────────────────────────────────────────────────────────┘
Таблица Д.19
Материалы и
дополнительная оснастка
для термитной
сварки-пайки выводов
электрохимической
защиты
┌─────────────────┬───────────────────┬─────────────┬─────────────────────┐
│ Назначение
│ Наименование │
ТУ │ Производитель │
│ │ материалов и │ │ │
│ │ дополнительной │ │ │
│ │ оснастки │ │ │
├─────────────────┼───────────────────┼─────────────┼─────────────────────┤
│
Для сварки │ Паяльно-сварочные
│ТУ 1718-001- │ ООО
"Велд Форс", │
│выводов
ЭХЗ │ стержни из │56222072-2005│(г.
Санкт-Петербург, │
│к
газопроводам │ медных
термитных │ │ Россия) │
│диаметром
от │смесей (ЭХЗ-1150) │ │ │
│Д 100 до Д
500 │ с многоразовой │ │ │
│
у у │графитовой оправкой│ │ │
├─────────────────┼───────────────────┼─────────────┼─────────────────────┤
│
Для сварки │ Паяльно-сварочные
│ТУ 1718-001- │ ООО
"Велд Форс", │
│выводов
ЭХЗ │ стержни из медных
│56222072-2005│(г. Санкт-Петербург, │
│к
газопроводам │ термитных
смесей │ │ Россия) │
│диаметром
от │ (ЭХЗ-1152) с │ │ │
│Д 600 до Д
1400│ многоразовой │ │ │
│
у у │графитовой оправкой│ │ │
├─────────────────┼───────────────────┼─────────────┼─────────────────────┤
│
Для сварки │ Разовая │ ТУ
│ ООО │
│выводов
ЭХЗ │ тигель-форма │ 522152-012-
│"Электро-химизделия",│
│к
газопроводам │с медной термитной
│ 59947226-05 │ (г. Лесной, Россия) │
│диаметром
от │ смесью (РТФ) │ │ │
│Д 500 до Д
1400│
│ │ │
│
у у │ │ │ │
├─────────────────┼───────────────────┼─────────────┼─────────────────────┤
│
Для сварки │ Одноразовая │ТУ 1793-005- │ ООО НПО │
│выводов
ЭХЗ │ тигель-форма с │43750384-2006│
"Нефтегазкомплекс", │
│к
газопроводам │ медной
термитной │ │(г. Саратов, Россия)
│
│диаметром
от │ смесью (РТФ-НГК) │ │ │
│Д 500 до Д
1400│
│ │ │
│
у у │ │ │ │
├─────────────────┼───────────────────┼─────────────┤ │
│
Для сварки │ Термитная
медная │ТУ 1793-001- │ │
│выводов
ЭХЗ │ смесь с │43750384-2006│ │
│к
газопроводам │ многоразовой │ │ │
│диаметром
от │ графитовой │ │ │
│Д 100 до Д
1400│ тигель-формой │ │ │
│
у у │ │ │ │
├─────────────────┼───────────────────┼─────────────┤ │
│Для
сварки │ Термокарандаш
из │ТУ 1793-004- │ │
│выводов
ЭХЗ │ прессованной │43750384-2006│ │
│к
газопроводам │ термитной
медной │ │ │
│диаметром
от │ смеси на клеевой │ │ │
│Д 100 до Д
1400│ основе с │ │ │
│
у у │
многоразовой │ │ │
│ │ графитовой │ │ │
│ │ тигель-формой │ │ │
└─────────────────┴───────────────────┴─────────────┴─────────────────────┘
Приложение
Е
(обязательное)
СВАРОЧНОЕ
ОБОРУДОВАНИЕ ДЛЯ РУЧНОЙ, МЕХАНИЗИРОВАННОЙ
И АВТОМАТИЧЕСКОЙ
СВАРКИ ГАЗОПРОВОДОВ, ОБОРУДОВАНИЕ
ДЛЯ ПОДОГРЕВА
<*>
--------------------------------
<*>
Требования к оборудованию, приведенные в настоящем разделе, распространяются на
вновь изготавливаемое оборудование.
Таблица Е.1
Требования
к техническим характеристикам
сварочных
выпрямителей тиристорного и инверторного типа
для ручной дуговой
сварки покрытыми электродами
┌──────────────────────────────────────────────┬──────────────────────────┐
│ Наименование показателя │ Требование │
├──────────────────────────────────────────────┼──────────────────────────┤
│
Номинальный сварочный ток при ПН = 60%,
│ 250 А │
│длительности
цикла 5 мин, при температуре
│
│
│окружающей
среды 40 °C не менее
│
│
├──────────────────────────────────────────────┼──────────────────────────┤
│
Диапазон рабочих токов
│ от 50 до 250 А
включ. │
├──────────────────────────────────────────────┼──────────────────────────┤
│
Диапазон рабочего напряжения
│ от 22 до 30 В включ. │
├──────────────────────────────────────────────┼──────────────────────────┤
│
Напряжение холостого хода
│ от 70 до 100 В
включ. │
├──────────────────────────────────────────────┼──────────────────────────┤
│
Диапазон регулировки тока короткого
│
│
│замыкания,
в процентах от номинального
│
│
│значения
сварочного тока, в зависимости
│
│
│от
диаметра электрода и пространственного
│
│
│положения
при сварке электродами:
│
│
│ - с основным видом покрытия │ от 100% до 150% включ. │
│ - с целлюлозным видом покрытия │ от 100% до 180% включ. │
├──────────────────────────────────────────────┼──────────────────────────┤
│
Время перехода от тока короткого замыкания
│ 0,01 с │
│к
рабочим установленным значениям тока
│
│
│для
сварочных выпрямителей тиристорного типа
│
│
│не
более
│
│
├──────────────────────────────────────────────┼──────────────────────────┤
│
Наклон вольт-амперных характеристик
│
│
│в
диапазоне рабочих токов при сварке
│
│
│электродами: │ │
│ - с основным видом покрытия │ от 0,7 до 1,0 В/А
включ. │
│ - с целлюлозным видом покрытия │от 0,35 до 0,45 В/А
включ.│
├──────────────────────────────────────────────┼──────────────────────────┤
│
Дистанционное регулирование сварочного тока
│ +/- 5 А │
│при
длине сварочных кабелей не менее 40 м
│
│
│с
точностью не хуже
│
│
├──────────────────────────────────────────────┼──────────────────────────┤
│
Переключение полярности сварочного тока │ │
│электронным
или механическим способом
│
│
└──────────────────────────────────────────────┴──────────────────────────┘
Таблица Е.2
Требования к
техническим характеристикам
сварочных
выпрямителей тиристорного и инверторного типа
для
механизированной сварки
┌────────────────────────────────────────────────────┬────────────────────┐
│ Наименование показателя │ Требование │
├────────────────────────────────────────────────────┼────────────────────┤
│
Номинальный сварочный ток при ПВ = 100%, │ │
│длительности
цикла 10 мин и при температуре
│ │
│окружающей
среды 40 °C при сварке проволокой: │ │
│ - сплошного сечения не менее │ 250 А │
│ - самозащитной порошковой не менее │ 315 А │
├────────────────────────────────────────────────────┼────────────────────┤
│
Диапазон регулирования напряжения на дуге │от 14 до 30 В включ.│
├────────────────────────────────────────────────────┼────────────────────┤
│
Наклон жесткой вольт-амперной характеристики │ 0,045 В/А │
│не
более │ │
├────────────────────────────────────────────────────┼────────────────────┤
│
Дистанционное регулирование напряжения на дуге при │ +/- 0,5 В │
│длине
сварочных кабелей не менее 40 м с точностью
│ │
│не
хуже
│ │
└────────────────────────────────────────────────────┴────────────────────┘
Таблица Е.3
Требования к
техническим характеристикам механизмов
подачи сварочной
проволоки и сварочных горелок
для
механизированной сварки
┌─────────────────────────────────────────────┬───────────────────────────┐
│ Наименование показателя │ Требование │
├─────────────────────────────────────────────┼───────────────────────────┤
│
Диапазон скорости подачи электродной
│от 0,6 до 16,0 м/мин включ.│
│проволоки
│
│
├─────────────────────────────────────────────┼───────────────────────────┤
│
Диаметр проволоки:
│
│
│ - сплошного сечения │ от 0,8 до 2,0 мм включ. │
│ - самозащитной порошковой │ от 1,6 до 3,2 мм включ. │
├─────────────────────────────────────────────┼───────────────────────────┤
│
Возможность изменения скорости подачи
│
│
│сварочной
проволоки переключателем на
│
│
│сварочной
горелке │ │
└─────────────────────────────────────────────┴───────────────────────────┘
Таблица Е.4
Требования к
техническим характеристикам
сварочных
выпрямителей тиристорного и инверторного типа
для автоматической
сварки плавящимся электродом
в защитных газах
Наименование показателя
|
Требование
|
Номинальный
сварочный ток при ПВ = 100%,
длительности цикла 10 мин и при температуре
окружающей среды 40 °C не менее
|
315 А
|
Диапазон
регулирования напряжения на дуге
|
от
14 до 30 В включ.
|
Наклон
жесткой вольт-амперной характеристики
не более
|
0,045 В/А
|
Дистанционное
регулирование параметров сварочного
процесса при длине сварочных и управляющих кабелей
не менее 40 м с точностью не хуже
|
+/- 0,5 В
|
Таблица Е.5
Требования к
техническим характеристикам
сварочных головок
для автоматической сварки
плавящимся
электродом в защитных газах
┌─────────────────────────────────────────────┬───────────────────────────┐
│ Наименование показателя │ Требование │
├─────────────────────────────────────────────┼───────────────────────────┤
│
Диаметр свариваемых труб
│ до 14 мм включ. │
├─────────────────────────────────────────────┼───────────────────────────┤
│
Диапазон скорости подачи электродной
│от 0,6 до 16,0 м/мин включ.│
│проволоки
│
│
├─────────────────────────────────────────────┼───────────────────────────┤
│
Диаметр проволоки: │ │
│ - сплошного сечения │ от 0,8 до 2,0 мм включ. │
│ - самозащитной порошковой │ от 1,2 до 2,2 мм включ. │
├─────────────────────────────────────────────┼───────────────────────────┤
│
│ -1 │
│
Частота колебаний электродной проволоки
│ от 0 до 200 мин
включ. │
├─────────────────────────────────────────────┼───────────────────────────┤
│
Амплитуда колебаний электродной проволоки
│ по ширине разделки │
├─────────────────────────────────────────────┼───────────────────────────┤
│
Время задержки электродной проволоки в
│ от 0,0 до 1,2 с
включ. │
│крайних
положениях │ │
├─────────────────────────────────────────────┼───────────────────────────┤
│
Угол наклона электродной проволоки
│ от 0° до 10°
включ. │
└─────────────────────────────────────────────┴───────────────────────────┘
Таблица Е.6
Требования к
техническим характеристикам
сварочных
выпрямителей тиристорного и инверторного
для автоматической
сварки под флюсом
Наименование показателя
|
Требование
|
Номинальный
сварочный ток при ПВ = 100%,
длительности цикла 10 мин и при температуре
окружающей среды 40 °C при сварке проволокой
сплошного сечения не менее
|
1250 А
|
Диапазон
регулирования напряжения на дуге
|
от
24 до 56 В включ.
|
Наклон
жесткой вольт-амперной характеристики
не более
|
0,045 В/А
|
Дистанционное
регулирование напряжения на дуге при
длине сварочных кабелей не менее 40 м с точностью
не хуже
|
+/- 0,5 В
|
Таблица Е.7
Требования
к техническим характеристикам сварочных головок
для автоматической
сварки под флюсом
Наименование показателя
|
Требование
|
Диаметр
свариваемых труб
|
до 1420 мм включ.
|
Диапазон
скорости подачи электродной проволоки
|
от
0,2 до 5,0 м/мин включ.
|
Диаметр
электродной проволоки сплошного
сечения
|
3,0; 3,2; 4,0 мм
|
Вылет
электродной проволоки
|
от 30 до 80 мм включ.
|
Поперечная
корректировка положения электродной
проволоки не хуже
|
+/- 75 мм
|
Бесступенчатая
регулировка скорости подачи
электродной проволоки
|
|
Угол
наклона электродной проволоки
|
0° до 30° включ.
|
Вместимость
бункера для флюса
|
не менее 10 дм3
|
Рабочий
ход суппорта вертикального перемещения
сварочной головки не менее
|
100 мм
|
Тормозной
момент кассеты с электродной
проволокой не менее
|
1,5 Н x м
|
Таблица Е.8
Сварочные
выпрямители тиристорного типа для ручной,
механизированной и
автоматической сварки
Марка
|
Технические характеристики
|
Производитель
|
Номинальный
сварочный
ток
|
Пределы
регулирования
сварочного
тока, А
|
Напряжение
холостого
хода, В
|
Номинальное
рабочее
напряжение,
В
|
Способ
сварки
|
1
|
2
|
3
|
4
|
5
|
6
|
7
|
ВДУ 306
МТУЗ
|
315
А, при
ПН 100%
|
30 - 350
|
не более
100
|
21 - 32
|
РД
|
ЗАО
"Уралтермосвар"
(Россия)
|
11 - 22
|
РАД
|
16 - 29
|
МП
МПС
|
ВДУ 506
МТУЗ
|
500
А, при
ПН 60%
|
30 - 500
|
не более
100
|
21 - 40
|
РД
|
ЗАО
"Уралтермосвар"
(Россия)
|
11 - 30
|
РАД
|
16 - 39
|
МП
МПС
|
ВД-306Д
|
300
А, при
ПВ 60%
|
50 - 350
|
не более
95
|
22 - 34
|
РД
|
ЗАО
"НПФ "ИТС"
(Россия)
|
10 - 350
|
12 - 24
|
РАД
|
ВД-306ДК
|
300
А, при
ПВ 60%
|
40 - 350
|
не более
85
|
17 - 34
|
РД
|
ЗАО
"НПФ "ИТС"
(Россия)
|
12 - 350
|
11 - 24
|
РАД
|
50 - 350
|
14 - 36
|
МП
МПС
|
ВД-506Д
|
500
А, при
ПВ 60%
|
50 - 350
|
не более
95
|
22 - 40
|
РД
|
ЗАО
"НПФ "ИТС"
(Россия)
|
12 - 500
|
12 - 30
|
РАД
|
ВД-506ДК
|
500
А, при
ПВ 60%
|
50 - 500
|
не более
85
|
22 - 40
|
РД
|
ЗАО
"НПФ "ИТС"
(Россия)
|
12 - 500
|
12 - 30
|
РАД
|
50 - 500
|
17 - 40
|
МП
МПС
|
ВДУ-1250УЗ
|
1250
А, при
ПВ 100%
|
250 - 1250
|
55
|
44
|
АФ
|
ЗАО
"НПФ "ИТС"
(Россия)
|
Idealarc
DC-400
|
450
А, при
ПВ 60%
|
60 - 500
|
54
|
12 - 42
|
РД
|
The Lincoln
Electric
Company (США)
|
45
|
12 - 42
|
РАД
МП
МПС
АПИ
|
Idealarc
DC-600
|
680
А, при
ПВ 60%
|
90 - 850
|
не более
100
|
24 - 42
|
РД
|
The Lincoln
Electric
Company (США)
|
70 - 850
|
13 - 42
|
МП
МПС
АФ
|
Idealarc
DC 1000
|
1000
А, при
ПВ 100%
|
150 - 1300
|
не более
100
|
16 - 46
|
МП
МПС
АФ
|
The Lincoln
Electric
Company (США)
|
LHF 400
|
315
А, при
ПВ 60%
|
8 - 400
|
80 - 87
|
20 - 36
|
РД,
РАД
|
ESAB AB
(Швеция)
|
LHF 405
Pipeweld
|
310
А, при
ПВ 60%
|
10 - 400
|
75
|
20 - 36
|
РД,
РАД
|
ESAB AB
(Швеция)
|
LAF 1250
|
1250
А, при
ПВ 100%
|
40 - 1250
|
51
|
22 - 44
|
АФ
|
ESAB AB
(Швеция)
|
Power
Wave
AC/DC 1000
|
1000
А, при
ПВ 100%
|
100 - 1000
|
не более
100
|
44
|
АФ
|
The Lincoln
Electric
Company (США)
|
Примечание. Обозначение способов сварки
по 3.3.
|
Таблица Е.9
Сварочные
выпрямители инверторного типа для ручной,
механизированной и
автоматической сварки
Марка
|
Технические характеристики
|
Производитель
|
Номинальный
сварочный
ток
|
Пределы
регулирования
сварочного
тока, А
|
Напряжение
холостого
хода, В
|
Способ
сварки
|
ДС 250.33
|
250
А, при
ПВ 60%
|
25 - 250
|
не более
85
|
РД
РАД
|
ООО
"Технотрон"
(Россия)
|
Pico 260
|
260
А, при
ПВ 60%
|
10 - 260
|
99
|
РД
|
ООО
"Инвертор-Плюс"
(Россия)
|
"Магма-315"
|
315
А, при
ПН 60%
|
5 - 350
|
55 - 85
|
РД
РАД
|
ООО
"НПП "ФЕБ"
(Россия)
|
"Форсаж-315М"
|
315
А, при
ПР 50%
|
20 - 315
|
70
|
РД
|
ФГУП "ГРПЗ"
(Россия)
|
"Форсаж-250М"
|
250
А, при
ПР 80%
|
15 - 250
|
80
|
РД
|
ФГУП "ГРПЗ"
(Россия)
|
Invertec
V350-PRO
|
350
А, при
ПВ 60%
|
5 - 350
|
80
|
РД
|
The Lincoln
Electric
Company (США)
|
70
|
РАД
|
80
|
МП
МПС
АПИ
|
Invertec
STT II
|
350
А, при
ПВ 60%
|
0 - 150
(базовый)
0 - 450
(пиковый)
|
не более
85
|
МП
ААДП
|
The Lincoln
Electric
Company (США)
|
Master 3500
|
285
А, при
ПВ 60%
|
10 - 350
|
70
|
РД
|
KEMPPI
(Финляндия)
|
Примечание. Обозначение способов сварки
по 3.3.
|
Таблица Е.10
Специальные
требования к сварочному оборудованию
┌─────────────────────────────────────────────────────┬───────────────────┐
│ Наименование показателя │ Требование │
├─────────────────────────────────────────────────────┼───────────────────┤
│Степень
защиты по ГОСТ 14254 не ниже, включая защиту:│ IP 22 │
│
- от проникновения внешних твердых предметов │ 12,5 мм │
│диаметром
более
│ │
│
- от вредного воздействия в результате проникновения│ до 15 включ. │
│воды
при каплепадении под номинальным углом
│ │
├─────────────────────────────────────────────────────┼───────────────────┤
│Группа
исполнения по допустимым механическим
│ М18 │
│воздействиям
по ГОСТ 17516.1 не ниже
│ │
│
- для механизмов подачи сварочной проволоки, │ М23 │
│сварочных
горелок не ниже
│ │
├─────────────────────────────────────────────────────┼───────────────────┤
│Климатическое
исполнение по ГОСТ 15150, включая
│ УХЛ2 │
│возможность
эксплуатации в диапазоне температур
│ │
│окружающей
среды (рабочее значение):
│ │
│
- для сварочных агрегатов и сварочных установок │от -45 °C до +40 °C│
│
- для сварочных выпрямителей тиристорного типа │от -40 °C до +40 °C│
│
- для сварочных выпрямителей инверторного типа │от -30 °C до +40 °C│
├─────────────────────────────────────────────────────┼───────────────────┤
│Возможность
эксплуатации при относительной влажности │ 80% │
│окружающей
среды (среднемесячное значение) при
│ │
│температуре
20 °C
│ │
└─────────────────────────────────────────────────────┴───────────────────┘
Таблица Е.11
Требования
к техническим характеристикам
сварочных агрегатов
для ручной дуговой сварки
покрытыми
электродами
Наименование показателя
|
Требование
|
Номинальный
сварочный ток при ПН 60%,
длительности цикла 5 мин, температуре окружающей
среды 40 °C не менее
|
250 А
|
Диапазон
рабочих токов
|
от
50 до 250 А включ.
|
Диапазон
рабочего напряжения
|
от
22 до 30 В включ.
|
Напряжение
холостого хода
|
от
70 до 100 В включ.
|
Время
перехода от тока короткого замыкания
к установленным значениям тока не более
|
0,01 с
|
Дистанционное
регулирование сварочного тока при
длине сварочных кабелей не менее 40 м с точностью
не хуже
|
+/- 5 А
|
Допустимые
отклонения величины сварочного тока
(напряжения) из-за взаимного влияния постов от
установленных значений
|
+/- 5%
|
Допустимые
отклонения величины сварочного тока
(напряжения) при колебаниях частоты вращения
приводного двигателя +/- 10%
|
+/- 2%
|
Переключение
полярности сварочного тока электронным
или механическим способом
|
|
Таблица Е.12
Требования к
техническим характеристикам
сварочных агрегатов
для механизированной сварки
проволокой
сплошного сечения в углекислом газе
и самозащитной
порошковой проволокой
┌────────────────────────────────────────────────────┬────────────────────┐
│ Наименование показателя │ Требование │
├────────────────────────────────────────────────────┼────────────────────┤
│Номинальный
сварочный ток при ПВ 100%,
│ │
│длительности
цикла 10 мин, при температуре
│ │
│окружающей
среды 40 °C при сварке проволокой:
│ │
│
- сплошного сечения не менее │ 250 А │
│
- самозащитной порошковой не менее │ 315 А │
├────────────────────────────────────────────────────┼────────────────────┤
│Наклон
жесткой вольт-амперной характеристики
│ 0,045 В/А │
│не
более
│ │
├────────────────────────────────────────────────────┼────────────────────┤
│Диапазон
регулирования напряжения на дуге
│от 14 до 30 В включ.│
├────────────────────────────────────────────────────┼────────────────────┤
│Дистанционное
регулирование напряжения на дуге
│ +/- 0,5 В │
│при
длине сварочных кабелей не менее 40 м не хуже
│ │
├────────────────────────────────────────────────────┼────────────────────┤
│Допустимые
отклонения величины сварочного тока
│ +/- 5% │
│(напряжения)
из-за взаимного влияния постов
│ │
│от
установленных значений
│ │
└────────────────────────────────────────────────────┴────────────────────┘
Таблица Е.13
Требования
к техническим характеристикам
автономных
многопостовых передвижных и самоходных
сварочных установок
для ручной, механизированной
и автоматической
сварки
┌──────────────────────────────────────────────────────────────┬──────────┐
│ Наименование показателя │Требование│
├──────────────────────────────────────────────────────────────┼──────────┤
│Потребляемая
мощность одного сварочного поста:
│ │
│
- при ручной дуговой сварке при ПН 60% не менее │7,5 кВ x А│
│
- при механизированной и автоматической сварке плавящимся │9,5 кВ x А│
│электродом
в защитных газах и открытой дугой при ПВ 100% │ │
│не
менее
│ │
│Допустимые
отклонения величины сварочного тока и напряжения │
+/- 5% │
│из-за
взаимного влияния постов от установленных значений │ │
├──────────────────────────────────────────────────────────────┼──────────┤
│Допустимые
отклонения величины входного напряжения питающей │ +/- 10% │
│сети
от установленных значений │ │
├──────────────────────────────────────────────────────────────┼──────────┤
│Допустимые
отклонения частоты вращения приводного двигателя │ +/- 10% │
│от
установленных значений
│ │
└──────────────────────────────────────────────────────────────┴──────────┘
Таблица Е.14
Сварочные
агрегаты для ручной и механизированной сварки
Марка
|
Технические характеристики
|
Производитель
|
Номинальный
сварочный
ток, А
|
Пределы
регулирования
сварочного
тока одного
поста, А
|
Напряжение
холостого
хода, В
|
Номинальное
рабочее
напряжение
поста, В
|
Способ
сварки
|
АДДУ-4001У1
<*>
|
400
А, при
ПН 60%
|
40 - 400
|
не более
100
|
21,6
- 36,0
|
РД
|
ЗАО
"Уралтер-
мосвар"
(Россия)
|
60 - 400
|
15 - 40
|
МП
МПС
|
АДДУ-2x2501У1
<**>
|
400
А, при
ПН 60%
|
40 - 400
|
не более
100
|
21,2
- 30,0
|
МП
|
То же
|
40 - 400
|
15 - 30
|
МПС
|
АДПР-2x2501ВУ1
<***>
|
250
А, при
ПН 60%
|
30 - 250
|
не более
100
|
21,6 - 36
|
РД
|
"
|
АДД-4004МУ1
|
400
А, при
ПН 60%
|
60 - 430
|
80 - 90
|
21,6 - 36
|
РД
|
"
|
АДД-4004МВУ1
|
400
А, при
ПН 60%
|
60 - 430
|
80 - 90
|
21,6 - 36
|
РД
|
"
|
АДД-2x2501ВУ1
|
250
А, при
ПН 60%
|
30 - 250
|
не более
100
|
21,2 - 30
|
РД
|
"
|
АДД-4x2501ВУ1
|
250
А, при
ПН 60%
|
30 - 250
|
80 - 90
|
21,2 - 30
|
РД
|
"
|
АДД-4004ПИУ1
|
400
А, при
ПН 60%
|
45 - 430
|
90
|
36
|
РД
РАД
|
ЗАО "Искра"
(Россия)
|
АДД-4004ПРУ1
|
400
А, при
ПН 60%
|
60 - 450
|
не более
100
|
36
|
РД
|
То же
|
АДД-5001ИУ1
|
500
А, при
ПН 60%
|
35 - 530
|
90
|
40
|
РД
|
"
|
АДД-2x2502ИУ1
|
250
А, при
ПН 60%
|
50 - 530
|
не более
100
|
30
|
РД
|
"
|
<*> В модификации АДДУ-4001ПРУ1 рекомендуется в
т.ч. для
воздушно-плазменной резки труб.
<**> В модификации АДДУ-2x2501ПРУ1 рекомендуется в
т.ч. для
воздушно-плазменной резки труб.
<***> Рекомендуется в т.ч.
для воздушно-плазменной резки труб.
|
Е.1.
Установки индукционного нагрева, установки для нагрева с применением
электронагревателей сопротивления, для нагрева с применением
электронагревателей комбинированного действия должны обеспечивать:
- возможность
нагрева и термообработки всех видов свариваемых соединений труб, СДТ, ЗРА
различных толщин, диаметров и конструкций до заданной температуры;
- необходимый
коэффициент мощности
для наибольшей производительности нагрева;
- максимальную
мощность всех каналов нагрева;
- ручное и
автоматическое (программируемое) регулирование процесса нагрева;
- наличие
отдельного программного устройства и возможность контроля температуры каждого
канала нагрева;
- плавное или
ступенчатое регулирование подаваемой мощности вторичной цепи;
- цикл нагрева
максимальной мощностью в течение длительного времени (десятки часов);
- электрическую
мощность и выходное (вторичное) напряжение источника питания с учетом потерь в
участках цепи электронагрева;
- устойчивую работу
источника питания электронагревателей при ПН 100%, продолжительный срок службы
источника питания;
- минимально
возможные габаритные размеры и массу для обеспечения перемещения в условиях
трассы;
- возможность
проведения сварки при сопутствующем (межслойном) подогреве.
Е.2.
Электронагреватели индукционные, сопротивления и комбинированного действия типа
КЭН должны обеспечивать:
- необходимый
коэффициент мощности
для наибольшей производительности нагрева;
- величину мощности
и удельной мощности (на 1 см2 поверхности нагрева), необходимую для нагрева до
заданной температуры;
- высокую
температуростойкость;
- высокий ресурс
работы при максимальной нагрузке (в пределах от 8 до 10 ч на одно сварное
соединение);
- гибкость и
механическую прочность, необходимую для частых перестановок, с ресурсом не
менее 300 ч;
- возможность
подогрева без перемещения отдельных секций.
Е.3.
Теплоизоляционные материалы должны обеспечивать:
- сохранение тепла,
образовавшегося при нагреве при минимизации тепловых потерь;
- безопасность
персонала от ожогов при выполнении операций нагрева;
- максимальную
температуроемкость, высокий ресурс работы, отсутствие канцерогенных и
керамических волокон, тонких волокон диаметром менее 6,0 мкм и других вредных
примесей.
Таблица Е.15
Установки
индукционного нагрева токами
средней частоты 400
- 10000 Гц для предварительного
и сопутствующего
(межслойного) подогрева
сварных соединений
Тип
|
Технические характеристики
|
Производитель
|
Мощ-
ность,
кВт
|
Частота, КГц
|
Напряжение,
В
|
Сила
тока
в цепи
нагрева,
А
|
Вид
электро-
нагре-
вателя
|
входная
|
вы-
ходная
|
первич-
ное
|
вто-
ричное
|
Комплект
индукционных
установок
ППЧ-20-10
|
3
x 20
|
0,05
|
10,0
|
3
x 380
|
110
|
3
x 200
|
Гибкий
индуктор
|
ООО "НПП
"Курай"
(Россия)
|
Установка
индукционная
Pro Heat TM 35
|
2
x 35
|
0,05
|
8,0
-
10,0
|
3
x 380
|
460
|
2
x 76
|
Гибкий
индуктор
|
ф. "Миллер"
(США)
|
Установка
индукционная
PIH
|
110
|
0,05
|
0,4
|
380
|
150
|
730
|
Жесткий
индуктор
|
ф. Pipe
Induction
Heat (США)
|
Установка
индукционного
подогрева
Delta 50
|
2
x 35
|
0,05
|
8,0
-
10,0
|
380
|
450
|
150
|
Гибкий
индуктор
|
ф. Parma-
progetti
(Италия)
|
Примечание. Приведенный перечень
установок индукционного нагрева
токами средней частоты
400 - 10000 Гц может дополняться или
пересматриваться по результатам квалификационных испытаний.
|
Таблица Е.16
Установки
индукционного нагрева токами
средней частоты 2500
Гц для предварительного
и сопутствующего
(межслойного) подогрева
и термообработки
сварных соединений
┌─────────────┬──────────────────────────────────────────────────┬────────┐
│ Тип
│ Технические
характеристики │Произ- │
│
├──────┬────────────┬──────────────┬──────┬────────┤водитель│
│ │Мощ- │Частота, КГц│Напряжение, В
│Сила │Вид │ │
│
│ность,├─────┬──────┼───────┬──────┤тока │электро-│ │
│ │кВт │вход-│выход-│первич-│вто- │в цепи│нагре- │
│
│ │ │ная │ная
│ное
│ричное│на-
│вателя │ │
│ │ │ │ │ │ │грева,│ │ │
│ │ │ │ │ │ │А │ │ │
├─────────────┼──────┼─────┼──────┼───────┼──────┼──────┼────────┼────────┤
│Установки │
│ │ │ │ │ │ │ООО "НПП│
│типа
"Интерм"│
│ │ │ │ │ │ │"Курай" │
│с
преобразо- │ │ │ │ │ │ │ │(Россия)│
│вателями
ППЧ │ │ │ │ │ │ │ │ │
│"Интерм │
63 │0,05 │1,6 -
│3 x 380│ 250 │ 250 │ Гибкий │ │
│63-2,4" │ │ │
2,6│ │ 400 │ 160
│индуктор│
│
│ │ │ │ │ │ 800 │
80 │ │ │
│"Интерм │ 100 │0,05 │1,6 - │3 x
380│ 250 │ 400 │ Гибкий │ │
│100-2,4" │ │ │
2,6│ │ 400 │ 250
│индуктор│
│
│ │ │ │ │ │ 800 │ 125
│ │ │
│"Интерм │ 160 │0,05 │1,6 - │3 x
380│ 400 │ 400 │ Гибкий │ │
│160-2,4" │ │ │
2,6│ │ 800 │ 200
│индуктор│
│
│"Интерм │ 200 │0,05 │1,6 - │3 x
380│ 400 │ 500 │ Гибкий │ │
│200-2,4" │ │ │
2,6│ │ 800 │ 250
│индуктор│
│
│"Интерм │ 250 │0,05 │1,6 - │3 x
380│ 400 │ 625 │ Гибкий │ │
│250-2,4" │ │ │
2,6│ │ 800 │ 312
│индуктор│
│
├─────────────┼──────┼─────┼──────┼───────┼──────┼──────┼────────┼────────┤
│Установка │ 250
│0,05 │1,6 - │3 x 380│ 200 │ 326
│ Гибкий │ООО "НПП│
│УТИ-250/2,4 │
│ │ 2,6│ │ 600 │ 420
│индуктор│"ЭЛТЕРМ"│
│ │ │ │ │ │ 800 │ 312
│
│(Россия)│
├─────────────┼──────┼─────┼──────┼───────┼──────┼──────┼────────┼────────┤
│Установки │
│ │ │ │ │ │ │ООО "НПП│
│типа
УИТ │ │
│ │ │ │ │ │"УНИТЕХ"│
│ │ │ │ │ │ │ │ │(Россия)│
│50-2,4 │
50 │0,05 │1,6 -
│3 x 380│ 350 │ 140 │Жесткий │ │
│ │ │ │
2,6│ │ │
│индуктор│ │
│100-2,4 │ 100 │0,05 │1,6 - │3 x
380│ 350 │ 280 │Жесткий │ │
│ │ │ │
2,6│ │ │ │индуктор│ │
│200-2,4 │ 2 x │0,05 │1,6 - │3 x
380│ 350 │ 2 x │Жесткий │ │
│ │ 100 │
│ 2,6│ │ │ 280 │индуктор│ │
├─────────────┴──────┴─────┴──────┴───────┴──────┴──────┴────────┴────────┤
│ Примечание.
Приведенный перечень установок
индукционного нагрева│
│токами
средней частоты 2500 Гц может дополняться или пересматриваться по│
│результатам
квалификационных испытаний. │
└─────────────────────────────────────────────────────────────────────────┘
Таблица Е.17
Установки для
нагрева способом электросопротивления
для
предварительного и сопутствующего (межслойного)
подогрева и
термообработки сварных соединений
Тип
|
Технические характеристики
|
Произ-
водитель
|
Мощность,
кВт
|
Напряжение,
В
|
Число
авто-
номных
кана-
лов
на-
грева
|
Сила тока, А
|
общая
|
на
канал
на-
грева
|
пер-
вич-
ное
|
вто-
рич-
ное
|
пер-
вич-
ная
|
вторич-
ная
сум-
марная
|
вторич-
ная на
канал
нагрева
|
ТП
6-100
|
100
|
16,0
|
380
|
40
-
120
|
6
|
160
|
1560
|
260
|
ООО "НПП
"Курай"
(Россия)
|
РТ-50-6
|
50
|
8,1
|
380
|
30,
60
|
6
|
80
|
910
|
135
|
ООО
"Ремонтные
технологии"
(Россия)
|
РТ-70-6
|
70
|
10,8
|
380
|
30,
60
|
6
|
110
|
1080
|
180
|
то же
|
РТ-100-12
|
100
|
8,1
|
380
|
30,
60
|
12
|
160
|
1620
|
135
|
"
|
РТ-150-12
|
150
|
10,8
|
380
|
30,
60
|
12
|
240
|
2160
|
180
|
"
|
Примечание. Приведенный перечень
установок для нагрева
способом
электросопротивления может дополняться или
пересматриваться по
результатам квалификационных испытаний.
|
Таблица Е.18
Установки
для нагрева с применением электронагревателей
комбинированного
действия для предварительного
и сопутствующего
(межслойного) подогрева
и термообработки
сварных соединений
┌────────────┬───────────────────────────────────────────────┬────────────┐
│ Тип
│ Технические
характеристики │Произ- │
│
├─────────────┬───────────────────┬───────┬─────┤водитель │
│ │Мощность, кВт│ Напряжение, В │Число
│Сила │
│
│
├─────┬───────┼─────────┬─────────┤авто- │тока,│ │
│ │общая│ на
│первичное│вторичное│номных │ А
│ │
│ │ │ канал │ │ │каналов│ │ │
│ │ │нагрева│ │ │нагрева│ │ │
├────────────┼─────┼───────┼─────────┼─────────┼───────┼─────┼────────────┤
│Установка │ 100 │ 90
│ 380 │
120 │ 1
│1000 │ООО "Нагрев"│
│с
ТДФЖ-1002 │ │ │(1 фаза) │ │ │ │
(Россия) │
├────────────┼─────┼───────┼─────────┼─────────┼───────┼─────┼────────────┤
│"Термо-1600"│
120 │ 19 │ 3 x 380 │ 85
│ 6 │ 320 │ ООО "РСП │
│ │ 85 │
20 │ 3 x 380 │ 75
│ 4 │ 320 │ "Алексий" │
│ │ 45 │
21 │ 3 x 380 │ 75
│ 2 │ 320 │ (Россия)
│
├────────────┼─────┼───────┼─────────┼─────────┼───────┼─────┼────────────┤
│"Термо-3000"│
300 │ 32 │ 3 x 380 │ 85
│ 6 │ 360 │ то же
│
│ │ │ 47,5 │ │ 145
│ 9 │
│ │
│
├─────┼───────┼─────────┼─────────┼───────┼─────┤ │
│ │ 200 │ 32
│ 3 x 380 │ 85 │
6 │ 360 │ │
├────────────┴─────┴───────┴─────────┴─────────┴───────┴─────┴────────────┤
│ Примечание. Приведенный перечень установок
для нагрева с применением│
│электронагревателей комбинированного действия
может дополняться или│
│пересматриваться
по результатам квалификационных испытаний. │
└─────────────────────────────────────────────────────────────────────────┘
Приложение
Ж
(рекомендуемое)
ФОРМЫ
ТИПОВЫХ ОПЕРАЦИОННО-ТЕХНОЛОГИЧЕСКИХ КАРТ
СБОРКИ И СВАРКИ
ОПЕРАЦИОННАЯ
ТЕХНОЛОГИЧЕСКАЯ КАРТА (типовая)
сборки и ручной дуговой сварки
электродами с основным видом покрытия неповоротных кольцевых стыковых
сварных соединений труб
|
Организация
|
Наименование
газопровода
|
Диаметр, толщина
стенки, мм
|
Способ сварки
|
Конструктивные
элементы сварных
соединений
|
Шифр карты
|
|
|
|
РД
|
труба + труба
|
|
Характеристика труб
|
Предварительный
подогрев
|
Подготовка под
сварку, сборка
и параметры
сварного шва
|
Сварочные
материалы
|
Но-
мер
ТУ
|
Диаметр,
мм
|
Толщина
стенки,
мм
|
Класс
прочности
|
Временное
сопротивле-
ние
разрыву,
МПа
(кгс/мм2)
|
Эквива-
лент
углерода,
%
|
Просушка перед
сваркой до ___ °C
независимо от
температуры
окружающего воздуха.
Предварительный
подогрев перед
сваркой до ___ °C
независимо от
температуры
окружающего воздуха.
Ширина зоны
подогрева __ мм
в каждую сторону от
свариваемых кромок
|
Рисунок
Минимальное
количество слоев
шва ___
|
Для
сварки
корневого,
подварочного,
заполняющих и
облицовочного
слоев:
- тип
- марка
|
|
|
|
|
|
|
Режимы сварки
|
Дополнительные требования и
рекомендации
|
Сварочные
слои
|
Марка
элек-
трода
|
Диа-
метр,
мм
|
Поляр-
ность
|
Сварочный
ток, А
|
1.
Допустимая минимальная толщина стенки __ мм.
2. Направление сварки всех слоев шва - на подъем.
3. Сварка каждого слоя шва выполняется одновременно не менее
чем двумя сварщиками.
4. Освобождать жимки центратора разрешается после завершения
сварки __ % периметра корневого слоя шва. В случае сварки
термоупрочненных труб освобождать жимки центратора следует
после сварки корневого слоя по всему периметру стыка.
5. Рекомендуется осуществлять сварку без прихваток. В случае
сварки с прихватками их количество должно быть не менее трех,
а длина каждой __ мм. Режим сварки - как для корневого слоя
шва.
6. Разрешается оставлять незаконченными сварные соединения,
если высота сварного шва составляет не менее 2/3 толщины
стенки трубы.
7. Температура на кромках труб перед сваркой корневого слоя
шва (выполнения прихваток) должна быть не ниже установленного
для каждой толщины стенки номинального значения.
8. Межслойная температура должна составлять не менее __ °C
и не более __ °C.
9. При проведении работ не должна нарушаться целостность
изоляции.
10. Электроды перед использованием должны быть прокалены
при температуре __ °C в течение __ ч
|
Корневой
|
|
|
|
|
Подварочный
|
|
|
|
|
Заполняющие
|
|
|
|
|
Облицовочный
|
|
|
|
|
|
|
|
|
|
|
|
|
|
|
|
|
|
|
|
|
|
|
|
|
|
┌──────────────────────────────────────────────────────────────────────────────────────┐
│ ПЕРЕЧЕНЬ И ПОСЛЕДОВАТЕЛЬНОСТЬ
ОПЕРАЦИЙ СБОРКИ И СВАРКИ
│
├───┬──────────┬────────────────────────────────────────────────────────┬──────────────┤
│ N │ Операция │ Содержание операций │ Оборудование │
│п/п│ │
│ и инструмент │
├───┼──────────┼────────────────────────────────────────────────────────┼──────────────┤
│ 1 │ Очистка │ Внутреннюю и наружную поверхности
торцов труб очистить │Скребок, щетка│
│
│ труб │от земли и других загрязнений │ │
├───┼──────────┼────────────────────────────────────────────────────────┼──────────────┤
│ 2 │Подготовка│ Осмотреть
наружные и внутренние поверхности торцов
│Ультразвуковой│
│
│ кромок │труб. │толщиномер, │
│
│ │ Устранить
шлифованием на наружной поверхности торцов
│шаблон │
│
│ │труб
царапины, риски, задиры глубиной до __ % от │сварщика УШС, │
│
│
│нормативной толщины стенки, но не более минусового │линейка, │
│
│ │допуска на
толщину стенки по ТУ или ГОСТ.
│шлифмашинка, │
│
│ │ Забоины и
задиры кромок глубиной до __ мм ремонтировать│калибратор, │
│
│
│электродами с основным видом покрытия типа Э50А (Е7016)
│газовая │
│
│ │диаметр
2,5 - 3,25 мм с предварительным подогревом
│горелка, │
│
│ │согласно
требованиям раздела "Предварительный подогрев".│контактный │
│
│ │ Зачистить
отремонтированные кромки труб шлифованием,
│термометр, │
│
│ │при этом
должна быть восстановлена требуемая разделка
│термокарандаш │
│
│ │кромок, а
толщина стенки трубы не должна быть выведена
│ │
│
│ │за пределы
минусового допуска.
│ │
│
│ │ Вмятины
на торцах труб глубиной до __ мм (__ % диаметра│ │
│
│ │труб)
выправить безударным разжимным устройством │ │
│
│ │с местным подогревом трубы до __
°C независимо │ │
│
│ │от
температуры окружающего воздуха. Торцы труб с │ │
│
│ │вмятинами
более __ мм (__ % диаметра труб) обрезать по
│ │
│
│ │периметру
и обработать механическим способом с требуемой│ │
│
│ │разделкой
кромок.
│ │
│
│ │ Наружное
усиление заводского шва сошлифовать
│ │
│
│ │заподлицо
с поверхностью трубы на длине __ мм от торца. │ │
│
│ │ Зачистить
до чистого металла прилегающие к кромкам
│ │
│
│ │внутреннюю
и наружную поверхности трубы на ширину
│ │
│
│ │не менее
__ мм
│ │
├───┼──────────┼────────────────────────────────────────────────────────┼──────────────┤
│ 3 │ Подогрев │ Осуществить
предварительный подогрев до температуры,
│Кольцевой │
│
│ │указанной
в разделе "Предварительный подогрев". В том │подогреватель,│
│
│ │случае,
если подогрев не требуется, произвести просушку │контактный │
│
│ │торцов
труб путем нагрева до __ °C при наличии следов
│термометр, │
│
│ │влаги или
наледи на кромках и/или при температуре
│термокарандаш │
│
│
│окружающего воздуха ниже __ °C. │ │
│
│ │ Замер
температуры торцов труб осуществлять не менее чем│ │
│
│ │в трех
точках по периметру стыка на расстояние ___ мм от│ │
│
│ │торцов
труб.
│ │
│
│ │ Снять
подогреватель
│ │
├───┼──────────┼────────────────────────────────────────────────────────┼──────────────┤
│ 4 │
Сборка │ Осуществить сборку
труб на _______________ центраторе. │Центратор ___,│
│
│ │ Смещение кромок должно быть
равномерно распределено по │шаблон
│
│
│ │периметру
стыка. Максимальная величина распределенного
│сварщика │
│
│ │смещения
не должна превышать __ от нормативной толщины
│УШС-3, линейка│
│
│
│стенки.
│ │
│
│ │ Величина
зазора между стыкуемыми кромками труб должна
│ │
│
│ │составлять
__ мм - в случае применения электродов диам. │ │
│
│ │3,0 - 3,25
мм, и __ мм - в случае применения электродов │ │
│
│ │диам. 2,5
мм
│ │
├───┼──────────┼────────────────────────────────────────────────────────┼──────────────┤
│ 5 │
Сварка │ В случае сварки с
прихватками их следует выполнить
│Наружный │
│
│ │равномерно
по периметру стыка. Зачистить прихватки
│центратор, │
│
│ │и
обработать шлифовальным кругом начальный и конечный │сварочный │
│
│ │участки
каждой из них.
│источник, │
│
│ │ Выполнить
сварку корневого слоя шва электродами
│шлифмашинка, │
│
│ │с основным
видом покрытия. │газовая │
│
│ │ Тщательно
зашлифовать абразивным кругом корневой слой
│горелка, │
│
│ │шва.
│контактный │
│
│ │
Осуществить визуальный контроль корневого слоя шва │термометр, │
│
│ │изнутри
трубы. При необходимости выполнить подварку
│шаблон │
│
│ │изнутри
трубы электродами с основным видом покрытия
│сварщика УШС, │
│
│ │участков,
имеющих непровары, несплавления и смещения
│линейка │
│
│ │кромок
более __мм. Подваренный слой должен иметь ширину │ │
│
│ │___ мм и
усиление __ мм.
│ │
│
│ │ Выполнить сварку заполняющих и
облицовочного слоев шва │
│
│
│
│электродами с основным видом покрытия. │ │
│
│ │
Производить послойную зачистку слоев от шлака и брызг. │ │
│
│ │ Выровнять
шлифмашинкой или напильником видимые грубые
│ │
│
│ │участки
поверхности облицовочного слоя шва и зачистить
│ │
│
│
│прилегающую поверхность трубы │ │
├───┴──────────┴────────────────────────────────────────────────────────┴──────────────┤
│Не оговоренные в данной технологической карте
операции должны выполняться
│
│в соответствии с требованиями: СТО Газпром
"Инструкция по технологиям
│
│сварки при строительстве и ремонте
промысловых и магистральных │
│газопроводов. Часть I"
│
├───────────────────┬───────────┬─┬─────────┬─┬──────────┬─┬─────┬─────────────────────┤
│ │ │ │ │ │ │ │ │ │
│Карта утверждена: │ │ │ │ │ │ │Дата:│"__"
________ ____ г.│
├───────────────────┼───────────┼─┼─────────┼─┼──────────┼─┼─────┼─────────┬───────────┤
│ │ должность │
│ подпись │ │
Ф.И.О. │ │ │ │ │
├───────────────────┼───────────┼─┼─────────┼─┼──────────┼─┼─────┼─────────┴───────────┤
│ │ │ │ │ │ │ │ │ │
│Карта разработана: │ │ │ │ │ │
│Дата:│"__" ________ ____ г.│
├───────────────────┼───────────┼─┼─────────┼─┼──────────┼─┼─────┼─────────┬───────────┤
│ │ должность │
│ подпись │ │
Ф.И.О. │ │ │ │ │
└───────────────────┴───────────┴─┴─────────┴─┴──────────┴─┴─────┴─────────┴───────────┘
ОПЕРАЦИОННАЯ
ТЕХНОЛОГИЧЕСКАЯ КАРТА (типовая)
сборки и механизированной сварки
проволокой сплошного сечения в углекислом газе корневого слоя шва
и самозащитной порошковой
проволокой заполняющих и облицовочного слоев шва неповоротных
кольцевых стыковых сварных соединений
труб
|
Организация
|
Наименование
газопровода
|
Диаметр,
толщина
стенки, мм
|
Способ сварки
|
Конструктивные
элементы
сварных соединений
|
Шифр карты
|
|
|
|
МП + МПС
|
труба + труба
|
|
Характеристика труб
|
Предварительный
подогрев
|
Подготовка под
сварку, сборка
и параметры сварного
шва
|
Сварочные
материалы
|
Но-
мер
ТУ
|
Диа-
метр,
мм
|
Толщина
стенки,
мм
|
Класс
прочно-
сти
|
Временное
сопротив-
ление
разрыву,
МПа
(кгс/мм2)
|
Экви-
валент
угле-
рода, %
|
Просушка перед сваркой
до __ °C независимо от
температуры окружающего
воздуха. Предварительный
подогрев перед сваркой
до __ °C независимо от
температуры окружающего
воздуха. Ширина зоны
подогрева __ мм в каждую
сторону от свариваемых
кромок
|
Минимальное количество
слоев шва __.
|
Для
сварки
корневого,
заполняющих и
облицовочного
слоев:
- тип
- марка
|
|
|
|
|
|
|
Режимы механизированной сварки корневого
слоя шва
|
Дополнительные требования
и рекомендации
|
Направ-
ление
сварки
|
Скорость
подачи
проволоки
<*>,
м/мин
|
Род тока,
полярность
|
Пико-
вый
ток,
А
|
Базовый
ток, А
|
Вылет
элек-
трода,
мм
|
Расход
газа,
л/мин
|
1.
Допустимая минимальная толщина стенки __ мм.
2. Направление сварки для корневого, заполняющих
и облицовочного слоев шва - на спуск;
подварочного слоя шва - на подъем.
3. Сварка каждого слоя шва выполняется
одновременно не менее чем __ сварщиками.
4. Рекомендуется осуществлять сварку без
прихваток. В случае невозможности осуществления
сварки без прихваток их количество должно быть
не менее __, а длина каждой __ мм. Режим сварки -
как для корневого слоя шва.
5. Разрешается оставлять незаконченными сварные
соединения в случае, если высота сварного шва
составляет не менее __ толщины стенки трубы.
6. Температура на кромках труб перед сваркой
корневого слоя шва (выполнения прихваток) должна
быть не ниже установленного для каждой толщины
стенки номинального значения.
7. Межслойная температура должна составлять
не менее __ °C и не более __ °C.
8. Допускается использование труб с V-образной
разделкой кромок после механизированной газовой
резки и последующей обработкой шлифмашинкой. При
этом угол скоса кромки должен составлять __°.
9. При проведение работ не должна нарушаться
целостность изоляции.
10. Перед выполнением облицовочного слоя следует
недозаполнить разделку на 1 - 2 мм в нижнем
и потолочном положениях.
11. Не допускается приваривать обратный кабель
к телу трубы.
12. Порошковая проволока (при отсутствии прямого
попадания влаги) не требует прокалки перед
использованием
|
|
|
|
|
|
|
|
<*> В положении __ ч сварка
осуществляется с поперечными
колебаниями без задержки на кромках при скорости подачи
проволоки __ м/мин, в положении __ ч без поперечных
колебаний при скорости подачи проволоки __ м/мин.
Скорость изменения заднего фронта
импульса ___.
Установка параметра горячего старта __.
Угол наклона электрода (назад): в
положении __ ч - __°,
в положении __ ч - __°.
|
Режимы сварки заполняющих и облицовочного
слоев шва
|
Сва-
рочные
слои
|
Направ-
ление
сварки
|
Диаметр,
мм
|
Поляр-
ность
|
Сва-
роч-
ный
ток,
А
|
Ско-
рость
подачи
про-
волоки,
м/мин
|
Напряжение,
В
|
|
|
|
|
|
|
|
|
|
|
|
|
|
|
|
|
|
|
|
|
|
При
сварке порошковой проволокой следует строго соблюдать
соотношение между скоростью подачи проволоки и
напряжением
|
|
|
|
|
|
|
|
|
|
|
|
|
|
|
|
|
|
|
|
|
|
|
┌────────────────────────────────────────────────────────────────────────────────────────────────────────┐
│ ПЕРЕЧЕНЬ И
ПОСЛЕДОВАТЕЛЬНОСТЬ ОПЕРАЦИЙ СБОРКИ И СВАРКИ │
├───┬──────────┬────────────────────────────────────────────────────────────────────────┬────────────────┤
│
N │ Операция │ Содержание
операций │ Оборудование │
│п/п│ │
│ и инструмент │
├───┼──────────┼────────────────────────────────────────────────────────────────────────┼────────────────┤
│
1 │ Очистка │ Внутреннюю и
наружную поверхности концов труб, свободных от │Скребок, щетка │
│ │
труб │изоляции, очистить
от земли и других загрязнений │ │
├───┼──────────┼────────────────────────────────────────────────────────────────────────┼────────────────┤
│
2 │Подготовка│ Осмотреть поверхность и кромки труб.
│Скребок, щетка, │
│ │
кромок │ Устранить
шлифованием на наружной поверхности неизолированных торцов │рулетка, │
│ │ │труб царапины, риски, задиры
глубиной до __ % от нормативной толщины
│линейка, рейки, │
│ │ │стенки, но не более минусового
допуска на толщину стенки по ТУ или ГОСТ.│машина │
│ │ │ Забоины и задиры фасок
глубиной до __ мм ремонтировать электродами с
│орбитальной │
│ │ │основным видом покрытия типа
Э60 диам. __ мм с предварительным
│резки, │
│ │ │подогревом до __°C; │шлифмашинка, │
│ │ │ Зачистить отремонтированные
поверхности кромок труб шлифованием, при
│шаблон сварщика │
│ │ │этом должна быть восстановлена
заводская разделка кромок, а толщина
│УШС │
│ │ │стенки трубы не должна быть
выведена за пределы минусового допуска.
│ │
│ │ │ Вмятины на концах труб
глубиной до __ мм выправить безударным разжимным│ │
│ │ │устройством с обязательным местным
подогревом изнутри трубы до __ °C
│ │
│ │ │независимо от температуры
окружающего воздуха. В случае повреждения
│ │
│ │ │изоляционного покрытия оно
должно быть отремонтировано.
│ │
│ │ │ Концы труб с забоинами и
задирами фасок более __ мм или вмятинами
│ │
│ │ │более __ мм следует обрезать,
а образовавшуюся кромку обработать станком│ │
│ │ │типа СПК или шлифмашинкой с
восстановлением заводской формы разделки
│ │
│ │ │кромок.
│ │
│ │ │ Зачистить до чистого металла
прилегающие к кромкам внутреннюю и
│ │
│ │ │наружную поверхности трубы на
ширину не менее __ мм
│ │
├───┼──────────┼────────────────────────────────────────────────────────────────────────┼────────────────┤
│
3 │ Подогрев │ Осуществить предварительный подогрев до температуры,
указанной │Кольцевой │
│ │ │в разделе
"Предварительный подогрев". В том случае, если подогрев │подогреватель, │
│ │ │не требуется, произвести
просушку торцов труб путем нагрева до __ °C
│контактный │
│ │ │при наличии следов влаги или
наледи на кромках.
│термометр, │
│ │ │ Замер температуры торцов труб
осуществлять не менее чем в точках
│термокарандаш │
│ │ │по периметру стыка на
расстоянии __ мм от торцов труб │ │
├───┼──────────┼────────────────────────────────────────────────────────────────────────┼────────────────┤
│
4 │ Сборка │ Сборку стыка производить на
внутреннем или наружном центраторе.
│Внутренний/ │
│ │ │ Смещение кромок должно быть
равномерно распределено по периметру стыка.│наружный │
│ │ │Максимальная величина
распределенного смещения не должна превышать __ мм│центратор, │
│ │ │(___% от нормативной толщины
стенки).
│сварочный │
│ │ │ Собрать стык с зазором __
мм.
│источник, │
│ │ │ При сборке на наружном
центраторе в окнах центратора равномерно по
│шлифмашинка, │
│ │ │периметру стыка выполнить
ручной дуговой сваркой на подъем прихватки
│металлическая │
│ │ │электродами типа Э50А диаметр
2,5 - 3,25 мм. Количество прихваток должно│щетка, шаблон │
│ │ │быть не менее ___, а длина
каждой ___ мм. Режим сварки - как для
│сварщика УШС-3, │
│ │ │корневого слоя шва. │линейка │
│ │ │ Снять наружный центратор,
зачистить прихватки и обработать шлифовальным│ │
│ │ │кругом начальный и конечный
участок каждой из них
│ │
├───┼──────────┼────────────────────────────────────────────────────────────────────────┼────────────────┤
│
5 │ Сварка │ После снятия наружного центратора
выполнить сварку корневого слоя шва
│Сварочный │
│ │ │проволокой сплошного сечения в
среде углекислого газа методом STT
│пост для │
│ │ │на спуск, обеспечивая плавный
вход и выход на вышлифованные участки
│механизированной│
│ │ │прихваток.
│сварки │
│ │ │ При использовании внутреннего
центратора выполнить сварку корневого
│проволокой │
│ │ │слоя шва проволокой сплошного
сечения в среде углекислого газа методом
│сплошного │
│ │ │STT на спуск без сварки
прихваток. Сварка выполняется одновременно двумя│сечения: в │
│ │ │сварщиками, при этом каждый
сварщик сваривает один из полупериметров
│углекислом газе │
│ │ │трубы.
│источники │
│ │ │ В месте начала выполнения
корневого слоя шва вторым сварщиком
│сварочного тока │
│ │ │(положение 0 ч) полностью
вышлифовать первые 1 - 2 см шва, выполненные
│"__", механизм
│
│ │
│первым сварщиком, и
далее сошлифовать до минимально возможной величины │подачи сварочной│
│ │ │верхнюю часть шва на длине не
менее 2 см для обеспечения плавного выхода│проволоки
"___",│
│ │ │на сварку второй
полуокружности трубы.
│горелка "___".
│
│ │ │ В месте выполнения
"замка" вторым сварщиком (положение 6 ч) сошлифовать│Сварочный
пост │
│ │ │до минимально возможной
толщины участок корневого слоя шва на длине
│для │
│ │ │не менее 2 см, выполненный
первым сварщиком.
│механизированной│
│ │ │ Произвести тщательную
обработку абразивным кругом поверхности корневого│сварки │
│ │ │слоя шва. │самозащитной │
│ │ │ Провести визуальный контроль
корневого слоя шва снаружи и изнутри
│порошковой │
│ │ │трубы. Усиление корневого слоя
шва изнутри трубы должно составлять __ мм│проволокой: │
│ │ │при ширине __ мм.
│источники │
│ │ │ При необходимости провести
ручную подварку дефектных участков, имеющих │сварочного тока │
│ │ │поверхностные дефекты,
непровары, несплавления, электродами типа Э50А
│"__", механизм
│
│ │ │диаметр 3,0 - 4,0 мм на
постоянном токе обратной полярности. Сварочный
│подачи сварочной│
│ │ │ток: __ А - при сварке электродами
диаметром 3,0/3,2 мм; __ А - при
│проволоки "___",│
│ │ │сварке электродами диаметром
4,0 мм. Подваренный слой должен иметь
│шлифмашинка, │
│ │ │ширину __ мм и усиление __
мм.
│молоток, зубило,│
│ │ │ Выполнить сварку самозащитной
порошковой проволокой на спуск первого
│напильник │
│ │ │и последующих заполняющих
слоев шва.
│ │
│ │ │ Место начала и окончания
процесса сварки каждого слоя (замок шва)
│ │
│ │ │должно располагаться на
расстоянии не менее __ мм от замков предыдущего │ │
│ │ │слоя шва. │ │
│ │ │ По завершении каждого прохода
производить послойную зачистку от шлака
│ │
│ │ │и брызг. При этом после
выполнения первого заполняющего слоя зачистка
│ │
│ │ │производится абразивным кругом
или дисковой проволочной щеткой, всех
│ │
│ │ │последующих слоев - дисковой
проволочной щеткой.
│ │
│ │ │ Перед наложением облицовочного
слоя выполнить сварку порошковой
│ │
│ │ │проволокой корректирующего
слоя в положениях __ ч и __ ч
│ │
│ │ │(ориентировочно). Расположение
корректирующего слоя зависит от толщины
│ │
│ │ │стенки труб и особенности
заполнения разделки каждым сварщиком.
│ │
│ │ │ Выполнить сварку порошковой
проволокой облицовочного слоя шва.
│ │
│ │ │ Выровнять шлифкругом видимые
грубые участки поверхности облицовочного
│ │
│ │ │слоя шва. Зачистить
прилегающую поверхность трубы от шлака и брызг │ │
├───┴──────────┴────────────────────────────────────────────────────────────────────────┴────────────────┤
│
Не оговоренные в данной технологической карте операции должны выполняться │
│в
соответствии с требованиями: СТО Газпром "Инструкция по технологиям │
│сварки
при строительстве и ремонте промысловых и магистральных
│
│газопроводов.
Часть I"
│
├────────────────────────────────────────────────────────────────────────────────────────────────────────┤
│
│
│Карта
утверждена: _______________ _______________ ________________ Дата: "__" __________ ____
г.│
│ должность подпись Ф.И.О. │
│Карта
разработана: ______________ _______________ ________________ Дата: "__" __________ ____
г.│
│ должность подпись Ф.И.О. │
└────────────────────────────────────────────────────────────────────────────────────────────────────────┘
┌────────────────────────────────────────────────────────────────────────────────────────────────────────┐
│ ОПЕРАЦИОННАЯ
ТЕХНОЛОГИЧЕСКАЯ КАРТА (типовая) │
│ сборки и автоматической сварки проволокой
сплошного сечения в защитных газах неповоротных кольцевых │
│ стыковых
сварных соединений труб │
├────────────────┬────────────┬──────────────┬─────────────────────┬───────────────────────┬─────────────┤
│ Организация
│Наименование│
Диаметр, │ Способ сварки │Конструктивные элементы│ Шифр
карты │
│ │газопровода │ толщина
│
│ сварных соединений │ │
│ │ │ стенки, мм
│
│ │ │
├────────────────┼────────────┼──────────────┼─────────────────────┼───────────────────────┼─────────────┤
│ │ │ │ АПГ │ труба + труба │ │
├────────────────┴────────────┴──────────────┼─────────────────────┼───────────────────────┼─────────────┤
│ Характеристика труб │ Предварительный │Подготовка под сварку, │ Сварочные
│
│
│ подогрев
│ сборка и параметры │
материалы │
│
│
│ сварного шва │ │
├───┬─────┬───────┬─────────┬─────────┬──────┼─────────────────────┼───────────────────────┼─────────────┤
│Но-│Диа-
│Толщина│ Класс │Временное│Экви- │ Просушка
перед │ Рисунок │Для сварки │
│мер│метр,│стенки,│прочности│сопро- │валент│сваркой до ___ °C │ │корневого, │
│ТУ
│мм │ мм
│ │тивление │угле- │независимо
от │Минимальное количество
│заполняющих и│
│ │
│ │ │разрыву, │рода,
│температуры │ слоев шва ____ │облицовочного│
│ │
│ │ │МПа │
% │окружающего воздуха.
│ │слоев: │
│ │
│ │ │(кгс/мм2)│ │Предварительный │ │- тип │
├───┼─────┼───────┼─────────┼─────────┼──────┤подогрев
перед │ │- марка │
│ │
│ │ │ │ │сваркой до ___ °C │ │ │
│ │
│ │ │ │ │независимо от │ │ │
│ │
│ │ │ │ │температуры │ │ │
│ │
│ │ │ │ │окружающего воздуха. │ │ │
│ │
│ │ │ │ │Ширина зоны подогрева│ │ │
│ │
│ │ │ │ │___ мм в каждую │ │ │
│ │
│ │ │ │ │сторону от │ │ │
│ │
│ │ │ │ │свариваемых кромок │
│ │
├───┴─────┴───────┴─────────┴─────────┴──────┴─────────────────────┼───────────────────────┴─────────────┤
│ Режимы автоматической
сварки │
Дополнительные требования
│
│
│ и
рекомендации │
├───────────────────────────┬──────────────────────────────────────┼─────────────────────────────────────┤
│ Параметры │ Наименование слоя шва │1. Допустимая минимальная
толщина │
│
├────────┬───────┬──────┬──────┬───────┤стенки
___ мм. │
│
│Корневой│1-ый
│2-ой и│ 4-ый │Облицо-│2. Межслойная температура
должна быть│
│ │ │запол- │3-ий │запол-│вочный │не менее
___ °C, при снижении │
│ │ │няющий
│запол-│няющий│
│температуры стык подогреть до │
│ │ │ │няющие│ │ │температуры __ °C. │
├───────────────────────────┼────────┼───────┼──────┼──────┼───────┤3.
Допускается оставлять │
│Направление
сварки │ │ │ │ │ │незавершенным стык, заваренный на
2/3│
├───────────────────────────┼────────┼───────┼──────┼──────┼───────┤толщины
стенки трубы (должно быть │
│Род
тока, полярность │ │ │ │ │ │сварено ___ слоев сварного
шва). │
├───────────────────────────┼────────┼───────┼──────┼──────┼───────┤ │
│Скорость
движения головки, │
│ │ │ │ │ │
│м/ч │ │ │ │ │ │ │
├───────────────────────────┼────────┼───────┼──────┼──────┼───────┼─────────────────────────────────────┤
│Скорость
подачи проволоки, │ │ │ │ │ │ Режимы ручной дуговой сварки │
│м/мин │ │ │ │ │ │ │
├───────────────────────────┼────────┼───────┼──────┼──────┼───────┼──────────┬──────────────────────────┤
│Вылет
электрода, мм │ │ │ │ │ │Параметры │ Наименование слоя шва │
├───────────────────────────┼────────┼───────┼──────┼──────┼───────┤
├───────────┬──────────────┤
│Сварочное
напряжение, В │ │ │ │ │ │ │Подварочный│
Облицовочный │
├───────────────────────────┼────────┼───────┼──────┼──────┼───────┼──────────┼───────────┼──────────────┤
│Сварочный
ток, А │ │ │ │
│ │Диаметр │ │ │
│ │ │ │ │ │ │электрода,│ │ │
│ │ │ │ │ │ │мм │ │ │
├───────────────────────────┼────────┼───────┼──────┼──────┼───────┼──────────┼───────────┼──────────────┤
│Угол
наклона электрода, ° │ │ │ │ │ │Тип │ │ │
│ │ │
│ │ │ │электрода │ │ │
├───────────────────────────┼────────┼───────┼──────┼──────┼───────┼──────────┼───────────┼──────────────┤
│Амплитуда
колебаний │ │ │ │ │ │Марка │ │ │
│электрода,
мм │ │ │ │ │ │электродов│ │ │
├───────────────────────────┼────────┼───────┼──────┼──────┼───────┼──────────┼───────────┼──────────────┤
│Скорость
колебаний │ │ │ │ │ │Род тока, │ │ │
│электрода,
см/мин │ │ │ │ │ │полярность│ │ │
├───────────────────────────┼────────┼───────┼──────┼──────┼───────┼──────────┼───────────┼──────────────┤
│Задержка
электрода │ │ │ │ │ │Сварочный │ │ │
│на
кромках, с │ │ │ │ │ │ток, А │ │ │
├───────────────────────────┼────────┼───────┼──────┼──────┼───────┼──────────┴───────────┴──────────────┤
│Защитный
газ Ar/CO , % │ │ │ │ │ │Электроды с основным видом │
│ 2 │ │ │ │ │ │покрытия прокаливать при
режимах, │
├───────────────────────────┼────────┼───────┼──────┼──────┼───────┤рекомендованных │
│Расход
газа, л/мин │ │ │ │ │ │заводом-изготовителем │
└───────────────────────────┴────────┴───────┴──────┴──────┴───────┴─────────────────────────────────────┘
┌────────────────────────────────────────────────────────────────────────────────────────────────┐
│ ПЕРЕЧЕНЬ И ПОСЛЕДОВАТЕЛЬНОСТЬ
ОПЕРАЦИЙ СБОРКИ И СВАРКИ
│
├───┬──────────┬─────────────────────────────────────────────────────────────────┬───────────────┤
│
N │ Операция │
Содержание операций │ Оборудование │
│п/п│ │
│ и инструмент │
├───┼──────────┼─────────────────────────────────────────────────────────────────┼───────────────┤
│
1 │ Очистка │Внутреннюю и наружную
неизолированную поверхности труб очистить
│Скребок, щетка │
│ │
труб │от снега, грунта и
других загрязнений
│ │
├───┼──────────┼─────────────────────────────────────────────────────────────────┼───────────────┤
│
2 │Подготовка│ Произвести механическую обработку торцов труб с
помощью │Шаблон УШС-3, │
│ │
кромок │кромкострогального
станка в соответствии со схемой разделки
│штангенциркуль,│
│ │ │кромок. │толщиномер, │
│ │ │ Осмотреть неизолированные
участки поверхности труб, примыкающие │шлифмашинка, │
│ │ │к торцам.
│кромко- │
│ │ │ Царапины, риски, задиры на
поверхности труб глубиной св. __ мм
│строгательный │
│ │ │устранить шлифованием, при
этом толщина стенки не должна быть
│станок с │
│ │ │выведена за пределы минусового
допуска. │гидростанцией │
│ │ │ Прилегающую к торцам
внутреннюю и наружную поверхности труб
│ │
│ │ │зачистить до чистого металла
на ширину не менее __ мм.
│ │
│ │ │ Сошлифовать наружное усиление
заводских швов на длине 8 - 10 мм │ │
│ │ │от торца таким образом, чтобы
его величина на торце была в
│ │
│ │ │пределах от __ до __ мм │ │
├───┼──────────┼─────────────────────────────────────────────────────────────────┼───────────────┤
│
3 │Установка │ Установить с помощью специального шаблона на
поверхности трубы │Шаблон, │
│ │
пояса │направляющий пояс
для сварочных головок
│направляющий │
│ │ │
│пояс │
├───┼──────────┼─────────────────────────────────────────────────────────────────┼───────────────┤
│
4 │ Подогрев │ Установить подогреватели и произвести подогрев
кромок стыкуемых │Кольцевые
│
│ │ │труб до температуры __ °C,
чтобы ширина зоны подогрева для каждой│подогреватели, │
│ │ │трубы была не менее __ мм от
торца. │контактный │
│ │ │ Замеры температуры подогрева
производить в точках, равномерно
│термометр или │
│ │ │разнесенных по периметру стыка
на расстоянии __ мм от торца трубы│термокарандаш │
├───┼──────────┼─────────────────────────────────────────────────────────────────┼───────────────┤
│
5 │ Сборка │ Произвести осмотр и при необходимости
зачистку металлическими
│Центратор │
│ │ │щетками секторов подкладного
кольца. │внутренний, │
│ │ │ Установить центратор таким
образом, чтобы медное подкладное
│воздушный │
│ │ │кольцо располагалось в
плоскости стыка.
│компрессор, │
│ │ │ Собрать стык без зазора.
Допускается локальный зазор
│щуп, шаблон │
│ │ │не более ___ мм.
│сварщика УШС-3,│
│ │ │ Величину наружного смещения
кромок рекомендуется соблюдать
│одиночные │
│ │ │в пределах до ___ мм.
Допускаются локальные смещения кромок труб │газовые │
│ │ │не более __ мм на длине не
более 1/6 периметра трубы.
│горелки, │
│ │ │ Обеспечить при сборке
расстояние между заводскими продольными
│контактный │
│ │ │швами на стыкуемых трубах не
менее __ мм.
│термометр или │
│ │ │ Проверить температуру
подогрева в трех точках равномерно
│термокарандаш │
│ │
│разнесенных по
периметру стыка на расстоянии __ мм от торца │ │
│ │ │трубы. В случае необходимости
подогреть стык до __ °C
│ │
├───┼──────────┼─────────────────────────────────────────────────────────────────┼───────────────┤
│
6 │ Сварка │ Установить на направляющий пояс
правую и левую сварочные головки│Центратор │
│ │ │для сварки корневого слоя
шва.
│внутренний, │
│ │ │ Произвести автоматическую
сварку корневого слоя шва на правом и │комплекс │
│ │ │левом полупериметрах трубы
одновременно.
│оборудования │
│ │ │ Интервал времени между
окончанием сварки корневого шва и началом│"___" для │
│ │ │сварки 1-го заполняющего шва
не более ___ мин.
│автоматической │
│ │ │ После окончания сварки
корневого слоя следует сдвинуть центратор│сварки │
│ │ │внутрь трубопровода, осмотреть
корневой шов изнутри трубы и,
│проволокой │
│ │ │в случае необходимости,
произвести ручную подварку участков
│сплошного │
│ │ │корневого шва с поверхностными
дефектами.
│сечения в │
│ │ │ Операции подъема
привариваемой трубы и последующей ее установки │защитных газах,│
│ │ │на опору, перемещение
центратора на очередную позицию сборки
│шлифмашинки, │
│ │ │следует производить после
окончания сварки __ слоя шва.
│шаблон сварщика│
│ │ │ Снять со стыка сварочные
головки для сварки корневого слоя шва. │УШС-3 │
│ │ │ Произвести доварку стыка, для
чего произвести установку на стык │ │
│ │ │сварочных головок, задание
параметров и сварку заполняющих и
│ │
│ │ │облицовочного слоев шва в
соответствии со схемой сварного шва.
│ │
│ │ │Допускается сварка заполняющих
и облицовочного слоев в два │ │
│ │ │валика. "Замки"
смежных слоев шва должны быть смещены на
│ │
│ │ │расстояние не менее __
мм.
│ │
│ │ │ Осмотреть сваренный шов.
Недопустимые наружные дефекты сварного │ │
│ │ │шва (поры, подрезы и др.)
вышлифовать и устранить автоматической │ │
│ │ │либо ручной дуговой сваркой.
Допускается увеличение ширины
│ │
│ │ │облицовочного слоя в месте
устранения дефектов на __ мм.
│ │
│ │ │ Снять сварочные головки
сварки облицовочного слоя шва
│ │
│ │ │и направляющий пояс со
стыка. │ │
│ │ │ Участки шва с усилением,
превышающим __ мм, зашлифовать.
│ │
│ │ │Зачистить сваренный стык от
брызг
│ │
├───┴──────────┴─────────────────────────────────────────────────────────────────┴───────────────┤
│
Не оговоренные в данной технологической карте операции должны выполняться │
│в
соответствии с требованиями: СТО Газпром "Инструкция по технологиям │
│сварки
при строительстве и ремонте промысловых и магистральных │
│газопроводов.
Часть I".
│
├────────────────────────────────────────────────────────────────────────────────────────────────┤
│
│
│Карта
утверждена: ______________ ______________ ______________ Дата: "__" _________ ____ г.│
│ должность подпись Ф.И.О. │
│Карта
разработана: ______________ ______________ ______________ Дата: "__" _________ ____ г.│
│ должность подпись Ф.И.О. │
└────────────────────────────────────────────────────────────────────────────────────────────────┘
БИБЛИОГРАФИЯ
[1] Руководящий документ Порядок применения сварочных материалов
Госгортехнадзора при
изготовлении, монтаже, ремонте
России РД
03-613-03 и реконструкции
технических устройств
для опасных
производственных объектов
(утвержден
Постановлением Госгортехнадзора
России от
19.06.2003 N 101)
[2] Руководящий документ Порядок применения сварочного оборудования
Госгортехнадзора при
изготовлении, монтаже, ремонте
России РД
03-614-03 и реконструкции
технических устройств
для опасных
производственных объектов
(утвержден
Постановлением Госгортехнадзора
России от 19.06.2003
N 102)
[3] Руководящий документ Порядок применения сварочных технологий
Госгортехнадзора при
изготовлении, монтаже, ремонте
России РД
03-615-03 и реконструкции технических
устройств
для опасных
производственных объектов
(утвержден
Постановлением Госгортехнадзора
России от
19.06.2003 N 103)
[4] Правила Правила аттестации сварщиков и специалистов
Госгортехнадзора
сварочного производства (утверждены
России ПБ
03-273-99 Постановлением
Госгортехнадзора России
от 30.10.2002 N
63)
[5] Руководящий документ Технологический регламент проведения
Госгортехнадзора
аттестации сварщиков и специалистов
России РД
03-495-02 сварочного производства
(утвержден
Постановлением
Госгортехнадзора России
от 25.06.2002 N
36)
[6]
Руководящий документ
Инструкция по применению стальных труб
ОАО
"Газпром" в газовой
и нефтяной промышленности
Р
51-31323949-58-2000 (утверждена ОАО
"Газпром" 05.02.2001)
[7] Правила Правила аттестации и основные
требования
Госгортехнадзора к
лабораториям неразрушающего контроля
России ПБ
03-372-00 (утверждены Постановлением
Госгортехнадзора
России от 02.06.2000 N
29)
[8] Правила Правила аттестации персонала
в области
Госгортехнадзора
неразрушающего контроля (утверждены
России ПБ
03-440-02 Постановлением
Госгортехнадзора России
от 23.01.2002 N
3)
[9]
Руководящий документ
Инструкция по визуальному и измерительному
Госгортехнадзора контролю
(утверждена Постановлением
России РД
03-606-03 Госгортехнадзора России от
11.06.2003 N 92)
[10] Строительные нормы Технологическое оборудование и
и
правила технологические
трубопроводы
СНиП
3.05.05-84 (утверждены
Постановлением Госстроя СССР
от 07.05.1984 N
72)
[11] Правила Правила устройства и
безопасной эксплуатации
Госгортехнадзора
технологических трубопроводов (утверждены
России ПБ
03-585-03 Постановлением
Госгортехнадзора России
от 10.06.2003 N
80)
[12] Руководящий документ Руководящий документ по технологии сварки
ОАО
"Газпром"
технологических и трубопроводов КС из
РД
51-31323949-38-98 теплоустойчивых и
высоколегированных сталей
(утвержден Членом
Правления ОАО "Газпром"
Б.В. Будзуляком
01.12.1998)
[13] Ведомственный Единая система управления охраной
труда
руководящий документ и
промышленной безопасностью в Открытом
ОАО
"Газпром"
Акционерном обществе "Газпром"
ВРД
39-1.14-021-2001
[14] Ведомственный Правила технической эксплуатации
руководящий
документ магистральных газопроводов
(утверждены
ОАО
"Газпром" Приказом
ОАО "Газпром" от 15.02.2000 N 22)
ВРД
39-1.10-006-2000*
[15] Ведомственные Инструкция по производству
строительных работ
строительные
нормы в охранных зонах
магистральных трубопроводов
ВСН
51-1-80 (утверждена
распоряжением Министерства
газовой
промышленности ВД-440 от 05.03.1980)
[16] СНиП 12-03-2001.
Безопасность труда в строительстве, ч. 1
[17] Правила Правила безопасности в
нефтяной и газовой
Госгортехнадзора
промышленности (утверждены Постановлением
России ПБ
08-624-03 Госгортехнадзора России от
05.06.2003 N 56)
[18] ПОТ РМ 020-2001.
Межотраслевые правила по охране труда при электро-
и
газосварочных работах (утверждены Постановлением Министерства труда
и
социального развития РФ от 09.10.2001 N 72)
[19] Правила устройства
электроустановок. ПУЭ
(утверждены Приказом Минэнерго России от 08.07.2002 N 204)
[20] Стандарт Американского Технические условия на трубы для
нефтяного
института трубопроводов
(Specification for Line Pipe)
API
5L-2004
[21] Стандарт Американского Электроды покрытые для дуговой сварки
сварочного общества
углеродистых сталей (Specification for Carbon
AWS A
5.1-91 Steel Electrodes for
Shielded Metal Arc
Welding)
[22] Стандарт Американского Электроды покрытые для дуговой сварки
сварочного общества
низколегированных сталей (Specification
AWS A
5.5-91 for Low Alloy Steel
Covered Arc Welding
Electrodes)
[23] Европейская норма Электроды покрытые для ручной дуговой
сварки
EN
499:1994 низколегированных
сталей (Welding consumables
- Covered
electrodes for manual metal arc
welding of non
alloy and fine grain steels -
Classifications)
[24] Европейская норма Электроды покрытые для ручной дуговой
сварки
EN
757:1997 высокопрочных
сталей (Welding consumables -
Covered
electrodes for manual metal arc
welding of high
strength steels -
Classifications)
[25] Стандарт Американского Электроды из углеродистой стали и флюсы для
сварочного общества дуговой
сварки под флюсом (Specification for
AWS A
5.17-89 Carbon Steel
Electrodes and Fluxes for
Submerged Arc
Welding)
[26] Стандарт Американского Электроды из углеродистой стали для дуговой
сварочного общества сварки в
среде защитных газов (Specification
AWS A
5.18-79 for Carbon Steel
Electrodes and Rods for Gas
Shielded Arc
Welding)
[27] Стандарт Американского Электроды из низколегированной стали и флюсы
сварочного общества для
дуговой сварки под флюсом (Specification
AWS A
5.23-89 for Low Alloy Steel
Electrodes and Fluxes for
Submerged Arc
Welding)
[28] Стандарт Американского Электроды и прутки из низколегированной
стали
сварочного общества для дуговой
сварки в защитных газах
AWS A
5.28-91
[29] Европейская норма Проволочные электроды и наплавленный
металл
EN
440:1995 для металлической
сварки в среде защитных
газов для
нелегированных и мелкозернистых
сталей (Welding
consumables - Wire electrodes
and deposits for
gas shielded metal arc
welding of non
alloy and fine grain steels -
Classification)
[30] Европейская норма Проволочные электроды для сварки под
флюсом
EN
756:1995 для нелегированных
и мелкозернистых сталей
(Welding consumables - Wire electrodes and
wire - flux
combinations for submerged arc
welding of non
alloy and fine grain steels -
Classification)
[31] Европейская норма Проволочные электроды, проволоки,
стержни
EN
12534:1999 и наплавленный
металл для металлической
сварки в среде
защитных газов для
высокопрочных сталей (Welding consumables -
Wire electrodes,
wires, rods and deposits for
gas shielded
metal arc welding of high
strength
steels - Classification)
[32] Стандарт Американского Электроды из углеродистой стали для дуговой
сварочного общества сварки
порошковой проволокой (Specification
AWS A 5.20-95 for Carbon Steel Electrodes for
Flux Cored
Arc Welding)
[33] Стандарт Американского Электроды из низколегированной стали
сварочного общества для
дуговой сварки порошковой проволокой
AWS A 5.29-80 (Specification for low alloy steel
electrodes
for flux cored
arc welding)
[34] Европейская норма Порошковые проволоки для электродуговой
EN
758:1998 сварки с или без
газовой защиты для
нелегированных и мелкозернистых
сталей
(Welding
consumables - Tubular cored
electrodes for metal arc welding with and
without a gas
shield of non alloy and fine
grain steels - Classification)
[35] Ведомственные Строительство магистральных и
промысловых
строительные нормы
трубопроводов. Контроль качества и приемка
ВСН
012-88 работ. Часть II.
Формы документации и правила
ее оформления в
процессе сдачи-приемки
(утверждены
Приказом Миннефтегазстроя
от 27.12.1998 N
375).
|