РЕКОМЕНДАЦИИ
ПО КОНТРОЛЮ КАЧЕСТВА КЛЕЕВЫХ СОЕДИНЕНИЙ
ДЕРЕВЯННЫХ КЛЕЕНЫХ КОНСТРУКЦИЙ
Рекомендовано к
изданию решением секции деревянных конструкций НТС ЦНИИСК им. Кучеренко.
Составлены к
нормативным документам по изготовлению деревянных клееных конструкций и
изделий.
Изложены общие
требования к проведению испытаний клеевых соединений конструкций, указаны
оборудование и аппаратура, необходимые для проведения испытаний; описаны методы
проверки качества древесины и клеевых соединений, методы определения прочности
клеевых соединений при различных напряженных состояниях: скалывании,
раскалывании, растяжении, изгибе и др.; некоторые специфичные виды испытаний
при оценке прочности соединений древесины с металлом, угловых соединений и др.;
методы оценки стойкости клеевых соединений к переменному действию влаги,
температуры и других эксплуатационных факторов.
Для работников
лабораторий производственных и научно-исследовательских организаций.
ПРЕДИСЛОВИЕ
Склеивание является
основным видом соединения древесины в строительных конструкциях и изделиях. От
качества клеевых соединений в значительной степени зависит работоспособность
конструкций, т.е. способность выполнять заданные функции в течение требуемого
периода эксплуатации.
Необходимое
качество клеевых соединений обеспечивается использованием соответствующих
материалов (древесины, клеев и др.) и соблюдением технологических режимов
изготовления клееных изделий. Составной частью технологического процесса
является контроль качества, который обычно включает три основных этапа:
контроль материалов, операционный контроль и контроль готовой продукции.
Одним из основных
показателей, характеризующих качество клеевых соединений, является прочность,
т.е. определение нагрузки, при которой разрушается образец при испытании, и
вычисление предела прочности при этой нагрузке, поэтому испытания прочности
соединений в общей системе контроля являются основными. Наряду с этим в ряде
случаев, например при изготовлении особенно ответственных конструкций, анализе
неудовлетворительных результатов контрольных испытаний, при аварийном состоянии
или разрушении конструкций во время эксплуатации, возникает необходимость в
дифференцированном подходе к оценке полученных прочностных показателей, при
котором наряду с контролем прочности клеевого соединения производят проверку
качества древесины и клеев, так как от их свойств в значительной степени
зависит прочность клеевого соединения. Такой подход позволяет выявить, что
является определяющим - прочность древесины или адгезионно-когезионная
прочность клея, зависящая как от свойств самого клея, так и от технологии
склеивания.
В связи с этим в
Рекомендациях описаны основные методы физико-механических испытаний древесины,
к числу которых относятся методы контроля прочности при различных видах
напряженного состояния (изгибе, растяжении, скалывании), оценки пороков,
проверки влажности и внутренних напряжений древесины.
Для оценки качества
клея в Рекомендациях описана методика контроля основных технологических свойств
(вязкости, жизнеспособности, времени отверждения).
Так как контроль
выполнения основных операций процесса изготовления клееных конструкций не имеет
прямого отношения к данным Рекомендациям и подробно описан в соответствующих
документах, в Рекомендациях перечислены только параметры, которые необходимо
контролировать.
В настоящее время
отсутствует какой-либо универсальный метод контроля прочности, при помощи
которого можно было бы полностью оценить качество клеевых соединений, поэтому
разработана довольно широкая гамма методов испытаний, позволяющих оценить
качество различных типов клеевых соединений при разном их напряженном
состоянии. Большая часть этих методов описана в Рекомендациях.
Следует отметить,
что для оценки прочности клеевых соединений не всегда используют схемы
испытаний, которые полностью моделируют напряженное состояние (например, сдвиг,
отрыв) в натурных конструкциях. Наибольшее внимание уделяют испытаниям клеевых
соединений на скалывание вдоль волокон древесины, так как это один из основных
видов напряженного состояния, возникающих в клееной древесине при приложении
внешней нагрузки. Исходя из этого, стандартный малый образец по ГОСТ 15613.1-77
принят не только для контроля кратковременной прочности при скалывании вдоль
волокон древесины, но и стойкости клеевых соединений.
Наряду с методами
определения кратковременной прочности клеевых соединений при различном
напряженном состоянии в Рекомендациях описаны методы контроля прочности
соединений, подвергнутых воздействиям, близким к реальным, т.е. тем, которые
воздействуют на клеевые соединения в процессе эксплуатации. Это дает
возможность оценивать, насколько изменяется начальная прочность, т.е.
прочность, достигнутая после завершения процесса склеивания, под воздействием
эксплуатационных факторов.
К сожалению, пока
еще недостаточно полно разработаны и исследованы методы контроля при совместном
воздействии на клеевые соединения статической или динамической нагрузок и
переменных температурно-влажностных факторов, поэтому в Рекомендациях описаны
только методики раздельной оценки прочности соединений под действием
статической нагрузки и при переменных температурно-влажностных воздействиях.
В процессе
изготовления клееных конструкций, а также их эксплуатации в клееной древесине
возникают внутренние напряжения, оказывающие непосредственное влияние на
прочность клеевых соединений, поэтому в Рекомендации включена методика
количественной оценки величины и распределения таких напряжений, хотя описанные
методы контроля пока еще нельзя считать оптимальными.
В Рекомендации
включены методы испытаний, на которые имеются ГОСТы, а также ряд нестандартных
методов, которые достаточно хорошо отработаны и используются на практике.
В Рекомендациях
систематизированы наиболее приемлемые методы контроля качества клеевых соединений
с указанием областей их использования.
В тех случаях,
когда методы контроля не являются основными и используются на практике
значительно реже, методика испытаний не описывается, а приводится лишь ссылка
на нормативный документ, где подробно описан этот метод.
Описанные в
Рекомендациях методы контроля могут применяться кроме контроля качества клееных
конструкций при исследовании новых видов клеев, нормировании их расчетных
характеристик, оценке технологических режимов склеивания и сопоставлении клеевых
соединений в клееных конструкциях различных видов.
Настоящие
Рекомендации составлены в развитие нормативных документов, регламентирующих
требования к изготовлению и контролю качества деревянных клееных конструкций.
Разработаны в
ЦНИИСК им. Кучеренко (д-р техн. наук Л.М. Ковальчук).
1. ОБЩИЕ
ПОЛОЖЕНИЯ
1.1. Рекомендации
распространяются на контроль качества клеевых соединений древесины,
используемых в деревянных несущих (арках, балках, фермах, рамах и др.) и
ограждающих (панелях стен и плитах покрытий) конструкциях и
столярно-строительных изделиях (оконных и дверных блоках, паркетных досках).
1.2. В
Рекомендациях описаны методы испытаний и оценки качества клеевых соединений и
используемых в них материалов; конкретные требования к качеству клеевых соединений
различных типов клееных конструкций и изделий содержатся в соответствующих
нормативных документах (ГОСТах; технических условиях и т.п.). Наряду с этим в
Рекомендациях приведены ориентировочные данные (Прил. 1) о величинах
контролируемых показателей и наиболее целесообразных случаях использования
описанных в Рекомендациях методов контроля.
1.3. Качество
клеевых соединений можно контролировать путем испытания специально
изготовленных образцов или образцов, вырезанных из клееных конструкций или их
элементов. Допускается вырезка образцов из неразрушенных частей клееных
элементов, оставшихся после других испытаний. В случае специального
изготовления образцов заготовки склеивают по технологии, установленной для
данного вида клееной продукции. Образцы следует изготавливать из древесины той
породы, из которой изготавливается клееная продукция.
В качестве
контрольных проводят испытания клееных элементов.
1.4. Основным
показателем, характеризующим качество клеевых соединений, является их
прочность, поэтому определение предела прочности клеевых соединений является
обязательным при оценке качества клееных изделий или их клеевых соединений.
Контроль качества
материалов (древесины, клеев) проводят только в отдельных случаях, например при
выполнении экспериментальных работ, методикой которых предусмотрена проверка
материалов, для расшифровки результатов испытаний клеевых соединений, когда не
ясно, что определяет прочность - древесина или клей, в некоторых спорных
случаях при оценке результатов контрольных испытаний и т.п. В этих же случаях
может потребоваться и оценка внутренних напряжений.
1.5. Для оценки
качества клеевых соединений и древесины можно использовать образцы трех видов:
малые, средние (промежуточные) и крупные, или клееные, элементы. Это деление
является довольно условным, так как четкую границу между размерами образцов
провести трудно.
Малые, как правило,
стандартные образцы имеют небольшую площадь разрушения при испытаниях
(например, при скалывании - 6 см2, растяжении - 0,8 см2 и т.п.),
изготавливаются из чистой (без видимых пороков) древесины. Их используют при
проведении научно-исследовательских работ, проверке адгезионно-когезионной
прочности клеев и т.п.
Для проведения
контроля качества непосредственно в производственных условиях с целью проверки
правильности осуществления заданных параметров процесса изготовления клеевых
изделий преимущественно используют средние (промежуточные) образцы, площадь
разрушения которых равна или приближается хотя бы в одном направлении
(например, по ширине сечения клееного элемента) к площади клеевых прослоек в
реальных конструкциях или изделиях.
Древесина средних
образцов может иметь пороки и дефекты, которые допускаются в клееных изделиях.
К числу крупных
образцов чаще всего относятся клееные многослойные элементы, моделирующие
клееные конструкции или их элементы. Эти образцы используют для контроля или
уточнения данных, полученных на малых или средних образцах.
1.6. При
комплексной оценке качества клееных изделий рекомендуется образцы различных
размеров и назначения вырезать из одного пакета. Примерная схема вырезки
образцов из прямолинейных клееных элементов показана на рис. 1.
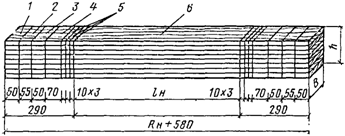
Рис. 1. Схема
вырезки образцов
из прямолинейных
клееных элементов
1 - отпад; 2 -
заготовки для малых образцов
(испытание на
скалывание); 3 - заготовки образцов
для испытаний на
послойное скалывание; 4 - образцы
для испытаний на
расслаивание; 5 - образцы
для исследования
внутренних напряжений;
6 - образец для
испытаний на изгиб
При вырезке малых
образцов одна из осей образца должна располагаться вдоль волокон древесины.
Годичные слои на торцовых поверхностях образцов должны быть параллельны одной
паре противоположных граней и перпендикулярны к другой. Между смежными гранями
образцов должны быть прямые углы.
Допустимые
отклонения от номинальных размеров рабочей части малых и средних образцов не
должны превышать +/- 0,5 мм. Любая величина, взятая в пределах допустимого
отклонения, должна быть выдержана по всему образцу с точностью до +/- 0,1 мм.
Размеры образца, не входящие в расчетные формулы (например, длина образца при
испытании зубчатых соединений на изгиб), должны быть выдержаны с точностью до 1
мм. Рабочие поверхности образцов должны быть чисто обработаны. Неровности
рабочих поверхностей образцов
не должны быть более 200 мкм по ГОСТ 7016-75.
Допустимые
отклонения от размеров и чистота обработки крупных образцов должны быть такими,
как у натурных конструкций или изделий.
1.7. Перед
испытаниями малые образцы необходимо кондиционировать при температуре 20 +/- 2
°C и относительной влажности воздуха 65 +/- 5% до приобретения древесиной
нормализованной влажности (т.е. влажности, равновесной среде с температурой 20
°C и относительной влажностью 65%) и хранить после кондиционирования до испытаний
в герметичной упаковке или сосудах, чтобы влажность образцов не изменялась.
Древесина средних и
крупных образцов должна иметь влажность, которая рекомендована для клееных
изделий, из которых они вырезаны.
Малые и средние
образцы следует испытывать, как правило, через 3 сут после склеивания, а
крупные - через 5 - 7 сут.
1.8. На каждый
образец должна быть нанесена маркировка, указывающая номер и характеристику
образца. Если образцы будут подвергаться влажностным воздействиям, маркировку
следует делать стойкой к увлажнению краской или другими подобными средствами.
1.9. Количество
образцов определяется целью испытаний и требуемой точностью контроля и обычно
указывается в нормативно-технической документации на клееные изделия или
методиках экспериментальных исследований.
Чаще всего
количество малых образцов должно быть не менее 20, средних - не менее 10,
крупных образцов или клееных элементов - не менее 3.
1.10. В помещении,
где проводят испытания, следует поддерживать температуру 20 +/- 2 °C и
влажность воздуха 65 +/- 5%. Допускается проводить непродолжительные испытания
в помещении с другой температурой и влажностью воздуха при условии их
проведения сразу же после кондиционирования образцов.
1.11. Для испытаний
малых и средних образцов используют универсальные машины по ГОСТ 7855-74 (с
погрешностью измерения не более 12% измеряемой нагрузки в диапазоне 200 - 2000
Н (20 - 200 кгс).
В зависимости от
типа и размера испытываемых образцов применяют соответствующие приспособления,
в которых закрепляются образцы, с помощью которых к образцам в машине
передается нагрузка. Конструкция приспособлений описана в соответствующих
разделах Рекомендаций.
Клееные элементы
конструкций испытывают на специальных стендах, оборудованных устройствами для
закрепления элементов и приложения нагрузки, конструируемыми в зависимости от
размеров и формы испытываемых элементов.
Для оценки
стойкости клеевых соединений к температурно-влажностным воздействиям необходимо
иметь:
сосуды из
нержавеющего металла или термостойкого стекла и электронагревательные приборы,
обеспечивающие постоянную температуру воды 20 +/- 2 °C при вымачивании и
охлаждении и 100 °C - при кипячении образцов;
сушильную камеру с
регулятором температуры и влажности для сушки образцов;
морозильную камеру
для замораживания образцов, обеспечивающую температуру до минус 30 +/- 3 °C;
термокамеры для
нагрева образцов, обеспечивающие температуру 60 +/- 3 °C;
стенды для выдержки
образцов в атмосферных условиях;
автоклав с
герметичной крышкой, снабженный манометром, насосами для создания давления и
вакуума при испытании образцов на расслаивание.
1.12. В зависимости
от конкретных видов испытаний требуются различные дополнительные приборы и
инструменты, например микроскоп, и приспособления для измерения внутренних
напряжений, вискозиметры, термометры и др. для контроля технологических свойств
клеев, щуп и лупа для контроля степени расслаивания образцов, влагомеры для
определения влажности древесины и др. Для измерения толщины и ширины заготовок
и образцов требуется инструмент с погрешностью не более 2%. Размеры рабочей
части образцов определяют с погрешностью не более 1%.
1.13. При
кратковременных испытаниях прочности малых и средних образцов древесины и
клеевых соединений образцы нагружают с постоянной скоростью роста напряжений
0,15 - 0,3 +/- (0,05 - 0,1) МПа/с, доводя образцы до разрушения. В стандартах
или другой нормативной документации для отдельных видов испытаний может быть
установлена другая скорость приложения нагрузки.
При испытании
крупных образцов и элементов конструкций нагрузку следует прилагать в течение 1
- 1,5 мин на каждом этапе нагружения.
1.14. Нагрузку
, при
которой произошло разрушение, определяют по максимальному отклонению стрелки
силоизмерителя машины с погрешностью не более цены деления шкалы. Предельное
значение шкалы не должно превышать нагрузку
более чем в 3 раза.
В качестве
показателя прочности принимают величину внешней разрушающей нагрузки при
регламентированной скорости нагружения. Отношение разрушающего усилия к
геометрическим характеристикам образца (площади испытываемого клеевого
соединения) характеризует его прочность (предел прочности).
Вычисление предела
прочности при различных видах испытаний производят с помощью соответствующих
формул, Па (МПа), с округлением до 0,1 МПа, принимая размерность входящих
величин в следующих единицах:
максимальная
(разрушающая) нагрузка - Н;
линейные размеры
образца (длина, ширина, толщина (высота) и т.п.) - м.
Предел прочности
определяют при влажности древесины в момент испытаний (меньше предела
гигроскопичности). В случае необходимости предел прочности приводят к влажности
12 или 15% с округлением до 1 МПа по формуле
,
где
- предел прочности при влажности древесины
12%;
- предел прочности при влажности, которую
имела древесина в момент испытаний;
- поправочный коэффициент на влажность, равный
для всех пород 0,04;
W - влажность
образца в момент испытаний, %.
1.15. При обработке
результатов испытаний должны быть вычислены:
среднее
арифметическое
, по
формуле, МПа,
,
где
- величина отдельного наблюдения;
n - количество
наблюдений;
среднее
квадратическое отклонение S по формуле
;
средняя ошибка
среднего арифметического по формуле
;
коэффициент
вариации V, по формуле, %
;
показатель точности
P для доверительной вероятности 0,95, по формуле, %
.
При анализе
результатов испытаний отдельные данные могут значительно отклоняться от
остальных и вызывать сомнение в их правильности. Эти данные следует
отбраковать, руководствуясь следующим:
находят среднее
арифметическое X без учета сомнительного значения D;
находят
вариационный размах R по формуле
,
где
и
- экспериментальные значения вариационного
ряда без учета сомнительного значения;
сомнительное
значение исключают при выходе его величины за пределы
.
Коэффициент z в
зависимости от численности совокупности определяется по табл. 1.
Таблица 1
────┬────┬───┬────┬─────┬───────┬────────┬───────┬───────┬───────┬─────────
n
│ 5 │ 6 │
7 │8 - 9│10 - 11│12 -
15 │16 - 22│23 - 25│26 - 63│64 - 150
────┼────┼───┼────┼─────┼───────┼────────┼───────┼───────┼───────┼─────────
z
│1,7 │1,6│1,5 │ 1,4 │ 1,3
│ 1,2 │
1,1 │ 1,0
│ 0,9 │
0,8
────┴────┴───┴────┴─────┴───────┴────────┴───────┴───────┴───────┴─────────
Если имеется
несколько единиц совокупности, величина которых вызывает сомнение, то значения
и R находят без них, а затем оценивают каждую
из них по приведенным выше правилам.
1.16. После
испытаний определяют влажность образцов. Пробой для определения влажности
является большая часть разрушенного образца.
Если средняя
влажность испытанных образцов определена по влажности нескольких образцов,
допускается вносить поправку на влажность в среднее арифметическое результатов
испытаний.
1.17. Результаты
испытаний заносят в протокол, в котором должна быть ссылка на стандарт или
другой документ, регламентирующий методику испытаний, характеристику образцов,
данные испытаний и др. Общая форма протокола определения предела прочности дана
в Прил. 2.
1.18. Учитывая, что
при определении прочности образцов и элементов конструкций происходит, как
правило, хрупкое разрушение, необходимо обращать особое внимание на соблюдение
правил техники безопасности, оговоренных в специальной литературе.
2. КОНТРОЛЬ
КАЧЕСТВА ДРЕВЕСИНЫ
Прочность
при статическом изгибе
2.1. Предел
прочности определяют путем испытаний малых образцов по ГОСТ 16483.3-73*,
средних - по ГОСТ 21554.2-76.
2.2. Малые образцы
изготавливают в форме прямоугольной призмы с поперечным сечением 20 x 20 мм и
длиной вдоль волокон 300 мм. Допускается определять предел прочности при
статическом изгибе на образцах после определения модуля упругости. Образцы
выбирают без пороков древесины.
Средние образцы
отличаются от пиломатериалов (досок) и заготовок, из которых они вырезаются,
только длиной, которая должна быть от 15 до 18 толщин в зависимости от
расстояния между центрами опор приспособления для испытания. За толщину
принимают размер по направлению приложения нагрузки. Для определения
минимальной прочности образцы выпиливают таким образом, чтобы сортообразующие
пороки были расположены на средней трети их длины. Допускается из одной доски
выпиливать несколько образцов.
2.3. Испытания
малых образцов проводят по схеме, изображенной на рис. 2, а, средних - по схеме
рис. 2, б. При испытаниях малые образцы помещают в машину радиальной
поверхностью кверху.
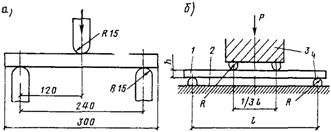
Рис. 2. Схема
испытаний образцов древесины
при статическом
изгибе
а - малых; б -
средних; 1 - образец; 2 - основание;
3 - нагружающий
нож; 4 - опоры
Для испытания
средних образцов расстояние между центрами нагружающих ножей должно быть равно
1/3 расстояния между центрами опор, а расстояние между центрами опор - не менее
12 и не более 15 толщин образца. При испытании средних образцов опоры и
нагружающие ножи должны быть высотой не менее двух толщин образца, длиной не
менее наибольшей ширины испытываемых образцов и с радиусом закругления, равным
1,5 - 2 толщинам образца.
Средние образцы
нагружают на пласть или кромку.
2.4. Предел
прочности при статическом изгибе
вычисляют для малых образцов по формуле
,
а для средних образцов - по формуле
,
где P - разрушающая
нагрузка;
l - расстояние
между центрами опор;
b - ширина образца;
h - высота образца.
Прочность
при продольном растяжении
2.5. Предел
прочности малых образцов определяют по ГОСТ 16483.23-73, а средних - по ГОСТ
21554.5-78.
2.6. Заготовки для
малых образцов следует выкалывать. Образцы изготавливают по форме и размерам,
указанным на рис. 3. Допускается применять образцы, состоящие из призмы
сечением 4 x 20 мм и длиной 350 мм и приклеенных к ее концам (по пласти)
боковых накладок толщиной 8 мм и формой по рис. 3. Прочность склеивания должна
быть не меньше прочности древесины при скалывании вдоль волокон.
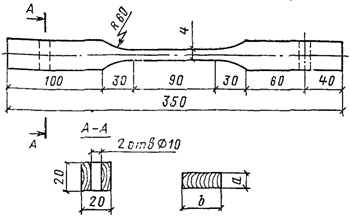
Рис. 3. Схема
изготовления и форма малых образцов
древесины при
испытании на продольное растяжение
Средние образцы
отличаются от пиломатериалов и заготовок, из которых они вырезаются, только
длиной. Общая длина образца должна быть такой, чтобы длина его рабочей части,
свободной от захватов, превышала ширину не менее чем в 8 раз.
Для определения
минимальной прочности образец выпиливают так, чтобы он включал наиболее слабое
сечение пиломатериала или заготовки. Это сечение должно быть расположено в
пределах зоны, распространяющейся на 1,5 ширины по обе стороны от центра
образца.
2.7. При испытании
малых образцов их помещают в захваты испытательной машины так, чтобы часть
каждой головки, граничащая с закруглением, оставалась свободной на протяжении
20 - 25 мм, а растягивающая нагрузка совпадала с продольной геометрической осью
образца.
Для зажима средних
образцов используют приспособление (рис. 4), состоящее из двух захватов,
соединенных с нагружающим механизмом машины и передающих усилие на образец с
помощью натяга, создаваемого клиновидными губками. Соприкасающиеся с образцом
поверхности губок должны иметь рифление и скос, постепенно уменьшающий давление
на образец от максимальной величины до нуля (рис. 5).
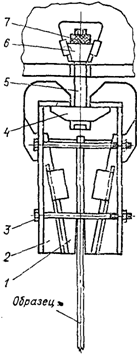
Рис. 4.
Приспособление для передачи
растягивающего
усилия на образец
1 - губка; 2 -
скоба; 3 - болт; 4 - основание;
5 - тяга; 6 -
сухарь; 7 - гайка
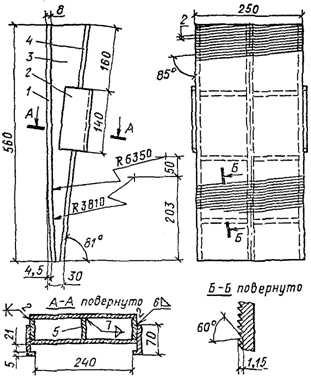
Рис. 5.
Клиновидная губка, используемая в захватах
при испытании на
растяжение
1, 4 - плиты; 2 -
направляющая; 3 - ребро; 5 - связь
При испытаниях
зажатый в захватах приспособления образец нагружают непрерывно до разрушения.
2.8. Предел
прочности каждого образца при растяжении вдоль волокон
вычисляют по формуле:
,
где P - разрушающая
нагрузка;
a - ширина образца;
b - толщина образца
(у малых образцов - размеры сечения рабочей части).
Прочность
при скалывании вдоль волокон
2.9. Предел
прочности малых образцов определяют по ГОСТ 16483.5-73*, а средних - по ГОСТ
21554.6-78.
2.10. Форма и
размеры малых образцов должны соответствовать указанным на рис. 6, а, а средних
- на рис. 6, б.
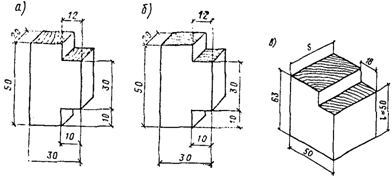
Рис. 6. Форма и
размеры образцов для испытаний
на скалывание вдоль
волокон древесины
а, б - малых со
скалыванием соответственно по тангентальной
и радиальной
плоскости; в - средних
Пороки,
увеличивающие сопротивление древесины скалыванию, и трещины, лежащие в плоскости
скалывания, в образцах не допускаются.
Испытание на
скалывание малых образцов проводят по тангентальной и радиальной плоскостям. В
средних образцах должны быть сохранены направление годовых слоев и типичный
наклон волокон тех пиломатериалов и заготовок, из которых они отобраны.
2.11. Испытания
проводят с помощью приспособлений, показанных на рис. 7, а для малых и на рис.
7, б - для средних образцов.
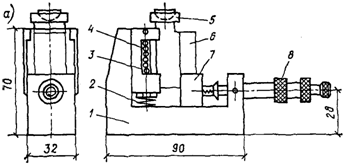
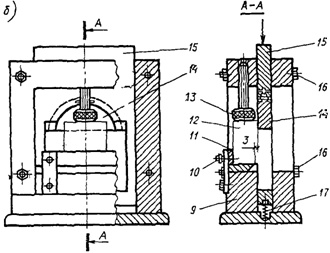
Рис. 7.
Приспособления для испытаний образцов
на скалывание вдоль
волокон древесины
а - малых; б -
средних; 1 - корпус; 2 - пружина;
3 - подвижная
планка; 4 - ролики; 5 - нажимная призма
с шаровой опорой; 6
- образец; 7 - подвижная опора;
8 - устройство для
прижима подвижной опоры; 9 - корпус;
10 - установочный
винт; 11 - поперечная планка;
12 - образец; 13 -
стопорный винт; 14 - самоцентрирующая
опора; 15 -
пуансон; 16 - болт; 17 - пружина
При испытании малых
образцов перемещением подвижной опоры обеспечивают прилегание опорных граней
образца к соответствующим поверхностям приспособления. Подвижная опора к
образцу должна прижиматься с силой, равной 5 - 9 Н (0,5 - 0,9 кгс).
При испытании
средних образцов (см. рис. 7, б) в приспособление устанавливают образец,
продвигая его через проем в пуансоне до соприкосновения с поперечной планкой,
положение которой регулируют установочным винтом так, чтобы между острым ребром
опорной поверхности приспособления и плоскостью ожидаемого скалывания образца
остался зазор 3 мм. Поворачивая опорный винт, обеспечивают плотное прилегание
головки винта к верхнему торцу образца. Образец с наклоном волокон
устанавливают в приспособлении так, чтобы исключить захват плоскостью
скалывания основной части образца. Закрепленный образец должен стоять в
приспособлении строго вертикально.
Приспособление с
закрепленными в нем малым или средним образцами помещают на нижнюю опорную
платформу испытательной машины таким образом, чтобы давление передавалось
сверху на пуансон приспособления.
2.12. Предел
прочности при скалывании вдоль волокон
вычисляют по формуле
,
где P -
максимальная нагрузка;
s - толщина образца
(для малых образцов ширина);
l - длина площадки
скалывания.
Плотность,
пороки и внутренние напряжения древесины
2.13. Плотность
древесины контролируют согласно требованиям ГОСТ 16483.1-73*, пороки и дефекты
древесины - по ГОСТ 2140-71, внутренние напряжения в древесине - по ГОСТ
11603-73.
Определение
влажности древесины
2.14. Влажность
определяют по ГОСТ 16483.7-71* и по ГОСТ 16588-71*. Последний ГОСТ относится к
контролю влажности пиломатериалов и заготовок.
2.15. Для
определения влажности пиломатериалов и заготовок, а также склеенных из них
средних и крупных образцов при влажности древесины до 25% с точностью до +/- 2%
используют электровлагомеры, например ЭВ-2К. Влажность измеряют в трех участках
на середине ширины каждой пласти заготовки. При длине образца менее 1 м
влажность можно замерять только на половине каждой пласти.
2.16. Для более
точного измерения влажности (+/- 0,5%) образцов, а также при влажности
древесины более 25% используют метод, основанный на сравнении массы влажных и
абсолютно сухих образцов. Для этой цели изготавливают образцы в форме
прямоугольной призмы с основанием 20 x 20 мм и высотой вдоль волокон 30 мм. При
определении влажности пиломатериалов и заготовок образцом является поперечный
срез размером вдоль волокон от 20 до 30 мм. При малом поперечном сечении берут
подряд несколько образцов так, чтобы их общая масса была от 10 до 50 г. Если
ширина заготовки более 150 мм, можно брать в качестве образца половину
поперечного среза. Образцы не должны иметь пороков древесины. Определение
влажности производят как до склеивания образцов, так и после проведения
испытаний.
Для определения
влажности образцы очищают от опилок и заусенцев, взвешивают с точностью до 0,01
г при массе до 50 г и с точностью до 0,1 г при большей массе и помещают в
сушильный шкаф. Если образцы невозможно взвесить сразу, то их необходимо
поместить в герметически закрытые сосуды, предварительно завернув каждый
образец в пленку из влагонепроницаемого материала.
Взвешенные образцы
высушивают при температуре 103 +/- 2 °C до абсолютно сухого состояния. Образцы
следует считать абсолютно сухими, когда разность массы между двумя последними
взвешиваниями будет не более 0,002 г у малых и 0,2 г - у средних образцов.
Влажность образцов
W вычисляют с точностью до 1% по формуле, %
,
где m - масса
образца до высушивания, г;
- масса образца после высушивания, г.
3. КОНТРОЛЬ
КАЧЕСТВА КЛЕЕВ
3.1. Качество клея
характеризуется его вязкостью, жизнеспособностью и продолжительностью
отверждения. Для определения этих показателей, согласно ГОСТ 20501-75,
приготовляют клей массой не менее 0,2 кг. После введения отвердителя клеевую
массу тщательно перемешивают и доводят до температуры 20 +/- 1 °C.
3.2. Вязкость клеев
определяют вискозиметрами ВЗ-4 и ВЗ-1 в соответствии с ГОСТ 9070-75.
Измерение вязкости
производят следующим образом. Тщательно перемешанный клей доводят до
температуры 20 +/- 1 °C. Перед замером вязкости вискозиметр при помощи
регулирующих винтов устанавливают в горизонтальном положении. Особое внимание
следует обратить на чистоту сопла. При работе на вискозиметре ВЗ-4 в качестве
приемника под сопло вискозиметра ставят стеклянный сосуд емкостью 150 мл, а при
работе на вискозиметре ВЗ-1 - мерную мензурку на 100 мл. Отверстие сопла
вискозиметра ВЗ-4 снизу закрывают и в воронку наливают до краев клей. Избыток
клея снимают стеклянной палочкой.
Для замера вязкости
открывают отверстие сопла вискозиметра. В момент появления капли клея из сопла
вискозиметра включают секундомер. При работе на вискозиметре ВЗ-4 секундомер
выключают после истечения всего клея из вискозиметра, а на вискозиметре ВЗ-1 -
после наполнения мензурки клеем на 50 мл. Определение вязкости проводят три
раза. Среднее время, с, является показателем условной вязкости.
3.3. Условное время
отверждения клеев, предназначенных для склеивания с нагревом, определяют
следующим образом (ГОСТ 20501-75). В пробирку диаметром 16 +/- 1 мм по ГОСТ
10515-75 помещают 2 г клея, зажимают ее между губками лапкодержателя и
погружают в кипящую воду так, чтобы уровень клея в пробирке был на 10 - 20 мм
ниже уровня воды. Одновременно с погружением пробирки в кипящую воду включают
секундомер. Клей непрерывно перемешивают стеклянной палочкой до начала его
гелеобразования. Результатом является среднее из трех измерений.
Для оценки времени
отверждения клеев, предназначенных для склеивания без нагрева, на
полиэтиленовую, целлофановую или другую пленку наливают слой клея толщиной 0,5
- 1 мм и выдерживают его при тех же температурно-влажностных условиях, при
которых осуществляют склеивание изделий. Среднее время, через которое
происходит хрупкий излом трех отливок при изгибе их на 90°, характеризует
условное время отверждения клея.
3.4. Для
определения жизнеспособности в стеклянный или фарфоровый стакан помещают 0,2 кг
свежеприготовленного клея, включают секундомер и выдерживают при температуре 20
+/- 1 °C. Рабочую жизнеспособность клея определяют временем, прошедшим с
момента приготовления клея до приобретения им максимально допустимой вязкости.
Полная
жизнеспособность выражается временем, прошедшим с момента введения отвердителя
до начала гелеобразования.
4. КОНТРОЛЬ
ТЕХНОЛОГИЧЕСКИХ ПАРАМЕТРОВ ПРОЦЕССА СКЛЕИВАНИЯ
4.1. Качество
механической обработки поверхности контролируют в соответствии с ГОСТ 7016-75.
Оно характеризуется высотой неровностей подлежащих склеиванию поверхностей.
4.2. Расход клея на
единицу склеиваемой поверхности, кг/м2, определяют путем взвешивания заготовок
длиной 1 м или прикрепленной к их поверхности бумаги, картона и т.п. до и после
нанесения клея. Разность массы соответствует удельному расходу клея.
4.3. Равномерность
нанесения клея на склеиваемые поверхности контролируется визуально.
4.4.
Продолжительность сборочно-запрессовочных операций, т.е. время с момента
нанесения свежеприготовленного клея до окончания запрессовки, при температуре и
влажности воздуха в цехе в момент склеивания определяют в ч.
4.5. Величину и
равномерность приложения давления контролируют при помощи динамометров,
манометров и других приборов в зависимости от конструкции запрессовочных
устройств.
4.6. Продолжительность
склеивания при данной температуре и влажности определяют в ч как время с
момента окончания запрессовки до распрессовки, т.е. снятия запрессовочного
давления.
5. КОНТРОЛЬ
КРАТКОВРЕМЕННОЙ ПРОЧНОСТИ КЛЕЕВЫХ СОЕДИНЕНИЙ
Прочность
пластевых и кромочных клеевых соединений
при скалывании
вдоль волокон древесины
5.1. Испытания
малых образцов проводят по ГОСТ 15613.1-77, а средних - по изложенной ниже
методике.
5.2. Малые образцы
вырезают из заготовок, имеющих вид прямоугольной призмы (рис. 8). Пороки,
увеличивающие сопротивление скалыванию, и трещины, лежащие в плоскости
скалывания, в образцах не допускаются.
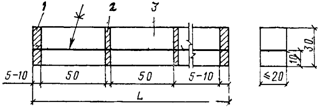
Рис. 8. Заготовка
для вырезки образцов на скалывание
вдоль волокон
древесины
1 - припуск; 2 -
пропил; 3 - заготовка для образца
Средние образцы для
испытаний на послойное скалывание вырезают из торцовых частей клееных элементов
во время их торцовки и доведения до проектных размеров. Заготовка имеет форму
пластины, ширина и высота которой соответствуют размерам поперечного сечения
элемента или части его; толщина заготовки равна 50 мм (вдоль волокон
древесины). Заготовку разрезают на прямоугольные призмы, которые и являются
образцами.
5.3. Малый образец
для испытаний на скалывание показан на рис. 9, а. Образец на послойное
скалывание представляет собой прямоугольную призму с основанием, равным 50 x 50
мм, и высотой, равной высоте заготовки или ее части (рис. 9, б). Усредненные
данные о размерах сечения устанавливают по результатам трех его измерений
(соответственно в середине и на концах). В местах измерения размеров определяют
влажность.

Рис. 9. Образцы для
испытаний на определение прочности
клеевых соединений
при скалывании вдоль волокон древесины
а - малый; б -
средний для испытаний на послойное
скалывание: 1 -
древесина; 2 - клеевые прослойки
5.4. При испытании
малые образцы устанавливают в приспособление, показанное на рис. 7, а.
Перемещением подвижной опоры обеспечивают прилегание опорных граней образца к
соответствующим поверхностям приспособления. Нагрузку на образец передают через
нажимную призму с шаровой опорой.
Испытания средних
образцов на послойное скалывание осуществляют в приспособлении, показанном на
рис. 10.
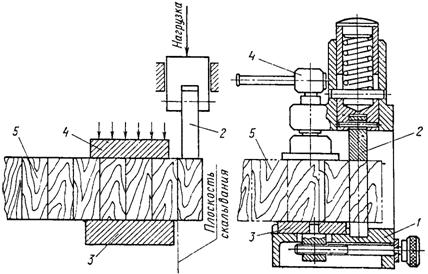
Рис. 10.
Приспособление для испытаний клеевых соединений
на послойное
скалывание
1 - основание
приспособления; 2 - пуансон; 3 - опора;
4 - прижимной винт;
5 - образец
Приспособление
устанавливают на нижнюю опорную плиту пресса. Образец помещают в проем
приспособления таким образом, чтобы направление волокон древесины совпадало с
направлением приложения нагрузки. При помощи прижима образец закрепляют в таком
положении, чтобы испытуемое сечение образца было расположено в одной плоскости
с задней по ходу подачи образца гранью пуансона. Затем при вертикальном
перемещении пуансона образец доводят до разрушения.
Цикл испытаний
повторяют для каждого следующего сечения после соответствующего перемещения и
закрепления образца.
5.5. Предел
прочности клеевого соединения при скалывании вдоль волокон
вычисляют по формуле
,
где
- максимальная (разрушающая) нагрузка;
l - длина площади
скалывания образца;
b - ширина.
Прочность
клеевого соединения при раскалывании
5.6. Предел
прочности при двустороннем раскалывании определяют по ГОСТ 15613.2-77.
5.7. Заготовку для
образцов изготавливают в виде прямоугольной призмы с клеевой прослойкой
посередине ширины заготовки, которая равна 40 мм. Толщина должна быть равна
толщине склеиваемых элементов, но не более 20 мм. Длина заготовки принимается в
зависимости от необходимого количества образцов. Форма и размеры образца, мм,
должны соответствовать указанным на рис. 11, а. Длина площади раскалывания
образца l должна быть 20 мм, ширина b - не более 20 мм. Дно пропилов должно
быть закруглено. Размеры площади раскалывания уточняют после разрушения
образца.
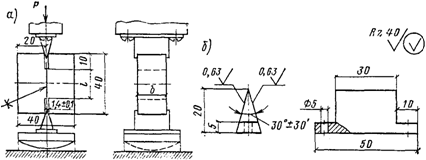
Рис. 11.
Испытание прочности клеевых соединений
при раскалывании
а - форма, размеры
образца, приспособление
для испытаний; б -
клинья
5.8. Образец
устанавливают в приспособление для испытания, как показано на рис. 11, б, между
двумя клиньями, острые углы которых входят в пропилы образца. Верхний клин
крепят жестко к верхней траверсе, а нижний устанавливают свободно на шарнирную
опору. На клинья наносят смазку по ГОСТ 1033-73.
Клинья (рис. 11, б)
изготавливают из стали марки 40 по ГОСТ 1050-74*.
Образец нагружают с
постоянной скоростью до разрушения.
5.9. Предел
прочности клеевого соединения при раскалывании
вычисляют по формуле
,
где
- максимальная нагрузка;
l - длина площади
раскалывания;
b - ширина.
Прочность
зубчатых и торцовых клеевых соединений
при растяжении
вдоль волокон древесины
5.10. Испытания
малых образцов для контроля торцовых соединений производят по ГОСТ 15613.3-77,
зубчатых - по ГОСТ 15613.5-79. Испытания средних образцов можно производить по
методике ГОСТ 21554.5-78 на испытание пиломатериалов на растяжение.
5.11. Заготовку для
образцов выпиливают из готовой продукции в форме прямоугольного бруска с
клеевым соединением посередине заготовки. Длина заготовки для испытания
торцовых соединений l = 250 мм, зубчатых - 300 мм. Толщина s и ширина b
заготовки должны соответствовать толщине и ширине испытываемой клееной
продукции или приниматься в зависимости от необходимого количества образцов.
Заготовка и схема раскроя ее на образцы указаны на рис. 12, а, а образец с
зубчатым клеевым соединением - на рис. 12, б.
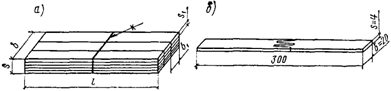
Рис. 12.
Определение прочности клеевых соединений
при растяжении
вдоль волокон древесины
а - схема раскроя
образцов; б - образец
с зубчатым клеевым
соединением
Толщина образца
равна 4 мм, ширина
- 20 мм. Образец с зубчатым соединением должен
включать не менее одного полного шипа. При включении нескольких шипов
расположение их в образце должно быть симметричным относительно продольной оси
образца.
5.12. Образец при
испытаниях устанавливают в захваты машины (рис. 13) так, чтобы рабочая часть
образца была не менее 120 мм.
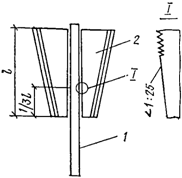
Рис. 13.
Приспособление для испытаний клеевых соединений
на растяжение вдоль
волокон древесины
1 - образец; 2 -
щечка захвата
5.13. Предел
прочности торцового или зубчатого соединения при растяжении вычисляют по
формуле
,
где
- максимальная нагрузка;
- ширина образца;
- толщина образца.
Прочность
зубчатых клеевых соединений
при статическом
изгибе
5.14. Предел
прочности определяют по ГОСТ 15613.4-78.
5.15. Малые образцы
имеют форму прямоугольной призмы с основанием 20 x 20, длиной 300 мм и зубчатым
клеевым соединением посередине длины. Древесина образцов должна быть без
видимых пороков и дефектов склеивания. Расположение шипов в образце по ширине
соединения должно быть симметричным относительно продольной оси образца и
одинаковым для всех испытываемых образцов.
Длина средних
образцов должна быть не менее 15 толщин. За толщину образца h принимают размер
по направлению приложения нагрузки. Средняя (рабочая с зубчатым соединением)
часть длины образца размером не менее 6h должна быть свободной от видимых
пороков древесины и дефектов склеивания.
Образцы должны
иметь сечение по толщине и ширине, равное полному сечению испытываемой клееной
продукции. Если оборудование не позволяет испытывать образцы полного сечения,
допускается испытание образцов уменьшенного сечения.
При испытании
нагружением на пласть клееную продукцию распиливают на несколько образцов
равной ширины, каждый из которых испытывают.
При испытании на
кромку из клееной продукции выпиливают образцы толщиной не менее одной трети
ширины испытываемой продукции. При этом если толщина образца составляет
половину или более ширины испытываемой клееной продукции, то испытывают один
образец от сечения. Если толщина образца менее половины ширины испытываемой
клееной продукции, то вырезают по одному образцу из обеих половин сечения.
Каждый образец, испытываемый на кромку, должен включать кромку первоначального
поперечного сечения испытываемой клееной продукции. При испытании эту кромку
размещают в растянутую зону (на опорах).
5.16. Испытания средних
образцов осуществляют в приспособлении, состоящем из основания с опорами и двух
нагружающих ножей (рис. 14). Опоры и нагружающие ножи должны быть высотой не
менее двух толщин h образца. Нагружающие ножи должны иметь радиус закругления
R, равный 1,5 - 4h. Опоры должны состоять из плоских стальных площадок толщиной
не менее 0,006h и шириной 0,85 - 1h, свободно поворачивающихся на осях или
катках. Длина ножей и опорных площадок должна быть не менее максимальной ширины
испытываемых образцов.
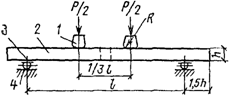
Рис. 14.
Приспособление для испытаний средних образцов
зубчатых клеевых
соединений при статическом изгибе
1 - нагружающий
нож; 2 - образец; 3 - стальная площадка;
4 - ось (каток)
Расстояние между
центрами опор l устанавливают в зависимости от толщины образца (12 - 15h).
Расстояние между центрами нагружающих ножей должно быть равно 1/3 расстояния
между центрами опор.
Испытания малых
образцов проводят по приведенной выше схеме при вертикальном расположении
шипов. Испытания средних образцов осуществляют с приложением нагрузки на пласть
или кромку, что указывается в нормативно-технической документации на
испытываемую клееную продукцию.
5.17. Предел
прочности
вычисляют по формуле
,
где
- максимальная разрушающая нагрузка;
l - расстояние
между центрами опор;
b - ширина образца;
h - толщина
образца.
За результат
испытания одного соединения при нагружении на пласть принимают среднее
арифметическое значение предела прочности всех испытанных образцов, вырезанных
из этого соединения.
За результат
испытания одного соединения при нагружении на кромку при двух испытанных
образцах, вырезанных из этого соединения, принимают меньшее значение предела
прочности.
При вычислении
предела прочности каждого образца учитывают большее значение влажности одной из
его половин.
При отклонении
влажности древесины образца от нормативной более чем на 2% результаты испытаний
должны быть пересчитаны.
Результаты
испытаний образцов, разрушившихся за пределами рабочей части по допустимым
порокам и дефектам на концах образца, не учитывают.
Прочность
клеевого соединения при отрыве
поперек волокон
древесины
5.18. Этот вид
испытаний преимущественно используют при контроле прочности склеивания
паркетных досок. Методика испытаний регламентируется ГОСТ 862.3-77.
5.19. Для испытаний
из заготовок паркетных досок вырезают образцы, форма и размеры которых указаны
на рис. 15, а. Пропилы в образцах делают на глубину, равную толщине паркетной
планки.
а)
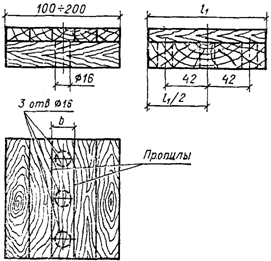
б)
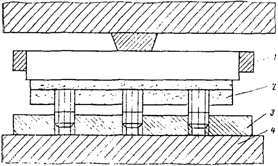
Рис. 15. Испытание
клеевых соединений на отрыв
а - форма и размеры
образца; б - приспособление
для испытаний; 1 -
опорная планка; 2 - образец
для испытаний; 3 -
вилка; 4 - опорная площадка
испытательной
машины
5.20. Испытания
проводят в приспособлении, показанном на рис. 15, б. Приспособление с образцом
помещают на опорную площадку испытательной машины и производят перемещение
нагружающей головки до разрушения образца.
5.21. Предел
прочности клеевого соединения при отрыве определяют по формуле
,
- разрушающая нагрузка;
l - длина образца;
b - ширина площади
отрыва;
d - диаметр
отверстия, равный 1,6 см.
Прочность
угловых клеевых соединений
5.22. Определение
прочности угловых соединений производят при сжатии уголков, каждая сторона
которых равна 250 мм.
5.23. В процессе
испытаний уголки центрируют в шарнирном приспособлении и подвергают сжатию по
схеме, указанной на рис. 16. Если испытательные машины снабжены шарнирными
опорами, то эти опоры могут быть использованы вместо указанных на схеме.
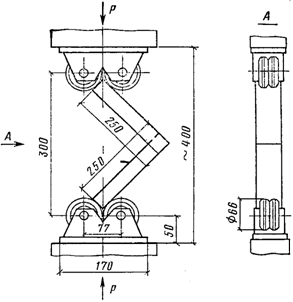
Рис. 16. Схема
испытаний прочности
угловых клеевых
соединений
5.24. Предел
прочности клеевого соединения вычисляют по формуле
,
где
- максимальная нагрузка при разрушении
образца;
F - площадь сечения
уголков.
Прочность
склеивания металлических штырей с древесиной
5.25. Контроль
качества склеивания металлических штырей с древесиной осуществляют путем
механических испытаний образцов на сдвиг при сжатии. Образцы изготавливают
специально или вырезают из клееных элементов конструкций с вклеенными штырями.
Размеры образца для испытаний показаны на рис. 17, а.
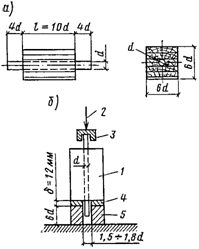
Рис. 17.
Испытание прочности склеивания
металлических
штырей с древесиной
а - образец; б -
схема испытаний: 1 - древесина;
2 - приложенное
сжимающее усилие; 3 - металлический шарнир;
4 - металлическая
прокладка; 5 - металлическая опора
Испытанию подлежат
5 параллельных образцов. Испытания проводят не ранее чем через 7 сут с момента
склеивания.
5.26. Испытания
образцов проводят в соответствии со схемой, приведенной на рис. 17, б.
Образец в прессе
необходимо устанавливать строго вертикально; вертикальная ось образца должна
совпадать с центральной вертикальной осью пресса.
5.27. Предел
прочности соединений определяют по формуле
,
где P - разрушающая
нагрузка;
l - длина заделки;
d - диаметр
арматуры.
6. КОНТРОЛЬ
КРАТКОВРЕМЕННОЙ ПРОЧНОСТИ КРУПНЫХ
КЛЕЕНЫХ ОБРАЗЦОВ И
ЭЛЕМЕНТОВ КОНСТРУКЦИЙ
6.1. При проведении
комплексных исследований клееных конструкций наряду с испытаниями малых и
средних образцов проводят испытания до разрушения крупных образцов и клееных
элементов конструкций.
Испытываемые
образцы и элементы могут быть прямолинейного (балки, элементы ферм),
криволинейного (гнутоклееные полурамы, арки кругового или стрельчатого
очертания) или ломаного (полурамы с зубчатым стыком, полурамы с фанерными
накладками) очертания. Иногда клееные образцы и элементы конструкций (например,
балки) по размерам и форме совпадают.
6.2. Для контроля
качества склеивания наиболее часто используют испытания прямолинейных элементов
в виде балок. Рекомендуются следующие размеры балок, мм (табл. 2).
Таблица 2
────────────────────────────┬───────────┬─────────────────────────
Образцы │ Длина
│ Сечение
│ ├────────────┬────────────
│ │ высота
│ ширина
────────────────────────────┼───────────┼────────────┼────────────
Модельные
балки │ 2200
│ 160 │
120
Элементы
конструкций │ 9000
│ 480 │
140
Эти рекомендации не
исключают возможности использования для испытаний балок других размеров, если
обоснована такая необходимость.
6.3. Крупные
образцы в виде модельных балок чаще всего загружают по схеме, указанной на рис.
18, а, а балки натурных размеров - по схеме рис. 18, б. Обе схемы позволяют
обнаруживать при испытании дефектные места как в зонах наибольших скалывающих
напряжений (например, в пластевых клеевых соединениях), так и нормальных
напряжений (например, в зубчатых соединениях).
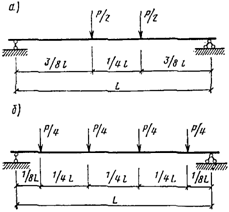
Рис. 18. Схема
испытаний балок
а - модельных; б -
натурных
Для контроля
качества криволинейных конструкций могут быть использованы схемы приложения
нагрузки, указанные на рис. 19, а.
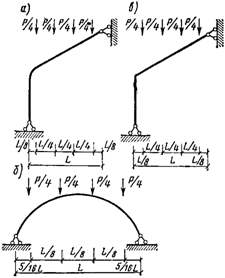
Рис. 19.
Контроль качества гнутоклееных конструкций
а - гнутоклеевых
рам; б - рам с прямолинейных элементов;
в - криволинейных
арок
6.4. Нагрузку в
процессе испытаний прикладывают ступенями. Величина ступени нагружения
принимается равной 10% величины контрольной нагрузки, которую определяют исходя
из условия, что в наиболее напряженном сечении испытываемой по заданной схеме
конструкции возникают напряжения, равные удвоенному расчетному сопротивлению.
6.5. Испытания
клееных элементов производят на испытательных машинах (прессах) или на
специальных стендах, оборудованных системами передачи нагрузки (рычаги, блоки)
или силовозбудителем (гидравлические домкраты).
При отсутствии
специального испытательного оборудования нагружение можно производить с помощью
тарированных штучных грузов (металлических блоков, кирпича, бетонных кубов и
т.п.), а также с помощью воды, заполняющей специальные металлические баки.
На рис. 19, в
показано загружение элементов конструкций при помощи гидродомкратов или грузов.
6.6. Передачу
нагрузки от одного силовозбудителя на две или четыре точки элементов
конструкции осуществляют с использованием траверс с опорными призмами и
катками, образующих статически определимую систему. Нагрузку от рычага
рекомендуется передавать не более чем на две точки, а от домкрата или машины -
не более чем на четыре точки. При большом числе точек приложения нагрузки
требуется установка нескольких рычагов или домкратов.
При применении
нескольких параллельных домкратов их силовые параметры должны быть по
возможности одинаковыми, а питание их должно производиться от одного насоса.
Распределительные траверсы не должны препятствовать деформациям испытываемых
элементов конструкций.
Площадь контакта
элементов конструкций с жесткими прокладками, через которые передается нагрузка
на испытываемый элемент, должна быть такой, чтобы при ожидаемой разрушающей
нагрузке напряжения смятия не превышали расчетного сопротивления древесины
местному смятию поперек волокон.
При испытании по
балочной схеме должно быть устранено возникновение распора, для чего одну из
опор выполняют подвижной в виде стального катка диаметром 50 - 80 мм,
уложенного между двумя жесткими металлическими пластинами или в виде ножевой
опоры на двух катках диаметром 50 - 80 мм. Применение подвижных опор, смещение
которых вызывает трение скольжения, не допускается. Площадка катания катков
должна быть выверена по уровню и оставаться горизонтальной во все время
испытаний.
Неподвижные опоры
должны допускать возможность свободного поворота концов элементов; такие опоры
выполняют в виде стального катка, приваренного к жесткой опорной пластине, или
в виде ножевой опоры.
Элементы
конструкций можно испытывать в вертикальном положении (внешние силы действуют
вертикально) или в горизонтальном положении (внешние силы действуют
горизонтально).
6.7. Элементы
конструкций при испытании должны быть раскреплены, чтобы не допустить в ходе
нагружения потери устойчивости из их плоскости. При необходимости замера
деформаций или перемещений во время испытаний отсчеты по приборам производят
после выдержки элементов под нагрузкой перед началом следующего этапа
нагружения. Нагрузку прикладывают равномерно одинаковыми ступенями в равные
промежутки времени.
Испытываемый
клееный элемент выдерживают после нагружения каждой ступени нагрузки одинаковое
время, превышающее время приложения нагрузки в 3 - 5 раз. Время выдержки на
каждой ступени загружения контролируют по секундомеру. Обычно оно должно быть в
пределах 5 мин.
Во время выдержки
осматривают поверхности элементов конструкции с целью фиксации появившихся на
данной ступени нагрузки трещин, смятия древесины и других признаков разрушения,
соблюдая при этом необходимые правила техники безопасности.
Во время испытаний
нагружение конструкции производят до разрушения.
6.8. За разрушающую
следует принимать нагрузку, достижение которой сопровождается хотя бы одним из
следующих признаков в элементе:
при фиксированной
(неизменной) нагрузке развиваются незатухающие перемещения (прогибы) или
деформации;
отмечается резкое
падение нагрузки даже без видимых признаков нарушения целостности элемента.
При испытании
обязательно фиксируется также время выдержки конструкции под последней ступенью
загружения (с момента приложения нагрузки до момента разрушения).
После разрушения
клееных элементов и снятия нагрузки производят их обследование для выявления
причин разрушения. При обследовании фиксируются очаги разрушения (скалывание на
опоре, сучок в растянутой зоне, непроклеенные места, трещины по древесине, по
клею и пр.).
6.9. Для оценки
качества клеевых соединений в клееных элементах или эксплуатируемых
конструкциях без их разрушения можно использовать разработанный Н.А. Гончаровым
экспресс-метод.
Для контроля
качества клеевых соединений этим методом перпендикулярно клеевым прослойкам
цилиндрической пилкой выпиливают образец диаметром 24 +/- 1 мм, как показано на
рис. 20. На полученном цилиндрическом образце слои древесины клееного элемента
нумеруют нечетными числами [1, 3, 5, (2n + 1)], а клеевые прослойки - четными.
Испытание образца производят раскалыванием вдоль волокон последовательно по
слоям древесины и клеевым прослойкам клином с углом заострения 45°, как
показано на рис. 20.
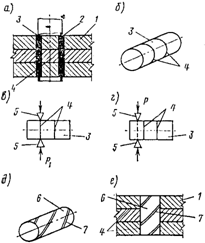
Рис. 20. Контроль
клеевых соединений
в готовых
конструкциях без разрушения
а - схема
выпиливания образца; б, в, г - образец
и схема испытаний;
д, е - заделка полученного от испытания
отверстия в
испытываемом элементе; 1 - клееная конструкция;
2 - цилиндрическая
пилка; 3 - цилиндрический образец;
4 - клеевые
прослойки; 5 - клинья; 6 - пробка из древесины
твердых пород; 7 -
канавка для клея
Качество клеевого
соединения оценивается условным коэффициентом, вычисленным по формуле
,
где
- усилие раскалывания по клеевому соединению;
и
- усилия раскалывания по древесине в смежных
слоях к клеевому соединению;
n - номер слоя
древесины.
Качество соединения
считается удовлетворительным, если коэффициент качества больше единицы, плохим
- меньше единицы. После взятия образца в отверстие в контролируемом клееном
элементе забивают с натягом 1 - 0,3 мм пробку из древесины березы влажностью
8%, смазанную клеем холодного отверждения.
7. КОНТРОЛЬ
СТОЙКОСТИ КЛЕЕВЫХ СОЕДИНЕНИЙ
К
ТЕМПЕРАТУРНО-ВЛАЖНОСТНЫМ ВОЗДЕЙСТВИЯМ
7.1. Стойкость
клеевых соединений оценивают, как правило, путем постоянного или переменного
воздействия температурно-влажностных факторов (кроме нагрузки) на малые
стандартные образцы по ГОСТ 15613.1-77 и периодической проверки их прочности
путем скалывания вдоль волокон древесины.
Методы оценки
стойкости основаны на определении относительного показателя прочности клеевых
соединений при испытании образцов на скалывание вдоль волокон. Стойкость
клеевых соединений к температурно-влажностным воздействиям характеризуется
отношением прочности образцов, подвергнутых указанным воздействиям, к прочности
контрольных образцов.
Образцы можно
подвергать температурно-влажностным воздействиям не ранее чем через 15 сут
после склеивания и выдержки их при температуре не ниже 16 °C.
Водостойкость
клеевых соединений
7.2. Водостойкость
определяют по ГОСТ 17005-71.
7.3. Из каждой
заготовки должно быть изготовлено не менее чем по 8 образцов для каждого вида
испытаний (контрольных, мокрых и высушенных после вымачивания, а также мокрых и
высушенных после кипячения).
7.4. Влагообработку
образцов производят путем вымачивания или кипячения в воде.
Образцы помещают в
сосуд с водой таким образом, чтобы они не соприкасались между собой и со
стенками сосуда и были покрыты водой на 2 - 3 см. Вымачивание образцов
производят в течение 48 ч в воде с температурой 20 +/- 2 °C. По истечении этого
времени образцы извлекают из воды, осушают чистой сухой тканью или
фильтровальной бумагой и одну половину их подвергают испытанию в мокром виде,
другую высушивают при нормальном температурно-влажностном режиме до достижения
влажности контрольных образцов, а затем испытывают.
Кипячение образцов
в воде производят в течение 3 ч. После кипячения образцы охлаждают в течение 30
мин в проточной воде, имеющей температуру 20 +/- 2 °C.
Охлажденные образцы
извлекают из сосуда, осушают и одну половину их подвергают обмеру и испытанию в
мокром виде, другую высушивают при нормальном температурно-влажностном режиме
до достижения влажности контрольных образцов, а затем испытывают.
7.5. Вначале
проводят испытания контрольных (без влагообработки) образцов. Затем испытывают
мокрые и высушенные после вымачивания образцы.
Если относительная
прочность клеевых соединений мокрых
или высушенных после вымачивания
образцов не достигает значения, указанного в
табл. 3 для малой группы водостойкости, дальнейшие испытания не проводят.
Таблица 3
──────────────────┬────────────────────────────────────────────────────────
Группа │ Относительная прочность клеевых
соединений, %
водостойкости
├────────────────────────────┬───────────────────────────
│ после вымачивания │ после кипячения
├─────────────┬──────────────┼─────────────┬─────────────
│ мокрых
│ высушенных │
мокрых │ высушенных
├─────────────┼──────────────┼─────────────┼─────────────
│ A
│ A │ A
│ A
│ 1
│ 2 │ 3
│ 4
──────────────────┼─────────────┼──────────────┼─────────────┼─────────────
Малая │ До 60
│ До 70 │ -
│ -
Средняя │ Более 60
│ Более 70 │
До 60 │ До 90
Повышенная │
Более 60 │ Более 90
│ Более 60 │
Более 90
Если относительная
прочность клеевых соединений после вымачивания выше указанной в табл. 3 для
группы малой водостойкости, то производят дальнейшие испытания образцов,
подвергнутых кипячению.
7.6. Подсчет
относительной прочности клеевых соединений мокрых
и высушенных
после вымачивания, а также охлажденных мокрых
и высушенных после кипячения
образцов производят по формулам:
;
;
;
,
где
- среднее арифметическое результатов испытаний
контрольных (без влагообработки) образцов;
- среднее арифметическое результатов испытаний
мокрых образцов после вымачивания;
- среднее арифметическое результатов
испытаний, высушенных после вымачивания образцов;
- среднее арифметическое результатов
испытаний, высушенных после кипячения образцов.
Результаты подсчета
относительной прочности клеевых соединений записывают в журнал (Прил. 3а).
7.7. В зависимости
от степени водостойкости клеевые соединения подразделяют на три группы: малую,
среднюю, повышенную.
Группу
водостойкости клеевых соединений в зависимости от относительной прочности их,
выраженной в процентах, определяют по табл. 3.
Группа
водостойкости клеевых соединений устанавливается по более низким показателям
относительной прочности.
Стойкость к
цикличным температурно-влажностным воздействиям
7.8. Оценку
стойкости производят по ГОСТ 17580-72.
7.9. Испытание
клеевых соединений на температурно-влажностные воздействия проводят циклами.
Механические
испытания образцов проводят после 40 циклов температурно-влажностных
воздействий. В исследовательской работе прочность проверяют после 6, 12, 24,
40, 60 и 100 циклов.
7.10. Один цикл
температурно-влажностных воздействий на образцы включает в себя следующее:
вымачивание
образцов в течение 20 ч в воде, имеющей температуру 20 +/- 2 °C;
выдержка мокрых
образцов в течение 6 ч при температуре минус 20 +/- 2 °C;
оттаивание образцов
в течение 16 ч при температуре воздуха 20 +/- 2 °C;
сушка образцов в
течение 6 ч при температуре 60 +/- 5 °C и влажности воздуха 60 - 75%.
7.11. Для
механических испытаний отбирают образцы, прошедшие цикличные
температурно-влажностные воздействия, и досушивают их при температуре не более
60 °C до достижения ими первоначальной влажности (влажности контрольных
образцов).
Механические
испытания контрольных образцов и образцов, прошедших цикличные
температурно-влажностные воздействия, на скалывание вдоль волокон проводят по
ГОСТ 15613.1-77.
7.12. Относительную
прочность клеевых соединений A подсчитывают по формуле
,
где
- среднее арифметическое результатов испытаний
образцов после цикличных температурно-влажностных воздействий;
- среднее арифметическое результатов испытаний
контрольных образцов.
Результаты
подсчетов относительной прочности клеевых соединений записывают в журнал (Прил.
3б).
7.13. В зависимости
от степени стойкости к цикличным температурно-влажностным воздействиям клеевые
соединения подразделяют на три группы стойкости: малую, среднюю, повышенную.
Группу стойкости
клеевых соединений к цикличным температурно-влажностным воздействиям определяют
в зависимости от величины их относительной прочности: до 30% - малая; от 30 до
60% - средняя; более 60% - повышенная.
Теплостойкость
и морозостойкость клеевых соединений
7.14. Оценку
стойкости к действию повышенных и пониженных температур производят по ГОСТ
18446-73.
7.15. Общее
количество испытываемых образцов формируют из трех серий, состоящих из не менее
8 образцов каждая. Первая серия состоит из контрольных образцов, подлежащих
испытанию на скалывание, вторая и третья - из образцов, подлежащих испытаниям
на теплостойкость или морозостойкость. Образцы одной из них испытывают на
скалывание при заданной температуре, а другой - после выдерживания их в течение
двух недель в нормальных температурно-влажностных условиях.
Влажность
контрольных образцов и образцов, испытываемых на скалывание при нормальных
температурно-влажностных условиях, должна быть 10 +/- 2%.
7.16. Испытания
клеевых соединений на теплостойкость производят выдерживанием образцов в
термокамере в течение двух недель при температуре 60 +/- 3 °C.
7.17. Испытания
клеевых соединений на морозостойкость проводят выдерживанием в морозильной
камере в течение двух недель при температуре минус 30 °C с нормальной (W = 10
+/- 2%) влажностью образцов; образцов с влажностью выше предела гигроскопичности
(W >= 30%), вымоченных в воде, имеющей температуру 20 +/- 2 °C в течение 48
ч.
7.18. Зазоры между
образцами, укладываемыми на сетки стеллажей термокамеры или морозильной камеры,
не должны быть менее 5 мм. К образцам, находящимся в камере, должен быть
обеспечен доступ воздуха со всех сторон. Общий объем загруженных в камеру
образцов не должен быть более 50% ее объема.
Колебания
температуры в различных частях камеры не должны быть более +/- 2 °C.
После укладки
образцов дверцы камеры закрывают и доводят до требуемой температуры. Момент
доведения температуры в камере до заданной считается началом испытаний на
теплостойкость или морозостойкость клеевых соединений.
7.19. После
истечения срока испытаний образцов на теплостойкость или морозостойкость половину
образцов (вторая серия) испытывают на скалывание до разрушения в режиме
температурных воздействий (плюс 60 °C или минус 30 °C) непосредственно в
камере, если она оборудована испытательной установкой, или вне ее с
поддержанием указанной температуры. При испытании образцов вне камеры время с
момента извлечения образца из камеры до начала нагружения не должно превышать 3
- 5 мин.
Оставшуюся часть
образцов (третья серия) выдерживают в течение двух недель в нормальных
температурно-влажностных условиях до достижения ими температуры и влажности
контрольных образцов, а затем испытывают на скалывание.
7.20. Относительную
прочность клеевого соединения подсчитывают с точностью до 1% по формуле
,
где
- относительная прочность клеевого соединения
после температурных воздействий (для образцов, испытываемых при заданной
температуре);
- относительная прочность клеевого соединения
после достижения образцами температуры и влажности контрольных образцов;
- среднее арифметическое результатов испытаний
образцов, подвергнутых температурным воздействиям;
- среднее арифметическое результатов испытаний
контрольных образцов.
Результаты подсчета
относительной прочности клеевых соединений записывают в журнал (Прил. 3в).
7.21. В зависимости
от степени стойкости к температурным воздействиям клеевые соединения
подразделяют на группы нормальной теплостойкости или морозостойкости;
пониженной теплостойкости или морозостойкости.
Группу
теплостойкости или морозостойкости клеевых соединений в зависимости от
относительной прочности их определяют по табл. 4.
Таблица 4
───────────────────┬───────────────┬───────────────────────────────────────
Показатели │
Группы │ Относительная прочность клеевых
│ │ соединений, %
│
├───────────────────┬───────────────────
│ │ I │ II
│ │ A │ A
───────────────────┼───────────────┼───────────────────┼───────────────────
Теплостойкость │Нормальная │ >= 75 │ >= 90
│Пониженная │ < 75 │ < 90
Морозостойкость │Нормальная │ >= 100 │ >= 100
│Пониженная │
< 100 │ < 100
Примечание.
Показатели относительной прочности клеевых соединений при определении
морозостойкости действительны как для сухих, так и для увлажненных образцов.
Группу
теплостойкости или морозостойкости клеевых соединений устанавливают по более
низким показателям их относительной прочности.
Атмосферостойкость
клеевых соединений
7.22. Оценку
атмосферостойкости производят по ГОСТ 19100-73.
7.23. Количество
образцов на каждый вид испытаний (контрольных, выдерживаемых в отапливаемом
помещении, и образцов, подвергаемых атмосферным воздействиям) должно быть не
менее 8.
На каждом образце
должна быть указана серия и дата начала испытаний.
Маркировка
наносится способом, обеспечивающим ее сохранность при длительном действии
образцов в условиях атмосферных воздействий.
7.24. Испытания
образцов на атмосферостойкость клеевых соединений проводят в различных
климатических зонах: сухой, нормальной и влажной в соответствии с
рекомендациями нормативных документов.
Для учета влияний
метеорологических условий на испытываемые образцы в журнал наблюдений
ежемесячно заносят следующие данные, получаемые от государственных
метеорологических станций:
температуру воздуха,
°C (средняя минимальная, максимальная);
количество часов с
температурой воздуха, °C: минус 30, от минус 30 до минус 15, от минус 15 до 0,
от 0 до плюс 15, от плюс 15 до плюс 30, от плюс 30 и выше:
количество осадков,
мм;
число дней с
осадками (дождь, снег);
количество
солнечных часов;
количество часов с
относительной влажностью воздуха, %: от 100 до 90, от 90 до 70, от 70 и ниже;
максимальную
скорость и преобладающее направление ветра.
7.25. Образцы,
испытываемые на атмосферостойкость клеевых соединений, помещают в стенды (рис.
21), устанавливаемые на испытательных площадках.
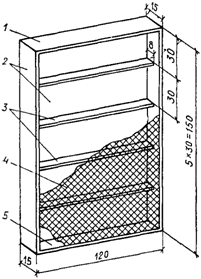
Рис. 21. Стенд для
испытаний клеевых соединений
на
атмосферостойкость
1 - крышка; 2 -
стенки; 3 - полки;
4 - защитная
съемная сетка; 5 - основание
Испытательные
площадки выбирают на открытом воздухе, вблизи метеорологических станций и вдали
от источников загрязнения воздуха.
Стенды
устанавливают лицевой стороной на юг, с углом наклона к горизонту,
соответствующим географической широте места испытания с точностью до 5°.
По высоте стенд
должен быть установлен выше уровня земли на 0,5 - 0,8 м и среднего уровня
покрова - на 10 - 15 см. Во время испытаний стенды систематически очищают от
снега.
Расположение
стендов должно обеспечивать свободное проветривание пространства между ними и
исключать затенение образцов.
Испытываемые
образцы устанавливают на полках стенда длинной стороной к его задней стенке и
крепят к ней тонкой проволокой из алюминия или другого некорродирующего материала.
Расстояние между образцами не должно быть менее 10 мм.
7.26. Сроки начала
и конца испытания образцов на атмосферостойкость клеевых соединений
определяются программой испытаний.
Для начала
испытаний образцов рекомендуется весенний период.
Съем образцов для
определения прочностных показателей целесообразно проводить:
после смены каждого
времени года при выставлении образцов на срок до трех лет;
после окончания
весенне-летнего и осенне-зимнего периодов года при выставлении образцов на срок
до пяти лет;
через каждый год
после весенне-летнего периода при выставлении образцов на срок 5 и более лет.
В течение первого
года экспозиции съем образцов должен производиться через 1, 3, 6, 9, 12 мес
после начала испытаний.
7.27. Одновременно
с началом испытаний образцов на атмосферные воздействия определяют прочность
контрольных образцов на скалывание вдоль волокон по ГОСТ 15613.1-77 для
определения начальной прочности клеевых соединений и закладывают на выдержку в
отапливаемом помещении контрольные образцы, механические испытания которых
проводят вместе с образцами, прошедшими атмосферные воздействия.
Образцы, снимаемые
со стенда для промежуточного контроля и после окончания испытания на
атмосферные воздействия, должны быть тщательно осмотрены для регистрации их внешнего
вида. Данные об образцах, снимаемых со стенда, записывают в журнал.
Для механических
испытаний образцы, снятые со стенда, а также контрольные образцы, выдерживаемые
в отапливаемом помещении, приводят к первоначальной влажности.
7.28. Относительную
прочность клеевых соединений A подсчитывают по формуле
,
где
- среднее арифметическое результатов испытаний
образцов после атмосферных воздействий;
- среднее арифметическое результатов испытаний
контрольных образцов, выдерживаемых в отапливаемом помещении.
В качестве критерия
оценки атмосферостойкости принимают следующие показатели:
изменение
механической прочности образцов (предел прочности при скалывании вдоль волокон,
характер разрушения);
изменение внешнего
вида образцов (растрескивание, коробление, изменение цвета);
изменение линейных
размеров образцов в момент съема со стенда.
Расслаивание
при переменном увлажнении
7.29. Образцы для
испытаний на расслаивание представляют собой пластину толщиной (вдоль волокон
древесины) 70 мм, а ширина и высота должны соответствовать размерам поперечного
сечения клееного элемента. Образцы вырезают из торцовой части конструкции или элемента
во время торцовки и доведения до проектных размеров.
7.30. Для контроля
качества склеивания образцы подвергают цикличному увлажнению и высушиванию. Для
ускорения увлажнения этот процесс осуществляют, вакуумируя образцы и вымачивая
их при избыточном давлении. С этой целью образцы помещают в автоклав на
подвижной тележке, оборудованной кассетами таким образом, чтобы обеспечивался
свободный доступ воды к торцам образцов.
Обработку образцов
осуществляют при цикличном действии "вакуум-давления" и высушивания.
Цикл
"вакуум-давления" повторяют два раза. Он включает:
выдержку образцов
под вакуумом 0,09 - 0,1 МПа в течение 30 - 40 мин при температуре 18 - 22 °C;
выдержку образцов в
воде под давлением 0,5 - 0,6 МПа в течение 2 ч;
высушивание
образцов до начальной влажности в сушильной камере при температуре 50 - 60 °C,
относительной влажности воздуха 25 - 30% и скорости движения воздуха 2 - 3 м/с.
7.31. Оценку
качества склеивания образцов производят после завершения каждого цикла
испытаний.
После высушивания
образцов замеряют суммарную длину раскрытия клеевых прослоек на обеих торцовых
поверхностях.
В качестве
показателя расслаивания принимают процентное отношение суммарной длины
расслоения по клеевым прослойкам к общему периметру клеевых прослоек, выходящих
на торец образца, по формуле
,
где l - суммарная
длина расслоений, мм;
b - ширина образца,
мм;
n - количество
клеевых прослоек в образце.
8. КОНТРОЛЬ
ПРОЧНОСТИ ПРИ ДЛИТЕЛЬНОМ ДЕЙСТВИИ
СТАТИЧЕСКОЙ
НАГРУЗКИ
8.1. Наиболее часто
длительную прочность контролируют путем испытания малых образцов на скалывание
(по ГОСТ 15613.1-77) и растяжение (по ГОСТ 15613.5-79). При необходимости можно
проверить длительную прочность на средних образцах, натурных конструкциях или
их элементах, что позволяет учесть масштабный фактор.
Для получения
сравнимых результатов оценки длительной прочности целесообразно использовать
стандартные образцы, на которых определяют кратковременную прочность.
8.2. Для испытаний
малых образцов на скалывание (при сжатии), а также больших конструкций и их
элементов при изгибе преимущественно используют рычажные установки,
обеспечивающие постоянство нагрузки во время испытаний. Максимальное
передаточное число таких установок 12 - 15 Н. Так как опорная часть, на которой
установлен образец, подвижна, а рычаг достаточно велик, в подобных установках
можно регулировать величину нагрузки в довольно широком диапазоне.
Схема рычажной
установки для определения длительной прочности клеевых соединений при
скалывании образцов вдоль волокон древесины показана на рис. 22.
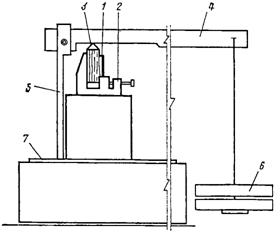
Рис. 22. Схема
рычажной установки для определения
длительной
прочности клеевых соединений
при скалывании
вдоль волокон древесины
1 - образец; 2 -
приспособление для установки образца;
3 - призма; 4 -
рычаг; 5 - стойка рычага;
6 - груз; 7 -
основание
8.3. Для испытаний
на растяжение малых стандартных образцов можно использовать рычажно-дисковые
установки, принцип работы которых заключается в многократной ступенчатой
передаче усилия через систему дисков с помощью стального троса.
8.4. Оценку
длительной прочности можно проводить двумя методами.
По первому методу
образцы нагружают и фиксируют, через сколько времени они разрушатся.
Уровни нагрузок
обычно принимают 0,8; 0,6; 0,4 от кратковременной прочности. На каждый уровень
нагрузки ставят не менее 5 образцов и фиксируют время до разрушения каждого из
них. Продолжительность испытаний составляет, как правило, не менее
(120 сут и более).
Длительную
статическую прочность определяют по уровню нагрузки, под которой образцы не
разрушаются в течение указанного времени.
По второму методу
образцы нагружают постоянной нагрузкой различного уровня, которая выбирается
таким образом, чтобы за время действия этой нагрузки не происходило разрушения
образцов. Через разные сроки действия постоянной нагрузки отбирают часть
образцов и определяют их кратковременную прочность.
8.5. Длительную
прочность оценивают по формуле
,
где
- предел прочности при действии длительной
статической нагрузки;
- кратковременная прочность.
9. КОНТРОЛЬ
ВНУТРЕННИХ НАПРЯЖЕНИЙ
9.1. Одним из
критериев оценки качества клееных конструкций являются внутренние напряжения,
возникающие в конструкциях на стадии их изготовления (технологические
напряжения) и применения в строительстве (эксплуатационные напряжения).
В настоящее время
отсутствует какой-либо универсальный метод, позволяющий количественно оценивать
внутренние напряжения на всех стадиях их возникновения и развития, поэтому в
экспериментальных исследованиях используют разные методы.
9.2. Для оценки
внутренних остаточных напряжений в клееной древесине можно использовать
стандартный метод (ГОСТ 11603-73), основанный на измерении упругих деформаций,
определении послойного модуля упругости, вычислении напряжений и построении их
эпюры. Этот метод имеет ограниченное применение из-за большой трудоемкости, так
как требует вырезки образцов из конструкций, измерения модуля упругости и т.п.,
поэтому для контроля внутренних напряжений в клееной древесине чаще используют
механические методы с применением статических датчиков усилий (давления).
9.3. Для определения
величины и распределения технологических напряжений по сечению клееных
элементов может быть использован метод, разработанный Л.О. Лепарским и А.П.
Кувшиновым. Метод должен дать возможность количественно определить нормальные
напряжения поперек волокон древесины, направленные вдоль высоты
(рис. 23, а) и вдоль ширины
(рис. 23, а) поперечного сечения конструкции.
Максимальная база замера
должна составлять 300 мм, а
- 600 мм. Для определения
секцию рассекают параллельно клеевым
прослойкам, как показано на рис. 23, г, при этом устанавливается интегральная
величина напряжений в слоях секции, т.е. средних напряжений, действующих на
всей длине слоя секции. Для определения
секцию рассекают перпендикулярно клеевым
прослойкам (рис. 23, в). Размеры отсекаемых слоев h могут колебаться в пределах
4 - 8 мм.
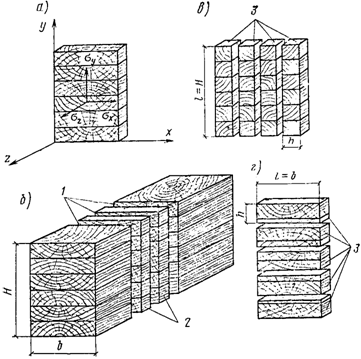
Рис. 23. Метод
определения величины и распределения
технологических
напряжений по сечению клееных элементов
а - схема
распределения напряжений; б - отбор пробы
для испытаний; в, г
- рассечение испытуемой секции
соответственно
перпендикулярно и параллельно клеевым
прослойкам; 1 -
пропилы; 2 - секции; 3 - слои секции
Пробы берут из
многослойных элементов деревянных клееных конструкций (рис. 23, б) высотой (H)
не более 600 мм, шириной (b) до 300 мм. Проба должна состоять из двух секций:
одна для измерения внутренних усилий, другая - для контроля влажности. Секции
выпиливают на круглопильном станке на расстоянии не менее 300 мм от торца
конструкции последовательными поперечными резами. При этом толщина каждой секции
вдоль волокон не должна превышать 15 +/- 0,5 мм.
Для определения
влажности секции взвешивают и определяют массу с погрешностью не более 0,01 г.
При необходимости выравнивания влажности последние выдерживают в помещении при
температуре 20 +/- 5 °C и относительной влажности воздуха 55 - 65% в течение 2
сут. После окончания выдержки повторно определяют массу секций. Одну из секций
помещают в сушильный шкаф с температурой 103 +/- 2 °C для высушивания до
постоянной массы.
Метод
предусматривает определение внутренних усилий, площади поперечного сечения,
вычисление напряжений и построение их эпюры.
Для измерения
размеров образца используется скоба с индикатором часового типа с погрешностью
не более 0,01 мм.
В момент
выпиливания определяют напряжения, возникающие перпендикулярно контуру секции.
После выпиливания секцию раскалывают на слои в направлении развития внутренних
напряжений, а возникающие при этом усилия фиксируют упругими элементами. Таким
образом определяют внутренние напряжения в каждом слое и в выпиленной секции в
целом. Действительные напряжения складываются из напряжений, определенных в
момент выпиливания секции, и напряжений, полученных при раскалывании секции на
отдельные слои.
Для измерения
усилий в секции при ее выпиливании из клееного элемента применяется специальное
устройство.
Схема устройства
изображена на рис. 24. Базой устройства является основание 1, выполненное в
виде четырехугольной рамки и составленное из вертикальных подвижной 2 и
неподвижной 3 штанг, соединяемых при помощи сухарей 6 и крепежных болтов,
закрепляемых гайкой 8, причем неподвижная вертикальная 3 и горизонтальная 5
штанги монолитно связаны между собой под прямым углом, который для увеличения
жесткости усилен приливом 9. Вертикальные 2, 3 и горизонтальные 4, 5 штанги
имеют продольные прорези 10, в которых закреплены крепежные болты сухарей 7 и
хвостовики 11 Г-образных упругих элементов 12, снабженных установочным
элементом в виде шурупа 13, ввертываемого в грань клееного элемента 14. Кроме
того, через прорезь горизонтальной штанги 4 проходят концы вертикальных штанг 2
и 3. На поверхности рабочей части упругих элементов смонтированы тензорезисторы
15, соединенные с коммутатором 16 и вторичным прибором 17; 18 - слои клееного
элемента.
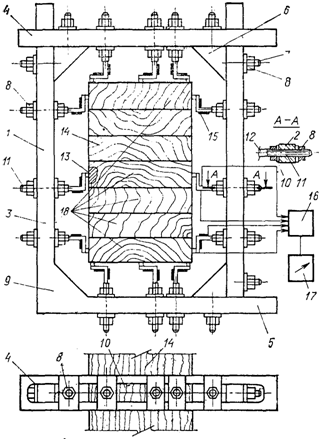
Рис. 24.
Схема устройства для определения
внутренних
напряжений в секции в момент выпиливания
ее из клееной
конструкции
Определение
внутренних напряжений в элементе конструкции с помощью описанного устройства
производится следующим образом. В выбранных точках периметра сечения элемента
14 в направлении взаимно перпендикулярных осей измерения внутренних усилий
ввинчивают установочные элементы 13. На хвостовики 11 упругих элементов 12
надевают через прорези 10 неподвижные и подвижные штанги 2, 3, 4 и 5.
Полученное после полной установки всех упругих элементов взаимное расположение
штанг фиксируется сухарями 6 и крепежными болтами 7. Затем снимают показания
вторичного прибора 17, принимая их за нулевые. При перераспределении внутренних
напряжений, вызванном нарушением целостности клееного элемента 14, или в
процессе развития в элементе температурно-влажностных деформаций, вызванных
неравномерным распределением влажности по сечению элемента, в упругих элементах
12 возникают усилия, препятствующие перемещению фиксируемых точек на
поверхности клееного элемента относительно неподвижного основания 1 на
величину, обусловленную жесткостью упругих элементов 12.
Усилия, требуемые
для препятствия перемещению и возникающие в клееном элементе 14, фиксируются по
показаниям вторичного прибора 17 и определяются при помощи тарировочных
графиков. Подсчет величин внутренних напряжений, возникающих одновременно в
двух взаимно перпендикулярных направлениях, производится по формулам:
;
,
где
и
- усилия, определяемые по тарировочным
графикам, Н;
- площадь поперечного сечения клееного
элемента, см2.
Для измерения
внутренних усилий при рассечении секции применяется специальное приспособление,
основанное на использовании датчиков давления с погрешностью измерения не более
2 Н. Устройство включает две опоры, смонтированные на общей станине. Одна опора
неподвижная, на ней смонтированы групповые зажимы для жесткого крепления
образца. Другая опора подвижная, на ней смонтированы датчики давления,
представляющие собой упругие элементы в виде консольных металлических балок
постоянного сечения и смонтированных на них тензорезисторных чувствительных
элементов, преобразующих давление в электрический сигнал. Для крепления образца
к упругому элементу предусмотрены индивидуальные зажимы.
Так как устройство
основано на механическом способе определения внутренних напряжений и
предполагает использование статических датчиков усилий, т.е. датчиков, частично
стесняющих полную деформацию образца
(рис. 25), погрешность измерения определяется
степенью стеснения деформаций образца и податливостью системы закрепления
образца. При оценке податливости по формуле
, где
- деформация свободного образца, мм,
необходимо, чтобы ее численная величина не превышала 30% величины свободной
деформации. Например, при величине внутренних усилий в образце P = 50 Н
свободная деформация (при модуле упругости древесины поперек волокон E = 265
МПа) равна:
. Чтобы
получить требуемую податливость, датчик усилия, т.е. упругий элемент, должен
иметь деформацию
. Тогда
.
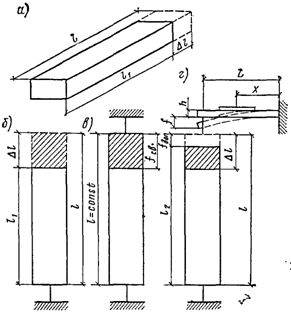
Рис. 25.
Схема измерения деформаций с помощью датчиков,
частично стесняющих
полную деформацию образца
а - образец; б -
свободная деформация образца;
в - стесненная
деформация образца; г - частично
стесненная
деформация образца
Определение
внутренних усилий в секции производят следующим образом. Намечают направление
замеряемых усилий: либо вдоль ширины, либо вдоль высоты поперечного сечения
исследуемой конструкции. Производят жесткое крепление одной грани секции на
неподвижной опоре устройства при помощи групповых зажимов. Затем центрируют
противоположную грань секции по отношению к упругим элементам и производят
крепление этой грани к упругим элементам при помощи индивидуальных зажимов.
Снимают отсчеты по вторичному прибору для всех задействованных чувствительных
элементов, принимая показания за нулевые. Подводят к закрепленной в устройстве
секции рамку с набором пил и рассекают секцию на слои. При этом ширина пропила
должна составлять не более 0,8 +/- 0,1 мм.
Сразу же после
распила секции снимают показания вторичного прибора, шкала которого
проградуирована в единицах давления с ценой деления 2 Н. Таким образом, для
каждого отсеченного слоя секции определяют среднее внутреннее усилие, возникшее
в нем по всей длине при перераспределении внутренних напряжений и стеснении
образующихся при этом деформаций.
После замера
внутренних усилий слои секции вынимают из устройства и при помощи индикаторной
скобы измеряют толщину и ширину слоев для подсчета площади их поперечного
сечения.
Внутренние
напряжения (в МПа) определяют для каждого слоя с погрешностью не более 0,005
МПа по выражению
,
где P - внутренние
усилия в слое секции, Н;
F - площадь
поперечного сечения слоя секции, см2.
По полученным
величинам напряжений в момент выпиливания секции из клееного элемента и
напряжений, определенных после выпиливания и рассечения секции на слои,
определяют действительные напряжения в том сечении клееного элемента, откуда
была выпилена данная секция, путем складывания величин напряжений, полученных
обоими устройствами.
Эпюру напряжений,
которая является характеристикой напряженного состояния выбранного сечения
деревянной клееной конструкции, строят следующим образом. На горизонтальной оси
откладывают отрезок в масштабе 3:1, соответствующий размеру секции в
направлении замера внутренних усилий. На этой оси откладывают последовательно
ширины всех слоев и пропилов. Если сумма ширин пропилов и слоев превышает общую
размерность стороны секции (из-за погрешности измерения), то излишек равномерно
распределяют между всеми слоями. На ординатах, проведенных через середину
участков горизонтальной оси, соответствующих ширинам слоев, откладывают
величины напряжений в масштабе 1 см ординаты равен 0,1 МПа. При этом напряжения
растяжения откладывают вниз от горизонтальной оси, а напряжения сжатия - вверх
от этой оси.
Исходя из условий
равновесия напряжений, горизонтальную линию при необходимости переносят в новое
положение с таким расчетом, чтобы площади эпюр с разными знаками были равны.
Погрешность измерения площади эпюры не более 1 мм2. Окончательную величину
внутренних напряжений определяют по шкале напряжений, соответствующей новому
положению горизонтальной оси.
Для измерения
внутренних технологических и эксплуатационных напряжений в поверхностных зонах
элемента в направлении, перпендикулярном его продольной оси, Л.О. Лепарским и
А.К. Цветковым разработана методика, заключающаяся в следующем.
На боковой
поверхности элемента по его длине устанавливают несколько пар реперов (рис. 26,
а) и с помощью измерительного микроскопа фиксируют расстояние
между реперами каждой пары с погрешностью +/-
0,003 мм. Затем выкалывают часть поверхностной зоны элемента вместе с реперами
так, чтобы получилась пластинка толщиной до 5 мм, шириной до 20 мм и длиной,
равной высоте элемента. Расстояние между реперами вновь измеряют с той же
погрешностью. После этого пластинку разрезают на несколько полосок, чтобы в
каждой полоске находилась одна пара реперов (рис. 26, б). Каждую полоску
закрепляют по концам в захватах специального устройства и деформируют таким
образом, чтобы расстояние между реперами равнялось расстоянию, которое было
между ними на поверхности элемента
, фиксируя
одновременно требуемое для этого усилие. Рассматривая отношение усилия к
площади поперечного сечения полоски, получают величину внутреннего напряжения
на участке, ограниченном реперами. Базовое расстояние между реперами, как
правило, принимается равным 80 мм.
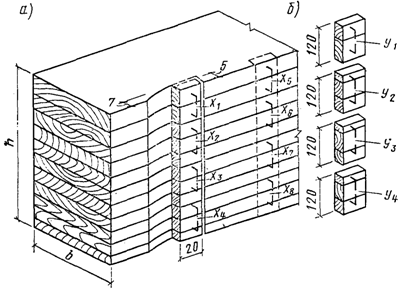
Рис. 26.
Оценка распределения напряжений
в поверхностной
зоне по высоте клееного элемента
а - схема отбора
пластин; б - схема распределения пластин
Выкалывание
пластины из боковой поверхности элемента осуществляют следующим образом: по
обеим сторонам от оси, вдоль которой установлены реперы, и на расстоянии 10 мм
от нее делают два параллельных пропила глубиной 7 мм. Пропилы заливают лаком
ХВ-784 для предотвращения изменения влажности древесины. Затем с одной стороны
от намеченной пластины стамеской выбирают канавку, стенкой которой является
срез пластины, после чего специальным ножом откалывают последнюю по высоте
элемента, сохраняя установленные на ней реперы.
Повторное измерение
расстояния между реперами производят сразу же после отделения пластины от
элемента, для чего ее помещают на горизонтальную поверхность и с помощью
прижимных планок предварительно выпрямляют. Разделив затем пластину на
образцы-полоски по числу пар реперов, каждый образец толщиной 5 мм, шириной 20
мм и длиной 120 мм закрепляют в описанном ниже устройстве (рис. 27).
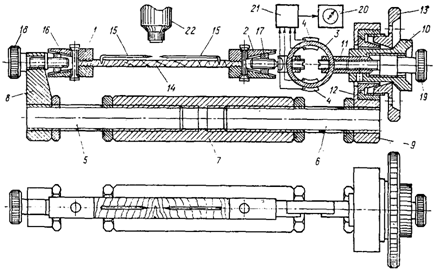
Рис. 27. Схема
устройства для определения внутренних
напряжений в
деревянных клееных конструкциях
Устройство включает
захваты 1 и 2, упругий элемент в виде кольца 3 с тензорезисторами 4. Основание
устройства выполнено составным из отдельных частей: двух штанг 5 и 6, имеющих
соответственно правую и левую резьбу и соединенных гайкой 7. На основании
установлены опора 8 для закрепления захвата 1 и опора 9 для закрепления захвата
2. На опоре 9 размещена фигурная гайка 10, взаимодействующая со скользящей
втулкой 11 и цанговым зажимом 12, снабженным обжимной гайкой 13.
Измерение
производят следующим образом. Вращая гайку 6, устанавливают необходимое
расстояние между опорами 8 и 9, на которых размещены захваты. Образец 14 с
установленными на нем реперами 15 закрепляют в захватах 1 и 2, выполненных в
виде губок, хвосты которых раздвигаются гайками 16 и 17 при вращении винтов 18
и 19. После установки образца в захватах фиксируют неподвижно цанговым зажимом
12 фигурную гайку 10, вращая при этом обжимную гайку 13. После такого
закрепления можно, вращая винт 19, растягивать или сжимать образец 14 до
требуемого расстояния между концами реперов 15, отмечая по вторичному прибору
20, связанному через коммутатор 21 с тензорезисторами 4, требуемое для этого
усилие. Измерение расстояния между концами реперов 15 производят с помощью
измерительного микроскопа 22.
Описанную методику
и аппаратуру можно также использовать для получения оценки внутренних
напряжений в различных местах сечения клееного элемента при условии их
разрушения. Для нахождения эпюры напряжений в каком-либо сечении клееного
элемента из него вырезают секции, имеющие размер в направлении вдоль волокон
древесины 20 мм и сечение, равное сечению элемента (рис. 28, а). Поскольку
внутренние напряжения уравновешены в общем объеме элемента и его распиловка
вызовет перераспределение напряжений, необходимо фиксировать деформированное
состояние древесины, которое было в секции до вырезки ее из элемента. Для этого
на боковые грани секции до ее выпиловки из элемента устанавливают попарно
контрольные реперы, как это показано на рис. 28, а. Зафиксировав расстояние
между контрольными реперами каждой пары
,
элемент распиливают по сечению 1. Сразу же после распиливания торцовую часть
образца изолируют от влаги двумя слоями лака ХВ-784 и фиксируют новое
расстояние
между контрольными реперами. Разность между
установленными значениями
и
,
является поправкой
на перераспределение деформаций в
рассматриваемом сечении. В первом приближении принимается, что поправка
,
взятая на одном уровне сечения между противоположными гранями элемента,
измеряется по его ширине по закону прямой линии (рис. 28, в).
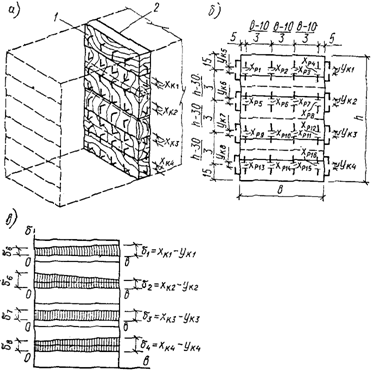
Рис. 28.
Определение эпюры внутренних напряжений
в сечении клееного
элемента
а - схема выпиловки
образцов; б - схема расстановки
реперов; в -
определение поправок к деформациям древесины
после выпиловки
образца из элемента; 1 - торцовый срез,
покрываемый
влагозащитным составом;
2 - открытый
торцовый срез
На торцовой грани
оставшейся части элемента устанавливают попарно рабочие реперы с таким
расчетом, чтобы можно было получить распределение напряжений до высоте сечения
на различном расстоянии от нижней грани (рис. 28, б). Зафиксировав расстояние
между рабочими реперами каждой пары
,
вносят поправку
в значение
,
получая тем самым то расстояние между рабочими реперами, которое должно было
быть до отпиливания части элемента. Если
, то
поправка
берется со знаком "+", если
- со знаком "-".
После этого
производят отпиливание секции от оставшейся части элемента по сечению 2,
изолируют от влаги вторую торцовую грань образца двумя слоями лака ХВ-784 и
раскалывают образец на полоски в направлении измерения напряжений таким
образом, чтобы в каждую полоску входили пары реперов по всем взятым уровням.
Эти полоски расчленяют по высоте на пластинки соответственно по числу пар
рабочих реперов, фиксируя расстояние
между рабочими реперами каждой пары, и
подсчитывают упругую деформацию каждой пластинки по формуле
.
Затем каждую пластинку закрепляют в
упомянутое выше устройство, деформируют на величину
и, фиксируя необходимое для этого усилие,
определяют имеющиеся в полоске напряжения. В случае если значение
,
подсчитанное по формуле, имело знак "+", то полоску в устройстве
растягивают, фиксируя тем самым наличие растягивающих напряжений. Если значение
имеет знак "-", то полоску,
предварительно закрепив ее в струбцинах, препятствующих изгибу, сжимают и
определяют величину сжимающих напряжений.
Описанная методика
позволяет установить эпюры напряжений по сечению торца элемента. В этом случае
нет необходимости устанавливать контрольные реперы и определять поправку. Для
определения влажности древесины во всех случаях используют части образца,
оставшиеся после выкалывания полосок. Перед взвешиванием проб на влажность
удаляют древесину, пропитанную влагоизолирующим лаком.
Приложение
1
ВИДЫ
КОНТРОЛЯ И РЕКОМЕНДУЕМЫЕ ОБЛАСТИ ИХ ПРИМЕНЕНИЯ
────────────────┬───────────────────────────┬────────────────────┬─────────
Вид контроля
│ Нормативный
документ, │ Показатели │Рекомен-
│ регламентирующий
методику │
│дуемая
│ испытаний образцов │ │область
├─────────────┬─────────────┼──────────┬─────────┤приме-
│ малых
│средних │
единица │величина │нения
│ (из чистой │(пиломате- │измерения │ │
│ древесины
│риалов и │ │ │
│без пороков)
│заготовок) │ │ │
────────────────┼─────────────┼─────────────┼──────────┼─────────┼─────────
1
│ 2 │ 3
│ 4 │
5 │ 6
────────────────┴─────────────┴─────────────┴──────────┴─────────┴─────────
I. Древесина (ель,
сосна)
1.
Прочность │ГОСТ │ -
│ МПа │ 70 - 80 │ 1, 2
при
статическом │16483.3-73*
│ │ │ │
изгибе
├─────────────┼─────────────┼──────────┼─────────┼─────────
│ -
│ГОСТ │ МПа
│ 30 - 50 │ 1, 3, 4
│ │21554.2-76 │ │ │
────────────────┼─────────────┼─────────────┼──────────┼─────────┼─────────
2.
Прочность │ГОСТ │ -
│ МПа │90 - 100 │ 1, 2
при
продольном │16483.23-73 │ │ │ │
растяжении
├─────────────┼─────────────┼──────────┼─────────┼─────────
│ -
│ГОСТ │
МПа │ 25 - 35
│ 1
│ │21554.5-78 │ │ │
────────────────┼─────────────┼─────────────┼──────────┼─────────┼─────────
3.
Прочность │ГОСТ │ -
│ МПа │6,0 - 6,5│ 1, 2, 3
при
скалывании │16483.5-73* │ │ │ │
вдоль
волокон
├─────────────┼─────────────┼──────────┼─────────┼─────────
│ -
│ГОСТ │ МПа
│3,5 - 4,5│ 1, 3, 4
│ │21554.6-78 │ │ │
────────────────┼─────────────┼─────────────┼──────────┼─────────┼─────────
4.
Плотность │ГОСТ │ -
│ кг/м3 │430 - 480│ 1
│16483.1-73* │ │ │ │
────────────────┼─────────────┼─────────────┼──────────┴─────────┼─────────
5.
Пороки │ГОСТ 2140-71
│ - │Рекомендуемые │ 1, 2, 3
│ │ │величины указываются│
│ │ │в нормативных │
│ │ │документах на │
│ │ │конкретные изделия │
│ │ │или регламентируются│
│ │ │методикой │
│ │ │исследований │
────────────────┼─────────────┼─────────────┼────────────────────┼─────────
6.
Внутренние
│Нестандартный│
- │ То же │
1, 3
напряжения │ │ │ │
────────────────┼─────────────┼─────────────┼──────────┬─────────┼─────────
7.
Влажность │ГОСТ │ -
│ % │10 +/- 2 │ 1, 2, 3
│16483.7-71* │ │ │ │
├─────────────┼─────────────┼──────────┼─────────┼─────────
│ │ГОСТ │ %
│10 +/- 3 │ 3, 4
│ │16588-71* │ │ │
II. Клеи
1.
Условная │ГОСТ
20501-75│ - │
с │100 - 400│ 1,
3, 4
вязкость │ │ │(по ВЗ-4) │ │
────────────────┼─────────────┼─────────────┼──────────┼─────────┼─────────
2.
Жизне- │ То же
│ - │
ч │ 1,5 - 2 │ 1,
3, 4
способность │ │ │ │ │
────────────────┼─────────────┼─────────────┼──────────┼─────────┼─────────
3.
Условное │ " │
- │
с │ 30 - 50 │ 1, 3
время │ │ │ │ │
отверждения │ │ │ │ │
III. Технологические параметры
процесса склеивания
(обработка поверхности, нанесение и
расход клея, давление
и время прессования)
│Рекомендации по │Рекомендуемые │
3, 4
│изготовлению и
контролю │величины
указываются│
│качества деревянных
клееных│в нормативных │
│конструкций │документах на │
│ │конкретные
изделия │
│ │или
регламентируются│
│
│методикой │
│
│исследований │
IV. Клеевые
соединения
Кратковременная
прочность
1.
Пластовых │ГОСТ │ │ МПа
│ 6,5 │
1, 3
и
кромочных │15613.1-77 │ │ │ │
соединений
├─────────────┼─────────────┼──────────┼─────────┼─────────
при
скалывании │ │Нестандарт- │
МПа │ 7 - 8 │
1, 4, 5
вдоль
волокон │ │ный - │ │ │
древесины │ │послойное │ │ │
│ │скалывание │ │ │
────────────────┼─────────────┼─────────────┼──────────┼─────────┼─────────
2.
То же, при │ГОСТ │ -
│ МПа │Не менее │ 1
раскалывании │15613.2-77 │ │ │ 0,5
│
────────────────┼─────────────┼─────────────┼──────────┼─────────┼─────────
3.
Зубчатых │ГОСТ │ -
│ МПа │
6 - 8 │ 1
и
торцовых │15613.3-77 │ │ │ │
соединений │(для │ │ │ │
при
растяжении │торцовых) │ │ │ │
вдоль
волокон
├─────────────┼─────────────┼──────────┼─────────┼─────────
│ГОСТ │ -
│ МПа │ 45 - 55 │ 1, 3
│15613.5-79 │ │ │ │
│(для │ │ │ │
│зубчатых) │ │ │ │
────────────────┼─────────────┼─────────────┼──────────┼─────────┼─────────
4.
Зубчатых │ГОСТ │ -
│ МПа │ 40 - 50 │ 1, 3, 4
клеевых │15613.4-78 │ │ │ │
соединений │ │ГОСТ │ │ 30
│
при
статическом │
│15613.4-78 │ │ │
изгибе │ │ │ │ │
────────────────┼─────────────┼─────────────┼──────────┼─────────┼─────────
5.
При отрыве │ГОСТ
862.3-77│ - │
МПа │Не менее │ 1,
3, 4
поперек
волокон │ │ │ │ 0,6
│
древесины │ │ │ │ │
────────────────┼─────────────┼─────────────┼──────────┼─────────┼─────────
6.
Угловых │ГОСТ
23166-78│ - │
МПа │Не менее
│ 1, 4
клеевых │ │ │ │ 0,4
│
соединений │ │ │ │ │
────────────────┼─────────────┼─────────────┼──────────┴─────────┼─────────
7.
Крупных
│Нестандартный│
- │Рекомендуемые │
1, 3
клееных
образцов│ │ │величины указываются│
и
элементов │ │ │в нормативных │
конструкций │ │ │документах на │
│ │ │конкретные изделия │
│ │ │или регламентируются│
│ │ │методикой │
│ │ │исследований │
Стойкость к
температурно-влажностным воздействиям
1.
Водостойкость│ГОСТ 17005-71│
- │Требуемая
степень │ 1, 2, 4
│ │ │водостойкости │
│ │ │(малая, средняя, │
│ │ │повышенная) │
│ │ │указывается в │
│ │ │нормативных или │
│ │ │других документах │
────────────────┼─────────────┼─────────────┼────────────────────┼─────────
2.
Стойкость │ГОСТ
17580-72│ - │Группа требуемой │
1, 2
к
цикличным │ │ │стойкости (малая, │
температурно- │ │ │средняя, повышенная)│
влажностным │ │ │указывается в │
воздействиям │ │ │нормативных или │
│ │ │других документах │
────────────────┼─────────────┼─────────────┼────────────────────┼─────────
3.
Тепло- и │ГОСТ
18446-73│ - │Требуемая степень │
1, 2
морозостойкость
│ │ │стойкости (нормаль- │
│ │ │ная, пониженная) │
│ │ │указывается в │
│ │ │нормативных или │
│ │ │других документах │
────────────────┼─────────────┼─────────────┼────────────────────┼─────────
4.
Атмосферо- │ГОСТ
19100-73│ -
│Допустимая степень
│ 1, 2
стойкость │ │ │изменения прочности │
│ │ │(относительная │
│ │ │прочность) │
│ │ │умазывается в │
│ │ │нормативных или │
│ │ │других документах │
────────────────┼─────────────┼─────────────┼──────────┬─────────┼─────────
5.
Расслаивание │ - │Нестандартный│ %
│5 после │ 1, 5
при
переменном │ │ │ │одного │
увлажнении │ │ │ │цикла и │
│ │ │ │10 после │
│ │ │ │трех │
│ │ │ │циклов │
────────────────┼─────────────┼─────────────┼──────────┴─────────┼─────────
6.
Длительное │Нестандартный│ -
│0,5 - 0,6 начальной │
1
действие │ │ │прочности │
статической │ │ │ │
нагрузки │ │ │ │
────────────────┼─────────────┼─────────────┼──────────┬─────────┼─────────
7.
Внутренние
│Нестандартный│Нестандартный│ МПа
│ 0,4 │
1, 3
напряжения │ │ │ │ │
Примечания. 1.
Цифры в графе 6 обозначают: 1 - при проведении исследований; 2 - при проведении
исследований, анализе результатов испытаний конструкций, а также для
составления заключений об аварийном состоянии конструкций; 3 - при отработке
технологии изготовления; 4 - при контроле производства и приемке серийной
продукции; 5 - при контроле и приемке уникальных конструкций и конструкций,
предназначенных для эксплуатации в тяжелых температурно-влажностных условиях.
2. Влажность
крупных образцов и элементов конструкций определяют по ГОСТ 16588-71*.
Приложение
2
Рекомендуемая форма
ПРОТОКОЛ
ОПРЕДЕЛЕНИЯ ПРЕДЕЛА ПРОЧНОСТИ ДРЕВЕСИНЫ
И КЛЕЕВЫХ СОЕДИНЕНИЙ
Порода древесины
Клей
Изделие
Дополнительная характеристика
образцов
Режим склеивания: Режим испытаний:
Температура, °C Температура воздуха при
испытании, °C
Влажность воздуха, % Влажность воздуха, %
Время с момента Длительность выдержки
образцов
приготовления клея до испытаний, ч
до окончания запрессовки, мин Скорость нагружения, Н/мин (кгс/мин)
Давление прессования,
МПа (кгс/см2)
Продолжительность прессования, ч
─────────┬───────────┬──────────┬───────────┬──────────┬──────────┬────────
Марки- │
Размеры
│Расстояние│Разрушающая│ Предел
│Влажность │Характер
ровка │
образца │ между
│ нагрузка, │прочности,│древесины,│разруше-
образцов
│ и площадь │ опорами, │
Н (кгс) │ МПа
│ % │ния
│ клеевого │
мм │ │(кгс/см2) │ │
│соединения,│ │ │ │ │
│ мм
│ │ │ │ │
─────────┼───────────┼──────────┼───────────┼──────────┼──────────┼────────
│ │ │ │ │ │
│ │ │ │ │ │
Дата "_____" _____________ 19 г. Подпись ____________________
Приложение
3
ПРОТОКОЛ
ОПРЕДЕЛЕНИЯ СТОЙКОСТИ КЛЕЕВЫХ СОЕДИНЕНИЙ
К
РАЗЛИЧНЫМ ТЕМПЕРАТУРНО-ВЛАЖНОСТНЫМ ВОЗДЕЙСТВИЯМ
Определение
водостойкости
─────┬──────────────────────────────┬────────────────────────┬─────────────
Марка│ Среднее арифметическое │Относительная прочность │ Группа
клея
│ показателей прочности │
клеевых соединений
│водостойкости
│
образцов, МПа (кгс/см2) │
образцов, подвергнутых │ клеевых
│ │ влагообработке, % │ соединений
├───────┬───────────┬──────────┼───────────┬────────────┤ (по более
│конт- │ после
│ после │
после │ после
│ низким
│рольных│вымачивания│кипячения
│вымачивания│ кипячения
│ показателям
│(без
├─────┬─────┼────┬─────┼─────┬─────┼────┬───────┤относительной
│влаго- │мок-
│высу-│мок-│высу-│мок- │высу-│мок-│высу- │ прочности)
│обра- │рых
│шен- │рых │шен- │рых │шен- │рых │шенных │
│ботки) │ │ных
│ │ных │
│ных │ │ │
├───────┼─────┼─────┼────┼─────┼─────┼─────┼────┼───────┤
│ │
в │ с
│ к │ кс │
│ │
│ │
│
M │ M │ M
│M │ M │ A
│ A │ A │
A │
│
ср │ ср │
ср │ ср │ ср
│ 1 │
2 │ 3 │
4 │
─────┼───────┼─────┼─────┼────┼─────┼─────┼─────┼────┼───────┼─────────────
│ │ │
│ │ │
│ │ │ │
│ │ │
│ │ │
│ │ │ │
"_____" _____________ 19
г. Подпись
____________________
Определение стойкости к цикличным
температурно-влажностным воздействиям
─────┬─────────────────────────────┬────────────────────┬──────────────────
Марка│ Среднее арифметическое │
Относительная │ Группа
стойкости
клея
│ показателей прочности │ прочность клеевых │клеевых соединений
│
образцов, МПа (кгс/см2)
│соединений образцов,│
к цикличным
├────────────────┬────────────┤ подвергнутых │
температурно-
│контрольных │после
термо-│термовлагообработке,│
влажностным
│(без термо- │влагообра- │
% │ воздействиям
│влагообработки) │ботки │ │
├────────────────┼────────────┼────────────────────┤
│ к
│ ц │ │
│ M
│ M │ A
│
│ ср
│ ср │ │
─────┼────────────────┼────────────┼────────────────────┼──────────────────
│ │ │ │
│ │ │ │
"_____" _____________ 19
г. Подпись
____________________
Определение теплостойкости и морозостойкости
─────┬───────┬─────────────────────────────┬───────────────────┬───────────
Марка│Темпе-
│ Средние арифметические │
Относительная │Группа
клея
│ратура │ показатели
прочности │ прочность клеевых
│теплостой-
│обра- │
образцов, МПа (кгс/см2) │
соединений после │кости
│ботки
├─────────┬───────────────────┤ температурных │и морозо-
│образ- │конт- │после температурных│ воздействий, % │стойкости
│цов, °C│рольных │
воздействий │ │клеевых
│ │ к
├────────┬──────────┼────────┬──────────┤соединений
│ │M │при │при
│при │при │
│ │ ср │заданной│нормаль- │заданной│нормаль- │
│ │ │темпера-│ной │темпера-│ной │
│ │ │туре │темпера- │туре A
│темпера- │
│ │ │ т │туре и │
1 │туре и │
│ │ │M │влажности │ │влажности │
│ │ │ ср │ н │ │ II │
│ │ │ │M │ │A │
│ │ │ │ ср │ │ │
─────┼───────┼─────────┼────────┼──────────┼────────┼──────────┼───────────
│ │ │ │ │ │ │
│ │ │ │ │ │ │
"_____" _____________ 19
г. Подпись
____________________