Утвержден и
введен в действие
Приказом
Ростехрегулирования
от 12 марта 2009 г.
N 113-ст
НАЦИОНАЛЬНЫЙ СТАНДАРТ РОССИЙСКОЙ ФЕДЕРАЦИИ
СПЕЦИАЛЬНЫЙ ПОДВИЖНОЙ СОСТАВ
ТРЕБОВАНИЯ К ПРОЧНОСТИ НЕСУЩИХ
КОНСТРУКЦИЙ И ДИНАМИЧЕСКИМ КАЧЕСТВАМ
Special rolling stock. Requirements for bearing
structure strength and dynamic
properties
ГОСТ Р 53337-2009
Группа Д55
ОКС 45.060.10
ОКП 31 8400
Дата введения
1 января 2010 года
Предисловие
Цели и принципы
стандартизации в Российской Федерации установлены Федеральным законом от 27
декабря 2002 г. N 184-ФЗ "О техническом регулировании", а правила
применения национальных стандартов Российской Федерации - ГОСТ Р 1.0-2004
"Стандартизация в Российской Федерации. Основные положения".
Сведения о
стандарте
1. Разработан
Открытым акционерным обществом "Научно-исследовательский и
конструкторско-технологический институт подвижного состава" (ОАО
"ВНИКТИ").
2. Внесен
Техническим комитетом по стандартизации ТК 236 "Тепловозы и путевые
машины".
3. Утвержден и
введен в действие Приказом Федерального агентства по техническому регулированию
и метрологии от 12 марта 2009 г. N 113-ст.
4. Введен впервые.
Информация об
изменениях к настоящему стандарту публикуется в ежегодно издаваемом
информационном указателе "Национальные стандарты", а текст изменений
и поправок - в ежемесячно издаваемых информационных указателях
"Национальные стандарты". В случае пересмотра (замены) или отмены
настоящего стандарта соответствующее уведомление будет опубликовано в
ежемесячно издаваемом информационном указателе "Национальные
стандарты". Соответствующая информация, уведомление и тексты размещаются
также в информационной системе общего пользования - на официальном сайте Федерального
агентства по техническому регулированию и метрологии в сети Интернет.
1. Область
применения
Настоящий стандарт
устанавливает объем расчетов и испытаний для определения и оценки показателей
динамики и прочности специального подвижного состава (далее - СПС), в т.ч.
стреловых кранов (далее - КС) на железнодорожном ходу хозяйственного
назначения, а также предназначенных для выполнения аварийно-восстановительных
работ.
Настоящий стандарт
определяет требования для обеспечения необходимых показателей динамики экипажных
частей, прочности металлоконструкций главных рам, кузовов, кабин, рам тележек,
шкворней, несущих конструкций рабочих органов, элементов рессорного
подвешивания, тягового привода, колесных пар (колесных центров, бандажей, осей
колесных пар и их соединений), букс, а также деталей крепления и страховки,
которые необходимы для надежного соединения и удержания в транспортном
положении рабочих органов, предохранения их от выхода за установленные габариты
и падения на путь.
Настоящий стандарт
не распространяется на составные части КС, находящиеся в ведении Ростехнадзора
России.
2.
Нормативные ссылки
В настоящем
стандарте использованы нормативные ссылки на следующие стандарты:
ГОСТ Р 51175-98.
Колеса зубчатые тяговых передач тягового подвижного состава магистральных
железных дорог. Технические условия
ГОСТ Р 51775-2001.
Колесные пары специального подвижного состава. Общие технические условия
ГОСТ Р 52627-2006.
Болты, винты и шпильки. Механические свойства и методы испытаний
ГОСТ 380-2005.
Сталь углеродистая обыкновенного качества. Марки
ГОСТ 398-96.
Бандажи из углеродистой стали для подвижного состава железных дорог широкой
колеи и метрополитена. Технические условия
ГОСТ 535-2005.
Прокат сортовой и фасонный из стали углеродистой обыкновенного качества. Общие
технические условия
ГОСТ 977-88.
Отливки стальные. Общие технические условия
ГОСТ 1050-88.
Прокат сортовой, калиброванный, со специальной отделкой поверхности из
углеродистой качественной конструкционной стали. Общие технические условия
ГОСТ 1215-79.
Отливки из ковкого чугуна. Общие технические условия
ГОСТ 1412-85. Чугун
с пластинчатым графитом для отливок. Марки
ГОСТ 1425-93.
Рессоры листовые для подвижного состава железных дорог. Технические условия
ГОСТ 1452-2003.
Пружины цилиндрические винтовые тележек и ударно-тяговых приборов подвижного
состава железных дорог. Технические условия
ГОСТ 1497-84 (ИСО
6892-84). Металлы. Методы испытаний на растяжение
ГОСТ 1583-93.
Сплавы алюминиевые литейные. Технические условия
ГОСТ 2246-70.
Проволока стальная сварочная. Технические условия
ГОСТ 4491-86.
Центры колесные литые для подвижного состава железных дорог колеи 1520 мм.
Общие технические условия
ГОСТ 4543-71.
Прокат из легированной конструкционной стали. Технические условия
ГОСТ 4728-96.
Заготовки осевые для подвижного состава железных дорог колеи 1520 мм.
Технические условия
ГОСТ 5457-75.
Ацетилен растворенный и газообразный технический. Технические условия
ГОСТ 5520-79.
Прокат листовой из углеродистой, низколегированной и легированной стали для
котлов и сосудов, работающих под давлением. Технические условия
ГОСТ 5582-75.
Прокат тонколистовой коррозионно-стойкий, жаростойкий и жаропрочный.
Технические условия
ГОСТ 5583-78 (ИСО
2046-73). Кислород газообразный технический и медицинский. Технические условия
ГОСТ 5632-72. Стали
высоколегированные и сплавы коррозионно-стойкие, жаростойкие и жаропрочные.
Марки
ГОСТ 6331-78.
Кислород жидкий технический и медицинский. Технические условия
ГОСТ 6713-91.
Прокат низколегированный конструкционный для мостостроения. Технические условия
ГОСТ 7293-85. Чугун
с шаровидным графитом для отливок. Марки
ГОСТ 7350-77. Сталь
толстолистовая коррозионно-стойкая, жаростойкая и жаропрочная. Технические
условия
ГОСТ 7565-81 (ИСО
377-2-89). Чугун, сталь и сплавы. Метод отбора проб для определения химического
состава
ГОСТ 8050-85.
Двуокись углерода газообразная и жидкая. Технические условия
ГОСТ 8479-70.
Поковки из конструкционной углеродистой и легированной стали. Общие технические
условия
ГОСТ 8617-81.
Профили прессованные из алюминия и алюминиевых сплавов. Технические условия
ГОСТ 9012-59 (ИСО
410-82, ИСО 6506-81). Металлы. Метод измерения твердости по Бринеллю
ГОСТ 9045-93.
Прокат тонколистовой холоднокатаный из низкоуглеродистой качественной стали для
холодной штамповки. Технические условия
ГОСТ 9466-75.
Электроды покрытые металлические для ручной дуговой сварки сталей и наплавки.
Классификация и общие технические условия
ГОСТ 9467-75. Электроды
покрытые металлические для ручной дуговой сварки конструкционных и
теплоустойчивых сталей. Типы
ГОСТ 10052-75.
Электроды покрытые металлические для ручной дуговой сварки высоколегированных
сталей с особыми свойствами. Типы
ГОСТ 10157-79.
Аргон газообразный и жидкий. Технические условия
ГОСТ 10304-80.
Заклепки классов точности B и C. Общие технические условия
ГОСТ 10791-2004.
Колеса цельнокатаные. Технические условия
ГОСТ 10885-85.
Сталь листовая горячекатаная двухслойная коррозионно-стойкая. Технические
условия
ГОСТ 14637-89 (ИСО
4995-78). Прокат толстолистовой из углеродистой стали обыкновенного качества.
Технические условия
ГОСТ 14955-77.
Сталь качественная круглая со специальной отделкой поверхности. Технические
условия
ГОСТ 14959-79.
Прокат из рессорно-пружинной углеродистой и легированной стали. Технические
условия
ГОСТ 16523-97.
Прокат тонколистовой из углеродистой стали качественной и обыкновенного
качества общего назначения. Технические условия
ГОСТ 18855-94 (ИСО
281-89). Подшипники качения. Динамическая расчетная грузоподъемность и
расчетный ресурс (долговечность)
ГОСТ 19281-89 (ИСО
4950-2-81, ИСО 4950-3-81, ИСО 4951-79, ИСО 4995-78, ИСО 4996-78, ИСО 5952-83).
Прокат из стали повышенной прочности. Общие технические условия
ГОСТ 19905-74.
Упрочнение металлических изделий поверхностной химико-термической обработкой.
Состав общих требований
ГОСТ 21354-87.
Передачи зубчатые, цилиндрические эвольвентные внешнего зацепления. Расчет на
прочность
ГОСТ 21357-87.
Отливки из хладостойкой и износостойкой стали. Общие технические условия
ГОСТ 21631-76.
Листы из алюминия и алюминиевых сплавов. Технические условия
ГОСТ 22536.0-87.
Сталь углеродистая и чугун нелегированный. Общие требования к методам анализа
ГОСТ 22703-91.
Детали литые автосцепного устройства подвижного состава железных дорог колеи
1520 мм. Общие технические условия
ГОСТ 23207-78.
Сопротивление усталости. Основные термины, определения и обозначения
ГОСТ 26271-84.
Проволока порошковая для дуговой сварки углеродистых и низколегированных
сталей. Общие технические условия
ГОСТ 27772-88.
Прокат для строительных стальных конструкций. Общие технические условия
ГОСТ 31334-2007.
Оси для подвижного состава железных дорог колеи 1520 мм. Технические условия.
Примечание. При
пользовании настоящим стандартом целесообразно проверить действие ссылочных
стандартов в информационной системе общего пользования - на официальном сайте
Федерального агентства по техническому регулированию и метрологии в сети
Интернет или по ежегодно издаваемому информационному указателю
"Национальные стандарты", который опубликован по состоянию на 1
января текущего года, и по соответствующим ежемесячно издаваемым информационным
указателям, опубликованным в текущем году. Если ссылочный стандарт заменен
(изменен), то при пользовании настоящим стандартом следует руководствоваться
заменяющим (измененным) стандартом. Если ссылочный стандарт отменен без замены,
то положение, в котором дана ссылка на него, применяется в части, не затрагивающей
эту ссылку.
3. Термины
и определения
В настоящем
стандарте применены следующие термины с соответствующими определениями:
3.1. Транспортный
режим: движение СПС с конструкционной или максимально разрешенной скоростью
своим ходом (для самоходных СПС), в составе поезда или с отдельным локомотивом.
3.2. Рабочий режим:
выполнение СПС функций по его назначению (рабочих операций).
3.3.
Конструкционная скорость: скорость, установленная техническим заданием, для
движения СПС на прямом горизонтальном участке пути отличного или хорошего
состояния.
3.4. Назначенный
срок службы: календарная продолжительность эксплуатации, при достижении которой
эксплуатация объекта должна быть прекращена независимо от технического
состояния.
3.5. Назначенный
ресурс: суммарная наработка, при достижении которой эксплуатация объекта должна
быть прекращена.
3.6. Технический
ресурс: предельный износ или ухудшение физических свойств материалов элементов
конструкции СПС до предельно допустимых значений, а также отказ одного или
нескольких элементов, восстановление которых не предусмотрено нормативными
документами.
3.7. Несущие
конструкции СПС: конструкции, воспринимающие эксплуатационные нагрузки.
3.8. Экипажная
часть СПС: конструкция, представляющая собой повозку, обеспечивающую движение
СПС по рельсовой колее и предназначенную для установки силового и
вспомогательного оборудования, рабочих органов, приводов, тормозной системы,
средств обслуживания.
3.9. Мягкое
нагружение: циклическое нагружение при постоянной амплитуде напряжений.
3.10. Жесткое
нагружение: циклическое нагружение при постоянной амплитуде деформаций.
4. Требования к динамическим качествам, воздействию
на путь, осевой
нагрузке и развеске экипажа
4.1. Показатели
динамических качеств, воздействия на путь, осевой нагрузки, развески экипажа
приведены в таблице 1.
Таблица 1
┌─────────────────────────────────────────────────────────────┬───────────┐
│ Наименование показателя │ Значение │
│
│показателя │
├─────────────────────────────────────────────────────────────┼───────────┤
│
Рамные силы по отношению к статической нагрузке от колесной │ │
│пары
на рельсы Р , не более: │ │
│ ст
│ │
│
- для щебеночного балласта │ 0,4 Р
│
│ │ ст
│
│
- для гравийного и песчаного балласта │ 0,3 Р
│
│
│ ст │
│
Коэффициенты вертикальной динамики буксовой ступени │ │
│рессорного
подвешивания к , не более: │ │
│ д │ │
│
- для служебных автомотрис │ 0,4
│
│
- для самоходного СПС
│ 0,5 │
│
- для несамоходного СПС
│ 0,7 │
│
Коэффициент запаса устойчивости от вкатывания колеса │ 1,5
│
│на
головку рельса эта, не менее │ │
│
Коэффициент запаса устойчивости от опрокидывания к ,
│ │
│
опр │ │
│не
менее: │ │
│
- наружу кривой
│ 1,5 │
│
- внутрь кривой
│ 1,2 │
│
Коэффициент конструктивного запаса к ,
не менее: │ │
│ кз │ │
│
- для самоходного СПС
│ 1,6 │
│
- для несамоходного СПС
│ 1,8 │
│
Запас на относительные перемещения элементов экипажа │Отсутствие │
│
│ касания │
│
Вертикальные ускорения кузова (главной рамы), не более: │ │
│
- для служебных автомотрис │ 0,4g
│
│
- для самоходного СПС
│ 0,5g │
│
- для несамоходного СПС
│ 0,7g │
│
Горизонтальные ускорения кузова (главной рамы), не более: │ │
│
- для служебных автомотрис │ 0,35g
│
│
- для самоходного СПС
│ 0,40g │
│
- для несамоходного СПС
│ 0,45g │
│
Показатель плавности хода в вертикальной и горизонтальной │ │
│плоскостях
W и W , не более: │ │
│ В
Г
│ │
│
- для служебных автомотрис │ 3,75 │
│
- для самоходного СПС
│ 3,85 │
│
- для несамоходного СПС
│ 4,00 │
│
Напряжения в наружной и внутренней кромках подошвы рельсов, │ 240
│
│МПа,
не более │ │
│
Напряжения в шпале под подкладкой, МПа, не более │ 2,2
│
│
Напряжения в балласте под шпалой, МПа, не более: │ │
│
- при щебеночном балласте │ 0,5
│
│
- при гравийном и песчаном балласте │ 0,3
│
│
Отклонение фактического значения силы тяжести от проектного │ 3
│
│значения,
%, не более
│ │
│
Разность нагрузок по колесам колесной пары, %, не более: │ │
│
- для самоходного СПС, кроме СПС <*> │ 4
│
│
- для несамоходного СПС <*> │ │
│
Разность нагрузок по приводным осям в одной тележке СПС, %, │ 3
│
│не
более
│ │
├─────────────────────────────────────────────────────────────┴───────────┤
│ <*> Для специального подвижного
состава, применяющего в конструкции│
│экипажной
части тележки моделей 18-100, 18-101, 18-102, 18-522, 18-9800,│
│УВЗ-10м и
другие тележки с
опорой кузова на
центральную пяту, в│
│соответствии
с Приложением И.
│
└─────────────────────────────────────────────────────────────────────────┘
5.
Требования к прочности и ресурсу СПС
5.1. Создаваемые
конструкции должны обеспечивать необходимую несущую способность и технический
ресурс всех элементов, предназначенных для восприятия эксплутационных нагрузок,
в течение назначенного срока службы.
5.2. Несущую
способность элементов конструкции оценивают по допускаемым значениям:
- напряжений;
- коэффициентов
запаса сопротивления усталости;
- коэффициентов
запаса долговечности.
5.3. При
напряжениях за пределом упругости работу конструкции рассматривают в условиях
квазистатического и малоциклового усталостного нагружений.
5.4. Несущие
конструкции СПС и узлы крепления оборудования не должны подвергаться
резонансным колебаниям во всем диапазоне скоростей движения. Частота их
собственных колебаний должна быть больше частоты вынужденных колебаний
экипажной части на рессорном подвешивании.
5.5. При назначении
ресурса необходимо учитывать характерные особенности конструкции СПС, технологии
изготовления и условий эксплуатации.
5.6. Назначенный
ресурс может быть установлен вновь по мере его выработки. Возможность
установления нового назначенного ресурса определяют с учетом деградационных
свойств материала, результатов технической диагностики, исследований
сопротивления усталости.
6. Расчет
конструкций СПС на стадии проектирования
6.1. Общие
требования к расчетам
6.1.1. При
проектировании СПС и его узлов должны быть обеспечены ходовые качества,
обеспечивающие безопасность движения в заданных условиях эксплуатации и
комфортные условия для персонала (для самоходных и обитаемых СПС).
6.1.2. Для
предварительной оценки ходовых качеств СПС или оптимизации его
упруго-диссипативных характеристик на стадии проектирования используют лицензионные
и аттестованные в установленном порядке программные комплексы, позволяющие
путем компьютерного моделирования определить значения основных динамических
показателей и по воздействию на путь, указанных в таблице 1 и разделе 7, при
движении в прямых и кривых участках пути, с учетом и без учета неровностей пути
с одновременным расчетом ускорения и перемещения произвольных точек любого
элемента модели конструкции, коэффициентов динамики, усилий в тягах и поводках,
рамных сил, сил взаимодействия в контакте "колесо - рельс",
вертикальных нагрузок от колес на рельсы, значения фактора износа,
коэффициентов безопасности.
Идентификацию
моделей вновь проектируемых единиц СПС проводят путем сравнения результатов
компьютерного моделирования с результатами натурных динамических и прочностных
испытаний единиц СПС с аналогичной экипажной частью.
Правила проведения
моделирования динамики экипажа приведены в Приложении А.
6.1.3. На стадии
проектирования СПС узлы экипажной части (главная рама, кузов, кабина, рама
ходовых тележек, шкворневой узел, оси колесных пар, буксы), а также несущие
конструкции рабочих органов должны быть рассчитаны на прочность под действием
сочетаний нагрузок, указанных в 6.2.
6.1.4. На стадии
создания несущих конструкций экипажной части и рабочих органов СПС проводят:
- предварительный
выбор материалов, размеров и конструктивных форм несущих элементов для заданных
параметров рабочего процесса;
- анализ
номинальных, местных напряжений и деформаций в наиболее нагруженных зонах для
различных сочетаний эксплутационных нагрузок, определяющих формирование блока
повреждающих циклов и характера нагружения;
- оценку
статической прочности и сопротивления усталости;
- оценку ожидаемого
ресурса.
6.1.5. Расчетам
подвергают:
- опасные сечения
крепежных деталей или предохранительных устройств (установочные элементы,
кронштейны, оси, пальцы, крюки, фланцы, транспортные фиксаторы, стопоры рабочих
органов и т.д.);
- места соединения
крепежного или предохранительного узла с несущей металлоконструкцией (сварные
швы, болты, заклепки и т.д.);
- узлы установки и
крепления рабочих органов.
6.1.6. Для
определения напряженно-деформированного состояния конструкций применяют
программы, основанные на методе конечных элементов, позволяющие решать задачи
как в линейной, так и в нелинейной постановке и оценить усталостную
долговечность различных вариантов одной конструкции уже на стадии
проектирования. Эти программы должны быть универсальными и совместимыми с
другими расчетными и графическими программами. Они должны иметь необходимую
библиотеку конечных элементов и возможность автоматического разбиения
конструкций на конечные элементы. При этом рекомендуется применять трехмерные
модели из объемных и оболочечных элементов, размер которых задают с учетом
разницы (не более 10%) результатов между собой и с результатами
экспериментальных исследований этой или аналогичной конструкции.
6.1.7. При
необходимости выполняют расчет собственных частот проектируемой конструкции,
чтобы не допустить их совпадения с основными частотами возбуждающих сил,
действующих со стороны пути.
6.1.8. Объем
расчетов в каждом конкретном случае выбирают индивидуально в зависимости от
накопленного опыта по исследованиям аналогичных конструкций.
6.2. Расчетные нагрузки и режимы
6.2.1.
Выделяют следующие группы нагрузок, действующих на СПС в процессе эксплуатации:
А - постоянно
действующие статические нагрузки от сил тяжести брутто конструкции и
установленного на ней оборудования и агрегатов, экипировочных материалов (воды,
смазки и т.п.);
Б - нагрузки,
обусловленные технологией ремонта: выкатка колесной пары, установка кузова на
домкраты, подъем краном при погрузке для транспортирования, а также подъем
груза при неработающих выдвижных опорах (у железнодорожных кранов) и аварийный
подъем одной стороны СПС вместе с тележкой за лобовый брус;
В - нагрузки,
возникающие при выполнении функций по назначению (рабочих операций);
Г - продольные
нагрузки, действующие вдоль оси и через автосцепки;
Д - динамические
нагрузки, возникающие при движении СПС в транспортном и рабочем режимах.
6.2.2. Для рам
тележек статическая нагрузка (группа А) включает в себя силы тяжести рамы и
надтележечного строения, обрессоренных частей привода и оборудования,
установленного на раме тележки. Силы тяжести для нагружения этого вида
определяют по весовой ведомости и конструкторской документации.
6.2.3. Нагрузки
группы Б включают в себя обязательные нагрузки для СПС всех типов и
специальные:
- к обязательным
нагрузкам относят выкатку колесных пар, установку СПС на домкраты, аварийный
подъем одной стороны вместе с тележкой за лобовый брус или автосцепку;
- к специальным
нагрузкам относят подъем груженого СПС при погрузке и выгрузке с
железнодорожного подвижного состава, работу без выдвижных опор (аутригеров) и
т.п. Необходимость расчета на специальные нагрузки определяют в зависимости от
конструкции СПС, назначения и условий эксплуатации, требований заказчика.
6.2.4.
Нагрузки группы В (далее - рабочие нагрузки) определяют характером рабочих
операций, выполняемых СПС. Значения и схемы приложения рабочих нагрузок, в т.ч.
сил распора боковых стенок (для снегоуборочных и других подобных машин),
определяют по конструкторской документации.
6.2.4.1. Силы
распора сыпучего груза
принимают как давление груза на поверхность
боковых стенок, которое вычисляют по формуле
, (1)
где
- коэффициент вертикальной динамики рессорного
подвешивания при движении СПС в груженом состоянии;
-
насыпная плотность груза;
g - ускорение
свободного падения;
y - расстояние от
поверхности груза до точки, в которой определяют давление;
- угол
естественного откоса сыпучего груза. При движении с конструкционной скоростью
равен нулю.
6.2.4.2. Значение
коэффициента вертикальной динамики
определяют экспериментально или оценивают по
экспериментальным данным для аналогичных узлов аналогичных конструкций при
соответствующей скорости движения. При отсутствии экспериментальных данных
коэффициент вертикальной динамики можно рассматривать как случайную функцию
вида
, (2)
где
- коэффициент вертикальной динамики;
-
среднее значение коэффициента вертикальной динамики;
-
параметр распределения, принимают равным 1,136;
-
доверительная вероятность. Рекомендуется в расчетах на прочность принимать
равной 0,97.
Коэффициент
вертикальной динамики
для СПС на вагонных тележках вычисляют как
квантиль функции
по формуле
. (3)
Среднее значение
коэффициента вертикальной динамики
при скорости движения V менее 55 км/ч
вычисляют по формуле
, (4)
где a -
коэффициент, для элементов кузова принимают равным 0,05, для обрессоренных
частей тележки - 0,1, для необрессоренных частей тележки - 0,5;
V - скорость
движения при расчетном режиме, м/с.
При скорости
движения V более 55 км/ч среднее значение коэффициента вертикальной динамики
вычисляют по формуле
, (5)
где b -
коэффициент, учитывающий влияние числа осей в тележке и группе тележек под
одной половиной экипажа;
-
статический прогиб рессорного подвешивания, м.
При скорости
движения менее 30 км/ч
принимают равным нулю.
При двухступенчатом
рессорном подвешивании при определении коэффициента вертикальной динамики
для рамы тележки учитывают прогиб первой
ступени, для кузова - полный статический прогиб двух ступеней.
Коэффициент,
учитывающий влияние числа осей в тележке и группе тележек под одним концом
экипажа, вычисляют по формуле
, (6)
где n - число осей
в тележке и группе тележек под одним концом экипажа.
Для бестележечных
экипажей (в жесткой раме) коэффициент b принимают равным числу осей под одним
концом экипажа.
6.2.4.3.
Конструкции СПС, на которые при выполнении рабочих операций действуют
статические нагрузки, рассчитывают на статическую прочность. При этом наряду с
нагрузками группы В учитывают постоянно действующие статические нагрузки группы
А.
6.2.4.4.
Конструкции СПС, воспринимающие в рабочем режиме переменные циклические
нагрузки, рассчитывают на сопротивление усталости. Метод расчета определяют по
числу циклов, которое СПС воспринимает за назначенный срок службы.
6.2.4.5. При
необходимости элементы экипажной части СПС по нагрузкам рабочего режима
проверяют на жесткость, а сжатые элементы - на устойчивость в соответствии с
требованиями норм, применяемых в вагоностроении.
6.2.5. Рамы СПС
рассчитывают на восприятие статических продольных нагрузок, действующих вдоль
оси автосцепок (группа Г). Эти нагрузки включают в себя сжимающие и
растягивающие силы, возникающие между единицами подвижного состава при
различных режимах движения поезда и при соударениях во время маневровой работы.
Эти нагрузки должны определять условия транспортирования СПС, возможность
включения в состав поезда, место расположения в поезде и пропуска через
сортировочные горки.
6.2.5.1. По
условиям транспортирования должны быть установлены две группы СПС:
первая - СПС,
транспортируемые в составе грузовых поездов без ограничения места его установки
в состав и пропускаемые (без роспуска) через сортировочные горки;
вторая - СПС,
транспортируемые своим ходом, отдельным локомотивом, следующие в хвосте
грузовых поездов без подталкивания, и в составе поездов массой не более 1000 т
и длиной до 400 м.
6.2.5.2.
СПС первой группы в части восприятия продольных сил и устойчивости в составе
поезда проектируют с учетом требований к грузовым вагонам. Остальные требования
устанавливают в соответствии с настоящим стандартом.
6.2.5.3.
Для СПС второй группы с собственной массой до 30 т продольная сила должна быть
равна его удвоенной силе тяжести, от 30 до 70 т - (+/- 1000) кН, от 70 до 100 т
- (+1000) кН и минус 1500 кН, от 100 до 200 т - (+1500) кН и минус 2000 кН.
6.2.5.4. Для вновь
проектируемых СПС расчетное продольное усилие должно быть указано в техническом
задании и соответствовать требованиям 6.2.5.2 и 6.2.5.3.
6.2.6. Экипажную
часть СПС рассчитывают на систему сил (группа Д), возникающих при работе,
движении в составе поезда или своим ходом, при реализации силы тяги и
торможении, при вписывании в кривые участки пути, а также на кососимметричные
нагрузки. Для СПС, включаемых в состав грузовых поездов без ограничения места
расположения, учитывают боковые силы при взаимодействии с другим подвижным
составом на кривых участках пути.
6.2.6.1.
Вертикальные динамические нагрузки определяют умножением статических
вертикальных нагрузок на коэффициент динамики
.
6.2.6.2. Нагрузки,
возникающие при тяге и торможении, определяют с учетом типа примененной
тормозной системы, силы нажатия тормозных колодок, конструкции тележек и
экипажа в целом, в том числе систем передачи силы тяги.
6.2.6.3. Нагрузки,
действующие при вписывании СПС в кривую, определяют по результатам
динамического вписывания при движении в кривой радиусом 600 м при непогашенном
ускорении 0,7 м/с2.
6.2.6.4.
Кососимметричные нагрузки, представляющие собой систему взаимно уравновешенных
вертикальных сил, приложенных со стороны рессорного подвешивания к раме тележки
или действующих между опорами кузова на тележки, учитывают только для жестких
рам или других конструкций, где они возникают. Кососимметричные нагрузки
состоят из четырех равных по значению вертикальных сил, из которых две,
расположенные по диагонали, действуют вверх, а две другие - вниз и могут
возникать в двух- или трехосных тележках со стороны букс на раму тележки при
несбалансированном рессорном подвешивании и между кузовом и тележкой, если
имеются четыре "жесткие" опоры кузова. Причиной появления
кососимметричной нагрузки может быть неодинаковая жесткость отдельных рессор
(пружин), неодинаковые стрелы их прогиба, разность установочных размеров, а
также неровности пути и другие аналогичные причины.
6.2.6.5. Нагрузку,
приложенную к одной буксе двухосной тележки, возникающую от вертикального
смещения одного колеса
,
вычисляют по формуле
, (7)
где z -
вертикальное эквивалентное смещение одного колеса, вызванное местными
неровностями пути и колес и отклонениями в размерах буксовых узлов и
подвешивания, с учетом вертикального отвода рельсовой нитки в переходном
отрезке кривой;
2b - расстояние
между центрами буксовых опор колесной пары;
2s - расстояние
между кругами катания колеса одной колесной пары, принимают равным 1,58 м;
-
жесткость буксовых пружин (над одной буксой);
-
жесткость рамы тележки при кососимметричной нагрузке (на 1/4 рамы).
Вертикальное
смещение одного колеса z вычисляют по формуле
z = 13 + L x 2, (8)
где L - база
тележки (расстояние между крайними колесными парами).
В двухосных
экипажах кососимметричную нагрузку учитывают только для главной рамы СПС.
6.2.7. Узлы
крепления рабочих органов рассчитывают для следующих нагрузок:
- вертикальных
статических от сил тяжести удерживаемого (установленного) оборудования и
динамических, вызванных ускорениями оборудования при колебаниях движущегося
СПС;
- поперечных
горизонтальных инерционных сил, возникающих при движении СПС;
- продольных
горизонтальных инерционных сил, возникающих вследствие соударения при движении
поезда, в процессе торможения, во время маневров;
- ветровой
нагрузки.
6.2.8. Элементы
типа растяжек и строп, которые изготавливают из стальных канатов, цепей,
прутка, полос, а также детали резьбовых соединений (болты, шпильки, стяжки)
рассчитывают на продольные нагрузки (растяжение).
6.2.9. Скобы,
крюки, кронштейны, проушины, рычаги и т.п. рассчитывают на изгиб и изгиб с
продольной нагрузкой.
6.2.10. Стопорные
детали (штыри, пальцы, упоры), а также детали соединения (заклепки, сварные
швы, болты) рассчитывают на срез и смятие.
6.2.11. Узлы
крепления рабочих органов рассчитывают на действие нагрузок групп В и Д.
6.2.11.1. Нагрузки
группы В определяют по 6.2.4.
6.2.11.2. Нагрузки
группы Д для узлов, устанавливаемых на раме СПС, рассчитывают при двух режимах
движения:
а) трогание
с места, осаживание или экстренное торможение при малых скоростях движения,
соударения при маневровой работе. Расчетная нагрузка, полученная суммированием
сил тяжести удерживаемого (установленного) оборудования и элементов крепления с
возникающей при этом силой инерции, прикладывается к центру тяжести
закрепляемого узла в виде двух составляющих вертикальной
и продольной
.
Вертикальную составляющую
вычисляют по формуле
, (9)
где
- сила тяжести удерживаемого (установленного)
оборудования;
N - нормативное
продольное усилие в данном режиме (см. 6.2.5.2 и 6.2.5.3);
Q - сила тяжести
СПС;
-
расстояние от центра тяжести СПС до оси автосцепки (по вертикали);
x - расстояние от
среднего поперечного сечения СПС до центра тяжести удерживаемого
(установленного) оборудования (вдоль продольной оси СПС);
- база
СПС.
Продольную
составляющую нагрузку
вычисляют по формуле
, (10)
где
- продольное ускорение.
Для оборудования,
установленного на главной раме на уровне и ниже автосцепки (1050 мм от головки
рельса) продольное ускорение
равняется 3g, на уровне крыши (до 5300 мм от
головки рельса) - 1,5g, на промежуточных уровнях продольное ускорение
изменяется линейно от 3g до 1,5g;
б) движение
с заданной скоростью. Расчетная нагрузка состоит из вертикальной, продольной и
боковой составляющих.
Вертикальную
составляющую
вычисляют по формуле
, (11)
где
- сила тяжести удерживаемого (установленного)
оборудования;
-
коэффициент вертикальной динамики, определяют экспериментально или по формуле
(3).
Продольную
составляющую нагрузки вычисляют по формуле (10). Для оборудования,
установленного на главной раме на уровне и ниже автосцепки (1050 мм от головки
рельса), продольное ускорение
принимают равным 0,6g, на уровне крыши (5300
мм от головки рельса) равным 0,3g.
Боковую
составляющую нагрузки
вычисляют по формуле
, (12)
где
- расчетное ускорение, принимают равным 1g.
6.2.12. Узлы
крепления оборудования, установленного на обрессоренных частях тележки,
рассчитывают с учетом сил инерции, исходя из ускорений в вертикальном
направлении, равных 1,5g и ускорений в продольном направлении, равных 3g.
6.2.13. Узлы
крепления оборудования, установленного на необрессоренных частях тележки,
рассчитывают с учетом сил инерции, исходя из ускорений в вертикальном
направлении, равных 1,5g, в продольном направлении, равных 3g.
6.2.14.
Предохранительные устройства рассчитывают на нагрузку, равную удвоенной силе
тяжести предохраняемого оборудования.
6.2.15. Колесные
пары и оси должны соответствовать ГОСТ Р 51775, ГОСТ 31334.
6.2.16. Пружины
рессорного подвешивания должны соответствовать ГОСТ 1452.
6.3. Оценка
прочности главных рам, рам тележек, несущих конструкций рабочих органов,
элементов крепления и предохранительных устройств
6.3.1. У главных
рам, рам тележек, несущих конструкций рабочих органов, элементов крепления
оценивают статическую прочность и сопротивление усталости в транспортном и
рабочем режимах, а также статическую прочность при восприятии нагрузок в
ремонтно-технологическом режиме.
При оценке
статической прочности напряжения при расчетных режимах сравнивают с
допускаемыми значениями.
Оценку
сопротивления усталости проводят при значениях напряжений, изменяющихся по
симметричному циклу или приводящихся к нему, следующими способами:
- по коэффициенту
запаса n по отношению к пределу выносливости детали
, если
число циклов нагружения элемента конструкции N в процессе эксплуатации равно
или выше базового числа
,
равного
,
соответствующего перелому кривой усталости;
- по коэффициенту
запаса n по отношению к ограниченному пределу выносливости детали
, если
за назначенный срок службы конструкции число циклов нагружения меньше базового
числа
;
- по вероятности
разрушения при ограниченной (заданной) долговечности.
Значения пределов
выносливости получают по результатам испытаний на усталость натурных деталей
или определяют по пределам выносливости соответствующих материалов
с учетом концентрации напряжений в детали.
В таблице 2
приведены классы нагруженности конструкций в зависимости от числа циклов
нагружения.
Таблица 2
Классы
нагруженности конструкций
┌─────────────┬────────────────┬─────────────┬──────────────┬─────────────┐
│ Класс
│ Н1 │ Н2
│ Н3 │ Н4
│
│нагруженности│ │ │ │ │
├─────────────┼────────────────┼─────────────┼──────────────┼─────────────┤
│ │ 4
│ 4 │ 5
│ 6 │
│Число
циклов │ До 2 x 10 │
От 2 x 10 │ От 2 x 10
│ Св. 2 x 10 │
│нагружения │ │ 5 │ 6
│ │
│ │ │ до 2 x 10
│ до 2 x 10 │ │
├─────────────┼────────────────┼─────────────┼──────────────┼─────────────┤
│Характер
│Квазистатическое│Усталостное │Смешанное │Многоцикловое│
│нагружения │малоцикловое │малоцикловое
│малоцикловое │ │
└─────────────┴────────────────┴─────────────┴──────────────┴─────────────┘
В таблице 3
приведены значения пределов выносливости для типовых сварных соединений из
наиболее употребляемых материалов отечественного и импортного производства в
зависимости от числа циклов нагружения (базы испытаний), установленных классом
нагруженности от Н1 до Н4 и степени влияния концентрации напряжений. В таблице
Б.1 (Приложение Б) приведены типовые примеры соединений деталей, вызывающих
соответствующую степень концентрации.
Таблица 3
┌──────┬──────────────────────────────────────────────────────────────────┐
│Класс
│ Значения пределов
выносливости, МПа, для
│
│нагру-├──────────────────────────────────────────────────────────────────┤
│жен- │ материала без сварного
шва │
│ности
├───────────────────┬──────────────────────────────────────────────┤
│ │Ст3 (аналог St 37) │ Ст09Г2 (аналог St 52) │
│
├───────────────────┼──────────────────────────────────────────────┤
│ │
190, 140, 93 │ 220, 190, 93 │
│
├───────────────────┴──────────────────────────────────────────────┤
│ │ сварного соединения
из │
│
├───────────────────┬──────────────────────────────────────────────┤
│ │Ст3 (аналог St 37) │ Ст09Г2 (аналог St 52) │
│
├───────────────────┴──────────────────────────────────────────────┤
│ │ степень влияния
концентрации │
│
├────┬────┬────┬────┬────┬───────┬───────┬────────┬────────┬───────┤
│ │ К0 │ К1 │ К2 │
К3 │ К4 │ К0 │
К1 │ К2
│ К3 │
К4 │
├──────┼────┼────┼────┼────┼────┼───────┼───────┼────────┼────────┼───────┤
│ Н1
│180 │180 │180 │180 │180 │ 270
│ 270 │250-270 │180-250
│110-150│
├──────┼────┼────┼────┼────┼────┼───────┼───────┼────────┼────────┼───────┤
│ Н2
│170 │160 │150 │110 │ 65
│170-240│150-210│130-180 │ 90-130 │ 55-75 │
├──────┼────┼────┼────┼────┼────┼───────┼───────┼────────┼────────┼───────┤
│ Н3
│120 │110 │ 90 │ 65 │ 40 │ 120
│ 110 │
90 │ 65
│ 40 │
├──────┼────┼────┼────┼────┼────┼───────┼───────┼────────┼────────┼───────┤
│ Н4
│170,│ -, │ -, │ -, │ -, │ -,
│ -, │
-, │ -,
│ -, │
│ │130,│95, │70,
│55, │ -, │ -, │
-, │ -,
│ -, │
-, │
│ │ 84 │ 75 │ 63 │
45 │ 27 │ 84 │
75 │ 63
│ 45 │
27 │
├──────┴────┴────┴────┴────┴────┴───────┴───────┴────────┴────────┴───────┤
│ Примечания. 1. Через запятую указаны
значения пределов выносливости│
│для
изгиба, растяжения-сжатия, изгиба с кручением соответственно. │
│ 2. К0 - незначительное влияние
концентрации, К1 - умеренное влияние│
│концентрации,
К2 - среднее влияние концентрации,
К3 - сильное
влияние│
│концентрации,
К4 - особенно сильное влияние концентрации. │
└─────────────────────────────────────────────────────────────────────────┘
Справочные данные
по основным характеристикам наиболее применяемых металлов приведены в таблице
В.1 (Приложение В).
6.3.2. Главная рама
(кузов). Транспортный режим
6.3.2.1. Продольное
нагружение по оси автосцепок
Режим соответствует
условиям, возникающим при соударениях во время маневровой работы и переходных
режимах движения в поезде. Определяют сумму напряжений от нормативных
продольных нагрузок на растяжение и сжатие (группа Г) и сил тяжести (группа А).
Условие прочности вычисляют по формуле
, (13)
где
- предел текучести материала.
Для СПС, предназначенного
для транспортирования и ускоренной выгрузки снега, загрязненного щебня и других
сыпучих материалов (типа засорителей), наряду с силами тяжести СПС и
оборудования необходимо учитывать максимальную силу тяжести перевозимого груза.
6.3.2.2. Движение с
конструкционной скоростью
Определяют сумму
напряжений от действия нагрузок группы А с добавлением переменных напряжений,
определяемых при конструкционной (транспортной) скорости, и напряжений от
нагрузок группы Г. Продольную силу принимают 0,5 от силы группы Г. Условие
прочности вычисляют по формуле
, (14)
где
- коэффициент вертикальной динамики (формула
3).
6.3.2.3.
Коэффициент запаса сопротивления усталости n вычисляют по формуле
, (15)
где
- предел выносливости стандартного образца при
симметричном цикле нагружения;
к - коэффициент
концентрации, учитывающий понижение сопротивления усталости;
-
амплитуда напряжений цикла;
-
коэффициент, характеризующий чувствительность металла к асимметрии цикла;
-
среднее напряжение цикла.
Коэффициент,
характеризующий чувствительность металла к асимметрии цикла
,
вычисляют по формуле
, (16)
где
- предел выносливости при отнулевом цикле.
При расчетах на
сопротивление усталости деталей из малоуглеродистой конструкционной и литой
стали (в том числе и сварных)
следует принимать для растянутых волокон (
более
0), равным 0,3, и для сжатых (
менее
0), равным 0.
За среднее
напряжение цикла принимают напряжения от нагрузок группы А, определенные
расчетным или экспериментальным путем, с учетом квазистатических сил,
возникающих при тяге, торможении или движении в кривой.
Амплитуду
напряжений цикла определяют экспериментально при движении СПС с транспортной
скоростью. На стадии проектирования амплитуду напряжений цикла рассчитывают по
формуле
. (17)
Значение коэффициента
вертикальной динамики
вычисляют по формуле (3). Значение
коэффициента концентрации напряжений вычисляют по формуле
, (18)
где
- эффективный коэффициент концентрации
напряжений, учитывающий форму детали и свойства материала;
-
коэффициент, учитывающий неоднородность материала детали, присущую прокату,
штамповке, литью. Для проката, поковки и штамповки
равен 1,1, для литья
изменяется от 1,2 до 1,3;
-
коэффициент, учитывающий внутренние напряжения в детали. При наибольшем
линейном размере в поперечном сечении детали до 250 мм
равен 1,0, от 250 до 1000 мм
изменяется пропорционально наибольшему
линейному размеру в сечении от 1,0 до 1,2;
- коэффициент,
учитывающий влияние абсолютных размеров детали. Значение его для образца
диаметром 10 мм равно 1,0, с увеличением линейного размера в поперечном сечении
детали до 200 мм
снижается от 0,76 до 0,60. При дальнейшем
увеличении линейного размера в поперечном сечении детали
снижается менее интенсивно;
-
коэффициент, учитывающий состояние поверхности детали.
Значение
эффективного коэффициента концентрации напряжений
для различных форм геометрических
концентраторов принимают по справочным данным или определяют через
теоретический коэффициент концентрации
. В
этом случае
вычисляют по формуле
, (19)
где q - коэффициент
чувствительности материала к концентрации напряжений;
-
теоретический коэффициент концентрации.
Для
малоуглеродистых сталей типа Ст3 коэффициент q может быть принят q = 0,7, для
низколегированных сталей q = 1.
При оценке
прочности узлов по максимальным амплитудам напряжений цикла (т.е. в зоне
концентрации напряжений)
принимают равным 1.
Ориентировочные
значения эффективного коэффициента концентрации
для сварных элементов из стали Ст3 приведены в
таблице 4.
Таблица 4
┌─────────────────────────────┬──────────────────────────┬────────────────┐
│ Характеристика соединения │
Вид соединения │ Коэффициент
│
│ │ │ концентрации
│
│ │ │ бета
│
│ │ │ к
│
└─────────────────────────────┴──────────────────────────┴────────────────┘
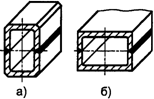
Балка прямоугольного 1,0
сечения, сваренная из:
а) штампованных П-образных
элементов;
б) двух швеллеров
───────────────────────────────────────────────────────────────────────────
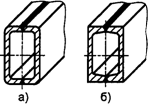
Балка прямоугольного 1,1
сечения, сваренная из:
а) штампованных П-образных
элементов;
б) двух швеллеров
───────────────────────────────────────────────────────────────────────────
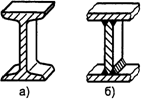
Балка двутаврового сечения а) 1,0
б) 1,1
───────────────────────────────────────────────────────────────────────────
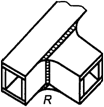
Сопряжение двух балок: а) От 1,3 до
1,5
а) R = 50 мм и более; б) От 1,6 до
2,0
б) R = 50 мм и менее; в) 2,1
в) под прямым углом
───────────────────────────────────────────────────────────────────────────
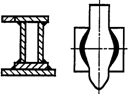
Соединение двух балок От 1,7 до
2,1
прерывистым сварным швом
───────────────────────────────────────────────────────────────────────────

Балка прямоугольного 1,1
сечения, сваренная из
листового проката
───────────────────────────────────────────────────────────────────────────

Балка замкнутого сечения 1,1
(два швеллера или двутавра,
объединенные верхним и нижним
листами)
───────────────────────────────────────────────────────────────────────────
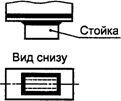
Приварка стойки (кронштейна) 2,1
или ребер (показано
пунктиром) к горизонтальному
листу балки, примыкание под
прямым углом
───────────────────────────────────────────────────────────────────────────
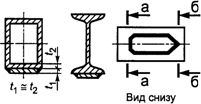
Приварка к полкам балки а - а
накладки с обваркой по От 1,6 до
2,1
периметру:
б - б
а - а) прямоугольной формы; От 1,5 до 1,7
б - б) вытянутой
языкообразной формы
───────────────────────────────────────────────────────────────────────────
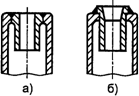
Вварка втулки:
а)
а) сварка встык с разделкой От 1,4 до 1,6
кромок свариваемых элементов; б)
б) соединение внахлест От 1,7 до
2,1
───────────────────────────────────────────────────────────────────────────
Значения
коэффициента в зависимости от состояния поверхности детали
приведены в таблице 5.
Таблица 5
Значения
коэффициента, учитывающего
состояние
поверхности детали

┌──────────────────────────────────────────────────────────┬──────────────┐
│ Обработка поверхности │ Значение к │
│
│ 4
│
├──────────────────────────────────────────────────────────┼──────────────┤
│Полированная
поверхность (образец)
│ 1 │
├──────────────────────────────────────────────────────────┼──────────────┤
│Станочная
обработка с обеспечением шероховатости
│ 0,9 │
├──────────────────────────────────────────────────────────┼──────────────┤
│Грубая
обработка на станке, обдирка, прокат │От 0,85 до 0,8│
├──────────────────────────────────────────────────────────┼──────────────┤
│Стальное
литье (после тщательной обработки пескоструйным
│ 0,8 │
│аппаратом)
│ │
└──────────────────────────────────────────────────────────┴──────────────┘
Если определено
фактическое значение предела выносливости детали, полученное в результате
натурных стендовых испытаний, коэффициент запаса сопротивления усталости n
вычисляют по формуле
, (20)
где
- предел выносливости натурной детали,
определенный экспериментально;
к - коэффициент
снижения предела выносливости, представляют собой отношение предела
выносливости образца к пределу выносливости детали.
При большой
асимметрии цикла (когда
менее 0,2) проверяют условие по формуле
. (21)
6.3.2.4.
Для оценки долговечности рекомендуется использовать линейную гипотезу
суммирования усталостных повреждений.
Суммарное число
циклов до разрушения вычисляют по формуле
, (22)
где
- число циклов, соответствующее точке перелома
кривой усталости;
m - показатель
степени наклонной ветви кривой усталости;
-
предел выносливости детали;
-
амплитуда цикла нагружения;
-
отношение числа циклов амплитуды
к суммарному числу циклов.
Показатель степени
наклонной ветви кривой усталости m при проектных расчетах вычисляют по формуле
, (23)
где c -
коэффициент, равный:
- от 12 до 20 для
деталей из углеродистой стали;
- от 20 до 35 для
деталей из легированной стали.
Коэффициент c
уточняется по результатам испытаний детали на усталость.
к - коэффициент
концентрации напряжений, учитывающий понижение сопротивления усталости,
определяемый по формуле (18).
При расчетах
используется безразмерный параметр - предельный коэффициент нагруженности
,
вычисляют по формуле
, (24)
где
- максимальная ступень напряжений в предельном
блоке нагружения, соответствующем разрушению при числе циклов
.
Предельный блок
нагружения пропорционален действующему блоку. Тогда выражение (22) можно
записать в виде формулы
. (25)
График уравнения
вторичной кривой усталости в относительных координатах приведен на рисунке 1.
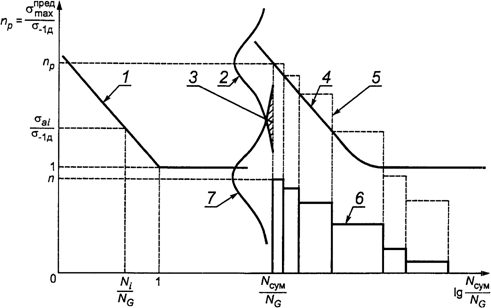
1 - первичная
кривая усталости; 2 - закон рассеяния кривой
усталости; 3 - зона
амплитуд, вызывающих относительное
повреждение детали;
4 - вторичная кривая усталости,
соответствующая
действующему блоку нагружения;
5 - предельный блок
нагружения, пропорциональный
действующему блоку,
соответствующий заданному числу
циклов
; 6 -
действующий блок нагружения;
7 - закон рассеяния
действующего блока нагружения
Рисунок 1.
График уравнения вторичной кривой
усталости в
относительных координатах
Число циклов до
разрушения, полученное по формуле (22), соответствует 50% вероятности. Если
требуется задать уровень напряжений меньший, чем заложен в формулу (22), то при
том же числе циклов получают меньшую вероятность разрушения. Разброс разрушений
определяют по разбросу пределов выносливости детали и воздействующих на нее
напряжений, распределенных по нормальному закону. Тогда квантиль нормального
распределения
,
соответствующий вероятности разрушения, вычисляют по формуле
, (26)
где
- относительный коэффициент запаса;
-
коэффициент вариации предела выносливости детали;
-
коэффициент вариации максимальной ступени напряжений в блоке нагружения.
Относительный
коэффициент запаса
вычисляют по формуле
, (27)
где
- предельный коэффициент нагруженности,
соответствующий точке на вторичной кривой усталости с абсциссой
,
определяемый по формуле (24);
n - действительный
коэффициент нагруженности;
-
максимальная ступень напряжений в действующем блоке нагружения;
-
максимальная ступень напряжений в предельном блоке нагружения.
Коэффициент
вариации предела выносливости детали вычисляют по формуле
, (28)
где
- среднее квадратическое отклонение предела
выносливости.
Коэффициент вариации
максимальной ступени напряжений в блоке нагружения вычисляют по формуле
, (29)
где
- среднее квадратическое отклонение
максимальных напряжений.
Действительный
коэффициент нагруженности n вычисляют по формуле
. (30)
Значения n и
показаны на рисунке 1.
По таблицам функций
нормального распределения в зависимости от квантиля определяют вероятность
разрушения. В таблице 6 в качестве примера приведены значения относительного
коэффициента запаса
,
соответствующего вероятности разрушения.
Таблица 6
┌───────────────────────────────┬────────────────────────────────┐
│ Вероятность разрушения │Относительный коэффициент
запаса│
├───────────────────────────────┼────────────────────────────────┤
│ 0,1 │ 1,28 │
├───────────────────────────────┼────────────────────────────────┤
│ 0,05 │ 1,38 │
├───────────────────────────────┼────────────────────────────────┤
│ 0,03 │ 1,45 │
├───────────────────────────────┼────────────────────────────────┤
│ 0,02 │ 1,51 │
├───────────────────────────────┼────────────────────────────────┤
│ 0,01 │ 1,61 │
├───────────────────────────────┼────────────────────────────────┤
│ 0,001 │ 1,96 │
├───────────────────────────────┴────────────────────────────────┤
│ Примечание. Приведенные данные рассчитаны
для коэффициентов│
│вариации
v = 0,15, v = 0,1. │
│ сигма-1д эпсилон │
└────────────────────────────────────────────────────────────────┘
Для транспортного
режима рекомендуется принимать вероятность разрушения, равную 0,02.
6.3.3. Главная рама
(кузов) и несущие конструкции рабочих органов. Рабочий режим
6.3.3.1. СПС,
применяемый для перевозки тяжелых грузов, предназначенный для механизации
погрузочно-разгрузочных работ, проверяют на действие вертикальной нагрузки,
включающей в себя собственную массу СПС и максимальную массу груза. Оценку
прочности проводят по допускаемым напряжениям по формуле
. (31)
6.3.3.2. Для СПС,
применяемых как тяговые единицы, определяют сумму напряжений при действии
нагрузок групп А и В и сил тяги при движении своим ходом со скоростью до 10 км/ч.
Оценку прочности проводят по допускаемым напряжениям по формуле
, (32)
где
- напряжения от сил тяги при движении своим
ходом;
-
предел текучести материала.
6.3.3.3. Для
несущих элементов главных рам снегоуборочных машин (кроме боковых стенок)
определяют напряжения, возникающие при движении СПС со снегом со скоростью,
разрешенной при движении груженой машины к месту выгрузки (не более 50 км/ч).
Учитывают напряжения от постоянной статической нагрузки группы А, сил от
рабочих нагрузок (в данном случае веса снега группы В), напряжения от нагрузок
группы Г и динамическую добавку, определяемую через коэффициент динамики.
Коэффициент динамики определяют при соответствующей скорости. Оценку прочности
проводят по формуле
. (33)
Оценку прочности
для боковых стенок с учетом распора проводят по формуле
. (34)
6.3.3.4. Прочность
конструкций СПС (главная рама, элементы рабочих органов и их креплений),
воспринимающих в рабочем режиме переменные нагрузки, оценивают по сопротивлению
усталости. Коэффициент запаса сопротивления усталости n вычисляют по формуле
(15), при этом он должен быть не менее 1,3. Статическую
и динамическую
составляющие цикла определяют из фактических
напряжений, возникающих в рабочем режиме.
Если значение
предела выносливости определено путем стендовых испытаний на усталость натурной
детали, коэффициент запаса сопротивления усталости определяют по формуле (20).
При этом коэффициент запаса сопротивления усталости должен быть не менее 1,2.
Для СПС, несущие
элементы которых при выполнении рабочих операций воспринимают переменные
нагрузки, изменяющиеся с высокой частотой (порядка от 10 до 20 Гц и выше), и за
назначенный срок службы имеют от
до
циклов нагружения, запас сопротивления усталости
должен быть не менее 2.
6.3.3.5. В случае,
когда при небольшом числе циклов нагружения (до
),
нагрузки и вызываемые ими напряжения превышают предел выносливости и достигают
предела текучести, и в зонах концентрации напряжений наряду с упругими
возникают пластические деформации, оценка по номинальным напряжениям
недостаточна. Зависимости между напряжениями и деформациями для расчетов в
упругопластической области получают экспериментально или аппроксимацией реальных
диаграмм деформирования. Коэффициенты деформаций
и концентрации напряжений
вычисляют по формулам
при
, (35)
при
, (36)
при
, (37)
при
, (38)
где
- теоретический коэффициент концентрации
напряжений в предположении упругого деформирования;
m - показатель
упрочнения материала в упругопластической области (0 <= m <= 1);
-
значение интенсивности номинальных напряжений, вычисляют по формуле
, (39)
где
- номинальные напряжения;
-
предел текучести материала.
Для
малоуглеродистых и низколегированных сталей характеристика упрочнения материала
m в упругопластической области равняется 0,3.
Уравнение кривой
усталости при мягком нагружении вычисляют по формуле
, (40)
где
- предел выносливости и предел прочности
материала;
N,
- число циклов до разрушения на уровне предела
выносливости и предела прочности материала;
v - показатель
степени наклонной ветви кривой малоцикловой усталости, определяется по формуле
. (41)
Малоцикловая
прочность при жестком нагружении определяется характеристиками пластичности
статического разрушения, а зависимость долговечности от значения пластической
деформации вычисляют по формуле
, (42)
где
- значение пластической деформации в цикле
нагружения;
N - число циклов до
разрушения;
m - показатель
наклона кривой усталости;
-
константа уравнения, определяется по формуле
, (43)
где
- коэффициент поперечного сужения.
Размах циклической
деформации
вычисляют по формуле (Коффина)
. (44)
То же
по формуле (Мэнсона)
, (45)
где
и B - константы, характеризующие интенсивность
протекания процесса при циклическом упругопластическом деформировании и
зависящие от степени исходного нагружения;
E - модуль
упругости материала.
-
характеризует пластическую составляющую,
и
характеризуют упругую составляющую размаха
циклической деформации
.
Параметры диаграмм циклического деформирования некоторых сталей в стабильном
состоянии приведены в таблице 7.
Таблица 7
Сталь ВСт3
|
Сталь 09Г2
|
Сталь 10ХСНД
|
Сплав АМГ61
|
Дельта
эпсилон,
%
|
Дельта
сигма,
МПа
|
Дельта
эпсилон,
%
|
Дельта
сигма,
МПа
|
Дельта
эпсилон,
%
|
Дельта
сигма,
МПа
|
Дельта
эпсилон,
%
|
Дельта
сигма,
МПа
|
0,2
|
332
|
0,05
|
105
|
0,05
|
105
|
0,2
|
140
|
0,3
|
458
|
0,10
|
210
|
0,10
|
210
|
0,3
|
211
|
0,4
|
515
|
0,15
|
303
|
0,15
|
315
|
0,4
|
275
|
0,5
|
553
|
0,20
|
363
|
0,20
|
415
|
0,5
|
319
|
0,6
|
583
|
0,25
|
435
|
0,25
|
485
|
0,6
|
350
|
0,7
|
610
|
0,30
|
482
|
0,30
|
535
|
0,7
|
372
|
0,8
|
635
|
0,35
|
520
|
0,35
|
585
|
0,8
|
389
|
0,9
|
658
|
0,40
|
548
|
0,40
|
631
|
0,9
|
401
|
1,0
|
682
|
0,45
|
569
|
0,45
|
669
|
1,0
|
410
|
1,1
|
701
|
0,50
|
585
|
0,50
|
703
|
1,1
|
418
|
1,2
|
718
|
0,55
|
594
|
0,55
|
730
|
1,2
|
425
|
1,3
|
733
|
0,60
|
610
|
0,60
|
756
|
1,3
|
431
|
1,4
|
747
|
0,65
|
620
|
0,65
|
779
|
1,4
|
437
|
1,5
|
761
|
0,70
|
629
|
0,70
|
800
|
1,5
|
442
|
1,6
|
775
|
0,75
|
635
|
0,75
|
816
|
1,6
|
447
|
1,7
|
787
|
0,80
|
644
|
0,80
|
833
|
1,7
|
451
|
1,8
|
800
|
0,85
|
650
|
0,85
|
849
|
1,8
|
455
|
1,9
|
811
|
0,90
|
657
|
0,90
|
863
|
1,9
|
460
|
2,0
|
821
|
1,00
|
671
|
1,00
|
877
|
2,0
|
464
|
2,1
|
832
|
1,10
|
684
|
1,10
|
890
|
2,1
|
467
|
2,2
|
842
|
1,20
|
693
|
1,20
|
903
|
2,2
|
471
|
2,3
|
852
|
1,30
|
704
|
1,30
|
916
|
2,3
|
474
|
2,4
|
862
|
1,40
|
715
|
1,40
|
929
|
2,4
|
477
|
2,5
|
871
|
1,50
|
724
|
1,50
|
940
|
2,5
|
480
|
2,6
|
880
|
1,60
|
733
|
1,60
|
-
|
-
|
-
|
Примечание. Дельта
сигма - напряжение,
соответствующее размаху
деформации Дельта эпсилон.
|
В таблице 8
приведены константы, характеризующие интенсивность протекания
упругопластического деформирования.
Таблица 8
┌─────────┬─────────────┬────────────┬─────────────┬───────────┬──────────┐
│Материал
│ C │ B
│ альфа │
бета │ пси, %
│
│ │ пси
│ │ │ │ │
├─────────┼─────────────┼────────────┼─────────────┼───────────┼──────────┤
│ВСт3 │
0,636 │ 0,015
│ 0,654 │
0,170 │ 50
│
├─────────┼─────────────┼────────────┼─────────────┼───────────┼──────────┤
│09Г2 │
0,340 │ 0,011
│ 0,653 │
0,142 │ 50
│
├─────────┼─────────────┼────────────┼─────────────┼───────────┼──────────┤
│10ХСНД │
0,400 │ 0,015
│ 0,653 │
0,140 │ 50
│
├─────────┼─────────────┼────────────┼─────────────┼───────────┼──────────┤
│АМГ61 │
0,060 │ 0,007
│ 0,400 │
0,100 │ 12
│
└─────────┴─────────────┴────────────┴─────────────┴───────────┴──────────┘
6.3.4. Рама
тележки. Транспортный режим
Для оценки
прочности рам тележек при статических нагрузках в транспортном режиме проверяют
следующие сочетания.
6.3.4.1. Трогание с
места. Определяют сумму напряжений от нагрузок группы А
, от
максимальной силы тяги при трогании
и кососимметричной нагрузки
.
Условие прочности вычисляют по формуле
. (46)
6.3.4.2. Движение в
тяговом режиме по кривой. Определяют сумму напряжений от нагрузок группы А
с добавлением динамических напряжений,
определенных при транспортной скорости, от сил тяги
, от
нагрузок, возникающих при движении в кривой
и кососимметричной нагрузки
.
Условие прочности вычисляют по формуле
, (47)
где
- коэффициент динамики, вычисляемый по формуле
(3).
6.3.4.3. Торможение
в кривой. Суммируют напряжения от нагрузок группы А (с учетом динамических),
торможения
,
движения по кривой
и кососимметричной нагрузки
.
Условие прочности вычисляют по формуле
, (48)
где
- коэффициент динамики (см. формулу 3).
При суммировании
напряжений, возникающих при движении в кривой и от кососимметричной нагрузки,
им присваивают такие же знаки, как у напряжений для режима нагружения
постоянной статической нагрузкой группы А.
6.3.4.4.
Коэффициент запаса сопротивления усталости n вычисляют по формуле (15). При
движении в прямой в режимах тяги или торможения среднее напряжение цикла
определяется соответственно как
, (49)
. (50)
Для оценки
принимают большее значение.
При движении в
кривой учитывают также статическую составляющую напряжений от вписывания в
кривую.
Для приближенных
расчетов можно принять
приблизительно равным
.
Амплитуду напряжений
вычисляют по формуле (17).
Коэффициент запаса
сопротивления усталости n должен быть не менее 1,5.
Если для рамы
тележки известен предел выносливости, то коэффициент запаса сопротивления
усталости n определяют по формуле (20). В этом случае коэффициент запаса
сопротивления усталости n для транспортного режима должен быть не менее 1,4.
Если для рамы
тележки установлен ограниченный срок службы, то расчет проводят на
долговечность (см. 6.3.2.4). Вероятность разрушения принимают не более 0,02.
6.3.5. Рама
тележки. Рабочий режим
6.3.5.1. В рабочем
режиме для оценки статической прочности рамы тележки напряжения от постоянной
статической нагрузки группы А суммируются с динамической составляющей
напряжений. Допускаемое напряжение -
.
Условие прочности вычисляют по формуле
, (51)
где
- значение амплитуд переменных напряжений от
рабочих нагрузок.
6.3.5.2.
Коэффициент запаса сопротивления усталости вычисляют по формуле 15. Значения
и
определяют по фактическим значениям напряжений
рабочего режима. Допускаемый коэффициент запаса сопротивления усталости [n]
принимают равным 1,5.
6.3.5.3. Если для
рамы тележки известен предел выносливости, то коэффициент запаса сопротивления
усталости n вычисляют по формуле 20. В этом случае допускаемый коэффициент
запаса сопротивления усталости [n] принимают равным 1,4.
6.3.5.4. Расчет на
долговечность проводят по методике, изложенной в 6.3.2.4. Вероятность
разрушения должна быть не более 0,02.
6.3.6. Главные рамы
и рамы тележек. Ремонтно-технологические режимы
6.3.6.1. Оценку
прочности в этих режимах проводят сравнением полученных значений напряжений с
допускаемыми значениями, равными
.
6.3.7. Элементы
крепления оборудования и предохранительные устройства. Транспортный режим
6.3.7.1. При оценке
прочности элементов крепления оборудования на главной раме значения напряжений,
полученных от нагрузок [см. 6.2.11.2 (перечисление а)], сравнивают с
допускаемыми значениями, равными
.
6.3.7.2. При оценке
прочности элементов крепления оборудования на главной раме значения напряжений,
полученных от нагрузок [см. 6.2.11.2 (перечисление б)], сравнивают с
допускаемыми значениями, равными
,
сопротивление усталости - с коэффициентом запаса n не менее 1,5.
6.3.7.3. При оценке
статической прочности элементов крепления оборудования на раме тележки значения
напряжений в них сравнивают с допускаемыми значениями напряжений, равными
,
сопротивление усталости - с коэффициентом запаса n не менее 1,5.
6.3.7.4. При оценке
долговечности вероятность разрушения принимают равной 0,02.
6.3.8. Элементы
крепления оборудования и предохранительные устройства. Рабочий режим
6.3.8.1. При оценке
значений статической прочности напряжения в элементах крепления рабочих органов
под действием статических нагрузок, возникающих при выполнении рабочих
операций, сравнивают с допускаемыми значениями по формуле
. (52)
Допускаемые
значения напряжений:
-
для элементов на главной раме;
-
для элементов на раме тележки.
6.3.8.2. В
зависимости от характера действующих нагрузок в рабочем режиме (высокой частоте
нагружения, непрерывной работе) проводят оценку значения сопротивления
усталости по формуле (15). Минимальное значение запаса сопротивления усталости
должно быть:
1,3 - для элементов
на главной раме;
1,5 - для элементов
на раме тележки.
6.3.8.3.
Предохранительные устройства оценивают по допускаемым значениям напряжений,
равным
.
6.3.8.4. Расчет на
прочность соединений (сварных, болтовых, заклепками) деталей крепления и
предохранительных устройств рабочих органов СПС проводят в соответствии с
действующими нормами расчета.
6.3.9. Детали
рессорного подвешивания рассчитывают на действие нагрузок А, Г и Д. Оценку
сопротивления усталости пружин проводят в соответствии с требованиями ГОСТ
1452.
6.3.10. Оценку
сопротивления усталости колесных пар с буксами и осей проводят в соответствии с
требованиями ГОСТ Р 51775.
6.3.11. Оценку
сопротивления усталости колес с дисковыми центрами проводят согласно
нормативным документам.
6.4. Оценка
прочности узлов тягового привода и тяговой трансмиссии
6.4.1. Подвески
тяговых электродвигателей и осевых редукторов
6.4.1.1. На
подвески тяговых электродвигателей и осевых редукторов действуют нагрузки: от
реактивных усилий при реализации тяги; высокочастотные нагрузки от осевых
редукторов и тяговых передач; усилия, связанные с относительными перемещениями
подрессоренных и неподрессоренных частей (рамы СПС) в вертикальной и
поперечно-горизонтальной плоскостях, в том числе при прохождении кривых малого
радиуса, оговоренного в технических условиях на СПС.
6.4.1.2. При
расчетах на прочность рассматривают сечения с учетом концентраторов напряжений
(ступенчатый переход, резьба хвостовика, шпоночные канавки и т.п.) и
действующих статических, квазистатических и динамических нагрузок
растяжения-сжатия, изгибающих моментов, возникающих при поперечных перемещениях
колесной пары относительно рамы тележки.
Оценку
относительных деформаций резиновых и резинометаллических амортизаторов
проводят:
- при работе
амортизаторов на сжатие;
- при работе
амортизаторов на сдвиг.
Значения
относительных деформаций сжатия
должны быть:
- от 0,05 до 0,1 -
при действии стационарных динамических нагрузок;
- от 0,1 до 0,15 -
при действии статических и квазистатических нагрузок со случайными и
эпизодическими кратковременными динамическими нагрузками.
Значения
относительных деформаций сдвига
должны быть:
- от 0,1 до 0,15 -
при действии стационарных динамических нагрузок;
- от 0,2 до 0,3 -
при действии статических и квазистатических нагрузок со случайными или регулярными
кратковременными динамическими нагрузками, следующими с интервалами во времени.
6.4.1.3. Оценку
запасов прочности стержня подвески тягового электродвигателя или осевого
редуктора и валов осевых редукторов выполняют по формуле (15).
6.4.2. Карданные
валы
6.4.2.1. При оценке
прочности карданных валов для тяговых трансмиссий СПС должны быть учтены:
- уровень
максимальных вращающих моментов, передаваемых валом;
- максимальные
частоты вращения карданного вала при конструкционной скорости движения;
- углы излома осей
валов в шарнирах карданного вала.
6.4.2.2. При оценке
несущей способности карданных валов должна использоваться кинематическая схема
трансмиссии, значения параметров силовой установки СПС, допускаемые длительные
и предельные крутящие моменты, при передаче которых возможны пластические
деформации элементов карданных валов.
6.4.2.3. Запас
прочности карданного вала при максимальной частоте вращения вычисляют по
формуле
, (53)
где
- максимальная частота вращения карданного
вала,
;
-
критическая частота вращения карданного вала,
.
6.4.2.4.
Критическую частоту вращения карданного вала вычисляют по формуле
, (54)
где
- коэффициент, равный
;
-
наружный диаметр трубы вала, мм;
-
внутренний диаметр трубы вала, мм;
L - расстояние между
центрами шарниров, мм.
6.4.2.5.
Максимальный угол излома осей валов в шарнирах вычисляют по таблице 9.
Таблица 9
Зависимость
максимального рабочего угла излома
осей валов в
шарнирах от частоты вращения вала
┌─────────────────┬───────────────────────────────────────────────────────┐
│ Наименование
│ Значение
показателя │
│ показателя
│
│
├─────────────────┼────────┬───────┬───────┬───────┬───────┬───────┬──────┤
│
Частота вращения│ 5000 │ 4500
│ 3500 │ 3000 │ 2500
│ 2000 │ 1500 │
│ -1
│ │ │ │ │ │ │ │
│n , мин
│ │ │ │ │ │ │ │
│
макс │ │ │ │ │ │ │ │
├─────────────────┼────────┼───────┼───────┼───────┼───────┼───────┼──────┤
│
Угол излома осей│ 3°30' │
3°50' │ 5°00' │ 5°45' │ 6°55' │ 8°40'
│11°30'│
│гамма │ │ │ │ │ │ │ │
│ макс
│ │ │ │ │ │ │ │
└─────────────────┴────────┴───────┴───────┴───────┴───────┴───────┴──────┘
Минимальные углы
излома осей валов в шарнирах карданного вала должны быть не менее 1° во
избежание бринеллирования поверхностей цапф крестовины и стаканов игольчатых
подшипников. Максимальный угол излома осей в шарнирах карданного вала в
горизонтальной плоскости
с учетом прохождения тележкой экипажа СПС
кривых участков пути минимального радиуса, определенного техническими условиями
на СПС конкретного типа, вычисляют по формуле
, (55)
где
- строительный угол излома осей в шарнирах в
горизонтальной плоскости;
- угол
излома осей в шарнирах, обусловленный прохождением СПС кривых участков пути,
вычисляют по формуле
, (56)
где
и
- расстояния от оси шкворневого узла тележки
до оси шарнира карданного вала вдоль оси СПС и в поперечном горизонтальном
направлениях, мм;
и
- расстояния между осями шарниров в продольном
и поперечном направлениях, мм;
- угол
поворота тележки в кривой в горизонтальной плоскости, град.
6.4.2.6. Угол
поворота тележки в кривой в горизонтальной плоскости вычисляют по формуле
, (57)
где
- расстояние между осями шкворневых отверстий
СПС, мм;
-
расстояние между осями колесных пар тележки, мм;
R - радиус кривой,
мм;
-
максимальный зазор между гребнями колес и боковыми гранями рельсов, мм. При
максимальной ширине колеи 1548 мм максимальный зазор между гребнями колес и
боковыми гранями рельсов
должен быть 61 мм.
Максимальный угол
излома осей в шарнирах карданного вала вычисляют по формуле
, (58)
где
- строительный угол излома осей в шарнирах в
вертикальной плоскости.
Значение
не должно превышать 80% значения угла излома в
шарнирах, определяемого конструктивными элементами вала и указанного в каталоге
на карданный вал.
6.4.3.
Подшипниковые узлы колесно-редукторных (КРБ) и колесно-моторных блоков (КМБ)
6.4.3.1. Расчет
номинальной долговечности подшипников проводят исходя из 90% надежности их
работы без появления признаков контактной усталости металла на рабочих
поверхностях колец и тел качения.
Номинальную
долговечность подшипников буксовых узлов и опор осевых редукторов L, в км
пробега СПС, вычисляют по формуле
, (59)
где
- диаметр среднеизношенных колес по кругу
катания;
-
обобщенный коэффициент, характеризующий совместное влияние качества металла
деталей подшипника и условий эксплуатации на долговечность подшипника;
C - значение
динамической грузоподъемности выбранного подшипника;
P - эквивалентная
динамическая нагрузка на подшипник;
p - показатель
степени (для роликовых подшипников p равен 10/3, для шариковых подшипников p
равен 3).
Номинальную
долговечность подшипников ведущей шестерни тяговых редукторов, в км пробега
СПС, вычисляют по формуле
, (60)
где i -
передаточное число осевого редуктора.
Значения
обобщенного коэффициента
при расчете долговечности подшипников
принимают в соответствии с данными справочника-каталога.
Значение
динамической грузоподъемности C определяют для:
- стандартных
типоразмеров подшипников - по справочнику-каталогу;
- для нестандартных
и опытных подшипников - по данным завода-изготовителя подшипников или по ГОСТ
18855.
Значение
обобщенного коэффициента, характеризующего совместное влияние качества металла
деталей подшипника и условий эксплуатации на долговечность подшипника
,
принимают:
- от 0,5 до 0,6 -
для роликовых подшипников с короткими цилиндрическими роликами;
- от 0,3 до 0,4 -
для сферических двухрядных роликовых подшипников;
- от 0,6 до 0,7 -
для подшипников с коническими роликами;
- от 0,7 до 0,8 -
для шариковых подшипников (кроме сферических).
При расчете
подшипников, изготовленных из стали электрошлакового переплава, обеспечении
гидродинамической пленки масла между контактирующими поверхностями колец и
роликов и отсутствии повышенных перекосов в узле значения
допускается принимать увеличенными в 1,5 - 2
раза.
В случае
возможности обводнения или загрязнения смазки, повышенных перекосов в узлах,
попадания в подшипник смазки из других узлов, переполнения или возможного
недостатка смазки значения
должны быть снижены.
6.4.3.2. Для
расчета номинальной долговечности подшипников предварительно рассчитывают
эквивалентную динамическую нагрузку на них по формулам и правилам расчета
эквивалентной нагрузки на подшипники по ГОСТ 18855.
6.4.3.3. Подшипники
буксовые роликовые с короткими цилиндрическими роликами, воспринимающие помимо
радиальной и осевую нагрузку (направленную вдоль оси колесной пары) торцами
роликов и бортами колец, подлежат проверке на соответствие допускаемой осевой
грузоподъемности действующим осевым силам.
6.4.3.4. В случае
применения подшипников с короткими цилиндрическими роликами в буксовом узле (для
тележек с упругой связью с рамой) расчетные значения действующих осевых сил
рекомендуется принимать равными:
-
горизонтальная осевая нагрузка, действующая на один подшипник и возникающая при
движении СПС с максимальной конструкционной скоростью в прямых участках пути,
- вертикальная сила, действующая на подшипник;
-
горизонтальная осевая нагрузка, действующая на один подшипник и возникающая при
движении специального подвижного состава с максимальной допустимой скоростью
при вписывании в кривые.
6.4.3.5. Значение
расчетной долговечности подшипников СПС должно составлять:
-
км пробега - буксового узла колесной пары и
опорных осевых подшипников тягового редуктора;
-
км пробега - ведущего вала тяговых редукторов.
Если для СПС
отдельного типа установлен пробег до капитального ремонта от 0,5 до
км, то значения расчетной долговечности
подшипников буксового узла принимают равным
км пробега.
7. Оценка динамических качеств и динамических показателей
7.1.
Правила оценки ходовых качеств
7.1.1. При оценке ходовых
качеств СПС должны быть определены:
- рамные силы
;
- коэффициент
вертикальной динамики
;
- коэффициент
запаса устойчивости колеса от вкатывания на головку рельса,
;
- коэффициент
запаса устойчивости от опрокидывания,
;
- вертикальные и
горизонтальные (поперечные) ускорения кузова (главной рамы) ВУ и ГУ;
- коэффициент
конструктивного запаса,
.
Для самоходного СПС
должны быть определены также показатели плавности хода в вертикальном и
горизонтальном (поперечном) направлениях
и
.
7.1.1.1.
Рамные силы - это поперечные горизонтальные силы, действующие на колесную пару
от подрессоренных масс экипажа. Расчетным путем рамную силу определяют методами
математического моделирования системы "экипаж-путь". В кривых
участках пути рамную силу допускается определять вписыванием в кривые.
При испытаниях
рамные силы определяют в зависимости от конструкции экипажа:
а) при челюстной
конструкции буксового узла при наличии осевых разбегов в буксах (свободных или
упругих) измерение рамных сил проводят посредством мессдозы (Приложение Г). При
скольжении оси в буксовом подшипнике возникает сила трения, которую суммируют с
силой, зафиксированной посредством мессдозы. Коэффициент трения при вращении
оси рекомендуется принимать равным 0,1. Рамную силу
при измерении ее мессдозой вычисляют по
формуле
, (61)
где
- сила, воспринимаемая мессдозой;
P - статическая
нагрузка на шейку оси;
б) при применении в
буксах упругих осевых упоров рамную силу
вычисляют по формуле
, (62)
где
- сила предварительной затяжки пружины;
f - деформация
пружины;
ж - жесткость
пружины.
При наличии жестких
осевых упоров в буксах отсутствует скольжение оси в подшипниках в момент
соприкасания торца оси и упора, поэтому
; (63)
в) при отсутствии
осевых разбегов в буксах возможно также измерение значений рамных сил по
значениям напряжений в челюстных кронштейнах. Проводят анализ конструкции
кронштейнов для нахождения места их наибольшей возможной деформации от рамных
сил, в этом месте наклеивают тензорезисторы (Приложение Д). Значение рамной
силы
вычисляют по формуле
, (64)
где
- измеренные значения напряжений слева и
справа;
-
соответствующие коэффициенты перевода напряжений в силы;
г) при бесчелюстных
буксах, упруго связанных с рамой, измерение значений рамных сил выполняют
измерением поперечных (горизонтальных) перемещений букс относительно рамы.
При отсутствии
разбегов букс относительно осей измеряют перемещение одной из букс данной
колесной пары. Значение рамной силы вычисляют по формуле
, (65)
где
- жесткость упругих буксовых связей слева и
справа;
-
измеренное перемещение.
При наличии
разбегов необходимо измерять перемещение каждой буксы оси. Значение рамной силы
вычисляют по формуле
, (66)
где
- измеренные перемещения слева и справа;
д) на двухосных
трехэлементных тележках (типа ЦНИИ-ХЗ, модели 18-100) или трехосных тележках
(типа УВЗ-10А, моделей 18-102 и 18-522) грузовых вагонов, примененных для СПС,
значения рамных сил измеряют тензорезисторами, наклеенными на боковые рамы
(Приложение Д). Значение рамной силы оси вычисляют по формуле
, (67)
где
- измеренные значения напряжений на левой и
правой боковых рамах;
-
соответствующие коэффициенты перевода значений напряжений в силы.
7.1.1.2.
Коэффициент вертикальной динамики
характеризует вертикальное силовое воздействие
на элементы экипажа и путь от колебаний надрессорного строения. Расчетным путем
его определяют методами математического моделирования системы
"экипаж-путь". Допускается определять коэффициент вертикальной
динамики
по эмпирическим формулам:
- для самоходного
СПС по формуле
, (68)
где V - скорость
движения, км/ч;
-
статический прогиб рессорного подвешивания, мм (при двухступенчатом рессорном
подвешивании за значение
принимают сумму статических прогибов обеих
ступеней).
- для несамоходного
СПС на вагонных тележках типов 18-100, УВЗ-9М, УВЗ-10А и пр. по формуле 3.
При испытаниях
коэффициент вертикальной динамики
определяют в зависимости от конструкции
рессорного подвешивания:
а) при
комбинированном рессорном подвешивании (Приложение Ж) значения коэффициента
вертикальной динамики
вычисляют по формуле
, (69)
где
- динамический прогиб пружины;
-
статический прогиб пружины.
Для такой
конструкции буксового узла коэффициент вертикальной динамики
определяют по значениям напряжений в рессорной
подвеске с учетом только значений напряжений от продольных сил. Коэффициент
вертикальной динамики
вычисляют по формуле
, (70)
где
- значение динамического напряжения в
подвеске;
-
значение статического напряжения в подвеске;
б) при бесчелюстных
буксах жесткость упругого элемента (пружины) суммируется с жесткостью упругих связей
(обычно это буксовые поводки (поводок), удерживающих буксу в раме.
Если центр силы
упругого элемента рессорного подвешивания смещен от центра буксы (например, как
у рессорного подвешивания путевой машины МПТГ), необходимо определить значение
упругой силы, действующей по оси буксы, а затем определить коэффициент
вертикальной динамики
по формуле 69;
в) коэффициент
вертикальной динамики подрессоренных масс экипажа на тележках типа ЦНИИ-ХЗ или
УВЗ-10А определяют по напряжениям в надрессорной балке. Статические напряжения
определяют аналогично статическим напряжениям в рессорных подвесках.
Коэффициент вертикальной динамики
вычисляют по формуле
, (71)
где
- значение динамического напряжения,
измеренное с левой или правой стороны тележки;
-
значение статического напряжения с левой или правой стороны тележки.
Коэффициент
вертикальной динамики неподрессоренных масс трехэлементной тележки определяют
по значениям напряжений на верхнем поясе боковой рамы;
г) в экипаже с
рессорным подвешиванием, состоящим из листовых рессор, коэффициент вертикальной
динамики
определяют измерением значений напряжений в
подвесках или серьгах. Допускается определение коэффициента вертикальной
динамики
по измеренному прогибу рессоры с учетом ее
силы трения, предварительно определив статический прогиб. В этом случае
коэффициент вертикальной динамики
вычисляют по формуле
, (72)
где
- измеренный динамический прогиб рессоры;
-
статический прогиб рессоры;
-
коэффициент относительного трения рессоры, вычисляют по формуле
, (73)
где T - значение
силы трения рессоры при статической нагрузке
на нее.
Значение силы
трения T определяют по диаграмме рессоры. На стадии проектирования силу трения
рессоры T вычисляют по формуле
. (74)
Коэффициент
относительного трения вычисляют по формуле
, (75)
где
- коэффициент трения между листами рессоры для
сохранившейся смазки листов, принимается равным 0,3;
n - общее число
листов в рессоре;
h - толщина листа
рессоры;
L - длина рессоры
по опорным точкам;
д) в экипаже с
упругими элементами рессорного подвешивания и установленными параллельно
фрикционными демпферами коэффициент динамики вычисляют по формуле
, (76)
где
- замеренный динамический прогиб упругого
элемента;
-
статический прогиб упругого элемента;
ж - жесткость
упругого элемента;
T - значение силы
трения в фрикционном демпфере, которую определяют на стенде или расчетом;
е) в экипаже с
упругими элементами рессорного подвешивания и установленными параллельно
гидравлическими демпферами коэффициент вертикальной динамики
вычисляют по формуле
, (77)
где
- измеренный динамический прогиб упругого
элемента;
-
статический прогиб упругого элемента;
ж - жесткость
упругого элемента;
-
коэффициент сопротивления (параметр) гидродемпфера;
-
круговая частота вынужденных колебаний. Учитывая, что при движении экипажа
апериодические неровности возмущают колебания экипажа с собственной частотой,
собственную частоту колебаний подпрыгивания вычисляют по формуле
, (78)
где ж - жесткость
упругого элемента;
m - масса упругого
элемента.
В Приложении Е
приведен график зависимости коэффициента
от коэффициента демпфирования Д.
7.1.1.3.
Коэффициент запаса устойчивости колеса от вкатывания на головку рельса
На колесную пару,
катящуюся по рельсовой колее, действуют вертикальные и горизонтальные силы. При
одновременном их действии возможно вкатывание (вползание) гребня набегающего
колеса на головку рельса с последующим сходом СПС с рельсов. В качестве критерия
оценки такой ситуации используют коэффициент запаса устойчивости колеса от
вкатывания на головку рельса
,
представляющий собой предельно допустимое отношение указанных сил, действующих
на набегающее колесо. Коэффициент запаса устойчивости колеса от вкатывания на
головку рельса
СПС с колесными парами, имеющими локомотивный
профиль колес, вычисляют по формуле
=


, (79)
где Q - сила
тяжести обрессоренных частей, приходящаяся на шейку оси колесной пары (далее -
КП);
q - сила тяжести
необрессоренных частей, приходящаяся на КП;
2b - расстояние между
точками приложения вертикальных сил к шейкам оси КП;
-
расстояние между точкой приложения вертикальной силы на шейку оси на набегающем
колесе (НК) и точкой контакта на гребне;
-
расстояние между точкой приложения вертикальной силы на шейку оси на
ненабегающем колесе (ННК) и точкой контакта на его поверхности катания;
-
коэффициент трения между гребнем набегающего колеса и рельсом;
-
коэффициент трения между поверхностью катания ненабегающего колеса и рельсом
и
принимают равными 0,25;
и
- коэффициенты вертикальной динамики в первой
ступени подвешивания на набегающем и ненабегающем колесах КП соответственно
(при обезгрузке
и
не менее 0);
-
рамная сила;
r - радиус колеса
по кругу катания;
-
параметр, определяемый по формуле
, (80)
- угол
между образующей рабочей поверхности реборды и горизонтальной плоскостью
(рисунок 2).
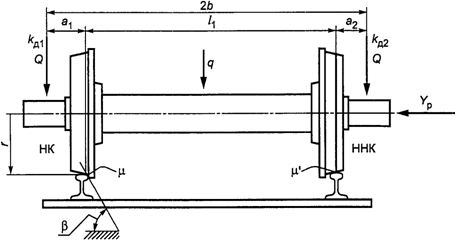
Рисунок 2.
Расчетная схема для формул (81) и (82)
Коэффициент запаса
устойчивости колеса от вкатывания на головку рельса
СПС с вагонным профилем колес вычисляют по
формуле
. (81)
Расчеты проводят по
компьютерным программам с подстановкой в формулы сил тяжести и размерных
характеристик экипажа, а также значений динамических сил, полученных в
результате расчета (см. 7.1.1.1 и 7.1.1.2) или проведения ходовых динамических
испытаний единицы СПС.
7.1.1.4.
Коэффициент запаса устойчивости колесной пары от "выжимания"
Другой опасный
случай сочетания вертикальных и горизонтальных сил может возникнуть при
"выжимании" СПС с нагрузкой на ось
менее 10 тс или шкворневую базу
менее 4000 мм, продольными силами при
транспортировании ее в поезде. Значение коэффициента запаса устойчивости
колесной пары от схода с рельсов при "выжимании"
вычисляют по формуле
x
x
, (82)
где
- угол между образующей гребня колеса и
горизонтальной плоскостью;
-
коэффициент трения между колесом и рельсом, принимают равным 0,25;
-
вертикальная нагрузка от тележки на рельсы;
N - расчетные
значения квазистатических продольных сжимающих сил, длительно действующие
(более 3 с) на автосцепки СПС в поезде, определяют с учетом условий движения
поезда, когда единицы подвижного состава (далее - ЕПС), прицепленные впереди от
проверяемого СПС по ходу движения, в т.ч. тяговый локомотив, производят торможение
на уклоне, а прицепленные в хвостовой части СПС ЕПС "накатываются" на
нее, создавая продольную силу;
-
продольная критическая сила;
-
коэффициент перекоса;
-
суммарный свободный поперечный разбег рамы кузова СПС относительно оси пути по
шкворню (у двухосного экипажа - по колесной паре). При определении суммарного
свободного поперечного разбега
учитывают максимальные значения износа гребней
колес, уширения колеи, перемещения кузова относительно тележки (при упругой
поперечной связи) и колесной пары относительно рамы (при упругой поперечной
связи из условия
);
L - половина длины
между упорными плитами автосцепок;
-
половина длины по осям автосцепок;
-
длина автосцепки, для автосцепки СА-3 принимают равной 1 м;
-
высота рабочей плоскости пятника над уровнем головки рельса;
-
расстояние от оси автосцепки до плоскости головок рельсов;
-
расстояние от шарнира шкворня до плоскости головок рельсов;
-
возвышение наружного рельса в кривой, принимают от 0 до 0,15 м;
- база
СПС;
R - радиус кривой,
принимают для расчетов 250 м. В прямых участках пути принимают равным
бесконечности.
В формуле верхние
знаки соответствуют установке I, когда набегающее колесо вкатывается на
наружный рельс, нижние - установке II, когда набегающее колесо вкатывается на
внутренний рельс.
Вертикальную
нагрузку от тележки на путь вычисляют с учетом ее обезгрузки при эксцентричном
действии продольных сил (для двухосного экипажа - от колесной пары на рельсы)
по формуле
, (83)
где
- вертикальная статическая нагрузка от тележки
на путь;
-
разность уровней осей сцепленных автосцепок, принимают равной 0,1 м;
-
жесткость рессорного подвешивания в вертикальной плоскости одной тележки (при
двухосном экипаже - колесной пары).
Остальные
обозначения - по формуле (82).
Коэффициент
вычисляют по формуле
, (84)
где
- продольные критические силы.
Расчетные значения
квазистатических продольных сжимающих сил вычисляют по формуле
, (85)
где n - число ЕПС в
поезде, прицепленных к хвостовой части СПС;
-
средний уклон, принимают равным
;
P - сила тяжести
одной ЕПС.
Продольные
критические силы вычисляют по формулам
, (86)
, (87)
где
- жесткость рессорного подвешивания в
горизонтальной (поперечной) плоскости одной тележки (при двухосном экипаже -
колесной пары).
Допускаемое
значение коэффициента запаса устойчивости
колесной пары против схода с рельсов СПС при
"выжимании" принимают равным 1,2.
Для определения
места установки СПС в поезде находят максимальную сжимающую СПС продольную силу
из условия, что
будет не менее 1,2. Затем определяют
допускаемое значение силы тяжести части поезда из ЕПС, которые можно прицепить
к СПС.
7.1.1.5.
Коэффициент запаса устойчивости от опрокидывания
При расчете запаса
устойчивости от опрокидывания необходимо учитывать, что при движении СПС по
кривому участку пути с максимальным непогашенным ускорением на него действует
центробежная сила, которая при сочетании с ветровой нагрузкой, продольными
сжимающими силами и поперечными колебаниями кузова на рессорах, создает момент,
опрокидывающий СПС наружу кривой.
При движении СПС по
кривой с малой скоростью в составе поезда в режиме тяги с учетом ветровой
нагрузки, сил тяжести от возвышения наружного рельса создается момент,
опрокидывающий СПС внутрь кривой.
Устойчивость СПС от
опрокидывания оценивают на стадии проектирования расчетным путем.
При опрокидывании
наружу кривой рассматривают движение единицы подвижного состава с максимальной
скоростью в составе поезда в кривой радиусом 650 м с возвышением наружного
рельса
равным 0, в режиме торможения поезда.
Устойчивость
экипажа СПС от опрокидывания внутрь кривой проверяют при движении ее в кривой
радиусом 300 м с возвышением наружного рельса
,
равным 150 мм.
Коэффициент запаса
устойчивости СПС от опрокидывания вычисляют по формуле
, (88)
где
- статическая вертикальная сила давления
колеса на рельс с учетом обезгрузки при действии вертикальных составляющих
продольных сил, действующих на кузов (главную раму) через автосцепку;
-
динамическая вертикальная сила давления колеса на рельс, вызванная действием
поперечных сил с учетом перемещений центров тяжести кузова и тележек;
-
допускаемый коэффициент запаса устойчивости от опрокидывания при опрокидывании
наружу кривой - 1,5, при опрокидывании внутрь кривой - 1,2.
Статические силы
давления колеса на рельс
вычисляют по формуле
, (89)
где
- сила тяжести экипажа;
n - число осей
экипажа;
-
вертикальная составляющая продольной силы, действующая на экипаж через
автосцепку.
Динамические силы
давления колеса на рельс
вычисляют по формуле
, (90)
где
- поперечная составляющая продольной силы,
действующая на экипаж через автосцепку;
-
боковые силы, действующие на кузов и тележку, зависящие от поперечных
составляющих сил тяжести, возникающих вследствие возвышения наружного рельса;
- сила
тяжести кузова и тележки;
-
высота от уровня головок рельсов до центров тяжести кузова и тележки;
-
высота от уровня головок рельсов до геометрических центров боковых проекций
кузова и тележки;
-
суммарное смещение центра тяжести тележки в поперечной плоскости от ее
продольной оси относительно осей колесных пар за счет зазоров в буксах,
челюстях;
-
суммарное смещение центра тяжести кузова в поперечной плоскости от его
продольной оси;
2S - расстояние
между кругами катания колес;
-
высота от уровня головок рельсов до продольной оси автосцепок, принимается
равной 1,050 м;
- силы
бокового давления ветра на кузов и тележку.
, (91)
где
- возвышение наружного рельса, принимают
максимальным, равным 0,15 м;
R - радиус кривой;
V - скорость
движения экипажа.
Значения боковых
сил, действующих на тележку, в случае опрокидывания наружу кривой вычисляют по
формуле
. (92)
Значения боковых
сил, действующих на кузов, в случае опрокидывания внутрь кривой (при отсутствии
центробежных сил) вычисляют по формуле
. (93)
Значения боковых
сил, действующих на тележку, в случае опрокидывания внутрь кривой (при
отсутствии центробежных сил) вычисляют по формуле
. (94)
Значения
вертикальной
и поперечной
составляющих продольной силы, действующей на
экипаж через автосцепку, вычисляют по формулам
, (95)
, (96)
где N - продольные
силы, действующие на кузов через автосцепку. Значения N принимают для расчетов
в зависимости от места установки СПС в поезде, от направления действия (сжатия
или растяжения), конструкции экипажа и осевой нагрузки;
-
разность уровней продольных осей сцепленных автосцепок, принимается 0,1 м;
2a - длина жесткого
стержня, образованного двумя сцепленными автосцепками;
-
длина экипажа по осям автосцепок.
Силы бокового
давления ветра на кузов и тележку вычисляются по формулам
, (97)
, (98)
где
- удельное давление ветра, принимается равным
500 Па;
-
площади боковых поверхностей кузова и тележки.
7.1.1.6.
Коэффициент конструктивного запаса рессорного подвешивания
вычисляют по формулам
, (99)
где H - минимальное
расстояние по вертикали между буксой и подрессоренной частью тележки или между
элементами главной рамы и тележки;
-
статический прогиб рессорного подвешивания;
-
максимальный прогиб пружины;
,
-
высота пружины в свободном состоянии;
-
минимальная высота пружины.
Примечание. Если
пружины имеют ограничители прогиба, замыкание которых произойдет до достижения
минимальной высоты пружины
,
принимают прогиб пружины до замыкания ограничителей
.
Коэффициент
конструктивного запаса рессорного подвешивания
используют также для проверки прочности рессор
(подвесок, серег и т.д.), работающих в вертикальном направлении. Наибольшую
вертикальную силу
,
действующую на указанную деталь рессорного подвешивания, вычисляют по формуле
,
(100)
где
- статическая сила, действующая на данную
деталь.
7.1.1.7. Запас на
относительные перемещения элементов экипажа
Характеристики
рессорного подвешивания, изложенные в Приложении Ж, должны исключать
возможность жестких ударов кузова, тележек и колесных пар при их взаимных
перемещениях во время движения СПС до конструкционной скорости.
7.1.1.8.
Вертикальные и горизонтальные (поперечные) ускорения кузова (главной рамы)
Вертикальные (ВУ) и
горизонтальные (ГУ) ускорения при расчетах определяют методами компьютерного
моделирования.
При испытаниях
ускорения измеряют над колесными парами у двухосного экипажа и у шкворня (пяты)
тележечного.
7.1.1.9.
Показателями плавности хода СПС в вертикальной и горизонтальной плоскости
оценивают динамические качества СПС, исходя из условий физиологического
воздействия ускорений и частот колебаний на организм человека, на
работоспособность электронного оборудования, сохранность груза.
7.2.
Показатели воздействия на путь
Оценку воздействия
СПС на путь проводят расчетным путем с использованием значений рамной силы и
коэффициента вертикальной динамики, полученных компьютерным моделированием или
при ходовых динамических испытаниях.
В результате
расчета определяют:
- максимальные
вероятные нагрузки на шпалы;
- максимальные
вероятные напряжения в шпалах под подкладкой;
- максимальные
вероятные напряжения в балласте под шпалой.
Показатели
определяют для каждой градации скорости движения и каждой конструкции пути.
В необходимых случаях
проводятся испытания по воздействию на путь.
8. Общие
требования к испытаниям
8.1.
Стендовые и ходовые прочностные испытания
8.1.1. Главные
рамы, несущие кузова (в том числе кабины), рамы тележек и тягового привода
подвергают стендовым испытаниям на прочность в рабочем и транспортном режимах
от статических нагрузок в вертикальном и продольном направлениях, испытаниям в
рабочем и транспортном режимах, а также при соударениях.
8.1.2. Детали
крепления и несущие конструкции рабочих органов испытывают под действием
нагрузок, возникающих на СПС в рабочем режиме, а также от нагрузок, возникающих
при маневрах и движении в транспортном состоянии.
8.1.3. СПС,
предъявляемый к испытаниям, должен быть изготовлен в соответствии с
конструкторскими чертежами. Перед началом работ его осматривают, при
необходимости измеряют, проверяют качество сварных соединений и наличие
элементов крепления и страховки от падения на путь деталей рабочих органов и
механической части привода.
8.1.4. Стендовым
испытаниям на прочность от статических нагрузок группы А подвергают несущие
металлоконструкции рам (кузовов):
- при опирании на
тележки или колесные пары;
- при выкатке
колесных пар;
- при подъеме за
автосцепку или лобовый брус для имитации дополнительных нагрузок, возникающих
при сходе СПС с рельсов (режим аварийный).
Эти испытания
главных рам (кузовов), полувагонов, платформ выполняют без установленного на
них оборудования. Для создания испытательных нагрузок используют специальные
мерные грузы. Схема нагружения нагрузками группы А должна соответствовать
развеске СПС.
8.1.5. Колесную
пару и ее элементы подвергают стендовым испытаниям на статические вертикальные
и боковые нагрузки.
8.1.6. Элементы
рессорного подвешивания испытывают в соответствии с ГОСТ 1452.
8.1.7. Стендовым
испытаниям на прочность от нагрузок по оси автосцепок (группа Г) подвергают
главную раму (кузов), платформу, вагон или отдельные узлы (шкворневой узел,
кабину и др.). При этом имитируют нагрузки, возникающие в процессе эксплуатации
(при тяге, торможении, соударениях при маневрах и движении в составе поезда).
По согласованию с заказчиком стендовые испытания на прочность от продольных
нагрузок могут быть проведены на полностью собранном СПС.
8.1.8. Стендовые
испытания на усталость проводят для получения показателей сопротивления
усталости конструкции (детали), которые вместе с данными о нагрузках в
эксплуатации, используют для оценки долговечности. По результатам этих испытаний
отрабатывают элементы конструкции (формы и размеры деталей, сопряжения и
способы их соединения и пр.) для уменьшения в них концентрации напряжений,
повышения технологичности, а также определяют необходимость и вид упрочнения.
Объем стендовых испытаний на усталость определяют наличием данных по
характеристикам сопротивления усталости элементов конструкции СПС.
8.1.9. При натурных
ходовых испытаниях на прочность несущие конструкции и элементы крепления
рабочих органов испытывают под действием нагрузок группы Д (см. 6.2.1),
возникающих при движении СПС в результате колебаний масс на рессорном
подвешивании при взаимодействии колес с рельсами и от вибрации оборудования и
конструкции. СПС приводят в транспортное состояние и осуществляют движение по
прямым, кривым участкам пути и стрелочным переводам на боковой путь с
конструкционной или максимально разрешенной скоростью (транспортный режим).
Отдельно реализуют режим прохода кривой малого радиуса, оговоренного
техническими условиями на конкретный СПС. Испытания проводят на полностью
оборудованном и готовом к эксплуатации СПС.
8.1.10. Натурным
испытаниям на соударение подвергают полностью оборудованный, экипированный СПС.
Этим испытаниям предшествуют статические испытания главной рамы (кузова) или их
расчеты. Соударение осуществляют путем накатывания испытуемой единицы СПС на
подпор или вагона-бойка, разгоняемого до заданной скорости, на испытуемую
единицу СПС, находящуюся в голове подпора. Измеряют силу удара в автосцепку,
скорость набегания СПС или вагона-бойка и напряжения в элементах объекта.
8.1.11. Натурные
испытания на прочность в рабочем режиме проводят для получения данных о
фактической нагруженности несущих конструкций и мест крепления рабочих органов,
а также в случаях, когда рабочие нагрузки имеют характерные особенности
(большие значения, переменные с высокой частотой, ударно-импульсного характера
и др.), способные вызвать высокие уровни напряжений в элементах конструкции
или, если такие напряжения получены в элементах рабочих органов при других видах
испытаний. Испытаниям в рабочем режиме подвергают СПС, полностью оборудованный,
в работоспособном состоянии и выполняющим свои функции в соответствии с
нормативными документами.
8.2.
Поколесное взвешивание
Отклонение
фактического значения силы тяжести СПС от значения, указанного в техническом
задании (ТЗ) на конкретный СПС, вычисляют по формуле
,
(101)
где P - фактическая
сила тяжести СПС, представляет сумму сил тяжести, действующих от каждого колеса
на рельс;
- сила
тяжести СПС, указанная в ТЗ.
Разность нагрузок
по колесам колесной пары, %, по осям в одной тележке и по сторонам вычисляют из
выражения
,
(102)
где
- наибольшие и наименьшие значения сил
тяжести, действующих на рельс, соответственно по колесам колесной пары, по осям
в одной тележке и по сторонам.
Оценку результатов
взвешивания "разность нагрузок по колесам колесной пары" СПС на
трехэлементных тележках (типа ЦНИИ-ХЗ) и подобных им проводят по нормам
допустимого поперечного и продольного смещения груза в вагонах (см. ЦМ-943).
Оценка развески СПС
приведена в Приложении И.
8.3.
Ходовые динамические и по воздействию на путь испытания
Опытные образцы СПС
подвергают ходовым динамическим испытаниям.
8.3.1. При
динамических испытаниях определяют и дают оценку динамическим качествам и
воздействию на путь СПС как повозки.
8.3.2. При
проведении ходовых динамических испытаний измеряют следующие динамические
показатели:
- рамные силы;
- напряжения в
элементах конструкции;
- вертикальные и
горизонтальные ускорения главной рамы над колесными парами для двухосного экипажа
или у шкворня пяты для тележечного экипажа;
- вертикальные и
горизонтальные деформации упругих элементов рессорного подвешивания экипажа;
- угловые
перемещения тележек относительно главной рамы в продольной поперечной
плоскости.
8.3.3. На основе
измеряемых параметров рассчитывают следующие показатели:
- коэффициенты
вертикальной динамики;
- показатели
плавности хода (для самоходного СПС и с обслуживающим персоналом);
- коэффициент
устойчивости колеса от вкатывания на головку рельса;
- напряжения в элементах
верхнего строения пути.
8.3.4. В
необходимых случаях для более полного исследования динамических качеств экипажа
СПС одновременно с ходовыми испытаниями проводят испытания по воздействию на
путь в кривых участках пути и стрелочных переводах. В пути измеряют следующие
показатели:
- кромочные
напряжения в подошве рельсов;
- боковые силы;
- горизонтальные и
вертикальные нагрузки на рельсы и шпалы.
Полный объем
измеряемых и рассчитываемых параметров определяют рабочей методикой испытаний с
учетом степени новизны и назначения СПС конкретного вида.
9.
Применяемые материалы и допускаемые напряжения
9.1. Материалы,
применяемые при изготовлении конструкций СПС, и сварочные материалы должны
соответствовать требованиям, установленным в нормативных документах на них. При
отсутствии сертификата качества изготовитель конструкции должен провести
испытания этих материалов на соответствие требованиям, установленным в
нормативных документах на применяемые материалы.
При отсутствии
сертификата качества на сталь, ее химический состав следует определять
проведением химического анализа по ГОСТ 7565 и ГОСТ 22536 и контролем
механических свойств по ГОСТ 1497.
9.2. Требования к
материалам, применяемым при изготовлении конструкций СПС
9.2.1. Технические
требования на металлопрокат и отливки для кузовов, рам, тележек и других
металлоконструкций СПС приведены в таблице В.1 (Приложение В).
Химический состав и
механические свойства сталей, применяемых при изготовлении конструкций, должны
соответствовать требованиям ГОСТ 380, ГОСТ 535, ГОСТ 977, ГОСТ 1050, ГОСТ
14637, ГОСТ 19281.
9.2.2. Качество
поверхности листового проката должно удовлетворять требованиям ГОСТ 14637, ГОСТ
16523, сортового и фасонного - ГОСТ 535.
9.2.3. Допускаемые
нормы искривления проката должны соответствовать значениям, приведенным в
таблице К.1 (Приложение К).
9.2.4. При
искривлениях проката, превышающих значения, указанные в таблице К.1, правку
проводят только в горячем состоянии при температуре не выше 900 °C (с
окончанием процесса правки при температуре не ниже 700 °C). Охлаждение после
правки необходимо осуществлять на воздухе при температуре не ниже 0 °C.
9.2.5. При правке
элементов из коррозионно-стойких (нержавеющих) сталей не должно быть
повреждения поверхности металла.
9.2.6. Искривление
листового и профильного проката, поступающего на заготовительные операции, не
должно превышать значений, приведенных в таблицах К.1 и К.2 (Приложение К).
9.2.7. Литые
несущие детали СПС должны быть изготовлены из низколегированных сталей марок
20ГЛ, 20ГФЛ, 20ДТЛ, нелегированных 15Л, 20Л, 25Л по ГОСТ 977 или других марок
по согласованию с заказчиком. Отливки следует применять только после
термической обработки, обеспечивающей получение равномерной и мелкозернистой
структуры.
Содержание марганца
в сварных деталях должно быть не более 1,4%, углерода - не более 0,23%.
Для стали типа
20Г1ФЛ допускается максимальное содержание углерода до 0,25% с гарантированной
ударной вязкостью при температуре минус 60 °C - 2,5 кГм/см2, при содержании
углерода не более 0,24% содержание марганца допускается до 1,5%.
9.2.8. Технические
требования и технические условия на поковки из конструкционной и легированной
стали по ГОСТ 8479 и ГОСТ 4543.
9.2.9. В
конструкциях СПС допускается применение соединений из коррозионно-стойких
(нержавеющих) сталей с низколегированными и углеродистыми сталями 09Г2, 09Г2Д,
09Г2С, 09Г2СД, 10ХНДП, 15ХСНД по ГОСТ 19282; Ст3сп, Ст5сп по ГОСТ 380; 16Д по
ГОСТ 6713; сталь 15, сталь 20 по ГОСТ 1050.
9.3. Сварочные
материалы
9.3.1. Электроды
для ручной дуговой сварки сталей должны соответствовать требованиям ГОСТ 9466 и
ГОСТ 9467.
9.3.2. Сварочная
проволока, применяемая при автоматической под флюсом и механизированной (под
флюсом и в среде защитных газов) сварке конструкций должна соответствовать
требованиям ГОСТ 2246, сварочная самозащитная порошковая проволока - ГОСТ
26271.
9.3.3. Флюс,
применяемый для сварки конструкций, должен соответствовать требованиям ГОСТ
9087.
9.3.4. Требования к
защитным газам, применяемым при сварке конструкций, должны соответствовать
требованиям ГОСТ 8050 (для углекислого газа) и ГОСТ 10157 (для аргона).
9.3.5. Требования к
газам, применяемым при резке сталей, должны соответствовать ГОСТ 5583, ГОСТ
6331 (для кислорода) и ГОСТ 5457 (для ацетилена).
9.4. Требования к
материалам для рессор и пружин
9.4.1. Рессоры,
пружины должны быть изготовлены из углеродистых и легированных сталей: 65Г,
55С2, 65С2А, 60С2, 60С2А, 60С2ХФА - по ГОСТ 14959.
9.4.2. Листовые
рессоры изготавливают в соответствии с требованиями ГОСТ 1425 при обеспечении
твердости термически обработанных листов 363... 432 HB или 40,5... 46,5
.
9.4.3. Пружины
цилиндрические винтовые тележек и ударно-тяговых приборов СПС должны
изготавливать в соответствии с требованиями ГОСТ 1452 из горячекатаного
круглого проката легированной рессорно-пружинной стали по ГОСТ 14955.
9.5. Для
изготовления несущих элементов экипажной части СПС сталей новых марок или иных
материалов рекомендуется применять литые стали с содержанием углерода не более
0,23%.
9.6. Для
изготовления амортизирующих элементов, прокладок (виброизолирующих и
уплотнительных) и др. необходимо использовать резины, обладающие
регламентированными свойствами. Оценку работоспособности резин проводят по
допускаемым напряжениям и относительным деформациям, приведенным в таблицах Л.1
и Л.2 (Приложение Л).
По согласованию с
заказчиком разрешается использовать другие марки резин, отвечающих требованиям
настоящего стандарта.
10. Оценка
влияния остаточных напряжений
на циклическую
долговечность конструкций
10.1.
Расчет коэффициента запаса сопротивления усталости сварного соединения с
высокими остаточными напряжениями
10.1.1. При
циклическом нагружении коэффициент запаса сопротивления усталости n сварного
соединения с высокими растягивающими остаточными напряжениями вычисляют по
формуле
,
(103)
где
- предел выносливости стандартного образца при
симметричном цикле нагружения;
к - коэффициент
концентрации, учитывающий понижение сопротивления усталости;
-
амплитуда напряжений цикла;
-
коэффициент, характеризующий чувствительность металла к асимметрии цикла;
-
среднее напряжение цикла, вычисляют по формуле
,
(104)
где
- остаточные напряжения в сварном шве.
Все показатели,
входящие в формулу (103), определяют по 6.3.2.3.
Значения остаточных
напряжений в зоне концентрации напряжений вычисляют по формуле
,
(105)
где
- остаточные напряжения в сварном шве;
-
предел текучести материала;
-
теоретический коэффициент концентрации напряжений;
-
максимальные напряжения цикла.
Значения остаточных
напряжений при отсутствии концентрации напряжений вычисляют по формуле
.
(106)
С возрастанием
среднего напряжения цикла
амплитуды предельных напряжений
уменьшаются.
10.1.2. Для
ориентировочных расчетов предел выносливости детали с учетом влияния остаточных
напряжений можно определить по формуле
,
(107)
где
- предел выносливости детали в исследуемой
зоне, определенный экспериментально.
Коэффициент запаса
сопротивления усталости в этом случае подсчитывают по формуле
,
(108)
где
- амплитуда напряжений цикла.
10.2.
Способы предупреждения появления остаточных напряжений в сварных конструкциях
СПС
Для предупреждения
появления остаточных напряжений при проектировании конструкции должны быть
выполнены следующие условия:
- число сварных
швов и сечений должно быть минимально необходимым по условиям прочности;
- сечения элементов
конструкции должны быть симметричными и составленными из минимального числа
сварных швов;
- в местах
соединения элементов конструкции, особенно в зоне действия максимальных
напряжений, необходимо обеспечить плавность сопряжений поверхностей сечений;
- при приварке к
растянутым поясам несущих конструкций деталей сварными швами, расположенными
нормально к силовому потоку, следует назначать расстояние между швами не менее
50 мм;
- в растянутых
поясах несущих конструкций следует закладывать двухсторонние угловые швы с
полным проваром;
- в напряженных
зонах конструкции число второстепенных деталей должно быть минимальным;
- стыковые
продольные швы несущих элементов должны быть расположены в зоне нейтрального
слоя общего поперечного сечения составного элемента (или в зоне центра тяжести);
- форма разделки
кромок должна обеспечивать минимальный объем наплавленного металла при условии
соблюдения прочности сварного соединения.
При изготовлении
конструкции следует выполнять следующие условия:
- назначать способ
сварки, который обеспечивает минимально возможную погонную энергию при
наложении сварных швов;
- соблюдать
рациональную технологию сварки (режим и последовательность наложения сварных
швов);
- в случае
необходимости применять обратную деформацию.
Сварка должна быть
выполнена в следующем порядке:
- сварка стыковых
швов в свободном состоянии, расположенных перпендикулярно к силовому потоку;
- сварка остальных
стыковых швов;
- заварка угловых
швов.
Места сварки
элементов несущих конструкций, подвергаемые в процессе эксплуатации
значительным по величине и продолжительности циклическим нагрузкам, должны быть
подвергнуты упрочнению. Способ упрочнения устанавливают в конструкторской
документации.
10.3.
Требования к устранению (снижению) остаточных напряжений
Для устранения
(снижения) остаточных напряжений используют:
- общую и локальную
термическую обработку (высокий отпуск);
- предварительный и
сопутствующий подогрев;
- поверхностное
пластическое деформирование шва и околошовной зоны (низкочастотная и
ультразвуковая обработка, обкатка роликами, наклеп многобойковым инструментом).
10.4.
Методы упрочнения
Для сварных швов и
околошовной зоны применяют следующие виды упрочнения:
- механическую
обработку швов;
- аргонодуговую
обработку швов;
- поверхностное
пластическое деформирование.
Приложение
А
(рекомендуемое)
ПРАВИЛА
ПРОВЕДЕНИЯ МОДЕЛИРОВАНИЯ
ДИНАМИКИ ПОДВИЖНОГО
СОСТАВА
А.1. Для оценки
динамических качеств проектируемых экипажей специального подвижного состава
проводят компьютерное моделирование. При моделировании используются программные
комплексы типов Adams (США), Simpack (Германия), Универсальный Механизм УМ
(Россия), имеющие специализированный модуль для железнодорожного подвижного
состава. Можно применять и другие лицензионные программные комплексы,
соответствующие требованиям 6.1.2.
Основные принципы
моделирования должны быть следующие:
- составляют модель
экипажа подвижного состава, которая представляется набором абсолютно твердых
тел, связанных посредством шарниров и силовых элементов (буксовые узлы,
пружины, рессоры, гасители, скользуны, боковые опоры);
- задают исходные
данные: инерционные, геометрические и упруго-диссипативные параметры экипажа,
параметры пути (план пути, неровности, жесткостные характеристики), режим
движения, метод вычисления;
- проводят расчет
динамических показателей экипажа в соответствии с разделом 4, а также
дополнительных показателей (углы поворота тележек, ускорения и другие) для
каждой скорости движения и плана пути;
- по выходным
значениям определяемых параметров проводят статистическую обработку.
А.2. Проведение
моделирования приведено на примере моделирования нового перспективного СПС на
универсальных двухосных тележках с использованием программного комплекса УМ.
Расчетная схема
экипажа СПС включает в себя семь твердых тел (кузов, две рамы тележки, 4
колесные пары) и имеет 42 степени свободы.
В модели заданы
следующие исходные параметры:
- масса кузова -
64000 кг;
- масса тележки -
14000 кг;
- неподрессоренная
масса на колесную пару - 3500 кг;
- осевая нагрузка -
23 тс.
Жесткости буксовой
ступени рессорного подвешивания:
- вертикальная на
буксу - 1720 кН/м,
- поперечная на
буксу - 2000 кН/м.
Жесткость
центральной ступени в вертикальном направлении
- (на тележку) -
2640 кН/м.
Жесткость
поперечной связи тележки с кузовом:
- в пределах зазора
от 0 до 20 мм - 360 кН/м,
- в пределах зазора
от 20 до 40 мм - 2100 кН/м.
Коэффициент
демпфирования буксовой ступени в вертикальном направлении на буксу должен быть
70 кН x с/м.
Коэффициент
демпфирования центральной ступени на тележку должен быть:
- в вертикальном
направлении 108 кН x с/м;
- виляния 56 кН x
с/м;
- бокового относа
56 кН x с/м.
Шкворневая база
кузова 8 м.
Колесная база
тележки 2,25 м.
Поперечное
расстояние между вертикальными пружинами и демпферами должно быть:
- буксовой ступени
2,1 м;
- центральной
ступени 2,2 м.
Радиус колеса по
кругу катания 0,525 м.
Профиль колес:
новый локомотивный по ГОСТ 11018.
Путевая структура:
прямые и кривые участки пути, рельсы Р65, неровности (отклонения левого и
правого рельсов в вертикальном и поперечном направлениях от продольной оси пути
с шагом 1 м) и жесткостные характеристики (в вертикальном направлении 44 МН/м,
в поперечном - 18 МН/м) должны соответствовать реальному железнодорожному пути
удовлетворительного содержания.
Модель сил
взаимодействия в контакте "колесо-рельс": использован алгоритм
FASTSIM, основанный на линейной теории Калкера.
Основные выходные
динамические показатели при расчетах следующие: рамные силы, вертикальные и
горизонтальные ускорения в кабинах машиниста, коэффициенты вертикальной
динамики буксовой и центральной ступеней рессорного подвешивания, углы поворота
тележек относительно кузова.
Расчеты проводились
при следующих режимах движения:
- в прямом участке
пути со скоростями 80, 100, 120 и 130 км/ч (конструкционная скорость 120 км/ч);
- в кривой радиусом
600 м со скоростями 80, 100 и 110 км/ч;
- в кривой радиусом
300 м при скоростях движения 50 и 70 км/ч.
В прямых участках
пути при скоростях до 130 км/ч получают следующие максимальные значения
динамических показателей: вертикальные ускорения кузова СПС не превышали 0,33g,
коэффициенты динамики буксовой ступени - 0,24, центральной - 0,19; рамные силы
- 34 кН (отношение рамной силы к осевой нагрузке составило 0,15),
горизонтальные ускорения кузова - 0,23g. Угловые перемещения тележек
относительно кузова - 10 мрад.
При моделировании
движения в кривой радиуса 600 м максимальные значения рамных сил составили 59
кН, в кривой 300 м - 55 кН. Отношение рамной силы к статической нагрузке не
превышало 0,26. В кривой 600 м при скорости 110 км/ч вертикальные ускорения
кузова достигали 0,32g, а горизонтальные ускорения - 0,36g. В кривой радиуса
300 м со скоростью 70 км/ч максимальные значения ускорений оказались ниже и
составили, соответственно, 0,21g и 0,28g.
Значения
коэффициентов вертикальной динамики в кривых участках пути в буксовой ступени
не превышали 0,30, а в центральной ступени - 0,22. Максимальные значения
угловых перемещений тележек в кривой 600 м достигали 15 мрад, в кривой 300 м -
23 мрад.
В результате
проведенного моделирования в прямых и кривых участках пути максимальные
расчетные значения основных динамических показателей экипажа СПС не превышали нормируемых
значений.
Приложение
Б
(рекомендуемое)
СТЕПЕНЬ ВЛИЯНИЯ
КОНЦЕНТРАЦИИ В СВАРНЫХ
СОЕДИНЕНИЯХ В
ЗАВИСИМОСТИ ОТ ИСПОЛНЕНИЯ
Таблица Б.1
┌──────────────────────────┬──────────────────────────────────────────────┐
│ Вид соединения │ Описание исполнения │
├──────────────────────────┴──────────────────────────────────────────────┤
│ Концентратор напряжений К0 -
незначительный │
└─────────────────────────────────────────────────────────────────────────┘
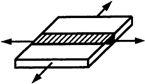
Детали соединены
стыковым швом специального
качества в
поперечном направлении к силе,
действующей на
соединяемые детали.
Детали соединены
стыковым швом специального
качества в
продольном направлении к силе,
действующей на
соединяемые детали
───────────────────────────────────────────────────────────────────────────
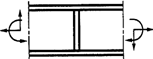
Листы стенок
соединены стыковым швом
специального
качества в поперечном направлении
───────────────────────────────────────────────────────────────────────────
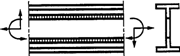
Листы стенок и
фасонные пояса из сортовой или
прутковой стали (за
исключением листовой
стали) соединены
стыковым швом (нормального
качества)
───────────────────────────────────────────────────────────────────────────
Концентратор напряжений К1 -
умеренный
───────────────────────────────────────────────────────────────────────────
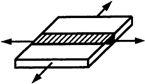
Детали соединены
стыковым швом нормального
качества в
поперечном направлении к силе,
действующей на соединяемые
детали
───────────────────────────────────────────────────────────────────────────
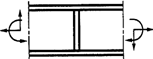
Листы стенок
соединены стыковым швом
(нормального качества) в поперечном
направлении
───────────────────────────────────────────────────────────────────────────
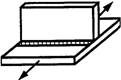
Сплошная деталь, к
которой в поперечном
направлении к силе,
действующей на соединяемые
детали, приварены
детали непрерывным угловым
швом с двусторонней
разделкой
───────────────────────────────────────────────────────────────────────────
Концентратор напряжений К2 -
средний
───────────────────────────────────────────────────────────────────────────
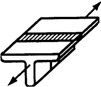
Детали из фасонной
или прутковой стали (за
исключением
листовой), соединенные стыковым
швом специального
качества в поперечном
направлении к силе,
действующей на соединяемые
детали
───────────────────────────────────────────────────────────────────────────
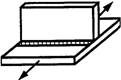
Сплошная деталь, к
которой в поперечном
направлении к силе,
действующей на соединяемые
детали, приварены
детали непрерывным
двусторонним
угловым швом (специального
качества) без
разделки
───────────────────────────────────────────────────────────────────────────
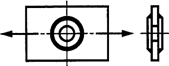
Сплошная деталь, к
которой приварены ступицы
угловым швом
(специального качества)
───────────────────────────────────────────────────────────────────────────
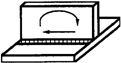
Угловой шов с
двусторонней разделкой
специального
качества при нагружении изгибом
и срезом
───────────────────────────────────────────────────────────────────────────
Концентратор напряжений К3 -
сильный
───────────────────────────────────────────────────────────────────────────
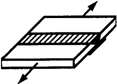
Сплошная деталь, к
которой в поперечном
направлении к силе,
действующей на соединяемые
детали, приварены
детали двусторонним угловым
швом (нормального
качества)
───────────────────────────────────────────────────────────────────────────
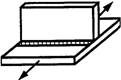
Сплошная деталь, к
которой в поперечном
направлении к силе, действующей
на соединяемые
детали, приварены
детали двусторонним угловым
швом (нормального
качества)
───────────────────────────────────────────────────────────────────────────
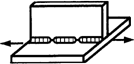
Сплошная деталь, к
которой приварены
продольные полосы
прерывистым двусторонним
угловым швом
───────────────────────────────────────────────────────────────────────────
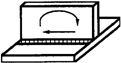
Шов с двумя
симметричными скосами одной
кромки с
двусторонним угловым швом
(нормального
качества) в местах присоединения
с изгибом и срезом
───────────────────────────────────────────────────────────────────────────
Концентратор напряжений К4 -
особо сильный
───────────────────────────────────────────────────────────────────────────
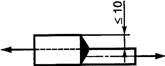
Детали разной
толщины несоосно соединены
стыковым швом
нормального качества без
разделки в
поперечном направлении к силе,
действующей на
соединяемые детали
───────────────────────────────────────────────────────────────────────────
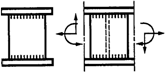
Листы поясов и
стенок, к которым приварены
поперечные ребра
непрерывным односторонним
угловым швом
нормального качества в поперечном
направлении к силе,
действующей на соединяемые
детали
───────────────────────────────────────────────────────────────────────────

Детали, наложенные
друг на друга, с
отверстиями или
прорезью, обваренные угловым
швом
───────────────────────────────────────────────────────────────────────────
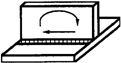
Присоединенные
детали приварены угловым швом
и нагружены изгибом
и срезом
───────────────────────────────────────────────────────────────────────────
Приложение
В
(рекомендуемое)
ОСНОВНЫЕ
МЕХАНИЧЕСКИЕ ХАРАКТЕРИСТИКИ
МЕТАЛЛОВ И ИХ
ВЕРОЯТНОСТНЫЕ ПАРАМЕТРЫ
Таблица В.1
Основные
механические характеристики
металлов,
применяемых в СПС
┌───────────────┬─────────┬─────────────┬──────────┬───────┬───────┬────────┐
│
Наименование │Вид │
Класс │ Толщина,
│Предел │Вре-
│Предел │
│ металла
│проката, │ прочности,
│ диаметр │теку- │менное │вынос- │
│ │термичес-│ марка
│ проката, │чести
│сопро- │ливости │
│ │кой │ │ мм
│сигма ,│тивле- │сигма
,│
│ │обработки│ │ │ т │ние │
-1 │
│ │ │ │ │Н/мм2 │сигма ,│Н/мм2 │
│ │ │ │ │ │ в │ │
│ │ │ │ │ │Н/мм2 │
│
├───────────────┼─────────┼─────────────┼──────────┼───────┼───────┼────────┤
│
Прокат │Лист │
16Д │ До 20
│ 235 │
375 │ 170
│
│низколегирован-│ │ │ 21 - 40 │
225 │ 375
│ 170 │
│ный
├─────────┼─────────────┼──────────┼───────┼───────┼────────┤
│конструкционный│Сортовой,│ 16Д
│ До 20 │
235 │ 375
│ 170 │
│для │фасонный │ │ 21 - 40 │
235 │ 375
│ 170 │
│мостостроения │ │ │ │ │ │ │
│по
ГОСТ 6713 │ │ │ │ │
│ │
├───────────────┼─────────┼─────────────┼──────────┼───────┼───────┼────────┤
│
Прокат
│Сортовой,│
Ст3сп │ До 10
│ 255 │
380 │ 180
│
│сортовой
и │фасонный │ │ 10 - 20 │
245 │ 370
│ 170 │
│фасонный
из │ │ Ст5сп
│ До 10 │
295 │ 490
│ 230 │
│стали │ │ │ 10 - 20 │
285 │ 490
│ 230 │
│углеродистой │ │ │ 20 - 40 │
275 │ 490
│ 255 │
│обыкновенного │ │ │ │ │ │ │
│качества
по │ │ │ │ │ │ │
│ГОСТ
535, │ │ │ │ │ │ │
│ГОСТ
380 │ │ │ │ │ │ │
├───────────────┼─────────┼─────────────┼──────────┼───────┼───────┼────────┤
│
Прокат │Лист, │
Ст3сп │ До 20
│ 245 │
370 │ -
│
│толстолистовой
│полоса │ │ 20 - 40 │
235 │ 370
│ - │
│из
углеродистой│ │ Ст5сп
│ До 20 │
285 │ 490
│ - │
│стали │ │ │ 20 - 40 │
275 │ 490
│ - │
│обыкновенного │ │ │ 40 - 100 │ 265
│ 490 │
- │
│качества
по │ │ │ │ │ │ │
│ГОСТ
14637, │ │ │ │ │ │ │
│ГОСТ
380 │ │ │ │ │ │ │
├───────────────┼─────────┼─────────────┼──────────┼───────┼───────┼────────┤
│
Прокат для │Листовой
│ С255 │2,0 - 3,9 │ 255
│ 380 │
- │
│строительных │широко- │
Ст3сп │ 4 - 10
│ 245 │
380 │ -
│
│стальных │полосный,│ │ 10 - 20 │
245 │ 370
│ - │
│конструкций │профили │ │ 20 - 40 │
235 │ 370
│ - │
│по
ГОСТ 27772 │Фасонный │ │ 4 - 10
│ 255 │
380 │ -
│
│ │прокат │ │ 10 - 20 │
245 │ 370
│ - │
│ │ │ │ 20 - 40 │
235 │ 370
│ - │
│
├─────────┼─────────────┼──────────┼───────┼───────┼────────┤
│ │Листовой │ С285
│2,0 - 3,9 │ 285 │
390 │ -
│
│ │широко- │
Ст3сп │ 4 - 10
│ 275 │
390 │ -
│
│ │полосный,│ │ 10 - 20 │
265 │ 380
│ - │
│ │профили │ │ │ │ │ │
│ │Фасонный │ │ 4 - 10
│ 285 │
400 │ -
│
│ │прокат │ │ 10 - 20 │
275 │ 390
│ - │
│
├─────────┼─────────────┼──────────┼───────┼───────┼────────┤
│ │Листовой │ С345
│2,0 - 3,9 │ 345 │
490 │ -
│
│ │широко- │
12Г2С │ 4 - 10
│ 345 │
490 │ -
│
│ │полосный,│ 09Г2С
│ 10 - 20 │ 325
│ 470 │
- │
│ │профили │ │ │ │ │ │
│ │Фасонный │ │ 4 - 10
│ 345 │
490 │ -
│
│ │прокат │ │ 10 - 20 │
325 │ 470
│ - │
│ │ │ │ 20 - 40 │
305 │ 460
│ - │
│ │Листовой │ С345К │
4 - 10 │ 345
│ 470 │
- │
│ │широко- │
10ХНДП │ │ │ │ │
│ │полосный,│ │ │ │ │ │
│ │профили │ │ │ │ │ │
│ │Фасонный │ │ 4 - 10
│ 345 │
470 │ -
│
│ │прокат │ │ │ │ │ │
├───────────────┼─────────┼─────────────┼──────────┼───────┼───────┼────────┤
│
Прокат для │Листовой
│ С375 │2,0 - 3,9 │ 375
│ 510 │
- │
│строительных │широко- │
12Г2С │ 4 - 10
│ 375 │
510 │ -
│
│стальных │полосный,│ │ 10 - 20 │
355 │ 490
│ - │
│конструкций │профили │ │ 20 - 40 │
335 │ 480
│ - │
│по
ГОСТ 27772 │Фасонный │ │ 4 - 10
│ 375 │
510 │ -
│
│ │прокат │ │ 10 - 20 │
355 │ 490
│ - │
│ │ │ │ 20 - 40 │
335 │ 480
│ - │
│
├─────────┼─────────────┼──────────┼───────┼───────┼────────┤
│ │Листовой │ С390
│ 4 - 50 │
390 │ 540
│ - │
│ │широко- │
14Г2АФ │ │ │ │ │
│ │полосный,│ │ │ │ │ │
│ │профили │ │ │ │ │ │
│ │Нормали- │ │ │ │ │ │
│ │зация │ │ │ │ │ │
│
├─────────┼─────────────┼──────────┼───────┼───────┼────────┤
│ │Листовой │ С440
│ 4 - 30 │
440 │ 590
│ - │
│ │широко- │
16Г2АФ │ 30 - 50 │
410 │ 570
│ - │
│ │полосный,│ │ │ │ │ │
│ │профили │ │ │ │ │ │
│ │Нормали- │ │ │ │
│ │
│ │зация │ │ │ │ │ │
│
├─────────┼─────────────┼──────────┼───────┼───────┼────────┤
│ │Листовой │ С590
│ 10 - 36 │ 590
│ 685 │
- │
│ │широко- │
12Г2СМФ │ │ │ │ │
│ │полосный,│ │ │ │ │ │
│ │профили │ │ │ │ │ │
│ │Улучшение│ │ │ │ │ │
├───────────────┼─────────┼─────────────┼──────────┼───────┼───────┼────────┤
│
Прокат из │Сортовой,│
375, 15ГФ, │ До 10
│ 375 │
510 │ 235
│
│стали │полосо- │
10Г2Б │ │ │ │ │
│повышенной │вой, │ │ │ │ │ │
│прочности │фасонный │ │ │ │ │ │
│по
ГОСТ 19281 │Лист, │ 15ГФ, 10Г2Б │ До 10
│ 375 │
510 │ 235
│
│ │гнутые │
14Г2АФ │ 10 - 50 │
375 │ 510
│ - │
│ │профили │ │ │ │ │ │
│
├─────────┼─────────────┼──────────┼───────┼───────┼────────┤
│ │Сортовой,│ 390, 10ХСНД
│ До 15 │
390 │ 530
│ 240 │
│ │полосо- │
15Г2СФ │ До 20
│ 390 │
530 │ 240
│
│ │вой, │ │ │ │ │ │
│ │фасонный │ │ │ │ │ │
│ │Лист, │
12Г2Б │ До 10
│ 390 │
510 │ 235
│
│ │гнутые │
15Г2СФ │ До 32
│ 390 │
510 │ 235
│
│ │профили │
15Г2АФДпс │ До 32
│ 390 │
510 │ 235
│
├───────────────┼─────────┼─────────────┼──────────┼───────┼───────┼────────┤
│
Прокат из │Лист, │
440, │ До 32
│ 440 │
590 │ 265
│
│стали │гнутые │
16Г2АФ │ │ │ │ │
│повышенной │профили │
18Г2АФпс │ │ │ │ │
│прочности │ │ │ │ │ │ │
│по
ГОСТ 19281 │ │ │ │ │ │ │
├───────────────┼─────────┼─────────────┼──────────┼───────┼───────┼────────┤
│
Прокат │Фасонный │
390, 12Г2ФД │ До 20 │
390 │ 520
│ 240 │
│фасонный
из │ │ │ │ │ │ │
│низколегирован-│ │ │ │ │ │ │
│ной
стали для │ │ │ │ │ │ │
│вагоностроения
│ │ │ │ │ │ │
│по │ │ │ │ │ │
│
│ТУ
14-1-5391-99│ │ │ │ │ │ │
├───────────────┼─────────┼─────────────┼──────────┼───────┼───────┼────────┤
│
Прокат │Тонкий │
08Ю │0,7 - 1,5 │от
180 │от 250 │ - │
│тонколистовой │лист │ │1,5 - 2,0 │до 205
│до 350 │ - │
│холоднокатаный
│ │ │2,0 - 3,9 │ 195
│ 250 │
- │
│из
низкоугле- │ │ │ │ │ │ │
│родистой │ │ │ │ │ │ │
│качественной │ │ │ │ │ │ │
│стали
для │ │ │ │ │ │ │
│холодной │ │ │ │ │ │ │
│штамповки │ │ │ │ │ │ │
│по
ГОСТ 9045 │ │ │ │ │ │ │
├───────────────┼─────────┼─────────────┼──────────┼───────┼───────┼────────┤
│
Прокат │Лист │
09Г2С │ 10 - 20 │
325 │ 470
│ 210 │
│листовой
из │ │ │ 20 - 32 │
305 │ 460
│ 210 │
│углеродистой │ │ │ │ │ │ │
│низколегирован-│ │ │ │ │ │ │
│ной
и │ │ │ │ │ │ │
│легированной │ │ │ │ │ │ │
│стали
для │ │ │ │ │ │ │
│котлов
и │ │ │ │ │ │ │
│сосудов, │ │ │ │ │ │ │
│работающих
под │ │ │ │ │
│ │
│давлением │ │ │ │ │ │ │
│по
ГОСТ 5520 │ │ │ │ │ │ │
├───────────────┼─────────┼─────────────┼──────────┼───────┼───────┼────────┤
│
Прокат │Сортовой
│ 08 │
До 80 │ 196
│ 320 │
- │
│сортовой │ │ 10
│ │ 205
│ 330 │
- │
│калиброванный │ │ 15
│ │ 225
│ 370 │
- │
│со
специальной │ │ 20
│ │ 245
│ 410 │
190 │
│отделкой │ │ 25
│ │ 275
│ 450 │
200 │
│поверхности
из │ │ 30
│ │ 295
│ 490 │
220 │
│углеродистой │ │ 35
│ │ 315
│ 530 │
240 │
│качественной │ │ 40
│ │ 335
│ 570 │
250 │
│конструкционной│ │ 45
│ │ 355
│ 600 │
270 │
│стали │ │ 50
│ │ 375
│ 630 │
280 │
│по
ГОСТ 1050 │ │ │ │ │ │ │
├───────────────┼─────────┼─────────────┼──────────┼───────┼───────┼────────┤
│
Сталь листовая│Лист │
Ст3сп+12Х1 │ 4 - 60
│ │ │ │
│горячекатаная │ │ 8Н10Т
│ │ 245
│ 370 │
- │
│двухслойная │ │ Ст3сп+08Х2 │ │ │ │ │
│коррозионно- │ │ 2Н6Т
│ │ 245
│ 370 │
- │
│стойкая │ │ 20К+12Х18Н │ │ │ │ │
│по
ГОСТ 10885 │ │ 10Т
│ │ 245
│ 400 │
- │
│ │ │ 20К+08Х22Н │ │ │ │ │
│ │ │ 6Т
│ │ 245
│ 400 │
- │
│ │ │ 09Г2+12Х18 │ │ │ │ │
│ │ │ Н10Т
│ │ 305
│ 440 │
- │
│ │ │ 09Г2С+12Х1 │ │ │ │ │
│ │ │ 8Н10Т
│ │ 325
│ 470 │
- │
│ │ │ 10ХСНД+12
│ │ │ │ │
│ │ │ Х18Н10Т
│ │ 390
│ 510 │
- │
├───────────────┼─────────┼─────────────┼──────────┼───────┼───────┼────────┤
│
Прокат из │Прутки и
│ 65Г │
До 180 │ 785
│ 980 │
450 │
│рессорно- │полосы │
55С2 │ │ 1175 │ 1270
│ 570 │
│пружинной │ │ 60С2
│ │ 1175
│ 1270 │ 570
│
│углеродистой │ │ 60С2А
│ │ 1375 │ 1570
│ 700 │
│и
легированной │ │ 60С2ХА
│ │ 1325 │ 1470
│ - │
│стали │ │ 60С2ХФА
│ │ 1470 │ 1670
│ 750 │
│по
ГОСТ 14959 │ │ │ │ │ │ │
├───────────────┼─────────┼─────────────┼──────────┼───────┼───────┼────────┤
│
Отливки │Нормали-
│ 20Л │
- │ 216
│ 412 │
165 │
│стальные
по │зация
│ 25Л │ │ 235
│ 441 │
175 │
│ГОСТ
977 │ │ 30Л
│ │ 255
│ 471 │
190 │
│ │ │ 20ГЛ
│ │ 275
│ 540 │
215 │
│ │ │ 20ФГ
│ │ 294
│ 491 │
195 │
│ │ │ 20Г1ФЛ
│ │ 314
│ 510 │
200 │
│ │ │ 30ГСЛ
│ │ 343
│ 589 │
230 │
│ │ │ 30ХГСФЛ
│ │ 392 │ 589
│ 240 │
│
├─────────┼─────────────┼──────────┼───────┼───────┼────────┤
│ │Закалка +│ 20ГЛ
│ - │
334 │ 530
│ - │
│ │отпуск │
30ГСЛ │ │ 392
│ 638 │
- │
│ │ │ 32Х06Л
│ │ 441
│ 638 │
- │
│ │ │ 30ХГСФЛ
│ │ 589
│ 785 │
- │
├───────────────┼─────────┼─────────────┼──────────┼───────┼───────┼────────┤
│
Отливки из │Нормали-
│ 20ГЛ │
- │ 300
│ 500 │
- │
│хладостойкой
и │зация │ 20ФТЛ
│ │ 320
│ 520 │
- │
│износостойкой │ │ 30ХГ2СТЛ
│ │ 600
│ 700 │
- │
│стали
├─────────┼─────────────┼──────────┼───────┼───────┼────────┤
│по
ГОСТ 21357 │Закалка +│ 20ГЛ
│ - │
400 │ 550
│ - │
│ │отпуск │
20ФТЛ │ │ 450
│ 570 │
- │
│ │ │ 30ГЛ
│ │ 490
│ 660 │ -
│
│ │ │ 30ХГ2СТЛ
│ │ 650
│ 750 │
- │
│ │ │ 30ХЛ
│ │ 550
│ 660 │
- │
│ │ │ 110Г13Л
│ │ 400
│ 800 │
- │
├───────────────┼─────────┼─────────────┼──────────┼───────┼───────┼────────┤
│
Листы из │Листы │
АМг2 │5,0 - 10,5│ -
│ 175 │
- │
│алюминия
и │ │ АМг3
│ 5 - 6 │
80 │ 185
│ - │
│алюминиевых │ │ То же
│6,0 - 10,5│ 80 │
185 │ -
│
│сплавов │ │ АМг5М
│0,6 - 4,5 │ 145 │
275 │ 100
│
│по
ГОСТ 21631 │ │ То же
│4,5 - 10,5│ 130 │
275 │ 100
│
│ │ │ АМг5
│ 5 - 6 │
130 │ 275
│ 100 │
│ │ │ То же
│6,0 - 10,5│ 130 │
275 │ 100
│
│ │ │ АМг6М
│ до 10,5 │ 155
│ 315 │
110 │
│ │ │ АМг6
│5,0 - 10,5│ 155 │
315 │ 110
│
│ │ │ 1915
│5,0 - 10,5│ 195 │
315 │ -
│
├───────────────┼─────────┼─────────────┼──────────┼───────┼───────┼────────┤
│
Профили │Прессо- │
АМг2 │ Все
│ 59 │
147 │ -
│
│прессованные │ванные │ АМг3, АМг5 │ размеры │
78 │ 176
│ - │
│из
алюминия и │профили │
АМг5М, │ │ 127
│ 236 │
90 │
│алюминиевых │ │ АМг6
│ │ 127
│ 255 │
90 │
│сплавов │ │ АМг6М
│ │
157 │ 314
│ 110 │
│по
ГОСТ 8617 │ │ 1915
│ │ 196
│ 314 │
110 │
│ │ │ 1915Т
│ │ 216
│ 343 │
120 │
│ │ │ 1935
│ │ 155
│ 245 │
- │
│ │ │ 1935Т
│ │ 155
│ 245 │
- │
├───────────────┼─────────┼─────────────┼──────────┼───────┼───────┼────────┤
│
Сплавы │ -
│ АМг12 │
- │ │
147 │ -
│
│алюминиевые │ │ (АЛ2)
│ │ │
147 │ -
│
│литейные │ │ АМг5Мц
│ │ -
│ 196 │
- │
│по
ГОСТ 1583 │ │ (АЛ28)
│ │ -
│ 196 │
- │
│ │ │ АМг6Л
│ │ -
│ 186 │
- │
│ │ │ (АЛ23)
│ │ │
186 │ -
│
│ │ │ АМг6лч
│ │ │
196 │ -
│
│ │ │ (АЛ23-1)
│ │ │
196 │ -
│
├───────────────┼─────────┼─────────────┼──────────┼───────┼───────┼────────┤
│
Металл шва или│ - │
Э42 │ -
│ - │ 411,5 │ -
│
│наплавленного │ │ Э46
│ │ -
│ 450,8 │ - │
│металла │ │ Э50
│ │ -
│ 490,0 │ - │
│(электроды │ │ Э42А
│ │ -
│ 411,6 │ - │
│покрытые │ │ Э46А
│ │ -
│ 450,0 │ - │
│металлические │
│ Э50А
│ │ -
│ 490,0 │ - │
│для
ручной │ │ │ │ │ │ │
│сварки │ │ │ │ │ │ │
│конструкционных│ │ │ │ │ │ │
│и │ │ │ │ │ │ │
│теплоустойчивых│ │ │ │ │ │ │
│сталей │ │ │ │ │ │
│
│по
ГОСТ 9467) │ │ │ │ │ │ │
├───────────────┼─────────┼─────────────┼──────────┼───────┼───────┼────────┤
│
Металл шва или│ - │
Э-07Х20Н9 │ -
│ - │
539 │ -
│
│наплавленного │ │ Э-07Х19Н11 │ │ -
│ 539 │
- │
│металла │ │ М3Г2Ф
│ │ -
│ 539 │
- │
│(электроды │ │Э-08Х19Н10Г2Б│ │ -
│ 539 │
- │
│покрытые │ │Э-08Х20Н9Г2Б │ │ -
│ 588 │
- │
│металлические │ │Э-10Х25Н13Г2Б│ │ -
│ 588 │
- │
│для
ручной │ │Э-03Х15Н9АГ4 │ │ │ │ │
│дуговой
сварки │ │ │ │ │ │ │
│высоко- │ │ │ │ │ │ │
│легированных │ │ │ │ │ │ │
│сталей
с │ │ │ │ │ │ │
│особыми │ │ │ │ │ │ │
│свойствами
по │ │ │ │ │ │ │
│ГОСТ
10052) │ │ │ │ │ │ │
├───────────────┼─────────┼─────────────┼──────────┼───────┼───────┼────────┤
│
Детали литые │Детали │
- │ -
│ 400 │
540 │ 210
│
│автосцепного │первой │ │ -
│ 450 │
560 │ 230
│
│устройства │группы, │ │ -
│ 500 │
600 │ -
│
│подвижного │нормали- │ │ │ │ │ │
│состава │зация │ │ │ │ │ │
│железных
дорог │закалка +│
│ │ │
│ │
│колеи
1520 мм │отпуск │ │ │ │ │ │
│по
ГОСТ 22703
├─────────┼─────────────┼──────────┼───────┼───────┼────────┤
│ │Детали │
- │ -
│ 295 │
490 │ -
│
│ │второй │ │ -
│ 345 │
510 │ -
│
│ │группы, │ │ │ │ │ │
│ │нормали- │ │ │ │ │ │
│ │зация │
│ │ │ │ │
├───────────────┼─────────┼─────────────┼──────────┼───────┼───────┼────────┤
│
Детали литые. │Нормали- │
20ГЛ │ -
│ 294 │
490 │ │
│Рама
боковая │зация + │20ГТЛ, 20ГФЛ │ -
│ 314 │
490 │ │
│и
балка │высокий │
20ХГНТЛ │ -
│ 373 │
540 │ │
│надрессорная │отпуск │ │ │ │ │ │
│по
нормативным │ │ │ │ │ │ │
│документам │ │ │ │ │ │ │
├───────────────┼─────────┼─────────────┼──────────┼───────┼───────┼────────┤
│
Заготовки │Квадрат,
│ ОС │
До 350 │ -
│ 580 │
260 │
│осевые
для │круг │ │ │ - │ 620
│ 275 │
│подвижного │ │ │ │ -
│ 650 │
280 │
│состава │ │ │ │ │ │ │
│железных
дорог │ │ │ │ │ │ │
│колеи
1520 мм │ │ │ │ │ │ │
│по
ГОСТ 4728 │ │ │ │ │ │ │
├───────────────┼─────────┼─────────────┼──────────┼───────┼───────┼────────┤
│
Колесные │Колеса │
20Л, 25Л │ -
│ 245 │
440 │ -
│
│центры
литые │Нормали- │ │ │ 265
│ 470 │
- │
│для
подвижного │зация + │ │ │ │ │ │
│состава │отпуск │ │ │ │ │ │
│железных
дорог │ │ │ │ │ │ │
│колеи
1520 мм │ │ │ │ │ │ │
│по
ГОСТ 4491 │ │ │ │ │ │ │
├───────────────┼─────────┼─────────────┼──────────┼───────┼───────┼────────┤
│
Колеса │Колеса │
1 │ -
│ - │882 -
│ - │
│цельнокатаные │Закалка +│ │ │
│ 1078│ │
│по
ГОСТ 10791 │отпуск │
2 │ -
│ - │911 -
│ - │
│ │ │ │ │ │
1107│ │
├───────────────┼─────────┼─────────────┼──────────┼───────┼───────┼────────┤
│
Бандажи из │Закалка
+│ 2 │
- │ -
│930 - │ -
│
│углеродистой │отпуск │ │ │ │
1110│ │
│стали
для │ │ 3
│ - │
- │1000 - │ -
│
│подвижного │
│ │ │ │
1270│ │
│состава │ │ │ │ │ │ │
│железных
дорог │ │ │ │ │ │ │
│широкой
колеи │ │ │ │ │ │ │
│по
ГОСТ 398 │ │ │ │ │ │ │
├───────────────┼─────────┼─────────────┼──────────┼───────┼───────┼────────┤
│
Чугун с │ -
│ СЧ15 │
До 50 │ - │ 105
│ - │
│пластинчатым │ │ СЧ20
│ │ -
│ 140 │
- │
│графитом
для │ │ СЧ25
│ │ -
│ 180 │
- │
│отливок │ │ СЧ30
│ │ -
│ 220 │
- │
│по
ГОСТ 1412 │ │ СЧ35
│ │ -
│ 260 │
- │
├───────────────┼─────────┼─────────────┼──────────┼───────┼───────┼────────┤
│
Чугун с │ -
│ ВЧ35 │
- │ 220
│ 350 │
- │
│шаровидным │ │
ВЧ40 │ │ 250
│ 400 │
- │
│графитом
для │ │ ВЧ45
│ │ 310
│ 450 │
- │
│отливок │ │ ВЧ50
│ │ 320
│ 500 │
- │
│по
ГОСТ 7293 │ │ │ │ │ │ │
├───────────────┼─────────┼─────────────┼──────────┼───────┼───────┼────────┤
│
Отливки из │ -
│ КЧ30-6 │
- │ -
│ 294 │
- │
│ковкого
чугуна │ │ КЧ35-10
│ │ -
│ 333 │ -
│
│по
ГОСТ 1215 │ │ КЧ37-12
│ │ -
│ 362 │
- │
│ │ │ КЧ45-7
│ │ -
│ 441 │
- │
├───────────────┼─────────┼─────────────┼──────────┼───────┼───────┼────────┤
│
Колеса │Цемента- │ 20ХН3А,
│ - │
735 │ 931
│ - │
│зубчатые │ция │
20Х2Н4А, │ │ 735
│ 931 │
- │
│тяговых
передач│Упрочне- │45ХН, 30ХН3А │ │ 590
│ 830 │
- │
│по
ГОСТ Р 51175│ние ТВЧ │ │ │ 590
│ 830 │
- │
├───────────────┼─────────┼─────────────┼──────────┼───────┼───────┼────────┤
│
Заклепки │ -
│ Ст2, Ст3 │
2 - 24 │ -
│ 310 │
- │
│классов │ │ 10кп, 15кп │ │ - │
310 │ -
│
│точности
B и C │ │ 10, 15
│ │ -
│ 330 │
- │
│по
ГОСТ 10304 │ │ 09Г2
│ │ -
│ 380 │
- │
│ │ │ 12Х18Н9Т
│ │ -
│ 430 │
- │
│ │ │ АМг5П
│ │ -
│ 160 │
- │
├───────────────┼─────────┼─────────────┼──────────┼───────┼───────┼────────┤
│
Болты, винты, │Горячая
│ Класс 3.6 │
6 - 36 │ 190
│ 330 │
- │
│шпильки │штамповка│ 10, 10кп
│ │ │ │ │
│по
ГОСТ 1759.4
├─────────┼─────────────┼──────────┼───────┼───────┼────────┤
│ │Холодная │ Класс 5.8
│ - │
420 │ 520
│ - │
│ │штамповка│ 10, 10кп,
│ │ │ │ │
│ │ │ 20, 20кп
│ │ │ │ │
├───────────────┼─────────┼─────────────┼──────────┼───────┼───────┼────────┤
│
Прокат из
│Сортовой,│
295 │ До 20
│ 305 │
440 │ 200
│
│стали │полосо- │
09Г2 │ 20 - 32 │
295 │ 430
│ 200 │
│повышенной │вой, │ 09Г2, 09Г2С │ │ │ │ │
│прочности │фасонный │ │ │ │ │ │
│по
ГОСТ 19281
├─────────┼─────────────┼──────────┼───────┼───────┼────────┤
│ │Лист, │
09Г2 │ До 20
│ 305 │
440 │ 200
│
│ │гнутые │ 09Г2, 09Г2С │ 20 - 32 │
295 │ 430
│ 200 │
│ │профили │
│ │ │ │ │
│
├─────────┼─────────────┼──────────┼───────┼───────┼────────┤
│ │Сортовой,│ 325
│ До 20 │
325 │ 325
│ 210 │
│ │полосо- │
09Г2С │ До 32
│ 325 │
450 │ 210
│
│ │вой, │ 14Г2, 15ГФ │ │ │ │ │
│ │фасонный │ 15ХСНД
│ │ │ │ │
│
├─────────┼─────────────┼──────────┼───────┼───────┼────────┤
│ │Лист, │
09Г2С │ 10 - 20 │
325 │ 470
│ 210 │
│ │гнутые │ 14Г2, 15ГФ │
До 32 │ 325
│ 450 │
210 │
│ │профили │
10Г2С1 │ 20 - 60 │
325 │ 450
│ 210 │
│
├─────────┼─────────────┼──────────┼───────┼───────┼────────┤
│ │Сортовой,│ 345
│ До 10 │
│ │ │
│ │полосо- │
09Г2С, │ │ 345
│ 480 │
220 │
│ │вой, │
10Г2С1, │ │
345 │ │ │
│ │фасонный │ 10ХНДП
│ │ 345
│ │ │
│ │ │ 15ХСНД,
│ │ 345
│ 480 │
220 │
│ │ │ 15ГФ
│ 10 - 20 │ 345
│ 480 │
220 │
│
├─────────┼─────────────┼──────────┼───────┼───────┼────────┤
│ │Лист, │09Г2С, 17ГС, │ До 10
│ 345 │
490 │ 225
│
│ │гнутые │10Г2С1, 14ХГС│ │ │ │ │
│ │профили │
10ХНДП │ До 10
│ 345 │
470 │ 220
│
│ │ │ 15ГФ, 17Г1С │ 10 -
20 │ 345
│ 490 │
225 │
│ │ │ 15ХСНД
│ До 32 │
345 │ 490
│ 225 │
├───────────────┴─────────┴─────────────┴──────────┴───────┴───────┴────────┤
│ Примечание. Не указанные
характеристики материалов устанавливают по│
│соответствующим
техническим условиям и нормативным документам. │
└───────────────────────────────────────────────────────────────────────────┘
В.1. В обозначении
марки и класса прочности сталей по ГОСТ 19281 с повышенной стойкостью против
атмосферной коррозии, поставляемой по требованию заказчика с гарантированным
содержанием меди, добавляется буква Д (09Г2Д, 09Г2СД и т.д.). Механические
характеристики таких сталей идентичны исходным (09Г2, 09Г2С и т.д.).
В.2. Для
двухслойных сталей по ГОСТ 10885 механические свойства принимают по основному
слою.
В.3. Пределы
текучести материалов швов при дуговой сварке рекомендуют принимать равными для
электродов марок 342 и Э42А -
,
марок Э46, Э46А, Э50 и Э50А -
, где
- предел прочности материала шва.
В.4. Приведенные
минимальные значения
и
, даны
с односторонней вероятностью от 0,90 до 0,95.
В.5. В таблице В.1
приведены средние значения предела выносливости
для деформации изгиба по данным литературных
источников, справочным и экспериментальным данным.
В.6. Для деталей,
работающих при растяжении-сжатии (ответственные высоконагруженные болты,
подвески), рекомендуют предел выносливости корректировать по приближенной
зависимости
.
В.7. При отсутствии
данных о значениях пределов выносливости для ориентировочных расчетов
рекомендуется использовать следующие эмпирические зависимости:
- для
малоуглеродистых и низколегированных конструкционных сталей типа марок Ст3,
стали 20, 09Г2, 09Г2С, 10Г2БД, 15ХСНД, 15ГФ
,
(В.1)
где
- средний предел выносливости стандартного
круглого образца при изгибе, МПа;
-
минимальное временное сопротивление, МПа;
- для литой стали
типа марок 20Л, 20ГЛ, 20ГТЛ, 20ФЛ, 20ГФЛ
;
(В.2)
- для алюминиевых
сплавов типа марок АМг5, АМг6, 1915
.
(В.3)
Таблица В.2
Вероятностные
параметры механических
характеристик
стальных изделий
┌────────┬──────┬──────────────────┬────────────┬────────────┬────────────┐
│ Вид
│Марка │Диаметр, толщина, │ Предел
│Временное
│Относитель- │
│изделия
│стали │ мм │ текучести │сопротивле- │ное │
│ │ │ │сигма , МПа │ние
сигма , │удлинение │
│ │ │ │ т
│ в │дельта, % │
│ │ │ │ │МПа │ │
│ │ │
├─────┬──────┼─────┬──────┼─────┬──────┤
│ │ │ │Мате-│Сред-
│Мате-│Сред- │Мате-│Сред- │
│ │ │ │мати-│не- │мати-│не- │мати-│не- │
│ │
│
│чес- │квад- │чес- │квад- │чес-
│квад- │
│ │ │ │кое │рати- │кое │рати- │кое │рати- │
│ │ │ │ожи- │чес- │ожи- │чес- │ожи- │чес- │
│ │ │ │дание│кое │дание│кое │дание│кое │
│ │ │ │ │от- │
│от- │ │от- │
│ │ │ │ │кло- │
│кло- │ │кло- │
│ │ │ │ │не- │
│не- │ │не- │
│ │ │ │ │ние, S│ │ние, S│ │ние, S│
├────────┼──────┼──────────────────┼─────┼──────┼─────┼──────┼─────┼──────┤
│
Прокат,│ 09Г2 │От 10 до 20 включ.│ 350 │ 23
│ 480 │ 25 │ 28
│ 3,0 │
│лист │
│От 21 до 40 включ.│
340 │ 24 │ 470 │ 26
│ 29 │ 3,0 │
│ │09Г2С │От 10 до 20
включ.│ 370 │ 23 │ 540 │ 25
│ 29 │ 3,0 │
│ │ │От 21 до 40 включ.│ 368
│ 29 │ 530 │ 28
│ 29 │ 3,2 │
│ │10Г2С1│От 10 до 50
включ.│ 392 │ 25 │ 548 │ 30
│ 28 │ 3,1 │
│ │10ХСНД│От 10 до 40
включ.│ 456 │ 30 │ 595 │ 35
│ 25 │ 4,1 │
│ │15ХСНД│От 10 до 40
включ.│ 394 │ 26 │ 553 │ 30
│ 27 │ 3,1 │
│ │16Г2АФ│От 10 до 40
включ.│ 490 │ 35 │ 655 │ 38
│ 25 │ 2,8 │
│ │Ст3сп │От 10 до 20
включ.│ 290 │ 23 │ 435 │ 22
│ 30 │ 3,2 │
│ │ │От 21 до 40 включ.│ 270
│ 27 │ 430 │ 25
│ 25 │ 2,9 │
├────────┼──────┼──────────────────┼─────┼──────┼─────┼──────┼─────┼──────┤
│
Прокат,│ 45 │
Не более 80 │ 760
│ 50 │1050 │ 72 │ -
│ - │
│круг │
│ От 81 до 120 │ 640 │ 43
│ 930 │ 64 │
- │ -
│
│ │ 40Х │
Не более 120 │ 850 │ 43
│1020 │ 51 │
- │ -
│
│ │ │
От 121 до 200 │ 740 │ 37
│ 910 │ 46 │
- │ -
│
├────────┼──────┴──────────────────┼─────┼──────┼─────┼──────┼─────┼──────┤
│
Отливки│ 20ГЛ нормализация │ 295 │ 23,1 │ 495
│ 25,5 │ 26 │ 2,7 │
│ │ 20ГТЛ нормализация │ 348 │ 35,0 │ 541
│ 34,7 │ 27 │ 4,3 │
│
│ 20ГТЛ термоулучшение │ 478 │ 48,3 │ 639 │
45,1 │21,5 │ 2,6 │
│ │ 110Г13Л закалка │ 400 │ -
│ 800 │ - │25,0 │ -
│
└────────┴─────────────────────────┴─────┴──────┴─────┴──────┴─────┴──────┘
Приложение
Г
(рекомендуемое)
ИЗМЕРЕНИЕ
РАМНЫХ СИЛ ПОСРЕДСТВОМ МЕССДОЗ
На рисунке Г.1
приведена букса колесной пары тепловоза ТЭЗ (аналогичные буксы применяются на
тепловозах с челюстными тележками 2ТЭ10Л, М62, ТГМ4, ТГМ6, на автомотрисах).
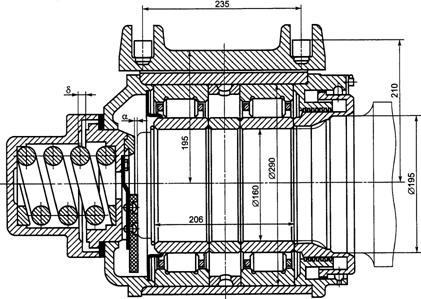
-
свободный разбег на сторону;
- упругий разбег
Рисунок
Г.1. Букса колесной пары тепловоза ТЭЗ
На рисунке Г.2
приведен опытный осевой упор буксы тепловоза ТЭЗ с установленной в нем
мессдозой.
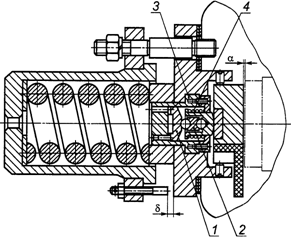
1 - мессдоза; 2 -
промежуточная деталь;
3 - втулка; 4 -
вспомогательная пружина
Рисунок Г.2.
Опытный осевой упор
буксы колесной пары
тепловоза ТЭЗ
Приложение
Д
(рекомендуемое)
СХЕМЫ
РАСПОЛОЖЕНИЯ И СОЕДИНЕНИЯ ТЕНЗОРЕЗИСТОРОВ
НА ТЕЛЕЖКАХ ДЛЯ
ИЗМЕРЕНИЯ РАМНЫХ СИЛ
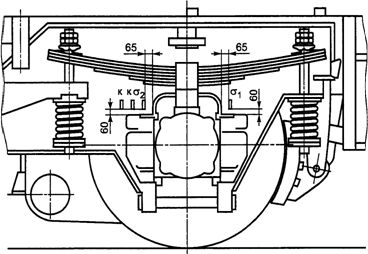
Рисунок Д.1. Схемы
расположения тензорезисторов
на челюстных
кронштейнах тележки
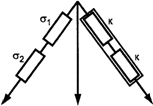
-
активные тензометрические датчики;
к - композиционные
тензометрические датчики
Рисунок Д.2. Схемы
соединения тензорезисторов
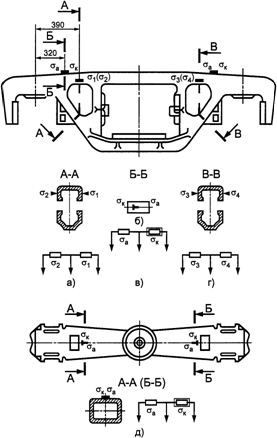
а) схема соединения
датчиков в сечении А - А;
б) схема наклейки
датчиков в сечении Б - Б; в) схема
соединения датчиков
в сечении Б - Б; г) схема
соединения датчиков
в сечении В - В; д) схема
соединения датчиков
в сечении А - А (Б - Б)
Рисунок Д.3. Схемы
расположения и соединения
тензодатчиков на
тележках моделей 18-100 (ЦНИИ-ХЗ)
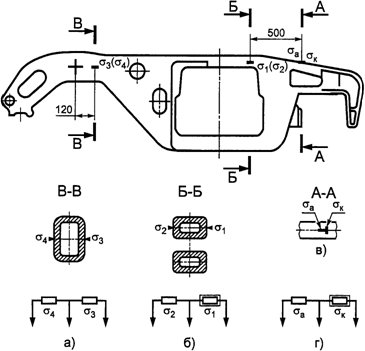
а) схема соединения
датчиков в сечении В - В;
б) схема соединения
датчиков в сечении Б - Б;
в) схема наклейки
датчиков в сечении А - А;
г) схема соединения
датчиков в сечении А - А
Рисунок Д.4. Схемы
расположения и соединения
тензодатчиков на
тележках моделей 18-102, 15-522
Приложение
Е
(рекомендуемое)
ПРИМЕР
ОЦЕНКИ ВЛИЯНИЯ УСИЛИЯ В ГИДРОДЕМПФЕРЕ
НА КОЭФФИЦИЕНТ
ДИНАМИКИ
Коэффициент
,
определяющий собой влияние усилия в гидродемпфере на коэффициент динамики
,
вычисляют по формуле
,
(Е.1)
где
- коэффициент сопротивления (параметр)
демпфера в размерности сила на единицу скорости поршня относительно корпуса
поршня (суммарный на СПС, или тележку, или колесную пару или буксу);
ж - жесткость
рессорного подвешивания (суммарная на СПС, тележку, колесную пару или буксу);
-
круговая частота собственных колебаний;
m - подрессоренная
масса (суммарная на СПС, тележку, колесную пару или буксу).
Примем для расчета
экипаж со следующими параметрами:
m = 7,13 кгс x
с2/см;
; ж =
583 кгс/см.
Коэффициент
демпфирования Д определяем по формуле
,
(Е.2)
где
- критическое значение коэффициента
сопротивления, при котором колебательный процесс прекращается.
Задаваясь рядом
значений Д, определяем соответствующие значения
, а
затем и коэффициента
.
Результаты расчетов приведены в таблице Е.1.
Таблица Е.1
Значения
коэффициента
в зависимости от коэффициента Д
Характеристики
|
Размерность
|
Значение характеристики
|
Д
|
-
|
0,1
|
0,2
|
0,3
|
0,4
|
0,5
|
0,6
|
0,7
|
бета
|
кгс
x с/см
|
13
|
26
|
39
|
52
|
64
|
77
|
90
|
гамма
|
-
|
1,02
|
1,08
|
1,16
|
1,28
|
1,4
|
1,55
|
1,71
|
По данным таблицы
построена графическая зависимость
,
приведенная на рисунке Е.1.
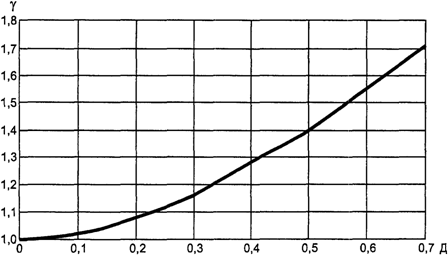
Рисунок Е.1.
Зависимость коэффициента,
характеризующего
влияние усилия в гидродемпфере
на
, от
коэффициента демпфирования Д
Приложение
Ж
(рекомендуемое)
ПРАВИЛА
РАСЧЕТА РЕССОРНОГО ПОДВЕШИВАНИЯ И ПОПЕРЕЧНЫХ СВЯЗЕЙ
Ж.1. СПС должен
быть снабжен системой рессорного подвешивания, обеспечивающей необходимые
ходовые качества и прочность конструкции на протяжении установленного срока
службы единицы СПС и эксплуатации ее со скоростями вплоть до конструкционной.
В качестве упругих
элементов рессорного подвешивания могут быть использованы винтовые пружины,
листовые рессоры, неметаллические (полиуретановые, резиновые) детали и их
комбинации. Применение только листовых рессор не рекомендуется.
Ж.2. Основными
параметрами рессорного подвешивания в вертикальной плоскости является общий
статический прогиб
, его
распределение по ступеням подвешивания и демпфирование.
Ж.3. Характеристики
рессорного подвешивания должны исключать возможность не предусмотренных
конструкцией соприкасаний и соударений кузова, тележек и колесных пар в
вертикальном и в горизонтальном направлениях.
Ж.4. Общий
расчетный статический прогиб от статической нагрузки при экипированном
состоянии СПС рекомендуется принимать в соответствии с таблицей Ж.1.
Таблица Ж.1
┌──────────────────────────────────┬──────────────────────────────────────┐
│ Конструкционная скорость, км/ч │Общий расчетный статический прогиб,
мм│
├──────────────────────────────────┼──────────────────────────────────────┤
│ 80 │ 80 - 90 <*> │
├──────────────────────────────────┼──────────────────────────────────────┤
│ 90 │ 90 - 100 │
├──────────────────────────────────┼──────────────────────────────────────┤
│ 100 │ 100 - 120 │
├──────────────────────────────────┼──────────────────────────────────────┤
│ 110 - 120 │ 120 - 140 │
├──────────────────────────────────┴──────────────────────────────────────┤
│
<*> Допускается применение
трехэлементных тележек. Для
увеличения│
│статического
прогиба рекомендуется в случаях, когда позволяет нагрузка на│
│рессорные
комплекты, изымать до 4-х пружин на тележке. Изъятие выполнять,│
│не
затрагивая подклиновых пружин и не
меняя центра упругости
каждой│
│группы
пружин.
│
└─────────────────────────────────────────────────────────────────────────┘
Статический прогиб
в центральной ступени рессорного подвешивания рекомендуется принимать как 70%
общего статического прогиба.
При применении во
второй ступени рессорного подвешивания неметаллических упругих элементов с
небольшим статическим прогибом основная часть статического прогиба может быть
сосредоточена в буксовой ступени.
Проектируя
рессорное подвешивание следует избегать совпадения собственных колебаний
надрессорного строения и изгибных колебаний главной рамы.
При значении
статического прогиба от 130 до 140 мм и при значениях менее 130 мм, но с близко
расположенными упругими элементами второй ступени к продольной вертикальной
плоскости симметрии необходимо проверять конструкцию на валкость надрессорного
строения по формуле:
,
(Ж.1)
где
- расчетный статический прогиб рессор;
-
поперечные расстояния соответственно между рессорами буксового и центрального
подвешивания;
-
высота центра тяжести кузова над осью колесной пары;
-
отношение прогиба буксового подвешивания
к общему прогибу
.
Необходимо также
проверять надрессорное строение на отсутствие выхода при колебаниях за
очертание соответствующего габарита подвижного состава.
Ж.5. При линейной
характеристике рессорного подвешивания статический прогиб вычисляют по формуле
,
(Ж.2)
где
- статическая нагрузка (брутто) на рессорный
комплект или отдельную рессору;
ж - соответствующая
жесткость пружины, рессоры.
Для рессорных
комплектов переменной жесткости жесткость ж берется как тангенс угла с осью
абсцисс касательной, проведенной в точке
характеристики комплекта (упругого элемента).
Ж.6. Соединение
кузова (главной рамы) с тележкой в поперечном горизонтальном направлении СПС с
конструкционной скоростью не более 90 км/ч может быть жестким. В этом случае
необходимо применить упругие осевые упоры для амортизации горизонтальных сил.
Упругим элементом такого упора может быть стальная цилиндрическая пружина или
деталь из резины (полиуретана). Жесткость упругого элемента должна быть от 2 до
4 кН/мм, предварительная затяжка - от 7,0 до 14,0 кН в зависимости от осевой
нагрузки, упругий ход - от 13 до 15 мм на сторону, свободный ход - от 1 до 2 мм
на сторону. Упругие упоры необходимо применять в необходимых случаях, также и
на двухосных СПС.
Как вариант
упругого осевого упора может быть применен упругий элемент, установленный в
кронштейне, укрепленном на раме тележки (главной раме двухосного экипажа)
против буксы.
Для СПС с конструкционной
скоростью 100 км/ч и более между кузовом и тележками необходимо применять
упругие поперечные связи, эквивалентные по жесткости маятниковой (люлечной)
подвеске длиной при конструкционной скорости, км/ч, не менее, мм:
500 мм - от 100 до
120 км/ч;
600 - 700 мм - от
120 до 140 км/ч.
Характеристика
упругой поперечной связи должна быть нелинейной с ходом на сторону от 40 до 45
мм. На первой половине хода (смещения) жесткость эквивалентна выбранной длине
маятника, на второй она должна возрастать с расчетом получения полной
возвращающей силы от 0,25 до 0,3 нагрузки, приходящейся на подвеску от кузова
(главной рамы)
.
Ж.7. Для создания
диссипативных сил в рессорном подвешивании необходимо применять демпферы
колебаний.
При одноступенчатом
рессорном подвешивании рекомендуется использовать демпферы сухого трения или
гидравлические демпферы. При двухступенчатом рессорном подвешивании в
центральной ступени необходимо применять гидравлические демпферы, а в буксовой
ступени, в зависимости от конструкционной скорости, значения его статического
прогиба, допускается их устанавливать или нет.
Ж.8. Демпфирование
оценивается значением коэффициента относительного демпфирования низкочастотных
форм колебаний Д.
Коэффициент
относительного демпфирования Д должен быть:
Ж.8.1. Для гашения
вертикальных колебаний подпрыгивания и галопирования кузова в рессорном
подвешивании со статическим прогибом более 80 мм при применении гидравлических
демпферов:
от 0,2 до 0,3.
При статическом
прогибе менее 80 мм принимать:
от 0,3 до 0,4.
При применении
рессорного подвешивания из листовых рессор сила трения в рессорном подвешивании
должна составлять от 4% до 6% от подрессоренной массы. Такая же сила трения
должна быть в рессорном подвешивании из пружин при установке параллельно им
фрикционного демпфера. То есть, коэффициент относительного трения
должен быть от 0,04 до 0,06.
Ж.8.2. Для
гашения колебаний относа кузова (главной рамы) относительно тележек гидравлическими
демпферами коэффициент относительного демпфирования Д должен быть:
от 0,3 до 0,4,
а фрикционными
демпферами - коэффициент относительного трения
должен быть:
от 0,06 до 0,07.
Ж.8.3. При гашении
колебаний относа кузова фрикционным трением [скользящие опоры кузова (главной
рамы)] необходим демпфирующий момент от 9% до 15% момента сил трения между
колесами и рельсами. При этом момент M сил трения между кузовом и тележкой
вычисляют по формуле
,
(Ж.3)
где
- статическая нагрузка на i-ю опору;
-
коэффициент трения в опоре;
-
расстояние от i-й опоры до шкворневого гнезда тележки.
Момент
сил трения колес тележки о рельсы вычисляют по
формуле
,
(Ж.4)
где
- статическая нагрузка колеса на рельс;
-
коэффициент трения колеса по рельсу;
-
расстояние от проекции центра тележки на плоскость, проходящую через опорные
поверхности головок рельсов до точки касания колеса с рельсом;
-
число колес в тележке.
Расстояние от
проекции центра тележки на плоскость, проходящую через опорные поверхности
головок рельсов до точки касания колеса с рельсом, вычисляют по формуле
,
(Ж.5)
где S = 1,58 м -
расстояние между кругами катания колесной пары;
-
расстояние до осевой линии i-й колесной пары вдоль тележки.
Ж.8.4. Для гашения
колебаний виляния гидравлическими демпферами значение коэффициента
относительного демпфирования Д такое же, как и при гашении колебаний относа по
Ж.8.2, для одновременного демпфирования колебаний относа и виляния могут быть
установлены демпферы в поперечном направлении, распределенные вдоль тележки на
необходимое расстояние. При гибкой поперечной связи кузова (главной рамы) с
тележкой, эквивалентной длине маятника от 500 до 600 мм, для гашения колебаний
относа фрикционным трением необходима сила трения от 5 до 7 кН, причем меньшие
значения следует принимать для легкого надрессорного строения.
Для гашения
горизонтальных колебаний гидравлическими демпферами применяют формулы (Ж.9 -
Ж.16), как и для вертикальных колебаний.
Ж.9. Характеристики
демпфирования уточняют при испытаниях СПС. Коэффициент относительного
демпфирования Д в вертикальной плоскости рекомендуется определять по формулам
,
(Ж.6)
где
- последовательно измеренные амплитуды
затухающих колебаний, расположенные по одну сторону нулевой линии.
При малом числе
периодов затухающих колебаний, наложения других видов колебаний этот способ
дает большую погрешность. В таких случаях коэффициент относительного
демпфирования Д определяют по упругим, диссипативным и массовым
характеристикам: как отношение работы диссипативных сил к работе упругих сил.
При одноступенчатом рессорном подвешивании с упруго-диссипативными элементами в
виде листовых рессор отношение работ вырождается в отношение сил по формуле
,
(Ж.7)
где T - сила трения
рессоры, равна половине ширины диаграммы рессоры по абсциссе
;
-
статическая нагрузка.
По этой же формуле
получают коэффициент относительного трения
при фрикционном демпфере, установленном
параллельно пружине.
При комбинированном
одноступенчатом рессорном подвешивании (на каждой буксе установлена листовая
рессора и последовательно ей пружины) коэффициент относительного трения
вычисляют по формуле
,
(Ж.8)
где
- коэффициент относительного трения листовой
рессоры;
-
статический прогиб рессоры;
-
статический прогиб пружины.
При одноступенчатом
рессорном подвешивании с параллельной установкой гидродемпферов коэффициент
относительного демпфирования вычисляют по формуле
,
(Ж.9)
где
- коэффициент сопротивления демпфера;
-
критический коэффициент сопротивления демпфера, вычисляют по формуле
,
(Ж.10)
где ж - вертикальная
жесткость рессорного подвешивания, приходящаяся на буксу;
m - подрессоренная
масса, приходящаяся на буксу;
-
собственная круговая частота
,
где g - ускорение
свободного падения, равно 9,81 м/с2;
-
статический прогиб.
При проектировании
экипажа коэффициент
вычисляют по формулам (Ж.9, Ж.10), задавшись
значением Д.
Фактический
коэффициент
демпфера определяют на специальном стенде.
Если диаграмма демпфера имеет вид эллипса, значение
вычисляют по формуле
,
(Ж.11)
где M - масштаб
записи силы сопротивления, определяемый градуировкой регистрационного механизма
стенда, кгс x с/см;
L - длина рабочей
диаграммы (в проекции на ось абсцисс), мм;
n - частота
колебаний поршня, Гц;
h - высота рабочей
диаграммы, прочерчиваемая писцом до установки демпфера, см.
В случаях, когда
форма диаграммы отличается от эллиптической,
вычисляют по формуле
,
(Ж.12)
где S - площадь
диаграммы, определяется планиметрированием.
Если гидравлические
демпферы установлены в обеих ступенях рессорного подвешивания параллельно
пружинам, то коэффициент относительного демпфирования Д определяют так же, как
и для одноступенчатого рессорного подвешивания по формуле (Ж.9), а коэффициент
вычисляют по формуле
,
(Ж.13)
где
- коэффициенты сопротивления гидродемпферов,
установленных в буксовой (первой) и центральной (второй) ступенях рессорного
подвешивания;
-
статический прогиб буксовой, центральной ступеней и суммарный соответственно.
Критический
коэффициент сопротивления вычисляют по формуле
,
(Ж.14)
где
- круговая частота собственных колебаний,
практически равная частоте при одноступенчатом рессорном подвешивании, с
прогибом, равным суммарному статическому прогибу двухступенчатого рессорного
подвешивания;
-
значения подрессоренной массы тележек и кузова;
-
коэффициент, учитывающий отношение жесткости буксовой ступени к жесткости
центральной ступени, вычисляют по формуле
,
(Ж.15)
где
- жесткость буксовой ступени;
-
жесткость центральной ступени.
При установке
демпферов в одной ступени соответствующее значение
,
равное нулю, формула (Ж.13) упрощается до одного члена.
Допускается
применение рессорного подвешивания, в котором листовая рессора и пружины расположены
последовательно, и параллельно им установлен гидравлический демпфер. При этом
принимают эквивалентное рессорное подвешивание, статический прогиб пружин в
котором равен сумме статических прогибов пружин и рессоры в реальном
подвешивании, и работа диссипативных элементов в обеих системах равна, причем
принимают характеристику гидродемпферов линейной. Коэффициент сопротивления
реального демпфера
вычисляют по формуле
,
(Ж.16)
где
- коэффициент сопротивления эквивалентного
демпфера, определяемого для заданного Д по формулам (Ж.9, Ж.10);
-
коэффициент динамики;
- нагрузка,
приходящаяся на листовую рессору;
-
статический прогиб рессоры.
Значение
коэффициента динамики
принимают таким же, как у аналогичной
экипажной части СПС с равной максимальной скоростью.
Коэффициент
вычисляют по формуле (Ж.10), коэффициент
относительного демпфирования Д вычисляют по формуле (Ж.9).
При установке в
рессорном подвешивании фрикционного демпфера с постоянной силой трения
коэффициент относительного трения вычисляют по формуле (Ж.7) как для листовой
рессоры. В случае переменной силы трения фрикционного демпфера коэффициент
относительного трения
и коэффициент относительного демпфирования Д
рессорного подвешивания с нелинейными упругими элементами определяют как
отношение работы диссипативных сил к работе упругих сил.
При применении в рессорном
подвешивании одновременно гидравлических и фрикционных демпферов приведенный
коэффициент Д следует принимать таким же, как указано выше.
При применении в
рессорном подвешивании эластомеров для определения работы диссипативных сил по
площади диаграммы нагружение-разгружение необходимо применить
планиметрирование.
Приложение
И
(рекомендуемое)
ОЦЕНКА
РАЗВЕСКИ СПС.
РАЗНОСТЬ НАГРУЗОК
ПО КОЛЕСАМ КОЛЕСНОЙ ПАРЫ
Оценку развески СПС
на тележках (моделей 18-100, 18-101, 18-102, 18-522, УВЗ-10м или аналогичных
им) с опорой кузова на тележку через центральную пяту, с жестким рессорным
подвешиванием, высоким коэффициентом относительного трения в демпферах
рессорного подвешивания, проводят по нормативным документам на смещение груза в
вагонах.
При определении
разности нагрузок по колесам колесной пары используют результаты взвешивания по
сторонам СПС. СПС рассматривают в виде "платформы" - главной рамы с
настилом, автосцепным и тормозным оборудованием и тележками, центр тяжести
которой не имеет поперечного смещения и "груза" - оборудования,
размещенного на раме, также учитывают груз, которым может загружаться СПС.
На рисунке И.1
приведена схема нагружения СПС при поперечном смещении центра тяжести
"груза".
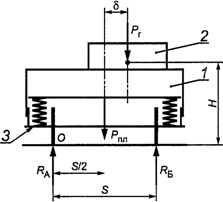
1 - главная рама
СПС ("платформа"); 2 - "груз";
3 - тележка; S -
расстояние между кругами катания
колесной пары, мм;
- сила тяжести "платформы";
- сила
тяжести оборудования;
- нагрузка
от колес на рельсы
разгруженной стороны СПС
по результатам
взвешивания;
- нагрузка от колес
на рельсы догруженной
стороны СПС по результатам
взвешивания; H -
высота общего центра тяжести СПС
с
"грузом" над уровнем головки рельса;
- искомое
поперечное смещение
центра тяжести
Рисунок И.1. Схема
нагружения СПС
Поперечное смещение
вычисляют по формуле:
,
(И.1)
где P - суммарная
сила тяжести "платформы" и "груза", вычисляют по формуле
.
(И.2)
Полученные смещения
"груза" сравнивают с допускаемыми, приведенными в таблице И.1.
Таблица И.1
Допускаемое
поперечное смещение общего центра
тяжести
"груза"
, мм,
на "платформе"
┌────────┬─────────────────────────────────────────────┬─────────┐
│
Масса │Высота общего центра
тяжести СПС с "грузом" H│ дельта, │
│груза,
т│ над уровнем головки рельса, м │
мм │
├────────┼─────────────────────────────────────────────┼─────────┤
│
До 10 │ До 1,2 │ 620
│
│ │ 1,5 │ 550
│
│ │ 2,0 │
410 │
├────────┼─────────────────────────────────────────────┼─────────┤
│До
30,0 │ До
1,2 │ 550
│
│ │ 1,5 │ 450
│
│ │ 2,0 │ 350
│
├────────┼─────────────────────────────────────────────┼─────────┤
│До
50,0 │ До
1,2 │ 350
│
│ │ 1,5 │ 280
│
│ │ 2,0 │ 250
│
│ │ 2,3 │ 200
│
├────────┼─────────────────────────────────────────────┼─────────┤
│До
55,0 │ До
1,5 │ 220
│
├────────┼─────────────────────────────────────────────┼─────────┤
│До
67,0 │ До
1,5 │ 180
│
│ │ 2,0 │ 140
│
│ │ 2,3 │ 120
│
├────────┼─────────────────────────────────────────────┼─────────┤
│
Свыше │ До 2,3 │ 100
│
│ 67,0
│
│ │
├────────┴─────────────────────────────────────────────┴─────────┤
│ Примечание.
Для промежуточных значений
массы "груза" и│
│высоты
H допускаемые смещения определяют линейной интерполяцией.│
└────────────────────────────────────────────────────────────────┘
Приложение
К
(обязательное)
ДОПУСКАЕМЫЕ НОРМЫ
ИСКРИВЛЕНИЯ ПРОКАТА
Таблица К.1
Допускаемые
нормы искривления проката
┌───────┬───────────────────┬─────────────────────────────────────────────┐
│ Вид
│ Конструктивный │
Допускаемое значение искривления проката │
│проката│ элемент │ в холодном состоянии │
│ │
├───────┬──────────────────┬──────────────────┤
│ │ │Относи-│ При правке │
При гибке │
│ │ │тельно
├─────────┬────────┼─────────┬────────┤
│ │ │оси │ Радиус │ Стрела │ Радиус │ Стрела │
│ │ │
│кривизны,│прогиба,│кривизны,│прогиба,│
│ │ │ │ r
│ f │
r │ f
│
└───────┴───────────────────┴───────┴─────────┴────────┴─────────┴────────┘
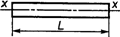
Лист x - x 50S
25S

───────────────────────────────────────────────────────────────────────────

Полоса x - x 100S
-
-
───────────────────────────────────────────────────────────────────────────

Уголок x - x 90b
45b

y - y 90b

───────────────────────────────────────────────────────────────────────────
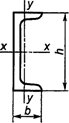
Швеллер x - x 50h
25h

y - y 90b
45b

───────────────────────────────────────────────────────────────────────────
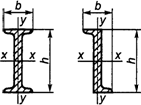
Двутавр x - x 50h
25h

или y - y 50b
25b

зетовый
профиль
───────────────────────────────────────────────────────────────────────────
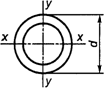
Труба x - x 60d
- 30d -
y - y
───────────────────────────────────────────────────────────────────────────
Таблица К.2
Допускаемые
нормы искривления проката перед
выполнением
заготовительных операций
┌────────┬───────────────────────┬─────────────────┬──────────────────────┐
│ Вид
│Конструктивный элемент │
Характер │ Допускаемое
значение │
│проката
│ │
деформации │ искривления │
│ │ │
├───────────────┬──────┤
│ │ │ │Функциональная
│ не │
│ │ │ │ зависимость
│более,│
│ │ │ │ │ мм
│
└────────┴───────────────────────┴─────────────────┴───────────────┴──────┘
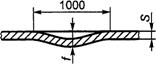
Лист, Отклонение от
полоса плоскостности на
1 м длины при
S <=
4 - 3,0
S >
4 - 1,5
───────────────────────────────────────────────────────────────────────────
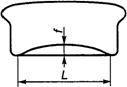
Полоса Отклонение от f <= 0,001L 5,0
прямолинейности
на ребро
───────────────────────────────────────────────────────────────────────────
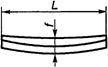
Уголок Отклонение от f <= 0,001L 5,0
прямолинейности
───────────────────────────────────────────────────────────────────────────
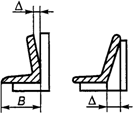
Уголок Отклонение от Дельта <= 0,01B -
перпендикулярнос-
ти полок
───────────────────────────────────────────────────────────────────────────
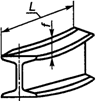
Двутавр, Отклонение от
швеллер плоскостности при
N <=
18 f <= 0,001L 4,0
N >=
20 f <= 0,001L 6,0
───────────────────────────────────────────────────────────────────────────
Приложение
Л
(обязательное)
ДОПУСКАЕМЫЕ
ПОКАЗАТЕЛИ РЕЗИНОВЫХ ДЕТАЛЕЙ
Таблица Л.1
Допускаемые
напряжения и относительные
деформации сжатия
резиновых деталей
┌────────────────────────┬──────────────────────────────────┬─────────────┐
│Наименование
показателя │ Значения допускаемых напряжений │
Значения │
│ │ сжатия, модулей сдвига и │ допускаемых │
│ │ упругости,
МН/м2, при твердости
│относительных│
│ │ по Шору │ деформаций │
│
├──────┬──────┬──────┬──────┬──────┤ сжатия
│
│
│30+/-3│40+/-3│50+/-4│60+/-4│70+/-4│ [эпсилон]
│
├────────────────────────┼──────┼──────┼──────┼──────┼──────┼─────────────┤
│
Модуль сдвига G │0,4 -
│0,5 - │0,6 - │0,9 - │1,3 - │ -
│
│ │ 0,5│
0,6│ 0,8│ 1,1│
1,5│ │
├────────────────────────┼──────┼──────┼──────┼──────┼──────┼─────────────┤
│
Модуль упругости E при│2,5 -
│3,0 - │4,0 - │6,0 - │8,5 - │ -
│
│ у │
3,0│ 4,0│ 5,5│
7,0│ 10,0│ │
│факторе
формы │ │ │ │ │ │ │
│Ф
<*> = 0,25 │
│ │ │ │ │ │
├────────────────────────┼──────┼──────┼──────┼──────┼──────┼─────────────┤
│
Допускаемое напряжение │
│ │ │ │ │0,15 - 0,20 │
│сжатия
при статических │ │ │ │
│ │ │
│нагрузках,
отнесенное │ │ │ │ │ │ │
│к
начальной площади │ │ │ │ │ │ │
│поперечного
сечения │ │ │ │ │ │ │
│недеформированного │ │ │ │
│ │ │
│резинового
элемента │ │ │ │ │ │ │
│[сигма]
при факторе │ │ │ │ │ │ │
│формы
Ф: │ │
│ │ │ │ │
│
0,25 │ 0,5 │ 0,6
│ 0,8 │ 1,0 │ 1,2
│ │
│
0,50 │ 0,7 │ 0,8
│ 1,0 │ 1,2 │ 1,5
│ │
│
0,75 │ 0,9 │ 1,0
│ 1,2 │ 1,5 │ 1,8 │ │
│
1,00 │ 1,1 │ 1,2
│ 1,5 │ 1,8 │ 2,2
│ │
│
1,25 │ 1,3 │ 1,5
│ 1,8 │ 2,2 │ 2,5
│ │
│
1,50 │ 1,5 │ 1,8
│ 2,0 │ 2,5 │ 2,8
│ │
├────────────────────────┼──────┼──────┼──────┼──────┼──────┼─────────────┤
│
Допускаемое напряжение │
│ │ │ │ │0,10 - 0,15 │
│сжатия
при статических │ │ │ │ │ │ │
│нагрузках
со случайными │ │ │ │ │ │ │
│и
эпизодическими │ │ │ │ │ │ │
│динамическими │ │ │ │ │ │ │
│нагрузками,
отнесенное │ │ │ │ │ │ │
│к
начальной площади │ │ │ │ │ │ │
│поперечного
сечения │ │ │ │ │ │ │
│недеформированного │ │ │ │ │ │ │
│резинового
элемента │ │ │ │ │ │ │
│[сигма]
при факторе │ │ │ │ │ │ │
│формы
Ф: │ │ │ │ │ │ │
│
0,25 │ 0,4 │ 0,5
│ 0,6 │ 0,8 │ 1,0
│ │
│
0,50 │ 0,5 │ 0,6
│ 0,8 │ 1,0 │ 1,2
│ │
│
0,75 │ 0,7 │ 0,8
│ 1,0 │ 1,2 │ 1,5
│ │
│
1,00 │ 0,9 │ 1,0
│ 1,2 │ 1,5 │ 1,8
│ │
│
1,25 │ 1,1 │ 1,2
│ 1,4 │ 1,8 │ 2,2
│ │
│
1,50 │ 1,3 │ 1,5
│ 1,6 │ 2,0 │ 2,5
│ │
├────────────────────────┼──────┼──────┼──────┼──────┼──────┼─────────────┤
│
Допускаемое нормальное │ │ │ │ │ │0,05 - 0,10 │
│напряжение
сжатия при │ │ │ │ │ │ │
│стационарных │ │ │ │ │ │ │
│динамических
нагрузках, │ │ │ │ │ │ │
│отнесенное
к начальной │ │ │ │ │ │ │
│площади
поперечного │ │ │ │ │ │ │
│сечения │ │ │ │ │ │ │
│недеформированного │ │ │ │ │ │ │
│резинового
элемента │ │ │ │ │ │ │
│[сигма]
при факторе │ │ │ │ │ │ │
│формы
Ф: │ │
│ │ │ │ │
│
0,25 │ 0,3 │ 0,4
│ 0,45 │ 0,6 │
0,75 │ │
│
0,50 │ 0,4 │ 0,45 │ 0,6 │ 0,75 │ 0,9 │ │
│
0,75 │ 0,55
│ 0,6 │ 0,75 │
0,9 │ 1,1 │
│
│
1,00 │ 0,7 │ 0,75 │ 0,9 │ 1,1
│ 1,3 │ │
│
1,25 │ 0,8 │ 0,9
│ 1,0 │ 1,3 │ 1,6
│ │
│
1,50 │ 1,0 │ 1,1
│ 1,2 │ 1,5 │ 2,0
│ │
├────────────────────────┴──────┴──────┴──────┴──────┴──────┴─────────────┤
│
<*> Фактором формы является отношение площади нагружения
к площади│
│свободной
(боковой) поверхности детали. │
└─────────────────────────────────────────────────────────────────────────┘
Таблица Л.2
Допускаемые
напряжения и относительные
деформации сдвига
резиновых деталей
Наименование
показателя
|
Значения допускаемых касательных
напряжений и модуля сдвига, МН/м2,
при твердости по Шору
|
Значения
допускаемых
относительных
деформаций
сдвига
[гамма]
|
40
+/- 3
|
50
+/- 4
|
60
+/- 4
|
70
+/- 4
|
Модуль сдвига G
|
0,4
-
0,5
|
0,6
-
0,7
|
0,9
-
1,1
|
1,3
-
1,5
|
-
|
Допускаемое
касательное напряжение
сдвига при статических
нагрузках [тау]
|
0,2
|
0,2
|
0,4
|
0,5
|
0,35 - 0,5
|
Допускаемое
касательное напряжение
сдвига при статических
нагрузках со случайными
и эпизодическими
кратковременными
динамическими
нагрузками [тау]
|
0,15
|
0,2
|
0,25
|
0,3
|
0,2 - 0,3
|
Допускаемое
касательное напряжение
сдвига при стационарных
динамических нагрузках
[тау]
|
0,1
|
0,15
|
0,18
|
0,22
|
0,1 - 0,15
|