Утверждены
Директором НИИЖБ
15 апреля 1986 года
РЕКОМЕНДАЦИИ
ПО ПРИМЕНЕНИЮ ДОБАВОК СУПЕРПЛАСТИФИКАТОРОВ
В ПРОИЗВОДСТВЕ СБОРНОГО И МОНОЛИТНОГО ЖЕЛЕЗОБЕТОНА
Печатается по
решению секции технологии бетонов НТС НИИЖБ Госстроя СССР от 15 апреля 1986 г.
Рекомендации
содержат основные положения по применению суперпластификаторов (СП) в
технологии тяжелого, легкого и ячеистого бетонов. Приведены характеристики
различных СП, методика подбора состава бетона. Показана эффективность СП и
особенности их применения в различных видах бетонов, изделий и конструкций,
технологиях их получения. Даны указания по контролю за
производством работ и качеством бетона, а также по технике безопасности и
охране труда.
Предназначены для
инженерно-технических работников строительных и заводских лабораторий,
промышленных предприятий, строительных, проектных и научно-исследовательских
организаций, занимающихся вопросами исследования, проектирования и изготовления
сборных и монолитных бетонных и железобетонных изделий и конструкций.
ПРЕДИСЛОВИЕ
Рекомендации
разработаны в развитие СНиП 3.09.01-85 "Производство сборных
железобетонных конструкций и изделий" и СНиП III-15-76 "Бетонные и
железобетонные конструкции монолитные" на основании проведенных
научно-исследовательских работ и имеющегося опыта по применению
суперпластификаторов в технологии сборного и монолитного бетона и железобетона.
Рекомендации
разработаны НИИЖБ Госстроя СССР (д-р техн. наук, проф. В.Г. Батраков, канд.
техн. наук Е.С. Силина, доктора техн. наук, профессора Ф.М. Иванов, Б.В. Гусев,
Л.А. Малинина, Н.А. Маркаров, В.И. Агаджанов, А.Т. Баранов, К.Д. Некрасов,
канд. хим. наук В.Р. Фаликман, кандидаты техн. наук Б.А. Усов, М.Г. Булгакова,
А.Л. Ционский, В.С.
Гершвальд, Т.А. Ухова, Р.К. Житкевич, Л.И. Будагянц, Н.Г. Матков, С.С.
Каприелов, С.А. Высоцкий, Н.П. Жданова, Б.Г. Веснин, А.С. Зурабян, В.А.
Беликов, Г.М. Мартиросов, Н.Ф. Башлыков, Л.А. Литвак, В.А. Морозов, И.И. Ершов,
инженеры М.И. Бейлина, М.В. Работина, В.П. Павлов, А.Г. Замиховский, И.А.
Романова, А.Т. Ханларов) и ЦНИИОМТП Госстроя СССР (кандидаты техн. наук Ю.Б.
Чирков, Е.П. Мазов, инженеры В.П. Чураков, Т.А. Пастухова), при участии ЦНИИС
Минтрансстроя СССР (кандидаты техн. наук В.С. Гладков, Э.А. Виноградова),
ВНИИжелезобетона Минстройматериалов СССР (канд. техн. наук В.Г. Довжик, д-р
техн. наук Н.Н. Долгополов, кандидаты техн. наук Ш.Т. Бабаев, Ю.И.
Долинский), Минстроя УССР (канд. техн. наук М.Ш. Файнер), Донецкого
ПромстройНИИпроекта (кандидаты техн. наук Ю.П. Чернышев, Л.А. Козлова),
Управления по элеваторостроению и специальным работам Агропромстроя РСФСР
(канд. техн. наук Э.И. Фурманов), Карагандинского политехнического института
(инж. И.И. Либерман) и Ивановского инженерно-строительного
института (канд. техн. наук Г.В. Серегин).
Рекомендации
составлены для использования при широком внедрении суперпластификаторов на заводах
и стройках страны.
В целях определения
научно-технической эффективности в результате применения настоящих Рекомендаций
дирекция НИИЖБ просит выслать "Справку" по форме, указанной в Прил. 7.
Все замечания и
пожелания просим направлять по адресу: 109389, Москва, 2-я Институтская ул., 6.
НИИЖБ Госстроя СССР, лаборатория N 18.
Дирекция НИИЖБ
1. ОБЩИЕ
ПОЛОЖЕНИЯ
1.1. Настоящие
Рекомендации распространяются на применение добавок суперпластификаторов (СП) в
бетонах на плотных и пористых заполнителях, в жаростойких бетонах плотной
структуры, твердеющих при тепловой обработке и в естественных условиях, а также
в ячеистых бетонах.
1.2.
Суперпластификаторы следует применять с целью получения следующих эффектов:
придания высокой
подвижности бетонным смесям (например, от 2 - 4 см до 20 см и более) без
последующего снижения прочности бетонов;
повышения
прочности, непроницаемости и других показателей качества бетонов за счет
водоредуцирующего действия;
получения
комбинированного эффекта с частичным использованием первых двух.
Схема, отражающая
техническую эффективность применения СП в бетонах, дана на рис. 1.
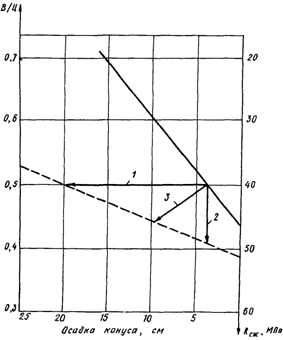
Рис. 1.
Схема влияния СП на свойства
бетонной смеси и
бетона
_____ - без
добавок; ---- - с добавкой СП;
1 - разжижающий
эффект СП; 2 - водоредуцирующий
эффект СП; 3 -
комбинированный эффект СП
1.3.
Целесообразность применения СП определяется достижением различных технологических
и экономических показателей эффективности при производстве железобетонных
изделий и конструкций и возведении сооружений, а также показателей
экономической эффективности при их эксплуатации.
1.4. Для повышения
показателей качества бетонных смесей и бетонов целесообразно применять СП в
комплексе с другими модификаторами: регуляторами схватывания и твердения,
стабилизаторами, воздухововлекающими добавками, ускорителями твердения и т.д.
1.5. Расчет
железобетонных конструкций из бетонов с суперпластификаторами может
производиться по СНиП 2.03.01-84 "Бетонные и железобетонные
конструкции".
2.
МАТЕРИАЛЫ
2.1. В
качестве вяжущих для тяжелых, легких и ячеистых бетонов рекомендуется применять
цементы по ГОСТ 10178-85 и ГОСТ 22266-76. Не следует использовать
пластифицированные цементы. Возможность применения других вяжущих определяется
экспериментальной проверкой и технико-экономическим обоснованием.
2.2. Для
высокопрочных бетонов (марок 600 и выше) рекомендуется использовать
портландцементы с нормальной густотой цементного теста не более 27%. Применение
цементов, обладающих признаками ложного схватывания, разрешается по получении
положительных результатов лабораторных испытаний.
2.3. Для
напрягающего бетона в качестве вяжущего рекомендуется применять: НЦ-10 (ТУ
21-20-48-82 Минстройматериалов СССР), НЦ-20 и НЦ-40 (ТУ 21-20-18-80
Минстройматериалов СССР).
2.4. Для
жаростойкого бетона в качестве вяжущих следует использовать:
шлакопортландцемент с активностью не ниже 40 МПа (ГОСТ 10178-85) с содержанием
шлака не менее 25% массы цемента, глиноземистый цемент с активностью 40 МПа
(ГОСТ 969-77).
2.5. Не следует
применять горячие цементы (с температурой выше 40 °C) по причине их повышенной
водопотребности, перерасхода цемента и быстрой потери подвижности смеси (в
бетонах по пп. 2.1 - 2.4).
2.6. В качестве
крупных заполнителей для тяжелого бетона следует применять материалы,
удовлетворяющие требованиям ГОСТ 26633-85, а также ГОСТ 10268-80, ГОСТ 8267-82,
ГОСТ 10260-82, ГОСТ 8268-82.
2.7. Для высокопрочного
бетона рекомендуется применять щебень, получаемый дроблением прочных (но менее
100 МПа) горных пород, с шероховатой поверхностью (граниты, диабазы, кремнистые
известняки и др.). Максимальную крупность зерен щебня следует ограничить
величиной, равной не более 1/3 толщины конструкции и 2/3 расстояния между
арматурными стержнями. Максимально допустимая крупность щебня - 40 мм.
2.8. Для легких
бетонов в качестве крупных заполнителей следует применять материалы по ГОСТ
9757-83 и ГОСТ 25820-83.
2.9. Для изготовления
жаростойких бетонов в качестве заполнителей (легкого и крупного) следует
применять шамотные заполнители, удовлетворяющие требованиям ГОСТ 20955-75* и
ГОСТ 23037-78.
2.10. В
качестве мелких заполнителей для тяжелых бетонов рекомендуется применять пески
по ГОСТ 10268-80 и ГОСТ 8736-85.
2.11. Для
высокопрочного бетона следует применять мелкий заполнитель, который должен
состоять из зерен кварца и полевого шпата. Рекомендуется предпочитать пески,
имеющие шероховатую поверхность зерен (овражные).
2.12. При
изготовлении мелкозернистых бетонов предпочтение следует отдавать горным
(овражным) пескам в сравнении с речными или морскими песками. В качестве
мелкого заполнителя кроме песков, указанных в пп. 2.10 и 2.11 настоящих
Рекомендаций, допускается (после проведения соответствующих испытаний в бетоне
и технико-экономических расчетов) применение отходов от дробления плотных
природных каменных пород (гранитные высевки) и др.
2.13. Для легких
бетонов следует применять мелкие заполнители: плотные пески по ГОСТ 8736-85,
пористые пески по ГОСТ 9757-83, а также их смеси.
2.14. В качестве
мелких заполнителей для тяжелых и легких бетонов рекомендуется также
использовать золы и золошлаковые смеси ТЭС, отвечающие требованиям ГОСТ
25818-83 и ГОСТ 25592-83.
2.15. Для
изготовления ячеистых бетонов следует применять материалы в соответствии с ГОСТ
25485-82 и "Инструкцией по изготовлению изделий из ячеистого бетона"
СН 277-80 (М., Стройиздат, 1981).
2.16. Вода,
применяемая для изготовления бетонов с добавкой СП и для ухода за ними, должна
соответствовать ГОСТ 23732-79.
2.17. В качестве
модификаторов бетонных смесей и бетонов рекомендуется применять СП С-3, Дофен,
а также 10-03, МФ-АР и 40-03, выпуск которых в настоящее время ограничен.
Свойства СП даны в Прил. 1.
2.18. В бетонах, к
которым предъявляются высокие требования по морозостойкости (дорожные и
аэродромные покрытия, гидротехнические, туннельные и мостовые конструкции и
сооружения), следует предусматривать применение СП совместно с
воздухововлекающими добавками, обеспечивая необходимое воздухосодержание
бетонных смесей, установленное нормативными документами.
2.19. Для улучшения
сохраняемости бетонной смеси с СП рекомендуется использовать комплексные
добавки в соответствии с "Рекомендациями по приготовлению бетонных смесей
повышенной сохраняемости с химическими добавками" (М., НИИЖБ, 1983).
3.
ЭФФЕКТИВНОСТЬ ПРИМЕНЕНИЯ СУПЕРПЛАСТИФИКАТОРОВ
3.1. Перечень
показателей эффективности, получаемых за счет применения СП в сборных
железобетонных конструкциях, представлен в табл. 1, в монолитных железобетонных
конструкциях - в табл. 2.
Таблица 1
Технологические,
экономические и социальные
показатели
эффективности, достигаемые за счет
применения СП в
сборных железобетонных конструкциях
─────────────────────────────────────────────┬─────────────────────────────
Наименование показателей │ Наличие показателей
│
эффективности и их величины
├────────────┬────────────────
│ при │ при ОК =
Const
│В/Ц =
Const │
─────────────────────────────────────────────┼────────────┼────────────────
1 │ 2
│ 3
─────────────────────────────────────────────┼────────────┼────────────────
1.
Сокращение времени и интенсивности │В 3 - 5 раз │В 1,3
- 1,5 раза
вибрации (либо сокращение числа вибраторов. │ │
В отдельных случаях отказ от вибрации) │ │
2.
Сокращение продолжительности формования
│2,5 - 3 "
│ 1,2 - 1,3 "
изделий,
конструкций, сооружений
│ │
3.
Экономия электроэнергии при приготовлении,│2,5 - 3,5 " │ 1,1 - 1,3
"
транспортировании и укладке бетонной
смеси │ │
4.
Снижение трудозатрат при изготовлении
│ 2 - 3 " │ 1,2 - 1,4
"
изделий
│ │
5.
Увеличение срока службы вибраторов, форм, │1,5 - 2 " │ 1,1 - 1,3
"
сокращение
затрат на их ремонт
│ │
6.
Снижение металлоемкости форм
│1,1 - 1,2 " │
-
(при
проектировании)
│ │
7.
Улучшение поверхности изделий, уменьшение │1,1 - 1,3 " │ 1,05
- 1,15 "
количества пор (при горизонтальном │ │
формовании) │ │
8.
Уменьшение операций по доделке готовых
│1,1 - 1,3 " │ 1,05 - 1,15 "
изделий
│ │
9.
Сокращение режима ТВО, в том числе до
│ - │ 2 - 5
передачи
усилия обжатия арматуры на бетон
│ │
(для
преднапряженных конструкций), ч │ │
10.
Снижение температуры, изотермического │ 10 - 15 │
15 - 25
прогрева,
°C
│ │
11.
Экономия пара, %
│ 10 - 15 <*>│
15 - 20
12.
Увеличение оборачиваемости форм
│ 5 - 10 │
10 - 20
(сокращение
сроков снятия опалубки) и
│ │
коэффициента
использования оборудования, %
│ │
13.
Увеличение производительности труда │ 10 - 30 │
30 - 50
(выпуска
продукции), %
│ │
14.
Сокращение парка форм, %
│ 5 - 10 │
10 - 20
15.
Экономия цемента <**>, %
│ - │
15 - 25
16.
Улучшение условий труда, снижение уровня │В 3 -
5 раз │В 1,3 - 1,5 раза
шума
и вибровоздействий
│ │
17.
Замена цемента на более низкую марку
│ - │ +
(или
на ШПЦ той же марки)
│ │
18.
Замена крупного плотного заполнителя
│ - │ +
на
менее плотный
│ │
19.
Замена крупного заполнителя на мелкий │
+ <***> │ +
20.
Снижение себестоимости продукции, руб./м3│ 1,2 - 5 │
4 - 8
--------------------------------
<*>
При использовании литых бетонных смесей иногда целесообразно увеличивать время
предварительной выдержки за счет сокращения на тот же период времени
изотермического прогрева.
<**>
Использование СП только в целях экономии цемента рекомендуется осуществлять в
тех случаях, когда стоимость его высока, и расходы, связанные с применением СП,
значительно перекрываются стоимостью сэкономленного цемента. Ориентировочные
показатели экономии цемента в бетонах различных марок даны в табл. 5.
<***>
В случае применения литых смесей замену части крупного заполнителя (15 - 10%)
на мелкий целесообразно проводить с целью снижения
расслаиваемости бетонной смеси.
Примечания. 1. За
эталон приняты бетонная смесь с ОК = 2 - 4 см и бетон
без добавок.
2. Знак
"+" означает наличие эффекта, знак "-"
- его отсутствие.
Таблица 2
Технологические,
экономические и социальные
показатели
эффективности, достигаемые
за счет применения
СП в монолитном строительстве
─────────────────────────┬────────────┬─────────────────┬──────────────────
Наименование
показателей │Бетонирова- │ Безвибрационное
│ Безвибрационное
│ние
набивных│ бетонирование │
бетонирование
│свай │ зданий в
│ зданий в щитовой
│напорным │
скользящей │ переставной
│методом │
опалубке │опалубке (аналог -
│(аналог
ВПТ)│ (аналог - │
традиционная
│ │ традиционная
│ технология)
│ │ технология)
│
─────────────────────────┼────────────┼─────────────────┼──────────────────
Снижение
трудоемкости │
В 4,4 раза │ В 1,5 раза │
В 1,3 раза
работ │ │ │
Снижение
расхода основных│ │ │
строительных
материалов: │
│ │
бетона, % │ 9
│ - │ -
арматуры, % │ 6
│ - │ -
Снижение
затрат │ -
│ 5 │ 3
на
механизацию, % │ │ │
Снижение
энергозатрат, % │ 23 │ 15
│ 11
Увеличение
себестоимости │ 2,0 │ 2,0
│ 2,0
бетона,
% │ │ │
Снижение
себестоимости │ 22
│ 7 │ 6
бетонирования,
% │ │ │
Сокращение
сроков │ В
2,2 раза │ В 1,05 раза │
В 1,1 раза
строительства │ │ │
Снижение
удельных
│ 11 │ 4
│ 4
капитальных
вложений, % │ │ │
Примечание. За
эталон приняты бетонная смесь и бетон без добавок.
3.2. В табл. 3
представлены показатели качества бетонных смесей и бетонов с СП по сравнению с
бетонной смесью и бетоном без добавки.
Таблица 3
Показатели
качества бетонных
смесей и бетонов с
добавками СП
──────────────────────────────────┬────────────────────────────────────────
Свойства
бетонных смесей и бетонов│
Ориентировочные показатели качества
│ бетонных смесей и бетонов с СП, %
├─────────────┬───────────┬──────────────
│ марок
│ марок │мелкозернистых
│ M300
- M500 │M600 - M800│
марок
│ │ │ M200 - M800
├─────────────┴───────────┴──────────────
│ при ОК,
см
├──────┬──────┬───────────┬──────┬───────
│2 - 4
│>= 20 │ 2 - 4 │2 - 4 │15 - 20
──────────────────────────────────┼──────┼──────┼───────────┼──────┼───────
1.
Водоцементное отношение
│ 80 │ 100
│ 75 │
80 │ 100
2.
Удобоукладываемость │
70 │ 20
│ 70 │
70 │ 25
3.
Воздухосодержание
│101,5 │ 103
│ 101 │ 102
│ 104
4.
Предел прочности при сжатии │
125 │ 100 │
130 │ 120 │
100
5.
Коэффициент призменной │ 105 │
95 │ 100
│ 100 │ 95
прочности │ │ │ │ │
6.
Прочность при осевом растяжении│ 105
│ 100 │ 105
│ 105 │ 100
7.
Прочность на растяжение │
105 │ 100 │
105 │ 105 │
100
при
изгибе │
│ │ │ │
8.
Начальный модуль упругости │
100 │ 95
│ 100 │ 100
│ 100
9.
Деформации усадки │
100 │ 110 │
110 │ 100 │
105
10.
Деформации ползучести
│ 95 │ 110
│ 110 │
75 │ 120
11.
Водопоглощение
│ 70 │ 100
│ 75 │
70 │ 85
12.
Водонепроницаемость │
300 │ 100 │
300 │ 200 │
110
13.
Морозостойкость │
130 │ 100 │
130 │ 120 │
100
14.
Коррозионная стойкость │
- │ -
│ - │ 125 │
100
в
сульфатных средах
│ │ │ │ │
15.
Стойкость в условиях │
130 │ 100 │
130 │ -
│ -
капиллярного
подсоса │ │ │ │ │
16.
Защитное действие по отношению│ 125
│ 100 │ -
│ - │
-
к
арматуре
│ │ │ │ │
Примечания. 1.
Показатели приведены для бетонов с оптимальной дозировкой СП С-3.
2. За 100% приняты
показатели качества для бетонов эталонного состава без СП с ОК
= 2 - 4 см.
3.3. Эффективность
СП зависит от минералогического и вещественного состава цемента, тонкости его
помола, состава бетона, технологии изготовления изделий и конструкций, а также
от дозировки СП. Границы оптимальных дозировок СП приведены в табл. 4. Уточнение
оптимальной дозировки производится на конкретных материалах и составах бетона,
применительно к конкретной технологии и условиям производства.
Таблица 4
Оптимальные
дозировки суперпластификаторов
──────────────────────────────┬────────────────────────────────────────────
Марка СП │ Границы оптимальных дозировок СП, %
──────────────────────────────┼────────────────────────────────────────────
С-3 │ 0,3 - 1,0
МФ-АР │ 0,3 - 1,0
10-03 │ 0,3 - 1,0
40-03 │ 0,2 - 1,0
Дофен │ 0,7 - 1,0
Примечание.
Дозировка СП дана в % массы цемента в пересчете на сухое вещество.
Таблица 5
Ориентировочные
величины снижения расхода цемента в бетонах
различных марок при
использовании суперпластификатора С-3
─────────────┬─────────────┬───────────────────────────────────────────────
Марка
бетона │ ОК,
см │ Снижение расхода цемента, %, при введении
│ │ суперпластификатора С-3 в количестве, %
│
├───────────────┬───────────────┬───────────────
│ │ 0,4
│ 0,8 │ 1,2
─────────────┼─────────────┼───────────────┼───────────────┼───────────────
M200
│ 2 - 4 │
2 - 3 │ 3 - 5
│ 5 - 7
│ 4 - 5
│ 3 - 4 │
5 - 7 │ 7 - 9
│ 12 - 14
│ 4 - 6 │
7 - 9 │ 10 - 12
│ 22 - 24
│ 6 - 8 │
10 - 12 │ 12 - 15
─────────────┼─────────────┼───────────────┼───────────────┼───────────────
M300
│ 2 - 4 │
3 - 5 │ 4 - 6
│ 6 - 8
│ 4 - 5
│ 4 - 6 │
8 - 10 │ 10 - 12
│ 12 - 14
│ 5 - 7 │
10 - 12 │ 12 - 15
│ 22 - 24
│ 12 - 15 │
18 - 20 │ 20 - 22
─────────────┼─────────────┼───────────────┼───────────────┼───────────────
M400
│ 2 - 4 │
6 - 8 │ 8 - 10
│ 10 - 12
│ 4 - 5
│ 8 - 10 │
10 - 12 │ 12 - 15
│ 12 - 14
│ 10 - 12 │
12 - 14 │ 15 - 18
│ 22 - 24
│ 12 - 15 │
18 - 20 │ 20 - 25
─────────────┼─────────────┼───────────────┼───────────────┼───────────────
M500
│ 2 - 4 │
10 - 12 │ 16 - 18
│ 18 - 20
│ 4 - 5
│ 12 - 15 │
18 - 20 │ 20 - 22
│ 12 - 14
│ 15 - 18 │
20 - 22 │ 22 - 25
─────────────┼─────────────┼───────────────┼───────────────┼───────────────
M600
│ 2 - 4 │
12 - 14 │ 18 - 20
│ 20 - 22
│ 4 - 5
│ 14 - 16 │
20 - 22 │ 22 - 25
3.4. Для всех видов
СП их оптимальная дозировка увеличивается с увеличением содержания
в составе клинкера.
3.5. С увеличением
содержания щелочей, а также стеклофазы в составе цементного клинкера эффект
пластификации от применения СП (при их одинаковой дозировке) снижается.
3.6. Эффективность
СП в наибольшей степени проявляется в чистоклинкерных портландцементах. При
применении портландцементов с активными минеральными добавками эффективность СП
снижается в тем большей
степени, чем выше гидравлическая активность и больше количество введенной
минеральной добавки.
3.7. Эффективность
добавки увеличивается по мере увеличения расхода цемента в составе бетона и
исходной подвижности бетонной смеси.
3.8. Разжижающий
эффект от применения СП в напрягающих бетонах используется для облегчения
укладки, исключения "ложного" схватывания, увеличения сроков
сохраняемости бетонной смеси. При этом имеет место повышение прочности и
самонапряжения на 10 - 20%, морозостойкости бетона - на 20 - 25%, а также водо-
и газонепроницаемости.
3.9. Эффект
повышения прочности и самонапряжения используется:
для увеличения
прочности и самонапряжения на 20 - 30%, морозостойкости на 30 - 50%, а также
водонепроницаемости и газонепроницаемости бетонов;
для сокращения
режима ТВО на 1 - 2 ч или сокращения сроков достижения проектной прочности и
самонапряжения для бетона нормального твердения;
для экономии
цемента до 100 кг/м3.
3.10. В ячеистых
бетонах эффективность СП имеет место при применении в качестве вяжущего
портландцементов и в меньшей степени - смешанного вяжущего (портландцемент +
известь), а в качестве кремнеземистого компонента - тонкомолотого кварцевого
песка.
3.11. Техническая
эффективность СП определяется в соответствии с "Рекомендациями по оценке
эффективности применения добавок в бетоне" (М., НИИЖБ, 1984).
3.12.
Технико-экономическая эффективность СП определяется в соответствии с
"Рекомендациями по технико-экономической оценке применения добавок в
бетоне" (М., НИИЖБ, 1985) и Прил. 2 настоящих Рекомендаций.
Примеры
эффективного использования СП даны в Прил. 3.
4. ОБЛАСТИ
ПРИМЕНЕНИЯ СУПЕРПЛАСТИФИКАТОРОВ
4.1. Рациональные
области применения суперпластификаторов (табл. 6) определяются их технической и
технико-экономической эффективностью (см. табл. 1 - 3), зависящей и от
стоимости СП (табл. 7).
Таблица 6
Рациональные
области применения
различных видов
суперпластификаторов
────────────────────────────────────────┬──────────────────────────────────
Виды изделий и конструкций │ Марка суперпластификатора
├──────┬──────┬──────┬──────┬──────
│
С-3 │МФ-АР │10-03
│40-03 │Дофен
────────────────────────────────────────┼──────┼──────┼──────┼──────┼──────
Железобетонные
изделия и конструкции
│ + │
- │ -
│ + │
+
из
бетона марок до M500 включительно
│ │ │ │ │
Железобетонные
конструкции из │ +
│ + │
+ │ -
│ -
высокопрочных
бетонов марок выше M500 │ │ │ │ │
Напорные
виброгидропрессованные трубы
│ + │
+ │ +
│ - │ -
Таблица 7
Стоимость
суперпластификаторов
─────────────┬────────────────────┬────────────────────────────────────────
Марка СП
│Стоимость СП (сухого│ N прейскуранта (ПР)
│ продукта), руб. │
─────────────┼────────────────────┼────────────────────────────────────────
С-3
│ 340 │Пр. N
05-01, поз. 1-1170, дополнение 1,
│ │2, 3 (утверждено
Госкомцен СССР,
│ │Постановление N 352
от 6/V-80)
МФ-АР
│ 366
<*> │Пр. N
05-02, поз. 2-073, дополнение 109
│ │(утверждено
Госкомцен СССР,
│ │Постановление N 395
от 20/V-86)
10-03
│ 1115 │Согласованная цена на опытно-
40-03
│ 246 │промышленные партии
Дофен
│ 295 │То же
--------------------------------
<*> Стоимость
20%-ного раствора.
4.2. Разжижающий
эффект СП целесообразно использовать при бетонировании тонкостенных
густоармированных, вертикально формуемых конструкций, конструкций сложной
конфигурации, монолитных полов, дорог и т.д.
4.3. Повышение
прочностных характеристик бетона рекомендуется использовать для получения
высокопрочных бетонов, увеличения выпуска продукции, экономии цемента,
сокращения сроков передачи напряжения с арматуры на бетон и т.д.
4.4. В большинстве
случаев следует использовать комбинированный эффект от применения СП, дающий
максимальную технико-экономическую эффективность.
4.5. В технологии
изготовления высокопрочных бетонов СП целесообразно применять:
с целью осуществления возможности применения портландцементов марки
500 (в ряде случаев имеется возможность получения бетонов марки M600 на
портландцементе и шлакопортландцементе марки 400);
при наличии
высокомарочных цементов (марок 550 и 600) - с целью снижения их расхода;
с целью замены
высокопрочного крупного заполнителя на менее прочный.
4.6. При применении
СП возможно получение высокопрочных бетонов, изготавливаемых из высокоподвижных
и литых бетонных смесей.
4.7. В бетонах для
транспортных сооружений рекомендуется применять С-3 при соблюдении требований
нормативных документов и ведомственных рекомендаций по производству бетонных
работ в транспортном строительстве, в том числе с применением С-3. Другие СП
допускается применять при наличии дополнительных рекомендаций, учитывающих
специфические особенности конструкций транспортных сооружений при обязательном
технико-экономическом обосновании.
Рациональные
области применения СП при изготовлении сборных и монолитных конструкций для
транспортного строительства представлены в Прил. 3.
4.8. В
мелкозернистых бетонах суперпластификатор С-3 <*> рекомендуется применять
с целью:
расширения
возможности замены бетона на крупном заполнителе мелкозернистым бетоном;
разжижения бетонных
смесей и облегчения их укладки в изделия и конструкции, в том числе
тонкостенные густоармированные вертикально формуемые;
сокращения расхода
цемента.
--------------------------------
<*>
Применение других СП возможно после их предварительной
проверки и при наличии экономического эффекта.
4.9.
Суперпластификатор С-3 рекомендуется применять в напрягающих бетонах с расходом
цемента от 450 до 600 кг/м3 и вводить в состав бетонной смеси с целью:
разжижения бетонной
смеси без снижения прочностных показателей;
повышения прочностных характеристики бетона при сжатии, осевом
растяжении и растяжении при изгибе без увеличения расхода цемента;
повышения
самонапряжения;
дополнительного
повышения водонепроницаемости и морозостойкости;
обеспечения
проектной прочности на сжатие и самонапряжение с уменьшенным расходом цемента.
4.10. При
приготовлении конструкционных легких бетонов марок M150 - M500 СП рекомендуется
применять в целях:
повышения
подвижности бетонной смеси;
повышения прочности
бетона;
снижения расхода
цемента.
4.11.
Суперпластификаторы могут применяться при изготовлении
конструкционно-теплоизоляционных легких бетонов марок M35 - M100 одновременно с
воздухововлекающими добавками в целях уменьшения водосодержания бетонной смеси
при оптимальной жесткости (5 - 10 с) и отпускной влажности бетона,
приготовленного на водопотребных мелких заполнителях (золе и золошлаковой смеси
ТЭС, вспученном перлитовом песке и др.).
4.12.
Суперпластификатор С-3 рекомендуется применять в жаростойких бетонах при
изготовлении изделий или монолитных футеровок и конструкций с большим процентом
армирования с целью разжижения бетонной смеси без снижения физико-механических
и термических свойств жаростойкого бетона.
4.13. Жаростойкие
бетоны на шлакопортландцементе с добавкой суперпластификатора С-3 рекомендуется
применять для сооружения фундаментов под различные тепловые агрегаты и для
футеровки тепловых агрегатов с температурой службы не более 1000 °C.
4.14. Жаростойкие
бетоны на глиноземистом цементе с добавкой суперпластификатора С-3
рекомендуется применять для футеровки тепловых агрегатов с температурой службы
не более 1300 °C.
4.15. При
изготовлении изделий из ячеистого бетона рекомендуется применять комплексную
добавку, состоящую из суперпластификатора С-3 и щелочного компонента.
4.16. Комплексную
добавку следует вводить в состав ячеисто-бетонной смеси с целью:
регулирования
процессов ее структурообразования и твердения;
интенсификации
процессов изготовления изделий из ячеистого бетона (интенсификации процесса
нарастания пластической прочности, сокращения предварительной выдержки перед
тепловлажностной обработкой, ускорения самого процесса обработки) и увеличения
выпуска продукции;
улучшения
физико-механических свойств ячеистого бетона (снижения плотности при заданной
прочности, повышения морозостойкости, трещиностойкости, снижения влажности
изделий).
5. ПОДБОР И
НАЗНАЧЕНИЕ СОСТАВА БЕТОНА
5.1. Подбор
состава бетона следует производить в соответствии с ГОСТ 27006-86 любым
апробированным на практике способом, обеспечивающим получение бетона в
конструкциях и сооружениях с показателями качества, нормируемыми стандартами
или проектной документацией.
5.2. Подбор
состава бетона с СП заключается в корректировке рабочего состава бетона без
добавки с учетом целей применения суперпластификатора.
5.3. Подбор состава
бетона с СП следует проводить в лабораторных условиях на сухих заполнителях,
при этом следует учитывать воду, входящую в состав раствора СП. Перемешивание
бетонной смеси предпочтительнее осуществлять механизированным способом, максимально
приближенным к условиям производства и обеспечивающим равномерность
распределения СП, однородность смеси и соответствие ее параметров нормативным
требованиям.
Тяжелый
бетон
5.4. Введение СП в
состав бетонной смеси рекомендуется производить:
а) одновременно со
всем количеством воды затворения;
б) в предварительно
перемешанную с большей частью воды затворения бетонную смесь;
в) после
приготовления бетонной смеси.
Введение СП в
соответствии с п. 5.4 "б" и "в" наиболее эффективно с точки
зрения увеличения подвижности и сохраняемости бетонной смеси. Выбор способа
введения СП зависит от потребности производства, применяемой технологии и
точности дозирования СП.
5.5. В тех
случаях, когда СП предназначаются для разжижения бетонной смеси, корректировка
ее состава заключается в выборе оптимальной дозировки СП и установлении доли
песка r в смеси заполнителей. Рекомендуемые дозировки СП приведены выше (табл.
4). С увеличением исходной подвижности смеси дозировка, необходимая для
получения высокоподвижных и литых бетонных смесей, снижается. Корректировку
состава рекомендуется производить в следующей последовательности:
а) подбирают состав
бетона без добавки (эталон) по п. 5.1 настоящих Рекомендаций с исходной осадкой
конуса (или жесткостью) бетонной смеси, применяемой на производстве;
б)
изготавливают второй состав бетона, отличающийся от первого тем, что в него
дополнительно вводят СП, например, в количестве 0,5% массы цемента; замеряют
осадку конуса (или жесткость) бетонной смеси;
в) в случае, если
осадка конуса (или жесткость) больше или меньше требуемой, соответственно
уменьшают или увеличивают дозировку СП на 0,05; 0,1; 0,15; 0,2% и т.д. в
зависимости от того, насколько осадка конуса (или жесткость) бетонной смеси,
полученной по п. 5.5 "б", отличается от
требуемой;
г) при
необходимости получения высокоподвижных и литых бетонных смесей следует
обращать внимание на их связность. В случае появления расслаиваемости бетонной
смеси необходимо ее уменьшить или исключить путем применения следующих технологических
приемов:
снижения дозировки
добавки до получения требуемой подвижности бетонной смеси;
введения
тонкомолотых наполнителей (зол ТЭС по ГОСТ 25818-83 и ГОСТ 25592-83, шлаков
гранулированных доменных и электротермофосфорных по ГОСТ 3476-74);
снижения
водосодержания бетонной смеси;
увеличения доли
песка в смеси заполнителей с соответствующим уменьшением доли крупного
заполнителя. В случае необходимости количество песка рекомендуется увеличивать
до 45% от общего объема заполнителей. Увеличение доли песка
зависит от вида и крупности применяемых заполнителей, расхода цемента и
подвижности бетонной смеси;
д) изготовленные и
пропаренные образцы испытывают в установленные сроки на сжатие;
е) если подобранный
состав бетона с СП имеет такую же прочность, как и бетон эталонного состава, и
удовлетворяет проектным требованиям, то он принимается за основу при назначении
производственного состава;
ж) если бетон с СП,
изготовленный из высокоподвижной или литой бетонной смеси, имеет прочность
ниже, чем эталон, то могут быть рекомендованы следующие способы повышения
прочности бетона:
изменение режима
термообработки в соответствии с п. 6.30 настоящих Рекомендаций;
увеличение
дозировки СП на 0,05 - 0,1% с одновременным снижением на 5 - 10% водоцементного
отношения (до требуемого уровня подвижности) бетонной смеси. Применение этого
способа должно быть экономически обосновано.
5.6. В тех
случаях, когда суперпластификаторы предназначаются для повышения прочности или
плотности бетонов, корректировка состава заключается в выборе оптимальной
дозировки СП и снижении водосодержания бетонной смеси:
а) оптимальная
дозировка СП выбирается в соответствии с п. 5.5 настоящих Рекомендаций с учетом
получения максимального разжижения бетонной смеси и максимальной прочности бетона;
б) после выбора
оптимальной дозировки СП проводится корректировка водоцементного отношения (до
получения исходного уровня подвижности бетонной смеси, принятого для бетонной
смеси без добавки).
5.7. При
использовании эффекта повышения прочности бетона от применения
суперпластификаторов для максимального сокращения режима термообработки,
ускорения оборачиваемости форм и увеличения выпуска продукции корректировка
состава бетона производится в соответствии с п. 5.6, а выбор режима
термообработки бетона - в соответствии с пп. 6.31, 6.32 и 6.34 настоящих
Рекомендаций.
5.8. При
использовании эффекта повышения прочности бетона от применения
суперпластификаторов для снижения температуры изотермического прогрева выбор
режима термообработки производится в соответствии с пп. 6.33 и 6.34 настоящих
Рекомендаций.
5.9. При
использовании эффекта повышения прочности бетона от применения
суперпластификаторов для максимального сокращения расхода цемента 1-й этап корректировки
состава производится в соответствии с п. 5.6 настоящих Рекомендаций. Определив
прирост прочности бетона после термообработки, сокращают расход цемента (из
расчета 0,8 - 1 кг на каждый 0,1 МПа прироста прочности) и воды, оставляя
постоянным водоцементное отношение, до получения смеси заданной подвижности или
жесткости и бетона требуемой прочности.
Примеры подбора
состава тяжелого бетона с СП даны в Прил. 4.
5.10. Корректировку
состава бетона в направлении использования водоредуцирующего действия СП
следует производить с учетом фактического увеличения расхода всех твердых
составляющих бетонной смеси.
5.11. При
изготовлении высокопрочных бетонов рекомендуется применять максимально
возможные дозировки СП с целью наибольшего снижения водоцементного отношения
бетонной смеси. Дозировка добавки должна быть подобрана экспериментальным путем
и экономически обоснована.
5.12. Опытные замесы бетона с добавкой СП должны приготовляться на тех же
заполнителях и вяжущем, которые приняты при расчете составов бетона без
добавок.
5.13. Для выявления
эффективности суперпластификаторов параллельно с образцами из бетонной смеси с
СП следует изготавливать образцы из контрольного состава без добавки или с
добавкой, применяемой ранее на производстве (эталон). Эталонная бетонная смесь
должна иметь подвижность, равную подвижности смеси, применяемой на
производстве. Для получения высокоподвижных и литых бетонных смесей для
транспортного строительства подвижность эталонной бетонной смеси должна
составлять 2 - 3 см. Размеры и форма изготавливаемых образцов, условия
уплотнения бетонной смеси должны соответствовать нормативной документации на
данный вид изделий.
5.14. Пропаривание
эталонных бетонных изделий и образцов с добавкой СП следует проводить
совместно, по режиму, принятому на производстве. Время предварительной выдержки
перед термообработкой эталонного состава и состава с СП не должно отличаться
более чем на 15 - 20% (например, при предварительной выдержке, равной 3 ч, - не
более 30 - 40 мин).
5.15. Все
подобранные в лаборатории составы бетонов и режимы тепловой обработки изделий и
конструкций следует откорректировать в производственных условиях.
Мелкозернистый
бетон
5.16.
Суперпластификатор С-3 рекомендуется вводить в мелкозернистые бетонные смеси в
количестве 0,5 - 1% массы цемента.
5.17. При
изготовлении изделий и конструкций из мелкозернистых бетонов с СП С-3 в
вертикальных формах рекомендуется использовать бетонные смеси с подвижностью от
4 до 16 см, в горизонтальных формах - с подвижностью от 2 до 4 см.
5.18. При проектировании
состава следует учитывать, что при введении СП С-3 в мелкозернистые бетонные
смеси величина водопотребности песка снижается:
пропорционально
увеличению дозировки СП;
с увеличением
крупности песка (в смеси состава Ц:П = 1:3 при
увеличении модуля крупности песка от 1,56 до 3,13 его водопотребность снижается
примерно в 2 раза);
с увеличением
количества цемента в составе бетонной смеси (при увеличении количества цемента
на 20 - 33% по массе водопотребность песка снижается в 1,1 - 2,4 раза в
зависимости от его крупности).
Напрягающий
бетон
5.19. При
применении СП С-3 в напрягающем бетоне для разжижения бетонной смеси с исходной
осадкой конуса 1 - 2 см рекомендуются следующие дозировки СП, %:
0,15 - 0,3
- для получения ОК = 4 - 12 см
0,3 - 0,4
- " "
ОК = 13 - 17 см
0,4 - 0,8
- " "
ОК >= 18 см
5.20. Для повышения
прочности и самонапряжения бетонов рекомендуемая дозировка СП составляет 0,2 -
0,7%. Водоцементное отношение при этом должно быть соответственно снижено на 20
- 30% по сравнению с бетонной смесью аналогичной подвижности без добавки.
Легкий
бетон
5.21.
Расчет и назначение составов легких бетонов с СП производят согласно
"Руководству по подбору составов конструктивных легких бетонов на пористых
заполнителях" (М., Стройиздат, 1975) со следующими дополнениями и
изменениями.
Ориентировочные
начальные расходы воды (по табл. 7 "Руководства") для смеси с СП
уменьшают на 20%. Для высокоподвижной пластифицированной смеси с осадкой конуса
15 - 17 см начальный расход воды принимают таким же, как для смесей с ОК = 3 - 7 см без СП.
5.22.
Расходы цемента для опытных замесов с СП принимают по табл. 5
"Руководства" с использованием следующих ориентировочных
коэффициентов, учитывающих подвижность пластифицированных смесей:
1 - 4 см
................. 0,9
5 -
9 " ................. 1,0
10 - 14
" ................. 1,1
15 - 17
" ................. 1,15
5.23. Выбор
дозировки добавки СП, обеспечивающей требуемый эффект пластификации, производят
на основе последовательно выполненных опытных замесов, из легкобетонной смеси
без добавки и с добавкой в количестве 0,3 - 0,6% массы цемента при его расходе
300 - 450 кг/м3 и 0,4 - 0,8% массы цемента при расходе 450 - 600 кг/м3. Состав
бетонов рассчитывают согласно "Руководству" с учетом указаний пп.
5.21 и 5.22 настоящих Рекомендаций.
5.24.
Опытным замесом уточняют расход воды в составе без добавки, обеспечивающий
требуемую подвижность смеси. По полученной разности между фактическим и
расчетным расходом воды уточняют водосодержание в составе для опытных замесов с
добавкой СП. Последовательно выполняют замесы с различными дозировками добавки
до тех пор, пока в результате испытания не будет достигнута требуемая
подвижность бетонной смеси. Из этого замеса изготовляют контрольные образцы для
определения прочности бетона.
5.25.
Выполняют два дополнительных замеса с найденной дозировкой добавки и с расходом
цемента, отличающимися на +20% от принятого, при соответственно уменьшенном
расходе песка, добиваясь в каждом из них путем корректировки расхода воды
требуемой подвижности пластифицированной легкобетонной смеси.
5.26. Из
этих замесов также изготавливают контрольные образцы, которые после тепловой
обработки по заданному режиму испытывают на сжатие. По полученной зависимости
устанавливают расход цемента для получения
требуемой прочности легкого бетона.
5.27. Приготовление
всех опытных замесов производят в лабораторном смесителе с обязательным
определением плотности свежеуложенной смеси и уточнением фактического расхода
материалов на 1 м3 бетона.
5.28. При
применении СП для улучшения технологии и качества легкого бетона на действующем
производстве за основу принимают производственный состав и осуществляют его
корректировку в зависимости от целей введения добавки с учетом следующих
положений:
а) при
изготовлении конструкций и изделий из конструкционных легких бетонов в формах
по поточно-агрегатной или конвейерной технологии подвижность пластифицированной
легкобетонной смеси не должна, как правило, превышать 9 см, а при стендовой
технологии - 15 см. При изготовлении изделий вертикально-кассетным способом, а
также объемных элементов подвижность смеси может быть повышена до 15 - 17 см и
более. При корректировке составов
высокоподвижных смесей в первую очередь должны приниматься меры, исключающие
расслоение легкобетонной смеси при формовании: для крупного заполнителя следует
отдавать предпочтение фракции 5 - 10 мм с плотностью зерна, близкой к плотности
бетона; наличие пористого песка является обязательным;
б) при ограниченной
степени пластификации расходы воды и цемента в составе бетона с добавкой СП
уменьшают при переходе от ОК = 1 - 4 см (без добавки)
к ОК = 5 - 9 см - на 10%, а к ОК = 10 - 15 см - на 5%. Необходимые дозировки СП
устанавливают согласно п. 5.23 настоящих Рекомендаций при уменьшенных расходах
воды и цемента. Окончательный расход цемента определяют дополнительными
замесами согласно пп. 5.25 и 5.26 настоящих Рекомендаций;
в) при введении СП
в целях экономии цемента пересчитывают составы бетона с уменьшенными на 20%
расходами воды и цемента, определяют требуемую дозировку СП по пп. 5.23 и 5.24
и уточняют расход цемента согласно пп. 5.25 и 5.26 настоящих Рекомендаций;
г) при введении СП
в целях повышения прочности легкого конструкционного бетона пересчитывают
составы бетона с уменьшенным на 20% расходом воды и далее определяют
необходимую дозировку добавки и уточняют расход цемента, обеспечивающий
требуемую повышенную прочность в соответствии с методикой, изложенной выше.
5.29. При
применении СП для изготовления изделий из конструкционно-теплоизоляционных
легких бетонов в горизонтальных формах подвижность легкобетонной смеси не
должна превышать 1 - 4 см. Уменьшение водосодержания, вызывающее повышение
плотности бетона, должно компенсироваться увеличением объема вовлеченного
воздуха с соответствующим повышением расхода воздухововлекающей или
порообразующей добавки. Расход остальных компонентов, плотность и прочность
бетона при этом не изменяются.
Примеры подбора
состава легких бетонов на пористых заполнителях представлены в Прил. 5.
Жаростойкий
бетон
5.30. При подборе
состава жаростойкого бетона с добавкой суперпластификатора С-3 за основу
принимается состав бетона, подобранный на конкретных материалах без добавки в
соответствии с "Руководством по возведению тепловых агрегатов из
жаростойкого бетона" (М., Стройиздат, 1983).
5.31.
Суперпластификатор С-3 рекомендуется вводить в жаростойкие бетоны в количестве
0,5 - 1,5% массы цемента. При этом срок начала схватывания бетона должен
составлять не менее 30 мин.
5.32. При
изготовлении изделий и конструкций из жаростойкого бетона с целью исключения
расслаиваемости бетонной смеси рекомендуется следующее:
ограничить ее
подвижность 10 см;
применять во всех
конструкциях (кроме фундаментов) крупный шамотный заполнитель с размером зерен
до 10 мм.
5.33. При подборе
состава жаростойкого бетона с суперпластификатором С-3 следует контролировать
его характеристики, перечень которых приведен в табл. 8.
Таблица 8
Перечень
характеристик, исследуемых при использовании
суперпластификатора
С-3 в жаростойком бетоне
────────────────────────────────────────┬──────────────────────────────────
Исследуемые характеристики │ Методика испытаний
────────────────────────────────────────┼──────────────────────────────────
Цементное тесто │
│
1.
Нормальная густота
│ГОСТ 310.3-76
2.
Сроки схватывания
│ГОСТ 310.3-76
3.
Равномерность изменения объема
│ГОСТ 310.3-76
4.
Прочность на сжатие
│ГОСТ 310.4-81
│
Бетонная смесь │
│
5.
Подвижность (жесткость)
│ГОСТ 10181.1-81
6.
Водоотделение
│ГОСТ 10181.4-81
│
Бетон │
│
7.
Прочность на сжатие после:
│ГОСТ 10180-78
7 сут нормального твердения, │
сушки при 110 °C, │
нагрева до температуры 800 °C │
8.
Температурная усадка
│Руководство по возведению
│тепловых агрегатов
│из жаростойкого бетона
9.
Термическая стойкость
│То же
10.
Температуры деформации под
│ГОСТ 23283-78
нагрузкой: │
4% сжатия │
40% сжатия или разрушения │
5.34.
Ориентировочные расходы материалов на 1 м3 бетона, которые могут быть
использованы при заказе исходных материалов и при подборе состава жаростойкого
бетона, приведены в табл. 9.
Таблица 9
Ориентировочные
составы жаростойких
бетонов с добавкой
суперпластификатора С-3
────────────────────┬────────────────────────────────┬─────────────────────
Вид вяжущего │ Расход материалов, │ Расход
│ кг на 1 м3
бетона │ суперпластификатора
├─────────┬──────────────────────┤С-3,
% массы цемента
│вяжущего
│заполнителя шамотного │
│
├───────────┬──────────┤
│ │ мелкого
│ крупного │
────────────────────┼─────────┼───────────┼──────────┼─────────────────────
Шлакопортландцемент
│ 450 │
700 │ 650
│ 0,5 - 1,2
Глиноземистый
цемент│ 400 │
750 │ 650
│ 0,8 - 1,5
Ячеистый
бетон
5.35. Подбор
состава ячеистого бетона с комплексной добавкой заключается в определении ее
оптимальной дозировки и корректировке состава бетона без добавок, подобранного
по методике, приведенной в "Инструкции по изготовлению изделий из
ячеистого бетона" СН 277-80 (М., Стройиздат, 1981). Рекомендуется
следующий исходный расход добавок: С-3 - 0,5% (массы цемента), щелочной
компонент - 0,1 - 0,4%. Для нахождения оптимальной дозировки расход добавок
следует варьировать в следующих пределах (по сравнению с исходным уровнем): С-3
+/- 0,3%, щелочной компонент +/- 0,2%.
5.36. При подборе
состава с добавкой соотношение между кремнеземистым компонентом и вяжущим
должно быть таким же, как и у бетона без добавок.
5.37. При расчете
количества газообразователя коэффициент его использования рекомендуется
уменьшить на 20 - 30% по сравнению с коэффициентами, рекомендуемыми СН 277-80.
5.38. Корректировка
состава ячеистого бетона из условия получения ячеистого бетона заданной
прочности при его наименьшей плотности производится следующим образом:
а) определяют
оптимальные дозировки добавок из условия получения максимально возможного
снижения водотвердого отношения, которое должно быть уменьшено на 20 - 30% по
сравнению с эталоном. При этом производится подбор состава ячеистого бетона
заданной плотности. Предварительную выдержку изделий, термообработку проводят
по тому же режиму, что и эталон;
б) по
результатам испытания контрольных образцов определяют оптимальное количество
добавок, обеспечивающее максимальный прирост прочности;
в) по формуле
, (1)
где
- наибольшая (фактическая) прочность бетона,
полученная по п. 5.38, б;
- расчетная плотность бетона, кг/м3;
- нормируемая прочность бетона, МПа;
- нормируемая плотность бетона, кг/м3,
определяют
плотность, при которой ячеистый бетон с добавкой приобретает нормируемую
прочность;
г) подбирают состав
ячеистого бетона расчетной плотности и изготавливают образцы с оптимальным (по
п. 5.38, б) количеством добавок, а также уменьшенным на 25% от массы каждого из
компонентов добавки и определяют показатели плотности и прочности этих бетонов.
6.
ПРОИЗВОДСТВО СБОРНЫХ ЖЕЛЕЗОБЕТОННЫХ КОНСТРУКЦИЙ
И ИЗДЕЛИЙ С
ПРИМЕНЕНИЕМ СУПЕРПЛАСТИФИКАТОРОВ
Хранение, подача и
дозирование суперпластификаторов
6.1. Отделение для
хранения СП целесообразно располагать рядом с бетоносмесительным узлом.
6.2. Суперпластификаторы
заводской концентрации следует хранить в емкостях, находящихся в отапливаемых
помещениях и оборудованных обогревательными приборами. Перед забором добавки
при выпадении из нее осадка последний должен быть растворен, а все содержимое
емкости тщательно перемешано.
6.3.
Суперпластификаторы следует вводить в бетонные смеси в виде растворов заводской
либо рабочей концентрации. Способ введения зависит от точности дозирующего
оборудования. Для применения СП по первому способу следует использовать дозаторы
Киевского объединения "Веда" типа 6145-АД-30 ГБЖ (предел взвешивания
от 0,5 до 30 кг) либо ИДПС-15 (предел взвешивания от 1 до 15 кг); по второму
способу (при 5 - 10%-ной концентрации рабочего раствора) - дозаторы воды
(дозирование растворов СП рекомендуется проводить по массе; разрешается
объемное дозирование при условии соблюдения его точности).
6.4. Растворы
рабочей концентрации приготавливаются в специальных баках, вместимость которых
должна обеспечить непрерывную работу бетоносмесительного узла не менее чем в
течение одной смены. Целесообразно наличие двух баков.
6.5. В расходных
емкостях рекомендуется установить указатели верхнего и нижнего уровня.
6.6. Трубопроводы,
соединяющие все емкости, насосы и дозатор, должны находиться при температуре не
ниже +5 °C. Трубопроводы должны иметь обратный уклон не менее 5 град.
6.7. Разрешается
кратковременное нахождение растворов добавок в системе трубопроводов. В конце
каждой смены необходима их промывка водой, исключающая сброс жидкости в
канализацию.
6.8. Конструктивные
элементы линии приема, хранения, приготовления, дозирования и подачи растворов
СП не следует изготавливать из низколегированных сталей.
Приготовление,
транспортирование
и формование бетонной
смеси
6.9. Для
приготовления бетонной смеси с СП допускается применение всех видов
бетоносмесителей при условии обеспечения равномерности перемешивания (в
соответствии с ГОСТ 7473-85).
6.10.
Транспортирование высокоподвижных и литых бетонных смесей (ОК
более 15 см) к постам формования должно осуществляться устройствами,
конструкция которых не допускает утечки цементного молока и исключает
расслаивание смеси. Количество перегрузок должно быть минимальным.
6.11. Ленточным
транспортером разрешается перемещать бетонные смеси, осадка конуса которых не
превышает 15 см. При этом угол подъема не должен превышать 18 град, угол спуска
12 град - для бетонной смеси с ОК до 4 см и
соответственно 12 град и 6 град - для бетонной смеси с ОК 4 - 15 см.
При перемещении
пластифицированных смесей по ленточным транспортерам должны соблюдаться
следующие условия:
поддерживающие и
направляющие ролики должны обеспечивать положение ленты в виде желоба;
верхняя лента
должна двигаться в направлении натяжной станции по поддерживающим роликам,
расположенным друг от друга на расстоянии не более 0,8 м;
ширина ленты не
должна быть менее 0,8 м;
перед подачей на
ленту первой порции бетона ленту следует смочить водой, а после ее остановки -
очистить от бетона;
для очистки ленты
от бетона после ведущего барабана следует установить плотно прилегающий
скребок;
сбрасывание бетона
с ленты должно осуществляться через натяжной барабан с установкой после него на
расстоянии 150 - 200 мм очищающего шпателя;
скорость движения
ленты транспортера не должна превышать 0,8 м/с.
6.12. Для
перемещения подвижных смесей, как правило, применяют рельсовые вагонетки,
вибробункеры и бадьи, транспортируемые краном или тельфером.
6.13. В бункерах
для подвижных смесей на выходе применяют двухчелюстные затворы, роторные
питатели, открывающие доступ бетону только при вращении барабана. Скорость
барабана не должна превышать 6 оборотов в минуту, а диаметр барабана - 0,9 м.
6.14. Для укладки
литых смесей применяют самоходные бетоноукладчики с выдачей смеси через гибкий
рукав (
159
мм).
6.15. Для изделий
из литых и высокоподвижных смесей желательно применение строганых плотных форм.
Места сопряжения бортов, пропусков арматуры следует проклеивать лентой или
закрывать специальными прокладками. Рекомендуется также применение форм с
нераскрывающимися или полугибкими бортами.
6.16. Применение
суперпластификаторов возможно при изготовлении изделий и конструкций по всем
существующим технологиям в соответствии со СНиП 3.09.01-85 "Производство
сборных железобетонных конструкций и изделий".
6.17. Следует
учитывать, что при производстве изделий с большими горизонтальными
поверхностями <*> подвижность бетонной смеси должна быть ограничена 14 -
16 см в связи с возможностью нарушения геометрических размеров изделия в
результате возникновения волнообразной поверхности при передвижении или
переносе формы.
--------------------------------
<*> По
конвейерной и поточно-агрегатной технологиям.
6.18. Применение
литых бетонных смесей (ОК >= 20 см) допускается
только в стендовой технологии.
6.19. Для
формования тонкостенных вертикально расположенных изделий и конструкций
рекомендуется применять пластифицированные смеси с осадкой конуса не более 12 -
14 см.
6.20. В качестве
основного режима виброуплотнения рекомендуется применять гармонический режим,
где основными параметрами являются амплитуда и частота колебаний вибрирующего
оборудования. Эффективность вибрационного воздействия при гармонических колебаниях
оценивается величиной их ускорения, которая выражается в долях от ускорения
свободного падения тела g и определяется по формуле
, (2)
где
;
A - амплитуда
колебаний, мм;
f - частота
колебаний, 1/с;
g - ускорение
свободного падения тела, равное 9,81 м/с2.
6.21. Для
уплотнения подвижных и литых смесей с добавками СП рекомендуется применять
низкочастотные режимы вибрирования при следующих величинах ускорений
вибраторов: 1,5 - 3,0g при частоте колебаний 85 Гц; 1 - 2g - при частоте 10 -
15 Гц. Техническая характеристика виброплощадок дана в табл. 10.
Тепловая обработка
бетона
6.26.
Тепловая обработка бетонов, изготовленных с суперпластификаторами, должна
производиться в соответствии со СНиП 3.09.01-85 и "Руководством по
тепловой обработке бетонных и железобетонных изделий" (М., Стройиздат,
1974) с учетом указаний настоящих Рекомендаций.
6.27. Тепловая
обработка бетонов с СП может осуществляться в тепловых агрегатах периодического
или непрерывного действия любой конструкции и с применением различных
теплоносителей, обеспечивающих получение заданных температурно-влажностных
условий твердения бетона. Рекомендуется осуществлять комплекс мероприятий,
устраняющих внешний массообмен.
6.28. С целью
предотвращения испарения влаги из бетона изделия, твердеющие в термоформах и
имеющие значительные открытые поверхности, следует изолировать от окружающей
среды влагонепроницаемыми материалами. Особое внимание на это требование должно
быть обращено при изготовлении бетонов из высокоподвижных и литых бетонных
смесей.
6.29. При
изготовлении бетонов из высокоподвижных и литых бетонных смесей с СП (при
сохранении водоцементного отношения, равного эталону), режим термообработки
следует, как правило, назначать таким же, как и для бетона без добавки.
6.30. В
отдельных случаях, когда максимальное использование разжижающего эффекта СП
может привести к некоторому снижению прочности бетона после пропаривания,
рекомендуется использование одного из предлагаемых методов изменения режима термообработки
(по сравнению с бетоном без добавки):
увеличение
предварительной выдержки на 1 - 2 ч с последующим сокращением на такой же
период времени изотермического прогрева;
увеличение времени
подъема температуры на 1 - 2 ч (уменьшение скорости подъема температуры на 5 -
7 °C/ч) с последующим сокращением на такой же период времени изотермического
прогрева;
осуществление
предварительной выдержки при повышенной температуре (30 - 40 °C);
назначение
ступенчатого режима подъема температуры (например, в первый час - 8 - 12 °C/ч,
второй - 12 - 14 °C/ч, третий - 15 - 17 °C/ч, четвертый - 18 - 24 °C/ч);
снижение
температуры изотермического прогрева на 20 - 25 °C при одновременном увеличении
длительности пропаривания в пределах допускаемой оборачиваемости форм и камер;
использование
специальных способов тепловой обработки: пропаривание в среде с избыточным
давлением паровоздушной смеси, пропаривание под механическим пригрузом,
предварительный паро- или электроразогрев бетонной
смеси до температуры 30 - 40 °C и др.
6.31.
Прирост прочности бетонов с СП (за счет уменьшения В/Ц
смеси) может быть использован для сокращения времени термообработки. Этот
технологический прием наиболее целесообразно применять в тех случаях, когда
перед предприятием стоит задача увеличения оборачиваемости форм.
6.32.
Сокращение режима термообработки возможно на всех ее этапах: предварительной
выдержки, подъема, изотермического прогрева и остывания. Сокращенный режим
рекомендуется подбирать экспериментально в зависимости от конкретных условий
производства.
6.33. При
уменьшении В/Ц за счет действия СП возможно также
снижение температуры изотермического прогрева (на 20 - 25 °C).
6.34. При
изменении режима термообработки следует учитывать, что расход пара, идущего на
разогрев бетона, составляет приблизительно 80%, а на изотермический прогрев -
20% от общего расхода пара.
Снижение
температуры изотермического прогрева на 20 °C (от 80 до 60 °C) экономит 30%
пара, идущего на разогрев бетона.
6.35. Частичное
сокращение времени тепловой обработки рекомендуется осуществлять параллельно с
достижением других эффектов от применения суперпластификаторов (сокращением
времени формования изделий, экономией электроэнергии, сокращением расхода
цемента и т.д.).
6.36. При
поступлении новых партий цементов и добавок или при каких-либо изменениях в
технологии производства изделий и конструкций режимы тепловой обработки бетона
с СП должны уточняться лабораторией экспериментально с учетом рекомендаций
настоящего раздела.
7.
ОСОБЕННОСТИ ИЗГОТОВЛЕНИЯ РАЗЛИЧНЫХ ВИДОВ
СБОРНЫХ ИЗДЕЛИЙ И
КОНСТРУКЦИЙ
Изделия и
конструкции из мелкозернистого бетона
7.1. Изготовление
конструкций из мелкозернистого (песчаного) бетона осуществляют в соответствии
со СНиП 3.09.01-85 "Производство сборных железобетонных конструкций и
изделий".
7.2. Мелкозернистые
бетоны из подвижных смесей с СП С-3 должны характеризоваться высокой
однородностью и связностью. Разжижение бетонных смесей без изменения
водоцементного отношения (например, от 4 см для эталона до 15 - 16 см) не
увеличивает их водоотделения. Снижение водоцементного отношения до уровня
исходной подвижности снижает водоотделение в 2,5 - 3,5 раза по сравнению с
эталоном.
7.3. Изготовление
мелкозернистых бетонных смесей рекомендуется производить в бетоносмесителях
принудительного действия. Допускается использование бетоносмесителей
гравитационного типа. Продолжительность перемешивания - не менее 90 с.
Ориентировочное
соотношение величин подвижности мелкозернистой смеси, определяемых различными
способами, представлено в табл. 11.
Таблица 11
Подвижность смесей,
определенная различными способами
───────────────────────┬─────────────────────────┬─────────────────────────
Осадка стандартного │
Глубина погружения
│Расплыв на встряхивающем
конуса, см │
конуса СтройЦНИЛ, см
│ столике, мм
(по ГОСТ 10181.1-81) │
(по ГОСТ 5801-78) │ (по ГОСТ 310.4-81)
───────────────────────┼─────────────────────────┼─────────────────────────
1 - 3 │ 2 - 3 <1> │
110 - 140
3 - 6 │ 3 - 5 │ 140 - 170
5 - 8 │ 4 - 6
│ 160 - 180
8 - 14 │ 6 - 8 │ 170 - 200
12 - 15 │ 7 - 9 │ 190 - 220
15 - 22 │ 8 - 11 │ 210 - 240
20 - 25
│ 10 - 14 │ 230 - 270
7.4. Термообработку
мелкозернистых бетонов, изготовленных из пластифицированных бетонных смесей,
следует производить по более мягким режимам, с увеличением предварительной
выдержки и уменьшением скорости подъема температуры. Назначение конкретного
режима термообработки осуществляется с учетом консистенции бетонной смеси и ее
повышенного по сравнению с эталоном (на 2 - 4%) воздухосодержания.
Изделия и
конструкции из легкого бетона
7.5. При применении
СП следует учитывать следующие особенности легких бетонов:
а) повышенную расслаиваемость высокоподвижных и литых
легкобетонных смесей вследствие различия в плотности отдельных составляющих;
б) повышение
плотности легкого бетона в сухом состоянии при уменьшении водосодержания
пластифицированных бетонных смесей;
в) влияние
прочности крупного и мелкого пористого заполнителя на эффект повышения
прочности легкого бетона и снижения расхода цемента при уменьшении
водосодержания пластифицированной бетонной смеси;
г) водопоглощающую
способность крупных и мелких пористых заполнителей, уменьшающих количество
активно действующего СП, введенного вместе с водой затворения;
д) наличие
пылевидных фракций в пористых песках и золах ТЭС, применяемых для приготовления
легких бетонов и уменьшающих эффективность пластификации смешанного вяжущего в
составе легкобетонной смеси;
е) большую
склонность к воздухововлечению при перемешивании легкобетонных смесей с
некоторыми СП ввиду активного влияния пористых заполнителей на этот процесс;
ж) повышенную
потерю подвижности пластифицированных легкобетонных смесей в силу
дополнительного отсоса воды пористыми заполнителями в процессе выдерживания и
транспортирования смесей.
7.6. Дозировки СП
для конструкционных легких бетонов, как правило, не должны превышать 0,6% массы
цемента в бетонах, приготовленных с мелким плотным заполнителем, и 0,7% массы
цемента в бетонах с мелким пористым заполнителем. Необходимая дозировка СП
устанавливается при подборе состава легкого бетона в зависимости от требуемой подвижности
смеси и целей применения СП.
7.7. При применении
СП для изготовления изделий из конструкционно-теплоизоляционных легких бетонов
в горизонтальных формах подвижность легкобетонной смеси не должна превышать 1 -
4 см. Уменьшение водосодержания, вызывающее повышение плотности бетона, должно
компенсироваться увеличением объема вовлеченного воздуха с соответствующим
повышением расхода воздухововлекающей или порообразующей добавки. Расход
остальных компонентов, плотность и прочность бетона при этом не изменяются.
7.8. При
приготовлении легкобетонных смесей растворы СП и других добавок должны
вводиться отдельно от остальной воды, после подачи всех материалов в смеситель.
Общая длительность перемешивания должна быть, как правило, на
30 с больше по сравнению с принятой для смеси без СП, но не должна превышать 5
мин.
7.9.
Транспортирование пластифицированной легкобетонной смеси должно производиться
средствами, исключающими ее расслоение и потерю составляющих. Общее время от
окончания перемешивания до укладки в форму и уплотнения не должно превышать 40
мин.
7.10.
Виброформование изделий из пластифицированных легкобетонных смесей
рекомендуется производить при пониженной частоте.
7.11. Тепловая
обработка изделий должна производиться с предварительной выдержкой в течение не
менее 2 - 3 ч до получения требуемой начальной прочности бетона согласно СНиП
3.09.01-85 "Производство сборных железобетонных конструкций и
изделий". При применении ускоренных режимов термообработки рекомендуется
сочетать СП с добавками-ускорителями (
, ННХК,
ННК), вводимыми в легкобетонную смесь в количестве 1 - 2% массы цемента.
7.12. При учете
всех особенностей технологии легких бетонов применение СП обеспечивает:
повышение
подвижности бетонных смесей для конструкционных легких бетонов от 1 - 4 до 17
см и более;
снижение расхода
цемента в конструкционных бетонах при той же подвижности бетонной смеси до 25%;
повышение прочности
легкого конструкционного бетона на одну марку;
повышение модуля
упругости конструкционных легких бетонов на 20%, уменьшение усадки на 15%;
уменьшение
отпускной влажности изделий из конструкционно-теплоизоляционных легких бетонов
на 2 - 3%.
Изделия и
конструкции из жаростойкого бетона
7.13. Приготовление жаростойкого бетона следует осуществлять по
утвержденным в установленном порядке применительно к условиям конкретного
производства технологическим картам, составленным на основании СНиП 3.09.01-85
"Производство сборных железобетонных конструкций и изделий" и
"Руководства по возведению тепловых агрегатов из жаростойкого бетона"
(М., Стройиздат, 1983) с учетом указаний настоящих Рекомендаций.
7.14. Бетонную
смесь на глиноземистом цементе рекомендуется приготавливать при температуре окружающего
воздуха не выше +25 °C.
7.15. Изготовление
крупноразмерных изделий и конструкций из жаростойкого бетона на глиноземистом
цементе без дополнительного охлаждения не допускается в связи с разогревом
бетонной смеси.
7.16.
Термообработку конструкций из жаростойкого бетона следует производить в
соответствии с указаниями пп. 6.26 - 6.36 настоящих Рекомендаций.
7.17. Твердение
изделий и конструкций в естественных условиях должно проходить при
относительной влажности воздуха не менее 90% и при температуре окружающего
воздуха 7 - 25 °C - для бетона на глиноземистом цементе и более 15 °C - для
бетона на шлакопортландцементе.
7.18. Бетон
на глиноземистом цементе следует увлажнять через 3 - 4 ч после укладки в
течение 48 ч. Необходимо избегать попадания на бетон сильных струй воды.
Изделия и
конструкции из ячеистого бетона
7.19. Изделия из конструкционно-теплоизоляционных и теплоизоляционных
ячеистых бетонов с добавкой СП С-3 следует изготавливать по литьевой и
резательной технологиям в соответствии с СН 277-80 и указаниями настоящих
Рекомендаций.
7.20. При
применении комплексной добавки для ячеистого бетона следует использовать
отдельные установки для хранения, подачи, приготовления и дозирования водных
растворов каждого из компонентов.
7.21. Раствор
щелочного компонента готовят в специальных емкостях путем растворения твердого
продукта. Для повышения скорости растворения твердых продуктов рекомендуется
подогревать воду до 40 - 70 °C и перемешивать раствор.
7.22. Растворы
химических добавок следует хранить при положительной температуре (в условиях
цеха), твердые продукты добавок - в соответствии с требованиями стандартов и
технических условий на добавки.
7.23. Добавки
растворов суперпластификаторов и щелочного компонента рекомендуется вводить в
газобетономешалку вместе или одновременно с водой затворения. Добавки следует
вводить в бетон в следующей последовательности: сначала щелочной компонент,
затем СП С-3. Возможно применение комплексной добавки в виде единого продукта
(при его наличии).
7.24. Формование
изделий следует производить в соответствии с технологическими схемами принятого
способа производства.
7.25. Заливку форм
газобетонной смесью следует выполнять за один прием в следующие сроки: через 12
- 15 мин после начала перемешивания - при литьевой технологии и через 25 - 30
мин - при резательной технологии.
7.26. Учитывая
ускоренный темп набора пластической прочности ячеисто-бетонного сырца,
изготовленного с применением добавки, контроль за
набором пластической прочности и временем срезки "горбушки" следует
начинать не позднее чем через 1 ч 30 мин после формования.
7.27. Для твердения
отформованных изделий из ячеистого бетона, приготовленного с применением
комплексных добавок на основе суперпластификатора, следует применять
автоклавную обработку и пропаривание.
7.28. При
применении комплексных добавок на основе СП С-3 время предварительной выдержки
изделий перед термообработкой может быть сокращено на 2,5 - 3 ч - для литьевой
технологии и на 1,5 - 2 ч - для резательной технологии.
7.29. В случае
необходимости режим термообработки может быть сокращен (за счет применения СП)
на 2 - 2,5 ч. Сокращение предварительной выдержки и режима термообработки может
быть проведено при условии получения ячеистого бетона с физико-техническими
свойствами, отвечающими требованиям действующих ГОСТ на изделия.
Пример эффективного
использования комплексной добавки в технологии ячеистого бетона дан в Прил. 3.
Изделия и
конструкции из напрягающего бетона
7.30. Бетоны на НЦ
должны изготавливаться в соответствии с требованиями "Рекомендаций по
применению бетонов на НЦ при возведении монолитных и сборно-монолитных
конструкций" (М., НИИЖБ, 1984), "Рекомендаций по изготовлению сборных
железобетонных изделий из бетона на НЦ" (М., НИИЖБ, 1984), а также с
учетом указаний настоящих Рекомендаций.
7.31. Приготовление
бетона на НЦ производится на бетоносмесительных установках гравитационного или
принудительного действия. Использование бетоносмесительных установок
непрерывного действия (шнековых) с продолжительностью перемешивания полминуты и
менее допускается только после опытной проверки однородности и стабильности
получаемой смеси.
7.32. При
использовании партий НЦ, обладающих ускоренным схватыванием, рекомендуется
использовать эффект разжижения смеси с помощью СП С-3 или осуществлять
приготовление бетонной смеси с замедлением схватывания методом предварительной
частичной гидратации в следующем порядке:
дозирование,
загрузка в смеситель песка, доувлажнение его до 4 - 6%, перемешивание 1 мин;
дозирование,
загрузка НЦ, перемешивание 1 - 2 мин;
дозирование,
загрузка крупного заполнителя (производится в любой момент в процессе
приготовления смеси, исходя из типа смесителя, удобства загрузки и т.д.);
затворение смеси,
введение СП С-3 с водой затворения, перемешивание 1 - 2 мин.
Конструкции для
транспортного строительства
7.33. Применение СП
рекомендуется во всех случаях производства конструкций из бетона марки M600 и
выше, при изготовлении конструкций из цемента недостаточной активности, а также
в соответствии с данными Прил. 3.
7.34. При
изготовлении бетонов для транспортного строительства с СП особое внимание
следует обращать на недопустимость расслоения бетонной смеси из-за
перевибрации, особенно при применении высокоподвижных и литых смесей.
7.35. Интенсивность
и длительность вибрационного воздействия на бетонную смесь должны
соответствовать ее подвижности с учетом конфигурации изделий.
7.36. При
формовании высоких элементов (например, мостовых балок) следует строго
соблюдать технологию бетонирования и послойной укладки бетонной смеси и
уплотнения.
7.37. Сокращение
режима термообработки бетонов с СП (в случае снижения В/Ц)
может достигать 8 - 10 ч (для длинных режимов, например, при изготовлении
мостовых балок). При более коротких режимах термообработки сокращение их
длительности достигает 4 - 6 ч.
При сохранении
длительности тепловой обработки рекомендуется снижать температуру
изотермического прогрева на величину до 20 °C.
7.38. Принятый
режим термообработки должен обеспечивать получение бетона с заданными
свойствами (прочностью, морозостойкостью, водонепроницаемостью). При этом
исключается возможность появления в изделиях и конструкциях температурных и
усадочных трещин.
Преднапряженные
конструкции
7.39. Сборные
преднапряженные конструкции следует изготавливать в соответствии с
"Руководством по изготовлению предварительно напряженных железобетонных
конструкций" (М., Стройиздат, 1978) с учетом указаний, изложенных ниже.
7.40.
Суперпластификаторы рекомендуется применять в преднапряженных конструкциях,
используя все те технологические преимущества, которые они могут давать (см.
табл. 1), а также - с целью улучшения качества преднапряженных конструкций,
связанного с наличием напрягаемой арматуры (стержневой, проволочной, прядевой)
и с изменением усилий в ней на стадии тепловой обработки и охлаждения бетона.
7.41. Во избежание технологических дефектов, а также для снижения величин
потерь преднапряжения в арматуре от температурного перепада рекомендуется
величину начальной прочности бетона выдерживать в пределах 0,2 - 0,6 МПа - для
изготовления конструкций на стендах по традиционной технологии (I вариант) и
менее 0,2 МПа - для изготовления конструкций в силовых формах и на стендах при
наличии устройств по регулированию натяжения арматуры (II вариант).
7.42. При
изготовлении преднапряженных конструкций по II варианту для замедления роста
прочности бетона на этапе подъема температуры в процессе его термообработки и
уменьшения возможности образования трещин подвижность бетонной смеси с СП
должна находиться в пределах 7 - 8 см.
7.43. Режим
термообработки должен обеспечивать прочность бетона к началу изотермического
прогрева не более 5 МПа.
7.44. Дозировка СП
определяется видом применяемого цемента и технологией изготовления конструкций
и обычно находится в пределах 0,4 - 0,8% массы цемента.
7.45. При
изготовлении конструкций в силовых формах рекомендуется применение послойного
формования, при котором в зону преднапряженной арматуры укладывается бетонная
смесь с СП, а поверх нее - бетонная смесь без добавок или с ускорителем
твердения. При этом возможно сокращение времени термообработки.
7.46. Особенностью
формования плит типа КЖС является то, что вертикальные ребра формуются из
бетонной смеси с СП, а горизонтальная часть плит - из бетонной смеси без
добавки или с ускорителем твердения. С целью обеспечения качественного
изготовления плит рекомендуется применять следующий режим их термовлажностной
обработки: подъем температуры осуществлять сразу после окончания формования в
течение 1 ч по одноступенчатому режиму, после чего - кратковременное повторное
вибрирование.
Виброгидропрессованные
трубы
7.47. Изготовление
виброгидропрессованных труб производится в соответствии с ГОСТ 12586.0-83 и
СНиП 3.09.01-83 (прил. 2 обязательное).
7.48. При
применении СП рекомендуется увеличение подвижности бетонной смеси до 6 - 8 см
(по сравнению с 2 - 3 см для бетонной смеси без добавок).
7.49. Бетонная
смесь не должна проявлять признаков расслаиваемости при транспортировании,
перегрузках, распределении на загрузочном конусе и в процессе формования трубы.
7.50. В случае
появления признаков расслаиваемости бетонной смеси, а также для улучшения
внутренней поверхности трубы рекомендуется на 10 - 15% увеличить долю песка в
составе бетонной смеси за счет сокращения расхода крупного заполнителя.
7.51. С целью
максимального уменьшения возможности прорезания бетона, изготовленного из
подвижных смесей, арматурой при ее напряжении следует применить один из двух
режимов прессования:
а) осуществить
отжим воды давлением 0,1 - 0,8 МПа в течение 15 - 60 мин, а затем поднять
опрессовочное давление до расчетного значения;
б) осуществить
выдержку перед прессованием при температуре +20 °C в течение 2 ч, а затем при
40 °C - 0,5 ч.
8.
ПРИМЕНЕНИЕ СУПЕРПЛАСТИФИКАТОРОВ В МОНОЛИТНОМ БЕТОНЕ
Дополнительные
требования к материалам и составу бетона
8.1. Для
приготовления монолитного бетона из бетонных смесей с СП следует применять
цементы по пп. 2.1 и 2.4 настоящих Рекомендаций с ограничением величины
нормальной густоты 28% и содержания
- 7%.
8.2. Рекомендуется
применять пески с модулем крупности в пределах от 1,6 до 2,6. При этом
содержание пылевидных, илистых и глинистых частиц не должно превышать 3 - 10%.
Доля песка в абсолютном объеме смеси заполнителей должна приниматься не менее
0,4.
8.3. Суммарное
содержание цемента и тонкодисперсных частиц заполнителей в бетонной смеси с
суперпластификатором С-3 должно быть не менее 400 кг/м3, минимальный расход
цемента - 300 кг/м3.
8.4. В качестве
крупного заполнителя для бетонной смеси рекомендуется применять щебень с
содержанием лещадки не более 10% по массе. Максимальные размеры зерен
заполнителя не должны превышать 40 мм.
8.5. Максимальное
содержание крупного заполнителя (частиц размером более 5 мм) в бетонной смеси
не должно превышать 0,8 м3/м3, а при использовании трубопроводного транспорта -
не более значений, указанных в табл. 12.
Таблица 12
Количество
крупного заполнителя, рекомендуемое
для изготовления
монолитных бетонов с суперпластификаторами
───────────────┬───────────────────────────────────────────────────────────
Максимальный
│ Объем крупного
заполнителя, м3/м3, при модуле крупности
размер зерен
│ мелкого
заполнителя
крупного
├─────────┬─────────┬─────────┬─────────┬─────────┬─────────
заполнителя,
мм│
1,4 │ 1,6
│ 1,8
│ 2,0 │
2,4 │ 2,6
───────────────┼─────────┼─────────┼─────────┼─────────┼─────────┼─────────
10
│ 0,55 │
0,52 │ 0,48
│ 0,45 │
0,42 │ 0,4
20
│ 0,65 │
0,63 │ 0,6
│ 0,58 │
0,56 │ 0,54
40
│ 0,76 │
0,74 │ 0,72
│ 0,7 │
0,67 │ 0,65
8.6. Рекомендуемый
гранулометрический состав заполнителей в зависимости от подвижности бетонной
смеси, обеспечивающий минимальный расход цемента, приведен на рис. 2.
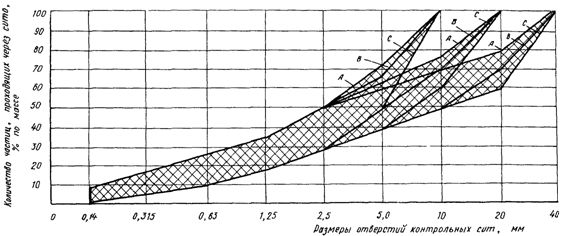
Рис. 2.
Рекомендуемый гранулометрический состав
заполнителей для
бетонных смесей с суперпластификатором С-3
A, B, C - граничные
значения максимального содержания
крупных частиц в
смеси заполнителей при различной
подвижности
бетонной смеси: A - ОК = 16 - 24 см;
B - ОК = 10 - 15 см; C - ОК = 5 - 9 см
8.7. Бетонные смеси
с СП должны иметь степень расслоения не более 5% и отклонение от заданной
подвижности не более +/- 1 см.
8.8. Подвижность
бетонной смеси назначается из условия технологичности бетонирования
конструкций. За оптимальную принимается подвижность, обеспечивающая минимальную
трудоемкость бетонирования при минимально возможном расходе цемента при условии
соответствия свойств бетона проектным требованиям.
8.9. Исходная
подвижность с СП должна назначаться с учетом ее изменения в процессе
транспортирования и подачи к месту укладки. Она определяется по формуле
, (3)
где ОК - заданная подвижность смеси при ее укладке в
конструкции, см;
,
- коэффициенты, учитывающие влияние
соответственно способов транспортирования и подачи смеси на изменение ее
подвижности (см. табл. 13).
Таблица 13
Ориентировочные
значения коэффициентов, учитывающих
влияние процессов
транспортирования
и подачи
,
на подвижность
бетонной смеси с расходом цемента марки 400,
содержащего
до 7%, в пределах 360 - 400 кг/м3
───────┬───────────┬─────────────────────────────┬─────────────────────────
ОК, см │Температура│ K при
продолжительности │ K
│окружающего│ т │ п
│ воздуха, │
транспортирования, мин │
│ °C
├─────────┬─────────┬─────────┼──────────┬──────────────
│ │ до 30
│ до 45 │
до 60
│кран-бадья│трубопроводный
│ │ │ │ │ │ транспорт
───────┼───────────┼─────────┼─────────┼─────────┼──────────┼──────────────
8
- 12 │до 20 °C │ 1,0
│ 1,05 │
1,2 │ 1,05
│ 1,0
│ │ ---
│ ---- │
--- │ ----
│ ----
│ │ 1,0
│ 1,03 │
1,1 │ 1,08
│ 1,03
│ │ │ │ │ │
│25 °C │
1,03 │ 1,25
│ - │
1,08 │ 1,1
│и выше │
---- │ ----
│ ---- │
---- │
----
│ │ 1,03
│ 1,15 │
1,25 │ 1,1
│ 1,25
│ │ │ │ │ │
│до 20 °C │
1,0 │ 1,1
│ 1,25 │
1,07 │ 1,0
│ │ ---
│ --- │
---- │ ----
│ ----
│ │ 1,0
│ 1,1 │
1,2 │ 1,1
│ 1,05
│ │ │ │ │ │
18
- 22│25 °C │ 1,05
│ 1,3 │
- │ 1,1
│ 1,15
│и выше │
---- │ ---
│ --- │
---- │ ----
│ │ 1,05
│ 1,2 │
1,3 │ 1,15
│ 1,2
Примечание. В
числителе - значения коэффициентов для бетонов, изготовленных на
портландцементе марки 400 с содержанием
до 5%, в знаменателе - то же, марок 400 - 500
с содержанием
.
8.10. Рекомендуемые
составы бетонных смесей с СП даны в табл. 14.
Таблица 14
Рекомендуемые
составы бетонных смесей
с суперпластификаторами
─────────────────────────────────────────┬─────────────────────────────────
Показатели │ Способ подачи
├────────────────┬────────────────
│ кран-бадья
│ трубопроводный
│
│ транспорт
─────────────────────────────────────────┼────────────────┼────────────────
Тяжелый бетон │ │
│ │
Расход
цемента, кг/м3 │ 300 - 450
│ 300 - 450
Расход
песка, кг/м3 │ 600 - 900
│ 700 - 1000
Расход
щебня, кг/м3 │
1000 - 1200 │ 950 - 1100
Дозировка
СП, %
│ 0,3 - 1,0 │
0,4 - 0,8
│ │
Легкий бетон │ │
│ │
Расход
цемента, кг/м3 │ 350 - 450
│ 350 - 450
Расход
песка:
│ │
пористого, л/м3 │ 400 - 500
│ 420 - 500
плотного, кг/м3 │ 600 - 800
│ 700 - 900
Расход
крупного заполнителя, л/м3 │ 700 - 900
│ 600 - 700
В/Ц
│ 0,38 - 0,55 │
0,4 - 0,5
ист │ │
Дозировка
СП, %
│ 0,4 - 0,9 │
0,4 - 0,7
Приготовление и
транспортирование бетонных смесей
8.11. При
применении СП в производстве бетонных работ рекомендуется использовать
эффективное современное оборудование и оснастку, автоматизированные и
механизированные бетоносмесительные установки и
бетонные заводы, автобетоносмесители, специализированные перегружатели,
усовершенствованные бункеры, бетононасосы, распределительные стрелы,
механические манипуляторы и т.д.
8.12. Бетонные смеси
с добавкой СП следует приготовлять в соответствии с ГОСТ 7473-85 и с учетом
указаний настоящих Рекомендаций.
8.13. Приготовление
бетонных смесей для бетонирования монолитных конструкций следует производить:
на стационарных
бетонных заводах;
в автобетоносмесителях;
по комбинированной
схеме.
8.14. Стационарные
бетонные заводы следует оборудовать помещениями и устройствами для хранения,
приготовления и дозирования химических добавок. Рекомендуется применять типовой
проект "Автоматизированного отделения по приготовлению жидких химических добавок
для бетона и раствора для бетоносмесительного узла производительностью 50
м3/ч" ТП 404-28-24, разработанный институтами "Гипростроммашина"
и ПИ-2 и распространяемый ЦИТП Госстроя СССР.
8.15. В качестве
бетоносмесителей рекомендуется использовать смесители как гравитационного, так
и принудительного типа. Оптимальная продолжительность цикла перемешивания
составляет 240 - 300 с - для
смесителей гравитационного типа и 100 - 150 с - для смесителей принудительного
типа.
8.16. Для
приготовления бетонной смеси на стационарном бетонном заводе добавки СП следует
вводить в состав бетонной смеси одним из следующих способов:
вместе с расчетным
(на замес) количеством воды затворения;
в предварительно
перемешанную бетонную смесь с частью (10 - 20%) воды затворения на 1 - 2 мин до
окончания перемешивания.
Второй способ
позволяет получить больший пластифицирующий эффект.
8.17. В качестве
транспортных средств для поставки бетонных смесей с СП
следует использовать автобетоносмесители и автобетоновозы.
8.18. Доставку
бетонных смесей с СП в зависимости от условий производства бетонных работ
рекомендуется осуществлять путем транспортирования:
готовой смеси;
частично
приготовленных смесей с последующим введением СП;
сухих смесей с
последующим их приготовлением в процессе доставки или на объекте.
8.19.
Транспортирование готовых смесей должно осуществляться в автобетоносмесителях и
автобетоновозах. Для уменьшения испарения влаги и исключения воздействия на
смесь атмосферных осадков и прямых солнечных лучей открытые части кузова автобетоновоза
и барабана автобетоносмесителя рекомендуется укрывать брезентом и т.п.
материалами. Данный способ доставки целесообразно использовать при
продолжительности транспортирования готовой смеси не более значений, указанных
в табл. 15.
Таблица 15
Допустимая
продолжительность транспортирования
бетонных смесей с
суперпластификаторами различных марок
───────────────┬────────────────────┬───────────┬──────────────────────────
Вид смеси
│ Средства │Температура│ Продолжительность
│ транспортирования │ бетонной │
транспортирования
│ │ смеси, °C │
бетонных смесей с СП, ч,
│ │ │ марок
│ │ ├────────────┬─────────────
│ │ │С-3, 40-03, │10-03,
МФ-АР
│ │ │ Дофен
│
───────────────┼────────────────────┼───────────┼────────────┼─────────────
Малоподвижная
│Автосамосвалы
│ 15 - 24 │
1 - 2,5 │ 1 - 2
│ │ 25 - 35
│0,25 - 0,75 │ 0,25 - 0,5
Высокоподвижная│Автобетоносмесители
│ 15 - 24 │
1 - 2 │ 1 - 1,5
и
литая │ │ 25 - 35
│ 1 - 1,5 │
0,5 - 1
То
же │Автобетоносмесители
│ 15 - 24 │ 2,5 - 4,5 │
2,5 - 4
│(по пп.
8.21 и 8.22 │ 25 - 35 │
1 - 2 │ 0,5 - 1,5
│настоящих │ │ │
│Рекомендаций) │ │ │
То
же │Автосамосвалы + │
15 - 24 │ 3 - 4,5
│ 1,5 - 2,5
│автобетоносмесители
│ 25 - 35 │ 1,5 - 2 │
1 - 1,5
│(по пп.
8.24 и 8.25 │
│ │
│настоящих │ │ │
│Рекомендаций) │ │ │
8.20. С
целью увеличения допустимого времени транспортирования готовых смесей, а также
снижения их расслаиваемости в процессе доставки рекомендуется в бетонную смесь
в комплексе с СП вводить воздухововлекающие добавки типа СНВ и СДО в количестве
0,005 - 0,015%, замедлитель схватывания НТФ в количестве 0,04 - 0,06%,
газообразующие добавки типа 136-41 - 0,05 - 0,07% массы цемента. Для
восстановления подвижности готовой бетонной смеси может быть использовано также
повторное введение СП в количестве 0,2 - 0,4% массы цемента, которое
целесообразно осуществлять непосредственно перед разгрузкой
автобетоносмесителя.
8.21. При
продолжительности транспортирования более указанной в
табл. 15 рекомендуется доставлять на объект сухую или частично приготовленную
смесь. В случае загрузки в автобетоносмеситель или автобетоновоз частично
приготовленной смеси на заводе товарного бетона вводится 2/3 воды затворения, а
1/3 - на строительной площадке вместе с СП.
8.22.
Окончательное приготовление бетонной смеси рекомендуется осуществлять в
автобетоносмесителях или смесителях-перегружателях, оборудованных емкостью для
дозирования и введения добавок.
Режим приготовления
(скорость вращения барабана и время перемешивания) бетонных смесей с СП в
автобетоносмесителе рекомендуется назначать в следующих пределах:
при загрузке
частично приготовленной смеси - 10 - 12 об/мин в
течение 10 - 15 мин;
при загрузке сухой
смеси - 6 - 10 об/мин в течение 15 - 20 мин.
8.23. Для
транспортирования готовых и частично приготовленных смесей при отрицательных
температурах ниже -15 °C целесообразно использовать автобетоносмесители или
автобетоновозы в зимнем исполнении. С целью предохранения бетонной смеси от
замерзания в процессе ее доставки рекомендуется в комплексе с СП использовать
противоморозные добавки типа НН в количестве, указанном в "Руководстве по
применению химических добавок в бетоне" (М., Стройиздат, 1981). При этом
количество суперпластификатора для получения равноподвижной смеси может быть
уменьшено на 15 - 25%.
8.24.
Приготовление бетонной смеси комбинированным способом заключается в следующем:
приготовление смеси
на стационарном бетонном заводе;
транспортирование
ее в автосамосвалах к узлам дополнительного перемешивания;
перегрузка в
средства дополнительного перемешивания - автобетоносмесители или
бетоноперегружатели;
дополнительное
перемешивание бетонной смеси;
транспортирование
смеси к месту укладки.
8.25.
Комбинированные схемы приготовления бетонной смеси с добавками, как правило,
следует применять при бетонировании монолитных конструкций литыми бетонными
смесями в случае недостаточного количества автобетоносмесителей.
Бетонную смесь
следует перегружать из автосамосвала в бетоноперегружатель или
автобетоносмеситель на узле дополнительного перемешивания полностью без
остатка, потерь или разделения на части.
8.26. Узлы
дополнительного перемешивания следует устраивать в непосредственной близости от
бетонируемого объекта. Их следует оборудовать помещениями для хранения и
подготовки СП, а также устройствами для их дозирования.
8.27. Введение СП в
состав бетонной смеси при комбинированном способе приготовления следует
производить одним из следующих способов:
на стационарном
бетонном заводе (в этом случае дополнительное перемешивание позволяет улучшить
однородность бетонной смеси и устранить ее возможное расслаивание в процессе
транспортирования);
на узле дополнительного
перемешивания (в этом случае транспортируется сухая или жесткая, частично
приготовленная бетонная смесь, а высокоподвижную или литую смесь получают на
объекте бетонирования).
8.28. Для
увеличения сохраняемости бетонных смесей следует руководствоваться указаниями
п. 8.20 настоящих Рекомендаций.
Подача и укладка
бетонной смеси, твердение бетона
8.29. Подача
бетонной смеси с СП в конструкцию должна осуществляться средствами,
исключающими потери жидкой фазы и промежуточные перегрузки смеси.
8.30. При
подаче бетонной смеси по традиционной схеме кран-бадья могут использоваться
герметичные поворотные бункера по ГОСТ 21807-76, оснащенные гибким рукавом для
распределения смеси непосредственно в бетонируемые конструкции. Длина и диаметр
гибкого рукава принимаются в зависимости от типа монолитных конструкций и
находятся в пределах соответственно 0,8 - 3 м и 150 - 300 мм.
8.31. При укладке
литых бетонных смесей с СП уплотнение смеси осуществляется под действием
гравитационных сил. Кратковременная вибрация глубинными вибраторами в течение 3
- 5 с рекомендуется при
бетонировании густоармированных конструкций, сооружений со сложной
конфигурацией, а также в местах узловых соединений конструкций.
8.32. Бетонные
смеси литой консистенции (без виброуплотнения) должны иметь осадку конуса к
моменту укладки не менее 18 см. Бетонные смеси с осадкой конуса менее 18 см
следует уплотнять при помощи вибрации. Продолжительность вибровоздействия
следует назначать на основе данных лаборатории. При этом следует учитывать, что
превышение оптимального времени вибрирования может привести к расслаиванию
бетонной смеси. Ее связность следует увеличить, используя указания п. 8.20
настоящих Рекомендаций.
8.33. При укладке
литой и высокоподвижной смесей в конструкции, имеющие уклон неопалубливаемой
поверхности более 3% от горизонтали, следует предусматривать меры,
предотвращающие сползание бетона.
8.34. При
уплотнении малоподвижных смесей с добавкой СП следует учитывать, что их
жесткость в 1,4 - 1,6 раза меньше, чем жесткость смесей эталонного состава без
добавки.
8.35. Свободное
сбрасывание смесей в армированные конструкции следует допускать с высоты не
более 2 м. При большей высоте следует применять лотки или бетоноводы, которые
при высоте более 10 м следует оборудовать гасителями скорости.
8.36. Допускается
сбрасывание смеси с высоты до 6 м в опалубку неармированных конструкций и
ячейки армоопалубочных блоков, не имеющих во внутреннем сечении арматуры или
каких-либо коммуникаций, при условии обеспечения сохранности опалубки и ячеек
армоопалубочных блоков.
8.37. Для
механизации приема, подачи и распределения бетонных смесей с СП рекомендуется
использовать бетононасосы и автономные распределительные стрелы или
механические манипуляторы.
8.38. Подвижность
бетонных смесей, транспортируемых с помощью пневмоустановок, должна составлять
6 - 12 см.
8.39. При укладке
бетонных смесей с СП напорным методом бетонирования виброобработка бетона не
требуется.
8.40. Для
обеспечения удобоперекачиваемости бетонных смесей с СП необходимо соблюдать
требования, приведенные в "Руководстве по укладке бетонных смесей
бетононасосными установками" (М., Стройиздат, 1978). При этом максимальный
объем крупного заполнителя на 1 м3 бетонной смеси в зависимости от модуля
крупности мелкого заполнителя и максимального размера зерен крупного
заполнителя следует принимать в соответствии с табл. 12.
8.41. Для расчета
технологических параметров трубопроводной подачи бетонной смеси с СП могут быть
использованы следующие эависимости:
; (4)
, (5)
где
,
- потери давления на прямых участках трубопровода
и в коленах (переходном конусе), МПа;
,
- соответственно длина прямых участков
трубопровода и колес (переходного конуса), м;
d - диаметр
трубопровода, м;
- средняя скорость движения бетонной смеси по
трубопроводу, м/с;
;
Q -
производительность бетононасоса, м3/ч;
- плотность бетонной смеси, кг/м3;
- безразмерный коэффициент, учитывающий
влияние местных сопротивлений, приведенный в табл. 16.
Таблица 16
Значения
коэффициента

для наиболее
характерных местных сопротивлений
───────────────────────────────────────────────────────┬───────────────────
Местное сопротивление │ K
│ м
───────────────────────────────────────────────────────┼───────────────────
Колено
90° с радиусом закругления 0,33 м
│ 6,7
То
же, с радиусом - 0,5 м │ 5,3
Колено
45° с радиусом - 0,33 м
│ 2,7
То
же, с радиусом - 0,5 м │ 1,6
Переходный
конус с 180 на 125 мм
│ 6
То
же, в виде колена 90° с радиусом 0,5 м │ 9,3
8.42. При
назначении периода выдерживания бетона до начала заглаживания и затирки
поверхностей следует учитывать более интенсивный набор критической прочности
бетона с СП по сравнению с бетоном без добавки, полученным из равноподвижной
смеси.
Опалубочные работы
8.43. Опалубка
бетонируемых конструкций должна быть плотной и не должна допускать утечки
бетонной смеси и разжиженного цементного теста. При бетонировании отдельными
захватками конструкцию следует разделять на участки по вертикали следующими
средствами:
опалубкой;
металлической
сеткой с ячейками размером 2 - 5 мм;
пленочными или
тканевыми материалами в комбинации с крупноячеистой несущей сеткой.
8.44. При расчете
скользящей опалубки следует учитывать меньшую среднюю величину трения-сцепления
бетона с СП по сравнению с бетоном без добавки. Ориентировочные значения
трения-сцепления для тяжелого бетона марок M200 - M300 и легкого марок M150 -
M200 с расходом цемента марки 400, равным 340 - 380 кг/м3, приведены в табл.
17.
Таблица 17
Ориентировочные
значения трения-сцепления
металлической
палубы опалубки с тяжелым и легким бетоном
при расходе цемента
марки 400, равном 340 - 380 кг/м3,
и содержании суперпластификатора С-3 - 0,5 - 0,6%
───────────────────┬───────────────────────────────────────────────────────
Подвижность │ Трение-сцепление, Н/м2
бетонной
смеси, см
├───────────────────────────┬───────────────────────────
│ Тяжелый бетон марки │
Керамзитобетон марки
├─────────────┬─────────────┼─────────────┬─────────────
│ M200
│ M300 │
M150 │ M200
───────────────────┼─────────────┼─────────────┼─────────────┼─────────────
10 - 12 │ 500
│ 620 │
550 │ 650
18 - 22 │ 250
│ 320 │
280 │ 320
8.45. При назначении
оптимальной скорости подъема скользящей опалубки следует учитывать более
интенсивный набор минимальной распалубочной прочности бетона с
суперпластификатором по сравнению с бетоном без добавки.
Скорость подъема
опалубки и интенсивность бетонирования устанавливается в зависимости от
принятой технологии и условий бетонных работ на основании результатов испытания
бетонных образцов в начальные сроки твердения.
8.46. При
бетонировании монолитных конструкций в переставных типах опалубки следует
учитывать большее боковое давление литой бетонной смеси с СП. Ориентировочные расчетные значения бокового давления литой смеси на
опалубку для тяжелого марок M200 - M300 и легкого марок M150 - M200 бетонов с
расходом цемента марки 400 340 - 380 кг/м3 приведены в табл. 18.
Таблица 18
Ориентировочные
значения коэффициента бокового давления
литой бетонной
смеси с расходом цемента 340 - 380 кг/м3
────────────────────────┬──────────────────────────────────────────────────
Высота слоя бетона, м │ Коэффициент бокового давления
├────────────────────────┬─────────────────────────
│ Тяжелый бетон │ Керамзитобетон
────────────────────────┼────────────────────────┼─────────────────────────
0,4
│ 0,99 │ 0,98
0,8 │ 0,98 │ 0,965
1,2 │ 0,97 │ 0,95
1,6 │ 0,93 │ 0,91
2,0 │ 0,86 │ 0,84
2,4 │ 0,76 │ 0,73
2,8 │ 0,64 │ 0,6
8.47. При напорном
бетонировании монолитных конструкций необходимо учитывать дополнительные
нагрузки на опалубку в результате действия гидродинамического давления
восходящего потока бетонной смеси. С достаточной для практики точностью
коэффициент, учитывающий увеличение бокового давления бетонной смеси на
опалубку при напорном бетонировании, может быть принят равным 1,35 - 1,4.
Особенности
изготовления монолитных конструкций
различных видов
8.48. Для
изготовления конструкций из высокопрочных монолитных бетонов марки M600,
получаемых из литых смесей, укладываемых без вибрации, и марок M600 - M700,
получаемых из смесей, уплотняемых вибрацией, в качестве крупного заполнителя
следует применять щебень из изверженных горных пород с прочностью по дробимости
не менее 120 МПа.
8.49. Для
изготовления высокопрочных монолитных бетонов марок M700 - M800, получаемых из
литых смесей, укладываемых без вибрации, марок M800 - M1000, получаемых из
смесей, уплотняемых вибрацией, к заполнителям предъявляются следующие
дополнительные требования:
содержание примесей
в крупных заполнителях - не более 0,25%, в мелком заполнителе - не более 1% (по
массе);
содержание глины в
комках - не допускается;
содержание частиц,
проходящих через сито 0,14 мм, - не более 5% (по массе);
рекомендуется
удалять из мелкого заполнителя частицы размером более 2,5 мм.
Максимальный размер
зерен крупного заполнителя следует устанавливать с учетом требований пп. 4.7 и
4.8 СНиП III-15-76, а также п. 3.10 "Руководства по укладке бетонных
смесей бетононасосными установками" (М., Стройиздат, 1978).
8.50. Бетонирование
массивных конструкций следует осуществлять в соответствии с существующими
нормативными документами с учетом требований настоящих Рекомендаций. При этом
необходимо обращать внимание на соблюдение темпа бетонирования.
8.51. Минимальный
темп подачи бетонной смеси следует назначать из условия обеспечения
монолитности бетона, достигаемой своевременным перекрытием слоев при послойном
бетонировании.
Минимальный темп
бетонирования следует рассчитывать по формуле
, (6)
где
- требуемый минимальный темп бетонирования,
м3/ч;
F - площадь сечения
бетонируемой конструкции или захватки, м2;
h - высота
укладываемого слоя бетона, м;
- начало схватывания бетонной смеси при
температуре 20 °C, ч;
- коэффициент, учитывающий влияние температуры
бетонной смеси на начало ее схватывания;
- продолжительность перевозки бетонной смеси
от бетонного завода до объекта, ч;
- продолжительность укладки бетона
(перегрузка, транспортирование от места выгрузки до места укладки и пр.), ч.
Значения
и
следует принимать по табл. 19 и при
необходимости уточнять в лаборатории.
Таблица 19
Время начала
схватывания бетонной смеси
в зависимости от ее
консистенции и температуры
───────────────┬───────────────────┬───────┬───────────────────────────────
Консистенция
│ Марка │t , ч│Величина K при температуре, °C
смеси
│суперпластификатора│ н.с │ т
│ │
├───────────────┬───────────────
│ │ │ 5 - 15
│ 25 - 35
───────────────┼───────────────────┼───────┼───────────────┼───────────────
Малоподвижная │С-3, 40-03, Дофен │3 - 4,5│ 1,3
│ 0,28
│10-03, МФ-АР │ 3 - 4 │ 1,2
│ 0,25
Высокоподвижная│С-3,
40-03, Дофен │ 4 - 6 │ 1,15
│ 0,52
или
литая
│10-03, МФ-АР │
4 - 5 │ 1,1 │ 0,4
8.52. Способы
применения СП С-3 в монолитном бетоне для транспортного строительства приведены
в Прил. 3 настоящих Рекомендаций.
8.53.
Суперпластификаторы рекомендуется применять для бетонирования монолитных
конструкций из конструкционных и конструкционно-теплоизоляционных бетонов
слитной структуры марки M150 и выше.
8.54. Для получения
удобоукладываемых связных легкобетонных смесей максимальное количество крупного
пористого заполнителя в них не должно превышать значений, указанных в табл. 14.
В смесях, предназначенных для перекачивания по трубопроводам, расход крупного
заполнителя должен быть не более 700 л/м3.
8.55. Для
изготовления легких бетонов рекомендуется применять плотные и пористые пески с
модулем крупности
.
8.56. С целью повышения эффекта введения СП, а также для обеспечения
связности и удобоперекачиваемости высокоподвижных и литых легкобетонных смесей
рекомендуется производить предварительное водонасыщение крупных пористых
заполнителей в специальных вакуум-установках (Прил. 6) в соответствии с
указаниями "Методических рекомендаций по транспортированию и укладке легкобетонных
смесей с помощью бетононасосных установок" (М., ЦНИИОМТП, 1983).
Примечание.
Водонасыщение заполнителей не рекомендуется в случаях, когда к бетону
предъявляются повышенные требования по морозостойкости (F выше 100 циклов).
8.57. Подбор
состава бетона для монолитного строительства должен производиться с учетом
требуемой подвижности бетонной смеси, которую рекомендуется назначать в
пределах 2 - 15 см при использовании заполнителей естественной влажности
насыпной плотностью до 600 кг/м3 и 2 - 24 см - при использовании предварительно
водонасыщенных крупных заполнителей плотностью более 600 кг/м3.
8.58. Подвижность
легкобетонных смесей, предназначенных для перекачивания по трубам, должна быть
не менее 6 см.
8.59. При
использовании водонасыщенного крупного заполнителя минимальное содержание
тонкодисперсной фазы (цемент + пылевидные частицы) рекомендуется не менее 400
кг/м3, а расход цемента при этом должен составлять не менее 270 кг/м3.
8.60. При
использовании крупного пористого заполнителя естественной влажности минимальное
содержание в смеси тонкодисперсной фазы рекомендуется не менее 430 кг/м3, а
расход цемента - 300 кг/м3.
8.61. С целью
повышения однородности легкобетонной смеси, а также при недостаточном
содержании в ней пылевидных частиц рекомендуется вводить тонкомолотые
минеральные добавки типа золы-уноса, бентонита, гидравлической извести и др.
8.62. С целью
улучшения технологических свойств (однородность, связность, удобоукладываемость
и др.) легкобетонной смеси и легкого бетона в комплексе с СП рекомендуется
применять следующие добавки:
для
конструкционно-теплоизоляционных бетонов марок M150 - M200 - СДО или СНВ в
количестве 0,05 - 0,1% массы цемента;
при производстве
бетонных работ в жаркую погоду - СДБ в количестве 0,2 - 0,25% массы цемента;
при производстве
бетонных работ при отрицательных температурах - нитрит натрия в количестве 3 -
5% или нитрит-нитрат-хлорид кальция в количестве 1 - 3% массы цемента.
8.63. При
использовании комплексных добавок концентрацию суперпластификатора уменьшают в
соответствии с пластифицирующим эффектом применяемых добавок.
8.64. Приготовление
легкобетонных смесей на крупном заполнителе любой влажности насыпной плотностью
более 700 кг/м3 может осуществляться в смесителях гравитационного или
принудительного типа, а при использовании заполнителя естественной влажности
насыпной плотностью менее 700 кг/м3 - только принудительного действия.
8.65.
Суперпластификатор рекомендуется вводить отдельно в смесь (после трехминутного
перемешивания компонентов с 80 - 90% воды затворения). Продолжительность
перемешивания после введения добавки и оставшегося количества воды должна
составлять не менее 1,5 - 2 мин.
8.66.
Продолжительность транспортирования готовых легкобетонных смесей на
обработанных водонасыщением пористых заполнителях не должна превышать значений,
указанных в табл. 15. Продолжительность транспортирования смесей, изготовленных
на сухих заполнителях, сокращается в 1,5 - 2 раза. При более длительном
транспортировании рекомендуется осуществлять приготовление бетонной смеси в автобетоносмесителях.
Конкретное время продолжительности транспортирования следует определять
экспериментально.
8.67. При
транспортировании легкобетонных смесей по схеме кран-бадья общее время ее
приемки, подачи и выгрузки не должно превышать 10 - 15 мин при температуре
окружающего воздуха не выше +20 °C и 5 - 10 мин в условиях повышенных
температур (> 25 °C).
8.68. Во избежание
расслаиваемости высота выгрузки легкобетонной смеси из бункеров не должна
превышать 1,5 м - при бетонировании вертикальных конструкций и 0,7 м -
горизонтальных.
8.69. Для подачи
литых легкобетонных смесей необходимо использовать герметичные поворотные
бункера с гибким рукавом (см. п. 8.30 настоящих Рекомендаций).
8.70.
Продолжительность перерывов при подаче легкобетонных смесей с СП бетононасосами
не должна превышать 15 мин. В жаркую погоду
или при нагреве бетоновода солнечными лучами
продолжительность перерывов должна быть сведена до минимума.
8.71. Для
глубинного уплотнения легкобетонных смесей с СП рекомендуется применять
высокочастотные вибраторы типа ИВ-66, ИВ-67 и ИВ-75 с частотой колебаний 150 -
200 Гц. Продолжительность вибрирования рекомендуется назначать в пределах 10 -
15 с для смесей с
подвижностью 10 - 15 см; 15 - 20 с - с подвижностью 5 - 9 см и 25 - 30 с - с
подвижностью 1 - 4 см. Виброуплотнение легкобетонной смеси в течение 5 - 10 с
целесообразно применять при литьевом способе укладки (ОК
>= 16 см) смеси в углах, стыках, а также густоармированных местах монолитных
конструкций.
8.52. При
производстве работ по подводному бетонированию напорным методом рекомендуется
применять высокоподвижные и литые бетонные смеси с добавкой СП подвижностью не
менее 14 см.
8.73. Бетонирование
буронабивных свай и подводное бетонирование рекомендуется проводить с помощью
бетононасосов.
При бетонировании
набивных свай диаметром 600 - 1200 мм рекомендуется применять напорный
бетоновод диаметром 125 мм при скорости нагнетания бетонной смеси в пределах
0,4 - 0,7 м/с.
8.74. При
бетонировании буронабивных свай и других сооружений напорным методом в случае
перерывов в подаче бетонной смеси на 10 - 15 мин и более перед возобновлением
подачи бетонной смеси следует поднять вертикальный стояк бетоновода и при
необходимости демонтировать верхние звенья бетоновода. При этом необходимо
заглубление нижнего конца вертикального стояка напорного бетоновода в ранее уложенную
бетонную смесь не менее чем на 2 м.
При изготовлении
набивных свай методом напорного бетонирования необходимо учитывать также, что
давление бетононасоса расходуется на преодоление сопротивления по подъему
столба бетонной смеси. При этом максимальная высота подъема H, м, бетонной
смеси в скважине может быть определена из выражения
, (7)
где
- давление, развиваемое бетононасосом, МПа;
P - гидравлические
потери напора, МПа, определяемые по формуле
,
где
- удельное сопротивление движению бетонной
смеси на 1 м горизонтального участка бетоновода, МПа/м;
l - общая длина
бетоновода, м;
- местные потери напора, МПа.
8.75.
Суперпластификаторы рекомендуется применять при нанесении торкрет-бетона
как по "мокрому", так и по "сухому" способу, в том числе
активированного торкрета. При этом прочность торкрет-бетона повышается на 15 -
20%, а водонепроницаемость - на 2 - 4 ати по сравнению с обычным
торкрет-бетоном.
8.76. При
изготовлении торкрет-бетона следует использовать следующие материалы:
портландцемент (или быстротвердеющий портландцемент), кварцевый песок с
,
тонкомолотый песок с удельной поверхностью 4000 см2/г
(для активированного торкрет-бетона) и щебень фракции 5 - 10 мм. Содержание в
смеси заполнителей крупной фракции (5 - 10 мм) не должно превышать 50%.
Суперпластификаторы рекомендуется вводить в смесь в виде 3%-ного раствора в
составе воды затворения.
8.77. При
торкретировании "мокрым" способом приготовление и транспортирование
бетонных смесей с суперпластификатором С-3 осуществляется согласно положениям
соответствующего раздела настоящих Рекомендаций.
8.78. При
"мокром" способе торкретирования рекомендуется использовать
бетононасосы - для подачи бетонных и растворных смесей и растворонасосы - для
растворов, не содержащих частиц заполнителя размером более 5 мм. При
торкретировании "сухим" способом суперпластификаторы вводят в
транспортируемую по материальным рукавам сухую смесь вместе с водой затворения
через водяной патрубок сопла: при использовании добавки в виде порошка
последнюю дозируют и загружают в нагнетательную установку вместе с другими
сухими компонентами торкрет-смеси. Возможно
использование дополнительной напорной емкости, в которой содержится водный
раствор суперпластификатора.
8.79. В процессе
торкретирования давление воздуха в цемент-пушке должно быть в пределах 0,3 -
0,4 МПа, а давление в напорной емкости с раствором суперпластификатора на 0,1
МПа больше. Установка должна быть снабжена манометрами и водомером (см. рис.
3).
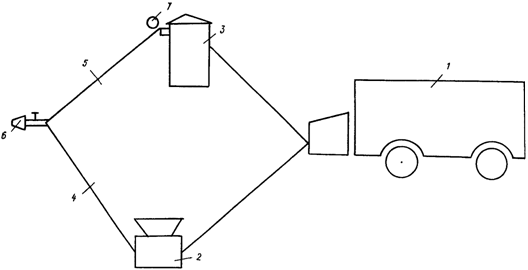
Рис. 3. Схема
установки для производства торкретных
работ с
использованием суперпластификаторов
1 - компрессор; 2 -
цемент-пушка; 3 - напорная емкость
с раствором добавки
расчетной концентрации;
4 - материальный
шланг; 5 - шланг для подачи
раствора добавки; 6
- сопло; 7 - манометр
8.80. При
приготовлении сухой смеси для активированного торкрет-бетона
следует провести предварительный помол песка (до получения необходимой удельной
поверхности) и перемешать его с цементом.
8.81. Устройство
гидроизоляции сооружений производится по обычным правилам торкретирования:
средняя толщина наносимого за один раз слоя не должна превышать 2 см, а каждый
последующий слой необходимо наносить до затвердения предыдущего слоя, т.е. не
позднее чем через 5 - 6 ч.
Рекомендуемые
составы смесей для торкретирования (в % по массе):
а) для торкрет-бетона марки M300:
портландцемент марки 400 ........................................ 30
песок
кварцевый
...................................... 60
суперпластификатор (3%-ный раствор) ............................. 10
б) для торкрет-бетона марки M400:
портландцемент марки M500 ....................................... 25
песок
кварцевый
...................................... 65
суперпластификатор (3%-ный раствор) ............................. 10
в) для
активированного торкрета:
портландцемент марки M400 ....................................... 40
тонкомолотый песок .............................................. 20
песок
кварцевый
...................................... 30
суперпластификатор (3%-ный раствор) ............................. 10
8.82. Изготовление
монолитных конструкций из жаростойкого бетона следует осуществлять в
соответствии с пп. 7.13 - 7.18 настоящих Рекомендаций.
8.83. Приготовление
мелкозернистых бетонов и инъекционных растворов с СП, предназначенных для
замоноличивания стыков в построечных условиях, осуществляется в соответствии с
"Руководством по проектированию и выполнению замоноличенных стыков колонн
железобетонных каркасов многоэтажных зданий" (М., НИИЖБ, 1976) и
указаниями настоящих Рекомендаций.
8.84.
Суперпластификаторы применяются с целью разжижения мелкозернистых и
инъекционных растворов, что обеспечивает:
замену двухстадийной
технологии укладки на одностадийную;
плотное
(качественное) заполнение полостей шва и подрезок бетона, в том числе за счет
непрерывной подачи смеси с одновременным вибрированием.
8.85. Оптимальные
дозировки СП следует назначать в следующих пределах: для бетонов - 0,5 - 0,9%,
для растворов - 0,4 - 0,8% массы цемента.
8.86. В случае
необходимости получения расширяющейся смеси в нее рекомендуется дополнительно
вводить суспензию алюминиевой пудры.
8.87. Бетонные
(растворные) смеси рекомендуется изготавливать в механических смесителях
объемом 50 - 100 л.
8.88. При
замоноличивании стыков рекомендуется применять термореактивную опалубку
(разработана институтом Оргтяжстрой Минтяжстроя СССР), представляющую собой
гибкую электронагревательную панель, внутренняя сторона которой одновременно
используется как опалубка.
Замоноличивание
стыков колонн в такой опалубке рекомендуется выполнять в следующей
последовательности:
а) проверить
работоспособность электронагревательной панели включением в питающую сеть на 2
- 3 мин;
б) закрепить
опалубку на колоннах при помощи обжимных приспособлений;
в) подать через
штуцер под давлением раствор до появления его в верхней части контрольного
отверстия опалубки;
г) выполнить
опрессовку раствора в стыке при давлении 0,1 МПа в течение 2 - 3 мин;
д) перекрыть
заслонкой входной штуцер на опалубке;
е) подключить
электронагревательную панель для прогрева стыка на 2 - 2,5 ч - летом и на 3 -
3,5 ч - зимой.
9. КОНТРОЛЬ
КАЧЕСТВА
9.1. Контроль
качества сборных железобетонных изделий и конструкций должен осуществляться в
соответствии со СНиП 3.09.01-85, монолитных конструкций и сооружений - в
соответствии со СНиП III-15-76 и с учетом требований настоящих Рекомендаций.
9.2. При применении
СП в технологии бетонов контроль за производством следует
осуществлять на следующих этапах работ:
при приемке,
хранении, транспортировании, приготовлении растворов и дозировании добавок;
при приготовлении,
транспортировании и укладке бетонных смесей;
при твердении
бетонов.
9.3. Контроль за производством работ и качеством бетона должен
осуществляться систематически так же, как и для бетона без добавок, в
соответствии с требованиями действующих стандартов, другой нормативной и
проектной документации.
9.4. При приеме СП,
поступивших с завода, их хранении, транспортировании и дозировании следует
иметь в виду те особенности добавок, которые указаны в Прил.
1.
9.5. По истечении
гарантийного срока хранения добавок их качество и эффективность следует
проверить непосредственно в бетонах.
9.6. Контроль за качеством растворов добавок состоит в проверке
их плотности. Не разрешается расходование растворов СП без их предварительного
тщательного перемешивания и без соответствующей корректировки тех растворов,
концентрация которых отличается от заданной.
9.7. Дозирование СП
следует осуществлять по массе или объему с точностью +/- 2% от его расчетного
количества.
9.8. При
изготовлении бетонной смеси следует контролировать длительность ее
перемешивания, температуру, подвижность, при необходимости - воздухосодержание.
9.9. При
транспортировании бетонной смеси на дальние расстояния следует контролировать
подвижность, температуру, расслаиваемость, а при необходимости -
воздухосодержание.
9.10. При укладке
бетонных смесей следует контролировать параметры виброуплотнения:
продолжительность, частоту и амплитуду колебаний.
9.11. При твердении
бетонов следует контролировать выбранный температурно-влажностный режим, а в
затвердевшем бетоне - его прочность (в контрольных кубах и при необходимости в
изделиях) и другие требуемые показатели качества (морозостойкость,
водонепроницаемость и т.д.), а также качество поверхности.
9.12. В процессе
твердения ячеисто-бетонной смеси следует определять кинетику нарастания
пластической прочности с целью определения предварительной выдержки перед
термообработкой.
9.13. Контроль
самонапряжения бетона на НЦ производится в соответствии с методикой,
приведенной в приложении к "Пособию по проектированию самонапряженных
железобетонных конструкций" (к СНиП 2.03.01-84 "Бетонные и железобетонные
конструкции").
10. ТЕХНИКА
БЕЗОПАСНОСТИ И ОХРАНА ТРУДА
10.1. При
производстве работ необходимо соблюдать правила техники безопасности согласно
требованиям главы СНиП III-4-80 "Техника безопасности в
строительстве", а также указания настоящего раздела.
10.2. При
проектировании узлов приготовления водных растворов добавок и бетонов с ними
необходимо строгое соблюдение требований действующих норм проектирования, в
частности, санитарной, взрывной, взрывно-пожарной и пожарной безопасности.
10.3. К работам по
подготовке материалов и приготовлению бетонных смесей, а также по формованию
изделий допускаются лица, изучившие оборудование, установки и прошедшие
инструктаж по технике безопасности.
10.4.
Суперпластификаторы относятся к веществам умеренно опасным. Их пары и
взвешенные в воздухе частицы высохшего вещества (пыль) раздражающе действуют на
слизистую оболочку глаз и на незащищенную кожу. Рабочие, занятые приготовлением
растворов добавок, должны пользоваться индивидуальными средствами защиты (резиновые
перчатки, фартуки, защитные очки, респираторы и т.д.).
10.5. Не следует
допускать к работам по приготовлению растворов добавок лиц с повреждением
кожного покрова (ссадины, ожоги, царапины, раздражения), с поражением век и
глаз.
10.6. Помещения для
приготовления растворов добавок, определения их качества и оптимальной
дозировки должны быть оборудованы приточно-вытяжной вентиляцией, а при
необходимости - местными отсосами.
10.7. Водные
растворы добавок суперпластификаторов непожароопасны. Однако продукты,
образующиеся после их высыхания, могут образовывать взрывоопасную смесь.
Поэтому места их проливов в помещении, а также тара и лабораторная посуда
должны быть промыты водой.
10.8. При работе на
низкочастотном оборудовании должны соблюдаться требования "Руководства по
улучшению условий труда рабочих вибро- и шумоопасных
профессий на предприятиях стройиндустрии" (М., Стройиздат, 1977), а также
"Руководства по ударной технологии изготовления железобетонных
изделий" (М., Стройиздат, 1979) и учитываться рекомендации настоящего
раздела.
Приложение
1
ХАРАКТЕРИСТИКИ
СУПЕРПЛАСТИФИКАТОРОВ
Суперпластификатор
С-3
1.
Суперпластификатор С-3 (ТУ 6-14-625-80** Минхимпрома) представляет собой добавку
на основе натриевых солей продуктов конденсации нафталинсульфокислоты и
формальдегида. Он должен отвечать требованиям, указанным в табл. 20.
Таблица 20
Требования к
суперпластификатору С-3
(в соответствии с
ТУ N 6-14-625-80**)
──────────────────────────────────────────────┬────────────────────────────
Наименование показателей │ Норма
──────────────────────────────────────────────┼────────────────────────────
1.
Внешний вид
│Жидкость коричневого цвета.
│Допускается осадок
2.
Содержание активного вещества в пересчете
│ 69
на сухой продукт, %, не менее │
3.
Содержание воды, %, не более
│ 68
4.
Содержание золы в пересчете на сухой
│ 38
продукт, %, не более │
5.
pH 2,5%-ного водного раствора
│ 7 - 9
2. СП С-3
поставляют в виде водного раствора 33 - 39%-ной концентрации в цистернах или
металлических бочках. Содержание воды в растворе указывается в паспорте.
Товарный продукт смешивается с водой в любых соотношениях.
3. СП С-3 может
выпускаться также в виде легкорастворимого неслеживающегося порошка коричневого
цвета с размером микрогранул 200 - 300 мкм. Порошкообразный продукт
транспортируют в мешках или резинокордных контейнерах объемом 1,0 и 1,5 м3. Его
растворы по своим свойствам полностью тождественны растворам жидкого
суперпластификатора той же концентрации.
4. СП С-3 изготавливается
Новомосковским заводом органического синтеза (г. Новомосковск Тульской обл.).
5. СП С-3 обладает
физическими свойствами, приведенными в табл. 21.
Таблица 21
Свойства водных
растворов
суперпластификатора
С-3 (при 20 °C)
───────┬──────┬────────┬────────────────┬────────────────────┬─────────────
│ │ │ -2 │ │
Концен-│Плот- │Содержа-│Вязкость x 10 ,│Удельная │Теплоемкость,
трация
│ность │ние │ Н x с/м2 │электропроводность x│ Дж/(кг x
К)
рас- │рас- │сухого
│
│ 3 -1
-1 │
твора,
│твора,│вещест- │ │x 10 x Ом , см
│
% │г/см3
│ва, г/л │
│ │
───────┼──────┼────────┼────────────────┼────────────────────┼─────────────
0
│0,998 │ 0 │
0,11 │ - │ 4,2
2
│1,008 │ 20,2 │
0,15 │ 4,44 │ 4,150
5
│1,023 │ 51,2 │
0,24 │ 5,65 │ 4,074
7
│1,033 │ 72,3 │ 0,32
│ 6,10 │ 4,024
10
│1,049 │ 104,9
│ 0,46 │ 6,57 │ 3,948
12
│1,059 │ 127,0
│ 0,58 │ 6,81 │ 3,898
15
│1,074 │ 161,1
│ 0,80 │ 7,10 │ 3,822
20
│1,099 │ 219,8
│ 1,30 │ 7,48 │ 3,696
25
│1,125 │ 281,1
│ 2,10 │ 7,78 │ 3,570
30
│1,150 │ 344,9
│ 3,11 │ 8,02 │ 3,444
33
│1,165 │ 384,4
│ 3,95 │ 8,15 │ 3,368
35
│1,175 │ 411,3
│ 4,63 │ 8,22 │ 3,318
37
│1,185 │ 438,5
│ 5,48 │ 8,30 │ 3,268
40
│1,200 │ 480,2
│ 7,11 │ 8,40 │ 3,192
6. Водный раствор
СП С-3 не изменяет своих свойств при нагревании до 85
°C. При замораживании до -40 °C и последующем полном оттаивании свойства
раствора также сохраняются. При температуре ниже +5 °C возможно образование
осадка (состоящего, в основном, из сульфата натрия и натриевой соли
,
смолистых продуктов), обладающего низкой пластифицирующей способностью. В
случае выпадения осадка перед применением СП С-3 его рекомендуется растворить
путем подогрева жидкой фазы острым паром или разбавления водой, после чего
тщательно перемешать раствор.
7. Анодная
поляризуемость стали в растворе СП С-3 составляет величину 0,28 - 0,34 мВ/мкА,
катодная - 20 - 25 мВ/мкА, коррозионный ток - 1,26 - 5,0 мкА/см2, что соответствует скорости коррозии
или 15 - 50 мкм/год. Поскольку коррозионный
процесс заторможен, для хранения добавки можно использовать оборудование,
изготовленное из обычной конструкционной стали.
В случае
образования осадка сульфата натрия низколегированные углеродистые стали
корродируют.
8. Гарантийный срок
хранения СП С-3 - 1 год <*>.
--------------------------------
<*> По
истечении гарантийного срока хранения суперпластификаторов рекомендуется
проверить их эффективность в бетонных смесях и бетонах для оценки возможности
их использования.
Суперпластификатор
МФ-АР
1. СП МФ-АР -
продукт конденсации меламина, формальдегида и натрия сульфаниловокислого. Он
должен отвечать требованиям ТУ N 6-05-1926-82 Минхимпрома (табл. 22).
Таблица 22
Требования к
суперпластификатору МФ-АР
(в соответствии с
ТУ N 6-05-1926-82)
──────────────────────────────────────────────┬────────────────────────────
Наименование показателей │ Норма
──────────────────────────────────────────────┼────────────────────────────
1.
Внешний вид
│Прозрачный раствор с легким
│осадком
2.
Растворимость в воде при 20 °C, %
│ 100
3.
Массовая доля сухого остатка, %
│ 20 +/- 2
4.
Плотность 20%-ного раствора смолы в воде
│ 1,08 - 1,12
при
20 °C, г/см3
│
5.
Вязкость 20%-ного раствора смолы при 20 °C,│
сП:
│
а) в момент изготовления │ 10 - 20
б) после хранения в течение 12 мес
│ 20 - 80
6.
Концентрация водородных ионов, pH при
│ 8,0 - 9,5
20
°C, в пределах
│
2. СП МФ-АР
поставляют в виде водного раствора с концентрацией сухого вещества 18 - 22%
(при увеличении концентрации более 22% раствор СП может загустевать в процессе
хранения). Водный раствор СП поставляют в бочках или цистернах. Возможно
получение СП в виде порошка, обладающего 100%-ной растворимостью. Порошкообразный СП может поставляться упакованным в мешки.
3. СП МФ-АР
изготавливается заводом "Метил" ПО Уралхимпласт Минхимпрома.
4. СП МФ-АР
обладает физическими свойствами, приведенными в табл. 23.
Таблица 23
Концентрация и
плотность водных растворов
суперпластификатора
МФ-АР (при 20 °C)
───────────────────────┬─────────────────────────┬─────────────────────────
Концентрация, % │
Концентрация, г/л │
Плотность, г/см3
───────────────────────┼─────────────────────────┼─────────────────────────
2,5 │ 25,5 │ 1,02
5 │ 52,0 │ 1,04
7,5 │ 78,8 │ 1,05
10 │ 106,0 │ 1,06
15 │ 162,0 │ 1,08
18 │ 195,3 │ 1,085
20 │ 218,0 │ 1,09
22 │ 250,8 │ 1,14
5. СП не изменяет
своих свойств при замораживании водного раствора при
температуре до -50 °C и нагревании его до температуры +35 °C. Следует избегать
многократного замораживания и оттаивания СП. Вязкость 20%-ного раствора
свежеприготовленной смолы в воде при 20 °C составляет 10 - 20 сП (сантипуаз).
СП МФ-АР не вызывает коррозии арматуры в бетоне, так как водный раствор СП
имеет слабощелочную реакцию (pH = 8,0 - 9,5).
Гарантийный срок
хранения добавки - 1 год.
Суперпластификатор
10-03
1. СП 10-03 -
продукт поликонденсации сульфированного триметинолмеламина.
2. СП 10-03
поставляется в виде водных растворов (прозрачная опалесцирующая, слегка
маслянистая жидкость) с концентрацией 20% и плотностью, равной 1,103 г/см3, в
металлических бочках или железнодорожных цистернах.
3. СП 10-03 должен
храниться в сухих помещениях при температуре не выше +20 °C в герметично
закрытой емкости, защищенной от воздействия солнечных лучей. При хранении
допускается осадок. Срок хранения - 3 мес со дня
изготовления.
4. СП 10-03
изготавливается на установках в гг. Москве, Енакиево (Донецкая
обл.) и Чапаевске (Куйбышевская обл.). Свойства водных растворов СП 10-03 даны
в табл. 24.
Таблица 24
Концентрация
и плотность водных растворов
суперпластификаторов
10-03 и 40-03 (при 20 °C)
───────────────┬─────────────────────────────┬─────────────────────────────
Концентрация,
%│ Концентрация, г/л │ Плотность, г/см3
├──────────────┬──────────────┼──────────────┬──────────────
│ 10-03
│ 40-03 │
10-03 │ 40-03
───────────────┼──────────────┼──────────────┼──────────────┼──────────────
9
│ 93,6 │
93,6 │
1,04 │ 1,04
17
│ 183,6 │
183,6 │ 1,08
│ 1,08
20
│ 206,0 │
218,0 │ 1,103
│ 1,09
23
│ 257,6 │
255,3 │ 1,12
│ 1,11
26
│ 296,4
│ 291,2 │
1,14 │ 1,12
29
│ - │ 330,6
│ - │ 1,14
31
│ - │ 356,5
│ - │ 1,15
33
│ - │ 382,8
│ - │
1,16
35
│ - │ 413,0
│ - │ 1,18
39
│ - │ 468,0
│ - │ 1,20
41
│ - │ 496,1
│ - │ 1,21
Суперпластификатор
40-03
1. СП 40-03
представляет собой смесь олигомерных соединений различной молекулярной массы,
получаемых при конденсации нефтяных сульфокислот с формальдегидом с последующей
нейтрализацией.
2. СП должен
храниться в закрытом помещении при температуре не ниже +5 °C. Гарантийный срок
хранения - 3 мес со дня изготовления. СП 40-03
готовится на опытно-промышленной установке института нефтехимических процессов
АН АзССР.
3. Свойства водных
растворов СП 40-03 даны в табл. 24.
Суперпластификатор
ДОФЕН
1. СП Дофен по ТУ 14-6-188-86
Минчермета УССР представляет собой добавку на основе продуктов конденсации с
формальдегидом сульфокислот нафталина, его производных и аналогов. При
получении используются моечные растворы (отходы) производства очищенных сортов
нафталина.
2. СП Дофен
поставляется в виде 32 - 40%-ного раствора в цистернах при металлических
бочках. Сухой остаток содержит 50 - 55% т.н. "активного вещества" и
до 18% сульфата натрия.
3. СП Дофен -
жидкость темно-коричневого цвета. Допускается осадок. При температуре ниже +15
°C возможна коагуляция, кристаллизация и выпадение в осадок части продукта. При
температуре -5 °C СП Дофен замерзает. После оттаивания и перемешивания продукт
восстанавливает свои первоначальные свойства.
4. СП Дофен
изготавливается фенольным заводом Минчермета УССР (г. Дзержинск Донецкой
области). Свойства водных растворов СП Дофен даны в табл. 25.
Таблица 25
Концентрация и
плотность водных растворов
суперпластификатора
Дофен (при 20 °C)
───────────────────────┬──────────────────────────┬────────────────────────
Концентрация, % │
Концентрация, г/л │
Плотность, г/см3
───────────────────────┼──────────────────────────┼────────────────────────
0 │ 0 │ 1,0
5 │ 50,8 │ 1,016
10 │ 104,2 │ 1,042
15 │ 160,2 │ 1,068
20 │ 218,4 │ 1,092
25 │ 278,5 │ 1,114
30 │ 343,5 │ 1,145
35 │ 408,8 │ 1,168
40 │ 476,8 │ 1,192
45 │ 548,1 │ 1,218
Приложение
2
МЕТОДИКА
РАСЧЕТА
ЭКОНОМИЧЕСКОЙ ЭФФЕКТИВНОСТИ СУПЕРПЛАСТИФИКАТОРОВ
1. Определение
экономического эффекта основывается на сопоставлении приведенных затрат по
базовому варианту (эталону) и варианту с применением добавок. Приведенные
затраты представляют собой сумму себестоимости и нормативной прибыли:
, (1)
где З - приведенные затраты, руб. на единицу измерения (1 м3
бетона, конструкции);
С - себестоимость
единицы измерения;
К - удельные капитальные вложения в производственные фонды;
- нормативный коэффициент эффективности
капитальных вложений (0,12 - 0,15).
2. При определении
экономического эффекта должна быть обеспечена сопоставимость сравниваемых
вариантов - базового варианта (эталона) и варианта с использованием добавок по
следующим основным показателям:
объему
производства;
показателям
технических свойств материалов, бетонной смеси, бетона, конструкций и т.п.;
социальным и
экологическим факторам.
3. За базу
сравнения (эталон) при определении экономического эффекта от применения добавок
принимаются:
на этапе
формирования планов научно-исследовательских, проектных и
опытно-конструкторских работ, принятия решений об организации производства -
технические показатели лучших добавок, изготавливаемых в СССР
или за рубежом, их стоимость, возможность массового изготовления и
использования добавки, доступность исходного сырья и т.п.;
на этапе формирования
планов внедрения новой техники и технологии, а также при подготовке
использования новых добавок на предприятиях - показатели технологии
изготовления бетонов с заменяемой добавкой (или без добавки, если добавка в
предшествующем году не применялась).
4. При определении
экономической эффективности применения добавок рассматриваются:
а) эффективность
применения добавок на предприятиях сборного железобетона и при возведении
строительных объектов из монолитного бетона и железобетона (хозрасчетный
эффект);
б) эффективность
организации производства и применения добавок на уровне строительных
министерств и ведомств (среднеотраслевая эффективность);
в)
народно-хозяйственная эффективность (с учетом расходов на всех этапах
разработки, создания, освоения производства и применения добавок, а также
эффекта при последующей эксплуатации зданий и сооружений за счет повышения
долговечности конструкций).
5. Расчет годового
экономического эффекта от применения СП на предприятиях стройиндустрии или в
строительных организациях производится по формуле
, (2)
где
и
- себестоимость продукции, изготавливаемой
соответственно без добавок (или по базовому варианту) и с рассматриваемой
добавкой;
и
- соответствующие удельные капиталовложения;
- годовой эффект производства продукции в м3
или других натурных единицах (например, при уменьшении сечения конструкции - в
штуках).
При этом все
показатели рассчитываются по фактическим данным конкретного предприятия или
организации (стоимость материалов, используемого и дополнительного
оборудования, расчетных калькуляций и т.д.).
6. При
реконструкции действующих технологических линий заводов ЖБИ хозрасчетный эффект
для предприятия определяется по формуле
, (3)
где
- дополнительные удельные капитальные
вложения, связанные с организацией применения добавок;
- уменьшение удельных капитальных вложений,
связанное с реализацией высвобождающихся основных фондов (в основном
формовочного, вибрационного и складского оборудования).
7. Если применение
добавки позволяет получить более качественные изделия (повышение классности
изделий, морозостойкости, водонепроницаемости и др.), то экономический эффект
для предприятия определяется по изменению цены на продукцию более высокого
качества по формуле
, (4)
где
и
- оптовые цены соответственно единицы
продукции повышенного качества и базового варианта;
и
- соответствующая себестоимость продукции;
- объем производства изделий повышенного
качества в натуральном выражении.
8. Если в
результате внедрения добавки увеличивается объем выпуска продукции, то в расчет
принимают относительную экономию по условно-постоянным косвенным расходам,
определяемую по калькуляции себестоимости продукции или по следующей
ориентировочной формуле
, (5)
где H - сумма
условно-постоянных расходов в составе расходов по содержанию и эксплуатации
оборудования цеховых и общезаводских расходов и т.д.;
и
- объем выпуска продукции (в м3, м2, шт.) до и после внедрения добавки в бетон.
9. Если применяемая
добавка позволяет сократить продолжительность возведения зданий или сооружений,
снизить трудоемкость производства бетонных и железобетонных работ, то
определяется дополнительная экономия от снижения накладных расходов в
соответствии с "Инструкцией по определению экономической эффективности
капитальных вложений в строительство" СН 509-78 (М., Стройиздат, 1979).
10. При оценке
повышения качества и долговечности конструкций затраты и издержки в процессе
эксплуатации зданий и сооружений за весь срок их службы определяются по
"Руководству по определению экономической эффективности повышения качества
и долговечности строительных конструкций" (М., Стройиздат, 1981).
11.
Народно-хозяйственный эффект определяется по разности общих приведенных затрат
(с учетом сферы эксплуатации зданий и сооружений) по исходному варианту
(эталону) и варианту с применением новой добавки в бетон.
12. При отсутствии
необходимых исходных данных предварительный экономический эффект от повышения
долговечности конструкций может определяться по формуле
, (6)
где
- себестоимость бетона без добавок (или по
базовому варианту с исходным уровнем долговечности);
- откорректированная себестоимость бетона
повышенной стойкости (с повышенным межремонтным сроком службы конструкций);
, (7)
где
- расчетная (плановая) себестоимость бетона
для конструкций повышенной долговечности;
- соотношение фактических и прогнозируемых
сроков службы конструкций без добавок (или по базовому варианту с исходным
уровнем долговечности) и с рассматриваемой добавкой.
13. Стоимость
добавок, цемента, заполнителей, форм и т.д. определяется на основании
действующих прейскурантов оптовых или временных цен. Стоимость доставки
материалов и изделий определяется на основании исходных данных заводов ЖБИ.
14. Удельные
капитальные вложения на строительство и оборудование установок для
приготовления рабочих растворов добавок принимаются на основании фактических
данных.
15. Удельные капитальные
вложения в организацию производства СП ориентировочно принимаются в размере 600
руб./т.
16. Для
предварительных расчетов при определении полной заработной платы рабочих к
тарифной ставке (или сдельной расценке) вводится коэффициент 1,48, учитывающий
дополнительную заработную плату, премии и отчисления на соцстрах.
17. Режимы тепловой обработки изделий с учетом предварительного
выдерживания для базового варианта (эталона) принимаются аналогичными
сложившимся на предприятии до применения СП.
Перечень данных,
необходимых для расчета
экономической
эффективности суперпластификаторов
Исходные данные
устанавливаются на предприятии по каждому основному виду изделия, при
приготовлении которого предполагается применять СП, и по каждой технологической
линии. Если на формовочной линии изготовляется продукция разных видов и
типоразмеров, исходные данные устанавливаются для наиболее массового
типоразмера изделия.
Если одноименная
продукция изготовляется на нескольких одинаковых формовочных линиях, исходные
данные устанавливаются для наиболее характерной линии.
Фактические
показатели действующих линий
1. Вид продукции,
вид и марка бетона, цемента, заполнителей, объем бетона (с выделением наиболее
массового изделия).
2. Технология
(поточно-агрегатная, конвейерная, кассетная, стендовая).
3. Количество линий
в пролете цеха (или сколько кассет, стендов).
4. Фактический ритм
формования (время пребывания формы на посту бетонирования, включая подачу и
съем форм), мин, средняя фактическая оборачиваемость форм (количество полных
оборотов в сутки).
5. Способы
уплотнения бетонной смеси (виброплощадки, вибронасадки, вибраторы и др.).
6. Количество смен
в сутки для предприятия и рассматриваемого цеха (линии).
7. Годовая
фактическая производительность линии.
8. Тип камер
твердения (ямные, щелевые, подземные и т.д.).
9. Фактическая
длительность тепловой обработки, ч (подъем
температуры, изотермическая выдержка, остывание) и температура изотермы.
10. Средний расход
пара для тепловой обработки, кг на 1 м3 бетона, или электроэнергии, кВт-ч/м3.
11. Средняя
оборачиваемость ямных камер в сутки.
12. Количество
камер в работе (для щелевых камер - количество щелей).
13. Единовременная
емкость камер (количество размещаемых в каждой камере форм).
14. Перечень
технологического и транспортного оборудования на формовочной линии, с указанием
веса каждой единицы и балансовой стоимости, в том числе форм.
15. Перечень
оборудования с указанием веса и стоимости каждой единицы на линии отделки.
16. Число рабочих,
обслуживающих формовочную линию за смену, а также линию отделки, в том числе
крановщики и стропальщики (тарифные разряды, профессии рабочих и распределение
по постам).
17. Состав бетонной
смеси, ее удобоукладываемость и подвижность.
18. Применяемая заводом
химическая добавка до использования СП.
19. Удельный расход
силовой электроэнергии на формование, кВт-ч/м3.
20. Заводская
калькуляция на изготовление изделия.
Приложение
3
ПРИМЕРЫ
ЭФФЕКТИВНОГО ИСПОЛЬЗОВАНИЯ СУПЕРПЛАСТИФИКАТОРОВ
Виброгидропрессованные
трубы
Формование
виброгидропрессованных труб с СП рекомендуется производить из бетонной смеси с ОК = 6 - 8 см (вместо 2 - 3 см без добавки). При этом имеют
место следующие показатели эффективности:
сокращение времени
формования на 30 - 40%;
сокращение времени
вибрации на 20 - 30% или уменьшение числа вибраторов на 30%;
сокращение расхода
электроэнергии (сжатого воздуха) на 20 - 30%;
уменьшение износа
технологического оборудования на 20 - 30%;
сокращение
трудозатрат на 5 - 6% (0,7 - 0,9 чел.-ч/м3);
снижение расхода
цемента на 2 - 5%;
снижение расхода
крупного заполнителя на 10 - 15%;
повышение
классности труб на 5 - 15%;
улучшение условий
труда;
снижение
себестоимости изделий на 4 - 6 руб./м3. <*>
--------------------------------
<*> В данном
приложении цифры по снижению себестоимости продукции приведены по отношению к
СП С-3.
Возможное ускорение
оборачиваемости форм и увеличение выпуска продукции дает дополнительный
экономический эффект. Дополнительный эффект от применения СП в виброгидропрессованных
трубах имеет место в сфере эксплуатации трубопровода: за счет снижения
шероховатости внутренней поверхности трубы снижаются затраты электроэнергии на
перекачку воды. В данном случае экономия электроэнергии может быть заменена
снижением материалоемкости за счет уменьшения диаметра трубы на одну ступень
при той же пропускной способности трубопровода.
Высокопрочные
бетоны
Возможно несколько
вариантов применения СП для получения высокопрочных бетонов.
При бетонировании
густоармированных конструкций (типа колонн), изготавливаемых по конвейерной
технологии, применение СП обеспечивает получение следующих эффектов.
Первый вариант:
а) замену цемента
марки 600 на цемент марки 500;
б) сокращение
расхода цемента на 3 - 5%;
в)
увеличение подвижности бетонной смеси в два раза (от 2 - 3 до 4 - 5 см);
г) сокращение
времени уплотнения бетонной смеси и расхода электроэнергии на 20 - 30%;
д) сокращение
трудозатрат на 4 - 5%;
е) уменьшение
износа технологического оборудования;
ж) снижение
температуры изотермического прогрева на 10 - 12 °C;
з) снижение расхода
технологического пара на 15 - 20%;
и)
улучшение условий труда;
к) снижение
себестоимости изделий на 2 - 4 руб./м3.
Второй вариант:
а) снижение расхода
цемента марки 600 на 12 - 15% (100 - 120 кг/м3);
б) эффекты,
перечисленные в пп. "в" - "и" первого варианта;
в) снижение
себестоимости изделий на 2 - 3 руб./м3.
При бетонировании
густоармированных конструкций по конвейерной технологии цикл формования
практически не может быть ускорен при условии сохранения численности бригады по
причине трудоемкости процесса армирования.
Третий
вариант:
При бетонировании
густоармированных тонкостенных конструкций (типа коробчатых настилов),
изготовляемых по стендовой технологии, применение СП дает возможность получить
следующие эффекты:
а) замену цемента
марки 600 на цемент марки 500;
б) увеличение
подвижности бетонной смеси от 5 - 7 см до 20 - 24 см;
в) сокращение
времени уплотнения бетонной смеси и расхода электроэнергии на 60 - 70%;
г) снижение
трудозатрат на формование изделий в 2 - 3 раза;
д) уменьшение
износа технологического оборудования;
е) улучшение
условий труда;
ж) увеличение
выпуска продукции на 40 - 60%;
з) снижение
себестоимости изделий на 4 - 5 руб./м3.
Конвейерная и
поточно-агрегатная технологии
Одним из наиболее
рациональных направлений применения СП в конвейерной и поточно-агрегатной
технологиях является увеличение подвижности бетонной смеси в 2 раза и более
(например, от 7 - 8 см до 14 - 16 см или от 20 - 40 с до 2 - 3 см). При этом
имеет место получение следующих эффектов.
Первый вариант:
сокращение времени
уплотнения бетонной смеси и расхода электроэнергии на 35 - 45%;
снижение трудозатрат
при формовании на 12 - 15%;
уменьшение износа
технологического оборудования;
сокращение
длительности ТВО на 2 - 4 ч;
снижение расхода
технологического пара на 5 - 10%;
снижение
трудозатрат на отделку готовой продукции на 15 - 20% (из высокоподвижных
смесей);
увеличение ритма
работы конвейера на 12 - 15% либо увеличение оборачиваемости форм;
увеличение выпуска
продукции;
улучшение условий
труда;
снижение
себестоимости изделий на 2,5 - 3,5 руб./м3.
Второй вариант
применения СП рекомендован в разделе "Высокопрочные бетоны" (второй
вариант).
Стендовая
технология
Применение
высокоподвижных и литых бетонных смесей с СП в стендовой технологии дает
возможность получения следующих эффектов.
Первый вариант:
разжижение бетонной
смеси, например, от 3 - 4 см до 20 - 22 см;
сокращение времени
бетонирования в 1,5 - 2 раза;
сокращение времени
укладки и расхода электроэнергии в 4 - 5 раз;
сокращение
трудозатрат на 35 - 45%;
уменьшение износа
технологического оборудования;
сокращение времени
изотермического прогрева на 2 - 3 ч с одновременным увеличением на такой же
срок времени предварительной выдержки;
экономия
технологического пара на 10 - 15%;
улучшение условий
труда;
снижение
себестоимости изделий на 1,3 - 2,7 руб./м3.
Возможное
увеличение выпуска продукции на 40 - 60% дает дополнительный экономический
эффект.
Второй вариант:
разжижение бетонной
смеси в 2 - 3 раза (например, от 3 - 4 см до 8 - 10 см);
сокращение времени
бетонирования на 25 - 35%;
сокращение времени
укладки и расхода электроэнергии в 2 - 2,5 раза;
сокращение
трудозатрат на 15 - 25%;
уменьшение износа
технологического оборудования;
сокращение режима
ТВО на 3 - 4 ч;
экономия
технологического пара на 20 - 30%;
увеличение
оборачиваемости форм в 1,2 - 1,3 раза;
увеличение выпуска
продукции на 20 - 30%;
улучшение условий
труда;
снижение
себестоимости продукции на 1,5 - 2,5 руб./м3.
Третий вариант -
изготовление густоармированных конструкций по стендовой технологии - рассмотрен
в главе "Высокопрочные бетоны" (третий вариант).
Кассетная
технология и объемные элементы
При изготовлении
изделий по кассетной технологии целесообразно использовать два направления
применения СП:
одновременное
снижение времени ТВО, температуры изотермического прогрева и частичное снижение
расхода цемента (первый вариант);
максимальное
снижение расхода цемента (второй вариант).
При этом
обеспечивается достижение следующих эффектов.
Первый вариант:
а)
сокращение времени уплотнения бетонной смеси и расхода энергии
в 1,5 раза;
б) сокращение
трудозатрат на 15 - 20%;
в)
уменьшение износа технологического оборудования;
г) сокращение
времени ТВО за счет изотермического прогрева на 1,5 - 2,5 ч;
д) снижение
температуры изотермического прогрева на 15 - 20 °C (до 70 °C);
е) снижение расхода
технологического пара на 25 - 35%;
ж) экономия цемента
на 5 - 8%;
з) увеличение
оборачиваемости форм на 12 - 14%;
и) увеличение
выпуска продукции на 10 - 20%;
к) снижение
себестоимости изделий на 1,5 - 2,0 руб./м3.
Второй вариант:
а) экономия цемента
на 14 - 16% (60 - 90 кг/м3);
б) эффекты,
перечисленные в пп. "а" - "в" первого варианта;
в) снижение
себестоимости изделий на 1,0 - 1,5 руб./м3.
Транспортное
строительство
Рациональные
области и способы применения СП С-3 в конструкциях, предназначенных для
транспортного строительства, даны в табл. 26 и 27.
Таблица 26
Рациональные
области и способы применения бетона
с СП в сборных
железобетонных конструкциях
транспортного
строительства
────────────────┬───────────────────────┬──────────────────────────────────
Подотрасли
│ Виды конструкций │
Способ использования СП
транспортного │ │(по рис. 1) и
достигаемые эффекты
строительства
│
│
────────────────┼───────────────────────┼──────────────────────────────────
1
│ 2 │ 3
────────────────┼───────────────────────┼──────────────────────────────────
Строительство │Балки и блоки пролетных│Способы
2 и 3 с повышением
мостов
и труб │строений │прочности бетона и
экономией тепла
│железнодорожных, │благодаря снижению температуры
или
│автодорожных
и │сокращению длительности
│городских мостов, │изотермического прогрева, со
│включая предварительно
│снижением трудозатрат на
│напряженные │бетонирование вследствие
повышения
│водопропускные трубы. │подвижности бетонной смеси до
│Столбчатые опоры, сваи
│10 - 12 см, с повышением
│ │производительности
линий по
│ │изготовлению
конструкций в
│ │заводских условиях, с повышением
│ │плотности бетона
│ │
Строительство │Конструкции обделки │Способы 2 и 3 с повышением
туннелей
и │туннелей: тюбинги, │водонепроницаемости и прочности
метрополитенов │цельно-секционные │бетона, с сокращением длительности
│обделки, колонны, │изотермического прогрева и
│ригели и др. │экономией тепла, а также
│ │повышением
производительности
│ │линий
│ │
Гидротехническое│Гидротехнические │То же.
строительство │предварительно │Способы 2 и 3 со снижением
│напряженные сваи и │температуры изотермического
│шпунт. Лицевые,
│прогрева и экономией тепла
│фундаментные и
анкерные│
│плиты для
набережных │
│уголкового типа │
│ │
│Оболочки большого │То же.
│диаметра, плиты │Способы 2 и 3 со снижением
│массивов-гигантов │трудозатрат на бетонирование
│ │за счет повышения
подвижности
│ │бетонной смеси
│ │
Строительство │Сборные дорожные плиты │Способы
2 и 3 с повышением
автомобильных
│и плиты ПАГ-14
│прочности бетона, сокращением
дорог
и │ │длительности
тепловлажностной
аэродромов │ │обработки или снижением
│ │температуры
изотермической
│ │выдержки и
экономией тепла, с
│ │повышением
производительности
│ │линий
│ │
Строительство │Колонны и балки, плиты │То же.
гражданских
и │перекрытий и панелей │Способ 3 с экономией цемента
промышленных │ │
зданий │ │
Таблица 27
Рациональные
области и способы применения
монолитного бетона
с добавкой С-3
в транспортном
строительстве
────────────────┬───────────────────────┬──────────────────────────────────
Подотрасли
│ Виды конструкций │
Способ использования СП
транспортного │ │ и достигаемые эффекты
строительства
│
│
────────────────┼───────────────────────┼──────────────────────────────────
1
│ 2
│ 3
────────────────┼───────────────────────┼──────────────────────────────────
Строительство │Буровые сваи │Способ 3 со снижением расхода
мостов
и труб │ │цемента.
│ │Способы 2 и 3 с повышением
│ │плотности и
коррозионной стойкости
│ │бетона
│ │
│Фундаменты на │То
же, а также способ 1
│естественном основании │со снижением трудозатрат
│и ростверки │на бетонирование смесями высокой
│ │подвижности
│ │
│Монолитные опоры и │Способ 1 со снижением трудозатрат
│покрытия проезжей
части│на бетонирование.
│моста, узлы │Способы 2 и 3 с повышением
│омоноличивания,
бетон │прочности бетона в раннем
возрасте
│заполнения сборно- │с
ускорением темпов строительства
│монолитных опор. │и оборачиваемости опалубки, с
│Ремонтные работы │повышением водонепроницаемости
│ │
Строительство │Обделки транспортных │То же
туннелей
и │туннелей и перегонных │
метрополитенов │туннелей метрополитенов│
│ │
Гидротехническое│Густоармированные │То же
строительство │конструкции шлюзов и │
│сухих доков, │
│вагоноопрокидывателей,
│
│паромных переправ │
│ │
Строительство │Однослойные покрытия │Способы 2 и 3 со снижением толщины
автомобильных │автомобильных
дорог и │покрытий, преимущественно
дорог и
│аэродромов и верхний
│аэродромных, за счет повышения
аэродромов │слой аэродромных │прочности бетона до класса B4,8
│покрытий. Ремонтные │и выше.
│работы │Способ 3 с экономией
цемента
│ │
Строительство │Фундаменты под колонны │Способ
1 со снижением трудозатрат
гражданских
и │и
стены зданий и под │на бетонирование.
промышленных
│технологическое
│Способ 3 со снижением расхода
зданий │оборудование, свайные
│цемента.
│ростверки │Способы 2 и 3 с ускорением
│ │строительства
│ │
│Монолитные стены и │То же
│перекрытия зданий, │
│возводимых с │
│использованием │
│скользящей, │
│объемно-переставной и
│
│других типов
опалубки │
Бетон (раствор) для
стыков
Замоноличивание
стыков можно осуществлять мелкозернистым бетоном и раствором. Использование
бетона позволяет получить следующие эффекты:
разжижить бетонную
смесь от 3 - 5 см до 18 - 24 см;
снизить расход воды
на 10 - 20%;
сократить расход
цемента на 20 - 30 кг/м3;
повысить прочность
бетона на 10 - 15%.
Применение
растворов позволяет:
разжижить
растворную смесь от 110 - 120 мм до 180 - 220 мм;
снизить расход воды
на 10 - 12%;
повысить прочность
цементно-песчаного раствора на 10 - 20%.
Применение СП С-3 в
1,5 раза сокращает время замоноличивания стыка при укладке бетона с
вибрированием и в 1,3 раза - при инъецировании раствором при крупности песка не
более 1 мм
.
Ячеистый бетон
Применение
комплексной добавки на основе СП С-3 в ячеистых бетонах позволяет:
а) снизить
водотвердое отношение смеси на 20 - 25%;
б) уменьшить время
выдержки изделий до автоклавной обработки на 1,5 - 2 ч;
в) сократить
продолжительность автоклавной обработки на 1 - 1,5 ч;
г) увеличить выпуск
продукции на 14 - 15%;
д) повысить
прочность бетона на 15 - 20%;
е) повысить
морозостойкость бетона в 2,5 - 3 раза;
ж) повысить модуль
упругости на 14 - 15%.
Ячеистые бетоны,
изготовленные с комплексной добавкой на основе СП С-3, по величине усадочных
деформаций удовлетворяют требованиям ГОСТ 25485-82 и существенно не отличаются
по показателям усадки от ячеистых бетонов без добавок.
Повышение вышеназванных
свойств ячеистого бетона с комплексными добавками на основе СП С-3 создает
предпосылки для снижения плотности ячеистого бетона на 15 - 20% и получения
ячеистого бетона пониженной плотности с заданными физико-механическими
свойствами.
Приложение
4
ПРИМЕРЫ
ПОДБОРА СОСТАВА
ТЯЖЕЛОГО БЕТОНА С
СУПЕРПЛАСТИФИКАТОРАМИ
Пример 1.
Требуется подобрать
состав тяжелого бетона марки M400 с суперпластификатором, формуемого из
бетонной смеси с осадкой конуса 22 - 24 см. Бетонная смесь того же состава без
добавки должна иметь осадку конуса 2 - 4 см. Твердение-термообработка по режиму
3 + 3 + 6 + 2 ч, температура изотермического прогрева - 80 °C. Прочность бетона
после термообработки - 70% от марочной.
Характеристика
используемых материалов:
цемент -
портландский среднеалюминатный M500 (активность 48,5 МПа, НГЦТ - 25%,
);
щебень - гранитный
фракции 5 - 20 мм (
);
песок - речной (
,
).
1. В соответствии с
ГОСТ 27006-86 подбирают состав бетона без добавки, имеющий следующие расходы
материалов, кг/м3:
цемент
....................... 392
песок
........................ 650
щебень .......................
1155
вода
......................... 200
В/Ц = 0,51; r = 0,36; ОК = 3,5 см.
2. Изготавливают
бетон аналогичного состава с 0,5% суперпластификатора (1,96 кг/м3) <*>.
Замеряют осадку конуса бетонной смеси. ОК = 18 см (на
4 - 6 см ниже требуемой).
--------------------------------
<*>
Количество СП дается в пересчете на сухой остаток.
3. Изготовляют
бетон аналогичного состава с 0,6% СП (2,35 кг/м3). Замеряют осадку конуса. Она
составляет более 24 см. Имеет место расслаивание бетонной смеси, водоотделение.
4. С целью
исключения этого явления опробуется один из нижеследующих приемов:
изготавливают бетон
аналогичного состава с 0,55% СП (2,16 кг/м3). Осадка конуса - 23 см;
изготавливают бетон
с 0,6% СП со сниженным В/Ц, равным 0,48. Осадка конуса
- 22 см;
изготавливают бетон
с 0,6% СП (2,35 кг/м3) с измененным соотношением крупного и мелкого
заполнителей (r = 0,38): расход песка - 686 кг/м3, щебня - 1119 кг/м3. Осадка
конуса - 22,5 см.
5. Из выбранного
состава бетонной смеси с СП (ОК = 22 - 24 см) и
состава бетонной смеси без добавки (ОК = 2 - 4 см) изготавливают образцы-кубы,
которые подвергают пропариванию по режиму, принятому на производстве (3 + 3 + 6
+ 2 ч). Температура изотермического прогрева - 80 °C.
6. Пропаренные
бетоны испытывают на прочность при сжатии. Получено, что
бетона без добавки - 33,5 МПа, бетона с СП -
31,2 МПа.
7. С целью
повышения прочности бетона с СП применяют один из следующих приемов:
повторно
изготовленный состав с СП пропаривают по режиму 5 + 3 + 4 + 2 ч;
изготавливают новый
состав бетона с дозировкой СП, превышающей предыдущую на 0,05 - 0,1%, и
соответственно на 5 - 10% снижается водосодержание бетонной смеси (до получения
ОК = 22 - 24 см). Образцы пропаривают по режиму 3 + 3
+ 6 + 2 ч.
8. Состав, имеющий
максимальную прочность (34,1 МПа), считается исходным для применения на производстве.
Пример 2.
Требуется за счет
применения суперпластификатора максимально увеличить прочность тяжелого бетона,
изготовленного из бетонной смеси, имеющей подвижность, равную подвижности
бетонной смеси без добавки (ОК = 2 - 4 см).
Исходные данные -
по примеру 1.
1. В соответствии с
примером 1 подбирают состав бетонной смеси с оптимальной дозировкой СП, имеющий
максимальную подвижность и дающий максимальную прочность бетона. (В данном
случае, если это экономически обосновано, предпочтительнее идти на увеличение
дозировки добавки с одновременным снижением водоцементного отношения).
2. Подобран
следующий состав бетона (расход материалов, кг/м3):
цемент
....................... 394
песок
........................ 653
щебень ....................... 1160
вода
......................... 188
СП
........................... 2,36 (0,6%)
В/Ц = 0,48; ОК = 23 см.
3. По
методике ГОСТ 310.4-76 ориентировочно определяют величину снижения
водопотребности растворной смеси. Она равна 20%.
4.
Изготавливают второй состав бетона, отличающийся от первого сокращенным
на 20% водосодержанием.
При этом, учитывая
фактическое увеличение расхода всех материалов на 1 м3 бетона, ведется
перерасчет его состава при условии сохранения расхода цемента на 1 м3 бетона,
равного расходу, указанному в п. 2 настоящего примера, т.е. - 394 кг/м3. В
результате расчета получен следующий фактический состав бетона (расход
материалов, кг/м3):
цемент
....................... 394
песок
........................ 675
щебень
....................... 1199
вода
......................... 150
СП
........................... 2,36 (0,6%)
В/Ц = 0,38.
Замеряют осадку
конуса. Она равна 6 см.
5.
Дополнительным снижением расхода воды на 2 - 3% (с одновременным перерасчетом
состава бетона) добиваются осадки конуса 2 - 4 см.
6. Изготовленный
бетон с добавкой и бетон без добавки пропаривают по режиму 3 + 3 + 6 + 2 ч.
7. Определяют
прочность пропаренных бетонов: для бетонов без добавки - 34,8 МПа, для бетона с
добавкой - 47,5 МПа.
Данный состав
бетона принимают к производству.
Пример 3.
Определить
возможность сокращения времени термообработки и температуры изотермического
прогрева для бетона с суперпластификатором.
Исходные данные -
по примеру 1.
1. По примеру 2
подбирают состав бетона, изготовленный из бетонной смеси с ОК
= 2 - 4 см и имеющий максимальный прирост прочности по сравнению с эталоном -
12,7 МПа.
2. Делают повторный
замес с СП; образцы пропаривают по режиму 2 + 3 + 4 + 2 ч (сокращают на 1 ч
время предварительной выдержки и на 2 ч время изотермического прогрева).
Температура изотермического прогрева - 80 °C. Прочность бетона после
пропаривания - 38,8 МПа.
3. Делают третий
замес с СП. Образцы пропаривают по режиму 2 + 3 + 4 + 2 ч. Снижают температуру
изотермического прогрева на 10 °C (до 70 °C). Прочность бетона после
пропаривания - 33,1 МПа. Данный режим термообработки считается оптимальным.
Пример 4.
Определить
возможность снижения расхода цемента для бетона с суперпластификатором при
условии сохранения подвижности бетонной смеси и прочности бетона.
Исходные данные -
по примеру 1.
1. По примеру 2
подбирают состав бетона с СП. Прирост прочности по сравнению с эталоном - 12,7
МПа.
2. Изготавливают
еще один состав бетона с сокращенным на 70 кг (по сравнению с составом,
приведенным в пп. 4 и 5 примера 2) расходом цемента. Для сохранения требуемой
подвижности бетонной смеси водоцементное отношение увеличивают на 0,02.
Получают следующий состав бетона (расход материалов, кг/м3):
цемент
....................... 324
песок
........................ 707
щебень
....................... 1257
вода
......................... 130
СП
........................... 1,94 (0,6%)
В/Ц = 0,40.
3. Замеряют осадку
конуса, ОК = 3 - 4 см.
4. Бетон
пропаривают по режиму 3 + 3 + 6 + 2 ч.
5. Определяют
прочность бетона. Она составляет 35,1 МПа. Данный состав бетона принимается к
производству.
Пример 5.
Определить
комплексное воздействие СП на бетонную смесь и бетон.
Исходные данные -
по примеру 1.
1. По примеру 1
подбирают состав бетона с СП.
Получено:
бетонная смесь
разжижается от 2 - 4 до 20 - 22 см;
прочность бетона -
на уровне эталона.
2. Существующая на
заводе технология требует применения бетонной смеси с ОК
= 6 - 8 см. Изготавливают второй состав бетона с СП по аналогии с примером 2
(см. пп. 3 - 5). Пропаривание бетона - по режиму 3 + 3 + 6 + 2 ч. Определяют
прочность бетона. Она равна 45,8 МПа.
3. Изготавливают
бетон такого же состава; режим термообработки сокращается на 2 ч, т.е. образцы
пропаривают по режиму 3 + 3 + 4 + 2 ч. Определяют прочность бетона. Она
составляет 38,1 МПа.
4. Изготавливают
бетон того же состава, пропаривание проводят по сокращенному режиму;
дополнительно на 20 °C снижается температура изотермического прогрева.
Определяют прочность бетона. Она составляет 35,7 МПа.
5. Изготавливают
бетон, в составе которого расход цемента сокращают на 20 кг/м3. Его фактический
состав (расход, кг/м3):
Ц ............................ 374
П
............................ 668
Щ ............................ 1190
В
............................ 150
Д
............................ 2,25 (0,6%)
В/Ц = 0,40.
6. Определяют
прочность бетона. Она составляет 32,1 МПа. Данный состав бетона и режим его
пропаривания принимают к производству.
Приложение
5
ПРИМЕРЫ
ПОДБОРА СОСТАВОВ КОНСТРУКЦИОННОГО БЕТОНА
НА ПОРИСТЫХ
ЗАПОЛНИТЕЛЯХ С СУПЕРПЛАСТИФИКАТОРОМ
Пример 1. Требуется
подобрать состав керамзитобетона марки по прочности М250 (отпускная прочность
80%), со средней плотностью
при осадке конуса 5 - 9 см. Цемент марки 550;
гравий керамзитовый фракции 5 - 10 мм с маркой по насыпной плотности 600, по
прочности - П = 125, плотность зерен керамзита в
цементном тесте
составляет 1,1 кг/л, пустотность - 45%; песок
плотный с водопотребностью
. В
качестве СП применяют добавку С-3 (20%-ный раствор). В соответствии с п. 5.2
настоящих Рекомендаций и по табл. 7 "Руководства по подбору составов
конструктивных легких бетонов на пористых заполнителях" (прил. 2) выбирают
ориентировочные начальные расходы воды
. Для
бетона без добавки СП
, а с
добавкой СП
.
В соответствии с п.
5.22 настоящих Рекомендаций и по табл. 5 - 7 "Руководства" (прил. 2)
с учетом поправок на марку цемента, крупность заполнителя и подвижность находят
расходы цемента для бетона без добавки СП
и с добавкой СП
.
По табл. 8
"Руководства" (прил. 2) находят по интерполяции объемные концентрации
керамзита при найденных расходах цемента, воды и заданных значениях средней
плотности бетона (1600 кг/м3), средней плотности зерен керамзита (1,1 кг/л) и
водопотребности песка (8%);
;
. Оба
значения удовлетворяют требованиям табл. 4 "Руководства"
.
Расход плотного
песка рассчитывают по формуле
.
Общий
ориентировочный расход воды находят по формуле
.
В соответствии с п.
5.23 настоящих Рекомендаций выбирают для опытных замесов дозировку С-3, равную
0,4 и 0,6% массы цемента и с учетом концентрации раствора добавки уменьшают
количество воды в замесах с СП.
Подобранный состав
бетона приведен в табл. 28.
Таблица 28
Составы
легкого бетона с добавкой СП и без нее
───┬──────────────────────────┬─────────┬──────────────────────────────────
N │ Наименование показателя │ Единица │ Номера составов
п/п│
│измерения├──────┬───────┬─────┬──────┬──────
│ │ │ 1
│ 2 │
3 │ 4
│ 5
───┼──────────────────────────┼─────────┼──────┼───────┼─────┼──────┼──────
1 │Расчетный состав бетона │ │ │ │ │ │
│цемент │ кг │ 422
│ 352 │ 352 │ 422 │ 282
│керамзит │ "
│ 380 │
462 │ 462 │ 473 │ 451
│песок │ "
│ 735 │ 733
│ 733 │ 646 │
829
│вода │ л │ 236
│ 194 │ 194 │ 195 │ 195
│добавка │ %
│ - │
0,4 │ 0,6 │ 0,6 │ 0,6
───┼──────────────────────────┼─────────┼──────┼───────┼─────┼──────┼──────
2 │Расходы материалов на 7 л
│ │ │ │ │ │
│цемент │ кг │2,954 │ 2,464
│2,464│2,954 │1,974
│керамзит │ "
│2,660 │ 3,234 │3,234│3,311 │3,157
│песок │ "
│5,145 │ 5,131 │5,131│4,422 │5,803
│вода (расч.) │ л
│1,652 │ 1,308 │1,284│1,277 │1,307
│вода (факт.) │ "
│1,685 │ 1,334 │1,310│1,277 │1,307
│раствор добавки │ "
│ - │ 0,050 │0,074│0,088
│0,058
───┼──────────────────────────┼─────────┼──────┼───────┼─────┼──────┼──────
3 │Осадка конуса │ см │ 7,5
│ 2,5 │ 8,5 │ 9,5 │ 7,5
───┼──────────────────────────┼─────────┼──────┼───────┼─────┼──────┼──────
4 │Плотность бетонной смеси │
кг/м3
│ 1770 │ - │1730 │ 1740 │ 1720
───┼──────────────────────────┼─────────┼──────┼───────┼─────┼──────┼──────
5 │Фактический расход │ │ │ │ │ │
│материалов на 1 м3 бетона
│ │ │ │ │ │
│цемент │ кг │ 421
│ - │ 350 │ 420 │ 273
│керамзит │ "
│ 379 │ -
│ 459 │ 475 │
443
│песок │ "
│ 734 │ -
│ 728 │ 649 │
813
│вода (с учетом
находящейся│ л │ 236
│ - │ 193 │ 196 │ 191
│в растворе СП) │ │ │ │ │ │
───┼──────────────────────────┼─────────┼──────┼───────┼─────┼──────┼──────
6 │Прочность на сжатие │
МПа │ 20,9 │ -
│22,2 │ 26,9 │ 20,7
│после тепловой обработки │ │ │ │ │ │
───┼──────────────────────────┼─────────┼──────┼───────┼─────┼──────┼──────
7 │Плотность бетона в сухом │
кг/м3
│ 1595 │ - │1590 │ 1605 │ 1570
│состоянии │ │ │ │ │ │
Объем опытного
замеса принимают равным 7 л (см. табл. 28), что достаточно для изготовления
шести контрольных образцов размером 10 x 10 x 10 см и определения
удобоукладываемости бетонной смеси.
В соответствии с п.
5.24 настоящих Рекомендаций выполняют замес без добавки СП. Измеряют осадку
конуса. Она оказалась равной 4,5 см. Добавляют 2% воды, вторично перемешивают
смесь и вновь определяют осадку конуса. Она равна 7,5 см. Определяют плотность
бетонной смеси, изготавливают контрольные образцы и рассчитывают фактический
расход материалов с учетом добавленной в замес воды и определенной плотности
смеси (см. табл. 28).
Последовательно
выполняют замесы с выбранными дозировками СП при увеличенном на 2% расходе
воды. При дозировке СП 0,4% (состав N 2) осадка конуса оказалась ниже заданной
(2,5 см). Считают, что состав N 2 не отвечает заданным требованиям, и исключают
его из последующего анализа.
При дозировке 0,6%
- осадка конуса оказалась в требуемых пределах (8,5 см). Для этого замеса
определяют плотность бетонной смеси, рассчитывают фактический расход материалов
и изготавливают образцы.
В соответствии с п.
5.25 настоящих Рекомендаций проводят дополнительно расчеты составов и замесы с
найденной дозировкой добавки (0,6% массы цемента) и расходами цемента +/- 20% от
,
определяя для каждого из них осадку конуса, плотность
бетонной смеси и изготавливая контрольные образцы (см. табл. 28).
Для построенной для
составов N 3 - N 5 зависимости
(рис. 4) определяют расход цемента для
получения требуемой отпускной прочности бетона с добавкой СП - 275 кг/м3. На
этот же график наносится результат, полученный в составе N 1 без СП. Оказалось,
что бетон эталонного состава (Ц = 422 кг/м3) и бетон с
0,6% добавки СП (Ц = 282 кг/м3) имеют практически одинаковую прочность и
плотность. При неизменном расходе цемента (Ц = 420
кг/м3) бетон с добавкой СП имеет большую на 25% прочность, чем бетон без
добавки. При найденных расходах цемента (275 кг/м3) и воды (191 л/м3) по
вышеприведенной методике рассчитывают расходы керамзита и песка в искомом
составе бетона и проводят проверочный замес.
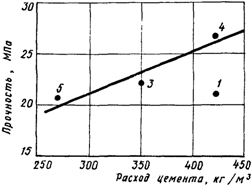
Рис. 4. Зависимость
прочности
керамзитобетона от
расхода цемента
Цифрами на графике
обозначены номера составов (состав N 2 не соответствует требованиям и исключен
из последующего анализа, поэтому точка 2 отсутствует на рисунке).
Пример 2. Требуется
подобрать состав керамзитобетона марки 150 при подвижности бетонной смеси 6 см.
Характеристика
материалов: цемент портландский марки 400; песок керамзитовый с насыпной
плотностью 750 кг/м3; гравий керамзитовый фракций 5 - 10 и 10 - 20 мм с
насыпной плотностью 450 и 435 кг/м3; суперпластификатор С-3 с концентрацией
35%.
За основу при
подборе состава принимают производственный состав на 1 м3 керамзитобетона марки
M150 без добавки СП:
цемент
................................. 380 кг
керамзит
фракции 5 - 10 мм ............. 360 л
То
же, 10 - 20 мм ............ 540
л
керамзитовый песок ..................... 465 л
вода
................................... 250 л
Подбор оптимального
состава бетона с добавкой СП С-3 (табл. 29) начинают с изготовления четырех
серий опытных образцов: без добавки (эталон) и с различным количеством добавки
СП (0,3; 0,45 и 0,6% массы цемента).
Таблица 29
Фактические
составы и прочность керамзитобетона
первой серии
───────┬────────────────────────────────────────────────────────┬──────────
Номер │ Фактический расход материалов на 1 м3
бетона │Прочность,
состава├───────┬─────────────────────────────┬──────────┬───────┤ МПа
│цемент,│ керамзит, л/кг │ С-3 <*> │вода, л│
│
кг
├─────────┬──────────┬────────┤ │ <**> │
│ │5 - 10 мм│10 - 20
мм│0 - 5 мм│
│ │
───────┼───────┼─────────┼──────────┼────────┼──────────┼───────┼──────────
1
│ 376 │ 361/158 │ 531/231 │458/344 │ 0/0
│ 247 │
11,3
2
│ 390 │ 364/164 │ 550/239 │474/366 │ 0,3/1,17 │ 222
│ 12,8
3
│ 381 │ 357/161 │ 539/235 │464/348 │0,45/1,72 │ 208
│ 14,0
4
│ 390 │ 364/164 │ 551/240 │474/356 │0,60/2,34 │ 207
│ 14,5
--------------------------------
<*> Перед
чертой - %, после черты - кг.
<**> Без
учета воды, находящейся в растворе добавки.
За счет снижения
расхода воды в составах бетона с СП добиваются одинаковой по сравнению с
эталоном подвижности бетонной смеси, равной 5 - 7 см. Замеряют плотность
изготовленных бетонных смесей и рассчитывают фактические составы бетонов.
Изготовленные
опытные образцы пропаривают по режиму 3 + 5 + 3 ч и испытывают на сжатие.
Строят график
зависимости прочности керамзитобетона от расхода С-3 (рис. 5).
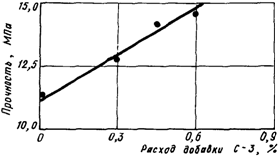
Рис. 5. Зависимость
прочности керамзитобетона
от расхода
суперпластификатора С-3
За оптимальный
принимают состав с расходом С-3, равным 0,45% массы цемента, так как это
количество дало наибольший прирост прочности (14 - 11,3 = 2,7 МПа) на единицу
расхода добавки. По полученным данным определяют возможное снижение расхода
цемента
.
.
Для проверки
состава керамзитобетона с пониженным расходом цемента изготавливают вторую
серию опытных образцов, принимая за исходный состав N 3 по табл. 29. Расход
цемента принимают с учетом возможного его снижения, т.е. 381 - 54 = 327 кг/м3.
Расход крупного заполнителя оставляют тем же, что и в составе N 3, а расход
керамзитового песка увеличивают на 30 л. Из состава изготавливают две серии
образцов. Одну испытывают после пропаривания, другую - после 28 сут твердения пропаренных
образцов в нормальных условиях. Получено: прочность после пропаривания - 11,2
МПа, после 28 сут твердения - 15,9 МПа, что удовлетворяет требованиям.
Приложение
6
ТЕХНИЧЕСКАЯ
ХАРАКТЕРИСТИКА
ВАКУУМ-УСТАНОВКИ "ПОТЕНЦИАЛ-3" ДЛЯ ПРОПИТКИ
ПОРИСТЫХ
ЗАПОЛНИТЕЛЕЙ ВОДОЙ И ВОДНЫМИ РАСТВОРАМИ ДОБАВОК
───────────────────────────────────────────────────┬───────────┬───────────
Характеристика │ Единица
│Показатели
│
изменения │
───────────────────────────────────────────────────┼───────────┼───────────
Производительность │ м3/ч
│ 12
Максимальное
разряжение в вакуум-камере │
МПа │ 0,09
Полезная
вместимость вакуум-камеры
│ м3 │
1,5
То
же, бака для дозирования воды и растворов
│ м3 │
1
добавок
│ │
Система
управления │ Пневмо-электрическая
Установочная
мощность
│ кВт │
15
Габаритные
размеры:
│ │
длина
│ мм │
3500
ширина
│ мм │
3260
высота
│ мм │
5000
Масса
установки без загрузки пористых заполнителей │ кг │
3440
Приложение
7
штамп предприятия, НИИЖБ Госстроя
СССР
ведомственная принадлежность, ОНТИ
адрес, реквизиты 109389,
Москва,
" ___ " ___________ 198_ г. 2-я Институтская,
6
СПРАВКА
об
использовании научно-технического достижения (НТД)
по
"Рекомендациям по применению добавок суперпластификаторов
в
производстве сборного и монолитного железобетона"
1. Наименование НТД
_______________________________________________________
(указать
вид продукции, технологический процесс
___________________________________________________________________________
или проект с использованием НТД)
2. Название объекта
_______________________________________________________
(указывается
стройка, предприятие, где применены
___________________________________________________________________________
конструкции, технология или проект с использованием НТД)
3. Реквизиты договора о сотрудничестве с НИИЖБ (если
имеются)
___________________________________________________________________________
4. Применение НТД по сравнению с
__________________________________________
(указать аналог)
позволило
снизить на единицу продукции (объекта):
сметную стоимость
руб., %
затраты труда
чел.-дн., %
расход: бетона м3, %
цемента кг, %
металла кг, %
энергии кг усл. топл., %
5. Годовой объем производства (использования)
продукции ___________________
6. Годовой эффект по приведенным затратам
_________________________________
(тыс. руб.)
7. Планируемый объем на _______________________ год
(период)
Руководитель организации
Примечание. Справка
не предполагает каких-либо финансовых отношений с НИИЖБ и не является
основанием для получения вознаграждения авторами Рекомендаций.