Утверждено
Приказом института
ВНИИжелезобетон
от 8 июля 1986 г. N
54
ПОСОБИЕ
ПО ТЕПЛОВОЙ ОБРАБОТКЕ СБОРНЫХ ЖЕЛЕЗОБЕТОННЫХ
КОНСТРУКЦИЙ И ИЗДЕЛИЙ
(К СНиП 3.09.01-85)
Рекомендовано к
изданию научно-техническим советом ВНИИжелезобетона Госстроя СССР.
Содержит основные
сведения по назначению режимов тепловой обработки сборных конструкций из
тяжелого и легкого бетонов в различных тепловых установках, данные по контролю
процесса тепловой обработки и качества бетона. Приведена методика расхода
теплоэнергии при рекомендуемых режимах тепловой обработки бетона.
Для
инженерно-технических работников заводов железобетонных изделий, проектных и
строительных организаций.
ПРЕДИСЛОВИЕ
Пособие разработано
к СНиП 3.09.01-85 "Производство сборных железобетонных конструкций и
изделий".
Пособие содержит
указания по тепловой обработке изделий из тяжелых и легких бетонов,
направленные на снижение энергоемкости этого технологического процесса при
производстве сборных железобетонных изделий и конструкций.
Даны классификация
цементов по их реакции на тепловое воздействие и рекомендации по режимам
тепловой обработки изделий из тяжелого и легкого бетонов в различных тепловых
установках (в камерах пропаривания, кассетах, термоформах).
Приведена методика
расчета и назначения энергосберегающих термосных режимов тепловой обработки
бетона. Дан метод расчета расхода тепловой энергии при этих режимах.
Рассмотрены
особенности тепловой обработки изделий из бетонов с химическими добавками, а
также с повышенными требованиями по морозостойкости и предварительно напряженных
конструкций. Пособие содержит сведения по контролю процесса тепловой обработки
и качеству бетона.
Пособие разработано
ВНИИжелезобетон Госстроя СССР (кандидаты техн. наук Р.В. Вегенер, Г.А.
Объещенко, С.Е. Ленский, Э.А. Соколова, С.М. Трембицкий, В.Г. Довжик, инженеры
В.П. Иванов, Б.Д. Дребский, Б.А. Верскайн, М.Г. Парфилова, С.Ю. Артемьев); НИИЖБ Госстроя СССР (доктора техн. наук Б.А. Крылов, Л.А. Малинина,
С.А. Миронов, Н.А. Маркаров, кандидаты техн. наук А.И. Ли, Е.Н. Малинский, Н.Н.
Куприянов, М.И. Бруссер, А.В. Лагойда, инж. Н.А.
Королева); НИИСФ Госстроя СССР (д-р техн. наук С.В. Александровский, канд.
техн. наук В.И. Лукьянов); ВНИПИТеплопроект Минмонтажспецстроя СССР (д-р техн.
наук И.Б. Заседателев, канд. техн. наук С.А. Шифрин); ВТУ Металлургического
комбината - г. Темиртау (инж. Д.С. Грейль); ЛИИЖТ МПС СССР (д-р техн.
наук П.Г. Комохов, канд. техн. наук Т.М. Петрова); ЛПИ им. Калинина Минвуза
РСФСР (д-р техн. наук А.А. Парийский, канд. техн. наук Л.И. Чумадова); ВЗИСИ
Минвуза РСФСР (д-р техн. наук А.Н. Счастный, инж. М.М.
Палеес); КТБ Мосоргстройматериалы Главмоспромстройматериалов (канд. техн. наук
Л.Н. Беккер).
1. ОБЩИЕ
ПОЛОЖЕНИЯ
1.1. Настоящее
Пособие распространяется на заводы, полигоны и отдельные цеха в составе
комбинатов стройиндустрии, изготовляющих строительные конструкции и изделия из
бетонов на плотных и пористых заполнителях и вяжущем на основе
портландцементного клинкера.
Примечание. Пособие
не распространяется на тепловую обработку изделий и конструкций из специальных
бетонов (ячеистых, автоклавного твердения, жаростойких, на напрягающих цементах
и др.), а также бетонов, изготовленных с применением специальных методов
уплотнения бетонной смеси (прессование, вибропрессование, центрифугирование и
т.д.) или предназначенных для эксплуатации в химически агрессивных водных и
газовых средах.
1.2. Тепловая
обработка сборных бетонных и железобетонных конструкций и изделий производится
с применением режимов, обеспечивающих минимальный расход
топливно-энергетических ресурсов и ускоренное достижение бетоном заданных
значений распалубочной, отпускной, передаточной (для предварительно напряженных
конструкций) или проектной прочности.
1.3. Под
распалубочной прочностью бетона понимается такая его прочность на сжатие, при
которой обеспечиваются распалубка (выемка из форм) и безопасное внутрицеховое
(внутризаводское) транспортирование изделий без их повреждения.
Значение
распалубочной прочности устанавливается технологическими правилами производства
для каждого вида изделия предприятием-изготовителем. При этом должны быть
обеспечены соответствующие температурно-влажностные условия для достижения при
последующем складировании и хранении отпускной прочности к моменту отгрузки
изделий с предприятия-изготовителя и проектной прочности в установленные сроки.
1.4. Отпускная и
передаточная прочности бетона должны соответствовать значениям, указанным в
проектной документации, ГОСТах или Технических условиях на данное изделие с
учетом требований ГОСТ 13015.0-83* (изменение N 1).
1.5. Проектная
прочность (класс или марка) бетона указывается в проектной документации, ГОСТах
или Технических условиях на данное изделие, и ее достижение должно быть
гарантировано предприятием-изготовителем в 28-суточном возрасте или в любой
другой срок, согласованный с проектной организацией - разработчиком изделия и
заказчиком-потребителем.
1.6. Проектирование
составов бетонных смесей для изделий, подвергаемых тепловой обработке, должно
производиться любыми известными способами, обеспечивающими достижение бетоном
на используемых материалах отпускной и проектной прочности в установленные
сроки при наименьшем расходе цемента. При этом не допускается увеличение
расхода цемента для достижения требуемой прочности в более короткие сроки по
сравнению с необходимым расходом для получения заданного класса (марки) по
прочности бетона, установленным при подборах состава, за исключением случаев,
предусмотренных СНиП 5.01.23-83, а также с целью экономии
топливно-энергетических ресурсов.
1.7. Тепловая
обработка сборных железобетонных конструкций и изделий может осуществляться в
камерах периодического или непрерывного действия, в специальных термоформах,
термопакетах и кассетных формах, а также под переносными колпаками. При этом в
качестве теплоносителя (источника тепловой энергии) могут использоваться водяной
пар, паровоздушная смесь, горячий воздух, электрический ток, солнечная энергия,
продукты сгорания природного газа.
1.8. Способы,
установки и общую продолжительность тепловой обработки следует выбирать на
основе технико-экономического анализа в зависимости от технологической схемы
производства, конструктивных особенностей изделий, тепловой инерционности
установок и фактических ритмов их работы, требуемой продолжительности
производственного цикла изготовления изделий, режима работы предприятия, а
также климатических факторов (для полигонов).
1.9. Режим тепловой
обработки должен подбираться в каждом конкретном случае экспериментально и
назначаться лабораторией с учетом фактического ритма работы тепловых установок
и указаний разд. 3 и 4 настоящего Пособия.
1.10. В целях
снижения расхода тепловой (электрической) энергии следует максимально
использовать возможности:
тепловой
инерционности установок и осуществления за счет этого термосного выдерживания
разогретых изделий;
учета набора
прочности в период межсменных перерывов, включая выходные и праздничные дни, и
снижения за счет этого максимальной температуры разогрева изделий;
учета набора
прочности бетона, в том числе после распалубки изделий, при выдерживании в цехе
на специальных площадках или в камерах "дозревания", а также в период
хранения на складах;
применения цементов
с более высоким показателем активности при пропаривании, а также
быстротвердеющих цементов;
применения
химических добавок, интенсифицирующих твердение бетона при тепловом
воздействии.
1.11. Сокращение
при необходимости длительности тепловой обработки с целью увеличения
оборачиваемости форм или тепловых агрегатов следует осуществлять за счет
применения быстротвердеющих цементов, химических добавок - ускорителей
твердения, предварительного электро- и пароразогрева
бетонных смесей, двухстадийной тепловой обработки с выдерживанием на второй
стадии форм с изделиями или распалубленных изделий в специальных камерах
"дозревания" и других технологических приемов, не приводящих к
увеличению расхода цемента и тепловой (электрической) энергии.
1.12. С целью обеспечения расхода тепловой энергии при тепловой обработке
в соответствии с Временными нормами для расчета расхода тепловой энергии при
тепловлажностной обработке сборных бетонных и железобетонных изделий в
заводских условиях (СН 513-79. М.: Стройиздат, 1980)
необходимо наладить оперативный учет расхода энергии, увеличить коэффициент
заполнения тепловых установок и осуществить мероприятия по максимальному
снижению непроизводительных энергозатрат (теплопотерь в окружающую среду, в том
числе при транспортировании теплоносителя, на нагрев форм, тепловых агрегатов и
др.).
1.13. При
строительстве новых и реконструкции действующих установок для тепловой
обработки бетона следует предусматривать специальные меры по экономному
расходованию тепловой энергии и устранению ее потерь за счет:
теплоизоляции
ограждений камер, элементов термоформ и кассетных установок;
изготовления
ограждающих конструкций из легкого бетона;
надежного
уплотнения торцевых проемов в туннельных и щелевых камерах и т.п.
Примечание.
Технические решения по повышению эффективности пропарочных камер приведены в
Рекомендациях по снижению расхода тепловой энергии в камерах для
тепловлажностной обработки железобетонных изделий (М.: Стройиздат, 1984) и в
типовом проекте 409-28-40 "Камеры периодического действия для тепловой
обработки изделий из тяжелого и легкого бетона".
1.14. При проектировании новых и реконструируемых технологических линий и
заводов сборного железобетона необходимо предусматривать дополнительные площади
в цехе выдерживания изделий (в формах или без них), камеры
"дозревания", утепленные склады для зимних условий, особенно в
районах Крайнего Севера, Сибири и Дальнего Востока, технические решения по
утилизации отработанного тепла из камер и др. Это позволит при некотором
увеличении первоначальных капитальных вложений сократить удельные
энергозатраты на тепловую обработку изделий, повысить оборачиваемость
формовочной оснастки и тепловых агрегатов и тем самым снизить эксплуатационные
расходы.
2. ЦЕМЕНТЫ
ДЛЯ БЕТОНОВ, ПОДВЕРГАЕМЫХ ТЕПЛОВОЙ ОБРАБОТКЕ
2.1. Для
производства бетонных и железобетонных изделий, подвергаемых тепловой
обработке, могут быть использованы портландцементы, быстротвердеющие цементы,
шлакопортландцементы, соответствующие требованиям ГОСТ 10178-85.
Сульфатостойкие и пуццолановые портландцементы следует применять только в
случаях, указанных в ГОСТ 22266-76*.
2.2. Одним из
основных показателей качества цемента для бетонов, подвергаемых тепловой
обработке, является активность его при пропаривании, определяемая по ГОСТ
310.4-81*.
Активность цемента
при пропаривании, характеризующая интенсивность твердения бетона на этом
цементе в условиях теплового воздействия, является не нормируемой, а
информационной характеристикой, численное значение которой для цементов
конкретного завода-изготовителя достаточно стабильно. Она должна учитываться
при назначении составов бетона и режимов тепловой обработки.
2.3. Учет
активности цемента при пропаривании позволяет предприятиям строительной
индустрии оптимизировать составы бетона по расходу цемента и режимы тепловой
обработки - по продолжительности и удельному расходу энергоресурсов.
2.4. В целях учета
активности цемента при пропаривании следует определять значение коэффициента
его эффективности при тепловой обработке,
:
,
где
- активность цемента при пропаривании по ГОСТ
310.4-81*;
-
активность цемента при нормальном твердении в возрасте 28 сут по ГОСТ
310.4-81*.
При экспрессном
определении коэффициента эффективности за величину
следует принимать гарантированную марку
цемента, указанную в паспорте.
2.5. В зависимости
от значения
цементы всех заводов подразделяются на три
группы согласно табл. 1.
Таблица 1
──────────────────────┬───────────────────────────┬────────────────────────
Группа цемента │ Цемент │ K
│ │ п
──────────────────────┼───────────────────────────┼────────────────────────
I │Высокоэффективный │0,68 и более
II │Среднеэффективный │0,57 - 0,67
III │Низкоэффективный │0,56 и менее
В
Прил. 1 приведены группы эффективности для цементов различных
заводов-изготовителей.
2.6.
Цементы I группы характеризуются высоким темпом набора прочности и
обеспечивают, как правило, получение 70%-ной прочности в зависимости от класса
(марки) бетона при режимах тепловой обработки с общей продолжительностью менее
15 ч.
2.7. Цементы II
группы характеризуются средним темпом набора прочности и обеспечивают получение
70%-ной прочности бетона при более длительных режимах тепловой обработки.
2.8. Цементы III
группы характеризуются низким темпом набора прочности. Применение этих цементов
для производства сборных изделий из бетонов класса B15 (M200) и B22,5 (M300),
подвергаемых тепловой обработке, требует увеличения расхода цемента.
2.9. Распределение
цементов по группам эффективности при тепловой обработке и их характеристики,
изложенные в пп. 2.6 - 2.8, распространяются как на портландцементы, так и на
шлакопортландцементы, но при применении последних получение 70% прочности
достигается при температурах 90 - 95 °C и длительности прогрева на 30% большей,
чем при применении равномарочных портландцементов.
2.10. При
использовании шлакопортландцемента в условиях тепловлажностной обработки
следует иметь в виду, что для обеспечения последующего роста прочности
необходима среда с высокой относительной влажностью. В воздушно-сухих условиях
рост прочности бетонов на шлакопортландцементах значительно замедляется.
2.11. Применение
пуццолановых портландцементов вследствие повышенной водопотребности бетонной
смеси приводит к увеличению расхода цемента (при получении равнопрочных
бетонов), повышению усадочных деформаций и понижению морозостойкости бетона.
Прочность бетонов на таких цементах при последующем твердении в воздушно-сухих
условиях практически не увеличивается.
Поэтому
пуццолановые портландцементы и их разновидности при тепловлажностной обработке
могут применяться только для изделий спецназначения с повышенными требованиями
по водостойкости и солестойкости.
2.12. Применение
пластифицированных цементов позволяет уменьшить водопотребность бетонной смеси.
Однако вследствие замедления сроков схватывания и начального твердения, а также
дополнительного воздухововлечения тепловлажностную обработку бетонов на таких
цементах следует осуществлять по режимам с более длительным предварительным
выдерживанием (не менее 4 - 6 ч), с замедленной скоростью подъема температуры
либо производить тепловую обработку под пригрузом или в напорных пропарочных
камерах.
2.13. Применение
глиноземистого цемента при тепловлажностной обработке изделий не допускается.
3. ТЕПЛОВАЯ ОБРАБОТКА ИЗДЕЛИЙ ИЗ ТЯЖЕЛЫХ БЕТОНОВ
Пропаривание
изделий в камерах периодического действия
3.1. При тепловой
обработке бетона в камерах периодического действия (ямных и тупиковых
туннельных камерах) прогрев изделий осуществляется при непосредственном их
контакте с теплоносителем или кондуктивным способом.
3.2. В качестве
теплоносителей в этих камерах могут применяться насыщенный водяной пар,
паровоздушная смесь, аэрированная горячая вода, продукты сгорания природного
газа.
Во избежание
значительных влагопотерь при тепловой обработке изделий предпочтительным
является использование в качестве теплоносителя насыщенного водяного пара. При
использовании других теплоносителей и источников тепловой энергии (продуктов
сгорания природного газа, электрообогрева, индукционного нагрева и т.п.),
имеющих более высокую температуру, чем бетон изделий, может происходить
интенсивное испарение влаги из бетона, приводящее к нарушению формирующейся
структуры. Интенсивность испарения влаги зависит от режима тепловой обработки,
водосодержания бетона, относительной влажности среды и скорости ее циркуляции. При значительных влагопотерях
помимо нарушения структуры в процессе тепловой обработки наблюдается замедление
процессов гидратации цемента в последующее время и как следствие недобор
проектной прочности бетона. В этом случае обязательным является обеспечение
влажности среды не менее 90 - 100% или защита открытых поверхностей изделий
влагонепроницаемыми материалами или пленкообразующими составами. В период
подъема температуры допускается снижение относительной влажности среды до 40 -
60%.
3.3. Структура режима тепловой обработки характеризуется длительностью
предварительного выдерживания, температурой и скоростью разогрева,
продолжительностью и способом (термосным или изотермическим) выдерживания
разогретых изделий и выражается как сумма времени отдельных ее периодов в часах,
например, 2 + 3 + 6 + 2 = 13, где 2 - время предварительного выдерживания; 3 -
время разогрева до заданной температуры; 6 - время выдерживания в термосных или
изотермических условиях; 2 - время остывания до
распалубки (для случая с выдерживанием в изотермических условиях); 13 - общая
продолжительность тепловой обработки).
Назначение режимов
тепловой обработки заключается в установлении оптимальной продолжительности
отдельных его периодов с целью обеспечения фактических ритмов работы тепловых
установок и получения требуемой прочности без ухудшения конечных
физико-механических свойств бетона.
3.4. Основным
назначением предварительного выдерживания изделий, отсчитываемого от момента
закрытия крышкой загруженной камеры до начала тепловой обработки, является создание
благоприятных условий для протекания процессов гидратации цементов и
формирования начальной структуры бетона, способной без нарушения воспринять
развивающиеся при последующем тепловом воздействии деструктивные процессы.
Вследствие влияния
многочисленных факторов на темп начального твердения бетона (активности
цемента, В/Ц бетона, скорости подъема температуры,
температурного уровня разогрева бетона и др.) длительность предварительного
выдерживания, необходимая для достижения бетоном требуемой начальной прочности,
не является величиной постоянной и колеблется от 1 - 2 до 4 - 8 ч.
Чем выше марка
цемента и класс бетона, жесткость бетонной смеси, а также температура, при
которой происходит предварительное выдерживание изделий, тем меньше может быть
длительность предварительного выдерживания. Введение химических добавок
(ускорителей твердения) приводит к сокращению, а поверхностно-активных добавок
- к удлинению оптимальной длительности предварительного выдерживания.
Увеличение
длительности предварительного выдерживания особенно целесообразно при
пропаривании распалубленных изделий, а также изделий с большими открытыми
поверхностями.
С целью снижения
энергоемкости процесса тепловой обработки при загрузке изделий в остывшие
камеры рекомендуется повысить температуру среды до 40 - 45 °C путем
кратковременной подачи пара. При этом струи пара не должны быть направлены на
поверхность свежеотформованных изделий.
Примечание.
Предварительное выдерживание изделий не предусматривается при тепловой
обработке изделий в малонапорных камерах, при использовании разогретых бетонных
смесей, а также при изготовлении изделий из жестких бетонных смесей с
дисперсным армированием.
3.5. Скорость
нагрева оказывает наибольшее влияние на развитие деструктивных процессов в
твердеющем бетоне, причем чем выше она, тем больше
вероятность возникновения структурных нарушений. Поэтому для исключения
излишних дефектов скорость нагрева бетона на поверхности изделий не должна
превышать 20 °C/ч. Исходя из этого условия следует
назначать скорость подъема температуры среды в камере.
Скорость подъема
температуры при пропаривании в зависимости от значения начальной прочности,
достигнутой в период предварительного выдерживания, может ориентировочно
приниматься по табл. 2.
Таблица 2
────────────────────────────────────┬──────────────────────────────────────
Начальная прочность бетона │
Скорость подъема температуры среды
при сжатии, МПа │ камеры, °C/ч
────────────────────────────────────┼──────────────────────────────────────
0,1 - 0,2 │ 10 - 15
0,2 - 0,4 │ 15 - 25
0,4 - 0,5 │ 25 - 35
0,5 - 0,6 │ 35 - 45
Более 0,6 │ 45 - 60
Примечание.
Определение начальной прочности бетона производится на образцах с ребром не
менее 10 см при испытании их на прессах мощностью не более 25 кН.
Повышение
температуры среды камеры со скоростью более 60 °C/ч, независимо от начальной
прочности бетона, не рекомендуется.
3.6. Ввиду
конвективно-кондуктивного характера теплопередачи при нагреве изделий в камерах
скорость подъема температуры оказывает существенное влияние на однородность
формирующегося температурного поля. С увеличением толщины изделия увеличивается
температурный перепад между центром и поверхностью бетона, что ведет к
неравномерному росту прочности. Поэтому при толщине изделий 40 см и более
скорость нагрева бетона на поверхности должна быть снижена до 10 - 15 °C/ч.
3.7. При
изготовлении изделий из высокоподвижных бетонных смесей (с осадкой конуса 8 см
и более) скорость подъема температуры должна быть снижена на 20 - 30%. При
использовании жестких смесей (с жесткостью 60 с и более) нагрев
может осуществляться с большей скоростью (на 15 - 20%).
3.8. В целях снижения деструктивного воздействия интенсивности нагрева
на формирующуюся структуру бетона, особенно при коротких периодах
предварительного выдерживания, допускается осуществлять подъем температуры с
прогрессивно возрастающей скоростью, при которой учитывается нарастание
прочности бетона в процессе подъема температуры, например, в первый час
скорость подъема температуры среды в камере принимается 10 - 15 °C/ч, во второй
- 15 - 25 °C/ч, в третий - 25 - 30 °C/ч и т.д. до достижения заданной
максимальной температуры.
3.9. Снижению структурных нарушений в бетоне способствует использование
ступенчатых режимов нагрева, когда, например, за первые 1 - 1,5 ч повышают
температуру в камере до 40 - 50 °C, выдерживают изделия при этой температуре
без подачи пара в течение 1 - 2 ч, а затем осуществляют интенсивный подъем
температуры до максимального заданного значения в течение 1 - 1,5 ч.
При загрузке
изделий в неохлажденную камеру с температурой 30 - 45 °C выдерживание в ней в
течение 1,5 - 2 ч равноценно первой ступени подъема температуры.
3.10. Максимально
допустимая температура бетона к концу периода нагрева не должна превышать 80 -
85 °C при использовании портландцементов (в том числе с минеральными добавками)
и 90 - 95 °C при использовании шлакопортландцементов.
Применение
пониженных температур разогрева, обеспечивающих достижение заданной прочности
бетона в требуемые сроки, позволяет снизить расход энергии в 1,5 - 2 раза по
сравнению с расходом при 80 - 85 °C.
3.11.
Выдерживание разогретых изделий в камерах до достижения заданной прочности
может осуществляться путем термосного или изотермического прогрева. С точки
зрения достижения минимальных энергозатрат на тепловую
обработку предпочтительным является использование термосного выдерживания.
Изотермический
прогрев должен приниматься в том случае, если термосное выдерживание в камере
не обеспечивает достижения заданной прочности к моменту распалубки. При
использовании изотермического прогрева необходимо до минимума сократить его
продолжительность с последующим термосным выдерживанием.
3.12.
Изотермический прогрев осуществляется путем подвода тепловой энергии в
количестве, компенсирующем затраты на нагрев ограждений камеры и потери через
них. Режимы тепловой обработки изделий из тяжелого бетона с изотермической
выдержкой при 80 °C для двух оборотов тепловых установок в сутки приведены в
табл. 3.
Таблица 3
───────────────┬───────────────────────────────────────────────────────────
Класс (марка) │ Режимы тепловой обработки, ч, при толщине бетона
бетона
│ в
изделиях, мм
├───────────────────┬───────────────────┬───────────────────
│ до 100 │ 100 - 300 │
300 - 400
───────────────┼───────────────────┼───────────────────┼───────────────────
B15
(200) │11 (3,5 + 5,5 + 2)
│12 (3,5 + 6,5 + 2) │13 (3,5 + 6,5 + 3)
───────────────┼───────────────────┼───────────────────┼───────────────────
B22,5
(300) │ 9 (3 + 4 + 2) │
10 (3 + 5 + 2) │11 (3 +
5,5 + 2,5)
───────────────┼───────────────────┼───────────────────┼───────────────────
B30
(400) │ 8,5 (3 + 3,5 + 2)
│ 9,5 (3 + 4,5 + 2) │10,5 (3 + 5 + 2,5)
───────────────┼───────────────────┼───────────────────┼───────────────────
B37,5
(500) │ 8 (3 + 3 + 2) │
9 (3 + 4 + 2) │ 10 (3 + 4
+ 2,5)
───────────────┼───────────────────┼───────────────────┼───────────────────
B45
(600) │ 7 (3 + 2 + 2) │
8 (3 + 3 + 2) │ 9 (3 + 3,5
+ 2,5)
Примечание. Режимы
тепловой обработки включают время подъема температуры среды в тепловом
агрегате, изотермического выдерживания и остывания без подачи пара.
3.13. Термосное
выдерживание разогретых изделий в камерах осуществляется без дополнительного
подвода тепла.
3.14. При термосном
выдерживании температура бетона изделий принимается согласно данным табл. 4 в
зависимости от группы цемента, класса бетона, требуемой оборачиваемости камер в
сутки n, заданной прочности бетона изделий (% от
) к концу термосного цикла, а также показателя A,
характеризующего длительность остывания разогретого блока камер с изделиями
(т.е. его тепловую инерцию).
Таблица 4
───────────────┬─────────────┬─────────────────────────────────────────────
Класс (марка) │ Заданная
│ Температура разогрева
бетона, °C,
бетона
│ прочность, │ при значениях показателя A
│ % от R
├──────────────┬───────────────┬──────────────
│ 28
│ 10 - 40 │
41 - 80 │ 81 - 150
───────────────┴─────────────┴──────────────┴───────────────┴──────────────
I группа цементов при оборачиваемости
камер в сутки n = 1
B15
(200) │ 50
│ 60 │ 55
│ 50
│ 60
│ 75 │ 70
│ 65
│ 70
│ - │ -
│ 80
───────────────┼─────────────┼──────────────┼───────────────┼──────────────
B22,5
(300) │ 50
│ 50 │ 45
│ 40
│ 60
│ 65 │ 60
│ 55
│ 70
│ 80 │ 75
│ 70
───────────────┼─────────────┼──────────────┼───────────────┼──────────────
B30
(400) │ 50
│ 40 │ 35
│ 30
│ 60
│ 50 │ 45
│ 40
│ 70
│ 65 │ 60
│ 55
───────────────┼─────────────┼──────────────┼───────────────┼──────────────
B37,5
(500) │ 50
│ 35 │ 30
│ 25
│ 60
│ 45 │ 40
│ 35
│ 70
│ 55 │ 50
│ 45
II группа цементов при оборачиваемости
камер в сутки n = 1
B15
(200) │ 50
│ 75 │ 70
│ 60
│ 60
│ - │ 80
│ 70
───────────────┼─────────────┼──────────────┼───────────────┼──────────────
B22,5
(300) │ 50
│ 60 │ 55
│ 45
│ 60
│ 75 │ 70
│ 65
│ 70
│ - │ 85
│ 80
───────────────┼─────────────┼──────────────┼───────────────┼──────────────
B30
(400) │ 50
│ 45 │ 50
│ 40
│ 60
│ 60 │ 55
│ 50
│ 70
│ 80 │ 75
│ 70
───────────────┼─────────────┼──────────────┼───────────────┼──────────────
B37,5
(500) │ 50
│ 40 │ 35
│ 30
│ 60
│ 50 │ 45
│ 40
│ 70
│ 70
│ 65 │ 60
III группа цементов при оборачиваемости
камер в сутки n = 1
B15
(200) │ 50
│ 85 │ 75
│ 65
│ 60
│ - │ -
│ 80
───────────────┼─────────────┼──────────────┼───────────────┼──────────────
B22,5
(300) │ 50
│ 75 │ 70
│ 65
│ 60
│ - │ 80
│ 75
───────────────┼─────────────┼──────────────┼───────────────┼──────────────
B30
(400) │ 50
│ 65 │ 60
│ 50
│ 60
│ 80 │ 70
│ 60
│ 70
│ - │ 80
│ 75
───────────────┼─────────────┼──────────────┼───────────────┼──────────────
B37,5
(500) │ 50
│ 55 │ 50
│ 40
│ 60
│ 70 │ 60
│ 50
│ 70
│ 80 │ 75 │ 65
I группа цементов при оборачиваемости
камер в сутки n = 1,5
B15
(200) │ 50
│ 75 │ 70
│ 70
│ 60
│ - │ 85
│ 80
───────────────┼─────────────┼──────────────┼───────────────┼──────────────
B22,5
(300) │ 50
│ 70 │ 65
│ 60
│ 60
│ 80 │ 75
│ 75
───────────────┼─────────────┼──────────────┼───────────────┼──────────────
B30
(400) │ 50
│ 60 │ 55
│ 50
│ 60
│ 75 │ 70
│ 70
───────────────┼─────────────┼──────────────┼───────────────┼──────────────
B37,5
(500) │ 50
│ 45
│ 40 │ 40
│ 60
│ 60 │ 55
│ 50
│ 70
│ 80 │ 75
│ 70
II группа цементов при оборачиваемости
камер в сутки n = 1,5
B15
(200) │ 50
│ 85 │ 80
│ 75
───────────────┼─────────────┼──────────────┼───────────────┼──────────────
B22,5
(300) │ 50
│ 80 │ 75
│ 70
│ 60
│ - │ -
│ 85
───────────────┼─────────────┼──────────────┼───────────────┼──────────────
B30
(400) │ 50
│ 70 │ 65
│ 65
│ 60
│ 85 │ 80
│ 75
───────────────┼─────────────┼──────────────┼───────────────┼──────────────
B37,5
(500) │ 50
│ 50 │ 45
│ 45
│ 60
│ 70 │ 65
│ 60
III группа цементов при оборачиваемости
камер в сутки n = 1,5
B22,5
(300) │ 50
│ - │ 85
│ 80
───────────────┼─────────────┼──────────────┼───────────────┼──────────────
B30
(400) │ 50
│ 80 │ 75
│ 70
│ 60
│ - │ -
│ 85
───────────────┼─────────────┼──────────────┼───────────────┼──────────────
B37,5
(500) │ 50
│ 70 │ 65
│ 60
│ 60
│ 85 │ 80
│ 75
Примечание.
Приведенные в таблице значения температур разогрева бетона приняты из условия
испытания контрольных кубов-образцов через 0,5 ч после окончания тепловой
обработки.
3.15. Показатель A
рассчитывается с учетом конструктивных и теплофизических особенностей блока
камер по Прил. 2.
3.16. В
табл. 4 приняты следующие постоянные значения:
длительность
оборота камеры при n = 1 - 24 ч, при n = 1,5 - 16 ч;
предварительное
выдерживание изделий в камере - 3 ч;
скорость подъема
температуры бетона изделий - 10 °C/ч;
суммарная
длительность загрузки и выгрузки камеры - 2 ч.
Длительность
подъема температуры в изделиях
, ч, определяется по формуле
, (1)
где
- температура разогрева, принимаемая по табл.
4.
Длительность
термосного выдерживания
, ч, определяется по следующим формулам:
для n = 1
, (2)
для n = 1,5
. (3)
3.17. С целью
снижения энергоемкости процесса при последующем твердении распалубленных
предварительно ненапряженных изделий в цехе не менее 12 ч следует уменьшить
расчетную температуру разогрева на величину, приведенную в табл. 5.
Таблица 5
─────────────────────────┬─────────────────────────────────────────────────
Группа цемента │ Температурная поправка, °C, при
числе оборотов
│ камеры в сутки
├────────────────────────┬────────────────────────
│ 1 │ 1,5
─────────────────────────┼────────────────────────┼────────────────────────
I │ 5 │ 10
II │ 5
│ 10
III │ 10 │ 15
3.18. При
назначении термосных режимов следует учитывать, что с увеличением заданной
прочности (распалубочной или передаточной) резко повышается расход энергии при
тепловой обработке. Например, при увеличении заданной прочности с 50 до 70% от
расход тепловой
энергии возрастает в 1,5 - 2 раза. В связи с этим следует стремиться к
назначению минимально возможных в местных условиях значений распалубочной или
передаточной прочности, учитывая последующее нарастание прочности бетона при
выдерживании в цехе или на складе готовой продукции при положительных
температурах наружного воздуха с учетом отгрузки изделий потребителям.
3.19. При
производстве сборных бетонных и железобетонных изделий, подвергаемых
тепловлажностной обработке, могут применяться различные химические добавки
(ускорители твердения, пластификаторы, а также комплексные добавки).
Выбор химических
добавок следует осуществлять в соответствии с требованиями ГОСТ 24211-80* и
рекомендациями СНиП 3.09.01-85.
3.20. Вследствие
различной эффективности действия химических добавок, зависящей не только от
вида и марки цемента, но и конкретного завода - изготовителя цемента, а также
состава бетона, режимы тепловой обработки бетона с химическими добавками
следует назначать опытным путем. При этом следует иметь в виду, что:
применение
ускорителей твердения позволяет снизить температуру разогрева бетона на 10 - 20
°C при неизменном общем цикле тепловой обработки или сократить режим на 2 - 3 ч
при неизменной температуре разогрева бетона;
при применении
добавок-пластификаторов, в том числе суперпластификаторов, корректировка режима
тепловой обработки должна быть увязана с технологическим приемом и целью их
введения, а именно: при пластификации смесей или экономии цемента при равной
удобоукладываемости бетонной смеси режимы тепловой обработки должны
корректироваться в сторону увеличения продолжительности предварительного
выдерживания и времени разогрева;
при уменьшении В/Ц и равной удобоукладываемости смеси режимы тепловой
обработки могут оставаться неизменными. Для ряда добавок-пластификаторов,
особенно суперпластификаторов, возможно снижение температуры разогрева изделий
на 20 - 30 °C для цементов I и II групп (для термосных режимов) или сокращение
длительности изотермического выдерживания на 1 - 2 ч (для изотермических
режимов).
3.21. При выгрузке
изделий из камер температурный перепад между поверхностью изделий и
температурой окружающей среды не должен превышать 40 °C.
3.22.
Изделия после распалубки в холодное время года (при среднесуточной температуре
наружного воздуха ниже 5 °C) необходимо выдерживать в цехе не менее 12 ч с
целью уменьшения температурно-влажностных напряжений, приводящих к образованию
трещин в изделиях. Ориентировочный прирост прочности бетона в течение этого
периода может приниматься по табл. 6.
Таблица 6
──────────────────┬────────────────────────────────────────────────────────
Класс (марка) │
Коэффициент увеличения прочности бетона изделий
бетона │ при распалубочной прочности, % от R
├──────────────────┬──────────────────┬──────────────────
│ 45 - 50 │ 55 - 60 │ 65 - 70
──────────────────┼──────────────────┼──────────────────┼──────────────────
B15
(200) │ 1,1 - 1,15 │
1,05 - 1,12 │ -
B22,5
(300) │ 1,1 - 1,15 │
1,05 - 1,12 │ 1,04 - 1,09
B30
(400) │ 1,09 - 1,15 │
1,05 - 1,09 │ 1,04 - 1,08
B37,5
(500) │ 1,06 - 1,12 │
1,05 - 1,09 │ 1,04 - 1,09
Особенности
тепловой обработки в камерах
непрерывного
действия
3.23. При тепловой
обработке изделий в камерах непрерывного действия их прогрев осуществляется с
применением "глухого" пара (регистров). Для повышения влажности среды
следует дополнительно предусматривать подачу "острого" пара через
перфорированные трубы. В горизонтальных камерах регистры устанавливаются на
полу и под потолком. В вертикальных камерах регистры устанавливаются вдоль
боковых стен по ее высоте. В качестве теплоносителя используется, как правило,
водяной насыщенный пар давлением 0,5 - 0,6 МПа.
3.24. При прогреве
изделий в камерах непрерывного действия следует применять изотермические режимы
тепловой обработки в соответствии с рекомендациями п. 3.12.
3.25.
Отличительная особенность тепловой обработки изделий в камерах непрерывного
действия состоит в том, что формы-вагонетки с изделиями перемещаются вдоль
камеры, проходя при этом три зоны с различными температурно-влажностными
параметрами: зону предварительной выдержки, зону активной тепловой обработки и
зону остывания.
3.26. В
горизонтальных камерах непрерывного действия температурные зоны должны быть
разделены. Для разделения зон рекомендуется применять механизированные шторные
разделители (по типу СМЖ-411 конструкции Гипростроммаша), а при их отсутствии -
воздушные завесы (конструкции СКТБ Главмоспромстройматериалов) или шторы из
теплостойкой резины.
В вертикальных
камерах непрерывного действия указанные в п. 3.25 зоны предопределены
конструкцией камеры и создаются самопроизвольно без использования специальных
разделителей.
С целью экономии
тепловой энергии торцы горизонтальных камер рекомендуется оборудовать дверьми с
механическим приводом (по типу СМЖ-445 конструкции Гипростроммаша) или
специальными герметизирующими устройствами конструкции СКТБ
Главмоспромстройматериалов.
3.27. Пребывание
изделий в зоне предварительной выдержки (для горизонтальных камер - в
форкамере) должно быть не менее одного часа. Рекомендуется создавать в
форкамере температуру 40 - 60 °C и относительную влажность 40 - 60% и за счет
рециркуляции паровоздушной среды, отбираемой из зоны охлаждения.
3.28. В зоне
активной тепловой обработки производится нагрев и изотермическая выдержка
изделий. Температура среды в этой зоне должна быть не более 80 - 85 °C при
относительной влажности среды не менее 90%. Отличительной особенностью зоны
активной тепловой обработки в горизонтальных камерах является равномерность распределения
температур среды по длине зоны, за исключением участков длиной 5 - 10 м у ее
торцов.
Для интенсификации
теплообмена между средой и изделием рекомендуется осуществлять в зоне активной
тепловой обработки рециркуляцию среды. Скорость движения паровоздушной среды не
должна превышать 1 м/с.
При двухсменном
режиме работы предприятия (по формованию) в третью (нерабочую) смену в зоне
активной тепловой обработки должна поддерживаться температура изотермической
выдержки.
3.29. В зоне
остывания горизонтальных камер изделия охлаждаются до 60 °C воздухом,
отбираемым из цеха приточной установкой. Отработанный нагретый воздух подается
в форкамеру либо удаляется вытяжной установкой в атмосферу.
Применение
вытяжного вентилятора при нахождении изделий в зоне остывания менее 1 ч
нецелесообразно.
3.30. При
изготовлении изделий на двухъярусных станах в верхнем ярусе рекомендуется
осуществлять нагрев изделий до 60 °C при относительной влажности среды 40 -
60%, а изотермическое выдерживание при температуре 80 - 85 °C производить в
нижнем ярусе стана при относительной влажности не менее 90%.
3.31. При изменении
ритма работы конвейера следует производить соответствующую корректировку
режимов тепловой обработки изделий.
Особенности
тепловой обработки изделий
в термоформах и
кассетных установках
3.32. При тепловой
обработке железобетонных изделий в термоформах и кассетных установках прогрев
бетона осуществляется контактно-кондуктивным способом путем подачи
теплоносителя (пара, горячей воды, разогретого масла и др.) в тепловые отсеки
(в бортах и поддоне форм, в стендах, в кассетных установках) или размещения в
этих отсеках электронагревателей.
3.33.
Конструктивное исполнение тепловых отсеков при использовании любых
теплоносителей и электронагревателей должно обеспечивать однородность
температурного поля на поверхности теплового отсека, непосредственно
контактирующего с бетоном изделий, в процессе всей тепловой обработки. Допустимый
перепад температур не должен превышать 10 °C. С этой целью рекомендуется
применять эжекторную систему пароснабжения с давлением пара 0,3 - 0,4 МПа.
3.34. При тепловой
обработке в термоформах и на обогреваемых стендах изделий, имеющих большие
открытые (неопалубленные) поверхности, через которые происходит контакт с
окружающей средой, в процессе нагрева и последующего выдерживания происходит
испарение влаги из бетона, что может привести к снижению его
физико-механических свойств и образованию трещин на поверхности изделий. Для
предотвращения интенсивных влагопотерь из бетона и снижения теплопотерь в
окружающую среду тепловая обработка изделий в термоформах и на обогреваемых
стендах должна осуществляться с обязательным укрытием неопалубленных
поверхностей паронепроницаемыми и теплозащитными материалами. В качестве таких
укрытий могут быть использованы пленочные покрытия и пленкообразующие составы
со слоем плитной теплоизоляции, многослойные пленочные покрытия с воздушными
прослойками, инвентарные термовлагоизоляционные покрывала.
В холодный период
года каждая термоформа должна быть укрыта теплоизолированной крышкой.
Благоприятные
температурно-влажностные условия твердения бетона при прогреве в термоформах
(особенно в условиях сухого и жаркого климата) могут быть получены путем
создания "покрывающих водных бассейнов" толщиной 3 - 5 см.
3.35. Для ускорения
прогрева изделий целесообразно бетонную смесь укладывать в предварительно
подогретые формы, а также применять предварительно разогретые до 50 °C бетонные
смеси.
3.36. С целью
снижения удельных энергозатрат при использовании
отдельных термоформ целесообразно осуществлять тепловую обработку в пакете. При
установке термоформ в пакет уменьшаются температурные перепады по сечению
изделий, так как нагрев их происходит с двух сторон. Верхняя
термоформа в пакете закрывается теплоизолированной крышкой. Борта форм должны
быть заполнены теплоизоляционным материалом.
3.37. При
изготовлении объемных элементов (шахт лифтов, коллекторов и т.п.) в термоформах
обработка производится с помощью подвижных и неподвижных тепловых секций. С
целью снижения продолжительности тепловой обработки объемных изделий
рекомендуется применение двухстороннего прогрева путем подачи пара с помощью
эжектора, как в тепловые секции, так и во внутреннюю полость сердечника формы.
3.38. При
изготовлении в термоформах длинномерных предварительно напряженных
железобетонных изделий пар подается в тепловые секции, расположенные в поддоне,
неподвижных и подвижных бортах формы. Вследствие большой длины изделий рекомендуется
распределять пар в секциях с помощью перфорированного трубопровода, уложенного
в нижней части секций.
3.39. При тепловой
обработке изделий в термоформах и кассетных установках с использованием в
качестве теплоносителя пара необходимо периодически удалять из тепловых отсеков
конденсат, накопление которого приводит к нарушению заданного режима тепловой
обработки.
3.40. Тепловая
обработка изделий в термоформах, обогреваемых отсеках и кассетных установках
может осуществляться по режимам, включающим в себя термосную или изотермическую
стадию выдерживания. Применение термосных режимов обеспечивает значительное
сокращение (в 1,5 - 2 раза) расхода тепловой энергии.
3.41.
Изотермические режимы рекомендуется применять при тепловой обработке изделий в одиночных термоформах - по данным табл. 3. При двух и
более оборотах набранных в пакет форм или кассетных машин в сутки режимы
тепловой обработки ориентировочно могут приниматься по данным табл. 7 (при
расположении паровых отсеков через два рабочих отсека).
Таблица 7
───────────────────┬────────────────┬─────────────────────────────
Класс (марка) │ Толщина бетона │ Режим тепловой обработки
бетона │ в изделиях, мм
│ при 80 - 90 °C, ч
───────────────────┼────────────────┼─────────────────────────────
B12,5
(150) │ До 100
│ 9 (1 + 4 + 4)
───────────────────┼────────────────┼─────────────────────────────
B12,5
(150) │ 100 - 200
│ 11 (1 + 5 + 5)
───────────────────┼────────────────┼─────────────────────────────
B15
(200) │ До 100
│ 8 (1 + 3,5 + 3,5)
───────────────────┼────────────────┼─────────────────────────────
B15
(200) │ 100 - 200
│ 9,5 (1 + 4 + 4,5)
───────────────────┼────────────────┼─────────────────────────────
B25
(350) │ До 100
│ 7 (1 + 3 + 3)
───────────────────┼────────────────┼─────────────────────────────
B25
(350) │ 100 - 200
│ 8,5 (1 + 3,5 + 4)
Примечания. 1.
Режим тепловой обработки включает время подъема температуры в тепловом отсеке,
изотермического выдерживания с подачей пара в отсеки, выдерживания без подачи
пара в отсеки.
2. При прогреве
изделий с двух сторон через один рабочий отсек общий цикл тепловой обработки
уменьшается на 1 ч за счет изотермического выдерживания.
3.42. При изготовлении изделий в кассетных формах, учитывая, что бетон
находится в практически замкнутом жесткой объеме и неопалубленная поверхность
незначительна, допускается подъем температуры в бетоне осуществлять без
предварительной выдержки со скоростью до 60 °C/ч, но при этом максимальная
температура на контакте бетона с поверхностью теплового отсека не должна быть
выше 100 °C.
3.43. С целью увеличения оборачиваемости термоформ и кассетных машин
рекомендуется производить двухстадийную тепловую обработку изделий: первую
стадию до приобретения бетоном распалубочной прочности, составляющей, как
правило, до 50% проектной прочности, и вторую - при последующем твердении в
соответствующих температурно-влажностных условиях (камеры дозревания без подачи
пара, в цехе или на складе при положительных температурах) до достижения
отпускной прочности.
Режимы
двухстадийной тепловой обработки изделий, изготовляемых по стендовой и
кассетной технологии, принимаются по табл. 8.
Таблица 8
────────────┬───────────┬──────────┬───────────────────────────────────────
Вид
│ Класс │ Толщина │
Режимы выдерживания, ч
технологии │ бетона
│ изделий,
├───────────────────┬───────────────────
│ │ мм │
I стадия │
II стадия
│ │ │при t = 75 - 80 °C │при
t = 60 - 70 °C
────────────┼───────────┼──────────┼───────────────────┼───────────────────
Стендовая │До B15 │200 - 400 │ 9 (3,5 + 5 + 0,5)
│ 5
(термоформы)├───────────┼──────────┼───────────────────┼───────────────────
│Более B15 │200 - 400 │ 7,5 (3 + 4 + 0,5)
│ 4
────────────┼───────────┼──────────┼───────────────────┼───────────────────
Кассетная │B15 │
До 100 │при t = 80 -
90 °C │ 5
│ │ │ 6 (1 + 3,5 + 1,5) │
├───────────┼──────────┼───────────────────┼───────────────────
│B25 │
До 100 │ 5 (1 + 2,5
+ 1,5) │ 4
├───────────┼──────────┼───────────────────┼───────────────────
│B15 │100 - 200 │ 6,5 (1 + 4 +
1,5) │ 5
├───────────┼──────────┼───────────────────┼───────────────────
│B25 │100 - 200 │ 5,5 (1 + 3 +
1,5) │ 4
Примечания. 1.
Вторая стадия тепловой обработки может производиться в агрегатах любого типа.
2. Перерыв между
первой и второй стадиями тепловой обработки должен быть не более 1 ч.
3.44. При
использовании термосного выдерживания разогретых изделий в пакете термоформ или
кассетных установках требуемая температура разогрева бетона в зависимости от
группы цемента, класса бетона по прочности, заданной распалубочной прочности и
оборачиваемости кассет может ориентировочно приниматься по данным табл. 9 (для
типовых кассетных машин Гипростроммаша с утепленными паровыми отсеками).
Таблица 9
──────────┬────────┬───────────────────────┬───────────────────────────────
Число
│ Группа │ Класс
(марка) │ Температура разогрева
бетона,
оборотов │цемента │ бетона │ °C, в зависимости от
заданной
в сутки
│ │ │ усредненной
относительной
│ │ │ прочности бетона, % от R
│ │ │ 28
│ │
├──────────┬──────────┬─────────
│ │ │ 50
│ 60 │
70
──────────┼────────┼───────────────────────┼──────────┼──────────┼─────────
1
│ I │B10 - B15 (150 - 200) │
50 │ 60
│ 75
│
├───────────────────────┼──────────┼──────────┼─────────
│ │B22,5 (300) │ 45
│ 55 │
65
├────────┼───────────────────────┼──────────┼──────────┼─────────
│ II
│B10 - B15 (150 - 200)
│ 55 │
70 │ 85
│
├───────────────────────┼──────────┼──────────┼─────────
│ │B22,5 (300) │ 50
│ 60 │
75
──────────┼────────┼───────────────────────┼──────────┼──────────┼─────────
2
│ I │B10 - B15 (150 - 200) │
65 │ 80
│ 95
│
├───────────────────────┼──────────┼──────────┼─────────
│ │B22,5 (300) │ 55
│ 65 │
85
├────────┼───────────────────────┼──────────┼──────────┼─────────
│ II
│B10 - B15 (150 - 200)
│ 70 │
85 │ 100
│
├───────────────────────┼──────────┼──────────┼─────────
│ │B22,5 (300) │ 60
│ 75 │
90
Примечания. 1. При
назначении длительности отдельных стадий термосного режима следует
руководствоваться рекомендациями, приведенными в п. 3.16, исключив при этом
время предварительного выдерживания.
2. При указанных
температурах разогрева относительная прочность бетона в периферийном слое
изделий меньше усредненной относительной прочности бетона в горячем состоянии
примерно на 10%.
Особенности
тепловой обработки бетона
с повышенными
требованиями по морозостойкости
3.45. К бетонам с
повышенными требованиями по морозостойкости относятся бетоны с F = 100 и более
по ГОСТ 10060-76.
3.46. Повышенная
морозостойкость бетонов достигается следующими технологическими приемами:
применением
соответствующего типа цемента;
назначением
возможно более низких значений водоцементного отношения и удобоукладываемости
смеси;
введением в
бетонную смесь воздухововлекающих, пластифицирующих и комплексных добавок на их
основе.
3.47. Для получения
бетонов повышенной морозостойкости без введения воздухововлекающих,
пластифицирующих и комплексных добавок должны применяться морозостойкие
заполнители и низко-алюминатные портландцементы (с содержанием минерала
не более 6%) без минеральных добавок типа трепела
или опоки.
Применение
пуццолановых портландцементов и обычных шлакопортландцементов с повышенным
содержанием шлака допускается лишь в бетонах, изготовляемых с применением
упомянутых выше химических добавок.
3.48. Использование
воздухововлекающих, пластифицирующих и комплексных добавок для повышения
морозостойкости и водонепроницаемости бетона должно осуществляться в
соответствии с Пособием по применению химических добавок в бетоне (М.:
Стройиздат, 1981).
3.49. При
изготовлении изделий с повышенными требованиями по морозостойкости должны
соблюдаться общие требования по технологии изготовления, обеспечивающие
получение плотного бетона с бездефектной структурой, особенно поверхностных
слоев изделий.
3.50. Режимы
тепловой обработки изделий из бетонов повышенной морозостойкости должны быть
мягкими и включающими:
предварительное
выдерживание не менее 3 ч;
подъем температуры
среды со скоростью не более 20 °C/ч;
изотермическое или
термосное выдерживание разогретых изделий до достижения требуемой прочности.
3.51. Расчетная
температура разогрева бетонов, к которым предъявляются повышенные требования по
морозостойкости, должна назначаться минимально возможной для получения в
заданный срок требуемой прочности и не превышать 80 °C.
Особенности
тепловой обработки
преднапряженных
конструкций
3.52. Режимы тепловлажностной обработки предварительно напряженных
изделий необходимо назначать не только из условий получения требуемой прочности
бетона (передаточной, проектной, отпускной), но и учитывать ряд особенностей,
связанных с наличием напрягаемой арматуры (проволочной, канатной, стержневой),
натянутой на упоры стенда или силовой формы, иначе при тепловлажностной
обработке может произойти снижение качества предварительно напряженных
конструкций вследствие:
возникновения
трещин (поперечных и продольных) при нагреве и охлаждении из-за неравномерного
прогрева и охлаждения бетона, металлических форм и напрягаемой арматуры;
уменьшения
(сверх допустимого по проекту) величины предварительного напряжения в арматуре
при стендовой технологии изготовления от температурного перепада (разности
между температурой напрягаемой арматуры, находящейся в пределах нагретой
камеры, и температурой наружной среды, в которой находятся устройства,
воспринимающие усилия предварительного напряжения);
обрыва
предварительно напряженной арматуры и временных анкеров на свободных участках
до передачи усилия обжатия на бетон;
ухудшения анкеровки
арматуры на опорных участках или вдоль конструкции, увеличения зоны передачи
напряжения;
увеличения ширины раскрытия
трещин при эксплуатационных воздействиях.
3.53. С целью
предотвращения возникновения трещин при тепловой обработке предварительно
напряженных конструкций, изготовляемых на стендах и в силовых формах,
необходимо предусматривать:
обеспечение условий,
при которых величина перепада между температурой среды в камере и упоров при
изготовлении изделий на стендах не превышала 65 °C, а температура разогрева
бетона не превышала 80 °C;
при изготовлении
изделий в силовых формах предварительное выдерживание, не превышающее 1 ч;
регулирование
начального предварительного напряжения в арматуре.
3.54. Режимы
тепловой обработки предварительно напряженных конструкций при изготовлении на
стендах приведены в табл. 10.
Таблица 10
─────────────────────────────────────────┬────────────────────────
Режимы тепловой обработки │ Время, ч
─────────────────────────────────────────┼────────────────────────
Подъем
температуры до 80 °C
│ 7
Изотермическое
выдерживание при 80 °C │ 6,5
Остывание │ 1,5
При изготовлении
предварительно напряженных конструкций в силовых формах время подъема
температуры сокращается на 2,5 ч, а время остывания - на 1,5 ч по сравнению с
данными, приведенными в табл. 3, при сохранении неизменным общего цикла
тепловой обработки.
3.55. С целью
исключения возможности появления трещин в бетоне при стендовом изготовлении
может быть использован метод регулирования предварительного напряжения и при
охлаждении изделий. В этом случае регулирование предварительного напряжения
производится путем отпуска натянутой арматуры с момента начала охлаждения
изделий.
При стендовой
технологии изготовления, кроме отпуска напряжения арматуры на неостывающий
бетон для предотвращения температурных трещин, рекомендуется также устройство
съемных вкладышей и температурных швов в металлических формах, частичная
распалубка изделия (удаление фиксаторов при достижении прочности бетона не
менее 3 МПа), а также предварительный подогрев формы.
3.56. Для
предотвращения технологических трещин и ухудшения анкеровки предварительно
напряженной арматуры, натянутой на силовые формы, рекомендуются следующие
мероприятия:
размещение изделий
с поддоном в камере сразу после формования;
немедленная после
тепловлажностной обработки передача усилия обжатия на горячий бетон и распалубка
изделия;
уменьшение величины
перепада между максимальной температурой изделия при распалубке и температурой
воздуха цеха (за счет снижения температуры прогрева, ограничения доступа
холодного воздуха в цех, устройств тепловых завес и др.).
3.57. С целью
исключения вредного влияния температурных деформаций на качество изделий,
изготовляемых по агрегатно-поточной и конвейерной технологии, следует
использовать поддоны:
у которых
равнодействующая сил натяжения (усилия предварительного напряжения) приложена центрально
или с минимальным эксцентриситетом относительно центра тяжести сечения поддона;
открытого профиля
(для многопустотных настилов и др.), которые при охлаждении меньше выгибаются и
тем самым уменьшается возможность возникновения трещин.
В зависимости от
конкретных условий производства, способов тепловлажностной обработки
конструкций, перед вводом в эксплуатацию новых силовых форм (поддонов)
рекомендуется их опытная проверка для предотвращения возможности возникновения
трещин в бетоне.
3.58. Для исключения
возможности обрыва стержневой арматуры или высаженных головок и других
временных анкеров при нагреве в процессе тепловой обработки предварительно
напряженных конструкций, изготовляемых в силовых формах, необходимо применять
химические добавки, замедляющие рост прочности бетона в период подъема
температур и особенно при использовании бетонов класса
B22,5 (M300) и более.
3.59. Тепловую
обработку предварительно напряженных конструкций, изготовляемых в силовых
формах, необходимо производить в неглубоких камерах периодического действия с
установкой изделий в один ярус или в туннельных камерах с коэффициентом
заполнения не менее 0,1.
3.60. При
изготовлении предварительно напряженных конструкций в зимнее время на полигонах
при отрицательных температурах режим тепловой обработки увеличивается на 2 ч за
счет периода изотермического выдерживания.
4. ТЕПЛОВАЯ ОБРАБОТКА ИЗДЕЛИЙ ИЗ ЛЕГКИХ БЕТОНОВ
4.1. При назначении режима тепловой обработки изделий из легких бетонов
существенное влияние оказывают не только особенности применяемого цемента,
класса бетона, удобоукладываемость бетонной смеси, но и структура бетона
(плотная, поризованная), наличие в его составе вовлеченного воздуха и объем
его, прочность и объемная концентрация крупного пористого заполнителя,
гидравлическая активность мелких пористых заполнителей, зол и золошлаковых
отходов ТЭС.
4.2. Для
конструкционно-теплоизоляционных легких бетонов, применяемых при изготовлении
ограждающих конструкций зданий, режим тепловой обработки должен обеспечить
минимально возможную отпускную влажность бетона изделий, не превышающую в
процентах по объему:
15 - для бетона
панелей и блоков производственных зданий и бетонов на вспученном перлитовом
песке и золах ТЭС;
13 - для бетона
панелей и блоков жилых и общественных зданий (за исключением приготовленных на
вспученном перлитовом песке и золах ТЭС).
4.3. Для
обеспечения минимальной отпускной влажности тепловую обработку следует
проводить в условиях, способствующих испарению влаги из изделий.
Такой прогрев может
осуществляться в тепловых установках периодического и непрерывного действия (в
камерах ямного, туннельного и щелевого типа), оборудованных регистрами, ТЭНами,
калориферами, инфракрасными излучателями или теплогенераторами для сжигания
природного газа. Максимальная температура среды в камерах сухого прогрева может
быть повышена в зависимости от необходимой длительности тепловой обработки до
150 °C. С целью обеспечения заданной влажности изделий камеры рекомендуется
оборудовать системой вентиляции.
При тепловой
обработке в термоформах не следует укрывать открытую поверхность изделий.
4.4.
Тепловлажностную обработку в паровоздушной среде с относительной влажностью 85
- 95% и температурой 90 - 95 °C допускается проводить для изделий,
изготовляемых из конструкционно-теплоизоляционных легких бетонов с низким начальным водосодержанием, или при производстве
панелей для промышленного строительства при условии обеспечения требований п.
4.2.
4.5. При назначении
режимов тепловой обработки изделий из конструкционно-теплоизоляционных легких
бетонов следует учитывать следующие особенности кинетики роста их прочности:
замедление
темпа нарастания прочности при тепловой обработке бетонов на гидравлически
активных мелких заполнителях (дробленом керамзитовом песке, золе ТЭС) тем
сильнее, чем ниже температура в тепловой установке;
увеличение
содержания вовлеченного воздуха и снижение проектной прочности и плотности
бетона приводят к замедлению темпа нарастания прочности при тепловой обработке,
проявляющегося тем заметнее, чем ниже температура в тепловой установке;
при снижении
плотности и прочности крупного пористого заполнителя темп нарастания прочности
при прочих равных условиях повышается, и проявляется тем заметнее, чем ниже
температура в тепловой установке.
Ориентировочные
данные по кинетике нарастания прочности конструкционно-теплоизоляционных легких
бетонов приведены в табл. 11.
Таблица 11
───────┬────────┬───────────────────────────────────────────────────────────────────────
Класс │Длитель-│ Прочность легкого бетона через 0,5 ч, % от
проектной при различных
(марка)│ность │ мелких заполнителях
и температуре, °C
бетона
│изотер-
├───────────────────────┬───────────────────────┬───────────────────────
│мической│ песок пористый │ зола ТЭС │ песок плотный
│выдерж-
├───────┬───────┬───────┼───────┬───────┬───────┼───────┬───────┬───────
│ки, ч │
60 │ 80
│ 95 │
60 │ 80
│ 95 │
60 │ 80
│ 95
───────┼────────┼───────┼───────┼───────┼───────┼───────┼───────┼───────┼───────┼───────
B3,5 │
6 │10 - 15│20 -
25│30 - 40│15 - 20│40 - 45│50 - 60│30 -
35│45 - 50│50 - 55
(50) │
│-------│-------│-------│-------│-------│-------│-------│-------│-------
│ │30 - 35│40 - 45│50 -
60│30 - 35│50 - 55│55 - 65│45 - 50│55 -
60│60 - 65
│ │ │ │ │
│ │ │ │ │
│
10 │25 - 30│35 -
40│55 - 60│35 - 40│50 - 55│70 - 75│50 -
55│65 - 70│70 - 75
│
│-------│-------│-------│-------│-------│-------│-------│-------│-------
│ │45 - 50│55 - 60│70 -
75│50 - 55│65 - 70│75 - 80│65 - 70│75 -
80│80 - 85
│ │ │ │ │ │ │ │ │ │
│
14 │35 - 40│45 -
50│70 - 75│45 - 50│60 - 65│80 - 85│60 -
65│70 - 75│75 - 80
│ │-------│-------│-------│-------│-------│-------│-------│-------│-------
│ │50 - 55│65 - 70│80 -
85│60 - 65│75 - 80│85 - 90│75 - 80│85 -
90│90 - 95
│ │ │ │ │ │ │ │ │ │
│
18 │40 - 45│55 -
60│75 - 80│50 - 55│65 - 70│85 - 90│65 -
70│75 - 80│80 - 85
│
│-------│-------│-------│-------│-------│-------│-------│-------│-------
│ │55 - 60│70 - 75│85 -
90│65 - 70│80 - 85│85 - 90│80 - 85│85 -
90│90 - 95
───────┼────────┼───────┼───────┼───────┼───────┼───────┼───────┼───────┼───────┼───────
B5
(75)│ 6 │20 - 25│25 - 30│45 -
45│25 - 30│40 - 45│55 - 60│40 - 45│45 -
50│50 - 55
│
│-------│-------│-------│-------│-------│-------│-------│-------│-------
│ │35 - 40│45 - 50│55 -
45│40 - 45│55 - 60│60 - 70│55 - 60│60 -
65│65 - 70
│ │ │ │ │ │ │ │ │ │
│
10 │35 - 40│45 -
50│60 - 65│45 - 50│60 - 65│75 - 80│60 -
65│65 - 70│70 - 75
│
│-------│-------│-------│-------│-------│-------│-------│-------│-------
│ │50 - 55│60 - 65│70 -
75│60 - 65│70 - 75│80 - 85│70 - 75│75 -
80│80 - 85
│ │ │ │ │ │ │ │ │ │
│
14 │45 - 50│55 -
60│75 - 80│55 - 60│70 - 75│80 - 85│65 -
70│75 - 80│80 - 85
│
│-------│-------│-------│-------│-------│-------│-------│-------│-------
│ │60 - 65│70 - 75│80 -
85│65 - 70│80 - 85│85 - 90│80 - 85│85 -
90│90 - 95
│ │ │ │ │ │ │ │ │ │
│
18 │50 - 55│60 -
65│80 - 85│60 - 65│70 - 75│75 - 80│75 -
80│80 - 85│85 - 90
│
│-------│-------│-------│-------│-------│-------│-------│-------│-------
│ │65 - 70│75 - 80│85 -
90│75 - 80│80 - 85│85 - 90│85 - 90│90 -
95│90 - 95
───────┼────────┼───────┼───────┼───────┼───────┼───────┼───────┼───────┼───────┼───────
B7,5 │
6 │25 - 30│30 -
35│40 - 50│35 - 40│50 - 55│55 - 65│40 -
45│50 - 55│55 - 60
(100) │
│-------│-------│-------│-------│-------│-------│-------│-------│-------
│ │ -
│ - │
- │ -
│ - │
- │ -
│ - │
-
│ │ │ │ │ │
│ │ │ │
│
10 │40 - 45│50 -
55│60 - 65│45 - 50│65 - 70│75 - 80│60 -
65│70 - 75│75 - 80
│
│-------│-------│-------│-------│-------│-------│-------│-------│-------
│ │ -
│ - │
- │ - │
- │ -
│ - │
- │ -
│ │ │ │ │ │ │ │ │ │
│
14 │50 - 55│60 -
65│75 - 80│60 - 65│70 - 75│80 - 85│70 -
75│80 - 85│80 - 85
│
│-------│-------│-------│-------│-------│-------│-------│-------│-------
│ │ -
│ - │
- │ -
│ - │
- │ -
│ - │
-
│ │ │ │ │ │ │ │ │ │
│
18 │55 - 60│65 -
70│80 - 85│70 - 75│80 - 85│85 - 90│75 -
80│85 - 90│85 - 90
│
│-------│-------│-------│-------│-------│-------│-------│-------│-------
│ │ -
│ - │
- │ -
│ - │
- │ -
│ - │
-
Примечание. Данные
таблицы относятся к бетонам с вовлеченным воздухом, приготовленным на крупном
заполнителе с маркой по прочности П100 и более - над чертой и П50 - под чертой.
4.6. При назначении
режима тепловой обработки изделий из конструкционно-теплоизоляционных легких
бетонов необходимо учитывать замедленный темп нарастания прочности бетона в
самом изделии по сравнению с кинетикой роста прочности в той же тепловой
установке контрольных образцов-кубов. Это обусловлено замедлением прогрева
бетона в изделии вследствие низкой его теплопроводности, проявляющимся тем
больше, чем ниже плотность бетона, больше толщина изделия, меньше относительная
влажность паровоздушной среды, снижающая величину коэффициента теплоотдачи. Для
ориентировочного определения средней прочности бетона в изделиях значение
прочности образца-куба следует принимать с коэффициентами, приведенными в табл.
12.
Таблица 12
────────────┬─────────────────────────────────────────────────────
Длительность│Коэффициент
снижения средней прочности бетона изделий
тепловой
│ при тепловой
обработке в камере при
обработки,
ч├─────────────────────────┬───────────────────────────
│ пропаривании │ сухом прогреве
│ при t = 90 - 95 °C │
при t = 100 - 120 °C
│ с использованием песка │ с использованием песка
├───────────┬─────────────┼────────────┬──────────────
│ плотного │
пористого │ плотного
│ пористого
│ │ или золы
│ │ или золы
────────────┼───────────┼─────────────┼────────────┼──────────────
6
│0,65 - 0,75│ 0,4 -
0,5 │ 0,5 - 0,6 │
0,1 - 0,2
10
│0,85 - 0,9 │ 0,8 -
0,9 │ 0,7 - 0,8 │
0,3 - 0,4
14
│ 0,9 - 0,95│ 0,85 - 0,95 │ 0,8 - 0,9 │
0,8 - 0,9
18
│0,95 - 1 │ 0,95 -
1 │ 0,9 - 0,95 │ 0,9 - 0,95
Примечание. Данные
относятся к бетону со средней плотностью 1000 кг/м3 при толщине изделия 35 см.
4.7. При тепловой обработке изделий из конструкционно-теплоизоляционных
легких бетонов, изготовленных на гидравлически активных мелких заполнителях,
содержащих активные пылевидные фракции (золы ТЭС, дробленый керамзитовый
песок), следует использовать режимы с максимально высокой температурой среды на
стадии изотермического прогрева (95 - 140 °C) для обеспечения наиболее полного
протекания реакции между активным кремнеземом мелких пористых заполнителей и
продуктами гидратации твердеющего цементного камня и возможности использования
этого эффекта для повышения прочности и снижения плотности легкого
бетона.
4.8. В случаях, когда по условиям организации технологического процесса,
например, при формировании изделий в две смены, имеется возможность увеличить
цикл тепловой обработки, следует применять энергосберегающие режимы с
пониженной температурой разогрева, назначаемые с учетом кинетики роста
прочности легкого бетона в зависимости от его класса (марки), вида мелкого и
прочности крупного заполнителей с использованием ориентировочных данных табл.
11 и 12.
При назначении
таких режимов тепловой обработки следует обеспечивать достижение требуемой
распалубочной прочности бетона в изделиях, которая должна составлять не менее 2
МПа (20 кгс/см2) при наличии кантователей и 3 МПа (30
кгс/см2) при их отсутствии, но не менее 35% от проектного класса (марки)
бетона.
4.9. В целях экономичного
использования тепловой энергии при назначении режимов тепловой обработки
следует учитывать последующее нарастание прочности бетона изделий в процессе их
остывания в цехе в течение 12 ч в соответствии с данными, приведенными в табл.
13.
Таблица 13
────────────────────────┬───────┬───────┬─────────┬───────┬───────
Распалубочная
прочность,│35 - 40│40 - 50│ 50 - 60 │60 - 70│70 -
80
%
от проектной │ │ │ │ │
────────────────────────┼───────┼───────┼─────────┼───────┼───────
Коэффициент
увеличения │2 - 2,3│1,6 -
2│1,4 - 1,6│1,2 - │1,1
-
прочности
бетона изделий│ │ │ │ 1,4│ 1,2
при
остывании │ │ │ │ │
4.10. При
установлении продолжительности и температуры тепловой обработки изделий из
конструкционно-теплоизоляционных легких бетонов необходимо проверять после
тепловой обработки достижение требуемой отпускной влажности бетона в изделиях
(W, %) по формуле
, (4)
где В - количество воды в свежеотформованной бетонной смеси с
учетом влаги, содержащейся в заполнителе и растворе химической добавки, кг/м3;
Ц - расход цемента, кг/м3;
i - интенсивность
испарения воды из изделия, кг/м2 x ч, определяемая по
табл. 14;
- общая
продолжительность тепловой обработки, ч;
-
толщина изделия, м.
Таблица 14
─────────┬────────────────────────────────────────────────────────
Начальное│
Интенсивность испарения воды i, кг/м2 x ч, при средней
влагосо- │температуре паровоздушной среды (фи = 40%) в
камере, °C
держание
├──────┬──────┬──────┬───────┬──────┬──────┬──────┬──────
В,
л/м3
│ 70 │
80 │ 90
│ 100 │ 110
│ 120 │ 130 │ 140
─────────┼──────┼──────┼──────┼───────┼──────┼──────┼──────┼──────
230
- 260│ 0,55 │ 0,6 │
0,7 │ 0,8
│ 0,9 │ 1,1 │ 1,3
│ 1,6
200
- 220│ 0,45 │ 0,5 │
0,55 │ 0,65 │ 0,75 │
0,9 │ 1 │ 1,2
160
- 190│ 0,4 │ 0,45 │
0,5 │ 0,6
│ 0,7 │ 0,8 │ 0,9
│ 1
Значения В и Ц устанавливаются по данным о фактическом составе бетона, а
при предварительных расчетах принимаются: Ц - по СНиП
5.01.23-83, В - по табл. 12 и 13 Руководства по заводской технологии
изготовления наружных стеновых панелей из легких бетонов на пористых
заполнителях (М.: Стройиздат, 1980).
Рассчитанная по
формуле (4) величина W не должна превышать более чем на 2% требуемую отпускную
влажность легкого бетона согласно п. 4.2.
4.11. В случаях когда рассчитанная по формуле (4) или определенная
экспериментально влажность легкого бетона выше требуемых значений, необходимо
принять меры для ее уменьшения. Для этого следует, в первую
очередь, использовать технологические приемы, снижающие начальное
водосодержание бетонной смеси: уменьшение расхода воздухововлекающей добавки,
применение одновременно с воздухововлекающей пластифицирующей добавки,
исключение возможности применения горячего керамзита, повышение жесткости смеси
и др. Во-вторых, следует провести мероприятия для интенсифицирования процесса
испарения влаги: принудительную вентиляцию в период остывания, повышение
температуры тепловой обработки, а при отсутствии таких возможностей рассмотреть
целесообразность увеличения длительности тепловой обработки.
4.12. Длительность
предварительного выдерживания и скорость подъема температуры среды при тепловой
обработке изделий из конструкционно-теплоизоляционного бетона принимаются в
соответствии с данными табл. 15 и 16.
Таблица 15
──────────────────┬───────────────────┬───────────────────────────
Объем
вовлеченного│Жесткость смеси, с │ Время предварительного
воздуха, % │ │ выдерживания, ч
──────────────────┼───────────────────┼───────────────────────────
0 - 5 │ 11 - 20 │ 0,5 - 1
5 - 10 │ 5 - 10 │ 1 - 1,5
5 - 10 │ 5 - 10 │ 1,5 - 2,5
10 - 15 │ 5 │ 2,5 - 3,5
Таблица 16
────────────────────────────┬─────────────────────────────────────
Способы тепловой обработки │ Скорость
подъема температуры среды,
│ °C/ч, не более
────────────────────────────┼─────────────────────────────────────
Сухой
прогрев в камерах │ 50
Прогрев
в термоформах │ 40
Пропаривание
в камерах │ 30
Примечание. При
применении предварительного разогрева смеси или разогрева изделий в форкамерах
предварительная выдержка составляет 0,5 - 1 ч, а скорость подъема температуры в
них - 30 - 45 °C/ч.
4.13.
Продолжительность изотермического прогрева должна определяться временем,
необходимым для достижения в центре изделий температуры 65 - 80 °C в
соответствии с данными табл. 17.
Таблица 17
─────────────────────────────────────────────────────────┬─────────────────
Способ тепловой обработки │Продолжительность
│ изотермического
│ прогрева, ч
─────────────────────────────────────────────────────────┼─────────────────
Сухой
прогрев при температуре до 150 °C │ 6 - 8
Пропаривание
в термоформах
│ 5 - 7
Пропаривание
в камерах острым паром при температуре
│ 4 - 6
85
- 95 °C
│
Пропаривание
в закрытых формах (кассетах) при температуре│ 5 - 7
95
- 100 °C
│
Тепловая
обработка с подогревом в форкамерах
│ 5 - 7
при
температуре 30 - 40 °C │
Тепловая
обработка с применением предварительного │ 4 - 6
разогрева
смеси │
Примечание. Большие
значения для изделий толщиной 300 - 400 мм, меньшие - при толщине 200 - 300 мм.
4.14. Скорость
остывания поверхности изделий после изотермического прогрева не должна быть
более 40 °C/ч. При выгрузке изделий из камеры температурный перепад между
поверхностью и температурой окружающей среды не должен превышать 40 °C.
4.15. Скорость
остывания поверхности изделий, к которым предъявляются повышенные требования по
морозостойкости, не должна превышать 20 °C/ч.
4.16. Способы и
режимы тепловой обработки изделий из конструкционных легких бетонов классов B10
- B30 применяются такие же, как для аналогичных изделий из тяжелых бетонов. При
этом следует учитывать: возможность снижения относительной влажности
паровоздушной среды в тепловом агрегате; влияние соотношения между прочностью
применяемого пористого заполнителя и проектного класса бетона на темп роста его
относительной прочности; увеличение длительности изотермического прогрева с
увеличением толщины изделия.
4.17. Тепловая
обработка изделий из конструкционных легких бетонов может производиться по
термосному или изотермическому режимам. Время предварительного выдерживания,
скорость подъема температуры и температура разогрева бетона должны назначаться
в зависимости от начальной прочности бетона, удобоукладываемости и температуры
бетонной смеси, группы применяемого цемента в соответствии с рекомендациями пп.
3.11 - 3.22.
4.18. С увеличением
марки по прочности крупного пористого заполнителя при данном классе бетона темп
нарастания прочности бетона при тепловой обработке замедляется. В случаях когда марка по прочности пористого заполнителя равна
или выше марки бетона, режимы тепловой обработки конструкционных легких бетонов
не отличаются от режимов тепловой обработки равнопрочных тяжелых бетонов. При
меньшей прочности заполнителя температура разогрева при термосном выдерживании
может быть снижена на 5 - 10 °C (тем больше, чем выше класс бетона и ниже марка
по прочности заполнителя), а длительность изотермического периода при
температуре 80 °C сокращена до величин, приведенных в табл. 18.
Таблица 18
────────────────┬───────────┬──────────────────────────────────────────────
Группа
цементов │ Класс │
Длительность изотермического прогрева
по
эффективности│ (марка) │ при температуре 80 °C для получения
заданной
при тепловой │
бетона │ относительной прочности конструкционного
обработке
│ │ легкого бетона через 0,5 ч после выхода
│ │ из камеры, %
│
├──────────┬───────────┬───────────┬───────────
│ │ 50
│ 60 │
70 │ 80
────────────────┼───────────┼──────────┼───────────┼───────────┼───────────
I
│B12,5 (150)│ 2 -
4 │ 4 - 6
│ 8 - 10 │ 17 - 20
├───────────┼──────────┼───────────┼───────────┼───────────
│B15 (200) │
2 - 4 │ 3 - 5
│ 4 - 7 │
8 - 12
├───────────┼──────────┼───────────┼───────────┼───────────
│B25 (350) │
1 - 3 │ 2 - 4
│ 3 - 6 │
7 - 11
────────────────┼───────────┼──────────┼───────────┼───────────┼───────────
II
│B12,5 (150)│ 4 -
6 │ 5 - 7
│ 9 - 11 │
-
├───────────┼──────────┼───────────┼───────────┼───────────
│B15 (200) │
3 - 5 │ 4 - 6
│ 5 - 8 │ 13 - 16
├───────────┼──────────┼───────────┼───────────┼───────────
│B25 (350) │
2 - 4 │ 3 - 5
│ 5 - 7 │
9 - 12
────────────────┼───────────┼──────────┼───────────┼───────────┼───────────
III
│B12,5 (150)│ 6 -
8 │ 10 - 12
│ 17 - 20 │
-
├───────────┼──────────┼───────────┼───────────┼───────────
│B15 (200) │
5 - 7 │ 6 - 8
│ 8 - 11 │ 17 - 20
├───────────┼──────────┼───────────┼───────────┼───────────
│B25 (350) │
4 - 6 │ 5 - 7
│ 7 - 10 │ 14 - 17
Примечание. Меньшие
значения относятся к тепловой обработке изделий толщиной до 200 мм,
приготовленных на пористых заполнителях минимальной прочности, большие -
толщиной более 300 мм, приготовленных на пористых заполнителях с оптимальной
прочностью.
4.19. Длительность
охлаждения изделий в камере устанавливается в зависимости от толщины изделия и
температуры окружающей среды в момент распалубки в соответствии с данными табл.
19.
Таблица 19
──────────────────┬────────────────────────────────────────────────────────
Толщина изделия, │ Длительность охлаждения в камере, ч, при температуре
мм │ окружающего воздуха, °C
├──────────────────┬──────────────────┬──────────────────
│ от +30 до +20 │
от +20 до +10 │ от +10 до -10
──────────────────┼──────────────────┼──────────────────┼──────────────────
До
200 │ 0,5 - 1 │ 1 - 1,5 │
1,5 - 2,5
200
- 300 │ 1 - 1,5 │
1,5 - 2 │ 2 - 3
Более
300 │ 1,5 - 2 │ 2 - 2,5 │ 2,5 - 3,5
5. КОНТРОЛЬ
И РЕГУЛИРОВАНИЕ РЕЖИМОВ
ТЕПЛОВОЙ ОБРАБОТКИ
ИЗДЕЛИЙ
5.1.
Эффективный контроль и регулирование режимов тепловой обработки изделий могут
быть осуществлены при выполненном комплексе работ, направленных на нормализацию
технологического теплопотребления.
Нормализация
включает в себя:
паспортизацию
действующих тепловых установок на предприятии и расчет агрегатных
технологических норм расхода тепловой энергии;
Примечание. Расчет
агрегатных технологических норм расхода тепловой энергии производится при
применении изотермических режимов по СН 513-79, при термосных режимах - по Прил. 3.
стабилизацию работы
системы теплоснабжения предприятия путем установки на теплопроводах
теплоизоляции (в соответствии с нормами допустимых тепловых потерь
ВНИПИТеплопроекта для изолированных трубопроводов) и регуляторов давления пара
на магистральных трубопроводах, например 21ч10НЖ или РД. Настройку регуляторов
давления пара рекомендуется производить из условия поддержания давления пара
перед камерами кассетами и термоформами не более 0,3 МПа (2 ати);
оборудование
каждого ввода в тепловую установку дроссельными диафрагмами в соответствии с
рекомендациями, изложенными в Прил. 4;
устранение утечек
пара в паропроводах, запорной арматуре и через неплотности в тепловых
установках;
обеспечение
работоспособности устройств для отвода и возврата конденсата
из тепловых установок.
5.2. Обеспечение
заданного температурного режима тепловой обработки, позволяющего получить
требуемые качественные характеристики бетона изделий, может быть осуществлено с
применением:
автоматизированных
систем управления и программного регулирования температуры и прочности изделий;
дроссельных
диафрагм, обеспечивающих подачу в тепловые установки расчетного количества
тепловой энергии (при отсутствии систем автоматического контроля и
регулирования).
Примечание. При
применении термосных режимов с использованием систем автоматического
регулирования температурный датчик должен регистрировать температуру изделий. С
этой целью настройку регулятора следует осуществлять с учетом коррекции между
температурой среды и температурой изделия, определяемой отдельно в каждом
конкретном случае.
5.3. В качестве
программных регуляторов температуры рекомендуется использовать:
электронные
программные регуляторы типа Р-31М, выпускаемые Ивано-Франковским заводом
"Геофизприбор" Минприбора СССР;
пневматические
системы программного регулирования типа "Пуск", серийно выпускаемые
Усть-Каменогорским заводом приборов Минприбора СССР;
комплексные системы
автоматизации тепловлажностной обработки;
систему СПУРТ-1 на
элементах пневмоавтоматики (изготовитель - Усть-Каменогорский завод приборов
Минприбора СССР);
комплекс СКРЖ на
базе блоков Р-31М (изготовитель - Тернопольский ЭРМЗ Минстроя УССР);
систему САУ-ТО на
базе блоков Р-31М (изготовитель - опытный завод ВНИИжелезобетона).
С той же целью
могут быть использованы другие, вновь разрабатываемые программные регуляторы
или системы, обеспечивающие регулирование температуры по заданной программе.
5.4. Для контроля
температуры рекомендуются термометры сопротивления (ТСМ, ТСП) и термопары (ТХК,
ТМК).
Контрольные датчики
температуры должны устанавливаться в местах, где температуру среды в тепловой
установке можно считать средней. В ямных камерах датчики устанавливаются в
специальных нишах внутри камеры на половине ее высоты в месте, исключающем
прямое попадание на них потока пара. В камерах непрерывного действия
(вертикальных или горизонтальных) контрольный датчик устанавливается в начале
зоны с максимальной температурой среды по возможности на уровне изделия.
При прогреве
изделий через паровые рубашки контрольный датчик температуры может помещаться
на линии отвода конденсата не далее 0,5 м от формы.
Для гарантии
постоянного нахождения датчика в проточном конденсате на конденсатоотводной
линии отвода конденсата за датчиком должен быть установлен конденсатоотводчик
или обратный клапан.
Если контрольный
датчик показывает температуру выше 95 °C, то это говорит о непосредственном
попадании на него струи пара, и необходимо принять соответствующие меры, например уменьшить подачу пара.
Как исключение
допускается производить замер температуры в камерах с помощью ртутного
термометра или термощупа.
5.5. Для
обеспечения заданного режима по нормируемому расчетному расходу пара (тепловой
энергии) в установке должны быть выполнены мероприятия, указанные в п. 5.1, и в
первую очередь следует стабилизировать давление пара в магистральных
трубопроводах. Расчет часового расхода пара и выбор дроссельной диафрагмы,
обеспечивающей этот расход, приведены в Прил. 4.
5.6. При всех
способах контроля оператор заносит в журнал время загрузки камеры (установки),
длительность отдельных периодов температурного режима, время открытия камеры
или выгрузки изделий из тепловой установки.
В зимнее время
оператор регистрирует не реже одного раза в смену и записывает в журнал температуру
воздуха в цехе, где хранятся распалубленные изделия.
6.
ОСОБЕННОСТИ КОНТРОЛЯ ПРОЧНОСТИ БЕТОНА
ПРИ ТЕПЛОВОЙ
ОБРАБОТКЕ
6.1. Контроль
прочности бетона изделий, подвергаемых тепловой обработке, производится в
соответствии с требованиями ГОСТ 13015.1-81 или ГОСТ 18105-86 со следующими
особенностями для различных видов тепловых установок.
6.2. При тепловой
обработке изделий в камерах периодического действия с применением
изотермических режимов контрольные кубы-образцы следует устанавливать в
специальных нишах, оборудованных в стенах камер, или на форме верхнего изделия.
Учитывая, что
температура кубов-образцов с достаточной степенью точности следует за
температурой среды в камере, при применении термосных режимов эти образцы
необходимо устанавливать внутри рабочего объема камеры, например, на форме
верхнего изделия или специальных площадках, пристроенных к стенкам (нишам)
камеры. Устанавливать контрольные образцы в нишу стен камер при тепловой
обработке изделий по термосным режимам запрещается.
6.3. При тепловой
обработке изделий в камерах непрерывного действия контрольные кубы-образцы
следует устанавливать на формах-вагонетках с изделиями.
6.4. При тепловой
обработке изделий в кассетах необходимо иметь в виду, что прочность бетона в
наиболее слабых (краевых) зонах панелей, как правило, выше, чем у контрольных
кубов, устанавливаемых в специальных нишах в паровых отсеках или на верхних
торцах изделий под колпаком. В связи с этим к прочности контрольных
кубов-образцов, испытываемых через 0,5 - 4 ч с момента их распалубки,
рекомендуется вводить коэффициенты 1,15 при их прогреве в нишах и 1,3 при
прогреве под колпаком.
6.5. При тепловой
обработке изделий в термоформах контрольные образцы прогреваются в специальных
нишах-карманах, расположенных в торцах термоформ. При контроле прочности бетона
изделий после завершения их тепловой обработки к прочности этих образцов,
испытываемых через 0,5 - 4 ч с момента распалубки, рекомендуется вводить
коэффициент 1,15.
6.6. Если при
отсутствии контроля и регулирования температурного режима контрольные
кубы-образцы после тепловой обработки не набирают заданную прочность, то
прочность бетона в изделиях должна быть установлена неразрушающими методами в
соответствии с ГОСТ 17624-78. Если и в этом случае прочность бетона не отвечает
заданным требованиям, изделия должны быть дополнительно выдержаны в тепловых
установках без подачи пара.
6.7. Если толщина
изделия отличается от размера ребра контрольных образцов более чем в три раза,
то режимы тепловой обработки изделий должны корректироваться опытным путем с
применением неразрушающих методов контроля.
Приложение
1
СООТВЕТСТВИЕ
ЗАВОДОВ-ИЗГОТОВИТЕЛЕЙ ГРУППАМ ЦЕМЕНТОВ
ПО ЭФФЕКТИВНОСТИ
ПРИ ПРОПАРИВАНИИ
────────┬─────────────────────────────────────┬───────────────────
N п.п. │ Завод-изготовитель │ Группа цемента
────────┼─────────────────────────────────────┼───────────────────
1
│Акмянский │ II
2
│Амвросиевский │ II
3
│Ангарский │ II
4
│Араратский │ III
5
│Ахангаранский │ I
6
│Ачинский │ I
7
│Балаклейский
│ II
8
│Бахчисарайский │ I
9
│Безмеинский │ I
10
│Бекабадский │ II
11
│Белгородский │ II
12 │"Большевик" │ II
13
│Броценский │ III
14
│Брянский │ III
15
│Волковысский │ II
16
│Волховский │ II
17
│Воркутинский │ II
18
│Воскресенский │ I
19
│"Гигант" │ I
20
│Горнозаводский │ I
21
│Днепродзержинский │ II
22
│Душанбинский │ I
23
│Днепропетровский │ II
24
│Енакиевский │ I
25
│Жигулевский │ I
26
│Здолбуновский │ III
27
│Ивано-Франковский │ II
28
│Каменец-Подольский │ I
29
│Кантский │ II
30
│Карагандинский │ II
31
│Карадагский │ III
32
│Карачаевочеркесский │ II
33
│Косинский │ II
34
│Катаев-Ивановский │ II
35
│Киевский │ II
36
│Коркинский │ II
37
│Косогорский │ II
38
│Краматорский
│ II
39
│Краснодарский │ III
40
│Красноярский │ II
41
│"Красный Октябрь" │ III
42
│Криворожский │ II
43 │Кричевский │ III
44
│Кузнецкий │ III
45
│Курментинский │ III
46
│Кувасайский │ II
47
│Липецкий │ II
48
│Магнитогорский │ II
49
│Михайловский │ II
50
│Мордовский │ II
51
│Новоийский │ I
52
│Невьянский │ II
53
│Нижнетагильский │ II
54
│Николаевский │ III
55
│Новотроицкий │ II
56
│Норильский │ II
57
│Одесский │ II
58
│"Октябрь" │ II
59
│Ольшанский │ III
60
│"Первомайский" │ III
61
│Пикалевский │ I
62
│"Победа Октября" │ II
63
│Подгоренский │ II
64
│Подольский │ II
65 │Поронайский │ III
66
│"Пролетарий" │ II
67
│"Пунане Кунда" │ II
68
│Рижский │ II
69
│Руставский │ III
70
│Рыбницкий │ II
71
│Савинский │ I
72
│Серебряковский │ II
73
│Семипалатинский │ II
74
│Сланцевский │ II
75
│"Спартак" │ II
76
│Спасский │ II
77
│Старооскольский │ III
78
│Стерлитамакский │ II
79
│Сухоложский │ II
80
│Теплоозерский │ I
81
│Тимлайский │ II
82
│Топкинский
│ II
83
│Усть-Каменогорский │ II
84
│Ульяновский │ I
85
│Чернореченский │ II
86
│Чимкентский │ III
87
│Чечено-Ингушский │ II
88
│Щуровский │ II
89
│Якутский │ III
90
│Яшкинский │ III
Приложение
2
РАСЧЕТ
ПОКАЗАТЕЛЯ ДЛИТЕЛЬНОСТИ ОСТЫВАНИЯ
A БЛОКА КАМЕР С
ИЗДЕЛИЯМИ
Показатель
длительности остывания A, ч, рассчитывается по формуле
, (1)
где
,
- соответственно объемная теплоемкость,
кДж/(м3 x °C), и объем бетона изделий в плотном теле, м3, в блоке камер;
,
- то же, ограждающих конструкций блока камер;
,
- то же, для металла в блоке камер:
. (2)
Здесь
- масса металла форм в блоке камер, кг;
- масса
металлических элементов крышек в блоке камер, кг;
- масса
стоек пакетировщиков (направляющих) внутри блока камер, кг;
- масса
стальной обшивки, учитываемая при теплоизоляции ограждений (например, по
типовому проекту 409-28-40);
-
соответственно коэффициент теплопередачи, Вт/(м2 x
°C), и площадь поверхности наружных стен блока камер выше нулевой отметки пола,
м2;
- то
же, для наружных стен ниже нулевой отметки пола;
- то
же, для днища блока камер;
- то
же, для крышек блока камер.
Для расчетов
рекомендуется принимать следующие значения объемных теплоемкостей
: для
тяжелого бетона изделий и ограждающих конструкций камер - 2500 кДж/(м3 x °C);
для керамзитобетона ограждающих конструкций камер - 1600 кДж/(м3 x °C) и для
металла форм, стоек и т.п. - 3800 кДж/(м3 x °C).
Значения
коэффициентов теплопередачи
приведены в табл. 1.
Таблица 1
───────────┬───────────────────────────────────────────────────────────────
Коэффициент│ Значения коэффициентов теплопередачи,
Вт/(м2 x °C)
├─────────────────────────────┬─────────────────────────────────
│ элементы ограждений камер │
при ограждениях из
│
├───────────────┬─────────────────
│ │тяжелого
бетона│ керамзитобетона
───────────┼─────────────────────────────┼───────────────┼─────────────────
K │Наружные стены выше нулевой │
5,8 │ 2,6
1
│отметки пола
│ │
───────────┼─────────────────────────────┼───────────────┼─────────────────
K │Наружные стены ниже нулевой │
2,3 │ 2,2
2
│отметки пола
│ │
───────────┼───────┬─────────────────────┼───────────────┼─────────────────
K
│Днище │из
бетона │ 2,3
│ 2,2
3
│
├─────────────────────┼───────────────┼─────────────────
│ │пустотный настил │ 1,3
│ -
───────────┼───────┴─────────────────────┼───────────────┼─────────────────
K
│Крышка
│ 5,8 │ 5,8
4
│
│ │
В случае утепления
внутренней поверхности ограждений из тяжелого бетона слоями изоляции толщиной
, м, с
сопротивлением теплопередаче
, (м2 x °C)/Вт, значения коэффициентов теплопередачи ограждений
принимаются по табл. 2.
Таблица 2
───────────────┬────────────┬──────────────────────────────────────────────
Материал
│Коэффициенты│
Значения коэффициентов теплопередачи,
ограждений
│ │Вт/(м2 x °C), при сопротивлении теплопередаче
│ │ R , (м2
x °C)/Вт
│ │ 0
│
├─────┬────┬─────┬─────┬─────┬─────┬─────┬─────
│ │ 0
│0,2 │ 0,4 │ 0,6 │ 0,8 │ 1
│ 1,2 │ 1,4
───────────────┼────────────┼─────┼────┼─────┼─────┼─────┼─────┼─────┼─────
Тяжелый
бетон │K │ 5,8 │2,7 │ 1,8
│ 1,3 │ 10 │ 0,9
│ 0,7 │ 0,6
│ 1 │ │
│ │ │
│ │ │
│K и K
│ 2,3 │1,6 │ 1,2 │ 10 │ 0,8 │ 0,7 │ 0,6 │
0,6
│ 2 3
│ │ │
│ │
│ │ │
───────────────┼────────────┼─────┼────┼─────┼─────┼─────┼─────┼─────┼─────
Керамзитобетон
│K │ 2,6 │1,7
│ 1,3 │ 10 │ 0,9
│ 0,7 │ 0,6 │ 0,6
│ 1 │ │
│ │ │
│ │ │
│K и K
│ 2,2 │1,6 │ 1,2 │ 10 │ 0,8 │ 0,7 │ 0,6 │
0,5
│ 2 3
│ │ │
│ │ │
│ │
Сопротивление
теплопередаче
, (м2 x °C)/Вт, рассчитывается по формуле
, (3)
где
- толщина i-го слоя ограждения (изоляции), м;
-
коэффициент теплопроводности материала i-го слоя ограждения, Вт/(м
x °C). Принимается по прил. 3 СНиП II-3-79* "Строительная теплотехника".
Для конструкций
ограждений с теплоизоляцией, имеющих воздушные прослойки, значения
сопротивления теплопередаче каждой из воздушных прослоек приводятся в табл. 3.
Таблица 3
────────────────────────────────┬──────┬───────┬──────┬──────┬──────┬──────
Толщина
воздушной прослойки, м
│ 0,03 │ 0,04 │
0,05 │ 0,1 │ 0,15 │
0,2
────────────────────────────────┼──────┼───────┼──────┼──────┼──────┼──────
R (м2 x °C)/Вт │ 0,28 │ 0,3
│ 0,32 │ 0,38 │ 0,41 │ 0,45
0 │ │ │ │ │ │
Примечание. При
наличии n воздушных прослоек величину
следует умножить на n.
Пример расчета
показателя длительности остывания A
I вариант.
Тепловая обработка железобетонных изделий, приготовленных на цементе I группы
класса B22,5 (M300) осуществляется в блоке, состоящем из трех камер ямного
типа. Внутренние размеры одной камеры, м: длина - 7,
ширина - 2,5, высота - 3,5. Заглубление днища камеры в грунт относительно пола
цеха - 0,5 м. Толщина бетонных стенок, днища и перегородок камеры - 0,3 м,
материал - тяжелый бетон.
Объем бетона
прогреваемых изделий в каждой камере -
, масса
находящегося в одной камере металла форм
, масса
металлических элементов крышки одной камеры
, масса
металла стоек пакетировщиков в одной камере
.
Расчет
Площадь поверхности
наружных стен блока камер выше нулевой отметки пола
,
площадь поверхности наружных стен блока
камер ниже нулевой отметки пола
,
поверхность днища блока камер
,
площадь поверхности крышек принимаем
равной площади поверхности днища
.
Объем бетона
ограждающих конструкций, включая перегородки
.
Общий объем металла в блоке камер по
формуле (2)
.
Значения объемных
теплоемкостей принимаем
для тяжелого бетона
изделий и ограждений
;
для металла форм,
стоек и крышек
.
Значения
коэффициентов теплопередачи
принимаем в соответствии с данными табл. 1.
Показатель
длительности остывания A рассчитываем по формуле
.
II вариант
(по типовому проекту 409-28-40). Ограждения камер толщиной 0,3 м из тяжелого
бетона (см. вариант I) изолированы жесткой минераловатной плитой толщиной 60
мм, покрытой фольгоизолом с воздушной прослойкой шириной 35 мм и стальным
листом толщиной 3 мм. Днище камеры состоит из пустотного настила толщиной 220
мм, песчаной подготовки толщиной 80 мм и слоя керамзитового гравия толщиной 200
мм.
Поскольку тепловая
изоляция выполнена с внутренней стороны, расчетные параметры остаются теми же,
что в варианте I:
площадь поверхности
наружных стен блока камер выше нулевой отметки пола
;
площадь поверхности наружных стен ниже нулевой отметки пола
;
площадь поверхности днища блока камер
;
площадь поверхности крышек камер
; объем
бетона ограждающих конструкций
; объем
материала теплоизоляции (минеральной ваты) - 8 м3. По СНиП II-3-79** удельная
теплоемкость минераловатных плит с объемным весом 200 кг/м3 c = 0,84 кДж/(кг x
°C), т.е.
.
Расход стали на
обшивку стен одной камеры
.
Расчет
Объем металла в
блоке камер (по формуле (2)):
.
Сопротивление
теплопередаче слоев ограждения
, (м2 x °C)/Вт, рассчитывается по формуле (3)
,
где
и
- соответственно толщина слоев тяжелого бетона
и минераловатной плиты, м;
и
- коэффициенты теплопроводности тяжелого
бетона и минераловатной плиты, принимаемые по СНиП II-3-79**:
и
;
-
сопротивление теплопередаче воздушной прослойки шириной 0,35 мм по табл. 3
.
.
Принимаем
и по табл. 2 определяем значения коэффициентов
теплопередачи
и
. Для
днища по табл. 1
.
Рассчитываем
показатель длительности остывания A по формуле (1)
.
Таким образом, для
блока камер с ограждениями из тяжелого бетона показатель длительности остывания
A равен 60 ч, а для теплоизолированных ограждений - 127 ч.
При изготовлении
изделий из бетона класса B22,5 на портландцементе I группы по активности при
пропаривании, требуемой прочности 70% от проектной марки и одном обороте камер
в сутки по табл. 4 назначаем температуру разогрева бетона: для неизолированных
камер - 75 °C, для теплоизолированных камер - 70 °C.
Приложение
3
РАСЧЕТ
РАСХОДА ТЕПЛОВОЙ ЭНЕРГИИ ПРИ ТЕПЛОВОЙ ОБРАБОТКЕ
ИЗДЕЛИЙ С
ПРИМЕНЕНИЕМ ТЕРМОСНЫХ РЕЖИМОВ
В камерах
периодического действия
Общий расход
тепловой энергии Q, МДж/м3, при разогреве бетона изделий на

определяется по
формуле
, (1)
где K -
коэффициент, учитывающий потери тепла с конденсатом. Численные значения
коэффициента приведены в табл. 1;
-
расход тепловой энергии на разогрев бетона изделий с учетом тепловыделения,
МДж/м3; определяется по табл. 2;
-
расход тепловой энергии на разогрев металла форм, МДж/м3; определяется по табл.
3;
-
расход тепловой энергии на разогрев элементов ограждений блока камер, включая
потери тепла за время разогрева, МДж/м3.
, (2)
где
- площадь поверхности наружных стен блока
камер выше нулевой отметки пола, м2;
-
площадь поверхности наружных стен блока камер ниже нулевой отметки пола, м2;
-
площадь поверхности днища, м2;
-
площадь поверхности крышки, м2;
-
площадь поверхности перегородок, м2;
- объем
бетона прогреваемых изделий, м3;
-
удельные потери тепловой энергии, приходящиеся на 1 м2
поверхности отдельных ограждений при различных температурах разогрева изделий,
°C; определяются по табл. 4 и 5, МДж/м2.
Таблица 1
─────────────────────────┬────────┬───────┬───────┬───────┬────────┬───────
Температура
разогрева, °C│ 40 │
50 │ 60
│ 70 │
80 │ 85
─────────────────────────┼────────┼───────┼───────┼───────┼────────┼───────
Коэффициент
K │ 1,03
│ 1,04 │ 1,045
│ 1,055 │ 1,065 │ 1,07
Таблица 2
─────────────┬─────────────────────────────────────────────────────────────
Класс
(марка)│ Расход тепловой
энергии, МДж/м3, для разогрева бетона
бетона
│ на тяжелых заполнителях
с учетом тепловыделения цемента
│ до температуры, °C
├──────────┬──────────┬─────────┬──────────┬────────┬─────────
│ 40
│ 50 │
60 │ 70
│ 80 │
85
─────────────┼──────────┼──────────┼─────────┼──────────┼────────┼─────────
B15
(200) │ 54
│ 75 │
92 │ 109
│ 126 │
134
─────────────┼──────────┼──────────┼─────────┼──────────┼────────┼─────────
B22,5
(300) │ 54
│ 71 │
88 │ 100
│ 113 │
121
─────────────┼──────────┼──────────┼─────────┼──────────┼────────┼─────────
B30
(400) │ 50
│ 67 │
80 │ 96
│ 105 │
109
─────────────┼──────────┼──────────┼─────────┼──────────┼────────┼─────────
B37,5
(500) │ 50
│ 63 │
75 │ 84
│ 92 │
96
Таблица 3
──────────────────┬────────────────────────────────────────────────────────
Масса металла │ Расход тепловой энергии, МДж/м3, для
разогрева металла
форм, т на 1 м3 │ форм до температуры, °C
бетона
├─────────┬────────┬─────────┬────────┬────────┬─────────
│ 40
│ 50 │
60 │ 70
│ 80 │
85
──────────────────┼─────────┼────────┼─────────┼────────┼────────┼─────────
2 │ 29
│ 42 │
54 │ 67
│ 80 │
84
3 │ 42
│ 59 │
75 │ 96
│ 113 │
121
4 │ 54
│ 80 │
100 │ 121
│ 146 │
159
5 │ 67
│ 96 │
126 │ 155
│ 180 │
192
6 │ 84
│ 113 │
151 │ 188
│ 214 │
226
Таблица 4
────────────────────────────┬──────────┬───────────────────────────────────
Ограждения │Компоненты│ Расход
тепловой энергии, МДж/м2,
│ тепловых
│ на разогрев и компенсацию потерь
│ потерь
│ при остывании
ограждений
│ │ из тяжелого бетона при
разогреве
│ │ изделий до температуры, °C
│
├─────┬─────┬─────┬─────┬─────┬─────
│ │ 40 │ 50
│ 60 │ 70 │ 80
│ 85
────────────────────────┬───┼──────────┼─────┼─────┼─────┼─────┼─────┼─────
Наружные
стены выше │ 5 │ q
│16,7 │17,6 │18,2 │18,8 │19,2 │19,5
нулевой
отметки пола при│ │ 1
│ │ │
│ │ │
длительности
перерывов,
├───┼──────────┼─────┼─────┼─────┼─────┼─────┼─────
ч │15 │ q'
│22,2 │25,5 │29,3 │31,8 │33,9 │35
│ │
1 │ │
│ │ │
│
────────────────────────┴───┼──────────┼─────┼─────┼─────┼─────┼─────┼─────
Наружные стены ниже нулевой │ q
│10,5 │11,7 │13
│14 │15,5
│15,9
отметки
пола │ 2 │
│ │ │
│ │
────────────────────────────┼──────────┼─────┼─────┼─────┼─────┼─────┼─────
Днище │ q
│10,5 │11,7 │13
│14 │15,5
│15,9
│ 3
│ │ │
│ │ │
────────────────────────────┼──────────┼─────┼─────┼─────┼─────┼─────┼─────
Крышка │ q
│ 5,9 │ 6,3 │ 6,7 │ 7,1 │ 7,7 │ 8
│ 4
│ │ │
│ │ │
────────────────────────┬───┼──────────┼─────┼─────┼─────┼─────┼─────┼─────
Перегородки
при длитель-│ 5 │ q │ 7,1 │ 9,6 │12,6
│15,1 │18 │19,7
ности
перерывов, ч
│ │ 5
│ │ │
│ │ │
├───┼──────────┼─────┼─────┼─────┼─────┼─────┼─────
│15 │ q'
│12,6 │17,6 │22,6 │28 │32,6 │35,6
│ │
5 │ │
│ │ │
│
Таблица 5
────────────────────────────┬──────────┬───────────────────────────────────
Ограждения
│Компоненты│ Расход тепловой энергии, МДж/м2,
│ тепловых
│ на разогрев и компенсацию потерь
│ потерь
│ при остывании
ограждений из
│ │
керамзитобетона при разогреве
│ │ изделий до температуры, °C
│
├─────┬─────┬─────┬─────┬─────┬─────
│ │ 40 │ 50
│ 60 │ 70 │ 80
│ 85
────────────────────────┬───┼──────────┼─────┼─────┼─────┼─────┼─────┼─────
Наружные
стены выше │ 5 │ q
│ 8,4 │ 9,2 │10,5 │11,3 │12,6 │13,2
нулевой
отметки пола при│ │ 1
│ │ │
│ │ │
длительности
перерывов, ├───┼──────────┼─────┼─────┼─────┼─────┼─────┼─────
ч │15 │ q'
│10,8 │12,1 │13,4 │14,6 │15,9 │16,3
│ │
1 │ │
│ │ │
│
────────────────────────┴───┼──────────┼─────┼─────┼─────┼─────┼─────┼─────
Наружные стены ниже нулевой │ q
│ 8 │ 8,4 │
8,8 │ 9,6 │10,9 │11,7
отметки
пола │ 2
│ │ │
│ │ │
─────┬──────────────────────┼──────────┼─────┼─────┼─────┼─────┼─────┼─────
Днище│из
керамзитобетона │ q
│ 8 │ 8,4 │
8,8 │ 9,6 │10,9 │11,7
│ │ 3
│ │ │
│ │ │
├──────────────────────┼──────────┼─────┼─────┼─────┼─────┼─────┼─────
│из керамзитобетонного │ q'
│ 9,2 │10,5 │12,1 │13,4 │15,5 │16,3
│пустотного настила │
3 │ │
│ │ │
│
│с подсыпкой │ │ │
│ │ │
│
│керамзитового гравия │ │ │
│ │ │
│
─────┴──────────────────────┼──────────┼─────┼─────┼─────┼─────┼─────┼─────
Крышка │ q
│ 5,9 │ 6,3 │ 6,7 │ 7,1 │ 7,7 │ 8
│ 4
│ │ │
│ │ │
────────────────────────┬───┼──────────┼─────┼─────┼─────┼─────┼─────┼─────
Перегородки
при длитель-│ 5 │ q │ 5,4 │ 7,5 │ 9,6
│11,7 │14,2 │15,1
ности
перерывов, ч
│ │ 5
│ │ │
│ │ │
├───┼──────────┼─────┼─────┼─────┼─────┼─────┼─────
│15 │ q'
│ 7,5 │10,5 │13,4 │16,3 │19,2 │20,9
│ │
5 │ │
│ │ │
│
При внутренней
тепловой изоляции ограждающих конструкций рассчитывается сопротивление
теплопередаче
, (м2 x °C)/Вт, по формуле
, (3)
где
- толщина i-го слоя ограждения, м;
-
коэффициент теплопроводности материала i-го слоя ограждения, Вт/(м
x °C). Принимается по прил. 3 СНиП II-3-79** "Строительная
теплотехника".
Если конструкция
ограждений с теплоизоляцией включает воздушные прослойки, сопротивление
теплопередаче каждой прослойки назначается по табл. 6.
Таблица 6
────────────────────────────────┬──────┬───────┬──────┬──────┬──────┬──────
Толщина
воздушной прослойки, м
│ 0,03 │ 0,04 │
0,05 │ 0,1 │ 0,15 │
0,2
────────────────────────────────┼──────┼───────┼──────┼──────┼──────┼──────
R
, (м2 x °C)/Вт │ 0,28 │ 0,3
│ 0,32 │ 0,38 │ 0,41 │ 0,45
0 │ │ │ │ │ │
Примечание. При
наличии n воздушных прослоек величину
следует умножить на n.
По принятым по
формуле (3) или табл. 6 значениям сопротивления теплопередаче по табл. 7
определяются коэффициенты к компонентам удельных тепловых потерь q, значения
которых приведены в табл. 4.
Таблица 7
────────────────────┬────┬────┬────┬────┬────┬────┬────┬────┬────┬────┬────
R
, (м2 x °C)/Вт
│ 0 │0,1 │0,2
│0,4 │0,6 │0,8 │ 1
│1,2 │1,4 │1,6 │1,8
0 │ │
│ │ │
│ │ │
│ │ │
────────────────────┼────┼────┼────┼────┼────┼────┼────┼────┼────┼────┼────
K │ 1
│0,64│0,47│0,32│0,25│0,2
│0,17│0,15│0,13│0,11│0,1
В тепловых
кассетных установках
Удельный расход
тепловой энергии при прогреве изделий по термосным режимам в типовых кассетах
"Гипростроммаш" приведен в табл. 8.
Таблица 8
──────────┬─────────────────┬─────┬────┬─────┬─────────────────────────────
Шифр │
Габариты │Коли-│g
, │Объем│ Расход тепловой энергии, Q,
установок
│ установки, м │чест-│
м │бето-│ МДж/м3, при разогреве
и
типовых │
│во │т/м3│на, │ изделий
до температуры, °C
проектов │ │изде-│ │м3
├────┬────┬────┬────┬────┬────
Гипро- │ │лий │
│ │ 40 │ 50
│ 60 │ 70 │ 80 │ 90
строммаш │ │ │
│ │ │
│ │ │
│
──────────┼─────────────────┼─────┼────┼─────┼────┼────┼────┼────┼────┼────
СМЖ-253 │8 x 3,76 x 0,16 │ 10
│2,5 │42,05│ 605│ 795│
965│1130│1320│1485
"
│8 x 3,76 x 0,14 │
10 │2,9 │36,79│
690│ 880│1045│1235│1400│1570
"
│8 x 3,76 x 0,12 │
12 │2,8 │37,84│
795│ 965│1130│1320│1570│1655
СМЖ-3212 │6,8 x 3,3 x 0,16 │ 10 │3,1 │28,8 │ 690│
880│ 965│1235│1400│1570
(СМЖ-3312)│ │ │
│ │ │
│ │ │
│
"
│6,8 x 3,3 x 0,14 │ 10
│3,6 │25,2 │ 690│
880│1045│1320│1485│1655
"
│6,8 x 3,3 x 0,12 │ 12
│3,5 │25,9 │ 795│
965│1130│1400│1570│1840
СМЖ-3222 │6,8 x 3,76 x 0,05│ 12 │7,5
│12,24│1675│2010│2280│2720│3160│3330
"
│6,8 x 3,76 x 0,05│ 14
│7,4
│14,28│1570│1925│2280│2640│3055│3330
СМЖ-3302 │8 x 3,3 x 0,16 │ 10
│2,6 │34,56│ 690│ 795│
965│1130│1320│1485
"
│8 x 3,3 x 0,14 │
10 │3 │30,24│ 690│
880│1045│1235│1485│1655
"
│8 x 3,3 x 0,12 │
12 │2,9 │31,1 │
795│ 965│1130│1400│1570│1840
СМЖ-3322 │6,8 x 3,3 x 0,06 │ 12 │8,2
│11,66│1485│1840│2200│2535│2890│3245
"
│6,8 x 3,3 x 0,06 │ 14
│7 │13,6
│1485│1840│2095│2535│2890│3245
7412/1 │6,5 x 3,3 x 0,1 │ 10
│4,2 │18,13│
880│1130│1320│1570│1760│2010
7412/2 │6,5 x 2,78 x 0,1 │ 10 │4,5 │15,05│
880│1130│1320│1570│1840│2010
7412/3 │6,5 x 2,78 x 0,12│ 10 │3,8 │17,4 │
795│1045│1235│1400│1655│1840
7412/4 │6,5 x 2,78 x 0,12│ 10 │4,1 │17,4 │
795│1045│1235│1400│1655│1840
7412/5 │6,5 x 2,78 x 0,14│ 6
│6,1 │
7,69│1045│1320│1570│1840│2095│2365
ПРИМЕР РАСЧЕТА
РАСХОДА ТЕПЛОВОЙ ЭНЕРГИИ
ПРИ ТЕРМОСНЫХ
РЕЖИМАХ
Для расчета расхода
тепловой энергии использованы данные примера, приведенного в
Прил. 3 настоящего Пособия.
Тепловая обработка
железобетонных изделий, приготовленных на цементе I группы класса B22,5 (M300),
осуществляется в блоке камер ямного типа: а) неизолированных с ограждениями из
тяжелого бетона, б) теплоизолированных минераловатными плитами, мм, толщиной 60 с воздушной прослойкой, шириной 35 и
обшивкой стальным листом толщиной 3.
Площадь поверхности
наружных стен блока камер выше нулевой отметки пола
,
площадь поверхности наружных стен блока камер ниже нулевой отметки пола
,
площадь поверхности днища блока камер
,
площадь поверхности крышек
,
площадь поверхности перегородок
.
Объем бетона
прогреваемых изделий в блоке камер
.
Масса металла форм,
приходящаяся на 1 м3 бетона
.
Расчет
варианта I (разогрев изделий
в неизолированных
камерах до температуры 75 °C)
Расход тепловой
энергии на разогрев бетона изделий (по табл. 2)
,
расход тепловой энергии на разогрев металла форм (по табл. 3)
,
расход тепловой энергии на разогрев и компенсацию потерь при остывании
ограждений из тяжелого бетона (по табл. 4):
для наружных стен
выше нулевой отметки пола
,
для наружных стен
выше нулевой отметки пола
,
для днища
,
для крышек
,
для перегородок
.
Рассчитываем суммарные удельные теплопотери по формуле (2)
МДж/м3,
.
Коэффициент K,
учитывающий потери тепла с конденсатом при разогреве изделий до 75 °C,
определяется по табл. 1 - K = 1,06.
Общий расход
тепловой энергии Q, МДж/м3, по формуле (1)
,
Q = 1,06 (107 + 105
+ 247) = 486,5 МДж/м3.
Расчет
варианта II (разогрев изделий
в
теплоизолированных камерах до температуры 70 °C)
Рассчитываем
сопротивление теплопередаче ограждающих конструкций
, м2 x °C/Вт, по формуле (3)
,
где
и
- соответственно толщина слоя тяжелого бетона
(0,3 м) и минераловатной плиты (0,06 м);
и
- соответственно коэффициенты теплопроводности
тяжелого бетона и минераловатной плиты, принимаемые по прил. 3 СНиП II-3-79**:
,
;
-
сопротивление теплопередаче воздушной прослойки шириной 0,35 м, по табл. 6
.
.
Принимаем
и по табл. 7 определяем коэффициент K = 0,145.
Определяем расход
тепловой энергии на разогрев и компенсацию потерь при остывании ограждения (по
табл. 4 и 5) с учетом коэффициента K = 0,145:
для наружных стен
выше нулевой отметки пола
,
для наружных стен
ниже нулевой отметки пола
,
для днища из
керамзитобетонного пустотного настила (по табл. 5)
,
для крышек
,
для перегородок
.
Рассчитываем суммарные удельные теплопотери по формуле (2)
.
Расход тепловой
энергии для разогрева бетона (по табл. 2)
.
Расход тепловой
энергии для разогрева металла форм (по табл. 3)
.
Общий расход
тепловой энергии по формуле (1) Q = 1,055 (100 + 96 + 84) = 295,4 МДж/м3.
Таким образом,
расход тепловой энергии для тепловой обработки железобетонных изделий класса
B22,5 (M300) составляет: в неизолированных камерах - 486 МДж/м3, в
теплоизолированных камерах - 295 МДж/м3.
Приложение
4
ПОДБОР
ДРОССЕЛЬНЫХ ДИАФРАГМ
1. Дроссельные
диафрагмы предназначены для обеспечения дозированной расчетной подачи пара в
тепловую установку в единицу времени.
Монтаж дроссельных
диафрагм следует производить одновременно на всех тепловых установках,
питающихся от каждого отдельного магистрального паропровода. В противном случае
произойдет перераспределение давления и пар будет
поступать в значительно меньшем количестве в установки, оснащенные дроссельными
диафрагмами, что приведет к недогреву изделий.
2. Дроссельные
диафрагмы устанавливаются на паровых вводах в установки как при наличии
автоматизированных систем регулирования температурного режима, так и без них.
При применении автоматических систем регулирования диафрагма подбирается из
условия максимального часового расхода пара. Дроссельные диафрагмы могут
эффективно работать только при оснащении магистральных паропроводов
регуляторами давления пара.
3. Дроссельная
диафрагма представляет собой стальную пластину толщиной 2 - 3 мм, в которой
выполнено отверстие, рассчитанное для пропускания требуемого количества пара
(см. рисунок).
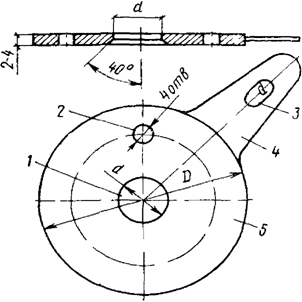
Дроссельная
диафрагма
1 - проходное
отверстие диафрагмы;
2 - крепежные
отверстия; 3 - клеймо;
4 - рукоятка; 5 -
корпус (шайба)
4. Для подбора
диаметра отверстий дроссельных диафрагм первоначально определяется удельный
расчетный расход тепловой энергии Q в соответствии с рекомендациями Прил. 3.