Введено в
действие
Распоряжением
Минтранса России
от 23 мая 2003 г. N
ОС-459-р
ОТРАСЛЕВОЙ ДОРОЖНЫЙ МЕТОДИЧЕСКИЙ ДОКУМЕНТ
МЕТОДИЧЕСКИЕ РЕКОМЕНДАЦИИ
ПО УСТРОЙСТВУ ОСНОВАНИЙ ДОРОЖНЫХ ОДЕЖД ИЗ
"ТОЩЕГО" БЕТОНА
1. Разработан Государственным унитарным институтом Росдорнии.
Внесен Управлением
инноваций и технического нормирования в дорожном хозяйстве Государственной службы дорожного хозяйства Министерства транспорта Российской
Федерации.
2. Принят и введен в действие Распоряжением Государственной
службы дорожного хозяйства Министерства транспорта Российской Федерации от
23.05.2003 N ОС-459-р.
ПРЕДИСЛОВИЕ
Методические
рекомендации составлены на основании исследований, проведенных ГП
"Росдорнии" в 1975 - 2002 гг.
При разработке
Методических рекомендаций учтен и обобщен опыт работы в этом направлении
Союздорнии, НИИМосстроя и накопленный производственный опыт Центродорстроя,
Вологодавтодора, Управления дорог Тюменской области, Магаданавтодора,
Алтайавтодора, ПРСО "Росавтомагистраль", Дирекции автомобильной
дороги Воронеж - Ростов, при строительстве МКАД.
В Методических
рекомендациях учтен зарубежный опыт проектирования и строительства дорожных
одежд из "тощего" бетона.
Рекомендации
содержат требования к бетону для оснований из смесей повышенной жесткости,
материалам для его приготовления, методы проектирования составов бетона,
основные положения по конструированию дорожных одежд со слоями из бетона,
технологии строительства оснований из смесей повышенной жесткости, а также
методы лабораторного и полевого контроля качества.
Приведена методика
расчета дорожной одежды с учетом межремонтных сроков службы, дающая возможность
варьировать и оптимизировать толщины конструктивных слоев и обеспечивающая
проектирование экономичных конструкций.
С учетом
накопленного опыта предложено нарезать швы в цементобетонном основании и
асфальтобетонном покрытии через 15 м, что обеспечивает защиту покрытия от
дальнейшего растрескивания и разрушения трещин и позволяет снизить затраты на
содержание швов.
Методические
рекомендации разработаны канд. техн. наук Л.Б. Каменецким и инж. О.Н.
Нагаевской.
Авторы выражают
благодарность специалистам Союздорнии и Центродорстроя, Федерального управления
автомобильных дорог "Северный Кавказ" и других организаций за
замечания, высказанные при рецензировании.
1. ОБЩИЕ
ПОЛОЖЕНИЯ
1.1. Рекомендации
предназначены для конструирования, расчета и строительства оснований из
"тощих" бетонов под капитальные типы покрытия.
1.2. Такие
конструкции дорожных одежд по сравнению с основаниями из несвязанных материалов
обладают повышенной долговечностью и обеспечены защитой от образования сетки
трещин, просадок и колейности.
1.3. Под
"тощим" бетоном понимается тяжелый бетон классов В5; В7,5; В10; В12,5; В15, получаемый из жестких смесей,
уплотняемых укаткой.
1.4. Экономичность
дорожных одежд с покрытиями и основаниями из жестких укатываемых смесей
обеспечивается за счет простоты технологии производства работ, применения
местных каменных материалов и вторичных промышленных ресурсов, экономии
цемента, а также за счет возможности устройства вышележащих конструктивных
слоев дорожной одежды без технологического перерыва, обязательного при
строительстве оснований из пластичного бетона.
1.5. Преимуществом
"тощего" бетона по сравнению с грунтами и каменными материалами,
укрепленными цементом, являются более высокая однородность и прочность таких
бетонов при более низком или одинаковом расходе цемента.
1.6. Толщины
конструктивных слоев дорожных одежд с основаниями из "тощего" бетона
рассчитывают по методике, изложенной в настоящих Рекомендациях.
2.
ТРЕБОВАНИЯ К "ТОЩЕМУ" БЕТОНУ И БЕТОННОЙ СМЕСИ
2.1. Для устройства оснований применяют жесткие бетонные смеси,
характеризующиеся удобоукладываемостью 40 - 90 с, определяемой по прибору типа
Вебе или другими методами, указанными в ГОСТ 10181-2000 с применением
переходных коэффициентов. Выбор жесткости смеси определяется имеющимся
распределяющим и уплотняющим оборудованием.
2.2.
"Тощий" бетон по прочности должен иметь показатели прочности,
соответствующие следующим классам (или маркам):
- по прочности при
сжатии: В5 (М75); В7,5 (М100); В10 и В12,5 (М150); В15
(М200);
- по прочности на
растяжение при изгибе:
;
;
;
.
Класс бетона В15
(М200) применяется для двухстадийного строительства.
Марку бетона по
морозостойкости следует принимать по табл. 1.
Таблица 1
Проектный
класс бетона
|
Минимальные проектные марки бетона по
морозостойкости
для районов со среднемесячной
температурой воздуха
наиболее холодного
месяца, °C
|
от 0 до -15 °C
|
ниже -15 °C
|
В5
|
50
|
50
|
В7,5
|
50
|
50/75 <*>
|
В10
|
50/75 <*>
|
50/75 <*>
|
В12,5
|
50/75 <*>
|
50/100 <*>
|
В15
|
100
|
100
|
--------------------------------
<*>
Минимальные марки бетона по морозостойкости при проектировании конструкций
дорожных одежд со сроком службы более 20 лет.
2.3. Требования к
бетону по прочности и морозостойкости должны быть обеспечены в возрасте 28 сут
или 90 сут.
Назначение марки
бетона в возрасте 90 сут допускается при применении смешанных
вяжущих (цемент + активная минеральная добавка) с целью экономии цемента, при
этом в возрасте 28 сут должна быть обеспечена прочность на сжатие не ниже 50%
марочной. При этом требуется технико-экономическое обоснование конструктивных
решений.
3.
ТРЕБОВАНИЯ К МАТЕРИАЛАМ ДЛЯ "ТОЩЕГО" БЕТОНА
3.1. В зависимости
от наибольшей крупности зерен заполнителей "тощие" бетоны делятся на:
- мелкозернистые -
до 5 мм;
- крупнозернистые -
до 40 мм.
Наибольший размер
зерен ограничен 40 мм из условия обеспечения устойчивости гранулометрического
состава щебня в бетонной смеси при уплотнении укаткой.
3.2. Материалы,
применяемые в "тощих" бетонах, должны соответствовать требованиям
ГОСТ 8267-93, ГОСТ 8736-85, ГОСТ 7473-94, ГОСТ 25192-82, ГОСТ 26633-91, ГОСТ
24640-91, ГОСТ 23732-79.
3.3. Щебень должен
подразделяться на фракции 5 (3) - 10; 10 - 20; 20 - 40 мм. Соотношение между
ними устанавливается экспериментально по наибольшей плотности смеси. Допускается
применение щебня непрерывной гранулометрии фракций 5 -
20 (25) при содержании частиц мельче 10 мм не менее 35 - 40%.
3.4. Суммарное
содержание пылевидных и глинистых частиц в песке и щебне допускается до 10% при
условии, что бетоны, приготовленные на этих заполнителях, по прочности и
морозостойкости удовлетворяют требованиям п. 2.2.
3.5. В качестве
вяжущих для приготовления "тощего" бетона применяют портландцементы и
шлакопортландцементы М300 и выше, удовлетворяющие требованиям ГОСТ 10178-85. С
целью экономии цемента допускается применение активных минеральных добавок по
ГОСТ 24211-91.
3.6. Для снижения
расхода цемента и регулирования сроков схватывания и твердения в жесткие
бетонные смеси рекомендуется вводить химические добавки пластифицирующего действия
(приложение 4 ГОСТ 26633-91).
Добавки и их
количество выбирают в зависимости от технологии производства работ и проектных
характеристик бетона.
Дозировку добавок
уточняют при экспериментальной проверке состава бетона.
В жестких
бетонных смесях эффективность действия добавок наблюдается при более высоких,
чем традиционные, расходах.
Повышенные
дозировки добавки применяют в качестве замедлителя схватывания при температуре
воздуха выше 25 °C.
3.7. Вода для
затворения бетонной смеси и приготовления растворов химических добавок должна
соответствовать требованиям ГОСТ 23732-79.
4.
ПРОЕКТИРОВАНИЕ СОСТАВА "ТОЩЕГО" БЕТОНА
4.1. При
проектировании состава "тощего" бетона необходимо руководствоваться
общими положениями проектирования цементобетонных смесей с учетом особенностей
технологии строительства. При этом должны быть заданы:
- средний уровень
прочности получаемого бетона, принимаемый в соответствии с ГОСТ 18105-86, п.
2.2 и ГОСТ 27006-86, с учетом фактической однородности бетона и планируемых
мероприятий по ее повышению;
- требуемая марка
по морозостойкости;
- требуемая
жесткость бетонной смеси для принятой технологии укладки и уплотнения.
Жесткость смеси назначается при выходе из смесителя и на месте укладки с учетом
времени транспортировки;
- вид и крупность
заполнителей;
- вид и марка
цемента.
4.2. Компоненты
бетонной смеси должны быть испытаны по стандартным методикам для определения
показателей их качества и соответствия их требованиям ГОСТ 26633-91.
4.3. Проектирование состава "тощего" бетона производят в
специализированных аттестованных в установленном порядке на этот вид
деятельности лабораториях или в научно-исследовательских институтах любыми
методами, обеспечивающими при минимальном содержании цемента заданные свойства
бетонной смеси, в том числе расчетно-экспериментальным методом абсолютных
объемов, а также по методу максимальной плотности. Правильность
проектирования должна быть подтверждена результатами испытания контрольных
образцов.
4.4. Водоцементное
отношение в "тощих" бетонах должно определяться расчетным путем в
зависимости от требуемой прочности бетона и активности цемента. Ориентировочный
расход воды для жестких бетонных смесей на 1 м3 следует назначать, кг (л):
120 - 145 - для
щебеночных заполнителей с водопоглощением от 0,1 до 2%;
145 - 165 - для
щебеночных заполнителей с водопоглощением от 2 до 8%.
При использовании в
качестве крупного заполнителя гравия расход воды уменьшается на 5 - 10 л.
4.5. Коэффициент
раздвижки зерен крупного заполнителя раствором при проектировании состава
следует назначать в пределах 1,3 - 1,5 для бетона класса В15 и до 1,8 для
бетонов класса менее В15.
4.6. Расходы
цемента определяются расчетом с учетом п. 1.4.7 ГОСТ 26633-91.
4.7. Расчетный
состав бетона должен быть экспериментально проверен по следующим критериям:
- жесткости смеси;
- расходу вяжущего;
- прочности и
морозостойкости образцов из бетона заданной жесткости.
5.
КОНСТРУИРОВАНИЕ ДОРОЖНОЙ ОДЕЖДЫ
С ОСНОВАНИЕМ ИЗ
"ТОЩЕГО" БЕТОНА
5.1. Дорожную
одежду с асфальтобетонными покрытиями на основании из "тощего" бетона
следует проектировать преимущественно на дорогах I - III категории с тяжелым и
интенсивным движением. При соответствующем технико-экономическом обосновании
допускается устройство ее на дорогах IV категории.
5.2. К конструкциям
дорожной одежды с основанием из "тощего" бетона предъявляются
следующие требования:
- обеспечение
требуемой прочности и долговечности под действием движения транспортных средств
и влияния природно-климатических факторов;
- обеспечение
ровности и получение высоких транспортно-эксплуатационных показателей дорожных
одежд;
- возможность
комплексной механизации работ;
- экономичность
конструкции и технологических решений.
5.3. Толщину
конструктивных слоев рассчитывают с учетом состава и интенсивности движения,
модуля упругости земляного полотна и климатических условий района
строительства.
Прочностные и
деформативные характеристики бетона принимают в соответствии с ВСН 197-91.
5.4. Толщины слоев
основания из "тощего" бетона и асфальтобетонного покрытия
рассчитывают в соответствии с ВСН 197-91 или Приложением 1 настоящих
Рекомендаций. Отличительной особенностью расчета по Приложению 1 является учет
межремонтных сроков службы отдельных слоев и дорожной одежды в целом.
5.5. Проектирование
дорожной одежды представляет собой единый процесс конструирования и расчета
дорожной конструкции на прочность, морозоустойчивость, а также назначение мер
по повышению трещиностойкости слоев с учетом возможности использования местных
материалов.
5.6. Расчетный срок
службы дорожной одежды в целом устанавливается не менее 25 лет.
Сроки службы
верхнего слоя покрытия устанавливаются в соответствии с межремонтными сроками в
зависимости от региона строительства и интенсивности движения по ВСН 41-88.
5.7. Толщину
основания из "тощего" бетона принимают не менее 15 см. В случае,
когда основание в течение длительного времени (но не более 1-го года с момента
укладки) используется для движения транспорта, его устраивают из бетона класса
В15 толщиной не менее 20 см.
5.8. Толщину
асфальтобетонных слоев определяют расчетом в зависимости от категории дороги и
толщины основания. При этом, исходя из условия обеспечения сдвигоустойчивости и
возможности устройства двухслойного покрытия, суммарная толщина слоев покрытия
должна быть не менее 8,0 см.
5.9. С учетом
мирового и отечественного опыта избежать появления трещин в таких конструкциях
практически невозможно.
Возникновение
трещин на покрытии связано с природой материалов основания и сегодня не
существует эффективных методов предотвращения появления отраженных трещин, о
чем свидетельствует мировой и отечественный опыт.
Речь может идти
только о регулируемом трещинообразовании. С этой целью в основании для
предотвращения хаотического образования трещин рекомендуется нарезать швы.
Расчетным путем на
стадии проектирования определить максимальное расстояние между швами из-за
влияния различных факторов не представляется возможным.
5.10. В
основании из "тощего" бетона классов В10; В12,5; В15 рекомендуется
устраивать швы сжатия через 12 - 15 м. Расстояние между швами может быть
уточнено в зависимости от толщин слоев, качества асфальтобетона и климатических
условий района строительства по согласованию с организацией-разработчиком. Швы
нарезают в затвердевшем бетоне на глубину 1/4 толщины слоя одним диском
минимальной толщины. Заполнение швов мастикой не производится. Армирование швов
сжатия не требуется, так как нагрузка с плиты на плиту передается за счет
зацепления смежных стенок шва.
Для повышения
эффективности такого решения в асфальтобетонном покрытии послойно нарезают швы
над швами в основании. Швы в верхнем слое асфальтобетонного покрытия заполняют
специальными герметизирующими материалами - мастиками битумно-полимерными типа
"Biguma" или "Новомаст".
5.11. С учетом конкретных
условий строительства и принятой конструкции дорожной одежды допускается, по
согласованию с Заказчиком и проектной организацией, не устраивать швы сжатия.
5.12. Если швы в
основании не устраивают, то между слоями основания из "тощего" бетона
и асфальтобетонным покрытием при соответствующем технико-экономическом
обосновании рекомендуется устраивать трещинопрерывающие прослойки из зернистых
материалов, обработанных битумом, или рулонных материалов. Такие решения должны
быть технологичными и доказавшими свою эффективность в отечественной практике
строительства. С учетом последнего допускается также армирование слоев покрытия
сетками из различных материалов.
Зернистые прослойки
и рулонные материалы следует укладывать по предварительно подгрунтованному слою.
5.13. Швы
расширения в основаниях из цементобетона не устраивают.
В конце рабочей
смены и при перерывах в бетонировании более двух часов устраивают рабочий шов.
Швы рабочие устраивают с установкой штыревых соединений для
улучшения передачи нагрузки с плиты на плиту в соответствии с ВСН
139-80.
5.14. На дорогах I
и II категории перед мостами и путепроводами рекомендуется устраивать
компенсационные швы, предназначенные для обеспечения в течение длительного
срока эксплуатации устойчивости и проектного положения искусственных
сооружений, нарушение которых возможно в жаркий период года за счет достаточно
высоких напряжений сжатия, возникающих в цементобетонном основании.
5.15. Продольный
шов в основании из "тощего" бетона шириной менее 11,50 м не
устраивают.
5.16. При
устройстве основания из "тощего" бетона с последующей укаткой для
повышения качества уплотнения краевых участков и улучшения работы всей
конструкции под нагрузкой ширину основания следует увеличивать на 0,25 м с
каждой стороны.
6.
ТЕХНОЛОГИЯ ПРОИЗВОДСТВА РАБОТ
ПРИ УСТРОЙСТВЕ
ОСНОВАНИЙ ИЗ "ТОЩЕГО" БЕТОНА
6.1. Приготовление
и транспортирование бетонной смеси
6.1.1. Смеси
"тощего" бетона рекомендуется приготавливать в смесителях
принудительного перемешивания как непрерывного, так и циклического действия и в
другом оборудовании, обеспечивающем требуемое качество перемешивания.
При
неудовлетворительном качестве перемешивания следует уменьшать скорость подачи
компонентов смеси.
Для обеспечения
однородности выпускаемой смеси и предотвращения ее расслоения
бетоносмесительные установки рекомендуется оборудовать бункерами-накопителями.
6.1.2. В процессе
приготовления бетонной смеси дозировка материалов при автоматическом режиме
взвешивания должна производиться по массе в соответствии с ГОСТ 7473-94.
6.1.3. Химические
добавки в бетонную смесь вводят с водой затворения.
6.1.4.
Транспортирование "тощего" бетона осуществляется в соответствии с
ГОСТ 7473-94.
При
транспортировании смесь должна быть защищена от влагопотери или переувлажнения.
Доставка должна
осуществляться по часовому графику, разработанному с учетом производительности
укладочных машин.
6.1.5. В случае
ведения бетонных работ при температуре наружного воздуха более 25 °C во
избежание ускоренного схватывания и увеличения жесткости бетонной смеси
обязательно введение добавки ЛСТ в количестве до 1% от массы цемента или других
замедлителей схватывания.
Время
транспортирования смеси "тощего" бетона без добавок-замедлителей при
температуре до 20 °C не должно превышать 1 ч, с добавками - 1,5 ч, при
температуре более 20 °C - соответственно 30 и 45 мин.
6.2. Устройство
основания из бетонной смеси
6.2.1. Устройство
основания из "тощего" бетона производится по технологическому
регламенту, разработанному и утвержденному в установленном порядке.
6.2.2. Работы по
устройству оснований из жестких бетонных смесей следует производить при
температуре воздуха более 5 °C.
6.2.3. Жесткую
бетонную смесь укладывают на хорошо уплотненный, спланированный и тщательно
очищенный нижележащий слой.
6.2.4. Для предотвращения
потерь влаги бетонной смесью и обеспечения качественного уплотнения перед
укладкой жесткой бетонной смеси подстилающий слой основания увлажняют из
расчета:
- 0,5 л/м2 - при температуре воздуха до 25 °C;
- 1,0 л/м2 - при температуре воздуха 25 °C и выше.
6.2.5. Жесткую
бетонную смесь по подстилающему слою следует распределять машинами, оснащенными
автоматической системой выдерживания ровности:
- профилировщиком
или бетоноукладчиком из комплекта машин типа ДС-110;
- бетоноукладчиком
ДС-169;
- универсальным
асфальтоукладчиком ДО-199 (Николаевского завода "Дормашина"),
"Титан" фирмы "АБГ-Ингерсолл Рэнд" (ФРГ-США),
фирмы "Блау Нокс" (Англия) и т.п.
Универсальные
асфальтоукладчики позволяют обеспечить наиболее высокий уровень качества
укладки.
Допускается
распределять жесткую бетонную смесь автогрейдерами или щебнеукладчиками с
тщательным нивелировочным контролем.
В этих случаях
укладку смеси можно производить с предварительной установкой рельс-форм,
упорных брусьев и без них. В последнем случае для обеспечения качественного
уплотнения распределение смеси производят на ширину, превышающую проектную на
0,25 м с каждого свободного края.
Смесь в основание
можно укладывать полосами шириной не более 11,50 м.
6.2.6.
Укладку смеси следует вести отдельными захватками длиной 30 - 40 м, чтобы
обеспечить задел для распределяющих и уплотняющих механизмов. Распределенная и
спрофилированная бетонная смесь должна немедленно уплотняться. Толщина
распределенного слоя должна быть на 15 - 20% больше толщины в уплотненном
состоянии и уточняться по ходу работы.
Дефекты поверхности
основания (впадины, разрывы) при укладке смеси должны быть устранены после
первого прохода уплотняющих средств.
Интервал от выпуска
жесткой бетонной смеси до окончательного уплотнения не должен превышать трех
часов, а в случае применения замедлителей схватывания - четырех часов в
зависимости от их свойств.
6.2.7. Механизмы
для уплотнения бетонной смеси следует выбирать из условия возможности
уплотнения смеси преимущественно в один слой.
Уплотнение
цементобетонной смеси осуществляется звеном катков.
Состав звена катков
и режим их работы определяется пробной укаткой из условия обеспечения скорости
движения потока, требуемой плотности и с учетом ограничений по времени,
изложенных в п. 6.2.6 настоящих Рекомендаций, количество, тип и режим работы
катков определяется по результатам пробного уплотнения.
В зависимости от
типа применяемых уплотняющих механизмов разрабатывается технологическая схема
уплотнения.
Укатка должна
производиться от обочин к оси дороги (рис. 1). Вальцы катков в течение всего
времени уплотнения смеси должны быть чистыми. Остановка катков во время укатки
на свежеуложенной смеси не допускается.
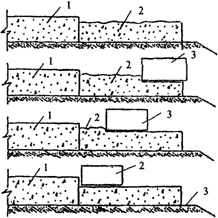
Рис. 1.
Технологическая схема устройства основания
при распределении
бетонной смеси на всю его ширину:
1 - старое
покрытие; 2 - распределенная на всю ширину
бетонная смесь
основания; 3 - валец катка; 4 - обочина
При такой схеме
уплотнения между двумя смежными полосами образуется так называемый "свежий"
шов (уплотнение смежной полосы произведено не более чем через 90 мин).
Если смежная полоса
будет уложена позднее, чем через 90 мин, то образуется так называемый
продольный "холодный" шов (бетон затвердел) (рис. 3, этап I). Перед
распределением смеси на смежной полосе вертикальная поверхность края
затвердевшего бетона тщательно очищается и смачивается водой (этап II).
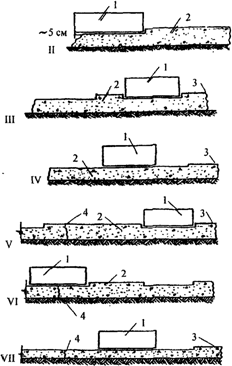
Рис. 2. Схема
уплотнения свежеуложенных первой
и примыкающих полос
покрытия из укатанного бетона
(поперечный
разрез):
1 - валец катка; 2
- покрытие из свежеуложенного бетона;
3 - неуплотненный
продольный край 30 - 45 см;
4 - продольный
"свежий" шов; II - VII - этапы уплотнения
свежеуложенного
бетона
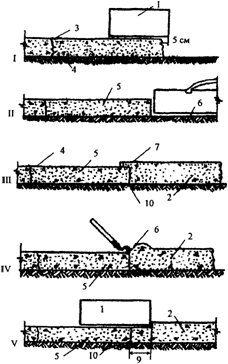
Рис. 3.
Схема уплотнения примыкающей к затвердевшему бетону
продольной полосы
покрытия с устройством
"холодного"
продольного шва:
1 - валец катка; 2
- покрытие из свежеуложенного бетона;
3 - продольный
свежий шов; 4 - уплотненный бетон;
5 - затвердевший
бетон; 6 - нож грейдера; 7 - перекрытый
(на ~ 7 см)
"холодный" шов свежим бетоном; 8 - перемещение
свежеуложенного
бетона за пределы "холодного" шва;
9 - уплотнение
свежеуложенного бетона над "холодным" швом;
10 -
"холодный" шов; I - V - этапы образования "холодного"
шва; II - VII -
этапы уплотнения свежеуложенного бетона
При распределении
бетонной смеси на второй полосе в примыкающей зоне свежий бетон перекрывает
уложенную полосу затвердевшего бетона на ширину 7,5 - 8 см (этап III). На этой
полосе (7,5 - 8 см) смесь вручную перемещают в сторону свежеуложенного бетона,
образуя валик (этап IV), и затем катком (с выключенным вибратором) уплотняют
шов, захватывая полосу свежеуложенного бетона шириной 30 см (не менее двух
проходов (этап V)).
До достижения
требуемой плотности уплотнение повторяют по приведенной схеме. В течение
процесса уплотнения каток с включенными вибраторами останавливать нельзя.
Вибраторы выключают за 1 - 1,5 м до остановки катка. В противном случае
образуются просадки на покрытии. Машинист должен регулировать скорость движения
катка (3 - 3,2 км/ч), амплитуду и частоту колебаний вальца.
После двух проходов
катками на пневмошинах рекомендуется сразу же производить уплотнение
виброкатком, следом за которым можно использовать легкий двухвальцовый каток.
6.2.8. Вибраторы
необходимо включать и выключать за пределами уплотняемой полосы при движении
катка.
6.2.9. В
исключительных случаях при необходимости остановки катка на уплотняемом слое
следует предварительно выключить вибрацию за 1,5 - 2 м до полной остановки
катка.
6.2.10. Очищать и
увлажнять вальцы катка следует за пределами уплотняемого слоя.
6.2.11. Во время
уплотнения цементобетонной смеси катки должны быть в непрерывном и равномерном
движении. Запрещается останавливать катки на неуплотненном слое или резко
менять направление движения.
6.2.12. Переезд
катка с одной уплотняемой полосы на другую необходимо осуществлять только по
ранее уплотненному участку.
6.2.13. Бетонную
смесь уплотняют до плотности, характеризующейся коэффициентом уплотнения К = 0,98 от полученной при подборе бетона. Ориентировочным
признаком окончания уплотнения является отсутствие следа на поверхности слоя
при проходе тяжелого катка. Окончательное заключение о достигнутой степени
уплотнения следует давать по результатам лабораторного контроля.
6.2.14. Швы сжатия
нарезают в затвердевшем бетоне одним диском в соответствии с проектом, ВСН
139-80 и требованиями п. 5.10 настоящих Рекомендаций.
6.2.15. Рабочие швы
в конце смены следует устраивать с помощью металлических упорных конструкций на
всю ширину и высоту укладываемого слоя. Допускается устраивать рабочий шов с
применением деревянных упорных досок. Конструкции или упорные доски следует
закреплять штырями. Вдоль рабочего шва смесь необходимо дополнительно уплотнять
трамбовками с отделкой поверхности вручную, подсыпая смесь на полосе шириной до
0,50 м. В начале следующей смены доску следует убрать и смесь уложить в стык к ранее уложенной.
Как правило,
рабочие швы должны совпадать с предусмотренными проектом швами сжатия.
Допускается в конце
смены производить раскатку бетона с образованием пандуса с последующей обрезкой
бетона нарезчиком швов и образованием рабочего шва на всю проектную толщину и
ширину сечения.
6.2.16. Уход за
бетоном из жесткой бетонной смеси следует осуществлять в соответствии с
требованиями СНиП 3.06.03-85 п. 12.25; п. 12.26 и ВСН 139-80.
Уход за
свежеуложенным бетоном должен осуществляться сразу после окончания уплотнения и
продолжаться до набора проектной прочности или до устройства слоев покрытия.
6.2.17. Наиболее
эффективно перекрытие основания слоями асфальтобетона сразу после уплотнения и
отделки поверхности с перерывом между укладкой слоев не более 4 ч, не допуская
высыхания бетона. В этом случае уход за бетоном не производится.
Если по условиям
производства работ перекрытие бетона основания сразу после его укладки
невозможно, то устройство вышележащих слоев покрытия разрешается производить
при достижении бетоном основания прочности не менее 70% от
проектной.
6.2.18. Движение
построечного транспорта и регулярного транспорта по покрытию, устроенному без
технологического перерыва, разрешается после набора цементобетоном 70% марочной
прочности.
7. КОНТРОЛЬ
КАЧЕСТВА
7.1. Контроль
качества жесткой бетонной смеси, бетона, а также качества строительства
оснований должен производиться в соответствии с общими требованиями ВСН 139-80
и настоящих Рекомендаций.
7.2. При
приготовлении и укладке бетона лаборатория обязана вести техническую
отчетность, а также текущий контроль за:
- качеством
материалов (наибольшая крупность заполнителя, влажность);
- правильностью
хранения материалов;
- качеством
приготовления бетонной смеси;
- соответствием
прочности бетона заданному классу;
-
транспортированием, распределением и уплотнением бетонной смеси;
- качеством ухода;
- условиями
твердения.
7.3. Учитывая
технологические особенности строительства конструктивных слоев дорожных одежд
из "тощего" бетона, лаборатория дополнительно должна проверять:
- степень
уплотнения уложенного слоя бетона на полную толщину методом лунки или прибором
КП-120 (Приложение 2) из расчета трех замеров на 10000 м2
основания с соответствующими записями в журнале контроля производства работ;
- влажность и
жесткость бетонной смеси на месте производства работ (Приложение 3);
- ровность
уложенного слоя в продольном и поперечном направлении;
- определять сроки
нарезки швов;
- качество нарезки
швов.
7.4. Качество
производства работ оценивают:
- по данным
лабораторного контроля на заводе и месте работ (результаты испытания исходных
материалов и контрольных образцов, состав бетона, журналы производства работ);
- на основании
визуального и инструментального обследований покрытия;
- испытанием
бетонных образцов-кернов, взятых из покрытия и основания.
На отобранные керны
составляют акты с указанием времени и места их взятия. Керны испытывают в
соответствии с методикой, изложенной в приложении 3 ВСН 139-80.
8.
ТРЕБОВАНИЯ БЕЗОПАСНОСТИ
8.1. К работам по
строительству автомобильных дорог с цементобетонным покрытием и основанием из
жестких бетонных смесей допускаются лица, достигшие 18 лет, признанные
медицинской комиссией годными к данной работе и прошедшие инструктаж в
соответствии с ГОСТ 12.0.004-79.
8.2. Для работы на
дорожно-строительных машинах и механизмах следует иметь соответствующее удостоверение,
на тягаче с прицепным дорожным механизмом - специальное обучение и практическую
подготовку.
8.3. Все работающие
должны пользоваться средствами индивидуальной защиты.
8.4. При
приготовлении смеси необходимо соблюдать Правила техники безопасности при
строительстве, ремонте и содержании автомобильных дорог (М., Транспорт, 1979).
8.5. Подъезд под
загрузочный бункер смесительной установки и выезд из-под него автосамосвалов должен
происходить только после сигнала машиниста (оператора) установки. Место
подъезда должно постоянно очищаться от просыпавшегося материала.
8.6. Застрявшую в
кузове смесь выгружают стоя на земле инструментом (скребком, лопатой) с
рукояткой длиной не менее 3 м.
8.7. При
распределении бетонной смеси автогрейдером скорость его должна быть
минимальной, расстояние между бровкой насыпи и внешними (по ходу) колесами - не
менее 1 м (расстояние может корректироваться в зависимости от конкретных
условий работ).
8.8. При работе
катков на пневматических шинах необходимо соблюдать требования указанных выше
Правил техники безопасности (пп. 4.104 - 4.110).
8.9. При нарезке
швов в затвердевшем бетоне необходимо соблюдать следующие требования:
- пользоваться
защитными очками и исправным защитным кожухом режущих дисков;
- не регулировать и
не перемещать машину во время нарезки (при вращающихся дисках), а также не
работать при незафиксированном положении диска.
8.10. При работе с
химическими добавками (ЛСТ, 135-41, СНВ, 119-215) следует соблюдать меры
предосторожности. При попадании добавок на кожу вымыть ее чистой водой с мылом,
при попадании в глаза - промыть чистой водой.
8.11. При уходе за
свежеуложенным бетоном с применением пленкообразующих материалов соблюдают те
же Правила техники безопасности пп. 5.70 - 5.78 и 11.27 - 11.33, а при хранении
- пп. 11.1 - 11.19.
Приложение
1
РАСЧЕТ
ДОРОЖНОЙ ОДЕЖДЫ НА ПРОЧНОСТЬ
1. Основные
положения и предпосылки расчета
При экономически
целесообразных толщинах битумосодержащих слоев появление трещин в
асфальтобетонных покрытиях на основаниях из цементобетона не исключено. Это
подтверждается обследованием эксплуатируемых покрытий, построенных на
основаниях из цементобетона различных марок (от М75 до М200). Основной размер
образовавшихся плит после 2 - 3 лет эксплуатации при отсутствии швов составляет
от 15 м до 20 м. Трещины имеют ярко выраженный температурный характер, и их
появление не отражается на несущей способности дорожной одежды.
Процесс
трещинообразования может регулироваться путем устройства поперечных швов в
основании из цементобетона.
В связи с этим
расчет толщины битумосодержащих слоев из условия обеспечения трещиностойкости
цементобетона от воздействия климатических факторов для предупреждения
появления трещин на поверхности покрытия экономически нецелесообразен.
Основным
критерием расчета является обеспечение трещиностойкости плит основания при
принятой надежности, увязанной с межремонтными сроками службы покрытия и
заданным сроком службы дорожной одежды до капитального ремонта под воздействием
повторных нагрузок, обусловленных составом и интенсивностью движения
автомобилей, и переменными суточными и сезонными температурами воздуха с учетом
солнечной радиации.
Основным несущим
слоем является плита цементобетонного основания. При этом под плитой
подразумевается участок покрытия, ограниченный двумя поперечными швами или
трещинами, расположенными на расстоянии более 5 м друг от друга, что позволяет
вести расчет бесконечной или полубесконечной плиты на упругом полупространстве
методом расчета жестких дорожных одежд.
Толщину
битумосодержащих слоев в соответствии с их деформативностью по известным зависимостям приводят к
эквивалентной толщине цементобетона. При этом предполагается полное сцепление
всех слоев дорожной одежды, достигаемое технологическими мероприятиями.
В цементобетонном
основании в зависимости от толщины конструктивных слоев и климатических условий
возникают температурные напряжения той или иной величины, учет которых обязателен
при расчете.
По установившейся
практике расчет дорожной одежды ведется на перспективную интенсивность движения
на последний год службы и толщины конструктивных слоев устанавливают, исходя из
суммарного количества расчетных нагрузок за принятый срок службы. Однако, в
зависимости от показателя прироста, интенсивность движения в первые годы службы
изменяется достаточно медленно. Поэтому дорожные одежды, запроектированные
таким образом и без учета межремонтных сроков службы, в первые годы обладают большим
запасом прочности.
Учет интенсивности
движения при расчете толщин конструктивных слоев следует проводить по периодам,
увязанным со сроками проведения ремонтов и, как правило, не превышающими 2 - 8
лет.
Учет межремонтных
сроков службы и роста интенсивности движения позволяет резко снизить
первоначальные строительные затраты и рационально распределить оставшиеся на
весь срок службы дорожной одежды. Это достигается постепенным наращиванием
битумосодержащих слоев по периодам, увязанным со сроками ремонта, что позволяет
добиться, чтобы конструкция на каждом интервале времени работала с надежностью,
соответствующей интенсивности расчетной нагрузки.
Расчет выполняют по
предельным состояниям, определяющим потерю работоспособности на основании
принятой расчетной схемы, используя нормируемые расчетные параметры.
Дорожные одежды
рассчитывают с учетом надежности (вероятности безотказной работы конструкции в
течение намеченного срока эксплуатации), принимаемым по табл. 1.
Таблица 1
┌─────────────────────────┬───────────────────┬───────────────────────────┐
│
Интенсивность расчетной │
Уровень │Коэффициент
прочности, К
│
│ нагрузки, ед./сут │
надежности │ пр
│
├─────────────────────────┼───────────────────┼───────────────────────────┤
│ Более 1000 │ 0,95 │ 1,00 │
├─────────────────────────┼───────────────────┼───────────────────────────┤
│ 500 - 1000 │ 0,90 │ 0,94 │
├─────────────────────────┼───────────────────┼───────────────────────────┤
│ Менее 500 │ 0,80 │ 0,87 │
└─────────────────────────┴───────────────────┴───────────────────────────┘
Расчет ведется
путем проверок предварительно назначенной конструкции дорожной одежды.
2. Исходные данные
для расчета дорожной одежды:
- категория дороги,
число полос движения;
- исходная
интенсивность движения, расчетные нагрузки;
- срок службы
дорожной одежды до капитального ремонта;
-
дорожно-климатическая зона;
- расчетные
характеристики материалов.
РАСЧЕТНЫЕ НАГРУЗКИ
И ИНТЕНСИВНОСТЬ ДВИЖЕНИЯ
Дорожная одежда
рассчитывается с учетом состава и интенсивности движения, ожидаемых
на год службы до капитального ремонта.
Расчетный срок
службы при определении конструкции дорожной одежды устанавливают не менее 25
лет.
Расчетную нагрузку
на колесо
определяют по формуле (1):
, (1)
где
- нормативная нагрузка,
;
- коэффициент динамичности, принимаемый 1,3.
Интенсивность
движения выражают количеством автомобилей, проходящих по одной наиболее
загруженной полосе. Коэффициент, учитывающий число полос движения, приведен в
табл. 2.
Таблица 2
Число полос движения
|
Значение коэффициента полосы для полосы
N
|
1
|
2
|
3
|
1
|
1,00
|
-
|
-
|
2
|
0,55
|
-
|
-
|
3
|
0,50
|
0,50
|
-
|
4
|
0,35
|
0,20
|
-
|
6
|
0,30
|
0,20
|
0,05
|
, (2)
где
- интенсивность движения по наиболее
загруженной полосе, авт./сут;
- интенсивность движения на последний год
службы, авт./сут;
- коэффициент, учитывающий число полос
движения (см. табл. 2).
Расчет
интенсивности движения на первый год службы ведется с учетом показателя
ежегодного роста интенсивности движения (q > 1).
, (3)
где
- расчетная интенсивность движения на первый
год службы, авт./сут;
- интенсивность движения по наиболее
загруженной полосе, авт./сут;
q - показатель
ежегодного роста интенсивности движения, q > 1;
T - срок службы
дорожной одежды, годы.
Нормативный состав
движения автомобилей каждой марки выражается в процентах от общего числа,
принимаемого за 100%, и определяется по формуле 4:
. (4)
Коэффициент
использования грузоподъемности автомобилей
.
Расчетную
интенсивность движения определяют, приводя автомобили с различными нагрузками
на колесо к расчетному автомобилю с расчетной нагрузкой на колесо путем
умножения на соответствующие коэффициенты приведения в соответствии с
приложением 1 ОДН 218.046-01
, (5)
где
- суммарное количество проходов расчетных осей
за сутки в первый год службы;
- коэффициент приведения автомобиля с
различными нагрузками на колесо к расчетному автомобилю;
- нормативный состав движения по маркам
автомобилей.
Суммарное
количество расчетных осей
за срок службы T лет определяется по формуле
6:
, (6)
где
- суммарное количество проходов расчетных осей
за срок службы T = t лет;
t -
продолжительность рассматриваемого срока службы, годы;
- количество расчетных суток в году от начала
протаивания до промерзания грунта основания.
Расчетную прочность
бетона на растяжение при изгибе определяют по формуле 7:
, (7)
где
- расчетная прочность бетона на растяжение при
изгибе;
- коэффициент набора прочности для бетона
естественного твердения
;
- коэффициент усталости бетона при повторном нагружении
;
- класс бетона по прочности на растяжение при
изгибе.
РАСЧЕТ ТОЛЩИН
КОНСТРУКТИВНЫХ СЛОЕВ
Предельное
состояние по прочности дорожной одежды в целом будет обеспечено, если
, (8)
где
- напряжения растяжения при изгибе на подошве
цементобетонного основания у края покрытия от расчетной нагрузки;
- напряжения растяжения при изгибе на подошве
цементобетонного основания от невозможности коробления бетонной плиты;
- коэффициент прочности фактический (должен
быть не ниже
,
принятого по табл. 1).
Расчет проводят
подбором толщин битумосодержащих слоев и слоя цементобетонного основания,
удовлетворяющих условию (8).
При гарантированном
во времени сцеплении между слоями асфальтобетона и цементобетона учитывается
совместная работа слоев на изгиб, при которой расчетную или эквивалентную
толщину слоя определяют по формуле
, (9)
где
- толщина слоя цементобетонного основания, см;
- толщина слоя асфальтобетонного покрытия, см;
- расчетный модуль упругости цементобетона,
МПа;
- расчетный модуль упругости асфальтобетона
МПа, определяется по формуле
, (10)
где
,
... -
модули упругости асфальтобетона каждого слоя. Для практических расчетов модуль
асфальтобетонного покрытия может быть принят
.
Определяют
напряжения от нагрузки на подошве цементобетонной плиты по формуле
, (11)
где P - расчетная
нагрузка на колесо, МПа;
r - радиус
отпечатка колеса, см;
- коэффициент условий работы
;
- коэффициент, учитывающий влияние места
приложения нагрузки;
L - упругая
характеристика плиты, которая определяется по формуле
, (12)
где
и
- модуль упругости и
коэффициент Пуассона цементобетона;
и
- модуль упругости и
коэффициент Пуассона материала основания;
- определяется в соответствии с ОДН
218.046-01.
Расчетные модули
грунтов и материалов основания определяют по ОДН 218.046-01.
Напряжения на
подошве бетонной плиты от невозможности коробления определяют по формуле
Тимошенко-Уэстергарда-Бредбери.
, (13)
где
- коэффициент температурного расширения
бетона;
- расчетный температурный перепад между
поверхностью и подошвой цементобетонной плиты, °C. Определяется по формуле
, (14)
где
- перепад температуры в течение суток на
поверхности асфальтобетонного покрытия, °C;
- угловая частота суточных колебаний
температуры, рад/ч;
;
и
- коэффициенты температуропроводности
соответственно асфальтобетона и цементобетона,
;
.
Определяем
суммарное напряжение от нагрузки и температуры
. (15)
Проверяем
выполнение основного условия прочности
. (16)
При
меньше
расчет необходимо повторить, изменив толщины
слоев. Задаваясь различными толщинами цементобетона, можно получить различные
толщины битумосодержащих слоев и путем технико-экономического анализа выбрать
оптимальное решение.
Расчеты толщин
конструктивных слоев проводят по периодам, увязанным с изменением интенсивности
движения и межремонтными сроками службы покрытия.
С этой целью по
формуле 6 определяют периоды времени, когда интенсивность расчетной нагрузки
достигнет значений, указанных в табл. 1.
В течение каждого
периода дорожная одежда работает с принятой надежностью.
Задав толщину слоя
основания и класс прочности бетона путем подбора толщины слоя асфальтобетона,
строят график, показывающий изменение коэффициента прочности дорожной одежды в
процессе эксплуатации.
По оси абсцисс
откладывают срок эксплуатации и соответствующую ему интенсивность расчетной
нагрузки. По оси ординат - коэффициент прочности.
Определение
требуемой толщины асфальтобетонного покрытия по периодам показано на графике
стрелками (диаграмма N 1).
Принимая различные
толщины слоев основания и различные классы бетона, можно получить набор
равнопрочных конструкций и затем путем технико-экономического анализа выбрать
конструкцию с минимальной стоимостью.
При усилении
конструкции при достижении коэффициента прочности
слоем асфальтобетона следует учитывать износ
покрытия. С учетом точности расчетов его можно принять
.
Толщину слоя асфальтобетона рассчитывают из условия, чтобы к году, когда
интенсивность движения расчетного автомобиля достигнет 1000 авт./сут,
коэффициент прочности был равен
.
Следующее усиление
конструкции производят в год, когда интенсивность движения расчетного
автомобиля достигнет 1000 авт./сут. Толщину слоя асфальтобетона рассчитывают из
условия, чтобы к концу срока службы коэффициент прочности был
.
Для практических
расчетов разработана программа расчета на ПЭВМ, позволяющая найти оптимальную
конструкцию.
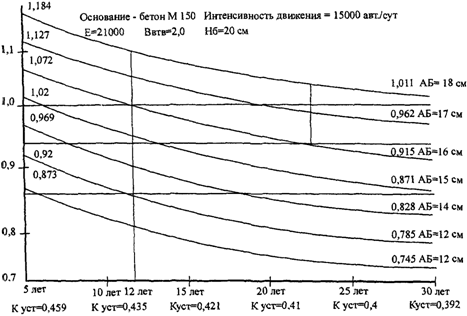
Приложение
2
МЕТОДИКА
ИЗГОТОВЛЕНИЯ
ОБРАЗЦОВ ПРИ ПОДБОРЕ БЕТОННОЙ СМЕСИ
И ЛАБОРАТОРНОМ КОНТРОЛЕ
Изготовление
контрольных образцов может осуществляться одним из предложенных способов:
- формованием на
прессе в формах-цилиндрах
:
1. Уплотняющая
нагрузка должна быть 30 МПа (300 кг/см2), время
приложения нагрузки - 3 мин. На каждый вид и срок испытания изготавливают не
менее 3 образцов. Высота образца после уплотнения должна быть 100 +/- 2 мм. Массу
навески бетонной смеси рассчитывают по теоретической насыпной плотности бетона
и объему образца.
2. Форму со
вставленным нижним вкладышем протирают влажной тканью и наполняют
предварительно взвешенной цементобетонной смесью через металлическую воронку. Смесь
укладывают в два слоя, каждый равномерно распределяют и штыкуют смесь в форме
ножом или шпателем 15 раз; затем вставляют верхний вкладыш и устанавливают
форму на нижнюю плиту пресса для уплотнения. Нагрузку доводят до 30,0 МПа и
выдерживают 3 мин; после чего нагрузку снимают, а образец извлекают из формы
выжимным приспособлением.
Не допускается
отделение воды из бетонной смеси при ее формовании. Если наблюдается
водоотделение или коэффициент уплотнения менее
, состав
бетона должен быть откорректирован.
Образцы с дефектами
(облом кромок и непараллельность верхней и нижней граней, раковины на боковой
поверхности) выбраковываются.
- Вибрирование с
пригрузом:
1. Изготовление
образцов должно осуществляться в формах-кубах 10 x 10 x 10 см или
формах-призмах 10 x 10 x 40 см вибрированием с пригрузом на стандартной
лабораторной виброплощадке в течение 3 мин. Вес пригруза 40 г/см2.
2. Способ и режим
твердения образцов бетона следует осуществлять по ГОСТ 10180-90 и ГОСТ 18105-86.
Приложение
3
ОПРЕДЕЛЕНИЕ
ПЛОТНОСТИ СВЕЖЕУЛОЖЕННОГО БЕТОНА
1. Метод замещения
объема
В уложенном слое
делают лунки диаметром около 25 см. Материал тщательно выбирают из лунок и
помещают в резиновые или целлофановые мешки, плотно завязывают, чтобы сохранить
влажность отобранной бетонной смеси.
Для определения
объема лунок над каждой из них устанавливают кольцо и воронку (см. рисунок).
Через воронку лунку заполняют до краев кольца одномерным сухим песком средней
крупности. Для нахождения объема лунок и кольца песок насыпают мерными сосудами
емкостью 2, 1, 0,5, 0,25 л (с делениями).
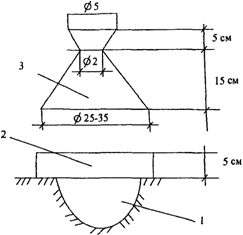
Определение
плотности свежеуложенного бетона
методом засыпки
лунки песком:
1 - лунка; 2 -
кольцо; 3 - воронка
Среднюю плотность
свежеуложенного бетона вычисляют по формуле
, г/см3,
где P - масса пробы
бетона, взятой из лунки, г;
V - объем сухого
песка, необходимого для заполнения лунки и кольца, см3;
- объем кольца, см3.
2. Прибором КП-120
В уложенном слое
делают лунки диаметром 25 см, а тщательно выбранную из лунок бетонную смесь
помещают в резиновые или целлофановые мешки и взвешивают.
Объем лунки
определяют прибором КП-120. Объем лунки, соответствующий объему извлеченного из
нее материала, находят заполнением лунки через резиновый баллон из
измерительного цилиндра водой, вытесняемой избыточным давлением, которое
создается в цилиндре насосом. Величину объема лунки устанавливают по разности
уровней воды в цилиндре до и после заполнения лунки. Среднюю плотность
свежеуложенного бетона определяют по формуле
, г/см3,
где V - объем
лунки, определенный прибором КП-120, см3.
Приложение
4
МЕТОДИКА
ОПРЕДЕЛЕНИЯ
ЖЕСТКОСТИ БЕТОННОЙ СМЕСИ В ПОЛЕВЫХ УСЛОВИЯХ
Жесткость бетонной
смеси в полевых условиях определяется с помощью прибора Союздорнии для
стандартного уплотнения и характеризуется количеством ударов, затрачиваемых для
достижения заданной плотности смеси.
Плотностью бетонной
смеси задаются 2400 кг/м3.
При подготовке
прибора на стойке с уплотнителем наносится риска, соответствующая положению
нижней поверхности стойки с уплотнителем, передающим ударную нагрузку, на
верхней плоскости разъемного стакана.
На весах взвешивают
навеску бетонной смеси, соответствующую объему разъемного цилиндра, умноженного
на заданную плотность бетонной смеси.
Внутреннюю
поверхность разъемного цилиндра и верхнего стакана протирают влажной тканью.
Бетонную смесь в
цилиндре уплотняют в два слоя.
Половину навески
укладывают в разъемный цилиндр, штыкуют 10 раз ножом и уплотняют гирей 2,5 кг.
Для уплотнения первого слоя принимают 60 ударов гири.
Затем стойку с
уплотнителем снимают, поверхность уплотненного бетона рыхлят ножом, высыпают
вторую половину навески и продолжают уплотнение бетонной смеси до совмещения
риски на стойке с уплотнителем с верхней плоскостью стакана.
По полученному
общему количеству ударов с помощью тарировочной кривой дважды определяют
жесткость бетонной смеси.
Общее время
испытания смеси не должно превышать 15 мин.
Тарировочную кривую
(зависимость между различной жесткостью бетонной смеси, определенной по ГОСТ
10181-00 и количеством ударов на приборе Союздорнии для достижения заданной
плотности бетона) строят для конкретных составов бетонных смесей в лабораторных
условиях. При изменении материалов, входящих в состав бетонной смеси,
тарировочная кривая уточняется.