Введен в действие
Постановлением
Госстандарта СССР
от 20 ноября 1981
г. N 5050
ГОСУДАРСТВЕННЫЙ СТАНДАРТ СОЮЗА ССР
ЗАГОТОВКИ ДЛЯ ТЕПЛООБМЕННИКОВ ЛИСТОВЫЕ
ПРОКАТНО-СВАРНЫЕ АЛЮМИНИЕВЫЕ
ТЕХНИЧЕСКИЕ УСЛОВИЯ
Rolled-welded aluminium sheet billets
for heat-exchangers.
Specifications
ГОСТ 25001-81
Группа В53
ОКП 51 5222
Постановлением
Государственного комитета СССР по стандартам от 20 ноября 1981 г. N 5050 срок
действия установлен с 01.01.1983 до 01.01.1988.
Настоящий стандарт
распространяется на листовые прокатно-сварные алюминиевые заготовки с
двусторонним раздувом каналов, предназначенные для изготовления теплообменников
испарителей и применяемые в бытовых холодильниках и морозильниках.
1.
СОРТАМЕНТ
1.1. Листовые
прокатно-сварные заготовки изготовляют по чертежам, согласованным между
изготовителем и потребителем.
В чертежах
указывают:
габаритные размеры
заготовок (ширина и длина) и предельные отклонения по ним;
длина, ширина,
наружная высота каналов и предельные отклонения по ним;
перекос рисунка в
направлении раскатки;
место и размер завальцовки входного и выходного каналов;
дополнительные
требования.
1.1.1. Суммарная
протяженность каналов, расположенных поперек направления раскатки, не должна
превышать 25% общей длины каналов.
1.1.2. Переход от
поперечного канала к продольному по внутреннему радиусу должен быть не менее 3
мм.
1.1.3. Канал под
капиллярную трубку должен быть расположен вдоль направления раскатки в зоне входного-выходного каналов.
По требованию
потребителя отдельные типоразмеры заготовок Каменск-Уральский металлургический
завод изготовляет с расположением указанного канала поперек направления
раскатки.
1.1.4. Отклонения
продольных каналов от прямолинейности на погонный метр длины рисунка не должен
быть более 5 мм.
1.2. Минимальное
расстояние между каналами должно быть не менее 10 мм.
1.3. Предельные
отклонения по длине рисунка должны быть +/- 2% от номинальных значений.
Пример условного
обозначения листовой прокатно-сварной заготовки, предназначенной для
изготовления теплообменника испарителя (ТИ) по чертежу (ХХХ) из алюминия марки
АД шириной 320 мм и длиной 1034 мм:
ТИ ХХХ АД 320 х
1034 ГОСТ 25001-81.
2.
ТЕХНИЧЕСКИЕ ТРЕБОВАНИЯ
2.1. Листовые
прокатно-сварные заготовки изготовляют в соответствии с требованиями настоящего
стандарта по технологической инструкции, утвержденной в установленном порядке.
2.1.1. Листовые
прокатно-сварные заготовки изготовляют методом раскатки карточек из алюминия
марок А7, А6, А5, А0 с химическим составом по ГОСТ
11069-74 и алюминия марок АД0, АД1, АД с химическим составом по ГОСТ 4784-74 с
допустимой массовой долей железа до 0,5%.
Карточки вырезают
из нагартованных листов толщиной 3,0 мм повышенной
точности изготовления и повышенной отделки поверхности по ГОСТ 21631-76.
2.2. Заготовки
листовые прокатно-сварные изготовляют в отожженном состоянии.
2.3. Исключен с 1 марта 1988 года. - Изменение N 2, утв.
Постановлением Госстандарта СССР от 30.06.1987 N 2857.
2.4. Поверхность
заготовок листовых прокатно-сварных должна быть без расслоений, плен, надрывов,
пятен коррозионного происхождения, шлаковых включений, а также пятен и полос от
пригоревшей смазки, если они не удаляются при контрольном травлении в растворе
с массовой долей NaOH 8 - 10% при 50 °С в течение 2 - 3 мин с последующим осветлением в растворе
с массовой долей
30%.
На поверхности
каналов заготовки листовых прокатно-сварных пузыри и гнезда от выкрашивания закатов не допускаются.
2.5. На поверхности
заготовок листовых прокатно-сварных допускаются:
1) металлические
мелкие закаты общей площадью не более 40 мм2;
2) гнезда от выкрашивания закатов, глубиной не более 0,06 мм. На каждой
стороне заготовки листовой прокатно-сварной допускается не более 10 гнезд,
расположенных в местах, свободных от каналов, на расстоянии не менее 2 мм от
края канала;
3) пузыри общей
площадью не более 20 мм2 с размерами каждого пузыря не
более 10 мм2, расположенного в местах, свободных от каналов, на расстоянии не
менее 2 мм от края канала;
4) единичные и
групповые царапины глубиной не более 0,05 мм. На каждой стороне заготовки
листовой прокатно-сварной допускается не более 5 царапин. Царапин при групповом
расположении не должно быть более 3 шт., которые указываются в квадрате 200 х
200 мм;
5) отпечатки в виде
мелких вмятин глубиной не более 0,05 мм. На каждой стороне заготовки листовой
прокатно-сварной допускается не более 5 отпечатков;
6) отпечатки от
валков в виде светлых и темных полос, идущие вдоль прокатки;
7) потертость;
8) цвета
побежалости;
9) на
каждой стороне заготовки листовой прокатно-сварной после химической и
механической обработки допускается в местах, свободных от каналов, на
расстоянии не менее 2 мм от края канала, скрытые дефекты металлургического
происхождения в виде единичных включений площадью не более 1,5 мм2 и глубиной, не превышающей допуск на толщину заготовки.
2.6. Местные
уширения каналов не должны быть более одной трети ширины канала на длине 15 мм
для испарителей и 40 мм для конденсаторов. Общее число местных уширений допускается не более двух на каждой заготовке.
2.7. Внутри каналов
допускается сухой остаток не более 30 мг на заготовку.
2.8. Внутри каналов
не допускается наличие влаги, находящейся в свободном состоянии при завальцованном входном и выходном каналах.
2.9. Величина
колебаний объема каналов от значения номинального объема
оформленных каналов до 150 см3 включительно не должна превышать +/- 12%.
Величина колебаний
объема каналов от значения номинального объема
оформленных каналов свыше 150 см3 устанавливается в чертеже.
2.10. Каналы
заготовок листовых прокатно-сварных должны быть герметичными и должны
выдерживать давление не менее 1,57 МПа (16 кгс/см2).
2.11. Исключен с 1 марта 1988 года. - Изменение N 2, утв.
Постановлением Госстандарта СССР от 30.06.1987 N 2857.
3. ПРАВИЛА
ПРИЕМКИ
3.1. Заготовки
листовые прокатно-сварные принимают партиями.
Партия должна состоять из заготовок одного типоразмера и оформлена одним
документом о качестве. Партия должна состоять из заготовок, разность колебаний
объемов каналов у которых не должна быть более 25% от меньшего значения объема.
Документ о качестве
должен содержать:
товарный знак или
товарный знак и наименование предприятия-изготовителя;
наименование
продукции и типоразмер;
номер партии;
количество
заготовок;
отметку ОТК;
дату отгрузки;
обозначение
настоящего стандарта.
3.2. Для
определения химического состава отбирают две заготовки. Допускается изготовителю
устанавливать химический состав заготовки в соответствии с документом о
качестве предприятия-изготовителя слитков или листов.
3.3. При контроле
качества заготовок изготовитель проверяет: габаритные размеры заготовок, длину
рисунка и его перекос на каждой заготовке; высоту каналов на каждой заготовке
или объем каналов на трех заготовках от партии; качество поверхности на каждой
заготовке, глубину дефектов на 2% от партии, но не менее 20 шт.
3.4. При входном
контроле качества заготовок потребитель проверяет: качество поверхности,
геометрические размеры и рисунок, наличие сухого остатка, наличие влаги,
находящейся в свободном состоянии, величину колебаний объема каналов,
герметичность.
Объем контроля
устанавливается потребителем в соответствии с ГОСТ 24297-87.
3.4.1. Контроль
качества поверхности каждой заготовки с целью выявления скрытых дефектов
потребитель проводит после механической и химической обработки.
Количество
заготовок со скрытыми дефектами до 01.01.1990 допускается не более 3,0% в
партии, с 01.01.1990 - не более 1,5%.
3.5. При получении
неудовлетворительных результатов испытаний по ним проводят повторные испытания
на удвоенной выборке, взятой от той же партии. Результаты повторных испытаний
распространяются на всю партию.
4. МЕТОДЫ
ИСПЫТАНИЙ
4.1. Анализ
химического состава алюминия проводят по ГОСТ 25086-82 или спектральным методом
по ГОСТ 3221-85.
4.2. Измерение
размеров заготовок листовых прокатно-сварных проводят измерительным
инструментом, обеспечивающим необходимую точность измерения. Ширину и длину
заготовки, а также длину и ширину рисунка канала измеряют измерительной
металлической линейкой по ГОСТ 8026-75 или шаблоном.
4.3. Испытания на
растяжение проводят по ГОСТ 1497-73.
4.4. Осмотр
поверхности заготовок проводят без применения увеличительных приборов.
Глубину залегания
дефектов измеряют профилометром по ГОСТ 19300-86 или глубиномером индикаторным
(специальным) по нормативно-технической документации.
Проверку качества
поверхности в соответствии с п. 2.5.9 проводят после химической обработки по
методу, указанному в Приложении 1.
4.5. Проверку
наличия влаги, находящейся в свободном состоянии, проводят индикатором -
марганцовокислым калием по покраснению на развальцованном или обрезанном
входном и выходном каналах.
Проверку наличия
сухого остатка проводят по методу, указанному в Приложении 3.
4.6. Контроль
величины колебания объема каналов проводят по методу, указанному в обязательном
Приложении 4.
Контроль
герметичности проводят по технической документации, утвержденной в
установленном порядке.
5.
МАРКИРОВКА, УПАКОВКА, ТРАНСПОРТИРОВАНИЕ И ХРАНЕНИЕ
5.1. На каждой
заготовке листовой прокатно-сварной в месте, указанном на чертеже, должны быть
выбиты металлическим клеймом или нанесены другими способами номер партии и
штамп отдела технического контроля предприятия-изготовителя.
По требованию
потребителя на заготовки клеймо не наносят.
5.2. Временная
противокоррозионная защита, упаковка, транспортирование и хранение - по ГОСТ
9.011-79.
Транспортная
маркировка грузовых мест по ГОСТ 14192-77 с нанесением манипуляционных знаков
"Осторожно, хрупкое", "Боится сырости", "Верх, не
кантовать" и с дополнительными надписями: наименование продукции и
типоразмер, марка алюминия и номер партии.
По требованию
потребителя заготовки теплообменников подвергаются консервации в соответствии с
требованиями ГОСТ 9.011-79.
Приложение
1
Обязательное
МЕТОД
ХИМИЧЕСКОЙ
ОБРАБОТКИ ЗАГОТОВОК ТЕПЛООБМЕННИКОВ
Метод применяется
при контроле качества поверхности заготовок теплообменников и включает
последовательные операции: травление, промывку, осветление, промывку и сушку.
1. Реактивы
Натр едкий
технический по ГОСТ 2263-79, раствор 80-100 г/м3.
Кислота азотная
концентрированная по ГОСТ 4461-77, раствор 200 г/м3.
2. Проведение
испытания
Травление
поверхности проводят в растворе едкого натра (NaOH)
при температуре 60 - 70 °С в течение 2 - 3 мин. После
чего промывают в теплой проточной воде при температуре 40 - 60 °С, а затем в
холодной проточной воде комнатной температуры. После промывки проводят
осветление поверхности в растворе азотной кислоты (
) при
комнатной температуре в течение 1 - 10 мин до полного осветления. Промывают в
холодной проточной воде при комнатной температуре и сушат подогретым воздухом.
Приложение
2
Рекомендуемое
МЕТОД
ПРОВЕРКИ ОСТАТОЧНОЙ
ВЛАГИ
Приложение 2
исключено с 1 марта 1988 года. - Изменение N 2, утв. Постановлением
Госстандарта СССР от 30.06.1987 N 2857.
Приложение
3
Обязательное
МЕТОД
ПРОВЕРКИ
ОСТАТОЧНОГО ЗАГРЯЗНЕНИЯ
Метод проверки
остаточного загрязнения основан на промывке растворителем (трихлорфторметан,
трихлорэтилен или хладон 113) контролируемого
элемента с последующей фильтрацией раствора и выделением сухого осадка.
1. Аппаратура и
реактивы
Трихлорэтилен по ГОСТ 9976-83.
Трихлорфторметан.
Хладон 113 по ГОСТ
23844-79.
Аппаратура для
контроля и ее установка приведены на чертеже.
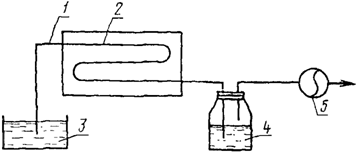
2. Проведение
испытания
Соединить элементы
установки с помощью сухих чистых медицинских резиновых трубок 1 (см. чертеж).
Включить вакуумный насос 5 и промыть контролируемый элемент 2 чистым
растворителем из сосуда 3. Продукты смыва поступают в пустой чистый сосуд 4.
Для интенсификации процесса промывки рекомендуется время от времени вынимать
трубку 1 из растворителя.
Если растворитель
после прохождения через контролируемый элемент остается чистым, промывку
следует закончить. После этого трубку 1 вынуть из растворителя и выключить
вакуумный насос. Раствор из сосуда 4 профильтровать через предварительно
осушенный при температуре 50 - 60 °С до постоянной
массы фильтр с погрешностью 0,1 мг. Промыть сосуд чистым растворителем и
раствор профильтровать через тот же фильтр. Поместить отработанный фильтр в
сушильный шкаф с температурой 50 - 60 °С и провести
выпаривание растворителя до постоянной массы фильтра. Определение массы фильтра
до и после испытаний проводится в одинаковых условиях.
Увеличение
массы фильтра по сравнению с первоначальной принимается за величину остаточного
загрязнения контролируемого элемента агрегата.
Приложение
4
Обязательное
МЕТОД
ИЗМЕРЕНИЯ
ВНУТРЕННЕГО ОБЪЕМА КАНАЛА
Метод предназначен
для контроля величины колебаний объема каналов
теплообменников и основан на измерении избыточного давления в каналах
при заполнении их мерным количеством воздуха.
1. Сущность метода
Метод измерения
внутреннего объема каналов базируется на законе Бойля-Мариотта, согласно
которому произведение объема газа на его давление при изотермическом процессе
остается неизменным.
2. Аппаратура
Рабочий цилиндр с
внутренним объемом от 300 до (500 +/- 5) см3.
Емкость с
калиброванным внутренним объемом: 100, 150, 175, 200, 225, 250, 300, 400, 450,
500 см3.
Манометр образцовый
пружинный МО-250-6 х 0,25 по ГОСТ 6521-72.
3. Проведение
испытаний
Перед измерением
внутренних объемов каналов испытываемых теплообменников проводят градуировку
рабочего цилиндра (1) для данной температуры окружающего воздуха. Для этого
емкости (5) с калиброванными внутренними объемами
,
,
соединяют поочередно с рабочим цилиндром через
манометр (3) и передвигают поршень (2) в крайнее правое положение.
Устанавливают
зависимость величины градуированных объемов от давления для конкретной
температуры окружающей среды в виде графика или таблицы.
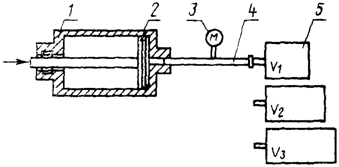
1 - рабочий
цилиндр; 2 - поршень; 3 - манометр;
4 - соединительная
трубка; 5 - емкость с калиброванным
внутренним объемом
Контроль внутреннего
объема каналов теплообменника проводят путем подачи воздуха из рабочего
цилиндра в каналы теплообменника. Величину давления на манометре сопоставляют с
данными таблицы или графика и определяют внутренний объем каналов, который
сравнивают с номинальным значением. Ошибка измерения внутреннего объема каналов
не должна превышать 1% и складываться из суммы погрешности измерительного
прибора и колебаний температуры окружающей среды".