Утверждены:
Управление научно-технической
политики в
строительной отрасли
ПРАВИТЕЛЬСТВО МОСКВЫ
КОМПЛЕКС АРХИТЕКТУРЫ, СТРОИТЕЛЬСТВА,
РАЗВИТИЯ И РЕКОНСТРУКЦИИ ГОРОДА
ТЕХНИЧЕСКИЕ РЕКОМЕНДАЦИИ
ПО КОНСТРУКЦИЯМ И ТЕХНОЛОГИИ СТРОИТЕЛЬСТВА ДОРОГ
В МЕСТАХ, ПОДВЕРЖЕННЫХ УСИЛЕННОМУ ВОЗДЕЙСТВИЮ
ТРАНСПОРТНЫХ НАГРУЗОК
ТР 135-02
Дата введения в
действие
1 июня 2003 года
Разработаны ГУП
"НИИМосстрой", НИИ МК МАДИ (ГТУ).
Утверждены
Управлением научно-технической политики в строительной отрасли.
Вводятся впервые.
"Технические
рекомендации по конструкциям и технологии строительства дорог в местах,
подверженных усиленному воздействию транспортных нагрузок" разработаны в
лаборатории дорожного строительства ГУП "НИИМосстрой"
кандидатами технических наук Л.В. Городецким, Р.И. Бега, старшим научным
сотрудником М.И. Клейман, научным сотрудником А.М. Балашовым, младшим научным сотрудником Н.Н. Маныловой,
ведущим инженером В.Ф. Деминым, инженером М.Ю. Соляниковым
и НИИ МК МАДИ (ГТУ) кандидатами технических наук
Э.В. Котлярским, Ю.Э. Васильевым, О.А. Воейко, старшим научным сотрудником Н.Н. Мироновым, научным
сотрудником М.Н. Алехиной.
Рекомендации
составлены на основе научно-исследовательских и опытно-производственных работ,
выполненных лабораторией дорожного строительства НИИМосстроя
и НИИ МК МАДИ (ГТУ) при строительстве третьего транспортного кольца,
капитальном ремонте Крылатского моста и других объектов, результатов
отечественных и зарубежных исследований других авторов.
Рекомендации
направлены на повышение долговечности и эксплуатационной надежности
автомагистралей, общегородского и районного значений.
Согласованы с ОАО
"Мосинжстрой", институтом "Мосинжпроект", ОАО "Гордорстрой".
1. ОБЩИЕ
ПОЛОЖЕНИЯ
1.1. Настоящие
технические рекомендации распространяются на конструкции и технологии
строительства дорог в местах, подверженных усиленному воздействию транспортных
нагрузок. К ним относятся скоростные автомагистрали типа
третьего транспортного кольца с колонным движением тяжелых транспортных
нагрузок, большим количеством развязок в разных уровнях, въездов и съездов с
уклонами 4% и более и с закруглениями малых радиусов, а также городские дороги
в местах частых торможений и разгонов, в том числе тяжелого общественного
транспорта, на остановках и перекрестках.
1.2. При расчете
таких дорожных одежд следует учитывать одновременное воздействие на покрытие
температурных перепадов и подвижных автомобильных нагрузок, в том числе
касательных (сдвиговых) усилий, возникающих при торможении, разгоне, движении
на уклонах и закруглениях.
1.3. Прочность
конструкции, ровность и устойчивый во времени необходимый коэффициент сцепления
покрытий могут быть достигнуты применением композитных материалов в виде литых
самоуплотняющихся бетонных смесей, жестких бетонных смесей, укладываемых
бетоноукладчиками со скользящими формами и следящим устройством, а также сдвигоустойчивых асфальтобетонных смесей.
Перспективными, особенно для мостовых конструкций, могут рассматриваться литые, в
том числе сероасфальтобетонные смеси.
1.4. Для устройства
оснований рекомендуется применять малоцементные
укатываемые бетонные смеси повышенной деформативности,
литые бетонные смеси, допускается применение пластичных бетонных смесей и
крупнозернистых сдвигоустойчивых асфальтобетонных
смесей, предпочтительно армированных базальтовыми или стальными волокнами.
1.5. Технические
рекомендации разработаны с учетом действующих нормативных документов и альбомов
типовых проектов "Конструкции дорожных одежд для г. Москвы" часть I и
II СК 6101-97, "Конструкции дорожных одежд с использованием продуктов
переработки промышленных и строительных материалов (базальтовых, отходов
бетонных и железобетонных конструкций, асфальтобетонов, изношенных шин и др.),
СК 6117-00.
2.
КОНСТРУКЦИИ ДОРОГ, ПОДВЕРЖЕННЫХ УСИЛЕННОМУ
ВОЗДЕЙСТВИЮ
ТРАНСПОРТНЫХ НАГРУЗОК
Автомагистрали типа
третьего транспортного кольца состоят большей частью из мостов, тоннелей,
эстакад, а искусственные основания дорожных одежд являются жесткими и
малодеформируемыми. Поэтому расчет таких дорожных одежд должен производиться
как на "скальном" основании с учетом физико-механических
характеристик вышележащих слоев.
Для этих
условий наиболее приемлемыми являются бетонные дорожные основания, выполняемые
из таких композитных материалов, как укатываемые или литые бетонные смеси, а
также асфальтобетонные плотные смеси типа Б. В остальных случаях следует
применять дорожные конструкции, близкие к традиционным, но с повышенными
требованиями к устройству земляного полотна, ровности, сдвигоустойчивости,
колееобразованию и коэффициенту сцепления покрытия.
2.1.
ИСХОДНЫЕ ДАННЫЕ ДЛЯ РАСЧЕТА И КОНСТРУИРОВАНИЯ
2.1.1.
Улицы и дороги г. Москвы, подверженные усиленному воздействию транспортных
нагрузок, в зависимости от интенсивности движения и назначения подразделяются
на магистральные улицы общегородского значения с интенсивностью движения более
3000 автомобилей в сутки (группа А) и районного значения с интенсивностью более
1000 автомобилей в сутки (группа Б).
К таким дорогам
относятся также федеральные скоростные магистрали типа МКАД, III-го транспортного кольца, по которым в часы пик
осуществляется колонное движение транспорта.
Усиленному износу
подвергаются также места торможений и разгона автотранспорта, в том числе
перекрестки и остановки общественного транспорта.
2.1.2. По
назначению магистральные улицы общегородского значения осуществляют
транспортную связь между жилыми, промышленными складскими районами, а также с
центром города, объектами общегородского значения, федеральными скоростными
магистралями и автомобильными дорогами общей сети.
Магистральные улицы
районного значения осуществляют местную транспортную связь в пределах жилых и
промышленных районов, а также связь с магистральными улицами общегородского
значения и скоростными дорогами.
2.1.3.
Перечисленные в пп. 2.1.1 и 2.1.2 городские дороги
рассчитываются и проектируются под нагрузку Н-30 с учетом температурных, а
также горизонтальных нагрузок (Приложения 1, 2) и особенностей принятых
конструктивных решений.
Для нормативной
нагрузки Н-30:
Масса
нагруженного автомобиля - 30
т
Статическая нагрузка на ось
- 120 кН (12 т)
Статическая нагрузка на колесо
- 60 кН (6,0 т)
Диаметр
отпечатка колеса - 0,36
м
Расчетная нагрузка
на ось или колесо автомобиля определяется как произведение нормативной нагрузки
на коэффициенты перегрузки и динамики. Коэффициент перегрузки П принимается от 1,0 до 1,4 в зависимости от условий
эксплуатации. Коэффициент динамики
.
При расчете
несущего слоя основания на воздействие построечного транспорта П = 1,1 и
суточные расчетные колебания температуры на
поверхности открытого цементобетонного слоя
принимают равным 17 °C.
2.1.4. Нормативные
характеристики цементобетона, требуемые для
строительства бетонных покрытий и оснований, приведены в таблице 2.1.
Таблица 2.1
Нормативная
характеристика бетонов
┌───┬────────────┬─────────┬───────────┬───────────┬─────────┬────────────┐
│
N │Наименование│ Класс │Нормативная│ Модуль
│Минималь-│ Примечание │
│п/п│ материала
│бетона по│ прочность │ упругости │ная марка│
│
│ │ │прочности│ на
│ E, МПа, │по моро-
│ │
│ │ │на сжатие│растяжение
│ не более │зостой- │ │
│ │ │ (марка) │при изгибе,│ │кости в │ │
│ │ │ │ н
│
│солевых │ │
│ │ │ │ R , МПа │ │растворах│ │
│ │ │ │ ри │ │ │ │
├───┴────────────┴─────────┴───────────┴───────────┴─────────┴────────────┤
│ Для покрытий │
├───┬────────────┬─────────┬───────────┬───────────┬─────────┬────────────┤
│
1 │Цементобетон│ В
│ │ │ 200
│Осадка │
├───┤
├─────────┼───────────┼───────────┼─────────┤конуса
при │
│
2 │ │ В30
│ 5,0 │
40000 │ 200
│укладке │
│ │ │ (М400) │ │ │ │комплектом │
├───┤
├─────────┼───────────┼───────────┼─────────┤со │
│
3 │ │ В27,5
│ 4,5 │
35000 │ 200
│скользящими │
│ │ │ (М350) │ │ │ │формами - │
├───┤
├─────────┼───────────┼───────────┼─────────┤2
- 4 см, │
│
4 │ │ В25
│ 4,0 │
29000 │ 200
│литьевым │
│ │ │ (М300) │ │ │ │методом - │
│ │ │ для
│ │ │ │18 - 14 │
│ │ │тротуаров│ │ │ │(12) см │
├───┴────────────┴─────────┴───────────┴───────────┴─────────┴────────────┤
│ Для
оснований │
├───┬────────────┬─────────┬────┬──────┬─────┬─────┬────┬────┬────────────┤
│ │ │ │из │из │из
│из │из │из
│ │
│ │ │ │ли-
│укаты-│литой│ука-
│ли- │ука-│ │
│ │ │ │той │ваемой│смеси│тыва-│той │ты-
│ │
│ │ │ │сме-│смеси │ │емой
│сме-│вае-│ │
│ │ │ │си │
│ │смеси│си
│мой │ │
│ │ │ │ │
│ │ │
│сме-│ │
│ │ │ │ │
│ │ │
│си │ │
├───┤
├─────────┼────┼──────┼─────┼─────┼────┼────┤ │
│
5 │Цементобето-│ В25 │4,0 │ 3,4 │29000│29000│200 │200
│Осадка │
│ │ны литые
и │ (М300) │
│ │ │
│ │ │конуса при │
├───┤укатываемые
├─────────┼────┼──────┼─────┼─────┼────┼────┤укладке │
│
6 │ │ В22,5
│ │ │ │
│200 │150 │литьевым
│
│ │
│ (М300) │
│ │ │
│ │ │методом - │
├───┤
├─────────┼────┼──────┼─────┼─────┼────┼────┤18
- 14 │
│
7 │ │ В15
│3,0 │ 2,7
│24000│20000│100 │100 │(12) см, │
│ │ │ (М200) │
│ │ │
│ │ │жесткость │
├───┤
├─────────┼────┼──────┼─────┼─────┼────┼────┤укатываемого│
│
8 │ │ В7,5 │1,8 │ 1,6 │13000│12000│100 │100
│бетона │
│ │ │ (М100) │
│ │ │
│ │ │90 - 120 с │
└───┴────────────┴─────────┴────┴──────┴─────┴─────┴────┴────┴────────────┘
2.1.5. При
значениях
и E, отличающихся от приведенных в таблице 1,
например, при использовании композитных материалов с добавлением битумной
эмульсии, полимеров, фибробетона, других добавок,
допускается принимать другие их значения, согласованные в установленном
порядке.
2.1.6. Расчетные
сопротивления цементобетона определяют по формулам:
- при расчете на
прочность
;
- при расчете на
выносливость
,
где
- коэффициент однородности материала;
- коэффициент роста прочности материала во
времени;
- коэффициент усталости материала.
Коэффициент
однородности материалов при расчете на 1-й и 2-й стадиях строительства
принимают равным 0,7. При расчете слоя основания на
непосредственное воздействие ограниченного количества проходов построечного
транспорта для материала нижнего слоя принимают
.
Коэффициент
принимают в зависимости от времени, прошедшего
с момента укладки слоя: через 28 суток - 1,0; через 1 год - 1,25; через 0,5
года - 1,15.
Коэффициент
усталости материала принимают: для оснований на 1-ой стадии строительства из
литой смеси - 0,7; из укатываемого бетона - 0,65; для цементобетонных покрытий
- 0,57; для оснований при последующей укладке покрытия не позднее чем через 7
суток - 0,52.
2.1.7. При расчете
конструктивных слоев дорожной одежды из цементобетона
на температурные воздействия следует учитывать уменьшение (релаксацию) усилий
вследствие ползучести материала и возникновения неупругих деформаций в
растянутой зоне сечения.
Этот фактор
учитывают умножением расчетных усилий (напряжений) на коэффициенты релаксации
и пластичности
,
принимаемые по таблице 2.2.
Таблица 2.2
Коэффициенты
релаксации и пластичности цементобетона
┌─────────────────────────┬──────────────────────┬────────────────────────┐
│Вид
предельного состояния│Коэффициент релаксации│Коэффициент пластичности│
│ │ К │ К │
│ │ р │ п │
├─────────────────────────┼──────────────────────┼────────────────────────┤
│Прочность │ 0,75 │ 0,60 │
├─────────────────────────┼──────────────────────┼────────────────────────┤
│Выносливость:
1 стадия │ 0,85 │ 0,75 │
├─────────────────────────┼──────────────────────┼────────────────────────┤
│ 2 стадия │ 0,90 │ 0,80 │
└─────────────────────────┴──────────────────────┴────────────────────────┘
2.1.8. Коэффициент
линейных температурных деформаций следует принимать равным:
- для цементобетона на гранитном щебне
;
- для цементобетона на известняковом щебне
.
2.1.9. Коэффициент
Пуассона
принимают равным:
- для цементобетона 0,15;
- для грунта 0,30.
2.1.10. Методика расчета дорожных одежд с цементобетонным покрытием на
бетонном основании, а также методика расчета различных бетонных оснований под
асфальтобетонные покрытия с учетом статических, температурных, подвижных
нагрузок, усилий торможения и разгона, выносливости и усталостной прочности
материала, роста его прочности во времени, стадийности строительства основания
и покрытия и других факторов приведена в Приложениях 1 и 2, а также в
"Технических рекомендациях по применению укатываемого малоцементного бетона в конструкциях дорожных одежд" ТР 138-03.
2.1.11. При
использовании в предлагаемых конструкциях различных слоев из асфальтобетонных
смесей к ним предъявляется ряд требований, обеспечивающих, прежде всего,
прочность при положительных температурах воздуха, сдвигоустойчивость,
трещиностойкость и водоустойчивость. В таблице 2.3
представлены нормативы по указанным показателям по рекомендованным видам
асфальтобетона.
Таблица 2.3
Нормативные
характеристики для асфальтобетонов
(применительно к
II-ой дорожно-климатической зоне)
┌───┬──────────────────────────────┬──────────────┬───────────────────────┐
│
N │ Наименование показателей │ Нормативное │ Нормативный документ │
│п/п│ │ значение
│
│
├───┼──────────────────────────────┼──────────────┼───────────────────────┤
│
1 │ 2 │ 3
│ 4 │
├───┼──────────────────────────────┼──────────────┼───────────────────────┤
│
1 │Предел прочности при сжатии
│ │ │
│ │при температуре 50 °C, МПа, │ │ │
│ │не менее, │ │ │
│ │для асфальтобетонов: │ │ │
│ │ высокоплотных │ 1,1
│ ГОСТ 9128-97 │
│ │ плотных типов: │ │ │
│ │
А
│ 1,0 │ " │
│ │
Б
│ 1,2
│ " │
│ │ пористых │ 0,7
│ " │
│ │ высокопористых │ 0,7
│ " │
│ │ плотных
крупнозернистых, │не нормируется│ ТУ 400-24-107-91* │
│ │тип II │ │ │
│ │ литых, тип
II │ 1,0
│ ТУ 400-24-158-89* │
│ │ литых сероасфальтобетонов
│ 1,2 │ТУ 5718-002-53737504-01│
├───┼──────────────────────────────┼──────────────┼───────────────────────┤
│
2 │Сдвигоустойчивость по: │ │ │
│ │- коэффициенту внутреннего │ │ │
│ │трения, МПа, не менее, │ │ │
│ │для асфальтобетонов, типов: │ │ │
│ │ высокоплотных │ 0,87
│ ГОСТ 9128-97 │
│ │ плотных, тип А │ 0,87
│ " │
│ │ плотных, тип В │ 0,81
│ " │
│ │- сцеплению при сдвиге │ │ │
│ │при 50 °C, не менее, │ │ │
│ │для асфальтобетонов, типов: │ │ │
│ │ высокоплотных │ 0,27
│ " │
│ │ плотных, тип А │ 0,25
│ " │
│ │ плотных, тип В │ 0,37
│ " │
├───┼──────────────────────────────┼──────────────┼───────────────────────┤
│
3 │Трещиностойкость по прочности │ │ │
│ │при расколе при 0 °C для всех
│ │ │
│ │типов асфальтобетона, МПа: │ │ │
│ │ не менее │ 3,5
│ ГОСТ 9128-97 │
│ │ не более │ 6,0
│ " │
├───┼──────────────────────────────┼──────────────┼───────────────────────┤
│
4 │Водостойкость, не менее,
│ │ │
│ │для асфальтобетонов: │ │ │
│ │ высокоплотных │ 0,95
│ ГОСТ 9128-97 │
│ │ плотных типов: │ │ │
│ │
А
│ 0,90 │ " │
│ │
Б │ 0,90
│ " │
│ │ пористых │ 0,70
│ " │
│ │ высокопористых │ 0,70
│ " │
│ │ плотных
крупнозернистых, │не
нормируется│ ТУ
400-24-158-91* │
│ │тип I │ │ │
│ │ литых сероасфальтобетонных
│ " │ТУ 5718-02-53737504-01 │
│ │ литых │ " │
ТУ 400-24-158-89* │
├───┼──────────────────────────────┼──────────────┼───────────────────────┤
│
5 │Глубина вдавливания штампа
│ │ │
│ │при 40 °C, мм, │ │ │
│ │для асфальтобетонов из: │ │ │
│ │ литых II и III типов │ 1 - 4
│ ТУ 400-24-158-89* │
│ │ литых сероасфальтобетонных
│ 1 - 5 │ТУ 5718-02-53737504-01 │
└───┴──────────────────────────────┴──────────────┴───────────────────────┘
2.1.12. Конструкции
дорожной одежды (рис. 2.1 - 2.3), где роль несущего слоя выполняет упругая
монолитная плита из асфальтобетона, рассчитываются в соответствии с
рекомендациями ВСН-5-92 "Инструкция по расчету и конструированию дорожных
одежд с монолитными асфальтобетонными покрытиями" с изменениями и
дополнениями от 27.10.1996. В этом случае оперируют прочностными и упругими
характеристиками асфальтобетонов, определенными по методике НИИМосстроя
при температуре 0 °C под воздействием кратковременных динамических нагрузок.
Значения этих параметров следует принимать по таблице 2.4.
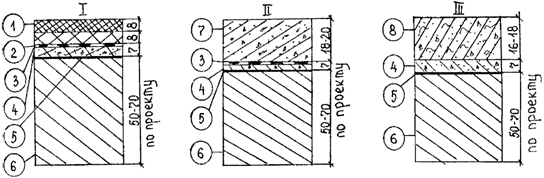
Рис. 2.1.
Конструкции дорожных одежд в зоне искусственных
сооружений на
жестком (скальном) основании
1 - асфальтобетон
высокоплотный или плотный, тип А
по ГОСТ 9128-97; 2
- асфальтобетон крупнозернистый плотный,
тип II по ТУ
400-24-107-91*, пористый по ГОСТ 9128-97;
3 - базальтовая
сетка по битумной эмульсии;
4 - выравнивающий
слой из тяжелого мелкозернистого бетона;
5 - битумная
эмульсия; 6 - несущая железобетонная плита
с коэффициентом
постели, близким к скальному основанию
(по типу Лефортовского тоннеля); 7 - монолитный бетон
(В40, F200 в солях,
W12, B < 5%); 8 - монолитный
фибробетон (В40, F200 в солях, W12, B < 5%)
Примечание. Размеры
указаны в см.
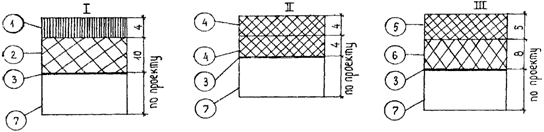
Рис. 2.2.
Дорожные конструкции для мостовых
переходов с
металлическими пролетными строениями
1 - литой
асфальтобетон, тип I, II по ТУ 400-24-58-89*;
2 - асфальтобетон
крупнозернистый пористый или
высокопористый по
ГОСТ 9128-97; 3 - гидроизоляционная
мастика типа "Битрек" по битумной эмульсии;
4 - сероасфальтобетон по ТУ 5718-002-53737504-01;
5 - асфальтобетон
мелкозернистый, тип А по ГОСТ 9128-97*;
6 - асфальтобетон
крупнозернистый, тип Б по ГОСТ 9128-97*;
7 - металлическое
пролетное строение
Примечание. Размеры
указаны в см.
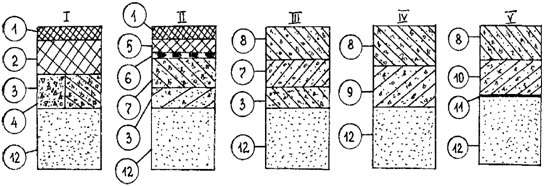
Рис. 2.3.
Варианты конструкций
дорожных одежд на
упругом основании
1 - асфальтобетон
мелкозернистый высокоплотный,
плотный тип А по ГОСТ 9128-97; 2 - монолитная плита
из асфальтобетона
крупнозернистого плотного типа II
по ТУ
400-24-107-91*; 3 - малоцементный укатываемый бетон
В7,5
(М100); 4 - уплотняемая щебеночная крупнозернистая
смесь тип I по ТУ
400-24-150-86; 5 - асфальтобетон
крупнозернистый,
плотный, тип Б по ГОСТ 9128-97*;
6 - базальтовая
сетка по битумной эмульсии; 7 - бетон
из литых или
пластичных смесей В22,5 (М300), P150 в солях;
8 - бетон из литых
или жестких смесей В30 (М400), P200
в солях; 9 - малоцементный укатываемый бетон
В15 - В22,5 (М200 -
М300), P150 в солях с укладкой двумя
равными слоями; 10
- фибробетон из литых смесей В22,5
(М300), P150 в
солях; 11 - полиэтиленовая пленка
или пергамин или
другой пленочный материал;
12 - песок с
коэффициентом фильтрации не менее 4 м/сутки
Таблица 2.4
Прочностные
и упругие характеристики асфальтобетонов
┌───┬────────────────────────────┬──────────────────────────┬─────────────┐
│
N │ Вид и тип асфальтобетона │
Значения показателей │
Коэффициент │
│п/п│ │ упругих и прочностных │однородности,│
│ │ │ свойств при изгибе │
К │
│ │
├─────────────┬────────────┤ о
│
│ │ │ изг │
E , МПа │ │
│ │ │ R , МПа
│ изг │ │
│ │ │ раст │ │ │
├───┼────────────────────────────┼─────────────┼────────────┼─────────────┤
│
1 │Плотный мелкозернистый типа:│ │ │ │
│ │ А │ 4,5
│ 6,0 │
0,70 │
│ │ Б │ 6
│ 9,5
│ 0,68 │
├───┼────────────────────────────┼─────────────┼────────────┼─────────────┤
│
2 │Высокоплотный
│ 4,0 │
6,0 │ 0,68
│
├───┼────────────────────────────┼─────────────┼────────────┼─────────────┤
│
3 │Крупнозернистый, тип II
│ 3,5 │
12,0 │ 0,62
│
├───┼────────────────────────────┼─────────────┼────────────┼─────────────┤
│
4 │Литые асфальтобетоны
│ 6,5 │
8,0 │ 0,75
│
│ │
сероасфальтобетоны │
7,0 │ 8,5
│ 0,75 │
└───┴────────────────────────────┴─────────────┴────────────┴─────────────┘
Примечание.
Принятые обозначения:
- прочность на растяжение при изгибе;
- модуль упругости при 0 °C.
2.2.
КОНСТРУКЦИИ ДОРОЖНЫХ ОДЕЖД СКОРОСТНЫХ АВТОМАГИСТРАЛЕЙ
В ЗОНЕ
ИСКУССТВЕННЫХ СООРУЖЕНИЙ НА ЖЕСТКОМ ОСНОВАНИИ
2.2.1. Под жестким
основанием подразумеваются тоннели, эстакады, мосты, выполненные из
высокопрочных железобетонных конструкций, коэффициент постели которых
приближается к скальному основанию и составляет более 1000 кг/см3. В этом
случае модуль упругости конструктивных слоев дорожных одежд уменьшается не
сверху вниз, как это принято для конструкций на упругом основании, а снизу
вверх.
На рис. 2.1
показаны принципиальные схемы таких конструкций.
2.2.2. Учитывая
особенности работы таких конструкций, общую толщину асфальтобетонного покрытия
следует принимать не менее 16 см (рис. 2.1).
Для
асфальтобетонного или бетонного покрытия (рис. 2.1 - I, II) с целью уменьшения
влияния разности деформаций с основанием выравнивающий слой из тяжелого
мелкозернистого бетона класса по прочности В25 - В27,5 следует укладывать по
слою битумной эмульсии, а между покрытием и выравнивающим слоем укладывать
базальтовую сетку с размером ячеек 25 x 25 мм по битумной эмульсии.
2.2.3. При
применении в покрытии монолитного фибробетона (рис.
2.1, III) базальтовая сетка может не укладываться, а толщина покрытия
уменьшается до 18 - 20 см (по расчету).
2.2.4. На мостовых
переходах, особенно с металлическими пролетными строениями, где большое
значение имеют не только эксплуатационные характеристики покрытий, но и их вес,
рекомендуются конструкции, представленные на рис. 2.2, с покрытиями из литого
асфальтобетона, сероасфальтобетона и плотного
мелкозернистого асфальтобетона.
2.2.5. Принимая во
внимание, что посередине некоторых мостов в замковой части (типа моста в
"Крылатском") вертикальные деформации значительны, рекомендуется в
этих случаях принимать конструкцию покрытия наиболее прочную на растяжение при
изгибе, эластичную и тонкую (рис. 2.2 варианты I и II).
2.3.
КОНСТРУКЦИИ ДОРОЖНЫХ ОДЕЖД НА УПРУГОМ ОСНОВАНИИ
2.3.1. Для
повышения эксплуатационной надежности конструкций на упругом основании в
местах, подверженных усиленному воздействию транспортных нагрузок,
рекомендуется более широко применять монолитные цементобетонные покрытия, а
также асфальтобетонные на различных основаниях. При этом особое внимание
следует уделять подготовке и уплотнению земляного полотна.
На рис. 2.3
представлены варианты конструкций, которые рекомендуются для практического
применения.
3.
ТРЕБОВАНИЯ К МАТЕРИАЛАМ КОНСТРУКТИВНЫХ СЛОЕВ
3.1. Материалы,
применяемые в конструктивных слоях дорожных одежд, должны удовлетворять
требованиям соответствующих нормативных документов и настоящих рекомендаций.
3.2. Для устройства
песчаного подстилающего слоя могут быть использованы пески природные или
искусственные, удовлетворяющие требованиям ГОСТ 8736-93, с коэффициентом
фильтрации не менее 4 м/сутки при ширине дна корыта до 12 м, а при ширине более
12 м К >= 4 м/сутки.
3.3. Для оснований
дорог следует использовать крупнозернистые смеси первого типа в соответствии с
требованиями ТУ 400-24-107-91* и таблицы 3.1.
Таблица 3.1
Зерновой состав
щебеночной смеси
Тип смеси
|
Содержание в смеси частиц, % от
массы,
проходящих через сито с размером
отверстий, мм
|
70
|
40
|
20
|
10
|
5
|
0,63
|
не
менее
0,005
|
Крупнозернистая,
I тип
|
80
- 100
|
40
- 50
|
20
- 30
|
15
- 25
|
12
- 20
|
5
- 10
|
0 - 3
|
3.4. Для
приготовления бетонных смесей в качестве вяжущего следует использовать
портландцемент без минеральных добавок марок не ниже "400",
отвечающий требованиям ГОСТ 10178-85*. В клинкере цемента, применяемого для
устройства бетонных покрытий и оснований, содержание трехкальциевого
алюмината не должно быть более 6 и 10% соответственно.
3.5. Пески для
приготовления бетонных смесей применяются природные, кварцевые или
полевошпатовые в чистом виде или с добавками. В качестве добавок могут быть
использованы искусственные пески, полученные дроблением прочных, морозостойких
пород. Допускается также применение одних искусственных песков. Пески должны
удовлетворять требованиям ГОСТ 8736-93*. Модуль крупности песков должен быть
более 2,0. Содержание глинистых, илистых или пылеватых частиц в песке,
предназначенном для устройства оснований и покрытий, не должно превышать по
массе 3% и 1% соответственно.
3.6. При приготовлении бетонных смесей, предназначенных для покрытий,
следует применять щебень из горных пород по ГОСТ 8267-93, для оснований -
гравий по ГОСТ 8267-93 или щебень из гравия по ГОСТ 8267-93 с размером зерен:
для покрытий - не более 20 мм, для оснований - не более 40 мм, для оснований из
укатываемого бетона не более 70 мм.
3.7. Щебень и
гравий должны разделяться на фракции 5 - 10, 10 - 20, 20 - 40 мм, 40 - 70 мм.
3.8. Зерновой
состав щебня (гравия) должен удовлетворять следующим требованиям: полный
остаток на ситах по массе должен быть для
;
;
.
3.9. Гравий и
щебень из гравия применяется только после промывки или сухой очистки.
Содержание глинистых, илистых и пылевидных частиц из горных пород должно быть
не более 1% по массе. Допускается применение щебня и щебня из гравия с
содержанием загрязнения не более 3% по массе в бетонных смесях, укладываемых в
основание дороги.
3.10. Марка щебня
по прочности в зависимости от дробимости при сжатии в
цилиндре исходной породы в водонасыщенном состоянии
должна быть не выше ДР-16 (не ниже 120 МПа) для изверженных пород, используемых
в бетонных смесях покрытий, и не выше ДР-15 (не ниже 80 МПа) для осадочных
пород - в бетонных основаниях дорог.
3.11. При
использовании в основаниях дисперсно-армированных литых смесей или укатываемых
бетонов допускается применение заполнителей из осадочных пород ДР-19 (60 МПа).
В этом случае для укатываемых бетонов рекомендуется использовать
фракционированный щебень крупностью 5 - 10, 10 - 20, 20 - 40 мм с их процентным
содержанием 15 - 25, 20 - 35 и 40 - 55% по массе соответственно. Допускается
также применение щебня непрерывной гранулометрии
5 - 40 мм.
3.12. Для получения
литых бетонных смесей с начальной осадкой конуса 4 - 5 см можно применять
добавки-суперпластификаторы на основе
меламиноформальдегидных или нафталиноформальдегидных
сульфированных смол, а в отдельных случаях - добавки типа мегносульфонатов.
3.13. Добавки-суперпластификаторы должны удовлетворять требованиям,
приведенным в таблице 3.2.
Таблица 3.2
Характеристика суперпластификаторов
┌──────────────────────────────────────────────┬─────────────┬────────────┐
│ Свойства суперпластификаторов │ Размерность │ Показатели
│
├──────────────────────────────────────────────┼─────────────┼────────────┤
│Содержание
вредных материалов
│ % │
20 - 40 │
│Плотность
│ г/см3 │ 1,1 - 1,22 │
│Водородный
показатель
│ pH │
7 - 9 │
│Вязкость │ Сп │
20 - 45 │
└──────────────────────────────────────────────┴─────────────┴────────────┘
3.14. При
использовании в качестве суперпластификатора водного
раствора добавки С-3 следует иметь в виду, что она не меняет своих свойств при нагреве до +85 °C и замораживании до -40 °C с
последующим оттаиванием.
Образующийся при
низкой положительной температуре (уже при плюс 5 °C и
ниже) осадок добавки растворяют подогревом ее жидкой фазы острым паром или
подогретой водой с последующим тщательным перемешиванием раствора.
Физические свойства
растворов С-3 при температуре плюс 20 °C приведены в таблице 3.3.
Таблица 3.3
Свойства водных
растворов суперпластификатора С-3 при 20 °C
┌─────────────────┬────────────────────┬────────────────────┬─────────────┐
│ Концентрация
│Плотность раствора, │ Содержание сухого │Теплоемкость,│
│ раствора, %
│ г/см3 │ вещества, г/л │
Дж/°C │
├─────────────────┼────────────────────┼────────────────────┼─────────────┤
│ 0
│ 0,998 │ 0 │ 4,2
│
│ 2
│ 1,008 │ 20,2 │ 4,150
│
│ 5
│ 1,023 │ 51,2 │ 4,074
│
│ 7
│ 1,033
│ 72,3 │ 4,024
│
│ 10
│ 1,049 │ 104,9 │ 3,948
│
│ 12
│ 1,059 │ 127,0 │ 3,898
│
│ 15
│ 1,074 │ 161,1 │ 3,822
│
│ 20
│ 1,099 │ 219,8 │ 3,696
│
│ 25
│ 1,125 │ 281,1 │ 3,570
│
│ 30
│ 1,150 │ 344,9 │ 3,444
│
│
33 │ 1,165 │ 384,4 │ 3,368
│
│ 35
│ 1,175 │ 411,3 │ 3,318
│
│ 37
│ 1,185 │ 438,5 │ 3,268
│
│ 40
│ 1,200 │ 480,2 │ 3,192
│
└─────────────────┴────────────────────┴────────────────────┴─────────────┘
3.15. При
отрицательных температурах воздуха для устройства дорожных конструкций из литых
бетонных смесей следует применять комплексные добавки: суперпластификаторы
и противоморозные добавки.
В качестве
противоморозных добавок для смесей без металлической фибры используются
хлористые соли натрия и калия (НХ, ХК), нитрата натрия (НН),
нитрит-нитрат-хлорид натрия (ННХН) или во всех случаях добавки формиата натрия
и гидрозима, не вызывающих коррозию металла.
Оптимальное
количество противоморозных добавок при применении суперпластификатора
С-3 в количестве до 1,0% от массы цемента назначается в соответствии с таблицей
3.4.
Таблица 3.4
Оптимальное
количество противоморозных добавок
для смесей,
твердеющих при отрицательных температурах
┌────────────────────┬────────────────────────────────────────────────────┐
│ Температура │
Содержание безводных солей, % от массы цемента │
│твердения
бетона,
°C├─────────┬─────────┬─────────┬──────┬──────┬────────┤
│ │ХН (NaCl)│ХК (CaCl)│НН (NaO )│ ННХК │ ФН
│Гидрозим│
│ │ │ │ 2 │ │ │ │
├────────────────────┼─────────┼─────────┼─────────┼──────┼──────┼────────┤
│ -5 │ 2
│ 2 │
- │ -
│ - │
- │
│ -5 │ 3
│ - │
- │ -
│ - │
- │
│ -5 │ -
│ - │
4 │ -
│ - │
- │
│ -5 │ -
│ - │
- │ 2
│ - │
- │
│ -5 │ -
│ - │
- │ -
│ 1,0 │ 0,5
│
│ -10 │ -
│ 4 │
- │ 3
│ - │
- │
│ -10
│ 5
│ - │
- │ -
│ - │
- │
│ -10 │ -
│ 8 │
- │ -
│ - │
- │
│ -10 │ -
│ - │
6 │ -
│ - │
- │
│ -10 │ -
│ - │
- │ -
│ 2,0 │ 1,0
│
│ -15 │ -
│ - │
8 │ -
│ - │
- │
│ -15 │ -
│ - │
- │ 6
│ - │
- │
│ -15 │ -
│ - │
- │ -
│ 4,0 │ 2,0
│
└────────────────────┴─────────┴─────────┴─────────┴──────┴──────┴────────┘
3.16. Для повышения
физико-механических показателей бетона следует использовать различные виды
металлических фибр, выпускаемых в г. Москве, Санкт-Петербурге, Кургане и др. Стальные
фибры должны удовлетворять требованиям ТУ 1276-001-40610949-95, ТУ
5263-001-04697311-96, разработанных ЗАО "Фибробетон",
АОЗТ "Курганстальмост" (табл. 3.5).
Таблица 3.5
Характеристика
рекомендуемых стальных фибр
для
дисперсно-армированных дорожных бетонов
┌────────────────────────────────────┬─────────────────┬──────────────────┐
│ Характеристика фибр │ Размерность
│ Показатели │
├────────────────────────────────────┼─────────────────┼──────────────────┤
│Длина
(L)
│ мм │ 35 - 40 │
│Диаметр
(d) │ мм
│ 0,4 - 0,7 │
│L/d │ -
│ 80 - 100 │
│Временное
сопротивление разрыву │ МПа
│ 400 - 1100 │
│Относительное
удлинение │ %
│ 14 - 8 │
└────────────────────────────────────┴─────────────────┴──────────────────┘
3.17. Для
распределения возникающих растягивающих напряжений при изгибе несущих дорожных
слоев следует использовать сетки из базальтового волокна марки СБП-Д в
соответствии с требованиями ТУ 218 РФ-001-0520477. Характеристика базальтовой
сетки представлена в таблице 3.6
Таблица 3.6
Характеристика
базальтовой сетки СБП-Д
┌────────────────────────────────────────┬───────────┬────────────────────┐
│ Характеристика │Размерность│ Показатели │
├────────────────────────────────────────┼───────────┼────────────────────┤
│Поверхностная
масса │ г/м2 │
320 +/- 40 │
│Размер
ячейки в свету
│ мм │ 25 x 25 (50 x 50) │
│Плотность
сетки:
│ │ │
│
- по основе │ ровин/мм │40 +/- 2 (20 +/- 2) │
│
- по углу
│ " │40 +/- 2 (20 +/- 2) │
│Разрывная
нагрузка, не менее:
│ │ │
│
- по основе
│ кН/м │ 45 │
│
- по углу
│ " │ 40 │
│Удлинение
по основе при разрыве,
│ % │ 4 +/- 1 │
│не
более
│ │ │
│Адгезия
к битуму, не менее
│ % │ 96 │
│Прочность
в узлах, не менее
│ кг │ 2 │
│Содержание
связующего, не менее │ %
│ 20 │
│Ширина │ м │100 +/- 5, 200 +/- 5│
└────────────────────────────────────────┴───────────┴────────────────────┘
3.18.
Конструктивные слои из асфальтобетона в предлагаемых конструкциях в большинстве
случаев выполняются из асфальтобетонных смесей по ГОСТ 9128-97,
регламентирующему специфические требования к минеральным материалам и битуму,
которые не вступают в противоречие с требованиями ГОСТ 8267-93 на щебень, ГОСТ
8736-93 на песок, ГОСТ 16557-78 на минеральный порошок и ГОСТ 22245-90 на
битумы.
3.19. Для
устройства монолитной упругой плиты (конструкция 3-I) рекомендуются к
применению асфальтобетонные смеси типа II по ТУ 400-24-107-91*, которые
выпускаются на традиционных материалах с некоторыми изменениями по прочности
применяемого щебня, как это указано в таблице 3.7.
Таблица 3.7
Марки щебня
Наименование показателя
|
Марка
по видам материала, не ниже
|
горные породы
|
Щебень
из
гравия
|
осадочные
|
изверженные
|
Дробимость щебня при сжатии
(раздавливании) в цилиндре
|
600
|
800
|
Др
12
|
Износ
щебня в полочном барабане
|
И-III
|
И-III
|
-
|
При выборе вязких
битумов для смесей этого типа предпочтение отдается термостойким битумам с
температурой размягчения по методу КиШ не ниже 50 °C
с пределами колебания показателя глубины проникания иглы
при 25 °C 10 - 20 единиц.
3.20. При подборе
асфальтобетонных смесей, формирующих монолитную плиту, следует учитывать, что
пористость минерального остова асфальтобетона должна составлять 15 - 19% по
объему, остаточная пористость 2 - 7% по объему и водонасыщение 1,5 - 6,0 по
объему.
Температура готовой
смеси при выпуске из смесителя должна быть в пределах 140 - 160 °C.
3.21. В дорожных конструкциях для мостовых переходов с металлическими
пролетными строениями в одном из вариантов (2-I) в верхнем слое покрытия
рекомендуется применение жестких литых асфальтобетонных смесей I и II типа по
ТУ 400-24-58-89*.
В этом случае в
качестве исходных материалов для приготовления смесей используются традиционные
минеральные материалы: щебень фракции 5 - 20 мм из природного камня или щебень
из гравия, пески природные и дробленые, минеральные порошки
активированные и неактивированные по ГОСТ 16557-78.
Основные требования
к щебню изложены в таблице 3.8.
Таблица 3.8
Прочность и
морозостойкость щебня
N
п/п
|
Наименование показателей свойств
|
Марка материалов, не ниже
|
Щебень
из изверженных и
метаморфических пород
|
Щебень
из гравия
|
1
|
Дробимость при сжатии
(раздавливании) в цилиндре
|
1000
|
-
|
2
|
Износ
в полочном барабане
|
И-II
|
И-II
|
3
|
Морозостойкость
|
F50
|
F25
|
Пески могут
применяться как I-го, так и II классов с группой по
крупности не ниже средней. Допускается использование смеси природного и
дробленого песков в соотношениях, позволяющих обеспечить требуемую пористость
минерального остова асфальтобетона.
3.22. В качестве вяжущего для приготовления литых асфальтобетонных смесей
применяют теплостойкие вязкие битумы по ГОСТ 22245-90, с обеспеченными
значениями нижеприведенных показателей свойств:
- глубина
проникания иглы
при 25
°C 0,1 мм, в пределах ...... 50 - 60
-
температура размягчения
по
методу КиШ, °C, не ниже ...... 52
-
температура хрупкости
по Фраас, °C, не выше
............ 12
3.23. При
проектировании составов литых асфальтобетонных смесей следует ориентироваться
на обеспечение требований по основным структурным показателям, указанным в
таблице 3.9.
Таблица 3.9
Свойства литого
асфальтобетона
N
п/п
|
Показатели свойств
|
Нормативные
значения
по типам
|
I
|
II
|
1
|
Пористость
минерального остова, % по объему,
не более
|
20
|
22
|
2
|
Водонасыщение,
% по объему, не более
|
1,0
|
1,0
|
3
|
Подвижность
смеси при 200 °C, мм, не менее
|
30
|
25
|
4
|
Температура
при выпуске, °C, в пределах
|
220
- 240
|
200
- 230
|
3.24. При
применении в конструкции сероасфальтобетонных литых
смесей (конструкция 2-II) следует руководствоваться ТУ 5718-002-53737504-01 для
определения качества исходных материалов, состава смеси и требуемых значений
показателей физико-механических свойств готового материала.
При приготовлении
смесей следует использовать щебень из природного камня, получаемый дроблением
изверженных горных пород, отвечающий требованиям ГОСТ 8267-93 и таблице 3.10
настоящих технических условий.
Основные
физико-механические свойства минерального заполнителя представлены в таблице
3.10.
Таблица 3.10
N
п/п
|
Наименование показателя
|
Нормативное
значение
|
1
|
Содержание
пылеватых, илистых и глинистых частиц
не более, %
|
1,0
|
2
|
Марка
по дробимости горной породы, не ниже
|
1000
|
3
|
Марка
по истираемости горной породы
|
И-I
|
4
|
Морозостойкость
|
F50
|
5
|
Суммарная
удельная эффективная активность естественных
радионуклидов не более, Бк/кг
|
740
|
По форме зерен
щебень должен быть кубовидной формы. Содержание зерен слабых пород не должно
превышать 5% по массе.
Для приготовления сероасфальтобетонных смесей необходимо использовать песок -
из отсевов дробления и обогащенный из отсевов дробления; природный и
обогащенный по зерновому составу не ниже средней группы, отвечающий требованиям
ГОСТ 8736-93. Допускается использование смеси природного и дробленого песков в
соотношении 1:1 или 1:2.
Материалы из
отсевов дробления горных пород для строительных работ, отвечающие требованиям
ГОСТ 8267-93 и ГОСТ 8736-93.
В смесях используют
минеральный порошок - неактивированный и
активированный, отвечающий требованиям ГОСТ 16557-78.
Применяют нефтяные
дорожные битумы, удовлетворяющие требованиям ГОСТ 22245-90* с температурой
размягчения по кольцу и шару не ниже 44 °C.
Сера техническая по
качественным показателям должна соответствовать требованиям ГОСТ 127.1-93. Для
приготовления смесей используется сера в комовом и гранулированном виде
(фракция не более 6 мм). Допускается использование в жидком виде.
3.25. Показатели физико-механических
свойств сероасфальтобетонных литых смесей должны
соответствовать требованиям, указанным в таблице 3.11.
Таблица 3.11
Требования к сероасфальтобетонным смесям
N
п/п
|
Показатели свойств
|
Нормативное
значение
|
1
|
Пористость
минерального остова, % объема, не более
|
22
|
2
|
Водонасыщение,
% объема, не более
|
0,5
|
3
|
Подвижность
смеси при 150 °C, МПа, не менее
|
30
|
4
|
Глубина
вдавливания штампа при температуре +40 °C,
мм, в пределах
|
1 - 5
|
5
|
Предел
прочности при сжатии при температуре +50 °C,
не менее (факультативно)
|
1,0
|
6
|
Температура
приготовления смеси, °C
|
140 - 150
|
3.26. Для защиты пролетных строений мостовых переходов рекомендуется к
применению гидроизоляционная мастика типа "БИТРЭК-И" (ТУ
5775-001-40010445-02) или "Новомаст" марок
БПГ 25 - БПГ 50 (ТУ 5775-002-18893843-02), представляющие собой готовые к
применению составы, в первом случае из химически модифицированного
мелкодисперсной резиновой крошкой битума, во втором - из битума нефтяного,
полимерных добавок и пластификатора, а при необходимости может включать
инертные наполнители.
3.27.
Композиционные мастики должны соответствовать требованиям действующих
технических условий:
- материал должен
представлять однородную массу без посторонних включений и сгустков размером
более 1 мм;
-
физико-механические показатели должны соответствовать требованиям, указанным в
таблице 3.12.
Таблица 3.12
Технические
требования к мастикам
N
п/п
|
Наименование показателя
|
Нормативное
значение
|
1
|
Условная
прочность, МПа, не менее
|
0,2
|
2
|
Относительное
удлинение при разрыве, %, не более
|
100
|
3
|
Водопоглощение, % массы, не более
|
0,2
|
4
|
Прочность
сцепления с бетоном, МПа, не менее
|
0,5
|
5
|
Теплостойкость,
°C, не ниже
|
90
|
6
|
Гибкость
на брусе с закруглением радиусом 5 мм, °C,
не выше
|
-5
|
Примечания. 1. При
испытании на гибкость при температуре не выше минус 5 °C на поверхности образца
не должно быть трещин.
2. Композиционные
мастики должны быть водонепроницаемыми. При испытании при давлении 0,001 МПа в
течение 72 ч и при давлении 0,03 МПа в течение 10 мин на поверхности образца не
должно быть наличия влаги.
3.28. В качестве
гидроизоляции пролетных строений мостов и путепроводов могут быть применены
рулонные гидроизоляционные материалы типа "Мостопласт"
(ТУ 5774-025-01393697-99), представляющий собой битумополимерный
наплавляемый материал, состоящий из полиэфирного нетканого полотна с
двусторонним нанесением малоокисленного битума,
модифицированного полиолефинами типа вестопласт,
полипропилена и наполнителя.
Физико-механические
показатели должны соответствовать требованиям, представленным в табл. 3.13.
Таблица 3.13
N
п/п
|
Наименование показателя
|
Нормативное
значение
|
1
|
Масса
1 м2, кг
|
5,5
+/- 0,2
|
2
|
Разрывная
сила при растяжении в продольном направлении,
Н/50 мм, не менее
|
200
|
3
|
Разрывная
сила при растяжении в поперечном направлении,
Н/50 мм, не менее
|
1000
|
4
|
Водонепроницаемость
при давлении 2 кгс/см2 в течение
24 ч, не менее
|
900
|
5
|
Температура
размягчения покровной массы, °C
|
абсолютная
|
6
|
Гибкость
на брусе радиусом R10, °C, не выше
|
-25
|
4.
ТЕХНОЛОГИЯ ПРОИЗВОДСТВА РАБОТ
4.1.
УСТРОЙСТВО ЗЕМЛЯНОГО ПОЛОТНА
И ПЕСЧАНОГО
ПОДСТИЛАЮЩЕГО СЛОЯ
4.1.1. Работы по
сооружению земляного полотна производят после окончания работ по вертикальной
планировке, прокладке новых и перекладке старых подземных инженерных сетей,
засыпке траншей и разрытий с послойным уплотнением. Все подземные сооружения и
кабели должны быть проложены вне строящихся дорог и улиц. В зоне проезжей части
дороги следует по возможности размещать дождеприемные
колодцы с решетками.
4.1.2. Сооружение
земляного полотна должно производиться согласно требованиям СНиП 3.05.03-85
"Автомобильные дороги" и в соответствии с техническим проектом
производства работ.
4.1.3. Ширина
корыта земляного полотна с учетом установки бортовых камней должна быть больше
ширины корыта на 0,5 м.
4.1.4. Работы по
устройству земляного полотна целесообразно производить экскаваторами с емкостью
ковша 0,2 м3 - 1,0 м3, бульдозерами мощностью 80 - 250 л.с.,
легкими и среднего веса автогрейдерами (Приложение 3).
4.1.5. Отсыпку
грунта насыпи следует начинать с крайних боковых полос с последующим
приближением к оси дороги. Толщину слоя отсыпки следует назначать с учетом коэффициента запаса на уплотнение грунта в зависимости от
его вида при влажности, близкой к оптимальной (табл. 4.1).
Таблица 4.1
Зависимость
коэффициента запаса на уплотнение
от вида грунта при
оптимальной влажности
┌──────────────────────────────────────┬──────────────┬───────────────────┐
│ Наименование грунта │ Оптимальная │Коэффициент запаса │
│ │
влажность, % │ на уплотнение │
├──────────────────────────────────────┼──────────────┼───────────────────┤
│ 1 │ 2
│ 3 │
├──────────────────────────────────────┼──────────────┼───────────────────┤
│Песок
крупный и гравелистый
│ 6 │ 1,3 │
├──────────────────────────────────────┼──────────────┼───────────────────┤
│Песок
средней крупности
│ 8 │ 1,3 │
├──────────────────────────────────────┼──────────────┼───────────────────┤
│Песок
мелкий и пылеватый
│ 10 │ 1,4 │
├──────────────────────────────────────┼──────────────┼───────────────────┤
│Супесь
легкая
│ 9 - 11 │ 1,25
│
├──────────────────────────────────────┼──────────────┼───────────────────┤
│Супесь
пылеватая
│ 9,13 │ 1,3 │
├──────────────────────────────────────┼──────────────┼───────────────────┤
│Суглинок
легкий │ 14 - 16
│ 1,2 │
├──────────────────────────────────────┼──────────────┼───────────────────┤
│Суглинок
тяжелый │ 16 - 18
│ 1,2 │
├──────────────────────────────────────┼──────────────┼───────────────────┤
│Глина │ 18 - 20
│ 1,16 │
└──────────────────────────────────────┴──────────────┴───────────────────┘
4.1.6. При
послойной отсыпке грунта земляного полотна каждый слой следует разравнивать,
соблюдая проектный продольный и поперечный уклоны. Отсыпанный слой следует
выравнивать автогрейдером под двухскатный или односкатный поперечный профиль. К
концу смены должен быть полностью отсыпан, выровнен и уплотнен слой грунта по
всему поперечному сечению земляного полотна. Движение транспортных средств,
отсыпающих очередной слой, необходимо регулировать по всей его ширине.
4.1.7.
Использование в одном слое насыпи разных видов грунтов не допускается, за
исключением случаев, когда такое решение специально предусмотрено проектом.
4.1.8. Во всех
случаях уплотнение грунтов земляного полотна необходимо производить при
оптимальной влажности до требуемой плотности (табл. 4.2).
Таблица 4.2
Рекомендуемые
коэффициенты уплотнения земляного полотна
┌───────────────┬───────────────────┬────────────────────┬────────────────┐
│
Вид земляного │ Часть
земляного │Глубина
расположения│ Коэффициент │
│ полотна
│ полотна │слоя от поверхности │ уплотнения
│
│ │ │
покрытия │грунта, не
менее│
├───────────────┼───────────────────┼────────────────────┼────────────────┤
│Насыпи │Верхняя │ до 1,5 │
1,00 - 0,98 │
│ │Нижняя │ 1,5 - 6,0 │
0,98 │
│ │неподтапливаемая │
более 6,0 │ 0,95 - 0,98
│
│ │Нижняя │ 1,5 - 6,0 │
0,95 - 0,98 │
│ │подтапливаемая │
более 6,0 │ 0,98
│
│Выемка
в местах│В слое
сезонного │ до 1,2 │
1,00 - 0,98 │
│с
нулевыми
│промерзания
│
│ │
│отметками │Ниже слоя сезонного│ до 1,2 │ 0,95
│
│ │промерзания │ │ │
└───────────────┴───────────────────┴────────────────────┴────────────────┘
Уплотнение грунтов
производят катками на пневматических шинах, кулачковыми или с гладкими
вальцами. Катки выбирают в зависимости от вида грунта и толщины слоя отсыпки в
соответствии с табл. 4.3.
Таблица 4.3
Рекомендуемые
катки для уплотнения грунтов
┌──────────────────────┬────────────────────┬─────────┬───────────────────┐
│ Модель, тип, марка │
Основные │ Масса, │Глубина уплотнения │
│ │ конструктивные │
т │(в плотном теле),
м│
│ │ особенности │ ├─────────┬─────────┤
│ │ │ │ связный
│несвязный│
│ │ │ │ грунт
│ грунт │
├──────────────────────┼────────────────────┼─────────┼─────────┼─────────┤
│ 1 │ 2 │ 3
│ 4 │
5 │
├──────────────────────┼────────────────────┼─────────┼─────────┼─────────┤
│ДУ-65,
100 │Самоходный пневмоко-│ 10 - 12 │ 0,20
│ 0,25 │
│ │лесный на спецшасси │ │ │ │
│ДУ-71 │Самоходные │ 17 - 25 │ 0,50
│ 0,60 │
│ДУ-58А │вибрационные │ 16
│ 0,40 │
0,60 │
│ДУ-64 │комбинированного │8,5 - 9,5│ 0,30
│ 0,50 │
│ДУ-70 │действия │ 6,5 - 7 │ 0,25
│ 0,40 │
│(ДУ-70-1
- кулачковый)│Вибрационные
│ │ │ │
│ДУ-74 │прицепные │ 8 - 9
│ 0,30 │
0,50 │
│(ДУ-74-1
- кулачковый)│(агрегатируемые) │ │ │ │
│К-701М-ВК │с тракторами Т-150К │
24,9
│ 0,40 │
0,60 │
│(в
т.ч. кулачковый)
│и К-701М, К-702М
│ │ │ │
│ДУ-62А │ │ 13
│ 0,40 │
0,60 │
└──────────────────────┴────────────────────┴─────────┴─────────┴─────────┘
Примечание. Связный
грунт - грунт, содержащий глинистых частиц более 12%. Несвязный грунт - грунт,
содержащий глинистых частиц менее 3%.
4.1.9. На участках
с нулевыми рабочими отметками и в выемках естественный грунт из корыта дорожной
одежды должен удаляться бульдозерами непосредственно перед отсыпкой песчаного
подстилающего слоя, а грунт уплотняют до требуемой плотности
с обеспечением водоотвода.
4.1.10. Для
осушения верхней части земляного полотна и дорожной одежды устраивают дренаж
мелкого заложения, состоящий из дренирующего слоя и дрен. Работы по устройству
дренажа выполняются непосредственно перед распределением песчаного
подстилающего слоя.
4.1.11. В качестве
дренажа мелкого заложения могут быть использованы керамзитобетонные трубофильтры, перфорированные асбоцементные, керамические и
полимерные дренажные трубы. Стыки и водоприемные отверстия дрен защищают от
заиливания муфтами и фильтрами, в качестве которых могут быть использованы
каменные материалы, нетканые синтетические материалы типа дорнит,
а также стеклохолсты.
4.1.12.
Технологический процесс устройства дренажей мелкого заложения в предварительно
подготовленной для этой цели траншее включает следующие этапы: рытье ровика,
устройство в нем подушки под трубы, укладку трубофильтров,
сопряжение их с водоприемниками, заполнение ровика песком и его уплотнение.
Трубы с раструбами
и трубофильтры обращают против уклона соответственно
раструбами и пазами.
4.1.13. Выпуск воды
из дрены осуществляют в водоприемные колодцы, причем конец трубы должен
выступать на 5 см относительно стенки колодца.
4.1.14. Зазоры
между трубчатыми дренами и стенками колодцев должны быть тщательно заделаны
цементно-песчаным раствором состава 1:3 или герметикой.
4.1.15. Устройство
песчаного подстилающего слоя должно производиться в соответствии с требованиями
СНиП 3.06.03-85 "Автомобильные дороги".
4.1.16. Песок
доставляется к месту строительства автомобилями-самосвалами и выгружается
непосредственно в корыто дороги. Допускается складирование песка на специально
отведенном месте с последующей подвозкой его к месту укладки автопогрузчиками.
Разравнивание песка производится бульдозерами или автогрейдерами по способу
"от себя" с соблюдением проектных уклонов и толщин с учетом запаса на
уплотнение.
4.1.17. Катки для
уплотнения песка применяют те же, что и для уплотнения земляного полотна (табл.
4.3). Особо тщательно следует уплотнять песок около дождеприемных
колодцев и в местах примыкания к инженерным сооружениям, где уплотнение
производится с помощью ручных электрических трамбовок типа ИЭ-4505 (ИЭ-4504).
4.2.
УСТРОЙСТВО ОСНОВАНИЯ
4.2.1. Основания
устраивают из уплотняемых щебеночных, укатываемых малоцементных,
пластичных и литых, в т.ч. армированных фиброй
бетонных смесей.
4.2.2. Щебеночные
смеси оптимального гранулометрического состава и влажности (4 - 6% по массе)
доставляют на объект автомобилями-самосвалами и выгружают на подготовленный
песчаный подстилающий слой или в приемный бункер щебнеукладчика.
4.2.3. Укладку
щебеночных смесей следует осуществлять щебнеукладчиками,
универсальными укладчиками с автоматическими следящими системами. Допускается
производить распределение щебеночных смесей автогрейдером слоями с учетом
коэффициента запаса на уплотнение.
4.2.4. Основание из
щебеночных смесей уплотняют самоходными катками не менее чем за 10 проходов.
Тип катка выбирают в зависимости от толщины уплотняемого слоя согласно табл.
4.4.
Таблица 4.4
Катки для
уплотнения щебеночных смесей
┌────────────────────────────────┬──────────┬──────┬──────────────────────┐
│ Основные
конструктивные │ Марка
│Масса,│ Толщина уплотняемого │
│ особенности │ │ т
│слоя (в плотном теле),│
│ │ │ │ м │
├────────────────────────────────┼──────────┼──────┼──────────────────────┤
│Катки
самоходные вибрационные │ ДУ-47Б
│ 8,5 │ 10 - 15 │
│с
гладкими вальцами,
│ ДУ-96 │ 7,8
│
│
│2-вальцовые │ ДУ-93
│8 (10)│
│
├────────────────────────────────┼──────────┼──────┼──────────────────────┤
│Катки
самоходные вибрационные │ ДУ-74-1 │ 9,5 │
20 - 25 │
│с
кулачковыми вальцами
│ ДУ-85-1 │ 13,5
│ │
├────────────────────────────────┼──────────┼──────┼──────────────────────┤
│Катки
самоходные комбинированные│
ДУ-97 │ 7,6 │
15 - 20 │
│с
вибрационным вальцом
│ ДУ-64 │ 9,5
│
│
│ │ ДУ-99
│ 10 │ │
└────────────────────────────────┴──────────┴──────┴──────────────────────┘
Смесь должна быть
уложена не позднее 3 часов после доставки ее на место производства работ.
4.2.5. Для
устройства оснований в зависимости от конструкции и стадийности строительства
дороги следует применять малоцементный укатываемый
бетон классов В7,5; В15; В22,5 (М100, 200, 300).
4.2.6. Малоцементная смесь поставляется на строительный объект в
автосамосвалах, где она должна быть защищена от потери влаги в сухую теплую
погоду, а в сырую от переувлажнения. Доставка смеси должна осуществляться по
часовому графику, разработанному с учетом производительности укладочных машин.
4.2.7. Время
транспортирования укатываемой смеси не должно превышать 60 минут. Время после
выпуска смеси до ее окончательного уплотнения в основании не должно превышать
120 минут.
4.2.8. Укладка
укатываемой смеси должна осуществляться бетоноукладчиками или универсальными
укладчиками с автоматическими следящими системами и поверхностными уплотняющими
рабочими органами.
На участках
площадью менее 1000 м2, где невозможно применение
указанных машин, укладку смеси можно выполнять экскаватором типа ЭО-2621 с
навесным оборудованием или автогрейдером слоями, толщина которых должна быть на
15 - 20% больше уплотняемого слоя и уточняться по ходу работы.
4.2.9. Укладка
укатываемой бетонной смеси ведется от бортового камня к оси дороги.
Движение укладочных
машин в продольном направлении должно происходить навстречу уклону, если он
больше 30%.
4.2.10. Укладку
смеси при ширине дороги до 9 м следует вести отдельными захватками длиной 40 -
50 м с таким расчетом, чтобы разрыв во времени укладки смежных полос не
превышал 1 часа во избежание обезвоживания боковой кромки ранее уложенной
полосы.
4.2.11. При ширине
дороги более 9 метров укладка смеси должна производиться двумя или тремя
бетоноукладочными машинами с опережением одного укладчика относительно другого
на 1 - 15 метров.
4.2.12. Дефекты
поверхности основания (впадины и разрывы) свежеуложенной смеси должны
устраняться по ходу работы подсыпкой смеси.
4.2.13. Для
уплотнения бетонной смеси следует преимущественно использовать самоходные
комбинированные вибрационные катки с пневматическими ведущими вальцами.
Уплотнение можно производить также самоходными пневматическими и гладковальцовыми катками.
Катки следует
выбирать из условия уплотнения смеси в один слой (табл. 4.5).
Таблица 4.5
Характеристика
катков и режимы
уплотнения
укатываемых бетонных смесей
┌────────────────┬────────────┬──────────┬─────────┬────────────┬─────────┐
│ Тип катка
│Марка катка │
Масса, │Жесткость│
Наибольшая │ Число │
│ │ │ т
│бетонной │ толщина
│проходов │
│ │ │ │смеси, с │уплотняемого│по одному│
│ │ │ │ │ слоя, см │
следу │
├────────────────┼────────────┼──────────┼─────────┼────────────┼─────────┤
│ 1
│ 2 │
3 │ 4
│ 5 │
6 │
├────────────────┼────────────┼──────────┼─────────┼────────────┼─────────┤
│Комбинированный,│ ДУ-58А
│ 16 │90 - 120 │ 30
│ 6 - 8 │
│самоходный, │ ДУ-6710.01 │ 13
│90 - 120 │ 30 │
6 - 8 │
│вибрационный │
ДУ-64 │ 9,5
│90 - 120 │ 30
│ 6 - 8 │
│ │ ДУ-74
│ 8 - 9 │90 - 120 │ 25
│ 6 - 8 │
│ │ Райле- │
14,25 │90 - 120
│ 35 │
6 - 8 │
│ │ 120РМ-МС-1 │9
(10, 15)│90 - 120 │
30 │ 6 - 8
│
│ │Райле-212(Д)│ 9,3
│90 - 120 │ 30 │
6 - 8 │
│ │ СА-25"
│ │ │ │ │
├────────────────┼────────────┼──────────┼─────────┼────────────┼─────────┤
│Самоходный
на │ ДУ-65
│ 1 - 12 │100 -
110│ 15 │ 8 - 10 │
│пневматических │ │ │ │ │ │
│шинах,
│ │ │ │ │ │
│статический │ │ │ │ │ │
├────────────────┼────────────┼──────────┼─────────┼────────────┼─────────┤
│Самоходный │
ДУ-73-1 │ 5 - 5,5 │90 - 100 │ 12
│12 - 14 │
│гладковальцовый │
ДУ-47Б-1 │ 6
│90 - 100 │
12 │12 - 14 │
│статический │
ДУ-63-1 │ 10
│100 - 110│
12 │12 - 14 │
└────────────────┴────────────┴──────────┴─────────┴────────────┴─────────┘
Катки ДУ-65,
ДУ-73-1, ДУ-47Б-1, ДУ-63-1 применяются для уплотнения технологического слоя и
оснований тротуаров.
4.2.14. Укатка с перекрытием следа на 15 - 25 см должна начинаться от обоих
бортовых камней к оси проезда при двухскатном профиле; при односкатном -
навстречу поперечному уклону. Уплотнение считается достаточным, когда
при проходе тяжелого катка на поверхности основания не остается следа.
Основание толщиной более 20 см рекомендуется устраивать в 2 слоя с послойным
уплотнением.
4.2.15. Вальцы
катков в течение всего времени уплотнения смеси должны быть чистыми и гладкими.
4.2.16. Остановка
катков во время укатки свежеуложенной смеси не допускается.
4.2.17. В
основаниях из укатываемых смесей швы расширения не устраивают. Швы сжатия в
конструкциях из укатываемого бетона класса В7,5 не
устраивают, классов В15 и В22,5 выполняют в свежеуложенном или отвердевшем
бетоне через 12 и 10 м соответственно.
4.2.18. В конце
рабочей смены в случае отсутствия температурного шва должен устраиваться
рабочий шов в виде упорной доски толщиной 5 см на всю ширину и высоту
укладываемой полосы. Вдоль рабочих швов бетонная смесь должна быть
дополнительно уплотнена поверхностными вибраторами с подсыпкой смеси вручную на
полосе 25 - 30 см. Перед возобновлением укладки смеси доска удаляется
и торец бетона обрабатывается цементно-песчаным раствором состава 1:1.
4.2.19. Устройство
основания из пластичного бетона, используемого при стадийном строительстве на 1
стадии в качестве покрытия, рекомендуется производить сразу после уплотнения малоцементной укатываемой смеси. В отдельных случаях
допускается укладка пластичной смеси спустя 3 часа после уплотнения укатываемой
смеси.
Во всех этих
вариантах подача бетонной смеси должна осуществляться без заезда транспорта на
нижний слой из укатываемого бетона.
4.2.20. При
невозможности соблюдения требований п. 4.2.19 устройство основания из
пластичного бетона производят после набора малоцементным
бетоном не менее 70% марочной прочности, но не ранее 7 суток с начала
строительства основания. В этом случае допускается заезд построечного
транспорта на нижний слой из укатываемого бетона.
4.2.21. Если разрыв
во времени между укладкой слоев не превышает 3-х часов, уход за ранее уложенным
малоцементным бетоном не производят, в случае
превышения - осуществляют при помощи битумной эмульсии.
Расход битумной
эмульсии при температуре воздуха во время укладки до +25 °C составляет 0,4 кг/м2, свыше +25 °C - 0,7 кг/м2.
4.2.22. Доставку
пластичной бетонной смеси можно осуществлять в автосамосвалах, при этом
продолжительность ее транспортирования не должна превышать 60 мин при
температуре воздуха до +25 °C и 90 мин - при температуре ниже +20 °C. В случае
невозможности выполнения этих требований транспортировку смеси следует
осуществлять только автобетоносмесителями.
В процессе
транспортирования смеси автосамосвалами ее следует защищать от атмосферных
воздействий и испарения влаги.
4.2.23.
Строительство оснований из пластичных бетонных смесей следует производить
бетоноукладчиками с автоматическими следящими системами.
4.2.24. Укладку и
уплотнение пластичной бетонной смеси следует производить непрерывно, избегая
остановок бетоноукладчика.
4.2.25.
Незначительные неровности и мелкие дефекты поверхности после прохода
бетоноукладчика исправляют с помощью ручных гладилок.
Шероховатость
основания, выполняющего роль покрытия при стадийном строительстве, достигается
обработкой поверхности свежеуложенного бетона щетками.
4.2.26. Нарезка
швов осуществляется в отвердевшем бетоне.
4.2.27. Уход за
бетоном из пластичных смесей выполняют при помощи пленочных материалов или
битумной эмульсии.
4.2.28. Технология
строительства бетонных конструкций из литых бетонных смесей, в том числе и
армированных фиброй, отличается от технологии строительства из пластичных
смесей необходимостью предварительной установки бортовых камней или устройства
опалубки и отсутствием распределяющих и уплотняющих механизмов.
4.2.29. Литая, в
том числе дисперсно-армированная смесь, должна доставляться на объект в автобетоносмесителях, во время движения
которых происходит непрерывное ее перемешивание.
Доставку литой
смеси следует осуществлять по часовому графику.
4.2.30. Техническая
характеристика автобетоносмесителей представлена в
табл. 4.6.
Таблица 4.6
Техническая
характеристика автобетоносмесителей
┌─────────────────────────┬───────────────────────────────────────────────┐
│ Техническая │ Модель │
│ характеристика ├─────────┬─────────┬─────────┬────────┬────────┤
│ │СБ-92В-2
│СБ-159Б-2│ СБ-172 │
СБ-211 │ СБ-234 │
├─────────────────────────┼─────────┼─────────┼─────────┼────────┼────────┤
│Объем
перевозимой смеси, │ 5 │
5 │ 6
│ 8 │
8 │
│м3 │ │ │ │ │ │
├─────────────────────────┼─────────┼─────────┼─────────┼────────┼────────┤
│Время
перемешивания, мин │ 15 - 20 │ 15 - 20 │ 15 - 20 │15 -
20 │15 - 20 │
├─────────────────────────┼─────────┼─────────┼─────────┼────────┼────────┤
│Высота
загрузки, м
│ 3,62 │
3,6 │ 3,6
│ 3,6 │
3,6 │
├─────────────────────────┼─────────┼─────────┼─────────┼────────┼────────┤
│Вместимость
бака │ 400
│ 400 │
4501 │ 450
│ 450 │
│для
воды, л
│ │ │ │ │ │
├─────────────────────────┼─────────┼─────────┼─────────┼────────┼────────┤
│Максимальная
скорость, │ 90
│ 80 │
80 │ 60
│ 60 │
│км/ч
│ │ │ │ │ │
├─────────────────────────┼─────────┼─────────┼─────────┼────────┼────────┤
│Габаритные
размеры, м
│7,5x2,5x │9,0x2,5x
│9,87x2,5x│8,0x2,5x│9,5x2,5x│
│ │ 3,62
│ 2,6 │
3,64 │ 3,6
│ 3,6 │
└─────────────────────────┴─────────┴─────────┴─────────┴────────┴────────┘
4.2.31. На объекте
следует визуально или при помощи стандартного конуса оценить подвижность литой
смеси, величина которой определяется значениями продольного уклона строящейся
дороги и может составлять 12 - 18 см.
В случае
недостаточной подвижности смеси на объекте дополнительно вводится добавка-суперпластификатор и производится дополнительное
перемешивание в течение 5 - 7 мин.
4.2.32. Готовая
литая бетонная смесь выливается из автобетоносмесителя
на предварительно уложенную по песчаному подстилающему слою полиэтиленовую
пленку.
4.2.33. Для
облегчения подачи литой смеси на расстояние 3 - 4 м следует применять удлиненные
лотки или инвентарные приставные лотки к автобетоносмесителю.
Для исключения расслаиваемости смеси угол наклона
лотка должен быть в пределах 45 - 60°.
При выгрузке смеси
бетономешалку автобетоносмесителя следует установить
вниз по естественному уклону дороги.
В труднодоступную
конструкцию дороги укладка бетонной смеси может производиться автобетоносмесителем совместно с бетононасосами типа "Штетгер", "Вибау"
и др.
4.2.34. Литая смесь
после ее укладки требует лишь незначительного распределения и профилирования,
что осуществляется специальным оборудованием типа фирмы "Голдблат".
В случае
необходимости, особенно на участках с продольным уклоном более
,
следует использовать для дополнительного уплотнения двухвальцовый
ручной каток, выпускаемый фирмой "Голдблат".
Смесь должна
распределяться и профилироваться против продольного уклона строящейся дороги.
4.2.35. В конце
рабочей смены устраивают поперечный температурный шов. Шов устраивают в виде
упорного бруса или металлического шаблона, обернутых
пергамином, на полную ширину и высоту укладываемой полосы дороги. Брус (шаблон)
закрепляется к грунту и бетону с помощью металлических штырей. После
возобновления работ установленный брус (шаблон) снимается.
4.2.36. Характер
устройства температурных швов в основания выполненных из пластичной или литой,
в т.ч. дисперсно-армированной смеси, определяется
температурой воздуха во время укладки, а также интервалом времени до
последующего строительства покрытия и должен определяться в каждом конкретном
случае и в соответствии с проектом.
При устройстве
покрытия через 7 дней после бетонирования температурные швы в основании из
литых и пластичных смесей устраивают через 10 - 12 м, а из
дисперсно-армированного бетона не чаще чем через 25 - 30 м.
При использовании
основания в качестве покрытия на период строительства расстояние между
температурными швами определяется проектом, но не должно быть чаще чем 7 и 5 м при ширине полосы движения 3,75 и 5,5 м
соответственно.
4.2.37. Уход за
свежеуложенным бетоном нужно осуществлять как и за
традиционным бетоном сразу после его укладки при помощи полиэтиленовой пленки,
водонепроницаемой бумаги, пергамина, толя, дорнита и
др. пленкообразующих материалов.
4.3.
УСТРОЙСТВО ПОКРЫТИЯ ИЗ МОНОЛИТНОГО БЕТОНА
4.3.1. Покрытия
могут устраиваться из литых самоуплотняющихся бетонных смесей, модифицированных
добавками, в т.ч. суперпластификаторами
(СП) с применением ручного оборудования или из подвижных смесей с осадкой
конуса 4 - 6 см с применением бетоноукладчиков со скользящими формами и
следящим устройством типа "Gomako"
(Приложение 3). Строительство покрытий рекомендуется осуществлять при
положительных температурах наружного воздуха.
4.3.2. При
использовании литьевой технологии покрытия устраиваются так же, как при строительстве
оснований, но при этом особое внимание следует обратить на очистку и подготовку
поверхности основания, устройство температурных швов и уход за твердеющим
бетоном.
Основание должно
быть тщательно очищено от пыли и грязи и промыто водой. Укладка пленкообразующих
или рулонных материалов по бетонному основанию не требуется.
Доставленную на
объект бетонную смесь доводят введением добавки СП до требуемой консистенции и
выгружают в опалубку. После ее распределения и, в случае необходимости, доуплотнения двухвальцовыми
ручными уплотнителями, поверхность покрытия выглаживается гладилками,
обрабатывается по контуру ручными инструментами в поперечном направлении -
широкими метровыми щетками из натурального ворса для получения уже на первой
стадии эксплуатации коэффициента продольного сцепления не менее 0,45. В
дальнейшем после обнажения текстуры бетона, насыщенного прочным кубовидным
гранитным щебнем крупностью не более 20 мм, коэффициент сцепления покрытия во
влажном состоянии должен составлять не менее 0,50.
4.3.3. Уход за
твердеющим бетоном должен осуществляться не менее 7 суток с поливом поверхности
водой не менее двух раз в сутки и укрыванием поверхности рулонным материалом
типа пергамин, полиэтиленовой пленкой и др.
4.3.4. Швы сжатия
должны нарезаться в отвердевшем бетоне на вторые-третьи сутки после
бетонирования по достижению кубиковой прочности не
менее 130 кг/см2. Продольные швы сжатия нарезаются по
границе полос движения, т.е. через 3,75 - 3,50 м, поперечные - с таким
расчетом, чтобы площадь плиты не превышала 30 м2.
Глубина нарезки швов должна составлять 1/4 толщины покрытия, ширина - 2 - 4 мм.
Швы сжатия могут
заполняться специальными тепло- и светостойкими мастиками типа "Битрек-Д, кл. Б" по ТУ
5718-004-05204776-01 или сухими мелкодисперсными смесями следующего состава на
1 м3: вода - 190 л; портландцемент М-500, ДО - 65 кг; песок чистый
(загрязненность менее 1%) с
1,5 - 1,7 - 1520 кг; герметизирующе-кольматирующий
материал "Акватрон-6" или "Аквастоп-7" - 5 - 8% от массы
цемента.
4.3.5. Швы сжатия в
покрытии должны по возможности повторять расположение швов сжатия в бетонном
основании, а при применении сталефибробетонного
покрытия расстояние между швами сжатия увеличивается в 1,5 - 2,0 раза и в
соответствии с проектом.
4.3.6. При
строительстве покрытий из сталефибробетона с
содержанием фибр в количестве 3% от веса бетонной смеси швы расширения не
устраиваются.
4.3.7. При
строительстве бетонных покрытий швы расширения устраиваются при протяженности
проезжей части более 200 погонных метров.
В остальных случаях
(типовые деформационные) швы расширения устанавливаются до бетонирования по
расчету (по проекту) в зависимости от толщины покрытия, конструкции дорожной
одежды, температуры укладки бетонной смеси и др. факторов.
Минимальное
расстояние между швами расширения составляет 70 пог.
м, максимальное - до 140 пог. м.
4.3.8. Применение
укладчиков со скользящими формами и копирной струной
позволяет производить одновременно формование дорожного полотна и ограждающих
конструкций (бортовых камней, в т.ч. мостовых,
разделительных барьеров, лотков и др.). Формование бетонной конструкции
осуществляется шириной до 2-х полос движения.
4.3.9. Движение бетоноукладчика может осуществляться по основанию, одна из
гусениц может передвигаться по готовому бетонному покрытию при наборе им
прочности не менее 50% от марочной, но не ранее чем через 3 суток после его
устройства.
Чтобы обеспечить высокое
качество бетонной конструкции, бетоноукладчик должен двигаться непрерывно со
скоростью, обеспечивающей проработку смеси, делая лишь кратковременные
остановки для наполнения бункера бетонной смесью.
Чтобы обеспечить
непрерывную работу укладчика, бетонную смесь следует доставлять по часовому
графику. Время с момента приготовления смеси до окончания ее укладки не должно
превышать 1,5 - 2 часов. Оптимальная подвижность бетонной смеси должна
находиться в пределах 3 - 5 см.
4.3.10. Сразу же
после бетонирования борта и покрытия производят вручную затирку отдельных
неровностей и раковин с помощью ручных инструментов. Затирку крупных раковин
производят с добавлением свежей бетонной смеси. Запрещается для облегчения
затирки поверхности свежеуложенного бетона использовать воду.
4.4.
УСТРОЙСТВО АСФАЛЬТОБЕТОННЫХ ПОКРЫТИЙ
Устройство
асфальтобетонных покрытий производится в соответствии с действующими
нормативными документами, регламентирующими строительный процесс: ТР 103-00 "Технические рекомендации по устройству
дорожных конструкций с применением асфальтобетона" и СНиП 3.06.03-85
"Автомобильные дороги". Учитывая особенности конструкций,
предложенных в настоящих рекомендациях, следует выделить и уточнить
технологические требования для следующих случаев.
УСТРОЙСТВО ПОКРЫТИЙ
ИЗ ГОРЯЧИХ АСФАЛЬТОБЕТОННЫХ СМЕСЕЙ
4.4.1. Основной
слой устраивается слоями максимально возможной толщины, чтобы обеспечить
монолитность плиты. При многослойной укладке все слои должны быть устроены в
течение одной смены. С этой целью рассчитывают оптимальную длину дневной
захватки. Каждый последующий слой укладывается только после остывания нижнего
до 50 °C при температуре наружного воздуха ниже +10 °C и до 20 - 30 °C при
температуре выше +10 °C.
4.4.2. Укладку и
уплотнение смесей при устройстве слоев толщиной 0,1 - 0,22 м осуществляют в
соответствии с нижеследующими рекомендациями:
а) для укладки
асфальтобетонных смесей следует применять асфальтоукладчики
с шириной укладываемой полосы 7,5 м, устраивая основной слой, как правило,
одновременно на всю ширину проезжей части;
б) при укладке
одним асфальтоукладчиком полосы шириной до 3,50 м
длина должна быть не более 60 - 100 м в зависимости от толщины слоя и
температуры наружного воздуха. Подача асфальтобетонной смеси должна быть не
менее 60 т/ч на каждый укладчик;
в) для
предотвращения раскатывания и разрушения кромки укладываемых слоев повышенной
толщины должны быть установлены боковые упоры, высота которых должна быть равна
толщине уплотненного слоя. Брусья устанавливают на технологический слой и
фиксируют их положение с внешней стороны штырями (2 шт. на брус длиной 4 - 5
м). Упоры следует устанавливать по ходу движения асфальтоукладчиков
с опережением на 0,4 - 0,5 длины сменной захватки;
г) если укладка
полосы прерывается на время, превышающее период остывания смеси, то заканчивать
полосу следует упорным брусом, устанавливаемым перпендикулярно к оси дороги
вплотную к слою уложенной асфальтобетонной смеси;
д)
уплотнение слоев толщиной более 0,1 м из крупнозернистых смесей следует
начинать сначала самоходными катками на пневматических шинах (6 - 8 проходов по
одному следу), а заканчивать гладковальцовыми катками
двухосными массой 10 - 13 т или трехосными массой 11 - 18 т (4 - 6 проходов)
или сначала катками массой 8 - 10 т (2 - 4 прохода), а затем катками массой 11
- 18 т (12 - 20 проходов);
е) рабочая
скорость движения катка на пневматических шинах при первых 2 - 3 проходах по
одному следу не должна превышать 2 - 3 км/ч; последующие проходы следует
производить со скоростью 12 - 15 км/ч. Давление воздуха в шинах катка в начале
укатки должно быть не более 0,3 МПа, а на заключительном этапе уплотнения 0,6 -
0,8 МПа;
ж) при
уплотнении смесей с содержанием щебня более 50% допустимо использовать
вибрационные катки, при этом первые два-три прохода по одному следу каток
делает с выключенным вибратором, затем три-четыре прохода с включенным. После работы вибратора доуплотнение и
выравнивание поверхности выполняют с помощью тяжелого катка.
4.4.3. При
устройстве основного слоя асфальтобетонного покрытия толщиной более 0,2 м
распределение и уплотнение смеси следует производить в два слоя (части). Для
обеспечения монолитности основного слоя устройство нижней части должно
опережать устройство верхней части не более чем на длину захватки, которая
принимается с таким расчетом, чтобы температура уплотненной нижней части к
моменту начала устройства верхней была бы не ниже 50 °C. В исключительных
случаях, когда нет возможности выполнить это условие и когда верхнюю часть
устраивают не по свежеуложенной нижней, а с разрывом во времени, необходимо
перед устройством верхней части монолитной плиты провести подготовку
поверхности нижней части (очистка, сушка, нанесение битумной эмульсии).
УСТРОЙСТВО ПОКРЫТИЙ
ИЗ ЛИТЫХ АСФАЛЬТОБЕТОННЫХ СМЕСЕЙ
4.4.4. Укладку
литых асфальтобетонных смесей производят механизированным способом без
последующего уплотнения смеси (тип I) и с уплотнением смеси вибротрамбующим
брусом асфальтоукладчика (тип II).
4.4.5.
Транспортирование смеси к месту производства работ в зависимости от ее типа
производится:
а) тип I в
специальных передвижных котлах (термос-бункерах), оборудованных
лопастной мешалкой и системой подогрева и обеспечивающих в необходимых случаях
порционную выгрузку с варьированием скорости выдачи смеси;
б) тип II в
автомобилях-самосвалах большой грузоподъемности, как правило, оборудованных
утепленными кузовами. Продолжительность транспортировки не должна превышать 30
- 40 мин.
4.4.6. При
распределении смеси используются:
а) тип I -
самоходные асфальтоукладчики для литого
асфальтобетона, оборудованные электронной следящей системой, с обогреваемой
выглаживающей плитой и обогреваемым приемным бункером, позволяющим производить
приемку смеси из передвижных котлов;
б) тип II - самоходные
асфальтоукладчики, оборудованные вибротрамбующей
плитой и приемным бункером, позволяющим производить выгрузку смеси из
автомобилей-самосвалов большой грузоподъемности.
4.4.7. При укладке
смеси в состав проекта производства работ должна включаться циклограмма
транспортировки смеси от АБЗ до объекта. В графике производства работ
указывается требуемое количество передвижных котлов (автомобилей-самосвалов),
время их прибытия на АБЗ, количество рейсов на каждую машину, время начала и
окончания работ, количество смеси.
4.4.8. Перед
началом загрузки передвижного котла смесью в нем зажигают форсунки
и производится нагрев его до 180 - 190 °C. Крышка загрузочного отверстия
передвижного котла должна быть открыта не ранее чем за 5 мин до загрузки котла
смесью.
4.4.9. В процессе
транспортирования смесь непрерывно перемешивается, а температура ее в котле
поддерживается на уровне 220 - 240 °C. Общее время перемешивания смеси в котле
должно быть не менее 20 мин.
4.4.10. Доставка
смеси к месту укладки должна быть непрерывной и производится навстречу движению
строительного потока. Производительность смесительной установки, количество
передвижных котлов и производительность асфальтоукладчика
должны быть согласованы между собой.
4.4.11. Выгрузка
смеси в приемный бункер асфальтоукладчика
производится при наклоне выпускного лотка и одновременной работе лопастной
мешалки в котле. Приемка автомобилей-самосвалов и выгрузка из них смеси в
приемный бункер асфальтоукладчика осуществляется под
руководством специально выделенного опытного рабочего-сигнальщика, имеющего
красную повязку.
4.4.12. Температура
смеси в асфальтоукладчике должна быть: для смеси типа
I - 220 - 240 °C, типа II - 210 - 230 °C.
4.4.13. Перед
распределением литой смеси выглаживающая плита асфальтоукладчика
должна быть установлена на край ранее уложенного слоя или на брус, толщина
которого и соответствует толщине укладываемого слоя. Для предотвращения
растекания укладываемого слоя применяется скользящая опалубка, перемещающаяся
за асфальтоукладчиком. При отсутствии ее до начала
распределения смеси должны быть установлены в продольном направлении и
закреплены деревянные или металлические брусья, состоящие из звеньев общей
длиной до 20 м. Высота бруса должна соответствовать проектной толщине
укладываемого слоя. По мере остывания уложенного слоя, брусья переставляются.
4.4.14.
Распределение смеси, как правило, производится одновременно и непрерывно по
всей ширине проезжей части улицы. При работе нескольких асфальтоукладчиков
они должны двигаться уступами с опережением 25 - 30 м.
При работе с одним асфальтоукладчиком длина захватки устанавливается из
расчета, чтобы край уложенной полосы при устройстве смежной полосы имел
температуру 100 - 130 °C.
4.4.15.
Обнаруженные дефекты на поверхности покрытия после распределения смеси,
особенно в местах примыкания к упорным брусьям, обрабатываются вручную с
помощью специальных ручных трамбовок.
4.4.16. Щебень
черный горячий для втапливания в покрытие
доставляется на объект в автомобилях-самосвалах до начала распределения смеси в
количестве, необходимом для бесперебойной работы; равномерно распределяется
механизмами или вручную по поверхности устраиваемого покрытия.
4.4.17. Обработка
поверхности покрытия производится россыпью по нему щебня черного горячего
фракций 3 - 5 (8) или 5 - 8 (10) мм. Россыпь щебня производится немедленно
после распределения смеси, вслед за асфальтоукладчиком,
равномерным слоем в одну щебенку. Ориентировочный расход щебня для смеси типа I
- 5 - 8 кг/м2. После распределения щебень
прикатывается ручным катком массой до 30 - 50 кг. После охлаждения уложенного
слоя до температуры наружного воздуха невтопившийся
щебень должен сметаться.
4.4.18. Движение
автомобильного транспорта по готовому покрытию открывается по достижении
покрытием температуры наружного воздуха, но не ранее чем через 3 часа после
завершения работ.
УСТРОЙСТВО ПОКРЫТИЙ
ИЗ ЛИТЫХ СЕРОАСФАЛЬТОБЕТОННЫХ СМЕСЕЙ
4.4.19. Устройство
покрытия начинают с подготовительных работ, в состав которых входят:
- приведение в
соответствие с проектной отметкой дождеприемных
решеток, люков колодцев подземных сооружений;
- очистка основания
от пыли и грязи механическими дорожными щетками, поливомоечными машинами или
сжатым воздухом; а при устройстве мостового полотна на мостах и путепроводах песко-
или водоструйная очистка в соответствии с требованиями рабочего проекта;
- обработка
подготовленного основания битумной эмульсией с расходом 0,3 - 0,4 л/м2. Одновременно с этим производится также обработка всех
выступающих мест конструкции, дождеприемных решеток,
люков колодцев подземных сооружений. При розливе эмульсии не допускается ее
концентрация в пониженных местах;
- геодезическая
разбивка с установкой копирных струн вдоль дороги на
бетонном основании, технологическом слое или нижнем слое покрытия.
4.4.20.
Транспортирование смеси к месту производства работ производится в специальных
самоходных установках с котлом-термосом, оборудованных обогревом и мешалкой с
автономным приводом. При транспортировании должны обеспечиваться непрерывное
перемешивание и температура смеси 140 - 160 °C.
Запрещается
использовать самоходные установки с приводом вала мешалки от двигателя
автомобиля через раздаточную коробку.
4.4.21. Перед
началом загрузки котел-термос (бункер) прогревается до температуры 120 - 140 °C
двумя подогревателями или форсунками (в зависимости от погодных условий время
прогрева может быть увеличено). Запрещается включать сцепление привода мешалки
до прогрева бункера и при наличии в нем остатков затвердевшей (не разогретой)
смеси, препятствующей движению лопастей мешалки. Крышка загрузочного отверстия
передвижного котла должна быть открыта непосредственно перед подачей автомобиля
под погрузку.
4.4.22. В процессе
транспортирования перемешивание смеси в передвижной установке должно быть
непрерывно. Температура в котле поддерживается путем периодического включения
форсунок и контролируется водителем по установленному в кабине водителя
прибору.
Категорически
запрещается нагревать смесь до температуры свыше 160 °C. Прибыв к месту
укладки, смесь выгружается при наклоне выпускного лотка и одновременной работе
лопастной мешалки в котле.
4.4.23. Смесь
распределяют специализированными асфальтоукладчиками
для литых асфальтобетонных смесей типа Vogele 1500
CAF, или специализированными распределителями типа EB фирмы Linhoff,
или типа GB фирмы Faendrich AG без последующего
уплотнения. Специализированные асфальтоукладчики для
литого асфальтобетона должны быть оборудованы электронной следящей системой,
обогреваемой выглаживающей плитой и обогреваемым приемным бункером, позволяющим
приемку смеси из передвижных котлов-термосов. Самоходные распределители
оборудуются электронной следящей системой, дистанционным управлением плавности
хода и устройством, обеспечивающим однородность смеси при укладке.
Распределитель не имеет обогреваемого приемного бункера. Смесь из
котлов-термосов выгружается перед распределителем непосредственно на
существующее основание или нижний слой покрытия. Поэтому применять
распределитель целесообразно только при температуре воздуха выше +10 °C.
4.4.24. Приемка
специализированных автомобилей и выгрузка из них смеси в приемный бункер асфальтоукладчика осуществляется под руководством
специально выделенного опытного рабочего сигнальщика, имеющего специальную
форму и красную повязку.
4.4.25. Перед
распределением литой смеси выглаживающую плиту асфальтоукладчика
или распределителя установить на край ранее уложенного слоя или на брус,
толщина которого соответствует толщине устраиваемого слоя, включить двигатель и
приборы разогрева плиты и бункера, установить в рабочее положение следящую
систему. Для предотвращения растекания укладываемого слоя применяется
скользящая опалубка. При отсутствии ее до начала распределения смеси должны
быть установлены в продольном направлении и закреплены упорные деревянные или
металлические брусья, состоящие из звеньев длиной до 6 м. Высота бруса должна
соответствовать проектной толщине укладываемого слоя. По мере остывания
уложенного слоя, брусья переставляются.
4.4.26. При работе
с одним асфальтоукладчиком или распределителем длина
захватки устанавливается из расчета, чтобы край уложенной полосы при устройстве
смежной полосы имел температуру не менее 70 - 80 °C.
Если температура
ранее уложенной смежной полосы ниже требуемой, ее край на ширину до 150 мм следует
прогреть с помощью линейки-разогревателя,
использующей тепловую энергию инфракрасного излучателя.
Линейка-разогреватель обеспечивает разогрев асфальтобетона на
глубину 30 - 40 мм за 2 - 3 минуты до температуры 80 - 100 °C. При сопряжении
смежных полос линейку-разогреватель перемещают
впереди асфальтоукладчика по краю ранее уложенной
полосы асфальтобетона.
4.4.27.
Обнаруженные дефекты на поверхности покрытия непосредственно после
распределения смеси, особенно в местах примыкания к бортовому камню и упорным
брусьям, обрабатываются вручную с помощью специального ручного инструмента.
4.4.28. При
окончании укладки смеси слой ее клинообразно утончается. При возобновлении
работ клинообразная часть слоя обрубается (обрезается) вертикально по рейке или
шнуру в направлении, перпендикулярном оси дороги. Толщина покрытия в местах
обрубки (обрезки) должна быть не меньше проектной.
4.4.29. При укладке
асфальтобетонных смесей в два и более слоев продольные
швы слоев следует смещать на 100 - 200 мм, причем продольный шов на верхнем
слое должен совпадать с осью дороги.
4.4.30. Если в
полосе укладки встречаются выступающие крышки колодцев, водоприемные решетки,
подача смеси из приемного бункера к выглаживающей плите прекращается,
выглаживающая плита асфальтоукладчика должна быть
поднята. После прохождения укладчиком водопропускных решеток или крышек
колодцев, плита должна быть опущена в исходное положение и подача смеси
возобновлена. Укладку смеси на пропущенном месте следует производить вручную
путем распределения и разравнивания смеси, оставшейся после укладчика, с
добавлением недостающего количества смеси из приемного бункера.
4.4.31. Температура
смеси при укладке должна быть не ниже 140 °C в летнее время и не выше 155 °C
при пониженных температурах.
4.4.32. Движение автомобильного
транспорта по готовому покрытию открывается по достижении покрытием температуры
наружного воздуха, но не ранее чем через 1 час после завершения работ.
5. КОНТРОЛЬ
КАЧЕСТВА
5.1. Технический
контроль устройства земляного полотна, песчаного подстилающего слоя,
цементобетонных оснований и асфальтобетонных и цементобетонных покрытий должен
оценивать их соответствие требованиям утвержденных проектов и действующих
нормативно-технических документов.
Технический
контроль включает: визуальный, инструментальное и лабораторное определение
показателей свойств, методы проведения которых
закреплены в государственных стандартах, технических условиях и ведомственных
строительных нормах.
5.2. При контроле
качества земляного полотна и песчаного подстилающего слоя и продольные профили
проверяют нивелировкой, размеры элементов в плане - стальной лентой, а ровность
поверхности - рейкой. Требуемая плотность грунтов земляного полотна и песчаного
подстилающего слоя должна быть не менее 0,98 от
оптимальной. Отклонение толщины песчаного слоя от проектной допускается в
пределах +/- 1 см. Коэффициент фильтрации песка должен быть не менее 3 м/сутки.
5.3. При приемке
качества установки бортовых камней проверяют их устойчивость, продольный уклон,
ровность кромки по горизонтали и вертикали, а также качество камней, их
размеры: возвышение бортов над лотком проезжей части, характер заделки швов.
5.4. При контроле
качества работ по устройству основания из щебеночных смесей проверяют: толщину
слоя, поперечные уклоны; уплотнение; ровность в соответствии со СНиП
3.06.03-85.
5.5. При приемке
основания из цементобетона и укатываемого малоцементного бетона проверяют отсутствие трещин,
прочность бетона лабораторными испытаниями вырубок, правильность установки
люков колодцев и водоприемных решеток. Допускаемые отклонения от проекта не
должны превышать по толщине плиты +/- 10 мм, по ровности - 5 мм при проверке
3-метровой рейкой, по прочности при испытании на изгиб - 5%, на сжатие - 10%.
5.6. В процессе
устройства асфальтобетонного покрытия контролируют:
а) ровность,
плотность и состояние (обработка вяжущими) основания,
правильность установки бортовых камней, решеток и люков колодцев подземных
сетей;
б) температуру
смеси на всех стадиях устройства покрытия;
в) ровность и
равномерность толщины устраиваемого слоя с учетом коэффициента уплотнения;
г) режим
уплотнения;
д) качество
сопряжения полос асфальтобетонного покрытия;
е) соответствие
поперечного и продольного уклонов проекту.
5.7. При контроле
готового покрытия проверяют: геометрические размеры, поперечные уклоны, толщину
слоев и сцепление их с нижележащими; коэффициент
уплотнения; показатели физико-механических свойств асфальтобетона, ровность и
коэффициент сцепления асфальтобетонного покрытия.
5.8. Ширину и
поперечный профиль покрытий проверяют через 100 м, ровность покрытия в
продольном и поперечном направлении проверяют через 30 - 50 м. Замеры ровности
производят на расстоянии 1 - 1,5 м от бортового камня.
5.9. Для контроля
качества готового асфальтобетонного покрытия отбираются пробы (вырубки и керны)
не ближе 1,5 м от бортового камня, пробы отбирают не ранее чем через 3-ое суток
после уплотнения и открытия движения автомобильного транспорта из расчета три
пробы с каждых 700 м2 покрытия.
5.10. Цементобетонные
покрытия принимаются к сдаче в 28-суточном возрасте и при наличии результатов
испытаний. При приемке проверяют:
- соответствие
утвержденному проекту конструкции основания, подстилающего слоя, дренажных
устройств и водостока - по актам на "скрытые" работы, журналам
производства работ и лабораторным данным;
- соответствие
уложенной смеси требованиям ГОСТа или требованиям настоящих Технических
рекомендаций;
- качество ухода за
бетоном по данным журналов;
- состояние
поверхности (отсутствие раковин, неровностей, наплывов, трещин);
- правильность
устройства швов;
- правильность
установки люков, колодцев, решеток.
Допускаемые
отклонения от проекта не должны превышать: по ширине покрытия - 5 см; толщине
плиты - 10%; по поперечному уклону - 5%; по ровности при проверке 3-метровой
рейкой - 5 мм; по прочности при испытании на изгиб - 5% и на сжатие - 10%.
6. ТЕХНИКА
БЕЗОПАСНОСТИ
6.1. При
строительстве различных слоев дорожной одежды следует соблюдать требования
строительных норм и правил по технике безопасности в строительстве, изложенные
в СНиП 12-03-2001 "Безопасность труда в строительстве", "Правила
по охране труда в дорожном строительстве", М., Стройиздат,
1989 г.
7. ОХРАНА
ОКРУЖАЮЩЕЙ СРЕДЫ
7.1. При устройстве
различных конструкций следует руководствоваться "Правилами организации
подготовки и производства земляных и строительных работ в г. Москве"
(Постановление Правительства Москвы N 207 от 17 марта 1998 г.).
7.2. В
подготовительный период строительства необходимо:
- оградить участок
производства работ;
- расчистить
площадку от кустарника и мелколесья, от пней и камней;
- снять
растительный слой грунта, переместить его на площадки, указанные в проекте, и в
дальнейшем использовать его при устройстве газонов;
- произвести
пересадку деревьев с трассы строящейся дороги;
- оставшиеся
деревья рядом со строящейся дорогой должны быть ограждены с целью недопущения
их повреждения при движении построечного транспорта.
7.3. На
строительной площадке должны быть определены и оборудованы специальные места
для заправки горючим и водой дорожно-строительных машин.
7.4. Газоны,
предусмотренные проектом озеленения дороги, должны быть засеяны многолетними
травами.
7.5. Все ИТР и
рабочие должны пройти инструктаж по охране окружающей среды в пределах
строящейся дороги.
7.6. Территория
строительной площадки после окончания работ по устройству дороги должна быть
очищена от строительного мусора и спланирована по проектным отметкам.
Приложение
1
ОСНОВНЫЕ
ПОЛОЖЕНИЯ
МЕТОДИКИ РАСЧЕТА
ИЗГИБАЕМЫХ ПОКРЫТИЙ С УЧЕТОМ
ПРОДОЛЬНЫХ СИЛ.
ПРИМЕР РАСЧЕТА
Проведенные НИИМосстроем исследования показали, что появление трещин и
нарушение целостности асфальтобетонных покрытий на различных основаниях
происходит, в основном, в период нулевых и небольших отрицательных и
положительных температур, когда несущая способность переувлажненного основания
минимальная, а асфальтовый бетон не дает значительных прогибов и работает как
упруго-жесткий материал.
Для учета этих
особенностей работы асфальтобетонных покрытий, когда их эксплуатационное состояние
определяется не максимально допустимой величиной прогиба, а в большей степени
кривизной поверхности, правильнее определять толщину не только бетонных, но и
асфальтобетонных покрытий, используя выводы теории упругости.
При этом дорожные
одежды должны проектироваться так, чтобы была обеспечена их прочность и
эксплуатационная надежность от влияния климатических факторов и автомобильных
нагрузок с учетом величин горизонтальных усилий, возникающих при торможении и
разгоне автотранспорта, движении на закруглениях и других особенностей. Чтобы
учесть в расчетах как вертикальные, так и горизонтальные составляющие нагрузки,
необходимо произвести соответствующую коррекцию.
При торможении
автотранспорта между колесами и покрытием дорожной одежды возникают
тангенциальные реакции
,
направленные горизонтально против движения, величина которых изменяется от 0 до
своего максимума и определяется по формуле:
,
где
- тормозной момент;
- радиус колеса автомобиля.
Максимальное
значение тангенциальных реакций характеризуется сцеплением колеса с покрытием
дорожной одежды без пробуксовки, поэтому значения тормозного (горизонтального)
усилия можно определить из зависимости
,
где
- коэффициент сцепления между колесом
автомобиля и дорожным покрытием;
P - масса
транспортного средства, приходящаяся на колеса.
Для повышения
эксплуатационных показателей дорог рекомендуемые конструкции на упругом
основании должны рассчитываться с учетом повторяемости воздействия нагрузок, а
разработанные составы смесей должны обеспечивать нормируемые коэффициенты
сцепления колес автотранспорта с покрытием.
Расчетная
интенсивность движения для магистральных улиц общегородского значения должна
быть не менее 4000 авт./сутки на одну полосу движения, районного значения не
менее 1000 авт./сутки.
На горизонтальном
сухом покрытии значение тормозного усилия может составить теоретически 75 - 80%
от полной массы транспортного средства, а ввиду того, что возникновение
тормозного усилия является следствием торможения автотранспорта, расчет
дорожных покрытий следует производить от совместного действия вертикальной и
горизонтальной нагрузок.
На рисунке 1, а
представлена расчетная схема плиты на упругом основании для определения
внутренних усилий от воздействия вертикальной и горизонтальной нагрузок. Здесь
вертикальная нагрузка P вызовет вертикальную реакцию упругого основания
, а
также горизонтальные реакции
и
, за
счет удлинения нижней грани плиты при изгибе. Горизонтальное усилие
вызовет реакцию упругого основания
,
препятствующую скольжению плиты по упругому основанию. Состояние равновесия
исходной системы будет сохраняться при соблюдении трех известных условий
статики. В результате соблюдения первого условия (сумма проекции всех сил на
ось абсцисс должна быть равна нулю) получаем, что значение равнодействующей от
вертикальной реакции упругого основания
по всей площади опирания
плиты по абсолютному значению будет равно вертикальному усилию P, т.е.
.
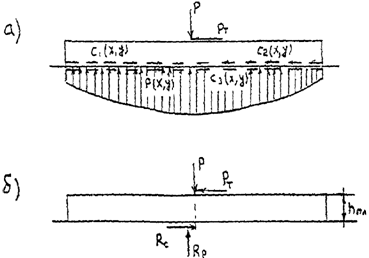
Рис. 1 а,
б. Расчетная схема плиты на упругом
основании под
действием заторможенного
(блокированного без
проскальзывания) колеса
автомобиля (а) и
эквивалентная схема (б)
При соблюдении
второго условия (сумма проекций всех сил на ось ординат должна быть равна нулю)
получаем, что равнодействующая горизонтальных реакций по всей площади опирания плиты равна по модулю горизонтальному усилию
, т.е.

;
.
Третье условие
статики (сумма моментов всех сил относительно края плиты должна быть равна
нулю) соблюдается, если внешний изгибающий момент, образованный парой сил
и
,
компенсируется моментом сил P и
, что
возможно только при смещении равнодействующей вертикальной реакции
по оси абсцисс (рис. 1, б).
Для введения в
расчет некоторого тормозного усилия необходимо произвести преобразование
исходной расчетной схемы таким образом, чтобы, изменив сочетания прикладываемой
внешней нагрузки, сохранить неизменной вертикальную реакцию упругого основания,
т.е. P(x, y) = const. Равнодействующая горизонтальной
реакции основания
и тормозное усилие
образуют пару сил с плечом, равным толщине плиты
,
которую можно заменить эквивалентным изгибающим моментом M (рис. 2, а).
Изгибающий момент M можно заменить фиктивной парой сил
и
,
равных между собой по модулю, противоположно направленных и действующих в
вертикальной плоскости (рис. 2, б).
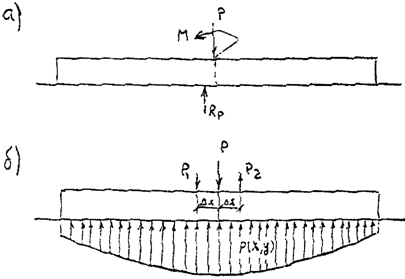
Рис. 2 а, б. Фиктивные расчетные схемы плиты
на упругом
основании для определения внутренних усилий
от воздействия
вертикальной и горизонтальной нагрузок
в местах усиленного
влияния транспортных нагрузок
Таким образом,
условием эквивалентности исходной и конечной расчетных схем является равенство
изгибающих моментов, т.е.
и
,
где
,
, в
итоге получаем
.
В полученной
зависимости величина
,
обозначающая расстояние между силами
, P и
P,
, не
должна превышать диаметр отпечатка следа колеса автомобиля, потому что
тормозное усилие, так же как и вертикальная нагрузка от массы транспортного
средства, передается на покрытие дорожной одежды посредством колеса.
С целью определения
влияния тормозного усилия на работу дорожной одежды была рассчитана
экспериментальная конструкция, представляющая собой железобетонную плиту
2П60.18 с размером 6,0 x 1,75 x 0,14 м3 на песчаном основании. В расчете
использовались следующие исходные данные: модуль упругости плиты E = 330000
МПа, коэффициент Пуассона плиты
,
модуль деформации основания
(что соответствует коэффициенту постели К = 4,0), коэффициент Пуассона основания
.
Расчет производился
по разработанной в НИИМосстрое методике определения
прогибов и изгибающих моментов в плите на упругом основании с коэффициентом
постели (модель Винклера), которая основывается на
использовании метода конечных разностей. Методика позволяет производить расчет
плит любой конфигурации и жесткости от любых произвольно приложенных одиночных
и комбинированных нагрузок с учетом кручения, переменных величин жесткости и
температуры с соблюдением всех граничных условий и размеров плит. Метод основан
на замене дифференциальных уравнений соответствующими уравнениями в конечных
разностях, т.е. введении конечных разностей вместо дифференциалов. С этой целью
поверхность плиты конечных размеров разбивается на равные прямоугольники,
образующие упругую сетку, и чем больше число узловых точек сетки, тем больше
неизвестных перемещений, тем точнее полученные результаты.
Составление
уравнений в конечных разностях изгиба плиты на упругом основании для всех узлов
упругой сетки в пределах контура плиты, а также граничных условий, обеспечивает
составление матрицы алгебраических линейных уравнений, необходимых для
определения величин неизвестных прогибов, а затем и изгибающих моментов.
Решение системы уравнений осуществляется методом Гаусса или другими известными
методами.
Этапы расчета:
- составление
уравнений прогиба плиты в конечных разностях для всех узловых точек в контуре
плиты;
- составление
уравнений граничных условий;
- проверка
полученных матриц A и B;
- решение матрицы
от всех видов загружений (получение значений прогибов
в узлах упругой сетки);
- определение
изгибающих величин моментов по найденным перемещениям;
- уточнение величин
изгибающих моментов под сосредоточенным грузом, распределенным по площадке,
размером
;
- оформление
полученных результатов.
Схема расположения
узлов упругой сетки в декартовых координатах приведена на рис. 3.
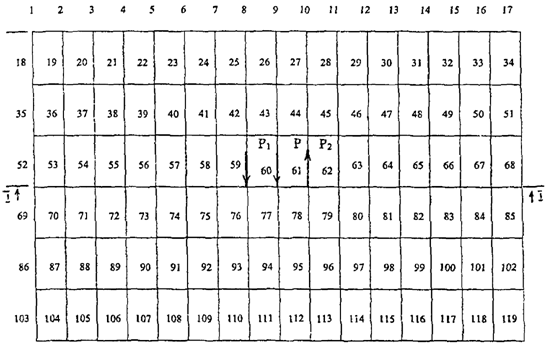
Рис. 3. Схема
расположения узлов
упругой сетки плиты
2П60.18
На рис. 3 не
показаны 2 ряда законтурных точек, необходимых для составления матрицы
уравнений. Расчет производился для двух вариантов нагружения
конструкции. В первом варианте сосредоточенная нагрузка величиной 50 кН
прикладывалась в центре плиты, т.е. в точке 60 упругой сетки. Во втором
варианте кроме центральной нагрузки в соседних по оси абсцисс точках
прикладывались фиктивные силы
и
,
причем
с отрицательным знаком. Значение фиктивных
сил, подсчитанное по приведенной выше зависимости, составило 0,13P или 6,5 кН. Такая схема загружения
конструкции соответствует торможению заднего колеса расчетного автомобиля в
центре плиты (рис. 4).
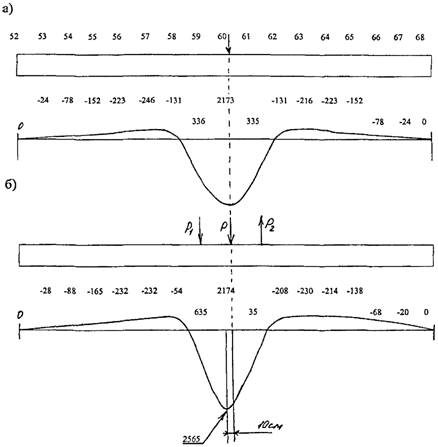
Рис. 4.
Эпюры моментов
плиты на упругом
основании в продольном сечении 1-1:
а) под действием
одиночной нагрузки P;
б) под действием
группы сил
,
, P
Произведенные
расчеты показали, что при торможении автотранспорта возникающее тормозное
(горизонтальное) усилие оказывает влияние на величины расчетных изгибающих
моментов. Наибольшая величина положительного изгибающего
момента от действия одиночной вертикальной силы P составляет 217,38 кН, в то
время как от совместного действия вертикальной и горизонтальной нагрузок
величина этого момента составляет 265,5 кН. Таким
образом, увеличение изгибающего момента в плите при торможении составило 18%,
причем максимум эпюры изгибающих моментов смещен в направлении действия
горизонтального усилия на 10 см, что подтверждено экспериментально.
Установленные
особенности работы дорожных конструкций в местах, подверженных усиленному
воздействию транспортных нагрузок, вызывают необходимость учета их усилением
толщин конструктивных слоев покрытия на 7 - 18% в зависимости от применяемых
конструктивных решений или же применением современных композитных материалов,
повышающих физико-механические характеристики конструктивных слоев дорожных
одежд.
Приложение
2
ОСНОВНЫЕ
ПОЛОЖЕНИЯ
МЕТОДИКИ РАСЧЕТА
ДОРОЖНЫХ ОДЕЖД ЖЕСТКОГО ТИПА
ПРИ ПОЭТАПНОМ
СТРОИТЕЛЬСТВЕ
1. Расчет дорожной
одежды и ее отдельных конструктивных слоев должен производиться по методу
предельных состояний на совместное воздействие силовых и климатических факторов
- автомобильных нагрузок и изменение температуры в суточном режиме, учитывая
вероятностный характер их сочетания в различных количественных соотношениях
коэффициентов перегрузок
и сочетаний
.
2. Расчет дорожной
одежды по методу предельных состояний должен обеспечивать ее сохранность от:
- хрупкого и
вязкого разрушения при однократном приложении максимальных нагрузок (расчет на
прочность);
- усталостного
разрушения под воздействием многократных повторяющихся нагрузок (расчет на
выносливость);
- потери
устойчивости формы вследствие морозного пучения земляного полотна.
3. Расчет дорожных
одежд проводят в следующей последовательности:
а) расчет одежды по
морозоустойчивости, т.е. определение общей толщины дорожной одежды, при которой
ее морозное пучение находится в заданных пределах;
б) расчет толщины
песчаного подстилающего слоя, обеспечивающего осушение одежды, верхнего слоя
земляного полотна и высокие прочностные показатели грунтового основания в
весенне-осенний период;
в) расчет
конструктивных слоев одежды по прочности и выносливости, обеспечивающей
соответствие возникающих усилий (растягивающих напряжений в связных слоях
одежды с учетом продольных сил) расчетным сопротивлениям материалов
соответствующих слоев.
4. Сочетание
нагрузок, коэффициенты сочетаний
, а
также расчетное положение автомобильной нагрузки следует принимать по таблице
1.
Таблица 1
┌─────────────┬─────────────────────────────────────────┬─────────────────┐
│ Вид
│ Автомобильная
нагрузка │ Температура
│
│
предельного
├────────────────┬────────────────────────┤ воздействия в │
│ состояния
│на полосе наката│на середине
продольного │ суточном режиме │
│ │ в центре плиты
│ края плиты │ │
│
├────────────────┴────────────────────────┴─────────────────┤
│ │ коэффициент сочетаний п
│
│ │ с │
├─────────────┼────────────────┬────────────────────────┬─────────────────┤
│Прочность │ 0,9 <*> │ 0,9 │ 0,9
│
├─────────────┼────────────────┼────────────────────────┼─────────────────┤
│Выносливость
│ 0,9 │ - │ 0,9
│
└─────────────┴────────────────┴────────────────────────┴─────────────────┘
--------------------------------
<*> При
расчете однослойного основания из цементобетона на
период строительства дорожной одежды.
5. Расчетной зоной
при расчете на прочность и выносливость является подошва (нижняя грань)
конструктивного слоя в месте приложения автомобильной нагрузки в сочетании с
температурными напряжениями. Критерием прочности является выражение:
,
где
- суммарное расчетное напряжение;
- нормативные напряжения от автомобильной
нагрузки;
- расчетные напряжения от суточного изменения
температуры.
7. Расчет на
выносливость жестких слоев одежды проводят исходя из следующих предпосылок:
- накопления
усталостных деструктивных явлений в материале при многократном комплексном
воздействии нормативных нагрузок;
- роста прочности
бетона во времени, т.е. наличия структурообразующего процесса;
- возможности
однократного воздействия на одежду в любой момент времени расчетной
автомобильной нагрузки в сочетании с температурными напряжениями.
Критерием
выносливости является выражение:
,
где
- коэффициент роста прочности бетона (п.
2.15);
- коэффициент усталости материала (п. 2.6),
определенный от многократного воздействия нормативных нагрузок.
8. Учет влияния
продольных сил на расчет изгибаемых слоев дорожных одежд производится в
соответствии с методикой, изложенной в Приложении 1.
При проверке
прочности дискретных слоев основания сдвигающим усилиям расчетным случаем
является проезд построечного транспорта по нижнему слою основания из цементобетона, цементогрунта или
щебня.
9. Учет несущей
способности асфальтобетонного покрытия при расчете дорожной одежды по прочности
и выносливости проводят по методике, изложенной в инструкции.
10. Расчет дорожной
одежды и ее элементов следует проводить для всех стадий строительства и
эксплуатации.
Основными
расчетными случаями являются:
- работа одежды (основания)
на 1-ом этапе строительства на воздействие построечного транспорта;
- работа одежды по
окончанию 2-го этапа строительства на воздействие городского транспорта.
Кроме этого, в
соответствии с принятой организацией строительства, следует проводить
проверочные расчеты прочности всех слоев на единичное воздействие тяжелого
строительного транспорта в период строительства дорожной одежды.
Приложение
3
МЕХАНИЗМЫ И
ИНСТРУМЕНТЫ ДЛЯ СТРОИТЕЛЬСТВА ДОРОГ В МЕСТАХ,
ПОДВЕРЖЕННЫХ
УСИЛЕННОМУ ВОЗДЕЙСТВИЮ ТРАНСПОРТНЫХ НАГРУЗОК
АВТОГРЕЙДЕР ДЗ-98В
Предназначен для возведения земляного полотна, устройства дорожных оснований и
покрытий, разнообразных планировочных работ, профилирования и отделки дорожного
полотна, а также для ремонта и содержания дорог, городских проездов и площадей.
Техническая
характеристика
Мощность
двигателя, кВт (л.с.) - 321 (180)
Трансмиссия
- механическая
Грейдерный
отвал:
длина, мм - 4270
высота, мм - 740
угол
резания, град -
30 - 70
угол
срезаемого откоса, град -
0 - 90
боковой
вынос, мм - 2400
опускание, мм - 500
Скорость
движения, км/ч:
вперед - 4,43 -
47
назад - 5,32
- 56
Габаритные
размеры, мм - 10300 x 3020 x 3950
Масса
эксплуатационная, т
- 19,5
Дополнительное оборудование: бульдозерное, кирковщик,
снегоочистительное
Изготовитель: ООО "Челябинский завод дорожно-строительных машин
им. Колющенко"
г. Челябинск
454, Россия, ул. Ст. Разина, 1
(3512) 61-24-07
АВТОГРЕЙДЕР ГС-1801
Предназначен для землеройно-профилировочных работ.
Техническая
характеристика
Мощность
двигателя, кВт (л.с.) - 132 (180)
Трансмиссия -
гидромеханическая
Грейдерный
отвал:
длина, мм - 3740
высота, мм - 620
боковой
вынос, мм - 700
угол
срезаемого откоса, град -
45
угол
поворота, град - 360
опускание ниже опорной поверхности, мм - 450
Бульдозерный отвал, мм:
длина - 2500
высота - 800
заглубление - 100
Рыхлитель:
ширина
рыхления, мм - 2100
глубина
рыхления, мм - до 250
число
зубьев -
5
Скорость
движения, км/ч:
вперед - 0 - 42
назад - 0 -
26,2
Габаритные
размеры, мм - 10500 x 2600 x 3550
Масса,
т -
17,5
Изготовитель:
ООО "Радицкий машиностроительный завод"
г. Брянск
241031, Россия, бульвар Щорса, 7
(901) 991-23-74
182116 Озеро
АВТОГРЕЙДЕР А-120
Предназначен для возведения земляного полотна, устройства дорожных оснований и
покрытий, разнообразных планировочных работ, а также для ремонта и содержания
дорог, городских проездов и площадей.
Техническая
характеристика
Мощность
двигателя, кВт (л.с.) - 132 (180)
Трансмиссия -
гидромеханическая
Рама -
шарнирно-сочлененная
угол
складывания -
27 град
Грейдерный
отвал, мм:
длина - 3740
высота - 650
боковой
вынос -
935
максимальное заглубление - 450
Бульдозерный отвал:
длина, мм - 2520
Скорость
движения, км/ч:
вперед - 7; 13;
24, 42
назад - 7; 25
Габаритные
размеры, мм
- 10800 x 2560 x 3550
Масса,
т -
14,2
Изготовитель: ООО "Челябинский завод дорожно-строительных машин
им. Колющенко"
г. Челябинск
454, Россия, ул. Ст. Разина, 1
(3512) 61-24-07
АВТОГРЕЙДЕР ДЗ-180А
Предназначены для
землеройно-профилировочных работ при строительстве и содержании дорог,
планировке откосов, выемок и насыпей, устройстве корыта дороги и боковых канав,
для смешивания грунтов с добавками и вяжущими материалами на полотне дороги,
рыхления асфальтовых покрытий и тяжелых грунтов в различных климатических
условиях.
Техническая
характеристика
Мощность
двигателя, кВт - 99
Трансмиссия -
механическая
Тип
рамы
- жесткая и шарнирно-
сочлененная
Грейдерный
отвал полноповоротный:
длина, мм - 4270
высота, мм - 740
угол
резания, град -
30 - 70
угол
срезаемого откоса, град -
0 - 90
боковой,
мм - 1000
опускание, мм - 500
Габаритные
размеры, мм - 9975 x 2500 x 3450
Масса,
т -
13,5
Оборудован
кирковщиком, системой "Профиль 30-2"
Изготовитель: ОАО "Брянский Арсенал", г. Брянск
241000, Россия, ул. Калинина, 98
(0832) 74-21-66
182115 Диск
АВТОГРЕЙДЕР
ДЗ-122А, ДЗ-122Б
Предназначены для
планировочных и профилировочных работ при строительстве и ремонте дорог,
возведении насыпей, сооружении дорожного корыта и распределении в нем
материалов основания дорог для очистки дорог от снега. Поставляются в комплекте
с бульдозерным отвалом и копровщиком. Базовые модели
имеют дополнительно по три исполнения, отличающиеся конструктивным исполнением
узлов.
Техническая
характеристика
Мощность
двигателя, кВт -
99
Грейдерный
отвал полноповоротный:
длина, мм - 3744
высота, мм - 632
угол
резания, град -
30 - 70
угол
срезаемого откоса, град -
90
боковой
вынос в обе стороны, мм - 800
Бульдозерный отвал, мм:
длина - 2527
высота - 860
Кирковщик, мм:
ширина киркования - 1318
глубина киркования - 260
Габаритные
размеры, мм - 10150 x 2500 x 3550
ДЗ-122А с
жесткой рамой, гидромеханической трансмиссией;
скорость движения вперед - 6,9 - 42,1 км/ч; назад -
7,0 - 23,8 км/ч;
масса - 14,523 т. ДЗ-122Б с шарнирно-сочлененной
рамой, гидромеханической
трансмиссией; скорость движения вперед - 7,4 - 43
км/ч;
назад - 7,7 - 25,2 км/ч; угол складывания полурам - 30 град;
масса - 14,6 т
Изготовитель: ОАО "Орловский завод дорожных машин", г. Орел
302042, Россия, Кромское шоссе, 3
(08622) 2-34-38
148143 Отвал
АВТОГРЕЙДЕР
ГС-10-01-02
Предназначен для выполнения различных видов землеройных и профилировочных работ на
грунтах I - III категорий при температуре окружающей среды от +40 до -40 °C.
Техническая
характеристика
Мощность
двигателя, кВт (л.с.) - 77 (105)
Передача -
гидромеханическая
Скорости, км/ч:
вперед - 4,7;
16,3; 10,9;
20,9; 35; 40
назад - 5,4;
16,0
Рама -
шарнирно-сочлененная
Грейдерный
отвал, мм:
длина - 2730
высота - 470
боковой
вынос - не менее 600
опускание ниже опорной поверхности - не менее 600
угол
поворота, град -
100
Бульдозерный отвал, мм:
длина - 2400
высота - 620
опускание ниже опорной поверхности - 100
подъем
над опорной поверхностью -
400
угол
резания (нерегулируемый), град -
50
Рыхлитель,
мм:
ширина
полосы рыхления - 1300
глубина
рыхления - до
250
число
зубьев -
3 (5)
Масса,
т -
6,3
Изготовитель: ОАО "Брянский Арсенал", г. Брянск
241000, Россия, ул. Калинина,
98
(0832) 74-21-66
182115 Диск
АВТОГРЕЙДЕР
ДЗ-201.01
Предназначен для
землеройно-профилировочных работ, а также очистки дорог от снега, грязи и др.
Техническая
характеристика
Базовый
трактор -
ЛТЗ-60АВ
Мощность
двигателя, кВт (л.с.) - 44,1 (60)
Грейдерный
отвал:
длина, мм - 2500
высота, мм - 500
боковой
вынос, мм - 500
заглубление, мм - 100
угол
резания, град -
30 - 70
угол
поворота, град - 34
Бульдозерный отвал, мм:
длина - 2000
высота - 500
заглубление - 50
Скорость
движения, км/ч:
вперед - до 20
назад - до
3,5
База/колея, мм - 5210/1495
Масса,
т -
6,25
Изготовитель: ООО "Радицкий машиностроительный
завод", г. Брянск
241031, Россия, бульвар Щорса, 7
(901) 991-23-74
182116 Озеро
АВТОГРЕЙДЕР ДЗ-201
Предназначен для
планировочных работ, а также очистки дорог от снега, грязи и др.
Техническая
характеристика
Базовый
трактор -
МТЗ-80/82
Мощность
двигателя, кВт (л.с.) - 57,4 (78)
Грейдерный
отвал:
длина, мм - 2500
высота, мм - 500
боковой
вынос, мм - 500
заглубление, мм - 100
угол
резания, град -
30 - 70
угол
поворота, град - 34
Бульдозерный отвал, мм:
длина - 2000
высота - 500
заглубление - 50
Скорость
движения, км/ч:
вперед - 1,9 - 35,5
назад - 4 - 9
База/колея, мм - 5230/1620
Масса,
т -
6,3
Изготовитель: ООО "Радицкий
машиностроительный завод",
г. Брянск
241031, Россия, бульвар Щорса, 7
(901) 991-23-74
182116 Озеро
ПРОФИЛИРОВЩИКИ
ОСНОВАНИЯ НА РЕЛЬСОВОМ ХОДУ Д-345А, Д-345Б
Предназначены для
подготовки, окончательной планировки и уплотнения песчаного основания под бетон
или сборные плиты при строительстве дорожных и аэродромных покрытий.
Техническая
характеристика
Модель
Д-345А: - ширина полосы плоского покрытия - 3,5; 5,0; 7,0 м
- двускатного
покрытия - 7,0 м
Модель
Д-345Б: - ширина полосы плоского покрытия - 3,75; 7,5 м
- двускатного
покрытия - 7,5 м
Изготовитель: Коростеньский завод дорожного машиностроения.
г. Коростень, Житомирская обл., 260100,
Республика
Украина, ул. Октябрьская, 1
(04142) 4-25-58
ПРОФИЛИРОВЩИК-ГРУНТОСМЕСИТЕЛЬ
ДС-178
Профилировщик-грунтосмеситель на пневмоколесном ходу полуприцепной к
трактору "Кировец" однопроходный
предназначен для устройства цементогрунтовых
оснований и асфальтобетонных покрытий.
Техническая
характеристика
Производительность, м/ч:
- при профилировании - 240
- при грунтосмешении - 180
Ширина
захвата, м - 3,75
Глубина
обработки, мм - 200
Рабочая
скорость движения, м/мин - 1,5 - 15
Габаритные
размеры, м - 13,55 x 5,78 x 3,61
Масса,
т -
25,8
Изготовитель: ОАО "Брянский Арсенал", г. Брянск
241000, Россия, ул. Калинина, 98
(0832) 74-23-33
182115 Диск
РАСПРЕДЕЛИТЕЛИ
ЦЕМЕНТОБЕТОНА
НА РЕЛЬСОВОМ ХОДУ
Д-375А, Д-375Б
Предназначены для
распределения цементобетонной смеси для последующего уплотнения и отделки
дорожных покрытий.
Техническая
характеристика
Модель
Д-375А: - ширина полосы плоского покрытия - 3,5; 5,0; 7,5 м
- двускатного
покрытия - 7,0 м
Модель
Д-375Б: - ширина полосы плоского покрытия - 3,75; 7,5 м
- двускатного покрытия - 7,5 м
Изготовитель: Коростеньский завод дорожного
машиностроения,
г. Коростень, Житомирская обл., 260100, Республика
Украина, ул. Октябрьская, 1
(04142) 4-25-58
БЕТОНОУКЛАДЧИК
ДС-169
Бетоноукладчик на
гусеничном ходу со скользящими формами производительностью 120 м/ч предназначен
для устройства монолитных цементобетонных покрытий при строительстве
внутрихозяйственных дорог местного значения.
Техническая
характеристика
Ширина укладываемой полосы, м -
4,5; 6,0; 7,0; 7,5
Толщина
укладываемой полосы, мм - 160 - 240
Мощность
двигателя, кВт -
125
Рабочая
скорость, м/мин - 1 - 20
Габаритные
размеры, м - 5,7 x 7,0 x 3,7
Масса,
т -
21,8
Изготовитель: ОАО "Брянский Арсенал", г. Брянск
241000, Россия, ул. Калинина, 98
(0832) 74-23-33
182115 Диск
БЕТОНООТДЕЛОЧНЫЕ
МАШИНЫ НА РЕЛЬСОВОМ ХОДУ Д-376А, Д-376Б
Предназначены для
разравнивания, уплотнения и выглаживания уложенного
бетона.
Техническая
характеристика
Модель
Д-345А: - ширина полосы плоского покрытия - 3,5; 5,0; 7,0 м
- двускатного
покрытия - 7,0 м
Модель
Д-345Б: - ширина полосы плоского покрытия - 3,75; 7,5 м
- двускатного
покрытия - 7,5 м
Изготовитель: Коростеньский завод дорожного
машиностроения,
г. Коростень, Житомирская обл.
260100 Республика Украина, ул. Октябрьская, 1
(04142) 4-25-58
БЕТОНОУКЛАДЧИК
COMMANDER III ФИРМЫ GOMAKO
Бетоноукладчик со
скользящими формами предназначен для устройства монолитных бордюров,
водосточных желобов, тротуаров, пешеходных дорожек, ограждений, парапетов,
бетонных покрытий шириной 6 м.
Техническая
характеристика
Тип
двигателя
- дизельный
Мощность,
кВт -
126,1
Скользящая
форма для устройства бордюра
и
водосточного желоба:
ширина, мм - 914
По
отдельному заказу возможна поставка
скользящих
форм для устройства:
монолитных тротуаров, бордюров,
водосточных желобов и др.
Фрезерный
рабочий орган для профилирования
основания
(секционный):
диаметр
фрезы, мм
- 610
ширина, мм - 1067
(в т.ч. ведущей секции - 610 мм, уширителя
- 457 мм)
Смещение
рабочего органа:
в
сторону, мм - 914
вверх, мм - 457
Габаритные
размеры, м:
Трехгусеничной машины
длина - 6,59
высота - 2,62;
3,53
ширина
транспортная -
2,59
Масса, кг - 12701;
13291
Четырехгусеничной машины в транспортном положении
длина -
10,74; 8,92
высота - 2,92;
3,23
ширина - 2,51
Масса, кг - 18961
АСФАЛЬТОУКЛАДЧИК
ДС-199
Асфальтоукладчик на гусеничном ходу с электрогидравлическим управлением предназначен для укладки и предварительного уплотнения
асфальтобетонных и битумоминеральных смесей на подготовленное основание при
строительстве автомобильных дорог улиц и площадей.
Техническая
характеристика
Производительность, т/ч - 210
Толщина
покрытия, мм
- 220
Мощность
двигателя, кВт -
44
Рабочая
скорость, м/мин - 1,6 - 7,7
Транспортная скорость, км/ч - 4,2
Емкость
бункера, т -
10
Ширина
рабочего органа, м:
минимальная - 3
максимальная - 4,4
Габаритные
размеры, м - 5,25 x 3,15 x 3,3
Масса,
т - 13,5
Изготовитель: ОАО "Дормашина" г.
Николаев, Республика Украина, 82019,
пр-т Ленина, 93
(0512) 37-40-74
АСФАЛЬТОУКЛАДЧИК
ДС-191-504 (ДС-191-506)
Гидрофицированный колесный асфальтоукладчик для укладки
покрытий дорог всеми видами асфальтобетонных смесей шириной от 3,0 до 4,5 метра
и толщиной до 300 мм с профилем покрытия до 7,5 м, модель ДС-191-506 - ширина
покрытия от 3,0 до 6,2 м.
Техническая
характеристика
Производительность, т/ч - до 500
Толщина
покрытия, мм - до 300
Модель
двигателя -
Д-245
Мощность
двигателя, кВт (л.с.) - 77,2 (105)
(По спецзаказу может устанавливаться двигатель
А-260.2 с мощностью 90,4 кВт (123 л.с.))
Скорости
движения:
транспортная, км/ч - 16
рабочая, м/мин - 0 - 30
Габаритные
размеры, мм - 7,6 x 3,6 x 3,7
Масса,
т -
19 (20)
Автоматический контроль профиля осуществляется системой
САУ
"РЕЛЬЕФ".
Изготовитель: ООО "Радицкий
машиностроительный завод", г. Брянск
241031, Россия, бульвар Щорса, 7
(901) 991-23-74
182116 Озеро
АСФАЛЬТОУКЛАДЧИК
ДС-181
Предназначен для укладки и предварительного уплотнения асфальтобетонных и
битумоминеральных смесей на подготовленное и уплотненное основание при
строительстве автомобильных дорог, городских улиц и площадей. Самоходный колесный гидрофицированный
с системой автоматики.
Техническая
характеристика
Производительность, т/ч - до 250
Толщина
покрытия, мм - 50 - 300
Модель
двигателя -
Д-245
Мощность
двигателя, кВт (л.с.) - 77,2 (105)
Скорости
движения: - 0
- 10
транспортная, км/ч - 18
рабочая, м/мин - 0 - 60
Емкость
бункера, м3/т - 6,7/10
Ширина
укладываемой полосы, м: - 3 - 4,5
со
вставками, м - до 7,5
Габаритные
размеры, мм - 7,22 x 3,2 x 2,81
Масса,
т -
17,5
Модели ДС-181-01 и ДС-181М с газовым подогревом
Изготовитель: ОАО "Брянский Арсенал", г. Брянск
241000, Россия, ул. Калинина, 98
(0832) 74-23-33
182115 Диск
АСФАЛЬТОУКЛАДЧИК
АСФ-К-2-02
Гидрофицированный колесный асфальтоукладчик для укладки
покрытий дорог всеми видами асфальтобетонных смесей шириной от 2,2 до 3,75
метра с толщиной до 250 мм с односкатным профилем до 40%.
Техническая
характеристика
Производительность,
т/ч - до 150
Толщина
покрытия, мм - до 250
Модель
двигателя -
Д-243
Мощность
двигателя, кВт (л.с.) - 57,4 (78)
Рабочая
скорость, м/мин - 0 - 10
Транспортная скорость, км/ч - 0 - 10
Емкость
бункера, т -
8
Ширина
рабочего органа, м:
базовая - 2,2
минимальная - 2,2
максимальная - 3,75
Габаритные
размеры, мм - 6,05 x 2,9 x 3,65
Масса,
т
- 13
Автоматический контроль профиля - система автоматического управления
САУ "РЕЛЬЕФ-01М" поставляется по заказу
Изготовитель: ООО "Радицкий
машиностроительный завод", г. Брянск
241031, Россия, бульвар Щорса, 7
(901) 991-23-74
182116 Озеро
АСФАЛЬТОУКЛАДЧИК
VOGELE 1500 CAF
Гидрофицированный колесный асфальтоукладчик для укладки литых
асфальтобетонных смесей шириной от 2,5 до 5,0 м с толщиной до 250 мм с
односкатным и двускатным профилем до 40%.
Техническая
характеристика
Производительность, т/ч До 36
Толщина
покрытия, мм До 250
Рабочая
скорость, м/мин 0 - 6
Транспортная скорость, км/ч 0 - 75
Емкость
бункера, т
3,50
Ширина
рабочего органа, м:
базовая 2,5
минимальная 2,5
максимальная
5,0
Габаритные
размеры, м 5,38 x 2,9 x 3,7
Масса,
т
9,95
Автоматический контроль профиля.
Изготовитель: JOSEF
VOGELE AG
Neckarauer
Strasse 168-228
D-68146 Mannheim
РАСПРЕДЕЛИТЕЛЬ
Гидрофицированный самоходный колесный (гусеничный) распределитель литых
асфальтобетонных смесей шириной укладки от 1,0 до 13,0 м (в зависимости от типа
распределителя).
Техническая
характеристика
│GB 10-40│GB 25-50
│GB 50-80│GB 75-130│EB 25-40│EB 50-75│EB 80-120
Фирма- │Linnhoff│ │ │ │ Faendrich AG │
производитель
│ │ │ │ │ │
Ширина │ │ │ │ │ │ │
рабочего │ │ │ │ │ │ │
органа,
м
│ │ │ │ │ │ │
-
минимальная │ 1,00 │
2,50 │ 3,00
│ 3,00 │
1,00 │ 2,25
│ 3,00
-
максимальная│ 4,00 │
5,00 │ 8,00
│ 13,00 │
1,00 │ 7,50
│ 11,75
Изготовитель: LT Linnhoff Maschinenbau GmbH,
Alter Postweg
26,
D-21614 Buxtehude,
Germany
Tel: (49) 4161 866
118
Fax: (49) 4161 866
188
E-mail:
info@lintec-gmbh.de
FAEHNDRICH AG
Alter Postweg 26
D-21614 Buxtehude
Germany
Tel: +49 (0) 4161
866 20
Fax: +49 (0) 4161
866 222
E-mail:
FAEHNDRICH-AG@t-online.de
МАШИНА ДЛЯ
СТРОИТЕЛЬСТВА ДОРОГ ЛИТЫМ АСФАЛЬТОМ 5817
Предназначена для приема готовой литой асфальтобетонной смеси, транспортирования к
месту работ (при перемешивании и поддержании рабочей температуры в пределах 190
- 200 °C) и дозирования подачи смеси на ремонтный участок.
Техническая
характеристика
Тип
установки
Самоходная на шасси
Тип
двигателя
Дизельный, Д 120
Мощность
двигателя, кВт
10,4
Система
подогрева смеси:
вид
используемого топлива Дизельное
подогреватель Факельный,
144.В106
количество подогревателей, шт.
2
теплопроизводительность подогревателей, 4,5
кДж/ч
расход
топлива подогревателем, кг/ч 4
Транспортная скорость, км/ч 0 - 60
Емкость
бункера, т
6,6
Габаритные
размеры, м 10,0 x 2,5 x 3,0
Масса,
т
4,50
Автоматический контроль профиля
Изготовитель: МОСГОРМАШ
115201, г. Москва, Каширский проезд, 13
Тел. 112-12-12, тел./факс 111-63-71
МАШИНА ДЛЯ
СТРОИТЕЛЬСТВА ДОРОГ ЛИТЫМ АСФАЛЬТОМ ОРД-1025
Предназначена для приема готовой литой асфальтобетонной смеси, транспортирования к
месту работ (при перемешивании и поддержании рабочей температуры в пределах 190
- 200 °C) и дозирования подачи смеси на ремонтный участок.
Техническая
характеристика
Тип
установки
Самоходная на шасси
Тип
двигателя
Дизельный, Д 120
Мощность
двигателя, кВт
10,4
Система
подогрева смеси:
- вид
используемого топлива Дизельное
-
подогреватель
Факельный
-
количество подогревателей, шт.
2
- мощность
подогревателей, кВт 45
- расход
топлива подогревателем, кг/ч 4
Транспортная скорость, км/ч 0 - 60
Емкость
бункера, т 8
- 9
Габаритные
размеры, м
10 x 2,5 x 3,1
Масса
установленного оборудования, т
3,7
Изготовитель: ЗАО "БЕЦЕМА"
143400, г. Красногорск Московской обл.,
Ильинское ш., 2-й км
Тел.: (095) 562-90-32, 562-30-57.
МЕХАНИЗМЫ И
ИНСТРУМЕНТ ДЛЯ УПЛОТНЕНИЯ ГРУНТОВ,
ЩЕБЕНОЧНЫХ СМЕСЕЙ,
УКАТЫВАЕМЫХ БЕТОНОВ, ЛИТЫХ БЕТОННЫХ
СМЕСЕЙ, ПЛАСТИЧНЫХ
БЕТОНОВ, АСФАЛЬТОБЕТОННЫХ СМЕСЕЙ
┌────────────────┬─────────────┬──────┬───────────────────────────────────┐
│
Наименование, │ Марка
│Масса,│ Назначение, уплотняемый материал │
│
тип механизма │ механизма │
т │ │
├────────────────┼─────────────┼──────┼───────────────────────────────────┤
│ 1
│ 2 │
3 │ 4 │
├────────────────┼─────────────┼──────┼───────────────────────────────────┤
│Катки
самоходные│ ДУ-95-2 │ 1,15 │Предназначены для
уплотнения │
│вибрационные
│ ДУ-72 │ 3,8
│оснований и покрытий из различных
│
│с
гладкими
│ ДУ-54М │ 1,5
│строительных материалов тротуаров, │
│вальцами │ │ │площадок, дорог │
│ │ ДУ-96
│ 7,8 │Предназначены
для уплотнения │
│ │ ДУ-93
│8 (10)│оснований и покрытий из
различных │
│ │ ДУ-47Б
│ 8,5
│дорожно-строительных материалов
│
│ │ │ │(окончательная отделка) │
│ │ │ │при больших объемах работ │
├────────────────┼─────────────┼──────┼───────────────────────────────────┤
│Катки
самоходные│ ДУ-74-1 │ 9,5
│Предназначены для послойного │
│вибрационные │
ДУ-85-1 │ 13,5
│уплотнения насыпных грунтов
│
│с
кулачковыми
│ │ │и нижних слоев оснований из │
│вальцами │ │ │различных
гравийно-песчаных │
│ │ │ │и щебеночных материалов │
├────────────────┼─────────────┼──────┼───────────────────────────────────┤
│Катки │ ДУ-97
│ 7,6 │Предназначены
для уплотнения │
│комбинированные │
ДУ-64 │ 9,5 │дорожных оснований и покрытий │
│с
вибровальцом
│ ДУ-99 │
10 │из различных материалов │
│ │ │ │при больших объемах работ │
├────────────────┼─────────────┼──────┼───────────────────────────────────┤
│Катки
самоходные│ ДУ-65 │
12 │ " │
│пневмоколесные │
ДУ-100 │ 14
│
│
├────────────────┼─────────────┼──────┼───────────────────────────────────┤
│Вибротрамбовки
│Dunapac LC 50│ 53
│Уплотнение всех видов грунта
│
│ │Dunapac
LT 52│ 54 │и покрытий в стесненных местах, │
│ │Dunapac
LT 65│ 67 │у колодцев, водосливных решеток, │
│ │ │ │бортовых камней и др. │
├────────────────┼─────────────┼──────┼───────────────────────────────────┤
│Виброуплотнители│ ВУ-800
│ 0,045│Предназначены для уплотнения всех │
│(виброплиты)
│ ВУ-1500 │ 0,1
│видов дорожных покрытий и грунтов
│
│ │ ОУ-60
│ 0,08 │при малых объемах работ. │
│ │
ОУ-80 │ 0,11
│Рекомендуемая толщина уплотняемого │
│ │ ДУ-90
│ 0,27 │слоя несвязного грунта - 20 - 30 см│
│ │ ВП-3
│ 0,7 │ │
├────────────────┴─────────────┴──────┴───────────────────────────────────┤
│ Примечания.
1. Ориентировочное число проходов катков массой 6 - 14 т│
│по
одному следу для связных грунтов 10 - 12, для
несвязных и малосвязных│
│-
6 - 8 при глубине уплотнения (в плотном теле)
соответственно 20 - 50│
│и
25 - 60 см.
│
│ 2. Ориентировочное число проходов катков
массой 6 - 14 т по одному│
│следу
для укатываемых бетонных смесей 8 -
12 при наибольшей
толщине│
│уплотняемого
слоя 12 - 30 см.
│
│ 3. Устройство оснований и покрытий
дорожных сооружений из литых│
│бетонных
смесей производится с применением ручного комплекта инструментов│
│по
типу комплекта фирмы "СТЕНЛИ". │
│ 4. Характеристики приведенного
оборудования и координаты
заводов-│
│изготовителей приведены в
Московском территориальном строительном│
│каталоге МТСК-5.6 "Машины и
оборудование для инженерных и
дорожно-│
│строительных
работ. Машины коммунальные". │
└─────────────────────────────────────────────────────────────────────────┘
Общий вид
инвентаря, применяемого для строительства
дорог из литых
бетонных смесей
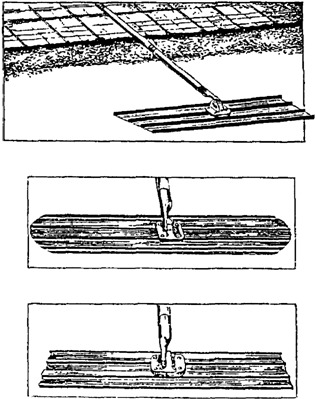
Разравнивание литой
бетонной смеси
при помощи
различной формы гладилок

Разравнивание и
уплотнение малоподвижной
и подвижной
бетонной смеси валиками
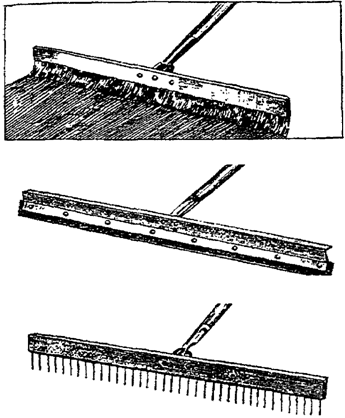
Инструменты для
обработки поверхности из свежеуложенного
бетона с волосяной
щеткой, резиновой насадкой
и приспособлением
для создания текстуры поверхности
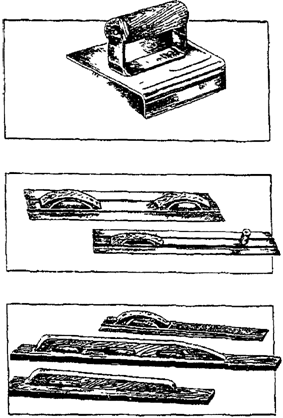
Инструменты для
обработки и контроля качества
поверхности
свежеуложенного бетона:
угловая затирка для
создания ровных кромок швов;
затирка и уровни
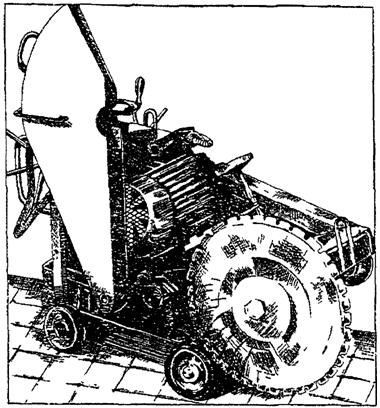
Общий вид нарезчика
температурных швов в бетонных
конструкциях (разработка НТЦ "Мосинжстрой")
АСФАЛЬТОУКЛАДЧИК
АСФК-2-04
(перспективный
образец)
Гидрофицированный колесный асфальтоукладчик для распределения
и укладки литых асфальтобетонных смесей шириной от 2,2 до 4,5 метров с толщиной
до 250 мм с односкатным профилем до 40%.
Техническая
характеристика
Производительность, т/ч - до 40
Толщина
покрытия, мм - до 250
Рабочая
скорость, м/мин - 0 - 45
Транспортная скорость, км/ч - 0 - 20
Емкость
бункера, т -
12
Ширина
рабочего органа, м:
-
базовая
- 2,2
-
минимальная
- 2,2
-
максимальная
- 4,5
Габаритные
размеры, мм:
-
длина
- 7220
- ширина
в
рабочем положении
- 3210
в
транспортном положении (без щек)
- 2500
- высота
с
поднятыми тентами
- 3950
с
опущенным тентом
- 3100
Масса,
т -
16
Автоматический контроль профиля - система автоматического
управления САУ "РЕЛЬЕФ-01М" поставляется по заказу
Изготовитель:
ОАО "Брянский Арсенал",
241000, Россия,
г. Брянск, ул. Калинина, 98
(0832) 74-21-66
факс (0832) 72-12-78.