Утвержден
Приказом
Министерства
регионального
развития
Российской
Федерации
от 29 декабря 2011
г. N 635
СВОД ПРАВИЛ
МОСТЫ И ТРУБЫ
АКТУАЛИЗИРОВАННАЯ РЕДАКЦИЯ СНиП 3.06.04-91
Bridges and pipes
СП 46.13330.2012
ОКС 93.040
Дата введения
1 января 2013 года
Предисловие
Цели и принципы
стандартизации в Российской Федерации установлены Федеральным законом от 27
декабря 2002 г. N 184-ФЗ "О техническом регулировании", а правила
разработки - Постановлением Правительства Российской Федерации "О порядке
разработки и утверждения сводов правил" от 19 ноября 2008 г. N 858.
Сведения о
своде правил
1. Исполнители -
ОАО ЦНИИС.
2. Внесен
Техническим комитетом по стандартизации ТК 465 "Строительство".
3. Подготовлен к
утверждению Департаментом архитектуры, строительства и градостроительной
политики.
4. Утвержден
Приказом Министерства регионального развития Российской Федерации (Минрегион
России) от 29 декабря 2011 г. N 635 и введен в действие с 1 января 2013 г.
5. Зарегистрирован
Федеральным агентством по техническому регулированию и метрологии
(Росстандарт). Пересмотр СП 46.13330.2010 "СНиП 3.06.04-91 Мосты и
трубы".
Информация об
изменениях к настоящему своду правил публикуется в ежегодно издаваемом
информационном указателе "Национальные стандарты", а текст изменений
и поправок - в ежемесячно издаваемых информационных указателях
"Национальные стандарты". В случае пересмотра (замены) или отмены
настоящего свода правил соответствующее уведомление будет опубликовано в
ежемесячно издаваемом информационном указателе "Национальные стандарты".
Соответствующая информация, уведомление и тексты размещаются также в
информационной системе общего пользования - на официальном сайте разработчика
(Минрегион России) в сети Интернет.
Введение
Настоящий свод
правил является актуализированной редакцией СНиП 3.06.04-91.
Свод правил
содержит правила, которые необходимо соблюдать при выполнении и приемке работ
при сооружении новых, реконструкции и капитальном ремонте существующих
постоянных мостов (в том числе путепроводов, виадуков, транспортных эстакад, пешеходных
мостов) и труб под насыпями железных дорог, линиями метрополитена и трамвая,
автомобильными дорогами (включая внутрихозяйственные дороги
сельскохозяйственных предприятий и организаций и дороги промышленных
предприятий), на улицах и дорогах городов, поселков и сельских населенных
пунктов, если иные не предусмотрены проектом.
Работа выполнена
авторским коллективом: ОАО ЦНИИС (доктора техн. наук А.А. Цернант, Г.С.
Переселенков, Г.С. Рояк, А.Р. Соловьянчик; кандидаты техн. наук К.М. Акимова,
Э.А. Балючик (руководитель работы), А.С. Бейвель, И.В. Грановская, В.Г.
Гребенчук, Ю.В. Новак, Г.Г. Орлов, В.П. Рыбчинский, А.Д. Соколов, Е.В.
Фальковский; инженер А.В. Кручинкин), ЗАО "Институт "ИМИДИС"
(канд. техн. наук Б.И. Кришман), МИИТ (доктора техн. наук В.М. Круглов, В.М.
Фридкин; канд. техн. наук В.А. Миленин), ОАО "Институт
Гипростроймост" (инженер Э.А. Гитман), ОАО "МОСТОТРЕСТ" (инженер
В.Н. Коротин), ООО "НПП СК МОСТ" (канд. техн. наук И.Д. Сахарова),
ООО "Следящие Тест-Системы" (канд. техн. наук С.Л. Ситников), ООО
"Союздорпроект" (инженер Ф.В. Винокур), ФГУП "НИИ Мостов и
дефектоскопии" (инженер С.А. Клюкин), Фонд "АМОСТ" (инженер Ю.А.
Цыткин).
1. Область
применения
Настоящий свод
правил устанавливает правила производства и приемки работ по сооружению новых и
реконструкции постоянных мостовых сооружений и труб:
на автомобильных
дорогах, включая внутрихозяйственные дороги сельскохозяйственных и промышленных
предприятий, на улицах и дорогах населенных пунктов;
на железных дорогах
колеи 1520 мм при движении пассажирских поездов со скоростями до 200 км/ч,
линиях метрополитена и трамвая;
на дорогах под
совмещенное движение транспортных средств - автомобильных и поездов железных
дорог, трамваев и метрополитена;
на пешеходных
дорогах.
Данные нормы не
распространяются на сооружение:
механизмов
разводных пролетов мостов;
мостов и труб на
внутренних автомобильных дорогах лесозаготовительных и лесохозяйственных
организаций, не выходящих на сеть дорог общего пользования и к водным путям;
галерей,
конструкций для пропуска селей, служебных эстакад;
коммуникационных
мостов, не предназначенных для пропуска транспортных средств и пешеходов.
2.
Нормативные ссылки
В настоящем своде
правил использованы ссылки на нормативные документы, приведенные в Приложении
А.
Примечание. При
пользовании настоящим сводом правил целесообразно проверить действие ссылочных
стандартов и классификаторов в информационной системе общего пользования на
официальном сайте национального органа Российской Федерации по стандартизации в
сети Интернет или по ежегодно издаваемому указателю "Национальные
стандарты", который опубликован по состоянию на 1 января текущего года, и
по соответствующим ежемесячно издаваемым информационным указателям,
опубликованным в текущем году. Если ссылочный документ заменен (изменен), то
при пользовании настоящим сводом правил следует руководствоваться замененным
(измененным) стандартом. Если ссылочный документ отменен без замены, то
положение, в котором дана ссылка на него, применяется в части, не затрагивающей
эту ссылку.
3. Термины
и определения
В настоящем своде
правил применены термины и определения в соответствии с Приложением Б.
4. Общие
положения
4.1. Работы, не
охваченные настоящим сводом правил или изложенные в недостаточном объеме, следует
выполнять в соответствии с указаниями проекта производства работ и
технологических регламентов.
4.2. При сооружении
мостов и труб, кроме требований настоящего свода правил, следует соблюдать
требования, содержащиеся в государственных стандартах, сводах правил, а также в
других нормативных документах, в том числе по технике безопасности,
производственной санитарии и пожарной безопасности.
Возведение
сооружений следует выполнять по проекту и в соответствии с технологическим
регламентом на конкретный вид работ. Технологические регламенты должны быть
согласованы с проектной организацией - разработчиком конструкций и утверждены
заказчиком.
Приемку работ и
качество их выполнения при сооружении мостов и труб следует подтверждать
исполнительной документацией.
4.3. При сооружении
мостов и труб следует осуществлять предусмотренные проектом разделы ОВОС
(оценка воздействия на окружающую среду) и ООС (охрана окружающей среды), меры
по охране окружающей природной среды и сохранению существующего в данной
местности природного баланса.
Применяемые
технологические решения должны соответствовать санитарным нормам и не допускать
опасного загрязнения водотока и подземных вод, заболачивания местности,
образования термокарстовых, эрозионных, наледных и других вредных процессов, а
также недопустимых выбросов загрязняющих веществ в атмосферу.
На примыкающих
территориях за пределами отведенных строительных площадок не допускаются:
вырубка леса и кустарника, устройство свалок отходов, складирование материалов,
повреждения дерново-растительного покрова, а также планировочные
дренажно-осушительные и другие работы, изменяющие существующий уровень
грунтовых вод.
До сдачи сооружения
в постоянную эксплуатацию на территории, где велись строительные работы, должны
быть очищены от временных зданий и вспомогательных сооружений, убраны
оставшиеся материалы и конструкции, проведена планировка поверхности грунта,
выполнены предусмотренные работы по рекультивации и благоустройству территории,
а также расчищены подмостовые русла и прочищены отверстия труб.
4.4. Конструкции
мостов и труб, в том числе из полимерных композиционных материалов (далее -
ПКМ), изготавливаемые на промышленных предприятиях, полигоне или в цехе
организации-подрядчика, должны отвечать установленным требованиям к качеству
продукции, причем качество продукции должно быть подтверждено исполнительной
документацией.
4.5. Методы,
очередность и продолжительность выполнения работ следует назначать с учетом
возможного влияния периодических или постоянных водотоков, колебания уровня
воды, размыва дна русла, волнения в акватории, ледохода, ледовых заторов,
наледи, карчехода, сели, интенсивности и повторяемости ветровых воздействий и
др.
При строительстве
мостов в акватории рек, озер и иных водоемов должны быть обеспечены
безопасность и согласованные в проекте размеры ущерба в работе организаций и
систем, хозяйственная деятельность которых связана с эксплуатацией или
использованием акватории этих водоемов (водный транспорт, рыбное хозяйство,
оросительные системы, водоснабжение, рекреация и т.п.).
Работы по
возведению мостового сооружения на открытых для движения, в том числе рабочего,
железных и автомобильных дорогах, путях сообщения в населенных пунктах и в
непосредственной близости от них должны производиться в соответствии с
согласованным проектом с соблюдением условий безопасности движения транспорта и
пешеходов, работающих людей, а также сохранности существующих зданий,
сооружений и коммуникаций, находящихся в зоне строительства.
4.6. При заготовке
местных материалов (щебня, песка, лесоматериалов) на месте строительства
необходимо обеспечивать контроль за качеством и исследованием свойств
материалов в объеме, предусмотренном техническими требованиями на
соответствующие материалы.
4.7. Строительные
организации до сдачи в эксплуатацию законченного строительством моста или трубы
должны вести систематические наблюдения за его техническим состоянием и
осуществлять контроль за положением и состоянием возведенных конструкций
сооружения в плане и профиле, особенно после прохода паводковых вод,
землетрясений, ураганных ветров и т.д.
Осмотр труб и
контроль за положением их звеньев (секций) должны быть осуществлены
строительной организацией через 2 - 3 месяца после засыпки труб грунтом.
Результаты контроля
необходимо оформлять соответствующим актом.
4.8. Загружение
части моста, законченной в соответствии с проектом, допускается только после ее
обследования и составления акта промежуточной приемки. Порядок указанного
загружения устанавливается проектом.
4.9. При размещении
строительной площадки и назначении конструкций вспомогательных сооружений и
устройств за рабочий горизонт воды принимается наивысший, возможный в период
выполнения работ уровень воды, соответствующий расчетному расходу ее с
вероятностью превышения до 10%.
Допускается при
соответствующем технико-экономическом обосновании принимать рабочий горизонт
воды, соответствующий расчетному расходу ее с вероятностью превышения до 50%.
5.
Геодезическое обеспечение строительства
5.1. Состав
геодезических работ, выполняемых при строительстве мостов и труб, должен
включать:
а) создание
геодезической разбивочной основы для строительства;
б) работы по
разбивке внутриплощадочных сооружений и временных зданий и сооружений (при их
наличии);
в) детальные
разбивочные работы и геодезический контроль точности геометрических параметров
возводимых сооружений и исполнительные съемки с составлением исполнительной
геодезической документации по ним.
Геодезические
работы по подпункту а) являются обязанностью заказчика, по подпунктам б) и в)
входят в обязанности подрядчика.
Геодезическая
разбивочная основа (ГРО) для строительства моста (трубы) должна обеспечивать:
требуемую точность
разбивки, сооружения и контроля работ на всех стадиях строительства;
максимальные
удобства для разбивки и контроля положения центров опор;
сохранность пунктов
ГРО в процессе строительства и после его завершения для использования их при
эксплуатации сооружения;
возможность
развития сети пунктов ГРО в процессе строительства; закладку (при
необходимости) новых пунктов после завершения земляных работ в пойменной части
либо сооружения новых полуостровков и островков в русловой части.
Геодезическую
разбивочную основу для строительства надлежит создавать с привязкой к имеющимся
в районе строительства пунктам геодезических сетей.
5.2. Геодезической
разбивочной основой для строительства моста (трубы) служат:
а) пункты мостовой
триангуляции, или трилатерации, или линейно-угловых сетей - в зависимости от
сложности с видимостью вдоль береговой линии (для мостов длиной более 300 м,
вантовых мостов, мостов на кривой, а также мостов с опорами высотой более 15
м);
б) пункты,
закрепляющие продольную ось моста (для трубы - точку пересечения оси дороги с
осью трубы);
в) пункты,
закрепляющие вспомогательную ось, параллельную главной оси, в случае
строительства мостов, перекрывающих пойменные участки длиной более 100 м, при
строительстве мостов в сложных условиях (природных или связанных с существующей
застройкой на участке работ) и в случае, если пункты основной оси могут быть
повреждены в процессе строительства;
г) высотные реперы
(марки);
д) точки по оси
подходов к мосту, в случае, если подходы входят в состав проекта моста;
е) точки по оси
пойменных опор мостов длиной более 100 м, вантовых мостов, мостов на кривых и
мостов с опорами высотой более 15 м;
ж) створные
плоскости, перпендикулярные продольной оси моста или расположенные под
проектным углом на суходоле, вынесенные в натуру по центрам мостовых опор;
з) другие пункты
ГРО, установленные с учетом условий местности, с которых можно производить
разбивку центров опор и осуществлять контроль за их положением в процессе
строительства.
5.3. В случае
пересечения осью моста острова на нем дополнительно следует установить не менее
одного пункта плановой геодезической разбивочной основы и одного высотного
репера.
Ось моста,
расположенного на кривой, привязывается к линии хорды, стягивающей начало и
конец моста. В случае расположения русловой части моста на прямой, а пойменных
частей - на кривых, на криволинейных участках моста следует закреплять
тангенсы, вершины углов и биссектрисы.
5.4. Плановое и
высотное положение пунктов ГРО должно быть определено в системе координат и
высот, принятых при разработке проектной документации для строительства
мостового перехода или эстакады (государственная, городская, условная).
Целесообразно
использовать условную систему координат - "мостовую", когда осью
абсцисс является прямая, соединяющая центры устоев моста, а за начало координат
следует принять пункт на оси абсцисс за пределами моста с расчетом, чтобы не
иметь отрицательных координат на весь район работ.
При построении ГРО
для осуществления строительства и наблюдения за деформациями элементов моста следует
применять высокоточные измерения с использованием глобальных спутниковых
навигационных систем GPS, ГЛОНАС, если применение традиционных методов
невозможно или экономически нецелесообразно.
5.5. Высотное
положение пунктов ГРО следует определять от реперов государственной сети.
Реперы, расположенные на противоположных берегах реки, должны иметь отметки в
единой системе отсчета высот. Помимо постоянных реперов, находящихся за
пределами рабочей зоны, у каждого возводимого сооружения следует закладывать рабочие
репера, с постоянным контролем их отметок.
5.6. На мостах
длиной более 100 м, вантовых мостах, мостах на кривых и мостах с опорами
высотой более 15 м пункты плановой и высотной геодезической основы следует
закреплять с железобетонными центрами и стальными трубами с приваренными к их
верхним торцам столиками для установки приборов с принудительным
центрированием.
Бетонный якорь
закрепления трубы должен располагаться ниже глубины сезонного промерзания
грунта.
На остальных
мостах, трубах и на трассе подходов допускается закреплять пункты плановой
геодезической разбивочной основы деревянными столбами с якорями.
5.7. Геодезические
разбивочные работы и пооперационный геодезический контроль при строительстве
мостов длиной более 300 м, вантовых мостов, мостов на кривых, а также мостов с
опорами высотой более 15 м следует выполнять по проекту производства
геодезических работ (ППГР), разработанному генеральной проектной организацией в
составе рабочей документации на строительство моста.
Для остальных
мостов и труб решения по геодезическим работам, включая схемы размещения
пунктов для выполнения геодезических построений и измерений, а также указания о
соблюдении необходимой точности и технических средствах геодезического контроля
выполнения строительно-монтажных работ, должны содержаться в проекте
производства работ.
5.8. В ППГР
дополнительно к требованиям, полученным при разработке проектов организации
строительства и проектов производства работ, должны быть приведены:
на период
подготовки к строительству - схемы закрепления пунктов геодезической
разбивочной основы, увязанные со стройгенпланом и график выполнения
геодезических работ;
на период
строительства - данные о точности и методы выполнения разбивочной сети моста,
схема расположения и закрепления пунктов сети; типы центров знаков; данные о
точности, методы, средства и порядок выполнения детальных разбивочных работ (в
том числе детальную разбивку мостовой опоры при монтаже пролетного строения),
контрольных измерений и исполнительных съемок; график выполнения геодезических
работ;
на период
наблюдений за перемещениями и деформациями сооружения - данные о точности,
методы, средства и порядок наблюдений за перемещениями и деформациями объектов
строительства; схема геодезической сети, данные о точности определения и методы
ее построения, типы центров знаков; график выполнения геодезических работ.
В ППГР должен быть
приведен также нормокомплект геодезических приборов и приспособлений.
ППГР, разработанный
генеральной проектной организацией, должен быть выдан подрядной организации до
передачи ей заказчиком геодезической разбивочной основы.
5.9. Геодезические
работы в процессе сооружения мостов и труб следует выполнять в объеме и с
точностью, обеспечивающими соответствие геометрических параметров проектной
документации требованиям СП 48.13330 и СП 126.13330, а также настоящего свода
правил.
5.10.
Передача заказчиком технической документации на созданную геодезическую
разбивочную основу для сооружения мостов и труб и закрепленных на местности
знаков оформляется актом.
К акту приемки
геодезической разбивочной основы должен быть приложен схематический план
мостового перехода с указанием местоположения пунктов, типов и глубины
заложения закрепляющих их знаков, координат пунктов, их пикетажных значений и
высотных отметок в принятой системе координат и высот.
Для мостов длиной
более 300 м, вантовых мостов и мостов на кривых, а также мостов с опорами
высотой более 15 м к акту приемки геодезической разбивочной основы необходимо
прилагать разбивочный план мостового перехода, включающий пункты
планово-высотной геодезической разбивочной основы с указанием всех необходимых
данных для выполнения разбивочных работ.
5.11. Геодезические
разбивочные работы в процессе сооружения мостов и труб, разбивка и закрепление
осей временных подъездных дорог, развитие (при необходимости) геодезической
разбивочной основы на мостах длиной менее 300 м или с зеркалом водотока менее
100 м, а также пооперационный контроль строительно-монтажных работ должны
выполняться подрядчиком. Исходными данными для разбивочных работ являются
координаты и высоты пунктов геодезической разбивочной основы, принятой от
заказчика.
5.12. При
строительстве моста исполнительный геодезический контроль работ также возложен
на строительную организацию на следующих этапах:
а) до начала работ
по сооружению моста в соответствии с 5.10 настоящего свода правил путем
контрольных измерений;
б) после разбивки
опор (до возведения фундаментов опор);
в) после возведения
фундаментов (до начала работ по возведению тела опор);
г) в процессе
возведения тела опор - каждый этап, в соответствии с ППГР;
д) после возведения
опор и разбивки осей подферменных площадок;
е) после установки
опорных частей в проектное положение;
ж) после установки
пролетного строения на опорные части.
5.13. Технические
требования, объем и способы контроля геодезической разбивочной основы приведены
в таблице 1.
Таблица 1
┌────────────────────────────────────────────┬────────┬───────────────────┐
│ Технические требования │Контроль│ Метод или
способ │
│
│ │ контроля │
├────────────────────────────────────────────┼────────┼───────────────────┤
│1.
Число пунктов геодезической разбивочной
│Каждого │
Измерительный │
│основы
для мостов длиной более 300 м,
│ пункта │
(геодезические │
│вантовых
мостов, мостов на кривой, мостов
│ │ измерения │
│с
опорами высотой более 15 м, а также при
│ │ при приемке │
│зеркале
водотока более 100 м принимается
│ │ геодезической │
│в
соответствии с проектом геодезической
│ │разбивочной
основы)│
│разбивочной
основы ППГР
│ │ │
├────────────────────────────────────────────┼────────┼───────────────────┤
│2.
Число реперов и пунктов плановой
│ │ │
│геодезической
разбивочной основы,
│ │ │
│закрепляющих
продольную ось моста,
│ │ │
│принимается
для:
│ │ │
│
труб и мостов длиной до 50 м - 1 репер
│Каждого │ То
же │
│и
не менее 2 пунктов на продольной оси моста│ репера │ │
│(трубы) │и
пункта│ │
│
мостов длиной от 50 до 300 м - по 1 реперу │ То же │ " │
│и
не менее 2 пунктов на каждом берегу
│ │ │
│
мостов длиной более 300 м, вантовых мостов,│ "
│ " │
│мостов
на кривой и мостов с опорами высотой │ │ │
│более
15 м - по 2 репера и не менее
│ │ │
│2
пунктов на каждом берегу
│ │ │
│
трасс подходов - не менее 1 репера
│ " │ " │
│и
2 пунктов на 1 км трассы
│ │ │
├────────────────────────────────────────────┼────────┼───────────────────┤
│3.
Средние квадратические ошибки определения│ │ │
│принимаются,
мм:
│ │ │
│
координат пунктов плановой геодезической
│Всех │ Измерительный │
│основы
- 6 │пунктов │ (уравнивание │
│
│плановой│
плановой │
│
│геодези-│
геодезической │
│
│ческой │ основы) │
│
│основы │ │
│
отметок реперов на берегах и опорах:
│ Всех │
Измерительный │
│постоянных
- 3, временных - 5
│реперов │(геометрическое или│
│ │ │тригонометрическое │
│
│ │ нивелирование │
│
│ │ с
использованием │
│ │
│ электронных │
│
│ │ тахеометров) │
├────────────────────────────────────────────┴────────┴───────────────────┤
│ Примечания. 1. При расположении трассы
подхода на кривой должны быть│
│закреплены:
начало и конец кривой, биссектриса и
вершина угла поворота│
│трассы.
│
│ 2. Реперы следует устанавливать на
расстоянии не более 80 м от оси,│
│но
за пределами земляного полотна, резервов, водоотводов и т.п. │
│ 3. Для наблюдения за перемещением и
деформацией опор моста, если это│
│предусмотрено
ППГР, необходимо предусмотреть фиксацию центра каждой опоры│
│на
стальной закладной детали.
│
└─────────────────────────────────────────────────────────────────────────┘
6.
Специальные вспомогательные сооружения
и устройства
(СВСиУ)
6.1. Конструкции
СВСиУ следует изготавливать в соответствии с проектом и требованиями настоящего
свода правил.
Возведение и
приемку СВСиУ необходимо осуществлять в соответствии с требованиями СП 70.13330
и настоящего свода правил.
6.2. Проект СВСиУ
должна разрабатывать генеральная проектная организация или по ее заказу другая
проектная организация в составе рабочих чертежей для строительства объекта в
соответствии с перечнем специальных вспомогательных сооружений, приспособлений,
устройств и установок, а также сложных временных сооружений и сетей. Рабочую
документацию СВСиУ разрабатывают на основе утвержденного проекта (утверждаемой
части рабочего проекта) в соответствии с заданием на проектирование и в увязке
с технологическими решениями производства работ.
Рабочая
документация СВСиУ должна содержать:
рабочие чертежи
конструкций в объеме, достаточном для изготовления этих конструкций, с
указанием требований по качеству применяемых материалов и изделий;
технические
требования к изготовлению конструкций;
указания о порядке
сооружения, загружения, испытания и эксплуатации с учетом климатических условий
места строительства;
расчеты (расчетные
листы), а в случаях, когда они не включаются в состав документации, выдаваемой
заказчику, указываются основные расчетные характеристики конструкций (расчетные
нагрузки, расчетные схемы, несущая способность, величина воздействия на
основные конструкции, работающие совместно с СВСиУ и т.п.);
технические решения
по обеспечению безопасности работающих в соответствии с требованиями СП
49.13330;
указания и
мероприятия по обеспечению требований охраны окружающей среды на период
возведения, эксплуатации и демонтажа данного вида СВСиУ.
6.3. СВСиУ,
находящиеся в пределах судового хода, должны быть оборудованы судовой
сигнализацией и специальными защитными конструкциями от навала судов.
6.4. При установке
опор СВСиУ на лежневое основание должны быть приняты меры к отводу от основания
поверхностных вод.
Земляные работы
вблизи опор следует выполнять только в соответствии с ППР.
6.5. Проектом СВСиУ
опорам и подмостям придается строительный подъем с учетом следующих размеров
остаточных деформаций, мм:
2 - при обжатии в
местах примыкания дерева к дереву на одно пересечение (контакт);
1 - при обжатии в
местах примыкания дерева к металлу на одно пересечение (контакт);
10 - при осадке
плотно подбитых лежней;
5 - при осадке
песочниц, заполненных песком.
6.6. При
расположении площадок для сборки пролетных строений на насыпи подхода к мосту
следует производить заблаговременную отсыпку грунта с тщательным послойным его
уплотнением, соответствующим требованиям проекта.
С поверхности
насыпи должен быть обеспечен водоотвод.
Перед каждым циклом
сборки или надвижки и после каждого ливневого дождя необходимо производить
нивелировку площадки и устранение возникающих деформаций.
6.7. Верхние
накаточные пути должны плотно прилегать к нижнему поясу надвигаемой конструкции
с учетом конфигурации всех выступающих из конструкции деталей.
6.8. Скорость
перекатки пролетных строений не должна превышать 60 м/ч, а надвижки на
устройствах скольжения - 25 м/ч. Скорость рабочего хода поршней домкратов,
применяемых для горизонтального перемещения балок, не должна быть более 5 мм/с.
Перед началом работ
все такелажное оборудование должно быть освидетельствовано и принято по акту.
6.9. При выполнении
работ с использованием плавучих систем всю акваторию следует предварительно
обследовать и осуществить необходимые работы для обеспечения глубины воды под
днищем не менее 0,2 м с учетом возможного колебания уровня воды в районе
перевозки.
6.10. Плавучие
системы надлежит комплектовать из понтонов закрытого типа или металлических
барж.
Перед установкой в
систему каждый понтон или баржа должны быть испытаны и приняты по акту.
6.11. При
перемещении плавучих систем с помощью буксиров системы должны быть снабжены
аварийными якорями и приспособлениями для непосредственного закрепления якорных
тросов на корпусе.
6.12. На углы
плашкоута должны быть нанесены несмываемой краской водомерные рейки. При
загружении плавсистемы необходимо контролировать соответствие фактической
осадки проекту.
6.13. Перед выводом
плавучей системы в акваторию необходимо получить прогноз погоды на время
выполнения работ.
При наличии выше по
течению реки плотины, ГЭС и т.д. необходимо на время проведения работ получить
согласование о недопустимости проведения водосброса.
6.14. Командный
пункт плавучей системы должен быть оборудован радиотелефонной связью с
буксирами, плавучими опорами и береговыми обустройствами.
6.15. Применяемые
при выполнении работ плавучие краны должны иметь остойчивость, допускающую
осуществление монтажных работ при скорости ветра до 10 м/с и волнении до 2
баллов (при высоте волны до 25 см).
6.16. При перемещении
самоходных портальных и козловых кранов, не имеющих синхронизации движения
ходовых тележек, неравномерность перемещения ног кранов не должна превышать
1/500 пролета крана.
6.17. Домкратные
установки должны быть с централизованным управлением, позволяющим регулировать
режим работы каждого домкрата или группы домкратов, и снабжены опломбированными
манометрами; домкраты должны иметь стопорные (страховочные) приспособления и
опираться на металлическое основание через фанерные прокладки, а на деревянное
основание - через стальную распределительную плиту.
Опирание пролетных
строений на домкраты допускается только через распределительную стальную плиту
и фанерную прокладку.
6.18.
Предусмотренные проектом испытания СВСиУ должны быть произведены в соответствии
с программой до их загружения.
6.19. СВСиУ перед
эксплуатацией должны быть осмотрены и приняты специальной комиссией, на что
должен быть составлен акт. Перечень СВСиУ, подлежащих приемке, необходимо
приводить в проекте производства работ (ППР).
6.20. Состояние
СВСиУ следует систематически контролировать. Осмотр и освидетельствование СВСиУ
необходимо производить перед их загружением и после прохода паводка.
7.
Арматурные и бетонные работы
7.1. При выполнении
арматурных и бетонных работ следует соблюдать требования ГОСТ 23118, СП
130.13330 и настоящих правил, а для железобетонных конструкций с использованием
стальных фибр (сталежелезобетонных) следует учитывать требования ГОСТ Р 52751.
Арматурные работы
7.2. Арматура,
имеющая на поверхности коррозию, за исключением высокопрочной проволоки и
канатов, допускается к применению при условии, что механические свойства и
размеры периодического профиля останутся не менее допустимых по стандартам.
7.3. Контроль
качества сварных стыков ненапрягаемой арматуры следует выполнять в зависимости
от их категории, указываемой в проекте конструкции сооружения, согласно
требованиям СП 35.13330. При этом методы, объемы контроля и допуски на дефекты
в сварных швах следует принимать в соответствии с требованиями ГОСТ 10922 [9] и
настоящего свода правил, а также с учетом указаний проекта, в том числе по
использованию разрушающего или неразрушающего методов контроля.
При неразрушающем
методе контролируется 100% сварных стыков первой категории, 50% - второй и 15%
- третьей.
7.4. Устройство
несварных стыковых соединений (обжимных, винтовых и др.) должно выполняться по
технологическим регламентам применительно к конкретному объекту строительства.
7.5. Для
обеспечения защитного слоя допускается применять бетонные "сухарики",
обеспечивающие требуемые проектом размеры.
7.6. Допускаемые
отклонения от проекта, мм:
габаритных размеров
вязаных арматурных каркасов и сеток:
для стоек,
балок, плит и арок +/- 10;
" фундаментов +/- 20;
расстояния между
отдельными стержнями или рядами арматуры при армировании в несколько рядов по
высоте в конструкциях толщиной более 1 м и фундаментах +/- 20;
в балках, арках, а
также плитах толщиной, мм:
св.
300 +/- 10;
от 100 до
300 +/- 5;
до 100
+/- 3;
расстояния между
хомутами балок и стоек, а также между связями арматурных каркасов +/- 10;
расстояния между
распределительными стержнями в одном ряду +/- 25;
положения хомутов
относительно проектной оси (вертикальной, горизонтальной или наклонной) +/- 15.
Всю установленную
арматуру сборных и монолитных конструкций (за исключением случаев, оговоренных
в рабочей документации) следует принимать до их бетонирования; результаты
освидетельствования и приемки следует оформлять актом на скрытые работы.
Контроль за
состоянием высокопрочной арматурной проволоки и арматурных канатов против
коррозионного растрескивания производится в случае несоблюдения условий их
хранения и правил выполнения работ, изложенных в настоящем своде правил.
Контроль производится в соответствии с ГОСТ 10884.
7.7. Все работы по
предварительному напряжению высокопрочной арматуры (ВА) на строительной
площадке должны вестись в соответствии с индивидуально разработанными
технологическими регламентами (далее - ТРПН), являющимися составной частью ППР.
7.8. Все
поставленные материалы и изделия, используемые для натяжения ВА, должны иметь
сертификаты и (или) паспорта, оформленные в соответствии с требованиями
стандарта на них и в обязательном порядке должны пройти входной контроль. Без
письменного акта прохождения входного контроля, утвержденного Заказчиком,
использование их запрещается.
7.9. Независимо от
наличия сертификата (паспорта) перед натяжением ВА необходимо проводить
контрольные испытания ВА с определением разрывного усилия, временного
сопротивления, предела текучести, модуля упругости, остаточного удлинения после
разрыва.
Перечисленные
данные должны указываться для каждого бунта проволоки (канатов) и связки
стержней вне зависимости от требования стандарта на их изготовление.
Для испытаний
высокопрочных проволоки, арматурных стержней и стальных канатов необходимо
брать по три образца от обоих концов каждого мотка (бунта). Разрешается
отбирать образцы в процессе установки в конструкцию. Если бунт использован не
полностью вместо конца бунта разрешается отбирать образцы от начала остатка
бунта.
В случае правки
высокопрочной проволоки контрольные испытания ее следует производить после
правки.
Испытанию подлежат
два образца из бунта - по одному из отобранных от начала и конца. Остальные
отобранные образцы сохраняются для проведения повторных испытаний до конца
строительства.
Отбор образцов
стержневой ВА необходимо осуществлять в соответствии с требованиями ГОСТ 5781 и
ГОСТ 10884.
7.10. При
несоответствии требований стандарта на изготовление ВА и результатов
контрольных испытаний для отдельных бунтов, для этих бунтов выполняются
повторные испытания на удвоенной выборке (с использованием ранее отобранных
образцов). Если при повторных испытаниях также получено несоответствие результатов
испытаний требованиям стандарта, тогда эти бунты бракуются. Установленные
пучки, в которых использована ВА из выбракованных бунтов, подлежат замене в
полном объеме. Запрещается использование ВА выбракованных бунтов.
7.11. Поставка ВА
на строительную площадку должна осуществляться так, чтобы их срок хранения (со
дня изготовления) к моменту инъецирования (омоноличивания) или натяжения (для
элементов, работающих без сцепления) не превышал 12 мес. Указанный срок может
быть увеличен, но не более чем до 24 мес, после проведения обследования и
проведения испытаний образцов на склонность к коррозионному растрескиванию.
Контроль производится в соответствии с ГОСТ 10884.
7.12. Перемещать
ВА, в том числе пучки, кранами без приспособлений или текстильных строп, предохраняющих
их от резких перегибов, повреждений и загрязнения, запрещается.
7.13.
Транспортирование каналообразователей должно осуществляться в специальных
контейнерах либо с применением иных приспособлений, исключающих повреждение и
искривление их, в том числе при погрузочно-разгрузочных работах. Следует
стремиться к минимальному сроку хранения жестяных каналообразователей в
условиях стройплощадки из-за высокой склонности их к коррозии. На стройплощадке
каналообразователи должны храниться под навесом в специальных контейнерах или
на деревянных подкладках, расположенных с шагом не более 1 м.
7.14.
Непосредственно перед установкой в опалубку каналообразователи должны быть
проверены по следующим параметрам:
сохранность формы:
отсутствие
овальности, искривлений и т.п.;
отсутствие
повреждений:
вмятин, проколов,
развальцовки ленты и т.п.;
отсутствие коррозии
на внешней поверхности для металлических каналообразователей. Допускается налет
ржавчины, удаляемый ветошью.
7.15. Хранение на
строительной площадке материалов и изделий СПН должно соответствовать
требованиям стандартов на их изготовление. Хранение должно осуществляться в
ненарушенной упаковке. В случае временного нарушения упаковки при дальнейшем
хранении упаковка должна быть восстановлена.
7.16.
Каналообразователи следует собирать в единое целое из отдельных звеньев с
помощью муфт, замков и иных приспособлений. Места соединений звеньев
каналообразователей должны быть герметичными. Аналогичным образом производится
соединение каналообразователя с опорной закладной деталью.
7.17. Закрепление
каналообразователя в проектном положении должно осуществляться на фиксирующих
рамках, устанавливаемых с шагом по длине конструкции 80 - 120 см.
Конструкция
фиксирующих рамок и закрепление на них должны быть определены проектом
производства работ и согласованы проектной организацией.
7.18. Если
каналообразователь используется после бетонирования не сразу, его концы после
предварительной продувки должны быть в обязательном порядке закрыты.
7.19. Перед
установкой ВА в забетонированную конструкцию проходимость канала должна быть в
обязательном порядке проверена с помощью специального калибра, соответствующего
внутреннему диаметру канала. При этом канал необходимо продуть сухим теплым
воздухом и, при необходимости, прочистить.
7.20. На
поверхности, устанавливаемой в конструкцию ВА, допускается наличие равномерного
налета ржавчины (поверхностное окисление), легко удаляемое сухой ветошью.
Наличие на поверхности язвенной коррозии (питингов) не допускается.
7.21. Запрещается
выполнение сварочных работ в непосредственной близости от ВА и
каналообразователей без защиты их от воздействия повышенной температуры и искр,
а также включение ВА в цепь электросварочных аппаратов или заземления
электроустановок.
7.22. В процессе
установки ВА запрещается приваривать (прихватывать) к ней распределительную
арматуру, хомуты и закладные детали, а также подвешивать опалубку, оборудование
и т.п.
7.23. Установку ВА
в каналообразователи разрешается выполнять следующими способами:
протаскиванием
предварительно сформированного пучка с помощью лидерного троса и лебедки.
Усилие протаскивания не должно превышать 5% контролируемого усилия. На входе в
канал скрутки, фиксирующие пучок, должны быть сняты;
проталкиванием по
одному арматурному элементу.
Допускается
выполнять установку ВА в каналообразователи с анкерами на сборочных площадках
вышеперечисленными способами с дальнейшим сматыванием их на технологические
катушки, транспортированием к месту установки, разматыванием и установкой в
конструкцию в соответствии с проектом.
7.24. ВА следует
устанавливать в сроки и в условиях, исключающих возможность возникновения
коррозии. При протягивании (проталкивании) ВА через каналообразователи следует
принимать меры по предотвращению ее повреждения.
7.25. Перед
установкой анкеров и стыков необходимо выполнить расконсервацию деталей,
находящихся в антикоррозионной защите. Анкера и стыки собираются в соответствии
с инструкцией разработчика СПН по их сборке и монтажу. Все отступления от этого
порядка должны быть согласованы.
7.26. Усилия,
порядок и последовательность напряжения ВА должны быть указаны в проекте. До
начала работ по натяжению для всех контрольных образцов используемой в процессе
натяжения ВА должны быть получены положительные результаты механических
испытаний.
Рабочие параметры
оборудования для натяжения ВА должны определяться по тарировочным кривым.
Тарировка домкратов для натяжения должна проводиться каждые 12 мес с помощью
поверенных измерительных приборов класса точности 0,2.
Манометры, по
которым контролируется давление рабочей жидкости в полости домкратов для
натяжения ВА, должны иметь класс точности 0,6 и должны быть подсоединены к
полости домкратов-ВА гидравлическим рукавом длиной не более 1,5 м.
7.27. В процессе
натяжения ВА необходимо контролировать:
усилие натяжения:
по манометру измерения давления рабочей жидкости в поршневой полости цилиндра
натяжения домкрата;
усилие запрессовки
клиновых захватов анкера (если это предусмотрено технологией работ): по
манометру измерения давления рабочей жидкости в поршневой полости цилиндра
запрессовки домкрата;
удлинение пучка
(вытяжка): перемещение указателей (метки), устанавливаемых на элементах ВА,
относительно торца конструкции сооружения (стенда);
деформации в
анкере: перемещение указателя (см. выше) при передаче напряжения с домкрата на
бетон конструкции или на стенд;
равномерность
натяжения отдельных элементов пучка: взаимное смещение меток, нанесенных на
элементы ВА;
равномерность
натяжения проволок в каждом семипроволочном канате, в том числе уход
центральной проволоки.
Все измерения и
наблюдения в процессе натяжения фиксируются актами или в журнале работ по
натяжению.
7.28. При
определении упругого удлинения (вытяжки) за условный ноль рекомендуется принимать
усилие предварительного напряжения, соответствующее 20% контролируемого усилия.
При сравнении фактической вытяжки с проектной необходимо учитывать:
диапазон усилия
натяжения, в котором определена проектная вытяжка и измерена фактическая
вытяжка;
значение
фактического модуля упругости;
удлинение пучка на
длине домкрата;
деформации
пассивного анкера (при натяжении с одной стороны);
деформации
конструкции (стенда).
7.29. При натяжении
с двух сторон контроль вытяжки ведут по сумме вытяжек на обеих сторонах пучка.
7.30. При натяжении
пучка с одной стороны анкер с противоположной пассивной стороны перед началом
работ должен быть приведен в рабочее состояние. Во время натяжения необходимо
контролировать работу пассивного анкера.
7.31. В процессе
натяжения ВА контроль вытяжки ведут по ступеням натяжения, которые могут
составлять не более 20% контролируемого усилия. Величину ступеней натяжения
назначает проектная организация. Результаты измерения вытяжек по ступеням,
относительное удлинение и усилие заносятся в журнал работ.
7.32. В случае
отклонения наблюдаемой в процессе натяжения вытяжки более чем на 15% от
проектной на одной или нескольких ступенях натяжения процесс натяжения должен
быть остановлен, а результаты контроля переданы проектной организации.
7.33. Необходимые
требования при натяжении арматуры на бетон:
прочность бетона
конструкции и ее частей должна быть не ниже установленной проектом для данной
стадии, что подтверждается неразрушающим методом контроля или испытанием
контрольных образцов; до начала натяжения необходимо убедиться в отсутствии
дефектов в бетоне;
обжимаемая
конструкция должна опираться в местах, указанных в проекте, опорные узлы должны
иметь свободу перемещения, опалубка монолитных конструкций должна находиться в
требуемом проектом положении;
анкеры и домкраты
должны быть отцентрированы относительно оси напрягаемой арматуры и сохранять
это положение в период натяжения.
7.34. Необходимые
требования при натяжении арматуры на упоры:
предварительно
выбрать слабину арматуры; при натяжении группы арматурных элементов или канатов
подтянуть их с усилием, составляющим 20% контролируемого при натяжении, и
закрепить в подтянутом положении;
следить за
состоянием и сохранением проектного положения арматуры, а также оттяжек или
других удерживающих приспособлений в местах ее перегиба;
обеспечить
компенсацию снижения натяжения в арматурных элементах, натягиваемых первыми,
перетяжкой или последующей подтяжкой части арматурных элементов;
порядок натяжения
ВА осуществляется строго по проекту;
не допускать потерь
напряжения в ВА (за счет разности температур натянутой арматуры и бетона
(стенда) в период его отвердения) сверх указанных в проекте, а для типовых
конструкций свыше 60 МПа.
7.35. Передачу
усилия натяжения ВА с упоров на бетон конструкции следует производить по
достижении бетоном прочности не ниже указанной в проекте. При этом необходимо
соблюдать следующие требования:
конструкция должна
быть оперта в местах, предусмотренных проектом, иметь свободу перемещения и не
подвергаться нагрузкам, не предусмотренным проектом, в том числе реактивным от
загружаемых упоров;
передачу усилия
напряжения ВА с упоров на бетон конструкции производить плавно с помощью
специальных устройств: порядок и последовательность отпуска отдельных элементов
ВА должны соответствовать проекту и ТРПН;
перед обрезкой
газовой горелкой ВА должна быть очищена от бетона между торцом конструкции и
упором;
в случае передачи
усилия с упоров на бетон конструкции при помощи газовой горелки зона нагревания
отдельных элементов ВА должна быть длиной не менее 20 см при разогреве до
красного каления, после чего можно полностью произвести обрезку арматуры;
обрезка ВА
электросваркой запрещается.
7.36. Минимальные
температуры окружающей среды при работе с насосными установками, домкратами и
манометрами устанавливаются по их паспортным данным.
7.37. Все измерения
в процессе натяжения фиксируются в журнале работ по натяжению. Результаты
натяжения ВА на объектах строительства в обязательном порядке передаются
проектной организации на согласование.
7.38. Натяжение
стержневой арматуры механическим и электротермическим способами следует
выполнять в соответствии с требованиями ТРПН.
7.39. Работы по
обрезке технологических "хвостов" ВА и инъецированию
каналообразователей в конструкциях моста могут быть разрешены только после
получения от проектной организации письменного согласования результатов
натяжения.
7.40. Нормативные
требования, которые следует выполнять при производстве работ и проверять при
операционном контроле, а также объем, методы или способы контроля приведены в
таблице 2.
Таблица 2
┌─────────────────────────────────────────┬──────────────┬────────────────┐
│ Технические требования │ Контроль
│Метод или способ│
│
│ │ контроля
│
├─────────────────────────────────────────┼──────────────┼────────────────┤
│1.
Продолжительность хранения │ 100%
│Регистрационный │
│высокопрочной
проволочной арматуры,
│высокопрочной │Психрометри- │
│семипроволочных
и стальных канатов │ арматурной
│ческий │
│в
закрытых помещениях или специальных
│ стали │
│
│емкостях
не более одного года.
│ │ │
│Допускаемая
относительная влажность │ │ │
│воздуха
не более 65%
│ │ │
├─────────────────────────────────────────┼──────────────┼────────────────┤
│2.
Допускаемые отклонения при заготовке, │ │ │
│установке
и натяжении напрягаемой ВА
│ │ │
│от
проектных значений:
│ │ │
│
взаимное продольное смещение высаженных │ Каждого
│ Измерительный │
│головок
на концах арматурного элемента - │ арматурного │
(проверка │
│0,5
мм на каждые 10 м длины пучка
│ элемента │
по шаблону) │
│
прочности высаженных головок
│6 контрольных │ Измерительный │
│высокопрочных
проволок на отрыв - не ниже│образцов перед│ (испытание
│
│гарантированного
разрывного усилия │началом
работ.│ на отрыв) │
│по
ГОСТ 7348 │ Повторные
│ │
│
│ испытания │ │
│
│после высадки │ │
│
│ 10 тыс. │ │
│
│ головок, │ │
│
│ в случае │ │
│
│замены матриц │ │
│ │ пуансонов
│ │
│
│ и ремонта │ │
│
│ оборудования │ │
│ │ для высадки │ │
│
│ головок │ │
│
размеров высаженных головок +/- 0,2 мм
│ То же │ Измерительный │
│
│ │ (измерение
│
│
│
│штангенциркулем)│
├─────────────────────────────────────────┼──────────────┼────────────────┤
│3.
Отклонения в расстояниях между
│ │ │
│канатами,
стержнями и другими элементами │ │ │
│напрягаемой
арматуры: │ │ │
│
при проектном расстоянии в свету
│ Каждого │ Измерительный │
│до
60 мм +/- 5 мм │
элемента │ │
│
то же, св. 60 мм +/- 10 мм
│ │ │
├─────────────────────────────────────────┼──────────────┼────────────────┤
│4.
Точность установки опорных закладных
│ │ │
│деталей │ │ │
│
в поперечном направлении
│ │ │
│
по вертикали и горизонтали +/- 10 мм
│ Каждой │ Измерительный │
│
в продольном направлении +/- 25 мм
│ закладной │ │
│
наклон оси +/- 1°
│ детали │ │
├─────────────────────────────────────────┼──────────────┼────────────────┤
│5.
Точность установки каналообразователей│
│ │
│в
поперечном сечении конструкции
│ │ │
│
в поперечном направлении
│Каждого │
Измерительный │
│
по вертикали и горизонтали +/- 10 мм
│канало- │ │
│
в продольном направлении +/- 50 мм
│образователя │ │
├─────────────────────────────────────────┼──────────────┼────────────────┤
│6.
Ровность каналообразователя с
│ То же │ Измерительный │
│исключением
проектной кривизны на длине │ │ │
│2
м - 15 мм
│ │ │
├─────────────────────────────────────────┼──────────────┼────────────────┤
│7.
Отклонения от проектного положения
│ │ │
│внутренних
анкеров при натяжении пучков
│ │ │
│ВА
на упоры:
│ │ │
│
ближайших к торцам балок в сторону торца│ Каждого
│ Измерительный │
│40
мм │
арматурного │ (измерение
│
│
то же, в сторону середины 60 мм
│ элемента │
рулеткой) │
│
остальных анкеров +/- 200 мм (при
│ │ │
│минимальном
расстоянии в свету между │ │ │
│анкерами
100 мм)
│ │ │
├─────────────────────────────────────────┼──────────────┼────────────────┤
│8.
Допускаемое отклонение контролируемой │
Каждого │ Измерительный │
│длины
L арматурного элемента (расстояние │
элемента │ (измерение
│
│между
внутренними плоскостями анкеров
│ │ при
установке │
│с
высаженными головками) +/- 0,001L,
│ │ в упоры или
│
│но
не более +50; -40 мм
│ │ на
специальном │
│
│ │ стенде)
│
├─────────────────────────────────────────┼──────────────┼────────────────┤
│9.
Перекос опорных (упорных) поверхностей│
Один раз │
Измерительный │
│в
местах установки домкратов и анкеров
│ в месяц │
(проверка │
│не
более 1:100
│при натяжении │
угольником │
│
│ на упоры │
и щупом │
│
│ и в каждом │ по выверенной │
│
│ анкере │
базе) │
│
│при натяжении │ │
│ │ на бетон
│ │
├─────────────────────────────────────────┼──────────────┼────────────────┤
│10.
Точность установки домкратов при
│ Каждой │ Измерительный │
│групповом
натяжении ВА относительно
│ установки │
(измерение │
│равнодействующей
усилия +/- 10 мм │ домкрата
│ линейкой) │
├─────────────────────────────────────────┼──────────────┼────────────────┤
│11.
Допускаемые отклонения величин усилий│ │ │
│натяжения
арматуры домкратами
│ │ │
│(от
контролируемого усилия)
│ │ │
│
в отдельных канатах, стержнях
│ │
Измерительный │
│и
проволоках при натяжении: │ │ (сравнение
│
│
поочередном (последовательном) +/- 5%
│ Каждого │
показаний │
│
│ арматурного │ манометра
│
│
│ элемента │ домкрата и
│
│
групповом (неравномерность натяжения
│20% арматурных│непосредственно │
│в
пучке) +/- 10%
│ элементов │
измеренного │
│
│в каждом пучке│
усилия) │
│
усилие в пучке +/- 5%
│Каждого пучка │ │
├─────────────────────────────────────────┼──────────────┼────────────────┤
│12.
Отклонение величины вытяжки
│ │ │
│от
проектной: │ │ │
│
при натяжении отдельных пучков,
│ Каждого │ Измерительный │
│одиночных
канатов или стержней <*>
│ арматурного │ (измерение
│
│+/-
10%
│пучка/элемента│
линейкой) │
│
среднее, при натяжении группы <**>
│каждой группы │ │
│пучков,
канатов, стержней +/- 5%
│ │ │
├─────────────────────────────────────────┼──────────────┼────────────────┤
│13.
Точность измерения упругого удлинения│ │ Измерительный │
│(вытяжки)
арматуры при ее натяжении:
│ │ (измерение
│
│
продольной 1 мм
│ Каждого │
инструментом │
│
поперечной (хомутов) 0,1 мм
│ измерения │соответствующей │
│
│ │ точности)
│
├─────────────────────────────────────────┼──────────────┼────────────────┤
│14.
Допускаемые суммарные потери усилий
│
│Измерительный │
│натяжения,
вызываемые трением в домкратах│ │(проверка │
│и
анкерных закреплениях, не более:
│ │по
манометру │
│
для анкеров с высаженными головками,
│Только при │и
вытяжке │
│стаканных
анкеров стальных канатов
│определении
│частотомером │
│и
клиновых анкеров с индивидуальным
│контроли- │или
иным │
│закреплением
элементов ВА +/- 2%
│руемого усилия│динамометри- │
│
для конусных анкеров группового
│и тарировке │ческим
прибором)│
│закрепления
пучка ВА +/- 5%
│домкратов │ │
├─────────────────────────────────────────┼──────────────┼────────────────┤
│15.
Отклонения в контролируемой длине
│ │
Измерительный │
│двухпетлевых
элементов при натяжении: │ │ (измерение
│
│
групповом +/- 10 мм
│ Каждого │
рулеткой │
│
поочередном +/- 30 мм
│ арматурного │ при
установке │
│ │
элемента │ в упоры или
│
│
│ │ на
специальном │
│
│ │ стенде)
│
├─────────────────────────────────────────┼──────────────┼────────────────┤
│16.
Допускаемые сроки нахождения
│ │ │
│арматурных
элементов в каналах до
│ │ │
│инъецирования
без специальной защиты │ │ │
│(при
среднесуточной относительной
│ │ │
│влажности
воздуха более 75%), сут <***>
│ │ │
│
30 - из параллельных проволок
│ Всех │Регистрационный │
│
15 - из канатов
│ арматурных │
(проверка │
│
30 - из стержней (из термически
│ элементов │
соответствия │
│упрочненной
арматуры) │ │ сроков)
│
├─────────────────────────────────────────┴──────────────┴────────────────┤
│
<*> В отдельных случаях,
по согласованию с проектной
организацией│
│+/-
15%.
│
│
<**> Группа пучков ВА одного типа,
натягиваемая последовательно на│
│одном участке
конструкции в ограниченный
период времени (несколько│
│рабочих
смен) одним и тем же оборудованием,
после которого разрешается│
│передача
нагрузки на обжатый участок конструкции. │
│
<***> Сверх указанного срока необходимо принимать специальные меры
по│
│временной
защите арматуры от коррозии. Нахождение напрягаемой арматуры в│
│каналах
при любом способе временной защиты арматуры
от коррозии более│
│8
мес не допускается. │
│
│
│ Примечания. 1. ВА, имеющая отклонения
значений усилий напряжения
и│
│вытяжек
более указанных в таблице величин, должны быть повторно натянута│
│или
заменена после согласования с проектной организацией. │
│ 2. Допускается оставлять в конструкции,
обжатой группой пучков
или│
│отдельных
арматурных элементов ВА не более 1% (по
площади поперечного│
│сечения)
оборванных или не полностью натянутых элементов, при этом таких│
│поврежденных
пучков (отдельных арматурных элементов) в группе должно быть│
│не
более 20% общего количества, а каждый из них должен иметь повреждение│
│не
более 5% (по площади).
│
└─────────────────────────────────────────────────────────────────────────┘
Укладка бетонной
смеси
7.41. Работы по
укладке бетонной смеси требуется выполнять по технологическим регламентам,
разработанным применительно к конкретной конструкции объекта строительства с
обязательным проведением теплофизических расчетов для определения температурных
режимов укладки.
7.42. Приготовлять
и транспортировать бетонную смесь следует в соответствии с ГОСТ 7473. При этом
бетонную смесь следует приготовлять в смесителях принудительного перемешивания;
допускается приготовление бетонных смесей с подвижностью 5 см и более в
гравитационных смесителях (свободного падения).
Требования к
приготовлению и транспортированию бетонных смесей для самоуплотняющегося бетона
(СУБ) определяются по техническим условиям производителя смесей.
Цементно-песчаные
растворы следует приготовлять в растворосмесителях. Допускается приготовление
цементно-песчаных растворов в бетоносмесителях принудительного перемешивания.
7.43. Растворы
добавок следует подавать в смеситель в соответствии с рекомендациями
производителя добавок. Концентрированные растворы добавок необходимо
приготовлять заблаговременно. Комплексные добавки необходимо смешивать
непосредственно перед заливкой в бетоносмеситель или дозировать раздельно.
7.44. При
приготовлении бетонных смесей с воздухововлекающими добавками продолжительность
перемешивания должна быть строго регламентирована. При этом необходимо
систематически контролировать воздухосодержание бетонной смеси.
7.45. Бетонную
смесь необходимо укладывать в соответствии с ППР и технологическим регламентом.
При этом бетонную смесь укладывают в форму или опалубку горизонтальными слоями
без технологических разрывов с направлением укладки в одну сторону во всех
слоях. При значительных площадях поперечного сечения бетонируемой конструкции
допускается укладывать и уплотнять бетонную смесь наклонными слоями, образуя
горизонтальный опережающий участок длиной 1,5 - 2 м в каждом слое. Угол наклона
к горизонту поверхности уложенного слоя бетонной смеси перед ее уплотнением не
должен превышать 30°. После укладки и распределения бетонной смеси по всей
площади укладываемого слоя уплотнение начинают с опережающего участка.
7.46. Бетонную
смесь можно подавать бетононасосами или пневмонагнетателями во все виды
конструкции при интенсивности бетонирования не менее 6 м3/ч, а также в
стесненных условиях и в местах, не доступных для других средств механизации.
7.47. Бетонная
смесь, потерявшая к моменту укладки заданную удобоукладываемость, подаче в
бетонируемую конструкцию не подлежит. Восстанавливать удобоукладываемость
бетонной смеси добавлением воды на месте укладки запрещается. Восстанавливать
удобоукладываемость бетонной смеси на месте укладки допускается добавлением
пластифицирующих добавок или суперпластификаторов при условии, что общее
количество добавок в смеси не будет превышать максимально допустимое
количество, установленное для данного типа добавок под контролем лаборатории.
7.48. Виброрейки,
вибробрусья или площадочные вибраторы могут быть использованы для уплотнения
только бетонных конструкций; толщина каждого укладываемого и уплотняемого слоя
бетонной смеси не должна превышать 25 см.
При бетонировании
железобетонных конструкций поверхностное вибрирование может быть применено для
уплотнения верхнего слоя бетона и отделки поверхности.
7.49. Открытые
поверхности свежеуложенного бетона немедленно после окончания бетонирования (в
том числе и при перерывах в укладке) следует надежно предохранить от испарения
воды. Свежеуложенный бетон должен быть также защищен от попадания атмосферных
осадков. Защита открытых поверхностей бетона должна быть обеспечена в течение
срока, обеспечивающего приобретение бетоном прочности не менее 70%.
7.50. При
бетонировании температуру укладываемой бетонной смеси следует увязывать с
температурой основания (таблица 3).
Таблица 3
┌───────────────────────────────┬─────────────────────────────────────────┐
│Температура
поверхностного слоя│ Допустимая
температура укладываемой │
│жесткого
основания, на которое │бетонной смеси по условию предупреждения │
│ укладывается бетон, °C │ температурных трещин, °C │
├───────────────────────────────┼─────────────────────────────────────────┤
│ 5 │ 10 (не более) │
│ 10 │ 10 - 20 (не более) │
│ 15 - 20 │ 10 - 25 │
└───────────────────────────────┴─────────────────────────────────────────┘
При бетонировании
массивных бетонных и железобетонных конструкций температура основания не должна
превышать 35 °C.
При разработке ППР
по возведению мостов в южных районах страны следует учитывать влияние солнечной
радиации на температурный режим бетона.
Устранение
дефектов, допущенных в ходе строительства, должно осуществляться по специальным
Технологическим регламентам.
7.51. Технические
требования, которые следует выполнять при производстве бетонных работ и
проверять при операционном контроле, а также объем, методы или способы контроля
приведены в таблице 4.
Таблица 4
┌───────────────────────────────────┬──────────────────────┬──────────────┐
│ Технические требования │ Контроль │ Метод
│
│ │ │ или способ
│
│ │ │ контроля
│
├───────────────────────────────────┼──────────────────────┼──────────────┤
│1.
На месте приготовления и укладки│ Не менее чем 2 раза │
Проверка │
│подвижность
смеси не должна │ в смену, а при │по ГОСТ 10181 │
│отличаться
от заданной более чем │
неустойчивой погоде, │с регистрацией│
│на
+/- 15%, а жесткость более чем
│нестабильной влажности│
в журнале │
│на
+/- 20 с │и колебаниях
зернового│ │
│
│состава заполнителей -│ │
│ │ через каждые 2 ч │ │
├───────────────────────────────────┼──────────────────────┼──────────────┤
│2.
Температуры составляющих и
│ Через каждые 4 ч │Регистра- │
│бетонной
смеси не должны отличаться│в зимнее время, 2 раза│ционный, │
│от
расчетной более чем на +2 °C
│ в смену - при │измерительный │
│(воды
и заполнителей при загрузке │ положительных │ │
│в
смеситель, бетонной (растворной) │ температурах воздуха │ │
│смеси
- на выходе из смесителя,
│только бетонной смеси │ │
│бетонной
(растворной) смеси - │ │ │
│на
месте укладки)
│
│ │
├───────────────────────────────────┼──────────────────────┼──────────────┤
│3.
Толщина укладываемого слоя
│ │ │
│бетонной
смеси не должна превышать:│ │ │
│
40 см - при уплотнении на
│ Постоянный │Измерительный,│
│виброплощадках
виброподдонами │ в процессе укладки │
визуально │
│или
гибкими вибросистемами
│ бетона │ │
│
25 см - то же, при бетонировании
│ То же │ То же
│
│конструкций
сложной конфигурации │ │ │
│и
густоармированных │ │ │
│
на 5 - 10 см длины рабочей части
│ " │ " │
│вибратора
при уплотнении тяжелыми │ │ │
│подвесными
вертикально │ │ │
│расположенными
вибраторами │ │ │
│
вертикальной проекции длины
│ " │ " │
│рабочей
части вибратора при │ │ │
│уплотнении
тяжелыми подвесными │ │ │
│вибраторами,
располагаемыми │ │ │
│под
углом до 35 °C к вертикали
│
│ │
│
1,25 длины вибронаконечника
│ " │ " │
│и
40 см - при уплотнении ручными
│
│ │
│глубинными
вибраторами │ │ │
│
25 см - при уплотнении
│ " │ " │
│поверхностными
вибраторами или │ │ │
│вибробрусками
в неармированных │ │ │
│конструкциях
и с одиночной │ │ │
│арматурой │ │ │
│
12 см - в конструкциях с двойной
│ " │ " │
│арматурой │ │ │
├───────────────────────────────────┼──────────────────────┼──────────────┤
│4.
При разделении на блоки
│
│ │
│бетонирования
следует │ │ │
│предусматривать: │ │ │
│
площадь каждого блока - не менее
│ Каждой конструкции │Измерительный,│
│50
м2
│
│регистра- │
│ │ │ционный │
│
высоту блока - не менее 2 м
│ То же │ То же
│
│
площадь рабочих швов блоков -
│ " │ " │
│в
перевязку
│
│ │
├───────────────────────────────────┼──────────────────────┼──────────────┤
│5.
Высоту свободного сбрасывания
│
│ │
│бетонной
смеси следует принимать │ │ │
│не
более, м:
│
│ │
│
2 - при бетонировании армированных│
Постоянный
│Измерительный,│
│конструкций │ │ визуальный
│
│
1 - при изготовлении сборных
│ То же │ То же
│
│железобетонных
конструкций │ │ │
│
6 - при бетонировании
│ " │ " │
│неармированных
конструкций, │ │ │
│устанавливаемых
из условия │ │ │
│обеспечения
однородности бетона │ │ │
│и
сохранности опалубки
│
│ │
└───────────────────────────────────┴──────────────────────┴──────────────┘
8.
Устройство оснований и фундаментов
8.1. Работы по
устройству оснований и фундаментов следует выполнять в соответствии с проектом,
проектом организации строительства и проектом производства работ, составленных
с учетом местных условий и требований СП 45.13330, СП 48.13330, СП 70.13330.
8.2. При приемке
работ по устройству фундаментов разных типов необходимо соблюдать требования
настоящего раздела, используя при этом следующие дополнительные материалы:
а) исполнительные
схемы расположения фундаментов, ростверков, свай и шпунтовых ограждений с
указанием их отклонений в плане и по высоте;
б) сводные
ведомости и журналы погружения свай, свай-оболочек и шпунта, журналы бурения и
бетонирования скважин для буровых свай;
в) результаты
динамических испытаний свай (забивных и вибропогруженных);
г) результаты
статических испытаний свай, свай-оболочек или грунтов (если они были
предусмотрены рабочей документацией);
д) результаты
контроля сплошности бетона буровых столбов неразрушающим ультразвуковым
методом.
8.3. Отступления от
проекта при производстве работ подлежат обязательному согласованию с проектной
организацией.
Устройство свай и
свай-оболочек
8.4. Сваи следует
забивать молотом на проектную глубину до получения расчетного отказа.
Опережающую
разработку песчаных грунтов при устройстве буронабивных свай следует выполнять
на 1 - 2 м ниже ножа оболочки при условии наличия в ее полости избыточного
давления воды, превышающего на 4 - 5 м уровень грунтовых вод в скважине.
8.5. Глубину лидерных
скважин следует принимать равной 0,9 заглубления сваи в грунт, а диаметр - 0,9
диаметра цилиндрической или 0,8 диагонали призматической сваи и уточнять по
результатам пробной забивки.
8.6. Сваи следует
погружать в толщу мерзлых грунтов в лидерные скважины.
Непосредственная
забивка свай допускается в пластичномерзлые глинистые или суглинистые грунты,
не имеющие твердых включений.
Практическую
возможность забивки имеющимся молотом свай и глубину их погружения в
вечномерзлый грунт необходимо устанавливать по результатам пробной забивки в
конкретных местных условиях.
Погружение свай в
предварительно оттаянный грунт допускается при необходимости заглубления их
низа в немерзлый грунт сквозь слой сезонного промерзания, а также в толщу
твердомерзлого песка.
8.7. Сваи-оболочки
в зоне положительных температур грунта и воды (по всей их высоте или только в
нижней части) следует заполнять бетонной смесью после приемки работ по их
погружению, извлечению из полости грунта, зачистки, приемки оснований (в том
числе уширенной полости) и установки, в случае необходимости, арматурного
каркаса.
После вынужденного
перерыва укладку бетонной смеси можно возобновить, если длительность перерыва
не привела к потере подвижности уложенной смеси. В противном случае работу
допускается продолжить после осуществления мер, обеспечивающих качественное
соединение укладываемой смеси с ранее уложенной.
8.8. Работы по
заполнению бетонной смесью полости железобетонных свай в пределах зоны
воздействия знакопеременных температур окружающей среды (воды, воздуха, грунта)
с запасом вниз на диаметр элемента, но не менее 1 м, следует выполнять с
соблюдением специальных требований, указанных в проекте и ППР (в отношении
подбора состава смеси, ее укладки, очистки внутренней боковой поверхности и
др.), направленных на предотвращение появления трещин в бетоне элементов.
8.9. Операционный и
приемочный контроль качества погружения в разные грунты свай и свай-оболочек
следует производить в соответствии с техническими требованиями, приведенными в
таблице 5.
Таблица 5
┌────────────────────────────────────────────┬──────────────┬─────────────┐
│ Технические требования │ Контроль
│ Способ │
│
│ │ контроля
│
├────────────────────────────────────────────┼──────────────┼─────────────┤
│1.
Смещение в плане центров свай и оболочек │ │ │
│от
проектного положения в уровне низа
│ │ │
│ростверка
или насадки не должны превышать:
│ │ │
│
а) для свай квадратного и круглого
│ │ │
│поперечного
сечений размером не более 0,6 м │ │ │
│(стороны
квадрата, меньшей стороны
│ │ │
│прямоугольника
или диаметра) при монолитном │ │ │
│ростверке
или насадке, в долях стороны
│ │ │
│или
диаметра:
│ │ │
│ при расположении их в фундаменте в один │ │ │
│ряд
по фасаду моста:
│ │ │
│ +/- 0,2 - вдоль моста │ Каждой сваи │ Приемочный │
│ +/- 0,3 - поперек моста │ То же │
То же │
│ при расположении свай в два ряда и более │ │ │
│по
фасаду моста:
│ │ │
│ +/- 0,2 для крайних рядов - вдоль моста │
" │ " │
│ +/- 0,3 для средних рядов - вдоль моста │
" │ " │
│ +/- 0,4 - поперек моста │ " │ " │
│
б) для свай квадратного, прямоугольного
│ " │ " │
│и
круглого поперечного сечений размером
│ │ │
│не
более 0,6 м - 5 см (независимо от числа
│ │ │
│рядов)
при сборных ростверках и насадках
│ │ │
│с
обязательным применением направляющих
│ │ │
│устройств
(каркасов, кондукторов, стрел)
│ │ │
│
в) для свай-оболочек диаметром более 0,6 м │ │ │
│до
3 м, погруженных с отклонениями, в долях │ │ │
│диаметра,
не должны превышать:
│ │ │
│ без применения направляющих устройств: │ │ │
│ 0,1 - для одиночных и при расположении │
Каждой │ " │
│в
один ряд по фасаду моста │сваи-оболочки │ │
│ 0,15 - при расположении в 2 ряда и более
│ То же │ " │
│ через направляющий каркас (кондуктор): │ │ │
│ 5 см - на суше │ " │ "
│
│
0,03H - на акватории с глубиной воды H
│ " │ " │
├────────────────────────────────────────────┼──────────────┼─────────────┤
│2.
Смещение осей закрепленного направляющего│ │ │
│каркаса
от проектного положения в уровне его│ │ │
│верха:
│ │ │
│
2,5 см - на суше
│ Каждой │ Приемочный │
│
│сваи-оболочки │
│
│
0,015H - на акватории глубиной воды H
│ То же │
То же │
├────────────────────────────────────────────┼──────────────┼─────────────┤
│3.
Отклонения (уменьшение) от проектной
│ │ │
│глубины
(с учетом местного размыва) глубины │ │ │
│погружения
свай и свай-оболочек на величину │ │ │
│не
менее 4 м:
│ │ │
│
а) свай (при условии обеспечения
│ │ │
│предусмотренной
проектом несущей способности│
│ │
│по
грунту) длиной, м:
│ │ │
│ до 10 - 25 см │ Каждой
сваи │ Измерение
│
│
│ │ лентой
│
│
│
│возвышающейся│
│
│ │ части
свай │
│ 10 и более - 50 см │ То же
│ То же │
│
б) свай-оболочек разной длины - 25 см
│ Каждой │
" │
│
│ оболочки │ │
├────────────────────────────────────────────┼──────────────┼─────────────┤
│4.
Уточнение несущей способности свай
│ │ │
│и
свай-оболочек, погруженных в немерзлые
│ │ │
│грунты,
по результатам испытаний:
│ │ │
│
а) свай:
│ │ │
│ по проекту фундаментов динамической │
Несущей │ Проверка
│
│нагрузкой │
способности │по ГОСТ 5686 │
│ │ │ (не менее
│
│
│ │ 3
испытаний │
│
│ │ в каждом
│
│
│ │ ростверке) │
│ то же, вдавливающей статической нагрузкой
│ То же │
То же, │
│
│ │ не менее
│
│
│ │ 2
испытаний │
│
│ │на
сооружение│
│ "
, выдергивающей статической нагрузкой│ " │ " │
│
б) свай-оболочек (или буровых свай):
│ │ │
│ по проекту фундаментов вдавливающей │
Несущей │Операционный
│
│статической
нагрузкой │
способности │по ГОСТ 5686 │
│
│ │ (не менее
│
│
│ │ 2 испытаний │
│
│ │ на 1
мост) │
│ то же, выдергивающей статической
нагрузкой│ То же │
То же, │
│
│ │ не менее
│
│ │ │ 2 испытаний │
│ "
, штампом грунта в основании свай-
│ " │Операционный │
│оболочек
(или буровых свай)
│ │по
ГОСТ 5686 │
│ │ │ (не менее
│
│
│ │ 1
испытания │
│
│ │ на
│
│
│ │ 1 ростверк)
│
├────────────────────────────────────────────┼──────────────┼─────────────┤
│5.
Уточнение несущей способности свай
│ │ │
│и
свай-оболочек (или буровых свай),
│ │ │
│погруженных
в вечномерзлые (за исключением
│ │ │
│твердомерзлых)
грунты, по результатам │ │ │
│испытаний: │ │ │
│
по проекту фундамента вдавливающей
│В
соответствии│Операционный │
│статической
нагрузкой │с
требованиями│по ГОСТ 5686 │
│
│ проекта, │ │
│
│ но не менее │ │
│
│ 1 испытания │ │
│
│ на 1 мост │ │
│
то же, выдергивающей статической нагрузкой │ То же
│ То же │
│ "
, штампом грунта в основании оболочки │ " │Операционный │
│
│ │по
ГОСТ 5686 │
├────────────────────────────────────────────┴──────────────┴─────────────┤
│ Примечания.
1. Значения допускаемых
отклонений от проектного│
│положения
в плане приведены для свайных элементов (свай и свай-оболочек),│
│используемых
в фундаментах и безростверковых
опорах с бетонируемым
на│
│месте
соответственно ростверком или насадкой.
В приведенные значения│
│допускаемых
отклонений от проектного положения в плане свайных элементов│
│включены
значения смещения их
в уровне низа
ростверка или насадки│
│вследствие
отклонения элементов от вертикали или изменения наклона. │
│ Значения
допускаемого изменения тангенса
угла от вертикали
(от│
│проектного
положения) наклонных свайных
элементов не должно
превышать│
│200:1
при расположении их в один ряд и 100:1 - в два ряда и более. │
│ 2. Для фундаментов и безростверковых опор
со сборными ростверком или│
│насадкой,
соединяемых со свайными элементами
с помощью омоноличенных│
│бетоном выпусков
стержней продольной арматуры,
значения допускаемых│
│отклонений
в плане от проектного положения
свайных элементов в
уровне│
│низа
ростверка или насадки следует принимать до 5 см. │
│ При сборных ростверке или насадке,
соединяемых со сваями или сваями-│
│оболочками сварными
болтовыми комбинированными стыками,
значения│
│допускаемых
отклонений принимают в соответствии с проектом. │
│ 3. Число
свайных элементов с
предельными значениями допускаемых│
│отклонений
не должно превышать 25% для однорядных фундаментов или опор и│
│40%
- для двух- и многорядных фундаментов. │
│ 4. При фактических отклонениях
свайных фундаментов от
проектного│
│положения, превышающих
предельно допускаемые значения,
решение о│
│возможности использования
элементов должна принимать
организация,│
│проектировавшая
фундаменты или безростверковые опоры. │
└─────────────────────────────────────────────────────────────────────────┘
Устройство буровых
свай
8.10. Для крепления
стенок скважин допускается использовать избыточное давление воды или глинистый
раствор.
8.11. В целях
предотвращения подъема и смещения в скважине арматурного каркаса укладываемой
бетонной смесью или в процессе извлечения бетонолитной инвентарной обсадной
трубы, а также во всех случаях армирования не на полную глубину буровой сваи в
конструкции каркаса необходимо предусмотреть фиксаторы для закрепления его в
проектном положении.
8.12. При
устройстве буронабивных свай забой скважины перед началом укладки бетонной
смеси должен быть очищен от грунтового шлама. При укладке бетонной смеси в
обводненных скважинах следует выдерживать минимальный временный диапазон между
временем зачистки забоя и началом бетонирования, установленный технологическим
регламентом.
Уплотнение
несвязных грунтов забоя скважины может выполняться методом виброштампования, в
том числе с добавлением жестких материалов (щебень, жесткая бетонная смесь и
т.п.). Требование к оборудованию и материалам, параметры виброштампа, величина
"отказа" устанавливаются в проекте и ППР.
8.13. Сухие
вертикальные скважины в песках, обсаженные стальными трубами или
железобетонными оболочками, а также необсаженные скважины, пробуренные в
пластах суглинков и глин, расположенных выше уровня подземных вод и не имеющих
прослоек и линз несвязанных и слабосвязанных толщиной более 20 см песков и супесей,
допускается бетонировать без применения бетонолитных труб способом свободного
сброса бетонной смеси с высоты до 6 м. Допускается укладывать бетонную смесь
способом свободного сброса с высоты до 40 м с заранее установленным арматурным
каркасом при наличии бункера с направляющим патрубком длиной не менее 3 м.
Бетонную смесь при этом используют с подвижностью 3 - 6 см. Чем глубже
скважина, тем меньше подвижность. Не допускается остаточный слой воды на забое
толщиной более 10 см.
Не допускается
укладка бетонной смеси способом свободного сбрасывания в наклонные и
обводненные скважины, заполненные водой. Бетонную смесь в них следует
укладывать способом вертикально перемещаемой трубы (ВПТ) или бетононасосами.
Во избежание
расслоения бетонной смеси не допускается попадание ее на арматурный каркас и
стенки скважины.
8.14. При
бетонировании как сухих, так и обводненных скважин с целью обеспечения
сплошности, прочности бетона свай, качества контакта бетона с грунтом на
боковой поверхности сваи может быть применен способ виброукладки и
виброштампования бетонной смеси. В процессе бетонирования необходимо на всех
этапах контролировать уровень бетонной смеси в скважине и заглубление
бетонолитной трубы в бетонную смесь (при бетонировании методом ВПТ). При этом
должна быть обеспечена целостность стенок скважины. Работы по виброуплотнению и
виброштампованию следует выполнять с соблюдением специальных требований,
указанных в проекте и ППР (требования к оборудованию, составу и технологии
укладки бетонной смеси и др.).
8.15. Операционный
и приемочный контроль качества устройства буровых свай следует осуществлять в
соответствии с техническими требованиями, указанными в таблице 6.
Таблица 6
┌──────────────────────────────────┬─────────────────┬────────────────────┐
│ Допускаемые отклонения │
Контроль │ Способ контроля │
├──────────────────────────────────┼─────────────────┼────────────────────┤
│1.
От проектного положения в
│
│ │
│плане,
в долях d, верха и наклона │ │ │
│оси
(tg альфа) буровых свай:
│
│ │
│
при расположении их в один ряд
│
│ │
│по
фасаду моста:
│
│ │
│ +/- 0,04; 1:200 - в пределах │
Каждой сваи │ Приемочный │
│акватории │ │ (измерения │
│ │ │теодолитом, отвесом
│
│ │ │ или лентой) │
│ +/- 0,02; 1:200 - на суше │ То же
│ То же │
│
при расположении свай в два ряда │ │ │
│и
более по фасаду моста:
│ │ │
│ +/- 0,1; 1:100 - в пределах │ " │ " │
│акватории │ │ │
│ +/- 0,05; 1:100 - на суше │ " │ " │
├──────────────────────────────────┼─────────────────┼────────────────────┤
│2.
Фактических размеров скважины
│
│ │
│от
проектных и уширенной полости
│
│ │
│(уширения),
см: │ │ │
│
+/- 25 - по глубине скважины │
Каждой скважины │
Операционный │
│(по
отметке ее забоя)
│
│ (измерения │
│ │ │по указаниям
проекта│
│ │ │ фундамента) │
│
+/- 5 - по диаметру скважины
│ То же │ То же │
│
+/- 10 - по глубине расположения │Каждого уширения │ " │
│низа
цилиндрической части уширения│ │ │
│
+/- 10 - по диаметру уширения
│ То же │ " │
│
+/- 5 - по высоте цилиндрической │
" │ " │
│части
уширения │ │ │
├──────────────────────────────────┼─────────────────┼────────────────────┤
│3.
От проектного положения
│
│ │
│элементов
арматурного каркаса │ │ │
│буровой
сваи, см: │ │ │
│
+/- 1 взаимного расположения │
Каждого каркаса │
Операционный │
│продольных
стержней по периметру │ │(измерения стальной
│
│каркаса │ │ лентой и линейкой)
│
│
+/- 5 длины стержней
│ То же │ То же │
│
+/- 2 шага спирали
│ " │ " │
│
+/- 10 расстояний между кольцами │
" │ " │
│жесткости │ │ │
│
+/- 10 расстояний между
│ " │ " │
│фиксаторами
защитного слоя │ │ │
│
+/- 1 высоты фиксаторов
│ " │ " │
│
+/- 2 диаметра каркаса в местах
│ " │ " │
│расположения
колец жесткости │ │ │
├──────────────────────────────────┼─────────────────┼────────────────────┤
│4.
Параметров бетонной смеси
│
│ │
│с
подвижностью П4 для подводной
│
│ │
│укладки
ее в скважины методом ВПТ:│
│ │
│
+/- 2 см подвижности
│ ГОСТ 10181 │
Операционный, │
│ │ │ проверка │
│ │ │ по ГОСТ 10181 │
│
+/- 2% водоотделения
│ То же │ То же │
├──────────────────────────────────┼─────────────────┼────────────────────┤
│5.
Показатели бетона свай:
│
│ │
│
не допускается нарушение │
Каждая свая │ Неразрушающий │
│сплошности │ (столб)
│ ультразвуковой │
│ │в
безростверковых│ метод. │
│
│опорах; не менее │ В
исключительных │
│ │ 15% свай
│ случаях - │
│ │ (столбов)
│ сейсмоакустическим │
│ │ в ростверке
│ методом │
│ │ каждой опоры
│ (при невозможности │
│ │(но не
менее 2 - │ контроля │
│ │ в ростверке)
│ ультразвуковым │
│ │ │ методом) │
│
+20; -5% прочности
│ То же │Испытания 6 образцов│
│ │ │из выбуренных
кернов│
│ │ │ сваи │
└──────────────────────────────────┴─────────────────┴────────────────────┘
Устройство
фундаментов мелкого заложения
8.16. Допускаемый
перерыв между окончанием разработки котлована и устройством фундамента следует
устанавливать в проекте, причем он не должен превышать двух суток. При
вынужденных сверх установленного срока перерывах должны быть приняты меры к
сохранению природных свойств грунта основания. Дно котлована до проектных
отметок (на 5 - 10 см) необходимо зачищать непосредственно перед устройством
фундамента.
8.17. До устройства
фундаментов должны быть выполнены работы по отводу поверхностных и подземных
вод от котлована. Способ удаления воды из котлована (открытый водоотлив или
дренаж, водопонижение и др.) должен быть выбран с учетом местных условий и
согласован с проектной организацией. При этом должны быть предусмотрены меры
против выноса грунта из-под возводимых и существующих сооружений, а также
против нарушения природных свойств грунтовых оснований.
При выполнении
работ без водоотлива в шпунтовом ограждении на принятое грунтовое основание
следует укладывать подводным способом тампонажную бетонную подушку, толщина
которой устанавливается в проекте, но не должна быть менее 1 м.
8.18. Разработку
грунта в котлованах следует вести методами, не допускающими ухудшения природных
свойств грунта, принятого в проекте в качестве естественного основания
фундамента мостового сооружения.
До начала работ по
устройству фундаментов подготовленное основание должно быть принято по акту
комиссией с участием заказчика и представителя строительной организации, а при
необходимости - представителя проектной организации и геолога.
Комиссия должна
установить соответствие фундамента проекту: расположение, размеры, отметку дна
котлована, фактическое напластование и свойства грунтов, а также возможность
заложения фундамента на проектной или измененной отметке.
Проверки для
установления отсутствия нарушений природных свойств грунтов оснований следует,
при необходимости, сопровождать отбором образцов для лабораторных испытаний,
проведением зондирования или штамповых испытаний основания.
В случае если
комиссией установлены значительные расхождения между фактическими и проектными
характеристиками грунтов основания и возникла в связи с этим необходимость
пересмотра проекта, решение о проведении дальнейших работ следует принимать при
обязательном участии представителей проектной организации и заказчика, кроме
того, для вечномерзлых грунтов следует выполнить проверку их температурного
состояния и в случае оттаивания грунта в процессе производства работ проектной
организации следует оценить осадку основания.
При возведении
монолитных фундаментов под них следует устраивать подготовку из уплотненного
слоя щебня или тощего бетона, обеспечивающую надежную установку арматуры и не допускающую
утечки раствора из бетонной смеси бетонируемого фундамента.
До устройства
фундамента на тампонажной подушке ее поверхность следует подготовить по
указаниям в проекте.
Установка блоков
фундамента и (или) укладка бетона на основание, покрытое водой, снегом или
льдом, не допускается.
8.19. Блоки сборных
фундаментов следует укладывать на тщательно выровненное песчаное основание или
песчано-цементную подушку толщиной не менее 5 см (на глинистых грунтах
основания).
Случайные переборы
грунта в отдельных местах должны быть заполнены тем же грунтом, доведенным до
естественной плотности.
8.20. Если грунты
основания должны быть сохранены в вечномерзлом состоянии (принцип I), то разработку
котлованов и устройство фундаментов следует выполнять при устойчивой
среднесуточной температуре воздуха ниже 0 °C. В случае разработки котлованов
при температуре выше 0 °C необходимо принять меры по защите основания от
оттаивания. Производить обогрев возводимых фундаментов способами, которые могут
вызвать оттаивание грунта основания, запрещается.
Если грунты
основания используются в оттаявшем состоянии (принцип II), то разработка
котлована может производиться в любое время года. При этом не должно допускаться
промерзание пучинистых грунтов.
8.21. Приемочный
контроль качества работ следует осуществлять согласно техническим требованиям,
указанным в таблице 7.
Таблица 7
┌──────────────────────────────────────────┬───────────┬──────────────────┐
│ Допускаемые отклонения │ Контроль │ Способ контроля │
├──────────────────────────────────────────┼───────────┼──────────────────┤
│Фактических
размеров и положения
│ │ │
│забетонированных
на месте (и сборных) │ │ │
│фундаментов
и ростверков от проектных, см:│
│ │
│
+/- 5 (+/- 2) размеров в плане
│ Каждого │
Приемочный │
│
│фундамента │ (измерения │
│
│и ростверка│теодолитом, лентой│
│
│ │ и линейкой) │
│
+2; -0,5 (+1; -0,5) толщины защитного
│ То же │
То же │
│слоя │ │ │
│
+/- 2 (+/- 1) положения по высоте верха
│ " │ " │
│(обреза)
фундамента или ростверка
│ │ │
│
2,5 (1) положения в плане относительно │
" │ " │
│разбивочных
осей
│ │ │
├──────────────────────────────────────────┴───────────┴──────────────────┤
│ Примечание. Значения, приведенные в
таблице в скобках,
относятся│
│к
сборным фундаментам и ростверкам. │
└─────────────────────────────────────────────────────────────────────────┘
В процессе
устройства фундаментов необходимо контролировать:
обеспечение
необходимых недоборов грунта в котловане, недопущение переборов и нарушений
структуры грунта основания;
недопущение
нарушений структуры грунта во время срезки недоборов, подготовки оснований и
укладки блоков фундаментов;
предохранение
грунтов в котловане от подтапливания подземными или поверхностными водами с
размягчением и размывом верхних слоев основания;
соответствие
характеристик вскрытых грунтов основания предусмотренным в проекте;
достаточность
примененных мер по защите грунта основания от промерзания в период от вскрытия
котлована и до окончания возведения фундамента;
соответствие
фактической глубины заложения и размеров фундамента, а также его конструкции и
качества примененных материалов предусмотренным в проекте.
9.
Сооружение железобетонных и бетонных мостов, труб
и конструкций из
полимерных композитных материалов (ПКМ)
9.1. При сооружении
железобетонных и бетонных мостов и труб следует соблюдать требования СП
70.13330, СП 130.13330, а также требования настоящего свода правил, включая
Приложения В, Г, Д, Е, Ж, И, отражающие особенности работ при сооружении мостов
и труб.
9.2. На период
выполнения монтажных работ по навесной сборке, подъемке, надвижке, перекатке,
перевозке и установке на плаву пролетных строений организацией, осуществляющей
строительство моста, должен назначаться ответственный за выполнение монтажных
работ.
9.3. Монтаж сборных
конструкций допускается начинать только после инструментальной проверки отметок
и положения в плане опор, фундаментов и временных устройств для монтажа, а
также выполнения разбивочных работ, определяющих проектное положение
монтируемых конструкций, с оформлением результатов проверки актом.
На опорах моста до
начала монтажа пролетных строений должны быть размечены оси опорных частей.
Инструментальный
контроль за сборкой конструкций должен осуществляться систематически - от
начала сборки до полного ее завершения. В процессе сборки следует проверять:
правильность положения установленных секций или блоков, совпадение фиксаторов,
закладных деталей, отверстий, каналов и элементов конструкций в стыках и
соединениях.
9.4. Геодезическую
проверку положения пролетного строения в плане и профиле необходимо производить
после сборки каждой панели (установки блока) или бетонирования захватки. При
геодезической проверке следует учитывать осадку опор в процессе строительства,
а в необходимых случаях - возможность появления временных деформаций от
неравномерного нагрева конструкции.
В процессе
продольной надвижки (поперечной перекатки) необходимо вести постоянный
геодезический контроль за положением пролетного строения и опор (пирсов). В
установленных проектом случаях следует контролировать напряженное состояние
элементов.
9.5. При монтаже
конструкций необходимо соблюдать следующие общие требования:
а) монтажные краны
устанавливать в местах, определенных ППР и размеченных в натуре. Прикрепление к
смонтированным конструкциям грузоподъемных приспособлений, оттяжек и отводных
блоков в местах, не предусмотренных проектом производства работ, запрещается;
б) снимать с
подмостей пролетные строения, раскружаливать их, замыкать шарниры и
регулировать опорные реакции или напряжения - в соответствии с техническими
требованиями, изложенными в рабочей документации;
в) сборку объемных
конструкций из плоских элементов (плит) производить с применением кондукторов
или других элементов, обеспечивающих проектную форму поперечного сечения и
продольного очертания, а также заданную толщину стыков;
г) удалять элементы
соединения и усиления только при отсутствии в них усилий.
9.6. Все
конструкции и их детали до монтажа или укрупнения перед монтажом должны быть
освидетельствованы. При обнаружении дефектов комиссия решает вопрос об их
устранении.
На элементы,
подлежащие монтажу, должны быть нанесены: номер и масса монтажной марки, центр
тяжести элемента, место строповки, а также контрольные осевые и нивелировочные
знаки.
9.7. Контактные
поверхности блоков железобетонных пролетных строений до подачи на монтаж или
перед укрупнительной сборкой должны быть обработаны пескоструйным способом или
щетками. Насечка стыкуемых поверхностей ударным инструментом запрещается.
Очищенные
поверхности элементов должны быть освидетельствованы и приняты.
Контактные
поверхности блоков пролетных строений из ПКМ перед укрупнительной сборкой
должны быть обработаны и подготовлены к сборке методами и приемами,
оговоренными в регламенте на проведение сборочных работ.
9.8. Строповочные
петли на соприкасающихся поверхностях (торцах) звеньев сборных железобетонных
труб перед монтажом последующего блока должны быть срезаны заподлицо с
поверхностью бетона; срубка петель зубилом или их загиб не допускаются.
9.9. Способы
опирания и крепления конструкций на транспортных средствах не должны вызывать
остаточных деформаций в конструкциях; торцевые поверхности блоков составных по
длине конструкций и изолированные поверхности должны быть предохранены от
повреждения.
Крупногабаритные
балки, сборные элементы пролетных строений и опор, а также предварительно
напряженные железобетонные конструкции следует перевозить в соответствии с
требованиями специально разработанных проектов или технических условий.
Установленные на
транспортные средства конструкции должны быть надежно закреплены от воздействия
ветровых, динамических и центробежных нагрузок. При этом необходимо
обеспечивать установленные габариты, свободное прохождение груза на кривых
участках пути, подвижность одного из концов конструкции в случае погрузки
конструкций на сцеп, а также устойчивость плавучих транспортных средств.
Устройство
монтажных соединений конструкций мостов
9.10. Арматурные
выпуски и закладные изделия необходимо сваривать после закрепления сборных
элементов в проектном положении.
Порядок сварочных
работ должен соответствовать указаниям проекта, требованиям СП 70.13330 и
обеспечивать наименьшие значения реактивных напряжений от сварки.
Способы выправки
погнутых арматурных выпусков должны исключать их излом и нарушение бетона
защитного слоя.
Омоноличивание
стыков допускается только после приемки сварочных и арматурных работ и
устранения выявленных дефектов.
Продольные стыки
между отдельными балками (плитами), а также стыки диафрагм разрезных пролетных
строений следует омоноличивать после установки балок на постоянные опорные
части. Порядок омоноличивания стыков неразрезных и температурно-неразрезных
пролетных строений устанавливается ППР.
9.11. Образующие
стык поверхности элементов до укладки бетона или раствора следует промыть и
обильно увлажнить.
9.12. Составы клеев
следует предварительно подбирать в построечной лаборатории с соответствующим
контролем качества составляющих материалов. При этом необходимо контролировать
модуль упругости и коэффициент Пуассона клеев. Соответствие подобранного
состава клея требованиям проекта необходимо дополнительно проверять испытанием
образцов (клееных кубиков) на сдвиг по клеевому шву.
При низких
положительных и отрицательных температурах следует пользоваться клеевыми
компонентами, способными отверждаться при отрицательных температурах без
специального обогрева клееных стыков.
Обогрев клееных
стыков допускается любым способом, соответствующим технологии монтажа и
обеспечивающим температурный режим, исключающий возникновение в конструкции
опасных температурных и химических воздействий на материал монтируемой
конструкции.
Клеи, наносимые на
увлажненные бетонные поверхности, или бетон, имеющий отрицательную температуру,
должны в своем составе иметь фуриловый спирт.
9.13. Клей следует
наносить на обе стыкуемые бетонные поверхности. При этом он не должен сплывать
с вертикальных поверхностей и должен иметь толщину наносимого слоя, достаточную
для получения плотного сплошного клеевого шва при обжатии стыка с образованием
валика по его контуру.
Клееный стык
следует обжимать сразу после нанесения клея. Для кратковременного обжатия
клееного стыка следует использовать преимущественно часть рабочей напрягаемой
арматуры или специальные инвентарные устройства, создающие равномерное по
сечению обжатие клееного шва с созданием в нем напряжений 0,05 - 0,2 МПа (0,5 -
2 кгс/см2).
При необходимости
выправки профиля и положения собираемой конструкции в плане допускается по
согласованию с проектной организацией устраивать до 15% клиновидных клееных
стыков с наибольшей толщиной шва 5 мм (в опорах - 10 мм). Клиновидные стыки
следует выполнять при положительной температуре отверждения клея в стыке до
проектной прочности (зимой только с обогревом клееного шва).
Применение в
клиновидных стыках клеев с ускорителями отверждения (зимние клеи) не
допускается.
При склеивании
составных по высоте опор допускается наносить клей на одну склеиваемую
поверхность и обжимать клееный шов последовательно устанавливаемыми блоками.
Сборку пролетных
строений из ПКМ следует проводить в строгом соответствии с утвержденным
регламентом по монтажу.
9.14. Затяжку
болтовых соединений следует проводить динамометрическими ключами с моментом
затяжки, установленным в проектной документации для данного болтового
соединения. Натяжение болтов необходимо производить от участков с плотным
прилеганием деталей соединяемого пакета к участкам с зазорами. В соединениях с
затянутыми болтами не допускаются зазоры между плоскостью конструкции, шайбами,
гайками и головками болтов.
При натяжении
болтов недопустима их перетяжка гайковертами. При этом должна обеспечиваться
возможность дотягивания болтов динамометрическими ключами путем поворота гайки
на угол до 30 - 60 градусов.
9.15. При
окончательной сборке узла, подвергаемого сверлению на месте монтажа и
состоящего из нескольких деталей, включая металлические, необходимо удалить
заусенцы на деталях, продукты сверления, стружку сухой салфеткой или
промышленным пылесосом. На механически обработанные поверхности наносится
защитное покрытие и затем производится сборка узла.
9.16. При сборке
элементов настила или установке съемных технологических плит настила необходимо
производить герметизацию стыков. Нанесение герметика на поверхности деталей и
их сборка должны быть выполнены в течение периода сохранения жизнеспособности
(скорость образования пленки) герметика. Герметик должен плотно прилегать к
поверхности, полностью заполнять углы и перекрывать кромку шва на 8 - 10 мм в
каждую сторону.
В зимний период
допускается организовать местный обогрев стыковых соединений способом,
соответствующим технологии монтажа и обеспечивающим температурный режим,
исключающий возникновение в конструкции опасных температурных и химических
воздействий на материал конструкции.
9.17. Технические
требования, которые следует выполнять при производстве работ по устройству
монтажных соединений и проверять при операционном контроле, а также объем,
методы или способы контроля приведены в таблице 8.
Таблица 8
┌───────────────────────────────────────┬────────────┬────────────────────┐
│ Технические требования │ Контроль
│ Метод или способ │
│ │ │ контроля │
├───────────────────────────────────────┼────────────┼────────────────────┤
│1.
Допустимое взаимное положение
│ │ │
│элементов
сборных железобетонных │ │ │
│конструкций,
соединяемых бетонируемыми │
│ │
│стыками: │ │ │
│
а) смещение наружных граней смежных
│ Всех │
Измерительный │
│стыкуемых
элементов 5 мм │
соединений │(измерение линейкой,│
│
│ │ визирование │
│
│ │ теодолитом │
│ │ │ или отвесом) │
│
б) отклонения осей стоек высотой H, м,│ │ │
│от
проектного положения в верхнем
│ │ │
│сечении,
мм:
│ │ │
│ до 4,5 - 10 │ Всех стоек
│ Измерительный │
│
│ │ (визирование │
│
│ │ теодолитом │
│ │ │ или отвесом) │
│ от 4,5 до 15 - 15 │ То же
│ То же │
│ св. 15 - 0,001H, но не более 35 │ "
│ " │
│
в) отклонения отметок верха стоек,
│ Всех │
Измерительный │
│колонн,
ригелей +/- 10 мм │
элементов │ (нивелирование) │
│
г) отклонения толщины швов между
│ │ │
│элементами
сборных конструкций, мм: │ │ │
│
+/- 10 - тонких швов толщиной от 20 │Всех стыков │ Измерительный │
│до
30 мм
│
│(измерение линейкой)│
│ +/- 20 - толстых швов толщиной 70 │
То же │ То же │
│и
более │ │ │
├───────────────────────────────────────┼────────────┼────────────────────┤
│2.
Допускаемая прочность бетона
│ │ │
│и
раствора омоноличивания стыка:
│ │ │
│
а) ко времени снятия кондукторов,
│ │ │
│временных
связей и распалубки не менее │
│ │
│15
МПа (150 кгс/см2)
│ │ │
│
б) перед раскружаливанием
│ │ │
│и
загружением монтажной или
│ │ │
│эксплуатационной
нагрузкой прочность │ │ │
│должна
соответствовать указанной │ │ │
│в
проекте для данной стадии работ
│ │ │
│
в) к моменту замораживания:
│ │ │
│ в конструкции обычного исполнения - │
100% │ Проверка │
│не
менее 70% проектной
│ │ по ГОСТ 10181 │
│ в конструкциях, предназначенных │ │ │
│к
эксплуатации в районах со средней
│ │ │
│температурой
наружного воздуха наиболее│
│ │
│холодной
пятидневки с обеспечением 0,92│
│ │
│ниже
минус 40 °C, - не менее 100%
│ │ │
│проектной,
а для бетонов с │ │ │
│воздухововлекающими
добавками - │ │ │
│не
менее 80%
│ │ │
├───────────────────────────────────────┼────────────┼────────────────────┤
│3.
Допускаемый тепловой режим выдержки │ │ │
│бетона
(раствора) омоноличивания стыка:│ │ │
│
а) температура стальных и
│ Перед │
Измерительный │
│сталежелезобетонных
конструкций перед │ началом
│ (измерение │
│укладкой
омоноличивающих смесей не ниже│
работ │ термометрами │
│5
°C
│ │или
термодатчиками) │
│
б) скорость изменения температуры при │
То же │ То же │
│нагреве
и остывании бетона или раствора│ │ │
│омоноличивания
5 - 7 °C/ч │ │ │
├───────────────────────────────────────┼────────────┼────────────────────┤
│4.
Допускаемое соединение сборных
│ │ │
│элементов
склеиванием: │ │ │
│
а) при склеивании на бетонных
│ Всех │
Визуальный │
│поверхностях
не допускается наличие
│склеиваемых │
(проверка │
│льда,
пыли, грязи и масляных пятен
│поверхностей│ под
микроскопом │
│
│ │ типа
МПБ-2, щупом, │
│
│ │ линейкой) │
│
б) для клееных плотных (обжимаемых)
│ Каждого │
То же │
│стыков
средняя толщина шва по
│ стыка │ │
│измерениям
(не менее чем в 4 точках │ │ │
│по
периметру сечения конструкции)
│ │ │
│должна
быть не более 3 мм
│ │ │
│
в) модуль упругости клея - 1500 МПа
│ Каждой │Визуальный (проверка│
│(15000
кгс/см2) │ партии
│ клея на образцах │
│
│подобранного│ клея
размером │
│
│состава клея│ 2 x
2 x 8 см │
│
│ │ при скорости их │
│
│ │ нагружения │
│
│ │ 0,2 - 0,4 МПа/с) │
│
г) коэффициент Пуассона - 0,25
│ То же │ То же │
└───────────────────────────────────────┴────────────┴────────────────────┘
Инъецирование
закрытых каналов
Общие положения
9.18. Инъецирование
закрытых и заполнение открытых каналов должна осуществлять специализированная
производственная бригада.
Инъецировать
закрытые и заполнять открытые каналы следует непосредственно за натяжением
группы или всех напрягаемых арматурных элементов монтируемой конструкции.
9.19. Допускаемые
сроки нахождения напрягаемых арматурных элементов без специальной защиты в
каналах до их заполнения инъекционным раствором (если иное не предусмотрено
проектом или технологическим регламентом) не должны превышать: для напрягаемых
элементов из параллельных проволок 30 сут, для канатов 15 сут.
Нахождение
напрягаемой арматуры в каналах при любом способе временной защиты арматуры от
коррозии более 8 мес не допускается.
9.20. Инъекционный
раствор должен быть приготовлен в двухъемкостных механических мешалках,
снабженных растворонасосами для нагнетания раствора. Для нагнетания раствора
следует применять растворонасосы ограниченной производительности с максимальным
давлением до 1,5 МПа (15 кгс/см2), обеспечивающие заполнение каналов со
скоростью 3 - 4 пог. м/мин и его опрессовку давлением не менее 0,6 МПа (6
кгс/см2). Использовать для инъецирования пневматические установки запрещается.
Шланг инъекционной
установки
для подачи раствора в каналы должен
выдерживать давление 1,2 МПа (12 кгс/см2). Напорная магистраль должна быть
снабжена запорными кранами на входе и выходах раствора из канала. На
дополнительных отводах предусматривают штуцера для установки манометров,
контролирующих давление опрессовки раствора (также манометром должен быть
снабжен растворонасос).
Диаметры
наконечника шланга насоса и отводных (промежуточных) трубок должны быть не
менее 14 мм. Диаметр отверстия в анкере, через которое инъецируют раствор,
должен быть не менее 16 мм.
9.21. Инъекционный
раствор следует нагнетать без перерыва в промытые и заполненные водой каналы.
Каналы длиной до 45
пог. м допускается инъецировать без заполнения водой.
Каналы длиной до 85
пог. м, в стесненных условиях производства работ, допускается инъецировать
частично заполненными водой путем введения непосредственно перед инъецированием
авангардной дозы воды объемом не менее 100 л с пластифицирующими добавками.
9.22. На момент
(период) времени проведения работ по инъецированию каналов температура на
открытом воздухе должна находиться в диапазоне значений от +5 °C до +25 °C.
9.23. На момент
замораживания инъекционного раствора его прочность должна быть не ниже 20 МПа
(200 кгс/см2).
9.24. Для
инъекционных растворов следует применять непластифицированный портландцемент
марки не ниже 500 с нормированным минералогическим составом (ГОСТ 10178) с
содержанием
не более 8%, без минеральных добавок (Д0).
Для инъекционных
растворов следует применять портландцементы с минимальной величиной нормальной
густоты цементного теста, не более 25,5%.
9.25. Период
времени с момента изготовления партии цемента до его использования в растворах
должен быть не более 60 сут, но не менее 7 сут. Перед использованием цемента
следует провести его пробный рассев. При содержании в цементе твердых включений
размером более 1,0 мм он подлежит просеиванию на сите с ячейкой 0,55 - 1,0 мм.
9.26. Допускается
применение в инъекционных растворах добавок или специальных цементов, в том
числе зарубежного производства, использованных при инъецировании каналов в
мостах со сроком эксплуатации не менее 10 лет, или допущенных к применению в
этой области национальными стандартами или прошедших испытания на отсутствие
негативного влияния на коррозионную стойкость напрягаемой арматуры.
9.27. Инъекционный
раствор должен иметь следующие потребительские свойства:
текучесть
инъекционного раствора, которая характеризует его подвижность, сразу после его
приготовления должна быть в пределах 20 - 40 с и не более 80 с на момент
времени окончания инъецирования канала (при дополнительном перемешивании перед
определением значения текучести);
величина оседания,
характеризуемая уменьшением объема раствора в канале (образование пазухи), не
должна превышать 2% первоначального объема раствора;
значения прочности
инъекционного раствора на сжатие должны быть на 7-е сутки - не менее 20 МПа
(200 кгс/см2), а на 28-е сутки - не менее 30 МПа (300 кгс/см2);
раствор должен быть
морозостойким.
При инъецировании
каналов с бетонными стенками морозостойкость проверяют для растворов с
водоцементным отношением более чем 0,45 и только в случаях, когда инъецирование
выполняют в период низких температур (ниже +5 °C).
При заполнении
каналов с металлическими стенками или стенками из полимерных материалов
морозостойкость определяют для составов с водоцементным отношением более чем
0,4 независимо от сезона выполнения работ.
9.28. Прочность
инъекционного раствора определяют путем испытания стандартных образцов-кубов
размером 10 x 10 x 10 см на сжатие по ГОСТ 10178 с масштабным коэффициентом,
равным 1.
9.29.
Морозостойкость инъекционных растворов проверяют путем измерения деформаций
удлинения контрольных образцов - призм (цилиндров) после их замораживания при
температуре минус 25 °C на момент достижения раствором прочности на сжатие,
равной 20 МПа (200 кгс/см2). Твердение контрольных образцов до начала испытания
осуществляется при нормальных условиях выдерживания. Инъекционный раствор
считается прошедшим испытания, если длина образцов после замораживания не
превышает их длину до замораживания.
9.30. Подбор
состава инъекционного раствора осуществляется лабораторией не менее чем за 10
сут до начала производства инъекционных работ. При этом используют те же
растворомешалки, что и при инъецировании.
9.31. Не позже, чем
за сутки до начала инъецирования следует произвести промывку каналов для
выявления их проходимости и герметичности путем заполнения их водой. Заполнение
водой канала следует производить при ограничении отверстий на выходном патрубке
канала и промежуточных трубках. Выявленные неплотности, в том числе стыков
инъекционных крышек с анкерной плитой, а также раковины необходимо заделать
сразу после удаления воды из канала.
9.32.
Производственную проверку состава инъекционного раствора следует произвести
путем приготовления (корректировки до +/- 2 л воды) в инъекционной установке
пробного замеса и отбора контрольных проб для определения свойств инъекционного
раствора. Состав раствора может быть принят к производству через сутки после
проверки величины оседания контрольной порции инъекционного раствора.
9.33. Нагнетание
раствора в канал следует производить непрерывно через специальный штуцер в
анкере, расположенном на конце канала. При расположении анкеров напрягаемой
арматуры в разных высотных уровнях раствор следует закачивать в канал со стороны
расположенного ниже анкера.
9.34. Составляющие
инъекционного раствора вводят в смесительную емкость инъекционной установки в
последовательности: вода, цемент, добавка, цемент.
9.35. Перемешивание
раствора в смесительной емкости, после окончания загрузки компонентов раствора
до его подачи в накопительную емкость, должно быть минимальным, но не менее 2
мин. Раствор, не использованный в течение 30 мин, не подлежит инъецированию и должен
быть удален из накопительной емкости.
9.36. Количество
раствора в накопительной емкости должно быть таким, чтобы исключать опасность
попадания воздуха в канал. Не рекомендуется начинать приготовление новой порции
раствора после заполнения канала до окончания его опрессовки.
9.37. Инъецирование
канала следует начинать при закрытых отводных трубках (если такие трубки
предусмотрены проектом) за исключением ближайшей к месту нагнетания трубки.
9.38. После выхода
из ближайшей к месту нагнетания отводной трубки воздуха, воды, не менее 5 л
шлама и раствора отводную трубку требуется перекрывать и одновременно открывать
следующую отводную трубку.
9.39. Операцию по
выпуску воздуха, воды, шлама и раствора необходимо повторять последовательно
для каждой отводной трубки, включая выходную на концевом анкере.
9.40. Нормальное
прохождение раствора по каналу при нагнетании контролируется по равномерному
вытеканию воды, шлама и раствора из выходных промежуточных трубок.
9.41. Опрессовку
раствора в канале производят после его заполнения. Опрессовку производят со
стороны напорного штуцера, в который нагнетают раствор. Опрессовка производится
под давлением на растворонасосе, равным 0,6 +/- 0,05 МПа (6 +/- 0,5 кгс/см2) в
течение 5 +/- 2 мин.
9.42. Вертикальные
каналы составных по высоте опор для инъецирования следует разбить на ярусы
высотой до 20 - 25 м, совмещая их с обрывом напрягаемой арматуры по высоте
опоры, предусмотренным проектом.
В верхней части
всех каналов нижних и промежуточных ярусов опоры следует устанавливать дополнительные
патрубки для выхода нагнетаемого снизу раствора и выпуска раствора для
инъецирования выше расположенного яруса опоры.
Вначале инъецируют
каналы нижнего яруса на всю его высоту без опрессовки раствора в канале, затем,
не ранее чем через 5 ч, участок канала вышерасположенного яруса опоры. Раствор
в каналах верхнего яруса опоры должен быть опрессован.
9.43. В случае
попадания воздушной пробки в канал в процессе инъецирования или закупорки
канала и невозможности его дальнейшего инъецирования, а также перерывах более
30 мин в подаче раствора (из-за временной неисправности инъекционной установки
и др.) канал на всем его протяжении должен быть экстренно промыт. Промывка
канала производится с помощью инъекционной установки или дублирующим
нагнетающим воду агрегатом со стороны выходного отверстия канала водным
раствором, содержащим пластифицирующие добавки до выхода с противоположного
конца канала светлой воды. При невозможности промывки канала с его
противоположного от начала нагнетания конца промывку канала допускается
производить через промежуточные трубки.
9.44. Перед
заполнением открытых каналов раствором (бетоном) стенки каналов и напрягаемую
арматуру следует очистить и продуть сжатым воздухом. Раствор (бетон) заполнения
необходимо тщательно уплотнить. При пакетном расположении напрягаемых
арматурных элементов в несколько рядов каналы следует заполнять в соответствии
с ППР. Открытая поверхность заполненных каналов должна быть надежно защищена от
влагопотерь.
9.45. В случаях
невозможности (после ряда попыток) промывки закупоренного канала допускается
его доинъецирование раствором через промежуточные отводные трубки или со
стороны выходного отверстия канала только после составления акта о дефекте
произведенных работ с последующим после окончания инъецирования обязательным
ремонтом образованного дефекта.
9.46. В процессе
проведения работ необходимо вести три вида контроля: контроль параметров
технологии нагнетания, свойств раствора и заполнения каналов:
контроль
технологических параметров (в том числе температур воздуха, конструкции,
раствора и его составляющих) производства работ по нагнетанию раствора
осуществляет руководитель работ (мастер) с отражением результатов в едином
журнале;
подбор составов и
контроль свойств инъекционных растворов производит строительная лаборатория с
составлением соответствующих карт, содержащих характеристики инъекционных
растворов (Приложение Н). Отбор проб инъекционного раствора на производстве
допускается осуществлять для одной группы заинъецированных без перерыва каналов
при неизменной технологии выполнения работ и составе раствора, включая
применение одной и той же инъекционной установки, использование одной и той же
партии цемента и типа добавок;
контроль заполнения
каналов осуществляют визуальным методом по степени заполнения отводных трубок
после затвердевания раствора. Выборочно качественное заполнение каналов
оценивают по контролю давления при опрессовке раствора манометрами со стороны
нагнетания и выхода раствора (не реже одного раза в смену);
допускается
дополнительно проводить контроль качества заполнения каналов по уровню
понижения затвердевшего раствора в отводных трубках (рекомендуется, чтобы
отводные трубки имели достаточную длину) и внутреннем пространстве инъекционных
крышек, характеризующих уменьшение объема раствора в канале.
Особенности
бетонирования монолитных конструкций
9.47. При выборе
типов опалубки необходимо соблюдать требования ГОСТ Р 52085, ГОСТ Р 52086.
При выборе типа
опалубки, применяемой при возведении бетонных и железобетонных конструкций опор
мостов, следует предусмотреть:
деформации опалубки
и упоров (предварительно напряженных конструкций) от усилий обжатия;
скругление прямых и
острых углов бетонируемой конструкции радиусом 20 мм или фаской размером не
менее 10 x 10 мм (если в проекте нет других указаний);
величину уклона
боковых поверхностей неразъемной блочной опалубки 1/20.
9.48. Приемку
инвентарной опалубки, поступающей с завода-изготовителя, следует осуществлять в
соответствии с требованиями СП 70.13330 и ГОСТ Р ИСО 2859-1.
9.49.
Подготовленную к бетонированию опалубку следует принимать по акту.
9.50. Поверхность
опалубки, соприкасающаяся с бетоном, должна быть перед укладкой бетонной смеси
покрыта смазкой. Смазку следует наносить тонким слоем на тщательно очищенную
поверхность.
Поверхность
опалубки после нанесения на нее смазки должна быть защищена от загрязнения,
дождя и солнечных лучей.
Не допускается попадание
смазки на арматуру и закладные детали.
Смазку опалубки
отработанными машинными маслами случайного состава применять не допускается.
9.51. Технические
требования, которые следует соблюдать при изготовлении и установке опалубки и
проверять при пооперационном контроле, а также объемы и способы контроля
приведены в таблице 9.
Таблица 9
┌─────────────────────────────────────┬───────────────┬───────────────────┐
│ Технические требования │ Контроль
│ Способ контроля │
├─────────────────────────────────────┼───────────────┼───────────────────┤
│1.
Допускаемые отклонения положения │
Промежуточный │
Измерительный │
│и
размеров установленной опалубки
│по мере монтажа│
(теодолитная │
│по
СП 70.13330, ГОСТ 25347
│и всей опалубки│и нивелирная съемки│
│и
ГОСТ 25346
│ │ и измерение │
│
│ │ рулеткой) │
├─────────────────────────────────────┼───────────────┼───────────────────┤
│2.
Допускаемые отклонения расстояния:│ │ │
│
между опорами изгибаемых элементов
│ │ │
│опалубки
и между связями вертикальных│ │ │
│поддерживающих
конструкций от │ │ │
│проектных
размеров, мм: │ │ │
│ 25 - на 1 м длины │ Каждого
│ Измерительный │
│ не более 75 - на весь пролет │
расстояния │ (измерение │
│
│ │ рулеткой) │
│
от вертикали или проектного наклона │ │ │
│плоскостей
опалубки и линий их │ │ │
│пересечений,
мм: │ │ │
│ 5 - на 1 м высоты │ Каждой
│ Измерительный │
│
│ плоскости │(измерение отвесом)│
│
на всю высоту: │ │ │
│ 20 - для фундаментов │ То же
│ То же │
│ 10 - для тела опор и колонн
высотой│ " │ " │
│до
5 м
│ │ │
├─────────────────────────────────────┼───────────────┼───────────────────┤
│3.
Допускаемое смещение осей опалубки│ │ │
│от
проектного положения, мм:
│ │ │
│
15 - фундаментов
│ Каждой оси │
Измерительный │
│
│ │ (измерение │
│
│ │ рулеткой) │
│
8 - тела опор и колонн фундаментов
│ То же │ То же │
│под
стальные конструкции
│ │ │
├─────────────────────────────────────┼───────────────┼───────────────────┤
│4.
Отклонение стоек домкратных рам
│ Каждой оси │
Измерительный │
│и
осей домкратов от вертикали
│ или стойки │(измерение отвесом)│
│не
допускается
│ │ │
├─────────────────────────────────────┼───────────────┼───────────────────┤
│5.
Допускаемая наибольшая разность
│Отметки каждого│
Измерительный │
│в
отметках ригелей домкратных рам -
│ ригеля │
(нивелирование) │
│10
мм
│ │ │
├─────────────────────────────────────┼───────────────┼───────────────────┤
│6.
Допускаемая "конусность"
│Каждой опалубки│
Измерительный │
│скользящей
опалубки на одну сторону │ │(измерение
отвесом)│
│на
1 м высоты +4; -2
│ │ │
├─────────────────────────────────────┼───────────────┼───────────────────┤
│7.
Обратная "конусность"
│ То же │ То же │
│не
допускается
│ │ │
├─────────────────────────────────────┼───────────────┼───────────────────┤
│8.
Допускаемое расстояние между
│ По проекту │
Измерительный │
│домкратами
и рамами (за исключением │ │ (измерение │
│мест,
где расстояние между рамами
│ │ рулеткой) │
│является
свободным размером) - 10 мм │ │ │
├─────────────────────────────────────┼───────────────┼───────────────────┤
│9.
Допускаемое смещение осей:
│ │ │
│
домкратов от оси конструкции - 2 мм │
Каждой оси │ То же │
│
перемещаемой или переставляемой
│ То же │ " │
│опалубки
относительно осей сооруже- │ │ │
│ния
- 10 мм │ │ │
├─────────────────────────────────────┼───────────────┼───────────────────┤
│10.
Допускаемое отклонение расстояния│Каждой опалубки│ Измерительный │
│между
внутренними поверхностями
│
│(измерение опалубки│
│опалубки
от проектных размеров 5 мм │ │ или первого │
│
│ │ изделия) │
├─────────────────────────────────────┼───────────────┼───────────────────┤
│11.
Допускаемые местные неровности
│ То же │
Измерительный │
│опалубки
3 мм │ │ (внешний осмотр │
│
│ │ и проверка │
│
│ │ двухметровой │
│
│ │ рейкой) │
└─────────────────────────────────────┴───────────────┴───────────────────┘
9.52. В
сборно-монолитные опоры бетонную смесь следует укладывать послойно в каждом
смонтированном ярусе контурных блоков с тщательным вибрированием смеси по всей
площади, особенно около вертикальных швов и у скосов блоков или применять СУБ
(самоуплотняющийся бетон).
Рабочие швы между отдельными
ярусами следует располагать на 20 - 30 см ниже верха смонтированного яруса
контурных блоков, но не более половины высоты контурного блока.
9.53. В полости
оболочек, расположенных в зоне действия знакопеременных температур, следует
укладывать бетонные смеси, в состав которых введены комплексные добавки с
воздухововлекающими или газообразующими компонентами.
Перед укладкой
бетонной смеси в полость оболочки верхняя часть бетона, уложенного подводным
способом, должна быть очищена от шлама и рыхлого бетона (имеющего поры).
9.54. Опалубка и
арматура массивных конструкций перед бетонированием должны быть очищены сжатым
(в том числе горячим) воздухом от снега, наледи и загрязнений. Очистка и нагрев
арматуры паром или горячей водой не допускаются.
Все открытые
поверхности свежеуложенного бетона после окончания бетонирования и при
перерывах в бетонировании должны быть тщательно укрыты и при необходимости
утеплены.
9.55. Ядро
сборно-монолитной опоры в период укладки и твердения бетонной смеси при
отрицательных температурах наружного воздуха необходимо бетонировать с
соблюдением следующих требований:
а) при температуре
до минус 15 °C смонтированные блоки должны быть покрыты съемным утепленным
щитом с люком для подачи бетонной смеси; внутренние поверхности блоков -
отогреты горячим воздухом; наружные поверхности контурных блоков допускается не
утеплять;
б) при температуре
минус 15 °C и ниже ядро опоры следует бетонировать в технологическом укрытии,
внутри которого должна поддерживаться положительная температура (до набора
бетоном прочности не ниже 70% проектной).
9.56. При
устройстве линейных монолитных конструкций на жестком основании (барьерное
ограждение, подпорные стенки и др.) должны предусматриваться мероприятия,
предотвращающие трещинообразование (снижение температурного градиента,
устройство швов и др.).
9.57. При навесном
бетонировании пролетных строений бетонирование каждой секции необходимо
производить без перерыва и без рабочих швов. Следующую секцию допускается
бетонировать после приобретения ранее уложенным бетоном прочности, указанной в
проекте.
9.58. Технические
требования, которые следует выполнять при бетонировании монолитных конструкций
и проверять при операционном контроле, а также объем и способы контроля
приведены в таблице 10.
Таблица 10
┌─────────────────────────────────────────┬─────────────┬─────────────────┐
│ Технические требования │ Контроль
│ Способ контроля │
├─────────────────────────────────────────┼─────────────┼─────────────────┤
│1.
Допускаемая прочность бетона:
│ │ │
│
тампонажного слоя до начала откачивания │Перед началом│ Проверка
│
│воды
из котлована - не менее 2,5 МПа
│ откачивания │ по
ГОСТ 10180 │
│(25
кгс/см2)
│ воды │
│
│
уложенного на момент затопления водой
│ Перед │
То же │
│не
менее 2,5 МПа (25 кгс/см2)
│ затоплением │ │
│
уложенного в оболочку подводным способом│ Перед
│ " │
│перед
очисткой от шлама и рыхлого слоя - │
очисткой │ │
│не
менее 2,5 МПа (25 кгс/см2)
│ │ │
├─────────────────────────────────────────┼─────────────┼─────────────────┤
│2.
Допускаемая температура отогретого │Перед началом│ Измерительный
│
│грунта
основания, старого бетона и
│бетонирования│и регистрационный│
│арматуры
во время укладки бетонной смеси │ │ │
│без
противоморозных добавок - не ниже
│ │ │
│5
°C
│ │ │
├─────────────────────────────────────────┼─────────────┼─────────────────┤
│3.
Допускаемая разность температур в
│ │ │
│уложенных
слоях бетона при отрицательных │ │ │
│температурах
воздуха при выдерживании │ │ │
│бетона: │ │ │
│
в термосе или при введении
│Через каждые │
То же │
│противоморозных
добавок - не более 10 °C │ 4
ч │ │
│
с обогревом - не более 20 °C
│ То же │ " │
├─────────────────────────────────────────┼─────────────┼─────────────────┤
│4.
Допускаемая температура:
│ │ │
│
бетонной смеси, укладываемой в ядро
│ " │
Измерительный │
│сборно-монолитной
опоры, при │ │ │
│отрицательной
температуре воздуха - │ │ │
│не
ниже 15 °C
│ │ │
│
внутренних поверхностей блоков перед
│ Перед │
То же │
│укладкой
бетонной смеси в ядро сборно-
│ укладкой │ │
│монолитной
опоры при отрицательной
│ бетона │ │
│температуре
воздуха - не ниже 5 °C │ │ │
└─────────────────────────────────────────┴─────────────┴─────────────────┘
Особенности
обеспечения твердения бетона в зимних условиях
9.59. При
среднесуточной температуре наружного воздуха ниже 5 °C и минимальной суточной
температуре ниже 0 °C необходимо принимать специальные меры по выдерживанию
уложенного бетона (раствора) в конструкциях и сооружениях, бетонируемых на
открытом воздухе.
Бетон может быть
выдержан способами, указанными в СП 63.13330, ГОСТ 10180, а также:
экзотермическим
способом, в том числе с компенсационным обогревом, при обеспечении
саморазогрева всего объема уложенного бетона;
в обогреваемых
технологических укрытиях, коробах, оболочках, под съемными колпаками и в других
подобных ограждающих конструкциях;
комбинированными
способами, сочетающими способы активного прогрева уложенного бетона с
последующим выдерживанием его способом термоса.
9.60. Способ
термоса следует применять при обеспечении начальной температуры уложенного
бетона не ниже 5 - 10 °C с последующим выдерживанием бетона под тепловой
изоляцией с расчетной температурой, зависящей от массивности конструкций, в
течение времени, необходимого для достижения прочности, установленной в ППР.
9.61.
Экзотермический способ следует применять при обеспечении начальной температуры
уложенного бетона не ниже 15 °C (по всему объему конструкции, в том числе по
контакту с ранее уложенным бетоном и основанием) при теплозащитных свойствах
ограждающих конструкций опалубки, когда уровень теплопотерь не превышает 60%
тепла, выделяемого бетоном в интенсивный период саморазогрева (в течение первых
3 сут).
9.62. Выдерживать
бетон без обогрева за счет введения противоморозных добавок допускается в
случаях, когда невозможно обеспечить температуру уложенного бетона в интервале
от 5 до 10 °C в течение первых 5 - 7 сут.
9.63. Контактный
обогрев уложенного бетона в термоактивной опалубке следует применять при
бетонировании конструкций с модулем поверхности 6 и более.
После уплотнения
открытые поверхности бетона и прилегающие участки щитов термоактивной опалубки
должны быть надежно защищены от потерь бетоном влаги и тепла.
9.64. Электродный
прогрев бетона необходимо производить в соответствии с технологическими
картами.
Запрещается
использовать в качестве электродов арматуру бетонируемой конструкции.
Электродный прогрев
следует производить до приобретения бетоном не более 50% расчетной прочности.
Если требуемая прочность бетона превышает эту величину, то дальнейшее
выдерживание бетона следует обеспечивать методом термоса.
Допускается
производить прогрев бетона нагревательными (греющими) проводами. Тип греющих
проводов, расстояние между ними, а также термическое сопротивление тепловой
изоляции при этом определяется в ППР.
Для защиты бетона
от высушивания при электродном прогреве и повышения однородности температурного
поля в бетоне при минимальном расходе электроэнергии должна быть обеспечена
надежная тепловлагоизоляция поверхности бетона.
9.65. Применение
бетона с противоморозными добавками запрещается в предварительно напряженных
железобетонных конструкциях; железобетонных, расположенных в зоне действия
блуждающих токов или находящихся ближе 100 м от источников постоянного тока
высокого напряжения; железобетонных, предназначенных для эксплуатации в
агрессивной среде; в частях конструкций, находящихся в зоне переменного уровня
воды.
При приготовлении
бетонной смеси с установленными проектом требованиями по морозостойкости
одновременно с противоморозной добавкой и добавкой - замедлителем схватывания
или пластификатором необходимо вводить в бетонную смесь воздухововлекающую или
газообразующую добавку.
9.66. При
омоноличивании сборных и сборно-монолитных конструкций с выдерживанием
уложенного бетона обогревными методами необходимо отогревать поверхностные слои
бетона, части конструкций, входящих в стык омоноличивания, арматуру и закладные
детали до температуры не ниже 5 °C, но не выше 25 °C на глубину не менее 30 см.
Температура
бетонной или растворной смеси, укладываемой встык, должна быть выше температуры
поверхностного слоя бетона омоноличиваемых конструкций на 5 - 10 °C.
9.67. При
омоноличивании конструкций с выдерживанием бетона с противоморозными добавками
поверхностные слои бетона омоноличиваемых конструкций допускается не
отогревать, но необходимо удалить наледь, снег и строительный мусор с
поверхностей бетона, арматуры и закладных деталей. Запрещается промывать
указанные поверхности солевыми растворами.
9.68. Открытые
поверхности уложенного бетона в стыках омоноличивания должны быть надежно
защищены от вымораживания влаги.
Видимые швы в
бетоне необходимо расшивать только при устойчивой положительной температуре
воздуха.
Монтаж опор
9.69. Блоки опор
необходимо устанавливать по уровню и отвесу на клиньях. Каждый ярус высотой не
более 5 м, а также основание под нижний ряд блоков следует нивелировать
поверху, устраняя допущенные отклонения. Во время выполнения работ швы блоков,
через которые возможна потеря раствора, необходимо плотно законопатить.
9.70. В процессе
выполнения работ по заполнению ядра опоры при отрицательной температуре воздуха
необходимо обеспечить незамерзание бетона (раствора) до набора им прочности не
ниже 70% проектной.
9.71. При монтаже
сборных конструкций стоечных опор мостов (путепроводов) стойки в башмаках
фундаментов следует временно закрепить с помощью специальных металлических
шаблонов или кондукторов.
Клинья при
закреплении должны входить в стакан подколонника на половину его глубины,
обеспечивая при этом возможность последующего замоноличивания колонны в
подколоннике и изъятие клиньев. Во всех случаях должны быть приняты меры против
попадания воды в стаканы подколонников и фундаментов.
9.72. Перед
монтажом блоки должны быть очищены от загрязнений и льда.
9.73. Технические
требования, которые следует выполнять при монтаже фундаментов и опор и
проверять при операционном контроле, а также объем и способы контроля приведены
в таблице 11.
Таблица 11
┌───────────────────────────────────────────────┬───────────┬─────────────┐
│ Технические требования │ Контроль │
Способ │
│
│ │ контроля
│
├───────────────────────────────────────────────┼───────────┼─────────────┤
│1.
Допускаемое смещение наружных граней смежных│Каждых
двух│Измерительный│
│сборных
блоков опор - 5 мм, но не более 10 мм
│ смежных │ (измерение │
│от
проектного положения наружной поверхности
│ блоков │
линейкой) │
│опоры
│ │ │
├───────────────────────────────────────────────┼───────────┼─────────────┤
│2.
Допускаемые отклонения:
│ │ │
│
в толщине швов в опорах, собираемых
│Выборочный │ То
же │
│из
контурных блоков на "мокрых" швах, +/- 5 мм │ │ │
│
осей блоков фундаментов и опор, собираемых
│ То же │
" │
│на
"мокрых" швах, +/- 10 мм │ │ │
├───────────────────────────────────────────────┼───────────┼─────────────┤
│3.
Допускаемые отклонения осей составных
│ │ │
│по
высоте конструкций опор, собираемых:
│ │ │
│
на клееных стыках в долях от высоты H - 1/250 │ Каждой
│Измерительный│
│
│ опоры │(визирование │
│
│ │
теодолитом │
│ │ │и нивелиром) │
│
на "мокрых" швах - не более 20 мм │ То же
│Измерительный│
│
│ │
(измерение │
│
│ │
рулеткой) │
├───────────────────────────────────────────────┼───────────┼─────────────┤
│4.
Допускаемые отклонения осей возведенных
│ │ │
│конструкций
в плане относительно разбивочных
│ │ │
│осей
опор:
│ │ │
│
осей свай, свай-оболочек и столбов в плане
│Выборочный │ То
же │
│в
уровне нижней поверхности насадок - 30 мм
│ │ │
│
осей стоек, колонн по верхнему торцу - 5 мм
│ " │ " │
├───────────────────────────────────────────────┼───────────┼─────────────┤
│5.
Допускаемое отклонение по высоте проектного │ "
│ " │
│положения
отметок верха свайных элементов
│ │ │
│(забивных
свай, свай-оболочек, буровых свай)
│ │ │
│относительно
нижней поверхности насадок - 50 мм│ │ │
├───────────────────────────────────────────────┼───────────┼─────────────┤
│6.
Допускаемый минимальный зазор между боковой │ "
│ " │
│поверхностью
свайных элементов, стоек опор
│ │ │
│и
боковой поверхностью отверстий в насадках -
│ │ │
│не
менее 30 мм
│ │ │
└───────────────────────────────────────────────┴───────────┴─────────────┘
Облицовка опор
9.74. При приемке
облицовочных блоков необходимо проверять их комплектность, соответствие
размеров требованиям проекта и настоящего свода правил, наличие паспортов с
указанием в них прочности и морозостойкости материалов, а также маркировку
изделий (нанесенную на верхние грани изделий несмываемой краской).
9.75. Очередной ряд
облицовочных блоков следует устанавливать по раскладочным чертежам до
бетонирования ряда (насухо).
Установку следует
начинать с угловых и криволинейных частей опоры. Установленную облицовку
следует надежно раскреплять для обеспечения устойчивого положения на весь
период бетонирования, а незаполненные швы между блоками (камнями) -
законопатить на глубину не более 30 мм средствами, предупреждающими вытекание
раствора. Перед установкой облицовочные блоки следует промыть от грязи и пыли.
При выполнении работ необходимо соблюдать меры предосторожности для
предохранения граней и кромок изделий от повреждений.
9.76. Ядро опоры с
облицовкой из природных камней следует бетонировать слоями в пределах высоты
одного ряда облицовки с оставлением возле смежных боковых граней изделия
вертикальных колодцев для заполнения швов раствором.
Естественные
природные камни, употребляемые в соответствии с проектом для облицовки, должны
быть крепких пород, однородного строения, без трещин, жил и прослоек, без
следов выветривания.
9.77. Нормативные
требования, которые следует выполнять при облицовке опор и проверять при
пооперационном контроле, а также объем и способы контроля приведены в таблице
12.
Таблица 12
Технические требования
|
Контроль
|
Способ контроля
|
1.
Допускаемые отклонения размеров лицевой
поверхности плит, облицовочных камней
и блоков от проектных размеров - 5 мм
|
Выборочный
|
Измерительный
(измерение
стальной рулеткой)
|
2.
Допускаемые неровности на лицевой
поверхности облицовочных железобетонных
и бетонных изделий не более - 5 мм
|
То же
|
Измерительный
(измерение
линейкой и проверка
по шаблону)
|
3.
Допускаемая величина выступов
грубоотколотой части над поверхностью
ленты или кромки изделий (при облицовке
изделиями с фактурой лицевой поверхности
типа "скала" (шуба)) не более - 50 мм
|
Сплошной
|
Измерительный
(измерение
линейкой)
|
4.
Допускаемые отклонения каждого ряда
установленной облицовки от проектного
положения на лицевой поверхности опоры
(относительно оси опоры) +/- 10 мм
|
"
|
То же
|
Сооружение труб
9.78. Блоки сборных
фундаментов под трубы непосредственно после приемки котлована следует
устанавливать на основание, выполненное с проектным уклоном и заданным
строительным подъемом.
Блоки следует
устанавливать посекционно в направлении от выходного к входному оголовку трубы.
Каждый блок или ряды блоков в пределах секции следует укладывать в соответствии
с проектом и выравнивать по одной из внутренних плоскостей. Блоки необходимо
укладывать предварительно очищенными сразу в проектное положение на слой
раствора; дополнительный подлив раствора под блок, а также его смещение после
схватывания раствора не допускаются.
Скосы в местах
сопряжения более глубокой части котлована под фундаменты оголовков с подошвой
котлована под тело трубы после кладки фундаментов оголовков должны быть
заполнены песчано-гравийной или песчано-щебеночной смесью, послойно уплотненной
и пролитой цементным раствором.
9.79. Вертикальные
швы каждого ряда блоков следует заполнять цементно-песчаным раствором, наружные
стороны вертикальных швов - заделывать заподлицо с поверхностью прилегающих
блоков.
9.80. Металлические
гофрированные трубы (МГТ) необходимо собирать или устанавливать в проектное
положение только после приемки грунтовой подушки для трубы.
9.81. При монтаже
трубы надлежит выполнять следующие требования:
а) выходной
оголовок следует монтировать до начала установки промежуточных звеньев;
б) при укладке
цилиндрических звеньев труб необходимо следить, чтобы бетонная подушка
обеспечивала под звеньями на установленном в проекте угле охвата плотный
контакт с поверхностью звена на всей длине;
в) устанавливать
прямоугольные и круглые звенья труб с плоской пятой на растворе подвижностью 6
- 8 см;
г) устанавливать
стальные гофрированные секции труб в спрофилированное шаблоном ложе,
охватывающее снизу не менее трети поперечного сечения трубы, или на горизонтальную
хорошо спланированную площадку, тщательно подбивая и одновременно уплотняя не
менее чем под одну треть поперечного сечения трубы песчаный грунт;
д) следить, чтобы
при монтаже гофрированных труб между головками болтов, гайками, шайбами и
гофрированными листами металлических конструкций не оставались частицы грунта.
9.82. Приемку
смонтированной трубы до засыпки ее грунтом необходимо оформить актом.
9.83. Нормативные
требования, которые следует выполнять при строительстве труб и проверять при
пооперационном контроле, а также объем и способы контроля приведены в таблице
13.
Таблица 13
┌───────────────────────────────────────────┬─────────────┬───────────────┐
│ Технические требования │ Контроль
│Способ контроля│
├───────────────────────────────────────────┼─────────────┼───────────────┤
│1.
Допускаемые отклонения в положении
│ │ │
│смонтированных
элементов конструкций труб: │
│ │
│
уступов в рядах фундаментных блоков │
Каждого │ Измерительный
│
│по
высоте не более 10 мм
│ уступа │
(измерение │
│
│ │ линейкой)
│
│
длины и ширины секций фундаментов
│Каждой секции│ Измерительный │
│+2;
-1 см
│ │ (измерение
│
│
│ │ линейкой)
│
│
относительные смещения железобетонных
│ Каждого │
То же │
│и
бетонных элементов - 10 мм
│ зазора │ │
│
зазоров между секциями фундаментов
│Каждой трубы │
" │
│и
звеньями (от проектной величины) +/- 5 мм│ │ │
│
продольной оси трубы в профиле и плане
│Каждой трубы │ Измерительный │
│(при
условии отсутствия участков застоя
│
│(нивелирование │
│воды)
- 30 мм
│ │и
съемки плана)│
├───────────────────────────────────────────┼─────────────┼───────────────┤
│2.
Допускаемая прочность цементно-песчаного│ │ │
│раствора: │ │ │
│
при укладке блоков фундамента - раствор
│ Не менее │
Проверка │
│класса,
применяемого по проекту,
│ объема │ по ГОСТ 5802 │
│но
не менее В20
│ раствора, │ │
│
В/Ц - не более 0,65
│укладываемого│
│
│
│ в один │ │
│
│ фундамент │ │
├───────────────────────────────────────────┴─────────────┴───────────────┤
│ Примечание. Зазоры между звеньями и
секциями фундаментов труб должны│
│быть
в одной плоскости.
│
└─────────────────────────────────────────────────────────────────────────┘
Сооружение
пролетных строений
9.84. Консольные,
консольно-шлюзовые и козловые краны, подъемники, краны-агрегаты должны быть
освидетельствованы до начала работ по установке пролетных строений (после
приведения их в рабочее положение). Работа кранов на насыпных грунтах
допускается только после уплотнения грунтов в соответствии с требованиями ППР.
9.85. При подъеме,
опускании и перемещении пролетных строений (балок) необходимо:
следить, чтобы
подъем и опускание выполнялись строго вертикально, при этом оттяжку конструкций
лебедками применять запрещается;
соблюдать зазор не
менее 0,2 м между низом устанавливаемой конструкции и головкой рельса или
грунта и до выступающих частей смонтированных конструкций не менее 0,5 м;
следить, чтобы
строповку выполняли только способом, оговоренным в ППР.
Строповка элементов
конструкций из ПКМ должна производиться мягкими текстильными стропами и
специальными траверсами. Строповка выполняется в строгом соответствии со схемой
строповки, являющейся обязательной частью проектной документации.
Запрещается
производить строповку непосредственно за элементы конструкции из ПКМ.
9.86. Перед
установкой железнодорожными консольными кранами на опоры пролетных строений и
отдельных балок необходимо:
а) предварительно
проверить насыпь подходов, состояние пути, прочность и устойчивость ранее смонтированных
конструкций и соблюдение габаритов приближения строений на возможность пропуска
кранов с грузом;
б) следить, чтобы
не было движения на путях, смежных с путем движения крана, и было снято
напряжение в контактной сети.
9.87. Порядок
перемещения кранов всех типов по ранее установленным пролетным строениям должен
определяться в ППР.
9.88. При
одновременной работе двух стреловых кранов операции необходимо выполнять в
строгом соответствии с ППР под непосредственным руководством ответственного за
безопасное производство работ. В ППР должны быть определены последовательность
операций (подъем, изменение высоты, поворот) по каждому крану, схема строповки
грузов и траектории их движения с учетом нагрузок на кран и его
грузоподъемности.
9.89. Технические требования,
которые следует выполнять при установке пролетных строений и проверять при
пооперационном контроле, а также объем и способы контроля приведены в таблице
14.
Таблица 14
Допускаемые смещения
|
Контроль
|
Способ
контроля
|
1.
Продольных осей железнодорожных
пролетных строений или их балок в плане
от разбивочных осей - 10 мм
|
Каждой балки
и пролетного
строения
|
Измерительный
(теодолитная
съемка)
|
2.
Автодорожных пролетных строений или их
балок - 0,0005 пролета, но не более 40 мм
|
То же
|
То же
|
3.
Деревянных пролетных строений - 20 мм
|
Каждой балки
и пролетного
строения
|
Измерительный
(теодолитная
съемка)
|
4.
Осей опирания балок пролетного
строения вдоль пролета - 15 мм
|
То же
|
То же
|
9.90. Подъем и
опускание пролетных строений домкратами и другими простейшими подъемными
механизмами и опускание на стальных инвентарных цилиндрических песочницах
следует производить при невозможности или нецелесообразности использования
кранов. При этом должно быть обеспечено устойчивое положение поднимаемого
пролетного строения и равномерное распределение нагрузки каждого подъемного
механизма в его основании.
9.91. При навесной,
полунавесной или уравновешенно-навесной сборках пролетных строений необходимо соблюдать
следующие требования:
а) началу сборки
конструкции должны предшествовать работы по тщательной выверке и закреплению
надопорного (анкерного) блока или группы анкерных блоков, определяющих
положение монтируемой консоли в плане и профиле. Конструкция реперов (марок),
способ ориентирования и точность фиксации положения блока в пространстве должны
быть указаны в ППР и увязаны с технологией изготовления блоков;
б) монтируемые
блоки или их элементы должны быть установлены в конструкцию в последовательности
и строгом соответствии с ППР;
в) запрещается
размещать на монтируемых консолях оборудование, конструкции и материалы, масса
которых не учтена проектом;
г) в процессе
монтажа должен быть обеспечен систематический контроль за положением в
пространстве каждого сборного элемента и конструкции; система контроля и
параметры, подлежащие систематическому контролю, должны быть указаны в ППР;
д) должна быть
исключена возможность случайных ударов устанавливаемой конструкции о
смонтированные.
9.92. Навесной
монтаж при опирании монтируемой консоли на две вспомогательные опоры (по
неразрезной схеме) допускается осуществлять как исключение, только при наличии
приложенной к проекту специальной инструкции при постоянном контроле величины
опорных реакций на обеих опорах, обязательном авторском надзоре и постоянном
контроле главного инженера строительства.
9.93. Опорные части
неразрезных пролетных строений после установки на них и приведения в проектное
положение надопорного блока должны быть заблокированы. Блокирующие устройства
должны соответствовать ППР. Конструкции опорных частей и блокирующих устройств
должны учитывать возможность их использования для корректировки положения
смонтированной части пролетного строения в плане и профиле.
Блокирующие
устройства необходимо снимать в последовательности, указанной в ППР.
9.94. Перед
бетонированием замыкающих блоков объединяемые секции следует надежно соединять
между собой, исключая возможность разрушения бетона омоноличивания в раннем
возрасте от температурных и других воздействий.
9.95. Натяжение
напрягаемых арматурных элементов при сборке составных по длине пролетных
строений необходимо выполнять в порядке, указанном в ППР. В конструкциях с
клееными стыками натяжение рабочей напрягаемой арматуры может быть выполнено
как до, так и после отверждения клея.
9.96. При натяжении
или снятии усилия предварительного натяжения с напрягаемых арматурных элементов
необходимо, кроме контроля за усилием и вытяжкой, в напрягаемой арматуре
контролировать прогиб конструкции, смещения в опорных частях и деформации в
бетоне согласно указаниям проекта конструкции.
Кратковременное
обжатие клеевых швов для удаления излишков клея и получения плотного клееного
стыка должно быть равномерным по сечению. Усилие обжатия назначается в
зависимости от консистенции клея и размеров (ширины) склеиваемых поверхностей.
По окончании обжатия клеевого шва все арматурные каналы в сечении должны быть
очищены от остатков клея.
При нанесении клея
на стыкуемые поверхности смежных блоков расстояние между их торцами должно быть
не менее 0,3 м, а блоки надежно зафиксированы для исключения самопроизвольного
сближения в процессе обработки склеиваемых поверхностей.
9.97. Технические
требования, которые следует выполнять при навесной сборке железобетонных
пролетных строений и проверять при операционном контроле, а также объем и
способы контроля приведены в таблице 15.
Таблица 15
Технические требования
|
Контроль
|
Способ контроля
|
1.
Допускаемые отклонения в профиле
и плане концов консоли составного
по длине пролетного строения,
собранного на клееных стыках,
от проектного положения +/- 50 мм
|
Каждого
пролетного
строения
|
Измерительный
(нивелирование
и визирование теодолитом,
измерение линейкой)
|
2.
Допускаемая величина
кратковременного обжатия клеевого
шва при навесной сборке не менее
0,2 МПа (2 кгс/см2)
|
Каждого
шва
|
Измерительный
(по манометру и вытяжке
арматуры)
|
3.
Допускаемые отклонения в профиле
и плане составного по длине
пролетного строения, собранного
на бетонируемых стыках, +/- 20 мм
|
Каждого
пролетного
строения
|
Измерительный
(измерение
линейкой, нивелирование
и визирование теодолитом)
|
9.98. Сборку
составных по длине пролетных строений на перемещаемых подмостях следует
выполнять в соответствии с инструкцией по эксплуатации монтажных агрегатов.
9.99. Проектную
геометрию составных по длине пролетных строений, собираемых на перемещаемых подмостях,
следует обеспечивать предварительной выверкой заданного в ППР положения в
пространстве рельсового пути для монтажных агрегатов. Профиль головки рельса
должен соответствовать упругой линии прогиба подмостей от загружения массы
монтируемых блоков и увязан с технологией изготовления сборных блоков на
заводе.
9.100. Опирание
монтажных агрегатов следует выполнять через раскружаливающие устройства,
обеспечивающие перемещение подмостей по вертикали в прямом и обратном
направлениях.
9.101. Сборке
каждой секции пролетного строения должна предшествовать тщательная выверка
положения и надежное закрепление первого "направляющего" блока.
Объединять все сборные блоки секции следует групповым склеиванием с соблюдением
соответствующих технологических зазоров в стыках, достаточных для удобного и
безопасного нанесения клея.
Предварительное
обжатие склеенных блоков секции должно быть равномерным по сечению и выполнено
в сроки, не превышающие технологическую жизнеспособность примененных рабочих
составов клея. По окончании обжатия стыковых швов все каналы для напрягаемой
арматуры должны быть очищены на всю длину от клея.
9.102. Стык каждой
смонтированной секции с готовым участком пролетного строения следует выполнять
из монолитного бетона. Ширина стыкового зазора определяется конструкцией стыка
и указывается в проекте.
9.103. Технические
требования, которые следует выполнять при сборке железобетонных пролетных
строений на перемещаемых подмостях и проверять при операционном контроле, а
также объем и способы контроля приведены в таблице 16.
Таблица 16
┌───────────────────────────────────────────┬──────────────┬───────────────┐
│ Технические требования │ Контроль
│Способ контроля│
├───────────────────────────────────────────┼──────────────┼───────────────┤
│1.
Допускаемые отклонения осей монтажных
│ │ │
│агрегатов
и подкранового пути от проектного│ │ │
│положения,
мм:
│ │ │
│
+/- 30 - оси монтажного агрегата
│Перед началом │ Измерительный │
│
+/- 2 - " рельса в плане │ сборки
│(нивелирование,│
│
+/- 2 - головки рельса в профиле,
│ каждого │
визирование │
│но
не более 1 мм разницы в уровне головок
│ пролета │
теодолитом) │
│рельсов
в любом сечении пути
│ │ │
├───────────────────────────────────────────┼──────────────┼───────────────┤
│2.
Допускаемые технологические зазоры, мм: │ │ │
│
не менее 600 - между "направляющим" блоком│ В процессе
│ Измерительный │
│и
первым присоединяемым и всеми
│сборки каждой │
(измерение │
│последующими
поочередно присоединяемыми
│ секции │
линейкой) │
│блоками
при групповом склеивании
│ │ │
│
не менее 400 - между выступающими анкерами│ В процессе
│ Измерительный │
│смонтированной
и ранее изготовленной секции│сборки каждой │ (измерение
│
│ │ секции
│ линейкой) │
│
не менее длины домкрата +400 мм, в случае │ То же
│ То же │
│натяжения
напрягаемой арматуры с установкой│ │ │
│домкрата
в стыке
│ │ │
└───────────────────────────────────────────┴──────────────┴───────────────┘
9.104. Надвижку и
перекатку пролетных строений следует выполнять под непосредственным
руководством главного инженера или начальника участка.
9.105. Надвижку
(перекатку) пролетных строений следует выполнять толкающими устройствами,
обеспечивающими плавное - без рывков и перекосов их перемещение.
В процессе надвижки
неразрезных пролетных строений следует контролировать в соответствии с
указаниями ППР фактические опорные реакции и деформации в конструкции.
9.106. При надвижке
пролетных строений, расположенных на продольном уклоне или вертикальной кривой,
уклон плоскости скольжения на каждой опоре должен быть равен уклону плоскости
низа пролетного строения на этой опоре.
В ППР должно быть
предусмотрено необходимое тормозное или стопорное устройство.
9.107. Проектное
положение пролетного строения в плане в процессе его надвижки должно
обеспечиваться специальными направляющими устройствами.
9.108. Для контроля
за поперечной перекаткой накаточные пути должны быть размечены несмываемой
краской через 0,001 расстояния между путями.
9.109. В процессе
надвижки и перекатки пролетных строений следует контролировать перемещения
верха опор моста средствами, гарантирующими автоматическое отключение толкающих
устройств.
На период надвижки
(перекатки) пролетного строения необходимо установить радиотелефонную связь
командного пункта со всеми участками работ.
9.110. Конструкция
плаза (стапеля) для изготовления секций пролетного строения на подходах должна
быть регулируемой в отметках и гарантировать от недопустимых осадок при
воздействии массы изготовляемой секции и монтажного оборудования.
9.111. Размеры
устройств скольжения должны обеспечивать установку в одном продольном створе с
ними домкратов для разгрузки и ремонта устройств скольжения.
9.112. Надвигаемая
конструкция с незаинъецированными арматурными каналами или с прочностью
инъекционного раствора менее 20 МПа (200 кгс/см2) должна быть дополнительно
рассчитана как конструкция с напрягаемой арматурой, не имеющей сцепления с
бетоном.
9.113. Надвижку
(перекатку) пролетных строений следует выполнять, как правило, в светлое время
суток и циклами, конечной целью которых должно быть опирание надвигаемого
пролетного строения на очередную капитальную или вспомогательную опору.
9.114. При
обнаружении на любом участке надвигаемой системы деформаций элементов
пролетного строения, вспомогательных обустройств либо неудовлетворительной
работы средств перемещения надвижку следует немедленно прекратить для принятия
необходимых мер.
Запрещается
устранять какие-либо неполадки во время движения пролетного строения.
9.115. Технические
требования, которые следует выполнять при продольной надвижке и поперечной
перекатке железобетонных пролетных строений и проверять при операционном
контроле, а также объем и способы контроля приведены в таблице 17.
Таблица 17
┌──────────────────────────────────────────┬──────────┬───────────────────┐
│ Технические требования │ Контроль │ Способ контроля │
├──────────────────────────────────────────┼──────────┼───────────────────┤
│1.
Допускаемое отклонение оси надвигаемого│ Каждого │
Измерительный │
│пролетного
строения от проектной не более │пролетного│ (визирование │
│50
мм
│ строения │
теодолитом, │
│
│ │измерение
линейкой)│
├──────────────────────────────────────────┼──────────┼───────────────────┤
│2.
Допускаемый забег одного конца против
│ То же │
То же │
│другого
при поперечной перекатке не более │ │ │
│0,001
длины пролета
│ │ │
├──────────────────────────────────────────┼──────────┼───────────────────┤
│3.
Допуски в установке антифрикционных
│ │ │
│прокладок
в устройствах скольжения │ │ │
│не
более, мм:
│ │ │
│
50 - зазор между смежными прокладками
│ Каждой │
Измерительный │
│по
длине
│прокладки │
(измерение │
│
│ │ линейкой) │
│
2 - разность толщин прокладок
│ То же │
То же │
│
10 - смещение относительно оси
│ " │ " │
│перекаточного
устройства │ │ │
├──────────────────────────────────────────┼──────────┼───────────────────┤
│4.
Допускаемая разность в отметках
│ │ │
│перекаточных
устройств одной опоры, мм: │ │ │
│
не более 2 - при подъеме пролетного
│ На всех │ " │
│строения
для смены прокладок
│ опорах │ │
│
" " 2 - в отметках перекаточных │
То же │ " │
│устройств
на одной опоре
│ │ │
│
+/- 5 - отклонение от проектной отметки
│ " │
Измерительный │
│
│ │ (визирование │
│ │ │ теодолитом) │
└──────────────────────────────────────────┴──────────┴───────────────────┘
9.116. При
перевозке и установке пролетных строений на плаву необходимо обеспечивать:
а) соответствие
выполняемых работ ППР по перевозке, согласованному в установленном порядке с
органами речного флота;
б) соблюдение
зазора между оголовками надстройки плавучей системы и низом пролетного
строения, допускающего беспрепятственную установку плавучей системы с учетом ее
колебаний от ветра и волны;
в) достаточный
объем сбрасываемого балласта с учетом компенсации потерь водоизмещения плавучей
опоры при ее всплытии вследствие упругой деформации пролетного строения,
погрузочных обустройств и самой плавучей опоры;
г) оборудование
якорных тросов приспособлениями для быстрого закрепления непосредственно за
плавучую опору при увеличении ветровой нагрузки.
9.117. На период
перевозки или надвижки пролетных строений на плаву необходимо установить
радиотелефонную связь командного пункта с буксирами, плашкоутами, опорами и с
ближайшим пунктом гидрометеорологической службы для получения регулярных
прогнозов о скорости и направлении ветра, осадках и колебаниях горизонта воды.
На пролетном строении необходимо установить приборы для измерения скорости
ветра.
Плавучая система
должна быть оборудована спасательными средствами.
9.118. Технические
требования, которые следует выполнять при перевозке и установке всех типов
пролетных строений на плаву и проверять при операционном контроле, а также
объем и способы контроля приведены в таблице 18.
Таблица 18
┌───────────────────────────────────────────┬─────────────┬───────────────┐
│ Технические требования │ Контроль
│Способ контроля│
├───────────────────────────────────────────┼─────────────┼───────────────┤
│1.
Закрепление плавучих опор за якоря
│ │ │
│для
фиксации плавучих систем в плане
│ │ │
│с
отклонениями от проектного положения, см:│ │ │
│
2 - во время погружения или опускания
│ Каждой │ Измерительный │
│пролетного
строения на опорные части
│ плавучей │
(измерение │
│
│ системы │
линейкой) │
│
10 - при выводе от погрузочных пирсов
│ То же │
То же │
│и
вводе плавучих опор в пролет моста
│ │ │
├───────────────────────────────────────────┼─────────────┼───────────────┤
│2.
Выполнение балластировки
│ Каждой │ Измерительный │
│и
разбалластировки плавучих опор с учетом
│ операции │
(измерение │
│превышения
допустимых деформаций, кренов
│ │мерной
рейкой) │
│и
дифферентов при поддержании уровня воды
│ │ │
│в
понтонах или отсеках барж с отклонением
│ │ │
│от
проектного положения не более +/- 5 см
│ │ │
├───────────────────────────────────────────┼─────────────┼───────────────┤
│3.
Контрольное траление движения плавучих
│ Контроль │Регистрационный│
│опор
на глубину, превышающую на 20 см │
трассы │ (траление)
│
│максимальную
осадку плавучей опоры, считая │ │ │
│от
возможного наиболее низкого горизонта
│ │ │
│воды,
- по проекту
│ │ │
├───────────────────────────────────────────┼─────────────┼───────────────┤
│4.
Перемещение пролетных строений по воде
│ │ │
│и
надвижку конструкций с применением
│ │ │
│плавучей
опоры допускается начинать:
│ │ │
│
при скорости ветра не более 5 м/с <*>
│Разовый перед│ Измерительный │
│
│началом работ│
(прибором, │
│
│ │ определяющим │
│
│
│скорость ветра)│
│
при колебании уровня воды до 15 см/сут
│ Каждый час
│Измерительный │
│
│ при │
(измерение │
│
│ перемещении │
рейкой) │
├───────────────────────────────────────────┼─────────────┼───────────────┤
│5.
Перемещение плавучей системы допускается│ Постоянный │ Измерительный │
│производить
со скоростью до 10 км/ч
│ при │
(прибором, │
│
│ перемещении │ определяющим
│
│
│ │ скорость
│
│
│ │ перемещения) │
├───────────────────────────────────────────┼─────────────┼───────────────┤
│6.
Зазор между верхом опорных частей
│ При выводе │
Измерительный │
│и
низом пролетного строения при вводе
│ и вводе │
(измерение │
│и
выводе его не менее 10 см
│ │ линейкой)
│
├───────────────────────────────────────────┴─────────────┴───────────────┤
│
<*> При внезапном усилении
ветра более 10 м/с
плавучую систему│
│следует
раскрепить неподвижно на якорях, а нагрузку
с тяговых устройств│
│(буксиров
или лебедок) снять.
│
└─────────────────────────────────────────────────────────────────────────┘
9.119. Резиновые и
резинофторопластовые опорные части следует устанавливать непосредственно на
подферменные площадки, подготовленные и выверенные в пределах отклонений,
указанных в таблице 19, а стальные и стаканные - на опалубленный по периметру
слой несхватившегося цементно-песчаного раствора или полимербетона толщиной до
3 см, при большей толщине выравнивающего слоя его необходимо армировать
(Приложение Л). Допускается стальные и стаканные опорные части устанавливать на
клинья или регулировочные устройства с последующим инъецированием зазоров клеем
на основе эпоксидной смолы или удалением клиньев.
Таблица 19
Допускаемые отклонения
|
Контроль
|
Способ
контроля
|
1.
От проектной разности отметок
поверхностей подферменных площадок
в пределах одной опоры не более +2 мм
|
Всех
подферменных
площадок
|
Измерительный
(нивелирование)
|
2.
Поверхностей подферменных площадок
от горизонтального (проектного)
положения 0,002 длины (ширины) площадки
|
Всех площадок
|
Измерительный
(по уровню)
|
3.
От проектной разности отметок
опорных поверхностей комплекта стальных
и стаканных опорных частей в пределах
одной опоры 0,001 расстояния между
осями ферм (балок)
|
Всех опорных
частей
|
Измерительный
(нивелирование)
|
4.
Оси стаканной линейно-подвижной
опорной части от направления проектного
перемещения опорного узла пролетного
строения 0,005 длины подферменника
|
Всех линейно-
подвижных опорных
частей
|
Измерительный
(измерение
линейкой)
|
9.120. Перед
инъецированием зазоров следует произвести их герметизацию и установку штуцеров
для нагнетания клея. По периметру каждой опорной части должно быть установлено
не менее четырех штуцеров. Штуцеры следует устанавливать непосредственно в
зазор (при уплотнении его жгутами) или в специально предусмотренные проектом
отверстия в опорных частях.
9.121. Для
омоноличивания анкерных болтов в теле опоры следует применять цементно-песчаный
раствор, полимербетон или клей на основе эпоксидной смолы с наполнителем.
9.122. Все опорные части,
поступающие на объект, следует сопровождать документом о качестве.
Перед установкой
стаканных опорных частей необходимо: убедиться в том, что верхняя плита, крышка
стакана и стакан плотно прижаты друг к другу пластмассовыми монтажными болтами;
проконтролировать параллельность плиты (крышки) и дна стакана; уточнить наличие
на поверхности верхних плит отверстий, фиксирующих ось опорных частей.
При наличии
указаний в проекте трущиеся поверхности стальных опорных частей и поверхности
катания перед установкой необходимо тщательно очистить и натереть графитом или
промазать дисульфид-молибденовой смазкой.
9.123. Подвижные
опорные части необходимо устанавливать согласно проекту с учетом температуры
воздуха в момент установки, а также усадки и ползучести бетона пролетных
строений.
При установке
опорных частей следует нанести риски, отмечающие взаимное начальное положение
их элементов, и клеймо с указанием температуры при установке пролетных
строений.
9.124. Допускаемые
отклонения, которые следует выполнять при установке опорных частей и проверять
при пооперационном контроле, а также объем и способы контроля приведены в
таблице 19.
10. Монтаж
стальных и сталежелезобетонных конструкций
10.1. При монтаже
стальных и сталежелезобетонных конструкций следует соблюдать требования СП
48.13330, настоящего раздела.
При монтаже
стальных конструкций висячих, вантовых и разводных мостов кроме требований
настоящего раздела следует выполнять специальные указания проекта сооружения,
ППР или других утвержденных документов, отражающих специфику сооружения
перечисленных систем мостов.
10.2. Все элементы
перед установкой их в конструкцию должны быть освидетельствованы. Состояние
элементов фиксируют актом. Металлоконструкции, имеющие повреждения или
деформации свыше допускаемых по нормативным документам, указаниям проекта на их
изготовление, должны быть освидетельствованы комиссией с составлением акта. В
комиссию должны входить представители строительной и проектной организаций,
заказчика и завода-изготовителя. По требованию заказчика в состав комиссии
могут быть включены представители научно-исследовательской организации.
Комиссия обязана
выявить причины возникновения дефектов, принять решения о способах их
исправления (или замене конструкций новыми) и указать организацию, которая должна
устранять дефекты. Акт освидетельствования высылается организации -
разработчику чертежей КМ.
Дефекты сварных
соединений, не обнаруженные на заводе, должен устранить завод - изготовитель
конструкций.
Заводские элементы,
в которых выявлены трещины в основном металле или в металле сварных швов,
переходящие на основной металл, или расслоения по кромкам, должны быть
заменены.
10.3.
Деформированные элементы (или отдельные их участки), не имеющие надрывов,
трещин и острых переломов, следует выправлять термическим или термомеханическим
способом. Правку этими способами необходимо выполнять по соответствующим
нормативным документам. Все деформированные элементы следует выправлять до
подачи их на монтаж. Акты обследования с рекомендациями по правке и приемке выправленных
конструкций с участием проектной организации и заказчика высылаются организации
- разработчику документации КМ.
10.4. При выгрузке
и складировании элементы стальных конструкций необходимо укладывать устойчиво
на деревянные подкладки толщиной не менее 150 мм, расстояние между которыми
должно исключать образование остаточных деформаций. При складировании в
несколько ярусов прокладки необходимо укладывать по одной вертикали с нижними.
Металлоконструкции не должны соприкасаться с грунтом в обязательном порядке;
минимальный зазор между конструкцией и грунтом - 150 мм. На конструкциях не
должна застаиваться вода. Высота штабеля не должна превышать 1,5 м. Фасонки,
накладки и другие мелкие стальные детали следует хранить на стеллажах со
сплошным дощатым настилом, а высокопрочные болты и прочие метизы - в закрытом
помещении или на стеллажах под навесами.
Не допускается
приварка или прихватка монтажных приспособлений к основным конструкциям.
При монтаже
стальных и сталежелезобетонных конструкций следует предусматривать их
заземление.
10.5. Вместе с
поставляемой на стройплощадку партией металлоконструкций завод-изготовитель
обязан представить в мостостроительную организацию сертификат качества на
данные стальные конструкции. После завершения заводом выполнения определенного
номера заказа к сертификату на весь заказ должна прилагаться следующая
документация:
полный комплект
исполнительных чертежей КМД, включая схему маркировки (монтажные схемы);
сводная ведомость
сертификатов на материалы, применявшиеся при заводском изготовлении данных
конструкций;
опись
аттестационных удостоверений заводских сварщиков, проводивших сварку конструкций
на заводе, с указанием даты и номера протокола их аттестации, выданного
аттестационным центром национального агентства контроля и сварки (НАКС);
ведомость
заключений контроля качества заводских сварных соединений методом
ультразвуковой дефектоскопии (УЗД) с указанием мест устранения дефектов (если
такие имелись).
10.6. Демонтаж
элементов соединения и усиления допускается производить при отсутствии в них
усилий, что достигается, как правило, поддомкрачиванием пролетного строения на
соответствующие перемещения и усилия. Необходимые величины перемещений, усилий
в домкратах и места их приложения должны быть приведены в ППР и
контролироваться в процессе демонтажа.
10.7. При монтаже
пролетных строений в северном исполнении необходимо принимать меры по предотвращению
хрупких разрушений металла.
10.8. Сварные
монтажные соединения надлежит выполнять по технологии, указанной в
ведомственных нормативных документах и технологических регламентах на монтажную
сварку конкретного объекта.
10.9. Сварку
тавровых соединений гибких арматурных упоров объединения железобетонной плиты с
главными балками следует выполнять оборудованием, обеспечивающим высокую
стабильность качества сварочного соединения согласно требованиям
Технологического регламента и (или) Руководства по эксплуатации. Оборудование
должно состоять из источника постоянного тока обратной полярности, мобильного
устройства с автоматическим циклом сварки и автоматической подачей флюса в зону
сварки, балластного сопротивления и гибкого кабеля длиной 30 метров и площадью
сечения 70 мм2.
Устройство
монтажных соединений
10.10. В
фрикционных соединениях для обеспечения расчетных коэффициентов трения
по контактным поверхностям требуется
специальная подготовка. В таблице 20 приведены значения коэффициентов трения
и надежности
в зависимости от способов подготовки
контактных поверхностей.
Таблица 20
┌─────────────────────────────────────┬────────────┬──────────────────────┐
│ Способ подготовки контактных │
Значение │Значение
коэффициента │
│ поверхностей во фрикционных │коэффициента│ надежности гамма │
│ соединениях │ трения мю │ bh │
│
│ │при
количестве болтов │
│
│ │ в полустыке: │
│ │
├───────┬──────┬───────┤
│
│ │ 2 - 4
│5 - 19│ 20 │
│
│ │ │ │и более│
├─────────────────────────────────────┼────────────┼───────┼──────┼───────┤
│1.
Дробеструйный или пескоструйный
│ 0,58 │
1,4 │ 1,3 │
1,2 │
│двух
поверхностей без нанесения
│ │ │ │ │
│фрикционной
грунтовки или с │ │ │ │ │
│последующим
нанесением грунтовки │ │ │ │ │
│на
этилсиликатной основе на обе
│ │ │ │ │
│поверхности
толщиной по 60 - 80 мкм │ │ │ │ │
├─────────────────────────────────────┼────────────┼───────┼──────┼───────┤
│2.
Дробеструйный или пескоструйный
│ 0,46 │
1,4 │ 1,3 │
1,2 │
│двух
поверхностей с последующим
│ │ │ │ │
│нанесением
на одну поверхность │ │ │ │
│
│этилсиликатной
грунтовки, на другую -│
│ │ │ │
│полиуретановой,
60 - 80 мкм │ │ │ │ │
├─────────────────────────────────────┼────────────┼───────┼──────┼───────┤
│3.
Дробеструйный или пескоструйный
│ 0,38 │
1,4 │ 1,3 │
1,2 │
│двух
поверхностей без нанесения
│ │ │ │ │
│фрикционной
грунтовки или с │ │ │ │ │
│последующим
нанесением полиуретановой│
│ │ │ │
│грунтовки
на обе поверхности толщиной│
│ │ │ │
│60
- 80 мкм
│ │ │ │ │
├─────────────────────────────────────┼────────────┼───────┼──────┼───────┤
│4.
Газопламенная обработка двух
│ 0,42 │
2 │ 1,6 │
1,3 │
│поверхностей
с полным удалением │ │ │ │ │
│прокатной
окалины │ │ │ │ │
├─────────────────────────────────────┼────────────┼───────┼──────┼───────┤
│5.
Очистка стальными
│ 0,35 │
2,5 │ 1,8 │
1,4 │
│механизированными
щетками двух │ │ │ │ │
│поверхностей
(без эффекта шлифовки) │ │ │ │ │
└─────────────────────────────────────┴────────────┴───────┴──────┴───────┘
Вид обработки
контактных поверхностей фрикционных соединений должен быть указан в чертежах
КМ.
10.11. Перед
обработкой контактных поверхностей фрикционных соединений с них необходимо
удалить наждачным кругом все неровности, в том числе заусенцы вокруг отверстий,
препятствующие плотному прилеганию элементов и деталей. Заусенцы на краях
отверстий должны быть удалены без снятия фасок.
Для пескоструйной
обработки следует применять сухой кварцевый песок фракций 0,6 - 2,5 мм; для
дробеструйной - литую или рубленую стальную дробь марок ДСЛ, ДСР N 0,8; 1,0;
1,2 по ГОСТ 11964. Сжатый воздух, используемый для обработки поверхностей,
должен быть очищен от влаги и масла.
При газопламенной
очистке контактных поверхностей следует применять, как правило, широкозахватные
кислородоацетиленовые горелки. Допускается применять пропан-бутан или природный
газ взамен ацетилена. При кислородоацетиленовой очистке горелки следует
перемещать со скоростью 1 м/мин, горение ацетилена должно происходить при
избытке кислорода.
Газопламенная
обработка поверхностей металлопроката толщиной менее 5 мм не допускается. Во
избежание коробления металл толщиной 5 - 10 мм следует очищать за два прохода
при скорости перемещения горелки, увеличенной до 1,5 - 2 м/мин.
Отставшую окалину и
продукты сгорания (шлак) следует удалять с поверхности сжатым воздухом или
металлическими щетками.
10.12. Контактные
поверхности болтовых соединений перед сборкой должны быть осмотрены и очищены
от грязи, льда, рыхлой ржавчины, отстающей окалины, масла, краски (за
исключением заводской грунтовки). Способ очистки назначается в зависимости от
характера загрязнения.
10.13.
"Черные" метизы (болты, гайки, шайбы), т.е. высокопрочный крепеж без
покрытия, перед постановкой в соединения необходимо очищать от заводской
консервирующей смазки.
Расконсервацию
метизов осуществляют кипячением в воде или выдержкой в течение 15 - 20 мин в
подогретом до 80 - 100 °C щелочном растворе следующего состава, в частях по
массе: каустической соды (натрий едкий по ГОСТ 2263) - 3: кальцинированной соды
(натрий углекислый по ГОСТ 5100) - 2; тринатрийфосфата (натрий фосфорнокислый
по ГОСТ 201) - 3; жидкого стекла (натрий кремний-кислый по ГОСТ 13078) - 2;
воды - 90. Остатки щелочного раствора удаляют промывкой метизов в воде, после
чего выполняют их сушку. После сушки выполняют очистку резьбы болтов
металлической щеткой и после контрольной прогонки выполняют смазку резьбы.
10.14. Для смазки
резьбы болтов, гаек и шайб после контрольной прогонки и окончательной очистки
резьбы рекомендуется опустить их в решетчатой таре в емкость объемом >= 0,4
м3 с составом из 80% неэтилированного бензина по ГОСТ Р 51866 и 20%
минерального масла по ГОСТ Р 51634 (типа автол) или трансмиссионного масла.
После извлечения метизов из этой емкости бензин испаряется, а на поверхности
высокопрочного крепежа остается тонкий слой смазки. Время испарения бензина при
положительной температуре составляет ~= 2 ч; ориентировочный расход бензина на 100
кг метизов составляет 2 л, масла - 0,4 л.
10.15. Допускается
смазывать резьбу высокопрочного крепежа путем опускания после очистки
металлической щеткой резьбы каждого болта на 5 - 7 мм в минеральное масло типа
автол или трансмиссионное масло. После стекания излишков масла выполняют
навинчивание гайки на этот болт по всей длине его резьбы.
10.16. Очищенные и
смазанные болтокомплекты (болт + 2 шайбы + гайка) следует хранить в закрытой
таре.
При комплектации
болтов гайками последние не должны иметь большого люфта и в то же время должны
свободно навинчиваться на болт "от руки", т.е. каждую пару "болт
+ гайка" проверяют при комплектации на наличие люфта в резьбе.
Комплектование
обработанных болтов двумя шайбами и гайкой выполняют одновременно с сортировкой
болтов по длинам. На монтаж подготовленные высокопрочные болты отправляют в
металлических емкостях с отсеками для болтов разной длины.
10.17. Период
времени от смазки метизов до их установки в соединение не должен превышать 10
сут, а до натяжения на расчетное усилие - 20 сут. Более длительное хранение
увеличивает коэффициент закручивания. При превышении срока хранения (более 10
сут) укомплектованные метизы должны быть повторно смазаны.
10.18. Во
фрикционном соединении ставить невысокопрочные болты в процессе монтажа не
допускается.
Конструкции с
болтовыми соединениями класса B и класса A точности вначале следует собирать на
временных болтах и пробках. Для достижения точного совпадения отверстий и
плотной стяжки пакета пробками заполняется 10% (но не менее 3 шт.), а болтами -
20% общего числа отверстий. При числе отверстий менее 10 устанавливаются 2 - 3
пробки и 1 - 2 болта.
Если по условиям
монтажа развертывание (райберование) отверстий и постановка в них постоянных
болтов невозможны сразу же за сборкой соединения, допускается число пробок
определять расчетом на действие строительных нагрузок, при этом число временных
болтов должно быть не менее 40% расчетного числа пробок. Пробки следует
рассчитывать на срез и смятие по СП 35.13330 в зависимости от прочности стали,
из которой они изготовлены. Диаметр временных (сборочных) болтов допускается
назначать на 1 - 6 мм меньше диаметров отверстий. Временные болты принимают,
как правило, точности класса C по ГОСТ 15589. Они должны обеспечить плотное
стягивание элементов в соединении с затяжкой, как правило, гайковертами на
усилие не менее 49 кН (5 тс).
10.19. Во
фрикционном соединении, собираемом на пробках и болтах, высокопрочные болты
должны свободно - без усилий - проходить в отверстия собранного пакета. При
затруднениях в постановке болтов из-за черноты, овальности или косины отверстий
следует развертывать их коническими развертками, диаметр которых не должен быть
менее номинального диаметра болтов и не более проектного диаметра отверстий.
Развертывание допускается только в плотно стянутых пакетах без применения
смазочно-охлаждающих жидкостей и воды.
В болтовых
соединениях несущего типа повышенной класса A или нормальной класса B точности
развертывание или прочистку отверстий следует производить коническими
развертками, диаметр которых соответствует принятому в проекте диаметру
отверстий с соответствующими допусками.
10.20. Каждый
высокопрочный болт фрикционного соединения комплектуется одной гайкой и двумя
круглыми шайбами - под головку болта и под гайку по ГОСТ Р 53664.
Если в стесненных
местах при ремонте и усилении старых мостов установить две шайбы невозможно,
допускается установить одну шайбу под деталь, которая при натяжении болта будет
вращаться при разности диаметров болта и отверстия не более 3 мм и размерах
головки болта и гайки по ГОСТ Р 53664.
Постоянные
цилиндрические болты класса B и класса A точности соединений несущего
(нефрикционного) типа комплектуют одной гайкой, одной шайбой под головку и
одной-двумя шайбами под гайку. В соединениях, где болты работают на срез и
смятие, резьба болта должна находиться вне отверстия, а гладкая часть стержня
не должна выступать из шайб.
В каждом затянутом
болте со стороны гайки должно оставаться не менее одного полного витка резьбы.
10.21. Гайки
высокопрочных болтов, натянутых до расчетных усилий, ничем дополнительно
закреплять не следует. В болтовых соединениях гайки закрепляют от раскручивания
с помощью пружинных шайб по ГОСТ 6402 или контргаек. Пружинные шайбы не следует
применять совместно с круглыми и при разности d болта и отверстия более 3 мм.
10.22. В болтовых и
фрикционных соединениях при монтаже металлоконструкций точное совпадение
отверстий обеспечивается постановкой монтажных точеных пробок номинальным
диаметром на 0,2 мм меньше проектного диаметра отверстий. Длина цилиндрической
части пробки должна быть на 10 - 15 мм больше толщины собираемого пакета.
Пробки для сборки
конструкций в обычном и северном исполнениях должны быть изготовлены из сталей
марки ВСт5пс2 по ГОСТ 535 или марки 295-6 по ГОСТ 19281.
10.23. Натяжение
высокопрочных болтов на расчетные усилия по СП 35.13330 следует производить
завинчиванием за гайку или головку болта до требуемой расчетной величины
крутящего момента M, определяемого по формуле
M = KPd,
где K - коэффициент
закручивания, равный 0,175 для "черных" болтов производства заводов
ОАО "Мостостройиндустрия" без покрытия и диапазона от 0,14 до 0,2 по
ГОСТ Р 53664;
P - расчетное
усилие натяжения высокопрочного болта. Для болтов диаметром 22, 24 и 27 мм
принимаются соответственно расчетные усилия 220 кН (22,5 тс); 258 кН (26,3 тс)
и 334 кН (34,2 тс) по ГОСТ Р 53664, для болтов класса 10.9 из стали марки 40Х
"селект" - по ГОСТ 4543;
d - номинальный
диаметр резьбы болта.
Болты чисто
фрикционных соединений необходимо, как правило, вначале затягивать гайковертом
до 50 - 90% расчетного усилия, затем дотягивать динамометрическим ключом до
расчетного усилия с контролем натяжения по величине прикладываемого крутящего
момента после геодезического контроля собранного фрикционного соединения.
Гидравлические
динамометрические ключи типа ГГ-200 следует тарировать перед первым их
применением (или после ремонта), повторно - после натяжения первой и второй
тысячи болтов, а затем периодически после натяжения каждых 5000 болтов.
Ручные
динамометрические ключи следует тарировать в начале и в середине каждой рабочей
смены контрольным грузом.
Все
динамометрические ключи, находящиеся в работе, должны быть пронумерованы.
Результаты их тарировки следует заносить в специальный журнал.
10.24. Натяжение
болтов необходимо производить от участков с плотным прилеганием деталей
соединяемого пакета к участкам с зазорами. Болты, расположенные рядом с
пробками, следует затягивать повторно после удаления пробок. В соединениях с
затянутыми болтами не допускаются зазоры между плоскостью конструкции, шайбами,
гайками и головками болтов. При остукивании молотком болт не должен дрожать и
смещаться.
10.25. Болты
комбинированных соединений (в узле сочетаются сварные и болтовые соединения)
натягивают в несколько этапов:
1) Установленные
высокопрочные болты на первом этапе затягивают с помощью пневматических
гайковертов до усилий, равных 60 - 70% проектного. Проверяют плотность
стягивания пакета, при этом определенные ряды болтов, по технологическому
регламенту, затягивают обычным "рожковым" ключом от руки.
2) Проводят весь
комплекс сварочных работ и выполняют геодезическую съемку данного
комбинированного узла.
3) Выполняют
дотяжку (тарировку) на следующем этапе после окончания всех сварочных работ на
конкретном узле пролетного строения высокопрочных болтов до проектных усилий
(на 100%) динамометрическими ключами статического действия с обеспечением при
этом требуемых величин крутящих моментов и торцы болтов помечают краской.
4) Сдают
фрикционное соединение на высокопрочных болтах представителю технадзора
Заказчика.
5) Выполняют
антикоррозионную защиту фрикционного соединения на высокопрочных болтах по
технологическому регламенту.
10.26. Натяжение
высокопрочных болтов на проектные усилия следует производить, как правило,
после окончания проверки проектного геометрического положения конструкции или
ее части. Гайки или головки болтов, натянутых на проектные усилия, отмечают
светлой масляной краской. Затянутые высокопрочные болты на проектное усилие
принимает представитель технадзора заказчика. Все работы по натяжению и
контролю регистрируют в журнале постановки высокопрочных болтов (ВПБ).
При приемке
смонтированных конструкций с фрикционными соединениями строительной
организацией должна быть предъявлена следующая документация:
журнал контроля
качества подготовки контактных поверхностей;
журнал контрольной
тарировки динамометрических ключей;
журнал постановки
высокопрочных болтов;
сертификаты
завода-изготовителя на метизы.
10.27.
"Чернота" (несовпадение отверстий в деталях собранного пакета) не
должна превышать разности номинальных диаметров отверстия и болта.
10.28. При подборе
болтов по длине применяют специальный щуп для промера толщины пакета, а для
удобства узлы размечают мелом с выделением участков, на которых устанавливают
болты одинаковой длины.
При сборке
конструкций из ПКМ длина болтов определяется из условия соединения
конструктивных элементов без захода резьбовой части на элементы из ПКМ.
Допускается по
согласованию с проектной организацией устанавливать в отверстие втулку из
нержавеющей стали с фланцем или без фланца в зависимости от ее конструкции с
размерами:
внутренний диаметр
на один миллиметр больше диаметра болта;
наружный диаметр
цилиндрической части втулки на 2 мм больше ее внутреннего диаметра;
диаметр фланца не
менее удвоенного наружного диаметра цилиндрической части втулки.
Втулки следует
устанавливать на клее холодного отверждения.
10.29. Каждый болт
устанавливают в соединении с двумя шайбами (одна ставится выпуклой стороной к
головке болта, а другая - выпуклой стороной к гайке). Ставить более одной шайбы
с каждой стороны пакета запрещается.
При сборке
конструкций из ПКМ используются 2 вида шайб:
при контакте с
элементом из ПКМ устанавливаются шайбы по ГОСТ 6958 (увеличенные);
при контакте с
металлическим элементом устанавливаются шайбы по ГОСТ 11371 (обычные).
10.30. В момент
установки высокопрочных болтов гайки должны свободно (от руки) навинчиваться по
резьбе и в то же время не иметь большого люфта. В противном случае гайку или
болт следует заменить, а отбракованные болты и гайки отправить на повторную
подготовку и комплектацию.
10.31. Длины болтов
назначают в соответствии с суммарной толщиной собираемых деталей, высотой гайки
и двух шайб с округлением до 10 мм. При этом выступающая за пределы гайки часть
болта (за исключением соединения элементов из ПКМ) должна иметь не менее одного
витка резьбы.
10.32. Все
поставленные высокопрочные болты затягивают сначала пневматическими
гайковертами. Причем, вначале затягивают гайковертами стяжные болты, которые
должны быть равномерно распределены по полю соединения и в непосредственной
близости от пробок.
10.33. Болты
затягивают окончательно (на 100%) специально протарированным контрольным
динамометрическим ключом, отсчет по которому берут в начале движения.
Рекомендуется затягивать высокопрочные болты (наносить метки на стекло измерительного
прибора динамометрического ключа) на усилие, превышающее проектное на 10% (на
релаксацию от обжатия всех элементов соединения).
При контроле
затяжки высокопрочных болтов представителем технадзора Заказчика фактический
момент закручивания должен быть не менее проектного и не превышать его более
чем на 20%. При обнаружении в узле хотя бы одного болта, не удовлетворяющего
этому требованию, контролю подлежат все болты соединения в данном узле. При
натяжении болтов за их головку величину указанных крутящих моментов следует
увеличить на 5%.
Натяжение болтов,
при контроле которых крутящие моменты выходят за указанные пределы, должно быть
доведено до требуемого значения.
10.34.
Динамометрические ключи должны быть пронумерованы. Их следует подвергать тарировке
в начале и в середине каждой рабочей смены. Результаты тарировки заносят в
специальный журнал ("Журнал тарировки динамометрических ключей").
10.35. При
натяжении высокопрочных болтов необходимо строго следить за тем, чтобы болты не
получали недопустимой перетяжки гайковертами. При этом должна обеспечиваться
возможность дотягивания болтов динамометрическими ключами путем поворота гайки
на небольшой угол (до 30 - 60°).
10.36. Применяемые
для натяжения высокопрочных болтов на проектные усилия (на 100%) ручные
рычажные динамометрические ключи должны обеспечивать регистрацию крутящих
моментов с погрешностью +/- 5%. Передаваемые ключом крутящие моменты
регистрируют во время движения ключа в направлении, отвечающем увеличению
натяжения. Затяжку болтов следует производить плавно и без рывков.
10.37. Сварные
монтажные соединения следует выполнять в соответствии с требованиями [8],
настоящего свода правил, проекта конструкции, технологических регламентов и
ППР. Перед сваркой металл следует прогревать пламенем газовой горелки.
Монтажную сварку разрешается производить при температуре металла не ниже минус
20 °C.
10.38. При
комплектации сварочных постов мостостроительной организации необходимо
выполнить ревизию каждого источника питания сварочной дуги, сварочных
автоматов, полуавтоматов и цепей управления, при этом особое внимание следует
обратить на качество изоляции всех проводов, а также на надежность выполнения
всех электрических соединений силовых, сварочных кабелей и цепей управления
указанным оборудованием.
10.39.
Приготовление металлохимической присадки - МХП (смешивание "крупки" с
химической добавкой) следует выполнять в специальном смесителе. Равномерное
обволакивание ("опудривание") химической добавкой металлических
гранул ("крупки") достигают при перемешивании в течение 4 - 5 мин.
После опудривания крупку необходимо просеять на сите с ячейкой 1 x 1 мм для
удаления излишков химической добавки.
10.40. Обрезку
технологических припусков элементов монтируемых металлоконструкций следует
выполнять полуавтоматами кислородной резки, обеспечивающими необходимое
качество резки. После этого требуется зачистка поверхности только от окалины и
грата без снятия основного металла.
Для обрезки
припусков небольшой протяженности (<= 500 мм) допускается ручная резка, при
этом должны быть обеспечены требования к качеству кромок по чертежам КМ после
зачистки их абразивным инструментом с удалением всех дефектов поверхности на
глубину не менее 1 мм.
10.41. Для удаления
отдельных дефектных участков стыкового или углового шва рекомендуется применять
газопламенные резаки с внутрисопловым смешением газов. Для вырезки дефектов шва
небольшой протяженности, а также для зачистки и механической обработки швов
рекомендуется применять механизированный инструмент (шлифовальные машинки)
различного типа и шлифовальные круги различного типа и толщин согласно
паспортным данным применяемого оборудования.
10.42. Удалять шлак
с поверхности шва и/или слоев шва рекомендуется малогабаритными пневмомолотками
различного типа.
10.43. Для
снабжения воздухом пневмоинструмента и пескоструйного оборудования
рекомендуется применение высокопроизводительных компрессоров, оснащенных
блоками подготовки воздуха (влаго- и маслоотделителями).
10.44. Монтажную
сварку конструкций стальных мостов надлежит выполнять в соответствии с
требованиями технологического регламента, устанавливающего последовательность
сборочно-сварочных операций на конкретном объекте, применяемую оснастку,
инструмент, оборудование, сварочные материалы, режимы сварки и порядок
наложения швов, операции по контролю качества.
10.45. Монтажная
сварка мостовых конструкций при температуре воздуха минус 20 °C и ниже должна
выполняться с применением технологических (защитных) укрытий, установленных с
лицевой и обратной сторон монтажного соединения, обогреваемых калориферами или
теплогенераторами. Температура воздуха внутри укрытий должна быть не ниже минус
10 °C на расстоянии 1 м от кромки стыка (по вертикали).
10.46. Переноска и
перекантовка краном собранных на прихватках крупногабаритных монтажных блоков
без применения специальных приспособлений, обеспечивающих неизменяемость их
формы, не допускаются.
10.47. При сборке
элементов под сварку на клетках, стендах, стапелях следует обеспечить проектный
строительный подъем пролетного строения. Необходимо также предусматривать
предварительные переломы и сдвиги в стыках для компенсации сварочных
деформаций, влияющих на окончательные размеры и форму конструкций. Величины их
назначаются в ППР и проверяются при сварке первых блоков. При сборке и сварке
крупных блоков необходимо учитывать также их деформации и взаимные смещения в
стыках от воздействия солнечной радиации.
Соединения,
собранные под сварку, должны быть предъявлены руководителю сварочных работ.
Если подготовленные стыки в течение 24 ч не были сварены, перед сваркой их
вновь необходимо предъявить.
Номер каждого
выполненного стыка по маркировочной схеме и дату сварки заносят в Журнал
сварочных работ с росписями сварщика и руководителя сварочных работ.
10.48. Элементы,
свариваемые на монтаже двусторонними швами с перекантовкой, допускается
перекантовывать только после остывания шва
первого прохода до температуры не выше 100 °C
с принятием мер против динамических нагрузок, а для стыков толщиной 25 - 40 мм
- не более 40 °C.
10.49. При
автоматической сварке под флюсом, в том числе и с применением МХП,
механизированной сварке в смеси защитных газов и ручной дуговой сварке стыковых
соединений с односторонними швами в нижнем положении следует применять съемные
(несплавляющиеся) подкладки, обеспечивающие формирование обратной стороны шва
без последующей его подварки и, как правило, без механической обработки.
Рекомендуются
следующие формирующие подкладки:
стекло-медные - для
автоматической сварки под флюсом и с МХП металла толщиной до 16 мм
включительно;
медные со
стеклотканью - для автоматической сварки под флюсом и с МХП металла всех
толщин;
медные со
стеклотканью - для автоматической сварки под флюсом по ручной или
механизированной подварке корня шва, для односторонней ручной дуговой сварки на
100% сечения шва в нижнем положении, а также для односторонней механизированной
сварки в смеси защитных газов в нижнем положении;
керамические - для
механизированной сварки в смеси защитных газов и ручной дуговой сварки.
Для медных
подкладок следует применять листовую или полосовую медь марок М0, М1, М1р, М2,
М2р, М3, М3р (ГОСТ 859 и ГОСТ 1173).
10.50. При сборке и
сварке монтажных соединений металлоконструкций пролетного строения следует
проводить пооперационный контроль качества выполнения требуемой цепочки
технологических операций в последовательности выполнения сначала сборки
монтажного соединения и затем его сварки.
10.51. К
неразрушающему ультразвуковому контролю качества монтажных сварных стыковых
соединений допускаются специалисты, аттестованные в установленном порядке на
второй уровень квалификации по ультразвуковой дефектоскопии (УЗД) сварных
соединений на объектах (металлоконструкции технических устройств, зданий и
сооружений) перечня объектов контроля; они обязаны иметь при себе во время
контроля швов действительные удостоверения, а копии указанных удостоверений
следует вложить в журналы сварочных работ.
10.52.
Исполнительной документацией по качеству сварных конструкций являются: журналы
монтажных работ; общий журнал работ; постановки и натяжения высокопрочных
болтов; сварочных работ; журнал ультразвукового контроля качества (УЗК)
монтажных сварных соединений; журнал пескоструйной очистки; журнал тарировки
динамометрических ключей; журнал контроля подготовки высокопрочных болтов, гаек
и шайб; технологический регламент по сборке и сварке монтажных соединений;
заключения по результатам неразрушающих методов контроля качества швов с
указанием всех обнаруженных дефектов (допустимых и недопустимых); заключения и
протоколы испытаний контрольных сварных технологических проб; акты проверки
соблюдения технологии монтажной сварки; материалы по выявлению причин появления
дефектов в швах и т.п.
10.53. Для создания
сквозной системы контроля за качеством сборочно-сварочных работ
мостостроительная организация разрабатывает маркировочную схему монтажных
сварных швов, в которой присваивается наименование и порядковый номер каждому
сварному шву, выполненному на монтаже, а также наименование, порядковый номер
швам и плитам, прошедшим укрупнительную сборку. Марки швов и элементов,
принятые в маркировочной схеме, едины для записи во всей исполнительной
документации. Маркировочную схему разрабатывают на каждое пролетное строение и
прикладывают к исполнительной документации.
10.54. Входной
контроль качества охватывает:
проверку полноты
проектно-технологической документации и ее соответствие требованиям норм;
контроль качества
поступающих на монтаж основных металлоконструкций;
контроль качества
поступающих в производство сварочных материалов путем проверки наличия и срока
годности свидетельств об их аттестации и проверки каждой партии сварочных
материалов в установленном порядке;
проверку состояния
сварочного оборудования, наличие и срок годности свидетельств об аттестации
оборудования;
контроль качества
поступающих в призводство сварочных технологий и режимов сварки путем
аттестации технологий сварки в АЦ НАКС;
проверку срока
годности документов (аттестационных удостоверений) у электросварщиков,
инженерно-технических работников и дефектоскопистов, выданных в соответствующих
аттестационных центрах.
10.55. Перед
началом монтажных сварочных работ на конкретном объекте, а также перед
передачей каждой новой партии одного из сварочных материалов на монтаж их
качество проверяется путем сварки и испытания контрольных технологических проб
с определением механических свойств. Сварка контрольных технологических проб
выполняется на стройплощадке конкретного строящегося объекта в реальных условиях
монтажа. По результатам испытаний таких контрольных сварных проб для
мостостроительной организации должны быть выданы протоколы испытаний и
заключения по возможности применения конкретных партий аттестованных сварочных
материалов в определенной их комбинации на стройплощадке при монтаже
металлоконструкций конкретного пролетного строения. Данные испытания и выдачу
указанных документов должны осуществлять специализированные организации.
Изготовление и испытание образцов из указанных контрольных сварных технологических
проб следует производить в соответствии с указаниями ведомственных нормативных
документов.
10.56. При приемке
сварных швов проводят визуально-измерительный контроль, ультразвуковой контроль
(УЗД) по ГОСТ 14782 и технологическому регламенту на монтажную сварку
конкретного объекта, а при необходимости уточнения данных ультразвукового
контроля выполняют радиографический контроль по ГОСТ 7512 (просвечивание
проникающим излучением), а также металлографические исследования макрошлифов на
торцах соединений и механические испытания контрольных сварных соединений по
ГОСТ 6996.
10.57. Швы
монтажных сварных соединений должны удовлетворять следующим условиям:
а) иметь гладкую
или равномерно чешуйчатую поверхность с плавными переходами к основному
металлу, без наплывов и не допускаемых подрезов (см. таблицу 21);
б) в многопроходных
швах облицовочные валики должны перекрывать друг друга на 1/3 ширины, а глубина
межваликовых впадин не должна превышать 0,5 мм;
в) все кратеры
должны быть заварены;
г) не должны иметь
недопустимых поверхностных дефектов;
д) механическая
обработка шва и околошовной зоны должна соответствовать чертежам КМ и
требованиям документации на неразрушающий контроль. Радиусы сопряжений в зонах
сплавления при механической обработке угловых швов должны быть не менее 3 мм,
стыковых швов - не менее 10 мм.
Таблица 21
Номинальный
размер катета
углового шва в тавровых,
угловых и нахлесточных
соединениях, мм
|
Предельные отклонения катета, мм,
при способе сварки
|
автоматическая
и механизированная
под флюсом
ГОСТ 8713,
ГОСТ 11533
|
механизированная
в смеси
защитных газов
ГОСТ 14771,
ГОСТ 23518
|
ручная
ГОСТ 5264,
ГОСТ 11534
|
До 5 включительно
|
+1
|
+1; -0,5
|
+1; -0,5
|
Св. 5 до 8 включительно
|
+2
|
+2; -1
|
+2; -1
|
Св.
8 до 12 включительно
|
+2,5
|
+2,5; -1,5
|
+2,5;
-1,5
|
Свыше 12
|
+3
|
+3; -2
|
+3; -2
|
Допускаемая вогнутость
углового шва
|
До 30% катета, но не более 3 мм
|
При несоблюдении
хотя бы одного из требований сварные швы подлежат ремонту до проведения
ультразвукового контроля и повторному визуально-измерительному контролю.
10.58. При
металлографическом исследовании макрошлифов на торцах сварных швов после срезки
выводных планок проверяют возможные дефекты в виде непроваров, пор и шлаковых
включений, трещин. На сварных технологических пробах, кроме того, определяют
коэффициент формы провара, ширину и очертание зон термического влияния (ЗТВ),
измеряют твердость различных зон сварного шва. В случае получения
неудовлетворительных результатов металлографического исследования макрошлифов
исследуют микроструктуру на полированных и травленых шлифах при сильном
увеличении (в 50 - 2000 раз) сварного шва и околошовной зоны с определением
размеров зерна.
Швы сварных
соединений не могут быть признаны годными, если по одному из использованных
методов контроля получены отрицательные результаты.
10.59. Соответствие
усилий натяжения высокопрочных болтов проектным контролируют путем выборочной
проверки крутящих моментов. Для этого проверяемый болт затягивают специально
протарированным контрольным динамометрическим ключом, отсчеты по которому берут
после начала поворота гайки, т.е. в движении гайки.
Усилие при контроле
и натяжении прикладывают с одной и той же стороны болта, отмечаемой мелом, ведя
поворот за гайку.
Количество болтов,
подлежащих контролю, - по таблице 22.
Таблица 22
Количество болтов в соединении,
шт.
|
Количество
болтов, подлежащих контролю,
шт.
|
До 5 включительно
|
2
|
От 6 до 20
|
3
|
21 и более
|
15%
|
При несоответствии
результатов контроля хотя бы для одного болта контролируют все болты данного
фрикционного соединения.
10.60. Конструкции
мостов со сварными монтажными соединениями после их сборки и сварки подлежат
поэтапной комиссионной приемке с составлением "Акта промежуточной приемки
ответственных конструкций".
Периодичность
приемки следует указывать в проекте производства работ (ППР) в зависимости от
способа монтажа конструкций и объемов выполняемых монтажно-сварочных работ.
При
конвейерно-тыловой сборке и продольной надвижке неразрезных стальных пролетных
строений приемку осуществляют перед надвижкой каждого очередного
смонтированного и сваренного участка пролетного строения. При наводке на плаву
- перемещаемыми секциями, при навесной сборке - попролетно или перед каждым
очередным перемещением монтажного крана по пролетному строению.
10.61. Допустимые
отклонения линейных размеров и геометрической формы смонтированных конструкций
пролетных строений стальных мостов приведены в таблице 23.
Таблица 23
─────────────────────────────────────────────┬─────────────────────────────
Наименование отклонения │ Значение предельного
│ отклонения, мм
─────────────────────────────────────────────┴─────────────────────────────
1.
Отклонение длины каждой главной балки
или
фермы пролетного строения от проектной
при
длине L, м:
до 50 включительно +/- 10
свыше 50
0,0002L
───────────────────────────────────────────────────────────────────────────
2.
Отклонение расстояний между соседними
узлами
главных ферм и связей при расстоянии
l,
м:
до 9 включительно 0,0003l
свыше 9
+/- 3
───────────────────────────────────────────────────────────────────────────
3.
Отклонение от проектных ординат
строительного
подъема пролетного строения,
смонтированного
целиком или частично
при
ординатах h, мм:
до 100 включительно +/- 10
свыше 100
+/- 0,1h
───────────────────────────────────────────────────────────────────────────
4.
Отклонение в плане оси главной балки 0,0002L
или
фермы от проектной оси при пролете L
───────────────────────────────────────────────────────────────────────────
5.
Отклонение в плане одного из узлов 0,001L
от
прямой, соединяющей два соседних с ним
узла
при длине панели L
───────────────────────────────────────────────────────────────────────────
6.
Отклонение расстояний между осями +/- 4
вертикальных
стенок сплошностенчатых
балочных
и коробчатых пролетных строений
───────────────────────────────────────────────────────────────────────────
7.
Отклонение расстояний по длине балок и +/- 2
коробок
между смежными вертикальными ребрами
жесткости,
к которым прикрепляются поперечные
балки
ортотропных и ребристых плит;
соответствующие
расстояния между поперечными
балками
ортотропных и ребристых плит
───────────────────────────────────────────────────────────────────────────
8.
Отклонение расстояний между осями
продольных
ребер ортотропных плит:
в зоне стыков и пересечений с поперечными +/- 2
балками
на других участках +/- 4
───────────────────────────────────────────────────────────────────────────
9.
Отклонения по высоте сплошностенчатых +/- 2
балок
и коробок в зоне цельносварных
или
комбинированных
───────────────────────────────────────────────────────────────────────────
10.
Допускаемая стрела выгиба осей элементов
длиной
l:
отдельных элементов главных ферм, балок, 0,001l, но не более 10 мм
коробок,
балок проезжей части
элементов связей 0,0015l, но не
более 15 мм
───────────────────────────────────────────────────────────────────────────
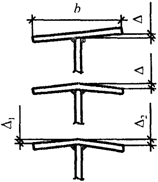
11.
Грибовидность, перекос, грибовидность
с
перекосом поясов сварных балок, коробок,
ортотропных
плит (для коробок и ортотропных плит
b
- величина свободного свеса пояса или настила,
для
двутавровых балок - ширина пояса)
11.1. В стыках, в местах сопряжения балок
с b/200, но не более 1 мм
другими
элементами, в зонах установки опорных
частей
и железобетонных плит с закладными
деталями
11.2. На других участках b/100 при
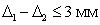
───────────────────────────────────────────────────────────────────────────
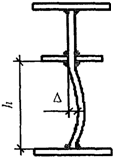
12.
Выпучивание стенки балок и коробок
при
свободной высоте стенки h
12.1. Для балок и коробок с поперечными 0,006h
ребрами
жесткости
12.2. Для балок без поперечных ребер
жесткости 0,003h
───────────────────────────────────────────────────────────────────────────
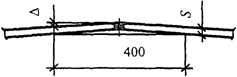
13.
Остаточные угловые деформации в сварных
стыковых
соединениях ("домики"), определяемые
стрелой
прогиба Дельта на базе 400 мм
при
толщине S стыкуемых листов, мм:
до 20 включительно 0,1S
свыше 20
2
───────────────────────────────────────────────────────────────────────────
14.
Допускаемая разность (в поперечном
направлении)
отметок узлов пролетного строения:
а) после установки его на опорные части
на опорах
0,001B
в пролете
0,002B
(B
- расстояние между осями ферм, балок,
коробок)
б) при сборке на подмостях, стапеле,
насыпи 0,001B
(B
- расстояние между стенками одной коробки
или
между осями смежных коробок)
───────────────────────────────────────────────────────────────────────────
Навесная,
полунавесная и уравновешенно-навесная сборки
10.62. В проекте на
навесную, полунавесную и уравновешенно-навесную сборки должны быть разработаны
и подтверждены расчетами, а в расчетах на ветровое воздействие, при
необходимости, и на моделях, способы обеспечения прочности, устойчивости и
неизменяемости собираемых конструкций и соединительных элементов на всех
стадиях монтажа.
10.63. Анкерные
закрепления пролетных строений должны быть рассчитаны из условия обеспечения
устойчивости положения системы "пролетное строение - кран" при максимальной
длине консоли и испытаны до начала монтажа нагрузкой, превышающей на 20%
расчетную нагрузку. Результаты испытаний анкеров следует фиксировать актом.
10.64. При
необходимости контроля за величиной опорной реакции на опоре устанавливают
гидродомкрат или гидравлический датчик давления (ГДД).
10.65. Для
обеспечения устойчивости против скольжения в продольном направлении монтируемое
пролетное строение следует, как правило, закреплять за капитальную опору через
неподвижные опорные части с установкой всех анкерных болтов или через подвижные
опорные части с установкой анкерных болтов и тщательным заклиниванием катков.
10.66. При
уравновешенно-навесном монтаже опережение сборки одной консоли пролетного
строения по отношению к другой более чем на одну панель не допускается. Для
замыкания консолей пролетного строения должны быть предусмотрены устройства,
обеспечивающие возможность вертикальных, горизонтальных и угловых перемещений
консолей для совпадения и фиксации торцов стыкуемых элементов. Замыкание
следует производить, как правило, в минимальные сроки при постоянной
температуре наружного воздуха.
10.67. Проектное
положение в плане и профиле собираемого навесным способом пролетного строения
должно обеспечиваться тщательной выверкой геометрического положения первых
панелей или надопорных блоков. Строительный подъем при этом должен
обеспечиваться точностью наведения отверстий в соединениях, определяющих
геометрию, с помощью точеных пробок и заполнения узлов болтами.
Регулировку
положения пролетного строения следует производить после его опускания на
очередную капитальную опору.
Отставание в
оформлении болтовых и фрикционных соединений от проектного в процессе сборки
должно быть минимальным и во всяком случае не более трех панелей, считая
собираемую.
При навесной сборке
пролетных строений с комбинированными болтосварными монтажными стыками все
сварные и болтовые соединения следует выполнять полностью в процессе сборки -
без отставаний.
10.68. При сборке
решетчатых ферм необходимо обеспечивать последовательное попанельное замыкание
геометрически неизменяемых секций; при сборке панелей в шпренгельных фермах -
геометрическую неизменяемость секций.
Вертикальную
подтяжку элементов при замыкании треугольников и точном наведении отверстий в
стыках допускается осуществлять сборочным краном при обеспечении контроля за
величиной прикладываемого усилия.
Одновременно со
сборкой секций главных ферм и элементов проезжей части необходимо устанавливать
продольные и поперечные связи в количестве, обеспечивающем устойчивость
собранной части пролетного строения. Отставание в сборке верхних продольных и
поперечных связей более чем на две панели, включая собираемую, не допускается.
10.69. При наводке
отверстий в собираемых конструкциях запрещается применять инструменты и приемы,
искажающие и сминающие отверстия. Запрещается проверять точность совпадения
отверстий пальцами.
10.70. Способы
перемещения и места закрепления монтажного крана на пролетном строении должны
быть указаны в ППР.
Перемещение
монтажного крана на очередную панель допускается только после образования
неизменяемой системы и установки проектного числа болтов.
Защита стальных
конструкций от коррозии
10.71. Основным
способом вторичной <1> защиты стальных конструкций от коррозии является
нанесение на их поверхность систем защитных покрытий на основе лакокрасочных
материалов.
--------------------------------
<1> Первичная
защита металлических конструкций от коррозии, отражающая требования к
проектированию конструкций без коррозионно-опасных зон-щелей, зазоров, карманов
с герметизацией таких зон до нанесения защитных покрытий в настоящем документе
не рассматривается.
10.72. Система
защитного покрытия, состоящая из грунтовочного, промежуточного и верхнего
(покрывного) слоев должна отвечать следующим требованиям:
надежно защищать
металл эксплуатируемых конструкций от коррозии при воздействии агрессивной
внешней среды и совокупности климатических факторов, соответствующих
макроклиматическому району расположения эксплуатируемого мостового сооружения
по ГОСТ 9.104 при категориях размещения по ГОСТ 15150;
иметь высокую
адгезию грунтовочного слоя к металлической поверхности и высокую межслойную
адгезию всех слоев системы покрытия;
промежуточный слой
системы покрытия должен отличаться высокими барьерными свойствами (способностью
препятствовать прониканию коррозионно-активных агентов к поверхности металла);
верхний покрывной
слой должен обладать высокими показателями прочности, износостойкости,
химстойкости, стойкостью к воздействию агрессивной атмосферы и жидких
агрессивных сред; стойкостью к УФ-излучению (при условии воздействия солнечной
радиации);
покрытия должны
быть быстросохнущими (время высыхания не более 24 ч), так как попадание на
непросохший слой загрязнений будет способствовать получению некачественной
защиты;
обладать
возможностью нанесения различными способами, преимущественно механизированными
(безвоздушное или пневматическое распыление).
10.73. Система
покрытия должна, как правило, иметь высокий прогнозируемый срок службы (не
менее 15 лет), поскольку затраты на восстановление покрытия часто превышают
затраты на его первичное нанесение, а качество восстановленного покрытия ниже
первоначального. Оценка срока службы защитного покрытия для конкретного
климатического района производится на основании ускоренных климатических
испытаний по ГОСТ 9.401. Выбор метода испытаний определяется условиями
эксплуатации конструкций мостового сооружения.
10.74. Процесс
производства работ по получению покрытий включает последовательное выполнение
операций по подготовке поверхности металлоконструкций, нанесению грунтовочного
покрытия, нанесению покрывных слоев, сушке каждого слоя покрытия и контролю
качества выполненного защитного покрытия.
10.75. Основную
часть работ по нанесению лакокрасочных материалов и получению надежных защитных
антикоррозионных покрытий рекомендуется производить на заводе-изготовителе.
Грунтовочный слой в обязательном порядке и промежуточный слой, по требованию
заказчика, необходимо наносить в заводских условиях с отапливаемыми цехами и
обеспечением пооперационного контроля подготовки поверхности, приготовления
составов ЛКМ и нанесения их на поверхность металла.
10.76.
Лакокрасочные покрытия для защиты стальных конструкций от коррозии следует
принимать по действующим нормативным документам.
Обезжиривание и
очистку поверхности следует производить в соответствии с требованиями ГОСТ
9.402.
Обезжиривание
производят с помощью щеток или ветоши, смоченных растворителем (уайт-спирит,
ацетон, сольвент и др.).
Очистку поверхности
металлоконструкций от ржавчины и окалины производят дробеметным или
дробеструйным способами. Допускается очистка труднодоступных мест
металлоконструкций с применением механизированного или ручного абразивного
инструмента.
После очистки
поверхность обеспыливают с помощью волосяных щеток или обдувкой сухим чистым
сжатым воздухом, который следует регулярно проверять на отсутствие в нем влаги
и масла.
В железнодорожных
мостах защиту от коррозии прилегающих к балластной призме поверхностей
металлического балластного корыта из черного проката следует осуществлять с
учетом требований настоящих правил в части работ в условиях монтажа, причем
степень очистки поверхностей перед нанесением защиты должна составлять не менее
, а
шероховатость, мкм, - Rz 40. Требования к материалам для защиты балластного
корыта следует указывать в проекте конструкций, причем в показатели свойств
следует включать в том числе адгезионную прочность после переменной нагрузки
тепло-холод и долговечность защиты - срок службы, как правило, не менее 25 лет.
Таблица 24
┌─────────────────────────────────┬─────────────────────┬─────────────────┐
│ Показатель │Нормативные значения │
Методы контроля │
│ │ показателей │ │
├─────────────────────────────────┼─────────────────────┼─────────────────┤
│1.
Долговечность системы покрытия│
Не менее 15 лет │ ГОСТ 9.401
│
├─────────────────────────────────┼─────────────────────┼─────────────────┤
│2.
Требования к материалам
│ Соответствие │
Проверка │
│ │ сертификатам, │ на соответствие │
│ │ стандартам, │ │
│ │ технической │ │
│ │ документации │ │
├─────────────────────────────────┼─────────────────────┼─────────────────┤
│3.
Внешний вид покрытия │
Отсутствие трещин, │ Визуально
│
│ │
пропусков, пузырей, │ по ГОСТ
9.407 │
│ │морщин
и др. дефектов│
│
├─────────────────────────────────┼─────────────────────┼─────────────────┤
│4.
Толщина покрытия │ Соответствие │
Толщиномеры │
│ │ технологическому │электромагнитного│
│ │ регламенту │ типа
│
│ │ для конкретной │ │
│ │ системы покрытия │ │
├─────────────────────────────────┼─────────────────────┼─────────────────┤
│5.
Адгезия покрытия к поверхности│ Не
более 2 баллов │ ГОСТ 15140,
│
│металла │ Не менее 2 МПа │
методом │
│ │ │ решетчатых
│
│ │ │ надрезов
│
├─────────────────────────────────┼─────────────────────┼─────────────────┤
│6.
Подготовка поверхности:
│
│ │
│
степень обезжиривания
│ Первая │ ГОСТ 9.402
│
│
степень очистки от окислов
│ Вторая │ ГОСТ 9.402
│
│ │ Sa 2, Sa 2 1/2 │ │
│
шероховатость
│ 40 - 80 │
ГОСТ 9.402 │
└─────────────────────────────────┴─────────────────────┴─────────────────┘
10.77. После подготовки
поверхности металлоконструкции ее, как правило, незамедлительно окрашивают.
Длительность перерыва между операцией подготовки поверхности и окрашиванием не
должна превышать 24 ч. При более длительном интервале поверхность осматривают
и, если ее состояние не соответствует требованиям 10.76, производят повторную
очистку.
Подготовленные под
окраску поверхности подлежат приемке отделом технического контроля завода или
мостовой инспекцией.
10.78. Технические
требования, которые следует выполнять при приемке работ, а также объем и
способы контроля приведены в таблице 25.
Таблица 25
┌────────────────────────────────────┬────────────────────┬───────────────┐
│ Технические требования │ Контроль │Способ контроля│
├────────────────────────────────────┼────────────────────┼───────────────┤
│1.
Допускаемое отклонение величины │
Решетчатых ферм - │ Измерительный
│
│ординат
строительного подъема после │ по узлам в уровне │(нивелирование)│
│установки
пролетного строения │ проезжей части; │ │
│на
опорные части (с учетом упругого │
сплошностенчатых │ │
│прогиба
от собственного веса
│пролетных строений -│ │
│пролетного
строения) для ординат │ в середине │ │
│высотой,
мм: │и
четвертях пролета │
│
│
100 и менее - не более 10 мм
│
│ │
│
св. 100 - не более 10%
│
│ │
├────────────────────────────────────┼────────────────────┼───────────────┤
│2.
Допускаемая разность (в │
Решетчатых ферм - │ Измерительный
│
│поперечном
направлении) отметок │ по узлам
в уровне │(нивелирование)│
│узлов
пролетного строения после
│ проезжей части; │ │
│установки
его на опорные части │ сплошностенчатых │ │
│при
расстоянии B между осями ферм,
│пролетных строений -│ │
│не
более:
│ в середине │ │
│
опорных узлов ферм и балок - 0,001B│и четвертях пролета │ │
│
одноименных узлов смежных ферм
│
│ │
│или
поперечных сечений балок -
│
│ │
│0,002B │ │ │
│
одноименных узлов смежных ферм
│
│ │
│железнодорожных
строений с ездой │ │ │
│на
стандартном мостобрусе - 8 мм
│
│ │
├────────────────────────────────────┼────────────────────┼───────────────┤
│3. Допускаемое отклонение в плане │ Каждого пролетного │
Измерительный │
│оси
главной балки или ферм
│ строения │
(съемка │
│от
проектной не более 0,0002L
│
│ в плане) │
│(где
L - пролет)
│
│ │
├────────────────────────────────────┼────────────────────┼───────────────┤
│4.
Допускаемое отклонение одного из │
Выборочный │
Измерительный │
│узлов
в плане от прямой, соединяющей│
при отклонении, │ (измерение
│
│два
соседних с ним узла, не более │
указанном в поз. 3 │
линейкой │
│0,001
длины панели
│ │
от натянутой │
│
│
│ струны) │
├────────────────────────────────────┼────────────────────┼───────────────┤
│5.
Допускаемая стрела выгиба осей
│
│ │
│элементов
длиной l: │ │ │
│
отдельных элементов главных ферм,
│Элементов, у которых│
Выборочный │
│балок
и балок проезжей части -
│обнаружена кривизна │ │
│0,001l │при
внешнем осмотре │
│
│
элементов связей - 0,0015l,
│
│ │
│но
не более 15 мм
│
│ │
├────────────────────────────────────┼────────────────────┼───────────────┤
│6.
Допускаемое выпучивание стенок
│ То же │ То же
│
│сплошных
балок высотой H не более │ │ │
│0,003H │ │ │
├────────────────────────────────────┼────────────────────┼───────────────┤
│7.
То же, при наличии ребер
│ " │ " │
│жесткости
не более 0,006H │ │ │
└────────────────────────────────────┴────────────────────┴───────────────┘
В заводских
условиях лакокрасочные покрытия следует наносить, включая подготовку
поверхности, в помещении при температуре от 5 до 40 °C и относительной
влажности воздуха не более 75%.
Влагоотверждаемые
одноупаковочные полиуретановые материалы допускается наносить при относительной
влажности воздуха от 40 до 98%.
10.79. В условиях
монтажа работы по нанесению лакокрасочных покрытий следует выполнять при
отсутствии атмосферных осадков, тумана, росы; при этом поверхность металла должна
быть чистой и сухой, температура стальной поверхности, подготовленной к
нанесению покрытия, должна быть на 3 °C выше точки росы.
10.80. Процесс
получения защитного антикоррозионного покрытия для металлических конструкций
следует проводить в соответствии с технологическими регламентами,
разработанными с учетом свойств материала и условий эксплуатации.
10.81. Технические
требования к качеству выполнения работ при получении защитных антикоррозионных
покрытий и методы контроля представлены в таблице 32.
10.82. Элементы
мостовых конструкций из ПКМ поступают на монтаж с нанесенным защитным
покрытием.
В случае проведения
на месте монтажа укрупненной сборки элементов или производства монтажа
посредством сварки производится местное восстановление лакокрасочного покрытия
(далее - ЛКП) узлов соединений. Нанесение ЛКП осуществляется в соответствии с
технологической инструкцией по его применению, являющейся неотъемлемой частью
проектной документации.
Обезжиривание
производят с помощью щеток или ветоши, смоченных растворителем (бензин,
ацетон). Допускается производить зачистку наждачной бумагой N 25,32 или
пескоструйную обработку поверхностей стеклопластиковых элементов. После очистки
поверхность обеспыливают с помощью волосяных щеток или обдувкой сухим чистым
сжатым воздухом и протирают ветошью, смоченной ацетоном.
Перерыв между
операцией подготовки поверхности и окрашиванием не должен превышать 1 ч. При более
длительном интервале между подготовкой поверхности и окрашиванием поверхность
повторно обезжиривают.
Окраску поверхности
производят эмалями, предусмотренными в проектной документации.
11.
Сооружение деревянных мостов
11.1. Нормы и
правила настоящего раздела распространяются на возведение железнодорожных,
автодорожных и городских постоянных деревянных мостов.
11.2. Деревянные
конструкции постоянных мостов следует изготовлять, как правило, на
специализированных заводах или в цехах. Конструкции железнодорожных мостов
следует применять только заводского изготовления.
Конструкции,
поступающие на строительную площадку, должны иметь максимальную заводскую
готовность.
Деревянные
конструкции для автодорожных мостов, за исключением клееных элементов,
допускается изготовлять на строительной площадке, соблюдая настоящие правила.
11.3. Для
изготовления деревянных конструкций следует применять породу древесины,
указанную в рабочей документации. Вместо сосны допускается использовать другие
хвойные породы (ель, пихту, кедр, лиственницу и т.п.) при согласовании замены с
проектной организацией-разработчиком.
11.4. Приемку с
входным контролем по СП 48.13330, сортировку и обмер лесоматериалов следует
производить с учетом породы древесины и вида лесоматериалов согласно требованиям
ГОСТ 2292, ГОСТ 6564, ГОСТ 3808.1, ГОСТ 6782.2, ГОСТ 9014.0 и ГОСТ 6782.1,
естественную сушку - по ГОСТ 3808.1 и ГОСТ 6782.2; хранение - по ГОСТ 9014.0.
11.5. Параметр
допустимой шероховатости поверхности элементов из пиломатериалов, в том числе
предназначенных для покраски, должен соответствовать требованиям ГОСТ 7016.
11.6. Отбор и
испытания образцов для определения прочностных характеристик древесины следует
производить при:
наличии указаний в
рабочей документации;
изготовлении
сквозных ферм и клееных балок;
использовании
древесины пониженной плотности;
замене на другую
породу древесины, не указанную в рабочей документации;
невозможности
объективной оценки качества древесины брусьев и круглых лесоматериалов по
сортообразующим признакам;
ширине годичных
слоев более 5 мм и содержании в них поздней древесины менее 20%.
11.7. Лабораторные
испытания по определению предела прочности образцов древесины следует
производить выборочно - не менее шести образцов от каждой партии лесоматериала
по ГОСТ 18321, испытания образцов из заготовок круглого леса и обрезных
пиломатериалов - по ГОСТ 21554.4, ГОСТ 21554.2, ГОСТ 21554.5, ГОСТ 21554.6; из
чистой древесины (малые образцы) - по ГОСТ 4.208.
Прочность образцов
клееного соединения древесины из пиломатериалов следует определять по ГОСТ
15613.3.
11.8. Припуск на
номинальные поперечные размеры пиломатериалов на усушку при распиловке круглого
леса с влажностью свыше 40% следует определять для хвойных пород по ГОСТ
6782.1, для лиственных пород - по ГОСТ 6782.2, увязав с допусками на
изготовление элементов.
11.9. Допуски,
характеризующие точность изготовления и сборки деревянных конструкций, следует
определять по ГОСТ 21779. Остальные отклонения не должны превышать допускаемых
отклонений, приведенных в таблице 26, а также в СП 45.13330.
11.10. Деревянные
конструкции и их элементы при хранении должны быть защищены от воздействия
атмосферных осадков и солнечной радиации. Элементы в штабелях должны опираться
на неповреждающие древесину прокладки с зазором, достаточным для проветривания,
и подкладки между элементами и грунтовым основанием не менее 20 см.
Клееные главные
балки пролетных строений следует хранить в положении, соответствующем рабочему
положению их в конструкции.
11.11. Для
обеспечения сохранности деревянных конструкций при погрузке, выгрузке и
транспортировании следует применять инвентарные устройства (мягкие стропы,
хомуты, контейнеры и т.п.) с установкой в местах опирания и соприкосновения элементов
с металлическими деталями мягких прокладок и подкладок (из прорезиненной ткани,
губчатой резины и др.).
11.12. Для
изготовления ответственных элементов и деталей соединений (опорных брусьев,
насадок, подушек, шпонок, нагелей и др.) следует использовать плотную,
прямослойную, не имеющую пороков древесину твердых лиственных пород, стойкую
против загнивания (дуба, бука).
11.13.
Лесоматериалы, бывшие в употреблении, допускаются к применению при условии, что
они удовлетворяют требованиям настоящих правил по качеству и прочности
древесины. Допускается выполнять ремонт и усиление отдельных несущих элементов
конструкции из лесоматериалов, бывших в употреблении.
11.14. Для
изготовления клееных элементов могут быть использованы пиломатериалы пониженной
сортности при условии удаления всех участков древесины, качество которых не
удовлетворяет требованиям рабочей документации.
11.15. Применение
разных пород древесины в одном несущем элементе конструкции не допускается.
Сухостойкую
древесину (высохшую на корню) всех пород, ввиду ее склонности к разрушению и
гниению, применять в деревянных мостах запрещается.
11.16. Влажность
древесины должна быть не более 25% (полусухая древесина). Влажность древесины
пиломатериалов не должна превышать 20%. Для дощатых ферм, а также мелких
деталей соединений (подушек, шпонок, колодок и др.) следует применять лес с
влажностью не более 15% (воздушно-сухая древесина).
11.17. Для
элементов клееных и клеефанерных конструкций пролетных строений применяют
пиломатериалы хвойных пород в соответствии с ГОСТ 8486, кроме пихты. Основным
материалом для клееных конструкций является сосна. Толщина пиломатериала до
строжки должна быть не более 40 мм - для элементов главных балок и не более 50
мм - для остальных элементов. Ширина досок не регламентируется.
11.18.
Бакелизированная фанера марок ФБС и ФБСВ должна быть склеена из березового
шпона с помощью фенол- или креозолформальдегидных смол. Рекомендуемая толщина
листов до 12 - 14 мм.
11.19. Для
склеивания элементов конструкций из пиломатериалов и фанеры должны применяться
фенолформальдегидные клеи КБ-3, ВИАМ-Ф9, резорциноформальдегидный ФР-12 и клеи
на основе эпоксидных смол.
11.20. Расчетные
металлические элементы из прокатного металла рекомендуется выполнять из
углеродистых горячекатаных сталей мартеновской или кислородно-конверторной
выплавки всех марок типа Ст3, стали для мостостроения М16С, а также
низколегированных конструкционных сталей 15ХСНД.
11.21. Окраска
деревянных элементов конструкций при влажности древесины свыше 22% не
допускается.
11.22. Строительные
гвозди по ГОСТ 4028, не удовлетворяющие по качеству требованиям ГОСТ 263, а
также гвозди, бывшие в употреблении, использовать в несущих соединениях
деревянных конструкций запрещается.
Применение гвоздей
по ГОСТ 4028 и высокопрочных дюбелей в соединениях элементов из древесины
лиственницы в замороженном состоянии не допускается.
11.23. Плоские рамы
надстроек опор следует собирать в горизонтальном положении на стеллажах,
выверенных по нивелиру и оборудованных шаблонами.
Надстройки опор
следует монтировать пространственными блоками или плоскими рамами. Перед
установкой в проектное положение в них необходимо произвести подтяжку и
подбивку скреплений и устранить дефекты, возникшие при транспортировании и
хранении.
По мере установки
блоков или рам надстроек, выверки положения в плане и по высоте их следует
раскрепить поярусно в жесткую геометрически неизменяемую систему постоянными, а
при необходимости - дополнительными временными связями.
Запрещается
приводить в проектное положение неправильно или с нарушением допусков собранную
надстройку опоры принудительной расклинкой, подтягиванием лебедкой, распором
домкратами, установкой дополнительных распорок и связей.
11.24. При
заготовке элементов конструкций должны быть предусмотрены припуски на их
номинальные размеры, устанавливаемые в зависимости от способа последующей
обработки элементов, включая концы, и влажности древесины (ГОСТ 6782.1 и ГОСТ
6782.2).
11.25. Поверхности
элементов деревянных конструкций должны быть остроганы (от коры и сучьев) с
сохранением естественной конусности (сбега). Цилиндровка бревен допускается
только при наличии указаний в рабочей документации.
11.26. Все
отверстия в деревянных и стальных элементах и деталях должны быть просверлены
на проектный диаметр (за исключением отдельных групп отверстий, оговоренных в
рабочей документации).
11.27. Отверстия в
элементах и деталях следует сверлить с использованием кондукторов, станков с
ЧПУ, приспособлений или шаблонов, позволяющих обеспечить в пределах допусков
взаимное проектное совпадение отверстий и взаимозаменяемость элементов и
деталей.
11.28. Монтажные
отверстия следует рассверливать на больший диаметр после окончания сборки
элементов и проверки всех контролируемых размеров конструкции, включая
строительный подъем.
11.29. Несущие
монтажные соединения деревянных конструкций следует собирать, как правило, на
постоянных крепежных деталях.
Порядок и
последовательность натяжения болтов и тяжей в конструкции должны исключать
образование в ней отклонений от проектного положения (перекосов, зазоров,
уступов и т.п.).
11.30. При перепаде
поверхностей (депланации), стыкуемых на накладках деревянных элементов,
превышающем нормируемую по таблице 26 величину, на выступающей части элемента
должен быть сделан скос с уклоном не круче 1:10 или использованы прокладки из
листового металла.
Таблица 26
┌────────────────────────────────────────┬──────────┬─────────────────────┐
│ Технические требования │ Контроль │ Способ контроля │
├────────────────────────────────────────┼──────────┼─────────────────────┤
│1.
Уменьшение фактических размеров
│ Каждого │ Приемочный, │
│поперечных
сечений несущих (расчетных) │
элемента │ измерительный │
│элементов
от проектных (в долях от
│ │ │
│диаметра
бревна или стороны бруса) 1/40 │
│
│
├────────────────────────────────────────┼──────────┼─────────────────────┤
│2.
Монтаж клеештыревого соединения
│ Каждого │ Операционный, │
│блоков
и балок при температуре воздуха
│ стыка │
измерительный, │
│не
ниже 5 °C
│ │ регистрационный │
│
│ │ (составление │
│ │ │исполнительной схемы)│
├────────────────────────────────────────┼──────────┼─────────────────────┤
│3.
Искривление или винтообразность
│ Каждого │ Операционный │
│стальных
несущих элементов и крепежных │
элемента │ (сплошной), │
│деталей
в зоне соединений на 1 м длины
│ │ измерительный │
│не
более 1 мм, но не более 10 мм на всю │ │ (линейкой) │
│длину │ │ │
├────────────────────────────────────────┼──────────┼─────────────────────┤
│4.
Местные неплотности в стыках сжатых
│ Каждого │ Операционный, │
│элементов
не более 2 мм │
несущего │ измерительный │
│ │соединения│ (линейкой, щупом) │
├────────────────────────────────────────┼──────────┼─────────────────────┤
│5.
Депланация (перепад поверхностей)
│ То же │ То же │
│стыкуемых
элементов для соединений,
│ │ │
│перекрываемых
накладками, не более 2 мм │
│
│
├────────────────────────────────────────┼──────────┼─────────────────────┤
│6.
Отклонение глубины врубок
│ Каждого │ Приемочный, │
│от
проектной не более +/- 2 мм
│ элемента │
измерительный │
├────────────────────────────────────────┼──────────┼─────────────────────┤
│7.
Отклонения расстояний между центрами │ │ │
│рабочих
болтов, нагелей, шпонок
│ │ │
│и
гвоздей в соединениях относительно
│ │ │
│проектных
отверстий:
│ │ │
│
входных +/- 2 мм
│Выборочный│
Операционный │
│
выходных:
│ │ │
│ поперек волокон 2% толщины пакета, │
То же │ То же │
│но
не более 5 мм;
│ │ │
│ вдоль волокон 4% толщины пакета, │
" │ " │
│но
не более 10 мм
│ │ │
├────────────────────────────────────────┼──────────┼─────────────────────┤
│8.
Отклонения расстояний между центрами │
" │ Приемочный, │
│дюбелей,
штырей и шурупов в соединениях │
│ измерительный, │
│относительно
проектных со стороны │ │ регистрационный │
│головок
(шляпок), в том числе в метал-
│ │ │
│лических
накладках, не более +/- 2 мм
│ │ │
├────────────────────────────────────────┼──────────┼─────────────────────┤
│9.
Число стыков <1> бревен в стенках
│ Каждого │ Операционный, │
│ряжа,
устраиваемых вразбежку, в одной
│ ряжа │визуальный, сплошной │
│промежуточной
секции от общего числа - │ │ │
│1/3
│ │ │
├────────────────────────────────────────┼──────────┼─────────────────────┤
│10.
Припуск на высоту ряжа или часть
│ То же │
Операционный, │
│его
высоты при изготовлении (на осадку
│ │ измерительный │
│венцов
конструкции и усушку древесины)
│ │ │
│5%
высоты │ │ │
├────────────────────────────────────────┼──────────┼─────────────────────┤
│11.
Отклонение отметок верхней плоскости│
Каждой │ Операционный, │
│насадок
от проектного положения +/- 5 мм│ опоры
│ измерительный │
├────────────────────────────────────────┼──────────┼─────────────────────┤
│12.
Смещение в плане верха деревянной
│ Каждой │
Приемочный, │
│опоры
относительно разбивочных осей
│ опоры │
измерительный │
│не
более +/- 20 мм
│ │ (теодолитная │
│
│ │съемка или
измерение │
│
│ │линейкой
от натянутой│
│ │ │ струны) │
├────────────────────────────────────────┼──────────┼─────────────────────┤
│13.
Отклонение от вертикали или
│ То же │ То же │
│проектного
наклона боковых поверхностей │
│ │
│конструкции
деревянных рамных опор (в │ │ │
│долях
от высоты рамы H) не более 0,005H │ │ │
├────────────────────────────────────────┼──────────┼─────────────────────┤
│14.
Отклонение размеров пролетного
│ │ │
│строения
от проектных не более, мм:
│ │ │
│
а) +/- 20 по длине при пролете размером│ Каждого │
Приемочный, │
│до
15 м включительно │пролетного│ измерительный │
│ │
строения │
│
│
б) +/- 30 по длине при пролете размером│
То же │ То же │
│св.
15 м включительно
│ │ │
│
в) +/- 10 по высоте при пролете
│ " │ " │
│размером
до 15 м включительно
│ │ │
│
г) +/- 20 по высоте при пролете
│ " │ " │
│размером
св. 15 м включительно
│ │ │
│
д) +/- 5 в расстояниях между узлами
│ " │ " │
│поясов │ │ │
├────────────────────────────────────────┴──────────┴─────────────────────┤
│
<1> Для крайних секций устройство стыков запрещается. │
└─────────────────────────────────────────────────────────────────────────┘
11.31. Рабочие
части резьбы болтов и тяжей при сборке конструкции, особенно с металлическими
накладками в стыках, надлежит предохранять от повреждений (колпачками, смазкой
или с применением других мер).
11.32. В несущих
болтах (тяжах) под головки и гайки необходимо поставить шайбы по ГОСТ 11371 -
по одной шайбе под головку и по две шайбы под гайку; в стяжных болтах (тяжах) -
соответственно по две шайбы. Пакеты из большего числа шайб на болтах и тяжах не
допускаются.
В местах примыкания
головки болта или гайки к наклонной плоскости элемента надлежит ставить косые
шайбы по ГОСТ 10908.
Гайки, головки
болтов (тяжей) должны плотно прилегать к поверхности шайб, а последние - к
поверхности древесины.
Допускается
расположение части резьбы болта (тяжа) внутри отверстия в древесине. Над
затянутой гайкой должно выступать не менее двух ниток резьбы с полным профилем.
Все гайки на болтах
(тяжах) должны быть закреплены от раскручивания контргайками, пружинными
шайбами или самоконтрящимися гайками.
11.33. В собранном
из элементов пакете, зафиксированном в проектном положении, допускается
несовпадение отверстий (чернота), не препятствующее свободной, без перекоса,
постановке скреплений.
Допускается
прочистка отверстий стянутых пакетов сверлом номинального диаметра при условии,
что величина черноты не превышает величины разности номинального диаметра
отверстия и скрепления, указанной в проекте.
11.34. Забивка
нагелей и болтов в отверстия древесины при их несовпадении (черноте)
запрещается. При величине несовпадения отверстий менее половины диаметра
отверстия допускается рассверливать под увеличенный диаметр, предусмотренный в
проекте (с постановкой скреплений соответствующего диаметра). При несовпадении
отверстий в несущих соединениях на величину более половины их диаметра
деревянные элементы подлежат замене.
11.35. При
соединении деревянных элементов стальными накладками и высокопрочными дюбелями
допускается применять пороховой монтажный инструмент с назначением
соответствующего объема порохового заряда по паспортным данным. Применение
дюбелей диаметром менее 6 мм в соединениях со стальными накладками толщиной до
9 мм с использованием порохового инструмента допускается производить без
предварительного сверления отверстий в накладках.
Установленный
дюбель должен плотно примыкать головкой (шайбой) к закрепляемой накладке, а
накладка - к поверхности деревянного элемента. При этом цилиндрическая часть
стержня дюбеля не должна выступать над поверхностью накладки или шайбы.
11.36. В
соединениях элементов на гвоздях, дюбелях и штырях диаметром 6 мм и более для
предотвращения раскалывания древесины при их забивке следует предусматривать
предварительное сверление в древесине гнезд (отверстий) диаметром в пределах
0,8 - 0,9 диаметра стержня скрепления.
11.37. Узловые
детали в рабочих плоскостях сжатых элементов следует для плотного стыкования
обрабатывать пропилом с применением переносных шаблонов. Местные неплотности в
стыках таких элементов не должны превышать нормируемых величин.
11.38. Дощатые
фермы, собираемые в горизонтальном положении на плазу, следует поднимать в
вертикальное положение для объединения их в пролетное строение способами,
исключающими недопустимые местные и общие деформации конструкции. Необходимо
предусматривать меры по обеспечению устойчивости положения и геометрической
неизменяемости пролетного строения и его отдельных частей.
В элементы дощатой
фермы сквозные рабочие гвозди следует забивать после выверки ее строительного
подъема. Гвозди в поясах следует забивать последовательно вертикальными рядами.
Длина гвоздей должна превышать суммарную толщину стенки не менее чем на 30 мм.
Концы гвоздей надлежит загибать, не повреждая древесины.
11.39. Брусья или
бревна простых и составных прогонов балочно-эстакадных мостов должны быть
связаны между собой скреплениями в соответствии с проектом и закреплены на
опорах от продольных и поперечных смещений на всех стадиях сборки.
11.40. Сборку
решетчатых ферм пролетных строений следует, как правило, производить в
вертикальном положении с учетом их конструктивных особенностей, способа монтажа
и местных условий.
11.41. Составные
прогоны и фермы пролетных строений следует собирать со строительным подъемом в
соответствии с указаниями проекта. Как правило, следует выполнять пояса полигональными
с углами перелома в местах стоек жесткости прогонов или в стыках ферм.
В решетчатых фермах
после выверки и постановки стыковых накладок допускается принудительно выгибать
пояса в три-четыре приема от середины к концам с помощью системы клиньев или
домкратов. Стыки поясов при этом могут быть временно усилены сжимами, хомутами
и т.п. устройствами, воспринимающими возникающие при этом усилия сдвига и
отрыва.
При принудительном
выгибании поясов технологические напряжения в элементах следует контролировать
с тем, чтобы они не превышали величин, предусмотренных проектом.
11.42.
Укрупнительную сборку блоков и объединение балок с клеештыревыми соединениями
следует осуществлять на стеллажах.
11.43. Собранное
пролетное строение до снятия его со сборочных стеллажей или подмостей должно
быть принято с составлением акта промежуточной приемки ответственных
конструкций, а обнаруженные при приемке отступления от проекта и дефекты в
конструкции - устранены.
11.44. При
возведении деревянных мостов должны быть выполнены предусмотренные проектом
конструктивные меры первичной защиты, в том числе зазоры между элементами,
обеспечивающие просыхание, проветривание и защиту конструкций от увлажнения.
11.45. После
выполнения защиты деревянные элементы конструкций не следует подвергать
какой-либо обработке, кроме сверления отверстий для постановки болтов.
Просверленные отверстия в древесине должны быть промазаны креозотовым маслом
или залиты при постановке скреплений биостойкой и водостойкой антисептической
пастой на основе трудновымываемых антисептиков.
11.46. Элементы
пролетных строений, фундаментов и надстроек опор и ледорезов деревянных мостов
должны быть защищены от агрессивного воздействия биологических агентов
(вторичная защита) в соответствии с требованиями проекта.
Поверхности
сопряжения сваи с насадкой необходимо покрывать антисептическими пастами, а
сверху в отверстия насадок забивать деревянные пробки и заливать пасту.
В процессе
выполнения работ все закрытые поверхности в узлах и врубках, верхние торцы
схваток и т.п. следует покрывать антисептическими пастами.
Сваи и стойки
рамно-лежневых опор у поверхности грунта и воды при сооружении моста следует
защищать обмазками и бандажами.
11.47. Для защиты
деревянных конструкций моста от возгорания, кроме мер, предусмотренных в
проекте, необходимо территорию под мостом на расстоянии не менее 30 м в обе
стороны от оси моста очистить от кустарника, валежника, стружек и других
горючих материалов.
12. Засыпка
водопропускных труб и устоев мостов.
Укрепительные
работы
Засыпка водопропускных
труб и устоев мостов
12.1. Засыпку
водопропускных труб и устоев мостов следует выполнять после освидетельствования
качества засыпаемых грунтов и проверки соответствия проекту выполненных работ
по возведению конструкций, устройства дренажей и гидроизоляции.
12.2. При
выполнении работ по засыпке водопропускных труб и устоев мостов, кроме
требований настоящего раздела, необходимо соблюдать требования СП 119.13330.
12.3. Отсыпку
конусов у мостов, а также участков насыпей за устоями мостов (на длину, равную
высоте насыпи за устоем плюс 2 м по верху и не менее 2 м - в уровне
естественной поверхности) и засыпку прогалов за подпорными стенками следует
выполнять дренирующими грунтами с коэффициентом фильтрации не менее 2 м/сут.
Послойное
уплотнение грунта конусов следует начинать от бровки откоса и выполнять
продольными ходами вокруг устоя.
Грунты конусов и
насыпей за устоями мостов, а также прогалов за подпорными стенками следует
уплотнять виброударными машинами или навесными вибротрамбовками.
12.4. При монтаже
трубы и подготовке ее к засыпке надлежит выполнять следующие требования:
а) выходной
оголовок круглых железобетонных труб (ЖБТ) и прямоугольные бетонные или железобетонные
трубы (ПБТ) следует монтировать до начала установки промежуточных звеньев;
б) при укладке
цилиндрических звеньев труб необходимо следить, чтобы бетонная подушка
обеспечивала под звеньями на установленном в проекте угле охвата плотный
контакт с поверхностью звена на всей длине;
в) устанавливать
прямоугольные и круглые звенья труб с плоской пятой на растворе подвижностью 6
- 8 см;
г) устанавливать
гофрированные секции труб МГТ в спрофилированное шаблоном ложе, охватывающее
снизу не менее трети поперечного сечения трубы, или на горизонтальную хорошо
спланированную площадку, или на геомембранную обойму, тщательно подбивая и
одновременно уплотняя не менее чем под одну треть поперечного сечения трубы
песчаный грунт;
д) следить, чтобы
при монтаже гофрированных труб между головками болтов, гайками, шайбами и
гофрированными листами металлических конструкций не оставались частицы грунта;
е) до засыпки
смонтированной трубы грунтом необходимо оформить актом ее приемку.
12.5. Для повышения
несущей способности МГТ и надежности ее работы рекомендуется до засыпки
придавать ее поперечному сечению овальность с большей осью по вертикали,
увеличивая вертикальный диаметр МГТ на величину до 3% номинального и закрепляя
сечение стойками. Стойки удаляют после отсыпки насыпи на проектную высоту.
В случаях
возведения водопропускных сооружений в районах распространения вечной мерзлоты
следует соблюдать также специальные указания проекта в части подготовки
оснований под засыпку и температурного режима засыпки в зависимости от принципа
использования грунтов основания в период эксплуатации.
12.6. При
сооружении ЖБТ и ПБТ пазухи котлованов фундаментов необходимо засыпать сразу
после приемки фундаментов. Не допускается засыпать пазухи при наличии в них
воды.
На участках мокрых
оснований пазухи и нижнюю часть призмы на высоту 0,5 м необходимо отсыпать до
начала устойчивых заморозков.
12.7. При засыпке
трубы вначале следует отсыпать грунтовую призму с двух сторон трубы, а затем
насыпь на проектную высоту.
Переезд через
сооружаемую трубу транспортных средств допускается только в случае отсыпки
поверх трубы слоя грунта толщиной не менее 1 м, а для бульдозеров - не менее
0,5 м.
Проезд над МГТ
диаметром до 3 м строительных машин с нагрузкой на ось до 10 тс допускается при
толщине слоя над верхом конструкции не менее 0,5 м (в плотном теле), с
нагрузкой на ось 11 - 20 тс - при толщине слоя не менее 0,8 м и с нагрузкой на
ось 21 - 50 тс - при толщине слоя не менее 1 м. Если проектом предусмотрена
меньшая толщина засыпки, то для пропуска машин через сооружение в месте их
проезда требуется досыпать грунт до указанной толщины.
Грунтовая обойма
МГТ диаметром более 3,0 м, как правило, армируется композитными комбинациями из
плоских и объемных георешеток с геотекстильными материалами. Для армирования
грунтовой обоймы МГТ следует применять геотекстиль со значением разрывной
нагрузки по расчету. Схема армирования во всех случаях определяется проектом.
Для устройства
заполнителя армогрунтовых мембран из объемных георешеток в грунтовых обоймах на
водопропускных сооружениях из МГС применяются грунты по таблице 28. Допускается
использовать грунтовую массу полускальных и скальных пород, получаемую при
разработке скальных выработок взрывным способом при максимальной крупности
обломков скального грунта не более размера ячейки георешетки.
Устройство
грунтовой обоймы выполняется в едином технологическом процессе с засыпкой трубы
до проектной отметки.
МГТ должна быть
заключена в грунтовую (армогрунтовую) обойму не позже чем через трое суток
после окончания работ по нанесению дополнительного защитного покрытия.
Устройство
грунтовых обойм МГТ следует вести с опережением возведения земляного полотна.
Необходимость оставления в насыпях прогалов для сооружения труб должна быть
обоснована проектом организации строительства, при этом ширину прогала (в
свету) понизу следует назначать из расчета обеспечения расстояния между
основанием откоса насыпи и стенкой МГТ на уровне горизонтального диаметра не
менее 4 м.
Грунтовую призму
следует сооружать под контролем представителей организации, строящей трубу, и
оформлять актом.
12.8. Особое
внимание необходимо уделять качеству уплотнения грунта в труднодоступных местах
- в нижних четвертях звеньев ЖБТ, в местах перехода звеньев в оголовки, в
гофрах МГТ и т.д.
12.9. При отсыпке
насыпи совместно с обоймой засыпку следует вести наклонными от МГТ слоями
(уклон не круче 1:5), толщина которых назначается в зависимости от
грунтоуплотняющих средств.
При расположении
ЖБТ и ПБТ на склонах лога засыпку следует начинать с низовой стороны, уделяя
особое внимание тщательному уплотнению слоев грунта. Уровень засыпки с низовой
стороны должен всегда превышать уровень грунта с верховой.
12.10. При засыпке
труб в зимнее время необходимо:
тщательно очищать
от снега и льда основание под призму;
не допускать
попадания снега и льда в пазухи между стенками котлована и фундамента ЖБТ и
ПБТ, а также в тело грунтовой призмы;
засыпать пазухи
между стенками фундамента и котлована ЖБТ и ПБТ, а также слои грунта
непосредственно над верхом звеньев на высоту не менее 1 м только талым грунтом.
12.11. Отсыпку
грунтовой призмы при засыпке водопропускных труб, сооружаемых в прогалах
насыпи, и засыпку прогалов за боковыми гранями трубы на ширину ее диаметра
следует выполнять дренирующими грунтами с коэффициентом фильтрации не менее 2
м/сут, если проектом не предусмотрены другие специальные решения.
Отсыпку грунта
следует производить с разворотом самосвала перед МГТ и подачей его для
разгрузки задним ходом вдоль оси насыпи или же с кольцевым движением
самосвалов.
Для засыпки МГТ в
прогалах можно использовать бульдозеры, перемещая ими грунт, специально
доставленный для этой цели и уложенный с обеих сторон МГТ на насыпи.
Отсыпку грунта
слоями во всех случаях необходимо начинать от МГТ по всей ее длине.
Засыпать МГТ необходимо
послойно в следующей последовательности:
грунт укладывают
одновременно с обеих сторон МГТ и разравнивают бульдозером;
после уплотнения
слоя грунта с одной стороны МГТ производят отсыпку второго слоя, а с другой
стороны - уплотнение грунта;
в таком же порядке
осуществляются отсыпка и уплотнение всех последующих слоев до верха МГТ.
Уплотнение каждого
слоя грунта, если оно производится при движении машин вдоль МГТ, следует
начинать с удаленных от нее участков и с каждым последующим проходом
приближаться к стенкам МГТ. Уплотнение грунта непосредственно у МГТ допускается
только тогда, когда с противоположной ее стороны уже отсыпан слой грунта этого
же горизонта по всей длине МГТ.
Уплотнять грунт
вокруг МГТ следует, как правило, машиной виброударного действия для стесненных
условий. При уплотнении слоев, расположенных ниже горизонтального диаметра МГТ,
машина должна передвигаться вдоль МГТ. Слои, находящиеся выше этого уровня,
целесообразно уплотнять челночным способом, если МГТ засыпается до возведения насыпи
или в широком прогале.
В процессе
уплотнения грунта катком последний должен перемещаться вдоль МГТ по кольцевой
схеме. Приближение скатов катка к трубе допускается на расстояние не более 1,0
м. Грунт у стенок МГТ при данной технологии необходимо уплотнять ручными
электротрамбовками.
Уплотнение грунта в
пазухах многоочковых МГТ рекомендуется производить механизированными ручными
трамбовками с обязательным соблюдением последовательности отсыпки слоев.
Толщина слоя в пазухе не должна превышать 0,15 м. Для засыпки пазух грунтом
следует использовать универсальные экскаваторы-планировщики с ковшами до 0,5
м3.
Послойное
уплотнение грунта засыпки следует выполнять продольными ходами вокруг тела
трубы.
Грунты засыпки тела
труб, а также прогалов насыпи за боковыми гранями следует уплотнять
виброударными машинами или навесными вибротрамбовками.
Допускаемое время
рабочего цикла от момента разработки грунта до окончания его уплотнения на
насыпи приведено в таблице 27.
Таблица 27
┌─────────────────────────┬──────────────────────┬────────────────────────┐
│ Температура наружного │
Содержание мерзлых │ Допускаемое время T, │
│ воздуха, °C │
комьев, % общего │мин, при
скорости ветра,│
│ │ объема грунта │ м/с │
│ │
├─────┬─────┬─────┬──────┤
│ │ │ 3
│ 7 │ 10
│Св. 10│
├─────────────────────────┼──────────────────────┼─────┼─────┼─────┼──────┤
│Выше
минус 10 │ До 10 включ. │ 240 │ 180 │ 140 │
120 │
│ │Св. 10 до
20 " │ 180 │ 130 │ 110
│ 90 │
│ │ " 20 до 30
" │ 120 │ 90 │
75 │ 60 │
├─────────────────────────┼──────────────────────┼─────┼─────┼─────┼──────┤
│От
минус 10 до минус 18 │ До 10 включ. │ 150 │ 120 │ 100
│ 80 │
│ │Св. 10 до
20 " │ 110 │ 90 │
75 │ 60 │
│ │ " 20 до 30
" │ 90 │
60 │ 50 │ 40
│
├─────────────────────────┼──────────────────────┼─────┼─────┼─────┼──────┤
│Ниже
минус 18 до минус 25│ До 10
включ. │ 120 │ 90 │
70 │ 60 │
│ │Св. 10 до
20 " │
70 │ 60 │ 50 │
45 │
│ │ " 20 до 30
" │ 60 │
45 │ 30 │ 20
│
└─────────────────────────┴──────────────────────┴─────┴─────┴─────┴──────┘
В зимних условиях
МГТ следует засыпать только талыми (сухими несмерзшимися) грунтами; при этом
рекомендуются грунтоуплотняющие машины ударного и виброударного действия.
Допустимое время рабочего цикла от момента разработки грунта до окончания его
уплотнения не должно превышать времени, в течение которого грунт сохраняет
способность к уплотнению.
В процессе засыпки
МГТ и уплотнения грунта должны быть исключены случаи каких-либо повреждений МГТ
и их защитного покрытия.
12.12. При засыпке
трубы и пазух котлованов в зимнее время должны вестись наблюдения (с записью в
журналы производства работ) за температурой укладываемого грунта, за тем, чтобы
в засыпке не было снега и льда. В журнале также следует указывать способы
контроля плотности.
После засыпки труб
укрепление откосов насыпей у оголовков ЖБТ и ПБТ, как правило, выполняется по
типу укрепления откосов прилегающих насыпей, а у оголовков МГТ выполняется
каменной наброской с применением геосеток с засыпкой растительным грунтом и
посевом трав, объемных георешеток с засыпкой щебнем, самонесущих блочных
одевающих стен и других видов покрытий, определенных проектом. На участках
возможного длительного стояния горизонтов подпертого уровня воды укрепление
откосов засыпки всех видов труб должно осуществляться с устройством обратного
фильтра.
12.13. Технические
требования по засыпке водопропускных труб, а также объем, методы и способы
контроля приведены в таблице 28.
Таблица 28
┌────────────────────────────────┬───────────────────┬────────────────────┐
│ Технические требования │
Контроль │ Способ контроля │
├────────────────────────────────┼───────────────────┼────────────────────┤
│1.
Ширина прогала в насыпи для │
Прогала на каждой │
Измерительный │
│сооружения
трубы не менее 10 м │ трубе │(измерение рулеткой)│
│и
не менее 4 м от подошвы откоса│ │ │
│насыпи
до трубы │ │ │
├────────────────────────────────┼───────────────────┼────────────────────┤
│2.
Размеры грунтовой призмы: │ │ │
│
верха - не ниже верха трубы │
Грунтовой призмы │ Измерительный │
│
откоса - не круче 1:5
│ на каждой трубе │(измерение откосным │
│ │ │шаблоном и
линейкой)│
├────────────────────────────────┼───────────────────┼────────────────────┤
│3.
Засыпка пазух <1> между
│ То же │
Измерительный │
│стенками
котлована и фундаментом│
│ (измерение │
│трубы
- горизонтальными слоями, │ │ плотномером) │
│одновременно
с обеих сторон │ │ │
│фундамента
на всю длину │ │ │
│котлована
с допустимым │ │ │
│опережением
на величину │ │ │
│уплотненного
слоя │ │ │
├────────────────────────────────┼───────────────────┼────────────────────┤
│4.
Толщина отсыпаемых слоев │ │ │
│грунтов
(в плотном теле), м: │ │ │
│
а) 0,40 - 0,45 глинистых
│ Каждого слоя │
Измерительный │
│грунтов
- при уплотнении │ │(измерение
линейкой)│
│машинами
на базе тракторов, │ │ │
│применяемыми │ │ │
│для
уплотнения насыпей │ │ │
│
б) 0,50 - 0,65 песчаных
│ То же
│ То же │
│грунтов
- при уплотнении теми же│ │ │
│машинами │ │ │
│ 0,20 - 0,25 песчаных │ " │ " │
│грунтов
- при уплотнении │ │ │
│пневмокатками
массой 25 - 30 т │ │ │
│
в) до 0,15 песчаных грунтов -
│ " │ " │
│при
уплотнении ручными │ │ │
│электротрамбовками │ │ │
├────────────────────────────────┼───────────────────┼────────────────────┤
│5.
Коэффициент уплотнения грунта│На горизонтах 0,25;│ Измерительный │
│грунтовой
призмы у МГТ - 0,95 │ 0,5 и 0,75d │
(для песчаных │
│ │ по
высоте с обеих │и глинистых грунтов │
│ │ сторон по оси │ прибором Ковалева, │
│ │ насыпи │
для щебенисто- │
│ │ на
расстоянии 0,1 │ галечниковых
и │
│ │и 1,0 м
от стенок -│дресвяно-гравийных -│
│ │
не менее 2 проб │ методом лунок) │
│ │ в каждой точке │ │
├────────────────────────────────┼───────────────────┼────────────────────┤
│6.
То же, ЖБТ и ПБТ - 0,95 │ В каждом │ То же │
│ │
уплотненном слое │ │
│ │грунта.
В сечениях │
│
│ │ по оси насыпи │ │
│ │ и с обеих
сторон │ │
│ │трубы на
расстоянии│
│
│ │ 0,6 и 1,0 м │ │
│ │ от стенок │ │
├────────────────────────────────┼───────────────────┼────────────────────┤
│7.
Коэффициент уплотнения грунта│
Каждого │ " │
│над
трубой на высоту 2 м в зоне │ уплотненного слоя │ │
│пониженного
уплотнения при │ │ │
│насыпях
высотой 8 м и более - │ │ │
│0,85
- 0,90 │ │ │
├────────────────────────────────┼───────────────────┼────────────────────┤
│8.
Уменьшение горизонтального │ Каждой трубы │
Измерительный │
│диаметра
МГТ в период засыпки │ по всей длине │ │
│и
уплотнения грунта до 3% d
│ │ │
├────────────────────────────────┴───────────────────┴────────────────────┤
│ Засыпка труб в зимних
условиях │
├────────────────────────────────┬───────────────────┬────────────────────┤
│9.
Допускаются грунты для │ Каждого │
Измерительный │
│засыпки
МГТ талые (сухие │
уплотненного слоя │
(измерение │
│несмерзшиеся),
имеющие в момент │
│температуры грунта) │
│уплотнения
t >= 0,5 °C. Время │ │ │
│рабочего
цикла от момента │ │ │
│разработки
грунта до окончания │ │ │
│его
уплотнения - не более │ │ │
│времени,
в течение которого │ │ │
│грунт
сохраняет возможность │ │ │
│к
уплотнению
│
│ │
├────────────────────────────────┼───────────────────┼────────────────────┤
│10.
Грунты для засыпки ЖБТ │ Каждой пробы │
Операционный │
│и
ПБТ - скальные,
│
│(измерение времени) │
│крупнообломочные,
крупный │ │ │
│и
средний песок. Допускаются
│
│ │
│глинистые
грунты, имеющие │ │ │
│влажность
не выше границы │ │ │
│раскатывания.
Глинистые грунты │ │ │
│полутвердой
консистенции │ │ │
│разрешается
применять при │ │ │
│отсутствии
грунтов меньшей │ │ │
│влажности
и только в талом │ │ │
│состоянии.
Время рабочего цикла │
│ │
│определяется
на объекте │ │ │
│ориентировочно
(см. таблицу 27) │
│ │
│Содержание
мерзлого грунта менее│ То
же │ Визуальный │
│30%.
Размер комьев мерзлого │ │ │
│грунта
менее 2/3 толщины │ │ │
│укладываемого
слоя │ │ │
│Размещение
мерзлого грунта - │ " │ " │
│равномерное
(не гнездами) │ │ │
│на
расстоянии более 1 м │ │ │
│от
поверхности откосов │ │ │
├────────────────────────────────┼───────────────────┼────────────────────┤
│11.
Подготовка насыпей для │ │ │
│сооружения
труб под вторые пути:│
│ │
│
из глинистых грунтов высотой
│ " │ Измерительный │
│более
1 м - нарезать уступы │ │ (измерение
лентой │
│шириной
от 1 до 1,5 м с │ │и откосным
шаблоном)│
│поперечным
уклоном 0,01 - 0,02 │ │ │
│
из дренирующих грунтов -
│ " │ Визуальный и │
│удалить
с откосов дерн │ │ измерительный │
│и
древесно-кустарниковую
│ │
(измерение глубины │
│растительность
и после этого │ │ рыхления │
│разрыхлить
откосы на глубину │ │ линейкой) │
│10
- 15 см │ │ │
├────────────────────────────────┼───────────────────┼────────────────────┤
│12.
Минимальная засыпка │ │ │
│для
пропуска паводковых вод │ │ │
│грунтовой
призмы труб: │ │ │
│
ЖБТ - на высоту d/2 │ " │ Измерительный │
│ │ │(измерение
рулеткой)│
│
ПБТ - " " H/2 │ " │ То же │
│
МГТ - " " d │ " │ " │
├────────────────────────────────┴───────────────────┴────────────────────┤
│
<1> При глубине заложения фундамента до 0,7 м пазухи следует
засыпать│
│грунтом
на полную высоту и уплотнять машиной виброударного действия
для│
│стесненных
условий на базе трактора ДТ-75 за два прохода по одному следу│
│со
скоростью 500 м/ч.
│
└─────────────────────────────────────────────────────────────────────────┘
Укрепительные
работы
12.14. Надводные
периодически подтопляемые откосы конусов, подходных насыпей, защитных и
регуляционных сооружений должны быть предварительно спланированы, как правило,
срезкой грунта. Подсыпка допускается при условии доведения ее плотности до
проектной. Подводные, постоянно затопленные откосы всех сооружений, склоны
берегов и дно рек должны быть очищены от крупных предметов (остатков
строительных конструкций, карчей, топляка и т.п.) и спланированы срезкой или
подсыпкой в соответствии с требованиями проекта без последующего уплотнения.
12.15. Подготовку
из набросного материала или геотекстиля в зимний период необходимо выполнять по
грунту, очищенному от снега и наледи. Полотна геотекстиля следует расстилать с
опережением относительно укладки плит не более 1 сут.
12.16. Плиты и
блоки решетки следует укладывать на откос от подошвы к гребню сооружения. В
покрытии из плит швы следует омоноличивать до затопления откоса. На постоянно
затопленные откосы или подводные склоны и дно реки покрытия из гибких плит
необходимо укладывать картами площадью более 100 м2 в виде "чешуи" с
нахлестом 0,5 - 1,5 м со специальных наплавных устройств в виде барабана или
стапеля в соответствии с ППР. Швы между плитами в картах омоноличивать не
следует.
12.17. Технические
требования по укрепительным работам, а также методы и способы контроля
приведены в таблице 29.
Таблица 29
┌───────────────────────────────┬─────────────────┬───────────────────────┐
│ Технические требования │
Контроль │ Метод или способ │
│ │ │ контроля │
├───────────────────────────────┼─────────────────┼───────────────────────┤
│1.
Отклонение поверхности │ 2 замера
│ Измерительный │
│грунта
откоса от проектной │ на поперечнике │
(измерение откосным │
│+/-
5 см │ с шагом,
│ шаблоном и линейкой)
│
│ │ указанным
│
│
│ │ в проекте
│ │
├───────────────────────────────┼─────────────────┼───────────────────────┤
│2.
Характеристика подготовки │ 1 раз
на партию │Проверка по ГОСТ 3344, │
│из
щебня, гравия, песчано- │ материала
│ГОСТ 8269.0, ГОСТ 8735,│
│гравийных
смесей - по │ │ ГОСТ 25607 │
│СП
34.13330, ГОСТ 8267, │ │ │
│ГОСТ
8736, ГОСТ 3344 │ │ │
├───────────────────────────────┼─────────────────┼───────────────────────┤
│3.
Минимальная толщина слоев │1
замер на 200 м2│
Измерительный │
│подготовки,
см: │ откоса
│ (измерение линейкой)
│
│
10 - при ручной укладке,
│
│
│
│
15 - при укладке механизмами
│
│
│
├───────────────────────────────┼─────────────────┼───────────────────────┤
│4.
Отклонение поверхности │ То же
│ Измерительный │
│подготовки
(ровность) +3 см │ │ (измерение шаблоном │
│на
базе 5 м │ │ и линейкой) │
├───────────────────────────────┼─────────────────┼───────────────────────┤
│5.
Характеристика геотекстиля │ На заводе-
│Проверка по действующим│
│(подготовки):
коэффициент │ изготовителе
│нормативно-техническим │
│фильтрации
K - 0,02 см/с, │ по действующим │
документам │
│ ф │ нормативно-
│ на геотекстиль │
│поверхностная
плотность │ техническим
│
│
│не
менее 30 кг на полосу │ документам
│
│
│шириной
5 см │ │ │
├───────────────────────────────┼─────────────────┼───────────────────────┤
│6.
Допускаемый нахлест полотен │ 1 замер на 50 м │ Измерительный │
│геотекстиля
при стыковании │ длины шва
│ (измерение линейкой)
│
│не
менее 10 см при сварке │ │ │
│и
склейке сплошным швом │ │ │
├───────────────────────────────┼─────────────────┼───────────────────────┤
│7.
Превышение граней смежных │1
замер на 100 м2│ То же │
│бетонных
и железобетонных плит │
поверхности │ │
│не
более 10 мм, ширина │ откоса
│
│
│раскрытия
швов в конструкциях │ │ │
│без
омоноличивания не более │ │ │
│10
мм; при большем раскрытии │ │ │
│швы
омоноличиваются │ │ │
└───────────────────────────────┴─────────────────┴───────────────────────┘
Устройство
армогрунтовых систем
12.18. При
устройстве концевых участков подходных насыпей и конусов обсыпных устоев должен
использоваться песок с коэффициентом фильтрации
.
12.19.
Геотекстильные и геопластиковые материалы, используемые для армирования
концевых участков насыпей и конусов, должны иметь прочностные характеристики,
достаточные для восприятия давления грунта при относительных деформациях не
более 0,5%.
Необходимо
предусматривать изоляцию полиэстровых материалов от контакта с бетоном.
Песок для отсыпки
армогрунтовых систем должен иметь коэффициент неоднородности
.
12.20. Допуски на
толщину слоев песка между армирующими прослойками устанавливаются +/- 5 см.
12.21. Коэффициент
уплотнения должен быть не менее 0,98 по кривой стандартного уплотнения.
Необходимое количество проходок катка по одному следу отрабатывается на пробном
уплотнении.
Коэффициент
уплотнения измеряется в каждом слое армогрунтовой конструкции с помощью режущих
колец и плотномеров.
12.22. Расстилка
армирующего полотна должна осуществляться на ровную поверхность песка после
укатки ее катками с гладкими валками без морщин и складок с нахлестом 50 см -
для геотканей и без нахлеста для пластиковых георешеток.
Геотекстиль и
георешетки крепятся металлическими шпильками, забиваемыми в грунт с шагом 5 -
10 см.
12.23. Водоотвод из
концевого участка насыпи осуществляется с помощью дренажных призм, продольной
дренажной трубы, укладываемой в нужных рядах дренажных призм и водоотводных
трубок в лицевой стене устоя.
Дренажная призма
должна быть отделена от песчаной засыпки разделительным фильтрующим материалом.
12.24. Каждый
отсыпанный слой армогрунтовой системы принимается и оформляется актом на
скрытые работы.
12.25. При ведении
работ в зимнее время должны быть предусмотрены условия, не допускающие
попадания снега, льда и мерзлых комьев песка в отсыпку. Доставка песка к
стройплощадке должна вестись на крытых автомашинах. Отсыпка и уплотнение песка
в период снегопада не допускается.
13.
Устройство конструкций дорожных одежд
Устройство верхнего
строения пути на железнодорожных мостах
13.1. Перед
отсыпкой балластного слоя вокруг крышек водоотводных трубок должен быть уложен
щебень или галька крупностью 80 - 120 мм. При отсыпке и уплотнении балласта, а
также при укладке пути следует принимать меры по предохранению гидроизоляции от
повреждения.
13.2. Мостовые
брусья, укладываемые на шкафных стенках устоев, следует прирубать по высоте по
всей площади опирания и закреплять.
13.3. Врубки и
отверстия в брусьях для болтов, костылей и шурупов необходимо антисептировать,
трещины заделывать антисептической пастой, а концы брусьев стянуть полосовым
железом. На брусьях следует проставить год укладки.
13.4. Для головок
заклепок и высокопрочных болтов поперек бруса необходимо вырубать канавки.
13.5. Над
подвижными концами пролетных строений в досках настила мостового полотна
следует делать разрывы, обеспечивающие его сохранность при изменении
температуры и перемещении пролетного строения.
13.6.
Работы по устройству мостового полотна на безбалластных железобетонных плитах и
сталефибробетонного полотна на железобетонных пролетных строениях с односкатным
водоотводом с ездой на балласте следует выполнять по ГОСТ Р 52751.
13.7. Уложенное
мостовое полотно до пропуска поездной нагрузки должно быть принято
представителем дистанции пути или отдела временной эксплуатации строительства.
Обнаруженные
дефекты необходимо устранять до пропуска поездной нагрузки.
13.8. Технические
требования, которые следует соблюдать при устройстве верхнего строения пути на
железнодорожных мостах и проверять при операционном контроле, а также объем и
способы контроля приведены в таблице 30 (кроме требований по 13.6).
Таблица 30
┌───────────────────────────────────────────┬─────────────┬───────────────┐
│ Технические требования │ Контроль
│Способ контроля│
├───────────────────────────────────────────┼─────────────┼───────────────┤
│1.
Отклонение отметки головки рельсов
│ │ │
│от
ординат проектной линии:
│ │ │
│
при ординатах менее 50 мм - не более 4 мм │ Каждого
│ Измерительный │
│
│ пролетного
│(нивелирование)│
│ │ строения
│ │
│ "
" более 50 мм -
" " 8%
│ То же │
То же │
├───────────────────────────────────────────┼─────────────┼───────────────┤
│2.
Отклонение оси рельсового пути в плане
│ │ │
│от
проектного положения, мм, не более:
│ │ │
│
на прямых участках пути с безбалластным
│ " │ Измерительный │
│мостовым
полотном - 30
│ │
(теодолитная │
│ │ │ съемка)
│
│
то же, при езде на балласте - 50
│ " │ То же
│
│
на кривых участках пути с безбалластным
│ " │ " │
│мостовым
полотном - 20 │ │ │
│
то же, при езде на балласте - 30
│ " │ " │
├───────────────────────────────────────────┼─────────────┼───────────────┤
│3.
Требования к укладке мостового бруса:
│ " │ │
│
эпюра укладки - по проекту
│ │
Измерительный │
│
│
│(нивелирование)│
│
расстояние в свету между брусьями (кроме
│ " │ Измерительный │
│брусьев
у поперечных балок) 10 - 15 см
│ │ (измерение
│
│
│ │ линейкой)
│
│
зазор между брусом и поясом поперечной
│ " │ То же
│
│балки
- не менее 1,5 см │ │ │
│
касание брусьями связей и фасонок -
│ " │
Визуальный │
│не
допускается
│ │ │
│
глубина врубок в местах опирания бруса
│Каждой врубки│ Измерительный │
│на
пояса продольных балок (ферм) стальных
│ │ (измерение
│
│пролетных
строений 5 - 30 мм
│ │ линейкой)
│
│
то же, на мостах с деревянными прогонами
│ То же │
То же │
│20
- 30 мм │ │ │
├───────────────────────────────────────────┼─────────────┼───────────────┤
│4.
Требования к устройству балластной
│ │ │
│призмы,
см:
│ │ │
│
толщина слоя балласта под шпалой -
│Каждой шпалы │
" │
│не
менее 25
│ │ │
│
максимальная толщина балласта под шпалой -│ То же
│ " │
│не
более 60
│ │ │
│
допуск на толщину балластного слоя - 5
│ " │ " │
├───────────────────────────────────────────┼─────────────┼───────────────┤
│5.
Допуск на расстояние в свету от
│На всей длине│ Измерительный │
│внутренней
грани головки путевых рельсов
│ │ (проверка
│
│до
контруголков не должен отличаться
│ │ шаблоном)
│
│от
проектного более чем на 10 мм
│ │ │
├───────────────────────────────────────────┼─────────────┼───────────────┤
│6.
Верх противоугонного уголка должен быть │ То же
│ То же │
│ниже
головки путевого рельса по проекту,
│ │ │
│но
не более 5 мм
│ │ │
└───────────────────────────────────────────┴─────────────┴───────────────┘
Устройство
конструкций дорожных одежд
13.9. До устройства
конструкции дорожной одежды должны быть выполнены и приняты все работы по
объединению балок (плит) пролетных строений, перекрытию зазоров, установке и
омоноличиванию конструкций деформационных швов, водоотводных трубок, лотков,
ограждений и деталей, закрепляемых на плите проезжей части моста, и, как правило,
уложены трубы коммуникаций.
Устройство
однослойной конструкции дорожной одежды автодорожных мостов в виде бетонного
выравнивающего слоя, выполняющего и гидроизолирующие функции, допускается
совмещать с омоноличиванием продольных стыков между балками пролетного
строения.
13.10. Для бетонных
слоев элементов мостового полотна - выравнивающего и защитного, а также
цементобетонного покрытия следует применять бетонную смесь, отвечающую
требованиям проекта по морозостойкости (соответствующей климатической зоне района
строительства) и водонепроницаемости.
Бетонная смесь
должна иметь в своем составе воздухововлекающие, газообразующие и другие
добавки по ГОСТ 24211, обеспечивающие получение указанных параметров. Введение
в бетон химических добавок - ускорителей твердения, вызывающих коррозию
арматуры, запрещается.
Стальные сетки,
применяемые для армирования бетонных слоев одежды, следует очищать от
антикоррозионной смазки.
Применение для
армирования защитного слоя плетеных сеток не допускается.
13.11. Производство
и приемку работ по устройству асфальтобетонных и цементобетонных покрытий
следует осуществлять в соответствии с СП 78.13330.
Если при устройстве
покрытия возникает необходимость выправления продольного профиля укладкой
дополнительных слоев, то конструкция дорожной одежды должна быть согласована с
проектной организацией.
При устройстве
конструкции дорожной одежды должна быть обеспечена герметичность ее сопряжения
с конструкциями деформационных швов, ограждениями и тротуарными блоками.
13.12. Укладку
переходных плит в узлах сопряжения автодорожных пролетных строений с насыпями
подходов следует выполнять в порядке и сроки, указанные в проекте, с учетом
конструкции плит, свойств грунтов насыпи и ее основания.
Допускается по
согласованию с заказчиком устройство временного покрытия в узлах сопряжения
моста с насыпью или временная укладка переходных плит с последующей съемкой их
для досыпки, доуплотнения верхней части насыпи и установки плит в проектное
положение.
13.13. При
расположении на мостах трамвайных путей рельсы следует укладывать в
соответствии с СП 84.13330.
13.14. Прокладка
коммуникаций и устройство освещения на мостах должны быть выполнены
специализированными организациями с учетом требований соответствующих сводов
правил.
При производстве
работ по устройству коммуникаций не допускается делать монтажные прихватки, а
также пазы и отверстия в конструкциях мостов без согласования с проектной
организацией.
13.15.
Гидроизоляцию следует выполнять в соответствии с проектом и соответствующими
нормативными документами.
Гидроизоляцию
следует выполнять непрерывной по всей ширине мостового полотна. Гидроизоляцию
допускается прерывать у парапетов или жесткой части комбинированных ограждений
в обоснованных случаях и при условии полного исключения попадания воды под
гидроизоляцию в местах ее обрыва.
13.16. Применяемые
для устройства гидроизоляции материалы должны соответствовать указанным в
проекте характеристикам и требованиям стандартов на их изготовление, а также
настоящего свода правил. Не допускается применять гидроизоляционные материалы
при отсутствии сертификата. В случае, когда при визуальном осмотре качество
материала вызывает сомнение, необходимо произвести его проверку в лаборатории.
Материалы для
гидроизоляции должны обладать следующими свойствами:
быть
водонепроницаемыми (не иметь признаков проникновения воды) при давлении воды
0,0981 МПа (1 кгс/см2) в течение 2 ч;
не иметь разрывов
при растяжении силой не менее 588,6 Н (60 кгс) произвольным образом вырезанного
образца (полоски шириной 50 мм) - для рулонных материалов;
не иметь трещин при
загибе на брусе радиусом 10 мм при температуре не выше минус 25 °C (для
материалов на полимерной основе);
быть устойчивыми к
агрессии щелочей, антиобледенителей, нефтепродуктов.
Они также должны
иметь:
относительное
удлинение при разрыве не менее 20% - для рулонных материалов;
водопоглощение в
течение 24 ч не более 1% массы;
прочность на раздир
с основой в произвольном направлении силой не менее 107,91 Н (11 кгс/см2) - для
рулонных материалов;
адгезию к материалу
проезжей части - не менее 0,2943 МПа (3 кгс/см2);
температуру
хрупкости битумного вяжущего по Фраасу - не выше минус 32 °C (для материалов на
битумной основе);
температуроустойчивость
(температуру размягчения по КиШ) не ниже 85 °C (при защитном слое из бетона); в
других случаях температуроустойчивость следует назначать исходя из температуры
двухслойного асфальтобетона 140 - 160 °C и литого асфальта - 180 - 200 °C;
устойчивость к
статическому продавливанию стальным шариком диаметром 10 мм на бетонном
основании силой не менее 245,25 Н (25 кгс) (при защитном слое из бетона
указанную проверку не производят).
13.17.
Гидроизоляцию железобетонных блоков (балок) пролетных строений железнодорожных
мостов предпочтительно выполнять при их изготовлении в заводских условиях.
13.18.
Гидроизоляционные работы на стройплощадке следует выполнять в сухую погоду,
предпочтительно при положительных температурах воздуха. При необходимости
выполнения работ при отрицательных температурах следует применять
гидроизоляционные материалы с температурой хрупкости не выше температуры
воздуха в период производства работ. Гидроизолируемые поверхности должны быть
свободными от снега и льда, луж.
13.19. Стыки
полотен рулонного гидроизоляционного материала или армирующих основ следует
устраивать внахлестку с учетом направления стока воды.
13.20.
Гидроизоляция у водоотводных трубок и в местах расположения столбов,
прерывающих сплошность гидроизоляционного ковра, должна быть выполнена перед
гидроизоляцией всей изолируемой поверхности. Дополнительная гидроизоляция у
водоотводных трубок должна быть заведена в их раструб и плотно обжата
вставляемым в него металлическим стаканом, предварительно покрытым битумной
грунтовкой.
Все зазоры между
деталями водоотводных трубок должны быть тщательно заделаны.
Гидроизоляция в
месте сопряжения с водоотводными трубками не должна иметь местных утолщений,
препятствующих стоку воды.
13.21. При
выполнении гидроизоляционных работ следует контролировать соответствие качества
гидроизоляции требованиям проекта и настоящего свода правил, проверить
герметичность у водоотводных трубок и деформационных швов, а также в местах
примыкания (в углах, к бортикам, бордюрам и столбам) и, кроме того, качество
выравнивающего, изолирующего и защитного слоев.
В слоях
гидроизоляции не должно быть непроклеев, складок, проколов и других
механических повреждений. На все обнаруженные в каждом слое повреждения
гидроизоляции должны быть поставлены заплаты.
13.22. Защитный
слой допускается укладывать только после приемки работ по устройству
гидроизоляции с составлением акта на скрытые работы.
13.23. На
ортотропных плитах стальных пролетных строений мостов конструкцию дорожной
одежды выполняют в соответствии с проектом состоящей, как правило, из
антикоррозионного и защитно-сцепляющего слоев с двухслойным асфальтобетонным
покрытием.
Могут быть устроены
также тонкослойные покрытия без асфальтобетонных слоев по ГОСТ Р 53627.
13.24. Подготовку
поверхности ортотропной плиты к устройству защитно-сцепляющего слоя следует
выполнять путем очистки металлического листа от грунтовочной краски, ржавчины
или прокатной пленки (окалины) методом струйно-абразивной обработки.
13.25.
Технологический перерыв между окончанием очистки и нанесением антикоррозионного
покрытия не должен превышать 7 ч при влажности воздуха до 70% и 3 ч - при
большей влажности воздуха.
13.26.
Антикоррозионные слои (при их наличии) выполняют, как правило, путем
пневматического или безвоздушного нанесения материалов грунтовки.
13.27. На готовом
антикоррозионном покрытии не должно быть дефектов: глянца, пузырей,
сморщиваний, кратеров, непрокрашенных мест. Не допускаются также отслаивание
покрытия и следы ржавчины.
Не допускаются по
нанесенному грунтовочному слою хождение людей и движение построечных
транспортных средств.
13.28.
Защитно-сцепляющий слой может быть нанесен непосредственно на подготовленную
поверхность металла - в соответствии с проектом, если он выполняет функции
антикоррозионной защиты металла.
13.29. По
антикоррозионному и защитно-сцепляющему слоям, так же, как и по гидроизоляции,
не допускается движение транспортных средств, кроме подвозящих асфальтобетонную
смесь, и асфальтоукладчика при укладке покрытия непосредственно на
гидроизоляцию.
На указанных слоях
не допускается длительная стоянка автомобилей, резкое торможение, развороты.
13.30.
Асфальтобетонное покрытие на проезжей части, предусмотренное в составе конструкции
дорожной одежды, выполняют двухслойным в соответствии с проектом, применяя
уплотняемый асфальтобетон особоплотный, типа Б I марки, щебеночно-мастичный (в
верхнем слое) по ГОСТ 9128, ГОСТ 31015 соответственно, либо литой асфальтобетон
- в одном или обоих слоях по техническим условиям завода-изготовителя.
При укладке
асфальтобетонного покрытия непосредственно на гидроизоляцию (защитно-сцепляющий
слой) материал последней должен выдерживать температуру соответствующего типа
асфальтобетона и не способствовать возникновению дефектов в укладываемом слое
покрытия в виде трещин за счет сдвигов при уплотнении асфальтобетонной смеси,
миграции вяжущего в смесь при укладке литой смеси.
При уплотнении
асфальтобетонной смеси не допускается включение вибрации на катках.
На тротуарах
укладывают асфальтобетонные смеси типов Г, Д II - III марок.
13.31. В случае
применения в верхнем слое литого асфальтобетона поверхности должна быть придана
шероховатость за счет рассыпки и прикатки черного щебня.
13.32. Технические
требования, которые следует выполнять при производстве работ по устройству
одежды ездового полотна и проверять при операционном контроле, а также объем и
способы контроля приведены в таблице 31.
Таблица 31
┌─────────────────────────────────────────┬────────────────┬──────────────┐
│ Технические требования │ Контроль
│ Способ │
│
│
│ контроля │
├─────────────────────────────────────────┼────────────────┼──────────────┤
│1.
Арматурная сетка для армирования
│
│ │
│(по
ГОСТ 23279):
│
│ │
│ 4B - I - 100 │На каждом мосту │ Проверка
│
│ р │ │по ГОСТ 23279 │
│
защитного слоя -------------
│
│ │
│ 4B - I - 100 │ │ │
│ р │ │ │
│ 6A - I - 100 │
То же │ То же
│
│
цементобетонного покрытия ------------
│
│ │
│ 6A - I - 100 │ │ │
├─────────────────────────────────────────┼────────────────┼──────────────┤
│2.
Допускаемая температура окружающего
│
│ │
│воздуха
при устройстве гидроизоляции, °C,│ │ │
│не
ниже: │ │ │
│
в заводских и монтажных условиях - 5
│ " │Измерительный │
│
│
│ (измерение │
│
│ │
термометром) │
│
на строительстве с применением битумных │ " │ То же
│
│мастик
- 5
│
│ │
│
то же, из резиноподобных материалов -
│ " │ " │
│минус
10 │ │ │
│
наплавляемых рулонных битумно-полимерных│ " │ " │
│материалов
- до минус 25
│
│ │
├─────────────────────────────────────────┼────────────────┼──────────────┤
│3.
Температура рабочих составов горячих
│ Каждой партии
│ " │
│битумных
мастик 160 - 180 °C
│ мастики │ │
├─────────────────────────────────────────┼────────────────┼──────────────┤
│4.
Допускаемые нахлест и смещение стыков │ │ │
│рулонных
гидроизоляционных материалов,
│
│ │
│мм:
│
│ │
│
нахлест в стыках продольного направления│
Каждого слоя │Измерительный
│
│рулона
- 60 - 100, в стыках поперечного
│
│ (измерение │
│направления
- 150 │ │ линейкой)
│
│
смещение в последующих слоях по
│ То же │
То же │
│отношению
к стыкам предыдущего слоя -
│
│ │
│не
менее 300
│
│ │
├─────────────────────────────────────────┼────────────────┼──────────────┤
│5.
Покрытие местных повреждений
│ Каждого │ " │
│гидроизоляционного
ковра заплатой от края│
повреждения │ │
│повреждения
- не менее 100 мм │ │ │
├─────────────────────────────────────────┼────────────────┼──────────────┤
│6.
Устройство асфальтобетонного
│ 1 вырубка │
Проверка │
│покрытия
- в соответствии с требованиями │
на 7000 м2, │по СП
78.13330│
│проекта │но не
менее 3-х │ │
│
│вырубок на мосту│ │
└─────────────────────────────────────────┴────────────────┴──────────────┘
13.33. При монтаже
конструкций пролетных строений и сходов из ПКП с нанесенным покрытием прохожей
части необходимо принять меры для защиты указанного покрытия от повреждений.
14. Приемка
законченных сооружений
14.1. При приемке в
эксплуатацию законченных строительством мостов и труб (пусковых комплексов)
следует выполнять требования настоящего свода правил.
14.2. Материалы
приемки в эксплуатацию мостов и труб необходимо оформлять актами
государственной приемочной комиссии, предусмотренными нормативными документами.
14.3. Все
законченные строительством мосты и трубы перед приемкой их в эксплуатацию
должны быть обследованы (освидетельствованы) в целях проверки их соответствия
утвержденному проекту и требованиям, установленным настоящим сводом правил к
качеству работ. При обследованиях и испытаниях (освидетельствованиях)
сооружений необходимо соблюдать требования СП 79.13330.
14.4. Не
подвергаемые испытаниям мосты и трубы при вводе в эксплуатацию должны быть
обкатаны транспортом с наиболее тяжелыми эксплуатационными нагрузками,
обращающимся на данной линии или дороге.
Обкатка
организуется эксплуатационной организацией, принимающей мост в эксплуатацию.
Результаты обкатки необходимо оформлять актом, составленным представителями
строительной, проектной и эксплуатационной организаций.
14.5. Перед
приемкой сооружения в эксплуатацию подмостовые русла и отверстия труб должны
быть расчищены от загромождающих их предметов; пути под путепроводами приведены
в соответствие с проектными отметками; на мостах и подходах установлены
дорожные знаки и сигналы судовой обстановки; испытаны устройства освещения;
опробованы механизмы, заградительная и оповестительная сигнализации разводных
мостов; закончены и испытаны системы защитных и предохранительных
приспособлений от блуждающих токов; установлены (при необходимости) габаритные
ворота; выполнен предусмотренный проектом комплекс противопожарных мероприятий.
14.6. При
отклонениях от проектных величин положения и размеров возведенных конструкций
мостов и труб, обнаруженных во время обследований при контрольных промерах и
инструментальных съемках, их необходимо оценивать с точки зрения влияния на
несущую способность и эксплуатационные качества сооружений. При этом следует
проверять соблюдение основных габаритных требований, размеров температурных
зазоров и деформационных швов, правильность расположения опорных частей на отступления
в осевых размерах (несоосности во взаимном расположении отдельных элементов),
приводящим к появлению в частях или элементах конструкции дополнительных
эксцентриситетов, соблюдение назначенных проектом уклонов.
При приемке
сооружений в эксплуатацию снижение расчетной несущей способности в отдельных
частях или элементах возведенных конструкций из-за обнаруженных отклонений в их
положении и размерах не должно превышать 5%.
14.7. Использование
незаконченных строительством мостов и труб для открытия по уже готовым частям и
конструкциям сооружений движения построечного транспорта и механизмов,
необходимых для завершения строительства, должно быть предусмотрено ППР.
Возможность
открытия такого движения должна определять комиссия после обследования
технического состояния возведенных конструкций с участием представителя
проектной организации; такое обследование должно обеспечивать безопасное
обращение предусматриваемых транспортных средств при установленных режимах и
скоростях движения.
14.8. Приемку во
временную эксплуатацию не полностью законченных строительством мостов и труб
под железную дорогу необходимо осуществлять в порядке, устанавливаемом
заказчиком.
Временная эксплуатация
железнодорожных мостов и труб допускается при условии, что строительство
собственно моста (трубы) закончено, проведено обследование конструкций и их
обкатка, а также выполнены испытания (если они предусмотрены).
Приложение
А
(обязательное)
НОРМАТИВНЫЕ
ССЫЛКИ
В настоящем своде
правил использованы ссылки на следующие нормативные документы:
ГОСТ Р 51634-2000.
Масла моторные автотракторные. Общие технические требования
ГОСТ Р 51866-2002.
Топлива моторные. Бензин неэтилированный. Технические условия
ГОСТ Р 52085-2003.
Опалубка. Общие технические условия
ГОСТ Р 52086-2003.
Опалубка. Термины и определения
ГОСТ Р 52751-2007.
Плиты из сталефибробетона для пролетных строений мостов. Технические условия
ГОСТ Р 52964-2008.
Вода питьевая. Методы определения содержания сульфатов
ГОСТ Р 53231-2008.
Бетоны. Правила контроля и оценки прочности
ГОСТ Р 53627-2009.
Покрытие полимерное тонкослойное проезжей части мостов
ГОСТ Р 53664-2009.
Болты высокопрочные цилиндрические и конические для мостостроения. Гайки и
шайбы к ним. Технические условия
ГОСТ 4.208-79.
СПКП. Строительство. Конструкции деревянные клееные. Номенклатура показателей
ГОСТ 9.104-79*.
Единая система защиты от коррозии и старения. Покрытия лакокрасочные. Группы
условий эксплуатации
ГОСТ 9.401-91.
Единая система защиты от коррозии и старения. Покрытия лакокрасочные. Общие
требования и методы ускоренных испытаний на стойкость к воздействию
климатических факторов
ГОСТ 9.402-2004.
Единая система защиты от коррозии и старения. Покрытия лакокрасочные.
Подготовка металлических поверхностей к окрашиванию
ГОСТ 9.407-84.
Единая система защиты от коррозии и старения. Покрытия лакокрасочные. Метод
оценки внешнего вида
ГОСТ 201-76.
Тринатрийфосфат. Технические условия
ГОСТ 263-75.
Резина. Методы определения твердости по Шору А
ГОСТ 310.3-76.
Цементы. Методы определения нормальной густоты, сроков схватывания и
равномерности измерения объема
ГОСТ 310.4-81.
Цементы. Методы определения предела прочности при изгибе и сжатии
ГОСТ 535-2005.
Прокат сортовой и фасонной стали углеродистой обыкновенного качества. Общие
технические условия
ГОСТ 859-2001.
Медь. Марки
ГОСТ 1173-2006.
Фольга, ленты, листы и плиты медные. Технические условия
ГОСТ 2263-79. Натр
едкий технический. Технические условия
ГОСТ 2292-88.
Лесоматериалы круглые. Маркировка, сортировка, транспортирование, методы
измерения и приемка
ГОСТ 3344-83.
Щебень и песок шлаковые для дорожного строительства. Технические условия
ГОСТ 3808.1-80.
Пиломатериалы хвойных пород. Атмосферная сушка и хранение
ГОСТ 4028-63.
Гвозди строительные. Конструкция и размеры
ГОСТ 4245-72. Вода
питьевая. Методы определения содержания хлоридов
ГОСТ 4543-71.
Прокат из легированной конструкционной стали. Технические условия
ГОСТ 5100-85. Сода
кальцинированная техническая. Технические условия
ГОСТ 5264-80*.
Ручная дуговая сварка. Соединения сварные. Основные типы, конструктивные
элементы и размеры
ГОСТ 5686-94.
Грунты. Методы полевых испытаний сваями
ГОСТ 5781-82. Сталь
горячекатаная для армирования железобетонных конструкций. Технические условия
ГОСТ 5802-86.
Растворы строительные. Методы испытаний
ГОСТ 6402-70*.
Шайбы пружинные. Технические условия
ГОСТ 6564-84.
Пиломатериалы и заготовки. Правила приемки, методы контроля, маркировка и
транспортирование
ГОСТ 6782.1-75.
Пилопродукция из древесины хвойных пород. Величина усушки
ГОСТ 6782.2-75.
Пилопродукция из древесины лиственных пород. Величина усушки
ГОСТ 6958-78. Шайбы
увеличенные. Классы точности A и C. Технические условия
ГОСТ 6996-66.
Сварные соединения. Методы определения механических свойств
ГОСТ 7016-82*.
Изделия из древесины и древесных материалов. Параметры шероховатости
поверхности
ГОСТ 7348-81.
Проволока из углеродистой стали для армирования предварительно напряженных
железобетонных конструкций. Технические условия
ГОСТ 7473-94. Смеси
бетонные. Технические условия
ГОСТ 7512-82.
Контроль неразрушающий. Соединения сварные. Радиографический метод
ГОСТ 8267-93.
Щебень и гравий из плотных горных пород для строительных работ. Технические
условия
ГОСТ 8269.0-97.
Щебень и гравий из плотных горных пород и отходов промышленного производства
для строительных работ. Методы физико-механических испытаний
ГОСТ 8486-86.
Пиломатериалы хвойных пород. Технические условия
ГОСТ 8713-79.
Сварка под флюсом. Соединения сварные. Основные типы, конструктивные элементы и
размеры
ГОСТ 8735-88. Песок
для строительных работ. Методы испытаний
ГОСТ 8736-93. Песок
для строительных работ. Технические условия
ГОСТ 9014.0-75.
Лесоматериалы круглые. Хранение. Общие требования
ГОСТ 9128-2009.
Смеси асфальтобетонные дорожные, аэродромные и асфальтобетон. Технические
условия
ГОСТ 10178-85.
Портландцемент и шлакопортландцемент. Технические условия
ГОСТ 10180-90.
Бетоны. Методы определения прочности по контрольным образцам
ГОСТ 10181-2000.
Смеси бетонные. Методы испытаний
ГОСТ 10587-84.
Смолы эпоксидно-диановые неотвержденные. Технические условия
ГОСТ 10884-94.
Сталь арматурная термомеханически упрочненная для железобетонных конструкций.
Технические условия
ГОСТ 10908-75.
Квадранты механические с уровнем. Технические условия
ГОСТ 10922-90.
Арматурные и закладные изделия сварные, соединения сварные арматуры и закладных
изделий железобетонных конструкций. Общие технические условия
ГОСТ 11371-78.
Шайбы. Технические условия
ГОСТ 11533-75.
Автоматическая и полуавтоматическая дуговая сварка под флюсом. Соединения
сварные под острыми и тупыми углами. Основные типы, конструктивные элементы и
размеры
ГОСТ 11534-75*.
Ручная дуговая сварка. Соединения сварные под острыми и тупыми углами. Основные
типы, конструктивные элементы и размеры
ГОСТ 11964-81.
Дробь чугунная и стальная техническая. Общие технические условия
ГОСТ 13078-81.
Стекло натриевое жидкое. Технические условия
ГОСТ 14771-76*.
Дуговая сварка в защитном газе. Соединения сварные. Основные типы,
конструктивные элементы и размеры
ГОСТ 14782-86.
Контроль неразрушающий. Соединения сварные. Методы ультразвуковые
ГОСТ 15140-78.
Материалы лакокрасочные. Методы определения адгезии
ГОСТ 15150-69.
Машины, приборы и другие технические изделия. Исполнения для различных
климатических районов. Категории, условия эксплуатации, хранения и
транспортирования в части воздействия климатических факторов внешней среды
ГОСТ 15589-70. Болт
с шестигранной головкой класса точности C. Конструкция и размеры
ГОСТ 15613.3-77.
Древесина клееная массивная. Метод определения предела прочности при растяжении
клеевого торцового соединения впритык
ГОСТ 18164-72. Вода
питьевая. Метод определения содержания сухого остатка
ГОСТ 18321-73*.
Статистический контроль качества. Методы случайного отбора выборок штучной
продукции
ГОСТ 19281-89.
Прокат из стали повышенной прочности. Общие технические условия
ГОСТ 21554.2-81.
Пиломатериалы и заготовки. Метод определения предела прочности при статическом
изгибе
ГОСТ 21554.4-78.
Пиломатериалы и заготовки. Метод определения предела прочности при продольном
сжатии
ГОСТ 21554.5-78.
Пиломатериалы и заготовки. Метод определения предела прочности при продольном
растяжении
ГОСТ 21554.6-78.
Пиломатериалы и заготовки. Метод определения предела прочности при скалывании
вдоль волокон
ГОСТ 21779-82.
Система обеспечения точности геометрических параметров в строительстве. Технологические
допуски
ГОСТ 22266-94.
Цементы сульфатостойкие. Технические условия
ГОСТ 23118-99.
Конструкции стальные строительные. Общие технические условия
ГОСТ 23518-79.
Дуговая сварка в защитных газах. Соединения сварные под острыми и тупыми
углами. Основные типы, конструктивные элементы и размеры
ГОСТ 23732-79. Вода
для бетонов и растворов. Технические условия
ГОСТ 24211-2008.
Добавки для бетонов и строительных растворов. Общие технические условия
ГОСТ 25346-89.
Основные нормы взаимозаменяемости. Единая система допусков и посадок. Общие
положения, ряды допусков и основных отклонений
ГОСТ 25347-82.
Основные нормы взаимозаменяемости. Единая система допусков и посадок. Поля
допусков и рекомендуемые посадки
ГОСТ 25607-2009.
Смеси щебеночно-гравийно-песчаные для покрытий и оснований автомобильных дорог
и аэродромов. Технические условия
ГОСТ 26633-91.
Бетоны тяжелые и мелкозернистые. Технические условия
ГОСТ 27006-86.
Бетоны. Правила подбора состава
ГОСТ 30515-97.
Цементы. Общие технические условия
ГОСТ 31015-2002.
Смеси асфальтобетонные и асфальтобетон щебеночно-мастичный. Технические условия
СП 34.13330.2010
"СНиП 2.05.02-85. Автомобильные дороги"
СП 35.13330.2011
"СНиП 2.05.03-84*. Мосты и трубы"
СП 45.13330.2010
"СНиП 3.02.01-87. Земляные сооружения, основания и фундаменты"
СП 48.13330.2011
"СНиП 12-01-2004. Организация строительства"
СП 49.13330.2011
"Безопасность труда в строительстве. Часть 1. Общие требования"
СП 63.13330.2012
"СНиП 52-01-2003. Бетонные и железобетонные конструкции. Основные положения"
СП 70.13330.2011
"СНиП 3.03.01-87. Несущие и ограждающие конструкции"
СП 78.13330.2011
"СНиП 3.06.03-85. Автомобильные дороги"
СП 79.13330.2001
"СНиП 3.06.07-86. Мосты и трубы. Правила обследований и испытаний"
СП 84.13330.2011
"СНиП III-39-76. Трамвайные пути"
СП 119.13330.2011
"СНиП 32-01-95. Железные дороги колеи 1520 мм"
СП 126.13330.2011
"СНиП 3.01.03-84. Геодезические работы в строительстве"
СП 130.13330.2011
"СНиП 3.09.01-85. Производство сборных железобетонных конструкций и
изделий".
Приложение
Б
(обязательное)
ТЕРМИНЫ И
ОПРЕДЕЛЕНИЯ
В настоящем своде
правил использованы следующие термины с соответствующими определениями:
Б.1. Водоотлив:
комплекс мероприятий и устройств, обеспечивающих удаление подземных или
поверхностных вод из открытых котлованов.
Б.2. Забой: рабочее
место, где происходит разработка грунта, перемещающееся в процессе производства
работ.
Б.3. Зачистка грунта:
съем слоя грунта с поверхности забоя скважины (котлована), разработанной с
недобором.
Б.4. Износ:
снижение показателей физических свойств элементов мостового сооружения
(физический износ) или появление несоответствия сооружения возросшим за период
эксплуатации требованиям к потребительским свойствам (моральный износ),
приводящие сооружение в неработоспособное состояние.
Б.5.
Износостойкость: свойство материала оказывать сопротивление изнашиванию в
определенных условиях эксплуатации или испытаний.
Б.6. Кессон:
устройство для обеспечения необходимых условий ведения работ под водой или в
водонасыщенном грунте при избыточном давлении воздуха.
Б.7. Колодец
опускной: полая вертикальная конструкция, погружаемая в грунт по мере его
разработки под действием собственного веса. Колодцы используют в качестве
конструкции фундамента или ограждения котлована, их изготавливают из бетона,
железобетона и металла, сборными и монолитными.
Б.8. Контрфорс:
вертикальный выступ или дополнительная конструкция, усиливающая основную
несущую конструкцию (подпорную стену снаружи) и воспринимающая, в основном,
горизонтальную силу.
Б.9. Крыло откосное
(стенка откосная): элемент устоя в виде стенки переменной высоты, опертой на
фундамент и расположенной под углом к оси моста. Предназначено для удержания
грунта насыпи подхода за устоем.
Б.10. Лежень
опорный: опора простейшего типа в виде горизонтального бруса, уложенного в теле
насыпи или на грунтовое основание, предназначенного для опирания переходных
плит или пролетного строения.
Б.11. Насадка:
элемент свайной или стоечной (железобетонной или деревянной) опоры,
объединяющий поверху головы свай или стоек.
Б.12. Недобор
грунта: слой грунта, оставляемый в выработке (забое скважины или дне котлована)
и подлежащий последующему удалению.
Б.13. Неработоспособное
состояние: состояние мостового сооружения, при котором значение хотя бы одного
функционального параметра не соответствует требованиям нормативно-технической и
(или) проектной документации.
Б.14. Несущая
способность: степень сопротивляемости материала, конструкции напряжениям от
постоянных и временных нагрузок.
Б.15. Нож ледореза:
режущая грань ледореза, непосредственно воспринимающая напор льда и
способствующая его разрушению.
Б.16. Оголовок
опоры: самая верхняя утолщенная, как правило, армированная часть опоры моста,
служащая для установки на нее опорных частей и непосредственно воспринимающая
опорные давления пролетных строений.
Б.17. Опора
анкерная: опора многопролетного моста, воспринимающая горизонтальные усилия,
собирающиеся с нескольких пролетов, от торможения, температурных воздействий и
других горизонтальных сил.
Б.18. Опора
временная: опора с ограниченным сроком службы, используемая в период
строительства, восстановления или ремонта моста.
Б.19. Опора гибкая:
опора, как правило, большой высоты, обеспечивающая частично или полностью
продольные перемещения пролетного строения за счет своей упругой податливости.
Опора двухрядная - свайная опора, состоящая из двух рядов свай по фасаду,
объединяемых общей насадкой.
Б.20. Опора
жесткая: массивная опора, обладающая значительной жесткостью в продольном
направлении моста, способная воспринимать всю горизонтальную нагрузку,
передающуюся от пролетного строения, или давление грунта насыпи и не
участвующая в обеспечении продольных перемещений пролетного строения за счет
собственной деформации.
Б.21. Опора
качающаяся: опора в виде стоек или стенки с шарнирами на концах.
Б.22. Опора
массивная: бетонная опора без внутренних полостей, размеры которой, как
правило, больше (по конструктивным соображениям) расчетных.
Б.23. Опора
монолитная: опора, забетонированная непосредственно на месте строительства.
Б.24. Опора моста:
несущий элемент мостового сооружения, поддерживающий пролетные строения и
передающий нагрузки от них на фундамент.
Б.25. Опора
пойменная: опора, расположенная в пойменной части моста, т.е. за пределами
средней межени.
Б.26. Опора
промежуточная (бык): опора многопролетного моста, расположенная между устоями.
Термин "бык" (применять его не рекомендуется) относится лишь к
жестким массивным опорам.
Б.27. Опора
пустотелая: опора с внутренними полостями в ее теле, предназначенными для
снижения расхода материала и общей массы с целью уменьшения давления на грунт.
Б.28. Опора рамная:
железобетонная или деревянная опора в виде рамы.
Б.29. Опора речная
(русловая): промежуточная опора, расположенная в русле реки, т.е. в зоне
межени.
Б.30. Опора
ряжевая: опора в виде деревянного сруба из бревен или брусьев с внутренними
перегородками; сруб заполняется камнем.
Б.31. Опора
сборная: опора из заранее изготовленных железобетонных или бетонных элементов,
объединенных тем или иным способом.
Б.32. Опора
сборно-монолитная: опора, выполненная из заранее изготовленных железобетонных
или бетонных элементов, объединенных на месте строительства бетоном, обычно
служащим заполнителем.
Б.33. Опора
свайная: опора, состоящая из одного или двух рядов свай (по фасаду),
объединенных поверху насадкой.
Б.34. Опора
стоечная: опора, часть которой выше обреза фундамента. Выполнена из стоек,
объединенных поверху насадкой.
Б.35. Опора
столбчатая: опора без фундамента, выполнена из одного или нескольких сплошных
или пустотелых столбов, объединенных либо не объединенных поверху ригелем.
Б.36. Опора
телескопическая: промежуточная опора, тело которой состоит из нескольких
ярусов. Размеры сечений опоры одинаковые по форме, уменьшаются в каждом ярусе,
но в пределах яруса постоянны.
Б.37. Отказ сваи:
средняя величина (в см) погружения в грунт забивной сваи от одного удара молота
в залоге за 10 ударов, а при вибропогружении - величина (в см) погружения сваи
в грунт от работы вибропогружателя за 1 минуту.
Б.38. Открылок
(крыло устоя): консольный элемент устоя, не имеющий фундамента и служащий для
удержания грунта насыпи подхода.
Б.39. Перила моста:
ограждающее устройство на тротуарах с внешней стороны моста.
Б.40. Площадка
подферменная: верхняя поверхность оголовка подферменной плиты, ригеля насадки,
служащая для установки подферменников или опорных частей пролетного строения.
Б.41. Подошва
фундамента: нижняя плоскость его, передающая нагрузку на грунтовое основание.
Б.42. Подферменник
(подферменный камень): элемент верхней части опоры моста, выполненный из камня
или в виде железобетонного выступа на подферменной площадке, предназначенный
для установки опорных частей и служащий для распределения опорного давления
пролетного строения на тело опоры.
Б.43. Полоса
безопасности: полоса между полосой движения автотранспортных средств и
тротуаром или боковой дорожкой (пешеходной, велосипедной).
Б.44. Полоса
движения: полоса проезжей части автомобильной дороги, ширина которой
устанавливается по максимально допустимой ширине пропускаемого транспортного
средства, включая его габарит и зазоры безопасности.
Б.45. Полоса
переходно-скоростная: дополнительная полоса проезжей части для обеспечения
разгона или торможения автомобилей при выезде или въезде в общий транспортный
поток, движущийся по основным полосам проезжей части.
Б.46.
Предварительно напряженные железобетонные конструкции: конструкции, в бетоне и
арматуре которых с целью улучшения потребительских (эксплуатационных) качеств
искусственно созданы дополнительные внутренние усилия. Как правило, в бетоне
создают дополнительные усилия сжатия за счет передачи на него дополнительных
усилий растяжения арматуры.
Б.47. Предельное
состояние: состояние, при котором конструкция, основание перестают
удовлетворять заданным эксплуатационным требованиям или требованиям при
производстве работ.
Б.48.
Противоусадочная арматура: устанавливаемая для локализации усадочных явлений в
бетоне.
Б.49. Процент износа:
показатель износа, характеризующий в процентах снижение в элементе мостового
сооружения потребительских свойств (функциональных параметров), принимаемый в
соответствии с устанавливаемыми нормативными значениями.
Б.50.
Работоспособное состояние: состояние мостового сооружения, при котором значения
всех функциональных параметров соответствуют требованиям нормативно-технической
и (или) проектной документации.
Б.51. Рабочая
арматура: назначаемая по расчету конструкций.
Б.52.
Распределительная арматура: предназначена для более равномерного распределения
усилий по площади.
Б.53. Реконструкция
мостового сооружения: комплекс работ, направленных на улучшение основных
потребительских качеств существующего (эксплуатируемого) мостового сооружения с
полным или частичным использованием его конструкций.
Б.54.
Ремонтопригодность: свойство объекта, заключающееся в приспособленности к
предупреждению и обнаружению причин возникновения отказов, повреждений и
поддержанию и восстановлению работоспособного состояния путем проведения
технического обслуживания и ремонтов.
Б.55. Ригель опоры:
верхняя железобетонная часть столбчатой опоры (а также массивной опоры).
Б.56.
Свая-оболочка: железобетонная полая круглая свая, полость которой заполняется
грунтом или бетоном.
Б.57. Свая-столб:
разновидность железобетонных цилиндрических или призматических свай сплошного
сечения, погружаемых в предварительно пробуренные скважины с последующим
заполнением зазора между боковыми поверхностями скважины и элемента
песчано-цементным или грунтовым раствором.
Б.58. Слив:
наклонно расположенная плоскость подферменной площадки, а также других
элементов опоры, обеспечивающая сток воды с поверхностей тела опоры.
Б.59. Стена
подпорная: конструкция, удерживающая от обрушения находящийся за ней массив
грунта, в том числе и находящиеся на нем нагрузки.
Б.60. Стена
шпунтовая: сплошная стенка, образованная шпунтом (деревянным, железобетонным,
стальным), служащая водонепроницаемой преградой и удерживающая от обрушения
грунт в ограждении котлованов.
Б.61. Стенка
обратная: боковая стена устоя, стоящая на фундаменте, удерживающая засыпку за
устоем.
Б.62. Стенка
шкафная: элемент верхней части устоя, отделяющий торец пролетного строения и
зону расположения опорных частей от грунта насыпи подхода.
Б.63. Тело опоры:
часть опоры, расположенная выше фундамента.
Б.64. Устой
анкерный: устой многопролетного моста, на котором расположены неподвижные
опорные части, воспринимающие горизонтальные усилия, собирающиеся с нескольких
пролетов.
Б.65. Устой
диванный: устой простейшего типа, выполненный в виде опертых на щебеночную
подушку и находящихся в грунте насыпи бруса или железобетонной плиты со шкафной
стенкой и открылками.
Б.66. Устой
козловый: устой железобетонный свайный или стоечный с двумя или более рядами
свай или стоек (по фасаду), у которого ряд свай или стоек со стороны пролетного
строения наклонный.
Б.67. Устой
обсыпной: устой, большая часть которого находится в грунте конуса насыпи,
выступающего за переднюю стенку устоя.
Б.68. Устой раздельный:
устой, состоящий из двух частей: обсыпного устоя и опоры типа промежуточной,
между которыми может быть устроена стенка, препятствующая проходу льда и воды
между конусом насыпи и опорой.
Б.69. Устой
свайный: устой, в котором насадка или насадка со шкафной стенкой и открылками
оперта на сваи.
Б.70. Устой с
обратными стенками: устой, к телу которого примыкают расположенные параллельно
оси моста под прямым углом две обратные стены постоянной высоты, равной высоте
устоя, входящие в тело насыпи и опертые на фундамент.
Б.71. Устой с
откосными стенками: устой, к телу которого под углом к оси моста примыкают две
стены переменной высоты, опертые на фундамент.
Б.72. Устой
столбчатый: устой, состоящий из сборных или монолитных столбов, объединенных
поверху железобетонным ригелем со шкафной стенкой и открылками.
Б.73. Устойчивость:
способность сооружений и их элементов сопротивляться внешним усилиям без
разрушения, сохраняя первоначальную форму, равновесие и положение.
Б.74. Фундамент:
элемент моста, передающий нагрузку от опоры на основание; нижняя часть опоры,
находящаяся целиком в грунте или частично в воде.
Б.75. Фундамент
глубокого заложения: передает нагрузку на основание подошвой и боковой
поверхностью.
Б.76. Фундамент
мелкого заложения: передает нагрузку на основание подошвой.
Б.77. Экология:
научные принципы национального природопользования и охраны живых организмов.
Б.78. Эстакада:
мостовое сооружение, предназначенное для пропуска транспортных средств над
территорией с оставлением свободного пространства под пролетными строениями.
Приложение
В
(обязательное)
МАТЕРИАЛЫ
ДЛЯ БЕТОНА И РАСТВОРА
В.1. В качестве
вяжущих материалов следует применять портландцемент и шлакопортландцемент,
соответствующие требованиям ГОСТ 10178 или ЦЕМ I и ЦЕМ II, а также
сульфатостойкие цементы, соответствующие требованиям ГОСТ 22266.
Для бетонов и
строительных растворов следует применять цемент Д0 или Д5 с содержанием
до 8% (по ГОСТ 10178).
Для каждой
поступившей партии цемента (не менее 8 т) следует определять его нормативную
густоту, сроки схватывания, равномерность изменения объема, а для
пластифицированного или гидрофобного портландцемента - пластичность и
гидрофобность.
При производстве
сборных конструкций и изделий, подвергаемых тепловлажностной обработке, следует
учитывать группу эффективности цемента при пропаривании (ГОСТ 30515). Применение
портландцементов III группы эффективности при пропаривании не допускается.
В.2. При
возникновении сомнения в соответствии качества цемента выданному паспорту
потребитель должен произвести отбор проб цемента по ГОСТ 30515 и направить их
для испытания в головную организацию по испытаниям цемента или в ее
региональные центры.
В.3. При
поступлении цемента с содержанием щелочных оксидов более 0,6% в пересчете на
или применении щелочесодержащих добавок с
водой затворения необходимо проверить заполнители на потенциальную реакционную
способность по отношению к щелочам. Данные по содержанию щелочных оксидов
следует запрашивать у цементного завода-поставщика.
Заполнители,
характеризующиеся величиной растворимого кремнезема более 50 ммоль/л, не
допускается применять без специальной проверки.
В.4. В качестве
крупного заполнителя для тяжелого бетона следует применять щебень из природного
камня и гравия, а также гравий - по ГОСТ 26633.
Щебень из
природного камня и гравия, а также гравий следует применять в виде фракций от 5
(3) до 10 мм, свыше 10 до 20 мм, свыше 20 до 40 мм и свыше 40 до 70 мм,
раздельно дозируемых при приготовлении бетонной смеси. Дозировка крупного
заполнителя должна осуществляться раздельно по фракциям.
Соотношение
отдельных фракций крупного заполнителя в составе бетона должно находиться в
пределах, указанных в ГОСТ 26633, таблица 5. Запрещается использовать для
приготовления бетонной смеси заполнитель фракции 20 - 40 мм и выше без
соответствующего ГОСТ 26633, таблица 5 количества фракций 5 - 10 и 10 - 20 (5 -
20) мм.
В качестве мелкого
заполнителя следует использовать песок, соответствующий требованиям ГОСТ 8736 и
ГОСТ 26633. Зерновой состав мелкого заполнителя для бетона мостов и труб должен
быть в пределах 2 - 3. Может быть применен смешанный песок из мелкого или очень
мелкого природного песка и дробленого песка отсевов дробления изверженных
горных пород. Не допускается применять в качестве мелкого заполнителя только
дробленый песок (песок из отсевов дробления) без смешения его с природным
песком.
В требуемых случаях
в бетонах следует применять наполнители: микрокремнезем, золу-унос, молотый
песок, доменный гранулированный шлак и др.
В.5. Применение
очень мелкого песка с модулем крупности от 1,5 до 1,2 допускается лишь в случае
отсутствия крупного, среднего или мелкого песка при обязательном условии
обеспечения стабильности зернового состава крупного заполнителя, поступающего в
бетоносмеситель от замеса к замесу (в пределах требования ГОСТ 26633),
раздельном дозировании каждой фракции щебня, подтверждении возможности получения
бетона с допустимым расходом цемента и при соответствующем
технико-экономическом обосновании.
Очень мелкий песок
следует укрупнять добавкой природного крупного песка или дробленого песка из
отсевов дробления, доводя его зерновой состав до требований ГОСТ 26633.
В.6. Технические
требования на материалы для бетона и раствора, которые следует обеспечивать при
производстве бетонных работ и проверять при операционном контроле, а также
объем, методы или способы контроля приведены в таблице В.1.
Таблица В.1
┌─────────────────────────────────────────┬───────────────┬───────────────┐
│ Технические требования │ Контроль
│Способ контроля│
├─────────────────────────────────────────┼───────────────┼───────────────┤
│1. Вид портландцемента для всех │ Каждой партии │ Входной
│
│конструкций
железнодорожных │ │регистрационный│
│и
автодорожных мостов и труб:
│ │ │
│
для бетона мостов - по ГОСТ 10178 │
То же │ Проверка
│
│(в
том числе марок 550-Д0, 550-Д5,
│ │по
ГОСТ 30515, │
│600-Д0,
600-Д5) при C A не более 8%
│ │ ГОСТ 310.3,
│
│ 3 │ │ ГОСТ 310.4,
│
│
│ │ ГОСТ 10178
│
│
гидрофобный или пластифицированный -
│ " │ То же
│
│по
ГОСТ 10178 при C A не более 8%
│ │ │
│ 3 │ │ │
│и
минеральной добавки не более 5%
│ │ │
│
сульфатостойкий - по ГОСТ 22266
│ " │ " │
│
с добавкой нефелинового шлама -
│ "
│ " │
│по
ГОСТ 10178 при C A не более 5%
│ │ │
│ 3 │ │ │
│и
нефелинового шлама не более 15%
│ │ │
│
с добавкой нефелинового шлама
│ " │ " │
│и
трепела - по ГОСТ 10178 при C A
│ │ │
│ 3 │ │ │
│не
более 5% и минеральной добавки
│ │ │
│не
более 15%, в том числе трепела
│ │ │
│не
более 3%
│ │ │
│
быстротвердеющий при обязательном
│ Каждой партии │
Проверка │
│введении
в бетон комплексной
│ │по
ГОСТ 30515, │
│газообразующей
(кремнийорганической) и │ │ ГОСТ 310.3,
│
│пластифицирующей
добавки - по ГОСТ 10178 │
│ ГОСТ 310.4, │
│при
C A не более 8% и минеральной добавки│ │ ГОСТ 10178
│
│ 3 │ │ │
│не
более 5%
│ │ │
├─────────────────────────────────────────┼───────────────┼───────────────┤
│2. Вид портландцемента для бетона │ Каждой партии │ Проверка
│
│внутренней
зоны заполнения (при блоках
│ │по
ГОСТ 30515, │
│облицовки)
в районах с умеренным
│ │ ГОСТ 310.3,
│
│или
суровым климатом:
│ │ ГОСТ 310.4,
│
│
│ │ ГОСТ 10178
│
│
по поз. 1 настоящей таблицы сульфато-
│ То же │
То же │
│стойкий
с минеральными добавками -
│ │ │
│по
ГОСТ 22266
│ │ │
│
с минеральными добавками, в том числе
│ " │ " │
│пластифицированный
или гидрофобный - │ │ │
│по
ГОСТ 10178 при C A не более 8%
│ │ │
│ 3 │ │ │
├─────────────────────────────────────────┼───────────────┼───────────────┤
│3.
Вид цемента для монолитных бетонных и │ │ │
│ненапрягаемых
железобетонных конструкций │
│ │
│в
подводных и подземных частях
│ │ │
│железнодорожных
и автодорожных мостов │ │ │
│и
труб:
│ │ │
│
портландцемент - по поз. 1 и 2 настоящей│ " │ " │
│таблицы,
шлакопортландцемент, │ │ │
│пуццолановый
портландцемент для бетонных │ │ │
│смесей,
укладываемых в массивы, а также
│ │ │
│для
конструкций, твердеющих при
│ │ │
│температуре
не ниже 10 °C - по ГОСТ 10178│ │ │
│и
ГОСТ 22266
│ │ │
├─────────────────────────────────────────┼───────────────┼───────────────┤
│4.
Вид портландцемента для конструкций
│ │ │
│одежды
ездового полотна:
│ │ │
│
для дорожных и аэродромных покрытий, а
│ " │ " │
│также
для бетона мостов - по ГОСТ 10178
│ │ │
├─────────────────────────────────────────┼───────────────┼───────────────┤
│5.
Характеристика крупного заполнителя
│ │ │
│для
тяжелого бетона - щебня из природного│ │ │
│камня
и гравия, а также щебня:
│ │ │
│
наибольший размер зерен (наибольшая
│ " │
Проверка │
│крупность)
- по ГОСТ 26633 и СП 70.13330 │ │по ГОСТ 8269.0 │
│
число фракций: │ │ │
│ не менее двух - из зерен наибольшей │
" │ То же
│
│крупностью
до 40 мм включ.
│ │ │
│ не менее трех - из зерен наибольшей │
" │ " │
│крупностью
70 мм
│ │ │
│ допускается одна - из зерен
крупностью│ " │ " │
│5
- 20 мм
│ │ │
│ стабильность зернового состава, │
2 - 3 раза │ Проверка
│
│подаваемого
в бетоносмеситель, в течение │ в
месяц │по ГОСТ 8269.0 │
│смены
- по ГОСТ 8267 и ГОСТ 26633
│в течение смены│(рассев частных│
│ │с отбором проб │ проб)
│
│
│ из бункеров- │ │
│
│ дозаторов │ │
│
│ через каждые │ │
│
│ 1,5 - 2 ч │ │
├─────────────────────────────────────────┼───────────────┼───────────────┤
│6.
Стабильность мелкого заполнителя
│ Каждой партии │
Проверка │
│для
тяжелого бетона - по ГОСТ 26633
│ │ по
ГОСТ 8735 │
├─────────────────────────────────────────┼───────────────┼───────────────┤
│7.
Качество воды, используемой для
│При организации│
Проверка │
│приготовления
бетонных и растворных │ производства │по ГОСТ 23732, │
│смесей,
промывки заполнителей и ухода │и
при изменении│ ГОСТ 18164, │
│за
бетоном - по ГОСТ 23732
│ источника │ ГОСТ Р 52964, │
│
│ водоснабжения │
ГОСТ 4245 │
│
│ или состава │ │
│
│примесей в воде│ │
└─────────────────────────────────────────┴───────────────┴───────────────┘
В.7. При возведении
железобетонных мостов применяют вибрационные и самоуплотняющиеся бетоны.
В случае
использования самоуплотняющихся бетонов (СУБ) необходимо дополнительно
проводить их испытания на ползучесть и усадку, а также определять модуль
упругости.
Приложение
Г
(рекомендуемое)
ТЕХНОЛОГИЧЕСКИЙ
МЕТОД ПОДБОРА СОСТАВА БЕТОНА
Г.1.
Ориентировочную величину требуемого водоцементного отношения В/Ц определяют по
формуле
,
(Г.1)
где
- средний уровень прочности бетона,
соответствующий проектному классу бетона, или расчетная прочность бетона,
кгс/см2;
- активность или гарантированная марка
цемента, кгс/см2;
В - содержание воды
в 1 м3 бетона, л;
Ц - расход цемента
на 1 м3 бетона, кг.
Г.2. Расчетную
прочность бетона
рекомендуется устанавливать, когда требуемая
прочность бетона на ведущем технологическом этапе (после цикла ускоренного
твердения на момент выдачи конструкции на открытый воздух в зимнее время и
т.п.) превышает величины прочности, достигаемые к этому времени бетоном, состав
которого подобран на получение бетона прочностью, соответствующей проектному
классу бетона на 28-е сут нормального твердения.
Расчетную прочность
бетона
рекомендуется определять по формуле
,
кгс/см2, (Г.2)
где
- часть, %, проектной прочности
(соответствующей проектному классу бетона), требуемая на ведущем
технологическом этапе;
- часть, %, расчетной прочности бетона,
достигаемая к заданному сроку, при целесообразной длительности ускоренного
твердения (или выдерживания); достигаемую прочность бетона назначают с учетом
особенностей конкретного цемента, сроков и температурных условий твердения
бетона от окончания укладки до заданного срока на ведущем технологическом
этапе; при испытаниях контрольных образцов эту прочность уточняют.
Г.3. Ориентировочно
количество воды затворения на 1 м3 бетонной смеси (плотно уложенной),
необходимой для получения требуемой удобоукладываемости, рекомендуется определять
по таблице Г.1.
Таблица Г.1
Наибольшая
крупность
щебня, мм
|
Количество воды, л/м3 бетонной смеси,
при требуемой
удобоукладываемости
|
жесткости, с
|
подвижности, см осадки конуса
|
50
- 80
|
20
- 40
|
1
- 2
|
3
- 4
|
5
- 6
|
7
- 8
|
9
- 10
|
11
- 14
|
15
- 22
|
70
|
130
|
140
|
150
|
155
|
160
|
165
|
170
|
180
|
190
|
40
|
135
|
145
|
155
|
160
|
165
|
170
|
175
|
185
|
195
|
20
|
140
|
155
|
165
|
170
|
175
|
180
|
185
|
200
|
210
|
10
|
150
|
165
|
175
|
180
|
185
|
190
|
195
|
215
|
225
|
Примечание. Количество воды затворения
приведено для бетонных смесей,
приготовленных на портландцементе, с
нормальной густотой цементного
теста, равной 26%, и среднезернистом песке без пластифицирующих добавок.
При введении пластифицирующих добавок
количество воды может
быть
уменьшено на 10 - 15 л на м3 бетона. При
использовании цемента с
иной
нормальной густотой, песка иной крупности или введении других химических
добавок количество воды должно быть соответственно откорректировано.
|
Г.4. Расход цемента
Ц на 1 м3 бетона рекомендуется определять по формуле
, кг.
(Г.3)
Г.5. Дальнейший
расчет рекомендуется производить исходя из того, что сумма абсолютных объемов
составляющих материалов равна 1 м3 плотно уложенной бетонной смеси.
Г.6. Абсолютные
объемы цементного теста и смеси заполнителей, а также содержание (масса)
заполнителей - песка и щебня в 1 м3 рекомендуется рассчитывать по следующим
формулам:
абсолютный объем цементного теста
:
, л;
(Г.4)
абсолютный объем смеси заполнителей
(песок + щебень)
:
, л;
(Г.5)
содержание (масса) заполнителей (песка и
щебня) З:
, кг.
(Г.6)
В том числе:
щебня
, кг;
(Г.7)
песка
П = З - Щ, кг.
(Г.8)
В формулах (Г.4) -
(Г.8):
- плотность цемента, кг/л;
Д - количество
химической добавки (в расчете на сухое вещество), кг;
- плотность сухого вещества добавки, кг/л.
При введении
нескольких добавок (комплексной добавки)
определяется по формуле
.
Приведенная
плотность смеси заполнителей
равна:
,
где
и
- плотность соответственно щебня и песка,
кг/л;
r = П/Щ -
соотношение по массе между песком и щебнем.
Г.7. Соотношение
крупной и мелкой фракции щебня (при наличии обеих фракций в необходимом
количестве) выбирают в пределах, указанных в ГОСТ 26633. При дефиците одной из
фракций (например, при дополнительном обогащении заполнителей перед подачей в
бетоносмеситель) соотношение фракций принимают таким, которое имеется
фактически в используемом заполнителе.
Г.8. Выбор
оптимального соотношения между количеством крупного и мелкого заполнителей,
максимально соответствующего природным свойствам используемых заполнителей,
технологическим факторам укладки и особенностям изготовляемой конструкции,
является важнейшим этапом подбора состава бетона. Соотношение r = П/Щ (песка и
щебня) рекомендуется определять из условия, что для конкретных заполнителей
существует единственное соотношение между количеством песка и щебня, которое
дает лучшую удобоукладываемость бетонной смеси при наименьшем расходе цемента и
воды. Это соотношение достоверно можно определить, оценивая свойства
заполнителей непосредственно в бетоне, т.е. определяя r в пробных лабораторных
замесах и уточняя в процессе опытного изготовления конструкций в
производственных условиях.
Г.9.
Наилучшее соотношение между количеством песка и щебня в лабораторных условиях
рекомендуется определять по наибольшей удобоукладываемости бетонной смеси при
одном и том же расходе цемента и воды. Для этого рекомендуется рассчитывать
составы бетона с r, равным от 0,3 до 0,9 (для крупнозернистых песков r, как
правило, колеблется от 0,5 до 0,9; для среднезернистых - от 0,4 до 0,7 и для
мелких - от 0,3 до 0,5). Составы следует рассчитывать через интервал в 0,1,
т.е. с r, равным 0,3; 0,4 и т.д. Для мелкого песка следует рассчитывать составы
с r через интервал 0,05.
Г.10. Лабораторные
замесы при определении наилучшего r рекомендуется приготовлять на заполнителях,
обязательно рассеянных на отдельные фракции; щебень должен быть разделен на
фракции 0 - 5, 5 - 10, 10 - 20, 20 - 40 и 40 - 70 мм; песок - на фракции от 0
до 5 мм и свыше 5 мм. При дозировке отдельных фракций должно быть сохранено их
среднее соотношение, фактически имеющееся в каждой номинальной фракции
применяемых заполнителей.
Если при наилучшем
r удобоукладываемость бетонной смеси не соответствует заданной, то состав
рекомендуется корректировать, уменьшая или увеличивая расход цемента и воды
(цементного теста) при неизменных В/Ц и r. При выборе соотношения между песком
и щебнем необходимо в пробных замесах проверять составы, дающие как увеличение,
так и снижение удобоукладываемости бетонной смеси.
Для сокращения
количества пробных лабораторных замесов рекомендуется вначале приготовить замес
со средним r из интервала, приведенного в п. 9, в зависимости от модуля
крупности песка. При резком отличии удобоукладываемости смеси от требуемой
рекомендуется соответственно корректировать расход цементного теста (изменяя
расход цемента и воды при постоянном В/Ц).
Г.11. В том случае,
когда подбирают состав бетона на материалах (цементе, заполнителях и добавках),
для которых не была заранее установлена фактическая зависимость прочности
бетона от В/Ц, после подбора наилучшего r в лабораторных условиях изготовляют контрольные
образцы из бетонных смесей с В/Ц, требуемым по расчету, а также уменьшенным и
увеличенным на 0,02 - 0,05. Удобоукладываемость бетонной смеси с уменьшенным и
увеличенным В/Ц доводят до заданной путем изменения (увеличения или уменьшения)
расхода цементного теста при неизменном r.
Г.12. Бетонные
смеси на основе составов, полученных в лабораторных условиях, для изготовления
контрольных образцов рекомендуется приготовлять в лабораторном или
производственном бетоносмесителе; приготовлять бетонную смесь с
воздухововлекающими добавками для изготовления контрольных образцов необходимо
только в производственном бетоносмесителе при строгом контроле длительности
перемешивания смеси.
В случае, если
удобоукладываемость бетонной смеси, приготовленной в производственном
бетоносмесителе, не соответствует требуемой, состав бетона необходимо
корректировать, соответственно изменяя расход цементного теста при неизменных
В/Ц и r. При отклонении воздухосодержания смеси от заданного рекомендуется
корректировать количество воздухововлекающего компонента в добавке.
Г.13. Для упрощения
расчетов и получения более достоверных результатов при определении наилучшего r
и удобоукладываемости смеси лабораторные замесы рекомендуется приготовлять на
основе воздушно-сухих заполнителей, т.е. предварительно высушенных на открытом
воздухе (или в лаборатории) на пленке или на бумаге без дополнительного
нагрева.
Г.14. Из каждой
серии изготовленных контрольных образцов часть образцов рекомендуется помещать
в камеру нормального твердения (в качестве эталона), а остальные вместе с
изготовляемыми конструкциями подвергать всему циклу ускоренного твердения или
выдерживания. При наличии лабораторной камеры с автоматическим управлением
контрольные образцы могут быть подвергнуты ускоренному твердению по той же
программе, что и конструкции на технологической линии.
На основании
испытаний контрольных образцов рекомендуется выбирать состав с тем минимальным
В/Ц, которое обеспечивает требуемую прочность бетона на ведущем технологическом
этапе.
Г.15. С учетом
влажности заполнителей рекомендуется рассчитывать опытный рабочий состав бетона
и производить опытное бетонирование конструкций. В процессе бетонирования
рекомендуется определять оптимальное r по технологическому признаку.
Показателем
(признаком) оптимального состава бетона и соответствия гранулометрического
состава заполнителей, принятому при подборе, является наличие на поверхности
свежеуложенного бетона вкраплений зерен щебня, выступающих на 1/3 своей
величины, с расстоянием между ними 3 - 6 см.
Скопление зерен
щебня, отделение их от уплотняемой массы и щебенистость поверхности
свидетельствуют о недостатке, а образование на поверхности бетона слоя
цементного раствора - об избытке песка в бетоне.
Г.16. При выборе
соотношения между количеством песка и щебня по технологическому признаку
разница между наилучшим r, подобранным в лабораторных условиях, и оптимальным r
может достигать +/- 0,15 в зависимости от конкретных технологических
особенностей изготовляемой конструкции и способов выполнения работ.
В связи с тем, что
такое изменение r при прочих равных условиях практически не отражается на
прочностных показателях бетона, зависимость прочности бетона от В/Ц для состава
с оптимальным r рекомендуется не уточнять. Состав бетона с оптимальным r
рекомендуется принимать за номинальный и рассчитывать на его основании рабочий
состав бетона, который необходимо корректировать в процессе производства
конструкций в соответствии с ГОСТ 27006.
Г.17. В процессе
выполнения бетонных работ фактический состав заполнителей в бетоне
рекомендуется контролировать также по технологическому признаку, уменьшая или
увеличивая r без изменения общего расхода заполнителей, цемента, воды и
добавок.
Приложение
Д
(рекомендуемое)
ПОДБОР
СОСТАВА ЦЕМЕНТНО-ПЕСЧАНОГО РАСТВОРА
МЕТОДОМ ПРОБНОГО
ЗАМЕСА
Для подбора состава
раствора рекомендуется использовать цементное тесто заданного качества.
Ориентировочную
величину требуемого В/Ц рекомендуется определять по формуле
,
(Д.1)
где
- проектная марка раствора при сжатии или
требуемая расчетная прочность раствора, кгс/см2;
- активность или гарантированная марка
цемента, кгс/см2.
Расчетную прочность
раствора при необходимости определяют по методике, изложенной в Приложении Г.
Приготовляют 5 - 7
л цементного теста с требуемым В/Ц и назначенным количеством добавок (если они
вводятся).
Отвешивают 5 кг
песка и помещают его на боек.
Отвешивают 2 - 3 кг
цементного теста и на бойке тщательно перемешивают его с песком,
последовательно добавляя в полученный раствор цементное тесто по 0,25 - 0,5 кг,
доводя подвижность растворной смеси до заданной величины.
На основании
положения, что сумма абсолютных объемов составляющих материалов равна 1 м3
плотно уложенной цементно-песчаной растворной смеси, по количеству
израсходованных на замес материалов рекомендуется рассчитывать объем
приготовленного цементно-песчаного раствора
, л, и
абсолютный объем добавок, израсходованный на замес,
, л,
по формулам:
, л;
(Д.2)
.
(Д.3)
В формулах (Д.2),
(Д.3):
,
- количество соответственно цемента и песка,
израсходованных на замес, кг;
- количество воды, израсходованной на замес,
л; в количестве воды
должна быть учтена вода, содержащаяся в
растворах добавок;
,
и т.д. - количество каждой добавки,
израсходованное на замес вместе с цементным тестом (в расчете на сухое вещество
добавки), кг;
,
,
- плотность соответственно цемента, песка и
сухого вещества каждой добавки, кг/л.
Расход материалов
(состав раствора), кг на 1 м3 рассчитывают делением количества каждого
составляющего материала, израсходованного на замес, на рассчитанный объем
замеса V и умножением на 1000.
В лабораторном или
производственном смесителе приготовляют цементно-песчаный раствор полученного
при подборе состава и изготовляют из него контрольные образцы. В том случае,
когда подбирают состав раствора из новых материалов, для которых заранее не
была установлена фактическая зависимость прочности раствора от В/Ц, после
подбора состава раствора изготовляют контрольные образцы из раствора с
расчетным В/Ц и с В/Ц, уменьшенным или увеличенным на 0,02 - 0,05.
На основании
испытаний контрольных образцов рекомендуется подбирать состав раствора с В/Ц,
обеспечивающим требуемую прочность при наименьшем расходе цемента.
Приложение
Е
(обязательное)
БЕТОНЫ И
РАСТВОРЫ
Е.1. Номинальный
состав бетона подбирают по утвержденному заданию в соответствии с ГОСТ 27006.
Состав бетона (раствора) для мостовых конструкций подбирают исходя из условия
обеспечения среднего уровня прочности, значение которого следует определять по
ГОСТ Р 53231 исходя из коэффициента вариации 13,5%.
Методы подбора
составов бетона и раствора приведены в Приложениях Г и Д.
Е.2. Введение в
бетонную (растворную) смесь комплексных добавок для обеспечения морозостойкости
обязательно для бетонов (растворов) с проектной маркой F200 и выше, а также для
бетонов (растворов) меньшей марки по морозостойкости на портландцементе, содержащем
более 5% минеральных добавок.
В случае
приготовления бетонов (растворов) марки по морозостойкости F100 без введения
комплексных добавок, содержащих воздухововлекающий (газообразующий) компонент,
В/Ц не должно превышать 0,55.
Для бетонов
(растворов) с нормированной морозостойкостью при использовании
пластифицированного портландцемента в бетонную смесь вместо комплексной добавки
следует вводить только воздухововлекающий (газообразующий) компонент, а при
использовании гидрофобного портландцемента - только пластификатор ЛСТ.
В бетонную смесь на
пластифицированном портландцементе не следует вводить суперпластификатор С-3.
Е.3. Оптимальную
дозировку добавок, вводимых в бетонную смесь, следует устанавливать
экспериментально при подборе состава бетона с учетом данных, указанных в
таблице Ж.1; дозировку воздухововлекающего компонента необходимо устанавливать
при строгом контроле времени перемешивания бетонной смеси и в последующем
регулярно корректировать из условия обеспечения на месте укладки заданного
содержания в смеси вовлеченного воздуха (с учетом его возможной потери при
транспортировании смеси).
Е.4. Введение в
бетонную смесь добавок - ускорителей твердения бетона для сокращения сроков
достижения бетоном требуемой прочности запрещается.
В бетонах с поташом
в качестве противоморозного компонента в составе комплексной добавки количество
добавки ЛСТ следует устанавливать в зависимости от количества вводимого поташа
с обязательной проверкой в лаборатории указанного сочетания с конкретным
цементом.
Е.5. Нормативные
требования, которые следует выполнять при приготовлении бетонов и растворов и
проверять при операционном контроле, а также объем и способы контроля приведены
в таблице Е.1.
Таблица Е.1
┌──────────────────────────────────────┬────────────────┬─────────────────┐
│ Технические требования │ Контроль
│ Способ контроля │
├──────────────────────────────────────┼────────────────┼─────────────────┤
│1.
Минимальный расход цемента, кг/м3
│
│ │
│бетона,
для конструкций,
│
│ │
│расположенных: │ │ │
│
ниже глубины промерзания
│ Всего объема │
Измерительный │
│или
возможного размыва дна - 230 │
укладываемого │(проверка работы
│
│
│ бетона │дозаторов цемента│
│
│ │ и
фактического │
│
│ │
выхода бетона) │
│
в подводной и надводной (надземной
│ То же │ То же
│
│частях)
сооружения - 260
│
│ │
│
в пределах переменного уровня воды
│ " │ " │
│или
промерзания грунта - 290
│
│ │
│
в мостовом переходе - 290
│ " │ " │
├──────────────────────────────────────┼────────────────┼─────────────────┤
│2.
Максимальный расход цемента, кг/м3 │ │ │
│бетона,
класса:
│
│ │
│
до В35 включ. - 450
│ Каждого объема │
" │
│ │
укладываемого │ │
│ │ бетона
│ │
│
В40 - 500
│ То же │ " │
│
В45 и выше - 550
│ " │ " │
├──────────────────────────────────────┼────────────────┼─────────────────┤
│3.
Водоцементное отношение, весовые
│
│ │
│части
по массе, в бетонах, не более:
│
│ │
│
подземной зоны - 0,65
│Каждого состава │ Регистрационный │
│
│ бетона │ │
│
с добавками для повышения их
│
│ │
│морозостойкости: │ │ │
│ марки по морозостойкости │ │ │
│
┌────┬────┬────┤ │ │
│
│F100│F200│F300│ │ │
│
├────┼────┼────┤ │ │
│
в железобетонных и │ - │0,50│0,45│ То же
│ То же │
│тонкостенных
бетонных │ │
│ │ │ │
│конструкциях
толщиной │ │
│ │ │ │
│менее
0,5 м │ │
│ │ │ │
│
├────┼────┼────┤ │ │
│
в бетонных массивных
│0,60│0,55│0,47│ " │ " │
│конструкциях │
│ │ │ │ │
│
├────┼────┼────┤ │ │
│
в блоках облицовки │ - │ -
│0,47│ " │ " │
├───────────────────────┴────┴────┴────┼────────────────┼─────────────────┤
│4.
Объем вовлеченного воздуха
│Один раз в смену│
Проверка │
│в
бетонных смесях на месте укладки
│ в условиях │
по ГОСТ 10181 │
│для
бетонов с нормированной
│ стабильного │ │
│морозостойкостью,
%: │ производства
│ │
│
в бетонных и железобетонных
│(при постоянных:│ │
│конструкциях
- 2 - 4 │ составе
│ │
│
в мостовом полотне - 5 - 6 │бетона, качестве│ │
│
│ материалов, │ │
│
│ режиме │ │
│ │
приготовления │ │
│
│ и уплотнения │ │
│
│бетонной смеси) │ │
│
│ и два раза │ │
│ │ в смену -
│ │
│
│ в других │ │
│
│ условиях │ │
├──────────────────────────────────────┼────────────────┼─────────────────┤
│5.
Количество химических добавок,
│
│ │
│вводимых
в бетонную смесь при ее │ │ │
│приготовлении,
% массы цемента: │ │ │
│
технических лигносульфонатов ЛСТ
│ Не реже одного │
Операционный │
│(сухого
вещества) - 0,1 - 0,2
│ раза в смену │
(проверка │
│
│
│плотности рабочих│
│ │ │ растворов,
│
│
│
│ добавок и │
│
│
│дозаторов добавок│
│
│ │при приготовлении│
│
│ │
бетонной смеси) │
│
модифицированных технических
│ То же │ То же
│
│лигносульфонатов
ЛСТМ-2 (сухого │ │ │
│вещества)
- 0,10 - 0,25 │ │ │
│
суперпластификаторов С-3 (сухого
│ " │ " │
│вещества)
- 0,3 - 0,7 │ │ │
│
воздухововлекающих компонентов
│ " │ " │
│комплексных
добавок СНВ, СДО, СВП, │ │ │
│КТП,
СПД (сухого вещества) -
│
│ │
│0,003
- 0,05 (уточняется при подборе
│ │ │
│состава
бетона из условия обеспечения │ │ │
│требуемого
объема вовлеченного │ │ │
│воздуха) │ │ │
│
кремнийорганической эмульсии КЭ-30-04│ Не реже одного │ " │
│(50%-ной
концентрации) - 0,4 кг/м3 │ раза в смену
│ │
│бетона │ │ │
│
щелочного стока производства │
То же │ " │
│капролактама
ЩСПК (сухого вещества) - │
│ │
│до
0,3
│
│ │
│
мылонафта, асидола, асидол-мылонафта │ " │ "
│
│(товарного
раствора) - 0,02 - 0,05 │ │ │
│
ацетоно-формальдегидной смолы АЦФ-3
│ " │ " │
│(сухого
вещества) - 0,1 - 0,2
│
│ │
│противоморозных
добавок: │ │ │
│
противоморозные добавки при расчетной│ │ │
│температуре
воздуха, минус °C │ │ │
│
┌────┬─────┬──────┬─────┬─────┤ │ │
│ │до 5│от 6 │от 11
│от 16│от 21│
│ │
│ │ │до 10│до 15 │до
20│до 25│
│ │
│
├────┼─────┼──────┼─────┼─────┤ │ │
│нитрита
│ 5 │ 7
│ 9 │
- │ -
│ Не реже одного │
Операционный │
│натрия │
│ │ │ │
│ раза в смену │
(проверка │
│ │ │
│ │ │
│
│плотности рабочих│
│ │ │
│ │ │
│
│ растворов, │
│ │ │
│ │ │
│
│ добавок и │
│ │ │
│ │ │
│
│дозаторов добавок│
│ │ │
│ │ │
│ │при приготовлении│
│ │ │
│ │ │
│ │
бетонной смеси) │
│
├────┼─────┼──────┼─────┼─────┤ │ │
│поташа │ 5
│ 7 │
9 │ 11 │ 14
│ То же │ То же
│
│
└────┴─────┴──────┴─────┴─────┤ │ │
│
суперпластификатор С-3, вводимый
│ " │ " │
│совместно
с нитритом натрия, - │ │ │
│0,3
- 0,6 │ │ │
│
технические лигносульфонаты ЛСТ
│ " │ " │
│(ЛСТМ-2),
вводимые в качестве │ │ │
│замедлителя
схватывания бетона │ │ │
│совместно
с поташом, - 0,3 - 1,2 │ │ │
└──────────────────────────────────────┴────────────────┴─────────────────┘
Приложение
Ж
(обязательное)
БЕТОНИРОВАНИЕ
СБОРНЫХ КОНСТРУКЦИЙ
Ж.1. На каждый тип
(или типоразмер) конструкций должны быть разработаны технологические карты,
регламентирующие технологический процесс на всех этапах производства.
Технологические карты разрабатывают на основе рабочей документации из условия
технологической обеспеченности требуемого качества изготовляемых конструкций в
конкретных условиях данного предприятия. Изготовление сборных конструкций без
технологических карт запрещается.
Ж.2. Бетонирование
сборных конструкций на открытых площадках допускается при обеспечении условий,
гарантирующих на каждом технологическом этапе приобретение бетоном заданной
прочности по всему объему конструкции.
Ж.3. Допускается
укладывать и уплотнять бетонную смесь наклонными слоями на всю высоту
поперечного сечения балки (в соответствии с 7.72 настоящего свода правил), если
опалубка не оборудована виброподдоном.
При бетонировании
конструкции с применением самоуплотняющихся бетонов применение виброуплотнения
не обязательно.
Ж.4. Блоки
составных по длине конструкций коробчатого сечения и плитноребристых
конструкций (ПРК) неразрезных пролетных строений, типовых балочных пролетных
строений и сборных опор мостов, монтируемых на клееных стыках, следует
изготовлять в цельнометаллической или комбинированной опалубке, оборудованной
гибкими вибросистемами, и бетонированием "в торец" с использованием в
качестве торца опалубки ранее забетонированного блока. Торцевую поверхность
бетона блока, сдвинутого в положение "отпечатка", покрывают перед
бетонированием очередного блока специальной разделительной смазкой: раствором
каолина, извести и других аналогичных материалов. Не допускается использовать
смазки, имеющие в своем составе различные виды масел. Бетонную смесь при
бетонировании блоков пролетных строений следует уплотнять виброподдоном и вибролистами
боковых щитов и внутренней части опалубки, включая группы вибраторов,
соответствующие зоне укладки бетонной смеси.
Ж.5. При
изготовлении звеньев труб с немедленной распалубкой должно быть обеспечено
свободное размещение - без напряжений и упругих деформаций всех элементов
арматурного каркаса по отношению к формующим поверхностям наружной опалубки и
сердечника виброформы. Также свободно необходимо располагать фиксаторы и
прокладки, гарантирующие толщину защитного слоя бетона и проектное расположение
арматуры. Бетонную смесь в опалубку подают небольшими порциями, не допуская ее
зависания на арматуре.
Бетонную смесь
следует подавать и уплотнять послойно слоем толщиной 25 - 40 см по всей площади
изготовляемой конструкции. Обнаруженные после немедленной распалубки мелкие
дефекты на поверхности бетона необходимо безотлагательно устранять затиркой
цементно-песчаным раствором или ремонтными составами (например, ЭМАКО, БИРСС и
т.д.). Крупные раковины и каверны с обнажением арматуры, оплывы бетона и осадка
стенок, трещины на внутренней и наружной поверхностях бетона звена, а также
отвалы поверхностного слоя бетона исправлению и затирке раствором не подлежат.
Звенья труб, имеющие указанные дефекты бетона, считаются бракованными.
Ж.6. При заводском
изготовлении мостовых железобетонных конструкций контроль качества
осуществляется организацией в области контроля качества изготовления и монтажа
мостовых конструкций.
Ж.7. Технические
требования, которые следует выполнять при бетонировании сборных конструкций и
проверять при операционном контроле, а также объем и способы контроля приведены
в таблице Ж.1.
Таблица Ж.1
┌──────────────────────────────────────────────┬────────────┬─────────────┐
│ Технические требования │ Контроль
│ Способ │
│
│ │ контроля
│
├──────────────────────────────────────────────┼────────────┼─────────────┤
│1.
Удобоукладываемость бетонной смеси:
│ │ │
│
при изготовлении оболочек на начало
│Не реже двух│Измерительный│
│центрифугирования
при укладке смеси в │раз в
смену │по ГОСТ 10181│
│полуформу
или на момент окончания укладки
│ │ │
│смеси
в сболченную форму - не менее 1 см │ │ │
│осадки
конуса
│ │ │
│
на месте укладки при изготовлении оболочек
│ Не реже │
То же │
│в
виброформах - 1 - 4 см осадки конуса
│одного раза │
│
│
│ в смену │ │
│
при изготовлении звеньев труб с уплотнением: │ │ │
│
вибросердечником - 30 - 25 с (до 1 см осадки │ То же
│ " │
│конуса) │ │ │
│
наружными вибраторами или глубинными
│ " │ " │
│вибраторами
с гибким валом - 2 - 4 см осадки
│ │ │
│конуса
│ │ │
│
на виброплощадках (в том числе с крутильными │ "
│ " │
│колебаниями)
- 40 - 60 с
│ │ │
│
блоков сборных опор и облицовочных блоков
│ │ │
│с
уплотнением:
│ │ │
│
на виброплощадках - 60 - 80 с
│Не реже двух│
" │
│
│раз в смену │
│
│
наружными и глубинными вибраторами - не более│ То же
│ " │
│2
см осадки конуса
│ │ │
├──────────────────────────────────────────────┼────────────┼─────────────┤
│2.
Количество отходящего шлама при
│ Каждой │Измерительный│
│изготовлении
центрифугированных оболочек
│конструкции │
или │
│не
менее 20 л/м3 бетона
│ │
визуальный │
├──────────────────────────────────────────────┼────────────┼─────────────┤
│3.
Интенсивность воздействия вибропригруза
│ Один раз │Измерительный│
│(при
изготовлении пустотных плит автодорожных │ в неделю
│ │
│пролетных
строений) на поверхность бетонной
│ │ │
│смеси
в статическом состоянии 3 - 4 кПа │ │ │
│(30
- 40 г/см2), амплитуда колебаний
│ │ │
│0,4
- 0,7 мм
│ │ │
├──────────────────────────────────────────────┼────────────┼─────────────┤
│4.
То же, пневмопригруза (вместо
│ То же │
То же │
│вибропригруза)
на поверхность бетонной смеси
│ │ │
│20
- 25 кПа (200 - 250 г/см2)
│ │ │
├──────────────────────────────────────────────┼────────────┼─────────────┤
│5.
Время работы виброплощадки при изготовлении│ │ │
│пустотных
плит автодорожных пролетных
│ │ │
│строений,
с, не менее:
│ │ │
│
после второго прохода бетоноукладчика при
│ Не реже │
" │
│уплотнении
нижнего слоя бетонной смеси - 80
│одного раза │
│
│
│ в смену │ │
│
при бетонировании стенок плиты (общее время
│ То же │
" │
│работы)
и выравнивании поверхности плиты
│ │ │
│(вместе
с пригрузом) - 120
│ │ │
│
при бетонировании верхнего слоя (общее время │ "
│ " │
│работы)
- 180
│ │ │
├──────────────────────────────────────────────┼────────────┼─────────────┤
│6.
Прочность бетона при изготовлении пустотных│ При │
Проверка │
│плит
автодорожных пролетных строений перед
│ отработке │ по
образцам │
│извлечением
пустотообразователей не менее │
технологии │ по │
│0,3
МПа (3 кгс/см2)
│ │ ГОСТ
10180, │
│ │ │неразрушающим│
│
│ │ методом
по │
│
│ │ГОСТ Р
53231 │
└──────────────────────────────────────────────┴────────────┴─────────────┘
Приложение
И
(обязательное)
ТЕПЛОВАЯ
ОБРАБОТКА СБОРНЫХ КОНСТРУКЦИЙ
И.1. Требуемую
прочность бетона изделий в сжатые сроки следует обеспечивать применением
тепловой обработки. Введение в бетон химических добавок - ускорителей твердения
запрещается.
И.2. Тепловую
обработку мостовых железобетонных конструкций необходимо производить следующими
способами:
тепловой обработкой
бетона в пропарочных камерах ямного или тоннельного типа, под переносными
(съемными) колпаками насыщенным паром низкого (до 0,3 МПа) давления;
контактным и
конвективным прогревом бетона, уложенного в теплоизолированные формы, с помощью
различных теплоносителей: пара, горячей воды, разогретого масла, электричества;
комбинированными
способами прогрева.
При соответствующем
технико-экономическом обосновании в целях экономии энергоресурсов допускается
изготовление изделий в теплоизолированных опалубках с выдерживанием методом
термоса, экзотермическим способом или сочетанием вышеуказанных методов тепловой
обработки.
Допускается также
применение в опытном порядке гелиотехнологий с использованием
светотеплоизолирующих покрытий, промежуточных теплоносителей и
теплоаккумулирующих веществ при условии исключения высушивания бетона.
Ускоренное
твердение бетона указанными способами, кроме тепловой обработки пропариванием и
контактным прогревом в термоформах, осуществляется с учетом вида конструкции и
условий выполнения работ по специальным инструкциям в составе проектов
технологических линий. Эти способы целесообразно, как правило, использовать в
полигонных условиях, а также в условиях, когда процесс тепловой обработки не является
лимитирующим и не оказывает решающего влияния на производительность
технологических линий, либо при отсутствии надежных источников тепла или
достаточных лимитов на них и в случаях, когда обеспечивается высокая (до 30 -
35 °C) температура укладываемой бетонной смеси.
И.3. Способ
тепловой обработки следует выбирать в зависимости от принятой (или
существующей) технологии изготовления конструкций (стендовой,
поточно-агрегатной, конвейерной), наличия теплоносителей и конструктивных
особенностей изделий (конфигурации, габаритности и массивности) в целях
обеспечения главного условия производства - достижения проектной
производительности технологической линии при минимальных экономических затратах
и обеспечении требуемого качества и долговечности конструкций и эффективного
использования топливно-энергетических ресурсов.
И.4. Тепловая
обработка изделий пропариванием применяется при изготовлении практически всех
мостовых железобетонных конструкций.
Тепловую обработку
в термоформах целесообразно применять для конструкций сложной конфигурации:
тавровых и двутавровых цельноперевозимых балочных пролетных строений,
изготавливаемых по стендовой технологии в стационарной опалубке или по
поточно-агрегатной технологии с использованием гидрофицированной стационарной
опалубки на посту формования и выдержки до набора распалубочной прочности:
коробчатых блоков и блоков ПРК составных пролетных строений.
И.5. При
проектировании технологических линий теплоноситель следует выбирать на
основании технико-экономических расчетов и целесообразности его применения в
конкретных условиях производства.
Применение
продуктов сгорания природного газа для тепловой обработки мостовых
железобетонных конструкций в ямных и тоннельных пропарочных камерах, а также
под съемными колпаками не допускается.
И.6. На заводах и
полигонах необходимо выдерживать установленные в проекте технологической линии
режимы тепловой обработки изделий, обеспечивающие минимальное время, требуемое
для достижения распалубочной, передаточной или отпускной прочности бетона.
Увеличение
установленной длительности тепловой обработки в будние дни должно быть
согласовано с проектной организацией-разработчиком технологических линий.
В выходные и
праздничные дни при увеличенной длительности выдерживания изделий в установках
ускоренного твердения бетона с целью экономии топливно-энергетических ресурсов
следует предусматривать энергосберегающие режимы тепловой обработки: с
пониженной температурой изотермического прогрева и частично-термосное
выдерживание.
И.7. При назначении
в проектной документации на конструкцию величин передаточной и отпускной
прочности бетона следует учитывать реальные технологические возможности их
достижения в производственных условиях.
И.8. При
проектировании заводских технологических линий необходимо предусматривать
начальную температуру бетонной смеси для конструкций, подвергаемых тепловой
обработке, в пределах от 20 до 35 °C. При формовании конструкций температура
опалубки и окружающей среды должна быть не ниже 15 - 20 °C. При более низкой
температуре окружающей среды отформованные изделия для обеспечения проектной
производительности технологических линий следует предварительно выдерживать в
термоактивной опалубке.
И.9. При разработке
проектов технологических линий по изготовлению мостовых железобетонных
конструкций необходимо предусматривать мероприятия по созданию условий для
выравнивания температуры по объему установок ускоренного твердения бетона, а
также по защите бетона от высыхания и трещинообразования в отдельные периоды
его ускоренного твердения и при выдаче на склад готовой продукции.
И.10. Для улучшения
условий теплообмена и стабилизации температуры паровоздушной среды по объему ямных
и тоннельных пропарочных камер и под съемными колпаками последние необходимо
оборудовать изотермическими смесителями или эжекторами-терморегуляторами.
И.11. Обогреваемые
элементы термоформ, системы введения и распределения теплоносителя должны
обеспечивать требуемый температурный режим во всех сечениях по длине и высоте
изготавливаемой конструкции. При использовании в качестве теплоносителя пара,
воды или масла разводку следует производить только регистрами; подача
теплоносителя непосредственно в полости термоформ не допускается.
Термоформы должны
иметь инвентарные влаготеплозащитные покрытия для защиты от охлаждения и
высыхания открытых поверхностей бетона изготовляемых конструкций.
И.12. При
разработке проектов технологических линий и технологических карт на
изготовление мостовых железобетонных конструкций необходимо предусматривать
мероприятия по предупреждению сушки бетона во время тепловой обработки и после
нее.
Способ увлажнения
греющей среды или защиты бетона от испарения следует выбирать на основании
технико-экономического обоснования.
И.13. Пропарочные
камеры, съемные колпаки и термоформы, как правило, должны быть оборудованы
системами автоматического управления тепловой обработкой, обеспечивающими
регулирование и контроль температурного режима и прочности твердеющего бетона
или температурного режима греющей среды.
И.14. Конструкция
до обжатия должна быть распалублена и освидетельствована. В случае обнаружения
дефектов (раковин, каверн), снижающих прочность конструкции, они должны быть
заделаны по согласованию с проектной организацией. Бетон, применяемый для
заделки, должен иметь прочность не ниже допустимой при обжатии.
Запрещается
распалубливание и освидетельствование конструкций до окончания полной их
тепловой обработки (кроме двухстадийной).
И.15. Для сборных
бетонных и железобетонных конструкций, подвергаемых тепловой обработке, расход
цемента следует принимать с учетом назначаемых в проектах величин передаточной
и отпускной прочности бетона, но не более расхода для фактической прочности
бетона, превышающей проектную для классов бетона до B35 450 кг/м3, B40 - 500
кг/м3, B45 - 550 кг/м3.
Для бетонов классов
выше B45 расход цемента может быть выше 550 кг/м3, при этом должны быть
обеспечены требуемые параметры (предварительное натяжение арматуры, усадка,
ползучесть и другие характеристики, учитываемые расчетом).
И.16. В тоннельных
пропарочных камерах, не имеющих устройств для стабилизации температурного
режима греющей среды (изотермосмесителей или эжекторов-терморегуляторов),
необходимо постоянно контролировать распределение температуры паровоздушной
среды в трех точках каждого из двух сечений камеры на расстоянии до 2 м от
ворот и в среднем сечении. Точки замера температур должны находиться на высоте
0,8 м от пола камеры, в средней части и у потолка камеры.
Контроль за
температурой паровоздушной среды необходимо осуществлять в течение всего цикла
тепловой обработки через каждые 2 ч.
В пропарочных
камерах, оборудованных системой автоматизации и устройствами для стабилизации
температуры паровоздушной среды, такой контроль необходимо осуществлять в трех
точках по высоте камеры через каждые 10 циклов тепловой обработки.
И.17. Технические
требования, которые следует выполнять при тепловой обработке сборных
конструкций и проверять при операционном контроле, а также объем, методы или
способы контроля приведены в таблице И.1.