Утвержден и введен в действие
Постановлением
Госстандарта России
от 20 марта 1996 г.
N 185
ГОСУДАРСТВЕННЫЙ СТАНДАРТ РОССИЙСКОЙ ФЕДЕРАЦИИ
РЕЛЬСЫ
МЕТОД ИСПЫТАНИЯ НА КОРРОЗИОННО-УСТАЛОСТНУЮ
ДОЛГОВЕЧНОСТЬ
Rails. Method of test on
corrosion fatigue life
ГОСТ Р 50865-96
Группа В42
ОКП 09 2100;
ОКС 45.080
Дата введения
1 января 1997 года
ПРЕДИСЛОВИЕ
1. Разработан Всероссийским научно-исследовательским институтом
железнодорожного транспорта (ВНИИЖТ).
2. Внесен Госстандартом России.
3. Утвержден и
введен в действие Постановлением Госстандарта России от 20 марта 1996 г. N 185.
4. Введен впервые.
1. ОБЛАСТЬ
ПРИМЕНЕНИЯ
1.1. Настоящий
стандарт устанавливает требования к методу коррозионно-усталостных испытаний
рельсов для определения числа циклов нагружения до
разрушения при заданных параметрах циклической нагрузки и коррозионной
агрессивности среды.
Требования
стандарта являются обязательными, кроме 7.7; 8.3.
Стандарт пригоден
для целей сертификации.
1.2.
Коррозионно-усталостные испытания рельсов проводят с целью:
а) построения
кривой усталости и определения предела выносливости на принятой базе испытания;
б) определения
среднего значения и среднеквадратического отклонения логарифма долговечности
при заданном уровне циклической нагрузки;
в) получения
исходных данных для определения показателей надежности и запасов прочности;
г) определения
остаточного ресурса после определенной наработки;
д) определения
влияния факторов внешней среды на коррозионно-усталостную долговечность
рельсов.
1.3. При проведении
испытаний следует руководствоваться настоящим стандартом, а также ГОСТ 25.507.
2.
НОРМАТИВНЫЕ ССЫЛКИ
В настоящем
стандарте использованы ссылки на следующие стандарты:
ГОСТ 25.502-79.
Расчеты и испытания на прочность в машиностроении. Методы механических
испытаний металлов. Методы испытаний на усталость
ГОСТ 25.505-85.
Расчеты и испытания на прочность. Методы механических испытаний металлов. Метод
испытаний на малоцикловую усталость при термомеханическом
нагружении
ГОСТ 25.507-85.
Расчеты и испытания на прочность в машиностроении. Методы испытания на
усталость при эксплуатационных режимах нагружения.
Общие требования
ГОСТ 27.002-89.
Надежность в технике. Основные понятия. Термины и определения
ГОСТ 23207-78.
Сопротивление усталости. Основные термины, определения и обозначения.
3. СУЩНОСТЬ
МЕТОДА
3.1. Сущность
метода заключается в изгибе полнопрофильной рельсовой
пробы, расположенной на двух опорах головкой вверх, путем приложения
циклической нагрузки в середине пролета. В зоне действия максимальных
напряжений от изгиба создается коррозионная среда и поляризация внешним током в
гальваностатическом или потенциостатическом режиме.
3.2. Влияние
коррозионной среды и внешнего тока оценивается:
а) по изменению
положения кривой ограниченной долговечности;
б) по числу циклов
до разрушения при одинаковой циклической нагрузке;
в) по величине
максимальной циклической нагрузки, которую выдерживают рельсы без разрушения
при заданной базе испытания. В качестве основы для сравнения используются
результаты усталостных испытаний на воздухе.
4.
ТРЕБОВАНИЯ К ОБЪЕКТАМ ИСПЫТАНИЙ
4.1. Объекты
испытаний должны представлять собой полнопрофильные
рельсовые пробы длиной 1200 - 1400 мм.
Рельсовые пробы
должны отбираться на расстоянии не менее 1,5 м от концов рельсов, чтобы
обеспечить единообразие условий холодной правки и уровня остаточных напряжений.
Если задачей
испытания является определение коррозионно-усталостной долговечности зоны
болтовых отверстий, то пробы отбирают от концов рельсов.
4.2. Рельсовые
пробы вырезают из рельса любым способом, кроме ударной или взрывной рубки.
4.3. Все пробы
перед испытанием должны подвергаться внешнему осмотру. Пробы от новых рельсов,
не находившиеся в эксплуатации, имеющие поверхностные дефекты металлургического
происхождения (закаты, волосовины, плены), а также забоины и вмятины,
испытаниям не подлежат.
4.4. Пробы от
рельсов, бывших в эксплуатации, отбираются таким образом, чтобы в центре пробы
одной партии находилась зона, расположенная между шпалами, а в центре проб
другой партии - зона, расположенная на шпале, поскольку характеристики
коррозионно-усталостной долговечности этих партий могут существенно отличаться.
4.5. Перед
проведением коррозионно-усталостных испытаний пробы в зоне контакта со средой
должны быть очищены от загрязнений и обезжирены.
4.6. Для построения
кривых разной вероятности неразрушения, оценки
среднего значения, среднеквадратического отклонения логарифма долговечности
испытывают партию рельсовых проб. Объем партии определяют, исходя из требуемой
точности оценки интересующего параметра, в соответствии с требованиями ГОСТ
25.502.
5.
ТРЕБОВАНИЯ К ИСПЫТАТЕЛЬНОМУ ОБОРУДОВАНИЮ
5.1. Испытания
должны проводиться на испытательных машинах, обеспечивающих требуемый уровень
нагрузки, стабильность максимальной и минимальной нагрузки цикла, частоты нагружения, формы цикла. Допускаемые отклонения и
погрешности оборудования - по ГОСТ 25.502.
5.2. Испытательные
машины должны быть оборудованы:
- автоматическим
выключателем, отключающим машину при изломе рельсовой пробы;
- счетчиком числа
циклов;
- аппаратурой для
автоматического контроля и регулирования заданных параметров нагружения;
- устройством для
подвода жидкой среды в зону возникновения коррозионно-усталостных трещин;
- устройством для
наложения внешнего тока.
5.3. Опорные
устройства должны обеспечивать приложение нагрузки в соответствии со схемой нагружения и не вызывать дополнительных напряжений, не
предусмотренных программой испытания, обеспечивать безопасность обслуживающего
персонала и оборудования при изломе рельсовой пробы.
6.
ТРЕБОВАНИЯ К ЖИДКОЙ СРЕДЕ И ВНЕШНЕМУ ТОКУ
6.1. Химический
состав и рН жидкой среды, создаваемой в зоне возникновения
коррозионно-усталостных трещин, должны моделировать химический состав и рН
среды, встречающейся в эксплуатации. Рекомендуется использовать для
моделирования промышленной среды 1%-ный раствор
серной кислоты, приморской атмосферы и засоленных участков - 3%-ный раствор хлорида натрия. Температура испытания комнатная
- 18 - 24 °С.
6.2. При
прогнозировании коррозионно-усталостной долговечности коррозионная среда должна
создаваться путем прижатия к подошве рельса прокладок или карточек для выправки
пути, увлажненных растворами, указанными в 6.1.
6.3. При сравнении
коррозионно-усталостной долговечности рельсов, изготовленных по различной
технологии, а также определении влияния состава жидкой среды или внешнего тока
жидкая среда должна подводиться к зоне возникновения коррозионно-усталостных
трещин с помощью специальной оснастки, изготовленной из неметаллических
материалов, обеспечивающей такую же площадь контактирования,
как и в эксплуатации. Пример конструкции оснастки приведен на рисунке 1. Контактирование с жидкой средой должно быть в течение всего
периода испытания, если программой испытания не предусмотрено переменное
воздействие жидкой среды с высушиванием.

1 - ванна, 2 -
пористый материал, 3 - электрод,
4 - раствор
электролита, 5 - резиновая шайба
Рисунок 1.
Приспособление для подвода коррозионной среды
и пропуска
электрического тока через зону контакта
подошвы рельса со
средой в процессе
коррозионно-усталостных
испытаний
6.4. Устройство для
пропуска внешнего тока через зону контакта рельсовой пробы с жидкой средой
(растворами электролита), рисунок 2, должно обеспечивать прохождение через
раствор электролита внешнего тока заданного уровня в течение всего периода
испытания, не создавать помехи в работе электрического оборудования
испытательной машины, обеспечивать безопасность обслуживающего персонала.
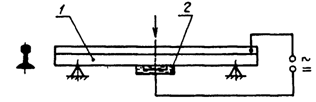
1 - рельсовая
проба, 2 - приспособление для подвода
коррозионной среды
и пропуска электрического тока
Рисунок 2. Схема
испытания рельсовых проб
на коррозионную
усталость
Рекомендуемый
диапазон внешнего тока от 10 до 1000 мА. Устройство должно обеспечивать
возможность проведения испытания при постоянном внешнем токе заданной
полярности и при переменном токе стандартной частоты.
7.
ТРЕБОВАНИЯ К ПРОВЕДЕНИЮ ИСПЫТАНИЙ
7.1. Испытания
проводят на многоцикловую усталость непрерывно до
разрушения рельсовой пробы и определяют циклическую долговечность при заданной
нагрузке.
7.2. Для построения
кривой коррозионной усталости испытывают не менее 8 одинаковых проб (от одного
рельса).
7.3. База испытания
для определения ограниченного предела выносливости при коррозионной усталости должна быть не менее
циклов нагружения.
Для определения предела выносливости на воздухе база испытания должна быть не
менее
циклов.
7.4. Частота
приложения циклической нагрузки при определении коррозионно-усталостной
долговечности должна не превышать 10 Гц.
7.5. При
прогнозировании коррозионно-усталостной долговечности воспроизводят все
основные условия эксплуатации, за исключением длительности воздействия среды.
Влияние концентраторов напряжения в виде коррозионных каверн оценивают по
специальной методике путем нанесения надрезов заданной формы и глубины.
Коэффициент
асимметрии цикла напряжений должен соответствовать значениям коэффициента
асимметрии, характерным для условий эксплуатации.
Примечание. В
подошве рельсов, работающих как балка на упругом основании, коэффициент
асимметрии равен минус 0,2.
7.6. При
сравнительных испытаниях в целях упрощения схемы закрепления рельсовых проб
рекомендуется проводить испытания при коэффициенте асимметрии цикла плюс 0,1.
Допускается использовать результаты испытаний, полученные при асимметрии цикла
0,1, в расчетах на долговечность только после внесения поправки в соответствии
с диаграммой предельных напряжений цикла по ГОСТ 23207.
7.7. Если
целью испытания является определение среднеквадратического отклонения или гамма-процентного ресурса при 4 - 5 уровнях циклической
нагрузки, испытания проводят на большем количестве проб. Число проб на каждом
уровне нагрузки зависит от требуемой точности определения указанных
характеристик и определяется в каждом конкретном случае.
8.
ОБРАБОТКА РЕЗУЛЬТАТОВ ИСПЫТАНИЙ
8.1. По результатам
испытаний на коррозионную усталость производят построение кривой усталости и
определение предела выносливости, соответствующих вероятности разрушения 50%.
Кривые усталости строят в полулогарифмических координатах
;
или в двойных логарифмических координатах
;
.
8.2. По результатам
испытания 5 - 10 образцов кривые усталости строят методом графического
интерполирования или методом наименьших квадратов для линейной зависимости:
y = ах + b, (1)
используя уравнения:
; (2)
. (3)
8.3. Для
аналитического представления результатов испытаний рекомендуется использовать
кинетические уравнения:
степенное
, (4)
которое в линеаризованном виде представляется как:
lgN = lgA + mlgP, (5)
где y = lgN; х = lgР;
а = m; b = lgA
или
логарифмическое:
, (6)
где y = Р; х = lgN;
; b =
В.
8.4.
Целесообразность использования того или иного кинетического уравнения для
обработки результатов коррозионно-усталостных испытаний определяется путем
проверки гипотезы линейности. Гипотезу линейности проверяют путем испытания нескольких
образцов на каждом уровне нагрузки, используемом для построения кривой
усталости. По результатам испытаний определяют коэффициенты в уравнениях
регрессии 4 - 6, средневзвешенную дисперсию экспериментальных точек
относительно средних значений числа циклов на каждом уровне нагрузки, вычисляют
F-критерий и сравнивают с табличным значением.
8.5. Статистические
характеристики долговечности (среднеквадратическое отклонение и гамма-процентный ресурс) определяют обработкой результатов
испытания нескольких образцов на каждом уровне нагрузки в соответствии с ГОСТ
25.502.
9. ПРОТОКОЛ
ИСПЫТАНИЙ
Протокол испытаний
рельсов на коррозионную усталость должен содержать:
- назначение
испытаний;
- тип рельса,
завод-изготовитель, номер плавки, химический состав, механические свойства, вид
термообработки;
- характер
распределения и уровень остаточных напряжений в подошве рельса;
- тип, марку
испытательной машины, основные технические характеристики, класс точности,
заводской и (или) инвентарный номер;
- тип, марку
регистрирующих приборов, заводской и (или) инвентарный номер;
- характеристику
нагрузки (максимальная, минимальная, частота нагружения,
схема нагружения);
- показания
регистрирующих приборов;
- дату начала и
окончания испытаний;
- показания счетчика
числа циклов в начале и в конце испытания или каждой ступени нагрузки;
- характеристику
среды (химический состав раствора, плотность) в зоне возникновения усталостной
трещины;
- описание
устройства для подвода и контроля коррозионной среды;
- число циклов до
разрушения.
Протокол испытаний
подписывается исполнителями и ответственными за испытания.
При проведении
испытаний с целью сертификации в протоколе указывается эта цель
и он утверждается руководителем испытательного центра.