Утверждены
Директором ЦНИИСК
им. Кучеренко
Госстроя СССР
27 апреля 1981 года
РЕКОМЕНДАЦИИ
ПО ЗАЩИТЕ ДЕРЕВЯННЫХ КОНСТРУКЦИЙ,
ЭКСПЛУАТИРУЕМЫХ В СКЛАДАХ МИНЕРАЛЬНЫХ УДОБРЕНИЙ
Рекомендованы к
изданию секцией деревянных конструкций Научно-технического совета ЦНИИСК им.
Кучеренко Госстроя СССР.
Рекомендации
содержат положения по выбору и нанесению защитных покрытий для деревянных
конструкций, эксплуатируемых в складах минеральных удобрений, контролю качества
защитных покрытий и предложения по схемам обследования деревянных конструкций в
складах минеральных удобрений.
Рекомендации
разработаны лабораторией долговечности деревянных конструкций ЦНИИСК (Шолохова
А.Б., Беккер А.В.) при участии Гипронисельхоза Минсельхоза СССР (Романов А.А.,
Кочурина Л.П.), ЦНИЭПСельстроя Минсельстроя СССР (Новгородский В.И.) и
Энергожилиндустрпроекта Минэнерго СССР (Шустерман И.Д.).
При подготовке
Рекомендаций были использованы материалы исследований, проведенных в ЦНИИСК им.
Кучеренко инженером Гусевым Б.П.
Научное
редактирование выполнено Славиком Ю.Ю.
Рекомендации
предназначены для инженерно-технических работников проектных,
научно-исследовательских институтов, заводов - изготовителей деревянных
конструкций и строительно-монтажных организаций.
1. ОСНОВНЫЕ
ПОЛОЖЕНИЯ
1.1. Настоящие
рекомендации регламентируют положения по выбору и нанесению защитных покрытий
для деревянных конструкций, эксплуатируемых в складах минеральных удобрений.
1.2. Рекомендации
распространяются на несущие и ограждающие деревянные клееные, деревянные и
клеефанерные конструкции зданий складов, используемых для переработки и
хранения минеральных удобрений, в незатаренном виде в различных климатических
зонах страны.
1.3. Рекомендации
предусматривают обеспечение срока службы деревянных конструкций, эксплуатируемых
в зданиях и сооружениях складов минеральных удобрений путем применения
различных защитных покрытий.
1.4. Рекомендации
предназначаются для использования проектно-технологическими организациями, а
также организациями, изготавливающими и эксплуатирующими деревянные конструкции
зданий и сооружений с агрессивной средой минеральных удобрений.
1.5. Рекомендации
включают:
- классификацию и
основные характеристики минеральных удобрений;
- общие требования
к проектированию деревянных конструкций для складов минеральных удобрений;
- степень
агрессивного воздействия солей минеральных удобрений в зависимости от
климатических зон;
- основные
характеристики защитных материалов;
- технологию
приготовления и нанесения защитных материалов;
- мероприятия по
технике безопасности при проведении защитных работ;
- контроль качества
защитных покрытий;
- предложения по
схемам обследования конструкций в складах минеральных удобрений;
- предложения по
проведению ремонтных работ и восстановлению защитных покрытий.
Агрессивное
воздействие среды минеральных удобрений
на древесину и
фанеру
1.6. Среды
минеральных удобрений по степени воздействия на древесину и фанеру делятся на неагрессивные, слабоагрессивные, среднеагрессивные и
сильноагрессивные.
1.7. Степень
агрессивного воздействия минеральных удобрений определяется их химическим
составом, дисперсностью, гигроскопичностью, растворимостью в воде.
1.8. При
определении степени агрессивного воздействия среды минеральных удобрений
необходимо учитывать климатические условия эксплуатации складских зданий и
сооружений, характеризующиеся зонами влажности (Приложение 1).
1.9. Основные типы
минеральных удобрений, хранение которых осуществляется в незатаренном виде, их
характеристика и агрессивная составляющая даны в табл. 1.
Таблица 1
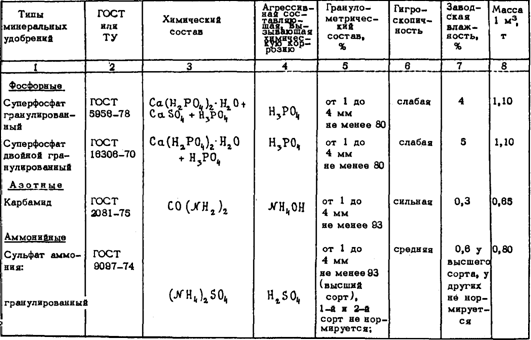
Продолжение таблицы
1
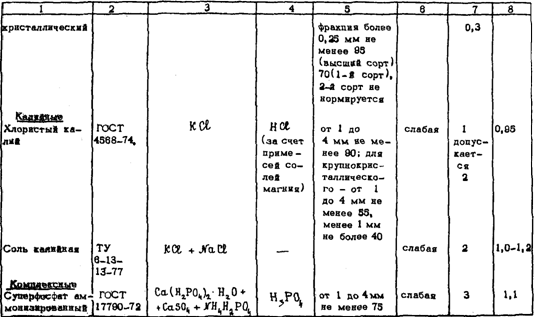
Продолжение таблицы
1
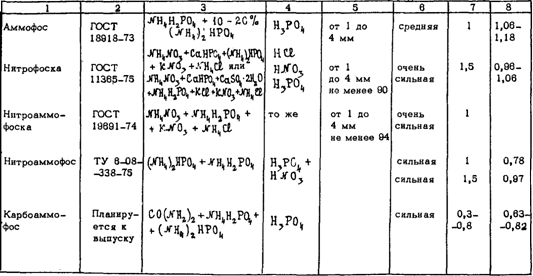
1.10. Воздействие
агрессивных сред минеральных удобрений на древесину и фанеру следует оценивать
по изменению цвета, поверхностной мацерации и по снижению прочностных
показателей древесины и фанеры в зоне коррозии (табл. 2).
Таблица 2
┌─────────────────────┬────────────┬──────────────────┬───────────────────┐
│Степень
агрессивного │ Изменение │
Поверхностная │Снижение
прочности │
│ воздействия среды │
цвета │ мацерация │<*> в зоне контакта│
│минеральных удобрений│ │ (расслоение │
со средой, % │
│ на древесину │ │ древесины) │
│
├─────────────────────┼────────────┼──────────────────┼───────────────────┤
│Неагрессивная │Без │Без изменений │ - │
│ │изменений │ │ │
│Слабоагрессивная │Небольшое │Начальное │ до 15 │
│ │ │повреждение углов
│ │
│Среднеагрессивная │Потемнение │Частичная │ от 15 до 25 │
│Сильноагрессивная │Значительное│Полная │ > 25 │
│ │потемнение │ │ │
└─────────────────────┴────────────┴──────────────────┴───────────────────┘
--------------------------------
<*>
Снижение прочности определяется на стандартных образцах (изгиб и сжатие вдоль
волокон), выпиленных в зоне контакта конструкций со средой.
1.11. При оценке
агрессивности среды минеральных удобрений на древесину и фанеру следует
руководствоваться данными табл. 3 в зависимости от влажности окружающей среды.
Таблица 3
┌───────────┬─────────────────────────────────────────────────────────────────────────────┐
│ Группы
│ Степень агрессивного воздействия среды минеральных удобрений на
древесину │
│
удобрений │ в зависимости от климатических зон
влажности │
│
├───────────────────────────┬─────────────────────────┬───────────────────────┤
│ │ сухая │ нормальная │ влажная │
│
├─────────────┬─────────────┼─────────────┬───────────┼───────────┬───────────┤
│ │ устойчиво
│ сухая │
умеренно │ умеренно │ влажная
│устойчиво │
│ │ сухая
│ │ сухая │
влажная │ │влажная │
├───────────┼─────────────┼─────────────┼─────────────┼───────────┼───────────┼───────────┤
│ 1
│ 2 │ 3
│ 4 │ 5
│ 6 │
7 │
├───────────┼─────────────┼─────────────┼─────────────┼───────────┼───────────┼───────────┤
│Фосфорные │неагрессивная│неагрессивная│неагрессивная│слабо- │слабо- │слабо- │
│ │ │ │ │агрессивная│агрессивная│агрессивная│
│Аммонийные
│неагрессивная│неагрессивная│слабо- │средне- │средне- │средне- │
│ │ │ │агрессивная │агрессивная│агрессивная│агрессивная│
│Азотные │неагрессивная│слабо-
│средне-
│средне-
│средне- │средне- │
│ │ │агрессивная │агрессивная
│агрессивная│агрессивная│агрессивная│
│Калийные │неагрессивная│неагрессивная│слабо- │средне- │средне- │средне- │
│ │ │ │агрессивная │агрессивная│агрессивная│агрессивная│
│Комплексные│неагрессивная│слабо-
│средне-
│средне-
│средне- │средне- │
│ │ │агрессивная │агрессивная
│агрессивная│агрессивная│агрессивная│
└───────────┴─────────────┴─────────────┴─────────────┴───────────┴───────────┴───────────┘
Примечание. <*> - зоны влажности даны в
соответствии с картой влажностно-климатических районов строительства
(Приложение 1).
Общие
требования к проектированию деревянных конструкций,
эксплуатируемых в
складах минеральных удобрений
1.12. Деревянные
клееные, деревянные и клеефанерные конструкции, применяемые в среде минеральных
удобрений, должны быть запроектированы и выполнены в соответствии с общими
требованиями СНиП II-25-82 "Деревянные конструкции. Нормы проектирования"
и "Руководства по изготовлению и контролю качества деревянных клееных
конструкций".
1.13. Общая
поверхность конструкций, применяемых в складах минеральных удобрений, должна
быть минимальной. Применение сквозных конструкций и конструкций, имеющих
открытые горизонтальные поверхности, не рекомендуется.
1.14. Несущие
деревянные клееные конструкции должны иметь массивное сплошное сечение.
Применение дощатых конструкций не рекомендуется.
1.15. Клеефанерные
конструкции коробчатого сечения должны быть запроектированы с учетом исключения
возможности запыления минеральными удобрениями их внутреннего пространства.
1.16. Выбор вида
защитного покрытия деревянных клееных и клеефанерных конструкций и способы
нанесения принимаются в зависимости от вида хранимых удобрений согласно
указаниям настоящих Рекомендаций.
1.17. Металлические
и железобетонные элементы должны быть надежно защищены от коррозии в
соответствии с требованиями СНиП II-28-73* "Нормы проектирования. Защита
от коррозии".
1.18. Нанесение
антикоррозионного защитного покрытия конструкций и элементов должно
производиться только в заводских условиях. После окончания монтажа должна быть
проведена антикоррозионная защита монтажных стыков.
2. ВЫБОР
ЗАЩИТНЫХ ПОКРЫТИЙ
2.1. Защитные
покрытия для деревянных конструкций складов минеральных удобрений должны
обладать:
- стойкостью к
солям минеральных удобрений;
- влагозащитными
свойствами;
- достаточной
адгезией к древесине и фанере;
- стабильностью
свойств в интервале температур от -40° до +50 °C;
- долговечностью.
2.2. Необходимость
применения защитных покрытий определяется в соответствии с табл. 3.
2.3. В устойчиво
сухой и сухой климатических зонах допускается применять деревянные клееные,
деревянные и клеефанерные конструкции без защитной обработки при условии
строгого соблюдения правил транспортировки и хранения деревянных конструкций
(см. раздел 4).
2.4. Для нормальной
и влажной климатических зон независимо от степени агрессивного воздействия
необходима защитная обработка деревянных конструкций от увлажнения и
воздействия среды покрытиями, стойкими к действию этих агрессивных сред.
2.5. Для защиты
деревянных клееных, деревянных и клеефанерных конструкций от агрессивного
действия среды минеральных удобрений рекомендуется два вида защитной обработки:
- поверхностное
нанесение лакокрасочных материалов;
- пропитка
(модификация) древесины и фанеры синтетическими смолами и мономерами, в том
числе и поверхностная.
Выбор вида
защитного покрытия определяется типом конструкций, условиями эксплуатации и
технологическими возможностями обработки.
2.6. Проведение
специальной биозащитной обработки деревянных и фанерных конструкций складов
минеральных удобрений не требуется, т.к. соли минеральных удобрений являются
антисептиками.
2.7. Для
защиты несущих деревянных конструкций, эксплуатируемых в прирельсовых,
припортовых и глубинных складах, в том числе и смешанного хранения минеральных
удобрений, следует применять лакокрасочные материалы <*> следующих видов:
- перхлорвиниловую
эмаль ХВ-785;
- сополимерные
эмали ХС-759, ХС-781, ХС-710;
-
алкидно-уретановую эмаль УРФ-1128;
- уретановый лак
УР-293.
--------------------------------
<*> Указанные
лакокрасочные материалы равноценны по стойкости к действию солей минеральных
удобрений и влаги.
Допускается
применять следующие лакокрасочные материалы:
- перхлорвиниловый
лак ХВ-784;
- сополимерный лак
ХС-724;
- эпоксидные смолы
ЭП-755, ЭП-773, ЭП-793, ЭП-56;
-
фенольно-эпоксидную эмаль - ФЛ-777;
- уретановую эмаль
- УР-49.
2.8. Для защиты
несущих деревянных конструкций, эксплуатируемых в зданиях и сооружениях,
предназначенных для хранения и переработки только аммонийных солей (кроме
селитры всех видов), помимо лакокрасочных материалов, указанных в п. 2.7,
допускается применение перхлорвиниловой эмали ХВ-1100.
2.9. При
необходимости огнезащиты несущих деревянных конструкций складов минеральных
удобрений следует применять перхлорвиниловую эмаль ХВ-5169 с расходом 600 г/м2 поверхности.
2.10. Для защиты
ограждающих конструкций (фанеры и каркаса) следует применять поверхностную
пропитку фенолоспиртами.
2.11. Для защиты
конструкций, находящихся в непосредственном контакте с минеральными удобрениями
(перегородки, подпорные стенки и др.), следует применять поверхностную пропитку
древесины и фанеры фенолоспиртами.
Допускается
применение для этих целей ацетилированной древесины.
2.12. В опорных
узлах допускается применять модифицированную метилметакрилатом древесину.
2.13. Защита торцов
несущих конструкций должна осуществляться применяемыми лакокрасочными
покрытиями (п. 2.7) при 6 - 8-кратном нанесении.
2.14. При
закреплении торцов конструкций в опорные башмаки типа "стакана"
необходимо осуществлять полную герметизацию зазора между торцом конструкции и
стенками стакана на всю высоту стакана тиоколовыми герметиками типа У-30М,
УТ-32 или эпоксидной шпаклевкой ЭП-0010.
2.15. Применение
других защитных материалов возможно только после проведения специального
комплекса испытаний по методикам, согласованным с ЦНИИСК.
3.
ТЕХНОЛОГИЯ ЗАЩИТНОЙ ОБРАБОТКИ
Основные
характеристики защитных материалов
Лакокрасочные
материалы
3.1.
Перхлорвиниловые и сополимерные эмали поставляются с завода-изготовителя в
готовом виде. Все рекомендуемые материалы, кроме ХС-759, однокомпонентные. В
эмаль ХС-759 перед нанесением вводится отвердитель N 5 в количестве 2,8 - 3,1
мас. ч. на 100 мас. ч. эмали. Отвердитель поставляется в комплекте с эмалью.
3.2. Уретановые лак
УР-293 и эмаль УР-49 - однокомпонентные системы, отверждение которых происходит
влагой воздуха, поэтому хранить их необходимо в плотно закрытых (запаянных)
емкостях.
3.3. Уретаново-алкидная
эмаль УРФ-1128 представляет собой однокомпонентную систему и поставляется в
готовом виде.
3.4. Эпоксидные
эмали представляют собой двухкомпонентные системы, состоящие из раствора
эпоксидных смол и пигментов в органических растворителях и отвердителя.
3.5. Поставка
эпоксидных эмалей осуществляется комплектно. Соотношение компонентов
указывается в паспорте на продукцию.
3.6.
Фенольно-эпоксидная эмаль ФЛ-777 поставляется комплектно в виде трех
компонентов:
I бакелитовый лак -
5 мас. ч.
II эпоксидная смола
- 2 мас. ч.
III алюминиевая
пудра - 0,5 - 2 мас. ч.
3.7. Основные
характеристики лакокрасочных материалов и технологические параметры даны в
табл. 4.
Пропиточные
составы
3.8. Фенолоспирты
представляют собой продукты конденсации фенола с формальдегидом, содержащие 50%
воды. Для повышения степени огнестойкости пропитанной древесины в фенолоспирты
вводится антипиреновая добавка в количестве 9 - 10%.
3.9. Для
производства ацетилированной древесины используется уксусный ангидрид,
прозрачная легколетучая жидкость с сильным запахом.
3.10. Метиловый
эфир метакриловой кислоты (метилметакрилат), применяемый для модификации
древесины, представляет собой прозрачную легколетучую жидкость с характерным
запахом. Для повышения огнестойкости модифицированной древесины и перевода ее в
категорию трудносгораемых материалов в пропиточный состав вводят до 30%
антипиреновой добавки.
3.11. Основные
характеристики пропиточных составов даны в табл. 5.
Таблица 5
┌───────────┬────────────┬───────┬─────────┬─────────┬─────────┬──────────┐
│Пропиточные│ ГОСТ или
│Содер- │Расход │Привес │ Глубина │ Порода
│
│ составы
│ ТУ │жание │материала│полимера
│пропитки,│древесины │
│ │ │основ-
│на 1 м3 │в │ мм
│ │
│ │ │ного │древе- │модифици-│ │ │
│ │ │веще- │сины, кг │рованной │ │ │
│ │ │ства, %│ │древе- │ │ │
│ │ │ │ │сине, % │ │ │
├───────────┼────────────┼───────┼─────────┼─────────┼─────────┼──────────┤
│Фенолспирты│ТУ │ 50
│200 - 300│ 10 - 20 │Поверх- │Хвойная и │
│ │6-05-1164-75│ │ │ │ностная │лиственная│
│ │ │ │ │ │1 - 3 │ │
│Ангидрид │ГОСТ │
100 │200 - 300│ 20 -
25 │Полная
│Хвойная и │
│уксусный │21039-75 │ │ │ │ │лиственная│
│Метил-
│ГОСТ │99,33
-│400 - 500│80 - 100 │Полная
│Лиственная│
│метакрилат
│16505-70 │ 99,82│ │ │ │ │
└───────────┴────────────┴───────┴─────────┴─────────┴─────────┴──────────┘
Герметизирующие
составы
3.12. Тиоколовый
герметик У-30М состоит из тиоколовой пасты, вулканизующего агента - пасты N 9 и
ускорителя - дифинилгуанидина (ДФГ).
3.13. Тиоколовый
герметик УТ-32 состоит из тиоколовой пасты, модифицированной эпоксидной смолой,
вулканизующей пасты N 9 и ускорителя ДФГ.
Основные
характеристики герметизирующих составов даны в табл. 6.
Таблица 6
┌──────────┬────────────┬───────┬───────────┬─────┬──────┬───────┬─────┬───────┐
│Гермети- │ГОСТ или ТУ
│Отверж-│Количество │Раст-│Время │Время │Тол-
│Расход │
│зирующие │ │дающие
│отвердителя│вори-│сушки,│полного│щина,│ на
│
│составы │ │агенты │ мас. ч., │тель │ ч
│отверж-│мм │ 1 м2, │
│ │ │ │100 мас. ч.│<**>
│ │дения, │ │
кг │
│ │ │ │ герметика │ │ │
сут │ │ │
├──────────┼────────────┼───────┼───────────┼─────┼──────┼───────┼─────┼───────┤
│Тиоколовые│ │ │ │ │ │ │ │ │
│герметики:│ │ │ │ │ │ │ │ │
│<*> │ │ │ │ │ │ │ │ │
│У-30М │ГОСТ │Паста 9│ 6 - 9
│ Р-4 │ 24 │
7 │0,7 -│1,2 -
2│
│ │13489-68 │
ДФГ │ 0,2 - 0,5
│ │ │ │
1,5│ │
│УТ-32 │ТУ │Паста 9│ 9 - 12
│ Р-4 │ 24 │
7 │0,7 -│1,2 -
2│
│ │38-105462-72│ ДФГ
│ 0,2 - 0,5 │ Р-5 │ │ │
1,5│ │
│Эпоксидная│ГОСТ
│Отвер- │ 8,5 │Р-4, │ 24
│ 3 - 5 │0,7 -│1,0 -
│
│шпаклевка
│10277-76 │дитель
│ │ Р-5
│ │ │ 1│
1,5│
│ЭП-0010 │ │1 │ │ │ │ │ │ │
└──────────┴────────────┴───────┴───────────┴─────┴──────┴───────┴─────┴───────┘
--------------------------------
<*>
Тиоколовые герметики поставляются в комплекте с отверждающими агентами. Точное
их соотношение указывается в паспорте на данную партию.
<**>
Допустимое количество вводимого растворителя для снижения вязкости герметика -
10 - 15%.
Приготовление
защитных составов
3.14. Все защитные
материалы должны иметь паспорт завода-изготовителя и соответствовать ГОСТу или
ТУ.
3.15. Приготовление
лакокрасочных составов должно выполняться в следующей последовательности:
разбавление
лакокрасочных материалов;
смешение
компонентов системы (в случае многокомпонентности лакокрасочных материалов);
фильтрование
лакокрасочных материалов;
определение рабочей
вязкости.
3.16. Эмали перед
употреблением необходимо перемешать до получения однородного материала без
осадка пигмента. Лаки после удаления поверхностной пленки перемешивать не
рекомендуется. Их следует осторожно слить в смеситель для разведения. Остаток с
осадком является отходом.
3.17. Фенолоспирты
для пропитки древесины и фанеры перед употреблением разбавляют до требуемой
плотности водой.
3.18.
Герметизирующие составы готовят путем последовательного введения в пасту
отвердителя и ускорителя.
3.19. После
приготовления рабочих составов необходимо осуществить контроль их качества и
соответствие ряда показателей данным ГОСТ или ТУ.
Подготовка
поверхности конструкций, подлежащих защите
3.20. Поверхность
деревянных конструкций, подлежащих защите, должна удовлетворять следующим
требованиям:
- влажность
элементов, подлежащих защитной обработке, не должна превышать 12 +/- 2%;
- поверхность
должна быть очищена от стружки, пыли и всякого рода загрязнений, которые могут
служить причиной снижения адгезионной прочности или снижать привес пропиточного
состава;
- жировые
загрязнения должны быть удалены растворителями (бензином, уайт-спиритом и др.);
- на поверхности
деревянных элементов не должно быть наплывов клея;
- после
механической обработки высота неровностей поверхности, предназначенных для
прозрачной отделки, не должна превышать 320 мк, а непрозрачной - 800 мк;
- острые кромки
должны быть закруглены радиусом более 5 мм;
- сверление
отверстий под болты, штыри, выборку пазов и др. следует осуществлять до
нанесения защитного покрытия или пропитки. При необходимости дополнительной
механической обработки на строительной площадке обнаженные места должны быть
покрыты лакокрасочным материалом или эпоксидной шпаклевкой.
Нанесение
защитных покрытий
3.21. Основными
способами нанесения защитных лакокрасочных материалов на поверхность
конструкций являются:
- пневматическое
распыление;
- безвоздушное
распыление (за исключением уретановых материалов);
- нанесение кистью
или валиком.
3.22. Способ
механизированной обработки выбирают с учетом объема работ, наличия
оборудования, вида и свойств применяемого защитного
материала, условий нанесения и т.д.
3.23. Для защиты
конструкций длиной свыше 1800 мм и сечением более 300 см2
должны быть использованы механизированные способы нанесения. Ручное нанесение
кистью или валиком применяется при малых объемах работ, невозможности
применения механизированных способов нанесения, при окраске дефектных мест
после механизированного нанесения и др.
3.24.
Перечень и технические характеристики оборудования для механизированного
нанесения лакокрасочных материалов приведены в "Методических рекомендациях
по применению прозрачных лаковых покрытий при комплексной защите клееных
деревянных конструкций для сельского хозяйства", ЦНИИСК им. Кучеренко, М.,
1976 г.
3.25. Сушку
лакокрасочных покрытий осуществляют при нормальной 18 - 23 °C или повышенной 40
- 65 °C температуре. Режимы послойной и окончательной сушки лакокрасочных
покрытий приведены в табл. 4.
3.26. При выборе
способа сушки необходимо учитывать:
- вид применяемого
лакокрасочного материала;
- размеры
конструкций;
- технологические
ограничения по температурному режиму.
3.27. При сушке
перхлорвиниловых материалов не рекомендуется использовать температуру выше 60
°C. Для уретановых материалов сушка при повышенной температуре не допускается.
3.28. Перечень и
технические характеристики оборудования для сушки лакокрасочных покрытий
приведены в "Методических рекомендациях" (см. п. 3.24).
Пропитка
древесины и фанеры фенолоспиртами
3.29. Пропитку
фанеры и элементов каркаса фенолоспиртами следует осуществлять в автоклавах под
давлением 0,7 - 1,3 МПа в течение 0,5 - 6 часов или в ваннах - 36 - 48 часов.
Температура раствора 18 - 25 °C.
3.30. Сушку и
полимеризацию фенолоспиртов целесообразно проводить в сушильных камерах или с
применением гидрофобной жидкости по следующему режиму:
- сушка при 40 °C -
24 часа,
- полимеризация при
105 - 120 °C - 2 - 4 часа,
- охлаждение до 40
°C - 1 час.
3.31. Все операции
по обработке фанеры и древесины фенолоспиртами необходимо осуществлять в
контейнерах с регулируемыми зажимными устройствами. Технологический регламент
по пропитке древесины и фанеры фенолоспиртами дан в Приложении 2.
3.32.
Ацетилированная древесина и древесина, модифицированная метилметакрилатом,
изготавливается на опытных установках и поставляется в готовом виде по ГОСТ
9629-80 "Заготовки из модифицированной древесины. Марки и размеры" и
ГОСТ 24329-80 "Древесина модифицированная. Способы модификации".
Контроль
качества защитных материалов и покрытий
3.33. Рабочие
лакокрасочные составы должны приготавливаться из материалов, имеющих паспорт
завода-изготовителя; хранение лакокрасочных материалов должно осуществляться в
соответствии с ГОСТ 9980-62.
3.34.
Приготовленные лакокрасочные составы перед нанесением должны контролироваться в
заводской лаборатории по следующим показателям:
- рабочая вязкость
(ГОСТ 8420-74);
- расход
лакокрасочного материала в зависимости от способа нанесения (МРТУ 6-10-699-67);
- время и степень
высыхания покрытия (ГОСТ 19007-73);
- содержание
летучих и нелетучих твердых и пленкообразующих веществ (ГОСТ 17537-72).
Результаты
испытаний должны быть внесены в журнал и храниться в лаборатории.
3.35. Качество
лакокрасочных покрытий контролируется по следующим показателям:
- соответствие
декоративного вида покрытий требованиям ГОСТ 9.032-74;
- адгезия пленки
покрытия к поверхности (ГОСТ 15140-78);
- визуальное
выявление дефектов покрытия;
- толщина покрытия:
прозрачного по ГОСТ 13639-75, непрозрачного - по ГОСТ 14644-75.
Основные
правила по технике безопасности
и охране труда при
работе с лакокрасочными материалами
3.36. При
проектировании отделений по защите клееных конструкций и проведении обработки
клееных элементов необходимо учитывать "Правила техники безопасности и
пожарной безопасности, производственной санитарии для окрасочных цехов" и
требования "Санитарных норм проектирования промышленных предприятий"
(СН 245-71).
3.37.
Проектирование складов хранения защитных материалов и выбор мест их
расположения необходимо осуществлять в соответствии с "Нормами и
техническими условиями проектирования складских предприятий и хозяйств для хранения легковоспламеняющихся и горючих
жидкостей" (НиТУ 108-56).
3.38. Проведение
работ по защите деревянных клееных конструкций и их элементов должно
осуществляться в помещениях, оборудованных приточно-вытяжной вентиляцией. В
случае неисправности вентиляционного оборудования необходимо прекратить работы,
связанные с нанесением защитных материалов, содержащих вредные вещества.
3.39. Концентрация
вредных паров в воздухе не должна превышать оптимальное значение по
"Санитарным нормам проектирования промышленных предприятий". Контроль за концентрацией паров должен осуществляться
ежедневно при помощи газоанализаторов.
3.40. При работе с
лакокрасочными материалами, содержащими ксилол, бензол, уайт-спирит,
бутилацетат, ацетон, необходимо защитить кожу работающих
от соприкосновения с применяемыми составами. Для этой цели могут быть
использованы комбинезоны, резиновые перчатки, респираторы, защитные очки и др.
3.41. Тара, в
которой хранятся защитные материалы, должна быть герметически закрыта и иметь
обозначение состава или его наименование, номер партии, наименование
завода-изготовителя. Хранение и транспортирование защитных материалов в
открытой или стеклянной таре не допускается.
3.42. Тара порожняя
из-под растворителей, смол и лакокрасочных материалов должна немедленно
удаляться из рабочего помещения и храниться на специальных площадках.
3.43. При работе с
лакокрасочными материалами необходимо соблюдать меры предосторожности,
предусмотренные для легковоспламеняющихся материалов.
3.44. В помещениях
для приготовления и нанесения лакокрасочных материалов не разрешается
производить сварочные и другие работы с открытым огнем, категорически
запрещается курение.
3.45. Прием пищи в
местах приготовления, хранения защитных материалов и проведения операций по
нанесению составов не допускается.
3.46. Лица,
выполняющие работы, связанные с приготовлением и нанесением защитных
материалов, должны проходить регулярный (не реже 2-х раз в месяц) инструктаж.
4. ХРАНЕНИЕ И ТРАНСПОРТИРОВКА ЗАЩИЩЕННЫХ ЭЛЕМЕНТОВ
ДЕРЕВЯННЫХ
КОНСТРУКЦИЙ
4.1. После
проведения защитной обработки деревянные клееные конструкции должны быть
выдержаны на складе готовой продукции не менее 7 - 10 суток.
4.2. При хранении
на складе готовой продукции между окрашенными элементами должны располагаться
прокладки.
4.3.
Транспортировка готовых элементов к месту монтажа должна осуществляться в
упакованном виде, предохраняющем покрытия от повреждений и увлажнения.
4.4. Транспортные
средства должны быть оборудованы устройствами и приспособлениями для
предохранения защитных покрытий от механического повреждения и загрязнения
(козырьки, прокладки, фартуки, накидки).
4.5. Погрузку и
разгрузку окрашенных элементов конструкций следует производить, избегая
повреждений покрытий.
4.6. Хранение
готовых элементов на монтажной площадке должно осуществляться в упакованном
виде в специальном помещении или под навесом.
5. ОСНОВНЫЕ
МЕРОПРИЯТИЯ ПО ТЕХНИЧЕСКОЙ ЭКСПЛУАТАЦИИ
ДЕРЕВЯННЫХ
КОНСТРУКЦИЙ В СКЛАДАХ МИНЕРАЛЬНЫХ УДОБРЕНИЙ
5.1. Лица,
ответственные за эксплуатацию зданий и сооружений для минеральных удобрений,
должны участвовать в приемке их в эксплуатацию и документально оформлять
наличие и состояние антикоррозионной защиты деревянных клееных и клеефанерных
конструкций, соединительных элементов и деталей в виде акта по рекомендуемой
форме 1.
5.2. Текущие
обследования, состоящие из визуального осмотра, определения сохранности
антикоррозионной защиты и необходимости ее ремонта или возобновления, должны
проводиться не реже одного раза в три месяца.
5.3. Здания,
сооружения и отдельные конструкции должны подвергаться периодическому
инструментальному обследованию не реже одного раза в пять лет с привлечением
специалистов в области деревянных конструкций и их защиты.
5.4. В процессе инструментального
обследования должно быть выполнено:
- определение
температурно-влажностных параметров воздуха внутри помещений;
- определение
влажности древесины конструкций;
- определение
степени запыленности конструкций минеральными удобрениями;
- отбор проб для
лабораторного анализа прочности, засоленности и поверхностной мацерации
древесины конструкций;
- лабораторные
исследования образцов, изготовленных из отобранных проб;
- общий осмотр
деревянных конструкций (отклонения из плоскости, величина прогибов,
выпучивание, явные разрушения от перегрузок и т.п.).
5.5. В случае
аварийного состояния конструкций должно производиться специальное
инструментальное обследование, имеющее целью выявление причин состояния
аварийности, выдачу решения о целесообразности замены или ремонта конструкций и
элементов и разработку мероприятий по временному усилению аварийных мест.
5.6. При
эксплуатации зданий и сооружений для хранения и транспортировки минеральных
удобрений с особой тщательностью должны соблюдаться общие положения и
требования по технической эксплуатации в части сохранности и своевременного
ремонта кровельных покрытий.
5.7. Данные всех
обследований должны фиксироваться в журналах эксплуатации сооружения по
прилагаемым формам 2, 3 и 4.
Предложения
по проведению ремонтных
и восстановительных
работ лакокрасочных покрытий
5.8. После монтажа
деревянных конструкций должен быть произведен тщательный осмотр ее поверхности
и выявлены все дефекты покрытия.
5.9. При
обнаружении дефектов (царапин, трещин, повреждений) необходимо провести
возобновление покрытия в следующем порядке:
- зашкурить
дефектный участок;
- нанести требуемое
количество слоев покрытия в соответствии с приведенной технологией нанесения и
с соблюдением режимов сушки.
5.10. При
обнаружении частичного разрушения покрытия, происшедшего в процессе
эксплуатации, следует немедленно принять меры к восстановлению покрытия.
5.11. При ремонте
(восстановлении) покрытия поврежденные участки поверхности конструкций должны
быть полностью освобождены от старого лакокрасочного материала, очищены и со
всей тщательностью подготовлены к повторному нанесению покрытия.
5.12. Удаление
старого лакокрасочного покрытия, если оно в результате отслоения или
растрескивания плохо держится на поверхности конструкций, производится
механическим способом - щетками или скребками. Более плотно держащиеся покрытия
рекомендуется удалять смывками.
5.13. Для удаления
покрытий холодной сушки рекомендуется применять смывку СД специальную (ТУ
6-10-1088-76) или АФТ-1 (ТУ 6-10-1202-71). Смывки наносятся на поверхность
краскораспылителем, кистью или тампоном.
На 1 м2 поверхности требуется 170 г смывки СД специальной или 150
г АФТ-1. Скорость воздействия на покрытие составляет соответственно 3 и 20 мин.
Смывки наносятся и
выдерживаются до тех пор, пока покрытие размягчится, набухнет или вспучится.
После этого покрытие удаляют шпателем или металлической щеткой.
5.14. После
применения смывок поверхность конструкции необходимо выдержать не менее суток
при температуре не ниже 15 - 17 °C для удаления различных компонентов смывок.
5.15. На вычищенные
и высушенные поверхности конструкции наносится соответствующее покрытие с
соблюдением всех требований.
Форма N 1
АКТ
о
приемке антикоррозийной защиты строительных конструкций
1. Эксплуатирующая организация
____________________________________________
___________________________________________________________________________
2. Здание (сооружение)
____________________________________________________
___________________________________________________________________________
3. Агрессивная среда
______________________________________________________
___________________________________________________________________________
(вид
хранимых удобрений, способ хранения и т.п.)
___________________________________________________________________________
4. Сведения об антикоррозионной защите
____________________________________
а) вид защиты
_____________________________________________________________
(пропитка,
покрытие и т.п.)
___________________________________________________________________________
б) защитный антикоррозионный состав
_______________________________________
___________________________________________________________________________
(наименование, марка, число слоев, способ
___________________________________________________________________________
нанесения по паспорту конструкции)
в) дата окончания антикоррозионных работ
__________________________________
г) дата ближайшего текущего осмотра конструкций
___________________________
___________________________________________________________________________
(не позднее чем через три
месяца)
Главный
инженер
Руководитель
строительной
эксплуатационного отдела
организации
заказчика
Дата "
" ________________ 19__ г.
Форма N 2
ЖУРНАЛ
ТЕКУЩИХ ИССЛЕДОВАНИЙ
Наимено-
вание
объекта
|
Дата
обсле-
дования
|
Вид
храни-
мого
удобре-
ния
|
Параметры
воздуха
|
Состояние
анти-
коррозионной
защиты
|
Отметка
о
дефектах
покрытия
и необхо-
димые
мероприя-
тия по
ремонту и
восстано-
влению
|
Сведения
о
ремонтных
и восста-
новитель-
ных меро-
приятиях
и дата их
проведе-
ния
|
|
t,
°C
|
фи,
%
|
|
дере-
вянных
конст-
рукций
и эле-
ментов
|
соеди-
нитель-
ных
эле-
ментов
|
|
1
|
2
|
3
|
4
|
5
|
6
|
7
|
8
|
9
|
|
Форма N 3
ЖУРНАЛ ИНСТРУМЕНТАЛЬНЫХ
ОБСЛЕДОВАНИЙ
Наименование
объекта _____________________________________
Дата
об-
сле-
дова-
ния
|
Наи-
мено-
вание
кон-
струк-
ций и
эле-
ментов
|
Срок
эксплу-
атации
в годах
|
Параметры
воздуха
|
Вид
хра-
нимого
удобре-
ния и
характер
контакта
с кон-
струк-
циями
|
Степень
запылен-
ности
конструк-
ций и
элементов
минераль-
ных удоб-
рений
|
Влаж-
ность
древе-
сины,
%
|
Состо-
яние
анти-
кор-
рози-
онной
защи-
ты
|
Состо-
яние
кон-
струк-
ций
и эле-
ментов
|
Отметка
об
отборе
проб
для
лабо-
ратор-
ных
иссле-
дований
|
t,
°C
|
фи,
%
|
1
|
2
|
3
|
4
|
5
|
6
|
7
|
8
|
9
|
10
|
11
|
Форма N 4
ЖУРНАЛ ЛАБОРАТОРНЫХ
ИССЛЕДОВАНИЙ
Наименование объекта ______________________________________
Данные
о
пробах,
отобран-
ных
из кон-
струкций
и эле-
ментов
|
Порода
древе-
сины
|
К-во
образ-
цов,
изго-
тов-
ленных
из
проб
|
Результаты
механических
испытаний
|
Глу-
бина
по-
верх-
ност-
ной
маце-
рации
|
Толщи-
на
защит-
ного
покры-
тия,
мкм
|
Оценка
адгезии
защит-
ных
покры-
тий
к дре-
весине
|
Оценка
влаго-
прони-
цаемос-
ти
покры-
тия
|
Приме-
чание
|
сжа-
тие
|
из-
гиб
|
ска-
лыва-
ние
|
1
|
2
|
3
|
4
|
5
|
6
|
7
|
8
|
8
|
10
|
11
|
Приложение
1
СХЕМАТИЧЕСКАЯ
КАРТА ВЛАЖНОСТНО-КЛИМАТИЧЕСКИХ ХАРАКТЕРИСТИК
РАЙОНОВ
СТРОИТЕЛЬСТВА
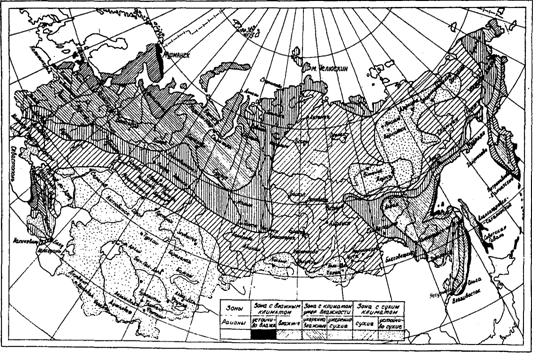
Приложение
2
ТЕХНОЛОГИЧЕСКИЙ
РЕГЛАМЕНТ
ПОВЕРХНОСТНОЙ
МОДИФИКАЦИИ ДРЕВЕСИНЫ И ФАНЕРЫ ФЕНОЛОСПИРТАМИ
Настоящий регламент
распространяется на технологический процесс модификации строительных деталей из
древесины и фанеры фенолоспиртами с целью повышения био-
и химстойкости, а также снижения водо- и влагопоглощения древесных материалов.
Модификации
подлежат строительные детали, изготовленные из древесины хвойных пород по ГОСТ
8486-66, не ниже III сорта, и березы по ГОСТ 2695-71, не ниже II сорта, а также
из фанеры по ГОСТ 3916-69: для химически агрессивных сред марки ФСФ - не ниже
сорта АВ/В; а для условий с повышенной влажностью марки ФК - не ниже сорта В/ВВ.
Строительные детали
перед процессом модификации должны иметь законченную механическую обработку.
Для модификации применяют фенолоспирты, которые должны отвечать ТУ
6-05-1164-75. В качестве сушильного агента и дополнительного гидрофобизатора
применяют керосино-газойлевую фракцию нефти. Основные
виды сырья и материалов, применяемые для осуществления технологического
процесса, приведены в табл. 1.
Таблица 1
┌──────────────────────────┬───────────────┬──────────────────────────────┐
│
Наименование материалов │ ГОСТ или ТУ
│ Показатели, обязательные │
│ │ │ для проверки │
├──────────────────────────┼───────────────┼──────────────────────────────┤
│ 1 │ 2
│ 3 │
├──────────────────────────┼───────────────┼──────────────────────────────┤
│Детали
строительные │ГОСТ
16588-79 │Влажность древесины перед │
│из
древесины хвойных
│
│пропиткой
│
│и
лиственных пород │ │ │
│Фенолоспирты │ТУ
6-05-1164-75│Плотность, вязкость, сухой
│
│ │ │остаток │
│Керосино-газойлевая
│ГОСТ 3900-47
│Плотность
│
│фракция
нефти │ГОСТ
6258-52 │Вязкость │
│ │ГОСТ
4333-48 │Температура вспышки │
└──────────────────────────┴───────────────┴──────────────────────────────┘
Процесс пропитки
осуществляют в пропиточном автоклаве, представляющем собой цилиндрический сосуд
со сферическими днищами. Одно из днищ глухое, другое - съемная крышка,
подвешенная к автоклаву на петлях и оборудованная клиновым запорным
устройством. Крышка должна открываться и закрываться дистанционно сжатым
воздухом. Она должна быть оборудована блокировочным устройством, предотвращающим
возможность открывания крышки при наличии в автоклаве жидкости или давления
свыше 0,1 МПа.
Пропиточный
автоклав должен быть рассчитан на рабочее давление 1,3 МПа (12 ати).
Маневровый цилиндр
по устройству повторяет пропиточный автоклав, отличаясь от последнего
отсутствием съемочной крышки. Он устанавливается над пропиточным автоклавом и в
период загрузки и выгрузки древесины используется как емкость для хранения
фенолоспиртов.
Рабочее давление -
0,7 МПа.
Мерник -
вертикальный герметически закрытый цилиндрический сосуд, емкость,
обеспечивающая поглощение фенолоспиртов при двух и более пропитках. Рабочее
давление - 1,3 МПа.
Вакуум-насос
предназначен для создания вакуума до 0,01 МПа в пропиточном и маневровом
автоклавах.
Вакуумирование
древесины должно производиться через поверхностный конденсатор.
Расходная емкость
объемом до 50 м3, в которую подаются фенолоспирты из баков хранения,
предназначена для подачи фенолоспиртов в маневровый цилиндр и мерник. Сжатый
воздух в мерник или пропиточный автоклав должен подаваться от соответствующих
аккумуляторов компрессорной станции. Автоклавы и мерник должны быть снабжены
предохранительными клапанами, отрегулированными на максимальное рабочее
давление, контрольно-измерительными приборами, регистрирующими температуру, величину
давления, а также указателями уровня жидкости в сосуде.
Каждый из указанных
сосудов должен быть снабжен техническими приборами контроля (манометры,
вакуумметры, термометры). Показатели приборов дублируются на щите управления.
Металлическая ванна
для пропитки выполняется из листовой стали марки Ст3 ГОСТ 14637-69, толщиной 5
- 6 мм, с крышкой. Размеры ванны определяются из расчета объема загрузки.
Например, для пропитки фанеры размерами 1500 x 1500 мм ванна с учетом размеров
стяжного устройства должна иметь минимальные внутренние размеры: длина - 2200
мм, ширина - 1300 мм и высота - 2200 мм. Поддон для стока фенолоспиртов после
пропитки должен иметь размеры ванны по длине и ширине, а по высоте 100 - 150
мм.
В качестве
приспособления для предотвращения коробления лесоматериалов в процессе
модификации служит стяжное устройство - контейнер. Стяжное устройство состоит
из двух накладок, соединяемых между собой болтами с пружинами.
Дополнительно
фанера или пиломатериалы фиксируются от смещений в накладках фиксаторами.
Одновременно
стяжное устройство должно выполнять функцию противовсплывного устройства.
Укладка материалов в стяжное устройство должна производиться на прокладках.
Прокладки,
рекомендуемые при модификации:
- фанеры -
металлические, толщиной не менее 3 мм, шириной 20 мм;
- пиломатериалов -
деревянные, обшитые с двух сторон жестью, шириной 40 - 50 мм, толщиной: при
сушке в гидрофобной жидкости не менее 10 мм, а в лесосушилке - 25 мм.
Длина прокладок
должна превышать ширину пакета материалов на 50 мм. Так, при ширине пакета
фанеры 1500 мм, минимальная длина прокладок должна быть 1550 мм.
Для сушки и
отверждения древесины, пропитанной фенолоспиртами, в воздушной среде должны
применяться скоростные высокотемпературные лесосушилки, обеспечивающие нагрев древесины
до 100 - 120 °C.
Для сушки,
полимеризации и придания дополнительной гидрофобизации древесины служит
автоклавная установка, которая состоит из автоклава, работающего при давлении
0,1 МПа, маневрового бака-подогревателя, расходного бака холодного сушильного
агента, конденсатора, разделительного бака, циркуляционного насоса и системы
трубопроводов.
Процесс модификации
включает:
- подготовку сырья
и материалов,
- пропитку
фенолоспиртами,
- сушку и
полимеризацию лесоматериалов, пропитанных фенолоспиртами.
Перед началом
пропитки определяют влажность материала. Предпропиточная влажность строительных
деталей из древесины не должна превышать 15 +/- 3%, а фанеры - 8 +/- 2%.
Перед загрузкой в
пропитку детали укладывают в стяжное устройство на прокладки через каждый ряд.
Прокладки должны располагаться поперек волокон древесины. Количество прокладок
должно обеспечивать формонеизменяемость материала в процессе модификации, но не
менее 5 штук на каждый ряд.
Пропитка
строительных деталей методом вымачивания в ваннах должна проводиться при
температуре фенолоспиртов 20 +/- 3 °C, а при автоклавной пропитке минимальная
температура фенолоспиртов допускается 15 °C. Во избежание отверждения
фенолоспиртов в процессе пропитки повышение температуры их при обоих способах
пропитки свыше 25 °C не допускается.
Загрузку деталей на
пропитку в ванну или автоклав необходимо производить в стяжном устройстве. В
каждую загрузку закладывают не менее трех контрольных образцов.
При пропитке
вымачиванием слой фенолоспиртов над деталями, загруженными в ванну, должен быть
не менее 10 см. Продолжительность вымачивания строительных деталей из фанеры не
менее 36 и не более 48 часов, а из пиломатериалов - от 6 до 10 суток. После
окончания процесса пропитки в ванне пропитанные детали
для стока фенолоспиртов выдерживают над ванной не менее 1 часа, а затем
устанавливают на поддон, где выдерживают еще не менее 1 часа. Собранные в поддоне фенолоспирты сливают в пропиточную
ванну.
Автоклавную
пропитку деталей из фанеры проводят по способу "давление", а из
пиломатериалов - "вакуум-давление". Режимы пропитки представлены в
табл. 2.
Таблица 2
┌───────────────────────────────────────────┬─────────────────────────────┐
│ Операции │ Продолжительность
операции, │
│
│ час, при пропитке деталей,
│
│
│ изготовленных
из: │
│
├──────────────┬──────────────┤
│
│ фанеры │пиломатериалов│
├───────────────────────────────────────────┼──────────────┼──────────────┤
│Создание
и выдержка вакуума 0,01 - 0,02 МПа│
- │ 0,5
│
│Создание
и выдержка жидкостного давления:
│ │ │
│ 0,7 - 0,9 МПа или │ 0,5 - 1,0
│ 6,0 │
│ 0,9 - 1,3 МПа │ 0,5
│ 5,0 │
│Технологическая
выдержка в автоклаве │ 0,5
│ 0,5 │
│пропитанной
древесины для стока
│ │ │
│фенолоспиртов │ │ │
└───────────────────────────────────────────┴──────────────┴──────────────┘
После пропитки
детали в стяжном устройстве направляют на площадку для атмосферной сушки или в
камеру для сушки и полимеризации.
Атмосферную сушку
пропитанных деталей осуществляют в стяжном устройстве на площадке, защищенной
от атмосферных осадков и прямой солнечной радиации, при температуре не ниже 15
°C до влажности 10 +/- 2%.
В зависимости от
температуры окружающего воздуха продолжительность атмосферной сушки для деталей
из фанеры может составлять 20 +/- 5 суток, а из пиломатериалов в зависимости от
поперечного сечения - от 30 до 50 суток.
Последующую
полимеризацию (отверждение) фенолоспиртов проводят в камере или в гидрофобной
жидкости при температуре:
100 °C - 4 час,
110 °C - 3 час,
120 °C - 2 час.
Сушку и
полимеризацию пропитанных фенолоспиртами деталей в лесосушильной камере или
гидрофобной жидкости осуществляют в одном технологическом процессе, по режимам,
представленным в табл. 3.
Таблица 3
┌────────────────────────────────────────────┬────────────────────────────┐
│ Операции │Продолжительность
операции, │
│
│час, при сушке-полимеризации│
│
│ деталей, изготовленных из: │
│ ├───────────┬────────────────┤
│
│ фанеры │ пиломатериалов │
├────────────────────────────────────────────┼───────────┼────────────────┤
│ 1 │ 2
│ 3 │
├────────────────────────────────────────────┼───────────┼────────────────┤
│Сушка
при: 40 +/- 5 °C
│ 24 │ 12
│
│ 50 +/- 5 °C │ -
│ 12 │
│Подъем
температуры сушильного агента
│ - │ 6
│
│до
120 °C по 10 - 15° в час
│ │ │
│То
же, по 20 - 40° в час
│ 2 - 3 │
- │
│Отверждение
при 120 +/- 2 °C
│ 2 │ 2
│
│Конечная
термообработка путем снижения
│ 2 - 3 │
2 - 3 │
│температуры
в камере или в автоклаве
│ │ │
│по
20 - 30°/ч до 60 - 80 °C
│ │ │
│Выдержка
в камере, автоклаве или в
│ 5 - 6 │
6 - 8 │
│остывочном
отделении до снижения температуры│ │ │
│материала
40 °C и ниже
│ │ │
└────────────────────────────────────────────┴───────────┴────────────────┘
Примечание. При
невозможности в сушильном устройстве достижения температуры отверждения 120 °C
продолжительность этой операции при температуре 100 - 110 °C удлиняется до 3 -
4 ч.
Качество
модификации характеризуется общим поглощением фенолоспиртов в кг/м3 и глубиной пропитки фенолоспиртами в мм.
Общее поглощение
фенолоспиртов (П) определяют по каждой партии строительных деталей, загружаемых
в ванну или автоклав, по формуле:
, (1)
где
и
- масса деталей (контрольных) до и после
пропитки, кг;
V - объем партии
деталей, м3;
или
, (2)
где Q - объем
фенолоспиртов, поглощенных партией деталей в процессе пропитки, м3, замеренный:
- при автоклавной
пропитке - по мернику,
- при вымачивании -
в ванне;
- плотность фенолоспиртов при 20 °C, кг/м3.
Дополнительно общее
поглощение гидрофобной жидкости при сушке-полимеризации
определяют по формуле
, (3)
где
- объем жидкости, поглощенной древесиной в
процессе обработки, замеренный по убыли ее в расходном баке холодного
сушильного агента, м3;
- плотность гидрофобной жидкости, кг/м3.
Общее поглощение
фенолоспиртов должно быть при модификации деталей, изготовленных из:
- фанеры - не менее
200 кг/м3;
- пиломатериалов -
не менее 100 кг/м3.
Дополнительное
поглощение гидрофобной жидкости не нормируется.
Глубина
проникновения фенолоспиртов в мм должна быть не менее при пропитке деталей,
изготовленных из:
- фанеры:
по наружному шпону
- сквозная,
по торцам листов -
1 мм;
- пиломатериалов:
по заболони - 3 мм,
по ядру и спелой
древесине - 0,5 мм.