Введен в действие
Постановлением
Госстандарта СССР
от 30 июля 1984 г.
N 2686
ГОСУДАРСТВЕННЫЙ СТАНДАРТ СОЮЗА ССР
СИСТЕМА СТАНДАРТОВ БЕЗОПАСНОСТИ ТРУДА
ПОЖАРОВЗРЫВООПАСНОСТЬ ВЕЩЕСТВ И МАТЕРИАЛОВ.
НОМЕНКЛАТУРА ПОКАЗАТЕЛЕЙ И МЕТОДЫ ИХ ОПРЕДЕЛЕНИЯ
Occupational safety standards
system. Fire and explosion
hazard of substances and
materials. Nomenclature of indices
and methods of their
determination
ГОСТ 12.1.044-84*
(СТ СЭВ 4831-84, СТ СЭВ 6219-88,
СТ СЭВ 6527-88, МС ИСО 4589)
Группа Т58
Постановлением
Государственного комитета СССР по стандартам от 30 июля 1984 г. N 2686 срок
действия установлен с 01.07.1985 до 01.07.1990.
Взамен <*>
--------------------------------
<*> ГОСТ
12.1.017-80, ГОСТ 12.1.021-80, ГОСТ 12.1.022-80, ГОСТ 12.1.032-81, ГОСТ
12.1.039-82, ГОСТ 13919-68, ГОСТ 13920-68, ГОСТ 17088-71.
Переиздание
(декабрь 1985 г.) с Изменением N 1, утвержденным в октябре 1985 г. (ИУС N 1 -
86).
Настоящий стандарт
распространяется на вещества и материалы, применяемые во всех отраслях
народного хозяйства.
Стандарт не
распространяется на взрывчатые и радиоактивные вещества и материалы.
Стандарт
устанавливает номенклатуру показателей пожаровзрывоопасности веществ и
материалов и методы их определения.
Настоящий стандарт
соответствует СТ СЭВ 4831-84 в части метода определения нижнего
концентрационного предела распространения пламени по пылевоздушным смесям;
МС ИСО 2592-73 в
части метода определения температуры вспышки нефтепродуктов в открытом тигле и
температуры воспламенения в приборе Кливленда;
Р ИСО 1326-70 в
части определения воспламеняемости и скорости горения пленки;
СТ СЭВ 6219-88 в
части определения кислородного индекса пластмасс;
(в ред. Изменения N 2, утв.
Постановлением Госстандарта СССР от 23.03.1989 N 608)
рекомендации СЭВ по
стандартизации РС 4168-73 в части определения кислородного индекса пластмасс;
СТ СЭВ 6527-88 в части метода определения концентрационных пределов распространения
пламени по газо- и паровоздушным смесям.
(в ред. Изменения N 3, утв.
Постановлением Госстандарта СССР от 23.03.1989 N 608)
(Измененная
редакция, Изм. N 1).
1. ОБЩИЕ
ПОЛОЖЕНИЯ
1.1. Показатели
пожаровзрывоопасности веществ и материалов определяются с целью получения
исходных данных для подразделения производств на категории в соответствии с
требованиями строительных норм и правил на проектирование производственных
зданий промышленных предприятий, утвержденных Госстроем СССР; Правил устройства
электроустановок, утвержденных Госэнергонадзором; при классификации судов в
соответствии с требованиями Правил классификации и постройки морских, речных
судов и судов смешанного плавания, утвержденных Регистром СССР, а также для
разработки систем по обеспечению пожарной безопасности и взрывобезопасности в
соответствии с требованиями ГОСТ 12.1.004-85 и ГОСТ 12.1.010-76.
1.2.
Пожаровзрывоопасность веществ и материалов определяется показателями, выбор
которых зависит от агрегатного состояния вещества и условий его применения.
1.3. При
определении пожаровзрывоопасности веществ и материалов различают:
газы - вещества,
абсолютное давление паров которых при температуре 50 °C равно или более 300 кПа
(3
) или
критическая температура которых менее 50 °C;
жидкости - вещества
с температурой плавления (каплепадения) более 50 °C;
твердые вещества и
материалы с температурой плавления (каплепадения) более 50 °C;
пыли - диспергированные
твердые вещества и материалы с размером частиц менее 850 мкм.
1.4. Номенклатура и
применяемость показателей пожаровзрывоопасности веществ и материалов приведены
в табл. 1.
Таблица 1
────────────────────────────┬─────────────────────────────────────
Показатель │ Применяемость показателей
│ пожаровзрывоопасности
├────────┬─────────┬─────────┬────────
│ газов │жидкостей│ твердых │ пылей
│ │ │ веществ │
────────────────────────────┼────────┼─────────┼─────────┼────────
Группа горючести │ +*
│ +* │
+* │ +*
Температура вспышки │
- │ +*
│ + │
-
Температура воспламенения │ -
│ + │
+ │ +
Температура │ +*
│ +* │
+* │ +*
самовоспламенения │ │ │ │
Нижний и верхний │ +
│ +* │
- │ +*
концентрационные
пределы │ │ │ │
распространения
пламени │ │ │ │
(воспламенения) │ │ │ │
Температурные пределы │
+ │ +
│ - │
-
распространения
пламени │ │ │ │
(воспламенения) │ │ │ │
Температура самонагревания│ -
│ - │
+ │ +
Температура тления │ -
│ - │
+ │ +
Условия теплового │
- │ -
│ + │
+
самовозгорания │ │ │ │
Минимальная энергия │
+ │ +
│ - │
+
зажигания │ │ │ │
Кислородный индекс │ -
│ - │
+ │ -
Способность взрываться │
+* │ +*
│ +* │
+*
и
гореть при взаимодействии │
│ │ │
с
водой, кислородом воздуха │
│ │ │
и
другими веществами │ │ │ │
Нормальная скорость │
+ │ +
│ - │
-
распространения
пламени │ │ │ │
Скорость выгорания │ -
│ + │
- │ -
Коэффициент │ -
│ - │
+ │ -
дымообразования │ │ │ │
Индекс распространения │
- │ -
│ + │
-
пламени │ │ │ │
Показатель токсичности │
- │ -
│ + │
-
продуктов
горения полимерных│
│ │ │
материалов │ │ │ │
Минимальное взрывоопасное │ +
│ + │
- │ +
содержание
кислорода │ │ │ │
Минимальная │
+ │ +
│ - │
+
флегматизирующая │ │ │ │
концентрация
флегматизатора │
│ │ │
Максимальное давление │
+ │ +
│ - │
+
взрыва │ │ │ │
Скорость нарастания │
+ │ +
│ - │
+
давления
при взрыве │ │ │ │
Примечания. 1. Знак
"+" означает применяемость, знак "-" - неприменяемость
показателя.
2. Знаком *
отмечены показатели, которые необходимо включать в стандарты и технические
условия на вещества и материалы. Нижний и верхний концентрационные пределы
распространения пламени обязательны только для легковоспламеняющихся жидкостей;
для пылей определения только нижний концентрационный предел распространения
пламени.
3. Кроме указанных
в табл. 1 могут быть определены и другие показатели, более детально
характеризующие пожаровзрывоопасность веществ и материалов.
1.5. Количество
показателей, необходимых и достаточных для характеристики пожаровзрывоопасности
веществ и материалов в условиях их производства, переработки, транспортировки и
хранения, определяет разработчик системы обеспечения пожаровзрывобезопасности
объекта.
2.
ПОКАЗАТЕЛИ ПОЖАРОВЗРЫВООПАСНОСТИ
2.1. Группа
горючести
2.1.1. Горючесть -
способность вещества или материала к горению.
2.1.2. По горючести
вещества и материалы подразделяют на три группы:
негорючие
(несгораемые) - вещества и материалы, не способные к горению в воздухе.
Негорючие вещества могут быть пожароопасными (например: окислители, а также
вещества, выделяющие горючие продукты при взаимодействии с водой, кислородом
воздуха или друг с другом);
трудногорючие
(трудносгораемые) - вещества и материалы, способные возгораться в воздухе от
источника зажигания, но не способные самостоятельно гореть после его удаления;
горючие (сгораемые)
- вещества и материалы, способные самовозгораться, а также возгораться от
источника зажигания и самостоятельно гореть после его удаления. Из группы
горючих веществ и материалов выделяют легковоспламеняющиеся вещества и
материалы.
Легковоспламеняющимися
называют горючие вещества и материалы, способные воспламеняться от
кратковременного (до 30 с) воздействия источника зажигания с низкой энергией
(пламя спички, искра, тлеющая сигарета и т.п.). Легковоспламеняющимися
называются жидкости с температурой вспышки не более 61 °C в закрытом тигле или
66 °C в открытом тигле.
2.1.3. Результаты
оценки группы горючести следует применять при подразделении материалов по
горючести; при определении категории производств по взрывной, взрывопожарной и
пожарной опасности, а также классов взрывоопасных и пожароопасных зон; при
разработке мероприятий по обеспечению пожарной безопасности в соответствии с
требованиями ГОСТ 12.1.004-85.
2.1.4. Сущность
метода определения горючести заключается в создании температурных условий,
наиболее способствующих горению, и оценке поведения испытуемых веществ и
материалов в этих условиях.
Методы
экспериментального определения горючести жидкостей, металлических порошков и плавящихся
твердых веществ приведены в п. 4.1, неплавящихся твердых веществ и материалов -
в п. 4.2.
Горючесть газов
определяют косвенно: газ, имеющий концентрационные пределы воспламенения в
воздухе, относят к горючим; при отсутствии концентрационных пределов
воспламенения и наличии температуры самовоспламенения газ относят к
трудногорючим; при отсутствии концентрационных пределов воспламенения и
температуры самовоспламенения газ относят к негорючим.
2.2.
Температура вспышки
2.2.1. Вспышка -
быстрое сгорание горючей смеси, не сопровождающееся образованием сжатых газов.
Температура вспышки
- самая низкая температура горючего вещества, при которой в условиях
специальных испытаний над его поверхностью образуются пары или газы, способные
вспыхивать от источника зажигания, но скорость их образования еще не достаточна
для устойчивого горения.
2.2.2. Значение
температуры вспышки следует применять при классификации жидкостей по степени
пожароопасности, при определении категории производств по взрывной,
взрывопожарной и пожарной опасности, а также классов взрывоопасных и пожарной
безопасности и взрывобезопасности в соответствии с требованиями ГОСТ
12.1.004-85 и ГОСТ 12.1.010-76.
2.2.3. Сущность
экспериментального метода определения температуры вспышки заключается в
нагревании определенной массы вещества с заданной скоростью, периодическом
зажигании выделяющихся паров и визуальной оценке результатов зажигания.
Методы
экспериментального и расчетного определения температуры вспышки приведены в пп.
4.3 - 4.5.
2.3.
Температура воспламенения
2.3.1. Температура
воспламенения - наименьшая температура вещества, при которой в условиях
специальных испытаний вещество выделяет горючие пары и газы с такой скоростью,
что после их зажигания возникает устойчивое пламенное горение.
2.3.2. Значение
температуры воспламенения следует применять при установлении группы горючести
веществ, оценке пожарной опасности оборудования и технологических процессов,
связанных с переработкой горючих веществ, при разработке мероприятий по
обеспечению пожаровзрывобезопасности технологических процессов в соответствии с
требованиями ГОСТ 12.1.004-85 и ГОСТ 12.1.010-76.
2.3.3. Сущность
экспериментального метода определения температуры воспламенения заключается в
нагревании определенной массы вещества, периодическом зажигании выделяющихся
паров и визуальной оценке результатов зажигания.
Методы
экспериментального и расчетного определения температуры воспламенения приведены
в пп. 4.6 - 4.8.
2.4.
Температура самовоспламенения
2.4.1. Температура
самовоспламенения - самая низкая температура вещества, при которой в условиях
специальных испытаний происходит резкое увеличение скорости экзотермических
реакций, заканчивающихся пламенным горением.
2.4.2. Значение
температуры самовоспламенения следует применять при оценке
пожаровзрывоопасности веществ, при определении группы взрывоопасной смеси по
ГОСТ 12.1.011-78 для выбора типа взрывозащищенного электрооборудования, при
разработке мероприятий по обеспечению пожаровзрывобезопасности технологических
процессов в соответствии с требованиями ГОСТ 12.1.004-85 и ГОСТ 12.1.010-76.
2.4.3. Сущность
метода определения температуры самовоспламенения заключается во введении в
нагретый сосуд определенной массы исследуемого вещества и визуальной оценке
результатов испытания. Варьированием температуры находят минимальную
температуру, при которой происходит самовоспламенение вещества.
Методы
экспериментального определения температуры самовоспламенения приведены в пп.
4.9; 4.10.
2.5. Нижний
и верхний концентрационные пределы распространения пламени (воспламенения)
2.5.1. Нижний
(верхний) концентрационный предел распространения пламени - минимальное
(максимальное) содержание горючего в смеси "горючее вещество -
окислительная среда", при котором возможно распространение пламени по
смеси на любое расстояние от источника зажигания.
2.5.2. Значение
нижнего концентрационного предела распространения пламени следует применять при
определении категории производств по пожаровзрывоопасности.
Значения нижнего и
верхнего концентрационных пределов распространения пламени следует применять
при расчете взрывобезопасных концентраций газов, паров и пылей внутри
технологического оборудования, трубопроводов, при проектировании вентиляционных
систем, а также при расчете предельно допустимых взрывобезопасных концентраций
газов, паров и пылей в воздухе рабочей зоны с потенциальными источниками
зажигания в соответствии с требованиями ГОСТ 12.1.010-76.
Допускается
использовать экспериментальные и расчетные значения концентрационных пределов
распространения пламени.
2.5.3. Сущность
метода определения концентрационных пределов распространения пламени
заключается в зажигании газо-, паро-, пылевоздушной смеси заданной конструкции
исследуемого вещества в объеме реакционного сосуда и установлении факта наличия
или отсутствия распространения пламени. Изменяя концентрацию горючего в смеси,
устанавливают ее минимальное и максимальное значение, при которых происходит
распространение пламени.
Методы
экспериментального и расчетного определения концентрационных пределов
распространения пламени приведены в пп. 4.11 - 4.14.
2.6.
Температурные пределы распространения пламени (воспламенения)
2.6.1.
Температурные пределы распространения пламени - такие температуры вещества, при
которых его насыщенные пары образуют в конкретной окислительной среде
концентрации, равные соответственно нижнему (нижний температурный предел) и
верхнему (верхний температурный предел) концентрационным пределам распространения
пламени.
2.6.2. Значение
температурных пределов распространения пламени следует применять при разработке
мероприятий по обеспечению пожаровзрывобезопасности в соответствии с
требованиями ГОСТ 12.1.004-85 и ГОСТ 12.1.010-76, при расчете пожаровзрывобезопасных
температурных режимов работы технологического оборудования, при оценке
аварийных ситуаций, связанных с разливом горючих жидкостей, и для расчета
концентрационных пределов распространения пламени.
Допускается
использовать температурные пределы распространения пламени, полученные
экспериментальным путем, методом пересчета из концентрационных пределов и
расчетно-аналитическим методом.
2.6.3. Сущность
метода определения температурных пределов распространения пламени заключается в
выявлении минимальной и максимальной температур жидкости, при которых пары,
находящиеся в равновесии с жидкой фазой, образуют с воздухом смесь, способную
воспламеняться от источника зажигания и распространять пламя в объеме
реакционного сосуда.
Методы
экспериментального и расчетного определения температурных пределов
распространения пламени приведены в пп. 4.15; 4.16.
2.7.
Температура самонагревания
2.7.1. Температурой
самонагревания называется самая низкая температура вещества, при которой
самопроизвольный процесс его нагревания не приводит к тлению или пламенному
горению.
2.7.2. Значение
температуры самонагревания следует применять при выборе безопасных условий
нагрева вещества, при разработке мероприятий по обеспечению пожаробезопасности
технологических процессов в соответствии с требованиями ГОСТ 12.1.004-85.
Безопасной
температурой длительного нагрева вещества считают температуру, не превышающую
90% температуры самонагревания.
2.7.3. Сущность
метода определения температуры самонагревания заключается в изотермическом
нагревании вещества и установлении минимально возможной температуры, при
которой в веществе возникают практически различимые экзотермические процессы
окисления и разложения.
Метод
экспериментального определения температуры самонагревания приведен в п. 4.17.
2.8.
Температура тления
2.8.1. Температура
тления - температура вещества, при которой происходит резкое увеличение
скорости экзотермических реакций окисления, заканчивающихся возникновением
тления.
2.8.2. Значение
температуры тления следует применять при экспертизах причин пожаров, при выборе
взрывозащищенного электрооборудования и разработке мероприятий по обеспечению
пожарной безопасности технологических процессов.
2.8.3. Сущность
метода определения температуры тления заключается в изотермическом нагревании образца
вещества (материала) при обдуве воздухом и визуальной оценке результатов
испытания. Варьированием температуры находят минимальную температуру
реакционной зоны сосуда, при которой происходит тление вещества.
Метод
экспериментального определения температуры тления приведен в п. 4.18.
2.9.
Условия теплового самовозгорания
2.9.1. Условия
теплового самовозгорания - экспериментально выявленная зависимость между
температурой окружающей среды, массой вещества и временем до момента его
самовозгорания.
2.9.2. Результаты
оценки условий теплового самовозгорания следует применять при выборе безопасных
условий хранения и переработки самовозгорающихся веществ в соответствии с
требованиями ГОСТ 12.1.004-85.
2.9.3. Сущность
метода определения условий теплового самовозгорания заключается в
изотермическом нагревании определенной массы вещества, приводящем к
возникновению горения (тления), и установлении зависимости между температурой,
при которой происходит тепловое самовозгорание вещества, его размерами и
временем до возникновения горения (тления).
Метод
экспериментального определения условий теплового самовозгорания приведен в п.
4.19.
2.10.
Минимальная энергия зажигания
2.10.1. Минимальная
энергия зажигания - наименьшее значение энергии электрического разряда, способной
воспламенить наиболее легковоспламеняющуюся смесь газа, пара или пыли с
воздухом.
2.10.2. Значение
минимальной энергии зажигания следует применять при разработке мероприятий по
обеспечению пожаровзрывобезопасных условий переработки горючих веществ и
электростатической искробезопасности технологических процессов в соответствии с
требованиями ГОСТ 12.1.004-85, ГОСТ 12.1.010-76 и ГОСТ 12.1.018-79.
2.10.3. Сущность
метода определения минимальной энергии зажигания заключается в зажигании газо-,
паро-, пылевоздушной смеси определенной концентрации электрическим разрядом
определенной энергии в объеме реакционного сосуда.
За минимальную
энергию зажигания принимают электрическую энергию заряженного конденсатора,
способную зажечь наиболее легковоспламеняющуюся газо-, паро-, пылевоздушную
смесь с вероятностью 0,01 при оптимальных параметрах искрового разряда.
Методы
экспериментального определения минимальной энергии зажигания приведены в пп.
4.20; 4.21.
2.11.
Кислородный индекс
2.11.1. Кислородный
индекс - минимальное содержание кислорода в кислородно-азотной смеси, при
котором возможно свечеобразное горение материалов в условиях специальных
испытаний.
2.11.2. Значение
кислородного индекса следует применять при разработке полимерных композиций
пониженной горючести и контроле горючести твердых материалов.
2.11.3. Сущность
метода определения кислородного индекса заключается в зажигании вертикально
закрепленного образца материала в кислородно-азотной среде и оценке результатов
испытания. Изменяя концентрацию кислорода в кислородно-азотной смеси,
определяют ее минимальное значение, при котором наблюдается самостоятельное
горение образца.
Метод
экспериментального определения кислородного индекса приведен в п. 4.22.
2.12.
Способность взрываться и гореть при взаимодействии с водой, кислородом воздуха
и другими веществами (взаимный контакт веществ)
2.12.1. Способность
взрываться и гореть при взаимодействии с водой, кислородом воздуха и другими
веществами - это качественный показатель, характеризующий особую пожарную
опасность некоторых веществ.
2.12.2. Результаты
оценки способности взрываться и гореть при взаимном контакте веществ следует
применять при определении категории производств; при выборе безопасных условий
проведения технологических процессов и условий совместного хранения и
транспортировки веществ и материалов.
2.12.3. Сущность
метода определения опасности взаимного контакта веществ заключается в
механическом смешивании испытуемых образцов в заданной пропорции и оценке
результатов испытания.
Метод
экспериментального определения опасности взаимного контакта веществ приведен в
п. 4.23.
2.13.
Нормальная скорость распространения пламени
2.13.1. Нормальная
скорость распространения пламени - скорость перемещения фронта пламени
относительно несгоревшего газа в направлении, перпендикулярном к его
поверхности.
2.13.2. Значение
нормальной скорости распространения пламени следует применять в расчетах
скорости нарастания взрывного давления газо-, паровоздушных смесей,
критического (гасящего) диаметра, при разработке мероприятий по обеспечению
пожаровзрывобезопасности технологических процессов в соответствии с требованиями
ГОСТ 12.1.004-85 и ГОСТ 12.1.010-76.
2.13.3. Сущность
метода определения нормальной скорости распространения пламени заключается в
создании газо-, паровоздушной смеси стехиометрического состава, зажигании ее и
оценке скорости перемещения фронта пламени.
Метод
экспериментального определения нормальной скорости распространения пламени
приведен в п. 4.24.
2.14.
Скорость выгорания
2.14.1. Скорость
выгорания - количество горючего, сгорающего в единицу времени с единицы
площади.
Скорость выгорания
характеризует интенсивность горения вещества в условиях пожара.
2.14.2. Значение
скорости выгорания следует применять при расчетных определениях
продолжительности пожара в резервуарах, интенсивности тепловыделения и
температурного режима пожара.
2.14.3. Сущность метода
определения скорости выгорания заключается в зажигании образца вещества в
реакционном сосуде и фиксировании убыли массы образца за определенный
промежуток времени.
Метод
экспериментального определения скорости выгорания приведен в п. 4.25.
2.15.
Коэффициент дымообразования
2.15.1. Коэффициент
дымообразования - величина, характеризующая оптическую плотность дыма,
образующегося при сгорании вещества (материала) с заданной насыщенностью в
объеме помещения.
2.15.2.
Значение коэффициента дымообразователя следует применять для классификации
материалов по дымообразующей способности.
По дымообразующей
способности материалы подразделяют на три группы:
с малой
дымообразующей способностью - коэффициент дымообразования до 50 включ.;
с умеренной
дымообразующей способностью - коэффициент дымообразования св. 50 до 500 включ.;
с высокой
дымообразующей способностью - коэффициент дымообразования св. 500.
2.15.3. Сущность
метода определения коэффициента дымообразования заключается в фотометрической регистрации
ослабления освещенности при прохождении света через задымленное пространство.
Метод
экспериментального определения коэффициента дымообразования приведен в п. 4.26.
2.16.
Индекс распространения пламени
2.16.1. Индекс
распространения пламени - условный безразмерный показатель, характеризующий
способность веществ распространять пламя по поверхности.
2.16.2.
Значение индекса распространения пламени следует применять для классификации
материалов.
Строительные
материалы, лакокрасочные и полимерные покрытия, ткани и пленки подразделяют:
не распространяющие
пламя - среднее арифметическое значение индекса распространения пламени равно
0;
медленно
распространяющие пламя - среднее арифметическое значение индекса
распространения пламени от 0 до 20 включ.;
быстро
распространяющие пламя - среднее арифметическое значение индекса
распространения пламени св. 20.
2.16.3. Сущность
метода определения индекса распространения пламени заключается в оценке
скорости перемещения фронта пламени по поверхности образца материала,
помещенного в зону действия теплового излучателя.
Метод
экспериментального определения индекса распространения пламени приведен в п.
4.27.
2.17.
Показатель токсичности продуктов горения полимерных материалов
2.17.1. Показатель
токсичности продуктов горения - отношение количества материала к единице объема
замкнутого пространства, при сгорании которого выделяющиеся продукты вызывают
гибель 50% подопытных животных.
2.17.2.
Значение показателя токсичности продуктов горения полимерного материала следует
применять для сравнительной оценки полимерных материалов.
Полимерные
материалы классифицируются по величине показателя токсичности продуктов
горения:
чрезвычайно опасные
- показатель токсичности до 13
;
высокоопасные -
показатель токсичности от 13 до 40
;
умеренно опасные -
показатель токсичности от 40 до 120
;
малоопасные -
показатель токсичности св. 120
.
2.17.3. Сущность
метода определения показателя токсичности заключается в установлении
зависимости летального эффекта продуктов горения от массы материала, отнесенной
к единице объема замкнутого пространства.
Метод
экспериментального определения показателя токсичности приведен в п. 4.28.
2.18.
Минимальное взрывоопасное содержание кислорода
2.18.1. Минимальным
взрывоопасным содержанием кислорода называется такая его концентрация в горючей
смеси, ниже которой воспламенение и горение смеси становится невозможным при
любой концентрации горючего в смеси, разбавленной данным флегматизатором.
2.18.2. Значение
минимального взрывоопасного содержания кислорода следует применять при расчетах
пожаровзрывобезопасных режимов работы технологического оборудования, выборе
режимов работы систем "азотного дыхания", выборе безопасных условий
работы пневмотранспорта, разработке мероприятий по обеспечению
пожаровзрывобезопасности в соответствии с требованиями ГОСТ 12.1.004-85 и ГОСТ
12.1.010-76.
2.18.3. Сущность
метода определения минимального взрывоопасного содержания кислорода заключается
в нахождении предельного содержания кислорода в газо-, паро- или пылевоздушной
смеси, при котором смесь является предельной по горючести.
Методы
экспериментального определения минимального взрывоопасного содержания кислорода
приведены в пп. 4.29; 4.30.
2.19.
Минимальная флегматизирующая концентрация флегматизатора
2.19.1. Минимальная
флегматизирующая концентрация - наименьшая концентрация флегматизатора в смеси
с горючим и окислительной средой, при которой смесь становится неспособной к
распространению пламени при любом соотношении горючего и окислительной среды.
2.19.2. Значение
минимальной флегматизирующей концентрации следует применять при расчетах
безопасных составов газовых и пылегазовых смесей, при разработке мероприятий по
пожаровзрывобезопасности технологических процессов в соответствии с
требованиями ГОСТ 12.1.004-85 и ГОСТ 12.1.010-76.
2.19.3. Методы
экспериментального определения минимальной флегматизирующей концентрации
флегматизатора приведены в пп. 4.29; 4.30.
2.20.
Максимальное давление взрыва
2.20.1.
Максимальное давление взрыва - наибольшее давление, возникающее при
дефлаграционном взрыве газо-, паро- или пылевоздушной смеси в замкнутом сосуде
при начальном давлении смеси 101,3 кПа.
2.20.2. Значение
максимального давления взрыва следует применять при разработке мероприятий по
пожаровзрывобезопасности технологических процессов в соответствии с
требованиями ГОСТ 12.1.004-85 и ГОСТ 12.1.010-76.
2.20.3. Сущность
метода определения максимального давления взрыва заключается в зажигании газо-,
паро-, пылевоздушной смеси заданной концентрации в объеме реакционного сосуда и
фиксировании развивающегося при воспламенении горючей смеси давления взрыва.
Изменяя концентрацию горючего в смеси, выявляют максимальное значение давления
взрыва.
Методы
экспериментального определения максимального давления взрыва приведены в пп.
4.31; 4.32.
2.21.
Скорость нарастания давления при взрыве
2.21.1. Скорость
нарастания давления при взрыве - производная давления взрыва по времени на
восходящем участке зависимости давления взрыва газо-, паро-, пылевоздушной
смеси в замкнутом сосуде от времени.
2.21.2. Значение
скорости нарастания давления при взрыве следует применять при расчетах
предохранительных устройств, при разработке мероприятий по
пожаровзрывобезопасности технологических процессов в соответствии с
требованиями ГОСТ 12.1.004-85 и ГОСТ 12.1.010-76.
2.21.3. Сущность
метода определения скорости нарастания давления при взрыве заключается в
нахождении максимальной скорости изменения давления, возникающего в объеме
реакционного сосуда при взрыве газо-, паро-, пылевоздушных смесей заданного
состава.
Методы
экспериментального и расчетного определения скорости нарастания давления при
взрыве приведены в пп. 4.31 - 4.33.
3. УСЛОВИЯ
ПОЖАРОВЗРЫВОБЕЗОПАСНОСТИ ПРИ ИСПОЛЬЗОВАНИИ
ВЕЩЕСТВ И
МАТЕРИАЛОВ
3.1. Условия
пожаровзрывобезопасности определяют на основании данных, приведенных в табл. 2.
Таблица 2
─────────────────────────┬─────────────────┬──────────────────────
Способ предотвращения │Регламентируемый │Условие
пожаровзрыво-
пожара, взрыва │
параметр │безопасности
и пожаровзрывозащиты │ │
─────────────────────────┴─────────────────┴──────────────────────
Предотвращение
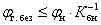
образования
горючей среды

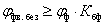
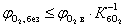
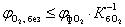
Ограничение Горючесть Горючесть вещества
воспламеняемости веществ и и материала должна
и
горючести веществ материалов быть не выше
и
материалов
регламентированной


Предотвращение

образования
в горючей
среде
(или внесения в

нее)
источников зажигания



- коэффициент безопасности к верхнему пределу
распространения пламени;
- коэффициент безопасности к энергии
зажигания;
- коэффициент безопасности к нижнему пределу
распространения пламени;
- коэффициент безопасности к концентрации
кислорода в смесях;
- коэффициент безопасности к температурам самовоспламенения,
самонагревания, среды, тления;
- коэффициент безопасности к минимальной
флегматизирующей концентрации флегматизатора в воздухе;
КИ - кислородный
индекс;
- допустимый кислородный индекс;
- безопасная температура, °C;
- температура вспышки, °C;
- допустимая температура вспышки, °C;
- минимальная температура среды, при которой
наблюдается самовозгорание образца, °C;
- температура самовоспламенения, °C;
- температура самонагревания, °C;
- температура тления, °C;
- минимальная энергия зажигания, Дж;
- безопасная энергия зажигания, Дж;
- безопасная концентрация газа, пара или пыли,
% об.;
- верхний концентрационный предел
распространения пламени по газо-, паро-, пылевоздушным смесям, % об.;
- безопасная концентрация горючих газов, паров
или пылей, % об.;
- нижний концентрационный предел
распространения пламени по
газо-, паро-, пылевоздушным смесям, %
об.;
- безопасная концентрация кислорода в смесях,
% об.;
- минимальная взрывоопасная концентрация
кислорода в смесях, соответствующая верхнему концентрационному пределу
распространения пламени, % об.;
- минимальная взрывоопасная концентрация
кислорода в смесях, соответствующая флегматизирующей концентрации, % об.;
- минимальная флегматизирующая концентрация
флегматизатора в воздухе, % об.;
- безопасная флегматизирующая концентрация
флегматизатора в воздухе, % об.
3.2. Коэффициент
безопасности
к показателям пожаровзрывоопасности
рассчитывают по формуле
, (1)
где
- коэффициент, учитывающий систематическую
погрешность метода определения показателя пожаровзрывоопасности;
- квантиль распределения Стьюдента при m
степенях свободы и уровне значимости
;
- коэффициент вариации экспериментального
показателя пожаровзрывоопасности.
3.3. Определение
коэффициентов безопасности к показателям пожаровзрывоопасности
Коэффициент
рассчитывают по формуле
, (2)
где
- относительная систематическая погрешность
метода определения параметра;
n - число
определений параметра конкретным методом;
,
- соответственно значение k-го определения
параметра и истинное значение.
Коэффициент
зависит от полноты учета в методике
объективных закономерностей, влияющих на параметр.
Уровень значимости
выбирают в зависимости от роли и места
показателя пожаровзрывоопасности в общей системе обеспечения
пожаровзрывобезопасности объекта, с учетом вероятности возникновения пожара и
вероятности воздействия опасных факторов пожара на человека, которые
установлены ГОСТ 12.1.004-85.
Квантиль
распределения Стьюдента
при m степенях свободы и уровне значимости
и коэффициент вариации
принимают в соответствии с данными, установленными
ГОСТ 11.004-74.
4. МЕТОДЫ
ОПРЕДЕЛЕНИЯ ПОКАЗАТЕЛЕЙ
ПОЖАРОВЗРЫВООПАСНОСТИ
ВЕЩЕСТВ И МАТЕРИАЛОВ
4.1. Метод экспериментального определения группы горючести жидкостей,
твердых плавящихся веществ и металлических порошков
4.1.1. Аппаратура
Прибор (черт. 1)
состоит из тигельной электропечи. Допускается использовать тигельную
электропечь любого типа с рабочим пространством диаметром от 120 до 200 мм и
высотой от 180 до 300 мм, позволяющую создавать температуру (900 +/- 10) °C;
кварцевого стакана
типа ВН-800 по ГОСТ 19908-80;
фарфорового тигля
низкой формы N 4 или 5 по ГОСТ 9147-80;
проволочного
держателя тигля;
смотрового зеркала
для наблюдения за образцом;
термоэлектрического
преобразователя типа ТХА по ГОСТ 6616-74 поверхностного, обыкновенного,
среднеинерционного, диаметром термоэлектродов 0,5 мм;
штатива;
керамической
подставки.
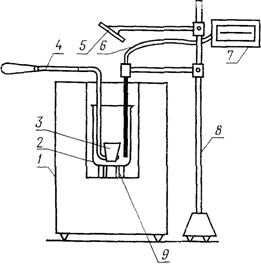
1 - тигельная
электропечь; 2 - кварцевый стакан;
3 - фарфоровый
тигель; 4 - держатель тигля; 5 - смотровое
зеркало; 6 -
термоэлектрический преобразователь;
7 - потенциометр; 8
- штатив; 9 - керамическая подставка
Черт. 1
Электронный
потенциометр типа КСП-4 с градуировкой
,
диапазоном измерения от 0 до 1000 °C, класс точности 0,5.
Секундомер по ГОСТ
5072-79, класс точности 3.
Весы лабораторные
общего назначения по ГОСТ 24104-88 с наибольшим пределом взвешивания 200 г,
класс точности 2.
(в ред. Изменения N 2, утв.
Постановлением Госстандарта СССР от 23.03.1989 N 608)
4.1.2. Проведение
испытаний
Перед проведением
испытаний устанавливают соответствие исследуемого вещества паспортным данным по
внешнему виду, плотности, коэффициенту рефракции, температуре кипения или
плавления входным контролем по ГОСТ 24297-87.
(в ред. Изменения N 2, утв.
Постановлением Госстандарта СССР от 23.03.1989 N 608)
В центре рабочего
пространства электропечи устанавливают кварцевый стакан на фарфоровой или
керамической подставке. В стакан на расстоянии от 5 до 10 мм от его стенки
вертикально опускают термоэлектрический преобразователь и закрепляют его в
штативе таким образом, чтобы рабочий конец находился в (4 +/- 1) мм от дна
стакана.
Электропечь
нагревают до температуры в рабочей зоне (900 +/- 10) °C.
Образец
исследуемого вещества массой 10 г помещают в тигель. Тигель с образцом
устанавливают в держатель и опускают в кварцевый стакан. Продолжительность
нагревания образца с момента введения его в электропечь составляет (3,0 +/-
0,1) мин.
Если образец в
течение этого времени не воспламеняется или начинает интенсивно кипеть без
воспламенения, испытание прекращают и считают его отказом.
Испытанию подвергают
пять образцов исследуемого вещества. Если хотя бы в одном из пяти испытаний
образец воспламенится, ему дают возможность разгореться, затем тигель с горящим
образцом выносят из электропечи, одновременно включают секундомер и определяют
продолжительность самостоятельного горения образца.
4.1.3. Обработка
результатов
Если образец вне
печи самостоятельно горит менее 5 с, то исследуемое вещество относят к группе
трудногорючих.
Если образец вне
печи продолжает гореть 5 с и более, то для определения группы горючести
необходимо провести дополнительное испытание на температуру воспламенения. При
наличии температуры воспламенения исследуемое вещество относят к группе
горючих, при отсутствии - к группе трудногорючих.
При испытании
неазеотропных смесей, состоящих из разнородных по горючести веществ, возможно
постепенное изменение горючести смеси по мере выкипания более летучего
компонента. В этом случае для правильной оценки горючести точно фиксируют
момент времени начала интенсивного кипения жидкости. Если этот момент времени
во всех пяти испытаниях не сопровождается воспламенением паров, то исследуемую
смесь считают негорючей.
Условия и
результаты испытаний регистрируют в протоколе испытаний.
4.1.4. Требования
безопасности
Прибор для
определения группы горючести следует устанавливать в вытяжном шкафу. Рабочее
место оператора должно удовлетворять требованиям электробезопасности по ГОСТ
12.1.019-79 и санитарно-гигиеническим требованиям по ГОСТ 12.1.005-88.
(в ред. Изменения N 2, утв.
Постановлением Госстандарта СССР от 23.03.1989 N 608)
4.2. Методы экспериментального определения горючести твердых веществ и
материалов
4.2.1. Метод
"Огневой трубы" для определения группы горючих веществ и материалов
4.2.1.1. Аппаратура
Прибор
"Огневая труба" (черт. 2а) состоит из камеры горения, представляющей
собой стальную трубу внутренним диаметром (50 +/- 3) мм, длиной (165 +/- 5) мм,
толщиной стенки (0,5 +/- 0,1) мм.
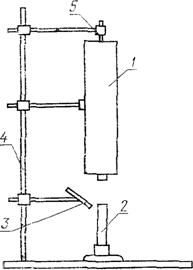
а)
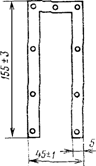
б)
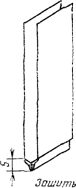
в)
1 - камера горения;
2 - газовая горелка; 3 - смотровое
зеркало; 4 -
штатив; 5 - держатель образца
Черт. 2
Камера закреплена
на штативе;
держателя образца;
газовой горелки
диаметром 7 мм;
смотрового зеркала
диаметром 50 мм, подвижно укрепленного на штативе.
Секундомер по ГОСТ
5072-79, класс точности 3.
Весы лабораторные
общего назначения по ГОСТ 24104-88 с наибольшим пределом взвешивания 200 г,
класс точности 2.
(в ред. Изменения N 2, утв.
Постановлением Госстандарта СССР от 23.03.1989 N 608)
Рамка стальная
(черт. 2б) из листа толщиной (0,5 +/- 0,1) мм.
Корзиночка
прямоугольной формы длиной (35 +/- 1) мм, высотой (150 +/- 3) мм, шириной (10
+/- 1) мм, выполненная из сетки с размерами. ячеек, препятствующими высыпанию
исследуемого вещества. Материал сетки - проволока из жаростойкой стали.
Полоски стеклоткани
по ГОСТ 8481-75 шириной (40 +/- 1) мм, длиной (340 +/- 5) мм, толщиной 0,1 мм.
4.2.1.2. Проведение
испытаний
Образцы должны
характеризовать средние свойства исследуемого вещества (материала). Для
испытаний изготовляют шесть образцов шириной (35 +/- 1) мм, длиной (150 +/- 3)
мм и фактической толщиной, не превышающей (10 +/- 1) мм. Сыпучие вещества и
материалы испытывают в корзиночках; плотность засыпки должна соответствовать
насыпной плотности, с которой вещество (материал) применяют на практике.
Пленочные материалы, способные при нагревании свертываться, закрепляют в
металлических рамках. Материалы, способные при нагревании плавиться, помещают в
полоски стеклоткани, сложенные петлей (черт. 2в). Расстояние от нижней кромки
образца до основания петли не должно быть менее 5 мм.
Подготовленные
образцы подвергают кондиционированию в соответствии с требованиями ГОСТ
12423-66.
Подготовленный к
испытанию и взвешенный образец подвешивают на крючок держателя образца в
вертикальном положении по центру камеры. Нижний конец образца (корзиночки)
должен выступать из камеры на (5 +/- 1) мм. Расстояние между нижним концом
образца и верхней кромкой горелки должно составлять (5 +/- 1) мм, при испытании
пенопластов оно может быть более 20 мм. Под образец по его центру устанавливают
горелку с высотой пламени (40 +/- 5) мм, одновременно включают секундомер и
определяют время зажигания, обеспечивающее устойчивое горение образца. Образцы,
помещенные в полоски стеклоткани, подвешивают на штативе (вне камеры) и
зажигают пламенем горелки с угла. После возгорания образца горелку удаляют и фиксируют
время самостоятельного горения (тления). Максимальное время зажигания образца
пламенем горелки не должно превышать 2 мин.
Остывший до
комнатной температуры образец вынимают из прибора и взвешивают, определяя
потерю массы образца.
Аналогичным образом
испытывают остальные пять образцов.
4.2.1.3. Обработка
результатов
Потерю массы
образца (М) при горении в процентах рассчитывают по формуле
, (3)
где
и
- масса образца до и после испытания, г.
Материал относят к
горючим при условии:
самостоятельное
пламенное горение и тление продолжалось более 60 с и потеря массы более чем у
одного образца (из шести) превысила 20%;
самостоятельное
пламенное горение продолжалось менее 60 с, но пламя распространилось по всей
поверхности образца при одновременной потере массы более чем у одного образца
свыше 90%;
самостоятельное
пламенное горение композиционных материалов, состоящих из горючих и негорючих
компонентов, продолжалось менее 60 с, но пламя распространилось по всей
поверхности образца и при этом выгорела вся органическая часть материала;
самостоятельное
пламенное горение композиционных материалов продолжалось более 60 с, а потеря
массы составила менее 20%. В таком случае потерю массы относят только к массе
органической части материала.
Если вышеизложенные
условия не выполняются, то испытание материала продолжают по методу КТ (п.
4.2.2).
Условия и
результаты испытаний регистрируют в протоколе испытаний.
4.2.1.4. Требования
безопасности
Прибор
"Огневая труба" следует устанавливать в вытяжном шкафу. При
проведении испытания оператор должен работать в противогазе, выбранном в
соответствии с токсичностью продуктов горения исследуемого материала. После
проведения каждого испытания включается вентиляция. Рабочее место оператора
должно удовлетворять санитарно-гигиеническим требованиям по ГОСТ 12.1.005-88.
(в ред. Изменения N 2, утв.
Постановлением Госстандарта СССР от 23.03.1989 N 608)
4.2.2.
Метод КТ для определения группы трудногорючих веществ и материалов
4.2.2.1. Аппаратура
Прибор (черт. 3)
состоит из керамической огневой камеры прямоугольной или цилиндрической формы
высотой (300 +/- 10) мм, толщиной стенок (16 +/- 2) мм, площадь поперечного
сечения которой составляет
мм2. Камера установлена на металлическую
цилиндрическую подставку, снабженную поворотной заслонкой для регулирования
подачи воздуха в зону горения и поддоном для сбора твердых продуктов горения;
газовой горелки
внутренним диаметром 7 мм;
механизма ввода
образца с держателем, фиксирующим положение образца в центре огневой камеры;
зонта с рукояткой,
установленного соосно на верхнюю кромку огневой камеры;
термоэлектрического
преобразователя типа ТХА по ГОСТ 6616-74 поверхностного, обыкновенного,
среднеинерционного, диаметром термоэлектродов 0,5 мм;
смотрового зеркала
для наблюдения за образцом в огневой камере.
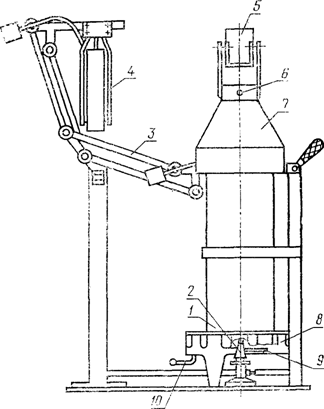
1 - огневая камера;
2 - газовая горелка; 3 - механизм ввода
образца; 4 -
держатель образца; 5 - смотровое зеркало;
6 -
термоэлектрический преобразователь; 7 - зонт;
8 - металлическая
подставка; 9 - поддон; 10 - рукоятка
поворотной заслонки
Черт. 3
Электронный
потенциометр типа КСП-4 с градуировкой
,
диапазоном измерения от 0 до 1000 °C, класс точности 0,5.
Ротаметр типа РМ по
ГОСТ 13045-81 с пределами измерения расхода газа до 0,1
.
Секундомер по ГОСТ
5072-79, класс точности 3.
Стеклоткань по ГОСТ
8481-75 толщиной 0,1 мм.
Весы лабораторные
общего назначения по ГОСТ 24104-88 с наибольшим пределом взвешивания 200 г,
класс точности 2.
(в ред. Изменения N 2, утв.
Постановлением Госстандарта СССР от 23.03.1989 N 608)
Асбестоцементная
плита шириной (60 +/- 1) мм, длиной (150 +/- 3) мм и толщиной (10 +/- 1) мм.
Корзиночка
прямоугольной формы длиной (60 +/- 1) мм, высотой (150 +/- 3) мм, шириной (10
+/- 1) мм, выполненная из сетки с размерами ячеек, препятствующими высыпанию
вещества. Материал сетки - проволока из жаростойкой стали.
Фольга алюминиевая
по ГОСТ 618-73 толщиной 0,08 - 0,10 мм.
4.2.2.2. Проведение
испытаний
Образцы должны
характеризовать средние свойства исследуемого вещества (материала). Для
испытаний готовят четыре образца исследуемого вещества (материала) шириной (60
+/- 1) мм, длиной (150 +/- 3) мм и фактической толщиной, не превышающей (10 +/-
1) мм; образцы пенопластов должны быть толщиной (30 +/- 1) мм. Масса образца не
должна быть менее 6 г. Сыпучие вещества и материалы испытывают в корзиночках;
плотность засыпки должна соответствовать насыпной плотности, с которой материал
применяют на практике. Материалы, способные при нагревании плавиться, помещают
в полоски стеклоткани, сложенные петлей. Расстояние от нижней кромки образца до
основания петли не должно быть менее 5 мм.
Подготовленные
образцы подвергают кондиционированию в соответствии с требованиями ГОСТ
12423-66.
Внутренняя
поверхность камеры горения перед каждым испытанием покрывается двумя-тремя
слоями алюминиевой фольги.
Исследуемый образец
закрепляют в держателе, зажигают газовую горелку и включают потенциометр. С
помощью ротаметра устанавливают такой расход газа в газовой горелке, при
котором контролируемая в течение 2 - 3 мин температура газообразных продуктов
горения в центре верхнего патрубка зонта составляла (200 +/- 5) °C. Затем в
камеру горения на 5 мин вводится исследуемый образец с целью выявления времени
зажигания
,
определяемого по характеру температурной кривой, записанной на диаграммной
ленте потенциометра.
За время зажигания
принимается время достижения максимальной температуры.
После определения
времени зажигания проводят три испытания с образцами исследуемого материала и
одно тарировочное испытание с асбестоцементной плитой, воздействуя на каждый
образец пламенем горелки в течение найденного времени зажигания. По истечении
времени зажигания прекращают подачу газа в горелку и оставляют образец в
огневой камере до остывания на время (20,0 +/- 0,1) мин
,
считая с момента ввода образца внутрь камеры.
В процессе
проведения испытания на диаграммной ленте потенциометра записывается
температура газообразных продуктов горения.
После каждого
испытания необходимо очистить рабочий конец термоэлектрического преобразователя
от твердых продуктов горения.
4.2.2.3. Обработка
результатов
По полученным на
диаграммной ленте температурным кривым газообразных продуктов горения
определяют площади под этими кривыми
(для тарировочного испытания) и
(основного испытания). Начальным уровнем при
определении
и
служит прямая, проведенная на диаграммной
ленте через две точки, соответствующие температурам образца в начальный период
испытания и в конечный период после истечения времени
.
Показатель
горючести (К) для каждого испытанного образца рассчитывают по формуле
. (4)
За показатель
горючести
исследуемого вещества (материала) принимают
среднее арифметическое значение показателей горючести, полученных при испытании
трех образцов.
Если
получено меньше или больше единицы, то для
получения достоверных результатов проводят три дополнительных испытания при
времени зажигания (
+ 10)
с и три испытания при времени зажигания (
- 10)
с. За окончательный результат принимают максимальное значение
,
полученное при времени зажигания
, (
+ 10)
и (
- 10)
с.
По величине
показателя горючести материалы классифицируются:
трудногорючие
<= 1,
горючие
> 1,
горючие
трудновоспламеняющиеся 1 <=
<= 2,5.
Условия и
результаты испытаний регистрируют в протоколе испытаний.
4.2.2.4. Требования
безопасности
Прибор КТ следует
установить в вытяжном шкафу. Рабочее место оператора должно удовлетворять
санитарно-гигиеническим требованиям ГОСТ 12.1.005-88.
(в ред. Изменения N 2, утв.
Постановлением Госстандарта СССР от 23.03.1989 N 608)
4.2.3. Метод
трубчатой электропечи для определения группы негорючих веществ и материалов
4.2.3.1.
Определение группы негорючих веществ и материалов осуществляется по методу,
изложенному в СТ СЭВ 382-76.
4.3. Метод экспериментального определения температуры вспышки
жидкостей в закрытом тигле
4.3.1. Аппаратура
Аппарат для
определения температуры вспышки нефтепродуктов и продуктов химических
органических в закрытом тигле по ГОСТ 1421-79.
Термометры типов ТН
1-1, ТН 1-2, ТН-6 по ГОСТ 400-80.
Секундомер по ГОСТ
5072-79, класс точности 3.
Барометр мембранный
метеорологический по ГОСТ 23696-79.
Камера холодильная
или охлаждающие смеси.
4.3.2. Проведение
испытаний
Перед проведением
испытаний устанавливают соответствие исследуемой жидкости паспортным данным по
внешнему виду, плотности, коэффициенту рефракции и температуре кипения входным
контролем согласно требованиям ГОСТ 24297-87.
(в ред. Изменения N 2, утв.
Постановлением Госстандарта СССР от 23.03.1989 N 608)
Образцы
легколетучих жидкостей с температурой кипения до 100 °C предварительно
охлаждают до 0 °C, вязких жидкостей - нагревают до текучести и проводят
испытание для оценки ориентировочной температуры вспышки, для чего образец
исследуемой жидкости наливают в тигель до метки. Тигель закрывают крышкой и
устанавливают в нагревательную ванну аппарата. В гнездо на крышке тигля
устанавливают термометр, выбранный в соответствии с температурой кипения
исследуемой жидкости. Подключают к электропитанию нагревательную ванну и
перемешивающее устройство, обеспечивая частоту вращения мешалки от 90 до
.
Зажигают газовую горелку аппарата и регулируют пламя таким образом, чтобы оно
имело форму шара диаметром от 3 до 4 мм. Нагревают образец исследуемой жидкости
со скоростью от 5 до 6 °C в мин, что обеспечивается регулятором скорости
нагрева и контролируется по секундомеру.
Через каждые 5 °C
повышения температуры проводят испытание на вспышку. В момент испытания на
вспышку перемешивание прекращают. Поворотом пружинного механизма открывают
заслонку и опускают пламя внутрь тигля на время от 1 до 2 с. Если при этом
произошла вспышка паров исследуемой жидкости, то нагревание образца прекращают
и показания термометра в момент появления вспышки принимают за температуру
вспышки. Если вспышка не произошла, то заслонку и газовую горелку возвращают в
исходное положение. Включают мешалку и продолжают нагревание образца.
Периодически опускают пламя газовой горелки внутрь тигля до получения вспышки.
Определив
ориентировочную температуру вспышки, проводят серию основных испытаний на трех
образцах исследуемой жидкости в той же последовательности, что предварительное
испытание. Образцы исследуемой жидкости, имеющей ориентировочную температуру
вспышки менее 50 °C, охлаждают до температуры, которая на 17 °C меньше
ориентировочной температуры вспышки. Нагревание образца за 10 °C до ориентировочной
температуры вспышки осуществляют со скоростью 1 °C в мин для жидкостей с
температурой вспышки до 104 °C и 2 °C в мин для жидкостей с температурой
вспышки свыше 104 °C.
Испытание на
вспышку проводят при повышении температуры на каждый 1 °C для жидкостей с
температурой вспышки до 104 °C и на каждые 2 °C для жидкостей с температурой
вспышки свыше 104 °C.
За температуру
вспышки каждого определения принимают показание термометра при появлении
пламени над частью или всей поверхностью образца.
4.3.3. Обработка
результатов
За температуру
вспышки исследуемой жидкости принимают среднее арифметическое трех определений
серии основных испытаний с поправкой на барометрическое давление.
Поправку
рассчитывают по формуле
, (5)
где P - фактическое
барометрическое давление, кПа.
Разность двух
последовательных результатов, полученных одним и тем же оператором при
постоянных условиях испытания с вероятностью 0,95, не должна быть более 3 °C
для температуры вспышки до 104 °C и 6 °C для температуры вспышки свыше 104 °C
при условии, что случайные погрешности преобладают над неисключенными
систематическими.
Условия и
результаты испытаний регистрируют в протоколе испытаний.
4.3.4. Требования
безопасности
Аппарат для
определения температуры вспышки следует устанавливать в вытяжном шкафу. Рабочее
место оператора должно удовлетворять санитарно-гигиеническим требованиям ГОСТ
12.1.005-88.
(в ред. Изменения N 2, утв.
Постановлением Госстандарта СССР от 23.03.1989 N 608)
4.4. Метод
экспериментального определения температуры вспышки жидкостей и твердых
плавящихся веществ в открытом тигле
4.4.1.
Аппаратура
Прибор ТВ (черт. 4)
состоит из фарфорового тигля низкой формы N 5 по ГОСТ 9147-80;
нагревательной
воздушной ванны, выполненной из стали, на дно которой уложена прокладка из
асбестового картона; сверху ванны помещают кольцо из паронита;
газовой горелки
диаметром сопла 1 мм;
подставки;
нагревательного
устройства, в качестве которого используют электрическую плитку, работающую от
электросети через автотрансформатор;
держателя
термометра, укрепленного на штативе.
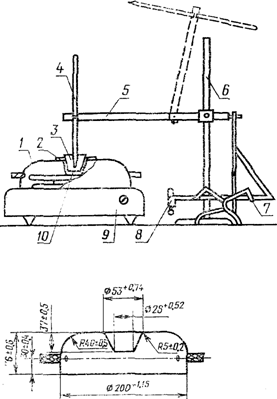
1 - нагревательная
ванна; 2 - кольцо из паронита;
3 - фарфоровый
тигель; 4 - термометр; 5 - держатель
термометра; 6 -
штатив; 7 - подставка для горелки;
8 - газовая
горелка; 9 - нагревательное устройство;
10 - асбестовая
прокладка
Черт. 4
Аппарат по ГОСТ
1369-79, применяемый для определения температур вспышки и воспламенения
нефтепродуктов в открытом тигле.
Секундомер по ГОСТ
5072-79, класс точности 3.
Барометр мембранный
метеорологический по ГОСТ 23696-79.
Термометры типа
ТЛ-2 1-А1 по ГОСТ 215-73 и типа ТН-2 по ГОСТ 400-80.
Экран
трехстворчатый, металлический, окрашенный с внутренней стороны черной краской,
каждая створка которого имеет ширину (500 +/- 10) мм, высоту (650 +/- 10) мм и
толщину 1 мм.
Холодильная камера
или охлаждающая смесь.
4.4.2.
Проведение испытаний
Перед проведением
испытаний устанавливают соответствие исследуемого вещества паспортным данным по
внешнему виду, плотности, коэффициенту рефракции, температуре кипения или
плавления входным контролем по ГОСТ 24297-87.
(в ред. Изменения N 2, утв.
Постановлением Госстандарта СССР от 23.03.1989 N 608)
Образцы
легколетучих жидкостей с температурой кипения до 100 °C предварительно
охлаждают до 0 °C, вязких жидкостей - нагревают до текучести. Проводят
испытание для оценки ориентировочной температуры вспышки, для чего образец
исследуемого вещества помещают в тигель до уровня на 12 мм ниже края тигля (до
указателя уровня в аппарате по ГОСТ 1369-79). Тигель с образцом устанавливают в
нагревательную ванну прибора ТВ (аппарата по ГОСТ 1369-79). В держателе
укрепляют вертикально термометр с таким расчетом, чтобы резервуар с ртутью
находился в центре тигля на равном расстоянии от дна тигля и поверхности
образца (в аппарате по ГОСТ 1369-79 термометр устанавливают посередине между
центром и стенкой тигля на расстоянии 6 мм от дна тигля). Положение термометра
и уровень заполнения тигля исследуемым веществом в приборе ТВ контролируют шаблонами.
Зажигают газовую горелку и регулируют длину пламени от 4 до 5 мм.
Для защиты от
движения воздуха прибор с трех сторон окружают экраном. Нагревают образец
исследуемого вещества со скоростью от 5 до 6 °C в мин, что обеспечивается
регулятором скорости нагрева и контролируется по секундомеру. Через каждые 5 °C
повышения температуры проводят испытание на вспышку. Для чего пламя газовой
горелки проносят от одной стороны тигля до другой в течение (1,5 +/- 0,5) с на
расстоянии (14 +/- 1) мм от поверхности исследуемого вещества. Если при этом
наблюдалась вспышка паров исследуемого вещества, то нагревание образца
прекращают и показание термометра в момент появления вспышки принимают за
температуру вспышки. Если вспышка не произошла, то нагревание образца продолжают,
периодически повторяя испытание на вспышку.
Определив
ориентировочную температуру вспышки, проводят серию основных испытаний на трех
образцах исследуемого вещества в той же последовательности, что и
предварительное испытание. Образцы исследуемого вещества, имеющие
ориентировочную температуру вспышки менее 50 °C, охлаждают до температуры,
которая на 17 °C меньше ориентировочной температуры вспышки. Нагревание образца
за 10 °C до ориентировочной температуры вспышки осуществляют со скоростью 1 °C
в мин для веществ с температурой вспышки до 70 °C и 2 °C в мин для веществ с
температурой вспышки более 70 °C.
Испытание на
вспышку проводят при повышении температуры на каждый 1 °C для веществ с
температурой вспышки до 70 °C и на каждые 2 °C для веществ с температурой
вспышки более 70 °C.
За температуру
вспышки каждого определения принимают показание термометра при появлении
пламени над частью или всей поверхностью образца.
4.4.3. Обработка
результатов
За температуру
вспышки исследуемого вещества принимают среднее арифметическое трех определений
серии основных испытаний с поправкой на барометрическое давление. Поправку
рассчитывают по формуле (5).
Разность между
двумя последовательными результатами, полученными одним и тем же оператором при
постоянных условиях испытаний с вероятностью 0,95, не должна быть более 5 °C на
приборе ТВ и 8 °C - на аппарате по ГОСТ 1369-79 при условии, что случайные
погрешности преобладают над неисключенными систематическими.
Условия и
результаты испытаний регистрируют в протоколе испытаний.
4.4.4. Требования
безопасности
Прибор для
определения температуры вспышки следует устанавливать в вытяжном шкафу. Рабочее
место оператора должно удовлетворять требованиям электробезопасности по ГОСТ
12.1.019-79 и санитарно-гигиеническим требованиям по ГОСТ 12.1.005-88.
(в ред. Изменения N 2, утв.
Постановлением Госстандарта СССР от 23.03.1989 N 608)
4.5. Методы расчета температуры вспышки
4.5.1. Методы
расчета температуры вспышки индивидуальных жидких веществ в закрытом тигле
4.5.1.1.
Температуру вспышки веществ
,
имеющих нижеперечисленные структурные группы (табл. 3), в градусах Цельсия
рассчитывают по формуле
, (6)
где
- размерный коэффициент, равный минус 73,14
°C;
- безразмерный коэффициент, равный 0,659;
- температура кипения исследуемой жидкости,
°C;
- число структурных групп вида j в молекуле;
- эмпирические коэффициенты, приведенные в
табл. 3.
Таблица 3
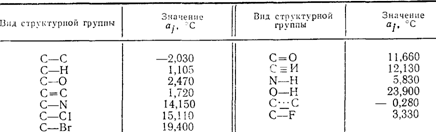
Средняя
квадратическая погрешность расчета
по формуле (6) составляет от 9 до 13 °C.
4.5.1.2. Более
точно температуру вспышки нижеперечисленных классов веществ рассчитывают по
формуле
, (7)
где a, b -
эмпирические коэффициенты, приведенные в табл. 4 вместе со средними
квадратическими погрешностями расчета.
Таблица 4
────────────────────────────┬─────────────────────────┬───────────
Класс веществ │ Коэффициенты │дельта, °C
├─────────────┬───────────┤
│ a, °C
│ b │
────────────────────────────┼─────────────┼───────────┼───────────
Алканы │ 10,59
│ 0,693 │
1,5
Спирты │ 53,37
│ 0,652 │
1,4
Алкиланилины │ 105,55
│ 0,533 │
2,0
Карбоновые
кислоты │ 36,15
│ 0,708 │
2,2
Алкилфенолы │ 64,50
│ 0,623 │
1,4
Ароматические
углеводороды │ 23,63
│ 0,665 │
3,0
Альдегиды │ -23,71
│ 0,813 │
1,5
Бромалканы │ 41,90
│ 0,665 │
2,2
Кетоны │ 44,77
│ 0,643 │
1,9
Хлоралканы │ 45,04
│ 0,631 │
1,7
Алкилацетаты │ 22,43
│ 0,702 │
1,2
Моноамины │ 18,65
│ 0,698 │
2,7
4.5.1.3. Если
известна зависимость давления насыщенных паров веществ от температуры, то
температуру вспышки в градусах Цельсия рассчитывают по формуле
, (8)
где
- константа, принимаемая в общем случае равной
;
- парциальное давление пара исследуемого
вещества при температуре вспышки, кПа;
- коэффициент диффузии пара в воздух,
;
- стехиометрический коэффициент кислорода в
реакции горения.
Средние
квадратические погрешности расчета температуры вспышки по формуле (8) для
веществ различных классов приведены в табл. 5.
Таблица 5
─────────────────────────────────────────────┬────────────────────
Класс веществ │ дельта, °C
─────────────────────────────────────────────┼────────────────────
Вещества,
состоящие из атомов C, H, O, N
│ 13
Галоидсодержащие
вещества │ 13
Фосфорорганические
вещества │ 10
4.5.2. Методы
расчета температуры вспышки индивидуальных веществ в открытом тигле
4.5.2.1.
Температуру вспышки в открытом тигле рассчитывают по формуле (6), используя
величины эмпирических коэффициентов
из табл. 6.
Таблица 6
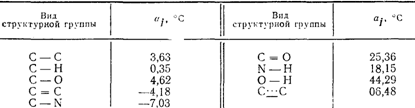
Коэффициенты
и
для расчета температуры вспышки в открытом
тигле соответственно равны минус 73,00 °C и 0,409.
Средняя
квадратическая погрешность расчета составляет 10 °C.
4.5.2.2. Если
известна зависимость давления насыщенных паров от температуры, то температуру
вспышки в открытом тигле рассчитывают по формуле (8), где
.
Средняя квадратическая погрешность расчета составляет 13 °C.
4.5.3. Методы
расчета температуры вспышки смесей горючих жидкостей в закрытом тигле
4.5.3.1.
Температуру вспышки смесей горючих жидкостей
в градусах Цельсия рассчитывают по формуле
, (9)
где
- мольная доля i-того компонента в жидкой
фазе;
- мольная теплота испарения i-того компонента;
- температура вспышки i-того компонента, °C;
R - универсальная
газовая постоянная.
Величина
может быть рассчитана по интерполяционной
формуле
, (10)
где
- температура кипения i-того компонента, °C.
Средняя
квадратическая погрешность расчета по формуле (10) составляет 9 °C.
4.5.3.2. Если
известна зависимость давления насыщенных паров от температуры для каждого из
компонентов, то температуру вспышки смеси
в градусах Цельсия рассчитывают по формуле
, (11)
где
;
;
;
,
- константы уравнения Антуана для i-того
компонента.
Средняя
квадратическая погрешность расчета составляет 11 °C.
4.5.3.3.
Температуру вспышки бинарных смесей жидкостей
,
принадлежащих одному гомологическому ряду, в градусах Цельсия рассчитывают по
формуле
, (12)
где
- температура вспышки легкокипящего
компонента, °C;
- гомологическая разность по температуре
вспышки в рассматриваемом ряду, °C;
x - массовая доля
высококипящего компонента в жидкой фазе;
m - разность между
числом углеродных атомов компонентов смеси;
x' - коэффициент,
учитывающий нелинейный характер зависимости
от x. При x >= 0,5 x' = 2x - 1, при x <
0,5 x' = 0.
Формула (12)
применима для гомологических рядов н-спиртов и сложных эфиров нормального
строения.
Средняя
квадратическая погрешность расчета составляет 2 °C.
4.6. Метод экспериментального определения температуры воспламенения
жидкостей и твердых плавящихся веществ
4.6.1. Аппаратура
Температуру
воспламенения определяют в приборах, применяемых для определения температуры
вспышки в открытом тигле (см. п. 4.4.1). К тиглю прибора ТВ дополнительно
прилагается крышка с отверстием в виде сектора, составляющим 25 - 35%
поверхности крышки.
4.6.2. Проведение
испытаний
Перед проведением
испытаний устанавливают соответствие исследуемого вещества паспортным данным по
внешнему виду, плотности, коэффициенту рефракции, температуре кипения или
плавления входным контролем по ГОСТ 24297-87.
(в ред. Изменения N 2, утв.
Постановлением Госстандарта СССР от 23.03.1989 N 608)
Образцы
легколетучих жидкостей с температурой кипения до 100 °C предварительно
охлаждают до 0 °C, вязких жидкостей нагревают до текучести. Проводят испытание
для оценки ориентировочной температуры воспламенения. Для чего образец
исследуемого вещества помещают в тигель до уровня на 12 мм ниже края тигля (до
указателя уровня в аппарате по ГОСТ 1369-79). Тигель устанавливают в
нагревательную ванну, закрепляют термометр, зажигают газовую горелку, окружают
прибор защитным экраном как указано в п. 4.4.2. Определение температуры
воспламенения может существовать как самостоятельный метод или осуществляться
после определения
на том же образце.
Нагревают образец
исследуемого вещества со скоростью от 5 до 6 °C в мин, что обеспечивается
регулятором скорости нагрева и контролируется по секундомеру. Через каждые 5 °C
повышения температуры проводят испытание на воспламенение. Для этого пламя
горелки проносят от одной стороны тигля до другой в течение (1,5 +/- 0,5) с на
расстоянии (14 +/- 1) мм от поверхности исследуемого вещества. Если при этом
пары исследуемого вещества воспламеняются и продолжают гореть не менее 5 с
(определяют по секундомеру), то нагревание образца прекращают, термометр
выводят из зоны горения и показание термометра в момент появления воспламенения
принимают за температуру воспламенения. Если воспламенение паров исследуемого
вещества не произошло или время самостоятельного горения после воспламенения
паров составляло менее 5 с, то нагревание образца продолжают. Периодически
проносят пламя горелки над тиглем, повторяя испытание на воспламенение.
Определив
ориентировочную температуру воспламенения, проводят серию основных испытаний на
трех образцах исследуемого вещества. При этом нагревание образца за 10 °C до
ориентировочной температуры воспламенения осуществляют со скоростью 1 °C в мин
для веществ с температурой воспламенения до 70 °C и 2 °C в мин для веществ с
температурой воспламенения более 70 °C.
Зажигание пламенем
газовой горелки проводят при повышении температуры на каждый 1 °C для веществ с
температурой воспламенения до 70 °C и на каждые 2 °C для веществ с температурой
воспламенения более 70 °C.
При определении
температуры воспламенения веществ, горючесть которых близка к границе,
разделяющей горючие и трудногорючие вещества, на приборе ТВ используют крышку с
отверстием. Пламя газовой горелки в этом случае проносят над отверстием в
крышке на расстоянии (14 +/- 1) мм от поверхности исследуемого вещества.
За температуру
воспламенения каждого испытания принимают наименьшую температуру образца, при
которой образующиеся пары воспламеняются при поднесении пламени газовой горелки
и продолжают гореть не менее 5 с после его удаления.
4.6.3. Обработка
результатов
За температуру
воспламенения исследуемого вещества принимают среднее арифметическое трех
определений серии основных испытаний с поправкой на барометрическое давление.
Поправку рассчитывают по формуле (5).
Разность двух
последовательных результатов, полученных одним и тем же оператором при
постоянных условиях испытания с вероятностью 0,95, не должна быть более 6 °C в
приборе ТВ и 8 °C в аппарате по ГОСТ 1369-79 при условии, что случайные
погрешности преобладают над неисключенными систематическими.
Условия и
результаты испытаний регистрируют в протоколе испытаний.
4.6.4. Требования
безопасности
Прибор для
определения температуры воспламенения следует устанавливать в вытяжном шкафу.
Рабочее место оператора должно удовлетворять требованиям электробезопасности по
ГОСТ 12.1.019-79 и санитарно-гигиеническим требованиям по ГОСТ 12.1.005-88.
(в ред. Изменения N 2, утв.
Постановлением Госстандарта СССР от 23.03.1989 N 608)
4.7. Метод
экспериментального определения температуры воспламенения твердых веществ и
материалов
4.7.1.
Аппаратура
Прибор (черт. 5)
состоит из вертикальной электропечи с двумя коаксиально расположенными
цилиндрами, выполненными из кварцевого стекла по ГОСТ 8680-73. Цилиндр
внутренним диаметром (80 +/- 5) мм, высотой (240 +/- 10) мм, толщиной стенки
(3,5 +/- 0,9) мм является рабочей камерой; второй цилиндр имеет внутренний
диаметр (110 +/- 5) мм. На цилиндры навиты спиральные электронагреватели общей
мощностью не менее 2 кВт, что позволяет создавать температуру в рабочей камере
(750 +/- 5) °C. Электронагреватели изготовлены из проволоки марки Х20Н80-Н по
ГОСТ 12766.1-77 диаметром 0,7 мм. Сопротивление спирали внутреннего
электронагревателя (40 +/- 3) Ом, внешнего - (50 +/- 5) Ом. Спирали навиты на
стеклянные цилиндры с определенным шагом, позволяющим поддерживать равномерное
температурное поле в рабочей камере на участке длиной (100 +/- 5) мм. Кожух
электропечи и экран выполнены из стали 12Х18Н9Т по ГОСТ 5632-72;
держателя и
контейнера для крепления образца, изготовленных из жаростойкой стали по ГОСТ
5632-72. Контейнер диаметром (48 +/- 1) мм и высотой (10 +/- 2) мм
устанавливают в кольцо держателя диаметром (50 +/- 1) мм;
газовой горелки с
электроприводом. Газовая горелка представляет собой запаянную трубку внутренним
диаметром (4 +/- 1) мм из жаростойкой стали; на боковой поверхности трубки на
расстоянии (3,0 +/- 0,5) мм от запаянного конца имеется отверстие диаметром
(0,8 +/- 0,1) мм. Периодичность подвода горелки в фиксированную точку, которая
находится на расстоянии (10 +/- 1) мм от поверхности образца, составляет (10 +/-
2) с. Электропривод состоит из кривошипного механизма и электродвигателя типа
РД-09А с частотой вращения
;
эжектора с
заслонкой, выполненного из стали 12Х18Н9Т по ГОСТ 5632-72, внутренним диаметром
верхней части (80 +/- 5) мм, нижней - (9 +/- 1) мм, длиной (500 +/- 5) мм.
Эжектор с заслонкой служит для подачи регулируемого от 0 до
потока воздуха, необходимого для создания
оптимальных условий воспламенения образца в рабочей камере.
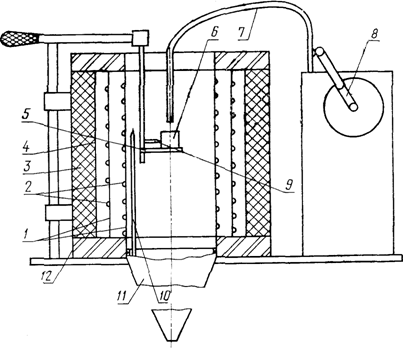
1 - стеклянные
цилиндры; 2 - спиральные электронагреватели;
3 -
теплоизоляционный материал; 4 - стальной экран;
5 - держатель
образца; 6 - стальной контейнер; 7 - газовая
горелка; 8 -
кривошипный механизм;
9, 10 - термоэлектрические
преобразователи;
11 - эжектор
Черт. 5
Термоэлектрические
преобразователи типа ТХА по ГОСТ 6616-74, поверхностные, обыкновенные,
среднеинерционные, диаметром термоэлектродов 0,5 мм.
Электронный
потенциометр типа КСП-4 с градуировкой
диапазоном измерения температур от 0 до 1000
°C, класс точности 0,5. В качестве исполнительных элементов в электрической
цепи между потенциометром и электронагревателями используют два реле, имеющих
четыре нормальнооткрытых и четырех нормальнозакрытых контакта, изготовленных по
нормативно-технической документации.
Ротаметр типа РМ по
ГОСТ 13045-81 с пределом измерения расхода газа до
.
Баллон газовый с
пропан-бутановой смесью вместимостью 5 дм3.
Секундомер по ГОСТ
5072-79, класс точности 3.
Весы лабораторные
общего назначения по ГОСТ 24104-88 с наибольшим пределом взвешивания 200 г,
класс точности 2.
(в ред. Изменения N 2, утв.
Постановлением Госстандарта СССР от 23.03.1989 N 608)
Зеркало для
наблюдения за образцом внутри реакционной камеры.
Микрокомпрессор с
подачей 32
.
4.7.2. Проведение
испытаний
Образцы должны
характеризовать средние свойства исследуемого вещества (материала).
Для испытаний готовят
не менее десяти образцов массой (3,0 +/- 0,1) г. Сыпучие и гранулированные
образцы массой (3,0 +/- 0,1) г помещают в контейнер, при этом плотность засыпки
должна соответствовать насыпной плотности, с которой вещество (материал)
применяют на практике.
Подготовленные
образцы подвергают кондиционированию в соответствии с требованиями ГОСТ
12423-66.
Устанавливают
термоэлектрические преобразователи в фиксированные точки рабочей камеры:
рабочий конец термоэлектрического преобразователя 9 располагают по центру
боковой поверхности образца, обеспечивая его надежный контакт с поверхностью
образца; рабочий конец термоэлектрического преобразователя 10, предназначенного
для контроля и регулировки температуры рабочей камеры, располагают на
расстоянии (10,0 +/- 0,5) мм от ее стенки и (130 +/- 5) мм от верхнего края
электропечи. Включают нагрев электропечи. При первом испытании температура в
рабочей камере должна быть равной температуре разложения исследуемого вещества
или (300 +/- 5) °C.
После установления
в рабочей камере стационарного температурного режима, определяемого по
постоянству показаний двух термоэлектрических преобразователей (расхождение
показаний которых не должно превышать 2,5%), держатель извлекают из рабочей
камеры, в контейнер помещают образец и возвращают держатель в исходное
положение. Зажигают факельное пламя горелки и, регулируя подачу газовоздушной
смеси, формируют пламя в виде клина длиной от 8 до 10 мм (цвет пламени -
голубой). Электропривод горелки включают в заданный режим работы. Наблюдают за
образцом в рабочей камере с помощью зеркала.
Если при заданной
температуре образец воспламенится, испытание прекращают, горелку останавливают
в положении "вне печи", держатель с образцом извлекают из камеры.
Отмечают в протоколе испытания температуру воспламенения и следующее испытание
проводят с новым образцом при меньшей температуре (например, на 50 °C меньше).
Если в течение (20
+/- 1) мин образец не воспламенится, испытания прекращают и в протоколе
отмечают отказ.
Методом
последовательных приближений определяют минимальную температуру рабочей камеры,
при которой за время не более 20 мин образец воспламеняется от воздействия
источника зажигания и горит более 5 с после его удаления, а при температуре на
10 °C меньше наблюдается отказ не менее чем для двух образцов.
Если вещество имеет
низкую скорость газификации при нагреве, то полученное значение температуры
воспламенения уточняют, проводя дополнительные испытания с меньшим расходом
воздуха.
4.7.3. Обработка
результатов
За температуру
воспламенения исследуемого вещества (материала) принимают среднее
арифметическое двух температур, отличающихся друг от друга не более чем на 10
°C, при одной из которых наблюдается воспламенение двух образцов, а при другой
- два отказа.
Разность двух
последовательных результатов, полученных одним и тем же оператором при
постоянных условиях испытания с вероятностью 0,95, не должна быть более 5 °C
при условии, что случайные погрешности преобладают над неисключенными
систематическими.
Условия и
результаты испытаний регистрируют в протоколе испытаний.
4.7.4. Требования
безопасности
Прибор для
определения температуры воспламенения следует устанавливать в вытяжном шкафу.
Рабочее место оператора должно удовлетворять требованиям электробезопасности по
ГОСТ 12.1.019-79 и санитарно-гигиеническим требованиям по ГОСТ 12.1.005-88.
(в ред. Изменения N 2, утв.
Постановлением Госстандарта СССР от 23.03.1989 N 608)
4.8. Методы расчета температуры воспламенения индивидуальных жидких
веществ
4.8.1. Температуру
воспламенения веществ, имеющих структурные группы, приведенные в табл. 7,
рассчитывают по формуле (6) с использованием эмпирических коэффициентов табл.
7.
Таблица 7
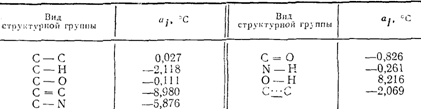
Коэффициенты
и
соответственно равны минус 47,787 °C и 0,8818.
Средняя
квадратическая погрешность расчета температуры воспламенения по формуле (6) составляет
5 °С.
4.8.2. В случае,
если известна зависимость давления насыщенных паров вещества от температуры, то
температуру воспламенения рассчитывают по формуле (8), где
(для фосфорорганических соединений
).
Средняя
квадратическая погрешность расчета температуры воспламенения по формуле (8)
составляет 6 °C.
4.8.3. Температуру
воспламенения
алифатических спиртов и сложных эфиров в
градусах Цельсия рассчитывают по формуле
, (13)
где
- температура кипения вещества, °C;
K - эмпирический
коэффициент, составляющий
для спиртов и
для сложных эфиров.
Средняя
квадратическая погрешность расчета температуры воспламенения по формуле (13)
составляет 2 °C для спиртов и 4 °C для сложных эфиров.
4.9. Метод экспериментального определения температуры
самовоспламенения газов, жидкостей и твердых плавящихся веществ
4.9.1. Аппаратура
Прибор (черт. 6)
состоит из реакционного сосуда, представляющего собой коническую колбу типа
Кн-250 ТС по ГОСТ 25336-82. Если температура самовоспламенения испытуемого
образца превышает температуру размягчения стекла колбы, допускается применять
аналогичные колбы из кварца или термостойкой нержавеющей стали;
термостата,
имеющего высоту рабочего пространства (230 +/- 5) мм, длину (200 +/- 5) мм,
ширину (170 +/- 5) мм. Термостат позволяет поддерживать постоянную температуру
от 50 до 600 °C. Внутри камеры термостата на одной из боковых стенок расположен
нагреватель мощностью (1,5 +/- 0,1) кВт, представляющий собой спираль из
проволоки марки Х20Н80-Н по ГОСТ 12766.1-77, закрепленную на фарфоровых
изоляторах вокруг крыльчатки вентилятора мощностью не более 100 Вт.
Равномерность нагрева поверхности реакционного сосуда достигается за счет циркуляции
воздуха в термостате с помощью вентилятора и применения регулятора температуры,
позволяющего плавно изменять подводимую к нагревателю энергию;
четырех
термоэлектрических преобразователей типа ТХА по ГОСТ 6616-74 поверхностных,
обыкновенных, среднеинерционных, диаметром термоэлектродов 0,5 мм.
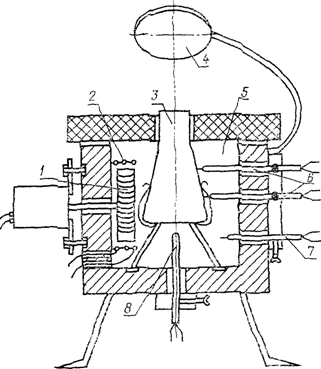
1 - крыльчатка
вентилятора; 2 - спиральный нагреватель;
3 - реакционный
сосуд; 4 - смотровое зеркало;
5 - термостат; 6,
7, 8 - термоэлектрические преобразователи
Черт. 6
Регулятор
температуры типа ВРТ-3, работающий в диапазоне температур от 50 до 800 °C.
Потенциометр
многоточечный с градуировкой
,
диапазоном измерения температур от 50 до 800 °C, класс точности 0,5.
Смотровое зеркало
для наблюдения за образцом внутри реакционного сосуда.
Набор мерных
пипеток 2-го класса по ГОСТ 20292-74 вместимостью от 0,1 до 2 см3 для дозировки
испытуемых веществ и введения их в реакционный сосуд.
Пылесос для
продувки реакционного сосуда (допускается продувка сжатым воздухом).
Весы лабораторные
общего назначения по ГОСТ 24104-88 с наибольшим пределом взвешивания 200 г,
класс точности 2.
(в ред. Изменения N 2, утв.
Постановлением Госстандарта СССР от 23.03.1989 N 608)
Секундомер по ГОСТ
5072-79, класс точности 3.
4.9.2. Проведение
испытаний
Устанавливают
входным контролем по ГОСТ 24297-80 соответствие исследуемого вещества
паспортным данным: газы - хроматографическим анализом, жидкости - по внешнему
виду, плотности, коэффициенту рефракции и температуре кипения, а плавящиеся
твердые вещества - по температуре плавления.
Перед испытанием
вязкие вещества нагревают, а вещества с температурой кипения, равной или ниже
комнатной температуры, охлаждают до температур, при которых можно легко набрать
в пипетку или шприц требуемое количество исследуемого вещества. В этом случае
перед отбором пробы пипетку или шприц также нагревают или охлаждают. При
исследовании пыли и твердых веществ готовят несколько навесок, отличающихся
друг от друга на 0,05 г. Для газов используют герметичный калиброванный
стеклянный шприц вместимостью 200 см3 и трехходовой кран с пламепреградителем
(черт. 7).
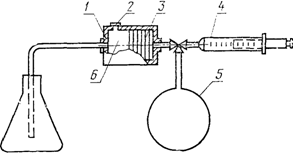
1 -
пламепреградитель; 2 - предохранительная мембрана;
3 - пластинки из
спеченного стекла (перегородки);
4 - герметичный
шприц; 5 - резервуар с газом;
6 - предкамера
Черт. 7
Устанавливают два
термоэлектрических преобразователя 6 к боковой поверхности реакционного сосуда
на расстоянии 25 и 55 мм от нижней части горла реакционного сосуда и один
термоэлектрический преобразователь 8 к дну колбы с таким расчетом, чтобы
рабочие концы термоэлектрических преобразователей были плотно прижаты к поверхности
реакционного сосуда. Четвертый термоэлектрический преобразователь 7
устанавливают в воздушном пространстве термостата, подсоединив его холодные
концы к регулятору температуры.
Определение
температуры самовоспламенения состоит из предварительных и основных испытаний.
В серии предварительных испытаний определяют наиболее легко
самовоспламеняющееся количество вещества, вводимого в реакционный сосуд. В
серии основных испытаний выявляют наименьшую температуру реакционного сосуда,
при которой наблюдается самовоспламенение наиболее легко самовоспламеняющегося
количества вещества.
При проведении
предварительных испытаний в нагретый до предполагаемой температуры
самовоспламенения (или до 300 °C при первом испытании) реакционный сосуд вводят
небольшое количество исследуемого вещества, например, 0,5 см3 (0,5 г). Включают
секундомер и с помощью зеркала наблюдают за веществом в сосуде. При появлении
пламени секундомер останавливают и считают, что произошло самовоспламенение.
Если пламя не появилось за время не более 5 мин, то испытание прекращают,
считая, что самовоспламенение не произошло и наблюдался отказ. После проведения
испытания продувают реакционный сосуд воздухом. Изменяя температуру
реакционного сосуда, повторяют испытания на самовоспламенение с таким же
количеством вещества до тех пор, пока не найдут такую минимальную температуру,
при которой происходит самовоспламенение данного количества вещества, а при
температуре на 5 °C меньше минимальной наблюдается отказ. Найденную минимальную
температуру принимают за температуру самовоспламенения данного количества
вещества в серии предварительных испытаний.
Таким же образом
находят температуру самовоспламенения шести-восьми проб исследуемого вещества,
отличающихся друг от друга на 0,05 - 0,2 см3 (г), и строят график зависимости
температуры самовоспламенения от величины пробы вещества. Если построенная
кривая не имеет минимума, то дополнительно определяют температуры
самовоспламенения нескольких проб для построения восходящей ветви кривой,
учитывая, что искомая кривая обычно имеет вид параболы. Величину пробы,
соответствующую минимуму полученной кривой, принимают за наиболее легко
самовоспламеняющееся количество вещества.
В серии основных
испытаний проводят пять испытаний на самовоспламенение с наиболее легко самовоспламеняющимся
количеством вещества при температуре на 5 °C ниже минимальной температуры
самовоспламенения, полученной в серии предварительных испытаний.
Если ни при одном
из пяти испытаний вещество не самовоспламенится, то температуру повышают на 5
°C и проводят вторую серию из пяти испытаний на самовоспламенение с таким же
количеством вещества. При получении во второй серии не менее двух испытаний с
самовоспламенением определение температуры самовоспламенения испытуемого
вещества считают выполненным.
Если в первой серии
из пяти испытаний получено хотя бы одно самовоспламенение, то температуру
реакционного сосуда снижают на 5 °C и вновь проводят пять испытаний на
самовоспламенение с таким же количеством вещества. Эту операцию повторяют до
тех пор, пока не будут получены пять отказов.
4.9.3. Обработка
результатов
За температуру
самовоспламенения исследуемого вещества принимают среднее арифметическое двух
температур, отличающихся друг от друга на 5 °C, при одной из которых
наблюдается самовоспламенение наиболее легко самовоспламеняющегося количества
вещества, а при другой - отказ.
Разность двух
последовательных результатов, полученных одним и тем же оператором при
постоянных условиях испытания с вероятностью 0,95, не должна превышать 5 °C при
условии, что случайные погрешности преобладают над неисключенными
систематическими.
Условия и
результаты испытаний регистрируют в протоколе испытаний.
4.9.4. Требования
безопасности
Прибор для
определения температуры самовоспламенения следует устанавливать в вытяжном шкафу.
При испытании токсичных веществ или веществ, выделяющих при горении и
термическом разложении токсичные пары и газы, скорость движения воздуха в
открытом проеме вытяжного шкафа должна быть не менее
.
Рабочее место оператора должно удовлетворять требованиям электробезопасности по
ГОСТ 12.1.019-79 и санитарно-гигиеническим требованиям по ГОСТ 12.1.005-88.
(в ред. Изменения N 2, утв.
Постановлением Госстандарта СССР от 23.03.1989 N 608)
4.10. Метод экспериментального определения температуры
самовоспламенения твердых веществ и материалов
4.10.1. Аппаратура
Аппаратура для
определения температуры самовоспламенения твердых веществ и материалов - по п.
4.7.1.
4.10.2. Проведение
испытаний
Образцы должны
характеризовать средние свойства исследуемого вещества (материала). Для
испытаний готовят не менее десяти образцов массой (3,0 +/- 0,1) г. Сыпучие и
гранулированные вещества массой (3,0 +/- 0,1) г помещают в контейнер, при этом
плотность засыпки должна соответствовать насыпной плотности, с которой вещество
применяют на практике.
Подготовленные
образцы подвергают кондиционированию в соответствии с требованиями ГОСТ
12423-66.
Устанавливают
термоэлектрические преобразователи в фиксированные точки рабочей камеры,
включают нагрев электропечи. При первом испытании температура
в рабочей камере должна быть равной
температуре разложения исследуемого вещества или (500 +/- 10) °C.
После установления
в рабочей камере стационарного температурного режима, определяемого по
постоянству показаний двух термоэлектрических преобразователей (расхождение
показаний которых не должно превышать 2,5%), держатель извлекают из рабочей
камеры, в контейнер помещают образец и возвращают держатель в исходное
положение. Наблюдают за образцом в рабочей камере с помощью смотрового зеркала.
Если образец
самовоспламенится, то регистрируют самовоспламенение при
.
Следующее испытание с новым образцом проводят при меньшей температуре
(например, на 50 °C). Если в течение 30 мин образец не самовоспламенится,
считают, что при температуре
получили отказ. Следующее испытание с новым
образцом проводят при большей температуре (например, на 50 °C). Изменяя
температуру в рабочей камере, определяют такую минимальную температуру, при
которой возникает пламенное горение образца при двукратном повторении
испытаний, а при температуре на 10 °C меньше наблюдаются два отказа.
4.10.3. Обработка
результатов
За температуру
самовоспламенения принимают среднее арифметическое двух температур,
отличающихся друг от друга не более чем на 10 °C, при одной из которых
наблюдается самовоспламенение двух образцов, а при другой - два отказа.
Разность двух
последовательных результатов, полученных одним и тем же оператором при
постоянных условиях испытания с вероятностью 0,95, не должна быть более 5 °C
при условии, что случайные погрешности преобладают над неисключенными
систематическими.
Условия и
результаты испытаний регистрируют в протоколе испытаний.
4.10.4. Требования
безопасности
Прибор для
определения температуры самовоспламенения следует устанавливать в вытяжном
шкафу. Рабочее место оператора должно удовлетворять требованиям
электробезопасности по ГОСТ 12.1.019-79 и санитарно-гигиеническим требованиям
по ГОСТ 12.1.005-88.
(в ред. Изменения N 2, утв.
Постановлением Госстандарта СССР от 23.03.1989 N 608)
4.11. Методы экспериментального определения концентрационных пределов
распространения пламени по газо-, паровоздушным смесям
4.11.1. Метод КП
4.11.1.1.
Аппаратура
Прибор КП-1 (черт.
8) состоит из реакционного сосуда-трубки из термостойкого химико-лабораторного
стекла внутренним диаметром от 50 до 55 мм, высотой (1500 +/- 100) мм, толщиной
стенки (2,0 +/- 0,5) мм. Нижняя часть сосуда закрывается пришлифованной
стеклянной пластинкой. В реакционный сосуд на расстоянии (100 +/- 10) мм от его
нижнего торца введены на шлифах электроды с наконечниками, изготовленными из
молибденовой проволоки диаметром 2 мм; разрядный промежуток электродов равен (8
+/- 2) мм. Подаваемое напряжение на электроды составляет (18 +/- 2)кВ,
выделяемая энергия искр на электродах при длительности разряда от 1 до 2 с
равна (35 +/- 5) Дж;
системы
циркуляционных трубок с кранами для вакуумирования реакционного сосуда,
сообщения его с атмосферой, подачи в него компонентов смеси по парциальным
давлениям, измеренным ртутным чашечным манометром;
высоковольтного
источника питания, с помощью которого на электродах образуется искровой разряд;
испарителя;
насоса-мешалки.
Термостатический
нагреватель любого типа для обогрева реакционного сосуда и трубопроводов при
проведении испытаний с легкоконденсируемыми парами жидкостей.
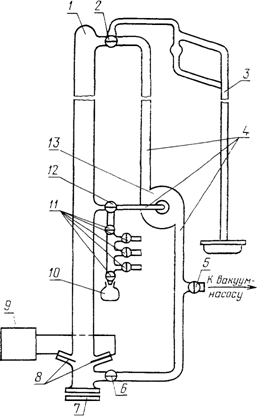
1 - реакционный
сосуд; 2, 5, 6, 11, 12 - краны; 3 - ртутный
манометр; 4 -
циркуляционные трубки; 7 - стеклянная
пластина; 8 -
электроды зажигания; 9 - высоковольтный
источник питания;
10 - испаритель; 13 - насос-мешалка
Черт. 8
4.11.1.2.
Проведение испытаний
Перед проведением
испытаний устанавливают соответствие исследуемого вещества паспортным данным
входным контролем согласно требованиям ГОСТ 24297-87.
(в ред. Изменения N 2, утв.
Постановлением Госстандарта СССР от 23.03.1989 N 608)
Перед проведением
испытаний прибор проверяют на герметичность, для чего закрывают нижнюю часть
реакционного сосуда пришлифованной стеклянной пластинкой, закрывают краны 11
(все остальные краны открыты). Сосуд вакуумируют до остаточного давления не
более 0,6 кПа и закрывают кран 5.
Если в течение 10
мин давление повысится не более чем на 0,3 кПа, прибор считается герметичным.
Работу прибора
проверяют по контрольному веществу - аммиаку жидкому синтетическому по ГОСТ
6221-82, нижний концентрационный предел которого должен быть равен (15,0 +/-
0,1)% об.
Предварительно
рассчитывают нижний и верхний концентрационные пределы распространения пламени
по газо-, паровоздушным смесям исследуемого
индивидуального вещества в процентах по формуле
, (14)
где
, (15)
,
,
,
,
,
- число атомов соответственно углерода, серы,
водорода, галоида, кислорода и фосфора в молекуле соединения;
,
- универсальные константы, значения которых
приведены в табл. 8.
Таблица 8
─────────────────────────┬─────────────────────┬──────────────────
Рассчитываемый предел │ a │ b
распространения пламени │ м │ м
─────────────────────────┼─────────────────────┼──────────────────
Нижний │ 8,684 │ 4,679
─────────────────────────┼─────────────────────┼──────────────────
Верхний │ │
при бета <= 7,5 │ 1,550 │ 0,560
при бета > 7,5 │ 0,768 │ 6,554
При определении
нижнего предела распространения пламени для первого испытания готовят газо-,
паровоздушную смесь, содержащую горючего газа (пара) вдвое меньше рассчитанного
предела, а при определении верхнего предела распространения пламени готовят
смесь, содержащую кислорода вдвое меньше, чем в смеси, соответствующей верхнему
пределу.
Для приготовления
газо-, паровоздушной смеси требуемого состава реакционный сосуд вакуумируют до
остаточного давления не более 0,6 кПа и затем поочередно подают в него
компоненты смеси по парциальным давлениям, открыв один из кранов 11, при закрытом
кране 5.
Парциальное
давление компонента
в килопаскалях рассчитывают по формуле
, (16)
где
- задаваемая концентрация компонента смеси, %
об.;
- атмосферное давление, кПа.
После впуска
компонентов смеси в реакционный сосуд закрывают краны 11, включают
насос-мешалку и перемешивают смесь в течение (4 +/- 1) мин. Затем закрывают
краны 2, 6, 12, снимают стеклянную пластинку 7 и зажигают смесь искрой за время
от 1 до 2 с. Результаты испытания оценивают визуально.
Если при первом
испытании смесь не воспламенилась или возникшее пламя не распространилось до
верхней части реакционного сосуда, то в каждом последующем испытании при
определении нижнего предела распространения пламени концентрацию исследуемого
вещества в смеси увеличивают не более чем на 10%, а при определении верхнего
предела уменьшают не более чем на 2%.
Если при первом
испытании наблюдается воспламенение с распространением пламени до верхней части
реакционного сосуда, то последующие испытания проводят соответственно с
уменьшенной (для нижнего предела) и увеличенной (для верхнего предела)
концентрацией исследуемого вещества в смеси.
После каждого
испытания прибор продувают воздухом для удаления газообразных продуктов горения
и охлаждения реакционного сосуда. Последующие испытания начинают после того,
как реакционный сосуд охладится до комнатной температуры.
4.11.1.3. Обработка
результатов
За предел
распространения пламени принимают среднее арифметическое шести ближайших
значений концентрации исследуемого вещества в смеси, при трех из которых
наблюдается воспламенение смеси с распространением пламени до верхней части
реакционного сосуда, а при других трех - отказ, т.е. смесь не воспламенилась
или возникшее пламя не распространилось до верхней части реакционного сосуда.
Разность двух
последовательных результатов, полученных одним и тем же оператором при
постоянных условиях испытания с вероятностью 0,95, не должна быть больше 0,1%
при условии, что случайные погрешности преобладают над неисключенными
систематическими.
Условия и
результаты испытаний регистрируют в протоколе испытаний.
4.11.1.4.
Требование безопасности
Прибор для
определения концентрационных пределов воспламенения газов и паров жидкостей
следует устанавливать в специальном шкафу, оборудованном вытяжной вентиляцией.
Рабочее место
оператора должно удовлетворять требованиям электробезопасности по ГОСТ
12.1.019-79 и санитарно-гигиеническим требованиям по ГОСТ 12.1.005-88.
(в ред. Изменения N 2, утв.
Постановлением Госстандарта СССР от 23.03.1989 N 608)
4.11.2. Метод,
применяемый для определения концентрационных пределов распространения пламени
по газо-, паровоздушным смесям галоидированных веществ
4.11.2.1.
Аппаратура
Установка
"Предел" (черт. 9) состоит из реакционного сосуда - цилиндра внутренним
диаметром (300 +/- 10) мм, высотой (800 +/- 30) мм, толщиной стенки не меньше 2
мм, изготовленного из стали 12Х18Н9Т по ГОСТ 5632-72. В верхней части
реакционного сосуда имеется герметично закрывающееся отверстие, которое служит
для продувки сосуда. Верхняя крышка выполнена из термостойкого стекла, через
которое с помощью зеркала ведут наблюдение за процессом распространения пламени
при испытании. Нижняя крышка выполнена из стали 12Х18Н9Т по ГОСТ 5632-72 и
перед зажиганием смеси открывается вручную с помощью коромысла и винта;
термоэлектрического
преобразователя типа ТХК по ГОСТ 6616-74 поверхностного, обыкновенного,
малоинерционного, диаметров проволоки 0,05 мм и милливольтметра с диапазоном
измерения температур от 200 до 1200 °C, предназначенных для обнаружения
слабосветящегося пламени;
зажигающего
устройства, в качестве которого используют электроды с разрядным промежутком от
5 до 7 мм, изготовленные из нержавеющей проволоки диаметром (3,0 +/- 0,3) мм.
Подаваемое напряжение на электроды составляет от 16 до 20 кВ. Выделяемая
энергия искр на электродах при длительности разряда от 1 до 2 с составляет от
30 до 40 Дж. Расстояние от верхней крышки сосуда до электродов равно (750 +/-
20) мм;
трубчатого
электронагревателя мощностью не менее 1 кВт. Нагреватель служит для
конвективного перемешивания смесей;
пакета сеток из
нержавеющей стали, содержащего от 2 до 3 слоев сеток с размером ячейки от 0,3
до 0,5 мм2. Расстояние между сетками в пакете составляет от 3 до 5 мм. Пакет
служит для предотвращения выброса пламени из реакционного сосуда;
концевого
выключателя, предотвращающего включение зажигающего устройства при закрытой
нижней крышке. Замыкание контактов концевого выключателя осуществляется нижней
крышкой реакционного сосуда при ее полном открытии;
трубопроводов с
клапанами для вакуумирования реакционного сосуда, сообщения его с атмосферой и
подачи в него компонентов смеси по парциальным давлениям, измеренным ртутным
манометром;
испарителя
вместимостью (500 +/- 10) см3, изготовленного из нержавеющей стали и рассчитанного
на давление до 7 МПа;
вакуумного насоса,
обеспечивающего остаточное давление не более 0,1 кПа;
высоковольтного
источника питания для зажигающего устройства.
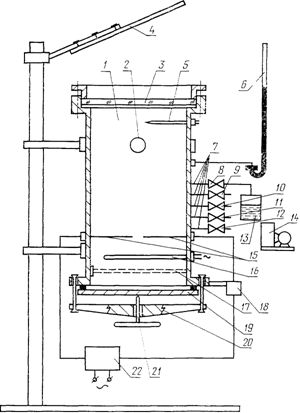
1 - реакционный
сосуд; 2 - отверстие для продувки;
3 - верхняя крышка;
4 - смотровое зеркало;
5 -
термоэлектрический преобразователь; 6 - ртутный
манометр; 7 -
трубопроводы; 8 - 12 - клапаны;
13 - испаритель; 14
- вакуумный насос; 15 - электроды
зажигания; 16 -
трубчатый электронагреватель;
17 - пакет сеток;
18 - концевой выключатель; 19 - нижняя
крышка; 20 -
коромысло; 21 - винт; 22 - высоковольтный
источник питания
Черт. 9
Термостатический
нагреватель любого типа для обогрева реакционного сосуда и трубопроводов при
проведении испытаний с легкоконденсируемыми парами жидкости.
4.11.2.2.
Проведение испытаний
Входным контролем
по ГОСТ 24297-87 устанавливают соответствие исследуемого вещества паспортным
данным.
(в ред. Изменения N 2, утв. Постановлением
Госстандарта СССР от 23.03.1989 N 608)
Перед испытанием
установку проверяют на герметичность, для чего закрывают нижнюю крышку
реакционного сосуда, отверстие для продувки 2 и все клапаны, кроме клапана 12.
Реакционный сосуд вакуумируют до остаточного давления 1,0 кПа и перекрывают
клапан 12. Если в течение 10 мин давление в сосуде повысится не более чем на
0,1 кПа, установка считается герметичной.
Работу установки
проверяют по контрольному веществу - пропану особой чистоты, нижний
концентрационный предел которого должен быть равен (2,05 +/- 0,15)% об.
Ориентировочные
пределы распространения пламени исследуемого индивидуального вещества
рассчитывают по формуле (14).
При определении
нижнего предела распространения пламени для первого испытания готовят газо-,
паровоздушную смесь, содержащую горячего газа вдвое меньше рассчитанного
предела, а при определении верхнего предела готовят смесь, содержащую кислорода
вдвое меньше, чем в смеси, соответствующей рассчитанному верхнему пределу.
Для приготовления
газо-, паровоздушной смеси требуемого состава реакционный сосуд вакуумируют до
остаточного давления (1,0 +/- 0,2) кПа и затем поочередно подают в него
компоненты смеси по парциальным давлениям. Парциальное давление компонента
рассчитывают по формуле (16).
После впуска
компонентов смеси в реакционный сосуд на трубчатый электронагреватель подают в
течение (30 +/- 5) с напряжение 60 В переменного тока. Перемешивание смеси
происходит за 5 - 7 мин во время охлаждения электронагревателя. При полном его
охлаждении давление в реакционном сосуде становится равным атмосферному.
Открывают нижнюю
крышку реакционного сосуда до упора с концевым выключателем, при этом контакты
концевого выключателя замыкаются и цепь зажигания оказывается подготовленной
для подачи искры.
Время с момента
открытия крышки до момента зажигания не должно быть более 3 с.
Результат испытания
на воспламенение оценивают визуально или с помощью термоэлектрического
преобразователя.
Если при первом
испытании смесь не воспламенилась или возникшее пламя не распространилось до
верхней части или стенок реакционного сосуда, то при каждом последующем
испытании при определении нижнего предела распространения пламени концентрацию
исследуемого вещества в смеси увеличивают не более чем на 10%, а при определении
верхнего предела уменьшают не более чем на 2%.
Если при первом
испытании смесь воспламенилась и возникшее пламя распространилось до верха или
стенок реакционного сосуда, то последующие испытания проводят соответственно с
уменьшенной (для нижнего предела) и увеличенной (для верхнего предела)
концентрацией исследуемого вещества в смеси.
После каждого
испытания реакционный сосуд продувают воздухом для удаления продуктов горения и
охлаждения стенок сосуда. Последующее испытание начинают после того, как
реакционный сосуд охладится до комнатной температуры.
4.11.2.3. Обработка
результатов
За предел
распространения пламени принимают среднее арифметическое шести ближайших
значений концентрации исследуемого вещества в смеси, при трех из которых
наблюдается воспламенение смеси, а при других трех - отказ.
Разность двух
последовательных результатов, полученных одним и тем же оператором при
постоянных условиях испытания с вероятностью 0,95, не должна быть более 0,1%
при условии, что случайные погрешности преобладают над неисключенными
систематическими.
Условия и
результаты испытаний регистрируют в протоколе испытаний.
4.11.2.4.
Требования безопасности
Установку для
определения пределов распространения пламени следует помещать в специальный
шкаф, оборудованный вытяжной вентиляцией.
Рабочее место
оператора должно удовлетворять требованиям электробезопасности по ГОСТ
12.1.019-79 и санитарно-гигиеническим требованиям по ГОСТ 12.1.005-88.
(в ред. Изменения N 2, утв.
Постановлением Госстандарта СССР от 23.03.1989 N 608)
4.12. Методы расчета концентрационных пределов распространения пламени
по газо-, паровоздушным смесям
4.12.1.
Методы расчета пределов распространения пламени индивидуальных веществ при
начальной температуре 25 °C
4.12.1.1. Метод
расчета нижнего предела распространения пламени
Нижний предел
в процентах рассчитывают по формулам:
(17)
или
, (18)
где
- коэффициент теплоты образования газа,
;
- стандартная теплота образования вещества в
газообразном состоянии при 25 °C,
;
,
- коэффициент соответственно j-того элемента и
s-той группы, влияющей на нижний предел распространения пламени;
,
- число атомов j-того элемента и число s-тых
структурных групп в молекуле вещества;
l, q -
соответственно число химических элементов и число типов структурных групп в
молекуле вещества, влияющих на нижний предел распространения пламени.
Значения
коэффициентов
,
, h и
формулы (17) приведены в табл. 9.
Таблица 9

Относительное
среднее квадратическое отклонение расчета
по формуле (17) составляет 9%.
Значения
коэффициентов
формулы (18) приведены в табл. 10.
Таблица 10
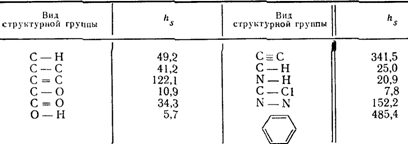
Относительное
среднее квадратическое отклонение расчета по формуле (18) составляет 9%.
Для
нижеперечисленных классов органических соединений нижний предел распространения
пламени рассчитывают с более высокой точностью по формуле (17) с коэффициентами
и
,
значения которых приведены в табл. 11.
Таблица 11
──────────────────┬────────────────────────┬───────┬──────────────
Класс соединений │ h │ h │ h
│ f │ s │ f
├────────┬───────┬───────┤ │ -1
│ h
│ h │
h │ │ моль x кДж
│ C
│ H │
O │ │
──────────────────┼────────┼───────┼───────┼───────┼──────────────
Углеводороды: │ │ │ │ │
алканы │ 3,919 │ 4,483 │ - │ 0
│ 0,0399
адкены │ 4,141 │ 4,727 │ -
│ 0 │
0,0419
Спирты │ 4,287 │ 4,889 │-0,522 │ 0
│ 0,0432
Ароматические │ 4,904 │ 5,569 │ -
│ 0 │
0,0489
углеводороды │ │ │ │ │
Относительное
среднее квадратическое отклонение расчета по формуле (17) с коэффициентами из
табл. 11 составляет 6%.
Примеры.
1. Рассчитать
диметилформамида
по формуле (17). Стандартная теплота
образования минус
.
Значения коэффициентов
и
берем из табл. 9.

Экспериментальное
значение
2,35% об. Относительная погрешность расчета
составляет 3,7%.
2. Рассчитать
о-ксилола по формуле (18). Из табл. 10 берем
значения коэффициентов
:


Экспериментальное
значение
1,0% об. Относительная погрешность расчета
составляет 3,8%.
4.12.1.2. Метод
расчета верхнего предела распространения пламени
Верхний предел
распространения пламени
в процентах расчитывают по формулам:
при
; (19)
при
. (20)
Коэффициент (K)
рассчитывают по формуле
, (21)
где q - число
различных структурных групп в молекуле вещества;
- коэффициент структурной группы;
- число атомов углерода в молекуле вещества;
- общее число полуторных, двойных и тройных
связей углерод-углерод в молекуле вещества;
- средняя кратность связей углерод-углерод в
молекуле вещества.
Значения
коэффициентов
приведены в табл. 12.
Таблица 12
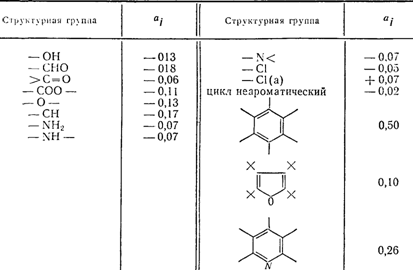
Примечание. Cl(a) -
атом хлора, соединенный с ароматическим циклом.
Относительное
среднее квадратическое отклонение расчета по формуле (19) составляет 16%, по
формуле (20) - 13%.
Пример. Рассчитать
кротонового альдегида по формуле (19).
Структурная формула альдегида
,
эмпирическая формула
.
;
;
;
.
Параметры
находим по табл. 12:
.
Рассчитываем
.

Экспериментальное
значение верхнего предела составляет 15,3% об.
Относительная
погрешность расчета 1,3%.
4.12.2. Метод
расчета пределов распространения пламени для смесей горючих веществ при
начальной температуре 25 °C
Метод
распространяется на вещества, не вступающие между собой в химическую реакцию
при начальной температуре. В число компонентов смеси может входить молекулярный
водород, объемная концентрация которого не должна превышать 75%.
Нижний (верхний)
предел распространения пламени для смеси
в процентах рассчитывают по формуле
, (22)
где
- концентрация k-того горючего компонента
смеси, % об.;
- предел распространения пламени k-того
горючего компонента, % об.;
n - число горючих
компонентов смеси.
В случае, если
какие-либо из величин
неизвестны, их рассчитывают по методам,
приведенным в п. 4.12.1.
Относительная
погрешность расчета не превышает 30%.
4.12.3. Методы
расчета пределов распространения пламени для смесей горячих веществ с негорючими
при начальной температуре 25 °C
Данные методы
расчета применяются в том случае, если компоненты смеси, состоящие из атомов C,
H, O, N, не вступают между собой в химическую реакцию при начальной температуре
и негорючими компонентами смеси являются двуокись углерода, избыточный азот и
водяной пар. В число горючих компонентов смеси может входить молекулярный
водород, объемная концентрация которого не должна превышать 75%.
4.12.3.1. Метод
расчета нижнего предела распространения пламени
Нижний предел распространения
пламени
в процентах рассчитывают по формуле
, (23)
где
- число молей воздуха, приходящихся на 1 моль
исходной смеси, рассчитывают по формуле
, (24)
где
- нижний предел распространения пламени k-того
горючего компонента, % об.;
- концентрация j-го негорючего компонента, %
об.;
- коэффициент j-го негорючего компонента;
m - число негорючих
компонентов смеси.
Значения
коэффициентов
приведены в табл. 13.
Таблица 13
─────────────────────────────────┬────────────────────────────────
Название вещества │ C
│ j
─────────────────────────────────┼────────────────────────────────
Азот │ 0,988
Двуокись
углерода │ 1,590
Водяной
пар │ 1,247
Относительная
погрешность расчета по формуле (23) не превышает 30%.
Пример. Рассчитать
смеси горючих веществ с негорючими. Состав
смеси, % об.: водород 6,3; окись углерода 5,25; метан 6,0; азот 72,45; двуокись
углерода 10,0.
Необходимые для
расчета данные по
в % об.: водорода 4,09; окиси углерода 12,5;
метана 5,28.
По формуле (24)
рассчитываем


.
По формуле (23)
рассчитываем


Экспериментальное
значение предела 34% об. Относительная погрешность расчета составляет 3,7%.
4.12.3.2. Метод
расчета верхнего предела распространения пламени
Метод применим для
смесей, в число компонентов которых не входит избыточный по отношению к воздуху
кислород.
Верхний предел
распространения пламени
для смеси в процентах рассчитывают по формуле
, (25)
где
- верхний предел распространения пламени
k-того горючего компонента, % об.;
- верхний условный предел распространения
пламени j-того негорючего компонента, % об.
Величину
для каждого негорючего компонента в процентах
рассчитывают по формуле
,
где
- минимальная флегматизирующая концентрация
негорючего (инертного) компонента, % об.;
- коэффициент флегматизации.
Минимальную
флегматизирующую концентрацию
каждого негорючего компонента в процентах
рассчитывают по формуле
, (27)
где
- коэффициент теплоты образования газа,
;
,
- свободные члены;
,
- коэффициенты атомов и структурных групп;
- число атомов вида j в молекуле горючего.
Значения
коэффициентов формулы (27) приведены в табл. 14.
Таблица 14
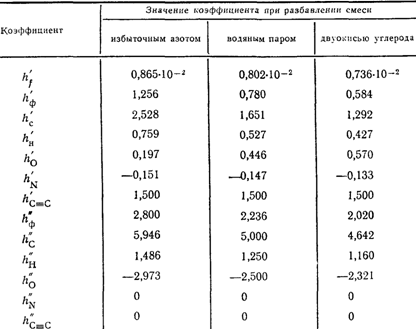
Величины
в килоджоулях на моль и
рассчитывают по формулам:
, (28)
, (29)
где
- стандартная теплота образования k-того
горючего компонента в газообразном состоянии,
;
- число атомов вида j в k-том горючем
компоненте.
Значение
коэффициента флегматизации
берут из табл. 15 в том случае, если среди
горючих компонентов смеси отсутствуют молекулярный водород и окись углерода. В
противном случае
рассчитывают по формуле (30) с использованием
данных из табл. 15
Таблица 15
─────────────────┬────────────────────────────────────────────────
Флегматизатор
│ K при флегматизации
│ ф
├───────────────┬───────────────┬────────────────
│ органических │ молекулярного │ окиси углерода
│ веществ
│ водорода │
─────────────────┼───────────────┼───────────────┼────────────────
Азот │ 0,100
│ 0,003 │
0,020
Двуокись
углерода│ 0,190 │
0,018 │ 0,096
Водяной
пар │ 0,160
│ - │ -
, (30)
где
- коэффициент флегматизации k-того горючего
компонента данным флегматизатором.
Пример.
Рассчитать
смеси. Состав смеси, % об.: водород 10,9;
метан 10,9; азот 78,2. Данные, необходимые для расчета: нижний и верхний
пределы распространения пламени водорода 4,09 и 72% об., метана 5,28 и 14% об.;
стандартная теплота образования метана минус
.
Рассчитываем
только горючей части смеси по формуле (28)

Рассчитываем
количество атомов каждого элемента, входящего в состав условной формулы по
формуле (29)
;
.
Рассчитываем
по формуле (27)


Коэффициент
флегматизации рассчитываем по формуле (30)
.
Рассчитываем
верхний условный предел распространения пламени для негорючего компонента по
формуле (26)

Рассчитываем
в смеси по формуле (25)

4.12.4. Метод
расчета пределов распространения пламени при начальных температурах, отличных
от 25 °C
Нижний предел
распространения пламени при температуре t в процентах рассчитывают по формуле
. (31)
Верхний предел
распространения пламени при температуре t в процентах рассчитывают по формуле
. (32)
Относительная
погрешность расчета
равна относительной погрешности расчета
,
приведенного в п. 4.12.1.
4.13. Метод
экспериментального определения нижнего концентрационного предела
распространения пламени по пылевоздушным смесям (НКПР)
4.13.1. Аппаратура
Установка (черт.
10) состоит из реакционного сосуда - цилиндра из стеклянной трубы по ГОСТ
8894-77 внутренним диаметром
мм, толщиной стенки (7 +/- 1) мм и высотой
(425 +/- 25) мм. Цилиндр имеет контрольную отметку на высоте 300 мм и закреплен
вертикально между двумя металлическими фланцами. Нижний фланец имеет
предохранительную мембрану, рассчитанную на давление (130 +/- 20) кПа;
системы распыления,
включающей расположенный у верхнего фланца распылитель, электромагнитный клапан,
клапаны, ресивер с манометром. Конструкции распылителей указаны на черт. 11,
12. Конусный распылитель (черт. 11) с эжекционной форсункой состоит из конуса,
служащего одновременно верхней крышкой реакционного сосуда, и форкамеры.
Форкамера состоит из корпуса и донышка, образующих внутреннюю сферу диаметром
(30 +/- 1) мм. Образец исследуемого вещества, помещенный на донышко форкамеры,
взвихривается при кратковременной подаче сжатого воздуха и через патрубок,
соединенный с конусом распылителя накидной гайкой, увлекается в реакционный
сосуд. Конус распылителя снабжен рассекателями, которые используются при
распылении вещества большой плотности. Другим типом распылителя, применяемого
для исследования металлических пылей, является распылитель с вихревой камерой и
распределительной решеткой, который содержит ввинченную в корпус камеры крышку
с соплом (черт. 12). В корпусе камеры напротив сопла имеется углубление для
образца исследуемого вещества. Камера представляет собой щель, которая
соединяет углубление в корпусе с выпускными отверстиями корпуса. Кожух связан с
корпусом резьбой. Донная часть кожуха выполнена в виде горизонтально
расположенной распределительной решетки. Величина кругового зазора между
распределительной решеткой и корпусом может регулироваться за счет резьбового
соединения кожуха с корпусом. Образец исследуемого вещества, помещенный в
углубление корпуса, взвихривается при кратковременной подаче сжатого газа через
сопло. Через выпускные отверстия частицы вещества выносятся на распределительную
решетку и затем в реакционный сосуд;
источника
зажигания. В качестве основного источника зажигания используют спираль из
проволоки марки Х20Н80-Н по ГОСТ 12766.1-77 диаметром 0,8 мм, длиной (900 +/-
10) мм. Внутренний диаметр спирали (8 +/- 1) мм, число витков 30, длина спирали
(50 +/- 1) мм. Напряжение, подаваемое на спираль, (36 +/- 2) В, мощность (470
+/- 10) Вт. Температура спирали при испытании (1050 +/- 50) °C. В качестве
контрольного источника зажигания используют пиротехнический воспламенитель ЭД-К3
марки НК-10/15. При отсутствии серийного воспламенителя пиротехнический
воспламенитель изготавливают на месте. Для этого алюминиевую пигментную пудру
ПАП-1 или ПАП-2 по ГОСТ 5494-71 смешивают с перекисью бария по ГОСТ 6054-75 в
соотношении 1:10. В качестве связующего используют раствор целлулоидного
коллоксилина в ацетоне по ГОСТ 2603-79. Общее количество коллоксилина в смеси
10%. Смесь наносят на проволоку по ГОСТ 12766.1-77 диаметром от 0,3 до 0,5 мм
до образования шарика диаметром 3 мм. Воспламенение осуществляется
электрическим током напряжением (90 +/- 10) В, подаваемым на пиротехнический
воспламенитель за время не более 0,3 с с момента начала распыления. Температура
пиротехнического воспламенителя около 2000 °C. Источник зажигания устанавливают
на расстоянии (150 +/- 5) мм от нижнего фланца;
блока управления,
обеспечивающего плавное или дискретное регулирование длительности импульсов
распыления в диапазоне от 0 до 0,5 с с точностью +/- 10% и синхронизацию
срабатывания источника зажигания с моментом окончания распыления.
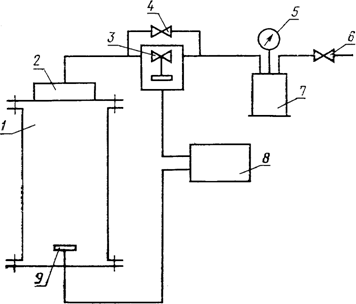
1 - реакционный
сосуд; 2 - распылитель;
3 -
электромагнитный клапан; 4, 6 - клапаны; 5 - манометр;
7 - ресивер; 8 -
блок управления; 9 - источник зажигания
Черт. 10
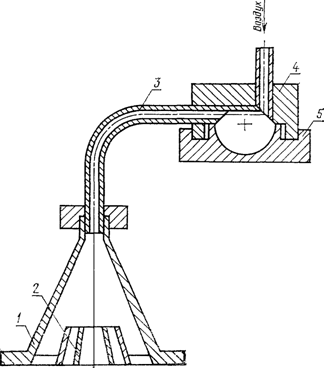
1 - корпус; 2 -
рассекатели; 3 - патрубок; 4 - корпус
форкамеры; 5 -
донышко
Черт. 11
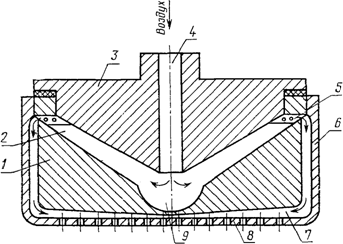
1 - корпус; 2 -
камера; 3 - крышка; 4 - сопло;
5 - выпускные
отверстия; 6 - кожух; 7 - круговой зазор;
8 -
распределительная решетка; 5 - углубление для навески
Черт. 12
Кольцевой
пробоотборник, состоящий из металлического плоского диска с установленным на
нем коаксиально относительно реакционного сосуда металлическим тонкостенным
стаканом высотой (150 +/- 2) мм, внутренним диаметром (50,5 +/- 0,5) мм.
Диаметр диска не меньше внешнего диаметра реакционного сосуда.
Весы лабораторные
общего назначения по ГОСТ 24104-88 с наибольшим пределом взвешивания 200 г,
класс точности 2.
(в ред. Изменения N 2, утв.
Постановлением Госстандарта СССР от 23.03.1989 N 608)
Сито вибрационное.
4.13.2. Проведение
испытаний
Перед проведением
испытаний устанавливают соответствие исследуемого вещества паспортным данным по
внешнему виду, влажности, зольности, дисперсности, а для плавящихся
органических веществ - дополнительно по температуре плавления входным контролем
по ГОСТ 24297-87. Проводят отсев частиц; при испытании используют пыли с
размером частиц менее 50 мкм для металлических веществ и менее 100 мкм для
других веществ.
(в ред. Изменения N 2, утв.
Постановлением Госстандарта СССР от 23.03.1989 N 608)
Проверяют
герметичность установки. Для этого открывают клапаны 4 и 6 и нагнетают в
систему воздух до давления не менее 100 кПа. Затем закрывают клапан 6 и
наблюдают по манометру 5 изменение давления. Если в течение 1 мин давление
изменится не более чем на 10 кПа, установку считают герметичной. Проверку
герметичности осуществляют ежедневно перед началом работы на установке.
Пригодность
установки к работе при ее освоении или замене ее сборочных единиц проверяют по
контрольному веществу. Для этого по излагаемому методу определяют значение
нижнего концентрационного предела распространения пламени бензойной кислоты по
ГОСТ 10521-78, которое должно быть равно (20,0 +/- 3,0)
.
Оптимальные
параметры режима распыления исследуемого вещества при данной конструкции
распылителя определяют путем подбора величины давления распыления и
продолжительности распыления. Давление распыления задают от 100 до 250 кПа,
продолжительность распыления от 0,2 до 0,4 с. Параметры режима распыления
считают оптимальными, если значение коэффициента относительной плотности осадка
составляет 1 +/- 0,5.
Коэффициент
относительной плотности осадка рассчитывают по формуле
, (33)
где
,
- масса осадка, мг, в стакане и на поверхности
диска пробоотборника, укрепленного на дне реакционного сосуда, после распыления
навески массой 0,5 г;
,
- соответственно площадь поперечного сечения
стакана и реакционного сосуда, см2.
Последовательность
проведения испытаний:
взвешивают навеску
исследуемого вещества;
помещают навеску в
распылитель;
герметизируют реакционный
сосуд;
подают в ресивер
воздух до требуемого давления;
устанавливают на
блоке продолжительность распыления;
включают источник
зажигания и распыляют навеску;
визуально фиксируют
воспламенение (горение пылевоздушной смеси с распространением пламени от
источника зажигания до контрольной отметки на реакционном сосуде или выше ее)
или отказ (отсутствие горения или распространение пламени ниже контрольной
отметки);
очищают реакционный
сосуд от остатков пыли и продуктов горения.
Определение НКПР
вещества начинают с выявления области концентраций, в которой возможность
воспламенения носит вероятностный характер (область неустойчивого
воспламенения).
Для первого испытания
используют навеску массой 0,2 г. Изменяя первоначальную массу навески на 10%,
находят ее минимальное значение, при котором получают шесть последовательных
воспламенений (частота воспламенения равна 1), и ее максимальное значение, при
котором получают шесть последовательных отказов (частота воспламенения равна
0). На каждой промежуточной навеске проводят шесть испытаний.
За воспламенение
принимают горение пылевоздушной смеси с распространением пламени от источника
зажигания до контрольной отметки на реакционном сосуде или выше ее, за отказ -
отсутствие горения или распространение пламени ниже контрольной отметки.
4.13.3. Обработка
результатов
Нижний
концентрационный предел распространения пламени (НКПР) в граммах на кубический
метр рассчитывают по формуле
, (34)
где
- математическое ожидание величины навески,
соответствующей НКПР, г;
V - вместимость
реакционного сосуда, м3;
- поправочный коэффициент.
Математическое
ожидание величины навески
,
соответствующей НКПР, рассчитывают по методу Спирмена-Кербера
, (35)
где b - минимальное
значение массы навески с частотой воспламенения, равной 1, г;
d - величина
изменения навески, г;
- сумма частот воспламенения во всей области
неустойчивого воспламенения.
Величину
поправочного коэффициента
рассчитывают по формуле
, (36)
где
- среднее значение относительной плотности
осадка, равное
, (37)
- значение относительной плотности осадка в
i-том испытании;
n - число
испытаний;
- доверительный интервал, равный
, (38)
где S - дисперсия;
- квантиль распределения Стьюдента при
одностороннем доверительном интервале и доверительной вероятности 0,95.
Дисперсию
рассчитывают по формуле
. (39)
Значения квантиля
в зависимости от числа испытаний приведены в
табл. 16.
Таблица 16
────────────────────────────────┬─────────────────────────────────
n │ t
│ альфа
────────────────────────────────┼─────────────────────────────────
10 │ 1,833
11 │ 1,812
12 │ 1,796
13 │ 1,782
14 │ 1,771
15 │ 1,761
16 │ 1,763
17 │ 1,746
18 │ 1,740
19 │ 1,734
20 │ 1,729
Условия и
результаты испытаний регистрируют в протоколах по форме:
Протокол
определения поправочного коэффициента

Параметры
режима распыления:
давление в
ресивере __________________________________________
продолжительность распыления _________________________________
───────┬────────┬─────────────────┬────┬─────┬────────┬───────────
Номер
│Исходная│Масса осадка, мг │ │
2│ n │
n 2
испыта-│ масса
├────┬────┬───────┤
K │(K ) │СИГМА K
│(СИГМА K )
ний
│навески,│ m │
m │m + m │
i │ i │
1 i│ 1 i
│ г │
с │ д │ с д│
│ │ │
───────┼────────┼────┼────┼───────┼────┼─────┼────────┼───────────
│ │ │
│ │ │
│ │
Результат
испытаний:
;
;
.
Протокол
испытаний НКПР
Наименование вещества ________________________________________
Параметры
режима распыления:
давление в
ресивере __________________________________________
продолжительность распыления _________________________________
───────────────────────────┬───────────────────────┬──────────────
Масса
навески, г │ Воспламения (+) или │
Частота
│отказы (-) в
испытаниях│воспламенения
──────────┬────────┬───────┼───┬───┬───┬───┬───┬───┤ СИГМА(+)
исходная
│распы- │остаток│ 1
│ 2 │ 3 │ 4 │ 5 │ 6 │ -------
│ленная │ │
│ │ │
│ │ │
6
──────────┼────────┼───────┼───┼───┼───┼───┼───┼───┼──────────────
│ │ │
│ │ │
│ │ │
4.13.4. Требования
безопасности
При проведении
испытаний реакционный сосуд следует устанавливать в специальном шкафу,
оборудованном вытяжной вентиляцией и обеспечиващем безопасность оператора в
случае взрыва реакционного сосуда. При работе следует использовать реакционный
сосуд без трещин и сколов.
В процессе
подготовки образцов, предназначенных для определения НКПР, применяют
индивидуальные средства защиты, выбираемые в соответствии со свойствами
исследуемого вещества.
Рабочее место
оператора должно удовлетворять требованиям электробезопасности по ГОСТ
12.1.019-79 и санитарно-гигиеническим требованиям по ГОСТ 12.1.005-88.
(в ред. Изменения N 2, утв.
Постановлением Госстандарта СССР от 23.03.1989 N 608)
4.14. Метод расчета нижнего концентрационного предела распространения
пламени по пылевоздушным смесям (аэровзвесям)
Нижний
концентрационный предел распространения пламени (НКПР) по аэровзвесям в граммах
на кубический метр рассчитывают по формуле
, (40)
где K -
безразмерный коэффициент, зависящий от кинетических и геометрических
характеристик аэродисперсной системы;
- расчетная концентрация горючего вещества в
воздухе, при которой адиабатическая температура горения смеси при постоянном
давлении составляет 1280 °C,
.
Величину
коэффициента K и концентрацию горючего
рассчитывают по формулам:
, (41)
, (42)
где
- массовая доля влаги или других инертных
добавок в веществе, %;
- стандартная теплота образования вещества в
твердом состоянии при 25 °C,
;
,
- коэффициенты соответственно j-того элемента
и s-той структурной группы, входящих в соединение и влияющих на величину
;
,
- массовая доля соответственно j-того элемента
и s-той структурной группы в соединении, %;
,
- молекулярная масса соответственно j-того
элемента и s-той структурной группы.
Значения
коэффициентов
и
приведены в табл. 9.
Пример. Рассчитать
НКПР флуорена
с массовой долей влаги 2%. Стандартная теплота
образования твердого флуорена равна
.
Массовая доля углерода
и водорода
в соединении составляет соответственно
,
.
Рассчитываем по
формуле (41)
,
а по формуле (42)
.
Рассчитываем НКПР
по формуле (40)
.
Экспериментальное
значение предела воспламенения
.
Относительная
погрешность расчета составляет 2,9%.
Для произвольной
начальной температуры азровзвеси
рассчитывают по формуле
, (43)
где
- расчетное значение НКПР аэровзвеси для
начальной температуры 25 °C;
t - начальная
температура аэровзвеси, °C.
Пример. Рассчитать
НКПР пыли бензойной кислоты
при начальной температуре 327 °C.
Экспериментальное значение составляет
,
.
По формуле (40)
значение
. По
формуле (43)

Относительная
погрешность расчета составляет 29%.
4.15. Метод экспериментального определения температурных пределов
распространения пламени
4.15.1. Аппаратура
Прибор (черт. 13)
состоит из сосуда с тремя горловинами из химико-лабораторного стекла ТС по ГОСТ
21400-75, наружный диаметр сосуда (65 +/- 2) мм, высота до горловин (125 +/- 5)
мм;
термоэлектрического
преобразователя ТХК по ГОСТ 6616-74 малоинерционного, двухзонного измерения, в
стеклянном чехле с расстоянием по высоте между зонами измерения температур (60
+/- 2) мм, диаметр термоэлектродов 0,5 мм;
двух источников
зажигания: искрового и спирального. Искровой состоит из двух электродов,
выполненных из молибденовой проволоки диаметром 1 мм марки МК-1-А по ГОСТ
18905-73 и вмонтированных в стеклянную пробку со шлифом. Разрядный промежуток
(5 +/- 1) мм. Подаваемое напряжение на электроды (18 +/- 2) кВ. Выделяемая
энергия искр на электродах при длительности разряда от 1 до 2 с составляет от
30 до 40 Дж. Спиральный состоит из вышеуказанных электродов, также
вмонтированных в стеклянную пробку со шлифом, к электродам крепится спираль из
проволоки марки Х20Н80-Н ГОСТ 12766.1-77 диаметром 0,3 мм длиной 30 мм.
Внутренний диаметр спирали (5 +/- 1) мм.
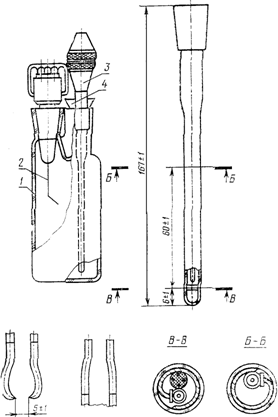
1 - трехгорлый
сосуд; 2 - источник зажигания;
3 -
термоэлектрический преобразователь; 4 - корковая пробка
Черт. 13
Термостат,
обеспечивающий нагрев до (310 +/- 5) °C, и криостат, обеспечивающий охлаждение
до (минус 55 +/- 2) °C, позволяющие поддерживать постоянную температуру с
точностью до 1 °C и наблюдать за распространением пламени в сосуде.
Пирометр визуальный
с исчезающей нитью по ГОСТ 8335-81.
Потенциометр типа
КСП-4 с градуировкой
,
диапазоном измерения температур от минус 50 до 300 °C, класс точности 0,5.
Барометр мембранный
метеорологический по ГОСТ 23696-79.
Секундомер по ГОСТ
5072-79, класс точности 3.
Регулятор
напряжения, максимальный ток нагрузки 8 А, регулируемое (выходное) напряжение
до 240 В.
Корковая пробка.
Цилиндр мерный по
ГОСТ 1770-74 вместимостью 100 см3.
Пылесос для
продувки реакционного сосуда.
Охлаждающие смеси.
4.15.2. Проведение
испытаний
Устанавливают
соответствие исследуемой жидкости паспортным данным по внешнему виду,
плотности, коэффициенту рефракции и температуре кипения входным контролем по
ГОСТ 24297-80.
Для
термостатирования образца исследуемой жидкости выбирают термостат или криостат
в зависимости от предполагаемых значений температурных пределов распространения
пламени.
В чистый сухой
реакционный сосуд помещают (70 +/- 2) см3 исследуемой жидкости, измеренной
мерным цилиндром. В одну из горловин сосуда устанавливают искровой источник
зажигания, искровой промежуток которого должен находиться в центре
паровоздушного пространства над слоем жидкости. Во вторую горловину
устанавливают термоэлектрический преобразователь так, чтобы один рабочий конец
находился в средней части жидкости, другой - в средней части паровоздушного
пространства. Третью горловину плотно закрывают корковой пробкой. Затем сосуд
помещают в термостат (криостат).
Для определения
нижнего (верхнего) предела распространения пламени исследуемую жидкость
охлаждают (нагревают) до температуры на 10 °C ниже (выше) предполагаемого
(расчетного) значения нижнего (верхнего) предела распространения пламени.
Предварительно значения температурных пределов распространения пламени
рассчитывают по формулам (46) - (48).
При заданной температуре
сосуд с исследуемой жидкостью термостатируют в течение (12 +/- 2) мин для
установления равновесия между жидкой и паровой фазами, разность температур
которых не должна быть более 1 °C. За результат определения принимают показания
нижней зоны термоэлектрического преобразователя.
После
термостатирования проводят испытание на воспламенение. Для этого ослабляют
плотность закрытия корковой пробки и включают источник зажигания на время от 1
до 2 с.
Если возникшее
пламя распространится по всему объему паровоздушного пространства или
вертикально вверх до горловины сосуда, то результат испытания принимают за
воспламенение. За отказ принимают вспышку или горение, происходящие на
источнике зажигания, или выброс пробки без видимого пламени.
Независимо от
результатов после каждого испытания сосуд пробивают воздухом.
В случае
воспламенения температуру исследуемой жидкости уменьшают на 5 °C при
определении нижнего предела и увеличивают на 5 °C при определении верхнего
предела. В случае отказа температуру исследуемой жидкости увеличивают на 5 °C
при определении нижнего предела и уменьшают на 5 °C при определении верхнего
предела.
Изменяя температуру
исследуемой жидкости, находят два таких значения температуры с разницей не
более 2 °C, при одном из которых происходит воспламенение, а при другом -
отказ.
Для веществ,
которые не воспламеняются от искрового источника зажигания, необходимо провести
испытания со спиральным источником зажигания. Питание к спиральному источнику
зажигания подают через регулятор напряжения с таким расчетом, чтобы спираль
накалялась до температуры 1000 - 1050 °C за время не более 4 с. Температуру
накаленной спирали проверяют пирометром.
4.15.3. Обработка
результатов
За температурный
предел распространения пламени принимают среднее арифметическое не менее трех
пар определений на воспламенение и отказ, полученных на трех образцах вещества.
Если при проведении
испытания атмосферное давление отличалось от 101,3 кПа, то полученное значение
температуры приводят к температуре при нормальном атмосферном давлении по
формуле
, (44)
где
- температура испытания, °C;
- атмосферное давление при
, кПа;
B,
- константы уравнения Антуана.
Для жидкостей с
неизвестными константами B и
значения температуры с поправкой на
атмосферное давление рассчитывают по формуле
, (45)
где
- размерный коэффициент,
.
Полученные значения
округляют до целого числа.
Разность двух
последовательных результатов, полученных одним и тем же оператором при постоянных
условиях испытания с вероятностью 0,95, не должна быть более 3 °C на нижнем
пределе и 5 °C на верхнем пределе при условии, что случайные погрешности
преобладают над неисключенными систематическими.
Условия и
результаты испытаний регистрируют в протоколе испытаний.
4.15.4. Требования
безопасности
Прибор для
определения температурных пределов распространения пламени следует
устанавливать в вытяжном шкафу. Рабочее место оператора должно удовлетворять
требованиям электробезопасности по ГОСТ 12.1.019-79 и санитарно-гигиеническим
требованиям по ГОСТ 12.1.005-88.
(в ред. Изменения N 2, утв.
Постановлением Госстандарта СССР от 23.03.1989 N 608)
4.16. Методы расчета температурных пределов распространения пламени
4.16.1. Расчет
температурных пределов распространения пламени для индивидуальных жидких
веществ
4.16.1.1.
Если известна зависимость давления насыщенных паров жидкости от температуры, то
величину нижнего или верхнего температурного предела распространения пламени
в градусах Цельсия рассчитывают по
соответствующему значению концентрационного предела распространения пламени
по формуле
, (46)
где A, B,
- константы уравнения Антуана;
- атмосферное давление, кПа.
Величина
может быть рассчитана по методам,
рекомендуемым в п. 4.12. Погрешность расчета по формуле (46) определяется
погрешностью величины
.
4.16.1.2.
Для веществ нижеперечисленных классов температурные пределы распространения
пламени рассчитывают по формуле
, (47)
где
- температура кипения, °C;
k, l -
коэффициенты, постоянные в пределах гомологического ряда, величины которых
приведены в табл. 17.
Таблица 17
───────────────────────────┬───────────────┬──────────────────────
Название гомологического │ Температурный │ Коэффициент
ряда │ предел
├──────────┬───────────
│ │ k
│ t °C
───────────────────────────┼───────────────┼──────────┼───────────
Углеводороды
алифатические │ Нижний │
0,69 │ 74
│ Верхний
│ 0,79 │
51
Спирты
алифатические │ Нижний
│ 0,61 │
38
│ Верхний
│ 0,69 │
15
Эфиры
сложные │ Нижний
│ 0,61 │
54
│ Верхний
│ 0,75 │
33
Алкиламины
первичные │ Нижний
│ 0,50 │
55
Погрешность расчета
по формуле (47) не превышает 10 °C.
4.16.1.3. В
случаях, не предусмотренных в пп. 4.16.1.1 и 4.16.1.2, величину нижнего
температурного предела распространения пламени
в градусах Цельсия рассчитывают по формуле
, (48)
где C - константа,
равная 2, если для расчета используют значение
в закрытом тигле, и равная 8, если для расчета
используют значение
в открытом тигле.
Значения
могут быть рассчитаны по методам, изложенным в
п. 4.5.
Погрешность расчета
по формуле (48) определяется погрешностью величины
и, как правило, не превышает 12 °C.
4.16.2. Расчет
температурных пределов распространения пламени для смесей жидкостей,
представляющих собой растворы
4.16.2.1. Если
известна зависимость давления насыщенных паров от температуры для каждого из
компонентов смеси, то температурный предел распространения пламени для смеси
в градусах Цельсия рассчитывают по формуле
, (49)
где k - число
компонентов смеси;
- коэффициенты активности i-того компонента;
- мольные доли i-того компонента в жидкой
фазе;
,
,
;
,
- константы уравнения Антуана для i-того
компонента;
- температурный предел распространения пламени
i-того компонента.
Средняя
квадратическая погрешность расчета составляет 10 °C для нижнего температурного
предела и не превышает 20 °C для верхнего.
4.16.2.2. В случае,
если хотя бы для одного компонента смеси неизвестна зависимость давления
насыщенных паров от температуры, нижний температурный предел распространения
пламени для смеси
в градусах Цельсия рассчитывают по формуле
, (50)
где
- мольная теплота испарения i-того компонента,
;
R - универсальная
газовая постоянная;
- нижний температурный предел воспламенения
i-того компонента, °C.
Величина
может быть определена по интерполяционной
формуле (10).
Средняя
квадратическая погрешность расчета по формуле (50) составляет 10 °C.
4.16.3. Расчет
нижнего температурного предела распространения пламени для смесей горючих и
негорючих жидкостей
Данный метод
расчета распространяется на смеси жидкостей, представляющие собой растворы. При
известной зависимости давления насыщенных паров от температуры для каждого
негорючего компонента нижний температурный предел распространения пламени для
смеси
в градусах Кельвина рассчитывают по формуле
, (51)
где
,
- мольные доли i-того горючего и j-того
негорючего компонента компонента в жидкой фазе;
,
- мольная теплота испарения i-того горючего и
j-того негорючего компонента,
;
- нижний температурный предел распространения
пламени i-того горючего компонента. K;
- условный нижний температурный предел
распространения пламени j-того горючего компонента в градусах Кельвина
рассчитывают по формуле
, (52)
где A, B,
- константы уравнения Антуана для данного
негорючего компонента;
- атмосферное давление, кПа;
- параметр, характеризующий флегматизирующее
или ингибирующее влияние негорючего компонента в паровой фазе. Величины
для наиболее распространенных негорючих
компонентов приведены в табл. 18.
Таблица 18
─────────────────────────────────┬────────────────────────────────
Название вещества │ гамма
─────────────────────────────────┼────────────────────────────────
Вода │ 1,23
Тетрахлорметан │ 4,80
1,1,2-Трифтортрихлорэтан │ 5,60
1,2-Дибромтетрафторэтан │ 21,30
Средняя
квадратическая погрешность расчета составляет 10 °C.
4.17. Метод экспериментального определения температуры самонагревания
твердых веществ и пылей
4.17.1. Аппаратура
Четыре
электрических сушильных шкафа вместимостью по 4 дм3 с регуляторами температуры,
позволяющими поддерживать температуру рабочей зоны от 40 до 200 °C.
Термоэлектрические
преобразователи малоинерционные, обыкновенные, типы ТХК по ГОСТ 6616-74 с
диаметром термоэлектродов 0,5 мм (по одному термоэлектрическому преобразователю
на каждый шкаф).
Потенциометр
автоматический многоточечный типа КСП-4 с градуировкой
,
диапазоном измерения температуры от 0 до 400 °C, класс точности 0,5.
Весы лабораторные
общего назначения по ГОСТ 24104-88 с наибольшим пределом взвешивания 200 г,
класс точности 2.
(в ред. Изменения N 2, утв.
Постановлением Госстандарта СССР от 23.03.1989 N 608)
Стаканчики для
взвешивания - по ГОСТ 25336-82 СВ 24/10 не менее 20 шт., СН 60/14 по ГОСТ
25336-82 не менее 24 шт.
Эксикаторы 2-250 по
ГОСТ 25336-82 с прокаленным хлористым кальцием не менее 3 шт.
Калориметр сжигания
для определения теплоты сгорания исследуемого вещества.
4.17.2. Проведение
испытаний
Исследуемое твердое
вещество предварительно измельчают до частиц размером не более 5 мм. Образцы
должны характеризовать средние свойства исследуемого вещества.
Для испытания
готовят 24 образца массой не менее 10 г каждый. Образцы взвешивают в бюксах (с
крышками), масса которых определена заранее.
В калориметре
определяют начальную теплоту сгорания
,
исследуемого вещества массой 1 г.
Сушильные шкафы
подключают к электрической сети и при помощи терморегуляторов устанавливают
температурный режим в шкафах, соответственно 60, 80, 100 и 120 °C. При
достижении заданной температуры в каждый шкаф помещают по шесть бюкс с
исследуемым веществом (крышки с бюкс снимают и располагают их рядом).
Испытание проходит
в течение 6 мес. Через каждый месяц из шкафов вынимают по одной бюксе,
предварительно закрыв ее крышкой, и тут же помещают в эксикатор.
После охлаждения в
эксикаторе (не менее 1 ч) бюксы взвешивают для определения потери массы
исследуемого вещества. Затем из каждой бюксы отбирают не менее пяти навесок
массой 1 г каждая для определения теплоты сгорания вещества, подвергавшегося
нагреву. Навески отбирают в предварительно взвешенные бюксы. Бюксы закрывают
крышками и до сжигания в калориметре хранят в эксикаторе.
За величину теплоты
сгорания принимают среднее арифметическое трех сжиганий, если расхождение между
средним арифметическим и результатом каждого сжигания не превышает 1%. При
большем расхождении проводят дополнительные сжигания навесок, пока не получат
не менее трех результатов, отличающихся не более чем на 1% от среднего
арифметического результатов всех сжиганий.
По результатам
определения теплоты сгорания вещества до и после нагрева составляют
неравенство:
, (53)
где
,
- теплота сгорания вещества, соответственно до
и после нагрева,
;
,
- масса образца соответственно до и после
нагрева, г;
1,03 - коэффициент,
учитывающий погрешность испытаний.
Если неравенство
(53) выполняется для образца из какого-либо шкафа, то значит, что принятая в
данном шкафу температура нагрева вещества создает возможность проявления в нем
экзотермического процесса.
В этом случае для
уточнения выявленной температуры шкаф с более высоким температурным режимом 120
°C переводят на режим 40 °C, а в остальных шкафах нагрев вещества продолжают
при прежнем температурном режиме.
Если равенство (53)
не выполняется, то шкаф с наиболее низким температурным режимом 60 °C переводят
на режим 140 °C, а в остальных шкафах нагрев вещества продолжают при прежнем
температурном режиме.
При получении
такого же результата в следующем месяце поступают аналогичным образом, повышая
температуру до 160 °C в шкафу с первоначальным температурным режимом 80 °C и
т.д.
Во всех случаях,
когда шкафы устанавливают на новый температурный режим, образцы вещества в них
заменяют на новые, отобранные из той же партии вещества, что и первоначальные
24 образца.
4.17.3. Обработка
результатов
За температуру
самонагревания исследуемого вещества принимают наиболее низкую температуру в
сушильном шкафу, при которой обнаруживаются условия выполнения неравенства
(53). При температуре на 20 °C ниже установленной температуры самонагревания
неравенство (53) не должно выполняться при нагревании в течение 6 мес.
Условия и
результаты испытаний регистрируют в протоколе испытаний.
4.17.4. Требования
безопасности
Сушильные шкафы
следует устанавливать в вытяжном шкафу. Рабочее место оператора должно
удовлетворять санитарно-гигиеническим требованиям по ГОСТ 12.1.005-88.
(в ред. Изменения N 2, утв.
Постановлением Госстандарта СССР от 23.03.1989 N 608)
4.18. Метод экспериментального определения температуры тления твердых
веществ и пылей
4.18.1. Аппаратура
Аппаратура для
экспериментального определения температуры тления приведена в п. 4.7.1.
4.18.2. Проведение
испытаний
Образцы должны
характеризовать средние свойства исследуемого вещества (материала). Для
испытаний готовят не менее десяти образцов исследуемого материала массой (3,0
+/- 0,1) г. Сыпучие и гранулированные вещества массой (3,0 +/- 0,1) г помещают
в контейнер, при этом плотность засыпки должна соответствовать насыпной
плотности, с которой вещество применяют на практике.
Подготовленные
образцы подвергают кондиционированию в соответствии с требованиями ГОСТ
12423-66.
Устанавливают
термоэлектрические преобразователи в фиксированные точки рабочей камеры,
включают нагрев электропечи. При первом испытании температура в рабочей камере
должна быть равной температуре разложения исследуемого вещества или (300 +/- 5)
°C.
После установления
в рабочей камере стационарного температурного режима, определяемого по
постоянству показаний двух термоэлектрических преобразователей (расхождение
показаний которых не должно превышать 2,5%), держатель извлекают из рабочей
камеры, в контейнер помещают образец и возвращают держатель в исходное
положение. Газовую горелку при этом используют в качестве магистрали для
подвода воздуха, который подают в горелку от насоса. Горелку опускают внутрь
рабочей камеры на расстояние (10 +/- 2) мм от поверхности образца.
Наблюдают за
образцом с помощью зеркала.
Если обнаружено
тление, то регистрируют тление при
и следующее испытание с новым образцом
проводят при меньшей температуре (например, на 30 °C меньше). Если в течение 20
мин образец не тлеет, считают, что при
получили отказ. Следующее испытание с новым
образцом проводят при более высокой температуре (например, на 30 °C больше).
Изменяя температуру в рабочей камере, определяют такую наименьшую температуру,
при которой наблюдается тление образца при двукратном повторении испытаний, а
при температуре на 10 °C меньше наблюдаются два отказа.
4.18.3. Обработка
результатов
За температуру
тления принимают среднее арифметическое двух ближайших температур, отличающихся
не более чем на 10 °C, при одной из которых наблюдается тление двух образцов, а
при другой - два отказа.
Разность двух
последовательных результатов, полученных одним и тем же оператором при
постоянных условиях испытания с вероятностью 0,95, не должна быть более 5 °C
при условии, что случайные погрешности преобладают над неисключенными
систематическими.
Условия и
результаты испытаний регистрируют в протоколе испытаний.
4.18.4. Требования
безопасности
Прибор для
определения температуры тления следует устанавливать в вытяжном шкафу. Рабочее
место оператора должно удовлетворять требованиям электробезопасности по ГОСТ
12.1.019-79 и санитарно-гигиеническим требованиям по ГОСТ 12.1.005-88.
(в ред. Изменения N 2, утв.
Постановлением Госстандарта СССР от 23.03.1989 N 608)
4.19. Метод экспериментального определения условий теплового
самовозгорания твердых веществ и пылей
4.19.1. Аппаратура
Термостат
вместимостью рабочей камеры не менее 40 дм3 с терморегулятором, позволяющим
поддерживать постоянную температуру от 60 до 250 °C.
Корзиночки
кубической формы размерами 35 x 35 x 35, 50 x 50 x 50, 70 x 70 x 70, 100 x 100
x 100, 140 x 140 x 140 и 200 x 200 x 200 мм (по десяти штук каждого размера) с
крышками. Материалом для корзиночек служит сетка из нержавеющей стали или
листовая нержавеющая сталь (при испытании плавящихся веществ). Номер сетки
выбирают в зависимости от величины частиц исследуемого вещества для
предотвращения высыпания образца.
Термоэлектрические
преобразователи типа ТХА малоинерционные, обыкновенные по ГОСТ 6616-74,
диаметром электродов 0,7 мм, в асбестовой изоляции (три штуки на одну
корзиночку).
Потенциометр типа
КСП-4 с градуировкой
,
диапазоном измерения температур от 0 до 1100 °C, класс точности 0,5.
Весы лабораторные
общего назначения по ГОСТ 24104-88 с наибольшим пределом взвешивания 200 г,
класс точности 2.
(в ред. Изменения N 2, утв.
Постановлением Госстандарта СССР от 23.03.1989 N 608)
4.19.2. Проведение
испытаний
К корзиночкам
крепят по три термоэлектрических преобразователя с таким расчетом, чтобы
рабочий конец одного термоэлектрического преобразователя находился внутри
корзиночки в ее центре, второго - соприкасался с внешней стороной ее, а рабочий
конец третьего термоэлектрического преобразователя находился в (30 +/- 1) мм от
внешней стенки корзиночки на высоте ее центра (черт. 14).
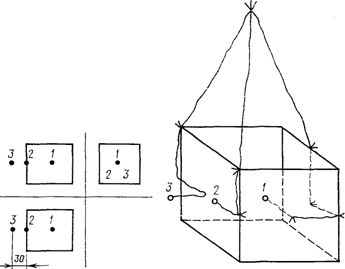
1, 2, 3 -
термоэлектрические преобразователи
Черт. 14
Образцы должны
характеризовать средние свойства исследуемого вещества (материала).
Заполняют
корзиночки исследуемым веществом. При испытании листового материала его
нарезают квадратиками, имеющими размеры корзиночки, и набирают в стопку,
соответствующую высоте корзиночки. В образцах из монолитных материалов
предварительно высверливают до центра отверстие диаметром (7,0 +/- 0,5) мм для
термоэлектрического преобразователя. Волокнистые и сыпучие материалы укладывают
в корзиночку с плотностью, соответствующей реальной плотности, с которой
материал применяют на практике. Корзиночку закрывают крышкой с отверстием для
термоэлектрического преобразователя.
Первое испытание
проводят при температуре рабочей зоны термостата (200 +/- 5) °C или на (80 +/-
20) °C ниже температуры самовоспламенения исследуемого вещества, если она
известна.
В центр термостата
подвешивают корзиночку размером 35 x 35 x 35 мм с исследуемым веществом.
Свободные концы термоэлектрического преобразователя пропускают через верхнее
отверстие термостата и подсоединяют к потенциометру. Скорость движения
диаграммной ленты потенциометра устанавливают
.
Наблюдают за изменением температуры в центре образца с помощью потенциометра.
Самовозгорание
образца проявляется или в резком повышении температуры в его центре до (450 +/-
50) °C или в плавном повышении температуры до величины, превышающей значение
температуры самовоспламенения вещества.
Отмечают время от
момента выравнивания температур образца и термостата до момента резкого подъема
температуры в образце или (при плавном росте температуры) до момента достижения
температуры самовоспламенения образца.
После того, как
процесс самовозгорания закончится (температура в центре образца снизится до
первоначальной), термостат выключают и извлекают корзиночку с веществом.
Если при заданной
температуре термостата самовозгорание не происходит в течение времени,
указанного в табл. 19, то испытание с новым образцом вещества проводят при
большей температуре (например, на 20 °C больше), если самовозгорание произошло,
то испытание повторяют при меньшей температуре (например, на 20 °C меньше).
Таблица 19
─────────────────────────────┬────────────────────────────────────
Размер корзиночки, мм │
Максимальное время, необходимое
│ для испытания образца данных
│ размеров на самовозгорание, ч
─────────────────────────────┼────────────────────────────────────
35 x 35 x 35 │ 6
50 x 50 x 50 │ 12
70 x 70 x 70 │ 24
100 x 100 x 100 │ 48
140 x 140 x 140 │ 96
200 x 200 x 200 │ 192
В процессе
испытаний определяют такую минимальную температуру, при которой образец
самовозгорается, а при температуре на 5 °C ниже минимальной самовозгорания не
происходит.
Аналогичные
испытания проводят с образцами в корзиночках других размеров.
4.19.3. Обработка
результатов
На основании
полученных результатов испытания строят графики зависимости логарифма
температуры самовозгорания от логарифма удельной поверхности и логарифма
времени до самовозгорания (черт. 15).
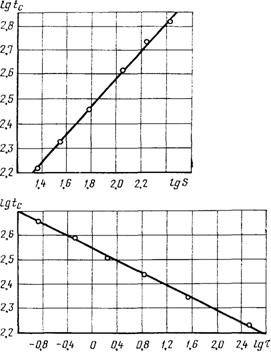
Черт. 15
Удельную
поверхность материала (S) в метрах в минус первой степени рассчитывают по
формуле
, (54)
где F - полная
наружная поверхность образца, м2;
V - объем образца,
м3;
a - линейный размер
образца, м.
Через точки на
графиках проводят прямые линии и составляют уравнения этих прямых
, (55)
, (56)
где
,
,
,
- коэффициенты, определяемые по опытным данным.
Приведенные
уравнения (55), (56) определяют условия теплового самовозгорания исследуемого
вещества: при какой температуре нагрева вещества может произойти самовозгорание
определенной массы его и какова длительность процесса до самовозгорания.
Условия и
результаты испытаний регистрируют в протоколе испытаний.
4.19.4. Требования
безопасности
Из-за выделения
токсичных продуктов термического разложения термостат следует устанавливать в
отдельном помещении с приточно-вытяжной вентиляцией, обеспечивающей кратность
обмена воздуха не менее восьми. Рабочее место оператора должно удовлетворять
санитарно-гигиеническим требованиям по ГОСТ 12.1.005-88.
(в ред. Изменения N 2, утв.
Постановлением Госстандарта СССР от 23.03.1989 N 608)
4.20. Метод экспериментального определения минимальной энергии
зажигания газов и паров жидкостей
4.20.1. Аппаратура
Установка (черт.
16) состоит из реакционного сосуда - взрывной бомбы из нержавеющей стали
12Х18Н9Т по ГОСТ 5632-72 вместимостью 1 дм3, рассчитанной на давление 2000 кПа.
В боковые гнезда по центру сосуда герметично вмонтированы фторопластовые
изоляторы с электродами зажигания в виде стальных стержней диаметром (1,0 +/-
0,2) мм с полусферическими наконечниками диаметром около 1,5 мм, на которые при
определении критического расстояния между электродами надевают стеклянные или
фторопластовые диски диаметром (25 +/- 1) мм. Расстояние между электродами
регулируют при помощи индикаторной головки или микрометрического винта. Один из
электродов закрепляют неподвижно. В заземленном (подвижном) электроде имеется
вакуумное уплотнение. При сборке установки должна быть обеспечена соосность
электродов (0,2 +/- 0,1) мм. Реакционный сосуд оборудован клапанами для ввода
испытуемой смеси и удаления продуктов горения, а также предохранительным
клапаном для сброса избыточного давления при воспламенении смеси. Для
визуального наблюдения за воспламенением смеси в сосуде предусмотрены смотровые
окна, выполненные из кварцевого стекла;
смесителя
вместимостью (18 +/- 2) дм3, изготовленного из нержавеющей стали 12Х18Н9Т по
ГОСТ 5632-72 и рассчитанного на давление до 500 кПа. Смеситель снабжен
образцовым манометром для измерения парциальных давлений компонентов
приготовляемой смеси и осушителем с хлористым кальцием;
баллонов с горючим
газом и воздухом, снабженных редукторами;
ртутного манометра
с ценой деления 0,1 кПа для измерения давления в реакционном сосуде;
вакуумного насоса,
обеспечивающего остаточное давление не более 0,2 кПа;
ионизатора;
электрической
системы зажигания, в которую входит высоковольтный стабилизированный источник
постоянного тока, обеспечивающий регулируемое рабочее напряжение до 20 кВ,
набор вакуумных или фторопластовых конденсаторов с электрическим зарядом от 0,5
до
пФ; статический киловольтметр типа С-196 или
аналогичный; измеритель электрического заряда типа Е8-1 или аналогичный;
ограничительное сопротивление зарядного тока от
до
Ом; пересчетный прибор для счета и регистрации
количества искровых разрядов.
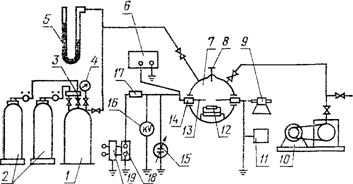
1 - смеситель; 2 -
баллоны с горючим газом и воздухом;
3 - осушитель с
хлористым кальцием; 4 - образцовый
манометр; 5 -
ртутный манометр; 6 - измеритель
электрического
заряда; 7 - реакционный сосуд;
8 -
предохранительный клапан; 9 - микрометрический винт;
10 - вакуумный
насос; 11 - пересчетный прибор;
12 - ионизатор; 13
- электрод (неподвижный);
14 - фторопластовый
изолятор; 15 - конденсатор;
16 - киловольтметр;
17 - ограничительное сопротивление;
18 - высоковольтный
источник постоянного тока;
19 - стабилизатор
напряжения
Черт. 16
4.20.2. Проведение
испытаний
Образцы должны
характеризовать средние свойства исследуемого вещества.
Перед проведением
испытаний реакционный сосуд проверяют на герметичность, вакуумируя его до
остаточного давления (0,50 +/- 0,1) кПа. Если в течение 10 мин после отключения
вакуум-насоса давление в реакционном сосуде повысится не более чем на 0,6 кПа,
то установка считается пригодной для проведения испытаний.
В смесителе готовят
по парциальным давлениям, измеряемым образцовым манометром 4, газо-,
паровоздушную смесь заданного состава. В случае подготовки паровоздушной смеси
смеситель снабжается электроподогревающим устройством для предотвращения
конденсации паров. Температуру в смесителе и в реакционном сосуде поддерживают
примерно равной верхнему температурному пределу воспламенения исследуемой
жидкости.
Определяют
критическое расстояние между электродами. Для этой цели на концах электродов
укрепляют фторопластовые или кварцевые диски, вакуумируют реакционный сосуд до
остаточного давления (0,5 +/- 0,1) кПа и затем впускают в него приготовленную в
смесителе стехиометрическую смесь исследуемого газа или пара с воздухом (если
испытания проводят при атмосферном давлении, то в сосуде необходимо установить
давление 101,3 кПа).
Из нулевого
положения, определяемого по омметру, электроды с дисками устанавливают на
расстоянии 0,1 мм друг от друга. Затем к неподвижному электроду подключают
вакуумный конденсатор с электрическим зарядом не более 400 пФ при испытании
газов и не более 700 пФ при испытании паров, включают высоковольтный источник
питания и вращением ручки регулятора напряжения по часовой стрелке плавно
поднимают напряжение до пробоя разрядного промежутка, устанавливая по
пересчетному прибору частоту искрения от 5 до 10 разрядов в минуту.
Испытания ведут до
воспламенения смеси или до получения 100 разрядов, если воспламенение не
происходит. Испытания на воспламенение повторяют четыре-пять раз с новыми
порциями смеси из смесителя. После проведения каждого испытания реакционный
сосуд поочередно наполняют воздухом и вакуумируют три-пять раз для удаления
испытанной смеси или продуктов горения.
Если воспламенение
не происходит, увеличивают разрядный промежуток электродов на 0,1 мм и проводят
аналогичную серию испытаний на воспламенение.
Если наблюдается
воспламенение, то это свидетельствует о достижении критического разрядного
промежутка для стехиометрической смеси.
Таким же способом
находят критический разрядный промежуток электродов для пяти-восьми смесей,
содержащих горючего компонента меньше или больше, чем в стехиометрической
смеси. По полученным данным строят кривую зависимости критического разрядного
промежутка электродов (ось ординат в логарифмических координатах) от
концентрации горючего компонента в смеси (черт. 17а). Величину разрядного
промежутка, соответствующую минимуму полученной кривой, принимают за
критическое расстояние между электродами, а соответствующую ему газо-,
паровоздушную смесь - за наиболее легковоспламеняющуюся смесь.
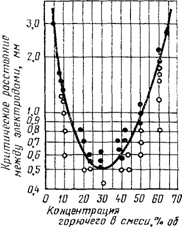
а)
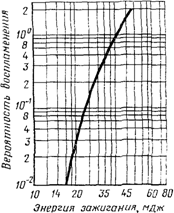
б)
Черт. 17
Затем приступают к
определению минимальной энергии зажигания, для этого с электродов снимают диски
и под электродами устанавливают ионизатор. Испытания на воспламенение газо-,
паровоздушной смеси выполняют точно так же, как при определении критического
расстояния между электродами, при этом испытывают только наиболее
легковоспламеняющуюся смесь. Каждую серию испытаний ведут при одном и том же
напряжении перед разрядом
и одном и том же электрическом заряде (C)
конденсатора до получения не менее 10 воспламенений смеси с вероятностью не
менее 0,1. Если при заданных
и C смесь не воспламенилась при 1000 разрядах
(при этом число разрядов в одной и той же порции смеси в реакционном сосуде не
должно превышать 100), то считают, что от данной энергии зажигания смесь не
способна воспламениться. В следующей серии увеличивают электрический заряд
конденсатора и так же испытывают смесь на воспламенение до получения не менее
10 воспламенений с вероятностью не менее 0,1 или до 1000 разрядов при
отсутствии воспламенений.
Последовательно
изменяя электрический заряд конденсатора и повторяя испытания, находят
зависимость энергии зажигания W от вероятности воспламенения (P).
4.20.3. Обработка
результатов
Вероятность
воспламенения смеси рассчитывают по формуле
, (57)
где m - число
испытаний, при которых смесь воспламенилась;
n - общее число
испытаний на воспламенение в данной серии.
Энергию зажигания
(W) в джоулях рассчитывают по формуле
, (58)
где C -
электрический заряд конденсатора, Ф;
,
- напряжение на конденсаторе соответственно
перед пробоем и после пробоя искрового промежутка, В.
В логарифмических
координатах строится кривая зависимости вероятности воспламенения от величины
энергии зажигания (черт. 17б).
Значение энергии
зажигания, соответствующее вероятности воспламенения 0,1, принимают за
минимальную энергию зажигания исследуемого вещества.
Разность двух
последовательных результатов, полученных одним и тем же оператором при
постоянных условиях испытания с вероятностью 0,95, не должна быть более 5 мДж
при условии, что случайные погрешности преобладают над неисключенными
систематическими.
Условия и
результаты испытаний регистрируют в протоколе испытаний.
4.20.4. Требования
безопасности
Реакционный сосуд
следует устанавливать в вытяжном шкафу. Для обеспечения безопасности работы
необходимо использовать блокировку, автоматически отключающую высоковольтный
источник питания от сети и заземляющую вывод высоковольтного источника питания
с блоком конденсаторов при любых переключениях аппарата.
Рабочее место
оператора должно удовлетворять требованиям электробезопасности по ГОСТ
12.1.019-79 и санитарно-гигиеническим требованиям по ГОСТ 12.1.005-88.
(в ред. Изменения N 2, утв.
Постановлением Госстандарта СССР от 23.03.1989 N 608)
4.21. Метод экспериментального определения минимальной энергии
зажигания пылей
4.21.1. Аппаратура
Установка (черт.
18) состоит из реакционной камеры прямоугольной формы, изготовленной из
листовой нержавеющей стали по ГОСТ 5632-72 толщиной (4 +/- 1) мм или оргстекла
толщиной (6 +/- 2) мм, в которой распыляется и зажигается пылевоздушная смесь.
На стенках камеры укреплены заостренные электроды из нержавеющей стали по ГОСТ
5632-72 диаметром (1,0 +/- 0,1) мм в цилиндрических изоляторах (из любого
диэлектрика) диаметром (15 +/- 1) мм;
виброситового
дозатора, включающего в себя вибратор и подвешенный на кронштейне стакан.
Нижнее отверстие стакана закрыто легкосменяемой металлической сеткой с ячейками
определенных размеров. Дозатор обеспечивает подачу в разрядный промежуток
заданного количества исследуемого вещества (концентрация аэровзвеси от 10 до
);
пылесборника;
блока зарядки
рабочего конденсатора, состоящего из источника высокого напряжения постоянного
тока, позволяющего подавать на электроды регулируемое напряжение от 0 до 30 кВ;
киловольтметра типа
С-196 или аналогичного;
измерителя
электрического заряда типа Е8-1 или аналогичного;
набора вакуумных
или фторопластовых конденсаторов с электрическим зарядом от 50 до 25000 пФ,
которые должны быть рассчитаны на рабочее напряжение от 8 до 10 кВ;
блока управления,
обеспечивающего заданную последовательность включения и выключения приборов
установки при ее работе в автоматическом режиме, а также блокировку дверцы
защитного шкафа и сигнализацию о наличии напряжения на установке;
счетного механизма
для регистрации количества искровых разрядов.
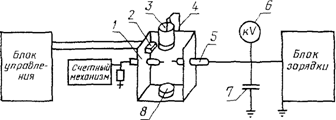
1 - реакционная
камера; 2 - вибратор; 3 - стакан;
4 - кронштейн; 5 -
электрод в изоляторе; 6 - киловольтметр;
7 - конденсатор; 8
- пылесборник
Черт. 18
4.21.2. Проведение
испытаний
Перед проведением
испытаний устанавливают соответствие исследуемого вещества паспортным данным по
внешнему виду, влажности, зольности, дисперсности, а для плавящихся
органических веществ - дополнительно по температуре плавления входным контролем
по ГОСТ 24297-87. Производят отсев частиц; при испытании используют пыли с
размером частиц менее 50 мкм для металлических веществ и менее 100 мкм для
других веществ.
(в ред. Изменения N 2, утв.
Постановлением Госстандарта СССР от 23.03.1989 N 608)
В стакан дозатора
насыпают пыль исследуемого вещества, включают вибратор и проверяют возможность
получения аэровзвеси различной концентрации.
Минимальную энергию
зажигания пылевоздушной смеси определяют в несколько этапов, начиная с
определения оптимальной концентрации исследуемого вещества. Для чего
устанавливают зависимость вероятности воспламенения от подаваемого на вибратор
напряжения. Эту зависимость определяют при заведомо зажигающей энергии (дающей
вероятность воспламенения от 0,3 до 0,5), при разрядном промежутке электродов
от 3 до 5 мм и при наличии в разрядной цепи активного сопротивления R.
Вероятность воспламенения смеси рассчитывают по формуле (57). При этом число
воспламенений должно быть одинаковым во всех испытаниях и не менее десяти.
Количество разрядов определяют по показаниям счетного механизма, а число воспламенений
- визуально.
Затем при найденном
напряжении на вибраторе, обеспечивающем наибольшую вероятность воспламенения
(черт. 19а), измеряют концентрацию пыли в пылевоздушной смеси при помощи
отсекателя (пружинного устройства), который мгновенно вводится в зону
расположения электродов. Определив массу пыли, осевшей на нижней плоскости
отсекателя, рассчитывают оптимальную концентрацию пылевоздушной смеси (Q) в
граммах на кубический сантиметр по формуле
, (59)
где M - масса пыли
на нижней плоскости отсекателя, г;
d - диаметр сита
виброситового дозатора, см;
h - расстояние
между плоскостями отсекателя, см.
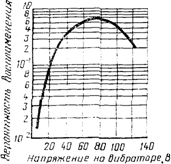
а)
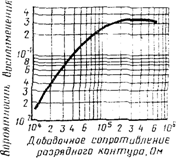
б)
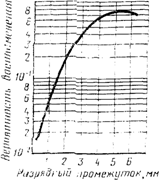
в)
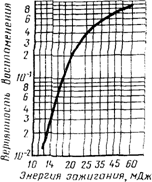
г)
Черт. 19
После выявления
оптимальной концентрации пылевоздушной смеси определяют оптимальные параметры
разрядного контура. За оптимальные параметры разрядного контура принимают такое
значение включенного последовательно к конденсатору добавочного активного
сопротивления (R), при котором обеспечивается наибольшая вероятность
воспламенения.
Оптимальное
значение добавочного сопротивления определяют при найденной оптимальной
концентрации пылевоздушной смеси и разрядом промежутке от 3 до 5 мм снятием
характеристик P = f(R).
По
экспериментальным данным при различных значениях R строят в логарифмических
координатах кривую зависимости вероятности воспламенения от величины
добавочного сопротивления в разрядном контуре (черт. 19б). Величина добавочного
сопротивления, соответствующая максимуму кривой, принимается за оптимальное
значение R. Если явного максимума кривой не наблюдается, а имеется монотонное
возрастание функции P = f(R), то за оптимальное значение R принимают параметры,
при которых угол наклона графика с горизонталью не превышает 15°.
При оптимальных
параметрах разрядного контура и оптимальной концентрации пылевоздушной смеси
определяют оптимальный разрядный промежуток электродов снятием характеристик P
= f(d). Оптимальным называют разрядный промежуток, обеспечивающий наибольшую
вероятность воспламенения. По экспериментальным данным строится кривая
зависимости вероятности воспламенения от величины разрядного промежутка (черт.
19в). Значение разрядного промежутка, соответствующее максимуму кривой
принимают за оптимальный разрядный промежуток.
При оптимальных
значениях концентрации, параметров разрядного контура и разрядного промежутка
определяют минимальную энергию зажигания снятием характеристик P = f(W).
4.21.3. Обработка
результатов
По
экспериментальным данным строят в логарифмических координатах кривую
зависимости вероятности воспламенения от величины энергии зажигания (черт.
19г).
Значение энергии
зажигания, соответствующее вероятности воспламенения 0,01, принимают за
минимальную энергию зажигания исследуемого вещества.
Разность двух
последовательных результатов, полученных одним и тем же оператором при
постоянных условиях испытания с вероятностью 0,95, не должна быть больше 5 мДж
при условии, что случайные погрешности преобладают над неисключенными
систематическими.
Условия и
результаты испытаний регистрируют в протоколе испытаний.
4.21.4. Требования
безопасности
Установку следует
помещать в вытяжной шкаф. Рабочее место оператора должно удовлетворять
требованиям электробезопасности по ГОСТ 12.1.019-79 и санитарно-гигиеническим
требованиям по ГОСТ 12.1.005-88.
(в ред. Изменения N 2, утв. Постановлением
Госстандарта СССР от 23.03.1989 N 608)
4.22. Метод экспериментального определения кислородного индекса
4.22.1. Аппаратура
Установка (черт.
20а) состоит из реакционной камеры - кварцевой трубки по ГОСТ 8680-73
внутренним диаметром не менее (75 +/- 1) мм и высотой (450 +/- 5) мм,
установленной вертикально на основании. Нижняя часть камеры на высоту 80 - 100
мм заполнена бусинами диаметром от 3 до 5 мм из стекла или другого материала
для обеспечения равномерной скорости газового потока по сечению камеры. Для
камеры диаметром от 75 до 100 мм при проведении испытаний с кислородно-азотной
смесью, концентрация кислорода в которой меньше 21%, следует использовать
колпачок, сужающее отверстие которого должно быть диаметром не более 40 мм;
держателя образца
любой конструкции для удерживания образца за основание в вертикальном положении
в центре камеры. Держатель снабжен проволочной сеткой с ячейками размером от 1
до 1,6 мм для улавливания частиц и капель, падающих с горящего образца;
двух ротаметров
типа РМ по ГОСТ 13045-81 с пределами измерения расхода газа до
;
трубопроводов с
клапанами для регулировки подаваемого в реакционную камеру газа;
рамки (черт. 20б)
для испытания пленочных и гибких листовых материалов;
источника зажигания
образца, представляющего собой горелку с выходным отверстием диаметром (2 +/-
1) мм. Топливом для горелки служит любой горючий газ, подачу которого
регулируют так, чтобы длина пламени была (16 +/- 4) мм при вертикальном
расположении горелки.
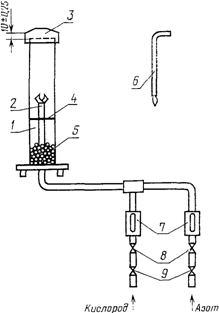
а)
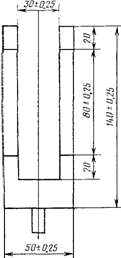
б)
1 - реакционная
камера; 2 - держатель образца;
3 - колпачок; 4 -
сетка; 5 - бусины; 6 - газовая горелка;
7 - ротаметры; 8, 9
- клапаны
Черт. 20
Секундомер по ГОСТ
5072-79, класс точности 3.
Азот газообразный
по ГОСТ 9293-74.
Кислород
газообразный технический по ГОСТ 5583-78.
4.22.2. Проведение
испытаний
Для испытаний
подготавливают не менее 15 образцов в форме брусков, размеры которых приведены
в табл. 20. Образцы должны характеризовать средние свойства исследуемого
материала.
Таблица 20
──────┬────────────────────────────────────────────┬──────────────
Форма
│ мм │Вид материала
образ-├─────────────┬──────────────┬───────────────┤
ца │
длина │ ширина
│ толщина │
│
├──────┬───────┼──────┬────────┤
│ │номин.│ пред.
│номин.│ пред. │
│ │ │ откл. │ │ откл. │
──────┼─────────────┼──────┼───────┼──────┼────────┼──────────────
I
│От 80 до 150 │
10 │+/- 0,5│ 4
│+/- 0,25│
Формованный
II
│От 80 до 150 │
10 │+/- 0,5│ 10
│+/- 0,5 │ Ячеистый
III
│От 80 до 150 │
10 │+/- 0,5│ <= 10,5 │
Листовой
IV
│От 70 до 150 │ 6,5
│+/- 0,5│ 3 │+/- 0,25│ Формованные
│ │ │ │ │ │и листовые
│ │ │ │ │ │материалы,
│ │ │ │ │ │используемые
│ │ │ │ │ │в электротех-
│ │ │ │ │ │нических
│ │ │ │ │ │устройствах
V
│ 140 +/- 0,5 │
52 │+/- 0,5│ <= 10,5 │
Гибкие
│ │ │ │ │пленки и листы
Поверхности
образцов не должны иметь трещин, сколов и других видимых дефектов.
На поверхность
образца наносятся метки: при испытании образцов формы I, II, III или IV по
методу А (зажигание верхнего торца образца) на расстоянии 50 мм от того конца
образца, который будет зажигаться;
при испытании
образцов формы I, II, III или IV по методу Б (зажигание верхнего торца и
боковой поверхности) на расстоянии 10 и 60 мм, а образцов формы V на расстоянии
20 и 100 мм от того конца, который будет зажигаться.
Метки наносят не
менее чем на две сопряженные поверхности.
Подготовленные
образцы подвергают кондиционированию в соответствии с требованиями ГОСТ
12423-66.
Калибруют систему
контроля скорости газового потока, обеспечивая точность измерения не менее чем
и контроль концентрации кислорода с помощью
химического газоанализатора или по стандартным кислородно-азотным смесям.
Калибровку проводят не менее одного раза в 6 мес.
Пригодность
установки к работе определяют измерением кислородного индекса контрольных
веществ, приведенных в табл. 21.
Таблица 21
─────────────────┬────────────────────────┬───────────────────────
Материал
│ Метод А │ Метод Б
├───────────┬────────────┼───────────┬───────────
│ пламенное │ тление
│ пламенное │ тление
│ горение
│ │ горение
│
─────────────────┼───────────┼────────────┼───────────┼───────────
Полипропилен
│ От 18,3 │
От 17,7 │ От 17,7
│ От 17,3
│ до 19,0
│ до 18,1 │
до 18,1 │ до 18,0
Полиметил-
│ │ │ │
метакрилат: │ │ │ │
толщина 3 мм
│ От 17,3 │
От 17,5 │ От 17,2
│ От 17,2
│
до 18,1 │ до 18,1
│ до 18,0 │
до 17,9
толщина 10 мм
│ От 17,9 │
От 17,8 │ От 17,5
│ От 17,5
│ до 19,0
│ до 18,7 │
до 18,5 │ до 18,6
Пленка ПВХ
│ │ │ │
толщина 0,02 мм│ -
│ - │
От 22,4 │ От 22,6
│ │ │ до 23,6
│ до 23,5
Испытания проводят
при температуре окружающего воздуха (23 +/- 2) °C и относительной влажности
воздуха (50 +/- 5)%.
Выбирают начальную
концентрацию кислорода в кислородно-азотной смеси. Величину начальной
концентрации кислорода оценивают на основе опыта работы с материалами,
аналогичными испытуемому. Если этого не удается сделать, то один из
приготовленных образцов сжигают на воздухе. При быстром горении образца
испытание начинают с концентрации кислорода, равной 18%. Если образец горит
медленно или неустойчиво, то начальная концентрация кислорода выбирается равной
21%. Если образец затухает на воздухе, то испытания начинают с концентрации
кислорода, равной 25%.
Образец
устанавливают вертикально в центре камеры таким образом, чтобы верхний торец
образца находился не менее чем на 100 мм ниже верхнего края камеры, а нижний
торец - не менее чем на 100 мм выше уровня бусинок.
Устанавливают
скорость газового потока через реакционную камеру равной (40 +/- 10)
. Перед
зажиганием каждого образца камеру следует продуть кислородно-азотной смесью
заданного состава в течение (30 +/- 2) с.
Зажигают
закрепленный образец, выбирая один из двух методов зажигания. Под зажиганием
понимают начало пламенного горения образца. Некоторые материалы могут гореть
без видимого пламени, например, в режиме тления. В протоколе испытаний в этом
случае необходимо делать соответствующую запись.
При использовании
метода зажигания А воздействуют пламенем горелки на верхний торец образца,
стараясь охватить пламенем всю площадь торца, при этом не касаясь пламенем
боковых поверхностей образца. Продолжительность зажигания составляет не более
30 с. Каждые 5 с горелку отстраняют от образца и оценивают площадь горения. При
охвате пламенем всего торца зажигание считают законченным.
При использовании
метода зажигания Б воздействуют пламенем горелки на верхний торец образца и его
боковые поверхности на расстоянии до 6 мм от верхнего торца. Продолжительность
зажигания составляет не более 30 с. Каждые 5 с горелку отстраняют от образца и
оценивают площадь горения. При распространении пламени до верхней метки
зажигание считают законченным.
Оценивают изменение
образца при горении, отмечая такие явления, как плавление и образование капель,
обугливание, неустойчивое горение, тление. Измеряют продолжительность горения
образца после зажигания и длину образца, по которой распространилось пламя.
Результат испытания считают положительным, если достигнуты критерии, указанные
в табл. 22.
Таблица 22
───────────────┬─────────┬────────────────────────────────────────
Форма образца │ Метод
│ Критерии
горения
│зажигания├──────────────────┬─────────────────────
│ │продолжительность │длина
распространения
│ │ горения, с │
пламени, мм
───────────────┼─────────┼──────────────────┼─────────────────────
I,
II, III, IV │ А │ 180 │
50 от верхнего
│ │ │торца образца
V
│ Б │ 180 │
80 ниже верхней
│ │ │метки
Испытанный образец
вынимают. Очищают камеру от твердых продуктов горения и охлаждают ее до
температуры (23 +/- 2) °C.
При испытании
следующего образца уменьшают концентрацию кислорода в газовой смеси, если
достигнут хотя бы один из критериев горения, указанных в табл. 22; увеличивают
концентрацию кислорода в газовой смеси, если ни один из критериев, указанных в
табл. 22, не достигнут.
Проводят
предварительные испытания с произвольным шагом изменения концентрации кислорода
в газовой смеси и определяют такие два значения концентрации кислорода,
различающиеся не более чем на 1%, при одном из которых выполняется хотя бы один
из критериев в табл. 22, а при другом ни один из указанных критериев не
выполняется. Из этих значений выбирают второе в качестве начального для
проведения серии основных испытаний.
Серия основных
испытаний проводится с контролируемой величиной шага d изменения концентрации
кислорода и заключается в нахождении такой концентрации, при которой происходит
изменение в характере горения образца в соответствии с критерием табл. 22, и в
статической оценке этой концентрации по малому числу испытаний с помощью метода
Диксона.
Начиная с
концентрации кислорода в газовой смеси, полученной в предварительных
испытаниях, испытывают один образец. Результат испытания записывают как X, если
удовлетворяется хотя бы один из критериев табл. 22, и как O в противоположном
случае. Полученное значение концентрации кислорода и результат испытания
являются первыми в серии испытаний
с контролируемым шагом. Используя шаг
изменения концентрации кислорода d, равный не менее 0,2% от общей газовой смеси
(т.е. уменьшая на d, если результат предыдущего испытания был X, и увеличивая
на d, если результат был O), испытывают серию образцов до тех пор, пока не
будет получен результат, отличающийся от результата первого испытания основной
серии. Полученные значения концентрации кислорода и результаты испытаний
составляют серию
. Затем
проводят еще пять испытаний, меняя концентрацию кислорода на d. Последнее
значение концентрации в серии основных испытаний обозначается как
, а все
результаты и соответствующие значения концентрации серии основных испытаний
записывают как
.
4.22.3. Обработка
результатов
Проверяют величину
шага изменения концентрации кислорода d,
-серии
в соответствии с условием
, (60)
где
- оценка стандартного отклонения концентрации
кислорода, рассчитываемая для последних шести испытаний в
-серии
(включая
) по
формуле
, (61)
где
- последовательные значения концентрации
кислорода, полученные в последних шести испытаниях
-серии;
КИ - кислородный
индекс, рассчитываемый по формуле (62), % об.;
n = 6.
Если условие
неравенства (60) не выполняется и
, то
повторяют испытания с увеличенным значением d до тех пор, пока не выполнится
условие (60). Если
, то
повторяют испытания с уменьшенным значением d до тех пор, пока не выполнится
условие (60) (при этом d не должно быть менее 0,2%, если нет специальных
требований на материал).
Если условия
неравенства (60) выполняются, то кислородный индекс рассчитывают по формуле
, (62)
где K - фактор,
выбираемый из табл. 23;
- окончательный шаг изменения концентрации
кислорода, выбранный в соответствии с условиями (60).
Значение K и его
математический знак зависят от результатов серии основных испытаний и могут
быть найдены из табл. 23 следующим образом:
Таблица 23
────────────┬───────────────────────────────────────┬─────────────
Результаты │ Значение K, для которых первыми │ Результаты
последних
│ результатами в серии
N являются │ последних
пяти
│
L │ пяти
испытаний,
├───────────────────────────────────────┤
испытаний,
начинающихся│ а │начинающихся
с X
├─────────┬─────────┬─────────┬─────────┤ с O
│ O
│ OO │
OOO │ OOOO
│
├─────────┴─────────┴─────────┴─────────┤
│ б │
├─────────┬─────────┬─────────┬─────────┤
│ X
│ XX │
XXX │ XXXX
│
────────────┼─────────┼─────────┼─────────┼─────────┼─────────────
1
│ 2 │
3 │ 4
│ 5 │
6
────────────┼─────────┼─────────┼─────────┼─────────┼─────────────
XOOOO
│ -0,55 │
-0,55 │ -0,55
│ -0,55 │
OXXXX
XOOOX
│ -1,25 │
-1,25 │ -1,25
│ -1,25 │
OXXXO
XOOXO
│ 0,37
│ 0,38 │
0,38 │ 0,38
│ OXXOX
XOOXX
│ -0,17 │
-0,14 │ -0,14
│ -0,14 │
OXXOO
XOXOO
│ 0,02 │
0,04 │ 0,04
│ 0,04 │
OXOXX
XOXOX
│ -0,50 │
-0,46 │ -0,45
│ -0,45 │
OXOXO
XOXXO
│ 1,17 │
1,24 │ 1,25
│ 1,25 │
OXOOX
XOXXX
│ 0,61 │
0,73 │ 0,76
│ 0,76 │
OXOOO
XXOOO
│ -0,30 │
-0,27 │ -0,26
│ -0,26 │
OOXXX
XXOOX
│ -0,83 │
-0,76 │ -0,75
│ -0,75 │
OOXXO
XXOXO
│ 0,83 │
0,94 │ 0,95
│ 0,95 │
OOXOX
XXOXX
│ 0,30 │
0,46 │ 0,50
│ 0,50 │
OOXOO
XXXOO
│ 0,50 │
0,65 │ 0,68
│ 0,68 │
OOOXX
XXXOX
│ -0,04 │
0,19 │ 0,24
│ 0,25 │
OOOXO
XXXXO
│ 1,60 │
1,92 │ 2,00
│ 2,01 │
OOOOX
XXXXX
│ 0,89 │
1,33 │ 1,47
│ 1,50 │
OOOOO
если первый
результат серии
был O, а первый результат серии из пяти
испытаний был X, то в графе 1 табл. 23 находят строку, значения которой
совпадают с результатами серии пяти испытаний. Значение K и его знак находят на
пересечении данной строки и одной из граф 2 - 5, для которой число O в
подзаголовке а соответствует числу О результатов в
-серии;
если первый
результат серии
был X, а первый результат серии из пяти
испытаний был O, то в графе 6 табл. 23 находят строку, значения которой
совпадают с результатами серии пяти испытаний. Значение K находят на
пересечении данной строки и одной из граф 2 - 5, для которой количество X в
подзаголовке б соответствует числу X результатов в
-серии.
Знак K в этом случае заменяется на противоположный.
Данный метод
определения КИ в состоянии обеспечить показатели точности, приведенные в табл.
24, для материалов, которые зажигаются без особых сложностей и спокойно горят.
Таблица 24
───────────────────────┬──────────────────────┬───────────────────
Приближенное значение │ Внутри лаборатории │Между лабораториями
на 95%-ном │ │
доверительном уровне │ │
───────────────────────┼──────────────────────┼───────────────────
Стандартное
отклонение │ 0,2 │ 0,5
Сходимость │ 0,5 │ -
Воспроизводимость │ - │ 1,4
4.22.4. Требования
безопасности
Установку для
определения кислородного индекса следует помещать в вытяжной шкаф или под
вытяжной зонт. Рабочее место оператора должно удовлетворять
санитарно-гигиеническим требованиям по ГОСТ 12.1.005-88.
(в ред. Изменения N 2, утв. Постановлением
Госстандарта СССР от 23.03.1989 N 608)
4.23. Метод экспериментального определения способности взрываться и
гореть при взаимодействии с водой, кислородом воздуха и другими веществами
4.23.1. Аппаратура
Электрический
сушильный шкаф вместимостью 4 дм3 с регулятором температуры, позволяющим
поддерживать постоянную температуру рабочей зоны от 40 до 200 °C с точностью
+/- 1 °C.
Термодинамический
преобразователь двухзонный, малоинерционный, типа ТХК по ГОСТ 6616-74,
диаметром термоэлектродов 0,5 мм.
Потенциометр типа
КСП-4 с градуировкой
,
диапазоном измерения температур от 0 до 200 °C, класса точности 0,5.
Фарфоровые тигли N
5 высокой формы по ГОСТ 9147-80.
Цилиндр мерный по
ГОСТ 1770-74 вместимостью 25 см3.
4.23.2. Проведение
испытаний
Перед проведением
испытаний устанавливают соответствие исследуемых веществ паспортным данным по
внешнему виду, плотности, коэффициенту рефракции, температурам кипения или
плавления входным контролем по ГОСТ 24297-87.
(в ред. Изменения N 2, утв.
Постановлением Госстандарта СССР от 23.03.1989 N 608)
Предварительные
испытания веществ на способность взрываться и гореть при взаимодействии с
другими веществами проводят путем контакта капли, кристаллика или небольшого
количества порошкообразного вещества с таким же количеством другого вещества
при комнатной температуре.
Если при этом
происходит энергичное взаимодействие (взрыв или самовоспламенение) веществ, то
такие вещества являются несовместимыми. Если при контакте малых количеств
веществ не происходит активного взаимодействия, то в последующих испытаниях
исследуют двухкомпонентные смеси испытуемых веществ в стехиометрическом
соотношении общим объемом до 20 см3. Для этого каждый из компонентов смеси
помещают в отдельный тигель. Тигли с исследуемыми образцами устанавливают в
термостат с заданной температурой испытания и выдерживают в течение 30 мин до
выравнивания температур исследуемых веществ и термостата. В тигель (в котором
будет производиться смешивание образцов) опускают один из рабочих концов
термоэлектрического преобразователя (другой рабочий конец измеряет температуру
внутри термостата) и вливают (всыпают) вещество из другого тигля. Смесь
перемешивают и по потенциометру наблюдают за показаниями термоэлектрического преобразователя
в течение 1 ч.
Если температура
смеси не повышается, то испытание прекращают. Для каждой смеси веществ проводят
не менее трех испытаний при температуре (20 +/- 2) °C, (50 +/- 2) °C и (100 +/-
2) °C.
Если при
температуре испытания вещество переходит в другое агрегатное состояние, то
испытание следует прекратить.
4.23.3. Обработка
результатов
Если температура
смеси в каждом испытании не повысилась более чем на 0,5 °C, то вещества считают
совместными с точки зрения пожарной безопасности и допускается их совместное
хранение.
Если температура
смеси хотя бы в одном испытании повысилась более чем на 0,5 °C, то для
окончательного вывода о совместимости определяют условия самовозгорания данных
смесей.
Условия и
результаты испытаний регистрируют в протоколе испытаний.
4.23.4. Требования
безопасности
Сушильный шкаф
следует устанавливать в вытяжном шкафу. Рабочее место оператора должно
удовлетворять санитарно-гигиеническим требованиям по ГОСТ 12.1.005-88.
(в ред. Изменения N 2, утв.
Постановлением Госстандарта СССР от 23.03.1989 N 608)
4.24. Методы экспериментального определения нормальной скорости
распространения пламени в газо-, паровоздушных смесях
4.24.1. Метод
оптимизации, применяемый для определения нормальной скорости в широком
диапазоне давлений и температур
4.24.1.1.
Аппаратура
Установка (черт.
21) состоит из сферической реакционной камеры вместимостью от 3 до 25 дм3.
Камера снабжена оптическим окном для наблюдения за процессом распространения
пламени, вентилятором или электронагревателем для конвективного перемешивания
смеси. На камере через клапан установлен манометр;
зажигающего
устройства, в качестве которого используют электроды с искровым промежутком от
0,5 до 2,5 мм. Выделяемая в искре энергия должна быть не более 0,1 Дж, а
длительность разряда не более 3 мс;
датчика давления
типа ДД-10 или аналогичного. Датчик давления через усилитель соединен с
осциллографом;
трубопроводов с
клапанами для подачи в камеру исследуемого вещества и воздуха;
пульта управления,
обеспечивающего синхронизацию момента зажигания смеси с началом регистрации
процесса распространения пламени;
хроматографа для
анализа состава исследуемой смеси;
вакуумного насоса,
обеспечивающего остаточное давление не более 1,0 кПа.
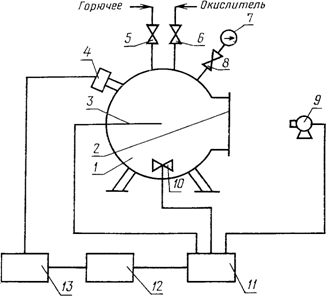
1 - реакционная
камера; 2 - смотровое окно; 3 - электроды
зажигания; 4 -
датчик давления; 5, 6, 8 - клапаны;
7 - манометр; 9 -
кинокамера; 10 - мешалка; 11 - пульт
управления; 12 -
осциллограф; 13 - усилитель
Черт. 21
4.24.1.2.
Проведение испытаний
Перед проведением
испытаний реакционную камеру проверяют на герметичность. Для этого при закрытом
клапане 5 вакуумируют реакционную камеру до остаточного давления 1,0 кПа и
перекрывают клапан 6. Если в течение 10 мин давление в сосуде повысится не
более чем на 0,1 кПа, установка считается герметичной.
Для приготовления
газовой смеси требуемого состава реакционную камеру вакуумируют до остаточного
давления 1,0 кПа. Затем поочередно в камеру подают компоненты смеси по
парциальным давлениям. Парциальное давление компонента рассчитывают по формуле
(16). После приготовления смесь перемешивают вентилятором в течение (5 +/- 1)
мин. Затем вентилятор отключают и через (5 +/- 1) мин проводят зажигание
горючей смеси зажигающим устройством, искровой промежуток которого расположен в
центре камеры.
Момент срабатывания
зажигающего устройства и изменение давления в камере от времени регистрируют
осциллографом, а процесс распространения пламени - кинокамерой.
С целью определения
максимального значения нормальной скорости для конкретного горючего вещества
испытания проводят на различных составах смеси, близких к стехиометрическому.
Испытание на
зажигание смеси, заданного состава, повторяют не менее пяти раз.
4.24.1.3. Обработка
результатов
Из
экспериментальной записи изменения давления от времени выбирают не менее пяти
значений
,
удовлетворяющих условию
, (63)
где
- начальное давление в камере, Па. Используют
также точку
(0), соответствующую моменту срабатывания
зажигающего устройства;
- давление, соответствующее точке перегиба
кривой изменения давления взрыва от времени, Па.
Расчетное значение
давления взрыва в камере получают интегрированием дифференциального уравнения
, (64)
в котором
, (65)
, (66)
где
- относительное давление;
p - текущее
расчетное давление в камере, Па;
- начальное давление в камере, Па;
t - время, с;
a - радиус камеры,
м;
,
- соответственно показатели адиабат смеси и
продуктов горения;
- относительная масса смеси в камере;
- текущее значение массы смеси, кг;
- начальное значение массы смеси, кг;
- относительное максимальное давление взрыва в
камере;
- максимальное давление взрыва в камере при
начальном давлении
, Па;
- текущее значение нормальной скорости
распространения пламени,
.
Радиус пламени
в метрах рассчитывают по формуле
. (67)
Зависимость
нормальной скорости от давления и температуры смеси принимают в виде
, (68)
где
- начальная скорость распространения пламени
при начальных давлении и температуре,
;
- текущее значение температуры смеси, K;
- начальная температура смеси в камере, K;
n - барический
показатель;
m - температурный
показатель.
В приближении
адиабатического сжатия смеси
, (69)
где
- термокинетический показатель.
Входящие в
расчетные формулы параметры
,
,
определяют термодинамическим расчетом. При
невозможности использования ЭВМ для решения уравнения (64) и отсутствии
расчетных значений
и
с целью упрощения вычисления могут проводиться
в приближении
, а
значение
может быть заимствовано из экспериментальных
данных.
Вид расчетной
зависимости p(t) определяется двумя неизвестными параметрами -
и
.
Сущность метода
оптимизации заключается в определении нормальной скорости (определение значений
и
согласно формуле (69)) посредством оптимизации
расчетной зависимости давления взрыва от времени в сферической камере
постоянного объема относительно экспериментальной записи давления.
Оптимизацию
расчетной зависимости изменения давления по экспериментальной осуществляют
минимизацией функционала
, (70)
где
- вектор-столбец неизвестных параметров
,
;
- экспериментальное относительное давление в
момент времени
;
- расчетное относительное давление в момент
времени
;
N - выбранное
количество точек экспериментальной зависимости давления от времени.
Минимизация
функционала (70) производится итеративно, причем
, (71)
где L - номер
итерации. Значение поправки
определяют при каждой итерации из выражения
, (72)
где
- матрица размерностью 2 x N;
- транспортированная матрица
;
- вектор-столбец размерностью N;
- матрица, обратная матрице
.
Транспонирование,
перемножение и обращение матриц осуществляется по стандартным процедурам,
имеющимся в библиотеках ЭВМ.
Итерационный
процесс прекращается при выполнении условия
, (73)
где
.
Элементы матрицы
определяются численным интегрированием
уравнения
(74)
с начальными
условиями
. В
уравнении (74) символ f использован для обозначения правой части уравнения
(64). Для определения элементов вектор-столбца
необходимо численно интегрировать уравнение
(64).
Дальнейшая
минимизация функционала (70) осуществляется варьированием начальной точки
отсчета времени. Для этого интегрирование уравнений (64) и (74) производят с
момента времени, лежащего в интервале +/- 20 мс относительно момента
срабатывания зажигающего устройства. В результате определяют момент времени t*,
которому соответствует минимальное значение функционала (70). Найденное при
этом значение
является искомым.
Доверительный
интервал значений определенных параметров находится по формуле
, (75)
где m, n = 1, 2
(индекс 1 соответствует параметру
,
индекс 2 - параметру
);
- m-ый элемент n-го собственного вектора
матрицы
;
- диагональная матрица, m-й диагональный
элемент которой равен
;
- m-ый диагональный элемент матрицы
;
- n-ое собственное значение матрицы
;
K = 2 - количество
параметров, по которым проводится оптимизация;
- табулированные значения критерия Фишера;
- доверительная вероятность;
- дисперсия экспериментальных данных.
Дисперсия
экспериментальных данных определяется по формуле
. (76)
Контроль
правильности определения нормальной скорости распространения пламени методом
оптимизации осуществляется сравнением экспериментальной и расчетной
зависимостей радиуса пламени от времени. Метод применим в условиях
пренебрежения конвекцией, когда число Фруда
.
, (77)
где
- видимая скорость пламени,
;
g - ускорение силы
тяжести,
;
d - диаметр камеры,
м.
Аналогичная
процедура определения
и
выполняется для серии испытаний. По полученным
результатам определяют среднеарифметические значения
и
и среднеквадратичные отклонения для данных
параметров.
Условия и
результаты испытаний регистрируют в протоколе испытаний.
4.24.1.3.1. Для
определения значений нормальной скорости в широком диапазоне давлений и
температур проводят серии испытаний, отличающиеся начальным давлением
. Для
каждой серии испытаний определяют значения
,
и изменение нормальной скорости в течение
взрыва по формуле (68). Температура смеси изменяется в течение взрыва по закону
. (78)
Используя формулы
(69), (78), строят серию изотерм на графике
.
Первую изотерму
строят по точкам
, где
значения
- заданы, а
- определены методом оптимизации. Для
построения следующих изотерм
по формуле (78) определяют относительное
давление
и давление
, при
котором температура смеси равна выбранному значению
с различным начальным давлением. Определив
значение
по формуле (69), находят значение нормальной
скорости
в каждом испытании, т.е. при одинаковой
температуре
и различных давлениях p.
4.24.1.4.
Требования безопасности
Реакционную камеру
следует устанавливать в вытяжном шкафу. Пульт управления и реакционную камеру
следует располагать в отдельных помещениях. Рабочее место оператора должно
удовлетворять требованиям электробезопасности по ГОСТ 12.1.019-79 и
санитарно-гигиеническим требованиям по ГОСТ 12.1.005-88.
(в ред. Изменения N 2, утв.
Постановлением Госстандарта СССР от 23.03.1989 N 608)
4.24.2. Метод
начального участка, применяемый для определения одиночных значений нормальной
скорости
4.24.2.1.
Аппаратура
Описание установки
приведено в п. 4.24.1.1.
4.24.2.2.
Проведение испытаний
Испытания
проводятся согласно п. 4.24.1.2.
4.24.2.3. Обработка
результатов
Результаты
испытаний обрабатывают по начальному участку фоторегистрации распространения
сферического пламени (в условиях пренебрежения конвекций согласно п. 4.24.13).
Нормальную скорость
распространения пламени
определяют при начальных значениях давления и
температуры в камере, используя только экспериментальные данные. Расчет
производят по формуле
, (79)
где
- видимая скорость распространения пламени,
;
- коэффициент расширения продуктов горения при
начальных значениях давления и температуры;
- максимальное давление взрыва в камере при
начальном давлении
.
Значение
определяют по кинограмме распространения
сферического пламени на начальном участке (до 1/3 радиуса камеры) по углу
наклона прямой, выражающей зависимость радиуса пламени от времени
распространения пламени.
Значение
коэффициента расширения продуктов горения
определяют по экспериментальным данным -
начальному
и максимальному давлению взрыва
в камере (по записи давления взрыва на
осциллограмме). Допускается определять
расчетным путем.
Разность двух
последовательных результатов, полученных одним и тем же оператором при
постоянных условиях испытания с вероятностью 0,95, не должна быть более
при условии, что случайные погрешности
преобладают над неисключенными систематическими.
Условия и
результаты испытаний регистрируют в протоколе испытаний.
4.24.2.4.
Требования безопасности
Требования
безопасности соответствуют п. 4.24.1.4.
4.24.3. Метод
горелки, применяемый для определения нормальной скорости пламени в газовых
смесях с добавками твердых или жидких частиц
4.24.3.1.
Аппаратура
Установка (черт. 22)
по шлирен-фотографированию конуса пламени на срезе сопла горелки включает в
себя систему подачи окислителя и горючего и оптическую систему
шлирен-фотографирования. Система подачи состоит из смесителя и линий подачи
горючего и окислителя, содержащих осушители, расходомеры, регулировочные и
редукционные клапаны. Сопло горелки снабжено рубашкой водяного охлаждения.
Оптическая система состоит из фотокамеры с фотопленкой и объективом,
проволочки, линз, щели и источника излучения.
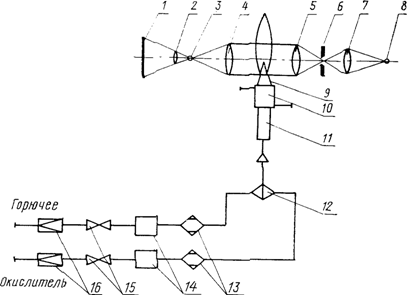
1 - фотопленка; 2 -
объектив фотокамеры; 3 - проволочка;
4, 5, 7 - линзы; 6
- щель; 8 - источник излучения;
9 - сопло горелки;
10 - рубашка охлаждения сопла горелки;
11 - горелка; 12 -
смеситель; 13 - осушители;
14 - расходомеры;
15 - регулировочные клапаны;
16 - редукционные
клапаны
Черт. 22
4.24.3.2.
Проведение испытаний
Линзой 7 фокусируют
изображение источника 8 на щель 6. Линзой 5 создают параллельный пучок лучей
для просвечивания пламени и совместно с линзой 4 фокусируют изображение щели 6
на проволочку 3 таким образом, чтобы при отсутствии пламени свет от источника 8
не поступал на объектив фотокамеры 2. Объектив фотокамеры 2 и линза 4
фокусируют изображение конуса пламени на фотопленку 1. Прорезь щели 6 и
проволочку 3 располагают параллельно оси конуса пламени.
По показаниям
расходомеров 14 задают смесь требуемой концентрации и, зная площадь истечения
на срезе сопла, устанавливают скорость истечения горючей смеси. В поток газа за
смесителем подают с необходимым расходом диспергированную твердую или жидкую
фазу.
Осуществляют
зажигание смеси на срезе горелки.
Производят
шлирен-фотографирование конуса пламени.
4.24.3.3. Обработка
результатов
Нормальную скорость
пламени рассчитывают по формуле
, (80)
где W - скорость
истечения газа на срезе горелки,
;
- угол при вершине конуса пламени горелки.
Значение W
определяют по показаниям расходомеров, величину
определяют по шлирен-фотографии.
4.24.2.4. Техника
безопасности
Горелку следует
устанавливать под вытяжной вентиляцией. Рабочее место оператора должно
удовлетворять санитарно-гигиеническим требованиям по ГОСТ 12.1.005-76.
4.25. Метод экспериментального определения скорости выгорания
жидкостей
4.25.1. Аппаратура
Установка (черт.
23) состоит из прибора СВ - двух сообщающихся сосудов, выполненных из стекла ТС
по ГОСТ 21400-75.
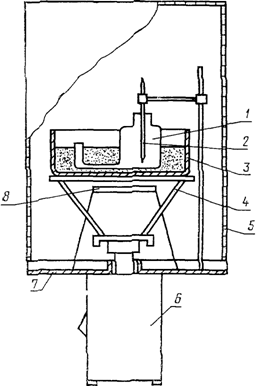
1 - прибор СВ; 2 -
термометр; 3 - металлический противень;
4 - кронштейн; 5 -
сетка; 6 - электрические весы;
7 - металлический
поддон; 8 - нагревательный элемент
Черт. 23
Один из них внутренним диаметром (10,0
+/- 0,2) мм, высотой (45 +/- 2) мм, толщиной стенки (1,0 +/- 0,1) мм служит
горелкой, другой внутренним диаметром (50 +/- 2) мм, высотой (60 +/- 2) мм
служит резервуаром для исследуемой жидкости. Сосуды сообщаются через
соединительную трубку длиной (25 +/- 2) мм, сплющенную по высоте (размеры
канала трубки 8 x 2 мм);
металлического
противня длиной (125 +/- 5) мм, шириной (75 +/- 5) мм, высотой (35 +/- 5) мм,
заполненного песком, в который устанавливают прибор СВ при испытании;
весов лабораторных
электрических квадратных с наибольшим пределом взвешивания 500 г, ценой деления
шкалы 100 мг;
металлического
поддона диаметром (300 +/- 10) мм, устанавливаемого сверху на корпус весов. По
центру поддона имеется отверстие диаметром (150 +/- 5) мм для чаши весов. По
периметру поддона установлена сетка высотой (600 +/- 10) мм, позволяющая
работать в вытяжном шкафу с включенной вентиляцией;
кронштейна, с
помощью которого противень с песком и прибором СВ устанавливаются на чашу
весов;
нагревательного
элемента со спиралью сопротивлением (0,9 +/- 0,1) Ом. Подаваемое на спираль
напряжение (12 +/- 2) В, сила тока (11 +/- 1) А;
термометра
лабораторного любого типа с пределом измерения от 0 до 200 °C с ценой деления
0,5 °C;
стеклянной
пластинки для гашения пламени горелки после испытания.
Секундомер по ГОСТ
5072-79, класс точности 3.
Алюминиевый экран
размером 120 x 120 мм, устанавливаемый между горелкой и резервуаром для
предупреждения перегрева и воспламенения жидкости в последнем.
Цилиндр мерный по
ГОСТ 1770-74 вместимостью 100 см3.
4.25.2. Проведение
испытаний
Перед испытанием
устанавливают соответствие исследуемой жидкости паспортным данным по внешнему
виду, плотности, коэффициенту рефракции и температуре кипения.
В резервуар прибора
СВ заливают исследуемую жидкость в количестве (60 +/- 10) см3 с таким расчетом,
чтобы уровень жидкости в горелке был на (2,5 +/- 0,5) мм ниже верхнего края
горелки. Уровень контролируется шаблоном.
На чашу весов с
помощью кронштейна устанавливают противень с песком и прибором СВ. Между горелкой
и резервуаром с исследуемой жидкостью ставят алюминиевый экран. В резервуар
опускают термометр, закрепленный в штативе. Нагревают жидкость до температуры
воспламенения и зажигают ее в горелке прибора СВ. Одновременно включают
секундомер и регистрируют через каждую минуту изменение массы жидкости.
Испытания продолжают не менее 15 мин, затем пламя тушат, накрыв горелку
стеклянной пластинкой. Испытания повторяют пять раз на том же образце, доливая
в резервуар жидкость до необходимого уровня.
Если после
испытания жидкость изменила цвет или верхняя часть горелки покрылась копотью,
то необходимо новый образец исследуемой жидкости залить в чистый прибор.
4.25.3. Обработка
результатов
Скорость выгорания
в килограммах на квадратный метр и минуту
рассчитывают по формуле
, (81)
где
- постоянная прибора,
;
d - внутренний
диаметр горелки, м;
m - масса жидкости,
сгоревшей к моменту времени
, кг;
- время горения жидкости, мин.
По полученным
данным строят кривую зависимости скорости выгорания исследуемой жидкости от
времени ее горения. За результат каждого испытания принимают максимальное
значение скорости выгорания (черт. 24).
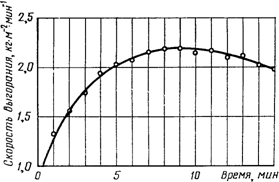
Черт. 24
За величину
скорости выгорания исследуемой жидкости принимают среднее арифметическое
максимальных значений скорости выгорания, полученных в пяти параллельных
испытаниях.
Линейную скорость
выгорания
в метрах на минуту рассчитывают по формуле
, (82)
где
- плотность жидкости,
.
Разность двух
последовательных результатов, полученных одним и тем же оператором при
постоянных условиях испытания с вероятностью 0,95, не должна быть более
при условии, что случайные погрешности
преобладают над неисключенными систематическими.
Условия и
результаты испытаний регистрируют в протоколе испытаний.
4.25.4. Требования
безопасности
Установку для
определения скорости выгорания жидкости следует помещать в вытяжной шкаф.
Рабочее место оператора должно удовлетворять требованиям электробезопасности по
ГОСТ 12.1.019-79 и санитарно-гигиеническим требованиям по ГОСТ 12.1.005-88.
(в ред. Изменения N 2, утв.
Постановлением Госстандарта СССР от 23.03.1989 N 608)
4.26. Метод экспериментального определения коэффициента
дымообразования твердых веществ
4.26.1. Аппаратура
Установка (черт.
25) состоит из камеры сгорания вместимостью
,
выполненной из листовой нержавеющей стали толщиной (2,0 +/- 0,1) мм. В камере
сгорания имеются верхнее и нижнее отверстия сечением 30 x 160 мм, соединяющие
ее с дымовой камерой. На боковой поверхности камеры сгорания расположено окно
из кварцевого стекла для наблюдения за образцом при испытании.
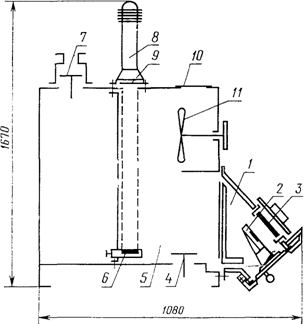
1 - камера
сгорания; 2 - держатель образца;
3 -
электронагревательная панель; 4, 7 - клапаны продувки;
5 - дымовая камера;
6 - фотоэлемент; 8 - осветитель;
9 - кварцевое
стекло; 10 - предохранительная мембрана;
11 - вентилятор
Черт. 25
Внутренняя
поверхность камеры теплоизолирована асбестовыми плитами типа асбосилит толщиной
от 18 до 20 мм и облицована алюминиевой фольгой толщиной 0,2 мм. В камере
сгорания установлены держатель образца и закрытая электронагревательная панель.
Электронагревательная панель размерами 120 x 120 мм смонтирована на верхней
стенке камеры и находится под углом 45° к горизонтали. Электроспираль панели
сопротивлением (28 +/- 0,5) Ом изготовлена из проволоки марки Х20Н80-Н по ГОСТ
12766.1-77 диаметром от 0,8 до 1,0 мм. Держатель образца выполнен в виде рамки
размерами 100 x 100 x 10 мм и закреплен на дверце камеры на расстоянии (60 +/-
1) мм от панели параллельно ее поверхности. В держатель устанавливают вкладыш
из асбосилита размерами 92 x 92 x 20 мм, в центре которого имеется углубление
для размещения образца. Углубление во вкладыше должно быть таким, чтобы
нагреваемая поверхность образца находилась на расстоянии (60 +/- 1) мм от
панели. Над держателем образца установлена газовая горелка, представляющая
собой трубку внутренним диаметром (2,0 +/- 0,1) мм. Высота пламени горелки от
10 до 12 мм. При испытании материалов в режиме горения пламя горелки касается
поверхности верхней части образца;
дымовой камеры
размерами 800 x 800 x 800 мм, выполненной из листовой нержавеющей стали
толщиной (2,0 +/- 0,1) мм. Внутренние стенки камеры оклеены черной бумагой или
покрыты черной матовой эмалью. В верхней стенке и в днище камеры имеются
отверстия для возвратных клапанов продувки, осветителя и предохранительной
мембраны. На боковой стенке камеры над верхним отверстием, соединяющим ее с
камерой сгорания, закреплен направляющий козырек, изолированный снизу
асбестокартоном и облицованный фольгой. На этой стенке установлен двухлопастный
вентилятор перемешивания дыма с частотой вращения не менее
. На
передней стенке камеры смонтирована дверца, имеющая по периметру уплотнение из
мягкой резины. Внутри камеры находится устройство для вертикального перемещения
фотоэлемента;
фотометрической
системы, состоящий из осветителя и фотоэлемента типа Ф-107 или Ф-25 по ГОСТ
2388-70. Осветитель должен обеспечить параллельность пучка света диаметром до
70 мм, фотоэлемент должен иметь характеристики, максимально приближенные к
спектральной чувствительности глаза человека. Фотоэлемент работает в блоке с
измерительным прибором люксметром, позволяющим измерять освещенность от 0 до 10
лк и от 0 до 100 лк. В качестве осветителя используют лампу накаливания
мощностью 100 Вт и напряжением 12 В или лазер типа ЛГ-78. Между осветителем и
дымовой камерой установлено защитное кварцевое стекло, нагреваемое
электроспиралью до температуры (130 +/- 10) °C;
термоэлектрического
преобразователя типа ТХА по ГОСТ 6616-74 среднеинерционного, обыкновенного,
диаметром электродов 0,5 мм, впаянного в центр медной пластины диаметром (12
+/- 1) мм, толщиной до 0,5 мм;
потенциометра типа
КСП-4 с градуировкой
,
диапазоном измерения температур от 0 до 1100 °C, класс точности 0,5;
регулятора
напряжения с максимальным током нагрузки 8 А, регулируемым (выходным)
напряжением до 240 В.
Весы лабораторные
общего назначения по ГОСТ 24104-88 с наибольшим пределом взвешивания 200 г,
класс точности 2.
(в ред. Изменения N 2, утв.
Постановлением Госстандарта СССР от 23.03.1989 N 608)
4.26.2. Проведение
испытаний
Для испытаний
изготавливают не менее десяти образцов исследуемого вещества шириной (40 +/- 1)
мм, длиной (40 +/- 1) мм и фактической толщиной, не превышающей 10 мм.
Отделочные и
облицовочные материалы, а также лакокрасочные и пленочные покрытия испытывают
нанесенными на ту же основу, которая принята в реальной конструкции. Если
область применения лаков и красок неизвестна, их испытывают нанесенными на
алюминиевую фольгу по ГОСТ 618-73 толщиной 0,2 мм.
Образцы перед
испытанием кондиционируют по ГОСТ 12423-66 при температуре (20 +/- 2) °C не
менее 48 ч. Образцы должны характеризовать средние свойства исследуемого
вещества (материала).
Испытания проводят
в двух режимах: термоокислительного разложения (тления) и пламенного горения.
Режим термоокислительного разложения (тления) обеспечивается при нагревании
поверхности образца до температуры (400 +/- 5) °C, при этом плотность теплового
потока равна (18 +/- 1)
.
Материалы, термостойкость которых выше 400 °C, испытывают при нагревании до 600
°C, плотность теплового потока равна (38 +/- 1)
. Во
всех случаях материалы не должны самовоспламеняться при испытании. Режим
пламенного горения обеспечивается при использовании газовой горелки и
нагревании поверхности образца до температуры (750 +/- 10) °C, при этом
плотность теплового потока равна (65 +/- 2)
.
Плотность теплового
потока измеряется с помощью датчика металлокалориметрического типа, описание
которого приведено в п. 4.27.1.
При наладке
установки определяют подаваемое на электронагревательную панель напряжение,
обеспечивающее указанные режимы испытания. Для чего вставляют в держатель
вкладыш с контрольным образцом из асбестоцемента по ГОСТ 4248-78 размерами 40 x
40 x 10 мм, в центре которого укреплен термоэлектрический преобразователь.
Дверцу камеры сгорания закрывают и подают напряжение на спирали
электронагревательной панели. Контроль стабилизированных условий нагревания
осуществляют с помощью потенциометра.
Перед проведением
испытаний проверяют исправность приборов, чистоту поверхности защитного стекла,
фотоэлемента и дымовой камеры.
При проведении
испытания в режиме пламенного горения вставляют в держатель вкладыш с
асбестоцементным образцом, закрывают обе камеры, подают на спирали
электронагревательной панели выбранное для данного режима напряжение, а также
подают напряжение на спираль, обогревающую защитное стекло. После выхода панели
на стабилизированные условия нагревания включают осветитель, измерительный
прибор люксметра, вентилятор перемешивания. Затем открывают камеру сгорания,
вынимают вкладыш с асбестоцементным образцом, зажигают газовую горелку, камеру
закрывают. Производят продувку дымовой камеры в течение 1 мин. Регулируют
диафрагмами осветитель, установив освещенность 100 лк и диаметр пучка света,
равный диаметру светочувствительной поверхности фотоэлемента. Показания
люксметра должны быть стабильными, допускается изменение освещенности не более
чем 0,5 лк за 1 мин.
Подготовленный
образец испытуемого материала устанавливают (при необходимости закрепляют) во
вкладыш, имеющий комнатную температуру, открывают дверцу камеры сгорания, без
задержки вставляют вкладыш в держатель и закрывают дверцу. Продолжительность
испытания определяется временем достижения минимальной освещенности, но не
более 15 мин.
По окончании
испытания включают вентилятор, открывают дверцу камеры сгорания, вынимают
вкладыш с остатками образца и закрывают дверцу. Дымовую камеру вентилируют до
полного удаления газообразных продуктов горения.
При испытании в
режиме термоокислительного разложения (тления) газовую горелку не зажигают,
устанавливают вкладыш с асбестоцементным образцом, подают соответствующее
напряжение на электронагревательную панель. Порядок проведения испытаний
аналогичен порядку, установленному для режима пламенного горения. В случае
самовоспламенения образца температуру испытания уменьшают с интервалом 50 °C.
Испытывают по пять
образцов исследуемого материала в каждом режиме.
С целью снижения
погрешности определения коэффициента дымообразования измерение минимальной
освещенности производят в диапазоне шкалы люксметра от 5 до 90 лк. Если эти
условия не выполняются для материалов с высокими значениями коэффициента
дымообразования, то уменьшают длину светового пути (положение фотоэлемента) или
ширину образца не более чем в два раза; для материалов с низкими значениями
коэффициента дымообразования увеличивают размер образца до 80 x 80 мм.
4.26.3. Обработка
результатов
По результатам
каждого испытания в режимах тления и пламенного горения коэффициент
дымообразования
в квадратных метрах - нипер на килограмм
рассчитывают по формуле
, (83)
где V - вместимость
дымовой камеры, м3;
L - длина светового
пути в задымленной среде, м;
m - масса образца
исследуемого материала, кг;
- оптическая плотность дыма, Нп;
E,
- соответственно начальная и минимальная
освещенность, лк.
Для каждой серии
испытаний рассчитывают среднее арифметическое не менее пяти значений
коэффициента дымообразования. За окончательный результат принимают наибольшее
значение из двух средних арифметических.
Классификация
материалов по дымообразующей способности приведена в п. 2.15.2.
Условия и результаты
испытаний регистрируют в протоколе испытаний.
4.26.4. Требования
безопасности
Установку для
определения коэффициента дымообразования необходимо помещать в вытяжной шкаф.
Рабочее место оператора должно удовлетворять требованиям электробезопасности по
ГОСТ 12.1.019-79 и санитарно-гигиеническим требованиям по ГОСТ 12.1.005-88.
(в ред. Изменения N 2, утв.
Постановлением Госстандарта СССР от 23.03.1989 N 608)
4.27. Метод экспериментального определения индекса распространения
пламени
4.27.1.
Аппаратура
Установка (черт.
26а) состоит из радиационной панели размерами 250 x 470 мм, нагреваемой горящим
газом или с помощью электроспирали. Газовая радиационная панель состоит из трех
горелок инфракрасного излучения. Для увеличения мощности радиации и уменьшения
влияния потоков воздуха перед панелью устанавливают сетку из жаростойкой стали.
Электрическая радиационная панель состоит из двух секций размерами 250 x 235
мм. Электроспираль изготавливают из проволоки марки Х20Н80-Н диаметром 1,2 мм
по ГОСТ 12766.1-77. Электрическое сопротивление спирали каждой секции (13,0 +/-
0,5) Ом. Радиационная панель укреплена на стойке высотой (2120 +/- 10) мм;
держателя образца,
включающего в себя подставку и рамку. Рамку изготавливают из листовой
жаростойкой стали толщиной (0,8 +/- 0,1) мм. На длинных рейках рамки (черт.
25б) нанесены деления через каждые (30,0 +/- 0,1) мм и пронумерованы участки от
нулевого до девятого сверху вниз;
вытяжного зонта с
размерами основания 360 x 360 мм и высотой (700 +/- 10) мм, установленного над
держателем образца на расстоянии (45 +/- 1) мм от верхней кромки радиационной
панели. Зонт изготовлен из тонколистовой стали;
термоэлектрического
преобразователя типа ТХА по ГОСТ 6616-74 поверхностного, обыкновенного,
среднеинерционного, диаметром электродов 0,5 мм, укрепленного в центре сечения
суженной части зонта на расстоянии (90 +/- 2) мм от его верхнего края;
газовой горелки,
установленной горизонтально между радиационной панелью и держателем образца на
расстоянии (8 +/- 1) мм от поверхности образца напротив середины нулевого
участка. Горелка представляет собой трубку из жаростойкой стали внутренним
диаметром (2,0 +/- 0,1) мм, имеющую со стороны держателя образца пять отверстий
диаметром 0,6 мм на расстоянии (20 +/- 1) мм друг от друга; на трубку надета
металлическая сетка N 04 по ГОСТ 3826-82. Длина пламени горелки должна быть
равной (11 +/- 1) мм.
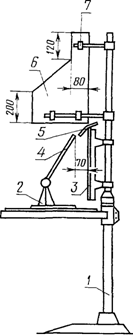
а)
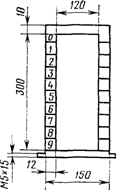
б)
1 - стойка; 2 -
подставка держателя образца;
3 - радиационная
панель; 4 - рамка держателя образца;
5 - газовая
горелка; 6 - вытяжной зонт;
7 -
термоэлектрический преобразователь
Черт. 26
Потенциометр типа
КСП-4 с градуировкой
,
диапазоном измерения температур от 0 до 400 °C, класса точности 0,5.
Секундомер по ГОСТ
5072-79, класс точности 3.
Образец
асбестоцементной плиты АЦЭИД 400 по ГОСТ 4248-78 длиной (320 +/- 2) мм, шириной
(140 +/- 2) мм, толщиной не более 10 мм.
Регулятор
напряжения с максимальным током нагрузки 8 А, регулируемым (выходным)
напряжением до 240 В.
4.27.2. Проведение
испытаний
Для испытаний
готовят пять образцов исследуемого материала длиной (320 +/- 2) мм, шириной
(140 +/- 2) мм, фактической толщиной, но не более 20 мм. Образцы должны
характеризовать средние свойства исследуемого вещества (материала). Отделочные
и облицовочные материалы, а также лакокрасочные и пленочные покрытия испытывают
нанесенными на ту же основу, которая принята в реальной конструкции.
Образцы перед
испытанием кондиционируют согласно требованиям ГОСТ 12423-66 при температуре
(20 +/- 2) °C не менее 48 ч.
Перед испытанием
образцов и проведением тарировки установки радиационную панель нагревают до
стационарной температуры, обеспечивающей плотность теплового потока на нулевом
участке образца (32 +/- 1)
, на
пятом участке (20 +/- 1)
, на
девятом участке (12,0 +/- 0,5)
.
Измерение плотности
падающего лучистого теплового потока производится с помощью датчика
металлокалориметрического типа. Датчик состоит из медной пластины (99,9% Cu)
размером 20 x 20 x 2 мм, закрепленной заподлицо в асбестоцементной плите
шириной 40 мм, толщиной 10 мм. Длина плиты принимается в зависимости от
размеров держателя образца, но не менее 40 мм. В плите под медной пластиной
делается углубление размером 18 x 18 x 4 мм. Лицевая сторона пластины покрыта
смесью ацетиленовой сажи и жидкого стекла. В центр пластины впаян
термоэлектрический преобразователь типа ТХК по ГОСТ 6616-74 обыкновенный,
поверхностный, малоинерционный, диаметром электродов 0,2 мм.
Величину плотности
теплового потока (q) в килоджоулях на квадратный метр и секунду рассчитывают по
формуле
, (84)
где m - масса
медной пластины, кг;
c - удельная
теплоемкость меди 0,39
;
- степень черноты поверхности медной пластины
0,95;
F - площадь
поверхности пластины, м2;
- повышение температуры датчика за время
, K;
- время нагрева медной пластины, если
не менее 5 K и не более 25 K, с.
Измерение теплового
потока производят после выхода радиационной панели на требуемый режим работы.
После измерения датчик охлаждают до комнатной температуры и закрепляют вместо
образца так, чтобы центральные части датчика и образца (или его отдельного
участка) совпадали. До начала измерений датчик находится вне зоны теплового
воздействия панели или экранируется.
При наладке
установки проводят ее тарировку с контролем не реже чем раз в 3 мес. Тарировка
установки заключается в определении теплового коэффициента установки
,
характеризующего количества тепла, подводимого к поверхности образца в единицу
времени и необходимого для повышения температуры дымовых газов на 1 °C. Для
этого в рамке держателя закрепляют образец асбестоцементной плиты, рамку
устанавливают под углом 30° к радиационной панели так, чтобы расстояние между
верхним краем рамки и металлической сеткой панели составляло не менее 70 мм.
Через 15 мин отмечают начальную температуру дымовых газов
.
Затем к образцу на уровне 1/2 его высоты подносят зажженную газовую горелку с
размером выходного отверстия 40,0 x 0,5 мм, обеспечивающую выделение теплоты со
скоростью (3,1 +/- 0,3)
.
Плоскость выходного отверстия горелки устанавливают параллельно поверхности
асбестоцементного образца и на расстоянии не менее 10 мм от нее. Через 10 мин
отмечают установившуюся температуру дымовых газов
.
Коэффициент
в килоджоулях на секунду и градус Цельсия
рассчитывают по формуле
, (85)
где
- удельная теплота сгорания газа,
,
определяемая по ГОСТ 10062-75;
Q - расход газа
газовой горелки,
.
В качестве
теплового коэффициента установки принимают среднее арифметическое результатов
пяти тарировочных испытаний.
Перед испытанием
каждого материала определяют начальную температуру
точно так, как при тарировке установки.
Образец исследуемого материала закрепляют в рамке держателя и делают на нем
отметки, соответствующие рискам на рамке держателя. Рамку с образцом
устанавливают перед нагретой радиационной панелью точно так, как при тарировке.
Материалы толщиной до 10 мм испытывают с подложкой из асбестоцементной плиты
толщиной 10 мм.
В процессе
испытания определяют:
время от начала
испытания до момента прохождения фронтом пламени нулевой отметки,
, с;
время
, в
течение которого фронт пламени проходит i-ый участок поверхности образца (i =
1, 2,... 9), с;
расстояние l, на
которое распространился фронт пламени, мм;
максимальную
температуру дымовых газов
, °C;
время от начала
испытания до достижения максимальной температуры
, с.
Испытание длится до
момента прекращения распространения пламени по поверхности образца или
достижения максимальной температуры дымовых газов, но не более 10 мин.
После испытания
каждого материала производят очистку рабочего конца термоэлектрического
преобразователя от сажи.
После испытания
десяти материалов производят очистку от сажи внутренней поверхности вытяжного
зонта.
4.27.3. Обработка
результатов
Для каждого образца
рассчитывают индекс распространения пламени (J) по формуле
, (86)
где 0,0115 -
размерный коэффициент,
;
0,2 - размерный
коэффициент,
.
В качестве индекса
распространения пламени исследуемого материала принимают среднее арифметическое
пяти значений индекса, полученных при параллельных испытаниях образцов.
Классификация
материалов, лакокрасочных покрытий и тканей по величине индекса распространения
пламени приведена в п. 2.16.2.
Условия и
результаты испытаний регистрируют в протоколе испытаний.
4.27.4. Требования
безопасности
Во время испытаний
материалов и тарировки установки следует включать принудительную вентиляцию
помещения, при этом скорость воздушного потока не должна быть более
.
Рабочее место оператора должно удовлетворять требованиям электробезопасности по
ГОСТ 12.1.019-79 и санитарно-гигиеническим требованиям по ГОСТ 12.1.005-88.
(в ред. Изменения N 2, утв.
Постановлением Госстандарта СССР от 23.03.1989 N 608)
4.28. Метод экспериментального определения показателя токсичности
продуктов горения полимерных материалов
4.28.1. Аппаратура
Установка (черт.
27) состоит из камеры сгорания вместимостью не менее
м3, выполненной из нержавеющей стали толщиной
(2,0 +/- 0,1) мм. Внутренняя поверхность камеры теплоизолирована
асбестоцементными плитами типа АЦЭИД 400 по ГОСТ 4248-78 толщиной (20 +/- 1) мм
и облицована алюминиевой фольгой по ГОСТ 618-73 толщиной 0,15 - 0,20 мм. На
верхней стенке камеры под углом 45° к горизонтали установлена
электронагревательная панель размерами 120 x 120 мм, нагреваемая
электроспиралью сопротивлением (28,0 +/- 0,5) Ом. Спираль изготовлена из
проволоки марки Х20Н80-Н по ГОСТ 12766.1-77 диаметром (0,9 +/- 0,1) мм. В
камере сгорания на ее дверце укреплен держатель образца, выполненный из
листовой жаростойкой стали в виде рамки размерами 100 x 100 x 10 мм, в которой
закреплен поддон из асбестоцемента. Поддон имеет углубление для фиксированного
размещения асбестоцементного вкладыша с образцом испытуемого материала.
Нагреваемая поверхность держателя образца и поверхность электронагревательной
панели параллельны, расстояние между ними равно (60 +/- 1) мм. Над держателем
образца расположена газовая горелка внутренним диаметром (2,0 +/- 0,1) мм таким
образом, что при испытании ее пламя длиной от 10 до 12 мм касается поверхности
верхней части образца.
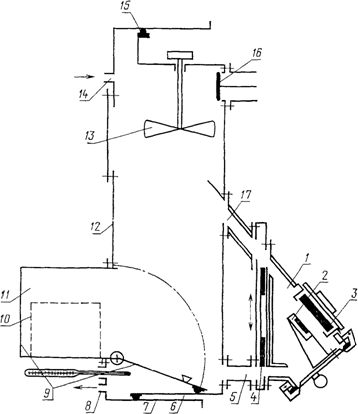
1 - камера
сгорания; 2 - держатель образца;
3 -
электронагревательная панель; 4 - заслонки;
5, 17 - переходные
рукава; 6 - стационарная секция
экспозиционной
камеры; 7 - подвижная секция экспозиционной
камеры; 8, 14 -
штуцера; 9 - дверцы предкамеры; 10 - клетка
для подопытных
животных; 11 - предкамера;
12 -
предохранительная мембрана; 13 - вентилятор;
15 - резиновая
прокладка; 16 - клапан продувки
Черт. 27
На боковой
поверхности камеры сгорания имеется окно из кварцевого стекла для наблюдения за
образцом при испытании;
экспозиционной
камеры, соединенной с камерой сгорания переходными рукавами с заслонками. Длина
верхнего рукава (250 +/- 5) мм, нижнего - (180 +/- 5) мм, проходные сечения рукавов
(160 x 40) мм и (160 x 30) мм соответственно. Внутренняя поверхность верхнего
рукава облицована асбестоцементом. Экспозиционная камера состоит из
стационарной и подвижной секций. По периметру стационарной секции имеется паз
для надувной резиновой прокладки с рабочим давлением до 6000 кПа. В верхней
части камеры находится четырехлопастный вентилятор перемешивания мощностью (100
+/- 2) Вт с частотой вращения
.
Кроме того, камера снабжена предохранительной мембраной из алюминиевой фольги
толщиной 0,3 мм, клапаном продувки, штуцерами для присоединения газоанализатора
и ввода термометра. Перемещением подвижной секции изменяют вместимость
экспозиционной камеры от 0,1 до 0,2 м3;
предкамеры
вместимостью
, м3,
оборудованной наружной и внутренней дверцами и смотровым окном. В предкамеру
помещают клетку с подопытными животными;
термоэлектрического
преобразователя типа ТХА по ГОСТ 6616-74 обыкновенного, среднеинерционного,
диаметром электродов 0,5 мм, впаянного в центр медной пластины диаметром (12
+/- 1) мм, толщиной до 0,5 мм;
потенциометра типа
КСП-4 с градуировкой
,
диапазоном измерения температур от 0 до 1100 °C, класс точности 0,5;
термометра
лабораторного любого типа с диапазоном измерения от 0 до 50 °C для измерения
температуры в нижней части экспозиционной камеры;
автоматических
газоанализаторов для непрерывного контроля состава газовоздушной среды в
экспозиционной камере;
регулятора
напряжения с максимальным током нагрузки 8 А, регулируемым (выходным)
напряжением до 240 В.
Весы лабораторные
общего назначения по ГОСТ 24104-88 с наибольшим пределом взвешивания 200 г,
класс точности 2.
(в ред. Изменения N 2, утв.
Постановлением Госстандарта СССР от 23.03.1989 N 608)
4.28.2. Проведение
испытаний
Образцы должны
характеризовать средние свойства исследуемого вещества (материала). Для
испытаний готовят не менее десяти образцов длиной (60 +/- 1) мм, шириной (60
+/- 1) мм и фактической толщиной, не превышающей 10 мм. Подготовленные образцы
кондиционируют в соответствии с требованиями ГОСТ 12423-66 в лабораторных
условиях не менее 48 ч и затем взвешивают.
Испытания проводят
в двух режимах: термоокислительного разложения (тления) при температуре
поверхности образца (400 +/- 5) °C (плотность теплового потока (18 +/- 1)
) и
пламенного горения при температуре поверхности образца (750 +/- 10) °C
(плотность теплового потока (65 +/- 2)
) с
зажженной газовой горелкой. Первый режим горения обеспечивается при напряжении
на спирали электронагревательной панели (135 +/- 5) В, второй - при напряжении
(200 +/- 5) В.
В предварительных
испытаниях определяют для каждого материала температурный режим, способствующий
выделению более токсичных продуктов горения. Для герметизации камеры нагнетают
воздух в надувную прокладку, вставляют в держатель образца вкладыш с контрольным
образцом из асбестоцемента по ГОСТ 4248-78 размерами 60 x 60 x 10 мм. На
центральном участке нагреваемой поверхности образца закрепляют
термоэлектрический преобразователь. Закрывают заслонки переходных рукавов и
внутреннюю дверцу предкамеры, выводят установку на режим пламенного горения.
После выхода
электронагревательной панели на стационарный режим открывают заслонки
переходных рукавов и дверцу камеры сгорания. Вынимают вкладыш с контрольным
образцом и термоэлектрическим преобразователем, зажигают газовую горелку.
Устанавливают в держатель вкладыш с образцом исследуемого материала. После
воспламенения образца газовую горелку немедленно отключают.
Продолжительность
горения образца определяют по времени достижения максимальных значений
концентрации окиси и двуокиси углерода в экспозиционной камере или принимают
равным (15,0 +/- 0,5) мин. Затем закрывают заслонки переходных рукавов и
включают вентилятор перемешивания. Клетку с животными помещают в предкамеру,
наружную дверцу которой закрывают.
После снижения
температуры газов в нижней части экспозиционной камеры до 30 °C открывают
внутреннюю дверцу предкамеры и фиксируют время начала экспозиции животных.
Экспозицию проводят в течение (30,0 +/- 0,5) мин при концентрации кислорода не
менее 16%. В каждом испытании используют десять белых мышей массой по (20 +/-
2) г.
По истечении
времени экспозиции открывают клапан продувки, заслонки переходных рукавов,
наружную дверцу предкамеры, включают вентилятор и вентилируют установку в
течение (10 +/- 1) мин. Регистрируют число погибших животных и характерные
признаки интоксикации.
Испытания в режиме
термоокислительного разложения (тления) проводят при температуре (400 +/- 5)
°C, при этом газовую горелку не зажигают. Термостойкие материалы испытывают при
температуре (600 +/- 5) °C (плотность теплового потока (38 +/- 1)
). В
случае самовоспламенения образца температуру испытания уменьшают с интервалом
50 °C.
Критерием выбора
режима основных испытаний служит наибольшее число летательных исходов в
сравниваемых группах подопытных животных.
При выбранном
температурном режиме в основных испытаниях находят ряд значений зависимости
летальности животных от величины отношения массы образца к вместимости
экспозиционной камеры. Для получения токсических эффектов меньше и больше
уровня летальности 50% изменяют вместимость экспозиционной камеры, оставляя
постоянными размеры образца исследуемого материала.
При определении
токсического эффекта учитывают гибель животных, наступившую во время
экспозиции, а также в течение последующих 14 сут.
В зависимости от
состава материалов при анализе их продуктов горения определяют количество окиси
и двуокиси углерода, цианистого водорода, акрилонитрила, хлористого водорода,
бензола, окислов азота, альдегидов и других веществ. Для оценки вклада окиси
углерода в токсический эффект измеряют содержание карбоксигемоглобина в крови
подопытных животных.
Если масса образца
принятых размеров (60 x 60) мм не позволяет выявить необходимый режим испытаний
или получить эффекты меньше и больше уровня летальности 50%, допускается
уменьшить размеры образца до (20 x 60) мм или увеличить их до (80 x 80) мм и
толщину до 20 мм.
4.28.3. Обработка
результатов
Полученный ряд
значений зависимости летальности от массы материала используют для расчета
показателя токсичности
.
Расчет проводится с помощью пробит-анализа или других способов расчета средних
смертельных доз и концентраций.
Классификация
материалов по величине показателя токсичности продуктов горения приведена в п.
2.17.2.
Если значение
близко к граничному значению двух классов, то
при определении степени опасности материала принимают во внимание режим
испытания, данные о составе продуктов горения, сведения о токсичности
обнаруженных соединений.
При содержании
карбоксигемоглобина в крови подопытных животных 50% и выше считают, что
токсический эффект продуктов горения обуславливается, в основном, действием
окиси углерода.
Условия и
результаты испытаний регистрируют в протоколе испытаний.
4.28.4. Требования
безопасности
Помещение, в
котором проводят испытания по определению токсичности продуктов горения, должно
быть оборудовано приточно-вытяжной вентиляцией. Необходимо обеспечить вытяжку
из экспозиционной камеры установки. Рабочее место оператора должно
удовлетворять требованиям электробезопасности по ГОСТ 12.1.019-79 и
санитарно-гигиеническим требованиям по ГОСТ 12.1.005-88.
(в ред. Изменения N 2, утв.
Постановлением Госстандарта СССР от 23.03.1989 N 608)
4.29. Метод экспериментального определения минимального взрывоопасного
содержания кислорода и минимальной флегматизирующей концентрации флегматизатора
в газо-, паровоздушных смесях
4.29.1. Аппаратура
Экспериментальное
определение минимального взрывоопасного содержания кислорода и минимальной
флегматизирующей концентрации флегматизатора в газо-, паровоздушных смесях
осуществляется на установках, приведенных в пп. 4.11.1.1; 4.11.2.1.
4.29.2. Проведение
испытаний
Минимальное
взрывоопасное содержание кислорода в газо-, паровоздушных смесях при заданном
флегматизаторе определяют на образцах, характеризующих средние свойства
исследуемого вещества, в два этапа:
определение
минимальной флегматизирующей концентрации флегматизатора;
вычисление
минимального взрывоопасного содержания кислорода по найденной минимальной
флегматизирующей концентрации флегматизатора.
Для определения
минимальной флегматизирующей концентрации заданного газообразного
флегматизатора устанавливают зависимость концентрационных пределов
распространения пламени по газо-, паровоздушной смеси от концентрации в ней
изучаемого флегматизатора. Для чего применяют приведенные в п. 4.11 методы
определения концентрационных пределов распространения пламени. При этом в
вакуумированный сосуд последовательно подают по парциальным давлениям
исследуемый газ (пары исследуемой жидкости) и заданный флегматизатор, а затем
подают воздух до выравнивания давления в реакционном сосуде с атмосферным.
Изменяя концентрацию исследуемого вещества в смеси при неизменном соотношении
флегматизатора и воздуха, находят нижний и верхний пределы распространения
пламени исследуемого вещества при заданной концентрации флегматизатора. Затем
увеличивают на 2% концентрацию флегматизатора и снова находят нижний и верхний
пределы распространения пламени по смеси. Проводя аналогичные испытания,
находят такое значение концентрации флегматизатора, при котором нижний и
верхний пределы распространения пламени по исследуемой смеси сливаются на
графике в одну точку
(черт. 28). Концентрацию флегматизатора,
соответствующую точке
,
принимают за минимальную флегматизирующую концентрацию. Испытания с
концентрациями компонентов смеси, соответствующими точке
,
должны быть воспроизведены не менее трех раз.
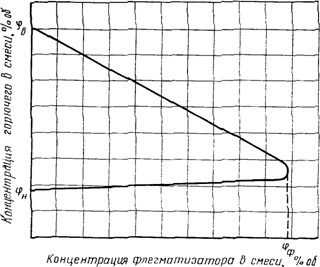
Черт. 28
4.29.3. Обработка
результатов
Минимальное
взрывоопасное содержание кислорода
в процентах рассчитывают по формуле
, (87)
где
- минимальная флегматизирующая концентрация
флегматизатора, % об.;
- концентрация водяного пара в воздухе, % об.
Разность двух
последовательных результатов, полученных одним и тем же оператором при
постоянных условиях испытания с вероятностью 0,95, не должны быть более 0,5%
при условии, что случайные погрешности преобладают над неисключенными систематическими.
Условия и
результаты испытаний регистрируют в протоколе испытаний.
4.29.4. Требования
безопасности
Установку для
проведения испытания следует помещать в специальный шкаф, оборудованный
вытяжной вентиляцией. Рабочее место оператора должно удовлетворять требованиям
электробезопасности по ГОСТ 12.1.019-79 и санитарно-гигиеническим требованиям
по ГОСТ 12.1.005-88.
(в ред. Изменения N 2, утв.
Постановлением Госстандарта СССР от 23.03.1989 N 608)
4.30. Метод экспериментального определения минимального взрывоопасного
содержания кислорода и минимальной флегматизирующей концентрации флегматизатора
в пылевоздушных смесях (аэровзвесях)
4.30.1.
Аппаратура
Установка (черт.
29) состоит из реакционного сосуда внутренним диаметром (105 +/- 5) мм, высотой
(450 +/- 5) мм, выполненного из нержавеющей стали марки 12Х18Н9Т по ГОСТ
5632-72 или другого коррозионно-стойкого материала. На расстоянии 1/2 высоты
сосуда имеются патрубок диаметром прохода от 20 до 60 мм для крепления датчика,
штуцер для отбора газовых проб. Сосуд рассчитан на давление (1000 +/- 10) кПа;
конусного
распылителя, который является верхней крышкой реакционного сосуда и выполнен из
того же материала, что и сосуд;
вихревой форкамеры
распылителя вместимостью от 100 до 200 см3;
обратного клапана с
условным диаметром прохода (5 +/- 1) мм, рассчитанного на давление до 2500 кПа;
клапана с
электроприводом любого типа с условным диаметром прохода (5 +/- 1) мм,
рассчитанного на давление не менее 980 кПа;
ресивера
вместимостью 1 дм3, рассчитанного на давление (1000 +/- 10) кПа. Ресивер
снабжен манометром;
смесителя -
герметичного цилиндрического сосуда вместимостью от 10 до 20 дм3, рассчитанного
на давление не менее 1000 кПа. Смеситель снабжен встроенной мешалкой с
электроприводом и штуцерами для подвода газов и крепления манометра;
источника
зажигания, в качестве которого используют накаленную до (1100 +/- 50) °C
электрическую спираль из проволоки марки Х80Н20-Н по ГОСТ 12766.1-77 диаметром
0,8 мм. Длина спирали (50 +/- 1) мм, внутренний диаметр (8,0 +/- 0,5) мм,
количество витков 30. Мощность, потребляемая спиралью при силе тока (13,0 +/-
0,5) А, составляет (475 +/- 25) Вт. В качестве контрольного источника зажигания
применяют пиротехнический воспламенитель типа ЭД-КЗ марки НК-10/15;
пуско-регулирующего
блока, в который входят - регулируемый источник питания электроспирали,
регистрирующий электронно-лучевой осциллограф, программное реле времени,
тензометрический усилитель, выбранный в соответствии с датчиком давления.
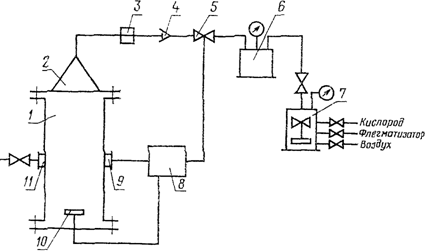
1 - реакционный
сосуд; 2 - конусный распылитель;
3 - вихревая
форкамера; 4 - обратный клапан; 5 - клапан
с электроприводом;
6 - ресивер; 7 - смеситель;
8 - пуско-регулирующий
блок; 9 - патрубок;
10 - источник
зажигания; 11 - штуцер
Черт. 29
Газоанализатор типа
"Газохром".
Весы лабораторные
общего назначения по ГОСТ 24104-88 с наибольшим пределом взвешивания 200 г,
класс точности 2.
(в ред. Изменения N 2, утв.
Постановлением Госстандарта СССР от 23.03.1989 N 608)
Вибрационное сито.
4.30.2. Проведение
испытаний
Перед проведением
испытаний устанавливают соответствие исследуемого вещества паспортным данным по
внешнему виду, влажности, зольности, дисперсности, а для плавящихся
органических веществ - дополнительно по температуре плавления входным контролем
по ГОСТ 24297-87. Проводят отсев частиц; при испытании используют пыли с
размером частиц менее 50 мкм для металлических веществ и менее 100 мкм для
других веществ.
(в ред. Изменения N 2, утв.
Постановлением Госстандарта СССР от 23.03.1989 N 608)
Проверяют
герметичность установки. Для чего в закрытый реакционный сосуд подают азот до
давления (1000 +/- 10) кПа. Если в течение 1 мин после прекращения подачи азота
падение давления составит не более (100 +/- 2) кПа, то герметичность установки
считают удовлетворительной.
Тарируют систему
измерения давления подачей азота в реакционный сосуд до давления (300 +/- 10)
кПа с интервалом 50 кПа, а затем сбрасыванием давления до нуля через те же
интервалы, фиксируя весь процесс с помощью осциллографа. По данным, снятым с
осциллограммы, строят тарировочный график зависимости отклонения луча
осциллографа от приращения давления, который должен представлять собой прямую
линию. В противном случае необходимо устранить неполадки в установке.
Определяют давление
"холостого" испытания установки
,
возникающее в реакционном сосуде от подачи распыляющего газа при включенном
источнике зажигания (время распыления 1 с, давление распыляющего газа в
ресивере (300 +/- 5) кПа).
Определение
минимального взрывоопасного содержания кислорода
состоит из предварительных и основных
испытаний. В серии предварительных испытаний находят такое количество
исследуемого вещества, при котором возникает наибольшее давление при
воспламенении образца в воздушной среде. Первое испытание начинают с образца
массой (0,50 +/- 0,01) г и постепенно увеличивают ее на (0,50 +/- 0,01) г. По
результатам испытаний строят кривую зависимости давления воспламенения от массы
образца. Массу образца, соответствующую максимуму этой зависимости, принимают
за оптимальную. Затем определяют минимальное взрывоопасное содержание кислорода
в его смеси с газообразным флегматизатором на
образцах оптимальной массы. Для чего в смеситель по парциальным давлениям
подают компоненты газовой смеси. В первом испытании концентрация кислорода в
смесителе равна его содержанию в воздухе нормального состава, а флегматизатор
подают в количестве, необходимом для создания в смесителе избыточного давления
450 кПа. Перемешивают газовую смесь в течение (5,0 +/- 0,1) мин и продувают ею
реакционный сосуд. Затем образец исследуемого вещества оптимальной массы
помещают в форкамеру распылителя, подают в ресивер из смесителя заготовленную
газовоздушную смесь до требуемого давления, включают источник зажигания и
распыляют образец. За воспламенение при этом принимают увеличение давления в
реакционном сосуде не менее чем на 10 кПа по сравнению с давлением
"холостого" испытания.
В зависимости от
результата первого испытания следующие испытания проводят соответственно с
увеличенной или уменьшенной на 1% концентрацией кислорода в газовой смеси.
После каждого испытания реакционный сосуд очищают от остатков пыли и продуктов
горения.
В серии
предварительных испытаний находят минимальную концентрацию кислорода, при
которой наблюдается воспламенение аэровзвеси, и максимальную концентрацию
кислорода, при которой воспламенение не происходит. Среднее арифметическое двух
этих величин принимают за минимальное взрывоопасное содержание кислорода
.
В серии основных
испытаний уточняют найденное значение
,
проводя испытания на воспламенение с образцами, отличающимися по массе от
оптимальной в меньшую и большую стороны на 0,2 г. С образцом, соответствующим
минимальному значению
,
следует получить не менее десяти последовательных отказов в испытаниях на
воспламенение.
4.30.3. Обработка
результатов
За минимальное
взрывоопасное содержание кислорода в аэровзвесях исследуемого вещества
принимают его минимальное значение, полученное в серии основных испытаний.
Минимальную
флегматизирующую концентрацию флегматизатора в процентах рассчитывают по
формуле
. (88)
Разность двух
последовательных результатов, полученных одним и тем же оператором при
постоянных условиях испытания с вероятностью 0,95, не должна быть более 0,5%
при условии, что случайные погрешности преобладают над неисключенными
систематическими.
Условия и
результаты испытаний регистрируют в протоколе испытаний.
4.30.4. Требования
безопасности
Установку для
определения минимального взрывоопасного содержания кислорода следует помещать в
специальный шкаф, оборудованный вытяжной вентиляцией. Рабочее место оператора
должно удовлетворять требованиям электробезопасности по ГОСТ 12.1.019-79 и
санитарно-гигиеническим требованиям по ГОСТ 12.1.005-88.
(в ред. Изменения N 2, утв.
Постановлением Госстандарта СССР от 23.03.1989 N 608)
4.31. Метод экспериментального определения максимального давления
взрыва и скорости нарастания давления при взрыве газов и паров жидкостей
4.31.1. Аппаратура
Установка (черт.
30) состоит из реакционного сосуда вместимостью 4 дм3, представляющего собой
две соединенные фланцами полусферы. Нижняя полусфера имеет термостатируемый
электронагреватель для проведения испытаний при повышенной температуре с
легкоконденсируемыми парами жидкостей. Реакционный сосуд должен быть рассчитан
на давление, которое не менее чем в два раза превышает максимальное давление
взрыва испытуемых смесей;
датчика давления с
верхним пределом измерения до 1000 кПа. Показания датчика давления фиксируются
электронно-лучевым осциллографом по ГОСТ 22737-77;
термоэлектрического
преобразователя типа ТХА по ГОСТ 6616-74 поверхностного, обыкновенного,
среднеинерционного, диаметром электродов 0,5 мм;
потенциометра типа
КСП-4 с градуировкой
,
диапазоном измерения температур от 0 до 400 °C, класс точности 0,5;
источника
зажигания, в качестве которого используют электроды с разрядным промежутком (5
+/- 1) мм или электрическую спираль. Электроды представляют собой проволоку из
нержавеющей стали по ГОСТ 5632-72 диаметром не менее 1 мм. Разрядный промежуток
электродов приходится на центр реакционного сосуда. Электрическая спираль
изготовлена из проволоки марки Х20Н80-Н по ГОСТ 12766.1-77 диаметром 0,3 мм и
длиной 30 мм; диаметр спирали не менее 5 мм. От источника питания на зажигающее
устройство подается напряжение: (3 +/- 1) кВ на электроды, (36 +/- 4) В на
спираль. Выделяемая энергия искр на электродах при длительности разряда от 1 до
2 с составляет от 30 до 40 Дж, температура накаленной спирали (1100 +/- 50) °C;
смесителя для
приготовления газо-, паровоздушной смеси, представляющего собой цилиндрический
сосуд вместимостью (20 +/- 5) дм3. Смеситель снабжен встроенной мешалкой с
электроприводом и штуцерами для подвода газов и крепления манометра. Смеситель
через кран сообщается с реакционным сосудом;
ртутного манометра
с ценой деления 0,1 кПа, соединенного через трехходовой кран с реакционным
сосудом;
вакуумного насоса,
обеспечивающего остаточное давление не более 0,6 кПа.
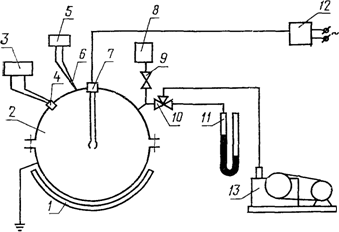
1 -
термостатируемый электронагреватель; 2 - реакционный
сосуд; 3 -
осциллограф; 4 - датчик давления;
5 - потенциометр; 6
- термоэлектрический преобразователь;
7 - источник
зажигания; 8 - смеситель; 9, 10 - краны;
11 - ртутный
манометр; 12 - источник питания;
13 - вакуумный
насос
Черт. 30
4.31.2. Проведение
испытаний
Устанавливают
соответствие исследуемого вещества паспортным данным входным контролем по ГОСТ
24297-87.
(в ред. Изменения N 2, утв.
Постановлением Госстандарта СССР от 23.03.1989 N 608)
Перед проведением
испытаний установку проверяют на герметичность. Для чего вакуумируют
реакционный сосуд при закрытом кране 9 до остаточного давления 0,6 кПа. Если в
течение 10 мин давление не повысится более чем на 0,2 кПа, установка считается
герметичной.
Тарируют систему
измерения давления подачей воздуха в реакционный сосуд до давления (1000 +/-
100) кПа с интервалом 50 кПа, а затем сбрасыванием давления до нуля через те же
интервалы, фиксируя весь процесс с помощью осциллографа. По данным, снятым с
осциллограммы, строят тарировочный график зависимости отклонения луча
осциллографа от приращения давления, который должен представлять собой прямую
линию.
Рассчитывают
стехиометрическую концентрацию исследуемого вещества. Для первого испытания
количество исследуемого вещества принимают равным 70% от рассчитанной
стехиометрической концентрации.
Для приготовления
газо-, паровоздушной смеси требуемого состава смеситель вакуумируют до
остаточного давления (0,5 +/- 0,1) кПа и затем поочередно подают в него
компоненты смеси по парциальным давлениям. Парциальное давление компонента
рассчитывают по формуле (16). После впуска компонентов включают мешалку и
перемешивают смесь в течение (6 +/- 1) мин. Реакционный сосуд вакуумируют до
остаточного давления (0,5 +/- 0,1) кПа, перепускают в него из смесителя заготовленную
газо-, паровоздушную смесь, перекрывают краны 9, 10 и зажигают смесь искрой или
спиралью. Результаты испытания регистрируются осциллографом. После взрыва
сбрасывают избыточное давление в атмосферу и два-три раза вакуумируют
реакционный сосуд для удаления газообразных продуктов горения.
Определение
максимального давления взрыва состоит из предварительных и основных испытаний.
В серии предварительных испытаний находят зависимость давления взрыва от
концентрации газа (пара) в смеси. Газо-, паровоздушную смесь, соответствующую
максимуму этой зависимости принимают за оптимальную.
В основных
испытаниях проводят серию из десяти испытаний с оптимальной газо-,
паровоздушной смесью и две серии из десяти испытаний со смесями, отличающимися
от оптимальной на 1 - 2% в большую и меньшую стороны.
4.31.3. Обработка
результатов
За величину
максимального давления взрыва исследуемой газо-, паровоздушной смеси принимают
наибольшее значение давления взрыва, полученное в трех сериях основных
испытаний.
Среднюю скорость
нарастания давления
в килопаскалях на секунду рассчитывают по
формуле
, (89)
где
- давление, возникающее в реакционном сосуде
при сгорании газо-, паровоздушной смеси, определяемое по осциллограмме
"давление - время", кПа;
- первоначальное давление в реакционном
сосуде, равное атмосферному давлению, кПа;
- время, в течение которого достигается
давление
, с.
Максимальную
скорость нарастания давления
в килопаскалях на секунду рассчитывают по
формуле
, (90)
где
- приращение давления, определяемое по
прямолинейному участку осциллограммы "давление - время" с помощью
тарировочного графика, кПа (черт. 31);
- время, в течение которого происходит приращение
давления
, с.
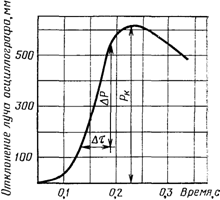
Черт. 31
За величины средней
и максимальной скоростей нарастания давления при взрыве исследуемой газо-,
паровоздушной смеси принимают их наибольшие значения, рассчитанные по
результатам основных испытаний.
Условия и
результаты испытаний регистрируют в протоколе испытаний.
4.31.4. Требования
безопасности
Установку следует
помещать в вытяжной шкаф. Рабочее место оператора должно удовлетворять
требованиям электробезопасности по ГОСТ 12.1.019-79 и санитарно-гигиеническим
требованиям по ГОСТ 12.1.005-88.
(в ред. Изменения N 2, утв.
Постановлением Госстандарта СССР от 23.03.1989 N 608)
4.32. Метод экспериментального определения максимального давления взрыва
и скорости нарастания давления при взрыве пылей
4.32.1. Аппаратура
Испытания
проводятся на установке, приведенной в п. 4.30.1.
4.32.2. Проведение
испытаний
Перед проведением
испытаний устанавливают соответствие исследуемого вещества паспортным данным по
внешнему виду, влажности, зольности, дисперсности, а плавящихся органических
веществ по температуре плавления входным контролем по ГОСТ 24297-87. Проводят
отсев вещества; при испытании используют пыли размером частиц менее 50 мкм для
металлических веществ и менее 100 мкм для других веществ.
(в ред. Изменения N 2, утв.
Постановлением Госстандарта СССР от 23.03.1989 N 608)
Проверяют
герметичность установки. Для чего в закрытый реакционный сосуд подают воздух до
давления (1000 +/- 10) кПа. Если в течение (1,0 +/- 0,1) мин после прекращения
подачи азота падение давления составит не более (100 +/- 2) кПа, то
герметичность установки считают удовлетворительной.
Тарируют систему
измерения давления подачей воздуха в реакционный сосуд до давления (800 +/-
100) кПа с интервалом 50 кПа, а затем сбрасыванием давления до нуля через те же
интервалы, фиксируя весь процесс с помощью осциллографа. По данным, снятым с
осциллограммы, строят тарировочный график зависимости отклонения луча
осциллографа от приращения давления, который должен представлять собой прямую
линию.
Определяют давление
"холостого" испытания установки
,
возникающее в реакционном сосуде от подачи распыляющего газа при включенном
источнике зажигания. Время распыления 1 с, давление распыляющего газа в
ресивере (300 +/- 5) кПа.
Определение
максимального давления взрыва состоит из предварительных и основных испытаний.
В серии предварительных испытаний находят оптимальную массу исследуемого
образца, при которой возникает наибольшее давление взрыва.
Последовательность
проведения испытания: взвешенный образец помещают в форкамеру распылителя,
подают в ресивер воздух до требуемого давления, устанавливают на
пускорегулирующем блоке продолжительность распыления, включают источник
зажигания и распыляют образец. За взрыв при этом принимают увеличение давления
в реакционном сосуде не менее чем на 10 кПа по сравнению с давлением
"холостого" испытания. После каждого испытания реакционный сосуд
продувают воздухом для удаления газообразных продуктов горения.
Первое испытание
начинают с образца массой (0,50 +/- 0,01) г, увеличивая ее в последующих
испытаниях на (0,20 +/- 0,01) г. По результатам испытаний строят кривую
зависимости давления взрыва от массы образца. Массу образца, соответствующую
максимуму этой зависимости, принимают за оптимальную.
Затем проводят
серию основных испытаний на десяти образцах оптимальной массы и по полученным
осциллограммам определяют давление взрыва.
4.32.3. Обработка
результатов
За величину
максимального давления взрыва пыли исследуемого вещества принимают наибольшее из
десяти значений давления взрыва, полученных в серии основных испытаний.
Среднюю скорость
нарастания давления
в килопаскалях на секунду рассчитывают по
формуле (89),
где
- давление, возникающее в реакционном сосуде
при сгорании пылевоздушной смеси, определяемое по осциллограмме "давление
- время", кПа;
- давление "холостого" и испытания,
кПа;
- время, в течение которого достигается
давление
, с.
Максимальную
скорость нарастания давления
в килопаскалях на секунду рассчитывают по
формуле (90).
За величины средней
и максимальной скоростей нарастания давления при взрыве пыли исследуемого
вещества принимают их наибольшие значения, рассчитанные по результатам основных
испытаний.
Условия и
результаты испытаний регистрируют в протоколе испытаний.
4.32.4. Требования
безопасности
Установку для
определения максимального давления взрыва следует помещать в специальный шкаф,
оборудованный вытяжной вентиляцией. Рабочее место оператора должно
удовлетворять требованиям электробезопасности по ГОСТ 12.1.019-79 и
санитарно-гигиеническим требованиям по ГОСТ 12.1.005-88.
(в ред. Изменения N 2, утв.
Постановлением Госстандарта СССР от 23.03.1989 N 608)
4.33. Метод расчета скорости нарастания давления при взрыве газов и
паров жидкостей
Метод заключается в
определении верхних границ для максимальной и средней скорости нарастания
давления при взрыве газов и паров жидкостей в сферической бомбе постоянного
объема.
Верхнюю границу для
максимальной скорости нарастания давления в килопаскалях на секунду
рассчитывают по формуле
, (91)
где
- начальное давление, кПа;
- нормальная скорость распространения пламени
при начальных давлении и температуре,
;
a - радиус бомбы,
м;
- безразмерное максимальное давление взрыва;
- максимальное давление взрыва, кПа;
- показатель адиабаты для испытуемой смеси;
- термокинетический показатель степени в
зависимости нормальной скорости распространения пламени от давления и
температуры.
Если значение
неизвестно, его принимают равным 0,4.
Верхнюю границу для
средней скорости нарастания давления в килопаскалях на секунду рассчитывают по
формуле
, (92)
где f
функция от параметров
,
,
,
значения которой находят с помощью номограмм, приведенных на черт. 32 и 33.
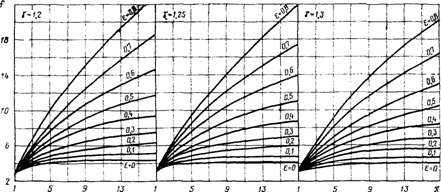
Черт. 32
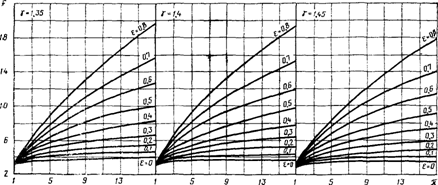
Черт. 33
Значения
и
находят термодинамическим расчетом или, в
случае невозможности расчета, принимают равными соответственно 9,0 и 1,4.
Пример. Рассчитать
максимальную и среднюю скорости нарастания давления при взрыве метана.
Исходные данные: a
= 1,825 м,
= 101 кПа,
= 291 K,
= 8,79,
= 1,39,
,
= 0,26.
Решение.
По формуле (91)
рассчитываем максимальную скорость нарастания давления:
.
С помощью номограмм
находим, что величина f
составляет 5,25. По формуле (92) рассчитываем среднюю скорость нарастания
давления:
.