Утверждены
Минмонтажспецстроем
СССР
27 марта 1985 года
ВЕДОМСТВЕННЫЕ СТРОИТЕЛЬНЫЕ НОРМЫ
МОНТАЖ ТЕХНОЛОГИЧЕСКОГО ОБОРУДОВАНИЯ
СТАЛЕПЛАВИЛЬНЫХ ЦЕХОВ
ВСН 396-85
Срок введения в
действие
1 января 1986 года
Внесены ГПИ Главметаллургмонтажем Минмонтажспецстроя СССР.
Утверждены
заместителем Министра монтажных и специальных строительных работ СССР К.К.
Липодатом 27 марта 1985 г.
Ведомственные
строительные нормы освещают вопросы организации, монтажа, выверки и
пусконаладочных работ оборудования сталеплавильных цехов. Рассмотрено
оборудование стационарных миксеров вместимостью 1300 и 2500 т, конвертеров
вместимостью 130 - 400 т, электросталеплавильных печей вместимостью 100 - 200
т, а также машин непрерывного литья заготовок МНЛЗ сортовых и слябовых типов.
Строительные нормы
разработаны с учетом новых нормативных документов, а также с учетом опыта монтажа
оборудования вышеперечисленных агрегатов. ВСН 396-85 выпускаются взамен ВСН
396-78 Минмонтажспецстроя СССР.
1. ОБЩИЕ
ПОЛОЖЕНИЯ
1.1. Настоящие
ведомственные строительные нормы распространяются на технологическое
оборудование сталеплавильных цехов и устанавливают требования к его монтажу и
индивидуальным испытаниям. Требования правил обязательны для проектных,
общестроительных и специализированных монтажных организаций, предприятий -
изготовителей оборудования в части относящихся к ним
требований.
1.2. Настоящие
правила разработаны в развитие требований главы СНиП 3.05.05-84 в части правил
монтажа технологического оборудования сталеплавильных цехов. Правила отражают
общие положения по монтажу основного оборудования сталеплавильных цехов и не
заменяют инструкций предприятий-изготовителей по монтажу конкретного
оборудования. Правила не распространяются на устройства, механизмы и системы
общего назначения (редукторы, муфты, системы смазки и другие), монтаж которых
выполняют в соответствии с требованиями специальных инструкций.
1.3. При
проектировании и производстве монтажных работ, помимо требований настоящих
правил, следует выполнять требования глав СНиП, стандартов и нормативных
документов, приведенных в обязательном приложении, а также требования
технической документации предприятий - изготовителей оборудования,
руководствоваться "Правилами о договорах подряда на капитальное строительство"
и "Положением о взаимоотношениях организаций генеральных подрядчиков с
субподрядными организациями".
1.4. Монтажные
работы должна выполнять специализированная организация, имеющая опыт монтажа
металлургического оборудования.
1.5. Основным
документом, определяющим организацию и последовательность строительно-монтажных
работ при сооружении сталеплавильных цехов, является проект организации
строительства (ПОС), разработанный в составе основного
проекта в соответствии с СН 47-74.
Технологическое
оборудование следует монтировать согласно проекту производства работ (ППР),
разработанному с учетом требований СНиП 3.05.05-84 и настоящих правил,
согласованному и утвержденному в установленном порядке.
1.6. На монтажную
площадку оборудование должно поступать в полном соответствии с ГОСТ 24444-80,
ОСТ 24.010.01-80 и техническими условиями на изготовление и поставку,
согласованными и утвержденными в установленном порядке. Нетранспортабельное
оборудование поставляют сборочными единицами, прошедшими на предприятии-изготовителе
полную контрольную сборку и испытания, имеющими монтажную маркировку,
обвязанными трубопроводами в объеме отгрузочных единиц и не требующими
доизготовления при монтаже.
1.7. Ревизию
оборудования производят в случае и порядке, оговоренных "Положением о
взаимоотношениях организаций - генеральных подрядчиков с субподрядными
организациями" и "Правилами о договорах подряда на капитальное
строительство".
1.8. Оборудование,
подлежащее монтажу, заказчики передают монтажной организации в соответствии со
СНиП 3.05.05-84 в зоне производства монтажных работ в полной исправности и в
сроки, предусмотренные согласованными сторонами графиком.
1.9. Монтажной
организации передается техническая документация в объеме, установленном СНиП
3.05.05-84, "Правилами о договорах подряда на капитальное
строительство", утвержденными Советом Министров СССР, и отраслевыми
стандартами соответствующих министерств.
1.10. Техническая документация на выполнение строительно-монтажных работ
должна быть выдана монтажной организации до 1 июля года, предшествующего
планируемому, и иметь отметку заказчика о принятии к производству работ.
Техническая
документация предприятий - изготовителей оборудования должна быть передана
заказчиком монтажной организации за 5 мес. до начала монтажных работ в соответствии
с ОСТ 24.010.01-80.
2.
ПОДГОТОВКА К ПРОИЗВОДСТВУ РАБОТ
2.1. К началу
производства работ по монтажу технологического оборудования генподрядчик должен
выполнить касающиеся его подготовительные работы согласно СНиП 3.05.05-84, а
также обеспечить питание электроэнергией по постоянной или временной схеме
технологических грузоподъемных средств и передаточных тележек, необходимых для
монтажа оборудования.
2.2. Монтажная
организация в период подготовки:
получает от
генподрядчика техническую и сметную документацию и обрабатывает ее;
выдает задание на
разработку ППР, рабочих чертежей металлоконструкций (КМД) и трубопроводов
(КТД);
обеспечивает
специализированную проектную организацию технической документацией согласно ВСН
319-77;
обобщает объемы
предстоящих работ;
проверяет
потребность в прокате, трубах, материалах и оформляет заявки на их получение;
размещает на
производственных базах и заводах заказы на изготовление трубопроводов и
металлоконструкций с учетом дополнительных технических требований;
комплектует объект
подъемно-транспортным и сварочным оборудованием, слесарным и
контрольно-измерительным инструментом;
принимает от
заказчика оборудование, а от генподрядчика - строительную готовность здания;
комплектует объект
рабочими, ИТР и организует их техническую учебу;
принимает по акту
технической готовности строительные конструкции для обеспечения работы мостовых
кранов;
увязывает рабочие
захватки, места складирования и пути подачи оборудования в монтажную зону с
производством работ по монтажу каркаса и встроенных помещений, а при
необходимости - работу стреловых или других кранов.
2.3. Фундаменты
здания и сооружения под монтаж оборудования принимают в соответствии с
требованиями СНиП 3.05.05-84, причем фундаменты принимают с установленными
фундаментными болтами или колодцами для болтов, плашками и реперами по
исполнительным схемам с указанием на них проектных и фактических размеров и
отметок.
Отклонения при
приемке фундаментных болтов не должны превышать размеров, приведенных в табл.
1.
Таблица 1
─────────────────────────────────────────────┬───────────────────
Отклонение │Размер допускаемого
│ отклонения, мм
─────────────────────────────────────────────┼───────────────────
От
плоскостности на длине фундамента до 60 м │ +/- 20
Размеров
(до 10 м), определяющих положение
│ +/- 5
фундаментных
болтов в плане │
Высотной
отметки болта
│ +20
От
вертикальности выступающей части болта
│ 1,5
Размеров
(до 10 м), определяющих положение
│ +20
осей
колодцев фундаментных болтов в плане
│
Размеров
(до 10 м), определяющих положения
│ +/- 10
осей
закладных деталей в плане
│
2.4. Расположение
плашек и реперов на фундаментах для фиксирования осей и высотных отметок,
необходимых для выверки оборудования сталеплавильных цехов, дается в схемах
геодезического обоснования, разрабатываемых организацией, проектирующей
фундаменты под оборудование на основании строительных заданий предприятий -
изготовителей технологического оборудования, и согласованных с организацией,
монтирующей оборудование. При разработке схем геодезического обоснования
следует руководствоваться требованиями СНиП 3.01.03-83.
3.
ПРОИЗВОДСТВО МОНТАЖНЫХ РАБОТ
3.1. К началу работ
по монтажу технологического оборудования в цехе должны быть смонтированы и в
установленном порядке сданы в
эксплуатацию технологические грузоподъемные средства и передаточные тележки,
которые будут использованы для производства работ, а также постоянные и
временные железнодорожные пути и автодороги, необходимые для подачи
оборудования.
3.2. Расконсервация
рабочих поверхностей оборудования производится в соответствии с ГОСТ 9.014-78.
Защитный состав, который покрывает оборудование, должен быть удален, как
правило, перед индивидуальным испытанием оборудования без разборки в
соответствии с указаниями, приведенными в технической документации
предприятия-изготовителя.
3.3. Очищенные и
протертые поверхности должны быть покрыты рабочей смазкой, указанной в
технических условиях или чертежах предприятия-изготовителя.
3.4. Способы
установки и выверки оборудования на фундаментах должны соответствовать
требованиям проектной документации, ВСН 361-76, СН 471-75 и "Руководства
по креплению технологического оборудования фундаментными болтами".
3.5. Допускаемые
отклонения на сборку и монтаж оборудования должны быть указаны в технической
документации предприятия-изготовителя. При отсутствии таких указаний
допускаемые отклонения не должны превышать значений, приведенных в настоящих
правилах на соответствующее оборудование. Установочные поверхности (базы)
должны быть указаны в технической документации предприятия-изготовителя.
Изменение установочной базы должно согласовываться с
предприятием-изготовителем.
3.6. При
закреплении оборудования на фундаментах преимущественно должен применяться
бесподкладочный метод монтажа.
3.7. Специальные
инструменты, приспособления и приборы, необходимые для монтажа оборудования,
поставляются предприятием-изготовителем в соответствии с ОСТ 24.010.01-80 и
согласованными техническими условиями.
3.8.
Крупногабаритные изделия (конвертеры, миксеры, электропечи), поставляемые по
техническим условиям разъемными составными частями, соединения которых подлежат
сварке непосредственно в зоне строительства, должны пройти на
предприятии-изготовителе полную контрольную сборку с подгонкой геометрических
размеров стыков в пределах допускаемых отклонений и в соответствии с монтажной
маркировкой.
Сварку опорного
кольца и корпуса конвертера, кожуха миксера выполняет предприятие-изготовитель
своими материальными и людскими ресурсами. В отдельных случаях указанные
сварочные работы могут быть по договоренности выполнены монтажной организацией
при полном обеспечении предприятием - изготовителем этих изделий потребными
материальными ресурсами (сварочные материалы, электроды, флюсы и пр.) и
инструкцией по сварке.
3.9. Сварочные
работы на ответственных конструкциях должны производиться при температуре не
ниже +10 °С. Место выполнения работ должно быть защищено от ветра и атмосферных
осадков.
4. МОНТАЖ
ОБОРУДОВАНИЯ МИКСЕРОВ ВМЕСТИМОСТЬЮ 1300 И 2500 Т
4.1. Укрупнять
блоки миксера следует мостовым заливочным краном или до пуска мостового крана -
стреловым краном соответствующей грузоподъемности.
4.2. Кожух миксера
собирают в соответствии с маркировкой, нанесенной при контрольной сборке
предприятием-изготовителем. Собираемые элементы кожуха подготавливают под
клепку или сварку в зависимости от конструктивного исполнения миксера. Днища
кожуха собирают в горизонтальном положении на стендах. Цилиндрическую часть
кожуха собирают в вертикальном положении на днище, используемом в качестве
кондуктора. Для обеспечения необходимой жесткости внутри кожуха устанавливают
временные крестовины из профильного металла.
Для сборки
элементов кожуха и обеспечения цилиндричности предприятие-изготовитель
поставляет комплект регулируемых монтажных средств и распорок.
4.3. Укрупненный
узел кожуха собирают двумя способами:
цилиндрическую
часть собирают полностью в вертикальном положении на одном из днищ, второе
днище устанавливают сверху, после чего собранный кожух кантуют в горизонтальное
положение и подготавливают к установке в проектное положение;
на двух днищах
собирают обе части кожуха в вертикальном положении, затем собранные части
кантуют в горизонтальное положение и стыкуют между собой на площадке
укрупнительной сборки или на предварительно смонтированной опорно-ходовой
части.
Способ сборки
выбирают при разработке ППР.
4.4. Допускаемые
отклонения овальности кожуха для миксеров вместимостью 1300 т равны 15 мм, для
миксеров вместимостью 2500 т - 20 мм.
4.5. Подготовку
элементов миксера под клепку или сварку их производят в соответствии с
инструкцией предприятия-изготовителя.
4.6. Вырезание
проемов под горловину и носок целесообразно производить после установки и
приварки их к кожуху.
4.7.
Последовательность установки и выверки оборудования миксера:
устанавливают
опорно-ходовую часть и нижние части бандажей, кожух и верхние части бандажей,
привод и прочее оборудование миксера (механизм открывания крышек, горелок,
шарнирных колен газовоздухопроводов, вентиляторы и др.).
4.8. При монтаже
опорно-ходовой части миксера сначала устанавливают опорные рамы, выверяют и
закрепляют фундаментными болтами (без окончательной затяжки), затем на
роликовые обоймы устанавливают укрупненные блоки, состоящие из нижней и
передней частей бандажей, которые выверяют и прикрепляют к опорам с помощью
временных распорок.
После монтажа всех
узлов миксера подливают его опоры.
Допускаемые
отклонения при монтаже опорно-ходовой части миксера приведены в табл. 2, а
схема выверки - на рис. 1.
Таблица 2
─────────────────────────────────────────────┬───────────────────
Отклонение │Размер допускаемого
│ отклонения, мм
─────────────────────────────────────────────┼───────────────────
Размеров,
определяющих положение продольной │
+/- 1
и
поперечной осей опор относительно разбивоч-│
ных
осей
│
Расстояния
между опорами
│ +/- 3
От
параллельности осей опор (на 1 м)
│ 0,2
Высотных
отметок опор
│ +/- 10
От
горизонтальности поверхности качения на
│ 0,1
опорах (на 1 м) │
Длины
линии контакта каждого ролика обоймы
│ 20% длины ролика
с
поверхностью качения опор и бандажей
│
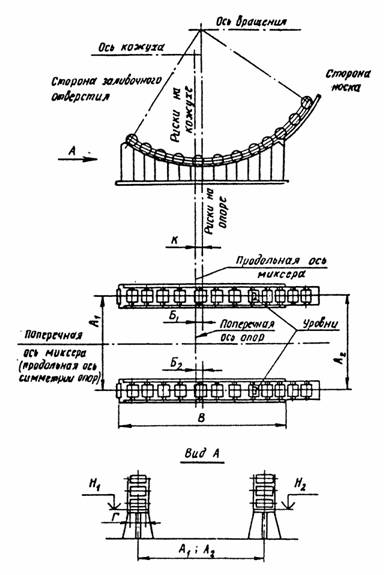
Рис. 1. Выверка
положения опор и роликовых обойм
опорно-ходовой
части миксера:
,
- расстояние между опорами;
,
- расстояние между
продольной осью
миксера и осью опоры;
,
- высотные отметки опор;
В - длина опоры; Г
- длина ролика; К - расстояние между продольной
осью миксера и
рисками на опоре, обойме и бандаже
4.9. Кожух миксера
вместимостью 1300 т устанавливают в проектное положение мостовым заливочным
краном; кожух миксера вместимостью 2500 т - двумя мостовыми кранами (при
наличии одного мостового крана кожух монтируют из двух частей). После установки
кожух прикрепляют к опорам.
4.10. Допускаемые
отклонения (справочные) при монтаже кожуха приведены в табл. 3.
Таблица 3
────────────────────────────────────────┬─────────────────────────
Отклонение │ Размер допускаемого
│ отклонения, мм
────────────────────────────────────────┼─────────────────────────
От
совмещения поперечной оси миксера
│ +/- 5
относительно
продольной оси симметрии │
опор
в плане │
Размера
между продольной осью миксера и │
+/- 2
поперечной
осью опор в плане │
Размеров,
определяющих положение осей
│ +/- 30
отверстий
на кожухе под заливочную │
горловину
и сливной носок относительно │
продольной оси симметрии миксера (замеры│
производят
по дуге кожуха) │
4.11. После
установки верхних частей бандажей и продольных стяжек окончательно затягивают
болты, соединяющие части бандажей между собой и кожух с бандажами. В процессе
утягивания кожуха бандажами временные крестовины, установленные внутри кожуха,
должны быть удалены.
4.12.
Последовательность монтажа механизма наклона миксера вместимостью 1300 т:
устанавливают
специальный редуктор, выверяют и закрепляют его анкерными болтами (без
окончательной затяжки);
устанавливают в
приямок фундамента рейку в сборе с кронштейном и направляющей коробкой; вводят
в зацепление рейку с шестерней и устанавливают направляющую коробку в проектное
положение;
прикрепляют
кронштейн рейки к кожуху миксера в соответствии с проектом;
подливают корпус
специального редуктора и окончательно затягивают анкерные болты;
устанавливают раму
с приводом в сборе, выверяют и закрепляют анкерными болтами; после подливки
рамы бетоном окончательно затягивают анкерные болты.
Допускаемые
отклонения при монтаже механизма наклона миксера приведены в табл. 4.
Таблица 4
───────────────────────────────────────┬─────────────────────────
Отклонение │ Размер допускаемого
│ отклонения, мм
───────────────────────────────────────┼─────────────────────────
Размеров,
определяющих положение │ +/- 2
вала-шестерни
относительно фактических │
осей
миксера │
Высотной
отметки оси вала-шестерни
│ +/- 1
От
горизонтальности оси вала-шестерни
│ 0,1
(на
1 м)
│
4.13.
Последовательность монтажа механизма наклона миксера вместимостью 2500 т:
устанавливают
опорную раму механизма, выверяют по разъему корпусов подшипников и закрепляют
фундаментными болтами (без окончательной затяжки);
в корпуса
подшипников устанавливают вал-шестерню в сборе с двумя рейками, направляющими
коробками и кронштейнами;
крепят к кожуху
миксера кронштейны реек, подливают опорные рамы механизма наклона и обтягивают
фундаментные болты;
устанавливают раму
привода и закрепляют фундаментными болтами, выверяют и прицентровывают редуктор
к валу-шестерне;
подливают раму
привода и окончательно затягивают фундаментные болты.
Допускаемые
отклонения при монтаже механизма наклона миксера вместимостью 2500 т см. в
табл. 4.
4.14. При установке
лебедок вспомогательных механизмов допускаемое отклонение от горизонтальности
не более 1 мм на 1 м.
4.15. Крышки
заливочного отверстия и сливного носка миксера должны прилегать всей своей
плоскостью к опорным фланцам отверстий.
4.16. В собранных
газовоздуховодах не должно быть перекосов и заклиниваний в шарнирных коленах.
5. МОНТАЖ
ТЕХНОЛОГИЧЕСКОГО ОБОРУДОВАНИЯ КОНВЕРТЕРОВ
ВМЕСТИМОСТЬЮ 130 -
400 Т
5.1. До начала
работ по укрупнительной сборке и монтажу конвертеров, кроме основных
подготовительных работ, предусмотренных СНиП 3.05.05-84 по монтажу
технологического оборудования и инструкцией предприятия-изготовителя, должны
быть выполнены следующие работы:
оставлены
монтажные проемы над сталевозными путями для перемещения домкратного устройства
с собранным конвертером к месту установки;
организована
площадка для укрупнительной сборки блоков конвертера в цехе в загрузочном
пролете на уровне пола цеха, на перекрытии рабочей площадки или другом месте в
зависимости от сроков поставки оборудования, конструкций рабочей площадки, а
также с учетом возможности транспортирования укрупненных блоков в зону монтажа;
смонтирован участок
сталевозных путей для сборки и передвижения домкратного устройства с собранным
конвертером;
оборудован тепляк
(в случае сборки и сварки блоков конвертера в зимнее время).
5.2. Необходимо,
чтобы в проекте здания на перекрытии рабочей площадки в зоне работы
загрузочного крана была предусмотрена площадка для укрупнительной сборки и
кантовки блоков конвертера.
5.3. Оборудование
конвертера передается в монтаж комплектно, максимально укрупненными блоками.
При этом разбивка оборудования конвертера на транспортабельные части и способы
его доставки должны быть согласованы с проектной организацией
Минмонтажспецстроя СССР.
5.3. Корпус и
опорное кольцо конвертера собирают в соответствии с маркировкой, нанесенной при
контрольной сборке предприятием, на специальных стендах, установленных на
несущие балки рабочей площадки или на бетонное основание на уровне пола.
Допускаемое отклонение от горизонтальности рабочей поверхности стендов не более
0,1 мм на 1 м.
Схема выверки
опорного кольца приведена на рис. 2.
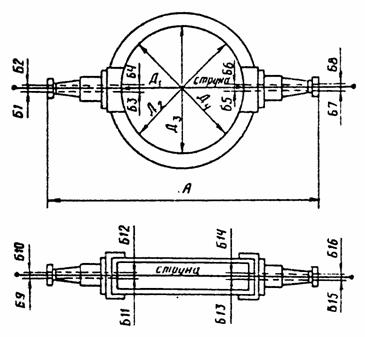
Рис. 2. Выверка
опорного кольца:
Д - внутренний
диаметр кольца; А - расстояние по наружным торцам цапф;
Б - расстояние от струны до края внутреннего отверстия цапф
5.5. Технологию
монтажа конвертера принимают в зависимости от типа и расположения
подъемно-транспортного оборудования, предусмотренного проектом цеха.
Как правило, при
монтаже конвертера следует применять домкратное устройство соответствующей
грузоподъемности, предназначенное для выполнения монтажных и ремонтных работ и
поставляемое предприятием-изготовителем по отдельному договору вместе с
оборудованием конвертера.
5.6. Последовательность
монтажа конвертера с использованием домкратного устройства (рис. 3):
устанавливают на
домкратное устройство корпус и опорное кольцо конвертера, устанавливают и
закрепляют соединительные элементы (тяги или шпильки);
собирают
подшипниковые опоры на цапфах опорного кольца, установленного на домкратном
устройстве;
монтируют
специальные редукторы на цапфах опорного кольца, установленного на домкратном
устройстве, и стойки подшипников на фундаментах;
надвигают на
домкратном устройстве собранный блок конвертера и устанавливают его в проектное
положение;
монтируют привод
конвертера, систему смазки, гидравлики и охлаждения.
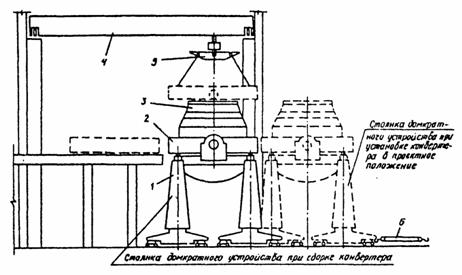
Рис. 3.
Монтаж конвертера:
1 - домкратное
устройство; 2 - опорное кольцо;
3 - корпус конвертера;
4 - мостовой заливочный кран;
5 - балансирная
траверса; 6 - полиспаст
5.7. Для монтажа специальных
редукторов на цапфах опорного кольца, установленного на домкратном устройстве,
необходимо, чтобы домкратное устройство и сталевозные пути были рассчитаны на
транспортировку конвертера в сборе с редукторами, а также на дополнительные
нагрузки, возникающие при установке первого редуктора на одну цапфу конвертера.
Вместо крюков
заливочного крана должна устанавливаться траверса, поставляемая предприятием -
изготовителем конвертера.
5.8. Опорное кольцо
следует устанавливать (относительно корпуса концентрично) на предварительно
выставленные пакеты прокладок на кронштейнах корпуса конвертеров так, чтобы
расстояние между базовыми поверхностями в кольце жесткости корпуса и опорном
кольце соответствовало проектному размеру.
5.9. Элементы
крепления корпуса к опорному кольцу поочередно устанавливают в соответствующие
гнезда в опорном кольце и кронштейнах корпуса и крепят в соответствии с
проектом. Окончательную фиксацию тяг в кронштейнах корпуса следует производить
после установки конвертера в проектное положение.
5.10. Подшипниковые
опоры следует собирать в соответствии с чертежами и инструкцией
предприятия-изготовителя в последовательности:
устанавливают на
цапфах опорного кольца подшипники, втулки, дистанционные кольца, крышки и
другие детали, регулируют подшипниковый узел и фиксируют внутренние кольца
подшипников затяжкой распорных втулок;
устанавливают
корпуса и крышки на собранные узлы подшипников и равномерно подтягивают
наружные кольца подшипников нажимными крышками;
проверяют качество
сборки подшипниковых опор, выполняя несколько качаний корпуса на цапфах на 100
- 120°.
5.11.
Последовательность установки специального редуктора на цапфе опорного кольца,
установленного на домкратном устройстве, в загрузочном пролете:
напрессовывают
редуктор на цапфу так, чтобы размер А между торцом
цапфы и торцом полого вала редуктора был не менее указанного на чертеже (рис.
4).
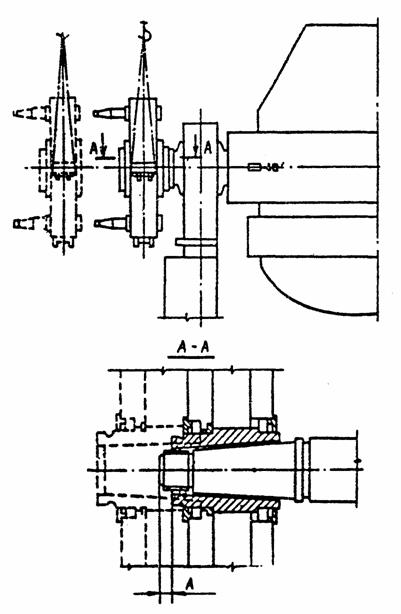
Рис. 4. Монтаж
редуктора специального:
А - расстояние
между торцом цапфы и торцом полога вала редуктора
На хвостовик
редуктора устанавливают гидрошайбу и заворачивают ее до упора в положение
напрессовки, на хвостовики цапфы устанавливают большую гайку гидрошайбы и
заворачивают ее до упора в корпус гидрошайбы;
подсоединяют к
гидрошайбе гидравлический насос и напрессовывают редуктор на цапфу; качество
напрессовки контролируют по отсутствию зазора между сопрягаемыми деталями и
усилию напрессовки. Давление в гидросистеме должно быть 35 - 40 МПа (350 - 400
кгс/см2).
Примечание. При
недостаточной грузоподъемности домкратного устройства специальный редуктор
монтируют после надвижки конвертера в проектное положение.
5.12. Стойки
опорных подшипников следует монтировать до надвижки конвертера. После надвижки
конвертера в проектное положение подливают стойки.
Допускаемые
отклонения при установке стоек приведены в табл. 5, а схема выверки стоек
опорных подшипников - на рис. 5.
Таблица 5
─────────────────────────────────────────────┬───────────────────
Отклонение │Размер допускаемого
│ отклонения, мм
─────────────────────────────────────────────┼───────────────────
От
совмещения осей стоек в плане относительно│ +/- 5
разбивочных
осей │
Расстояния
между осями, соответствующими
│ +/- 10
фактическому
расстоянию между осями опорных │
подшипников │
Высотных
отметок верхних опорных площадок
│ +/- 10
стоек │
Разности
высотных отметок опорных площадок
│ +/- 1
обеих
стоек в поперечном сечении
│
От
горизонтальности опорных площадок (на 1 м)│ 0,1
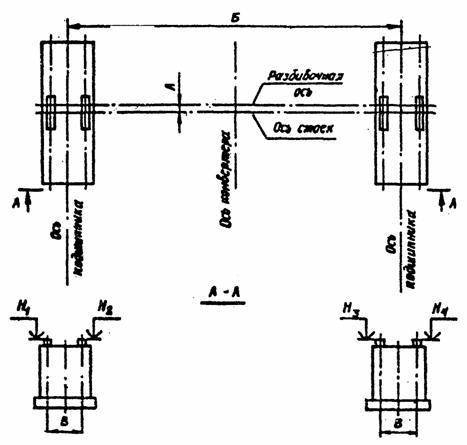
Рис. 5. Выверка
стоек опорных подшипников:
А - расстояние
между разбивочной осью и осью станины в плане;
Б - расстояние между осями подшипников;
-
- отметки
верхних опорных
площадок стоек
5.13. Конвертер
надвигают в проектное положение на домкратном устройстве, передвигаемом с
помощью полиспаста и электрической лебедки (см. рис. 3).
После надвижки
проверяют положение конвертера относительно проектных осей и опорных стоек; в
случае смещения оси конвертера относительно проектной оси более чем на 10 мм
конвертер сдвигают в соответствующую сторону домкратами, установленными на
стойках домкратного устройства.
5.14. Конвертер,
выверенный относительно осей, поддомкрачивают, снимают разъемные кольца и
опускают на стойки до упора корпусов подшипников, которые шпильками крепят к
стойкам, затем окончательно опускают конвертер.
5.15. Для
предотвращения самопроизвольного поворота конвертера следует раскрепить опорное
кольцо вертикальной распоркой, прикрепляемой к подкрановой балке.
5.16. После
установки конвертера в проектное положение производят работы на корпусе:
вырезают отверстия
в корпусе и приваривают сливной носок в соответствии с рабочими чертежами;
устанавливают листы
защиты, причем лист защиты, расположенный под сливным носком, подрезают по
контуру носка;
устанавливают шлем,
причем монтажный разъем следует располагать вдоль оси цапф.
5.17. Перед
монтажом привода должны быть смонтированы проектные обслуживающие площадки для
обеспечения безопасных условий производства работ.
До надвижки
конвертера в проектное положение на фундамент устанавливают удерживающее
устройство и временно укладывают на деревянные брусья подвесную балку. После
установки конвертера в проектное положение монтируют привод конвертера:
соединяют
специальный редуктор и гидравлический буфер с подвесной балкой;
монтируют навесные
приводы и пружинные буферы, регулируют пружинными буферами горизонтальность
навесных редукторов;
окончательно
устанавливают гидравлический буфер в проектное положение, затягивают болты
крепления стойки к опорной балке и приваривают ограничители;
монтируют установку
командоаппарата, сельсин и тахогенератор.
5.18. Навесные приводы устанавливают и напрессовывают на конусы
быстроходных вал-шестерен специальных редукторов аналогично установке
специального редуктора (см. п. 5.11 настоящих правил), используя малую
гидрошайбу, причем допускаемое отклонение от горизонтальности навесного
редуктора должно быть не более 0,2 мм на 1 м. Качество напрессовки редуктора
контролируют по размеру, указанному на чертеже, отсутствию зазора между
сопрягаемыми деталями и усилию напрессовки. Давление в гидросистеме
должно быть 5 - 6 МПа (50 - 60 кгс/см2).
6. МОНТАЖ
УСТАНОВКИ ДЛЯ ПОДАЧИ КИСЛОРОДА В КОНВЕРТЕР
6.1. Для монтажа
установки рекомендуется использовать механизм, которым монтируют строительные
конструкции здания. Если здание закрыто к моменту поставки оборудования
установки, используют высокоподъемный мостовой кран, который к началу работ по
монтажу установки должен быть смонтирован, испытан и введен в действие.
6.2. Оборудование
установки для подачи кислорода монтируют согласно ППР. Сначала монтируют
опорную раму с механизмом передвижения, затем укрупненный блок, состоящий из
направляющей, передвижной платформы, кареток и противовесов; потом систему
подвода кислорода и воды и устанавливают фурмы.
6.3. Допускаемые
отклонения при установке рамы приведены в табл. 6, а схемы выверки опорной рамы
- на рис. 6.
Таблица 6
────────────────────────────────────────┬────────────────────────
Отклонение │ Размер допускаемого
│ отклонения, мм
────────────────────────────────────────┼────────────────────────
Размеров,
определяющих положение рамы
│ +/- 10
в
плане относительно разбивочных осей
│
Высотной
отметки рабочей поверхности
│ +/- 10
головок
рельсов │
От
горизонтальности рабочей поверхности │ 0,5
головок
рельсов в продольном и попереч- │
ном
направлениях (на 1 м)
│
От
перпендикулярности рабочей поверхнос-│ 0,5
ти
упорного рельса (на 1 м)
│
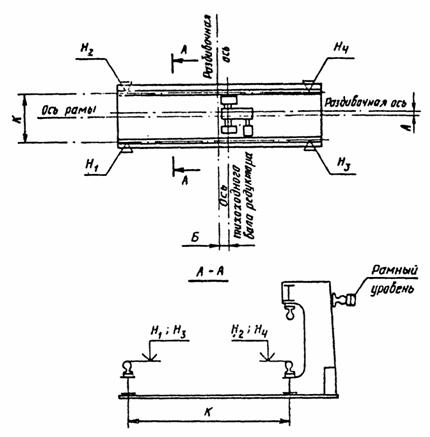
Рис. 6. Выверка
опорной рамы установки
для подачи
кислорода в конвертер:
А - расстояние
между разбивочной осью и осью рамы;
Б - расстояние
между разбивочной осью и осью тихоходного
вала редуктора;
-
- отметки рабочей поверхности
головки рельса; К - расстояние между осями рельсов
6.4. Укрупнительную
сборку направляющей с платформой производят согласно маркировке
предприятия-изготовителя.
Каретки и
противовесы необходимо надежно прикрепить к направляющим стальным канатам.
Перед подъемом блока необходимо временно снять с платформы упорный ролик, а с
рамы - верхний опорный рельс.
6.5. Допускаемые
отклонения при установке укрупненного блока направляющей с платформой приведены
в табл. 7.
Таблица 7
─────────────────────────────────────────────┬───────────────────
Отклонение │Размер допускаемого
│ отклонения, мм
─────────────────────────────────────────────┼───────────────────
Плотности
прилегания упорного ролика к
│ 0,05
упорному
рельсу │
Плотности
прилегания опорных катков к рельсу │ 0,05
со
стороны фурмы
│
Зазора,
равного 4 мм, между поверхностью
│
опорного
катка и нижним рельсом рамы со сто- │
роны,
противоположной фурме │
7. МОНТАЖ
ОХЛАДИТЕЛЕЙ КОНВЕРТЕРНЫХ ГАЗОВ
7.1. К началу производства работ по монтажу охладителя должны быть
смонтированы в необходимом объеме (предусмотренном ППР на монтаж охладителя) и
сданы по акту промежуточной технической готовности конструкции здания,
оставлены проемы, установлены временные опорные конструкции в соответствии с
ППР.
Охладитель
ОКГ-180 радиационно-конвективного типа
7.2. Перед монтажом
укрупняют следующие основные блоки охладителя (рис. 7):
кессон - нижние и
верхние рамы откатной тележки, опорный пояс кессона, опорная рама, фронтовая
панель с кессоном фурменным, боковые панели с экранами отверстий для подачи
сыпучих материалов;
подъемный газоход -
фронтовая, задняя, правая и левая панели;
опускной газоход -
фронтовая, задняя и левая панели, блок экономайзеров.
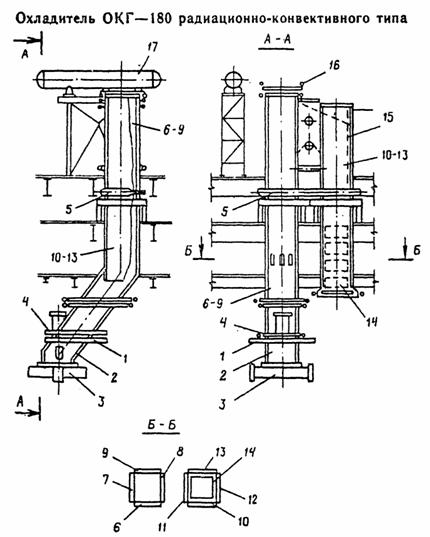
Рис. 7. Разбивка на
блоки котла-охладителя ОКГ-180:
1 - откатная
тележка кессона; 2 - панели кессона; 3 - юбка;
4 - опорный пояс
кессона; 5 - опорный пояс; 6 - 9 - панели
подъемного газохода
(фронтальная, левая, правая и задняя);
10 - 13 -
панели опускного газохода (фронтальная, левая,
правая и задняя);
14 - блок экономайзеров; 15 - ширмы;
16 - защитный экран
и крышка; 17 - барабан
Доукрупняются также
защитный экран и потолочный экран подъемного газохода, защитный экран кессона,
барабан.
При
совмещенном монтаже конструкций здания и охладителя башенным краном в
зависимости от конкретных условий допускается производить укрупнение панелей
подъемного и опускного газоходов в пространственные блоки, при этом опускной
газоход укрупняется из трех панелей (фронтовой, задней и правого нижнего блока
панели) с установкой временных связей в плоскости временно не установленных
панелей.
7.3. Сборка
и сварка панелей производится в кондукторах для предотвращения поводки панелей
при сварке.
7.4. Трубопроводы в
пределах котла укрупняются в блоки, размеры которых определяются возможностью
их перемещения и установки.
7.5.
Допускаемые отклонения при сборке блоков охладителя приведены в табл. 8.
Таблица 8
─────────────────────────────────────────────┬───────────────────
Отклонение │Размер допускаемого
│ отклонения, мм
─────────────────────────────────────────────┼───────────────────
Разности
размеров диагоналей
│ +/- 5
Перекоса
труб из плоскости блока
│ +/- 5
Перекоса
труб в плоскости блока
│ +/- 2
От
соосности осей труб при стыковке
│ 1
От
горизонтальности оси коллектора
│ 3
От
прямолинейности оси трубы в месте сварного│ 2
стыка
(на расстоянии 200 мм от оси стыка)
│
7.6. Укрупненные
блоки поверхностей нагрева проверяют прогонкой по трубам шара диаметром
согласно техническим условиям предприятия-изготовителя. Газоходы необходимо
проверить на газовую плотность керосином.
7.7. Перед подъемом
на блоках следует установить подмости, лестницы и другие приспособления,
обеспечивающие безопасные условия производства работ в соответствии с ППР.
7.8. При монтаже
охладителя конвертерных газов башенным краном, предназначенным для монтажа
строительных конструкций здания, последовательно устанавливают:
кессон - тележку
кессона, опорную раму и опорный пояс на тележке, левую боковую, заднюю, правую
боковую и фронтовую панели, защитный экран и юбку;
подъемный газоход -
панели (или пространственный блок), защитный экран и крышку;
опускной
газоход - нижний блок правой панели, задняя и фронтовая панели (или
пространственный блок панелей), водяной экономайзер, ширмы, левую боковую
панель, верхний блок правой панели и бункера, барабан, трубопроводы в пределах
охладителя.
При монтаже
охладителя следует строго соблюдать очередность установки блоков охладителя и
конструкций здания, предусмотренную графиком совмещенного производства работ.
7.9. В закрытом
здании при монтаже охладителя с помощью мостовых кранов и монтажных балок
последовательно устанавливают: барабан, опускной газоход, кессон и подъемный
газоход.
7.10. При установке
панелей следует пользоваться временными монтажными опорами и подвесками,
которые убирают после установки стационарных опор.
7.11. Строповочные
приспособления после монтажа со всех блоков срезают.
7.12. При монтаже
панелей под скользящие опоры подсыпают графит.
7.13. Допускаемые
отклонения при монтаже панелей приведены в табл. 9.
Таблица 9
────────────────────────────────────────┬────────────────────────
Отклонение │ Размер допускаемого
│ отклонения, мм
────────────────────────────────────────┼────────────────────────
Размеров,
определяющих положение коллек-│
+/- 5
торов
относительно осей охладителя │
Высотной
отметки коллектора
│ +/- 5
От
горизонтальности оси коллектора
│ 3
От
соосности осей труб при стыковке
│ 1
Размера
между осями крайних труб сосед- │
+/- 2
них
блоков
│
7.14. Перед
монтажом водяного экономайзера необходимо подготовить места опирания
коллекторов. Если блоки устанавливают во временное положение, то заранее
следует подготовить места опирания и подвеса блоков, обеспечивающие легкое
передвижение их в проектное положение. Допускаемые отклонения при монтаже
водяного экономайзера приведены в табл. 10.
Таблица 10
────────────────────────────────────────┬────────────────────────
Отклонение │ Размер допускаемого
│ отклонения, мм
────────────────────────────────────────┼────────────────────────
Размеров,
определяющих положение осей
│ +/- 5
коллектора
относительно осей газохода │
Высотной
отметки коллектора
│ +/- 3
От
горизонтальности коллектора (на 1 м) │ 2
Размеров,
определяющих положение осей
│ +/- 5
коллектора │
7.15. Подъемный и
опускной газоходы монтируют, как правило, мостовым краном ремонтного
устройства.
7.16. Перед
подъемом барабана проверяют положение опор. Допускаемые отклонения при монтаже
барабана приведены в табл. 11.
Таблица 11
────────────────────────────────────────┬────────────────────────
Отклонение │ Размер допускаемого
│ отклонения, мм
────────────────────────────────────────┼────────────────────────
Расстояния
между опорами │ -
От
вертикальности оси барабана
│ 1,5
От
горизонтальности барабана по отметкам│ 2
крайних
очков или штуцеров │
Расстояния
между продольной осью бараба-│
+/- 5
на и осевыми линиями фронтовых колонн │
металлоконструкций │
От
плоскостности прилегания подушек и
│ 1
барабана │
7.17. Подъем
барабана производят в соответствии с ППР башенным краном, занятым на монтаже
конструкций здания.
Для монтажа
барабана в закрытом здании должны быть предусмотрены: проем, монтажная балка,
пути надвижки барабана от монтажного проема к месту его установки.
Задание на
устройство проема, монтажной балки, путей надвижки барабана и т.д. должно
выдаваться головной проектной организации организацией, разрабатывающей раздел ПОС "Монтаж технологического оборудования".
Размеры монтажного
проема в плане должны обеспечить подъем барабана в горизонтальном положении, а
грузоподъемность монтажной балки - соответствовать массе барабана.
7.18. Сваривают
трубы поверхностей нагрева и контролируют качество швов в соответствии с
техническими условиями предприятия-изготовителя и требованиями Госгортехнадзора
СССР.
7.19.
Вспомогательное оборудование охладителя (горелки, вентиляторы, циркуляционные
насосы, дымососы и др.) монтируют в соответствии с инструкциями
предприятий-изготовителей.
7.20. Оборудование
газоочистки монтируют одновременно с конструкциями здания в соответствии с ППР
монтажными кранами по совмещенному графику производства работ, а в закрытом
здании - проектными грузоподъемными средствами и монтажными приспособлениями.
7.21. После монтажа
трубчатых поверхностей нагрева производят очистку внутренних поверхностей
нагрева от коррозии, грата, окалины и других загрязнений по инструкции
предприятия-изготовителя.
Очистку внутренних
поверхностей нагрева производят в нижеприведенной последовательности:
промывка химически
очищенной водой при температуре 60 - 80
°C по закрытому циклу (общая, поконтурная и индивидуальная промывка со
вскрытием коллекторов и барабана и удалением грязи);
щелочение
тринатрийфосфатом, или едким натрием, или кальцинированной содой при огневом
разогреве коксовым или другим газом от временных горелок;
отмывка питательной
водой путем продувок и подпиток при циркуляции по замкнутому циклу, а также
индивидуальная промывка труб;
отмывка с
применением композиций на основе комплексонов при огневом обогреве (кислотная
промывка);
многократный обмен
котловой воды и последующая щелочная пассивация;
вскрытие всех
коллекторов и барабана, очистка от грязи, индивидуальная промывка каждой трубы;
заполнение котла
водой эксплуатационного качества.
7.22. На всех этапах
подготовки охладителя к пуску необходимо следить по реперам за тепловым
расширением элементов охладителя.
7.23. Паровое
опробование, консервацию и пуск охладителя производят по инструкции
предприятия-изготовителя.
Охладитель
ОКГ-400 радиационного типа
7.24. Перед
монтажом укрупняют следующие основные блоки охладителя:
кессон - откатная
тележка, опорные балки (два плоских вертикальных блока), пространственный блок
панелей кессона, юбка;
стационарный
газоход - два пространственных блока газохода (нижний и верхний), крышка.
Указанная блочность рациональна при совмещенном монтаже конструкций здания и
охладителя башенным краном.
7.25. Сборку блоков
газоходов производят в соответствии с пп. 7.3 - 7.5 настоящих правил.
Допускаемые отклонения при сборке пространственных блоков см. в табл. 8.
7.26.
Последовательность монтажа охладителя башенным краном, предназначенным для
монтажа строительных конструкций здания (рис. 8):
устанавливают
откатную тележку кессона, опорные балки (два плоских вертикальных блока);
монтируют
пространственный блок кессона с помощью башенного крана и полиспаста,
прикрепленного к конструкциям здания, устанавливают балки, не вошедшие в состав
тележки и опорных конструкций кессона;
устанавливают
временные опорные балки под нижний блок стационарного газохода (балки
раздвигают для свободного прохода блока), одновременно устанавливают проектные
опорные балки под опускной газоход, заднюю балку под подъемный газоход и балку
направляющих поясов, которые также раздвигают с учетом прохода блоков газохода;
краном заводят
сверху нижний блок, временные опорные балки подводят под временные опоры блока
и устанавливают блок на 15 мм ниже проектного на клиновые домкраты;
устанавливают три
остальные опорные балки подъемного газохода верхнего блока;
монтируют верхний
блок выше проектной отметки на 500 мм, сдвигают, стыкуют опорные балки и
опускают на них блок;
производят стыковку
нижнего и верхнего блоков газохода, монтируют угловую панель;
с помощью кранов
устанавливают барабан;
монтируют
трубопроводы в пределах котла;
юбку монтируют из
двух половин после окончательного монтажа кессона и установки конвертера на
фундамент.
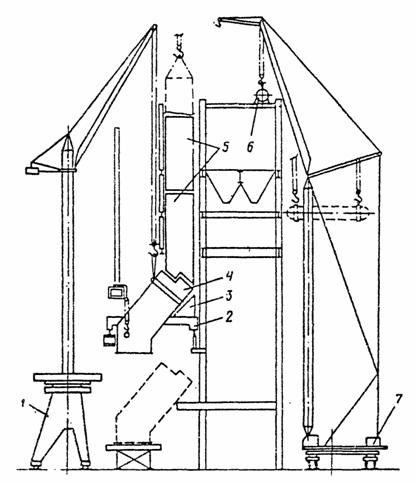
Рис. 8.
Монтаж котла-охладителя ОКГ-400:
1 - башенный кран
грузоподъемностью 50 т; 2 - откатная тележка;
3 - опорные балки
кессона; 4 - кессон; 5 - блоки подъемного
газохода (нижний и
верхний); 6 - барабан котла;
7 - рельсовый кран
грузоподъемностью 50 т
7.27. При монтаже
охладителя следует строго соблюдать очередность установки блоков охладителя и
конструкций здания, предусмотренную графиком совмещенного производства работ.
7.28. В закрытом
здании при монтаже охладителя с помощью башенных, мостовых кранов и монтажных
балок последовательно устанавливают: барабан, панели опускного газохода, панели
подъемного газохода и кессон.
7.29. При выводе в
вертикальное положение панелей подъемного газохода для уменьшения прогиба
панели поддерживают в середине полиспастами, прикрепленными к конструкциям
здания.
7.30. Проверки,
выполняемые при монтаже блоков охладителя ОКГ-400, аналогичны проверкам при
монтаже охладителя ОКГ-180.
8. МОНТАЖ
ТЕХНОЛОГИЧЕСКОГО ОБОРУДОВАНИЯ
ЭЛЕКТРОСТАЛЕПЛАВИЛЬНЫХ
ПЕЧЕЙ ВМЕСТИМОСТЬЮ 200 И 100 Т
С ГИДРАВЛИЧЕСКИМ
ПРИВОДОМ
8.1. Укрупнительную
сборку блоков печи следует производить на стендах мостовым загрузочным краном
согласно монтажно-маркировочной схеме предприятия-изготовителя на рабочей
площадке.
При этом
конструкции рабочей площадки необходимо проверить на воздействие монтажных
нагрузок.
8.2. Люльку печи
собирают на шпальных выкладках и устанавливают на ней опоры (фиксаторы) кожуха.
Допускаемые
отклонения при сборке люльки приведены в табл. 12.
Таблица 12
─────────────────────────────────────────────┬───────────────────
Отклонение │Размер допускаемого
│ отклонения, мм
─────────────────────────────────────────────┼───────────────────
От
горизонтальности рабочей поверхности
│ 0,3
люльки
во взаимно перпендикулярных направле- │
ниях
(на 1 м)
│
Расстояния
между секторами
│ +/- 3
От
параллельности секторов (на 1 м)
│ 0,5
От
перпендикулярности секторов поверхности
│ 0,5
люльки
(на 1 м)
│
8.3. Из элементов
заводской поставки кожух печи укрупняют на специальном стенде в блок, состоящий
из кожуха и коробки песочного затвора.
Допускаемое
отклонение овальности при сборке кожуха - 20 мм.
Кожух сваривают в
соответствии с технологической инструкцией на сварку и разделом "Сварка
стальных конструкций" ОСТ 24.940.01.
8.4. Шахту печи
собирают в блок, состоящий из верхних и нижних секций с направляющими роликами,
металлоконструкций площадок и лестниц.
8.5. Портал печи
собирают в блок, состоящий из консолей, связывающих площадок, водоохлаждаемых
коробок и обвязочных трубопроводов. После сборки блока производят
гидравлическое испытание систем водоохлаждения в соответствии с техническими
требованиями предприятия-изготовителя.
8.6.
Водоохлаждаемый трубчатый свод собирают в укрупненный блок, состоящий из
каркаса и панелей свода. Систему водоохлаждения свода подвергают
гидравлическому испытанию в соответствии с техническими требованиями чертежей
предприятия-изготовителя.
8.7. При монтаже
укрупненных блоков и отдельных узлов печи последовательно устанавливают (рис.
9):
две фундаментные
балки;
люльку механизма
наклона и гидроцилиндры;
статор
электромагнитного перемешивания металла;
опорные тумбы
системы подъема и поворота свода;
кожух печи;
водоохлаждаемый
свод и центральную купольную часть свода;
механизм подъема и
поворота свода;
систему перемещения
электродов.
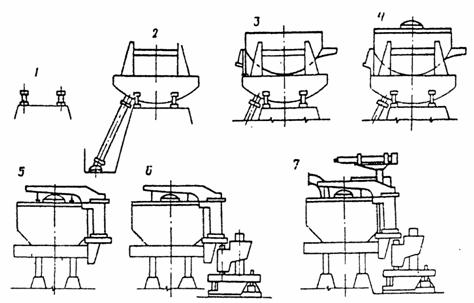
Рис. 9. Монтаж
электросталеплавильной печи с гидравлическим приводом:
1 - фундаментные
балки; 2 - люлька и гидроцилиндр; 3 - кожух;
4 - водоохлаждаемый
свод; 5 - узел консоли-портала шахты;
6 - механизм
подъема и поворота свода; 7 - система электрододержателей
Системы смазки,
гидравлики, пневматики и водоохлаждения монтируют параллельно с основными
узлами печи в соответствии с рабочими чертежами и требованиями инструкции
предприятия-изготовителя.
8.8. Допускаемые
отклонения от проектного положения при монтаже фундаментных балок приведены в
табл. 13.
Таблица 13
─────────────────────────────────────────────┬───────────────────
Отклонение │Размер допускаемого
│ отклонения, мм
─────────────────────────────────────────────┼───────────────────
От
совмещения балки относительно разбивочной │ +/- 5
оси
│
Расстояния
между балками
│ +/- 3
Высотной
отметки рабочей поверхности балок
│ +/- 5
Разности
уровней рабочих поверхностей балок
│ 0,2
(на
1 м)
│
От
параллельности балок между собой (на 1 м) │ 0,5
От
горизонтальности рабочих поверхностей
│ 0,5
балок
(на 1 м)
│
8.9. Укрупненный
блок люльки устанавливают на фундаментные балки и проверяют совпадение шипов с
отверстиями в балках наклоном люльки в обе стороны. Затем люльку устанавливают
горизонтально и закрепляют клиньями. Допускаемое отклонение от горизонтальности
не более 0,2 мм на 1 м.
8.10. При монтаже
гидроцилиндров механизма наклона выверяют соосность гидроцилиндров и секторов
люльки, после чего производят подливку фундаментных балок и кронштейнов
гидроцилиндров.
8.11. Кожух печи
выставляют на люльке механизма наклона со смещением поперечных осей в сторону
рабочего окна согласно чертежам предприятия-изготовителя, после чего монтируют
рабочее окно, сливной желоб, площадки для обслуживания песочного затвора и
рабочие площадки на люльке.
8.12. Установку
центральной купольной части свода на водоохлаждаемый свод производят так, чтобы
оси электродных отверстий соответствовали распаду электродов относительно оси
кожуха.
8.13.
Последовательность монтажа механизма подъема и поворота свода:
собранный узел
консоли, портала и шахты устанавливают на опорные тумбы люльки и выверяют
горизонтальность верхних плоскостей консоли;
устанавливают на
фундамент основание механизма подъема и поворота свода, затем балансиры и
поворотную ось;
монтируют на
основании поворотную платформу, соединив ее с балансирами и поворотной осью,
допускаемые отклонения приведены в табл. 14;
после установки
гидроцилиндров подъема свода и упора каретки на стойках поворотной платформы
монтируют каретку.
Таблица 14
─────────────────────────────────────────────┬───────────────────
Отклонение
│Размер допускаемого
│ отклонения, мм
─────────────────────────────────────────────┼───────────────────
От
горизонтальности верхней плоскости плат-
│ 0,2
формы
(на 1 м)
│
От
вертикальности поворотной оси (на 1 м)
│ 0,1
От
горизонтальности дугообразного опорного │ 0,2
рельса
основания (на 1 м)
│
После соединения
стоек перемычкой производят опробование механизма подъема и поворота свода. При
этом должен обеспечиваться свободный вход толкателя каретки в
коническое гнездо шахты до упора в основание с односторонним зазором между
коническими поверхностями толкателя и гнезда со стороны кожуха печи, а
также должно обеспечиваться прилегание плоских упоров каретки и шахты согласно
технической документации предприятия-изготовителя.
8.14.
Последовательность монтажа системы перемещения электродов:
проверяют фиксацию
плунжеров от выпадания из цилиндров при транспортировании, опускают в стволы
шахты стойки и соединяют с цилиндрами перемещения электродов;
монтируют на
стойках электрододержатели, контролируя положение их головок по отверстиям в
центральной керамической части свода.
8.15. После
выполнения футеровки электропечи устанавливают электродные уплотнения,
газоотсос, устройство для ввода кислорода в печь и газокислородные горелки.
9. МОНТАЖ
ОБОРУДОВАНИЯ УСТАНОВКИ
ДЛЯ ПОВЫШЕНИЯ
КАЧЕСТВА СТАЛИ
Электропечь
для выплавки синтетических шлаков
9.1. Блоки печи
укрупняют на специальных стендах мостовым краном согласно
монтажно-маркировочной схеме предприятия-изготовителя.
9.2. Кожух печи
сваривают в соответствии с технологической инструкцией на сварку и разделом
"Сварка стальных конструкций" ОСТ 24.940.01.
9.3.
Последовательность монтажа укрупненных блоков и элементов печи: устанавливают
фундаментные балки, опорные балки печи, рабочую площадку, кожух, холодильники,
рабочее окно с приводом перемещения дверцы, шлаковую летку с механизмом
закрывания, систему перемещения электродов, сводное кольцо и электроды.
9.4. Системы
смазки, водоохлаждения и пневматики монтируют параллельно с основными узлами в
соответствии с рабочими чертежами и инструкцией предприятия-изготовителя.
Положение кожуха
печи фиксируют планками, которые приваривают на расстоянии 10 мм от кожуха.
9.5. Допускаемые
отклонения при монтаже кожуха приведены в табл. 15.
Таблица 15
─────────────────────────────────────────┬───────────────────────
Отклонение │ Размер допускаемого
│ отклонения, мм
─────────────────────────────────────────┼───────────────────────
От
совмещения осей печи относительно раз-│ +/- 5
бивочных
осей │
Высотной
отметки опорной части кожуха
│ +/- 5
От
горизонтальности пода печи (на 1 м)
│ 0,3
От
вертикальности стенок кожуха печи
│ 0,3
(на
1 м)
│
9.6.
Последовательность монтажа системы перемещения электродов:
устанавливают шахту
с направляющими роликами и блоки противовеса, затем на кронштейнах - приводы
перемещения электродов;
временно
устанавливают рейки в шахте и вводят их в зацепление с приводными шестернями,
устанавливают в шахту стойки с электрододержателями, регулируют зазор между
роликами и направляющими поверхностями стойки и прикрепляют рейки к стойке.
При монтаже системы
перемещения электродов контролируют отклонение от вертикальности стойки (не
более 0,2 мм на 1 м) и зазор между неработающими роликами и опорной
поверхностью стойки (значение зазора 1 - 3 мм).
10. МОНТАЖ
МАШИН НЕПРЕРЫВНОГО ЛИТЬЯ ЗАГОТОВОК (МНЛЗ)
10.1. К началу
производства работ по монтажу оборудования МНЛЗ, кроме основных
подготовительных работ, предусмотренных СНиП 3.05.05-84, должны быть выполнены
следующие работы:
смонтирована
рабочая площадка МНЛЗ, за исключением съемных балок и щитов;
сдана мастерская по
наладке и выверке узлов МНЛЗ;
закончены
строительные работы, включая отделочные, в маслоподвалах и помещениях насосных
и аккумуляторных станций.
10.2. Заказчиком
должна быть обеспечена паспортизация и индексация настраиваемого сменного
оборудования. Стендовую настройку сменного оборудования выполняют на
специальных (настроечных) стендах, принятых в эксплуатацию.
10.3. Оборудование
МНЛЗ монтируют эксплуатационными мостовыми кранами в направлении от первого
ролика горизонтальной части роликовой зоны машины в обе стороны. Оборудование
разливочной площадки и приемно-транспортное оборудование могут монтироваться
независимо от монтажа оборудования технологического канала МНЛЗ.
Оборудование
блюмовых многоручьевых МНЛЗ радиального типа
10.4. Очередность
монтажа составных частей многоручьевых МНЛЗ:
рамы под
тянуще-правильные машины и опорные балки под роликовые секции;
разводка
трубопроводов системы водоохлаждения (частично);
тянуще-правильные
машины;
роликовые секции;
механизм качания
кристаллизатора;
роликовые секции
под кристаллизатором;
кристаллизатор;
устройство уборки и
хранения затравки;
установка затравки;
тележки для
промковша и подъемно-поворотный стенд.
10.5. Допускаемые
отклонения при монтаже рам тянуще-правильной машины и опорных балок под
роликовые секции приведены в табл. 16 и на рис. 10.
Таблица 16
─────────────────────────────────────────────┬───────────────────
Отклонение │Размер допускаемого
│ отклонения, мм
─────────────────────────────────────────────┼───────────────────
Высотных
отметок осей опор роликовых секций
│ +/- 0,5
и
тянуще-правильных машин
│
Размеров,
определяющих положение осей опор
│ +/- 1
роликовых
секций и тянуще-правильных машин
│
относительно
базовой стенки кристаллизатора в│
горизонтальной
плоскости │
От
горизонтальности осей опор роликовых
│ 0,1
секций
и тянуще-правильных машин (на 1 м)
│
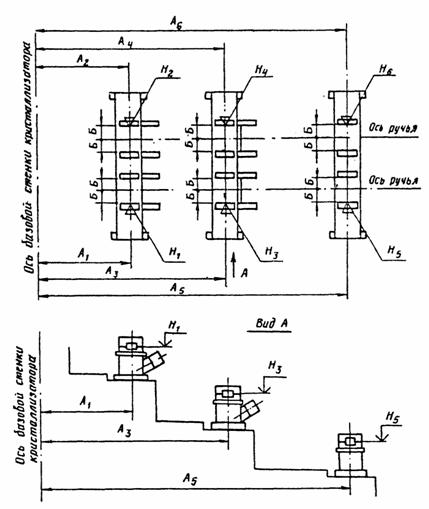
Рис. 10. Выверка
опорных балок под роликовые секции:
-
- расстояние между осью опоры и базовой
стенкой
кристаллизатора; Б
- расстояние между стойкой оси и осью ручья;
-
- высотная отметка осей опор
10.6. После
установки рам и опорных балок устанавливают трубопроводы системы
водоохлаждения, расположенные между рамой механизма качания и
нижерасположенными балками.
10.7. Перед
монтажом тянуще-правильных машин обеспечивают свободный доступ к нижним
роликам, для чего снимают рычаги с роликами и тягами, выбив по четыре клина на
каждом рычаге, и экраны. Допускаемые отклонения при монтаже тянуще-правильной
машины приведены в табл. 17.
Таблица 17
───────────────────────────────────────────┬─────────────────────
Отклонение │Размер допускаемого
│ отклонения, мм
───────────────────────────────────────────┼─────────────────────
Размеров,
определяющих положение машины в
│ +/- 1
горизонтальной
плоскости │
Высотных
отметок верхних образующих роликов│
+/- 0,2
От
горизонтальности нижних роликов (на 1 м)│ 0,1
Установку рычагов с
верхними роликами производят после монтажа роликовой секции, примыкающей к
тянуще-правильной машине.
10.8. Шаблон по
мере выставки роликов перемещается вверх от роликов тянуще-правильных машин.
Допускаемые отклонения при монтаже роликовых линий приведены в табл. 18.
Таблица 18
─────────────────────────────────────────┬───────────────────────
Отклонение │ Размер допускаемого
│ отклонения, мм
─────────────────────────────────────────┼───────────────────────
Зазора
между шаблоном и роликом
│ 0,2
Размера,
определяющего положение оси
│ +/- 1
канала,
оборудованного торцевыми роликами│
секций
относительно оси соответствующего │
ручья │
От
горизонтальности роликов (на 1 м)
│ 0,1
10.9. Допускаемые
отклонения при установке рам под механизмы качания кристаллизаторов аналогичны
допускаемым отклонениям для рам и опорных балок, приведенных в табл. 17.
Допускаемые
отклонения при выверке оси качания рычага приведены в табл. 19 и на рис. 11.
Таблица 19
────────────────────────────────────────┬────────────────────────
Отклонение │ Размер допускаемого
│ отклонения, мм
────────────────────────────────────────┼────────────────────────
Размеров,
определяющих положение оси
│ +/- 0,5
качания
рычага относительно базовой │
стенки
кристаллизатора в горизонтальной │
плоскости │
Высотной
отметки
│ +/- 0,5
От
параллельности относительно базовой
│ 0,1
стенки
кристаллизатора (на 1 м) │
От
горизонтальности (на 1 м)
│ 0,1
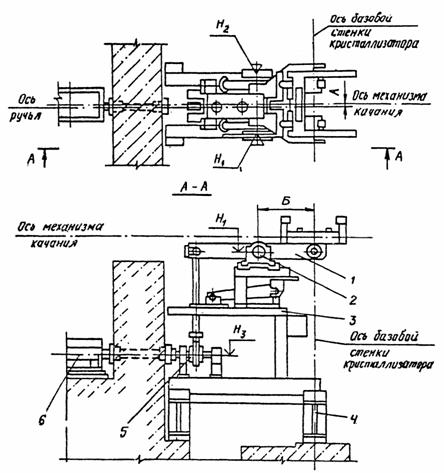
Рис. 11. Выверка
механизма качания кристаллизатора:
А - расстояние
между продольной осью механизма качания и осью ручья;
Б - расстояние между осью качания рычага и базовой стенкой
кристаллизатора;
-
- высотная отметка вала эксцентрика; 1 -
рычаг; 2 - опора рычага;
3 - верхняя рама; 4
- опорная рама; 5 - эксцентрик; 6 - привод
Допускаемые
отклонения при выверке узла эксцентрика и двигателя приведены в табл. 20.
Таблица 20
────────────────────────────────────────────┬────────────────────
Отклонение │Размер допускаемого
│ отклонения, мм
────────────────────────────────────────────┼────────────────────
Размеров,
определяющих положение узла экс-
│ +/- 1
центрика
относительно разбивочных осей в │
горизонтальной
плоскости │
Высотных
отметок
│ +/- 0,5
От
параллельности осей валов │ 0,8
От
соосности валов (на 1 м)
│ 1
10.10. Роликовые
секции, устанавливаемые под кристаллизатором, перед установкой настраивают на
специальном стенде. На место роликовой секции устанавливают эталон секции. С
помощью подкладок, установленных под опорами, обеспечивают зазор между
шаблоном, установленным на базовые ролики ранее установленной секции, и
роликами секций под кристаллизатором не более 0,2 мм. При этом опоры эталона
должны плотно прилегать к опорам, установленным на раме механизма качания
кристаллизатора. Допускаемое отклонение от совмещения боковых реперов эталона и
оси ручья +/- 0,5 мм. После выполнения указанных регулировок опоры надежно
закрепляют.
10.11. Рычаг
механизма качания кристаллизатора устанавливают в горизонтальное положение. На
место кристаллизатора устанавливают эталон кристаллизатора.
С помощью
подкладок, установленных под опорами, обеспечивают зазор между шаблоном,
установленным на роликовые секции, и роликами эталона кристаллизатора не более 0,2
мм. При этом опоры эталона кристаллизатора должны плотно прилегать к опорам на
механизме качания.
Прилегание роликов
эталона кристаллизатора к шаблону проверяют в крайних положениях рычага, зазор
при этом не должен превышать 0,2 мм.
10.12. После установки
кристаллизатора контролируют его положение. Допускаемое отклонение базовой
стенки кристаллизатора от шаблона, установленного на базовые ролики секции под
кристаллизатором, не должно превышать 0,2 мм. Допускаемое отклонение оси
канала, образованного узкими стенками кристаллизатора, от оси ручья не должно
превышать 0,5 мм.
10.13. Допускаемые
отклонения при выверке оборудования устройства уборки и хранения затравки
приведены в табл. 21.
Таблица 21
──────────────────────────────────────────────┬──────────────────
Отклонение │Размер допускаемо-
│го отклонения, мм
──────────────────────────────────────────────┼──────────────────
От
совмещения продольной оси симметрии пере-
│ +/- 3
кидного
лотка относительно оси ручья
│
От
совмещения конусных проточек под канат от- │ +/- 1
носительно
оси ручья
│
От
параллельности осей роликов и оси барабана │ 0,1
привода
перемещения относительно базовой стен-│
ки
кристаллизатора (на 1 м)
│
От
горизонтальности осей роликов и оси бараба-│ 0,1
на привода (на 1 м) │
От
совмещения внутренней цилиндрической │ +/- 1
поверхности
направляющей с горизонтальной про-│
водкой
тянуще-правильных машин
│
10.14. Допускаемые
отклонения при выверке рельсовых путей тележек для промковша приведены в табл.
22.
Таблица 22
─────────────────────────────────────────────┬───────────────────
Отклонение │Размер допускаемого
│ отклонения, мм
─────────────────────────────────────────────┼───────────────────
Высотных
отметок головок парных рельс
│ +/- 1
Расстояния
между рельсами
│ +/- 1
От
горизонтальности парных рельс и контр-
│ 0,5
рельса
(на 1 м)
│
10.15. До начала
монтажа подъемно-поворотного стенда монтируют балки и направляющие рельсы.
Допускаемые отклонения при монтаже рельсов приведены в табл. 23.
Таблица 23
────────────────────────────────────────────┬────────────────────
Отклонение │Размер допускаемого
│ отклонения, мм
────────────────────────────────────────────┼────────────────────
Высотной
отметки головки рельса
│ +/- 2
От
горизонтальности поверхностей рельсов
│ 0,3
(на
1 м)
│
Расстояния
по осям рельсов
│ +3
10.16. На
расстоянии 4 - 4,5 м от оси проектного положения подъемно-поворотного стенда на
балках для надвижки стенда с помощью мостового крана собирают стенд из блоков
заводской готовности и предварительно укрупненных блоков.
10.17. Надвижку
стенда в проектное положение производят с помощью устройства для монтажа и
ремонта стенда. При применении для надвижки ходовых колес стенд после надвижки
устанавливают в следующей последовательности:
поднимают
гидроцилиндром платформу со стороны колес с ребордами на высоту 30 мм;
вынимают планку,
расположенную над осью колес, и устанавливают ее под осью;
устанавливают
регулировочную прокладку и опускают платформу, устанавливают шпонку;
прикрепляют
платформу к балке.
Аналогичные
операции производят с другой стороны стенда.
10.18. Стенд
выверяют относительно разбивочных осей по высоте и контролируют вертикальность
оси вращения стенда путем измерения высотной отметки точки на расстоянии 5500
мм от оси вращения стенда в двух взаимно перпендикулярных положениях. Разность
отметок при повороте стенда на 180° не должна превышать 4 мм. Допускаемые
отклонения при выверке стенда приведены в табл. 24 и на рис. 12.
Таблица 24
─────────────────────────────────────────────┬───────────────────
Отклонение │Размер допускаемого
│ отклонения, мм
─────────────────────────────────────────────┼───────────────────
Размеров,
определяющих положение стенда отно-│
+/- 1
сительно
разбивочных осей
│
Высотных
отметок
│ +/- 0,5

Рис. 12. Выверка
вертикальности поворотной платформы:
-
- высотные отметки кронштейна на расстоянии R
5500
от оси поворотной
колонны
Смонтированные
системы охлаждения подвергают промывке. Систему охлаждения кристаллизатора
промывают в течение 72 ч, контролируя степень загрязнения воды каждые 24 ч. При
неудовлетворительных результатах время промывки увеличивают по указанию
шефмонтажного персонала предприятия-изготовителя или представителя технадзора
заказчика.
Систему охлаждения
слитка без присоединения коллектора с форсунками промывают в течение 48 ч, с
присоединением коллектора - в течение 24 ч; допускается засорение не более 2%
форсунок в течение 2 ч промывки.
Систему охлаждения
машин и экранов промывают в течение 48 ч, контролируя при этом степень
загрязнения отходящей воды в соответствии с проектом.
Оборудование
МНЛЗ радиально-криволинейного типа
10.19. При монтаже
составных частей машины последовательно устанавливают:
стойки под
роликовые секции вторичного охлаждения;
станину съемного
блока;
рамы секций
вторичного охлаждения;
разводку
трубопроводов системы водоохлаждения (частично);
кассеты с роликами;
механизм качания
кристаллизатора;
устройство для
демонтажа роликовых секций;
привод роликовых
секций;
кристаллизатор;
механизм подъема
затравки;
разливочный стенд.
10.20. Допускаемые
отклонения при монтаже стоек под ролики вторичного охлаждения приведены в табл.
25 и на рис. 13.
Таблица 25
─────────────────────────────────────────────┬───────────────────
Отклонение │Размер допускаемого
│ отклонения, мм
─────────────────────────────────────────────┼───────────────────
Высотных
отметок цапф стоек
│ +/- 0,2
Размера
от оси опоры до базовой стенки
│ +/- 0,5
кристаллизатора │
Размера
от оси ручья до фиксированной опоры
│ +/- 0,5
по
внутренней торцевой стенке опоры
│
От
перпендикулярности оси опоры относительно │ 0,2
оси
ручья (на 1 м)
│
От
горизонтальности цапф (на 1 м)
│ 0,1
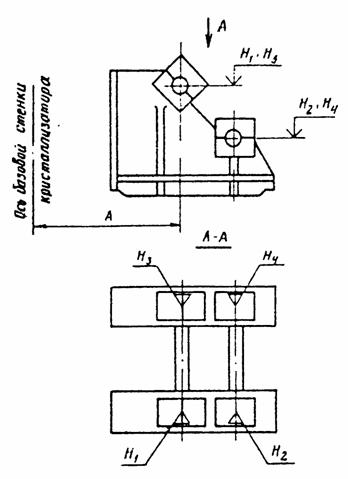
Рис. 13. Выверка
стоек роликов вторичного охлаждения:
А - расстояние от
оси опоры до базовой стенки кристаллизатора;
-
- высотные отметки цапф стойки
После окончательной
выверки нижних роликов подливают стойки.
10.21. На
выверенные стойки устанавливают рамы секций вторичного охлаждения с опорными
осями. Допускаемые отклонения при монтаже рам секций вторичного охлаждения
приведены в табл. 26.
Таблица 26
─────────────────────────────────────────────┬───────────────────
Отклонение │Размер допускаемого
│ отклонения, мм
─────────────────────────────────────────────┼───────────────────
Высотных
отметок привалочных поверхностей рам│
+/- 0,2
на горизонтальном участке под кассеты (или │
шпоночных
пазов)
│
Размера
от базовой стенки кристаллизатора до │
+/- 1
осей
валов червячных редукторов приводов
│
настройки (или до дальнего края шпоночного │
отверстия) │
Размера
от продольной оси ручья до привалоч- │
+/- 1
ной
поверхности рамы под подушки
│
От
перпендикулярности поперечной оси рамы и
│ 0,1
продольной
оси ручья МНЛЗ (на 1 м) │
От
горизонтальности привалочных поверхностей │ 0,1
рамы
под подушки кассет (на 1 м)
│
Углов
между привалочными поверхностями
│ +/- 6''
Высотные размеры
привалочных поверхностей рам или шпоночных лазов регулируют с помощью клиновых
подкладок.
10.22. Кассеты с
роликами перед установкой на рамы секций предварительно выверяют на стенде.
Допускаемые отклонения при выверке кассет с роликами секций вторичного
охлаждения приведены в табл. 27, а при монтаже кассет - в табл. 28.
Таблица 27
─────────────────────────────────────────────┬───────────────────
Отклонение │Размер допускаемого
│ отклонения, мм
─────────────────────────────────────────────┼───────────────────
Размера
от опорной поверхности нижней части
│ -0,15
кассет
до поверхности бочки ролика
│
Прилегания
шаблона к бочкам роликов
│ 0,1
От
параллельности бочки роликов и опорной
│ 0,2
поверхности
кассеты (по длине бочки) │
Таблица 28
─────────────────────────────────────────────┬───────────────────
Отклонение │Размер допускаемого
│ отклонения, мм
─────────────────────────────────────────────┼───────────────────
Высотных
отметок роликов
│ +/- 0,2
Размера
от базовой стенки кристаллизатора до │ +/- 0,5
центра
роликов │
Размера
между крайними роликами кассет по
│ +/- 0,5
центрам
роликов
│
Размера
от продольной оси ручья до края бочки│ +/- 1,5
ролика │
От
перпендикулярности роликов относительно
│ 0,1
продольной
оси ручья (на 1 м) │
От
горизонтальности роликов (на 1 м)
│ 0,1
10.23. Перед
монтажом верхние части секций вторичного охлаждения устанавливают на стенд и
выверяют верхние ролики. Допускаемые отклонения при монтаже верхних частей
приведены в табл. 29.
Таблица 29
─────────────────────────────────────────────┬───────────────────
Отклонение │Размер допускаемого
│ отклонения, мм
─────────────────────────────────────────────┼───────────────────
Размера
между бочками верхнего и нижнего
│ +/- 0,2
ролика │
От
параллельности бочек верхних и нижних
│ 0,15
роликов
между собой (на 1 м)
│
Прилегания
бочки роликов к шаблону
│ 0,2
10.24. Допускаемые
отклонения при монтаже приводов роликов приведены в табл. 30.
Таблица 30
─────────────────────────────────────────────┬───────────────────
Отклонение │Размер допускаемого
│ отклонения, мм
─────────────────────────────────────────────┼───────────────────
Высотной
отметки верхних и нижних ведущих и
│ +/- 0,2
ведомых
валов
│
Размера,
определяющего положение осевой линии│
+/- 0,5
привода
ролика относительно базовой стенки
│
кристаллизатора │
Размера,
определяющего положение оси нижнего │
+0,5
ведущего
вала относительно базовой стенки
│
кристаллизатора │
От
параллельности осей валов
│ 0,5
Отклонение
от соосности
│ 0,3
10.25. Допускаемые
отклонения при монтаже разливочного стенда, механизма качания кристаллизатора,
механизма подъема затравки приведены в табл. 31.
Таблица 31
─────────────────────────────────────────────┬───────────────────
Отклонение │Размер допускаемого
│ отклонения, мм
─────────────────────────────────────────────┼───────────────────
От
совмещения продольных базовых поверхностей│ +/- 0,5
и
осей механизмов относительно соответствую- │
щих
продольных осей машин
│
От
совмещения поперечных базовых поверхностей│ +/- 0,5
и
осей механизмов относительно базовой стенки│
кристаллизатора │
Высотных
отметок базовых поверхностей меха-
│ +/- 0,5
низмов │
От
горизонтальности базовых поверхностей
│ 0,2
механизмов
(на 1 м) │
От
вертикальности базовых поверхностей меха- │ 0,2
низмов
(на 1 м) │
Правильность
установки механизма выверяют по обработанным базовым поверхностям, указанным в
инструкциях предприятия-изготовителя по монтажу соответствующих механизмов.
11.
ИСПЫТАНИЕ СМОНТИРОВАННОГО ОБОРУДОВАНИЯ. ПРИЕМКА РАБОТ
11.1.
Индивидуальное испытание оборудования без нагрузки производят в соответствии с
требованиями СНиП 3.05.05-84 и технической документацией предприятий -
изготовителей оборудования.
11.2. При
индивидуальном испытании оборудования выполняют требования, предусмотренные
рабочей документацией, стандартами и техническими условиями и необходимые для
проведения индивидуальных испытаний отдельных машин, механизмов и агрегатов с
целью подготовки оборудования к приемке рабочей комиссией для комплексного
опробования.
11.3. К началу
индивидуального испытания оборудования должен быть закончен монтаж систем
смазки, гидравлики, пневматики и охлаждения, а также закончены работы по
монтажу и наладке электрооборудования и средств автоматизации, систем защиты и
контроля в объеме, необходимом для проведения индивидуальных испытаний.
11.4. В процессе
испытаний необходимо устранить обнаруженные дефекты монтажа и неисправности
оборудования, которые в первом случае исправляет монтажная организация, а во
втором - предприятие - изготовитель оборудования.
11.5.
Индивидуальные испытания оборудования производит монтажная организация по
программе, согласованной с заказчиком и представителем шефмонтажного персонала
предприятия-изготовителя.
Сроки проведения
индивидуального испытания устанавливают графиками, разработанными
генподрядчиком совместно с механомонтажными, электромонтажными и
электроналадочными организациями и согласованными с заказчиком.
11.6.
Индивидуальное испытание без нагрузки отдельных видов оборудования
сталеплавильных цехов производят с соблюдением требований, изложенных в пп.
11.7 - 11.14 настоящих норм.
11.7. Перед
испытанием конвертера необходимо проверить: затяжку всех болтовых соединений,
наличие смазки на трущихся поверхностях, работу системы жидкой смазки,
срабатывание электрических блокировок и сигнализации и наладку тормозов.
Последовательность
испытания механизмов привода конвертера:
прокручивают привод
наклона совместно с конвертером на 45° в одну и другую сторону на минимальной
скорости;
прокручивают
привод совместно с конвертером на 360° в одну и другую сторону (не менее трех
раз) на минимальной и максимальной скоростях с остановкой конвертера в
промежуточных положениях через 10°.
При испытании
конвертера ведут наблюдения за работой редукторов, соединений валов, тормозов,
систем смазки, состоянием подшипниковых опор, состоянием соединений корпуса
конвертера с кольцом.
Шум в редукторах
должен быть ровным, низкого тона, без дребезжания и стуков; в подшипниковых
опорах не должно быть посторонних звуков (стука, потрескивания, хруста),
температура нагрева подшипников не должна превышать температуру окружающей
среды более чем на 65 °C. Продолжительность бесперебойной работы конвертера - 2
ч. После прокрутки конвертер футеруют и ставят на сушку.
После сушки
футеровки должна быть проведена проверка самовозврата наклоненного конвертера в
исходное положение при отключении и растормаживании двигателей привода.
11.8.
Последовательность испытания установки для подачи кислорода в конвертер:
прокручивают привод
механизма передвижения установки;
прокручивают
механизм подъема фурмы (подъем и опускание). Производят не менее трех подъемов
фурмы на повышенной скорости, испытывают плотность соединения фурмы с рукавами
подачи воды и кислорода на соответствующее давление: рукавов воды - водой,
рукавов кислорода - очищенным сжатым воздухом (при надежно заглушенном рабочем
отверстии фурмы). При испытаниях не должно быть течи воды и пропуска воздуха.
Во время испытания
установки следят за работой редукторов, муфт, тормозов, реечного зацепления,
звездочек, за плавностью перемещения платформ установки и плавностью
перемещения в направляющих каретки и противовеса. Продолжительность испытания
фурмы - 2 ч (при одновременной работе механизма подъема фурмы и подаче
охлаждающей воды).
11.9. При испытании миксера сначала выполняют 50 поворотов
нефутерованного миксера в обе стороны в пределах полного угла на пониженной и
нормальной скоростях с остановками в промежуточных положениях. Затем осуществляют 30 - 40 поворотов миксера с разогретой
футеровкой в обе стороны в пределах полного угла с остановками в промежуточных
положениях, наблюдая за работой редукторов, соединений валов, тормозов, систем
смазки, реечного зацепления, за полнотой опирания бандажей на ролики
опорно-ходовой части и возвращением опорно-ходовой части в первоначальное
положение, правильностью срабатывания шарнирных колен газовоздухопроводов.
11.10. При
испытании электросталеплавильной печи проверяют механизмы наклона печи, подъема
заслонок рабочих окон, подъема свода, поворота свода, зажима и перемещения
электродов. Продолжительность испытания каждого механизма - 10 циклов
бесперебойной работы.
Механизм наклона
испытывают в два этапа:
проверяют
правильность зацепления шипов на секторах люльки с отверстиями в фундаментных
балках (при неподлитой одной балке) трехкратным наклоном люльки в обе стороны
(в пределах рабочих углов наклона); после проверки фундаментную балку подливают
и окончательно закрепляют анкерными болтами;
проверяют работу
механизма (выполняют семь наклонов в обе стороны люльки со смонтированным на
ней оборудованием и с футерованным корпусом печи), регулируя действие каждого
конечного выключателя на заданные проектом положения.
Механизм подъема
свода испытывают пятикратным подъемом и опусканием свода. При испытании
проверяют работу конечных выключателей.
Механизм поворота
свода испытывают пятикратным поворотом тумбы на заданный угол, проверяя работу
привода, прилегание роликов к рельсам, работу стопора, конечных выключателей, и
регулируют командоаппарат.
При испытании
механизма зажима электродов сначала проверяют действие пневмопроводов и
пружинного зажима электродов, затем проверяют работу механизма в проектном
положении с полным набором электродов из 5 секций, а также проверяют надежность
зажима электрода, отсутствие проскальзывания и зависания.
Механизм
перемещения электродов испытывают в три этапа: без электрода, с облегченным
электродом и с полным электродом. При испытании проверяют легкость перемещения
механизма, регулируют положение конечных выключателей и работу командоаппарата.
11.11.
Пусконаладочные работы и индивидуальное испытание электросталеплавильной печи с
гидравлическим приводом производят одновременно с пусконаладочными работами и
испытанием насосно-аккумуляторной станции и электрогидравлического регулятора.
Перед испытанием электросталеплавильной печи проводят промывку и опробование на
плотность и прочность систем гидропровода, водоохлаждения и воздухоподвода,
проверяют уплотнения цилиндров, плунжеров, валов и осей и при необходимости подтягивают
крышки уплотнений.
Составные части и механизмы печи проверяют на соответствие направления
движений надписям на пультах управления, на правильность срабатывания
блокировок и конечных выключателей, отсутствие утечек масла, воды и воздуха в
приводах исполнительных механизмов.
11.12. При
испытании МНЛЗ проверяют механизмы стенда подъемно-поворотного, тележки для
промковшей, механизм качания кристаллизатора, кристаллизатор, механизмы зоны
вторичного охлаждения, тянуще-правильные машины, устройства уборки и хранения
затравки.
Продолжительность
индивидуальных испытаний механизмов без нагрузки, кроме оговоренных особо, - 2
ч, шестеренной клети - 4 ч непрерывной работы.
11.13. По окончании
индивидуальных испытаний без нагрузки оборудование принимает по акту рабочая
комиссия для комплексного опробования.
11.14. При
сдаче оборудования рабочей комиссии монтажная организация предъявляет
техническую документацию согласно СНиП 3.05.05.-84.
11.15. Комплексное
опробование оборудования вхолостую и под нагрузкой производит заказчик с
привлечением представителей генерального подрядчика, субподрядных организаций,
проектировщиков и изготовителей оборудования.
11.16. Монтажная
организация обеспечивает несение дежурств ее инженерно-техническим персоналом
совместно с персоналом эксплуатации и генподрядчика для оперативного
привлечения работников по устранению дефектов монтажных работ, выявленных в
период комплексного опробования оборудования на эксплуатационных режимах.
12. ТЕХНИКА
БЕЗОПАСНОСТИ
12.1. При
выполнении механомонтажных работ необходимо руководствоваться требованиями:
СНиП III-4-80;
системы стандартов
безопасности труда (ССБТ);
санитарно-гигиенических
норм и правил Минздрава СССР;
правил техники
безопасности Госгортехнадзора СССР, Госэнергонадзора Минэнерго СССР;
правил пожарной
безопасности при производстве строительно-монтажных работ ГУПО МВД СССР;
других правил
техники безопасности, утвержденных в установленном порядке органами
Государственного надзора или соответствующими министерствами и ведомствами СССР
по согласованию с Госстроем СССР.
12.2. Конкретные
мероприятия по технике безопасности, средства подмащивания и приспособления для
обеспечения безопасных условий труда должны разрабатываться в ППР.
12.3. Организация
работ в соответствии с ППР, контроль за применением в
соответствии с назначением монтажно-технологической оснастки, грузоподъемных
машин, механизированного инструмента и средств защиты работающих, инструктаж
рабочих о безопасных методах ведения работ возлагается на инженерно-технических
работников строительно-монтажных организаций.
12.4. Монтаж
оборудования производится с применением средств подмащивания, обеспечивающих
удобство работы и безопасность работающих. Средства подмащивания должны
соответствовать требованиям СНиП III-4-80, ГОСТ 12.2.012-75, ГОСТ 24258-80 и
ГОСТ 24259-80.
12.5. Участки
производства работ по монтажу тяжеловесного и крупногабаритного оборудования,
расконсервации и обезжиривания, индивидуального испытания необходимо ограждать
сигнальными и защитными ограждениями по ГОСТ 23407-78 и обозначать знаками
безопасности по ГОСТ 12.4.026-76* и надписями установленной формы.
12.6. Во избежание
падения рабочих монтажные проемы, технологические подвалы и глубокие приямки в
фундаментах должны быть ограждены инвентарными защитными ограждениями,
выполненными в соответствии с ГОСТ 12.4.059-78, или закрыты сплошным настилом.
12.7. Все лица,
занятые на монтажных работах, должны быть обеспечены средствами индивидуальной
защиты в зависимости от вида выполняемых работ и в соответствии с типовыми
отраслевыми нормами бесплатной выдачи спецодежды, спецобуви и предохранительных
приспособлений, утвержденными Госкомтрудом СССР и ВЦСПС, а также ГОСТ
12.4.011-75*.
12.8.
Механизированный инструмент и средства малой механизации, применяемые при
производстве работ, должны быть исправными и использоваться строго по
назначению.
12.9. Кантование и
установка тяжеловесного оборудования в проектное положение с помощью одного или
двух кранов, а также монтаж оборудования в зонах, не обслуживаемых мостовыми
кранами с применением специальных траверс, должны производиться под
непосредственным руководством специально назначенного инженерно-технического
работника.
12.10. Строповку
оборудования и конструкций следует осуществлять за специальные строповочные
приспособления инвентарными стропами или специальными грузозахватными
устройствами, изготовленными по утвержденному проекту. Расстроповку необходимо
производить только после надежного проектного или временного закрепления
монтируемых узлов.
12.11.
Расконсервацию, очистку от коррозии и обезжиривание оборудования необходимо
производить в специальных помещениях или на открытых площадках.
Закрытые помещения
должны быть оборудованы приточно-вытяжной вентиляцией. При использовании
летучих химических веществ (бензина, уайт-спирита и т.п.) воздух в помещении
необходимо периодически проверять на наличие в нем вредных веществ. Содержание
вредных веществ в воздухе рабочей зоны не должно превышать предельно допустимых
концентраций по ГОСТ 12.1.005-76.
12.12. Помещения и
площадки, где проводятся работы по расконсервации и очистке оборудования,
должны быть оборудованы противопожарным инвентарем.
12.13. Химические
материалы, выделяющие вредные или взрывопожароопасные вещества, разрешается
хранить на рабочих местах в количествах, не превышающих сменной потребности.
Использованные
кислотные и щелочные растворы, масла, растворители, обтирочный материал, отходы
ингибированной бумаги должны собираться в специальную тару и регулярно
вывозиться в отведенные места.
12.14. Перед
проведением испытаний оборудования необходимо проверить наличие всех проектных
кожухов, ограждений, систем сигнализации.
Исправление
дефектов, выявленных при испытании на работающем оборудовании, недопустимо.
12.15. При
производстве работ на монтажной площадке одновременно несколькими
строительно-монтажными организациями генподрядчик обязан совместно с
субподрядными организациями разработать мероприятия по охране труда и технике
безопасности, обязательные для всех организаций, принимающих участие в
строительно-монтажных работах.
Приложение
Обязательное
ПЕРЕЧЕНЬ
ОСНОВНЫХ
НОРМАТИВНЫХ ДОКУМЕНТОВ,
ТРЕБОВАНИЯ КОТОРЫХ ДОЛЖНЫ ВЫПОЛНЯТЬСЯ ПРИ МОНТАЖЕ
ОБОРУДОВАНИЯ
СТАЛЕПЛАВИЛЬНЫХ ЦЕХОВ
СНиП 3.05.05-84
"Технологическое оборудование. Основные положения"
СНиП III-4-80
"Техника безопасности в строительстве"
СНиП III-1-76
"Организация строительного производства"
СНиП III-3-81
"Приемка в эксплуатацию законченных строительством предприятий, зданий и
сооружений. Основные положения"
СНиП 3.01.03-83
"Геодезические работы в строительстве"
СНиП 3.02.01-83
"Основания и фундаменты"
СНиП III-15-76
"Бетонные и железобетонные конструкции монолитные"
СНиП III-16-80
"Бетонные и железобетонные конструкции сборные"
СНиП III-18-75
"Металлические конструкции"
СНиП III-Г.10.4-67
"Теплоэнергетическое оборудование. Правила производства и приемки
монтажных работ"
СНиП III-Г.10.12-66
"Оборудование очистки газов. Правила производства и приемки монтажных
работ"
ГОСТ 24444-80
"Оборудование технологическое. Общие монтажно-технологические
требования"
ОСТ 24.010.01-80
"Оборудование металлургическое. Общие технические
требования на изделия внутрисоюзного и экспортного исполнений"
ОСТ 24.290.03-79
"Оборудование и устройства смазочных, гидравлических и пневматических
систем. Общие технические требования"
ОСТ 24.290.05-81Е
"Станции циркуляционных смазочных систем металлургического оборудования.
Общие технические условия"
СН 471-75
"Инструкция по креплению технологического оборудования фундаментными
болтами"
ВСН 361-85/ММСС
СССР "Инструкция по установке технологического оборудования на фундаментах"
ВСН 411-80
"Инструкция по монтажу смазочных, гидравлических и пневматических систем
общепромышленного назначения"
"Правила
устройства и безопасной эксплуатации грузоподъемных кранов". Утверждены Госгортехнадзором СССР 30.12.69
"Правила
пожарной безопасности при производстве строительно-монтажных работ". Утверждены ГУПО МВД СССР 04.11.77
"Правила
пожарной безопасности при производстве сварочных и других огневых работ на
объектах народного хозяйства". Утверждены ГУПО
МВД СССР, Госгортехнадзором СССР и ВЦСПС 29.12.72
"Положение о
взаимоотношениях организаций генеральных подрядчиков с субподрядными
организациями". Утверждены Госстроем СССР и
Госпланом СССР 31.07.70 с изменением от 31.05.75
"Правила о
договорах подряда на капитальное строительство"