Утверждены
Директором ЦНИИСК
им. В.А. Кучеренко
2 октября 1981 года
РЕКОМЕНДАЦИИ
ПО ПРИМЕНЕНИЮ МАТЕРИАЛОВ КОМПЛЕКСНОГО ДЕЙСТВИЯ
ДЛЯ ЗАЩИТЫ ДЕРЕВЯННЫХ КОНСТРУКЦИЙ
Рекомендованы к
изданию секцией деревянных конструкций научно-технического совета ЦНИИСК им.
Кучеренко.
Рекомендации
содержат сведения о материалах комплексного действия, применяемых для защиты
деревянных конструкций от увлажнения, биоповреждения и возгорания.
Рекомендации
разработаны лабораторией долговечности деревянных конструкций ЦНИИСК им.
Кучеренко (кандидатом технических наук Мышеловой Г.Н., инж. Костиной Г.И.) под
общей редакцией канд. техн. наук Славика Ю.Ю.
В разработке
Рекомендаций участвовали проф. Горшин С.Н. и канд. техн. наук Максименко Н.А.
(ВНИИдрев, Сенежская лаборатория консервирования древесины); кандидаты техн.
наук Шолохова А.Б., Сорин В.С., Васильева Н.Ф., Ладыгина И.Р., канд. биол. наук
Мазур Ф.Ф., инженеры Абрамушкина Е.А., Сардонникова Т.Ф. (ЦНИИСК им.
Кучеренко); канд. техн. наук Василевская П.В. (ЛЛТА им. Кирова); кандидаты
техн. наук Колганова М.Н. и Левитес Ф.А. (ВНИИПО МВД СССР); канд. техн. наук Свистунова
Н.М. (НПО "Лакокраспокрытие"); канд. хим. наук Эрмуш Н.А. (Институт
химии древесины АН ЛатвССР); канд. хим. наук Покровская Е.Н., инж. Никифорова
Т.П. (МИСИ им. Куйбышева); канд. хим. наук Родэ В.В., канд. техн. наук Костюк
В.А. и инж. Фонская Н.Г. (ИГИ).
Рекомендации
предназначены для инженерно-технических работников проектных,
научно-исследовательских институтов, заводов - изготовителей деревянных
конструкций.
1. ОБЩИЕ
ПОЛОЖЕНИЯ
1.1. Рекомендации
разработаны в развитие положений главы СНиП III-19-75 "Деревянные
конструкции. Правила производства и приемки работ", а также главы СНиП
II-25-80 "Деревянные конструкции. Нормы проектирования".
1.2. Рекомендации
распространяются на составы, предназначенные для комплексной защиты деревянных,
в том числе клееных, конструкций от увлажнения, биоразрушения и возгорания.
1.3. В
Рекомендациях рассмотрены составы, обладающие био-, огнезащитными свойствами,
огне- и влагозащитными свойствами, био- и влагозащитными и био-, огне- и влагозащитными
свойствами.
1.4. В
Рекомендациях приведены технические характеристики защитных составов, уровень
их защитной способности, технология защитной обработки (приготовление рабочих
растворов, технологические параметры различных способов нанесения и сушки);
изложена последовательность защитной обработки, обеспечивающей комплексную
защиту конструкций.
1.5. В
Рекомендациях приведены основные требования по технике безопасности при
хранении, приготовлении и нанесении защитных составов.
1.6. Рекомендации
позволяют осуществить выбор составов для защиты конструкций с учетом условий их
эксплуатации.
1.7. Рекомендации
предназначены для инженерно-технического персонала предприятий, изготавливающих
деревянные конструкции, а также для сотрудников проектных и научно-исследовательских
институтов, занимающихся вопросами защиты деревянных конструкций и изделий.
2.
ТРЕБОВАНИЯ К ЗАЩИТНЫМ МАТЕРИАЛАМ
2.1. Для
комплексной защиты деревянных конструкций от увлажнения, биоразрушения и
возгорания могут быть использованы водо- и органикорастворимые составы и
лакокрасочные материалы, обладающие огнебио- или биовлаго-, или огневлаго-, или
комплексом влагобиоогнезащитных свойств.
2.2. К
защитным материалам предъявляются следующие требования:
а) уровень защитной
способности:
1) огнезащитные
свойства - группа возгораемости защищенной древесины по стандарту СЭВ 2437-80
или по ГОСТ 16363-76 в зависимости от требований главы СНиП II-2-80
"Противопожарные нормы проектирования зданий и сооружений";
2) влагозащитные
свойства - категория покрытий и пропиточных составов по ГОСТ 22406-77 не ниже
ограниченно влагозащитной (коэффициент влагопроницаемости не более 0,70);
3) биозащитные
свойства (токсичность - по ГОСТ 16712-71) - отсутствие обрастания защищенных
образцов мицелием домового гриба Кониофора церебелла и потеря массы защищенного
образца в процессе испытаний не более 5% от потери массы незащищенного
контрольного образца;
б) срок защитного
действия: для лакокрасочных покрытий и пропиточных составов при поверхностном
нанесении - не менее 4 лет; для пропиточных составов при глубокой пропитке - не
менее 10 лет;
в) отсутствие
вредных выделений из защищенных конструкций в процессе их эксплуатации (для
составов, предназначаемых для защиты поверхностей конструкций, выходящих в
помещение).
2.3. К пропиточным
защитным составам, кроме положений п. 2.2, предъявляются также требования:
- высокая
проникаемость пропиточных составов;
- устойчивость к
вымыванию по ГОСТ 16713-71 (для составов, эксплуатируемых в атмосферных
условиях или помещениях с повышенной относительной влажностью).
2.4. К защитным
покрытиям, кроме положений п. 2.2, предъявляются также требования:
- высокая
адгезионная прочность сцепления с древесиной и древесными материалами не менее
1,5 МПа;
- устойчивость к
разрушающему воздействию солнечных лучей, выветриванию по ГОСТ 6992-68 (для
покрытий, эксплуатируемых в атмосферных условиях).
3. МАТЕРИАЛЫ ДЛЯ ЗАЩИТЫ ДЕРЕВЯННЫХ
КОНСТРУКЦИЙ ОТ
БИОРАЗРУШЕНИЯ И ВОЗГОРАНИЯ
3.1. Для защиты
деревянных конструкций от биоразрушения и возгорания рекомендуются водо- или
органикорастворимые составы, обладающие одновременно свойствами антисептика и
антипирена.
Биоогнезащитные
составы
Органикорастворимые
3.2. Препарат ТХЭФ
<*> - раствор трихлорэтилфосфата в четыреххлористом углероде.
--------------------------------
<*> А.с. N
674903. Опубл. в Б.И., 1979, N 27.
- Трихлорэтилфосфат
- хлорэтиловый эфир фосфорной кислоты -
бесцветная органикорастворимая жидкость с содержанием основного вещества 97,3%,
плотностью 1,425 г/см3; температурой вспышки 225 °C.
- Четыреххлористый
углерод
- бесцветная тяжелая жидкость, плохо
растворимая в воде с плотностью 1,595 г/см3; при соприкосновении с открытым
пламенем или раскаленными предметами разлагается с выделением фосгена; негорюч,
неогнеопасен.
3.3.
Препарат ПТАС - смесь пентахлорфенола, трихлорэтилфосфата, ацетона и
уайт-спирита.
- Пентахлорфенол
- мелкие гранулы желтовато-серого цвета,
получаемые хлорированием фенола, хорошо растворимые в минеральных и
растительных маслах; температура плавления 190 °C, кипения - 309 °C; плотность
1,978 г/см3; обладает высокой химической стойкостью и низкой летучестью.
- Ацетон
- прозрачная, бесцветная, легко
воспламеняющаяся жидкость с плотностью 0,792 г/см3, смешивающаяся во всех
отношениях с водой, спиртом, эфиром; температура вспышки минус 18 °C,
самовоспламенения 465 °C.
- Уайт-спирит -
бензин, растворитель - узкая высококипящая фракция бензина прямой перегонки с
плотностью 0,795 г/см3; температура вспышки минус 33 °C.
Водорастворимые
3.4.
Препараты МС 3:7, МС 1:1 - водный раствор смеси диаммонийфосфата, сульфата
аммония и фтористого натрия.
- Диаммонийфосфат
- кристаллический порошок белого цвета
(допускается желтоватый или сероватый оттенок) с содержанием фосфорного
ангидрида не менее 50%, аммиака не менее 22,5%, воды не более 5,0%; хорошо
растворим в воде, гигроскопичен, не корродирует черный металл; нетоксичен;
пожаро- и взрывобезопасен.
- Сульфат аммония
- кристаллический (гранулированный) порошок
белого или светло-серого цвета с содержанием азота в пересчете на сухое
вещество не менее 20,8%; нелетуч, гигроскопичен, пожаро- и взрывобезопасен.
- Фтористый натрий
NaF - продукт разложения содой водной суспензии кремнефтористого натрия или его
смеси с фтористоводородной кислотой - порошок белого или серого цвета;
содержание основного вещества 80 - 95%; пожаро- и взрывобезопасен.
3.5.
Препарат ХМБ-444 - смесь натриевого или калиевого бихромата, медного купороса и
борной кислоты.
- Бихромат калия
- калиевая соль двухромовой кислоты; получают
взаимодействием бихромата натрия и хлористого калия - кристаллы
оранжево-красного цвета с содержанием основного вещества 99,3 - 99,7%; пожаро-
и взрывобезопасен.
- Медный купорос
(сульфат меди)
- полупрозрачные кристаллы синего или голубого
цвета с содержанием основного вещества 92 - 98%, хорошо растворимые в воде;
негорюч, нелетуч, легко выщелачивается, сильно корродирует металлы; пожаро- и
взрывобезопасен.
- Борная кислота
- блестящие чешуйки или бесцветные мелкие
кристаллы с содержанием основного вещества 98,5 - 99,5%; негигроскопична.
3.6.
Препарат МБ-1 - смесь медного купороса, углекислого аммония, буры и борной
кислоты.
- Углекислый
аммоний
- кристаллы белого цвета, растворимые в воде,
спирте и глицерине; содержание аммиака 30 - 31%; при нагревании до 58 °C
разлагается с выделением аммиака и углекислого газа.
- Борная кислота -
см. п. 3.5.
- Бура
- белая кристаллическая негигроскопичная соль.
При нагревании бура вспучивается, выделяет пары воды; при температуре 741 °C
сплавляется в стеклянную массу; пожаро- и взрывобезопасна.
3.7. Препарат ББ -
смесь буры и борной кислоты - см. пп. 3.5 и 3.6.
3.8.
Препарат ПББ <*> - смесь пентахлорфенолята натрия, буры и борной кислоты.
--------------------------------
<*> А.с. N
504647. Опубл. в Б.И., 1976, N 8.
- Пентахлорфенолят
натрия
- натриевая соль пентахлорфенола -
кристаллический продукт серо-сиреневого цвета; растворимость 20% при 20 °C; не
снижает прочности древесины, корродирует медь, латунь, но не черные металлы;
обладает слабой проникающей способностью; активно сорбируется на поверхности
древесины.
- Бура и борная
кислота - см. пп. 3.5 - 3.6.
3.9.
Препарат ПБС <1> - смесь пентахлорфенолята натрия, борной кислоты и
кальцинированной соды.
--------------------------------
<1> А.с. N
618282. Опубл. в Б.И., 1978, N 29.
- Пентахлорфенолят
натрия - см. п. 3.8.
- Борная кислота -
см. п. 3.5.
- Кальцинированная
сода
- мелкокристаллический порошок белого или
светло-серого цвета; содержание основного вещества 87,0 - 96,5%, содержание
влаги не более 0,5 - 1,0%.
3.10.
Препарат ХМХА <2> - смесь бихромата натрия или калия, сульфата меди и
хлористого аммония.
--------------------------------
<2> А.с. N
810494. Опубл. в Б.И., 1981, N 9.
- Бихромат натрия
- кристаллы и гранулы от светло-оранжевого до
темно-красного цвета; содержание основного вещества 96,9 - 98,9%; пожаро- и
взрывобезопасен.
- Сульфат меди -
см. п. 3.5.
- Хлористый аммоний
- белая мелкокристаллическая соль, хорошо
растворимая в воде, гигроскопична, корродирует черный металл; при нагревании
свыше 35 °C разлагается на аммиак и хлористый водород, которые затрудняют
пламенное горение.
3.11. Препарат ХМББ
<3> - смесь бихромата натрия или калия, сульфата меди, буры, борной
кислоты и ледяной уксусной кислоты.
--------------------------------
<3> А.с. N
571376. Опубл. в Б.И., 1977, N 33.
- Бихромат натрия -
см. п. 3.10.
- Сульфат меди -
см. п. 3.5.
- Бура - см. п.
3.6.
- Борная кислота -
см. п. 3.5.
- Ледяная уксусная
кислота
- бесцветная прозрачная жидкость с резким
специфическим запахом; растворимость в воде - полная; содержание основного
вещества - 80 - 99,5%; температура вспышки 38 °C, самовоспламенения 454 °C.
3.12.
Препарат ДМФ <4> - смесь диаммонийфосфата, мочевины и фтористого натрия.
--------------------------------
<4> А.с. N
663581. Опубл. в Б.И., 1979, N 19.
- Диаммонийфосфат -
см. п. 3.4.
- Мочевина
- кристаллы или белый кристаллический порошок,
растворимый в воде, этаноле, метаноле; гигроскопичен; содержание основного
вещества 99%; температура плавления 131 °C, вспышки 182 °C, самовоспламенения
640 °C.
- Фтористый натрий
- см. п. 3.4.
- Борная кислота -
см. п. 3.5.
- Кальцинированная
сода - см. п. 3.9.
3.14. Препарат ТМФ
<*> - смесь триполифосфата натрия, мочевины и фтористого натрия.
--------------------------------
<*> А.с. N
844302. Опубл. в Б.И., 1981, N 25.
- Триполифосфат
натрия
- порошок белого цвета с содержанием основного
вещества 88 - 94%.
- Мочевина - см. п.
3.12.
- Фтористый натрий
- см. п. 3.4.
3.15. ТФБА
- тетрафторборат аммония - белый мелкокристаллический порошок с высокой растворимостью
в воде; легко проникает в древесину.
Технические
характеристики биоогнезащитных препаратов приведены в табл. 1.
Таблица 1
┌───────────┬────────────────────────┬──────┬─────┬──────┬─────────────────────┐
│ Марка
│ Компоненты препарата,
│Раст- │Вымы-│Пропи-│Прочие
характеристики│
│
препарата │ их соотношение, │вори- │вае-
│точный│
│
│
(состава) │ % по массе; ГОСТ,
ТУ │мость │мость│коэф-
│ │
│ │ │в
воде│ │фици- │ │
│ │ │при │
│ент │ │
│ │ │20
°C,│ │<1> │ │
│ │ │% │
│ │ │
├───────────┼────────────────────────┼──────┼─────┼──────┼─────────────────────┤
│ 1
│ 2 │ 3
│ 4 │
5 │ 6 │
├───────────┼────────────────────────┼──────┼─────┼──────┼─────────────────────┤
│ ТХЭФ
│Трихлорэтилфосфат
│ - │ НВ
│ - │Древесину не окраши- │
│ │ТУ 6-05-1611-78 -
40│ │ │ │вает, не скрывает ее │
│ │Четыреххлористый
углерод│ │ │ │текстуру; не снижает │
│ │ГОСТ 4-75 -
60│ │ │ │прочность древесины и│
│ │ │ │ │ │клеевых соединений; │
│ │ │ │ │ │пропитанная древесина│
│ │ │ │ │
│не может быть обрабо-│
│ │ │ │ │ │тана лакокрасочными │
│ │ │ │ │ │материалами │
├───────────┼────────────────────────┼──────┼─────┼──────┼─────────────────────┤
│ ПТАС
│Пентахлорфенол
│ - │ НВ
│ 1,6 │Древесину
не │
│ │ГОСТ 18395-73 -
4│ │ │ │окрашивает; снижает │
│ │Трихлорэтилфосфат │
│ │ │прочность древесины │
│ │ТУ 6-05-1611-78 -
20│ │ │ │при статическом │
│ │Ацетон ГОСТ 2768-79 -
38│ │ │ │изгибе на 3%, не │
│ │Уайт-спирит │ │
│ │корродирует металлы │
│ │ГОСТ 3134-78 -
38│ │ │ │ │
├───────────┼────────────────────────┼──────┼─────┼──────┼─────────────────────┤
│ МС 3:7
│Диаммонийфосфат
│ - │ ЛВ
│ - │Древесину не окраши- │
│ │ГОСТ 8515-75 -
6,0│ │ │ │вает; снижает проч- │
│ │Сульфат аммония │ │ │ │ность древесины при │
│ │ГОСТ 9097-74 - 14,0│ │ │ │сжатии вдоль волокон │
│ │Фтористый натрий │ │ │ │и поперечном изгибе │
│ │ГОСТ 2871-75 -
1,5│ │ │ │на 10%; корродирует │
│ │Вода - 78,5│ │ │ │черные металлы │
├───────────┼────────────────────────┼──────┼─────┼──────┼─────────────────────┤
│ МС 1:1
│Диаммонийфосфат
│ - │ ЛВ
│ 0,5 │Древесину не
окраши- │
│ │ГОСТ 8515-75 -
7,5│ │ │ │вает; снижает проч- │
│ │Сульфат аммония │ │ │ │ность древесины при │
│ │ГОСТ 9097-74 -
7,5│ │ │ │сжатии вдоль волокон │
│ │Фтористый натрий │ │ │ │и поперечном изгибе │
│ │ГОСТ 2871-75 -
2,0│ │ │ │на 10%; корродирует │
│ │Вода - 83,0│ │ │ │черные металлы │
├───────────┼────────────────────────┼──────┼─────┼──────┼─────────────────────┤
│ ХМБ-444
│Бихромат натрия
│ - │ ТВ
│ - │Древесину окрашивает │
│ ТУ
│ГОСТ 2651-78 - 5│ │ │ │в зеленоватый цвет; │
│65-14-23-75│или │ │ │ │вызывает коррозию │
│ │Бихромат калия │ │ │ │металлов; пропитанная│
│ │ГОСТ 2652-78 │ │ │ │древесина склеивается│
│ │Медный купорос │ │ │ │и может быть │
│ │ГОСТ 19347-77 -
5│ │ │ │обработана │
│ │Борная кислота │ │ │ │лакокрасочными │
│ │ГОСТ 18704-78 -
5│ │ │ │материалами │
│ │Вода - 85,0│ │ │ │ │
├───────────┼────────────────────────┼──────┼─────┼──────┼─────────────────────┤
│ МБ-1
│Медный купорос
│ - │ ТВ
│ - │Древесину окрашивает │
│ ТУ 66
│ГОСТ 19347-77 - 2,7│ │ │ │в зеленоватый цвет, │
│ ЛатвССР
│Углекислый аммоний <2>
│ │ │ │легко проникает │
│ 0.68-76
│ГОСТ 3770-75 - 3,5│ │ │ │в нее; не снижает │
│ │Бура ГОСТ 8429-77 - 5,4│ │ │ │прочность древесины. │
│ │Борная кислота │ │ │ │Безопасен для людей │
│ │ГОСТ 18704-78 -
3,4│ │ │ │и животных │
│ │Вода - 85│ │
│ │ │
├───────────┼────────────────────────┼──────┼─────┼──────┼─────────────────────┤
│ ББ-11
│Бура ГОСТ 8429-77 -
10│ - │ ЛВ
│ - │Древесину не окраши- │
│ ГОСТ
│Борная кислота
│ │ │ │вает, обладает высо- │
│23787.6-79
│ГОСТ 18704-78 - 10│ │ │
│кой проницаемостью; │
│ │Вода - 80│ │
│ │пропитанная
древесина│
│ │ │ │ │ │склеивается и может │
│ │ │ │ │ │быть обработана лако-│
│ │ │ │ │ │красочными материа- │
│ │ │ │ │ │лами. Безопасен для │
│ │ │ │ │ │людей и животных │
├───────────┼────────────────────────┼──────┼─────┼──────┼─────────────────────┤
│ ПББ-255
│Пентахлорфенолят натрия │8 - 12│ ТВ │ 0,2
│Древесину не окраши- │
│ ГОСТ
│ТУ 6-04-6-80 - 1,7│ │ │ │вает; не снижает │
│23787.7-79
│Бура ГОСТ 8429-77 - 4,15│
│ │ │прочность древесины │
│ │Борная кислота │ │ │ │при сжатии и стати- │
│ │ГОСТ 18704-78 - 4,15│ │ │ │ческом изгибе; │
│ │Вода -
90│ │ │ │пропитанная древесина│
│ │ │ │ │ │склеивается и может │
│ │ │ │ │ │быть обработана │
│ │ │ │ │ │лакокрасочными │
│ │ │ │ │ │материалами │
├───────────┼────────────────────────┼──────┼─────┼──────┼─────────────────────┤
│
ПББ <...> │Пентахлорфенолят натрия │8 - 10│ ТВ │ 0,4
│То же
│
│ │ТУ 6-04-6-80 -
1,7│ │ │ │ │
│ │Борная кислота │ │ │ │ │
│ │ГОСТ 18704-78 - 4,15│ │ │ │ │
│ │Сода кальцинированная │
│ │ │ │
│ │ГОСТ 10689-75 - 4,15│ │ │ │ │
│ │Вода - 90│ │
│ │ │
├───────────┼────────────────────────┼──────┼─────┼──────┼─────────────────────┤
│
ХМББ-3324 │Бихромат натрия или
│7 - 11│ ТВ │
1,0 │Древесину окрашивает │
│ ГОСТ
│калия ГОСТ 2651-78 - 2,5│ │ │ │в серовато-зеленый │
│23787.2-79
│Сульфат меди
│ │ │ │цвет; не снижает │
│ │ГОСТ 19347-77 - 2,5│ │ │ │прочности древесины │
│ │Бура ГОСТ 8429-77 - 1,7│ │ │ │при сжатии │
│ │Борная кислота │ │ │ │и статическом изгибе;│
│ │ГОСТ 18704-78 - 3,3│ │ │ │корродирует черные │
│ │Вода - 90│
│ │ │металлы; пропитанная │
│ │ │
│ │ │древесина склеивается│
│ │ │ │ │ │и может быть обрабо- │
│ │ │ │ │ │тана лакокрасочными │
│ │ │ │
│ │материалами │
├───────────┼────────────────────────┼──────┼─────┼──────┼─────────────────────┤
│
ХМХА-1110 │Бихромат натрия или
│25 - │ ТВ │ 1,2
│Древесину малоценных │
│ │калия ГОСТ 2651-78 -
2,5│ 35│ │ │пород окрашивает под │
│ │Сульфат меди │ │ │ │ценные (орех, серый │
│ │ГОСТ 19347-77 - 2,5│ │ │ │клен), не снижает │
│ │Хлористый аммоний │ │ │ │прочность древесины │
│ │ГОСТ 2210-73 - 25,0│ │ │ │при сжатии, снижает │
│ │Вода - 70│ │
│ │прочность
древесины │
│ │ │ │ │ │при статическом │
│ │ │ │ │
│изгибе на 3 - 5%
│
├───────────┼────────────────────────┼──────┼─────┼──────┼─────────────────────┤
│ ДМФ-552
│Диаммонийфосфат
│10 - │ ЛВ │ 0,6
│Древесину
│
│ │ГОСТ 8515-75 -
8,3│ 30│ │ │не окрашивает, │
│ │Мочевина │ │ │ │не снижает прочность │
│ │ГОСТ 2081-75 -
8,3│ │ │ │древесины при сжатии,│
│ │Фтористый натрий │ │ │ │снижает прочность │
│ │ГОСТ 2871-75 -
3,4│ │ │ │древесины при │
│ │или │ │ │ │статическом изгибе │
│ │Кремнефтористый натрий │
│ │ │на 3 - 5% │
│ │ГОСТ 87-77 │ │ │ │ │
│ │Вода - 80│ │
│ │ │
├───────────┼────────────────────────┼──────┼─────┼──────┼─────────────────────┤
│ ФБС-255
│Фтористый натрий
│ 7 │ ЛВ
│ 0,6 │Древесину │
│ │ГОСТ 2871-75 - 1,2│ │ │ │не окрашивает, │
│ │Борная кислота │ │ │ │не снижает прочность │
│ │ГОСТ 18704-78 - 2,9│ │ │ │древесины при сжатии │
│ │Кальцинированная сода │
│ │ │и статическом изгибе │
│ │ГОСТ 10689-75 - 2,9│ │ │ │ │
│ │Вода - 93│
│ │ │ │
├───────────┼────────────────────────┼──────┼─────┼──────┼─────────────────────┤
│ ТМФ-552
│Триполифосфат натрия
│ 7 │ ЛВ
│ 0,7 │То же │
│ │ГОСТ 13493-77 - 2,9│ │ │ │ │
│ │Мочевина │ │ │ │ │
│ │ГОСТ 2081-75 - 2,9│ │ │ │ │
│ │Фтористый натрий - 1,2│ │ │ │ │
│ │или │ │ │ │ │
│ │Пентахлорфенолят натрия
│ │ │ │ │
│ │или │ │
│ │ │
│ │Кремнефтористый натрий │
│ │ │ │
│ │Вода - 93│
│ │ │ │
├───────────┼────────────────────────┼──────┼─────┼──────┼─────────────────────┤
│ ТФБА
│Тетрафторборат аммония
│ - │ ЛВ
│ - │Древесину не окраши- │
│ │ТУ 6-08-297-74 -
15│ │ │ │вает, не снижает │
│ │Вода - 85│
│ │ │прочность древесины, │
│ │ │ │ │ │слабо корродирует │
│ │ │ │ │ │металл; пропитанная │
│ │ │ │ │ │древесина склеивается│
│ │ │ │ │ │и может быть обрабо- │
│ │ │ │ │ │тана лакокрасочными │
│ │ │ │ │ │материалами │
└───────────┴────────────────────────┴──────┴─────┴──────┴─────────────────────┘
Примечания.
<1> Отношение глубины проникновения пропиточного состава к
соответствующему показателю для дистиллированной воды при пропитке по способу
ВАДВ.
<2>
Углекислый аммоний может быть заменен водным раствором 25%-ного аммиака.
Приготовление
огнебиозащитных пропиточных составов
3.16.
Крупнокристаллические и слежавшиеся в комки компоненты предварительно
размельчают и просеивают через сито с проволочными сетками по ГОСТ 3584-73 или
ГОСТ 6613-73 (размер стороны ячейки в свету должен быть не менее 1 мм).
Приготовление
растворов рекомендуется производить в резервуарах, снабженных подогревающими и
смесительными устройствами, фильтрами для задержания нерастворившихся частиц
перед выпуском готового раствора, а также крышками, плотно закрывающими
загрузочные люки.
3.17. Навеску
каждого компонента препарата
в кг вычисляют по формуле
,
где m - количество
приготавливаемого раствора, кг;
n - содержание
компонента в препарате, %;
C - заданная
концентрация раствора, %;
q - содержание
основного вещества в продукте, %.
Органикорастворимые
составы
3.18. ТХЭФ.
Компоненты в требуемых по табл. 1 количествах тщательно перемешивают в течение
15 - 30 мин. Температура компонентов и воздуха в помещении, где осуществляется
приготовление состава, должна быть не ниже 15 °C.
3.19. ПТАС.
Пентахлорфенол перемешивают с трихлорэтилфосфатом при температуре 18 - 20 °C и
оставляют на два часа. Затем последовательно вводят ацетон и уайт-спирит.
Приготовленный состав тщательно перемешивают в течение 15 мин.
Водорастворимые
составы
3.20. МС 3:7, МС
1:1. На основе результатов анализа технического диаммонийфосфата, приведенных в
сопроводительном паспорте, производят расчет потребных количеств указанных
продуктов для приготовления необходимого количества (для примера 100 кг)
пропиточного раствора
(для МС 3:7),
(для МС 1:1),
где Ф - количество
потребного технического диаммонийфосфата, кг;
Б - содержание в
продукте
в % по данным аналитического паспорта;
А - содержание в
продукте
в % по данным аналитического паспорта.
В 75% от общего
количества воды, подогретой до температуры 50 - 60 °C, растворяют при
постоянном перемешивании расчетное по анализу количество сухого технического
диаммонийфосфата. Контролируют плотность раствора ареометром (ГОСТ 1300-74).
После достижения плотности 1,170 к нему добавляют 25%-ный раствор аммиака до
слабо-розового окрашивания раствора на индикатор-фенолфталеин. Это необходимо
для перевода в диаммонийфосфат моноаммонийфосфата, содержащегося в технических
продуктах.
После этого
добавляют сернокислый аммоний и фтористый натрий.
Оставшееся,
согласно рецепту, количество воды приливают к раствору с учетом воды,
содержащейся в фосфорнокислом аммонии, и количества добавленного раствора
аммиака.
Приготовленный
пропиточный раствор хорошо перемешивают, процеживают через сетку 1200 отв./см2,
дают отстояться в течение суток.
3.21. ХМХА. В воде,
подогретой до 60 °C, растворяют бихромат натрия и сульфат меди. После
тщательного перемешивания добавляют хлористый аммоний. Допускается использовать
воду без подогрева.
3.22. ДМФ, ТМФ. При
приготовлении растворов компоненты растворяют в воде, подогретой до 60 - 80 °C.
Последовательность введения компонентов не регламентируется.
3.23. ФБС. В воде,
подогретой до 90 °C, растворяют фтористый натрий и борную кислоту. После
растворения добавляют кальцинированную соду.
3.24. ПББ. В воде,
подогретой до 90 °C, растворяют буру и борную кислоту, а затем при достижении раствором
температуры 70 °C добавляют пентахлорфенолят натрия.
3.25. ПБС. В воде,
подогретой до 90 °C, растворяют борную кислоту и кальцинированную соду, а затем
при достижении раствором температуры 70 °C добавляют пентахлорфенолят натрия.
3.26. ХМББ. В одной
емкости в воде, подогретой до 60 - 70 °C, растворяют бихромат натрия (калия),
медный купорос и борную кислоту. Во второй емкости в воде, подогретой до той же
температуры, растворяют буру. Затем раствор буры при тщательном перемешивании
приливают к первому раствору и добавляют уксусную кислоту, квалификации
"ледяная" в количестве, обеспечивающем pH раствора 4 - 4,5 (до
полного исчезновения мути). Растворение медного купороса должно производиться в
посуде, не реагирующей с медью.
3.27. МБ-1.
Пропиточный раствор получают при смешивании двух рабочих растворов (на примере
100 л пропиточного раствора).
Первый рабочий
раствор.
В 15 л воды при
температуре 30 °C растворяют 3,1 кг медного купороса. Затем после охлаждения
раствора до 20 °C в нем растворяют 4,0 кг углекислого аммония для образования
медно-аммиачного комплекса. Аммоний углекислый следует добавлять в раствор
постепенно, поскольку реакция образования комплекса сопровождается бурным
выделением углекислого газа.
Аммоний углекислый
следует добавлять до получения прозрачного раствора.
Второй рабочий
раствор.
В 68 л воды (t = 55
- 60 °C) растворяют смесь, состоящую из 6,1 кг буры и 3,9 кг борной кислоты. Не
охлаждая, второй рабочий раствор приливают к первому рабочему раствору,
тщательно перемешивают и только затем приготовленный раствор охлаждают.
3.28.
ББ-11, ТФБА. Для приготовления растворов используют воду, подогретую до 90 °C.
Последовательность введения компонентов ББ-11 не регламентируется.
Технология
защитной обработки
3.29. Технология
защитной обработки биоогнезащитными составами с указанием уровня их защитной
способности приведена в табл. 2.
Таблица 2
┌─────────┬─────────┬──────┬──────────────────────────────────────────────┐
│ Марка
│Рекомен- │Общее │ Уровень защитной способности │
│препарата│дуемые │погло-│ при указанном поглощении │
│(состава)│способы │щение
├─────────────────────────┬────────────────────┤
│ │обработки│кг/м3
│ огнезащита <2> │
биозащита │
│ │ │<1>
├─────────────────────────┼─────────┬──────────┤
│ │ │ │
группа горючести
│пороговое│группа
│
│ │ │ │
защищенной древесины
│поглоще- │биостой-
│
│ │
│ │ по ГОСТ 16363-76 │ние, %, │кости │
│ │ │ │
(показатель потери │по
ГОСТ │защищенной│
│ │ │ │
массы образца (%)
│16712-71 │древесины │
│ │ │ │ при огневых испытаниях │ │ │
│ │ │ │
по указанному ГОСТу)
│ │ │
├─────────┼─────────┼──────┼─────────────────────────┼─────────┼──────────┤
│ 1
│ 2 │
3 │ 4 │ 5
│ 6 │
├─────────┼─────────┼──────┼─────────────────────────┼─────────┼──────────┤
│ТХЭФ
<4> │А, Б, В, │
15 │Трудновоспламеняемая
(13)│ - │Биостойкая│
│ │Д, Е <3> │ │ │ │ │
│ПТАС │
Б - Ж │ 35
│То же (28)
│ 1,5 │
То же │
│ │ │ 85
│Трудногорючая (6)
│ │ │
│МС
3:7 │ Д
│ 66 │Трудногорючая │ -
│ " │
│МС
1:1 │ Д, Ж
│ 30 │Трудновоспламеняемая (16)│ -
│ " │
│ │ │ 66
│Трудногорючая (9)
│ - │
" │
│ББ-11 │
А - Ж │ 60
│Трудногорючая
│ 0,18 │
" │
│МБ-1 │
То же │ 80
│То же
│ - │
" │
│ХМБ-444 │
А - Ж │ 90
│Трудногорючая
│ - │Биостойкая│
│<4> │ │ │ │ │ │
│ПББ │
То же │ 28
│Трудновоспламеняемая (20)│
0,3 │ То же
│
│ │ "
│ 76 │Трудногорючая (9) │ │ │
│ПБС │
" │ 30
│Трудновоспламеняемая (20)│
1,6 │ "
│
│ │ │ 81
│Трудногорючая (8)
│ │ │
│ХМББ
<4> │ " │
28 │Трудновоспламеняемая
(28)│ 1,5 │
" │
│ │ │ 79
│Трудногорючая (9)
│ │ │
│ХМХА
<4> │ " │
26 │Трудновоспламеняемая
(19)│ 1,77 │
" │
│ │ │ 75
│Трудногорючая (8)
│ │ │
│ДМФ
│ "
│ 25 │Трудновоспламеняемая (23)│ 0,8
│ " │
│ │ │ 76
│Трудногорючая (7)
│ │ │
│ФБС │
" │ 26
│Трудновоспламеняемая (25)│
1,5 │ "
│
│ │ │ 81
│Трудногорючая (7)
│ │ │
│ТМФ │
А - Ж │ 28
│Трудновоспламеняемая (26)│ │ │
│ │ │ 80
│Трудногорючая (9)
│ 1,5 │Биостойкая│
│ТФБА │
То же │ 21
│Трудновоспламеняемая (24)│ - │
То же │
│ │ │ 73
│Трудногорючая (9)
│ │ │
└─────────┴─────────┴──────┴─────────────────────────┴─────────┴──────────┘
Примечания.
1. Приведенные величины общего поглощения, обеспечивающего перевод древесины в
категории трудновоспламеняемых и трудногорючих материалов по ГОСТ 16363-76,
являются ориентировочными.
2.
Классификация защищенной древесины по возгораемости (несгораемая,
трудносгораемая и сгораемая) согласно требованиям СНиП II-2-80
"Противопожарные нормы проектирования зданий и сооружений"
устанавливается по методике стандарта СЭВ 2437-80 "Пожарная безопасность в
строительстве. Возгораемость строительных материалов. Метод определения группы
трудносгораемых материалов".
3. Основные
виды пропитки
А. Диффузионная
(ГОСТ 10432-72)
Б. Нанесение на
поверхность (ГОСТ 20022.9-76)
В. Вымачивание
(ГОСТ 19017-73)
Г. Панельный (ГОСТ
20022.4-75)
Д. Прогрев-холодная
ванна (ГОСТ 20022.6-76)
Е.
Вакуум-атмосферное давление-вакуум (ГОСТ 20022.3-76)
Ж.
Вакуум-давление-вакуум (ГОСТ 20022.7-76 для водорастворимых составов).
4. При
использовании способа "прогрев-холодная ванна" прогрев осуществляется
"сухим воздухом" или паром с последующим погружением в раствор с
температурой 20 °C.
4. МАТЕРИАЛЫ ДЛЯ ЗАЩИТЫ ДЕРЕВЯННЫХ КОНСТРУКЦИЙ
ОТ ВОЗГОРАНИЯ И
УВЛАЖНЕНИЯ
4.1. Для защиты
деревянных конструкций от возгорания и увлажнения рекомендуются лакокрасочные
материалы, обладающие одновременно огневлагозащитными свойствами. Допускается
проведение последовательной комбинированной обработки конструкций огнезащитными
материалами с последующим нанесением атмосферо- или влагозащитных материалов.
Огневлагозащитные
материалы
4.2. ОС-12-03 -
органосиликатная композиция различных цветов - суспензия силикатных и окисных
компонентов в толуольном растворе модифицированных кремнеорганических полимеров
(полиорганосилоксанов). Поставляется заводом-изготовителем в комплекте с
отвердителем (1 - 2%).
Органосиликатная
композиция в отвержденном состоянии обладает малой водопроницаемостью и
теплопроводностью, значительной термо- и морозостойкостью; стойкостью в
атмосферных условиях и газообразных агрессивных средах; выдерживает резкие
перепады температур от -60 до +600 °C.
Материалы для
последовательной обработки
с целью защиты от
возгорания и увлажнения
Огнезащитный
материал (ОФП, ВПД, ПП) с последующим нанесением атмосферо- или влагостойкого
лакокрасочного материала.
4.3. ОФП -
огнезащитное фосфатное покрытие - смесь наполнителя (каолин, зола-уноса ТЭС),
связующего (полиметафосфат натрия), антипирена (гидроокись алюминия, мочевина)
и пигмента (железный сурик или окись цинка) - однородная масса без запаха; цвет
красновато-коричневый (при использовании железного сурика) или серовато-белый
(при использовании окиси цинка).
- Зола-уноса ТЭС -
продукт, содержащий углистое вещество, кусочки обожженной глины, зерна кварца,
гематиты, шарики стекла; содержание
не менее 40%,
не менее 15%.
- Полиметафосфат
натрия
- стекловидное прозрачное вещество, хорошо
растворимое в воде; содержание основного вещества 61,5%; образует стабильный
клейкий раствор с pH = 5,5; пожаро- и взрывоопасен, нетоксичен.
- Гидроокись
алюминия -
- мелкокристаллический порошок белого цвета;
продукт разложения алюминатных растворов в производстве глинозема.
- Мочевина
- см. п. 3.12.
- Железный сурик
- природный неорганический пигмент
красно-коричневого цвета, состоящий из окиси железа с примесью глинистых
минералов и кварца; содержание окиси железа 65 - 70%; нетоксичен.
- Окись цинка (ZnO)
- аморфный порошок белого или слегка желтоватого цвета, нерастворим в воде,
растворяется в минеральных кислотах, уксусной кислоте, в растворах щелочей,
аммиака и углекислого аммония.
4.4. ВПД -
огнезащитное вспучивающееся покрытие - смесь термостойких и газообразующих
наполнителей в водном растворе полимерных связующих - текучая серовато-белого
цвета паста, обладающая тиксотропными свойствами; при хранении загустевает.
Перед употреблением необходимо тщательное перемешивание, допускается разбавление
водой (в соотношении 1 в.ч. воды на 10 в.ч. ВПД). Поставляется в двух
упаковках: основа (см. табл. 3) и аммофос. Основа - смесь
меламино-мочевино-формальдегидной смолы ММФ-50, водного раствора натриевой соли
карбоксиметилцеллюлозы, мелема и дициандиамида; изготовляется на заводе и
поставляется в готовом виде.
- ММФ-50
меламино-мочевино-формальдегидная смола - продукт конденсации меламина и
мочевины с формальдегидом в щелочной среде; мутноватая жидкость зеленоватого
цвета, без механических примесей; содержание нелетучих веществ 52 +/- 2%,
вязкость по ВЗ-4 при 20 +/- 0,5 °C 11 - 15 с.
- Мелем
- порошок белого или серовато-желтого цвета с
наличием комков, размером до 15 мм; содержание основного вещества 80 - 90%;
слабогигроскопичен, практически не растворяется в воде и органических
растворителях; нетоксичен, пожаро- и взрывоопасен.
- Дициандиамид
- мелкие кристаллы белого цвета; содержание
основного вещества 93 - 98%; температура плавления 201 - 207 °C; при нагревании
выше температуры плавления разлагается с выделением аммиака; трудногорюч,
малотоксичен.
- Аммофос - продукт
нейтрализации фосфорной кислоты аммиаком; содержание основного вещества 93 -
98%, массовая доля усвоения
- 44 - 52%; массовая доля азота - 10 - 12%.
4.5. ПП <*> -
поверхностно-пропиточный состав - водный раствор углекислого калия с добавкой
поверхностно-активного вещества, бесцветная жидкость с плотностью 1,24 г/см3.
--------------------------------
<*> А.с. N
916528. Опубл. в Б.И., 1982, N 12.
- Углекислый калий
- мелкокристаллический порошок с содержанием
основного вещества 92 - 98%.
-
Сульфонат-эмульгатор - ПАВ - смесь алкилмоносульфонатов; содержание основного
вещества 92%.
Лакокрасочные
материалы
4.6. ПФ-115
- пентафталевая эмаль - суспензия сложных полиэфиров пентаэритрита и фталевой
кислоты, модифицированных жирными кислотами растительных масел, в смеси с
пигментами, наполнителями, сиккативами и растворителями; имеет широкую гамму
цветов (более 20). Поставляется заводом-изготовителем в готовом виде.
Отвержденное
однородное глянцевое покрытие ПФ-115 обладает высокой атмосферостойкостью в
условиях умеренного климата, эластичностью и высокой адгезионной прочностью
сцепления с защищаемой поверхностью. Покрытие стойко к температурным колебаниям
от -40 до +50 °C.
4.7. ХВ-785 -
перхлорвиниловая эмаль - суспензия пигментов в растворе хлорированной
поливинилхлоридной и алкидной смол в смеси летучих органических растворителей с
добавлением пластификатора. Поставляется заводом-изготовителем в готовом виде.
Отвержденное
покрытие стойко к воздействию агрессивных газов, кислот, растворов солей и щелочей
при температуре не выше 60 °C.
Эмали ХВ-785
черного и красно-коричневого цвета стойки к химически агрессивным средам и
атмосферным воздействиям.
4.8. ХВ-784
- перхлорвиниловый лак (бывш. ХСЛ) - раствор хлорированной поливинилхлоридной
смолы в смеси летучих органических растворителей с добавлением пластификатора.
Поставляется заводом-изготовителем в готовом виде.
Отвержденное
покрытие может эксплуатироваться в диапазоне температур от -40 до +60 °C;
устойчиво в условиях умеренного климата и в химически агрессивных средах.
4.9. КО-174 -
кремнеорганическая эмаль - суспензия неорганических и органических пигментов в
кремнеорганическом лаке с добавлением растворителя; имеет широкую цветовую
гамму. Выпускается заводом-изготовителем в готовом виде.
Отвержденное
покрытие КО-174 стойко в атмосферных условиях; обладает термостойкостью и
эластичностью.
Технические
характеристики огневлагозащитных материалов приведены в табл. 3.
Таблица 3
┌────────┬────────────────────────┬─────────┬───────────┬───────────────────┐
│Марка │
Компоненты и их
│Раствори-│ Исходная
│Прочие технические │
│мате- │соотношение, % (мас.); │тель │вязкость по│ характеристики │
│риала │ ГОСТ, ТУ │ │ ВЗ-4 при │ │
│(соста-
│
│ │18 - 22
°C,│ │
│ва) │ │ │ с
│ │
├────────┼────────────────────────┼─────────┼───────────┼───────────────────┤
│ 1
│ 2
│ 3 │
4 │ 5 │
├────────┼────────────────────────┼─────────┼───────────┼───────────────────┤
│ОС-12-03│ТУ
84-725-78 │ Ксилол │Не менее 18│Содержание │
│ │ │ │ │нелетучих веществ -│
│ │ │ │ │45%; однородное │
│ │ │ │ │гладкое покрытие, │
│ │ │ │ │укрывистое, │
│ │ │ │ │8 цветов; прочность│
│ │ │ │ │при ударе по │
│ │ │ │ │прибору У-2-20-25 │
│ │
│ Материалы для последовательной
огневлагозащитной обработки
│
│ОФП │Полиметафосфат натрия │
Вода │ 20 - 50
│ - │
│ГОСТ │технический │ │ │ │
│23790-79│ГОСТ
20291-80 - 35 - 40│ │ │ │
│ │Гидроокись алюминия ГДО
│ │ │ │
│ │ТУ 48-01-17-70 │ │ │ │
│ │ - 14 - 16│ │ │ │
│ │Каолин <1> или глина │ │ │ │
│ │ - 4 - 6│ │ │ │
│ │Зола-уноса ТЭС - 14 -
16│ │ │ │
│ │Железный сурик │ │ │ │
│ │ГОСТ 8135-74 или │ │ │ │
│ │окись цинка │ │ │ │
│ │ГОСТ 10262-76 - 4 -
6│ │ │ │
│ │Мочевина ГОСТ 6691-77 │ │ │ │
│ │или тиомочевина │ │ │ │
│ │ГОСТ 6344-73 - 18 - 22│ │ │ │
│ │Вода -
44,4│ │ │ │
│С
после-│ПФ-115 ГОСТ 6465-76
│Сольвент,│ 80 - 100
│Содержание │
│дующим │ │ уайт-
│ │нелетучих
веществ -│
│нанесе-
│ │
спирит │ │45 - 55%; покрытие │
│нием │ │ │ │однородное глянце- │
│ПФ-115 │ │ │ │вое, укрывистое; │
│ │ │ │ │прочность при │
│ │ │ │ │изгибе не более │
│ │ │ │ │1 мм; при ударе не │
│ │ │ │ │менее 40 кгс x см │
│ │ │ │ │твердость не менее │
│ │ │ │ │0,15 - 0,20 │
│ПП │Углекислый калий │ -
│ - │Плотность рабочего │
│Инструк-│ГОСТ
10690-73 - 25│ │ │раствора 1,24 г/см3│
│ции │Поверхностно-активное │ │ │ │
│ВНИИПО │вещество <2> - 1,0 -
1,5│ │ │ │
│МВД
СССР│Вода - 74,0 -
73,5│ │ │ │
│С
после-│ХВ-784 ГОСТ 7313-75
│ Р-4 │
20 - 50 │Содержание │
│дующим │
│ │ │нелетучих веществ │
│нанесе-
│
│ │ │14 - 17%; покрытие │
│нием │ │ │ │прозрачное, одно- │
│ХВ-784 │ │ │ │родное, глянцевое, │
│ │ │ │ │не скрывает текс- │
│ │ │ │ │туру древесины; │
│ │ │ │ │твердость пленки │
│ │ │ │ │по маятниковому │
│ │ │ │ │прибору - 0,50; │
│ │ │ │ │прочность на изгиб │
│ │ │ │ │не более 1 мм │
│ │ ┌ │ │ │ │
│ВПД │
|Меламино-мочевино- │
Вода │ -
│ - │
│ГОСТ │
|формальдегидная │ │ │ │
│25130-82│ |смола ММФ │ │ │ │
│ │ |ТУ-6-10-664-79 │ │ │ │
│ │ |
- 31,90│
│ │ │
│ │ |5%-ный водный │ │ │ │
│ │ |раствор натриевой │ │ │ │
│ │ос- |соли карбокси- │ │ │ │
│ │но- {метилцеллюлозы │ │ │ │
│ │ва |(марка 85-500) │ │ │ │
│ │ |ОСТ 6-05-386-80 │ │ │ │
│ │ |
- 15,94│
│ │ │
│ │ |Мелем │ │ │ │
│ │ |ТУ-6-03-463-79 │ │ │ │
│ │ |
- 18,44│
│ │ │
│ │ |Дициандиамид │ │ │ │
│ │ |ГОСТ 6988-73 │ │ │ │
│ │ |
- 6,22│ │ │ │
│ │ └ │ │ │ │
│ │Аммофос марки А │ │ │ │
│ │ГОСТ 18918-79 -
27,5│ │ │ │
│С
после-│ПФ-115 ГОСТ 6465-76
│Сольвент,│ 80 - 100
│Содержание │
│дующим │ │ уайт-
│ │нелетучих
веществ │
│нанесе-
│ │
спирит │ │45 - 55%. Покрытие │
│нием │ │ │ │укрывистое, одно- │
│ПФ-115 │ │ │ │родное, глянцевое; │
│ │ │ │ │прочность при │
│ │ │ │ │изгибе не более │
│ │ │ │ │1 мм; прочность │
│ │ │ │ │при ударе не менее │
│ │ │ │ │40 кгс x см; │
│ │ │ │ │твердость не менее │
│ │ │ │ │0,15 - 0,20 │
│или │ │ │ │ │
│ХВ-785 │ХВ-785 ГОСТ 7313-75 │
Р-4, │ 30 - 100 │Содержание │
│ │ │сольвент
│ │нелетучих
веществ │
│ │ │ │ │23 - 36%. Покрытие │
│ │ │
│
│однородное, укры- │
│ │ │ │ │вистое; твердость │
│ │ │ │ │пленки по маятнико-│
│ │ │ │ │вому прибору не │
│ │ │ │ │менее 0,34 - 0,40; │
│ │ │ │ │прочность на изгиб │
│ │ │ │ │не более 1 мм │
│или │ │ │ │ │
│КО-174 │КО-174 ТУ-6-02-576-75 │
Р-5 │ 13 - 25
│Содержание │
│ │ │ │ │нелетучих веществ │
│ │ │ │ │20 - 25%; покрытие │
│ │ │ │ │укрывистое, одно- │
│ │ │ │ │родное, матовое или│
│ │ │ │ │полуматовое; проч- │
│ │ │ │ │ность на изгиб не │
│ │ │ │ │более 3 мм, твер- │
│ │ │ │ │дость не менее 0,32│
└────────┴────────────────────────┴─────────┴───────────┴───────────────────┘
Примечания.
1. Каолин или глина с содержанием (по массе)
не менее 30% и
не менее 40%.
2. В
качестве поверхностно-активного вещества могут быть использованы:
ПО-ЗАИ - 1,5% по
массе (ТУ 38-10923-75);
Сульфанол
бессульфатный - 1,5% по массе (ТУ 6-01-1-157-78);
Сульфанат - 1,0% по
массе (ГОСТ 15034-69).
Первичные
алкисульфаты
(СТП 75-72).
Приготовление
огневлагозащитных материалов
4.10.
ОС-12-03 - лакокрасочный материал заводского изготовления. Поставляется в
комплекте с отвердителем (ТБТ, ПБТ, АГМ-3), вводимым в количестве 0,6 - 1,2%.
Операции по
приготовлению рабочих лакокрасочных составов должны выполняться в следующей
последовательности:
- смешение
компонентов состава (если он неоднокомпонентный);
- разбавление
лакокрасочных материалов растворителями;
- размешивание
лакокрасочных материалов;
- фильтрование
лакокрасочных материалов;
- определение
рабочей вязкости.
Разведение
лакокрасочных материалов до рабочей вязкости проводят растворителями в
соответствии с требованиями ГОСТа и ТУ на конкретные материалы. Рецептура
комбинированных растворителей приведена в Приложении 7. Вязкость рабочих
составов определяют вискозиметром ВЗ-4 при температуре лакокрасочного материала
20 +/- 0,5 °C по ГОСТ 8420-74.
Перед наливом
эмалей, лаков и растворителей отверстие и поверхность тары необходимо тщательно
вытирать от грязи и пыли для устранения возможности загрязнения материалов.
После вскрытия тары при наличии пленки ее следует осторожно удалить, не
смешивая со всем лакокрасочным материалом.
Эмали и краски
перед разведением необходимо тщательно перемешивать чистой деревянной мешалкой
до получения однородного материала без малейшего осадка пигмента на дне тары.
Лаки после удаления
пленки перемешивать не рекомендуется: их следует осторожно слить в смеситель
для разведения. Остаток с осадком сливают в специальный бак для отходов.
Рабочие составы
перед нанесением должны быть профильтрованы. Для фильтрации применяют
проволочные тканые сетки по ГОСТ 3584-73 или ГОСТ 6613-73.
4.11. ОФП в
сочетании с лакокрасочным материалом. Приготовление ОФП должно осуществляться в
следующей последовательности:
- приготовление
сухой смеси;
- приготовление
шликера.
Приготовление сухой
смеси. Приготовление сухой смеси осуществляется централизованным порядком в
заводских условиях. При небольших объемах работ допускается приготовление сухой
смеси на строительной площадке; при этом должна быть обеспечена защита
компонентов и оборудования от увлажнения и загрязнения.
Компоненты смеси,
имеющие влажность более 2% по массе, должны быть высушены при температуре не
более 100 +/- 10 °C в любом сушильном оборудовании (сушильный шкаф, печь,
барабан).
Полиметафосфат
натрия, глина и тиомочевина должны быть раздроблены в щековых дробилках до
частиц размером не более 15 мм.
Дозирование
компонентов производят весовым дозатором с погрешностью не более +/- 0,1% по
массе.
Смешение и помол
компонентов осуществляется в шаровой мельнице с фарфоровыми мелящими телами до
тонкости помола не более 2% по массе остатка на сите N 018 по ГОСТ 3485-73.
Объемная масса
сухой смеси в уплотненном состоянии не должна превышать 215 кг/м3.
Сухая смесь должна
храниться в полиэтиленовой таре, крафтмешках, фанерных и металлических бочонках
в течение не более 1 года в сухих помещениях.
Приготовление шликера.
Приготовление шликера осуществляется в лопастных мешалках периодического
действия. Допускается приготовление шликера вручную в металлической емкости.
В чистую мешалку
заливают необходимое количество воды, подогретой до температуры 20 - 70 °C,
загружают сухую смесь и перемешивают до получения однородного состава.
При применении
мочевины ее предварительно растворяют в воде, а затем в полученный раствор
загружают остальную сухую смесь.
Сухая смесь (с
тиомочевиной) должна составлять 5 весовых частей, а водопроводная вода - 4
весовые части.
Приготовленный
шликер процеживают через сито по ГОСТ 3584-73 с отверстиями в свету не более 1
мм. Если остаток на сите превышает 2% (по массе), перемешивание повторяют.
Шликер должен
храниться без потери свойств в герметично закрытой таре в сухих помещениях при
температуре не менее 5 °C в течение не более 6 мес.
В случае загустения
шликер разбавляют водой температурой 20 - 70 °C до требуемой вязкости.
ПФ-115, ХВ-785 -
лакокрасочные материалы заводского изготовления. Технология приготовления
лакокрасочных материалов приведена в п. 4.10.
4.12. ПП в
сочетании с ХВ-784. Для приготовления пропиточного раствора в воде, нагретой до
температуры 50 - 60 °C, при постоянном перемешивании растворяют углекислый
калий.
В водный раствор,
имеющий температуру 18 - 22 °C и плотность не ниже 1,24 (по ГОСТ 1300-74),
добавляют поверхностно-активное вещество.
Приготовленный
пропиточный раствор хорошо перемешивают, дают отстояться в течение суток.
Отстоявшийся
раствор сливают при помощи резинового шланга в приготовленную тару и используют
для пропитки.
Перхлорвиниловый
лак ХВ-784 - материал заводского изготовления. Технология приготовления
рабочего лакокрасочного состава приведена в п. 4.10.
4.13. ВПД в
сочетании с лакокрасочным материалом. Огнезащитный состав ВПД поставляется
заводом-изготовителем в двух упаковках: в одной упаковке - основной компонент
пасты (см. табл. 3), в другой - аммофос.
Для приготовления
рабочего состава оба компонента перемешивают в растворосмесителе типа СО-26Б
или СО-23Б, СО-46А, а затем дважды пропускают через краскотерку типа СО-110,
СО-116. При приготовлении рабочего состава его температура не должна превышать
35 °C.
Рабочий состав
должен храниться не более суток при температуре не ниже 5 и выше 30 °C в
закрытой емкости.
Лакокрасочные
материалы ПФ-115, ХВ-785 и КО-174 заводского изготовления. Технология
приготовления рабочих лакокрасочных составов представлена в п. 4.10.
Технология
защитной обработки
4.14. Технология
защитной обработки огневлагозащитными материалами с указаниями уровня их
защитной способности приведена в табл. 4.
Таблица 4
┌─────────┬─────────────────┬──────┬──────┬─────────────────────┬─────────┐
│ Марка
│Способ нанесения │Толщи-│Расход│ Уровень защитной │Адгезион-│
│материала├────────┬────────┤на │соста-│ способности │ная │
│(состава)│рекомен-│допуска-│покры-│ва,
├──────────┬──────────┤прочность│
│ │дуемый │емый
│тия, │г/м2 │огнезащита│влагоза- │сцепления│
│ │ │ │мкм │
│ │щита │с поверх-│
│ │ │ │ │
├──────────┼──────────┤ностью │
│ │ │ │ │ │
группа │категория
│древеси- │
│ │ │ │ │ │горючести │ защитных
│ны, МПа │
│ │ │ │ │ │защищенной│ покрытий
│ │
│ │ │ │ │ │древесины │ по ГОСТ │ │
│ │ │ │ │ │ по ГОСТ │ 22406-77 │ │
│ │ │ │
│ │ 16363-76
│ │ │
├─────────┼────────┼────────┼──────┼──────┼──────────┼──────────┼─────────┤
│ 1
│ 2 │
3 │ 4
│ 5 │
6 │ 7
│ 8 │
├─────────┼────────┼────────┼──────┼──────┼──────────┼──────────┼─────────┤
│ОС-12-03
│Пневма- │Безвоз- │ 250
│ - │Трудно- │Влаго- │1,6 - 2,4│
│ │тическое│душное │
│ │воспламе-
│защитное │ │
│
│распыле-│распыле-│ │ │няемая │(К = 0,25)│ │
│ │ние │ние, │
│ │(16)
<1> │<2> │ │
│ │ │кисть, │
│ │ │ │ │
│ │ │валик │
│ │ │ │ │
│ │
│ Материалы для последовательной
огневлагозащитной обработки
│
│ОФП │То же │Кисть │600 - │500 -
│Трудно- │Влаго- │1,5 - 1,8│
│с
после- │ │ │ 800│
700│горючая │защитное │ │
│дующим │ │ │ │ │(5) │ │ │
│нанесе- │
│ │ │ │ │ │ │
│нием │ │ │ │ │ │ │ │
│ПФ-115 │
" │Безвоз- │90 - │ 250
│ │ │ │
│ │ │душное │
110│ │ │ │ │
│ │ │распыле-│ │ │ │ │ │
│ │ │ние, │
│ │ │ │ │
│ │ │кисть, │
│ │ │ │ │
│ │ │валик │
│ │ │ │ │
│ВПД │Пневма- │Безвоз- │150
- │ 750 │Трудно- │Влаго- │
- │
│с
после- │тическое│душное
│ 200│ │горючая │защитное │ │
│дующим │распыле-│распыле-│ │ │(6) │ │ │
│нанесе- │ление
│ние, │ │ │ │ │ │
│нием │ │кисть, │
│ │ │ │ │
│ПФ-115 │ │валик │
│ │ │ │ │
│или │ │ │ │ │ │ │ │
│ХВ-785 │ │ │90 - │ 250
│ │ │ │
│или │ │ │ 110│ │ │ │ │
│КО-174 │ │ │ │ │ │ │ │
│ПП │То же │Кисть, │
- │ 300 │Трудно- │Влаго- │1,3 - 1,6│
│с
после- │ │валик │
│ │воспламе-
│защитное │ │
│дующим │ │ │ │ │няемая │(К = 0,32)│ │
│нанесени-│ │ │70 - │250 - │(22) │ │ │
│ем
ХВ-784│ │ │ 90│
300│ │ │ │
└─────────┴────────┴────────┴──────┴──────┴──────────┴──────────┴─────────┘
Примечания.
1. В скобках указана средняя величина потери массы образца (%) при испытаниях
по ГОСТ 16363-76.
2. В
скобках указано значение показателя условной влагопроницаемости при испытаниях
по ГОСТ 22406-77.
4.15. ОС-12-03.
Технологические параметры нанесения и сушки лакокрасочного материала приведены
в табл. 1 и 2 Приложения 1.
4.16. ОФП в
сочетании с лакокрасочным материалом. При нанесении способом пневмораспыления
используют насос типа БНР или пистолет-краскораспылитель по ГОСТ 7385-73 при
давления воздуха 0,5 МПа. Расстояние от форсунки распылителя до окрашиваемой
поверхности не более 40 см для пистолета-краскораспылителя и не более 70 см для
БНР.
При
пневмораспылении производят трехкратное нанесение; при нанесении вручную
необходима двухразовая обработка.
Продолжительность
межслойной сушки при температуре 18 - 23 °C - 24 ч; при температуре 50 °C - 2
ч; при 100 °C - 6 мин.
При нанесении ОФП
температура воздуха должна быть не ниже +10 °C, относительная влажность не
более 75%.
Лакокрасочный
материал ПФ-115, ХВ-785 наносят после полного высыхания покрытия ОФП (не ранее
чем через сутки). Технологические параметры различных способов нанесения и
сушки лакокрасочных материалов приведены в табл. 1 и 2 Приложения 1.
4.17. ПП в
сочетании с ХВ-784. Нанесение пропиточного состава ПП можно производить
механизированным способом (пневматическое распыление) или вручную (кисть,
валик) при строгом соблюдении норм расхода состава (см. табл. 4).
Пропиточный состав,
нагретый до 50 - 60 °C, наносят за два раза; при нанесении состава при его
температуре 15 - 18 °C необходима трехкратная обработка. Нанесение пропиточного
состава должно производиться при температуре воздуха не ниже +10° и
относительной влажности не выше 70%.
Продолжительность
выдержки между обработками должна быть не менее 6 ч при указанных параметрах
температуры и влажности воздуха.
Нанесение
лакокрасочного материала ХВ-784 на деревянные конструкции, обработанные
составом ПП, должно производиться после полного высыхания поверхности древесины
до влажности 10 - 12%.
Технологические
параметры различных способов нанесения и сушки лака ХВ-784 приведены в табл. 1
и 2 Приложения 1.
4.18. ВПД в
сочетании с лакокрасочным материалом. Нанесение огнезащитного состава ВПД может
осуществляться механизированным способом нанесения (пневматическое или
безвоздушное распыление) или вручную (кисть, валик).
Нанесение и сушка
состава должны производиться при температуре окружающего воздуха не ниже +10 и
не выше 35 °C и влажности не более 80%. Продолжительность выдержки между
обработками при указанных параметрах воздуха не менее 5 ч; практическое
высыхание - 24 ч; окончательное формирование покрытия происходит через 4 - 5
сут после нанесения последнего слоя. Нанесение лакокрасочного материала должно
осуществляться только после окончательного формирования покрытия ВПД.
Способы нанесения
лакокрасочных материалов (ПФ-115, ХВ-785, КО-174) и их технологические
параметры приведены в табл. 1 и 2 Приложения 1.
5. МАТЕРИАЛЫ ДЛЯ ЗАЩИТЫ ДЕРЕВЯННЫХ КОНСТРУКЦИЙ
ОТ УВЛАЖНЕНИЯ И
БИОРАЗРУШЕНИЯ
5.1. Для защиты от
увлажнения и от биоразрушения рекомендуются влагобиозащитные лакокрасочные или
маслянистые материалы, или последовательная комбинированная поэтапная обработка
водорастворимым антисептиком и атмосферо- или влагостойким лакокрасочным
материалом.
Влагобиозащитные
материалы
Лакокрасочные
5.2.
Перхлорвиниловый лак ХВ-784 - см. п. 4.8.
5.3.
Перхлорвиниловая эмаль ХВ-124 - раствор перхлорвиниловой смолы в смеси летучих
органических растворителей с добавлением других смол, пластификаторов и
пигментов. Поставляется заводом-изготовителем в готовом виде.
В отвержденном
состоянии покрытие ХВ-124 матовое, эластичное, трещиностойкое, имеет прочное
сцепление с древесиной; влагоморозостойкое, обладает также стойкостью к морской
атмосфере. Рекомендуется применять в условиях умеренного и тропического
климата.
Маслянистые
5.4. КМ -
масло каменноугольное - продукт перегонки каменноугольной смолы коксовых печей.
Жидкость темно-коричневого цвета с резким специфическим запахом, не вымываемая
водой; токсична, выкипает при температурах в пределах 200 - 400 °C.
5.5. КСМ - смесь
каменноугольного (КМ) и сланцевого (СМ) масел.
- Масло сланцевое -
продукт переработки горючих сланцев; фракции, отгоняющиеся при 210 - 350 °C;
условная вязкость при 80 °C не более 1,3 - 1,4, плотность при 20 °C не более
0,995 г/см3; температура вспышки 100 °C, температура самостоятельного горения
395 °C; менее токсично по сравнению с каменноугольным маслом, в остальном имеет
те же свойства.
5.6. КАМ - смесь
каменноугольного (КМ) и антраценового (АМ) масел.
- Масло
антраценовое - технические характеристики аналогичны КМ (см. п. 5.4 настоящего
раздела).
5.7. ПМВ - смесь
петролатума, пентахлорфенола и зеленого масла.
- Петролатум -
неводная гидрофобная жидкость светло-коричневого цвета, состоящая из смеси
парафина и церизинов с высоковязким очищенным маслом; удельный вес 0,85 г/см3,
температура каплепадения (застывания) - 55 °C, температура вспышки 240 - 250
°C; содержание воды не более 1%; взрывоопасен.
- Пентахлорфенол -
см. п. 3.3.
Материалы для
последовательной обработки
с целью защиты от
увлажнения и биоразрушения
Водорастворимые
антисептики: кремнефтористый аммоний (КФА), тетрафторборат аммония (ТФБА) и др.
в сочетании с атмосферо- или влагостойкими лакокрасочными материалами (ПФ-115,
ПФ-133, ПФ-14, МЧ-181, ПФ-170, ХВ-1100, ХВ-110, УР-49, УРФ-1128, УР-19).
5.8. КФА -
кремнефтористый аммоний - безводная аммонийная соль кремнефтористоводородной
кислоты; белый кристаллический порошок с легким запахом аммиака; обладает
высокой растворимостью в воде; легко проникает в древесину и вымывается из нее;
снижает свои защитные свойства при контакте с цементом, мелом; негигроскопичен,
неогнеопасен.
5.9. ТФБА - см. п.
3.15.
5.10. ПФ-115 - см.
п. 4.6.
5.11. МЧ-181 -
алкидно-карбамидная эмаль - суспензия пигментов в алкидно-карбамидном лаке
кислотного отверждения. Поставляется заводом-изготовителем в готовом виде.
5.12. ПФ-133 -
пентафталевая эмаль - суспензия сложных полиэфиров пентаэритрита и фталевой
кислоты в смеси с пигментами, наполнителями, сиккативами и растворителями.
Поставляется заводом-изготовителем в готовом виде.
Отвержденное
покрытие обладает высокой атмосферостойкостью в условиях умеренного климата,
эластичностью и высокой адгезионной прочностью сцепления с древесиной.
5.15. ХВ-1100,
ХВ-110 - перхлорвиниловые эмали - растворы перхлорвиниловой смолы в смеси
летучих органических растворителей с добавлением других смол, пластификаторов и
пигментов. Поставляется заводом-изготовителем в готовом виде.
Отвержденное
покрытие устойчиво к воздействию атмосферных факторов в условиях умеренного
климата.
5.14. УР-49 -
уретановая эмаль - суспензия пигментов в растворе лака УР-293. Поставляется
заводом-изготовителем в комплекте с растворителем Р-189.
Отвержденное
глянцевое покрытие обладает высокой прочностью, твердостью, влагостойкостью,
высокой адгезионной прочностью сцепления с древесиной; может эксплуатироваться
в атмосферных условиях умеренного климата под навесом.
5.15. УРФ-1128 -
уретаново-алкидная эмаль - суспензия пигментов в уралкидах с добавлением
сиккативов. Поставляется заводом-изготовителем в готовом виде.
Отвержденное глянцевое
покрытие обладает влагоморозостойкостью и высокой адгезионной прочностью
сцепления с древесиной, атмосферостойкостью.
Технические
характеристики влагобиозащитных материалов приведены в табл. 5.
Приготовление
влагобиозащитных материалов
5.16. Лакокрасочные
материалы (ХВ-784, ХВ-124, ПФ-115, ПФ-133, ПФ-14, МЧ-181, ХВ-1100, ХВ-110,
УР-49, ПФ-170, УР-19, УР-293) и маслянистые жидкости (КМ, СМ, АМ, ПМ)
поставляются заводом-изготовителем в готовом виде. Технология приготовления
рабочих лакокрасочных растворов приведена в п. 4.10.
5.17. Для
приготовления составов КСМ и КАМ необходимо осуществить подогрев каждого
компонента до 60 - 80 °C при тщательном перемешивании. Смешение компонентов
должно производиться без снижения их температуры. Перемешивание смеси
продолжают в течение 20 - 30 мин, после чего ей дают отстояться. При охлаждении
вязкость состава возрастает. Перед употреблением составы нагревают до требуемой
температуры.
5.18. Для
приготовления состава ПМВ необходимо подогреть петролатум до температуры 80 -
90 °C и при непрерывном перемешивании добавить пентахлорфенол и зеленое масло.
При охлаждении смесь загустевает. Перед употреблением ее нагревают до требуемой
температуры.
5.19. Приготовление
водорастворимых антисептиков должно осуществляться по методике приготовления
биоогнезащитных составов (см. пп. 3.16 - 3.28).
Технология
защитной обработки
5.20. Технология
защитной обработки влагобиозащитными материалами с указанием уровня их защитной
способности приведена в табл. 6.
Таблица 6
┌─────────┬─────────────────┬───────────┬─────────┬───────────────────────┐
│ Марка
│ Рекомендуемые │
Общее │ Толщина
│ Уровень защитной │
│раствора
│способы обработки│поглощение,│покрытия,│ способности │
│ │ │ПГ, кг/м3. │ мкм
├─────────┬─────────────┤
│ │ │ Удержание,│ │биозащита│ влагозащита
│
│ │ │ УД, г/м2. │
├─────────┼─────────────┤
│ │ │ Расход,
│ │группа │
категория │
│ │ │ РД, г/м2 │ │биостой- │ защитных
│
│ │ │ │ │кости │ покрытий и │
│ │ │ │ │защищен- │ пропиточных
│
│ │ │ │ │ной │ составов по │
│ │ │ │ │древесины│ГОСТ 22406-77│
├─────────┼─────────────────┼───────────┼─────────┼─────────┼─────────────┤
│ 1
│ 2 │ 3
│ 4 │
5 │ 6
│
├─────────┼─────────────────┼───────────┼─────────┼─────────┼─────────────┤
│ХВ-784 │Пневматическое │
РД 350 │ 70 - 90
│Био-
│Влагозащитное│
│ │или безвоздушное │ │ │стойкая │(0,32) <1> │
│ │распыление. │ │ │ │ │
│ │Допускается │ │ │
│ │
│ │нанесение вручную│ │ │ │ │
│ │(кисть, валик) │ │ │ │ │
│ХВ-124 │То же │ РД
│100 - 120│То же
│То же (0,26) │
│ │ │ 250 - 300 │ │ │ │
│КМ │Способ пропитки │
ПГ │ -
│ " │Влагозащитное│
│ │"давление-давле- │
100 - 180 │ │ │ │
│ │ние-вакуум". │ │ │ │ │
│ │Допускаются все │ │ │ │ │
│ │способы пропитки │ │ │ │ │
│ │под давлением │ │ │ │ │
│КСМ │То же │ ПГ
│ - │
" │То же │
│ │ │ 105 - 185 │ │ │ │
│КАМ │ " │ "
│ - │
" │ " │
│ПМВ │Способ пропитки │ ПГ 3 - 7 │
- │Био- │Влагозащитное│
│
│"прогрев-холодная│
<2> │ │стойкая │ │
│ │ванна". │ │ │ │ │
│ │Допускаются все │
│ │ │ │
│ │способы пропитки │ │ │ │ │
│ │под давлением │ │ │ │ │
│Водораст-│Всеми
способами │УД 35 - 50 │ -
│ " │
│
│воримыми
│поверхностной │ <3>
│ │ │ │
│антисеп-
│пропитки (опрыс- │
│ │ │ │
│тиками, │кивание, погруже-│ │ │ │ │
│КФА,
ТФБА│ние, вымачивание,│
│ │ │ │
│ │кисть и т.д.) │ │ │ │ │
│с
после- │Пневматическое
│ РД │90 - 120 │ "
│Влагозащитное│
│дующим │или безвоздушное │ 250 - 350
│ │ │(0,15 - 0,27)│
│нанесени-│распыление. │ │ │ │ │
│ем
лако- │Допускается
│ │ │ │ │
│красочных│нанесение
вручную│ │ │ │ │
│материа-
│(кисть, валик) │ │ │ │ │
│лов │ │ │ │ │ │
│(ПФ-115,
│ │ │ │ │ │
│ПФ-133, │ │ │ │ │ │
│МЧ-181, │ │ │ │ │ │
│ХВ-1100,
│ │ │ │ │ │
│ХВ-110, │ │ │ │ │ │
│УР-49, │ │ │ │ │ │
│УРФ-1128,│ │ │ │ │ │
│ПФ-170, │ │ │ │ │ │
│УР-19 │ │ │ │ │ │
└─────────┴─────────────────┴───────────┴─────────┴─────────┴─────────────┘
Примечания.
1. В скобках указана величина коэффициента условной влагопроницаемости по ГОСТ
22406-77.
2.
Поглощение препарата ПМВ указано в килограммах пентахлорфенола.
3.
Удержание дано в пересчете на сухую соль.
5.21.
Технологические параметры различных способов нанесения и сушки лакокрасочных
материалов механизированным способом и вручную приведены в табл. 1 и 2
Приложения 1.
5.22. Технология
пропитки под давлением маслянистыми антисептиками должна соответствовать ГОСТ
20022.5-75.
5.23. Технология
пропитки древесины водорастворимыми антисептиками способом нанесения на поверхность
должна соответствовать ГОСТ 200022.9-75.
5.24. Нанесение
лакокрасочных материалов на поверхность, обработанную водорастворимыми
антисептиками, должно осуществиться после подсушки древесины до влажности 12
+/- 2% и удаления с ее поверхности выкристаллизовавшейся соли антисептика.
6.
МАТЕРИАЛЫ ДЛЯ КОМПЛЕКСНОЙ ЗАЩИТЫ ДЕРЕВЯННЫХ КОНСТРУКЦИЙ
ОТ УВЛАЖНЕНИЯ,
БИОРАЗРУШЕНИЯ И ВОЗГОРАНИЯ
6.1. Для защиты
деревянных конструкций от увлажнения, биоразрушения и возгорания рекомендуются
составы, обладающие полным комплексом влагобиоогнезащитных свойств, или
проведение обработки огнебиозащитным материалом с последующим нанесением
влагозащитного материала.
Биоогневлагозащитные
материалы
6.2. ХВ-5169 -
перхлорвиниловая эмаль - раствор перхлорвиниловой смолы в смеси летучих
органических растворителей с добавлением других смол, пластификаторов и
пигментов. Поставляется заводом-изготовителем в готовом виде.
В отвержденном
состоянии укрывистое покрытие ХВ-5169 обладает атмосферобиоогнезащитными
свойствами, имеет прочное сцепление с древесными подложками.
6.3. Буроугольная
композиция (БК) <*> - смесь расплавленного воска, олифы
"Оксоль", буры, экстракта сиккатива и воды. Состав рецептурного приготовления.
Срок хранения состава не более 6 мес.
--------------------------------
<*> А.с. N
818870. Опубл. в Б.И., 1981, N 13.
Буроугольный воск
получают методом экстракции бурых углей бензином; температура каплепадения не
ниже 82 °C; воспламенения - 275 °C; содержание смолы не более 20%; при
нормальной температуре воск находится в твердом состоянии; химически инертен,
нетоксичен; при нагревании выше 150 °C воск разлагается с выделением
углеводородов.
- Олифа
"Оксоль" - продукт окисления растительных масел с последующим
введением сиккатива и разбавлением уайт-спиритом; содержание пленкообразующего
вещества 54,5 - 55,5%; условная вязкость по ВЗ-4 при 20 °C 18 - 25 с; время
высыхания при 20 °C 20 - 24 ч.
- Бура - см. п.
3.6.
При нагревании до
85 - 95 °C буроугольная композиция - жидкость коричневого цвета без запаха, с
плотностью при 90 °C 0,890 г/см3. БК может быть использована в качестве
покрывного и пропиточного составов.
В отвержденном
состоянии покрытие (пропитанная зона древесины) обладает атмосферостойкостью,
биоогнезащитными свойствами, имеет прочное сцепление с древесными подложками,
не скрывает текстуру древесины.
6.4. Пентафталевая
эмаль ПФ-115 с добавкой препарата огнебиозащитного действия ПББ-255.
Пентафталевая эмаль
ПФ-115 - п. 4.6, табл. 3 и 4.
Препарат ПББ - п.
3.8 табл. 1 и 2.
Материалы для
последовательной обработки
с целью защиты от
биоразрушения, возгорания и увлажнения
6.5.
Водорастворимый пропиточный состав, обладающий биоогнезащитными свойствами
(ББ-11, ХМБ-444, ТФБА, ПББ, ХМББ), с последующей обработкой влагостойким
лакокрасочным материалом (ПФ-115, ХВ-1100, МЧ-181, ПФ-133, ПФ-170, ХВ-110,
УР-49, УРФ-1128, УР-19) или последующей сушкой - пропиткой в маслянистой
гидрофобной жидкости (петролатуме).
Перед нанесением
лакокрасочных материалов на антисептированную, антипирированную поверхность
необходимо просушить древесину при мягких режимах до влажности 12%, очистить
поверхность от выкристаллизовавшейся соли антисептика-антипирена.
Использование
маслянистой жидкости позволяет совместить операцию сушки древесины, увлажненной
в процессе обработки водорастворимым биоогнезащитным составом, с ее
гидрофобизацией.
Технические и
технологические характеристики огнебиозащитных препаратов приведены в разделе 3
и в табл. 1 и 2; лакокрасочных материалов - в разделе 4 и в табл. 3 и 4;
петролатума - в разделе 5 и в табл. 5 и 6.
6.6. Технические
характеристики биоогневлагозащитных материалов приведены в табл. 7.
Таблица 7
┌─────────────┬──────────────────┬─────────────┬─────────┬────────────────────┐
│ Марка
│ Компоненты и их
│ Исходные │Раствори-│ Прочие технические │
│ материала
│соотношение, % по
├──────┬──────┤тель │
характеристики │
│ │ массе; ГОСТ, ТУ │по
│плот- │
│ │
│ │ │ВЗ-4 │ность,│ │ │
│ │ │при │г/см3 │ │ │
│ │ │20 °C,│ │ │ │
│ │ │с │
│ │ │
├─────────────┼──────────────────┼──────┼──────┼─────────┼────────────────────┤
│ 1
│ 2 │ 3
│ 4 │
5 │ 6 │
├─────────────┼──────────────────┼──────┼──────┼─────────┼────────────────────┤
│ХВ-5169 │ТУ 6-10-745-76 │30 -
│ - │
Р-4 │Укрывистое
покрытие;│
│ │ │ 70│ │ │матовое, различных │
│ │ │ │ │ │цветов, кроме │
│ │ │ │ │ │белого. Прочность │
│ │ │ │ │ │пленки при ударе │
│ │ │ │ │ │30 кгс x см; при │
│ │ │ │ │ │изгибе по шкале │
│ │ │ │ │ │гибкости не более │
│ │ │ │ │ │1 мм │
│БК │Буроугольный воск
│ │0,890 │ Олифа
│Покрытие │
│ │ТУ 39-01-232-76 │
│при
│"Оксоль" │светло-коричневого │
│ │ - 10│ │80 - │ │цвета, матовое, не │
│ │Олифа
"Оксоль" │ │ 85 °C│ │скрывающее текстуру │
│ │ГОСТ 190-78 - 70│ │ │ │древесины │
│ │Сиккатив │ │ │ │ │
│ │ГОСТ 1003-73 - 10│ │ │ │ │
│ │Бура ГОСТ 8429-77
│ │ │ │ │
│ │ -
5│ │ │ │ │
│ │Вода -
5│ │ │ │ │
│ПФ-115 │ПФ-115 │50 - │
-
│Сольвент,│Укрывистое покрытие │
│с
добавкой │ГОСТ 6465-76 - 89│
70│ │ уайт-
│различных цветов │
│ПББ-255 │ПББ-255 │ │ │ спирит │(см. табл. 3) │
│ │ГОСТ 23787.7-79 │
│ │ │ │
│ │ - 11│ │ │ │ │
│
│
│ Материалы для последовательной
биоогневлагозащитной обработки
│
│Водораствори-│См.
табл. 1 │ │ │ │ │
│мые
биоогне- │
│ │ │ │ │
│защитные │ │ │
│ │ │
│составы
ББ-11│
│ │ │ │ │
│или
ХМБ-444 │ │ │ │ │ │
│или
ТФБА или │
│ │ │ │ │
│ПББ │ │ │ │ │ │
│с
последующим│См. табл. 3 и 5
│ │ │ │ │
│нанесением │ │ │ │ │ │
│лакокрасочных│ │ │ │ │ │
│материалов │ │ │ │ │ │
│ПФ-115 │ │ │ │ │ │
│или
ХВ-1100 │ │ │ │ │ │
│или
ХВ-110 │ │ │ │ │ │
│или
МЧ-181 │ │ │ │ │ │
│или
ПФ-133 │ │ │ │ │ │
│или
ПФ-170 │ │ │ │ │ │
│или
УРФ-1128 │
│ │ │ │ │
│или
УР-19 │ │ │
│ │ │
│или
УР-49 │ │ │ │ │ │
│Водораство- │См. табл. 1 │ │ │ │ │
│римые
био- │ │ │ │ │ │
│огнезащитные
│ │ │ │ │ │
│составы │ │ │ │ │ │
│ББ-11
или │ │ │ │ │ │
│ХМБА-444
или │ │ │ │ │ │
│ТФБА
или │ │ │ │ │ │
│ПББ
или ХМББ │
│ │ │ │ │
│с
последующей│См. табл. 5
│ │ │ │ │
│сушкой- │ │ │ │ │ │
│пропиткой │ │ │ │ │ │
│в
петролатуме│ │ │ │ │ │
└─────────────┴──────────────────┴──────┴──────┴─────────┴────────────────────┘
Приготовление
биоогневлагозащитных материалов
6.7. ХВ-5169.
Лакокрасочный материал заводского изготовления. Технология приготовления
рабочего раствора приведена в п. 4.10.
6.8. Буроугольная
композиция БК. В размельченный и расплавленный буроугольный воск при
непрерывном перемешивании добавляют требуемое количество олифы
"Оксоль" и сиккатива. Растворенную в кипящей воде буру вводят в
состав медленно малыми порциями. Состав со всеми компонентами перемешивают до
получения однородной смеси в течение 20 - 30 мин.
При охлаждении
смесь загустевает и перед употреблением ее необходимо нагреть до температуры 80
- 90 °C.
6.9. Пентафталевая
эмаль ПФ-115 с добавкой ПББ-255. ПББ-255 приготовляют путем смешивания
размельченных сухих компонентов, просеянных через сито с диаметром отверстий
0,2 мм. Требуемое количество добавки ПББ в сухом порошкообразном состоянии
вводят в пентафталевую эмаль ПФ-115 малыми порциями при непрерывном
перемешивании в течение 20 - 30 мин.
Технология
защитной обработки
6.10. Технология
защитной обработки биоогневлагозащитными материалами с указанием уровня их
защитной способности приведена в табл. 8.
Таблица 8
┌────────┬─────────────────────┬────────┬──────┬──────┬───────────────────────────────┐
│Защитное│ Способ защитной │Поглоще-│Толщи-│Адге-
│ Уровень защитной способности
│
│средство│ обработки │ние ПГ, │на │зион-
├────────────┬──────────┬───────┤
│ │ │кг/м3. │покры-│ная │влагозащита
│огнезащита│био- │
│ │ │Расход │тия,
│проч- │
│ │защита
│
│
├──────────┬──────────┤РД, │мкм
│ность,├────────────┼──────────┼───────┤
│ │рекоменду-│допуска- │г/м2.
│ │МПа │категория │группа │группа │
│ │емый │емый │Удержа- │ │ │защитных │горючести │био- │
│ │ │ │ние УД, │ │
│покрытий и │защищенной│стой- │
│ │ │ │г/м2 │
│ │пропиточных
│древесины │кости │
│ │ │ │ │ │ │составов │по ГОСТ │защи-
│
│ │ │ │ │
│ │по ГОСТ │16363-76 │щенной │
│ │ │ │ │ │ │22406-77 │(потеря │древе- │
│ │ │ │ │ │ │(показатель │массы │сины │
│ │ │ │ │ │ │условной │образцов │
│
│ │ │ │ │ │ │влагопро- │при огне- │ │
│ │ │ │ │ │ │ницаемости) │вых испы-
│ │
│ │ │ │ │ │ │ │таниях, %)│ │
├────────┼──────────┼──────────┼────────┼──────┼──────┼────────────┼──────────┼───────┤
│ 1
│ 2 │
3 │ 4
│ 5 │
6 │ 7
│ 8 │
9 │
├────────┼──────────┼──────────┼────────┼──────┼──────┼────────────┼──────────┼───────┤
│ХВ-5169
│Пневмати- │Кисть,
│РД 600 │ 250 │1,9 - │Влагозащит-
│Трудновос-│Био- │
│ │ческое │валик │ │ │
2,8│ное покры-
│пламеняе- │стойкая│
│ │распыление│ │ │ │ │тие (0,17) │мая (21) │
│
│БК │Пневмати- │Кисть, │РД 130 │80 -
│1,5 - │То же (0,29)│То же (25)│ То же │
│(покров-│ческое │валик │ │ 100│
2,1│ │ │ │
│ный │распыление│ │ │ │ │ │ │ │
│состав)
│с нагревом│
│РД 270 │130 -
│2,0 - │ " (0,15)│ "
(23)│ " │
│ │ │ │ │ 150│
3,0│ │ │ │
│БК │Прогрев │ │ПГ 46 - │ -
│ - │Влаго- │
" (20)│ "
│
│(пропи-
│сухим │ │ 60│ │ │защитный │ │ │
│точный │воздухом -│ │ │ │ │пропиточный │ │
│
│состав)
│прогрев │ │ │ │ │состав │ │ │
│ │паром - │ │ │ │ │(0,19) │ │ │
│ │погружение│Прогрев │ПГ 30 - │ -
│ - │То же (0,32)│ "
(28)│ " │
│ │в раствор │сухим │ 45│ │ │ │ │ │
│ │ │воздухом -│ │ │ │ │ │ │
│ │ │погружение│ │ │ │
│ │ │
│ │ │в раствор;│ │ │ │ │ │ │
│ │ │погружение│ │ │ │ │ │ │
│ │ │в раствор │ │ │
│ │ │ │
│ПФ-115
с│Пневмати- │Кисть,
│РД 250 -│100 - │2,5 - │Влагозащит- │ "
(25)│ " │
│добавкой│ческое │валик │
300│ 120│ 3,0│ное покры- │ │ │
│ПББ-255
│распыление│
│ │ │
│тие (0,32) │ │ │
│
│
│ Материалы для последовательной биоогневлагозащитной обработки │
│Водные │Способы │Способы │УД 40 - │ -
│ - │
-
│Трудновос-│
" │
│растворы│Б,
В <1> │Д, Е, Ж │
60 <2>│ │ │ │пламеняе- │ │
│биоогне-│ │ │ │ │ │ │мая │ │
│защитных│ │Способы │ПГ 60 - │ -
│ - │
- │Трудно- │
" │
│составов│ │Д, Е, Ж │
90│ │ │ │горючая │
│
│с
после-│Пневмати- │Безвоздуш-│РД 250 -│100 - │1,8
- │Влагоза- │ │ │
│дующим │ческое │ное распы-│ 350│ 150│
3,2│щитное │ │ │
│нанесе-
│распыление│ление,
│ │ │ │покрытие │ │ │
│нием │ │кисть, │ │ │ │(0,15 - │ │ │
│лакокра-│
│валик │ │ │ │ 0,32)│ │ │
│сочных │ │ │ │ │ │ │ │ │
│материа-│ │ │ │ │ │ │ │ │
│лов │ │ │ │ │ │ │ │ │
│Водный │Способ │Способ Д │ПГ 60 - │ -
│ - │
-
│Трудновос-│Био-
│
│раствор
│Е, Ж │ │ 90│ │ │ │пламеняе- │стойкая│
│биоогне-│ │ │ │ │ │ │мая │ │
│защитных│ │ │ │ │ │ │ │ │
│составов│ │ │ │ │ │ │ │
│
│с
после-│Способ Д │ -
│ │ │ │Влагоза- │ │ │
│дующей │ │ │ │ │ │щитный │ │ │
│сушкой-
│ │ │ │ │ │пропиточ- │ │ │
│пропит-
│ │ │ │ │ │ный состав │ │ │
│кой
в │ │ │ │ │ │(0,26 - │ │ │
│петрола-│ │ │ │ │ │
0,32)│ │ │
│туме
<3>│ │ │ │ │ │ │ │ │
└────────┴──────────┴──────────┴────────┴──────┴──────┴────────────┴──────────┴───────┘
Примечания.
1. Способы пропитки приведены в примечании 3 табл. 2.
2. В
пересчете на сухую соль антисептика (антипирена).
3. После пропитки
необходимо удалить избытки петролатума с поверхности пропитанных элементов до
их остывания.
6.11. ХВ-5169.
Технологические параметры механизированного и ручного способов нанесения и
сушки лакокрасочного материала приведены в табл. 1 и 2 Приложения 1.
6.12. а) БК -
покровный состав. Нанесение буроугольной композиции может осуществляться
механизированным способом (пневматическим распылением с нагревом) и вручную
(кисть, валик).
Перед нанесением
защитной композиции необходимо в течение 30 - 40 мин прогревать поверхность
древесины сухим воздухом с температурой 80 °C. Температура рабочего раствора
должна быть 80 - 90 °C. Рабочая вязкость раствора по ВЗ-4 при указанной
температуре 30 - 35 с. Толщина одного слоя при пневматическом распылении 35 -
40 мкм, при ручном нанесении 60 - 70 мкм.
б) БК - пропиточный
состав. Пропитка может осуществляться следующими способами: прогрев сухим
воздухом - погружение в раствор; прогрев сухим воздухом - прогрев паром -
погружение в раствор; погружение в раствор.
Первый способ
пропитки. Температура сухого воздуха при прогреве 100 °C, температура раствора
80 °C. Продолжительность выдержки при прогреве воздухом и в растворе не менее 1
ч.
Второй способ
пропитки. Температура сухого воздуха при прогреве - 80 °C; температура влажного
пара - 120 °C, температура раствора - 80 °C. Продолжительность выдержки при
прогреве воздухом и паром - не менее 30 - 40 мин; в растворе - не менее 1 ч.
Третий способ
пропитки. Температура рабочего раствора 80 °C. Продолжительность выдержки в
растворе не менее 1 ч.
6.13. ПФ-115 с
добавкой ПББ-255. Технологические параметры нанесения аналогичны параметрам
нанесения лакокрасочного материала ПФ-115 без добавки (см. табл. 1 и 2
Приложения 1).
7. КОНТРОЛЬ
КАЧЕСТВА ЗАЩИТНЫХ МАТЕРИАЛОВ
И ЗАЩИТНЫХ
ОБРАБОТОК
7.1. Для
обеспечения высокого качества защитных покрытий и пропиток, а также их
эксплуатационной стойкости обязательно строгое соблюдение технологического
процесса защитной обработки. Контролю подлежат:
- материалы,
применяемые для защитной обработки;
-
последовательность основных операций;
- режимы
технологической операции.
Контроль
качества защитных материалов
7.2. Защитные
материалы и их компоненты должны иметь паспорт завода-изготовителя с указанием
срока их годности.
7.3. Защитные
материалы (пропиточные составы, лакокрасочные материалы) должны удовлетворять
требованиям соответствующих ГОСТ или ТУ и контролироваться по показателям,
указанным в этих нормативных документах.
Пропиточные составы
7.4. При
приготовлении рабочих пропиточных растворов необходимо контролировать:
- дозировку
компонентов;
- температуру воды
для водорастворимых составов (термометр по ГОСТ 215-73);
- концентрацию
приготовленного раствора по его плотности (ареометр по ГОСТ 1300-74).
Лакокрасочные
материалы
7.5. При
приготовлении рабочих лакокрасочных составов необходимо контролировать:
- вязкость по ГОСТ
8420-74;
- содержание
нелетучих веществ по ГОСТ 17537-72.
Контроль
качества защитной обработки
при использовании
пропиточных составов
7.6. При
пропитке способом нанесения на поверхность необходимо контролировать удержание
пропиточной жидкости, определяемое по разности массы пропитываемого материала
до и после пропитки.
Удержание защитного
средства в г/м2 вычисляют по формуле
, (1)
где Q - количество
удержанной пропиточной жидкости, г;
C - концентрация
раствора антисептика-антипирена, %;
S - площадь
пропитываемой поверхности, м2.
7.7. При пропитке
способом погружения определение проводят для каждой загрузки изделий; для
пропитки способом опрыскивания и нанесения кистью на 20 деталях (элементах).
При пропитке
древесины (фанеры) в конструкциях удержание защитного средства определяют по
расходу пропиточной жидкости по формуле
, (2)
где
- масса емкости с пропиточной жидкостью до
пропитки, г;
- масса емкости с пропиточной жидкостью после
пропитки, г.
7.8. При
пропитке способом вымачивания необходимо контролировать глубину пропитки и
поглощение пропиточной жидкости по разности массы пропитываемого материала до и
после пропитки.
Поглощение
защитного средства в кг/м3 вычисляют по формуле
, (3)
где Q и C - см. п.
7.6;
V - объем
пропитываемого материала, м3.
Глубину пропитки в
загрузке определяют на 10 случайно выбранных изделиях не позднее чем через 2 ч
после их выгрузки из ванны.
Пробу для
определения глубины пропитки берут посередине длины изделий пустотелым буром с
внутренним диаметром 5 мм.
Глубину пропитки
защитными средствами, окрашивающими древесину, определяют по ширине окрашенной
зоны; для неокрашивающих защитных средств необходимо предварительное нанесение
на поверхность пробы раствора индикатора.
7.9. При пропитке
панельным способом необходимо контролировать глубину пропитки из расчета одна
проба на каждые 3 м2 панели и поглощение пропиточной жидкости по каждой панели.
Методика
определения глубины пропитки приведена в п. 7.8.
Удельное поглощение
защитного средства
в кг на 1 м2 панели вычисляют по формуле
, (4)
где Q - расход
пропиточной жидкости на панель, кг;
C - концентрация
защитного средства в пропиточной жидкости, %;
S - площадь панели.
7.10. При пропитке
способами прогрев-холодная ванна, вакуум-атмосферное давление-вакуум,
давление-давление-вакуум, вакуум-давление-вакуум необходимо контролировать
глубину пропитки и поглощение по разности объема пропиточной жидкости до и
после пропитки.
Методика
определения глубины пропитки и поглощения защитного средства в кг/м3 приведена
в п. 7.8.
При пропитке в
маслянистых жидкостях поглощение (q) определяют по формуле
, (5)
где
- количество поглощенной пропиточной жидкости,
м3;
- плотность маслянистой пропиточной жидкости,
кг/м3.
Контроль
качества защитной обработки
при использовании
лакокрасочных материалов
7.11. Лакокрасочные
покрытия (после полного завершения всех операций по нанесению и сушки
лакокрасочных материалов) контролируют по следующим показателям:
- соответствие
декоративного вида покрытия требованиям ГОСТ 9.032-74;
- адгезия пленки
покрытий к защищаемой поверхности по методике, приведенной в Приложении 8;
- толщина
лакокрасочного покрытия по ГОСТ 13639-75 (для прозрачных покрытий), по ГОСТ
14644-75 (для непрозрачных покрытий).
8. ТЕХНИКА
БЕЗОПАСНОСТИ
8.1. При
организации и производстве всех видов работ по защитной обработке конструкций,
при проектировании цехов, имеющих в своем составе окрасочные отделения и
отделения пропитки конструкций био- и биоогнезащитными составами (препаратами),
необходимо соблюдать все действующие правила по технике безопасности и пожарной
безопасности, изложенные в следующих документах:
СНиП III-А.11-70.
Техника безопасности в строительстве
СНиП II-А.5-70*.
Противопожарные нормы проектирования зданий и сооружений
СНиП II-М.2-72*.
Производственные здания промышленных предприятий. Нормы проектирования
СН 245-71.
Санитарные нормы проектирования промышленных предприятий. М.: Стройиздат, 1972
Правила и нормы
техники безопасности, пожарной безопасности и производственной санитарии для
окрасочных цехов. М.: ВЦНИИОТ, 1974
НиТУ 108-56. Нормы
и технические условия проектирования складских предприятий и хозяйств для
хранения легковоспламеняющихся и горючих жидкостей
Правила техники
безопасности и промышленной санитарии в деревообрабатывающей промышленности.
М.: Стройиздат, 1966
ГОСТ 12.3.005-75.
Система стандартов безопасности труда. Работы окрасочные. Общие требования
безопасности
ГОСТ 12.1.004-76.
Система стандартов безопасности труда. Пожарная безопасность. Общие требования
ГОСТ 12.1.005-76.
Система стандартов безопасности труда. Воздух рабочей зоны. Общие
санитарно-гигиенические требования.
Техника
безопасности при работе
с биоогне- и
биовлагозащитными пропиточными составами
8.2. Сухие
порошкообразные вещества до употребления должны храниться в помещении,
защищенном от атмосферных осадков. Хранение их без тары (навалом) запрещается.
8.3. Деревянная и
бумажная тара из-под биовлаго- и биоогнезащитных препаратов должна
уничтожаться. Металлическая тара после тщательной промывки теплой водой может
быть использована для технических целей.
8.4. Раскупоривание
тары с пылящими компонентами должно производиться под вытяжным зонтом.
8.5. Участки цехов,
где проводят работы по приготовлению растворов, должны иметь приточно-вытяжную
вентиляцию. Приготовление растворов должно производиться в закрытых емкостях,
снабженных механическими мешалками. Во избежание распыления порошкообразные
компоненты перед загрузкой рекомендуется слегка смачивать водой. Перемешивание
раствора в реакторе должно производиться при закрытом люке.
Пропиточные ванны
как загруженные, так и незагруженные должны быть закрыты крышками.
8.6. Рабочие должны
быть обеспечены специальными одеждой и обувью, а также индивидуальными
средствами защиты глаз, кожных покровов и органов дыхания (см. Приложение 4).
8.7. При попадании
пропиточных растворов или сухих солей на кожу необходимо промыть это место
большим количеством теплой воды с мылом. При попадании их в глаза нужно промыть
глаза большим количеством теплой воды и 3%-ным раствором борной кислоты, а
затем обратиться к врачу.
Состав защитных
паст и мазей, применяемых для профилактики кожных заболеваний, приведен в
Приложении 5.
8.8. Специальная
одежда должна подвергаться стирке или химчистке не реже 1 раза в 10 сут.
8.9. Рабочие должны
быть обеспечены набором бытовых помещений в соответствии с санитарными нормами
проектирования промышленных предприятий, утвержденными Государственным
комитетом СССР по делам строительства.
8.10. Курить и
принимать пищу на месте проведения работ запрещается.
8.11. По окончании
работ персонал должен пройти санитарную обработку (вымыться под душем, прополоскать
рот, сменить одежду).
8.12. Стены, полы и
потолки в помещении, где производятся работы по приготовлению растворов и по
защите деревянных конструкций, должны быть удобными для влажной уборки. Полы
должны иметь уклон 1/100.
8.13. Загрязнять
водоемы отходами биовлаго- и биоогнезащитных составов и препаратов
категорически запрещается. Места стока смывных вод после чистки ванн и способы
обезвреживания вод должны быть заранее определены и согласованы с
санинспекцией.
Техника
безопасности при работе
с лакокрасочными
материалами
8.14. Используемые
лаки и эмали, как правило, являются пожароопасными и токсичными материалами,
что обусловлено свойствами растворителей, пластификаторов, разбавителей и др.
компонентов (см. Приложения 2 и 3).
8.15. При приготовлении
и нанесении лакокрасочных материалов должны строго соблюдаться требования
правил пожарной безопасности и промышленной санитарии.
8.16. Все работы,
связанные с приготовлением и нанесением лакокрасочных материалов, должны
проводиться в помещениях, оборудованных приточно-вытяжной вентиляцией и
противопожарными средствами.
8.17. Содержание
вредных веществ в воздухе рабочей зоны не должно превышать предельно допустимые
концентрации (см. Приложение 2).
8.18. Лица,
выполняющие работы по приготовлению и нанесению лакокрасочных материалов,
должны быть обеспечены средствами индивидуальной защиты (см. Приложение 4).
8.19. Хранение
лакокрасочных материалов в производственных помещениях, за исключением
помещений лакоприготовительной и централизованной подачи, не допускается. В
помещениях лакоприготовительной и централизованной подачи допускается хранение
этих материалов в плотно закрытой таре в количествах не выше сменной
потребности.
8.20. На каждой
бочке, бидоне, банке и другой таре с лакокрасочным материалом и растворителем
должны быть наклейки и бирки с точным названием и обозначением этих материалов.
Тара должна быть исправной, с плотно закрывающейся крышкой.
8.21. Порожняя тара
из-под растворителей и лакокрасочных материалов должна немедленно удаляться из
помещения и храниться на специальных площадках не ближе, чем 20 м от
производственных помещений.
8.22. Оборудование
по централизованной подаче лакокрасочных материалов, нанесению, а также сушке
лакокрасочных покрытий следует содержать под постоянным наблюдением,
обеспечивающим его герметичность.
Неплотности в
трубопроводах, воздуховодах и т.п., обнаруженные в процессе эксплуатации,
подлежат немедленному устранению.
8.23. Очистка
оборудования для нанесения лакокрасочных покрытий от осевших материалов должна
производиться после каждой смены при работающей вентиляции.
8.24. Выбор
растворителей должен производиться с учетом их вредности. Если для разбавления
того или иного состава могут применяться растворители разного класса опасности
(см. Приложение 2), предпочтение следует отдать наименее вредным из них.
Приложение
1
ТЕХНОЛОГИЧЕСКИЕ
ПАРАМЕТРЫ ЗАЩИТНОЙ ОБРАБОТКИ
ЛАКОКРАСОЧНЫМИ
МАТЕРИАЛАМИ
Таблица 1
┌────────┬─────────────────────────────────────────────────────────────────────────────┐
│Лакокра-│ Способы
нанесения
│
│сочный
├────────────┬───────────────────┬────────────────────────────────────────────┤
│материал│ вручную
│ пневматическое │
Безвоздушное распыление
│
│ │
(кисть, │ распыление без ├───────────────────┬────────────────────────┤
│ │ валик)
│ подогрева │
без подогрева │ с
подогревом │
│
├──────┬─────┼──────┬──────┬─────┼──────┬──────┬─────┼──────┬─────┬─────┬─────┤
│ │рабо- │тол- │рабо-
│давле-│тол- │рабо- │рабо- │тол- │рабо-
│рабо-│тол- │тем- │
│ │чая │щина │чая │ние
│щина │чая
│чее │щина │чая │чее
│щина │пера-│
│ │вяз- │одно-│вяз- │сжато-│одно-│вяз- │дав-
│одно-│вяз-
│дав- │одно-│тура │
│ │кость │го │кость │го │го
│кость │ление,│го
│кость │ле-
│го │на- │
│ │по │слоя,│по │возду-│слоя,│по │МПа
│слоя,│по
│ние, │слоя,│гре- │
│ │ВЗ-4 │мкм
│ВЗ-4 │ха, │мкм
│ВЗ-4 │ │мкм │ВЗ-4
│МПа │мкм │вания│
│ │при │
│при │МПа │
│при │ │ │при │
│ │мате-│
│ │20 °C,│ │20 °C,│ │
│20 °C,│
│ │20 °C,│ │
│риа- │
│ │с │
│с │ │ │с │ │ │с │
│ │ла, │
│ │ │ │ │ │ │ │ │ │ │ │
│°C │
├────────┼──────┼─────┼──────┼──────┼─────┼──────┼──────┼─────┼──────┼─────┼─────┼─────┤
│ 1
│ 2 │
3 │ 4
│ 5 │
6 │ 7
│ 8 │
9 │ 10
│ 11 │ 12 │ 13
│
├────────┼──────┼─────┼──────┼──────┼─────┼──────┼──────┼─────┼──────┼─────┼─────┼─────┤
│ПФ-115,
│40 - │25 - │25 - │0,20 -│20 - │30 - │13 -
│25 - │75 -
│ 6 │45 - │90 - │
│ПФ-133 │
45│ 40│ 32│
0,25│ 30│ 45│
20│ 35│ 80│ │
50│ 100│
│ПФ-170 │40 -
│20 - │20 -
│0,20 -│15 - │
60 │12 - │20 - │ -
│ - │
- │ -
│
│ │ 45│
25│ 25│ 0,25│
25│ │ 16│
35│ │ │
│ │
│ХВ-110 │
│ │ │ │ │ │ │ │ │ │
│ │
│ХВ-124 │38 -
│25 - │17 -
│0,20 -│15 - │8 - 22│12 - │20 - │40 - │
6 │35 - │50 - │
│ │ 40│
30│ 23│ 0,25│
25│ │ 15│
25│ 45│ │
40│ 60│
│ХВ-1100
│ │ │ │ │ │ │ │ │ │ │
│ │
│ХВ-5169
│38 - │25 - │18 - │0,25 -│25 - │ -
│ - │
- │ - │
- │ -
│ - │
│ │ 40│
30│ 22│ 0,30│
35│ │ │ │ │ │
│ │
│ХВ-784 │20 -
│20 - │16 -
│0,20 -│10 - │18 -
│12 - │18 -
│ - │
- │ -
│ - │
│ │ 40│
25│ 22│ 0,25│
15│ 22│ 15│
22│ │ │
│ │
│ХВ-785 │35 -
│25 - │17 -
│0,20 -│15 - │18 -
│12 - │20 - │40
- │ 6
│35 - │50 - │
│ │ 40│
35│ 20│ 0,25│
25│ 22│ 15│
25│ 45│ │
40│ 60│
│УР-49 │30 -
│25 - │13 -
│0,25 -│15 - │ - │
- │ -
│ - │
- │ -
│ - │
│ │ 60│
30│ 15│ 0,30│
20│ │ │ │ │ │
│ │
│УР-293 │
- │25 - │13 - │0,25 -│10 - │ -
│ - │
- │ -
│ - │
- │ -
│
│ │ │
35│ 15│ 0,30│
15│ │ │ │ │ │
│ │
│УРФ-1128│35
- │25 - │18 - │0,25 -│25 - │ -
│ - │
- │ -
│ - │
- │ -
│
│ │ 40│
35│ 20│ 0,30│
30│ │ │ │ │ │
│ │
│ОС-12-03│20
- │20 - │20 - │0,25 -│30 - │ 25
│12 - │ 35 │40 -
│ 6 │45 - │50 - │
│ │ 60│
35│ 25│ 0,30│
40│ │ 15│ │
45│ │ 50│
60│
└────────┴──────┴─────┴──────┴──────┴─────┴──────┴──────┴─────┴──────┴─────┴─────┴─────┘
Таблица 2
Технологические
параметры сушки лакокрасочных материалов
┌─────────────┬───────────────────────────────────────────────────────────┐
│Лакокрасочное│ Продолжительность │
│ покрытие
├───────────────────────┬─────────────────────┬─────────────┤
│ │практического
высыхания│ межслойной сушки, ч │
полной │
│ │ при температуре
├──────────┬──────────┤полимеризации│
│ │ 18 - 23 °C x ч │18 - 23 °C│50 - 65 °C│
пленки, сут │
├─────────────┼───────────────────────┼──────────┼──────────┼─────────────┤
│ПФ-115 │ 24 - 48 │
24 │ 1
│ 5 │
│ПФ-133 │ 36 │ 8
│ - │
5 │
│ПФ-170 │ 72 │ 48
│ 3 │
5 │
│ХВ-110 │ 3 │ 1
│ 0,5 │
5 - 7 │
│ХВ-124 │ 2 │ 1
│ 0,3 │
5 - 7 │
│ХВ-1100 │ 1 │ 0,5
│ 0,3 │
5 - 7 │
│ХВ-5169 │ 3 │ 1
│ 0,5 │
5 - 7 │
│ХВ-784 │ 1 │ 1
│ 0,5 │
7 - 10 │
│ХВ-785 │ 6 │ 2
│ 1 │
7 - 10 │
│УР-49 │ 24 │ -
│ - │
5 │
│УР-293 │ 20 │ 20
│ - │
5 │
│УРФ-1128 │ 6 │ 6
│ 1,5 │
2 │
│ОС-12-03 │
24 │ 1
│ - │
5 - 7 │
│МЧ-181 │ 24 │ -
│ 0,5 │
5 - 7 │
└─────────────┴───────────────────────┴──────────┴──────────┴─────────────┘
Приложение
2
ПРЕДЕЛЬНО
ДОПУСТИМЫЕ КОНЦЕНТРАЦИИ
ВРЕДНЫХ ВЕЩЕСТВ В
ВОЗДУХЕ РАБОЧЕЙ ЗОНЫ
┌────────────────────────────────┬──────────┬─────────────┬───────────────┐
│ Наименование вещества │ Величина │ Класс
│ Агрегатное │
│ │ПДК,
мг/м3│опасности <*>│
состояние │
├────────────────────────────────┼──────────┼─────────────┼───────────────┤
│Ацетон │ 200
│ 4 │Пары │
│Кислота
борная │ 10
│ 3 │Пары и аэрозоли│
│Ксилол │ 50
│ 3 │Пары │
│Кислота
уксусная │ 5
│ 3 │То же │
│Сольвент-нафта
(в пересчете │ 100
│ 4 │ " │
│на
C) │ │ │ │
│Толуол │ 50
│ 3 │ " │
│Уайт-спирит
(в пересчете на C) │ 300
│ 4 │ " │
│Фтористоводородной
кислоты соли │ 1 │ 2 │Аэрозоли │
│(в
пересчете на HF) │ │ │ │
│Хроматы,
бихроматы (в пересчете │
0,01 │ 1
│То же │
│на
CrO ) │ │ │ │
│ 3 │ │ │ │
│Четыреххлористый
углерод │ 20
│ 2 │Пары │
│Бутилацетат │ 200
│ 4 │То же │
│Пентахлорфенол │ 0,1
│ 1 │Пары и аэрозоли│
│Пентахлорфенолят
натрия │ 0,1
│ 1 │То же │
└────────────────────────────────┴──────────┴─────────────┴───────────────┘
--------------------------------
<*>
Согласно ГОСТ 12.1.007-76, вредные вещества по степени воздействия на организм
подразделяются на 4 класса опасности:
1 класс - вещества
чрезвычайно опасные;
2 класс - вещества
высокоопасные;
3 класс - вещества
умеренно опасные;
4 класс - вещества
малоопасные.
Приложение
3
ХАРАКТЕРИСТИКА
ПОЖАРООПАСНОСТИ РАСТВОРИТЕЛЕЙ
┌──────────────┬───────────────────────────────────┬──────────────────────┐
│
Растворитель │
Температура, °C │
Пределы взрываемости │
│
├─────────────────┬─────────────────┤
в смеси с воздухом, │
│ │ вспышки
│самовоспламенения│
% (по объему) │
├──────────────┼─────────────────┼─────────────────┼──────────────────────┤
│Ацетон │ -18
│ -500 │ 2,15 - 1,0 │
│Ксилол │ 17 - 29
│ 553 - 618 │
2,2 - 14,7 │
│Сольвент │ 34
│ 520 │ 1,0 - 3,8 │
│Толуол │ 30 - 40
│ 536 │ 1,28 - 7,0 │
│Уайт-спирит │
33 │ 260
│ 1,4 - 6,0 │
│Р-4 │ -7
│ 550 │ 1,65 (нижний) │
│Р-5 │ -1
│ 497 │ 1,83 (нижний) │
│Р-24 │ -6
│ 461
│ - │
└──────────────┴─────────────────┴─────────────────┴──────────────────────┘
Приложение
4
СРЕДСТВА
ИНДИВИДУАЛЬНОЙ ЗАЩИТЫ
ДЛЯ РАБОЧИХ,
ЗАНЯТЫХ НА ОПЕРАЦИЯХ ПО ПРИГОТОВЛЕНИЮ
И НАНЕСЕНИЮ
ЗАЩИТНЫХ СОСТАВОВ И ПРЕПАРАТОВ
┌─────────┬──────────────┬─────────────────────────────────────────────────────────────────┐
│Составы │
Операции │ Наименование средств индивидуальной
защиты │
│(препара-│ ├──────┬──────┬───────┬────┬─────┬─────┬─────┬─────────┬─────┬────┤
│торы) │
│комби-│комби-│фартук
│шлем│сапо-│бо-
│пер- │рукавицы │рес- │очки│
│ │ │незон │незон
│клеен- │х/б │ги
│тинки│чатки├─────┬───┤пира-│за-
│
│ │ │х/б с │х/б │чатый
│
│рези-│кожа-│рези-│ком-
│х/б│тор │щит-│
│ │ │кисло-│ │или │
│новые│ные
│новые│бини-│
│ │ные │
│ │ │то- │
│проре- │
│ │ │
│ро- │ │
│ │
│ │ │стой- │ │зинен- │ │
│ │ │ван- │ │
│ │
│ │ │кой │
│ный с │ │
│ │ │ные
│ │ │
│
│ │ │про- │
│нагруд-│ │
│ │ │
│ │ │
│
│ │ │питкой│ │ником │
│ │ │
│ │ │
│ │
├─────────┼──────────────┼──────┼──────┼───────┼────┼─────┼─────┼─────┼─────┼───┼─────┼────┤
│Пропиточ-│Раскупоривание│
+
│ │ │ + │
+ │ │
│ + │
│ + │ +
│
│ные │тары │ │ │
│ │ │
│ │ │
│ │ │
│составы
и│Приготовление │ + │
│ + │ +
│ + │
│ + │
│ │ │
│
│препараты│раствора │ │ │ │ │
│ │ │
│ │ │
│
│ │Пропитка, │
+ │ │
+ │ + │
+ │ │
+ │ │
│ │ │
│ │укладка │ │ │
│ │ │
│ │ │
│ │ │
│ │пропитанных │
│ │ │ │
│ │ │
│ │ │
│
│ │заготовок │ │ │
│ │ │
│ │ │
│ │ │
│Лакокра-
│Приготовление │
│ + │
+ │ │
│ + │
│ + │
│ + │ +
│
│сочные │рабочих │ │ │
│ │ │
│ │ │
│ │ │
│материалы│составов │ │ │ │ │
│ │ │
│ │ │
│
│ │Нанесение │
│ +
│ │ + │
│ + │
│ + │
│ + │ +
│
│ │составов │ │ │
│ │ │
│ │ │
│ │ │
│ │ручным краско-│ │ │ │ │
│ │ │
│ │ │
│
│ │распылителем │
│ │ │ │
│ │ │
│ │ │
│
│ │Нанесение │ │
+ │ +
│ │ │
+ │ │
│ + │ + │
│
│ │составов │ │ │
│ │ │
│ │ │
│ │ │
│ │кистью, вали- │ │ │ │ │
│ │ │
│ │ │
│
│ │ком, шпателем │ │ │ │ │
│ │ │
│ │ │
│
│ │Нанесение │ │
+ │ +
│ + │ │
+ │ │
+ │ │
│ │
│ │составов │ │ │
│ │ │
│ │ │
│ │ │
│ │на конвейере │
│ │ │ │
│ │ │
│ │ │
│
│ │и окрасочных │
│ │ │ │
│ │ │
│ │ │
│
│ │камерах │ │ │
│ │ │
│ │ │
│ │ │
│ │Очистка окра- │ │
+ │ │ + │
│ + │
│ + │
│ + │
│
│ │сочных камер │
│ │ │ │
│ │ │
│ │ │
│
└─────────┴──────────────┴──────┴──────┴───────┴────┴─────┴─────┴─────┴─────┴───┴─────┴────┘
Примечание. Срок
носки комбинезонов, шлема, сапог и ботинок - 12 мес, фартука - 6 мес, рукавиц
комбинированных - 1 мес, рукавиц х/б - 2 мес, респиратора и защитных очков - до
износа.
Приложение
5
СОСТАВ
ЗАЩИТНЫХ ПАСТ И МАЗЕЙ,
ПРИМЕНЯЕМЫХ ДЛЯ
ПРОФИЛАКТИКИ КОЖНЫХ ЗАБОЛЕВАНИЙ
┌──────────────────────────┬──────────────────────────────────────────────┐
│ Компоненты │ Количество компонентов, % │
│
├───────────────────────────────────────┬──────┤
│ │ пасты │мазь │
│
├──────┬─────┬────┬──────┬─────────┬────┤Селис-│
│
│Хиот-6│ИЭР-1│ПМ-1│"Ялот"│"Биоло- │"Ми-│ского │
│ │ │ │
│ │гические
│ко- │ │
│ │ │ │
│
│перчатки"│лан"│ │
├──────────────────────────┼──────┼─────┼────┼──────┼─────────┼────┼──────┤
│ 1 │ 2
│ 3 │ 4
│ 5 │
6 │ 7 │
8 │
├──────────────────────────┼──────┼─────┼────┼──────┼─────────┼────┼──────┤
│Желатин
пищевой или │ 2,4 │ │ 2
│ │ 19,7
│ │ 1,9 │
│фотожелатин │ │ │
│ │ │ │
│
│Крахмал
пшеничный │ 5,6 │ │14,1│ │ │ │ 14,1 │
│или
картофельный │ │ │
│ │ │ │
│
│Глицерин │ 72,0 │ 10 │10,6│ │ │ │ 14,1 │
│Жидкость
Бурова │ 10,0 │ │
│ │ │ │
│
│Тальк │ │ │ 8,1│ 1,2 │ │ │ 21,1 │
│Бензин
или борная кислота │
│ │ │
│ │ │
1,9 │
│Мыло
натриевое │ │ 12 │
│ │ │ │
│
│Каолин │ │ 40 │10,1│ │ │ 30 │ │
│Вазелиновое
масло │ │ │ 7,5│ │ │ │
9,4 │
│Салициловая
кислота │ │ │ 0,3│ │ │ │
│
│Спирт
этиловый │ │ │ 1,7│ │
58,7 │ │
│
│Мыло
ядровое │ │ │
│ 39,6 │
│ 10 │ │
│Касторовое
масло │ │ │
│ 19,6 │
│ │ │
│Казеин │ │
│ │ │
19,7 │ │
│
│Аммиак
(25%-ный) │ │ │
│ │ 1,9
│ │ │
│Ланолин │ │ │
│ │ │ 10 │ │
│Вода │ 10 │ 38
│43,6│ 39,6 │
│ 50 │ 37,5 │
└──────────────────────────┴──────┴─────┴────┴──────┴─────────┴────┴──────┘
Приложение
6
СТОИМОСТЬ ОСНОВНЫХ
МАТЕРИАЛОВ,
ИСПОЛЬЗУЕМЫХ ДЛЯ
ЗАЩИТНОЙ ОБРАБОТКИ КОНСТРУКЦИЙ
┌──────────────────────────────┬────────────────┬────────────┬────────────┐
│ Наименование материала │ ГОСТ, ОСТ, ТУ │Прейскурант-│Прейскурант │
│ │ │ная цена 1 т│ │
│ │ │материала │ │
│ │ │в руб. │ │
├──────────────────────────────┼────────────────┼────────────┼────────────┤
│ 1 │ 2
│ 3 │ 4
│
├──────────────────────────────┴────────────────┴────────────┴────────────┤
│ Лакокрасочные
материалы │
│Перхлорвиниловая
эмаль ХВ-1100│ГОСТ 6993-79
│ 600 - 730 │ N 05-04
М.,│
│ │ │ │ 1980
│
│Перхлорвиниловая
эмаль ХВ-210 │ГОСТ 18374-79
│ 750 - 1000 │ То
же │
│Перхлорвиниловая
эмаль ХВ-5169│ТУ 6-10-748-75
│ 650 │
" │
│бежевая,
шаровая │ │ │ │
│Пентафталевая
эмаль ПФ-115 │ГОСТ 6465-76 │ 850 - 1420 │ "
│
│Уретаново-алкидная
эмаль │ТУ 6-10-1421-76
│1200 - 1400 │
" │
│УРФ-1128 │ │ │ │
│Пентафталевая
эмаль ПФ-133 │ГОСТ 926-63 │ 750 - 1250 │ "
│
│Пентафталевый
лак ПФ-170 │ГОСТ 15907-70 │
820 │ "
│
│Алкидно-карбамидная
эмаль │ТУ 6-10-720-74 │ 780 - 1100 │ "
│
│МЧ-181 │ │ │ │
│Уретановый
лак УР-293 │ТУ 6-10-1462-74
│ 1800 │
" │
│Буроугольный
воск │ТУ 39-01-232-76
│ 2200 │
" │
│Перхлорвиниловый
лак ХВ-784 │ГОСТ 7313-75 │ 580 - 670 │
" │
│Перхлорвиниловая
эмаль ХВ-785 │ │ │ │
│
│
│ Огнезащитные
краски │
│Огнезащитное
фосфатное │ГОСТ
23790-79 │ 450
│ │
│покрытие
ОФП │ │ │ │
│Огнезащитное
вспучивающееся │ГОСТ
25130-82 │ 1150
│ │
│покрытие
ВПД │ │ │ │
│ │
│ Пропиточные составы и их
компоненты │
│Аммоний
кремнефтористый │ОСТ
6-08-2-75 │ 104
│ N 05-01, │
│технический │ │ │ ч. 1, М., │
│ │ │ │ 1980
│
│Бихромат
калия технический │ГОСТ
2652-78 │ │ │
│Высший
сорт │ │ 325
│ То же │
│I
сорт │ │ 310
│ │
│Кислота
борная I сорт │ГОСТ
18704-78 │ 610
│ То же │
│Диаммоний
фосфат технический │ГОСТ
8515-75 │ │ │
│Марка
А │ │ 475
│ " │
│
" Б │ │ 375
│ " │
│Сульфат
аммония технический │ГОСТ
9097-74 │ │ │
│сорт
I │ │ 40
│ │
│
" II │ │ 32,5
│ │
│Бихромат
натрия технический │ГОСТ
2651-78 │ 312
│ " │
│Медный
купорос сорт II │ГОСТ
19347-74 │ 320
│ " │
│Тетрафторборат
аммония │ТУ 6-08-297-74 │
530 │ "
│
│технический │ │ │ │
│Натрий
фтористый технический │ГОСТ
2871-75 │ │ │
│сорт
I │ │ 360
│ " │
│
" II │ │ 225
│ │
│Трихлорэтилфосфат │ТУ 6-05-1611-76
│ 2000 │
" │
│Пентахлорфенол │ГОСТ 18395-73 │
800 │
" │
│Бура │ГОСТ
8429-77 │ 525
│ " │
│Пентахлорфенолят
натрия │ТУ 6-04-6-80 │
830 │ "
│
│Сода
кальцинированная сорт II │ГОСТ 10689-75
│ 52 │
" │
│Кислота
ледяная уксусная │ГОСТ
19814-74 │ 353
│ " │
│сорт
II │ │ │ │
│Хлористый
аммоний │ГОСТ
2210-73 │ 215
│ " │
│Мочевина │ГОСТ 2081-75 │
102 │ "
│
│Кремнефтористый
натрий сорт I │ГОСТ 87-77
│ 162 │
" │
│Триполифосфат
натрия сорт II │ГОСТ 13493-77 │
350 │ │
│Каменноугольное
масло │ГОСТ 2770-74 │
60 │ │
│Калий
углекислый │ГОСТ
10690-73 │ │ │
│сорт
I │ │ 180
│ │
│сорт
II │ │ 150
│ │
│сорт
III │ │ 125
│ │
└──────────────────────────────┴────────────────┴────────────┴────────────┘
Приложение
7
СОСТАВ И
СТОИМОСТЬ РАСТВОРИТЕЛЕЙ
┌───────────────┬───────────────┬────────────────┬────────────┬───────────┐
│
Наименование │ ГОСТ, ТУ
│ Состав
│Прейскурант-│Прейскурант│
│ │ │ растворителя, │ная цена 1 т│ │
│ │ │ %
│материала, │ │
│ │ │ │руб. │ │
├───────────────┼───────────────┼────────────────┼────────────┼───────────┤
│Растворитель │ГОСТ 8727-77 │Ацетон - 26│ 190
│Прейскурант│
│Р-4 │ │Бутилацетат -
12│ │N 05-04 │
│ │ │Толуол - 62│ │М., 1980 │
│То
же Р-5 │ГОСТ 7827-77 │Бутилацетат - 30│ 520
│ То же │
│ │ │Ацетон - 30│ │ │
│ │ │Ксилол - 40│ │ │
│ "
Р-24 │То же │Ацетон - 15│ 200
│ " │
│ │ │Ксилол - 35│ │ │
│ │ │Сольвент - 50│ │ │
│ "
Р-189 │ТУ
6-10-1508-75│Бутилацетат - 50│
- │ "
│
│ │ │Этилацетат - 50│ │ │
│Углерод │ГОСТ 4-75 │
- - │
315 │Прейскурант│
│четыреххлорис-
│ │ │ │N 05-01 │
│тый
сорт I │ │ │ │ │
└───────────────┴───────────────┴────────────────┴────────────┴───────────┘
Приложение
8
МЕТОД
ОПРЕДЕЛЕНИЯ АДГЕЗИИ ПОКРЫТИЙ К ДРЕВЕСНЫМ ПОДЛОЖКАМ
Сущность метода
заключается в измерении усилия, необходимого для равномерного отрыва участка
покрытия от подложки с помощью металлического штампа, приклеенного к покрытию
эпоксидным клеем, у которого адгезия к покрытию заведомо больше, чем адгезия
покрытия к подложке.
Адгезия покрытия
определяется с помощью устройства, схема которого показана на рис. 1.
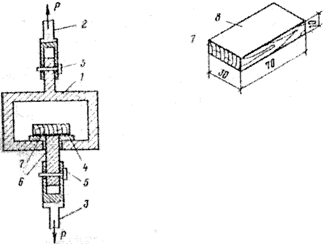
Рис. 1. Схема
устройства для определения адгезии
лакокрасочного
покрытия методом равномерного отрыва штампа
1 - корпус; 2 -
верхний захват; 3 - нижний захват;
4 - направляющая
втулка; 5 - шпилька; 6 - штамп;
7 - образец; 8 -
лакокрасочное покрытие
Испытания проводят
на образцах древесины, фанеры, древесно-стружечных плит или других древесных
материалов, адгезию покрытия к которым необходимо определить. В зависимости от
целей испытания образцы либо выпиливают из элемента конструкции с нанесенным на
него покрытием либо готовят специально.
Покрытие сначала
шлифуют шкуркой N 5, затем протирают ацетоном. Для приклеивания штампа, который
имеет цилиндрическую форму с диаметром основания 15 мм, используют состав на
основе эпоксидной смолы К-153. Штамп с нанесенным клеевым слоем прижимают к
поверхности образца рукой. Излишки выдавившегося клея осторожно удаляют.
Испытания проводят
после выдержки образца в течение 2 - 3 сут при температуре 18 - 22 °C. Перед
установкой образца в устройство покрытие вокруг штампа подрезают лезвием
безопасной бритвы или острым ножом. Образец вставляют в устройство и отрывают штамп
с покрытием от подложки в разрывной машине со скоростью нагружения 35 - 50
мм/мин.
Величину адгезии A
определяют по формуле, МПа:
,
где P - усилие
отрыва, Н;
F - площадь штампа,
см2.
При показателе
точности P = 5% необходимое количество образцов составляет 8 - 10 шт.
При повторном
использовании штампы должны быть очищены от остатков клея (клей легко удаляется
после прогрева штампа на электроплитке), зачищены шкуркой N 5 и обезжирены
ацетоном.