Утвержден и введен в
действие
Приказом Росстандарта
от 14 сентября 2011
г. N 296-ст
НАЦИОНАЛЬНЫЙ СТАНДАРТ РОССИЙСКОЙ ФЕДЕРАЦИИ
ДОРОГИ АВТОМОБИЛЬНЫЕ ОБЩЕГО ПОЛЬЗОВАНИЯ
АСФАЛЬТОБЕТОН ДОРОЖНЫЙ ЛИТОЙ ГОРЯЧИЙ
МЕТОДЫ ИСПЫТАНИЙ
Automobile
roads of general use. Hot road mastic asphalt.
Test methods
EN 12697-20:2003
Bituminous
mixtures. Test methods for hot mix asphalt.
Indentation using cube or
Marshal specimens
(NEQ)
EN 13108-20:2006
Bituminous
mixtures. Material specifications. Type testing
(NEQ)
ГОСТ Р 54400-2011
Группа Ж18
ОКС 93.080.20;
ОКП 57 1841
Дата введения
1 мая 2012 года
Предисловие
Цели и принципы
стандартизации в Российской Федерации установлены Федеральным законом от 27
декабря 2002 г. N 184-ФЗ "О техническом регулировании", а правила
применения национальных стандартов Российской Федерации - ГОСТ Р 1.0-2004 "Стандартизация в Российской Федерации.
Основные положения".
Сведения о
стандарте
1. Разработан
Автономной некоммерческой организацией "Научно-исследовательский институт
транспортно-строительного комплекса" (АНО "НИИ ТСК") и Открытым
акционерным обществом "Асфальтобетонный завод N 1", г.
Санкт-Петербург (ОАО "АБЗ-1", г. Санкт-Петербург).
2. Внесен Техническим комитетом по стандартизации ТК 418
"Дорожное хозяйство".
3. Утвержден и
введен в действие Приказом Федерального агентства по техническому регулированию
и метрологии от 14 сентября 2011 г. N 296-ст.
4. В настоящем
стандарте учтены основные нормативные положения следующих европейских
региональных стандартов:
- ЕН 12697-20:2003
"Смеси битумные. Методы испытания горячей асфальтовой смеси. Часть 20. Вдавливание с использованием кубов или образцов Маршалла" (EN
12697-20:2003 "Bituminous mixtures.
Test methods for
hot mix asphalt. Indentation using cube or Marshall specimens",
NEQ);
- ЕН 13108-20:2006
"Смеси битумные. Требования к материалам. Методы
испытания в зависимости от типа" (EN 13108-20:2006 "Bituminous mixtures. Material specifications. Type testing", NEQ).
5. Введен впервые.
Информация об
изменениях к настоящему стандарту публикуется в ежегодно издаваемом
информационном указателе "Национальные стандарты", а текст изменений
и поправок - в ежемесячно издаваемых информационных указателях
"Национальные стандарты". В случае пересмотра (замены) или отмены
настоящего стандарта соответствующее уведомление будет опубликовано в
ежемесячно издаваемом информационном указателе "Национальные стандарты".
Соответствующая информация, уведомление и тексты размещаются также в
информационной системе общего пользования - на официальном сайте Федерального
агентства по техническому регулированию и метрологии в сети Интернет.
1. Область
применения
Настоящий стандарт
распространяется на асфальтобетон дорожный литой горячий и на смеси
асфальтобетонные дорожные литые горячие (далее - смеси литые), применяемые для
устройства покрытий на автомобильных дорогах общего пользования, мостовых
сооружениях, тоннелях, а также для производства ямочного ремонта, и
устанавливает методы их испытаний.
2.
Нормативные ссылки
В настоящем
стандарте использованы нормативные ссылки на следующие стандарты:
ГОСТ Р ИСО 5725-1-2002. Точность (правильность и прецизионность) методов и результатов измерений. Часть 1.
Основные положения и определения
ГОСТ Р 53228-2008. Весы неавтоматического действия. Часть 1.
Метрологические и технические требования. Испытания
ГОСТ Р 54401-2011. Дороги автомобильные общего пользования.
Асфальтобетон дорожный литой горячий. Технические требования
ГОСТ 12801-98.
Материалы на основе органических вяжущих для дорожного
и аэродромного строительства. Методы испытаний.
Примечание. При пользовании настоящим стандартом целесообразно проверить
действие ссылочных стандартов в информационной системе общего пользования - на
официальном сайте Федерального агентства по техническому регулированию и
метрологии в сети Интернет или по ежегодно издаваемому информационному
указателю "Национальные стандарты", который опубликован по состоянию
на 1 января текущего года, и по соответствующим ежемесячно издаваемым
информационным указателям, опубликованным в текущем году. Если ссылочный
стандарт заменен (изменен), то при пользовании настоящим стандартом следует
руководствоваться заменяющим (измененным) стандартом. Если ссылочный стандарт
отменен без замены, то положение, в котором дана ссылка на него, применяется в
части, не затрагивающей эту ссылку.
3. Термины
и определения
В настоящем
стандарте применены термины по ГОСТ Р 54401, ГОСТ Р
ИСО 5725-1, а также следующие термины с соответствующими определениями.
3.1. Керн: образец
асфальтобетона, извлеченный из слоя покрытия посредством специального вида
бурения, применяемый для определения его физико-механических характеристик.
3.2. Объединенная
проба: проба, образованная путем тщательного смешивания всех точечных проб
смеси литой или кернов, предварительно разогретых до вязкотекучего
состояния.
3.3.
Производственный замес (порция): асфальтобетонная смесь литая определенного
количества и состава, надлежащим образом перемешанная за определенное время при
однократном дозировании исходных материалов.
3.4. Результативный
состав: состав определенной асфальтобетонной смеси с указанием компонентов и
усредненных результатов исследований смеси с точки зрения гранулометрического
состава и содержания растворимых вяжущих веществ, полученный в результате
текущего производственного контроля.
3.5. Стандартное
отклонение: показатель рассеивания значений случайной величины относительно ее
математического ожидания.
3.6. Точечная
проба: масса асфальтобетонной смеси литой, равная 750 - 1000 г, отобранная из
партии смеси за один прием.
3.7. Усталостная
долговечность: свойство материала не разрушаться с течением времени под
действием изменяющихся циклических нагрузок.
3.8. Штыкование: перераспределение (уплотнение) смеси литой в
форме с целью удаления вовлеченного воздуха путем вертикального погружения в
смесь металлического шпателя или стального штыря.
4. Общие
положения
4.1. Образцы
взвешивают на лабораторных весах общего назначения 4-го класса точности по ГОСТ
Р 53228 с допускаемой погрешностью взвешивания не
более 0,1% массы. Массу образцов определяют в граммах с точностью до 0,01 г.
4.2. Результаты
испытаний приводят с точностью до второго разряда.
4.3. Воздух в
помещении, в котором проводят испытания, должен быть (20 +/- 5) °C.
5. Отбор
проб
5.1. Отбор проб при
приготовлении смеси литой в производственных смесительных установках
осуществляют при ее выгрузке из смесителя или при выгрузке смеси из стационарного кохера в
мобильный кохер. Для испытаний необходимо отобрать
объединенную пробу, составленную из трех-четырех тщательно перемешанных между
собой точечных проб.
5.2. Отбор точечных проб смеси литой при ее выгрузке из смесителя
производят (в зависимости от типа асфальтовой смесительной установки и ее
производительности) из ее разных производственных замесов (порций) либо с
минимальным интервалом времени 5 мин. Выходящий из смесителя материал должен
быть однородным, зерна минеральной части смеси должны быть полностью покрыты
вяжущим веществом, без признаков слипания мелких частиц в комки.
5.3. При отборе
точечных проб в процессе выгрузки смеси литой из специального
бункера-накопителя в мобильный кохер
пробы отбирают с минимальным интервалом времени 1 мин.
5.4. При проведении
потребителем контрольных испытаний отбор проб производят непосредственно из кохеров (или их отгрузочных устройств), при этом из одного
или нескольких кохеров (в зависимости от объема
контролируемой партии смеси) отбирают три-четыре точечные пробы для одной
объединенной пробы. Допускается производить отбор проб с дорожного полотна
непосредственно после выгрузки смеси литой из транспортных средств до начала ее
застывания и формирования поверхностного шероховатого слоя методом втапливания "по горячему".
5.5. Масса
объединенной пробы смеси должна быть не менее 3 кг.
5.6. Для отбора
проб из слоя сформировавшегося дорожного покрытия выбирают участок на
расстоянии не менее 0,5 м от края покрытия или оси дороги. При этом с площади
покрытия, равной 2000 м2, отбирают одну пробу, масса
которой должна составлять не менее 3 кг. Допускается извлекать несколько кернов
с указанной выше площади для формирования объединенной пробы.
6.
Приготовление смеси литой в лаборатории
6.1. При
приготовлении смесей литых в лаборатории минеральную часть (щебень, песок,
минеральный порошок) предварительно высушивают, а вяжущее
разогревают до вязкотекучего состояния.
6.1.1. Минеральные
материалы в количестве, заданном по составу, отвешивают в металлическую
емкость, перемешивают, нагревают до температуры 200 °C и добавляют требуемое
количество вяжущего, предварительно нагретого в
отдельной емкости до температуры 160 °C. Полученную смесь
литую в условиях постоянного перемешивания доводят до температуры не выше 215
°C (в случае применения в смеси полимерно-битумного вяжущего) и до температуры
не выше 230 °C (в случае применения в смеси вязкого битума).
6.1.2. В процессе
подготовки образцов смеси литой не допускают перегрева материалов. Длительность осуществления лабораторного замеса смеси литой,
определяемого с момента начала перемешивания компонентов с вяжущим до ее полной
гомогенизации, не должна превышать 5 - 10 мин. Смесь должна быть однородной, с
равномерным покрытием минеральной части вяжущим, без признаков слипания мелких
частиц в комки и перегрева.
7.
Контрольные образцы смеси литой и асфальтобетона
7.1.
Физико-механические свойства асфальтобетона на основе смеси литой определяют на
образцах-кубах, изготовленных в соответствии с разделом 8. Допускают проведение
испытаний на образцах цилиндрической формы при определении
значений показателя предела прочности на растяжение при расколе при температуре
0 °C, а также на кернах, извлеченных из покрытия, при определении значений
показателей водонасыщения.
7.2. Формы для
изготовления образцов-кубов должны быть стальные и могут иметь любую
конструкцию, обеспечивающую размер образца-куба 7,07 x 7,07 x 7,07 см.
7.3. Правила
подготовки образцов при проведении факультативных испытаний изложены в Приложении
А.
8. Изготовление образцов
8.1. Образцы-кубы
для определения физико-механических свойств асфальтобетона литого изготовляют
путем послойного заполнения форм смесью литой, приготовленной в лабораторных
условиях из набора ее исходных ингредиентов, а также из проб смеси литой,
отобранных на смесительной установке или на участке производства работ (в том
числе разогретых кернов). Перед заливкой в форму смесь нагревают на песчаной
бане или в термостате до температуры не менее 190 °C, но не выше 215 °C (в
случае применения в смеси полимерно-битумного вяжущего) и не выше 230 °C (в
случае применения в смеси в качестве вяжущего вязкого битума). Из отобранной
объединенной пробы готовят не менее двух образцов-кубов.
При подготовке
образцов-кубов из объединенной пробы смеси, полученной из разогретых кернов
верхнего слоя покрытия, щебень шероховатого слоя с поверхности кернов следует
предварительно удалить.
8.2. Масса смеси,
необходимой для изготовления одного образца-куба, находится в пределах от 750
до 950 г.
8.3. Внутреннюю
очищенную поверхность формы рекомендуется обработать силиконовой смазкой,
глицерином либо порошковой известью. Заполнение формы производят послойно в три
приема. Каждый слой тщательно штыкуют металлическим шпателем
с шириной лезвия не более 70 мм или стальным штырем диаметром от 6 до 10 мм на
глубину 10 - 20 мм 10 - 15 раз равномерно, по всей площади, а затем
утрамбовывают деревянной трамбовкой квадратного сечения с размером грани от 3
до 6 см 7 - 10 раз. Трамбование осуществляют
равномерно по всей плоскости с незначительным усилием, исключающим выдавливание
смеси из формы. Поверхность образца-куба выравнивают по верхнему краю формы и
заглаживают горячим металлическим шпателем, имеющим температуру от 100 °C до
230 °C.
8.4. Изготовленные
образцы-кубы выдерживают в форме до достижения ими комнатной температуры в
условиях их естественного охлаждения. К испытаниям приступают после достижения
образцами-кубами комнатной температуры.
9.
Определение физико-механических свойств
9.1. Определение
пористости минерального остова
9.1.1. Сущность
метода заключается в определении объема пор, имеющихся в минеральной части
(остове) смеси литой или асфальтобетона на ее основе.
9.1.2. Определение
пористости минерального остова выполняют в соответствии с ГОСТ 12801 (раздел
11). Определение средней плотности литого асфальтобетона осуществляется на
образцах-кубах.
9.2. Определение
остаточной пористости
9.2.1. Сущность
метода заключается в определении объема пор, имеющихся в смеси литой или
асфальтобетоне на ее основе.
9.2.2. Определение
остаточной пористости выполняют в соответствии с ГОСТ 12801 (раздел 12).
9.3. Определение
водонасыщения
9.3.1. Сущность
метода заключается в определении количества воды, поглощенной образцом-кубом
или образцом вырубки (керном) при заданном режиме насыщения.
9.3.2. Определение
водонасыщения осуществляется в соответствии с ГОСТ 12801 (раздел 13) на
образцах-кубах или образцах-вырубках (кернах).
9.4. Определение
глубины вдавливания штампа
9.4.1. Сущность
метода заключается в определении деформации образца под действием приложенной
постоянной вертикальной нагрузки, передаваемой на образец через шток (штамп) с
плоским основанием определенной площади, за фиксированное время.
9.4.2. Для
выполнения испытаний используют следующее оборудование:
- прибор для
определения глубины вдавливания штампа (рисунок 1) с водяной баней объемом
минимум 7,5 л, регулирующими устройствами температуры (с отклонениями +/- 0,5
°C) и циркуляции воды;
- зажимная форма
(рисунок 2) для установки образца-куба;
- штамп
цилиндрической формы (рисунок 3) круглого сечения площадью 500 мм2;
- контрольный
термометр 1-го класса точности с ценой деления 0,1 °C.
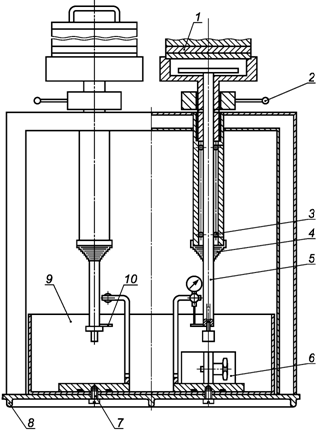
1 -
гиря-разновеска; 2 - подъемный механизм; 3 - шариковые
втулки; 4 -
защитный кожух; 5 - шток; 6 - зажимная форма;
7 - крепежный винт;
8 - ребро жесткости; 9 - водная баня;
10 - контактная
пластина индикатора часового типа
Рисунок 1.
Прибор для испытания глубины вдавливания штампа
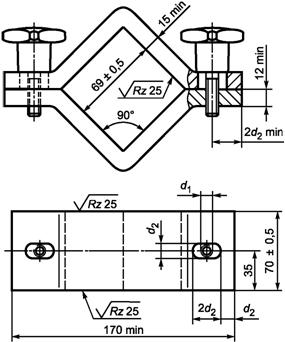
- диаметр резьбы;
- диаметр направляющей прорези
Рисунок 2.
Зажимная форма для установки кубической пробы

Рисунок 3.
Испытательный штамп площадью основания 500 мм2
9.4.3. Проведение
испытания
Образец-куб
извлекают из формы для изготовления и вставляют в зажимную форму испытуемой
плоскостью вверх. Плоскость, подвергаемая испытанию на вдавливание, должна быть
одной из четырех граней пробы, сформированных боковыми стенками формы в
процессе ее изготовления. Испытание проводят только на пробе, зафиксированной в
зажимной форме. Усилие, прикладываемое при обжатии образца-куба в форме, должно
обеспечивать его надежную фиксацию в зажимной форме, исключая смятие и иные
деформации. При этом обязательного полного смыкания фланцев противоположных
стяжных скоб не требуется. Опорная плоскость пробы, зафиксированной в зажимной
форме, должна выступать на величину не более 1 мм от опорной плоскости формы
или совпадать с ней для обеспечения полного соприкосновения кубической пробы с
укрепленным основанием водяной бани в процессе испытания. Подготовленный
указанным способом образец погружают вместе с зажимной формой в водяную баню
прибора (емкость для термостатирования), где его
выдерживают при заданной температуре (40 +/- 1) °C в течение не менее 60 мин.
Штамп устанавливают
на верхнюю плоскость пробы как можно ближе к ее середине так, чтобы расстояние
от боковой поверхности штампа до любой из зажимаемых боковых граней пробы было
не менее 10 мм. Пробу предварительно подвергают воздействию нагрузки в (2,5 +/-
0,1) кг в течение (10 +/- 1) мин. Затем производят обнуление индикатора глубины
вдавливания штампа и к пробе прикладывают рабочую нагрузку, равную (52,5 +/-
0,1) кг. Спустя следующие (30 +/- 1) мин и (60 +/- 1) мин с момента приложения
этой нагрузки со шкалы индикатора снимаются показания глубины вдавливания
штампа с точностью до 0,01 мм.
Каждый образец
должен быть подвергнут не более чем одному испытанию. Испытывают не менее двух
образцов-кубов. Допускают использовать для проведения данного теста
образцы-кубы, испытанные ранее на водонасыщение.
За конечный
результат испытания принимают среднее арифметическое значение результатов измерения глубины вдавливания штампа в течение
первых 30 мин с момента приложения рабочей нагрузки, выраженное в миллиметрах и
округленное до 0,01 мм. Подобным способом подсчитывают среднее арифметическое
результатов измерения глубины вдавливания штампа за период последующих 30 мин
приложения к нему рабочей нагрузки. Разница между числовыми значениями средних
арифметических глубины вдавливания штампа по окончании первых и последующих 30
мин определяет числовое значение увеличения показателя вдавливания штампа в
течение последующих 30 мин (см. ГОСТ Р 54401, таблица
4). Расхождение между результатами двух любых измерений не должно превышать 20%
среднего арифметического значения, при определении которого использовались
данные результаты измерения, или 0,2 мм, если среднее арифметическое значение
оказывается менее 1 мм.
Показатели
сходимости результатов испытаний, полученных в условиях повторяемости (сходимости)
и воспроизводимости в соответствии с ГОСТ Р ИСО 5725-1 для одного результата испытаний как среднего
арифметического двух результатов измерений глубины вдавливания штампа
(испытания, проведенного с использованием минимально допустимого количества образцов,
равного двум), приведены в таблице 1.
Таблица 1
┌────────────────────────────────────────┬────────────────────────────────┐
│ Показатели сходимости │ Глубина вдавливания штампа │
│ результатов испытаний ├───────┬─────────────┬──────────┤
│
│до 1 мм│от 1 до 6 мм,│свыше 6 мм│
│
│ │ %
числовых │ │
│
│ │ значений
│ │
│
│ │ результатов
│ │
├────────────────────────────────────────┼───────┼─────────────┼──────────┤
│
Стандартное отклонение повторяемости
│ 0,1 │
10 │ 0,6
│
│ r │ │ │ │
│(сходимости)
сигма │ │ │ │
├────────────────────────────────────────┼───────┼─────────────┼──────────┤
│
Предел повторяемости (сходимости)
│ 0,3 │
28 │
1,7 │
│ r │ │ │ │
│r
= 2,77 сигма
│ │ │ │
├────────────────────────────────────────┼───────┼─────────────┼──────────┤
│
Стандартное отклонение
│ 0,2 │
20 │ 1,2
│
│ R │ │ │ │
│воспроизводимости сигма │ │ │ │
├────────────────────────────────────────┼───────┼─────────────┼──────────┤
│
Предел воспроизводимости │ 0,6
│ 55 │
3,3 │
│ R │ │ │ │
│R
= 2,77 сигма
│ │ │ │
└────────────────────────────────────────┴───────┴─────────────┴──────────┘
9.4.4. Определение
глубины вдавливания штампа асфальтобетона литого, полученного из кернов,
производят на образцах кубической формы, приготовленных в соответствии с
разделом 8.
9.5. Определение
результативного состава смеси литой
9.5.1. Сущность
метода заключается в определении содержания вяжущего и зернового состава
минеральной части смеси литой.
9.5.2. Определение
результативного состава смеси литой выполняют в соответствии с ГОСТ 12801
(раздел 23). В случае необходимости использования при подборе зерновых составов
квадратных сит для определения зернового состава смеси литой необходимо
применять комплект таких базовых сит в соответствии с ГОСТ Р
54401.
При определении
результативного состава смеси, полученной из разогретых кернов верхнего слоя
покрытия, щебень шероховатого слоя с поверхности кернов следует предварительно
удалить.
9.5.3. При
использовании метода экстрагирования вяжущего допускают использование приборов-экстракторов,
работающих по принципу центрифужной экстракции и
функционирующих в автоматическом режиме.
9.6. Определение
однородности литых асфальтобетонов
9.6.1. Сущность
метода заключается в статистической обработке значений показателей свойств
литых асфальтобетонов в выборке из лабораторного журнала и оценке их
однородности по коэффициенту вариации показателя глубины
вдавливания штампа при температуре 40 °C за 30 мин.
9.6.2. Определение
значения показателя однородности осуществляют в соответствии с ГОСТ 12801
(раздел 27).
9.7. При
проектировании составов смесей литых проводят факультативные испытания,
указанные в Приложении А. Испытания проводят с целью определения соответствия
получаемых результатов требованиям ГОСТ Р 54401, а
также дополнительным требованиям к физико-механическим свойствам литых
асфальтобетонов, предъявляемым потребителем.
Приложение А
(рекомендуемое)
ФАКУЛЬТАТИВНЫЕ
ИСПЫТАНИЯ СМЕСЕЙ ЛИТЫХ
А.1. При
проектировании составов смесей литых проводят следующие факультативные
испытания:
А.1.1. Определение
реологических характеристик и показателей деформативности
Испытания выполняют
в соответствии с ГОСТ 12801 (раздел 17). Определяют показатели: предел
прочности на растяжение при изгибе, предельная относительная деформация
растяжения при изгибе, модуль деформации. Испытания проводят в диапазоне
температур образцов от минус 50 °C до 50 °C.
Рекомендуемые значения тестовых температур: 20 °C, 0 °C, минус 20 °C.
Подготовку
образцов-балок осуществляют в соответствии с А.2. Допускают проведение
испытаний с использованием изъятых из асфальтобетонного покрытия образцов,
предварительно подготовленных и удовлетворяющих требованиям к геометрическим
параметрам образцов-балок.
А.1.2. Определение
параметров усталостной долговечности
В данном виде
испытаний производят тестирование литых асфальтобетонов на специально
сконструированных приборах при изгибе образцов-балок в четырех точках по [1],
[2]. Нагружение образцов литого асфальтобетона
производят при разных амплитудах, в диапазоне частот от 0,5 до 60,0 Гц
прибором, способным обеспечить приложение испытательной нагрузки на образец,
изменяющейся по синусоидальному закону. В ходе испытания определяют значения
комплексного модуля упругости литого асфальтобетона, циклической долговечности и
плотности рассеянной энергии. Процесс испытания может происходить в двух
режимах управления: деформацией и нагрузкой.
Подготовку
образцов-балок осуществляют в соответствии с А.2. Допускают проведение
испытаний с использованием изъятых из асфальтобетонного покрытия образцов,
предварительно подготовленных и удовлетворяющих требованиям к геометрическим
параметрам образцов-балок.
А.1.3. Определение
предела прочности на растяжение при расколе при температуре 0 °C
Испытание выполняют
в соответствии с ГОСТ 12801 (раздел 16).
Подготовку образцов
осуществляют путем формования смеси литой в стандартные металлические
цилиндрические формы диаметром 71,4 мм по ГОСТ 12801 (подраздел 5.1). Процедура
подготовки смеси и формовки образцов должна соответствовать требованиям раздела
8. Геометрические размеры образцов должны соответствовать требованиям ГОСТ
12801 (раздел 6, таблица 5).
А.2.
Подготовка образцов-балок (призм) для факультативных испытаний
Образцы
изготавливают в стальных формах любой конструкции, в соответствии с выбранной
методикой испытаний, обеспечивающей стабильность размеров образцов-балок.
Внутреннюю очищенную поверхность формы обрабатывают силиконовой смазкой,
глицерином или порошковой известью. Максимально допустимая температура смеси
литой в момент заполнения форм должна соответствовать значениям температур,
указанным в ГОСТ Р 54401 (таблица 3).
Максимальный размер
щебня, применяемого в тестируемых литых асфальтобетонах, не должен превышать
0,5 толщины формуемого образца-балки.
Заполнение формы
производят послойно в два или три приема. Каждый слой тщательно штыкуют и
утрамбовывают деревянной трамбовкой квадратного сечения равномерно по всей
поверхности с незначительным усилием, исключающим выдавливание смеси из формы.
Поверхность образца выравнивают вровень с краями формы и заглаживают горячим
металлическим шпателем, имеющим температуру от 100 °C до 230 °C. Изготовленный
образец выдерживают в форме до достижения им комнатной температуры в условиях
естественного охлаждения. К испытанию рекомендуют приступать не ранее чем через
12 ч, в течение которых образцы-балки хранятся при комнатной температуре.
БИБЛИОГРАФИЯ
[1] ЕН 13108-20 Смеси битумные. Технические условия на материал.
Часть 20.
Методы испытания в зависимости от типа
[2] ЕН 12697-24 Смеси битумные. Методы испытаний горячих
асфальтовых
смесей. Часть 24. Сопротивляемость усталостным явлениям.