ТН80-I
То же, трубы
диаметром условного прохода 1200 мм, II класса, предназначенные для
трубопроводов с внутренним давлением 1,3 МПа (13 кгс/см2),
с закладными изделиями:
ТН120-IIук
2.
ТЕХНИЧЕСКИЕ ТРЕБОВАНИЯ
2.1. Трубы
следует изготовлять в соответствии с требованиями настоящего стандарта и
технологической документации, утвержденной в установленном порядке, по
чертежам, приведенным в ГОСТ 12586.1-83.
2.2. Трубы
должны быть водонепроницаемыми и выдерживать внутреннее испытательное гидростатическое
давление, МПа (кгс/см2):
2,4 (24)
- для труб 0 класса;
1,8 (18)
- " " I
класса;
1,2 (12)
- " " II
класса;
0,6 (6)
- " "
III класса.
Трубы,
предназначенные для трубопроводов с внутренним давлением, превышающим расчетное
значение (п. 1.1), и оговоренные в заказе на их изготовление, должны
выдерживать испытательное давление, увеличенное соответственно на 0,3 МПа (3
кгс/см2).
2.3. Трубы
должны быть трещиностойкими. При внутренних
испытательных гидростатических давлениях, указанных в табл. 2, образование
трещин в бетоне труб не допускается.
Таблица 2
─────────┬──────────┬─────────────────────────────────────────────
Диаметр │ Марка
│ Контрольное
внутреннее гидростатическое
условного│ трубы │
давление, МПа (кгс/см2), при проверке
прохода │ │ трещиностойкости
трубы
трубы d,│
├──────────────────────┬──────────────────────
мм │ │ при приемосдаточных │ при возрасте бетона
│ │ испытаниях (при │ к моменту испытания
│ │возрасте
бетона 2 сут)│ 100 сут
─────────┼──────────┼──────────────────────┼──────────────────────
500
│ТН50-0 │2,65
(27) │2,60 (26,5)
│ТН50-I │2,11 (21,5) │2,11 (21,5)
│ТН50-II │1,62 (16,5) │1,62 (16,5)
│ТН50-III │1,18 (12,0) │1,18 (12,0)
─────────┼──────────┼──────────────────────┼──────────────────────
600
│ТН60-0 │2,7
(27,5) │2,60 (26,5)
│ТН60-I │2,16 (22) │2,11 (21,5)
│ТН60-II │1,62 (16,5) │1,62 (16,5)
│ТН60-III │1,18 (12,0) │1,18 (12,0)
─────────┼──────────┼──────────────────────┼──────────────────────
800
│ТН80-I │2,35
(24) │2,26 (23)
│ТН80-II │1,81 (18,5) │1,77 (18)
│ТН80-III │1,27 (13) │1,27 (13)
─────────┼──────────┼──────────────────────┼──────────────────────
1000
│ТН100-I │2,45
(25) │2,35 (24)
│ТН100-II │1,91 (19,5) │1,86 (19)
│ТН100-III │1,37 (14) │1,37 (14)
─────────┼──────────┼──────────────────────┼──────────────────────
1200
│ТН120-I │2,50
(25,5) │2,35 (24)
│ТН120-II │1,96 (20) │1,86 (19)
│ТН120-III │1,42
(14,5) │1,37 (14)
─────────┼──────────┼──────────────────────┼──────────────────────
1400
│ТН140-I │2,60
(26,5) │2,40 (24,5)
│ТН140-II │2,01 (20,5) │1,91 (19,5)
│ТН140-III │1,47 (15) │1,42 (14,5)
─────────┼──────────┼──────────────────────┼──────────────────────
1600
│ТН160-I │2,60
(26,5) │2,40 (24,5)
│ТН160-II │2,01 (20,5) │1,91 (19,5)
│ТН160-III │1,47 (15) │1,42 (14,5)
(Измененная
редакция, Изм. N 1).
2.4. Между
закладными изделиями труб, предназначенных для эксплуатации в условиях
воздействия блуждающих токов (п. 1.4), должен быть электрический контакт.
2.5. Трубы
должны удовлетворять требованиям ГОСТ 13015.0-83:
по показателям
фактической прочности бетона (в проектном возрасте, передаточной);
к качеству
арматурных и закладных изделий и их положению в трубе;
к защите от
коррозии.
2.6. Трубы
следует изготовлять из тяжелого бетона по ГОСТ 26633-85 классов по прочности на
сжатие:
В30 - трубы марок
ТН50-III и ТН60-III;
В40 - трубы
остальных марок.
2.5, 2.6. (Измененная редакция, Изм. N 1).
2.7. (Исключен, Изм. N 1).
2.8. Значения
нормируемой передаточной прочности бетона труб (прочности бетона к моменту
передачи на него усилия обжатия от спиральной арматуры) должны соответствовать указанным в табл. 3.
Таблица 3
──────────┬─────────────┬─────────────────────────────────────────
Диаметр
│Вид контроли-│ Нормируемая передаточная прочность
условного
│руемой проч- │ бетона, МПа (кгс/см2), трубы класса
прохода
│ности бетона
├────────┬──────────┬──────────┬──────────
трубы
│ │ 0
│ I │
II │ III
d, мм
│ │ │ │ │
──────────┼─────────────┼────────┼──────────┼──────────┼──────────
500,
600 │На
сжатие │- │35,3 (360)│31,4
(320)│23,5 (240)
├─────────────┼────────┼──────────┼──────────┼──────────
│На растяжение│2,9
(30)│- │- │-
│при раскалы-
│ │ │ │
│вании │ │ │ │
──────────┼─────────────┼────────┼──────────┼──────────┼──────────
800,
1000 │На сжатие │- │- │31,4 (320)│25,5 (260)
├─────────────┼────────┼──────────┼──────────┼──────────
│На растяжение│- │2,9 (30) │- │-
│при раскалы-
│ │ │ │
│вании │ │ │ │
──────────┼─────────────┼────────┼──────────┼──────────┼──────────
1200 │На
сжатие │- │- │35,3 (360)│31,4 (320)
├─────────────┼────────┼──────────┼──────────┼──────────
│На растяжение│- │2,9 (30) │- │-
│при раскалы-
│ │ │ │
│вании │ │ │ │
──────────┼─────────────┼────────┼──────────┼──────────┼──────────
1400,
1600│На сжатие
│- │- │35,3 (360)│31,4 (320)
├─────────────┼────────┼──────────┼──────────┼─────────
│На растяжение│- │3,2 (33) │- │-
│при раскалы-
│ │ │ │
│вании │ │ │ │
2.9. Поставку труб
потребителям следует производить после испытания их на водонепроницаемость и трещиностойкость.
2.10.
Качество материалов, применяемых для приготовления бетона труб, должно
обеспечивать выполнение технических требований к бетону, установленных настощим стандартом, и соответствовать требованиям:
цемент - ГОСТ
10178-85;
заполнители - ГОСТ
10268-80, ГОСТ 8267-82, ГОСТ 10260-82 и ГОСТ 8736-85;
вода - ГОСТ
23732-79.
Крупный заполнитель
следует применять фракций: от 5 до 10 мм, от 5 до 15 мм, св. 10 до 20 мм.
2.8 - 2.10. (Измененная редакция, Изм. N 1).
2.11.
Арматурная проволока должна удовлетворять требованиям:
классов В-II и Вр-II по ГОСТ 7348-81;
классов В-I и Вр-I по ГОСТ 6727-80.
Стальная
холоднокатаная лента из низкоуглеродистой стали (для разделительных полос)
должна удовлетворять требованиям ГОСТ 503-81.
2.12. Форма
и размеры арматурных и закладных изделий для труб должны соответствовать приведенным в ГОСТ 12586.1-83.
2.13. Значения
действительных отклонений геометрических параметров труб не должны превышать
предельных, указанных в табл. 4.
Таблица 4
мм
─────────┬────────────────────────────────────────────────────────
Диаметр │ Пред. откл.
условного├────────┬────────┬─────────┬──────────┬────────┬────────
прохода │по │по │по │по │по │
по
трубы
│внут- │толщине
│наружному│внутренне-│длине │ширине и
d
│реннему │стенки │диаметру │му
диамет-│калибро-│ высоте
│диаметру│цилин- │втулочно-│ру
растру-│ванной │заходной
│трубы │дричес- │го конца │ба трубы
│части │ фаски
│d │кой час-│d и
│d │раструба│раструба
│ i │ти тру- │ е
│ 1 │трубы а
│ трубы
│ │бы
t │буртика │ │ │
│ │ │трубы d │ │ │
│ │ │ 3 │ │ │
─────────┼────────┼────────┼─────────┼──────────┼────────┼────────
500,
600,│+/- 4 │+/- 4 │+/- 2 │+/- 2 │+35; -5 │+7; -5
800 │ │ │ │ │ │
─────────┼────────┼────────┤ │ │ │
1000, │+/- 5 │+/- 5 │ │ │ │
1200 │ │ │ │ │ │
─────────┤ │
├─────────┼──────────┤ │
1400, │ │ │+/- 2,5 │+/- 2,5 │ │
1600 │ │ │ │ │ │
2.14. Толщина
защитного слоя бетона труб должна быть не менее 15 мм.
2.15.
Значения действительных параметров шероховатости внутренней поверхности трубы в
пределах ее полезной длины должны соответствовать указанным
в табл. 5.
Таблица 5
──────────────────────────────────┬───────────────────────────────
Параметр шероховатости │Допускаемые значения параметров
по ГОСТ 2789-73 │ шероховатости, мм,
труб
│ категорий по шероховатости
─────────────────────┬────────────┼────────────────┬──────────────
Наименование │ Обозначение│ первой
│ второй
─────────────────────┼────────────┼────────────────┼──────────────
Среднее │ Ra │
<= 0,1 │ <= 0,06
арифметическое │ │ │
отклонение
профиля │ │ │
Средний
шаг │ Sm │ >= 4 │ >= 6
неровностей
профиля │ │ │
Примечание.
Параметры шероховатости внутренней поверхности труб не являются браковочными до
01.01.93.
2.16. На
поверхностях труб не допускаются:
трещины на
наружной и внутренней поверхностях труб;
наплывы и околы, а также раковины диаметром более 3 мм и глубиной
более 2 мм на стыковых поверхностях раструба и втулочного конца труб;
раковины диаметром
более 10 мм и глубиной более 2 мм на остальной наружной поверхности;
наплывы и околы бетона ребер на торцевых поверхностях труб высотой
(глубиной) более 5 мм;
следы (риски)
шириной и глубиной более 1,5 мм на стыковой поверхности раструба от
шлифовального инструмента;
более трех раковин
на площади 0,01 (100 х 100 мм) на любом участке стыковой поверхности.
2.17. Раковины на
трубах и околы бетона ребер торцевых поверхностей,
размеры которых превышают указанные в п.
2.16, допускается устранять путем заделки нетоксичными материалами,
предохраняющими арматуру труб от коррозии и предотвращающими фильтрацию воды
между уплотняющим резиновым кольцом и бетонной поверхностью.
2.18. Трубы не
должны иметь отслоений наружного защитного слоя бетона.
Отслоения защитного
слоя бетона размерами в кольцевом и продольном направлениях трубы, не
превышающими значения 0,4d, допускается устранять с применением материалов,
предохраняющих арматуру от коррозии.
2.13 - 2.18. (Измененная редакция, Изм.
N 1).
2.19. Концы
продольной напрягаемой арматуры труб не должны выступать из бетона и должны
быть вместе с прилегающими участками поверхности бетона покрыты
цементно-казеиновой обмазкой толщиной 0,5 - 0,6 мм. Состав обмазки по массе
1:0,05:0,4 (цемент, казеиновый клей, вода). Допускается применять обмазки из
других нетоксичных материалов, обеспечивающих коррозионную и механическую
стойкость покрытия.
3.
КОМПЛЕКТНОСТЬ
3.1.
Предприятие-изготовитель обязано поставлять потребителю трубы комплектно с
уплотняющими резиновыми кольцами (одно кольцо на одну трубу), изготовленными по
техническим условиям и имеющими паспорта-сертификаты. Размеры уплотняющих колец
в нерастянутом состоянии должны соответствовать указанным
в ГОСТ 22000-86.
По требованию
потребителя предприятие-изготовитель обязано поставлять дополнительные
уплотняющие резиновые кольца в количестве, согласованном между ними.
4. ПРАВИЛА
ПРИЕМКИ
4.1. Приемку
труб следует производить партиями в соответствии с требованиями ГОСТ 13015.1-81
и настоящего стандарта.
Число труб в партии
должно быть не более 100.
4.2. Трубы
принимают:
по результатам
периодических испытаний - по показателям шероховатости внутренней поверхности
труб;
по результатам
приемосдаточных испытаний - по показателям водонепроницаемости и трещиностойкости труб, наличия закладных изделий и
электрического контакта между ними, прочности бетона (классу по прочности на
сжатие, передаточной прочности), соответствия арматурных и закладных изделий
требованиям ГОСТ 12586.1-83, точности геометрических параметров, толщины и
отслоения защитного слоя бетона, качества поверхности труб.
(Измененная
редакция, Изм. N
1.)
4.3. Приемку труб по их водонепроницаемости, наличию закладных изделий и
электрического контакта между ними, по отклонению от внутреннего диаметра
раструба труб, качеству внутренней поверхности раструба и наружной поверхности
втулочного конца труб, по наличию трещин на бетонных поверхностях, отслоения
наружного защитного слоя бетона и антикоррозионной защиты концов продольной
напрягаемой арматуры, а также правильности нанесения маркировочных надписей и
знаков следует проводить по результатам сплошного контроля.
4.4. Трубы считают
выдержавшими испытание на водонепроницаемость, если к моменту его окончания на
поверхности труб не будет обнаружена фильтрация воды в виде влажных пятен,
капели или течи.
4.5. Испытанию на трещиностойкость следует подвергать одну трубу от партии.
4.5.1. Трубы партии
считают выдержавшими испытание на трещиностойкость,
если к моменту его окончания контрольная труба удовлетворяет требованию п. 2.3.
Наличие фильтрации воды в виде влажных пятен или капели по
превышении испытательного давления на водонепроницаемость не является
основанием для браковки труб при испытании их на трещиностойкость.
4.6. Трубы, не
выдержавшие испытание на водонепроницаемость и трещиностойкость,
могут быть подвергнуты повторному испытанию.
Повторное испытание
труб на водонепроницаемость проводят через семь суток после первого испытания
при хранении труб во влажных условиях или через две суток - при пропитке труб
жидким стеклом или композициями на его основе.
От партии, не
выдержавшей испытания на трещиностойкость, отбирают
для повторных испытаний две трубы, ранее не подвергавшиеся проверке.
4.7. Если трубы 0,
I и II классов при повторных испытаниях на водонепроницаемость или трещиностойкость не удовлетворяют требованиям настоящего
стандарта по этим показателям, то они могут быть перемаркированы
с переводом на один класс ниже.
Трубы III класса,
не выдержавшие повторных испытаний на водонепроницаемость или трещиностойкость, признают нестандартными.
(Измененная
редакция, Изм. N 1).
4.8. Трубы считают
выдержавшими испытание по наличию электрического контакта между закладными
изделиями, если значение сопротивления цепи не превышает 1 Ом. Трубы, не
имеющие электрического контакта между закладными изделиями, допускается
поставлять как трубы без закладных изделий.
4.9. Наличие
отслоения наружного защитного слоя бетона устанавливают по глухому звуку при
ударе молотком по поверхности трубы.
4.10. Испытания на
шероховатость внутренней поверхности труб проводят перед началом их массового
изготовления и в дальнейшем при изменении вида заполнителя, конструкции резинового
чехла и марки пластифицирующих добавок, но не реже одного раза в 6 мес.
Испытанию следует подвергать две трубы каждого диаметра.
(Измененная
редакция, Изм. N 1).
4.10.1, 4.10.2,
4.11. (Исключены, Изм. N 1).
5. МЕТОДЫ
КОНТРОЛЯ И ИСПЫТАНИЙ
5.1.
Гидростатические испытания труб на водонепроницаемость и трещиностойкость
следует проводить после двухсуточной выдержки их в цехе.
Значение
испытательного давления определяют с помощью манометра, имеющего II класс
точности и цену деления не более 0,05 МПа (0,5 кгс/см2).
5.1.1.
Гидростатические испытания труб проводят по следующему режиму. Трубы испытывают
путем повышения давления на 0,1 - 0,25 МПа (1 - 2,5 кгс/см2)
в минуту до значений, указанных в пп. 2.2 и 2.3, и
выдерживают под испытательным давлением в течение 5 мин. При испытании труб на трещиностойкость допускается падение давления не более 0,1
МПа (1 кгс/см2).
(Измененная
редакция, Изм. N 1).
5.1.2.
Допускается применение ультразвукового метода контроля и оценки трещиностойкости труб по ГОСТ 24983-81.
5.2. Контроль
наличия электрического контакта между закладными изделиями трубы проводят при
помощи омметра с ценой деления не более 0,5 Ом.
5.3.
Прочность бетона труб следует определять по ГОСТ 10180-78 на серии
образцов-кубов с ребром 100 мм, изготовленных из бетонной смеси рабочего
состава и твердевших в условиях согласно ГОСТ 18105-86. Прочность бетона на
сжатие следует определять испытанием вибрированных
образцов, а на растяжение при раскалывании - испытанием образцов, изготовленных
вибрированием и последующим прессованием под давлением 0,2 МПа (2 кгс/см2).
5.4.
Толщину защитного слоя бетона в трубах определяют при помощи электромагнитного
прибора типа ИЗС по ГОСТ 22904-78 или другими методами, обеспечивающими необходимую
точность измерения.
При отсутствии
приборов допускается определять толщину защитного слоя бетона путем отбивки его
в трех местах трубы: в середине раструба, в месте перехода от раструба к
цилиндрической части трубы и во втулочном конце трубы на расстоянии 300 мм от
торца.
Отбивку защитного
слоя в каждом из указанных мест производят по наружному диаметру не менее чем в
трех точках (через 120°) с последующей обязательной заделкой отбитых мест
раствором состава по массе 1:2,5:0,4 (цемент, песок, вода).
(Измененная
редакция, Изм. N 1).
5.5. Качество
защитного слоя бетона в трубах определяют путем тщательного простукивания
наружной поверхности труб молотком массой 250 г.
5.6.
Размеры труб и качество их поверхностей должны контролироваться согласно ГОСТ
26433.0-85, ГОСТ 26433.1-89 и настоящему стандарту.
5.7. Для контроля
геометрических размеров труб следует применять стандартный измерительный
инструмент или специальные приспособления, обеспечивающие необходимую точность
измерения и аттестованные органами метрологической службы.
5.7.1. Проверку
размеров труб проводят следующим образом:
толщину стенок
измеряют штангенциркулем или другими приспособлениями в
четырех точках в середине между швами по двум взаимно перпендикулярным
диаметрам на расстоянии 300 мм от втулочного торца трубы;
наружный диаметр
втулочного конца трубы и буртика измеряют калибрами с промером по двум взаимно
перпендикулярным диаметрам;
внутренний диаметр
калиброванной части раструба измеряют нутромером или штангенциркулем по двум
взаимно перпендикулярным диаметрам в точках, отстоящих на расстояниях 40, 80 и
110 мм от торца трубы;
внутренний диаметр
трубы измеряют нутромером по двум взаимно перпендикулярным диаметрам на
расстоянии 500 мм от ее торцов.
5.8.
Параметры шероховатости внутренней поверхности трубы Ra
и Sm по ГОСТ 2789-73 определяют по методике,
приведенной в обязательном Приложении.
6.
МАРКИРОВКА, ТРАНСПОРТИРОВАНИЕ И ХРАНЕНИЕ
6.1.
Маркировка труб - по ГОСТ 13015.2-81. Маркировочные надписи и знаки следует
наносить на наружной поверхности раструба каждой трубы.
6.2.
Требования к документу о качестве труб, поставляемых потребителю, - по ГОСТ
13015.3-81. В документе о качестве труб следует дополнительно приводить
значения параметров шероховатости внутренней поверхности труб, а также марку
уплотняющих резиновых колец и обозначение технических условий на эти кольца.
6.3. Трубы
перемещают с помощью траверс, не допускающих повреждения труб. Перекатка труб
допускается только по каткам, укладываемым с таким расчетом, чтобы трубы не
опирались раструбами и втулочными концами на катки или пол.
6.4. Трубы следует
хранить на складе готовой продукции в штабелях рассортированными
по маркам.
Число рядов труб по
высоте должно быть не более указанного в табл. 6.
Таблица 6
────────────────────────────────────┬─────────────────────────────
Диаметр условного прохода трубы │
Число рядов труб по высоте
d, мм │
────────────────────────────────────┼─────────────────────────────
От
500 до 1000 включ. │ 4
1200 │ 3
1400
и 1600
│ 2
6.5. Под каждый
нижний ряд труб штабеля должны быть уложены две подкладки на расстоянии 1 м от
торцов труб. Конструкция подкладки не должна позволять раскатываться первому
ряду труб. Подкладки устанавливают параллельно под цилиндрическую часть труб.
На месте
постоянного складирования труб подкладки следует закреплять на площадке.
Трубы в рядах
укладывают так, чтобы раструбы двух рядом лежащих труб были обращены в разные
стороны. Трубы каждого последующего ряда располагают по длине перпендикулярно к
предыдущему ряду.
6.6. При погрузке
труб на транспортные средства и их выгрузке должны соблюдаться меры
предосторожности, исключающие возможность повреждения труб.
Автомобили или
железнодорожные платформы, предназначаемые для перевозке труб, должны иметь седлообразные подкладки,
исключающие возможность смещения и соприкасания труб.
6.7. При выполнении
погрузочно-разгрузочных работ с трубами не допускаются:
применение цепей и
тросов с узлами или выступами, которые могут повредить бетон;
переноска труб при
закреплении троса в одной плоскости или путем пропуска его через трубу, а также
с помощью крючков, зацепляемых за концы трубы;
перемещение труб по
земле волоком;
разгрузка труб со
свободным падением;
свободное (без
торможения) перекатывание труб по наклонным плоскостям;
перемещение труб
без катков или без подкладок.
Приложение
Обязательное
ОПРЕДЕЛЕНИЕ
ПАРАМЕТРОВ ШЕРОХОВАТОСТИ
ВНУТРЕННЕЙ
ПОВЕРХНОСТИ ТРУБЫ
1. Параметры шероховатости внутренней поверхности трубы Rа и Sm по ГОСТ 2789-73
определяют по результатам испытаний на шероховатость поверхности двух
канифолевых слепков (отпечатков) размерами 80 х 15 х 20 мм, снятых с
контролируемой поверхности трубы в точках, расположенных на расстоянии 500 мм
от втулочного и раструбного торцов трубы.
2. Аппаратура и
материалы
2.1. Для
определения параметров шероховатости применяют:
профилограф-профилометр модели 293 Московского завода "Калибр" или
другие средства контроля, обеспечивающие измерение параметров шероховатости Ra в пределах 0,04 - 0,11 мм, Sm
- в пределах 4 - 8 мм;
разборную
металлическую рамку (черт. 1);
емкость для разогрева
канифоли;
ящик для хранения
слепков;
сосновую канифоль
по ГОСТ 19113-84;
порошковый графит
по ГОСТ 17022-81;
смазочное масло.
Разборная
металлическая рамка
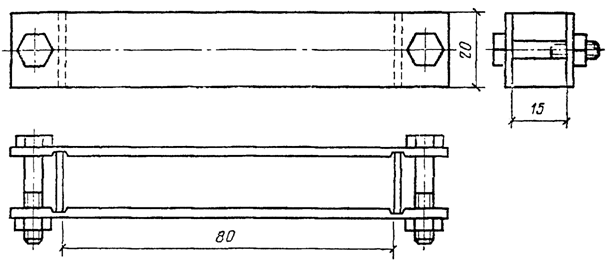
Черт. 1
(Измененная
редакция, Изм. N 1).
3. Подготовка к
испытанию
3.1. Для
изготовления слепков приготавливают смесь канифоли с порошком графита
(соотношение 100:1 по массе) и разогревают ее в емкости до жидкого состояния.
3.2. Две рамки для изготовления слепков очищают, смазывают их внутренние
поверхности тонким слоем масла и устанавливают в лотке трубы вдоль ее оси на
расстоянии 500 мм от втулочного и раструбного концов.
3.3. Подготовленные
рамки наполняют разогретой смесью канифоли с графитом и выдерживают в трубе в
течение 10 мин.
3.4. Рамки с
затвердевшей в них смесью снимают с поверхности трубы и разбирают.
Изготовленные слепки маркируют и укладывают в ящик для хранения. На боковых
поверхностях слепка наносят: номер слепка, номер и марку трубы.
4. Проведение
испытаний
4.1. Со слепков
записывают профилограммы шероховатости. Для этого
слепок устанавливают на измерительную площадку
профилографа-профилометра вдоль оси движения
иглы прибора и производят запись профиля поверхности на базовой длине, равной
75 мм. Игла прибора при записи должна перемещаться по центру слепка.
4.2. При записи
профиля поверхности регистрируют значение параметра на
индикаторе прибора и записывают его в журнал
наблюдений и на профилограмме.
4.3. Ленту с
записанной профилограммой отрывают и маркируют,
записывая на ней номер и марку контролируемой трубы, номер слепка.
5. Обработка
результатов
5.1. Параметр шероховатости Rа трубы
определяют как среднее арифметическое значение результатов испытаний двух
слепков, снятых с внутренней поверхности трубы во втулочной и раструбной
частях.
5.2. Для
определения параметра
на профилограмме
(черт. 2) проводят среднюю линию профиля. Для этого на профилограмме
выделяют высшую и низшую точки профиля в пределах базовой длины (черт. 2, точки А и В) и проводят горизонтальные линии выступов и впадин
профиля. Отмечают точки пересечения кривой профиля со средней линией и
определяют их число на базовой длине.
Пример фрагмента профилограммы внутренней поверхности трубы
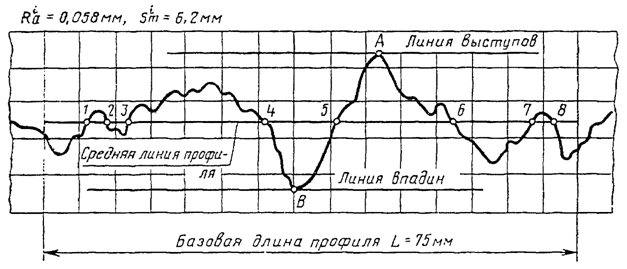
Черт. 2
5.3. Параметр
в мм для каждой профилограммы вычисляют по формуле
,
где n - число точек
пересечения кривой профиля со средней линией в пределах базовой длины.
5.4. Параметр шероховатости Sm трубы
определяют как среднее арифметическое значение результатов испытаний двух
слепков, снятых с внутренней поверхности трубы во втулочной и раструбной
частях.
5.5. В журнале, в
котором заносят результаты испытаний, должны быть предусмотрены следующие
графы:
- дата изготовления
трубы;
- марка и номер
трубы;
- номер резинового
чехла внутренней формы трубы;
- номер слепка;
- значения
параметров шероховатости
, Ra,
и Sm.