Введен в действие
Приказом Ростехрегулирования
от 5 декабря 2007
г. N 352-ст
МЕЖГОСУДАРСТВЕННЫЙ СТАНДАРТ
ОСИ ДЛЯ ПОДВИЖНОГО СОСТАВА ЖЕЛЕЗНЫХ ДОРОГ КОЛЕИ 1520
ММ
ТЕХНИЧЕСКИЕ УСЛОВИЯ
Axles
for rolling stock of 1520 mm gauge railways.
Specifications
ГОСТ 31334-2007
Группа В41
ОКП 31 0000
МКС 45.080
Предисловие
Цели, основные
принципы и основной порядок проведения работ по межгосударственной
стандартизации установлены ГОСТ 1.0-92 "Межгосударственная система
стандартизации. Основные положения" и ГОСТ 1.2-97 "Межгосударственная
система стандартизации. Стандарты межгосударственные, правила и рекомендации по
межгосударственной стандартизации. Порядок разработки, принятия, применения,
обновления и отмены".
Сведения о
стандарте
1. Разработан
Федеральным Государственным унитарным предприятием "Всероссийский
научно-исследовательский институт железнодорожного транспорта" (ФГУП
ВНИИЖТ), Федеральным Государственным унитарным предприятием
"Государственный научно-исследовательский институт вагоностроения (ФГУП ГосНИИВ)", Институтом черной металлургии Украины (ИЧМ
НАНУ), ТК 4 и ОАО "Уральский институт металлов" (ГНЦ РФ ОАО УИМ).
2. Внесен Федеральным агентством по техническому регулированию
и метрологии.
3. Принят
Межгосударственным советом по стандартизации, метрологии и сертификации
(Протокол N 31 от 8 июня 2007 г.).
За принятие
проголосовали:
┌────────────────────┬─────────────┬──────────────────────────────────────┐
│Краткое
наименование│Код страны по│ Сокращенное наименование │
│ страны по │МК (ИСО 3166)│национального
органа по стандартизации│
│МК
(ИСО 3166) 004-97│004-97
│ │
├────────────────────┼─────────────┼──────────────────────────────────────┤
│Азербайджан │ AZ
│Азстандарт │
│Армения │ AM
│Минторгэкономразвития │
│Беларусь │ BY
│Госстандарт Республики Беларусь │
│Казахстан │ KZ
│Госстандарт Республики Казахстан │
│Кыргызстан │ KG
│Кыргызстандарт │
│Молдова │ MD
│Молдова-Стандарт │
│Российская
Федерация│ RU │Федеральное агентство по техническому │
│ │ │регулированию и
метрологии │
│Таджикистан │ TJ
│Таджикстандарт │
│Узбекистан │ UZ
│Узстандарт │
│Украина │ UA
│Госпотребстандарт Украины │
└────────────────────┴─────────────┴──────────────────────────────────────┘
4. Настоящий
стандарт разработан с учетом основных нормативных положений международного
стандарта ИСО 1005-3-82 "Подвижной состав железных дорог. Часть 3. Оси для тяговых и прицепных вагонов. Требования к качеству" (ISO 1005-3:1982
"Railway rolling stock material - Part 3: Axles for tractive and trailing stock -
Quality requirements. First edition").
5. Приказом
Федерального агентства по техническому регулированию и метрологии от 5 декабря
2007 г. N 352-ст межгосударственный стандарт ГОСТ 31334-2007 введен в действие
в качестве национального стандарта Российской Федерации с 1 июля 2008 г.
6. Взамен ГОСТ
30237-96 и ГОСТ 30272-96.
1. Область
применения
Настоящий стандарт
распространяется на черновые (профильные заготовки) и чистовые оси в исполнении
УХЛ по ГОСТ 15150 для подвижного состава железных дорог колеи 1520 мм и
метрополитенов.
Допускается по
согласованию между изготовителем и потребителем изготовлять оси в соответствии
с требованиями Приложения А <*>.
--------------------------------
<*> В этом
случае одновременное применение требований основного текста стандарта и
Приложения А не допускается.
2.
Нормативные ссылки
В настоящем
стандарте использованы нормативные ссылки на следующие межгосударственные
стандарты:
ГОСТ 9.014-78.
Единая система защиты от коррозии и старения. Временная противокоррозионная
защита изделий. Общие требования
ГОСТ 12.1.004-91.
Система стандартов безопасности труда. Пожарная безопасность. Общие требования
ГОСТ 12.1.005-88.
Система стандартов безопасности труда. Общие санитарно-гигиенические требования
к воздуху рабочей зоны
ГОСТ 12.1.007-76.
Система стандартов безопасности труда. Вредные вещества. Классификация и общие
требования безопасности
ГОСТ 12.2.003-91.
Система стандартов безопасности труда. Оборудование производственное. Общие
требования безопасности
ГОСТ 12.2.017-93.
Система стандартов безопасности труда. Оборудование кузнечно-прессовое. Общие
требования безопасности
ГОСТ 12.3.002-75. Система
стандартов безопасности труда. Процессы производственные. Общие требования
безопасности
ГОСТ 1497-84 (ИСО
6892-84). Металлы. Методы испытания на растяжение
ГОСТ 1778-70 (ИСО
4967-79). Сталь. Металлографические методы определения неметаллических включений
ГОСТ 2789-73.
Шероховатость поверхности. Параметры и характеристики
ГОСТ 4728-96.
Заготовки осевые для подвижного состава железных дорог колеи 1520 мм.
Технические условия
ГОСТ 5639-82. Стали
и сплавы. Метод выявления и определения величины зерна
ГОСТ 7565-81 (ИСО
377-2-89). Чугун, сталь и сплавы. Метод отбора проб для определения химического
состава
ГОСТ 8026-92.
Линейки поверочные. Технические условия
ГОСТ 9454-78.
Металлы. Методы испытания на ударный изгиб при пониженных,
комнатной и повышенных температурах
ГОСТ 10243-75.
Сталь. Методы испытаний и оценки макроструктуры
ГОСТ 11018-2000.
Тяговый подвижной состав железных дорог колеи 1520 мм. Колесные пары. Общие
технические условия
ГОСТ 14192-96.
Маркировка грузов
ГОСТ 15150-69.
Машины, приборы и другие технические изделия. Исполнения для различных
климатических районов. Категории, условия эксплуатации, хранения и
транспортирования в части воздействия климатических факторов внешней среды
ГОСТ 20415-82.
Контроль неразрушающий. Методы акустические. Общие положения
ГОСТ 21105-87.
Контроль неразрушающий. Магнитопорошковый метод
ГОСТ 21650-76.
Средства скрепления тарно-штучных грузов в транспортных пакетах. Общие
требования
ГОСТ 22780-93 (ИСО
1005-9-86). Оси для вагонов железных дорог колеи 1520 (1524) мм. Типы,
параметры и размеры
ГОСТ 30552-98.
Заготовки профильные (необработанные оси) для подвижного состава железных дорог
колеи 1520 мм. Припуски и допуски.
Примечание. При
пользовании настоящим стандартом целесообразно проверять действие ссылочных
стандартов по указателю "Национальные стандарты", составленному по
состоянию на 1 января текущего года, и по соответствующим информационным
указателям, опубликованным в текущем году. Если ссылочный стандарт заменен
(изменен), то при пользовании настоящим стандартом следует руководствоваться
заменяющим (измененным). Если ссылочный стандарт отменен без замены, то
положение, в котором дана ссылка на него, применяется в части, не затрагивающей
эту ссылку.
3. Термины
и определения
В настоящем
стандарте применены следующие термины с соответствующими определениями:
3.1. Черновая ось
(профильная заготовка): ось, полученная методом горячего деформирования,
подвергнутая термической обработке, имеющая припуск под механическую обработку
и прошедшая ультразвуковой контроль.
3.2. Чистовая ось:
ось, окончательно механически обработанная, подвергнутая по всей длине
упрочнению накатыванием роликами и прошедшая ультразвуковой и магнитный
контроль.
3.3. Прозвучиваемость: проницаемость оси с торцевой поверхности
ультразвуковыми волнами в осевом направлении, заключающаяся в сравнении
амплитуды эхо-сигнала от противоположного торца оси с амплитудой эхо-сигнала от
эталонного отражателя в стандартном образце.
4. Технические требования
4.1. Технические
требования к черновым осям
4.1.1. Черновые оси
должны соответствовать требованиям настоящего стандарта.
4.1.2. Черновые оси
изготовляют из осевых заготовок по ГОСТ 4728 или из слитков той же марки стали.
4.1.3.
Химический состав стали - по ГОСТ 4728.
4.1.4.
Форма, размеры и предельные отклонения геометрических размеров черновых осей
должны соответствовать ГОСТ 30552 и чертежам, согласованным в установленном
порядке.
4.1.5.
Черновые оси изготовляют методами горячего деформирования: свободной ковкой,
штамповкой, винтовой прокаткой и радиально-ротационным деформированием.
4.1.6. Степень укова или обжатия металла при изготовлении черновых осей
для вагонов магистральных железных дорог, локомотивных осей и осей специального
подвижного состава должна быть не менее 3, а для осей вагонов метрополитенов -
не менее 5.
4.1.7. Черновые оси
могут иметь технологический припуск для изготовления образцов; диаметр припуска
должен быть не менее диаметра конца черновой оси. Допускается во время ковки
припуск надрубить.
4.1.8. После
формообразования черновые оси должны быть подвергнуты термической обработке -
нормализации или нормализации с последующим отпуском. Все термические операции
следует осуществлять при автоматической регистрации заданных режимов.
4.1.9.
Механические свойства металла термически обработанных черновых осей должны
соответствовать указанным в таблице 1.
Таблица 1
Механические
свойства и ударная вязкость
┌──────────────┬─────────────┬─────────────┬──────────────────────────────┐
│ Временное │
Предел
│Относительное│
Ударная вязкость при 20 °C
│
│сопротивление
│ текучести │
удлинение │ KCU, Дж/см2 │
│при
растяжении│сигма ,
Н/мм2│ дельта, % │
(кгс x м/см2) │
│сигма , Н/мм2 │
т │ │ │
│ в
│ (кгс/мм2) │ │ │
│ (кгс/мм2)
├─────────────┴─────────────┼─────────────────┬────────────┤
│ │ не менее │Среднее значение,│Минимальное
│
│ │ │ не менее
│ значение │
├──────────────┴───────────────────────────┴─────────────────┴────────────┤
│ Образцы из подступичной части │
├──────────────┬─────────────┬─────────────┬─────────────────┬────────────┤
│ 580 - 610
│ 300 (31) │
20,0 │ 49 (5,0)
│ 34 (3,5) │
│ (59 - 62)
│ │ │ │ │
│ 620 - 640
│ 310 (32) │
19,0 │ 39 (4,0)
│ 29 (3,0) │
│ (63 - 65)
│ │ │ │ │
│ 650 (66)
│ 325 (33) │
18,0 │ 34 (3,5)
│ 29 (3,0) │
│ и более
│ │ │ │ │
├──────────────┴─────────────┴─────────────┴─────────────────┴────────────┤
│ Образцы из шейки или
технологического припуска
│
├──────────────┬─────────────┬─────────────┬─────────────────┬────────────┤
│ 600 - 620
│ 310 (32) │
20,0 │ 54 (5,5)
│ 39 (4,0) │
│ (61 - 63)
│ │ │ │ │
│ 630 (64)
│ 330 (34) │
19,0 │ 44 (4,5)
│ 34 (3,5) │
│ и более
│ │ │ │ │
├──────────────┴─────────────┴─────────────┴─────────────────┴────────────┤
│ Примечание. Нормы по пределу текучести
факультативны. │
└─────────────────────────────────────────────────────────────────────────┘
При получении
неудовлетворительных результатов испытаний на образцах из технологического
припуска шейки или самой шейки допускается проводить испытания на образцах из подступичной части.
Примечание. При
изготовлении черновых осей методом винтовой прокатки или свободной ковки нормы
для образцов из шейки или технологического припуска такие же, как и для
образцов из подступичной части.
4.1.10. Правку
черновых осей проводят в горячем состоянии после нагрева под нормализацию или
после отдельного нагрева до температуры не выше 700 °C без последующей
термообработки. Температура в конце процесса правки должна быть не ниже 600 °C.
4.1.11.
Радиальное биение поверхности черновых осей (шеек и средней части) относительно
поверхности подступичных частей - в соответствии с
ГОСТ 30552.
4.1.12.
Поверхность черновых осей, подлежащих дальнейшей обработке у потребителя,
должна быть очищена от окалины, глубина залегания дефектов не должна превышать
75% одностороннего фактического припуска на обработку черновых осей. Для
определения глубины залегания видимых дефектов предприятие-изготовитель должно
выполнять контрольные местные вырубки (зачистки). Допускается по согласованию с
потребителем изготовлять черновые оси винтовой прокатки без очистки от окалины
и с глубиной залегания наружных дефектов до 85% одностороннего фактического
припуска на обработку дефектов.
На поверхности
черновых осей, изготовленных винтовой прокаткой, допускается винтовой след от
валков, высота которых не входит в поле предельных отклонений по диаметру.
4.1.13. Не
допускаются флокены, несплошности,
инородные металлические и неметаллические включения, следы усадочной раковины,
а также дефекты макроструктуры, превышающие требования ГОСТ 4728.
В черновых осях,
предназначенных для изготовления полых сверленых осей, допускается наличие
центральной осевой рыхлости, если она распространяется от центра на расстоянии
не более 0,7 радиуса отверстия.
4.1.14. Оси
должны прозвучиваться с торца в продольном
направлении, затухание ультразвуковых колебаний на частоте 2 - 2,5 МГц не
должно превышать 46 дБ.
4.1.15.
Балл неметаллических включений в стали (кроме недеформирующихся силикатов) не
должен быть более 4 по ГОСТ 1778.
4.1.16.
Микроструктура термообработанных черновых осей должна
быть однородной перлитно-ферритной.
Величина зерна
должна быть не крупнее номера 5 по ГОСТ 5639.
4.1.17. На
каждой черновой оси в горячем состоянии на средней части должны быть четко выбиты
знаки маркировки высотой 10 - 15 мм и глубиной 1 - 3 мм через тире или с
промежутками.
4.1.17.1. Для
черновых осей, изготовленных из осевых заготовок:
- две последние
цифры года изготовления;
- номер плавки;
- порядковый номер
оси, начинающийся с условного номера предприятия-изготовителя. Перед однозначным условным номером ставят три нуля, перед
двузначным - два нуля, перед трехзначным - один нуль.
Для черновых осей
винтовой прокатки нули перед условным номером предприятия-изготовителя не
ставят. Черновым осям сборной партии для вагонов метрополитена присваивают
условный номер плавки по нумерации предприятия-изготовителя.
Повторение номера в
течение года не допускается.
Пример маркировки
черновой оси, изготовленной в 2002 году с номером плавки - 17248; с номером
черновой оси 000530085 (5 - номер предприятия-изготовителя; 30085 - порядковый
номер оси, изготовленной с начала года):
02 17248 000530085
Допускается делать
промежуток между условным номером предприятия-изготовителя и порядковым номером
черновой оси.
4.1.17.2. Для
черновых осей, изготовленных ковкой из слитка:
- условный номер
предприятия-изготовителя;
- месяц и две
последние цифры года изготовления;
- номер плавки;
- порядковый номер
оси, начинающийся с номера предприятия-изготовителя.
4.1.17.3. Каждая
черновая ось должна иметь клейма технического контроля и представителя
заказчика. Для черновых осей, изготовленных свободной ковкой из слитка, эти
клейма ставят на площадке длиной 25 мм и шириной 15 мм между номером плавки и
номером черновой оси.
4.1.18. На черновых
осях, изготовленных ковкой из слитка, должны быть выбиты литеры:
А - на черновых
осях, изготовленных из головной (верхней) части слитка;
Б - на черновых осях, изготовленных из части слитка, следующей за
головной.
Литеры должны быть
выбиты на головном конце черновой оси.
4.2.
Технические требования к чистовым осям
4.2.1. Чистовые оси
должны соответствовать требованиям настоящего стандарта.
4.2.2.
Чистовые оси изготовляют из черновых осей. Размеры и предельные отклонения
геометрических размеров чистовых осей должны соответствовать ГОСТ 11018, ГОСТ
22780 и чертежам, согласованным в установленном порядке с заказчиком.
4.2.3. На
поверхности чистовых осей черновины и видимые
поверхностные дефекты не допускаются. Не допускаются обнаруженные
магнитопорошковым методом контроля волосовины, размеры и количество которых
превышают указанные в таблице 2.
Таблица 2
Допустимое
количество и размер волосовин
на поверхности
чистовых осей
┌───────────────┬─────────────────────────────────────────────────────────┐
│Часть
чистовой │ Тип
подвижного состава
│
│ оси
├──────────────────────┬──────────────────────┬───────────┤
│ │ Грузовые и │Локомотивы и моторные
│Вагоны │
│ │ пассажирские вагоны;
│ вагоны электро- │метро- │
│ │ прицепные вагоны │
и дизель-поездов, │политена │
│ │ электро- и дизель- │специальный подвижной
│<***> │
│ │ поездов <*> │ состав <**> │ │
├───────────────┼──────────────────────┼──────────────────────┼───────────┤
│
Галтель │ Не
допускаются │ Не
допускаются │ Не │
│ │ │ │допускаются│
├───────────────┼──────────────────────┼──────────────────────┼───────────┤
│
Цилиндрическая│ Не допускаются, если:│ Не
допускаются, если:│ Не
│
│часть
шейки │ длина отдельной │ длина отдельной │допускаются│
│ │волосовины - более │волосовины - более │ │
│ │10 мм; │10 мм; │ │
│
│ более 3 шт.
волосовин│ более 2 шт. волосовин│ │
│ │в любом поперечном │в любом поперечном │ │
│ │сечении; │сечении; │ │
│ │ более 5 шт. волосовин│
более 4 шт. волосовин│
│
│ │всего │всего │ │
├───────────────┼──────────────────────┼──────────────────────┼───────────┤
│Средняя
часть │ Не
допускаются, если:│ Допускаются, если:
│ Не │
│ │ длина отдельной │ длина отдельной │допускаются│
│ │волосовины - более │волосовины - не более │ │
│ │50 мм; │25 мм; │ │
│ │ не более 3 шт. │ не более 2 шт. │ │
│ │волосовин в любом │волосовин в любом │ │
│ │поперечном сечении
│поперечном сечении
│ │
├───────────────┴──────────────────────┴──────────────────────┴───────────┤
│
<*> При нескученном и нестрочечном
расположении допускаются без│
│ограничения
количества волосовины длиной до 3 мм на всех частях осей, за│
│исключением
галтелей. │
│
<**> При нескученном и нестрочечном
расположении допускаются без│
│ограничения
количества волосовины длиной до 2 мм на шейке и до 3
мм на│
│всех
остальных частях осей. │
│
<***> При нескученном расположении
допускаются без ограничения│
│количества
волосовины длиной до 1 мм на шейке и до
2 мм на средней
и│
│подступичных частях осей.
│
│ │
│ Примечание.
Расположение волосовин на
поверхности оси по ее│
│образующей
считают строчечным. Волосовины,
составляющие одну строчку│
│и имеющие
длину на шейке
менее 10 мм,
на подступичной или│
│предподступичной части - менее 15 мм и
на средней части
оси - менее│
│20
мм, принимают за одну волосовину длиной, равной общему отрезку прямой,│
│на
которой они расположены. │
└─────────────────────────────────────────────────────────────────────────┘
4.2.4. Расположение
волосовин, при котором в любом месте их число на площадке размером 50 x 50 мм
превышает 5 шт., считают скученным. При этом волосовины длиной до 1 мм при нестрочечном их расположении не учитывают.
На средней части
чистовой оси не должно быть забоин. Допускаются забоины глубиной более 1 мм,
если они не выводят ось за пределы допускаемых отклонений на размеры и если они
плавно зачищены вдоль оси. Место зачистки должно быть проверено средствами
дефектоскопии. Видимые невооруженным глазом продольные мелкие риски на подступичной части оси глубиной не более 0,03 мм должны
быть плавно зачищены вдоль оси. Более глубокие риски не допускаются.
4.2.5. Не
допускается на поверхностях центровых отверстий наличие кольцевых рисок
глубиной более 0,08 мм и продольных - глубиной более 0,5 мм.
4.2.6.
Каждая чистовая ось должна быть подвергнута ультразвуковому контролю в
соответствии с 8.3.
4.2.7. Оси после
механической обработки должны быть подвергнуты упрочнению накатыванием роликами
в шейках, предподступичных, подступичных
и средней частях, а также в галтелях перехода от одних частей к другим по
нормативному документу, согласованному в установленном порядке.
4.2.7.1. Накатанная
поверхность на цилиндрической поверхности шейки и предподступичной
части оси вагонов железных дорог и оси вагонов метрополитена может начинаться
для осей типа РУ1 на расстоянии не более 8 мм, а для
осей типа РУ1Ш - не более 22 мм от торца с последующим постепенным увеличением
твердости и глубины накатанного слоя.
4.2.7.2. Увеличение
твердости накатанной поверхности вагонных осей должно составлять не менее 22%;
локомотивных осей и осей специального подвижного состава - не менее 20%
исходной. Глубина слоя металла с повышенной твердостью - 0,02 - 0,04 диаметра
упрочняемого сечения.
Накатанная
поверхность может не доходить до края шеек и подступичных
частей не более чем на 18 - 20 мм с последующим постепенным увеличением глубины
накатанного слоя.
Для тепловозов
промышленного транспорта допускается упрочнение накатыванием только подступичных частей, шеек осей и их галтелей.
4.2.8.
Шероховатость Rz подступичных
частей всех видов осей и буксовых шеек локомотивных осей перед накатыванием -
не более 20 мкм (Ra <= 6,3 мкм) по ГОСТ 2789,
остальных частей и заходного конуса на подступичной части - не более 40 мкм (Ra
<= 12,5 мкм).
4.2.9. Перенос
клейм и маркировки с необработанной поверхности черновой оси на торец чистовой
проводят под наблюдением отдела технического контроля предприятия,
обрабатывающего ось, и удостоверяют клеймом.
4.2.10.
Расположение знаков маркировки и клейм на торце чистовой оси должно
соответствовать указанному на рисунке:
1 - для вагонных
осей под подшипники качения с торцевым креплением шайбой; для моторных осей
электропоездов и дизель-поездов;
2а - для
локомотивных осей под подшипники скольжения; 2б - под подшипники качения и осей
специального подвижного состава;
3 - для осей
вагонов метрополитенов.
Высота знаков
маркировки - 6 мм.
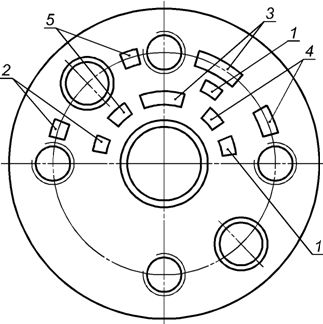
1 - приемочные
клейма; 2 - условный номер предприятия,
проводившего обработку и перенос знаков маркировки;
3 - номер оси; 4 -
две последние цифры года изготовления
черновой оси; 5 -
клеймо технического контроля
Рисунок 1.
Знаки и клейма на торце вагонной оси
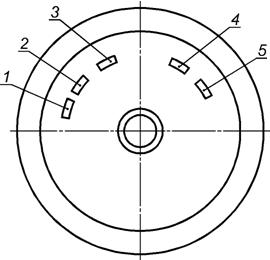
а

б
1 - условный номер
предприятия - изготовителя черновой оси;
2 - месяц и две
последние цифры года изготовления черновой
оси; 3 - номер оси;
4 - клейма технического контроля
предприятия-изготовителя
и представителя заказчика,
принявших чистовую ось; 5 - условный номер
предприятия-изготовителя,
обработавшего черновую ось
Рисунок 2. Знаки и
клейма на торце локомотивной оси
Примечание. Если
торцы чистовых осей являются рабочими элементами конструкции буксовых узлов, то
знаки маркировки и клейм выбивают на цилиндрической поверхности буртов или
другой нерабочей поверхности, указанной на рабочем чертеже; высота цифр: для
рисунка 2а - 10 мм, для рисунка 2б - 6 мм.
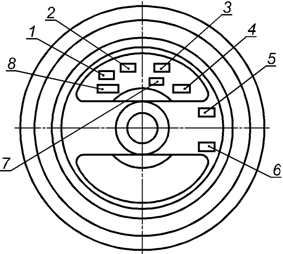
1 - условный номер
предприятия-изготовителя
или товарный знак;
2 - номер оси; 3 - номер плавки;
4 - дата
изготовления оси; 5 - приемочные клейма ОТК;
6 - приемочные
клейма приемщика вагонов;
7 - дата обработки
оси; 8 - условный номер предприятия,
перенесшего знаки маркировки
Рисунок 3.
Знаки и клейма на торце со стороны
удлиненной ступицы
осей вагонов метрополитена
5.
Требования безопасности
5.1. При
изготовлении осей следует руководствоваться ГОСТ 12.3.002, а также инструкциями
по технике безопасности предприятий, утвержденными техническими руководителями
предприятий-изготовителей.
5.2. Безопасность
при изготовлении осей обеспечивают выбором соответствующих производственных
процессов по ГОСТ 12.2.003 и режимов работы производственного оборудования - по
ГОСТ 12.2.017, режимов пожарной безопасности - по ГОСТ 12.1.004, способов
безопасного производства погрузочно-разгрузочных работ - по ГОСТ 12.1.004,
соблюдений требований санитарной безопасности - по ГОСТ 12.1.007.
5.3. Безопасность
эксплуатации осей обеспечивается выполнением требований разделов 4 и 7
настоящего стандарта.
6.
Требования охраны окружающей среды
6.1. При
изготовлении осей следует применять технологические процессы, не загрязняющие
окружающую среду, и предусматривать комплекс мероприятий с целью ее охраны.
6.2.
Метеорологические условия и содержание вредных веществ в рабочей зоне
производственных помещений должны соответствовать требованиям ГОСТ 12.1.005 и
ГОСТ 12.1.007 для категории работ средней тяжести.
7. Правила приемки
7.1. Для проверки
соответствия осей требованиям настоящего стандарта проводят приемосдаточные и
периодические испытания.
7.2. Предприятие -
изготовитель черновых осей проводит выборочный входной контроль осевых
заготовок на соответствие требованиям ГОСТ 4728.
Объем контроля
определяет предприятие - изготовитель черновых осей.
7.3. При
приемосдаточных испытаниях черновых осей должны быть предъявлены документы с
номерами плавок и результатами химических анализов состава стали.
Черновые и чистовые
оси, принятые отделом технического контроля предприятия-изготовителя, должны
быть предъявлены для приемки представителю заказчика.
7.4.
Приемосдаточные испытания
7.4.1. На
приемосдаточные испытания черновые оси для вагонов магистральных железных дорог
предъявляют партиями. Партия должна состоять из черновых осей одной плавки,
прошедших термообработку по одному режиму. Число черновых осей в партии - не
более 150 шт.
7.4.1.1.
Допускается остаток черновых осей данной плавки (до 80 шт.) присоединять к
партии из этой плавки.
Если остаток
черновых осей более 80 шт., то его следует считать отдельной партией.
Допускается составлять
сборную партию из черновых осей разных плавок, ранее прошедших испытания с
удовлетворительными результатами.
7.4.2. Черновые оси
локомотивов и моторных вагонов, изготовленных винтовой прокаткой, штамповкой и
радиально-ротационным деформированием, предъявляют к приемке партиями. Партию
составляют из черновых осей одной плавки, прошедших термическую обработку по
одному режиму.
7.4.3.
Приемосдаточным испытаниям подвергают каждую черновую ось для локомотивов,
моторных вагонов и специального подвижного состава, изготовленную свободной
ковкой из осевых заготовок по ГОСТ 4728 или непосредственно из слитка, а также
для вагонов метрополитенов, изготовленную ковкой непосредственно из слитка.
При изготовлении
двух и более черновых осей из одного слитка испытанию подвергают ось,
изготовленную из головной части слитка.
7.4.4. Черновые оси
для вагонов метрополитенов, изготовленные винтовой прокаткой или ковкой из
осевых заготовок по ГОСТ 4728, принимают партиями. Партия должна состоять из
черновых осей одной плавки. Число черновых осей в партии - не более 150 шт.
Допускается
составлять сборную партию черновых осей винтовой прокатки, полученную перекатом
из черновых осей разных плавок, ранее прошедших испытания с удовлетворительными
результатами, но имевших отклонения по размерам. Сборную партию принимают как
новую.
7.5. При
приемосдаточных испытаниях черновых и чистовых осей контролируют параметры
согласно таблицам 3, 4.
Таблица 3
Порядок и объем
проведения приемосдаточных
испытаний черновых
осей
┌──────────────┬──────────────────────────────────────────────────────────┐
│ Параметр
│ Тип
транспортного средства
│
│ приемки и
├──────────┬────────────────────────┬──────────────────────┤
│ показатель
│Вагоны │ Локомотивы и моторные │ Вагоны
метрополитена │
│качества
осей │магист- │ вагоны, электро- и │ │
│ │ральных │
дизель-поезда, │ │
│ │железных │локомотивы промышленного│ │
│ │дорог │транспорта, специальный
│ │
│ │ │ подвижной состав │ │
├──────────────┼──────────┼──────────┬─────────────┼───────────┬──────────┤
│
Метод │Все
методы│ Винтовая │ Свободная
│ Свободная │ Винтовая │
│изготовления │ │прокатка, │ковка из │ковка
и │прокатка и│
│осей
(4.1.5) │ │радиальная│осевых │горячая │свободная │
│ │ │ковка и │заготовок и │штамповка │ковка из │
│ │ │горячая │непосредст- │непосредст-│осевых │
│ │ │штамповка │венно из │венно из │заготовок │
│ │ │из осевых │слитка │слитка │ │
│ │ │заготовок │ │ │ │
├──────────────┼──────────┼──────────┼─────────────┼───────────┼──────────┤
│
Объем партии,│ 150 <*>
│ Оси одной│ Каждая ось │Каждая ось │ 150 <**>
│
│шт.,
не более │ │плавки │ │ │ │
├──────────────┴──────────┴──────────┴─────────────┴───────────┴──────────┤
│ Объем выборки осей для
испытания │
├──────────────┬──────────┬──────────┬─────────────┬───────────┬──────────┤
│
Контроль │ 1
│ 2 │ Каждая ось │Каждая ось │ 1
│
│механических │ │ │ <***> │ │ │
│свойств │ │ │ │ │ │
│(4.1.9) │ │ │ │ │ │
├──────────────┼──────────┴──────────┴─────────────┴───────────┴──────────┤
│
Размеры, │ Каждая ось (4.1.4, 4.1.11, 4.1.12,
4.1.17) │
│внешний
вид, │ │
│качество │
│
│нанесения │
│
│маркировки │
│
├──────────────┼──────────────────────────────────────────────────────────┤
│
Контроль │ Черновые оси,
изготовленные из осевых заготовок, -
│
│макроструктуры│по входному контролю осевых заготовок;
черновые оси, │
│(4.1.13)
│изготовленные из слитка, - на оси, изготовленной │
│ │из головной части
слитка
│
├──────────────┼──────────────────────────────────────────────────────────┤
│
Контроль │ На
черновых осях, изготовленных из осевых заготовок, - │
│микроструктуры│на одной оси; на оси, изготовленной
непосредственно │
│(4.1.16) │из слитка, - на одной оси,
изготовленной из головной │
│ │части слитка
│
├──────────────┼──────────────────────────────────────────────────────────┤
│
Контроль │ При
изготовлении осей из осевых заготовок - по входному │
│загрязненности│контролю на осевые заготовки или по
ГОСТ 4728; при
│
│стали
неметал-│изготовлении
осей методом свободной ковки из слитков -
│
│лическими
│по ГОСТ 1778 на каждой 15-й плавке │
│включениями │
│
│(4.1.15) │ │
├──────────────┼──────────────────────────────────────────────────────────┤
│
Ультразвуко- │ Каждая ось │
│вой
контроль │
│
│внутренних │
│
│дефектов │
│
│(4.1.14,
│
│
│4.2.6) │ │
├──────────────┼──────────────────────────────────────────────────────────┤
│
Химический
│ По входному
контролю осевых заготовок или по ГОСТ 4728
│
│состав
стали │ │
│(4.1.3) │
│
├──────────────┴──────────────────────────────────────────────────────────┤
│
<*> Допускается остаток черновых осей от одной плавки в количестве
не│
│более
80 шт. присоединять к одной партии из
этой плавки. Остаток
осей│
│более
80 шт. следует считать отдельной партией. │
│ Допускается составлять сборную партию из
черновых осей разных плавок,│
│ранее
прошедших испытания с удовлетворительными
результатами. │
│
<**> Допускается составлять сборную партию, полученную перекатом
из│
│черновых
осей винтовой прокатки разных плавок, ранее прошедших испытания│
│с
удовлетворительными результатами, но имевших отклонения размеров. │
│
<***> При изготовлении двух и более черновых осей из одного
слитка -│
│только
на оси, изготовленной из головной части слитка. │
└─────────────────────────────────────────────────────────────────────────┘
Таблица 4
Порядок и
объем проведения приемосдаточных
испытаний чистовых
осей
Показатель качества
осей
|
Объем
выборки
|
Внешний вид (4.2.3), размеры (4.2.2),
качество нанесения
маркировки (4.2.10)
|
Каждая ось
|
Определение внутренних дефектов методом
ультразвукового
контроля (8.3)
|
Каждая ось
|
Определение поверхностных дефектов методом магнито-
порошкового контроля (7.15)
|
Каждая ось
|
7.6. Механические
свойства металла определяют:
- на одной черновой
оси для вагонов магистральных железных дорог и вагонов метрополитенов,
изготовленных из осевых заготовок, от каждой контролируемой партии. Результаты
распространяют на всю партию;
- на двух черновых
осях для локомотивов и моторных вагонов, изготовленных винтовой прокаткой,
радиально-ротационным деформированием и штамповкой, от каждой контролируемой
партии. Результаты распространяют на всю партию;
- на каждой
черновой оси для локомотивов, моторных вагонов и специального подвижного
состава, изготовленных свободной ковкой из осевых заготовок и непосредственно
из слитка, и для вагонов метрополитенов, изготовленной непосредственно из
слитка;
- при изготовлении
двух и более черновых осей для локомотивов и моторных вагонов из одного слитка
только на черновой оси, изготовленной из головной части каждого слитка.
Результаты распространяются также на черновые оси, изготовленные из остальной
части слитка.
Проверку
механических свойств металла черновых осей проводят на предприятии-изготовителе
до их механической обработки.
7.7. Контролю
макроструктуры подвергают черновые оси, изготовленные: из слитка - одну
черновую ось из головной части каждого слитка, из осевых заготовок - по
документам на осевую заготовку.
7.8. Контролю
микроструктуры подвергают черновые оси, изготовленные из слитка, - одну
черновую ось из головной части каждого слитка, из осевых заготовок - одну ось
из партии.
7.9. Контроль
загрязненности стали неметаллическими включениями - по документам о качестве на
осевую заготовку или по ГОСТ 4728. При ковке непосредственно из слитка - по
ГОСТ 1778.
7.10. При получении неудовлетворительных результатов по одному из видов
испытаний должна быть проведена повторная проверка по всему комплексу испытаний
на удвоенном числе образцов (от двух черновых осей для вагонов магистральных
железных дорог и вагонов метрополитена и от четырех черновых осей для
локомотивов и моторных вагонов, изготовленных винтовой прокаткой,
радиально-ротационным деформированием и штамповкой - по одному комплекту).
Если результаты
повторной проверки окажутся неудовлетворительными хотя бы по одному из
показателей, то всю партию черновых осей следует подвергнуть повторной
термической обработке, после чего их подвергают всему комплексу испытаний.
7.10.1. При
получении неудовлетворительных результатов механических испытаний образцов из
черновых осей, изготовленных из слитков, допускается перед повторной проверкой
подвергнуть их термической обработке вторично вместе с остатком припуска при
одинаковых температурных режимах.
После термической
обработки черновая ось должна быть подвергнута приемосдаточным испытаниям. При
получении неудовлетворительных результатов хотя бы по одному из показателей
черновую ось считают не соответствующей требованиям настоящего стандарта.
7.10.2. В случае получения неудовлетворительных результатов механических испытаний
черновой оси сборной партии оси соответствующей плавки не принимаются и
подвергаются повторной термической обработке.
Остальная часть
сборной партии черновых осей предъявляется как новая партия.
7.11. Проведение
более двух повторных термических обработок не допускается. Вторую
термообработку проводят для непрозвучивающихся осей.
Дополнительный
нагрев под правку до температуры 700 °C термической обработкой не считается.
7.12. После термической
обработки каждая черновая и чистовая ось должны быть подвергнуты
ультразвуковому контролю на прозвучиваемость и
отсутствие внутренних дефектов.
7.13. Допускается
подвергать повторной термической обработке с последующей правкой черновые оси,
имеющие радиальное биение, превышающее допустимое.
7.14. Черновые оси
с нечеткой маркировкой не принимают. Допускается исправлять маркировку в
холодном состоянии, если можно установить номер плавки и порядковый номер
черновой оси.
7.15.
Каждая чистовая ось должна быть подвергнута магнитопорошковому контролю на
отсутствие поверхностных дефектов по условному уровню чувствительности Б по ГОСТ 21105.
7.16. При
периодических испытаниях контроль качества накатывания роликами следует
проводить на одной окончательно обработанной:
- вагонной оси
ежемесячно от каждых 500 шт., накатываемых на однотипных станках;
- локомотивной оси,
оси специального подвижного состава и оси вагонов метрополитена один раз в
полгода от каждых 200 шт.
Для проверки
качества накатывания допускается использовать оси, забракованные по другим
параметрам.
8. Методы
контроля
8.1. Геометрические
размеры черновых осей и глубину залегания поверхностных дефектов измеряют
методом непосредственной оценки с допустимой погрешностью, мм:
- для диаметров
и глубины зарубки - +/- 0,5;
- для длин
от 0 до 1000 мм - +/- 1,0;
- "
" " 1001 "
2000 мм - +/- 2,0;
- "
" свыше 2001 мм - +/-
3,0.
8.2. Размеры
чистовых осей, кроме диаметров, измеряют предельными калибрами или универсальными
средствами измерения с допустимой погрешностью +/- 1,0 мм.
Диаметры чистовых
осей измеряют инструментом с ценой деления, мм:
- 0,01 - подступичных и предподступичных
частей всех типов осей;
- 0,005 - шеек осей
вагонов магистральных железных дорог и вагонов метрополитенов;
- 0,01 - шеек осей
локомотивов под подшипники скольжения;
- 0,002 - шеек осей
локомотивов под подшипники качения.
8.3. Ультразвуковой контроль черновых и чистовых осей на прозвучиваемость и отсутствие внутренних дефектов металла
следует проводить путем их прозвучивания в продольном
и поперечном направлениях при шероховатости торцов Rz
<= 20 мкм (Ra <= 6,3 мкм) по ГОСТ 2789, при
этом:
8.3.1. Не
соответствуют требованиям контроля на прозвучиваемость
оси, в которых затухание ультразвуковых колебаний на частоте 2,0 - 2,5 МГц
превышает 46 дБ.
При ультразвуковом
контроле на отсутствие внутренних дефектов не соответствуют требованиям оси, в
которых амплитуда эхо-сигналов равна или превышает амплитуду эхо-сигналов от
эталонного плоскодонного отражателя, залегающего на той же глубине, что и
дефект, и имеющего диаметр:
- 3,0 мм
(эквивалентная площадь 7,1 мм2) при глубине залегания до 380 мм;
- 6,0 мм ( " " 28,3 мм2)
" " " до 700 мм;
- 9,0 мм ( " " 63,6 мм2)
" " "
более 700 мм.
8.3.2. Не
соответствуют требованиям стандарта чистовые оси, в которых при контроле по эхо-импульсному методу продольными волнами в радиальном
направлении обнаружены внутренние дефекты:
- амплитуда
эхо-сигналов равна или превышает амплитуду эхо-сигналов от эталонного
отражателя диаметром 6,0 мм, залегающего на той же глубине, что и дефект
(эквивалентная площадь дефекта равна или более 28,3 мм2),
если в одной оси обнаружены шесть или более дефектов и минимальное условное
расстояние между любыми двумя из них более 50 мм.
8.3.3. Не
соответствуют требованиям чистовые оси, в которых при контроле по эхо-импульсному методу с цилиндрической поверхности
поперечными волнами обнаружены внутренние дефекты:
- амплитуда
эхо-сигналов равна или превышает амплитуду эхо-сигнала от эталонного
плоскодонного отражателя диаметром 3,0 мм, залегающего на той же глубине, что и
дефект (эквивалентная площадь дефекта равна или более 7,1 мм2).
Условия и порядок
проведения ультразвукового контроля, техническая документация на контроль,
подготовка дефектоскопов - по ГОСТ 20415.
Конкретная методика
испытаний должна быть согласована с потребителем в установленном порядке.
8.4. Контроль
механических свойств металла черновых осей (4.1.9) при испытаниях на растяжение
и ударный изгиб проводят на образцах.
Образцы изготовляют
из припуска, оставленного при формообразовании шейки, или из подступичной части черновой оси.
Припуск должен быть
предварительно заклеймен и может быть отделен от черновой оси после ее
термической обработки.
Для черновых осей,
изготовленных винтовой прокаткой и методами свободной ковки из осевых заготовок
по ГОСТ 4728, допускается изготовлять образцы из шейки черновой оси.
Для испытания на
растяжение берут один образец диаметром 10 мм пятикратной расчетной длины, для
испытания на ударный изгиб - четыре образца:
- от любой черновой
оси для вагонов магистральных железных дорог и вагонов метрополитена,
изготовленной из осевой заготовки, из контролируемой партии;
- от двух любых
черновых осей для локомотивов и моторных вагонов от контролируемой партии,
изготовленных из осевых заготовок винтовой прокаткой, радиально-ротационным
деформированием и штамповкой;
- от одной черновой
оси, изготовленной радиально-ротационным деформированием, - для локомотивов
промышленного транспорта, из контролируемой партии;
- от каждой
черновой оси для локомотивов, моторных вагонов и специального подвижного
состава, изготовленной методами свободной ковки из осевых заготовок по ГОСТ
4728 или непосредственно из слитка; при изготовлении двух и более черновых осей
из слитка - только от черновой оси, изготовленной из головной части слитка.
Схема вырезки
образцов для механических испытаний представлена на рисунке 4. Пробы
(заготовки) образцов вырезают из осей на расстоянии не менее половины радиуса
черновой оси плюс 10 мм от ее поверхности в направлении, параллельном
образующей. Заготовки образцов для определения механических свойств допускается
вырезать автогеном при условии оставления припуска не менее 30 мм на сторону.
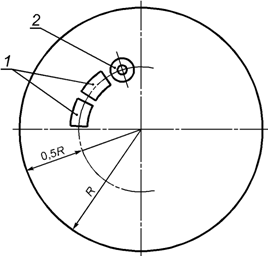
1 - две заготовки
для четырех образцов на ударную вязкость;
2 - заготовка
образца для испытания на растяжение
Рисунок 4. Схема
вырезки образцов
для механических
испытаний
8.5. Испытания на
растяжение (4.1.9) следует проводить на образцах типов I, II, III N 4 по ГОСТ
1497.
8.6. Ударную
вязкость (4.1.9) определяют на образцах типа I по ГОСТ 9454.
Допускается делать
концентраторы сверлением.
8.7. Радиальное
биение поверхности элементов (шеек и средней части) черновой оси относительно
поверхности подступичных частей определяют как
разность зазоров с двух противоположных сторон контролируемой плоскости между
лекальной линейкой типа ШД по ГОСТ 8026 или другим аттестованным средством
измерения, наложенным на поверхности подступичных
частей, и поверхностью шеек и средней части. Контроль осуществляют не менее чем
в двух перпендикулярных плоскостях посередине длины контролируемых элементов, а
при вращении на станке - по биению оси.
8.8. Отбор проб для
контрольного химического анализа - по ГОСТ 7565.
8.9. Химический
состав принимают по ГОСТ 4728 или по плавочному
химическому составу слитков. Допускается при приемке черновых осей по
требованию представителя заказчика проводить контрольный химический анализ.
8.10. Контроль
дефектов макроструктуры (4.1.13) - по ГОСТ 10243.
Макроструктуру
черновых осей, изготовленных из осевых заготовок, проверяют по ГОСТ 4728.
8.11. Контроль
неметаллических включений (4.1.15) - по ГОСТ 4728.
При изготовлении
черновых осей из слитков контроль неметаллических включений проводят по методу
Ш-1 ГОСТ 1778.
8.12. Образцы для
контроля микроструктуры должны быть изготовлены из одного из недеформированных
концов образца на растяжение вдоль плоскости, перпендикулярной к продольной
оси.
Контроль
микроструктуры - по ГОСТ 5639.
8.13. Для проверки
качества накатывания (4.2.7) чистовых осей вырезают продольные шлифы, по
сечению которых определяют твердость:
- у вагонных осей -
из шейки и подступичной части;
- у осей вагонов
метрополитенов - из шейки, подступичной и средней
частей;
- у локомотивных
осей и осей специального подвижного состава - из шейки и подступичной
части.
8.14. Маркировку
проверяют визуально. Оси с неясной маркировкой не принимают. Допускается
исправлять маркировку в холодном состоянии, если можно установить номер плавки
и номер оси.
9.
Транспортирование и хранение
9.1. Каждая партия
черновых и чистовых осей должна сопровождаться документом, удостоверяющим их
соответствие требованиям настоящего стандарта и включающим:
- наименование
предприятия-изготовителя;
- номер плавки;
- номера черновых и
чистовых осей;
- химический состав
стали - по ГОСТ 4728 или из плавочного анализа (для
черновых осей сборных партий - химический состав используемых плавок);
- тип или номер
чертежа черновой оси; тип чистовых осей (для вагонов железных дорог - по ГОСТ
22780);
- результаты
испытаний;
- обозначение
настоящего стандарта.
Документ должен
быть подписан представителем отдела технического контроля
предприятия-изготовителя и представителем заказчика.
Указанный документ
следует хранить на предприятии-изготовителе 15 лет.
При изготовлении
чистовой оси на нескольких предприятиях каждое делает запись о выполненных операциях,
подписывает их и пересылает вместе с осями. Указанный документ предприятие,
сформировавшее колесную пару, хранит 20 лет.
9.2. Чистовые оси
должны быть защищены от коррозии по ГОСТ 9.014 и ударов.
Не допускается
погрузка и разгрузка черновых и чистовых осей при помощи магнита.
9.3. Условия
транспортирования черновых и чистовых осей в части воздействия климатических
факторов - по группе 7 (Ж1), а хранения - по группе
(ОЖ3) ГОСТ 15150.
9.4. Черновые оси
транспортируют пачками массой до 10 т.
Прочностные данные
обвязок должны обеспечивать их сохранность при транспортировании и проведении
погрузочно-разгрузочных работ по ГОСТ 21650.
Погрузку, крепление
и транспортирование черновых осей на открытом подвижном составе следует
осуществлять в соответствии с правилами перевозки грузов.
На пачке должен
быть прикреплен ярлык с транспортной маркировкой по ГОСТ 14192.
9.5. Чистовые оси
транспортируют в законсервированном виде в специальных контейнерах или упаковке
в соответствии с правилами перевозки грузов на открытом подвижном составе.
10.
Гарантии изготовителя
10.1. Изготовитель
черновых и чистовых осей гарантирует соответствие осей требованиям настоящего
стандарта при соблюдении условий эксплуатации, транспортирования и хранения.
10.2. Изготовитель
черновых осей гарантирует показатели качества металла (4.1.14, 4.1.16) на весь
срок службы оси.
10.3. Гарантийный
срок эксплуатации чистовой оси:
- локомотивов и
вагонов магистральных железных дорог - 8,5 лет со дня ввода в эксплуатацию колесной
пары;
- вагонов
метрополитенов - 800000 км пробега или четыре года со дня ввода в эксплуатацию.
В случае
переформирования колесной пары осей всех типов гарантийные обязательства на подступичные части оси прекращаются.
В случае перешлифовки шеек осей вагонов метрополитенов гарантии по
шейкам снимаются.
10.4. Гарантии не
распространяются на готовые оси, подвергнутые любым видам сварки, обработке
газовой горелкой, подогреву, металлизации, нанесению слоев электролитическим
или химическим способом при ремонте и техническом обслуживании колесных пар у
потребителя.
Приложение А
(рекомендуемое)
ИСО
1005-3-82
ПОДВИЖНОЙ СОСТАВ
ЖЕЛЕЗНЫХ ДОРОГ.
ЧАСТЬ 3.
ОСИ ДЛЯ ТЯГОВЫХ И
ПРИЦЕПНЫХ ВАГОНОВ. ТРЕБОВАНИЯ К КАЧЕСТВУ
А.1. Назначение и
область применения
А.1.1. Настоящая
часть стандарта определяет требования к изготовлению и поставке осей подвижного
состава из нелегированных и легированных сталей в соответствии с таблицей А.1 и
разделом А.4.
Таблица А.1
Марки
сталей, химический состав, виды термообработки
и механические
свойства
┌─────┬────────────────────────────────────────────┬───────┬────────────────────────────────┐
│Марка│ Химический состав, не более
<1> │Термо-
│ Механические свойства
<3> │
│стали├────┬────┬────┬────┬────┬────┬────┬────┬────┤обра-
├───────┬─────┬─────────┬────────┤
│ │ C
│ Si │ Mn
│ P │ S │ Cr │ Cu │ Mo │ V │ботка │Предел │Удли-│Предел │Ударная │
│ │
│ │ │
│ │ │
│ │ │в усло-│теку- │нение│прочности│вязкость│
│ │
│ │ │
│ │ │
│ │ │виях │чести
│A, % │на растя-│образцов│
│ │
│ │ │
│ │ │
│ │ │постав-│R <4>,│ │жение │
при
│
│ │
│ │ │
│ │ │
│ │ │ки
<2> │ e │ │R , Н/мм2│
20 °C │
│ │
│ │ │
│ │ │
│ │ │ │Н/мм2,
│ │ m │<5> KU, │
│ │
│ │ │
│ │ │
│ │ │ │не │
│ │не менее│
│ │
│ │ │
│ │ │
│ │ │ │менее │
│ │ │
├─────┼────┼────┼────┼────┼────┼────┼────┼────┼────┼───────┼───────┼─────┼─────────┼────────┤
│
А1
│0,40│0,50│1,20│0,04│0,04│0,30│0,30│0,08│0,05│ N
│ 300 │ 22
│520 - 650│ 25 │
│
<6> │ │ │
│ │ │
│ │ │
│ T │
350 │ 24 │550 - 700│ 40
│
├─────┼────┼────┼────┼────┼────┼────┼────┼────┼────┼───────┼───────┼─────┼─────────┼────────┤
│
А2
│0,50│0,50│1,20│0,04│0,04│0,30│0,30│0,08│0,05│ N
│ 360 │ 17
│600 - 750│ 20 │
│ │
│ │ │
│ │ │
│ │ │
T │ 390
│ 19 │620 -
770│ 25 │
├─────┼────┼────┼────┼────┼────┼────┼────┼────┼────┼───────┼───────┼─────┼─────────┼────────┤
│
А3
│0,40│0,50│1,60│0,04│0,04│0,50│0,30│0,40│0,10│ N
│ 420 │ 19
│650 - 800│ 40 │
│ │
│ │ │
│ │ │
│ │ │
T │ │ │ │ │
├─────┼────┼────┼────┼────┼────┼────┼────┼────┼────┼───────┼───────┼─────┼─────────┼────────┤
│
А4
│0,40│0,50│0,80│0,04│0,04│1,20│0,30│0,35│0,10│ N
│ 420 │ 19
│650 - 800│ 40 │
│ │
│ │ │
│ │ │
│ │ │
T │ │ │ │ │
├─────┴────┴────┴────┴────┴────┴────┴────┴────┴────┴───────┴───────┴─────┴─────────┴────────┤
│
<1> А.5.1.1.
│
│
<2> N - нормализация или нормализация с отпуском; T - закалка и
отпуск │
│(А.4.2
и А.7.7.2).
│
│
<3> R - предел текучести;
R - предел прочности при
растяжении; A -
│
│ e m │
│ __
│
│удлинение
после разрыва (L = 5,65 \/S ); KU - ударная вязкость образцов с │
│ о о │
│U-образным
надрезом при 20 °C; 1 Н/мм2 = 1 МПа.
│
│
<4> Требования к R
являются удовлетворительными, если значение │
│ e
│
│разрушающего напряжения
растяжения R равно
или более нормируемого │
│
10,5 │
│значения
R .
│
│ e
│
│
<5> Среднее из трех значений при испытании; один
отдельный результат
│
│может
быть ниже минимального значения, приведенного в таблице, но не менее │
│70%
этого значения.
│
│
<6> Если по соглашению требуется
сталь без термообработки (прокатка │
│или
ковка), то применяют обозначение А0 вместо А1, и
механические свойства
│
│в
условиях поставки должны быть следующими: │
│ R
не менее 280 Н/мм2; R = 500 - 650 Н/мм2; A = 20%; KU не менее │
│ e m min │
│20
Дж. │
└───────────────────────────────────────────────────────────────────────────────────────────┘
А.1.2.
Дополнительно к этой части ИСО 1005-3 применяют требования ИСО 404.
А.2. Нормативные
ссылки
ИСО 82-76. Сталь.
Испытание на растяжение
ИСО 83-76.
Испытание на ударную вязкость по Шарпи (образцы с U-образным надрезом)
ИСО 377-1-89. Отбор
и подготовка образцов и проб для испытаний деформированной стали. Часть 1.
Образцы и пробы для механических испытаний
ИСО 377-2-89. Отбор
и изготовление образцов и проб для испытаний деформируемой стали. Часть 2.
Образцы для определения химического состава
ИСО 404-92. Сталь и
заготовки стальные. Общие технические требования поставки
ИСО 643-83. Стали.
Микрографическое определение размеров ферритных или аустенитных
зерен
ИСО 5948-94.
Подвижной состав железных дорог. Ультразвуковой приемочный контроль.
А.3. Информация,
представляемая потребителем
При заказе
потребитель должен сообщить следующую информацию:
a) номер настоящего
стандарта;
b) марку стали
(А.4.1);
c) вид
термообработки (А.4.2, А.6.5);
d) качество
поверхности (А.4.3);
e) необходимость
контрольного анализа (А.5.1.2);
f) необходимость
исследования микроструктуры на неоднородность и размер зерен (А.5.2.2.2 и
таблица А.4);
g) виды требуемых
испытаний (А.5.2.2.3, А.7.3.1, А.7.7.3.5, А.7.8.5 и таблица А.4);
h) допуски на
размеры (А.5.4.1);
j) необходимость
специальной маркировки (А.5.5);
k) условия
требуемого контроля (А.7.1);
m) необходимость
специальной подготовки проб и образцов для испытаний (А.7.7.2);
n) методы
антикоррозионной защиты (А.8.1);
p) необходимость
согласования гарантийных условий (раздел А.9).
А.4.
Классификация
Оси следует
классифицировать в заказе или прилагаемых к нему документах в соответствии с
используемой маркой стали, условиями термообработки и качеством поверхности,
методом контроля (таблица А.3).
А.4.1.
Марки сталей
Настоящий стандарт
определяет следующие марки стали в соответствии с их свойствами, приводимыми в
таблице А.1:
нелегированные
стали А1 и А2;
легированные стали
А3 и А4.
А.4.2. Виды
термообработки
Оси могут
поставляться:
a) без
термообработки <*>;
--------------------------------
<*> С учетом
исключения, приведенного в таблице А.1 (сноска 6), при заказе осей без
термообработки следует учитывать следующее. Потребитель может обусловить
предельное содержание элементов. В этом случае ответственность за получение
требуемых механических свойств возлагается на предприятие, проводящее
термообработку. Если предельное содержание элементов не оговорено в заказе, то
изготовитель должен гарантировать, что поставляемые оси будут иметь
механические свойства, приведенные в таблице А.1.
b) в состоянии
нормализации или нормализации с последующим отпуском (символ N) - марки А1 и А2;
c) подвергнутые
закалке и отпуску (символ T) - марки А1, А2, А3 и А4.
Независимо от вида
термообработки, указанного в заказе, в случае неэффективно проведенной дегазации
следует принять соответствующие меры, которые могут включать, например,
медленное охлаждение, с тем, чтобы избежать возникновения флокенов.
Если оговорены такие требования, то администрация железных дорог должна быть
проинформирована о проведенных операциях.
А.4.3.
Качество поверхности
При поставке
поверхности должны быть установленного качества:
a) после черновой
штамповки или черновой прокатки в случае, если оси изготовлены методом горячей
ковки или горячей прокатки и не подвергались какой-либо механической обработке;
b) после черновой
механической обработки, если ось не подвергалась окончательной (чистовой)
механической обработке, но подвергалась грубой черновой обработке полностью или
только в определенных местах, которые должны быть механически обработаны;
c) полуобработанные, если окончательной механической обработке
подвергнуты только определенные участки, которые рассматриваются как
окончательно обработанные;
d) окончательно
обработанные, когда все участки оси, которые должны подвергаться механической
обработке, окончательно обработаны.
А.5.
Технические требования
А.5.1. Химический
состав
А.5.1.1.
Максимальное содержание различных химических элементов приведено в таблице А.1.
Эти значения определяют при анализе плавки. Содержание Cr,
C, Mo и V определяют в изделии, однако предварительно
содержание этих элементов контролируют при анализе плавки.
А.5.1.2.
Если необходимо выполнить контрольный анализ изделия, то это должно быть
оговорено в заказе. В этом случае данные анализа изделия могут отличаться от
требований, изложенных в таблице А.1, на значения, приведенные в таблице А.2.
Таблица А.2
Допускаемые
отклонения данных анализов плавки и изделия
┌────────┬──────────────────────────────────────┬─────────────────────────┐
│Элемент
│ Максимальное значение в соответствии │ Допускаемое
отклонение │
│ │со спецификацией при анализе
плавки, %│данных анализа изделия, %│
├────────┼──────────────────────────────────────┼─────────────────────────┤
│Углерод │ От
0,30 до 0,50 │ +0,03 │
│Кремний
│ 0,50 │ +0,04 │
│Марганец│ 0,80 │ +0,06 │
│ │ 1,20 │ +0,08 │
│ │ 1,60 │ +0,10 │
│Фосфор │ 0,04 │ +0,005 │
│Сера │ 0,04 │ +0,005 │
└────────┴──────────────────────────────────────┴─────────────────────────┘
А.5.2. Физические
свойства
А.5.2.1. Обработка
поверхности
А.5.2.2.
Отсутствие дефектов
А.5.2.2.1. Общие
положения
Оси должны прозвучиваться по всей длине и не иметь каких-либо
дефектов, мешающих использованию осей.
А.5.2.2.2.
Микроструктура
Микроструктура
нормализованных или подвергнутых закалке и отпуску осей должна быть равномерной
и типовой для обусловленной термообработки. При определении по ИСО 643 размер
зерен должен быть не более балла 5.
А.5.2.2.3.
Другие характеристики внешнего вида и прочности
Если в заказе или
прилагаемых к нему документах для контроля дефектов предусматриваются магнитная
дефектоскопия, проверка ультразвуком (ИСО 5948) или исследование макроструктуры
с помощью серных отпечатков, то критерии приемки должны быть обусловлены в
заказе или прилагаемых к нему документах.
При оценке качества
макроструктуры с помощью серных отпечатков используют методические указания по
контролю макроструктуры, если не оговорены другие документы.
А.5.3. Механические
свойства
Механические
свойства осей после термообработки должны соответствовать данным таблицы А.1.
А.5.4. Размеры
А.5.4.1.
Размеры осей должны соответствовать приведенным в
заказе или прилагаемых к нему документах в пределах указанных допусков.
А.5.5.
Маркировка (А.6.4)
Маркировку
установленных размеров наносят в горячем или холодном состоянии в месте,
определяемом национальными стандартами, заказом или прилагаемыми документами.
Если не оговорены
другие требования, то каждая ось должна иметь клеймо со следующими данными:
a) маркой фирмы;
b) номером плавки;
c) маркой стали и
условиями термообработки (сноски 2 и 6 к таблице А.1);
d) датой
изготовления (месяц и две последние цифры года изготовления).
Если не оговорены
другие требования, то оси следует клеймить на такую глубину, которая позволяла
бы при окончательной механической обработке удалить маркировку.
Не допускается
применять клейма с острыми углами, если клеймение проводится не на торцевой
поверхности оси.
А.6.
Изготовление осей
А.6.1.
Сталеплавильный процесс
Оси изготовляют из
стали, полученной мартеновским, электродуговым и кислородно-конвертерным
способами; другие процессы для выплавки стали допускается использовать по
соглашению между потребителем и изготовителем. Сталь следует выдерживать до
полного успокоения в печи или ковше.
А.6.2. Изготовление
осей
Оси изготовляют из
слитков методами:
a) только ковки
(А.6.2.1);
b) только прокатки
(А.6.2.2);
c) прокатки и
последующей ковки (А.6.2.3).
А.6.2.1. Оси,
изготовляемые только ковкой
Максимальная
площадь поперечного сечения оси, изготовленной ковкой, должна быть равна не
более 1/3 площади минимального поперечного сечения первоначального слитка.
А.6.2.2. Оси,
изготовляемые только прокаткой
Максимальная
площадь поперечного сечения оси, изготовленной прокаткой, должна быть равна не
более 1/5 площади минимального первоначального слитка.
А.6.2.3.
Оси, изготовляемые прокаткой с последующей ковкой
Максимальная
площадь поперечного сечения оси, изготовленной методом прокатки и последующей
ковки, должна быть равна не более 1/4 площади минимального поперечного сечения
первоначального слитка.
А.6.3. Удаление
дефектных участков
Участки слитков,
квадратных заготовок или круглого проката, не соответствующие требованиям
А.5.2.2, следует удалять до или во
время изготовления оси.
А.6.4.
Маркировка осей при их изготовлении
Все слитки,
квадратные заготовки, круглый прокат и оси маркируют на каждой стадии
изготовления так, чтобы перед поставкой каждая ось или образец для испытаний
могли быть маркированы в соответствии с требованиями, изложенными в А.5.5. Там,
где клеймо отличается от конечной маркировки, определяемой в соответствии с
А.5.5, оно не должно быть видимым после механической обработки на готовой оси.
А.6.5.
Термообработка
После горячей
обработки и маркировки оси следует подвергать термообработке, обусловленной в
заказе или прилагаемых к нему документах (А.4.2).
Как правило,
различные виды термообработки необходимо выполнять так, чтобы гарантировать:
a) равномерность
структуры сопоставимых частей той же самой оси и осей одной партии;
b) отсутствие
деформации.
А.6.6. Механическая
обработка
Условия
механической обработки должны соответствовать требованиям, предъявляемым к
качеству поверхности и допускам. На механически обработанных торцевых
поверхностях следует обозначить центр с тем, чтобы облегчить выполнение
последующих токарных операций и получить центровые отверстия готовых осей без
затруднения.
А.6.7. Устранение
дефектов
А.6.7.1. Правка
необработанных осей
Правку осей
проводят перед любой механической обработкой и до того, как вырезают образцы
для механических испытаний и микрографического исследования.
Если правку
осуществляют при температуре ниже 500 °C, то оси после правки следует
подвергать термообработке по таблице А.3.
Таблица А.3
┌─────────────────────────────────────┬───────────────────────────────────┐
│Условия
термообработки осей до правки│
Термообработка после правки
│
├─────────────────────────────────────┼───────────────────────────────────┤
│
a) Не подвергающиеся термообработке │ Неполный
отжиг при температуре │
│ │от
500 °C до 650 °C │
│
b) Не подвергающиеся │ Не требуется
дополнительная │
│термообработке,
которые следует
│термообработка, кроме обусловленной│
│поставлять
нормализованными или │в заказе │
│после
закалки и отпуска
│
│
│
c) Нормализованные │ Неполный отжиг при
температуре │
│ │от
500 °C до 650 °C или вновь │
│
│подвергнуть нормализации
│
│
d) Подвергающиеся закалке и отпуску │ Неполный
отжиг при температуре │
│ │от
500 °C до тау' = 30 °C (тау' - │
│
│ т т │
│
│действительная температура закалки)│
│ │или
вновь подвергнуть закалке │
│ │и
отпуску │
└─────────────────────────────────────┴───────────────────────────────────┘
Если нормализованные
оси подвергают правке при температуре, равной или превышающей 500 °C, то их
механические свойства и структура должны соответствовать требованиям настоящего
стандарта.
А.6.7.2.
Допускаемые методы исправления дефектов
Исключая
поверхности, подвергаемые чистовой механической обработке, например места
посадки колеса, шеек и галтелей, на которых не допускаются исправления,
поверхностные дефекты допускается удалять вырубкой или шлифованием при условии,
что не возникнет тепловое растрескивание и будут
выдержаны допуски на размеры.
А.6.7.3. Недопускаемые методы исправления дефектов
Не допускаются
любые виды сварки, обработка газовой горелкой, подогрев, металлизация,
нанесение слоя электролитическим или химическим способом и т.д. В таких случаях
всю партию осей бракуют.
А.7. Контроль осей
А.7.1. Виды
технического контроля
А.7.1.1.
Потребитель должен оговорить в заказе методы контроля (раздел А.6), требования
к качеству (раздел А.5), кто проводит контроль:
a) представитель
отдела контроля качества изготовителя;
b) в присутствии
потребителя, представителя органа, назначенного им.
Если отсутствуют
требования в заказе, то следует руководствоваться таблицей А.4.
Таблица А.4
Виды и
число проводимых испытаний
┌─────────────────┬────────────────┬─────────────┬─────┬────────────┬─────┐
│Термообработка
в │ Вид испытания │Классификация│Объем│ Число осей
│Число│
│условиях
поставки│
│ видов │испы-│ в партии, │испы-│
│ │ │испытаний
<1>│таний│подвергаемых│таний│
│ │ │ │<2> │ испытаниям │на │
│ │ │ │ ├────────────┤ось │
│ │ │ │ │Общее число │ │
│ │ │ │ │
осей в
│ │
│ │ │ │ │
партии │ │
│ │ │ │ ├─────┬──────┤ │
│ │ │ │ │Менее│Более │ │
│ │ │ │ │ 100 │ 100 │
│
├─────────────────┼────────────────┼────┬────┬───┼─────┼─────┴──────┴─────┤
│1.
Все виды │Химический │ m
│ a │ - │ c │
По А.5.1.1, │
│термообработки │анализ │ │
│ │ │А.5.1.2, А.7.7.3.1│
├─────────────────┼────────────────┼────┼────┼───┼─────┼─────┬──────┬─────┤
│2.
Нормализация, │Испытание на
│ m │ b │ h │c, h │ 1
│ 2 │
1 │
│закалка
и отпуск │растяжение
│ │ │
│ │ │ │ │
├─────────────────┼────────────────┼────┼────┼───┼─────┼─────┼──────┼─────┤
│3.
Термообработка│Испытание на │
│ │ │
│ │ │ │
│не
предусмотрена │растяжение: │
│ │ │
│ │ │ │
│ │ для стали А0 │ m │ b
│ f │ c │
1 │ 2
│ 1 │
│ │<3> │ │
│ │ │
│ │ │
│ │ для стали │ m
│ b │ f │ c
│ 1 │
2 │ 1
│
│ │А1
- А4 <4> │ │
│ │ │
│ │ │
├─────────────────┼────────────────┼────┼────┼───┼─────┼─────┼──────┼─────┤
│4.
Нормализация, │Испытание
│ m │ b │ f │c, h │ 1
│ 2 │
3 │
│закалка
и отпуск │на удар (KU)
│ │ │
│ │ │ │ │
├─────────────────┼────────────────┼────┼────┼───┼─────┼─────┼──────┼─────┤
│5.
Термообработка│Испытание │ │
│ │ │
│ │ │
│не
предусмотрена │на удар (KU): │
│ │ │
│ │ │ │
│ │ для стали А0 │ m │ b
│ f │ c │
1 │ 2
│ 3 │
│ │ для стали │ o
│ b │ h │ c
│ 1 │
2 │ 3
│
│ │А1
- А4 │ │
│ │ │
│ │ │
├─────────────────┼────────────────┼────┼────┼───┼─────┼─────┼──────┼─────┤
│6.
Нормализация, │Микроструктура
│ m │ a │ h │c, h │ 1
│ 2 │
3 │
│закалка
и отпуск │
│ │ │
│ │ │ │ │
├─────────────────┼────────────────┼────┼────┼───┼─────┼─────┼──────┼─────┤
│7.
Термообработка│Микроструктура │ o
│ a │ h │ c
│ 1 │
2 │ 3
│
│не
предусмотрена │
│ │ │
│ │ │ │ │
├─────────────────┼────────────────┼────┼────┼───┼─────┼─────┴──────┼─────┤
│8.
Все виды │Макроструктура │ o
│ a │ h │ p │По А.7.7.3.5│ 1
│
│термообработки │ │ │
│ │ │ │ │
├─────────────────┼────────────────┼────┼────┼───┼─────┤
├─────┤
│9.
Все виды │Ультразвуковой │ o
│ a │ h │ p
│ │ 1
│
│термообработки │контроль │ │
│ │ │ │ │
├─────────────────┼────────────────┼────┼────┼───┼─────┼─────┬──────┼─────┤
│10.
Все виды │Магнитоскопия │ o
│ a │ h │ p
│100% │ 100% │
1 │
│термообработки │ │ │
│ │ │
│ │ │
├─────────────────┼────────────────┼────┼────┼───┼─────┤ │ ├─────┤
│11.
Все виды │Внешний вид │ m
│ a │ f │ p
│ │ │
1 │
│термообработки │и размеры │ │
│ │ │
│ │ │
├─────────────────┴────────────────┴────┴────┴───┴─────┴─────┴──────┴─────┤
│
<1> m - обязательное испытание; │
│ o
- испытание проводят по согласованию с заказчиком; │
│ a - испытание проводит отдел контроля
качества изготовителя по │
│ИСО
404;
│
│ b - испытание проводят в присутствии
потребителя; │
│ h - испытание проводят до
термообработки;
│
│ f - испытание проводят после
окончательной обработки.
│
│
<2> c - оси из стали одной плавки; │
│ c, h - оси из стали одной плавки, подвергнутые
одной и той же│
│термообработке;
│
│ p - ось, принимаемая за единицу
испытания. │
│
<3> См. сноску 6 к таблице А.1. │
│
<4> Испытание проводят в условиях поставки и на контрольных
образцах,│
│подвергавшихся термообработке, предусмотренной для
данных марок сталей│
│(А.4.1
и А.7.7.2).
│
└─────────────────────────────────────────────────────────────────────────┘
А.7.1.2. Передача
функций контроля потребителем отделу контроля качества изготовителя не лишает
права потребителя контролировать эффективность системы контроля изготовителя и
методов испытаний и проверок. Ему должно быть разрешено
присутствовать при любых испытаниях, проводимых предприятием-изготовителем, и
проверять записанные результаты.
А.7.2. Контроль
изготовления
А.7.2.1. Если
контроль изготовления осуществляет отдел контроля качества изготовителя или
потребителя, то необходимо руководствоваться следующим.
А.7.2.1.1.
Изготовитель должен ознакомить потребителя с основным процессом, используемым
для выполнения заказа, а также согласовать с ним основные изменения, которые он
собирается осуществить и которые могут повлиять на
качество осей.
А.7.2.1.2.
Изготовитель обязан при приемке подтвердить, что требования к изготовлению осей
выполнены (А.7.5).
А.7.3. Контроль
характеристик осей
А.7.3.1.
Виды испытаний
В таблице А.4
приведены виды испытаний, которые следует проводить, и степень их
обязательности.
А.7.3.2. Число
осей, подвергаемых испытаниям, и комплектование партий
Соответствующее
число осей для каждого типа испытаний приведено в таблице А.4.
Для проведения
приемочных испытаний оси должны быть сгруппированы в партию. Каждая партия
должна включать оси, изготовленные из стали одной плавки и подвергавшиеся
одинаковой термообработке, если она применялась. В партию могут входить оси
разной формы и размеров.
А.7.3.3. Условия
приемки осей
При предоставлении
осей для контроля испытаний условия должны соответствовать требованиям,
приведенным в таблице А.4.
А.7.4.
Представление осей для контроля испытаний потребителем
А.7.4.1.
Потребитель (А.7.1.1) должен быть письменно уведомлен (А.7.5.2) о дате
представления осей для контроля с указанием числа осей в каждой партии и номера
заказа.
А.7.4.2.
Если контроль испытания, который в соответствии с таблицей А.4 должен
осуществляться после механической обработки, проводит потребитель (А.7.1.1), то
изготовитель должен представить данные в два этапа, а именно:
a) после
окончательной термообработки, но перед механической обработкой;
b) после
окончательной обработки.
А.7.5.
Сертификат
А.7.5.1. Если
контроль качества продукции проводит отдел контроля качества изготовителя или
заказчика, то изготовитель должен подтвердить выполнение требований настоящего
стандарта. Сертификат окончательных испытаний должен также содержать
результаты:
- химического
анализа;
- испытаний на
растяжение;
- испытаний на
удар.
А.7.5.2.
Изготовитель должен обеспечить представление соответствующих сертификатов
испытаний, за которые он несет ответственность:
a) при поставке,
если ему доверено осуществлять все испытания, или
b) при первом
представлении для контроля (А.7.4.2), если ему передано право контроля в этот
период испытаний.
А.7.6. Число
проводимых испытаний (проверок)
Число осей,
представленных для контроля, и число испытаний, приходящихся на каждую ось, приведены в таблице А.4.
А.7.7. Отбор проб и
подготовка образцов для испытаний
А.7.7.1. Отбор проб
После маркировки
партии контролер должен произвольно отобрать ось или оси для испытаний. Оси
должны быть помечены несмываемой краской в месте вырезки образца. Образцы
вырезают из осей или из зоны припуска длиной не менее 200 мм.
А.7.7.2.
Подготовка проб и образцов для испытаний
Если нет других
требований, то условия подготовки проб и образцов для испытаний должны
соответствовать требованиям ИСО 377.1, ИСО 377.2 со следующими дополнениями.
Если оси заказывают
нетермообработанными, исключая оси типа А0 (таблица А.1), то образцы, предназначенные для
механических испытаний, следует подвергать термообработке, установленной в
таблице А.1 для данной марки стали. Если в соответствии с таблицей А.1
предусматриваются два вида термообработки для данной марки стали, то вид
требуемой термообработки должен быть указан в заказе или прилагаемых к нему
документах.
На образцах для
испытаний должно оставаться клеймо контролера и изменять его можно только в
присутствии контролера.
А.7.7.3. Число и
местоположение образцов для испытаний
Образцы для
испытаний следует вырезать из заранее клейменных
участков, предназначенных для вырезки образцов, их должен маркировать
контролер.
А.7.7.3.1.
Химический анализ
Изготовитель должен
сообщить результаты анализа плавки, из которой получена сталь. Если потребитель
желает проверить ее состав по всем или некоторым элементам, то отбирают одну из
следующих проб на одной из испытуемых осей:
- не менее 50 г
мелкой стружки, набранной с полного поперечного сечения оси;
- в случае
проведения спектрального анализа - одна проба для анализа из образца для
проведения испытаний на растяжение, указанного на рисунке А.1.
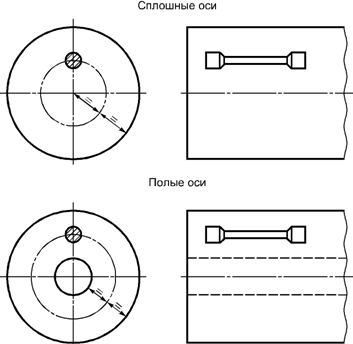
Рисунок А.1
А.7.7.3.2.
Испытание на растяжение
Один образец для
испытаний должен быть вырезан из места, указанного на рисунке А.1.
Образцы для
испытаний должны быть подготовлены в соответствии с требованиями ИСО 82 и иметь
диаметр от 10 до 16 мм и длину, равную пяти диаметрам.
А.7.7.3.3.
Испытание на удар (образец с U-образным надрезом)
Для испытаний
должны быть вырезаны три образца из места, указанного на рисунке А.2. Внешние
образцы для испытаний должны близко примыкать к среднему образцу для испытаний
на удар.
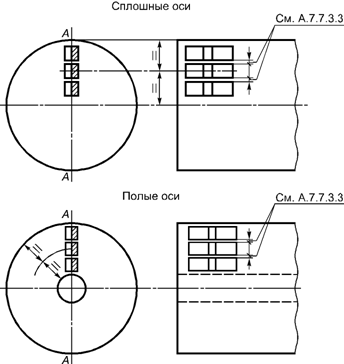
Рисунок А.2
Маркировка образцов
для испытаний на удар должна обеспечить распознавание продольных поверхностей
образцов для испытаний, параллельных диаметру АА участка оси (рисунок А.2).
Образцы для
испытаний следует изготовлять в соответствии с требованиями ИСО 83. Ось надреза
должна быть параллельной диаметру АА (рисунок А.2).
А.7.7.3.4.
Исследование микроструктуры
Образцы для
исследования должны быть изготовлены из одного из недеформированных концов
образца на растяжение вдоль плоскости, перпендикулярной к продольной оси.
Сечение, полученное
таким образом, должно быть подготовлено в соответствии с требованиями ИСО 643.
А.7.7.3.5.
Исследование макроструктуры, ультразвуковая дефектоскопия, магнитография
Если предусмотрены
исследования макроструктуры или магнитография, то
требования, связанные с числом испытаний и участками осей, которые следует
подвергать испытаниям, следует указывать в заказе или прилагаемых к нему
документах.
Если
предусматривается ультразвуковой контроль, то его проводят в соответствии с ИСО
5948.
А.7.8. Методы
испытаний
А.7.8.1. Химический
анализ
Химический анализ
следует выполнять в соответствии с методикой, устанавливаемой соответствующими
международными стандартами и согласованной с потребителем. В случае разногласий
следует использовать только методики, рекомендуемые ИСО.
А.7.8.2. Испытание
на растяжение
Испытания на
растяжение должны быть выполнены в соответствии с требованиями ИСО 82.
А.7.8.3. Испытание
на удар (образцы с U-образным надрезом)
Испытания на удар
следует выполнять в соответствии с требованиями ИСО 83.
А.7.8.4.
Исследование микроструктуры
Исследование
микроструктуры следует выполнять в соответствии с требованиями ИСО 643.
А.7.8.5.
Исследование макроструктуры, ультразвуковой контроль и магнитография
Требования, связанные
с исследованием макроструктуры и магнитографией,
оговаривают в заказе или прилагаемых к нему документах.
Если другие
требования не согласовывались, то приемочный ультразвуковой контроль проводят в
соответствии с требованиями ИСО 5948.
А.7.8.6. Контроль
размеров
А.7.9. Заключение
по контролю
При любых дефектах
внешнего вида или при отклонениях размеров ось бракуют. Ось бракуют также при
обнаружении с помощью ультразвуковой дефектоскопии и магнитоскопии
отклонений, превышающих допустимые.
При любых других
дефектах, обнаруженных в осях и не отвечающих требованиям стандарта, всю
соответствующую партию бракуют в соответствии с требованиями ИСО 404.
А.7.10. Повторные
испытания
Если другие условия
не согласовывались, то повторные испытания проводят в соответствии с ИСО 404.
А.8. Поставка
А.8.1.
Защита от коррозии при транспортировании
После контроля и до
передачи на хранение или перед отправкой все окончательно обработанные
механическим способом поверхности осей, прошедших приемку, должны быть защищены
от коррозии методом, согласованным с потребителем.
Примечание. Любые
защитные покрытия эффективны в течение ограниченного срока, особенно если
транспортирование осуществляется по морю или в географические районы с
повышенной влажностью. Поэтому по прибытии к месту назначения оси должны быть
немедленно подвергнуты ревизии; при этом определяют необходимость проведения
дополнительной защиты от коррозии.
А.8.2. Защита от
механического повреждения при транспортировании
Окончательно
обработанные механическим способом части осей, прошедших приемочные испытания,
должны быть надежно защищены до отправки для предотвращения их от механического
повреждения при транспортировании.
А.9.
Гарантии изготовителя
Условия, изложенные
в контракте о гарантиях, должны быть согласованы между потребителем и
изготовителем при составлении соглашения и оформлении заказа.